最新IE生产线平衡资料
合集下载
IE生产线平衡的资料PPT资料37页

稼动率=投入工时/可供工时 *100% 计划停线工时=计划停线时间*人数 计划停线时间=无计划时间+换线时间+判停时间
上例中,若换线时间是15分钟,则计划停线工时为20人 *15min=300min=5H,则投入工时和稼动率为:
60H-5H=55H 稼动率=55H/60H=92%
2019/10/22
时间测试
分解动作时间量测,一般每个动作测量5 次为宜; 量测人员应站在作业员斜后面1米以外, 以能看清楚全部操作动作为准则; 测试中不能打扰作业员的正常操作和引 起作业员的紧张;
时间测量流程
作业内容
数据与信息记录
测试中判断作业员的速度水平,并作如 实记录,不可修改量测数据; 若有其他特殊情況,也应加以实录;
2019/10/22
6
相关的概念
概念6:平衡损失 平衡损失=(总工时-单件标准时间)*设定产能
时间
T1 T2 T3 T4 T5
等待时间
单个产品平衡损失 =等待时间之和
S1 S2 S3 S4 S5
工站
概念7:平衡率100%代表﹕ 1.工站之间无等待,前后产能一致﹔ 2.工站节拍相同,动作量相同(动作量是指工站中各种必要动
素的时间总量); 3.平衡损失时间为零; 4.设计效率最大化; 5.前后流程的设计可以更完善(如下图).
2019/10/22
7
相关的概念
(交叉流程)
(直通流程 1 ) (直通流程 2 )
概念8:高效率 1. 通常认为高效率就是:快速,简单&大规模 2. 我们认为沒有浪费的时候才是高效率的 操作效率=实际产量/设定产能*100% 整体工厂效率(OPE)=平衡率*稼动率*操作效率
上例中,若换线时间是15分钟,则计划停线工时为20人 *15min=300min=5H,则投入工时和稼动率为:
60H-5H=55H 稼动率=55H/60H=92%
2019/10/22
时间测试
分解动作时间量测,一般每个动作测量5 次为宜; 量测人员应站在作业员斜后面1米以外, 以能看清楚全部操作动作为准则; 测试中不能打扰作业员的正常操作和引 起作业员的紧张;
时间测量流程
作业内容
数据与信息记录
测试中判断作业员的速度水平,并作如 实记录,不可修改量测数据; 若有其他特殊情況,也应加以实录;
2019/10/22
6
相关的概念
概念6:平衡损失 平衡损失=(总工时-单件标准时间)*设定产能
时间
T1 T2 T3 T4 T5
等待时间
单个产品平衡损失 =等待时间之和
S1 S2 S3 S4 S5
工站
概念7:平衡率100%代表﹕ 1.工站之间无等待,前后产能一致﹔ 2.工站节拍相同,动作量相同(动作量是指工站中各种必要动
素的时间总量); 3.平衡损失时间为零; 4.设计效率最大化; 5.前后流程的设计可以更完善(如下图).
2019/10/22
7
相关的概念
(交叉流程)
(直通流程 1 ) (直通流程 2 )
概念8:高效率 1. 通常认为高效率就是:快速,简单&大规模 2. 我们认为沒有浪费的时候才是高效率的 操作效率=实际产量/设定产能*100% 整体工厂效率(OPE)=平衡率*稼动率*操作效率
IE生产线平衡资料

详细描述
瓶颈工序分析的目的是找出生产线上存在瓶颈工序的原因,并采取措施对其进行 优化或调整,以提高整个生产线的平衡率和产能。针对瓶颈工序的优化措施可能 包括改进工艺流程、提高设备精度、增加人员培训等。
04
生产线平衡的优化方法
调整工序作业内容
总结词
通过合理分配作业内容,平衡各工序 的工作量,提高生产效率。
实现生产计划的高效执行,缩短产品从投入到产 出的时间,提高整体生产效率。
降低生产成本
通过优化生产流程和减少浪费, 降低原材料、能源和水等资源
的消耗。
减少生产过程中的设备和人 力成本,提高设备和人力资
源的利用效率。
提高生产效率可以降低单位产 品的成本,从而增加企业的市
场竞争力。
提升产品质量
01
生产线平衡有助于确保产品在生产过程中的稳定性和一致性, 减少不良品和次品率。
06
结论
生产线平衡的成果与收益
生产效率提升
质量稳定性增强
通过优化生产线布局和平衡各岗位工作量 ,显著提高了生产效率,缩短了生产周期 ,减少了在制品数量。
平衡的生产线减少了操作员之间的差异, 降低了产品缺陷率,提高了质量的稳定性 和一致性。
减少浪费
提高员工满意度
生产线平衡有助于减少生产过程中的等待 、空闲和搬运等浪费,降低了生产成本。
02
提高生产过程的可控制性和可预测性,及时发现和解决生产过
程中的问题。
通过优化生产流程和提高员工技能,提高产品质量的整体水平,
03
满足客户需求。
03
生产线平衡的评估指标
生产线平衡率
总结词
生产线平衡率是评估生产线平衡状态的重要指标,它反映了生产线上各工序作业时间的均衡程度。
瓶颈工序分析的目的是找出生产线上存在瓶颈工序的原因,并采取措施对其进行 优化或调整,以提高整个生产线的平衡率和产能。针对瓶颈工序的优化措施可能 包括改进工艺流程、提高设备精度、增加人员培训等。
04
生产线平衡的优化方法
调整工序作业内容
总结词
通过合理分配作业内容,平衡各工序 的工作量,提高生产效率。
实现生产计划的高效执行,缩短产品从投入到产 出的时间,提高整体生产效率。
降低生产成本
通过优化生产流程和减少浪费, 降低原材料、能源和水等资源
的消耗。
减少生产过程中的设备和人 力成本,提高设备和人力资
源的利用效率。
提高生产效率可以降低单位产 品的成本,从而增加企业的市
场竞争力。
提升产品质量
01
生产线平衡有助于确保产品在生产过程中的稳定性和一致性, 减少不良品和次品率。
06
结论
生产线平衡的成果与收益
生产效率提升
质量稳定性增强
通过优化生产线布局和平衡各岗位工作量 ,显著提高了生产效率,缩短了生产周期 ,减少了在制品数量。
平衡的生产线减少了操作员之间的差异, 降低了产品缺陷率,提高了质量的稳定性 和一致性。
减少浪费
提高员工满意度
生产线平衡有助于减少生产过程中的等待 、空闲和搬运等浪费,降低了生产成本。
02
提高生产过程的可控制性和可预测性,及时发现和解决生产过
程中的问题。
通过优化生产流程和提高员工技能,提高产品质量的整体水平,
03
满足客户需求。
03
生产线平衡的评估指标
生产线平衡率
总结词
生产线平衡率是评估生产线平衡状态的重要指标,它反映了生产线上各工序作业时间的均衡程度。
IE生产线平衡资料课件
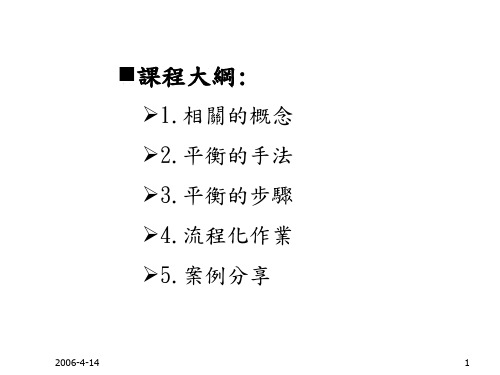
平衡的步驟
Steps 7: 改善總結報告: 平衡率 設定產能﹑實際產能﹑人均產能(單機產能) 損失分析 品質分析 成本改善率 Steps 8: 標準化
流程化作業
1. 平衡率目標:與大設備相連≧85% 其他≧ 95%
2. 平衡改善小組的職責:
生產單位:改善前/后之工時測量,山積表制作﹑分析及改善方案之實施.制工單位:協助生產單位擬定及推動改善方案,跟蹤方案效果評估及各種相關文件修訂及系統表單發行﹔品管單位:負責改善前/后產品品質評估﹔工務單位:主導及其它改善事項協助﹐設備改善﹔ IE﹑經管﹑企划:改善前后產線效益評估及跟進.
平衡的步驟
S1標准時間為﹕t2+t3; S1工站時間為﹕t4
S1-2
S1-1
當S1-1不需等S1-2就能開始, S1工站時間為﹕ T3+S1-1提前開始的時間(t4-t3)
S1工站時間=?
?
Steps 5: 建立新的模擬流程 新的FLOW CHART/ SOP (SWR發行)Steps 6: 實施新的模擬流程 改善后時間測量 改善后山積表制作
程序分析使用的圖表: 工藝程序圖 / 流程程序圖/ 路線圖程序分析符號--表示操作--表示搬運/運輸--表示檢驗--表示暫存或等待--表示受控的貯存 --派生符號,由上面的符號合成.
程序改善
例: 流程程序圖
程序分析技巧通過5W1H系統地分析程序的組成是否合理和必要“ECRS”四大原則: 取消(Eliminate); “完成了什么?是否必要?為什么?” 合並(Combine); “誰完成?何時完成?哪里?如何?” 重排(Rearrange); 取消合並重排 簡化(Simplify); 確認必要簡單方法/設備生產.五大內容: 工藝流程分析—取消/合並/重排工序,減少浪費 搬運分析—考量重量、距離、方法、工具、路線 檢驗分析—按產品要求設計合理站點和方法 貯存分析—使物料及時供應 等待分析—減少和消除引起等待的因素
Steps 7: 改善總結報告: 平衡率 設定產能﹑實際產能﹑人均產能(單機產能) 損失分析 品質分析 成本改善率 Steps 8: 標準化
流程化作業
1. 平衡率目標:與大設備相連≧85% 其他≧ 95%
2. 平衡改善小組的職責:
生產單位:改善前/后之工時測量,山積表制作﹑分析及改善方案之實施.制工單位:協助生產單位擬定及推動改善方案,跟蹤方案效果評估及各種相關文件修訂及系統表單發行﹔品管單位:負責改善前/后產品品質評估﹔工務單位:主導及其它改善事項協助﹐設備改善﹔ IE﹑經管﹑企划:改善前后產線效益評估及跟進.
平衡的步驟
S1標准時間為﹕t2+t3; S1工站時間為﹕t4
S1-2
S1-1
當S1-1不需等S1-2就能開始, S1工站時間為﹕ T3+S1-1提前開始的時間(t4-t3)
S1工站時間=?
?
Steps 5: 建立新的模擬流程 新的FLOW CHART/ SOP (SWR發行)Steps 6: 實施新的模擬流程 改善后時間測量 改善后山積表制作
程序分析使用的圖表: 工藝程序圖 / 流程程序圖/ 路線圖程序分析符號--表示操作--表示搬運/運輸--表示檢驗--表示暫存或等待--表示受控的貯存 --派生符號,由上面的符號合成.
程序改善
例: 流程程序圖
程序分析技巧通過5W1H系統地分析程序的組成是否合理和必要“ECRS”四大原則: 取消(Eliminate); “完成了什么?是否必要?為什么?” 合並(Combine); “誰完成?何時完成?哪里?如何?” 重排(Rearrange); 取消合並重排 簡化(Simplify); 確認必要簡單方法/設備生產.五大內容: 工藝流程分析—取消/合並/重排工序,減少浪費 搬運分析—考量重量、距離、方法、工具、路線 檢驗分析—按產品要求設計合理站點和方法 貯存分析—使物料及時供應 等待分析—減少和消除引起等待的因素
生产线平衡概述(IE)

生产线平衡--简述
1.生产线平衡的定义 2.生产线平衡的计算 3.提高生产线平衡的方法
1.生产线平衡的定义
• 生产线平衡:即对生产的全部工序进行平均化,调
整作业负荷,以使各作业时间尽可能相近的技术手段与方 法。 • 目的:是消除作业间不平衡的效率损失以及生产过剩。
2.生产线平衡的计算
• 生产线的平衡计算式 :
• 平衡率=(各工序时间总和/(工站数*CT))*100% • CT即节拍,指最长工序(瓶颈工序)时间。
以某条流水线为例,共7个工序,瓶颈工序为工序6:。
如上: 平衡率=T/CT*7=53.64/(8.95*7)=85%
ห้องสมุดไป่ตู้
3.怎样提高生产线平衡
• 1、对瓶颈工序进行作业改善,优化瓶颈工序的作业方法,操作动作, 以及改善工装夹具等。 • 2、运用ECRS原则改善生产流程。
取消(Eliminate):该工作或动作完成了什么?是否必要或可以取消? 合并(Combine): 如果工作或动作不能取消,则考虑能否可与其他工作合 并。 重排(Rearrange): 对工作的顺序进行重新排列。 简化(Simplify); 指工作内容和步骤的简化,亦指动作的简化,能量的节 省。
• 3、增加全能工来平衡流水,只要平衡率提高了,人均产量就等于提 高了,单位产品成本也随之下降。
以上 谢谢观阅!
IE工程师:
1.生产线平衡的定义 2.生产线平衡的计算 3.提高生产线平衡的方法
1.生产线平衡的定义
• 生产线平衡:即对生产的全部工序进行平均化,调
整作业负荷,以使各作业时间尽可能相近的技术手段与方 法。 • 目的:是消除作业间不平衡的效率损失以及生产过剩。
2.生产线平衡的计算
• 生产线的平衡计算式 :
• 平衡率=(各工序时间总和/(工站数*CT))*100% • CT即节拍,指最长工序(瓶颈工序)时间。
以某条流水线为例,共7个工序,瓶颈工序为工序6:。
如上: 平衡率=T/CT*7=53.64/(8.95*7)=85%
ห้องสมุดไป่ตู้
3.怎样提高生产线平衡
• 1、对瓶颈工序进行作业改善,优化瓶颈工序的作业方法,操作动作, 以及改善工装夹具等。 • 2、运用ECRS原则改善生产流程。
取消(Eliminate):该工作或动作完成了什么?是否必要或可以取消? 合并(Combine): 如果工作或动作不能取消,则考虑能否可与其他工作合 并。 重排(Rearrange): 对工作的顺序进行重新排列。 简化(Simplify); 指工作内容和步骤的简化,亦指动作的简化,能量的节 省。
• 3、增加全能工来平衡流水,只要平衡率提高了,人均产量就等于提 高了,单位产品成本也随之下降。
以上 谢谢观阅!
IE工程师:
IE工业工程训练之生产线平衡

數據整理和計算
測試完畢,對數據進行整理和計算,補充測量有懷疑 或錯漏的數據; ❖ 計算可信度95%所需的樣本數量,補測差異樣本數量
資料分析與處理
對量測記錄之所有資料進行分析,對比ST的差異程 度,解決發現的問題; ❖ 若分析發現標準時間制定不當,應及時修改,必要時 調整制程.
工時測量的作用﹕
❖ 獲取各工站的實際操作時間﹐為山積表制作﹐時間平 衡作准備﹔
(直通流程 2 )
相關的概念
概念9:改善
I. 同樣的投入更大的輸出; II. 不增值(無效)增值(有效)
?不增值? 等待 不良 庫存 移動 ……
例1: 減少移動與庫存提高效率 例2: 減少無效動作提高效率
概念10:多能工
平衡的手法
工時測量 山積表 程序改善 損失分析 作業條件改善 打破平衡
3.平衡損失時間為零
4.設計效率最大化
5.前后流程的設計可以更完善(如下圖)
相關的概念
(交叉流程)
(直通流程 1 )
概念8:高效率 1. 通常認為高效率就是:快速,簡單&大規模 2. 我們認為沒有浪費的時候才是高效率的 操作效率=實際產量/設定產能*100% 整體工廠效率(OPE)=平衡率*稼動率*操作效率
燥劑放入箱內
13 封裝及貼出廠標簽
搬運到暫存區 暫存等待出貨
程序改善
❖ 程序分析技巧
1. 通過5W1H系統地分析程序的組成是否合理和必要
2. “ECRS”四大原則:
3.
取消(Eliminate); “完成了什么?是否必要?為什
么?”
❖ 合並(Combine); “誰完成?何時完成?哪里?如何?”
IE工业工程训练之生产线平衡
課程大綱:
现场IE改善案例分析生产线平衡分析改善案例
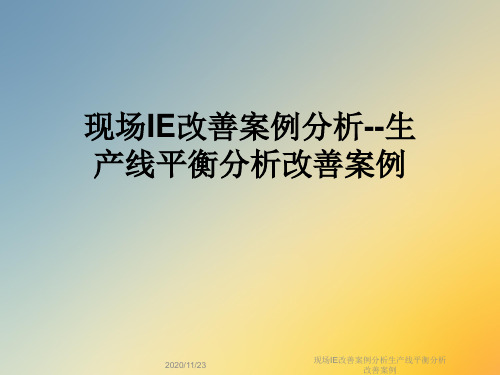
不平衡率(%)= 100% —平衡率(%)
对生产线来说,不平衡率越小越好,一般控 制5%-13%之间,至少要控制在15%以下。
现场IE改善案例分析生产线平衡分析 改善案例
案例:工时测定和线平衡计算
请大家观看电子分厂电装3人柔性线视频
1、一边看一边测试,最后计算平衡率 2、计算一下线小时理论产量 3、提出提升线平衡的思路方法
(1)改善的4大原則
1)减少动作次数 2)同时使用双手 3)缩短移动距离 4)使动作变得轻松
现场IE改善案例分析生产线平衡分析 改善案例
(2) IE动作改善的4原则:
ECRS原则 1、Eliminate ——取消 2、Combine ——合并 3、Rearrange ——重排 4、Simplify ——简化
现场IE改善案例分析生产线平衡分析 改善案例
生产线平衡的改善实例
电子电装7人柔性线,改善前各工位的作业时间如下所示:
现场IE改善案例分析生产线平衡分析 改善案例
生产线平衡的改善实例
电子电装7人柔性线,改善前各工位的作业时间如下所示:
现场IE改善案例分析生产线平衡分析 改善案例
生产线各工位的分析如下:
生产线改善前后各管理指标比较
1、生产线平衡率方面
生产线平衡效 率提高了52%
2、工人人数方面
工人人数由原 来的7人减少至 于3人
3、生产效率方面
生产效率提升 了12.1%
现场IE改善案例分析生产线平衡分析 改善案例
全员参与的思想准备
• 给予和获取信息 • 接受非寻常的工作方法和解决方案 • 对目前的方法提出疑问 • 不允许找借口 • 马上改正错误 • 问五个“为什么”,发掘出问题的真正原因 • 每个人意见都是有价值的 • 不追求完美,一个60%的解决方案,比一个几乎
IE手法生产线平衡ppt课件
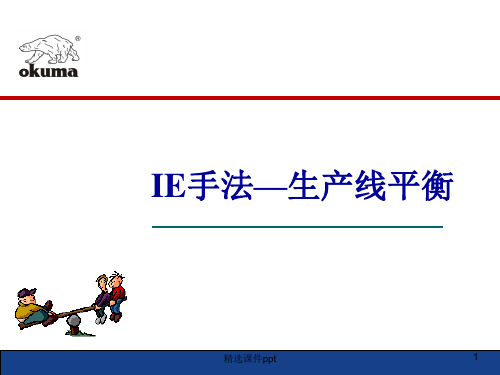
作 业 时 间
工序 1 2 3 4 5
2、合并作业 省略工序
精选课件ppt
1人
作
业
2人
时
间
工序 1 2 3 4 5
3、减人
34
提高平衡率的四大手法
符号 名 称
内容
E
取 消 任何无价值的可作以业不,做如吗?搬运等,
Eliminate 予以取消 如果不做会变如何?
C
合 并 对可于以把无两法个取以消上而的又工程必结要合者在,一看起是吗否?
了解﹐如出现不平衡的状态时﹐习惯用人员增补来 弥补﹐这是一个不动脑筋的做法﹐不足为取。
除了上面介绍的技法以外﹐也可以对材料﹑零件包
括设计方法来检讨﹐有否缩短工时的方法。
生产线补进新手时﹐因新手对工作不熟悉﹐熟练不
足。在配置上尤其要注意﹐会造成很大的不平衡使 产量大幅度下降﹐或对新手造成异常的工作压力。
IE手法—生产线平衡
精选课件ppt
1
精选课件ppt
2
生产线中的问题点
WIP(在制品) 生产周期长 各种浪费多(等待、动作、搬运…) ……
精选课件ppt
3
产生这些问题的主要原因
生产线中各工序时间不均衡
精选课件ppt
4
生产平衡的两个基本概念
瓶颈
标准工时
精选课件ppt
5
什么是瓶颈?
瓶颈是企业在 实现其目标的过 程中现存的或潜
如生产在线的各个工序都能互相配合无间﹐我 们称之谓生产线平衡﹐而这生产线定能获得一 定的效益;
但如各工序间不能相互配合﹐拥有不少等候的 时间﹐这情况我们则称之谓生产线不平衡。
精选课件ppt
15
影响的因素
生产线平衡IE教材

估算
分支定界—举例
第3步:可能的方案
方案3-1:{(3), (8)} 方案3-2:{(7)} T31 = 5+3 = 8, S31 = [(46-10-8-8)/10]+3=5 T32 = 6, S31 = [(46-10-8-6)/10]+3=6 选方案3-1进行
估算
分支定界—图示
(1), (2), (5)
(4), (5) (3), (8) (7) (10) (7)
(1), (2), (6)
(3), (5) (4) (7), (5) (3), (9)
(4), (8)
(9), (10)
(10), (11)
(11)
COMSO 2) A为当前所有没有分配的作业集合 3) B为A中从顺序约束的要求的意义上说可选 择的作业集合 4) 如果iB, 且tiT,那么将i置于F, 如果B中没 有任何i能满足, 则T=C 5) 从F中随机选取一个作业i, A=A-i, T=T-ti, 此时,如果A为空,算法停止, 否则转3).
COMSOAL—例子
节拍C=70秒
计算过程
位置排序法
对所有作业i计算它本身和它所有的后续作业 的加工时间的和,记为Pwi, 将Pwi按大小排序 按照排序先后和分配工序。
位置排序法—例
作业
a b
PW
138 118
序号
1 3
作业
g h
PW
102 87
序号
5 7
c
d e f
112
123 85 97
A A A A B B B B i i C C C i i A 0 A A B 0 B B C 0 C C A B
IE现场培训流水线平衡-组长1解读

通过这样一个分析,可以看出,工价有解决的方式,但车间停顿仍然是一个很大 的因素,它很大程度上影响到正常生产,工人的应得收入.
工人停顿多了,就会越来越懒了,而且会更难管了。不管是什么原因,组长 必须去找办法解决,长期麻烦的不会是别人,只会是组长自己。
因此,解决的办法,就是做好生产线平衡。
三、了解生产平衡的概念
主要原因
B.工人有事不做
③走动搬运/机器修理(与生产环境/机器有关)
工人的自我意识,可控性,与车间管理有关 C.工人时做时不做
停顿所带来的影响
工人的收入少,工人人心不稳,流动量大,难管理; 完成不了上级给的目标.每天要解释,心情也不好; 组长每天这里跑那里忙,没时间管理生产现场……
必须认识到的事
分析 总作业时间
897.14
总作业人数
32
瓶颈时间
34.82" 小时产量
103
平衡率
合计
32 897 80.51% 人当理论产量 32.3
改善落筒贴工序:瓶颈在落筒贴,建议把修筒顶留给纳膊做。
生产线平衡测试
改善后:
Pitch Diagram
40.0
35.0
30.0
25.0
20.0
15.0
10.0
5.0
将工序总时间按照人数进行平均化分配, 使各作业人员所做单件工序花费的时间尽可 能相近,以此确保进货量与出货量均衡,工序产 量保持均衡的一种方法,这种方法也是生产 流程设计中最重要的方法
生产线平衡的条件及好处
条件: 样衣; 工序表信息的及时性与准确性(主要在工序上与工时上); 产前准备是否充分:辅料、裁片等是否能满足第二天的生产需求 组员的技术特点合理分配工艺流程,提前准备好排位; 组员配合和现场跟进平衡人员合理的测时调整……
工人停顿多了,就会越来越懒了,而且会更难管了。不管是什么原因,组长 必须去找办法解决,长期麻烦的不会是别人,只会是组长自己。
因此,解决的办法,就是做好生产线平衡。
三、了解生产平衡的概念
主要原因
B.工人有事不做
③走动搬运/机器修理(与生产环境/机器有关)
工人的自我意识,可控性,与车间管理有关 C.工人时做时不做
停顿所带来的影响
工人的收入少,工人人心不稳,流动量大,难管理; 完成不了上级给的目标.每天要解释,心情也不好; 组长每天这里跑那里忙,没时间管理生产现场……
必须认识到的事
分析 总作业时间
897.14
总作业人数
32
瓶颈时间
34.82" 小时产量
103
平衡率
合计
32 897 80.51% 人当理论产量 32.3
改善落筒贴工序:瓶颈在落筒贴,建议把修筒顶留给纳膊做。
生产线平衡测试
改善后:
Pitch Diagram
40.0
35.0
30.0
25.0
20.0
15.0
10.0
5.0
将工序总时间按照人数进行平均化分配, 使各作业人员所做单件工序花费的时间尽可 能相近,以此确保进货量与出货量均衡,工序产 量保持均衡的一种方法,这种方法也是生产 流程设计中最重要的方法
生产线平衡的条件及好处
条件: 样衣; 工序表信息的及时性与准确性(主要在工序上与工时上); 产前准备是否充分:辅料、裁片等是否能满足第二天的生产需求 组员的技术特点合理分配工艺流程,提前准备好排位; 组员配合和现场跟进平衡人员合理的测时调整……
IE基础知识培训生产线平衡分析.pptx

1.缩短生产一个产品的组装时间(增加单位时间的产量) 2.提高生产线的工作效率(包括作业人员,工具,设备) 3.减少工程间的准备工作 4.改善生产线的平衡 5.对新的流程作业方式改善制造方法
3/38
生产线平衡的优点
1. 平均分配各作業員的工作負荷 2. 找出瓶頸作業項目 3. 建立裝配線的標準速度 4. 決定工位的數目 5. 決定裝配以及包裝的人工成本 6. 決定每項作業項目佔總工作量的百分比 7. 幫助工廠佈置的工作 8. 降低生產成本
1/38
IE 基 础 知 识 培 训
---生产线平衡分析
2/38
生产线平衡的定义
依照流動生產的工程順序 ,從生產目標算出週期時間 ,將作業分割或結合,使各工作站的負荷均勻,提高生產效 率的技法,稱之生产线平衡。
生产线平衡的目的
生产线平衡的目的是通过平衡生产线使现场更加容易理解 “一个流”的必要性及生产作业控制的方法。
11/38
使用标准时间的优点
1 客观分析动作,不受产品性质,作业性质等影响.避免了对 操作者熟练程度,工作状态等的判断及对ST的影响.
2 避免了以往经验数据和停表法的人为因素对ST影响,提高 产能评估精度.
3 能发现操作人员的无效动作和浪费现象,可使操作者,操作 对象,工具三者合理地布置和安排.简化操作方法,删除无 效动作.
4 合理调配工位,提高平衡率
提高效率.
5 利用绩效管理,评估操作的工作表现.
6 增强分析者和操作者的信心.
12/38
标准时间的建立
1 专业时间分析法有:胶卷分析法;跑表法;PTS 法;WF法;MTM法等等.现在SONY工司将以上法 则综合起来,业内人士称为MOST法.但此法则 没有世界认证和论文出版,这里也不做详细解 释.
3/38
生产线平衡的优点
1. 平均分配各作業員的工作負荷 2. 找出瓶頸作業項目 3. 建立裝配線的標準速度 4. 決定工位的數目 5. 決定裝配以及包裝的人工成本 6. 決定每項作業項目佔總工作量的百分比 7. 幫助工廠佈置的工作 8. 降低生產成本
1/38
IE 基 础 知 识 培 训
---生产线平衡分析
2/38
生产线平衡的定义
依照流動生產的工程順序 ,從生產目標算出週期時間 ,將作業分割或結合,使各工作站的負荷均勻,提高生產效 率的技法,稱之生产线平衡。
生产线平衡的目的
生产线平衡的目的是通过平衡生产线使现场更加容易理解 “一个流”的必要性及生产作业控制的方法。
11/38
使用标准时间的优点
1 客观分析动作,不受产品性质,作业性质等影响.避免了对 操作者熟练程度,工作状态等的判断及对ST的影响.
2 避免了以往经验数据和停表法的人为因素对ST影响,提高 产能评估精度.
3 能发现操作人员的无效动作和浪费现象,可使操作者,操作 对象,工具三者合理地布置和安排.简化操作方法,删除无 效动作.
4 合理调配工位,提高平衡率
提高效率.
5 利用绩效管理,评估操作的工作表现.
6 增强分析者和操作者的信心.
12/38
标准时间的建立
1 专业时间分析法有:胶卷分析法;跑表法;PTS 法;WF法;MTM法等等.现在SONY工司将以上法 则综合起来,业内人士称为MOST法.但此法则 没有世界认证和论文出版,这里也不做详细解 释.
IE之平衡生产线LineBalancing
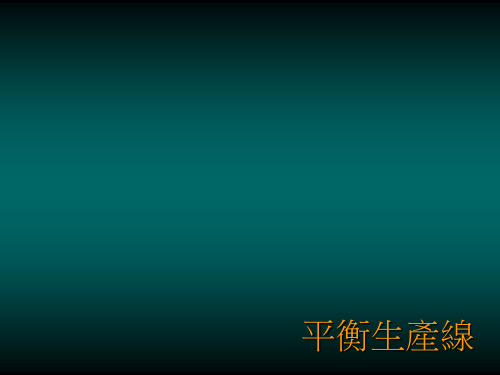
# of pieces of Std. WIP
95 Pair
TAKT Time
Part Path
Total Square Feet
54.0 sq.mtr.
作業/練習: 加工過程繪製圖
➢ 去工廠 ➢ 將目前的加工過程狀況完成於其標準作
業表單內
記錄目前的狀況
1. 目前處境的基本狀況 2. 產品製程與加工過程繪製圖
時間為1週期
c Copyright, All Rights Reserved Productivity, Inc. 1999
觀察的 加工過程:
貼大底
No.
作業部位
12
時間觀察表單
3 4 56 7 8 9
日期:
6/28/00 觀察者:
Rich
時間:
1:54PM 觀察者:
Fred
Component
10 11 12 13 14 15 Task Time
附加價值率 (一雙)
建議
%
記錄目前的狀況
1. 目前處境的基本狀況 2. 產品製程與加工過程繪製圖
(標準作業表單=SWS) 3. 時間觀察測試表單 (TOS) 4. 間隔時間 (end-of-line rate)
間隔時間 (Takt Time)
➢ 工廠的節奏:
每雙產品之客戶率須滿足客戶的需求
➢ 計算:
觀察的 加工過程:
貼大底
No.
作業部位
1 拿鞋面
2 拿大底
3 鞋面貼大底
4 放入輸送帶
12 5 10 170 180
時間觀察表單
3 4 56 7 8 9
日期:
6/28/00 觀察者:
Rich
精选IE工业工程生产线平衡课件
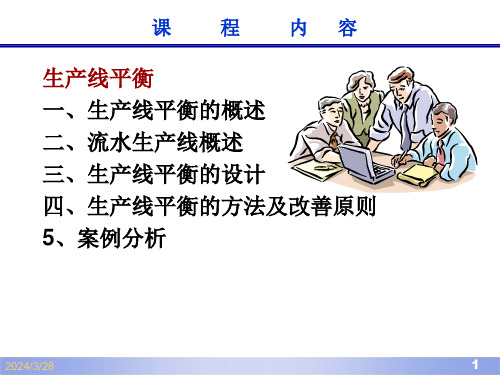
1、 流水生产线平衡设计应解决的若干基本问题
三、流水生产线平衡的设计方法
● 进行产品和零件的分类● 改进产品和零件的结构,使之适合流水生产● 审查和修改工艺规程● 收集整理设计工作所需要的资料
2、 流水线平衡设计的准备工作
三、流水生产线平衡的设计方法
G
7
E
H
11
E
I
3
G、H
总时间
66
解:
阶位法的工作步骤如下
① 作图表示装配工艺过程中各作业元素的先后关系,并标明每项作业元素的时间。 ② 从作业元素先后关系图找出每项作业元素的后续作业元素,计算它们的时间总和,即每项作业元素的阶位值。 ③ 按阶位值的大小,由大到小,将作业元素排队,制成作业元素阶位表。 ④ 从阶位值最高的作业元素开始,向工作地分配作业要素。每分配一项作业元素,计算一次在节拍时间内的剩余时间。若剩余时间足够安排另一项作业元素,从阶位表中找出阶位值次高的作业元素分给该工作地。若剩余时间不够安排其它作业元素,就向下一个工作地分配,直到全部作业要素都被安排入工作地为止。
3、 单品种流水线平衡方法
②平衡图分析
②平衡图分析---改善案例:
③生产线平衡率的计算:
衡量生产线平衡的好坏,可以用生产线平衡率或平衡损失率来进行定量衡量。在计算生产线平衡率或平衡损失率前,必须先设定计算的时间基准,即生产周期。如案例2-1,可以发现决定生产线的作业时间周期的工序时间是最长工序的时间(Pitch Time),也就是说Pitch Time(节拍时间)等于周期时间 (Ct)(注:在完成各工序后,每隔Pitch Time完成一个或批产品)另外一种计算方法同样可以得到Cycle Time,即由以每小时平均成品产量,求得一个产品的Ct
三、流水生产线平衡的设计方法
● 进行产品和零件的分类● 改进产品和零件的结构,使之适合流水生产● 审查和修改工艺规程● 收集整理设计工作所需要的资料
2、 流水线平衡设计的准备工作
三、流水生产线平衡的设计方法
G
7
E
H
11
E
I
3
G、H
总时间
66
解:
阶位法的工作步骤如下
① 作图表示装配工艺过程中各作业元素的先后关系,并标明每项作业元素的时间。 ② 从作业元素先后关系图找出每项作业元素的后续作业元素,计算它们的时间总和,即每项作业元素的阶位值。 ③ 按阶位值的大小,由大到小,将作业元素排队,制成作业元素阶位表。 ④ 从阶位值最高的作业元素开始,向工作地分配作业要素。每分配一项作业元素,计算一次在节拍时间内的剩余时间。若剩余时间足够安排另一项作业元素,从阶位表中找出阶位值次高的作业元素分给该工作地。若剩余时间不够安排其它作业元素,就向下一个工作地分配,直到全部作业要素都被安排入工作地为止。
3、 单品种流水线平衡方法
②平衡图分析
②平衡图分析---改善案例:
③生产线平衡率的计算:
衡量生产线平衡的好坏,可以用生产线平衡率或平衡损失率来进行定量衡量。在计算生产线平衡率或平衡损失率前,必须先设定计算的时间基准,即生产周期。如案例2-1,可以发现决定生产线的作业时间周期的工序时间是最长工序的时间(Pitch Time),也就是说Pitch Time(节拍时间)等于周期时间 (Ct)(注:在完成各工序后,每隔Pitch Time完成一个或批产品)另外一种计算方法同样可以得到Cycle Time,即由以每小时平均成品产量,求得一个产品的Ct
生产线平衡A(IE)
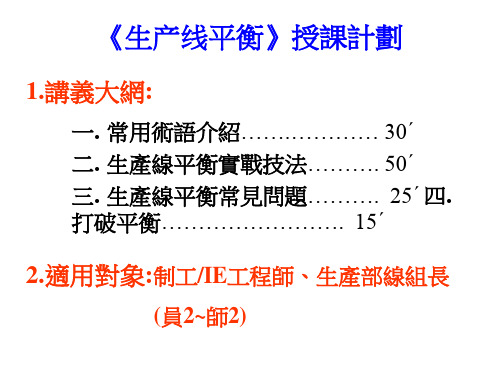
(1)取消(Eliminate)——取消不必要的工序、动作、操作, 这是不需要投资的一种改进,是改进的最高原则。
改善案例: Horizon M/B小支架取消1pc拉釘
4PCS拉釘
前板處減少1PC拉釘
改善前: M/B小支架兩端均以2PCS拉釘固定,過於密集.向設
計建議減少拉釘,最終將前板一側2PCS拉釘改為1PC拉釘.
瓶頸的制約
在流水線生產作業 模式中,制約產能的就 是瓶頸工站,一旦產生 瓶頸,前工站的產品無 法流下去,后工站無產 品可做,就會造成短暫 的停止,從而降低整條 線的產能.
瓶頸的認識
一條生產線上可能存在多個瓶頸.
瓶頸是永遠存在的,克服其中的一個,又會有另 一個工站成為新的瓶頸.
我們無法永遠地消除瓶頸,但我們可以盡可能 地使各工站處於最接近均衡的狀態,從而達到 產能和生產力的最大化.
要求 供應商 改用吸 塑包材, 並取消 打結.
改善案例:燈線包裝改善
改善前: 將每格刀卡放2PCS.
改善后: 保持原包裝,每層箱放10捆. 取消拆包裝,分裝之時間.
生產線平衡實戰技法 2. 6M分析改善法.
(1). Man (人員方面) :
1-1. 瓶頸站應由效率較佳或訓練較久之人員擔任; 1-2. 第一站工作及新手避免工作負荷過重; 1-3. 勞動強度高、易疲勞的工站建立人員輪替制度; 1-4. 鼓勵有經驗者的老手從事瓶頸站的作業; 1-5. 建立候補人員制度; 1-6. 多能工訓練;
计算公式:
節拍= 有效工作時間 產出數量
如何確定節拍? 1.依據產能需要. 2.依據產線作業模式.
例:每小時產出400台,則節拍為: 1小時 ×3600秒/小時 ÷400 = 9秒/台
例:计算节拍
改善案例: Horizon M/B小支架取消1pc拉釘
4PCS拉釘
前板處減少1PC拉釘
改善前: M/B小支架兩端均以2PCS拉釘固定,過於密集.向設
計建議減少拉釘,最終將前板一側2PCS拉釘改為1PC拉釘.
瓶頸的制約
在流水線生產作業 模式中,制約產能的就 是瓶頸工站,一旦產生 瓶頸,前工站的產品無 法流下去,后工站無產 品可做,就會造成短暫 的停止,從而降低整條 線的產能.
瓶頸的認識
一條生產線上可能存在多個瓶頸.
瓶頸是永遠存在的,克服其中的一個,又會有另 一個工站成為新的瓶頸.
我們無法永遠地消除瓶頸,但我們可以盡可能 地使各工站處於最接近均衡的狀態,從而達到 產能和生產力的最大化.
要求 供應商 改用吸 塑包材, 並取消 打結.
改善案例:燈線包裝改善
改善前: 將每格刀卡放2PCS.
改善后: 保持原包裝,每層箱放10捆. 取消拆包裝,分裝之時間.
生產線平衡實戰技法 2. 6M分析改善法.
(1). Man (人員方面) :
1-1. 瓶頸站應由效率較佳或訓練較久之人員擔任; 1-2. 第一站工作及新手避免工作負荷過重; 1-3. 勞動強度高、易疲勞的工站建立人員輪替制度; 1-4. 鼓勵有經驗者的老手從事瓶頸站的作業; 1-5. 建立候補人員制度; 1-6. 多能工訓練;
计算公式:
節拍= 有效工作時間 產出數量
如何確定節拍? 1.依據產能需要. 2.依據產線作業模式.
例:每小時產出400台,則節拍為: 1小時 ×3600秒/小時 ÷400 = 9秒/台
例:计算节拍
- 1、下载文档前请自行甄别文档内容的完整性,平台不提供额外的编辑、内容补充、找答案等附加服务。
- 2、"仅部分预览"的文档,不可在线预览部分如存在完整性等问题,可反馈申请退款(可完整预览的文档不适用该条件!)。
- 3、如文档侵犯您的权益,请联系客服反馈,我们会尽快为您处理(人工客服工作时间:9:00-18:30)。
IE生产线平衡资料
相关的概念
产出的速度取决于时间 最长的工站,称之瓶颈 瓶颈在哪里? 了解加工的过程
2020/10/22
2
相关的概念
概念1: 平衡率
用语衡量流程中各工站节拍符合度的一個综
合比值;
单件标准时间
平衡率= ----------------------100%
瓶颈时间工位数
时
T2
瓶颈时间
测试样本大小計算
山积表
山积表的使用: [图表生成方法]
山积表:将各分解动作时间,以叠加式直方图表现 的一种研究作业时间结构的手法.
样式:
產品xxx工時山積表
秒
10
8 6
0
0 1.5
1.5 0.5
1.5
10 2
1.5 2
10
0.5 1.3
2
10 3
0 4
4
4
6
1
3
1.5 3
2
2
3.5
3.5
2
2
2020/10/22
4
相关的概念
概念4:设定产能 设定产能(H) =3600(S)/瓶颈时间(S) 设定产能(班)=投入時間/瓶颈时间(S)
思考:1)为什么设定产能(班) =投入工时/总工时 总工时=瓶颈时间*作业人数
2)总工时 VS 单件标准时间
概念5:实际产量 实际产量是可供时间內所产出的良品数 1)人均产能=实际产量/投入时间/人数 2)单机台产能=实际产量/投入时间/机台数
时间测试
分解动作时间量测,一般每个动作测量5 次为宜; ❖ 量测人员应站在作业员斜后面1米以外, 以能看清楚全部操作动作为准则; 测试中不能打扰作业员的正常操作和引 起作业员的紧张;
时间测量流程
作业内容
数据与信息记录
测试中判断作业员的速度水平,并作如 实记录,不可修改量测数据; ❖ 若有其他特殊情況,也应加以实录;
0
12 0.5
1.8 1
1.5
10
10
2 2.5 5 2
1
0
0 2
0.5 1
2
10 2
12
2 1.5 6.5 4
2 2.5
1
M5 M4 M3 M2 M1
S1 S2 S3 S4 S5 S6 S7 S8 S9 S10 S11 S12 S13 S14 S15 S16 工站
工時测量(秒表)
工具: 秒表 ❖ 观测板、铅笔 时间记录表、计算器 山积表
方式: 一般测时法 ❖ 连续测时法
2020/10/22
10
时间测量流程
作业內容
选定测试工站
选定工站,阅读SOP和观察作业员操作,了解 該工站的全部操作內容;并询问作业员加以 确认;
拆解动作
将工站动作拆解成若干个单一的操作內容, 并填入<<时间记录表>>
搬运到暂存区 暂存等待出货
2020/10/22
16
程序改善
程序分析技巧 1. 通过5W1H系统地分析程序的组成是否合理和必要 2. “ECRS”四大原则:
使用工站时间制作山积表
2020/10/22
14
程序改善
程序分析使用的图表: 工艺程序图 / 流程程序图/ 路线图
程序分析符号 1. --表示操作 2. --表示搬运/运输 3. --表示检验 4. --表示暂存或等待 5. --表示受控的贮存 6. --派生符号,由上面的符号合成.
素的时间总量); 3.平衡损失时间为零; 4.设计效率最大化; 5.前后流程的设计可以更完善(如下图).
2020/10/22
6
相关的概念
(交叉流程)
(直通流程 1 ) (直通流程 2 )
概念8:高效率 1. 通常认为高效率就是:快速,简单&大规模 2. 我们认为沒有浪费的时候才是高效率的 操作效率=实际产量/设定产能*100% 整体工厂效率(OPE)=平衡率*稼动率*操作效率
2020/10/22
15
例: 流程程序圖
材料仓库
2 AI、 SMT加 工 1 前加工
3 手插件 4 锡炉 5 剪脚 6 修 整 (正 背 面 )
7 折分基板 8 ICT测 试
8 穿 焊 OPC(PSC) 9 锡 面 /正 面 检 查 10 中 间 检 查 11 组 装 CASE 12 溶 着 /锁 螺 丝 13 电 测 检 查 14 包 装 15 OQC检 查
概念3:投入工时
20人*3H=60H
投入工时=可供工时-计划停线工时
稼动率=投入工时/可供工时 *100% 计划停线工时=计划停线时间*人数 计划停线时间=无计划时间+换线时间+判停时间
上例中,若换线时间是15分钟,则计划停线工时为20人 *15min=300min=5H,则投入工时和稼动率为:
60H-5H=55H 稼动率=55H/60H=92%
2020/10/22
7
相关的概念
概念9:改善
I. 同样的投入更大的输出; II. 不增值(无效)增值(有效)
?不增值?
等待 不良
库存 移动
……
例1: 减少移动与库存提高效率 例2: 减少无效动作提高效率
2020/10/22
8
概念10:多能工
2020/10/22
9
平衡的手法
工時测量 山积表 程序改善 损失分析 作业条件改善 打破平衡
间
T1
T4
T3
T5
S1 S2 S3
S4
S5
工站
单件标准时间 = T1+T2+T3+T4+T5 (流程中各工站所有动作标准时间之和)
2020/10/22
3
相关的概念
概念2:可供工时 可供工时=可供时间 *人数-借出工时 可供时间:上班时间內,为某产品生产而投入的所有时间
例:A线有20个直接作业人员,某天14:00开始换线生产B产品, 到17:00生产结束,那么,投入到B产品的可供时间为:
数据整理和计算
测试完毕,对数据进行整理和计算,补充 测量有怀疑或错漏的数据; ❖ 计算可信度95%所需的样本数量,补测差 异样本数量.
资料分析与处理
对量测记录之所有资料进行分析,对比 ST的差异程度,解决发现的问题; ❖ 若分析发现标准时间制定不当,应及时 修改,必要时调整制程.
工时测量的作用﹕ 获取各工站的实际操作时间,为山积表制作,时间平衡作准备; 通过时间观测,分析作业价值,发现问题和改善空间; 形成标准,比较实际差异,找出问题;
2020/10/22
5
相关的概念
概念6:平衡损失 平衡损失=(总工时-单件标准时间)*设定产能
时间
T1 T2 T3 T4 T5
等待时间
单个产品平衡损失 =等待时间之和
S1 S2 S3 S4 S5
工站
概念7:平衡率100%代表﹕ 1.工站之间无等待,前后产能一致﹔ 2.工站节拍相同,动作量相同(动作量是指工站中各种必要动
相关的概念
产出的速度取决于时间 最长的工站,称之瓶颈 瓶颈在哪里? 了解加工的过程
2020/10/22
2
相关的概念
概念1: 平衡率
用语衡量流程中各工站节拍符合度的一個综
合比值;
单件标准时间
平衡率= ----------------------100%
瓶颈时间工位数
时
T2
瓶颈时间
测试样本大小計算
山积表
山积表的使用: [图表生成方法]
山积表:将各分解动作时间,以叠加式直方图表现 的一种研究作业时间结构的手法.
样式:
產品xxx工時山積表
秒
10
8 6
0
0 1.5
1.5 0.5
1.5
10 2
1.5 2
10
0.5 1.3
2
10 3
0 4
4
4
6
1
3
1.5 3
2
2
3.5
3.5
2
2
2020/10/22
4
相关的概念
概念4:设定产能 设定产能(H) =3600(S)/瓶颈时间(S) 设定产能(班)=投入時間/瓶颈时间(S)
思考:1)为什么设定产能(班) =投入工时/总工时 总工时=瓶颈时间*作业人数
2)总工时 VS 单件标准时间
概念5:实际产量 实际产量是可供时间內所产出的良品数 1)人均产能=实际产量/投入时间/人数 2)单机台产能=实际产量/投入时间/机台数
时间测试
分解动作时间量测,一般每个动作测量5 次为宜; ❖ 量测人员应站在作业员斜后面1米以外, 以能看清楚全部操作动作为准则; 测试中不能打扰作业员的正常操作和引 起作业员的紧张;
时间测量流程
作业内容
数据与信息记录
测试中判断作业员的速度水平,并作如 实记录,不可修改量测数据; ❖ 若有其他特殊情況,也应加以实录;
0
12 0.5
1.8 1
1.5
10
10
2 2.5 5 2
1
0
0 2
0.5 1
2
10 2
12
2 1.5 6.5 4
2 2.5
1
M5 M4 M3 M2 M1
S1 S2 S3 S4 S5 S6 S7 S8 S9 S10 S11 S12 S13 S14 S15 S16 工站
工時测量(秒表)
工具: 秒表 ❖ 观测板、铅笔 时间记录表、计算器 山积表
方式: 一般测时法 ❖ 连续测时法
2020/10/22
10
时间测量流程
作业內容
选定测试工站
选定工站,阅读SOP和观察作业员操作,了解 該工站的全部操作內容;并询问作业员加以 确认;
拆解动作
将工站动作拆解成若干个单一的操作內容, 并填入<<时间记录表>>
搬运到暂存区 暂存等待出货
2020/10/22
16
程序改善
程序分析技巧 1. 通过5W1H系统地分析程序的组成是否合理和必要 2. “ECRS”四大原则:
使用工站时间制作山积表
2020/10/22
14
程序改善
程序分析使用的图表: 工艺程序图 / 流程程序图/ 路线图
程序分析符号 1. --表示操作 2. --表示搬运/运输 3. --表示检验 4. --表示暂存或等待 5. --表示受控的贮存 6. --派生符号,由上面的符号合成.
素的时间总量); 3.平衡损失时间为零; 4.设计效率最大化; 5.前后流程的设计可以更完善(如下图).
2020/10/22
6
相关的概念
(交叉流程)
(直通流程 1 ) (直通流程 2 )
概念8:高效率 1. 通常认为高效率就是:快速,简单&大规模 2. 我们认为沒有浪费的时候才是高效率的 操作效率=实际产量/设定产能*100% 整体工厂效率(OPE)=平衡率*稼动率*操作效率
2020/10/22
15
例: 流程程序圖
材料仓库
2 AI、 SMT加 工 1 前加工
3 手插件 4 锡炉 5 剪脚 6 修 整 (正 背 面 )
7 折分基板 8 ICT测 试
8 穿 焊 OPC(PSC) 9 锡 面 /正 面 检 查 10 中 间 检 查 11 组 装 CASE 12 溶 着 /锁 螺 丝 13 电 测 检 查 14 包 装 15 OQC检 查
概念3:投入工时
20人*3H=60H
投入工时=可供工时-计划停线工时
稼动率=投入工时/可供工时 *100% 计划停线工时=计划停线时间*人数 计划停线时间=无计划时间+换线时间+判停时间
上例中,若换线时间是15分钟,则计划停线工时为20人 *15min=300min=5H,则投入工时和稼动率为:
60H-5H=55H 稼动率=55H/60H=92%
2020/10/22
7
相关的概念
概念9:改善
I. 同样的投入更大的输出; II. 不增值(无效)增值(有效)
?不增值?
等待 不良
库存 移动
……
例1: 减少移动与库存提高效率 例2: 减少无效动作提高效率
2020/10/22
8
概念10:多能工
2020/10/22
9
平衡的手法
工時测量 山积表 程序改善 损失分析 作业条件改善 打破平衡
间
T1
T4
T3
T5
S1 S2 S3
S4
S5
工站
单件标准时间 = T1+T2+T3+T4+T5 (流程中各工站所有动作标准时间之和)
2020/10/22
3
相关的概念
概念2:可供工时 可供工时=可供时间 *人数-借出工时 可供时间:上班时间內,为某产品生产而投入的所有时间
例:A线有20个直接作业人员,某天14:00开始换线生产B产品, 到17:00生产结束,那么,投入到B产品的可供时间为:
数据整理和计算
测试完毕,对数据进行整理和计算,补充 测量有怀疑或错漏的数据; ❖ 计算可信度95%所需的样本数量,补测差 异样本数量.
资料分析与处理
对量测记录之所有资料进行分析,对比 ST的差异程度,解决发现的问题; ❖ 若分析发现标准时间制定不当,应及时 修改,必要时调整制程.
工时测量的作用﹕ 获取各工站的实际操作时间,为山积表制作,时间平衡作准备; 通过时间观测,分析作业价值,发现问题和改善空间; 形成标准,比较实际差异,找出问题;
2020/10/22
5
相关的概念
概念6:平衡损失 平衡损失=(总工时-单件标准时间)*设定产能
时间
T1 T2 T3 T4 T5
等待时间
单个产品平衡损失 =等待时间之和
S1 S2 S3 S4 S5
工站
概念7:平衡率100%代表﹕ 1.工站之间无等待,前后产能一致﹔ 2.工站节拍相同,动作量相同(动作量是指工站中各种必要动