铝合金电化学着色
电化学沉积铝
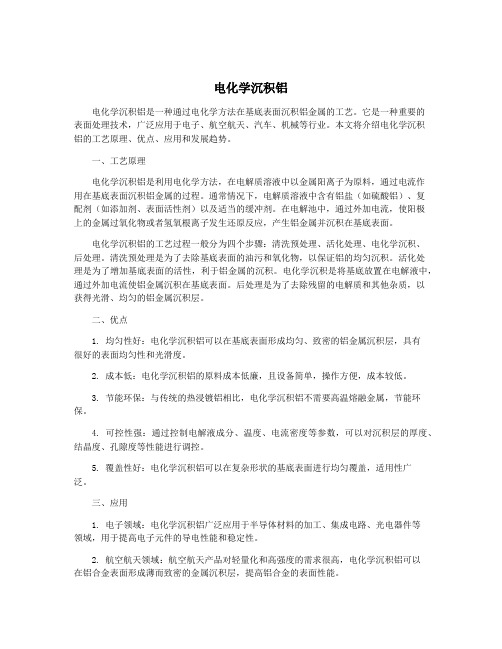
电化学沉积铝电化学沉积铝是一种通过电化学方法在基底表面沉积铝金属的工艺。
它是一种重要的表面处理技术,广泛应用于电子、航空航天、汽车、机械等行业。
本文将介绍电化学沉积铝的工艺原理、优点、应用和发展趋势。
一、工艺原理电化学沉积铝是利用电化学方法,在电解质溶液中以金属阳离子为原料,通过电流作用在基底表面沉积铝金属的过程。
通常情况下,电解质溶液中含有铝盐(如硫酸铝)、复配剂(如添加剂、表面活性剂)以及适当的缓冲剂。
在电解池中,通过外加电流,使阳极上的金属过氧化物或者氢氧根离子发生还原反应,产生铝金属并沉积在基底表面。
电化学沉积铝的工艺过程一般分为四个步骤:清洗预处理、活化处理、电化学沉积、后处理。
清洗预处理是为了去除基底表面的油污和氧化物,以保证铝的均匀沉积。
活化处理是为了增加基底表面的活性,利于铝金属的沉积。
电化学沉积是将基底放置在电解液中,通过外加电流使铝金属沉积在基底表面。
后处理是为了去除残留的电解质和其他杂质,以获得光滑、均匀的铝金属沉积层。
二、优点1. 均匀性好:电化学沉积铝可以在基底表面形成均匀、致密的铝金属沉积层,具有很好的表面均匀性和光滑度。
2. 成本低:电化学沉积铝的原料成本低廉,且设备简单,操作方便,成本较低。
3. 节能环保:与传统的热浸镀铝相比,电化学沉积铝不需要高温熔融金属,节能环保。
4. 可控性强:通过控制电解液成分、温度、电流密度等参数,可以对沉积层的厚度、结晶度、孔隙度等性能进行调控。
5. 覆盖性好:电化学沉积铝可以在复杂形状的基底表面进行均匀覆盖,适用性广泛。
三、应用1. 电子领域:电化学沉积铝广泛应用于半导体材料的加工、集成电路、光电器件等领域,用于提高电子元件的导电性能和稳定性。
2. 航空航天领域:航空航天产品对轻量化和高强度的需求很高,电化学沉积铝可以在铝合金表面形成薄而致密的金属沉积层,提高铝合金的表面性能。
3. 汽车行业:汽车零部件的防腐、耐磨、导电等要求也推动了电化学沉积铝的应用,如发动机、制动系统、传动系统等零部件的表面处理。
铝合金表面电化学处理

铝合金表面电化学处理
铝合金表面电化学处理是指将铝合金表面经过电化学处理而形成一层薄膜,从而改变表面特性,来提升其耐腐蚀性,降低摩擦系数和抗冲击性能的过程。
铝合金表面电化学处理包括氧化处理、亚氧化处理和电泳处理三种方式。
氧化处理:将铝合金表面放入到温度为200-300℃的高温氧化液中,在高温氧化液中,铝合金表面上的氧化物会不断地生成,而氧化物则会随时间的延长而不断地加厚,当氧化物膜厚度达到所需要的尺寸时,便可以停止氧化处理。
氧化处理有利于提高铝合金表面的耐腐蚀性和抗冲击性能,其表面硬度也会增加,但它的摩擦系数会略微增加。
亚氧化处理:亚氧化处理通常分为盐酸亚氧化处理和硫酸亚氧化处理两种方式。
盐酸亚氧化处理,将铝合金表面放入到温度为80-90℃的盐酸溶液中,在盐酸溶液中,铝合金表面上的氧化物会不断地生成,而氧化物则会随时间的延长而不断地加厚,当氧化物膜厚度达到所需要的尺寸时,便可以停止处理。
相对于氧化处理,亚氧化处理可以形成一层更加致密的氧化物膜,因此其抗腐蚀性更好,同
时因为在亚氧化处理过程中,氧化物膜的厚度增加,摩擦系数也会增加。
电泳处理:电泳处理是一种特殊的电化学处理方法,它可以在较低温度下,用电解液中的电解质来形成薄膜,从而改变表面特性。
电泳处理中,在电解质的作用下,铝合金的表面会析出氧化物和氢氧化物,而这些氧化物和氢氧化物便会构成一层可以抵抗腐蚀的薄膜,此外,电泳处理还可以提高铝合金的抗冲击性能。
总之,铝合金表面电化学处理是一种有效的改善表面性能的方法,它可以显著提高铝合金的耐腐蚀性,抗冲击性和抗摩擦性,使其应用于航空航天、汽车制造、电子设备等领域更加广泛。
铝合金表面处理原理讲解

铝合金表面处理原理第一章概述一、铝及铝合金表面处理的目的:(主要指阳极氧化)1、防腐蚀天然氧化膜→薄,阳极氧化膜→厚≥10μm漆膜→耐磨、耐蚀、耐光、耐候2、防护—装饰形成微孔人工氧化膜后,可染成各种颜色和图案。
3、功能作用绝缘性≥100μm微孔渗渍硫化钼润滑剂→摩擦系数↓电沉积磁性金属→磁性录音盘、记忆元件等等。
二、铝及其合金表面处理的分类机械法、化学法、电化学法、阳极化膜后处理(见后面附录)三、铝型材表面处理产品种类目前市场上常见的有:1)阳极氧化(银白、砂白料)2)阳极氧化+ 电解着色(浅古铜、古铜、黑色等)3)电泳涂漆4)静电喷漆、氟碳喷漆5)静电粉末喷涂第二章铝材阳极氧化前的处理铝合金建筑型材生产工艺流程:铝材装架→脱脂→水洗→碱蚀→水洗(二道)→中和(出光)→水洗→阳极氧化(DC法)→水洗→封孔水洗→着色(AC→水洗→卸架第一节装架一、方式:横吊式、竖吊式纵吊式特点:1、适合大批量生产:每批可装载大量铝材2、减少装卸工人:减轻了装卸时的劳动力3、降低生产成本:溶液带出量少,减少化学品消耗量,夹具不浸入处理液中,减少夹具消耗量。
4、减少用水量:带出水量减少,耗水量及废水处理量减少。
适于生产能力在600吨/月以上。
目前,一般采用横吊式为多。
二、注意事项:(横吊式)1)铝材要有一定倾角(3º~ 5º)→便于氧化时气泡逸出。
2)扎料要紧,导电杆脱模要干净→保证导电良好。
3)每根料之间间距应保证→防止色差。
4)避免不同型号、长度的料扎在一起着色→防止色差。
5)每次上料面积要一定,最好是对极面积的80%,最大100%。
第二节脱脂处理一、目的:除去制品表面的工艺润滑油、防锈油及其他污物,以保证在碱洗工序中,制品表面腐蚀均匀和碱洗槽的清洁,从面提高氧化制品质量。
二、油脂种类:动物油、植物油→属皂化油,可与苛性碱发生皂化反应矿物油→属非皂化油,不与苛性碱发生皂化反应锯切液三、脱脂方法与原理1)有机溶剂:酒精、煤油、汽油、丙酮、甲苯、三氯乙烯、四氯化碳等。
铝合金阳极氧化电解着色是铝合金表面处理中重要的方法之一
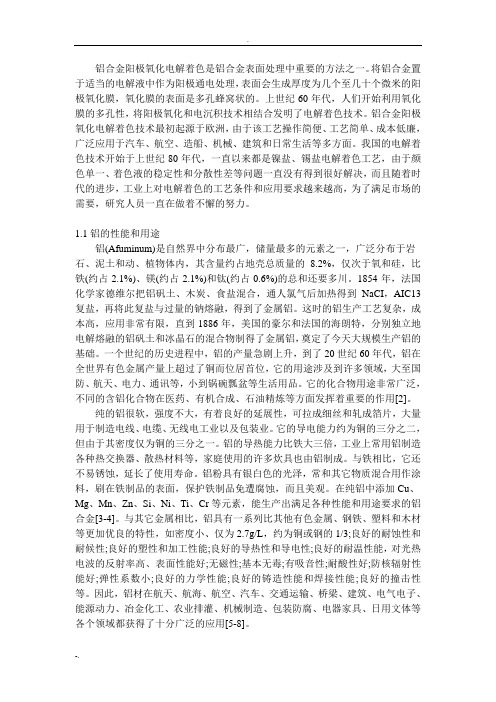
铝合金阳极氧化电解着色是铝合金表面处理中重要的方法之一。
将铝合金置于适当的电解液中作为阳极通电处理,表面会生成厚度为几个至几十个微米的阳极氧化膜,氧化膜的表面是多孔蜂窝状的。
上世纪60年代,人们开始利用氧化膜的多孔性,将阳极氧化和电沉积技术相结合发明了电解着色技术。
铝合金阳极氧化电解着色技术最初起源于欧洲,由于该工艺操作简便、工艺简单、成本低廉,广泛应用于汽车、航空、造船、机械、建筑和日常生活等多方面。
我国的电解着色技术开始于上世纪80年代,一直以来都是镍盐、锡盐电解着色工艺,由于颜色单一、着色液的稳定性和分散性差等问题一直没有得到很好解决,而且随着时代的进步,工业上对电解着色的工艺条件和应用要求越来越高,为了满足市场的需要,研究人员一直在做着不懈的努力。
1.1铝的性能和用途铝(Afuminum)是自然界中分布最广,储量最多的元素之一,广泛分布于岩石、泥土和动、植物体内,其含量约占地壳总质量的8.2%,仅次于氧和硅,比铁(约占2.1%)、镁(约占2.1%)和钛(约占0.6%)的总和还要多川。
1854年,法国化学家德维尔把铝矾土、木炭、食盐混合,通人氯气后加热得到NaCI,AIC13复盐,再将此复盐与过量的钠熔融,得到了金属铝。
这时的铝生产工艺复杂,成本高,应用非常有限,直到1886年,美国的豪尔和法国的海朗特,分别独立地电解熔融的铝矾土和冰晶石的混合物制得了金属铝,奠定了今天大规模生产铝的基础。
一个世纪的历史进程中,铝的产量急剧上升,到了20世纪60年代,铝在全世界有色金属产量上超过了铜而位居首位,它的用途涉及到许多领域,大至国防、航天、电力、通讯等,小到锅碗瓢盆等生活用品。
它的化合物用途非常广泛,不同的含铝化合物在医药、有机合成、石油精炼等方面发挥着重要的作用[2]。
纯的铝很软,强度不大,有着良好的延展性,可拉成细丝和轧成箔片,大量用于制造电线、电缆、无线电工业以及包装业。
它的导电能力约为铜的三分之二,但由于其密度仅为铜的三分之一。
铝合金本色阳极化
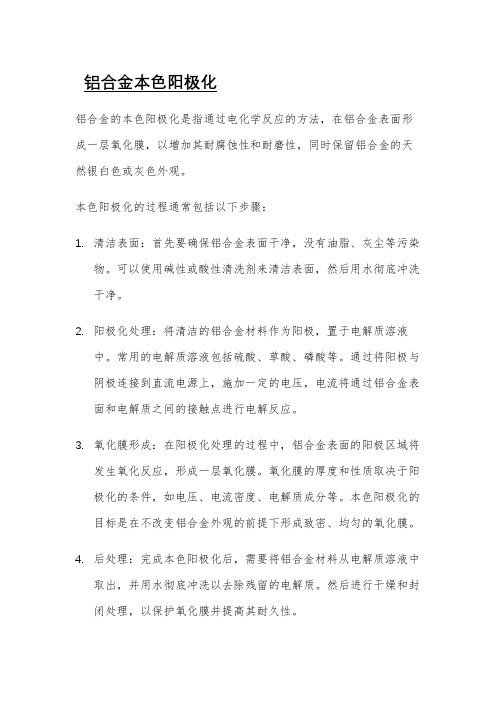
铝合金本色阳极化
铝合金的本色阳极化是指通过电化学反应的方法,在铝合金表面形成一层氧化膜,以增加其耐腐蚀性和耐磨性,同时保留铝合金的天然银白色或灰色外观。
本色阳极化的过程通常包括以下步骤:
1.清洁表面:首先要确保铝合金表面干净,没有油脂、灰尘等污染
物。
可以使用碱性或酸性清洗剂来清洁表面,然后用水彻底冲洗干净。
2.阳极化处理:将清洁的铝合金材料作为阳极,置于电解质溶液
中。
常用的电解质溶液包括硫酸、草酸、磷酸等。
通过将阳极与阴极连接到直流电源上,施加一定的电压,电流将通过铝合金表面和电解质之间的接触点进行电解反应。
3.氧化膜形成:在阳极化处理的过程中,铝合金表面的阳极区域将
发生氧化反应,形成一层氧化膜。
氧化膜的厚度和性质取决于阳极化的条件,如电压、电流密度、电解质成分等。
本色阳极化的目标是在不改变铝合金外观的前提下形成致密、均匀的氧化膜。
4.后处理:完成本色阳极化后,需要将铝合金材料从电解质溶液中
取出,并用水彻底冲洗以去除残留的电解质。
然后进行干燥和封闭处理,以保护氧化膜并提高其耐久性。
需要注意的是,本色阳极化只是对铝合金表面进行保护处理,不能改变铝合金的基本物理和化学性质。
此外,不同类型的铝合金可能需要调整阳极化处理的参数,以获得理想的效果。
因此,在进行本色阳极化之前,建议咨询专业的阳极氧化加工厂或专家,以确保正确的处理方法和参数。
铝合金阳极氧化及着色

1 前言铝及其合金材料由于其高的强度/重量比,易成型加工以及优异的物理、化学性能,成为目前工业中使用量仅次于钢铁的第二大类金属材料。
然而,铝合金材料硬度低、耐磨性差,常发生磨蚀破损,因此,铝合金在使用前往往需经过相应的表面处理以满足其对环境的适应性和安全性,减少磨蚀,延长其使用寿命。
在工业上越来越广泛地采用阳极氧化的方法在铝表面形成厚而致密的氧化膜层,以显著改变铝合金的耐蚀性,提高硬度、耐磨性和装饰性能。
阳极氧化是国现代最基本和最通用的铝合金表面处理的方法。
阳极氧化可分为普通阳极氧化和硬质阳极氧化。
铝及铝合金电解着色所获得的色膜具有良好的耐磨、耐晒、耐热和耐蚀性,广泛应用于现代建筑铝型材的装饰防蚀。
然而,铝阳极氧化膜具有很高孔隙率和吸附能力,容易受污染和腐蚀介质侵蚀,心须进行封孔处理,以提高耐蚀性、抗污染能力和固定色素体。
2 铝及铝合金的阳极氧化2.1 普通阳极氧化铝及其合金经普通阳极氧化可在其表面形成一层Al2O3膜,使用不同的阳极氧化液,得到的Al2O3膜结构不同。
阳极氧化时,铝表面的氧化膜的成长包含两个过程:膜的电化学生成和化学溶解过程。
只有膜的成长速度大于溶解速度时,氧化膜才能成长、加厚。
普通阳极氧化主要有硫酸阳极氧化、铬酸阳极氧化、草酸阳极氧化和磷酸阳极氧化等,以下介绍一些普通阳极氧化新工艺[骐骥导航:机械网址导航]。
2.1.1 宽温快速阳极氧化[1]硫酸阳极氧化电解液的温度要求在23℃以下,当溶液的温度高于25℃时,氧化膜变得疏松、厚度薄、硬度低、耐磨性差,因此在原硫酸溶液中加入氧化添加剂对原工艺进行改进,改进后的溶液配方为:硫酸(ρ=1.84g/cm3)150-200g/L(最佳值160g/L)CK-LY添加剂20-35g/L (最佳值30g/L)铝离子 0.5-20g/L (最佳值5g/L)CK-LY氧化添加剂包括特定的有机酸和导电盐,前者能提高电解液的工作温度,抑制阳极氧化膜的化学溶解,在较高的温度下对抑制氧化膜疏松有良好的作用;后者能增强电解液的导电性,提高电流密度,加快成膜速度。
AA6063铝合金着色 Zr 无铬转化膜及其电化学性能

AA6063铝合金着色 Zr 无铬转化膜及其电化学性能陈廷益;路文;李文芳;付业琦【摘要】The zirconium salt as main raw materials,chrome-free chemical conversion treatment was carried out on AA6063 aluminium alloy at room temperature.Through the analysis of SEM,XRD and electrochemical test,the properties of the chrome-free conversion coating were studied.The results show that zirconium coating grows from needle like small cell structure to large round cell,and then develops to uniform black and grey conversion coating;the thickness of zirconium coating is about 8.79μm,which is mainly composed of KZrF3 (OH)2 ·H2 O and KZrF3 O·2H2 O;the corrosion resist-ance of the zirconium coating is improved by hundreds times than aluminium alloy,and is equivalent to chrome conversion coating;the corrosion resistance of zirconium coating has a certain relationship with post treatment process,the coating structure equivalent circuit is R 1 +C2/R 2 +M3 .%以锆盐为主要原料,实现常温下对 AA6063铝合金的无铬化学转化处理。
金属的氧化,磷化和着色

金属的氧化、磷化和着色7.1 铝合金氧化与着色铝是银白色金属,相对原子质量26.98,密度2.7g/cm3,熔点659.8℃,标准电极电位一1.66V,纯铝的强度低,若加入适量的其他元素,如铜、镁、锌和硅等制成各种铝合金,强度大大提高,并赋予了一系列优良的性能,如较高的机械强度,优良的导热性及导电性,无磁性,密度小,腐蚀产物无毒等,因此在飞机、汽车、电器、仪表、日用品等方面,·获得广泛的应用。
铝是一种两性金属,化学性质活泼,能在空气中形成一层氧化膜,但膜薄、孔隙大、不连续且机械强度较低,不能满足使用要求。
用化学或电化学方法,可在铝及铝合金的表面获得几十到几百微米的氧化膜,大大提高零件的抗腐蚀能力,增强耐磨性,提高绝缘性,美化外观,并可作为涂装的底层使用。
7.1.1铝及铝合金化学氧化7.1.1.1 铝及铝合金化学氧化原理铝及铝合金的化学氧化是在含有氧化剂的弱酸性或弱碱性溶液中进行,在弱碱性溶液中A13+与溶液中的OH-形成可溶性的Al00H,而后转化为难溶的r一Al203·H20附着在铝及铝合金的表面;在含有磷酸、铬酸和氟化物的弱酸性溶液中,Al与H3P04、Cr2072-反应生成Al203及AlP04、CrP04薄膜。
由化学反应生成的膜厚达一定值(0.5~4μm)时,由于膜无松孔,阻碍了溶液与基体金属的接触,使膜生长停止,为了保持一定的孔隙,使膜继续增厚,需向溶液中加入弱酸或弱碱,所以酸和碱是化学氧化成膜的主要成分;再者,为了抑制酸和碱对膜的过度溶解腐蚀,还向溶液中加入氧化剂铬酐或铬酸盐,使膜的生长和溶解保持一定的平衡,以达到较厚的膜层(碱性液中厚度可达到2~39m;酸性溶液中厚度可达到3~4μm)。
7.1.1.2铝及铝合金化学氧化工艺铝及铝合金化学氧化工艺见表7-1。
7.1.1.3铝及铝合金化学氧化后封闭处理化学氧化膜可在30~60g/L的重铬酸钾溶液中封闭处理,温度90~95℃,时间5~10min;或铬酐5g/L,温度40~45℃,时间l0~15s,以提高其耐蚀性。
常用铝合金表面氧化标记
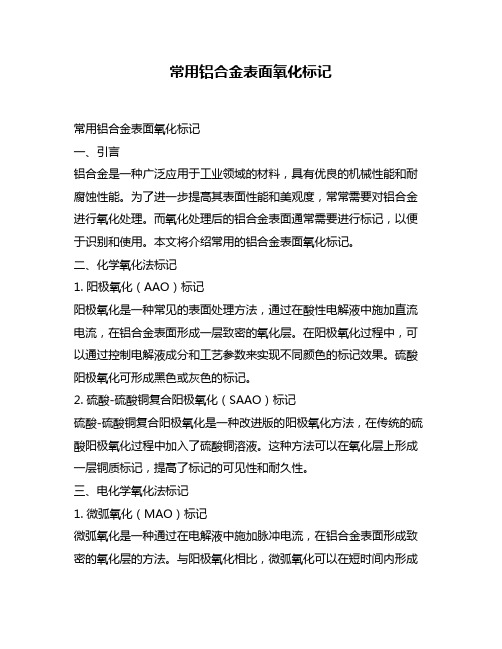
常用铝合金表面氧化标记常用铝合金表面氧化标记一、引言铝合金是一种广泛应用于工业领域的材料,具有优良的机械性能和耐腐蚀性能。
为了进一步提高其表面性能和美观度,常常需要对铝合金进行氧化处理。
而氧化处理后的铝合金表面通常需要进行标记,以便于识别和使用。
本文将介绍常用的铝合金表面氧化标记。
二、化学氧化法标记1. 阳极氧化(AAO)标记阳极氧化是一种常见的表面处理方法,通过在酸性电解液中施加直流电流,在铝合金表面形成一层致密的氧化层。
在阳极氧化过程中,可以通过控制电解液成分和工艺参数来实现不同颜色的标记效果。
硫酸阳极氧化可形成黑色或灰色的标记。
2. 硫酸-硫酸铜复合阳极氧化(SAAO)标记硫酸-硫酸铜复合阳极氧化是一种改进版的阳极氧化方法,在传统的硫酸阳极氧化过程中加入了硫酸铜溶液。
这种方法可以在氧化层上形成一层铜质标记,提高了标记的可见性和耐久性。
三、电化学氧化法标记1. 微弧氧化(MAO)标记微弧氧化是一种通过在电解液中施加脉冲电流,在铝合金表面形成致密的氧化层的方法。
与阳极氧化相比,微弧氧化可以在短时间内形成较厚的氧化层,并且具有更好的耐磨性和耐腐蚀性能。
在微弧氧化过程中,可以通过调节电解液成分和工艺参数来实现不同颜色的标记效果。
2. 水热法标记水热法是一种将铝合金样品浸泡在高温高压水溶液中进行处理的方法。
在水热法过程中,铝合金表面会发生局部的氧化反应,形成不同颜色的标记。
这种方法适用于对大面积铝合金进行标记。
四、物理气相沉积法标记物理气相沉积是一种利用高能离子束轰击铝合金表面,在表面形成一层致密的氧化层的方法。
物理气相沉积法标记的特点是标记图案清晰、耐久性好,适用于对小尺寸铝合金进行标记。
五、激光刻蚀法标记激光刻蚀法是一种利用高能激光束在铝合金表面进行刻蚀的方法。
通过控制激光束的功率和扫描速度,可以在铝合金表面形成不同深度和形状的标记。
这种方法具有高精度、高效率和无污染等优点,适用于对各种尺寸和形状的铝合金进行标记。
铝合金表面处理常见工艺

铝合金表面处理常见工艺铝合金以及铝型材的使用已经非常的广泛,为了满足我们的具体使用需求,在使用这些材质时,需要对其表面进行相应的处理,来提高铝合金材质的表面美观度以及使用性能.下面是有关铝合金表面处理常见工艺。
1、喷砂,主要作用是表面清理,在涂装(喷漆或喷塑)前喷砂可以增加表面粗糙度,对附着力提高有一定贡献,但贡献有限,不如化学涂装前处理。
2、着色:对铝进行上色主要有两种工艺:一种是铝氧化上色工艺,另外一种是铝电泳上色工艺。
在氧化膜上形成各种颜色以满足一定使用要求如光学仪器零件常用着黑色纪念章着上金黄色等。
3、导电氧化(铬酸盐转化膜)——用于既要防护又要导电的场合。
4、化学氧化:氧化膜较薄,厚度约为0.5~4微米且多孔,质软,具有良好的吸附性,可作为有机涂层的底层,但其耐磨性和抗蚀性能均不如阳极氧化膜;铝及铝合金化学氧化的工艺按其溶液性质可分为碱性氧化法和酸性氧化法两大类。
按膜层性质可分为:氧化物膜、磷酸盐膜、铬酸盐膜、铬酸-磷酸盐膜。
5、电化学氧化,铝及铝合金的化学氧化处理设备简单,操作方便,生产效率高,不消耗电能,适用范围广,不受零件大小和形状的限制。
氧化膜厚度约为5~20微米(硬质阳极氧化膜厚度可达60~200微米),有较高硬度,良好的耐热和绝缘性,抗蚀能力高于化学氧化膜,多孔,有很好的吸附能力。
6、喷涂:用于设备的外部防护、装饰通常都在氧化的基础上进行。
铝件在涂装前应进行前处理才能使涂层和工件结合牢固,一般的有三种方法1、磷化(磷酸盐法)2、铬化(无铬铬化)3、化学氧化。
7:阳极氧化:就是利用电解原理在某些金属表面上镀上一薄层其它金属或合金的过程。
刷镀合用于局部镀或修复。
滚镀合用于小件,如紧固件、垫圈、销子等。
通过电镀,可以在机械制品上获得装饰保护性和各种功能性的表面层,还可以修复磨损和加工失误的工件。
电镀液有酸性的、碱性的和加有铬合剂的酸性及中性溶液,不管采用何种镀覆方式,与待镀制品和镀液接触的镀槽、悬挂具等应具有一定程度的通用性。
铝及铝合金的电化学氧化
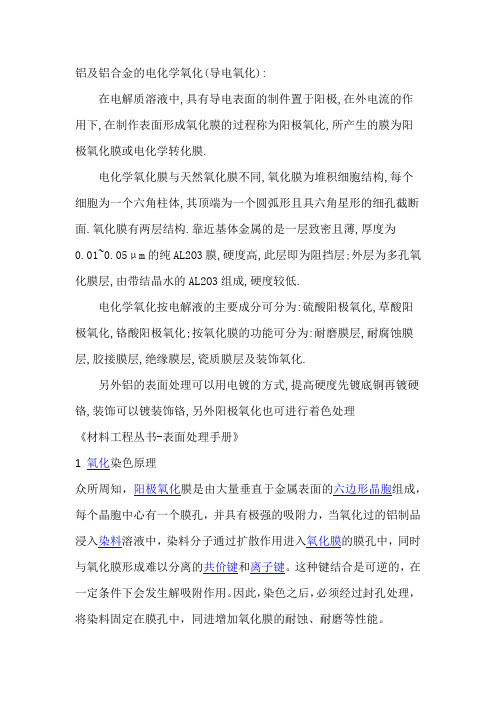
铝及铝合金的电化学氧化(导电氧化):在电解质溶液中,具有导电表面的制件置于阳极,在外电流的作用下,在制作表面形成氧化膜的过程称为阳极氧化,所产生的膜为阳极氧化膜或电化学转化膜.电化学氧化膜与天然氧化膜不同,氧化膜为堆积细胞结构,每个细胞为一个六角柱体,其顶端为一个圆弧形且具六角星形的细孔截断面.氧化膜有两层结构.靠近基体金属的是一层致密且薄,厚度为0.01~0.05μm的纯AL2O3膜,硬度高,此层即为阻挡层;外层为多孔氧化膜层,由带结晶水的AL2O3组成,硬度较低.电化学氧化按电解液的主要成分可分为:硫酸阳极氧化,草酸阳极氧化,铬酸阳极氧化;按氧化膜的功能可分为:耐磨膜层,耐腐蚀膜层,胶接膜层,绝缘膜层,瓷质膜层及装饰氧化.另外铝的表面处理可以用电镀的方式,提高硬度先镀底铜再镀硬铬,装饰可以镀装饰铬,另外阳极氧化也可进行着色处理《材料工程丛书-表面处理手册》1 氧化染色原理众所周知,阳极氧化膜是由大量垂直于金属表面的六边形晶胞组成,每个晶胞中心有一个膜孔,并具有极强的吸附力,当氧化过的铝制品浸入染料溶液中,染料分子通过扩散作用进入氧化膜的膜孔中,同时与氧化膜形成难以分离的共价键和离子键。
这种键结合是可逆的,在一定条件下会发生解吸附作用。
因此,染色之后,必须经过封孔处理,将染料固定在膜孔中,同进增加氧化膜的耐蚀、耐磨等性能。
2 阳极氧化工艺对染色的影响在氧化染色整个流程中,因为氧化工艺原因造成染色不良是比较普遍的。
氧化膜的膜厚和孔隙均匀一致是染色时获得均匀一致颜色的前提和基础,为获得均匀一致的氧化膜,保证足够的循环量,冷却量,保证良好的导电性是举足轻重的,此外就是氧化工艺的稳定性。
硫酸浓度,控制在180—200g/l。
稍高的硫酸浓度可促进氧化膜的溶解反应加快,利于孔隙的扩张,更易于染色;铝离子浓度,控制在5—15 g/l。
铝离子小于5g/l,生成的氧化膜吸附能力降低,影响上色速度,铝离子大于15g/l时,氧化膜的均匀性受到影响,容易出现不规则的膜层。
铝合金消光电泳涂漆工艺原理

1.铝合金消光电泳涂漆工艺原理铝合金的消光电泳涂漆是在阳极氧化膜的表面进行的。
与光亮电泳类似,其生产工艺流程如下:除油→水洗→碱蚀→水洗→水洗→中和→水洗→阳极氧化→水洗→纯水洗→电解着色→纯水洗→热纯水洗→纯水洗→电泳→RO1水洗→R O2水洗→滴干→预干→固化。
消光电泳与透明电泳基本一致,均是以铝型材作为阳极,在直流电的作用下,发生电化学反应,带电荷的涂料粒子受电场的作用,向被涂物移动,使电泳涂料析出沉积在型材表面,形成一层漆膜,整个反应包括电泳、电解、电沉积和电渗四个同时进行的过程。
不同之处主要包括电泳漆原料和生产工艺参数,消光电泳漆较光亮性电泳漆其分子量要大得多,一般在70000—80000g/mol之间;另外,在工艺控制上,其电泳电压、槽液温度及电泳时间皆有区别,通常情况下,对于同一色号料来说,消光电泳电压、时间及温度都要高于透明电泳,此外,与光亮电泳相比多了一道预干工序,减少阴冷潮湿天气滴干时产生的水迹状物,这与电泳漆特性有密切关系。
2.立式氧化消光电泳涂漆质量影响因素与控制方法普通电泳涂漆并不能掩盖型材的表面缺陷,而消光电泳也只能掩盖小部分基材表面缺陷,且因氧化生产流程较长且流水作业连贯性强,尤其是采用氧化立吊式自动化生产,往往是同一类缺陷在一个时间段所生产的产品中存在较多,每一个工艺阶段产生的缺陷到固化处理后会基本暴露,这也导致电泳型材的成品率比普通氧化型材要低,而消光电泳属于高端产品,其表面处理后的细微缺陷则更易显现出来。
生产中常见缺陷的原因及对策如下:(1)水痕对此类缺陷比较一致的说法是进入电泳槽前型材表面水膜不均匀造成的。
特别是冷天出现概率较大,我们采取减少热纯水洗,延长滴干时间,或是避开阴冷潮湿天气集中生产,对于热天生产出现的少量水痕,一是将型材热水洗后充分冷却,再进人电泳前的纯水槽;再是及时更换一定量的纯水,保证纯水槽温与室温一致;三是将型材快速从纯水槽转移至电泳槽,操作人员动作协调是可以避免这类缺陷出现的。
铝及铝合金阳极氧化着色工艺规程
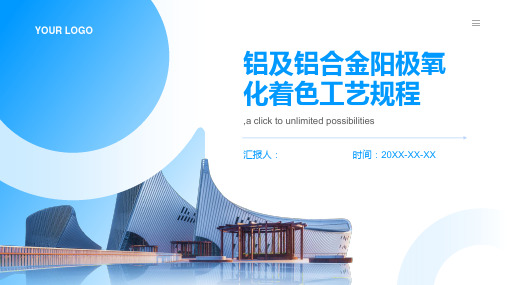
控制措施:调整工艺参数、 优化工艺流程、加强过程 控制等
质量标准:符合相关国家 标准和行业标准
检测频率:根据生产实际 情况确定检测频率
检测记录:记录检测结果, 便于追溯和分析
着色质量检测与控制
检测项目:颜色均匀性、光泽度、耐磨性等 检测方法:目测、色差仪、耐磨试验等 控制措施:调整工艺参数、更换原材料、加强过程管理等 质量标准:符合相关国家标准和行业标准
着色原理及方法
阳极氧化:在铝 及铝合金表面形 成氧化膜,提高 耐磨性和耐腐蚀 性
着色原理:利用 电解液中的金属 离子与氧化膜中 的氧离子发生化 学反应,形成有 色化合物
着色方法:根据 需要选择不同的 电解液和着色温 度,控制着色时 间和着色深度
着色效果:可以 获得各种颜色的 氧化膜,如黑色、 蓝色、红色等
PART 6
封闭处理工艺
封闭处理的作用及原理
封闭处理:在阳 极氧化过程中, 通过封闭处理, 使氧化膜表面形 成一层致密的保 护层,提高氧化 膜的耐腐蚀性和 耐磨性。
原理:封闭处理 是通过化学反应, 在氧化膜表面形 成一层致密的保 护层,阻止外界 环境对氧化膜的 侵蚀,提高氧化 膜的耐腐蚀性和 耐磨性。
工艺流程:水洗→脱脂→ 水洗→中和→水洗→干燥
脱脂剂:常用的有碱性脱 脂剂、酸性脱脂剂、中性 脱脂剂等
脱脂温度:根据工件材质 和脱脂剂种类确定,一般 在40-60℃之间
脱脂时间:根据工件材质 和脱脂剂种类确定,一般 在5-15分钟之间
脱脂效果检验:目测工件 表面无油脂、污垢等,水 洗后无泡沫产生
碱蚀处理
铝及铝合金阳极氧化着色原理
阳极氧化原理
阳极氧化是一种电 化学过程,通过电 解液中的电流作用, 使铝及铝合金表面 形成一层氧化膜。
铝合金的着色原理与应用

铝合金的着色原理与应用1. 引言铝合金是一种广泛应用于工业和民用领域的材料,具有轻质、耐腐蚀和强度高等优点。
然而,铝合金外表常常需要进行着色处理以增强其装饰性和耐久性。
本文将介绍铝合金的着色原理以及其在实际应用中的相关技术和前景。
2. 铝合金的着色原理铝合金的着色原理是通过在铝表面形成一层氧化膜,利用氧化膜的微观结构和光学性质来实现。
常用的着色方法包括电化学着色、阳极氧化着色和化学着色等。
2.1 电化学着色电化学着色是将铝材料置于电解液中,通过电解作用在铝表面生成希望的氧化膜和着色物质。
常见的电化学着色方法有硫酸铜法、硫酸锡法和硫酸钴法等。
每种方法都有不同的色彩范围和耐久性。
2.2 阳极氧化着色阳极氧化着色是将铝材料作为阳极,在电解液中进行氧化处理,形成一层厚度适当的氧化膜,再通过染色将氧化膜着色。
常用的染色材料有有机染料、无机染料和金属染料等。
2.3 化学着色化学着色是利用化学反应在铝表面产生着色物质,常用的方法有酸性氧化着色、碱性氧化着色和沉积着色等。
化学着色可以在较短时间内实现着色,且色彩范围广。
3. 铝合金着色的应用领域铝合金的着色广泛应用于建筑、家居和汽车等领域,下面将重点介绍其在这些领域的应用。
3.1 建筑领域中的应用在建筑领域,铝合金的着色主要用于窗户、门窗框架、幕墙和室内装饰等。
着色后的铝合金能够增加建筑物的美观性,同时提高其抗风、耐腐蚀和耐候性能。
3.2 家居领域中的应用在家居领域,铝合金的着色应用广泛,包括家具、照明、厨房用具和卫浴设备等。
着色后的铝合金产品具有轻质、耐用和易于清洁的特点,能够满足家居产品对于外观和质量的要求。
3.3 汽车领域中的应用在汽车领域,铝合金的着色常用于汽车车身和零部件。
着色后的铝合金能够提高汽车的整体质感和外观效果,同时减轻车身重量,提高燃油效率和减排排放。
4. 铝合金着色的前景随着人们对于环保、美观和品质的要求不断提高,铝合金着色技术将得到进一步的发展和应用。
铝合金表面腐蚀与化学处理及着色技术研究

维 修与 保 养
以及溶胶凝胶法等 ,在此不做列述 。
南方农机
2 0 1 5 . 6
6 3
多化学处理仍难 以完全替代传统 的铬酸盐处理方法,加 之着色技术受到一定 的限制,无铬 技术 的应用 受到很大
制约 ,有必要加大对无铬技术 的研究力度 。
参考文献
2 铝 合 金 表 面 腐 蚀 处 理 及 着 色 技 术 分 析
6 2
南方农机
维修 与 保 养
铝合金表面腐蚀 与化学处理 及着色技术研 究
邓合 辉 , 苏念 盛
( 南南铝业股 份有 限公 司,广 西 南 宁 5 3 0 0 3 1 )
摘 要:金属材料应用较为广泛,其在腐蚀性环境 中容 易发 生腐蚀 ,对其进行 防护尤为必要。本文主要 介绍 了铝合金表 面腐蚀及
的研究与应用 已经成为一种趋势 。
三价铬 ,三价铬本身并不具备较强 的耐腐蚀性 能,需通 过 电化 学反应再次转变为六价铬 , 三价铬实际上上起到
的是一个转换作用 。铬元素来源较广,但是不能够长期
1 金属腐蚀种类及铝合金腐蚀防护技术
1 . 1 腐 蚀种 类
金属腐蚀是一个渐进性过程,可发生在大气 、水及
各种溶液剂等有机环境中,不 同类型的腐蚀 ,其表现特
点存在很大差异 ,对应采用 的防护措施也不 同,如应力 腐蚀会有裂纹生成 ,应避免材料应力集 中:腐蚀疲劳由 腐蚀介质引起 ,应 降低 p H值 ;裂缝腐蚀会形成浓差 电
池,应增加 p H值。此外 ,还有点蚀、氢脆、晶间腐蚀 、
无铬技术包括 阳极氧化技术 、 化学转化 技术 以及其
他一些无铬处理技术 ,其 中,阳极氧化技术是 目前应用 最为全面 的铝合金表面处理技术 , 通过外加适 当的电流 密度,以给定 电解质为阳极 ,形成防腐蚀氧化物,覆盖 在铝合金表面 , 此种氧化物薄膜可使金属表面状态及性 能发生改变 ,提高其耐磨性和耐腐蚀性。通常铝合金被
铝及铝合金阳极氧化性能介绍

为什么有些铝材可以阳极氧化着色有些铝材不可以阳极氧化着色?一、阳极氧化的原理阳极氧化处理是利用电化学的方法,在适当的电解液中,以合金零件为阳极,不锈钢、铬、或导电性电解液本身为阴极,在一定电压电流等条件下,使阳极发生氧化,从而使工件表面获得阳极氧化膜的过程。
按其电解液的种类及膜层性质可分为硫酸(可以着色)、铬酸、(不需着色)、混酸、硬质(不能着色)和瓷质阳极氧化;根据各种阳极氧化膜的染色性能,只有硫酸阳极氧化获得的氧化膜最适宜染色;其他如草酸、瓷质阳极氧化膜(微弧氧化)虽能上色,但干扰色严重;铬酸阳极氧化膜或硬质氧化膜均不能上色;综合所述,要达到阳极氧化上色的目的,仅有硫酸阳极氧化可行。
二、硫酸阳极氧化对铝合金材质的限制1、合金元素的存在会使氧化膜质量下降,同样条件下,在纯铝上获得的氧化膜最厚,硬度最高,抗蚀性最佳,均匀度最好。
铝合金材料,要想获得好的氧化效果,要确保铝的含量,通常情况下,以不低于95%为佳。
2、在合金中,铜会使氧化膜泛红色,破坏电解液质量,增加氧化缺陷;硅会使氧化膜变灰,特别是当含量超过4.5%时,影响更明显;铁因本身特点,在阳极氧化后会以黑色斑点的形式存在。
三、铝合金基础知识工业中使用的铝合金有两大类,即变形铝合金和铸造铝合金。
1、变形铝合金不同牌号的变形铝合金具有不同的成分、热处理工艺和相应的加工形态,因此它们分别具有不同的阳极氧化特性。
按照铝合金系,从强度最低1xxx系纯铝到强度最高7xxx系铝锌镁合金。
1xxx系铝合金又称“纯铝”,一般不用于硬质阳极氧化。
但在光亮阳极氧化和保护性阳极氧化具有很好的特性。
2xxx系铝合金又称“铝铜镁合金”,由于合金中的Al-Cu金属间化合物在阳极氧化时易溶解,因此难以生成致密的阳极氧化膜,在保护性阳极氧化时,其耐腐蚀性更差,因此此系列的铝合金不易阳极氧化。
3xxx系铝合金又称“铝锰合金”,不会使阳极氧化膜的耐腐蚀性下降,但是由于Al-M n金属间化合物质点,会使阳极氧化膜呈现灰色或灰褐色。
铝合金硬质氧化有几种方法

铝合金硬质氧化分为化学氧化和电化学氧化(俗称阳极氧化)两大类。
用于装饰的目的往往需进行着色处理,着色的方法有化学着色和电解着色之分。
铝合金硬质氧化之化学氧化处理所获得的膜层比较薄,一般厚度为0.5μm——4μm,质软不耐磨,抗蚀能力低于阳极氧化膜,一般不宜单独使用。
由于化学氧化膜吸附能力较好,主要作用油漆的底层。
阳极氧化的氧化膜厚度约为5——20微米(硬质阳极氧化膜厚度可达60——200微米),拥有较高硬度,良好的耐热和绝缘性,抗蚀能力高于化学氧化膜,多孔,有很好的吸附能力。
化学氧化处理所需设备简单、操作方便,生产效率高而成本低,适用范围广,不受零件大小和形状的限制,可以氧化大型零件和组合件(如点焊件、铆接件、细长管子等)。
经化学氧化后涂装,可有效地提高零件的耐蚀能力。
铝合金硬质氧化之铝阳极氧化膜综合性能优于化学氧化膜,应用更为广泛,主要用途有:(1)防护性。
提高零件的耐磨、耐蚀、耐气候腐蚀。
(2)装饰性。
制成本色光亮膜,看成彩色膜。
(3)绝缘性。
作为电容器介质膜,铝线卷绝缘膜,每微米厚度可耐25V电压。
(4)提高与有机涂层的结合力,作涂装底层。
(5)提高与无机覆盖层的结合力,作电镀、搪瓷的底层。
(6)开发中的其他功能用途,在多孔膜中沉积磁性合金作记忆元件、太阳能吸收板、超高硬质膜、干润滑膜、触媒膜等。
铝合金上色方法

铝合金上色方法铝合金上色方法多种多样,根据具体情况和需求可以选择不同的方法。
以下提供50种铝合金上色方法,并展开详细描述。
1. 电化学着色法:在阳极氧化的基础上,通过电解着色工艺将铝合金表面染上丰富的色彩,具有良好的耐腐蚀性和耐磨性。
2. 电泳涂装法:通过在电场作用下,在铝合金表面沉积涂料颗粒,形成均匀的涂层,可实现各种颜色的上色效果。
3. 陶瓷涂装法:利用陶瓷颗粒在高温条件下与铝合金表面反应,形成耐磨、耐蚀的陶瓷涂层,同时具有丰富的颜色选择。
4. 喷涂法:将颜色鲜艳的喷涂漆喷涂到铝合金表面,颜色丰富多样,但耐磨性和耐蚀性相对较差。
5. 摩擦氧化法:通过在铝合金表面施加摩擦热,使其在空气中形成氧化膜,可呈现出不同的色彩效果。
6. 染色法:将铝合金表面浸泡在染料溶液中,使其染上所需的颜色,然后通过后续工艺固化染色层。
7. 化学着色法:利用化学反应在铝合金表面形成具有一定厚度和颜色的氧化膜,来实现上色效果。
8. 水膜转印法:根据需求将图案或颜色印刷在水膜上,然后将水膜覆盖在铝合金表面,经过固化形成丰富的图案和色彩。
9. 涂层叠加法:通过在铝合金表面先后涂覆不同颜色或不同性质的涂层,形成叠加的上色效果。
10. 激光印刷法:利用激光技术将需要的图案或文字直接激光印刷在铝合金表面,实现精细的上色效果。
11. 沉积法:通过化学或物理方法,在铝合金表面沉积具有颜色的金属或化合物薄层,来实现上色效果。
12. 油墨印刷法:使用油墨在铝合金表面进行印刷,形成丰富的图案和颜色。
13. 气相沉积法:利用化学气相沉积技术将具有颜色的化合物或涂料沉积在铝合金表面,形成均匀的上色效果。
14. 离子注入法:利用离子注入技术将带有所需颜色的离子注入铝合金表面,改变其表面颜色。
15. 淬火着色法:通过将经过淬火处理的铝合金在热油中加热,形成一定的氧化层,呈现出特殊的颜色。
16. 蚀刻法:利用化学蚀刻技术在铝合金表面产生微小的凹槽,然后在蚀刻后的表面进行上色处理,形成艺术感十足的效果。
- 1、下载文档前请自行甄别文档内容的完整性,平台不提供额外的编辑、内容补充、找答案等附加服务。
- 2、"仅部分预览"的文档,不可在线预览部分如存在完整性等问题,可反馈申请退款(可完整预览的文档不适用该条件!)。
- 3、如文档侵犯您的权益,请联系客服反馈,我们会尽快为您处理(人工客服工作时间:9:00-18:30)。
铝合金电化学着色所谓的金属表面着色是金属通过化学浸渍、电化学法和热处理法等在金属面形成一层带有某种颜色,并且具有一定耐蚀能力的膜层。
生成的化合物通常为具有相当化学稳定性的氧化性、硫化物、氢氧化物和金属盐类。
这些化合物往往具有一定的颜色,同时由于生成化合物厚度不同等原因,对光线有反射、折射、干涉等效应而呈现不同的颜色。
电化学着色法,这种着色法可以分为两种:一种为一步电解着色法,又称自然着色法,是指铝合金在特定的电解条件下阳极氧化的同时进行着色的方法。
根据着色的原因,又可以将其分为合金着色法(自然发色法)和溶液着色法(电解发色法)两类。
合金着色法是利用阳极氧化过程中铝合金的添加成分(如硅、铁、锰等)的氧化而引起氧化膜着色;而溶液着色法是通过电解液组成及电解条件的改变引起氧化膜着色。
另一种为二步电解着色法,又称二次电解着色法,通常简称为电解着色。
该方法是指着色前对铝合金进行一次阳极氧化,再将阳极氧化后的铝合金置于无机盐电解质溶液中进行电解,溶液中的金属离子渗到氧化膜多孔层的底部,形成金属、金属氧化物或金属化合物沉积,由于沉积物对光的散射作用而显现各种颜色。
目前在工业生产中多采用交流电,利用锡盐、镍盐、锰盐等着色盐进行电解着色。
铝合金制品通过电化学氧化在其表面形成铝氧化膜,并进行着色,可以大大改善这些制品的耐磨、抗蚀性及抗变色能力,在航天和船舶制造工业等方面得到了广泛的应用。
又由于其着色的选择性好,而在建筑、高级装饰品、日用品工业等方面得到大量的应用。
电解着色的机制电解着色是通过在多孔型阳极氧化膜的微孔底部沉积非常细小的金属和金属氧化物颗粒,对光的散射效应而获得不同颜色。
国内外大量研究报道指出,不论何种金属盐的电解着色膜,阳极氧化膜中的沉积物既有晶态的金属离子,也有非晶态的金属氧化物或氢氧化物存在;各着色液的着色膜色调不同可能与析出颗粒的尺寸和分布有关;颜色深浅不同,则是与氧化膜的厚度、沉积颗粒的数量有关。
电解着色的阳极氧化膜是以氧化铝为主的掺杂半导体,它像二极管一样,对流过它的交流电具有整流作用。
交流电解着色过程中,交流电的负半周(阴极反应),在阳极氧化膜的微孔中的金属离子减少,在多孔层的孔底还原析出金属,同时电子从金属迁移到阻挡层表面;交流电的正半周(阳极反应),铝继续氧化,并且多孔层中孔底的部分沉积金属也会被氧化,成为金属氧化物。
正是这些沉积金属和金属氧化物颗粒对光的散射而显现各种颜色。
交流电解着色过程实质上是阳极氧化膜交替处于阳极(交流电的正半周)状态和阴极(交流电的负半周)状态的过程。
其中,阳极状态还有重建阳极氧化膜的阻挡层,促进孔中金属氧化物形成,使得阴极析出的氢气迅速得到逸出释放,从而阻止氧化膜脱落等作用。
下面是主要工艺过程表面处理根据制品在机械加工成型后的表面损伤程度以及对制品的不同要求,在氧化前必须进行机械磨光或机械抛光。
化学除油制品表面沾附的油污必须除去,否则将影响F道工序。
常用的是碱性化学除油法。
即通过皂化及乳化作用分别将动、植物油以及矿物油污除去。
化学抛光化学抛光是一项金属表面光饰加工技术。
化学抛光时,铝以离子形式溶解而进入溶液并聚集在制品的表面附近,使制品表面的溶液粘度增大,导致铝的溶解速度下降。
由于粘液的比重较大,易沉积于铝件的凹陷处,所以,制品表面凹陷处近似于钝化状态;而表面凸出部分的粘液层非常薄,故凸起部分易与新鲜溶液接触而被溶解。
另外,制品在溶解时,那些晶格较大、在机械抛光时产生的晶体变形层以及排列不整齐的晶粒等最先被溶解,从而使制件表面的晶格排列更趋于整齐、晶粒将更加紧密和细小。
铝的钝度越高、晶粒越细,化抛的质量也就越高。
近年来应用的无氮氧化物气体(无黄烟)的新型酸性化抛液,其成分为:H3PO4、H2SO4、HNO3、(NH )2SO4、CO(NH2)2、CuSO4、AlPO4。
它们的作用及影响:H3PO4:是化抛液中起切削和溶解作用的最主要成分。
含量要求在70%~80%之间,若过低,将使化抛速度减慢,制品表面不易得到较高的光亮度。
H2SO4:没有它,虽然制品表面仍可得到光泽,但很容易产生点蚀,故它在化抛液中的含量以5%~10%为宜。
HNO3:其含量以3%~8%为宜,过高,会使制品表面出现点蚀,而且当温度较高时极易生成乳白色氧化膜;但低于2%将大大降低制品表面的光亮度。
NH 盐和CO(NH2)2:具有抑制操作过程中放出氮氧化物气体的作用。
加入的比例是:NH+盐:CO(NH2)2=3:2。
Cu2+:在制品表面起辅助阳极作用,对电解液具有活化作用。
含量一般为0.02%。
Al3+:不仅有助于加快铝的溶解,而且也有抑制产生氮氧化物气体的作用。
当含量为7%~10%时,对氮氧化物气体的消除以及化抛质量均有利,并且在取下限时还可延长化抛液的使用寿命。
电化学着色法电化学着色是藉金属微粒对入射光的吸收和散射而产生颜色,在特定介质下,色泽深浅由金属粒子沉积量决定,而与氧化膜厚度无关。
着色时是将铝及铝合金制品先在硫酸溶液中制出洁净、透明多孔的阳极氧化膜,然后移到酸性的金属盐溶液中,施以交流电处理,将金属微粒不可逆地电沉积在氧化膜孔隙的底部,凡能由水溶液中电沉积出来的金属,大部分都可用在电化学着色上,但其中只有几种金属盐具有实用价值,如锡、镍、钴盐和用得较少的铜盐。
氧化膜的封闭及时对铝及铝合金制品作封闭处理,是为了使着色后的氧化膜能够保持色泽以及提高其耐蚀、耐磨、耐晒等方面的性能。
封闭处理的实质,是对多孔状氧化膜的孔隙作封口处理。
在多种封闭方法中,常用的有沸水、蒸汽和盐溶液三种封闭法。
以用沸水和蒸汽进行封闭为最好,其次是重铬酸盐和水解盐类的封闭亦很好。
沸水、蒸汽封闭法在沸水中,氧化膜表面及孔壁的无水A12O3水化,体积膨胀,从而达到封闭孔隙的目的。
当无水A12O3水化为一水化合物时,体积比原来增33%,再进一步水化为三水化合物时,体积将比原来增加100%以上。
利用蒸汽压力可使氧化膜变得更加细密,以提高其耐蚀、耐磨等性能。
盐溶液封闭法重铬酸盐封闭法(俗称填充法)是在重铬酸盐水溶液中,氧化膜吸附了重铬酸盐后发生化学反应,生成碱式铬酸铝[Al(OH)CrO4]和碱式重铬酸铝[A1(OH)Cr207],这些生成物填满皮膜的孔隙,起到封孔作用,经重铬酸盐封闭的制品表面呈橙黄色。
水解盐类封闭法是在某些金属盐溶液中,利用金属盐被氧化膜吸附后,发生水解作用,生成氢氧化物沉淀,填充在孔隙内达到封闭的目的。
常用作封闭的金属盐有钻、镍盐类,其水解反应为:NiSO4+2H2O—Ni(OH)2+H2SO4 (加热、水解)由于这些氢氧化物沉淀几乎是无色透明的,而且还能与有机染料分子形成配合物,此法特别适用于防护装饰性氧化膜经着色后的封闭处理。
电解着色的类型锡盐电解着色我国和欧美国家常用的是锡盐电解着色。
锡盐着色的主要着色盐是硫酸亚锡,利用亚锡离子电解还原在阳极氧化膜的微孔中沉积而着色。
但是亚锡离子在溶液中很不稳定,极易被氧化为锡离子,而失去着色能力。
因此,锡盐着色要注意槽液的控制和添加稳定剂。
生产中通常通过提高槽液酸度,减少槽液与空气的接触,控制槽液温度,加入抗氧化剂、络合剂来改善槽液的稳定性,保持优良的着色性能。
其中,槽液酸度通常是通过加入硫酸来控制。
另外,络合剂应该选择不仅络合亚锡离子,达到稳定槽液的目的,还应络合铝离子等杂质,减轻杂质离子对于电解着色的有害影响。
锡盐电解着色抗杂质性能好,电解着色溶液分布能力强,工业控制较简单。
但是,就浅色系着色而言,锡盐着色的色差和色调比较难控制。
镍盐电解着色镍盐电解着色在日本比较普遍,早在40多年前日本人浅田太平就申请了有关交流镍盐电解着色的专利。
镍盐电解着色常用的着色盐是硫酸镍,由其提供金属镍离子,在电解过程中沉积并显色。
镍盐电解着色速度快,槽液稳定性好,并且可以满足市场上对浅色系(如仿不锈钢色、浅香摈色)的需求,但是对于槽液的杂质比较敏感。
锡、镍混合盐电解着色因为锡盐电解着色和镍盐电解着色时,单独的离子沉积各有局限性,所以在实际生产中会根据不同需要搭配使用引,采用锡.镍混合盐电解着色引,解决单锡盐电解着色或单镍盐电解着色中存在的各种问题,获得高质量的符合要求的着色膜。
其他盐电解着色除了上面所提到的着色盐外,还有锰盐、铁盐、铜盐、银盐和硒盐电解着色,它们都有工业应用,且它们有各自的着色特点。
如锰盐电解着金黄色,色泽稳定,工艺流程简单;铁盐成本低,且在某些时候可以用硫酸铁或硫酸亚铁作为着色主盐,替代镍盐或锡盐;铜盐、银盐和硒盐也分别可以着紫红、黄绿、钛金色等几种颜色。
各种金属盐所着出的颜色各有特点,不同的金属盐着出的颜色可能相同或相近,同一种金属盐也有可能着出几种不同色系的颜色。
单Sn盐和Sn-Ni混合盐电解着色是我国和欧美各国主要的着色方法由于混盐着色稳定性好,色种多,可获得咖啡色和纯黑色,而且含有合金成分其耐蚀性更好,色调黄中透红,所以混和盐着色是主流程序。
由于装饰的需要,提高铝材多色化的要求,于是电解着色新技术、新色种应时而生。
碱蚀成哑光、细砂面的不着色的铝型木才也很行销。
近两年来钛金色为主色调的浅色调,如钛金色、香槟色、仿不锈钢色、金黄色深受人们的欢迎,已进入宾馆、写字楼、住宅和家庭内部装饰。
两槽法着钛金色技术,已投产十几条生产线。
上述型材目前主要有广东地区生产,北方和西北方还是空白。
与生产浅色调相配的抛光技术也急待开发,从保护环境的观点出发应以机械抛光为主,国外80%以上采用机械抛光。
我国尚待开发。
作为应对措施无硝烟的两酸抛光正在开发使用。
纵观我国型材市场,铝型材在今后10后内仍将以电解着色为主导。
青铜色系着色已经降至20%以下,并有继续萎缩之势。
而以钛金色为主的浅色调将在我国流行起来。
浅色型材加电泳涂漆更是锦上添花,是高档型材的标志。
抛光后着浅色铝型材可与电泳相媲美,一定会热销。
另外纯黑型材,与环境对比度强,也很行销。
混盐着色的工艺控制镍锡混和盐除着青铜色系之外,也可着成不锈钢色、香槟色和纯黑色,故是一种用量大面广的实用的技术。
镍盐和亚锡盐的影响锡盐为主,两者共存是由于竞争还原提高了着色速度和均匀性。
亚锡盐用量少且比单锡盐更稳定,色调黄中透红更好看。
镍盐以20-25g/L为宜,浓度太高色偏暗,但是纯黑色时宜升至45-50g/L。
一般亚锡盐6—8#L为宜。
夏季取下限,冬季取上限,着纯黑色需升至10-12g/L。
着色添加剂添加剂起到提高着色速度、均匀性和防止亚锡盐水解等三大作用。
我国自研的添加剂在稳定性、着色均匀性、消耗量和控制水平上可同国际上同类产品媲美。
但目前有些厂家粗制滥造,造成亚锡水解、工艺不稳定。
硫酸它起防止锡盐水解和提高电导的双重作用,游离硫酸控制在15-20g/L为宜。
硫酸偏低光泽性好些,但亚锡稳定性下降;酸度太高着色速度和光泽下降。