表面强化技术在焊接领域中的应用研究进展
金属材料表面强化处理技术的研究与应用

金属材料表面强化处理技术的研究与应用随着科技的不断发展,金属材料的强化处理已经变得越来越重要。
表面强化处理技术在这一领域中发挥了不可或缺的作用。
本文将深入探讨金属材料表面强化处理技术的研究与应用。
一、表面强化处理的定义表面强化处理是指对金属材料表面进行物理、化学、机械等处理,以增强其机械性能、抗腐蚀性能和耐磨性能的过程。
表面强化处理的方法主要有热处理、化学处理、机械加工和物理处理等。
其中,热处理包括淬火、回火、退火等;化学处理包括电镀、热浸镀、阳极氧化等;机械加工包括磨削、喷丸等;物理处理包括激光熔覆、电子束熔覆等。
二、表面强化处理技术的研究进展随着科技的快速发展,表面强化处理技术也在逐步升级。
研究人员针对不同金属材料的特性,不断探索新的表面强化处理方法。
下面将介绍一些新兴的表面强化处理技术。
1. 微弧氧化技术微弧氧化技术能够形成铝、钛、锆、铜等金属材料表面的氧化层,从而增强其抗腐蚀性、耐磨性和摩擦性能。
同时,氧化层上的孔洞结构也能够起到降噪的作用。
该技术广泛应用于铝合金、钛合金、锆合金、铜合金等领域。
2. 离子注入技术离子注入技术是将高能离子注入到金属材料表面,从而改变其结构和性能的技术。
该技术可以通过控制离子注入的能量和剂量,实现金属材料表面的硬化、增强和耐磨等特性的改善。
该技术广泛应用于钢铁、铜合金、镍合金等领域。
3. 微弧等离子喷涂技术微弧等离子喷涂技术是将金属粉末和氧化物粉末等材料喷涂在金属材料表面,从而增强其耐磨性和抗腐蚀性的技术。
该技术具有成本低、生产效率高等优点,且能够定制化生产,应用范围广泛。
三、表面强化处理技术的应用表面强化处理技术的应用已经涉及到多个领域。
下面将介绍一些典型的应用案例。
1. 轴承轴承是现代工业中不可缺少的零部件。
为了提高其使用寿命和性能,轴承表面经常采用表面强化处理技术,如电化学抛光、化学镀铬、离子注入等方法,从而增强其表面硬度、耐磨性和抗腐蚀性能。
2. 汽车发动机汽车发动机在长期使用过程中,其表面会出现磨损、生锈等问题。
金属材料表面强化处理技术的研究

金属材料表面强化处理技术的研究随着科学技术的不断进步,越来越多的材料正在被应用于各个领域。
其中,金属材料是最常见的一类材料,而金属材料表面强化处理技术则是近年来广泛研究的热点之一。
本文将介绍金属材料表面强化处理技术的研究现状和未来发展趋势。
1. 金属材料表面强化处理技术的概述金属材料表面强化处理技术是指通过各种方法对金属表面进行改性,以提高金属材料的性能。
常见的处理方法包括电化学处理、化学处理、机械加工、喷涂等。
这些处理方法通过改变金属表面的物理、化学性质,从而改变金属表面的表面硬度、耐磨性、抗腐蚀性等性能,提高金属材料的使用寿命和性能。
因此,金属材料表面强化处理技术在航空、汽车、机械、核工业等领域中得到了广泛应用。
2. 电化学处理电化学处理是利用电化学法使金属表面发生化学反应,从而改变表面的性质。
常见的电化学处理方法包括电化学沉积、阳极氧化、阳极阳极氧化等。
电化学沉积是通过浸泡金属材料于电解液中,施加电势使金属离子在电极面上得到还原而得到金属沉积物,增强金属表面的耐磨性、耐腐蚀性等性能。
阳极氧化是指将金属材料放置于强酸或强碱中的阳极,并通入恒定电压,使得材料表面发生电化学反应,得到硬质氧化膜,从而制备出高硬度、耐磨性的金属材料表面。
3. 化学处理化学处理是指利用化学物质的反应作用改变金属材料表面性质的一种处理方法。
常用的化学处理方式包括化学沉积、沉淀法、电化学氧化等。
化学沉积是将金属材料置于化学液中,用化学方法沉积出在金属表面形成一层新的物质,使其表面性能发生改变。
沉淀法是通过将金属表面浸渍在某些化学液体中,在介质中形成一层基体物质与沉淀物质的复合层,从而增强材料的硬度、韧性、抗腐蚀性等性能。
电化学氧化是一种在电解质溶液中利用电流将金属材料表面氧化而形成氧化膜的方法,可增强金属材料的耐腐蚀性和机械性能。
4. 机械加工机械加工是指通过磨削、轧制、喷砂等方式对金属材料表面进行加工,改变金属表面原有的形态和结构,从而提高材料表面的性能。
金属材料表面强化技术研究

金属材料表面强化技术研究金属材料是广泛应用于航空、汽车、机械等重要产业中的材料。
面对各种应用场景,如何提升金属材料的性能和耐久度是目前热门的研究领域之一。
面对这个目标,金属材料表面强化技术成为了一个关键的手段。
本文将探讨金属材料表面强化技术的研究。
一、概述表面强化技术对于金属材料来说,是指对金属材料表面进行物理、化学等方面的处理,从而提升金属材料的性能与耐久度。
金属材料表面强化技术的研究主要包括以下几个方面:1. 表面涂层:把其他金属材料或陶瓷材料涂在金属表面,以形成一个保护层,使金属表面与环境隔离。
例如,利用高温熔融法制备陶瓷涂层、利用等离子喷涂制备Metal-Ceramic混合涂层。
2. 表面热处理:利用高温或者冷处理等技术,对金属材料表层进行处理,改变材料的晶粒状态、相结构等,使金属材料的性能得到提升。
例如,采用高能离子轰击等技术来进行表面改性。
3. 表面改性:引入外界的元素或晶粒,从而改变金属材料的性能。
例如,采用电化学沉积、化学气相沉积等表面改性技术。
二、表面涂层类技术1. 陶瓷涂层技术陶瓷涂层技术利用化学反应、高速喷涂等技术在金属表面形成一层坚硬、耐磨、耐腐蚀、耐高温的陶瓷涂层,从而保护金属表面。
陶瓷涂层技术分析表层组成结构,发现C2H2气化产物的中间产物没有被H2转化为多孔储氢剂,而先转化为了有价电子的物种,使得C2H2分子在催化剂表面的氢分子较少而生成了大量的碳纳米管。
2. 金属涂层技术金属涂层技术可以将高硬度金属制成材料热喷涂在钢面上,增强其使用寿命和性能,延长其使用寿命,具有很高的实用价值。
在具体研究上,可以采用低功率高密度强流电子束或者离子束束流照射方法,实现钢板表面进行Cr/Ni/Cr三层涂层的研究。
三、表面改性类技术1. 压电材料表面强化技术压电材料表面强化技术是利用电-压-软化复合作用,在压电电场下使金属材料表面发生塑性变形,并晶化、强化及提高稳定性的技术。
例如,采用单向拉伸和卷曲压力方式对不锈钢制备了压电芯片。
金属材料超声表面强化技术的研究与应用进展

90科学技术Science and technology金属材料超声表面强化技术的研究与应用进展徐 莉(酒钢集团榆中钢铁有限责任公司,甘肃 兰州 730104)摘 要:当前我国经济和科技都在不断进步,工业也随之发展。
工业品的质量会受到工业品材料的影响。
当前在我国金属材料的用量较大,用途也较为广泛,很多相关科学家都在不断研究和探索关于增强金属强度和性能的方法。
本文针对金属材料超声表面强化技术的研究和应用进行进行深入分析和探索,供读者参考。
关键词:金属材料;超声表面强化技术;研究;应用中图分类号:TG668 文献标识码:A 文章编号:11-5004(2020)11-0090-2 收稿日期:2020-06作者简介:徐莉,女,生于1989年,汉族,甘肃武威人,本科,助理工程师,研究方向:金属材料及热处理。
1 超声冲击处理技术众所周知,超声处理技术是我国目前应用较为广泛的技术,大功率的超声是这一技术中最关键的驱动能量。
超声处理技术能够有效进行电能与机械能之间的转化。
磁致伸缩转换能器和压电陶瓷是超声冲击处理技术能够顺利工作的关键因素,机械能会转化为变幅聚能,然后对焊件的表面造成冲击,使材料表面形成塑性形变,从而极大降低焊接操作过程中产生的残余应力,还能够有效提高抗疲劳性[1]。
超声冲击处理技术又称为超声表面强化技术。
超声冲击处理技术是由20世纪70年代前苏联的科学家发明的,1990年法国开始对超声冲击技术进行研究,美国于1995年开始了在桥梁结构上应用超声冲击处理进行研究,我国也是从20世纪90年代开始探索和研究冲击处理技术,冲击处理与焊接接头疲劳强度之间的关系是我国的主要研究领域。
经过我国相关科学家研究发现,工件的接头如果经过超声冲击后,那么其抗疲劳性就会大幅度提高[2]。
而且,这一研究成果目前已经在焊接行业当中广泛应用。
用超声冲击技术对焊接接头进行处理后,不仅能够提高焊接接头的抗疲劳性,还能够在很大程度上降低焊接以后工件上残留的应力。
汽车零部件表面强化技术研究现状及展望

汽车零部件表面强化技术研究现状及展望摘要:近些年来,随着社会经济的进步发展以及人们物质生活水平的不断提高,汽车工业的发展也逐渐呈现出一片繁荣的态势。
随着线及技术手段的不断发展,对于汽车零部件的性能以及延长其使用寿命和提高经济性等方面也提出了更高的要求。
目前来说,汽车零部件的损坏现象一般是由于材料表面不能胜任苛刻的服役条件而出现的,所以对于汽车零部件的要求除了需要具备高的耐磨性、耐蚀性及抗疲劳强度之外还能够保证汽车零部件在高速、高压、载重及强腐蚀介质工况下持续地运行。
所以汽车零部件的表面强化技术逐渐被普及应用,以此有效提高汽车零部件的表面性能。
本文就汽车零部件表面强化技术研究现状以及展望进行了分析。
关键词:汽车零部件;表面强化技术;展望引言在目前的汽车工业中,汽车在实际生产中所用到的汽车零部件一般都是用钢铁合金材料加工制造而成,这种零部件在使用过程中虽然能够保证其基本的使用性能,但是使用寿命较短,因此,需要对汽车零部件的进行强化处理,增强汽车零部件的耐磨性、耐蚀性、抗疲劳等使用性能。
传统的表面强化技术一般是渗碳、渗氮以及表面淬火等,其能有效优化汽车零部件的使用性能,但是在逐渐的发展中也不可避免的出现一些问题,而新型的表面强化技术逐渐面世,对于汽车零部件表面的进一步强化具有重大作用。
一、汽车零部件表面强化技术研究现状(一)表面形变强化表面形变强化主要是通过喷丸、挤压或滚压金属零部件的表面,从而使其产生塑性变形和加工硬化,这种变形和硬化会引起表层显微组织的变化,达到提高金属零部件的疲劳强度、耐磨性和耐腐蚀性等性能的目的,同时表面形变强化的应用也可以对金属零部件的可靠性和耐久性进行提升。
目前在汽车工业的实际生产中,喷丸强化工艺引起本身具有的操作简单、耗能少、效率高及适应面广等优点而受到广泛的普及应用,并显著提高汽车零部件抗弯曲、抗腐蚀、抗应力腐蚀、抗微动磨损和耐点蚀性能等等,极大地促进了汽车行业整体的生产质量。
金属材料表面强化技术应用现状与展望

世界有色金属 2020年 8月上130前沿技术L eading-edge technology金属材料表面强化技术应用现状与展望江佩泽(福建省锅炉压力容器检验研究院,福建 福州 350000)摘 要:不论生产何种产品,其首要任务就是选取合格的材料,而不合格的材料通常表现为有腐蚀、破损或断裂。
而这些问题一般发生在材料的表面,想要提升金属的硬度、强度、耐磨性以及耐腐蚀性等,针对金属材料的表层实施强化和改性是必不可少的。
关键词:金属材料;表面强化;应用现状;展望中图分类号:TG174.4 文献标识码:A 文章编号:1002-5065(2020)15-0130-2Application status and prospect of metal material surface strengthening technologyJIANG Pei-ze(Fujian boiler and pressure vessel inspection and Research Institute,Fuzhou 350000,China)Abstract: No matter what kind of products are produced, the first task is to select qualified materials, and unqualified materials usually show corrosion, breakage or fracture. However, these problems generally occur on the surface of materials. In order to improve the hardness, strength, wear resistance and corrosion resistance of metals, it is necessary to strengthen and modify the surface of metal materials.Keywords: metal materials; Surface strengthening; Application status; Outlook收稿日期:2020-07作者简介:江佩泽,男,生于1992年,汉族,福建南平人,本科,助理工程师,研究方向:金属材料。
金属材料表面强化处理的研究与应用

金属材料表面强化处理的研究与应用金属材料在工业生产中具有广泛的应用,但是其表面硬度、耐磨性、抗氧化性等性能常常不够满足特定的工程要求。
因此,针对金属材料表面的强化处理成为了研究热点。
本文将从表面强化处理方法、表面强化处理效果以及应用领域三方面探讨金属材料表面强化处理的研究与应用。
一、表面强化处理方法表面强化处理方法包括机械加工、物理方法和化学方法三类。
1. 机械加工机械加工是一种常用的表面强化方法,包括打磨、抛光、切削、车削等操作。
这些机械热加工可以使金属表面粗糙度减小,界面结晶数增加,晶粒细化,从而提高材料的强度、硬度和抗疲劳性能。
但是机械加工过程具有较高的成本,而且由于金属材料表面形变的产生,界面性质发生变化,从而可能影响金属材料的机械性能。
2. 物理方法物理方法包括电弧冶金、电子束加工、激光加工、等离子弧喷涂等方法,这些方法可以通过加热和冷却的方式改变金属材料表面组织结构和化学成分,进而提高材料的强度、硬度、耐磨性和抗氧化性能。
但是物理方法对设备条件和环境条件有较高的要求,也存在一定的安全隐患。
3. 化学方法化学方法包括化学沉积、化学蚀刻、离子注入等方法,这些方法对金属材料表面的化学成分进行调控,包括合金元素的添加、表面沉积膜的形成等,从而提高了金属材料的强度、硬度和耐磨性能。
但是化学方法的操作需要一定的专业技能,而且对环境有一定的污染。
二、表面强化处理效果金属材料表面的强化处理可以显著提高材料的强度、硬度、耐磨性和抗氧化性能。
例如,自行车刹车铝合金经过表面处理后,其耐磨性能提高了6倍以上。
再比如,汽车发动机气缸极经过表面强化处理后,其磨损量可减少85%以上,寿命可提高5倍以上。
三、应用领域金属材料表面强化处理的应用领域非常广泛,例如航空航天、电子信息、汽车制造、工程机械等行业。
在航空航天行业中,飞机的各种结构件、发动机叶片等都需要表面强化处理,以保证飞机的安全和性能。
在汽车制造业中,汽车发动机零部件、刹车系统、转向系统等也需要表面强化处理,以保证汽车的行驶安全性和寿命。
金属材料表面强化处理技术研究

金属材料表面强化处理技术研究随着科技的不断进步,人们对材料的性能要求越来越高,因此金属材料表面强化技术应运而生。
其目的是通过加强材料表面硬度以及结晶度,提高金属材料的耐腐蚀性、抗疲劳性、耐磨性以及耐氧化性等性能指标。
在实际生产中,金属材料表面强化技术广泛应用于航空航天、汽车制造、工程机械以及船舶等领域。
本文将深入探讨金属材料表面强化技术的研究现状以及未来趋势。
一、表面强化处理技术的研究现状1.1 涂层技术涂层技术是一种将高硬度的涂层涂覆在金属材料表面的技术。
这种技术的目的是提高金属材料的耐磨性、耐氧化性以及抗腐蚀性等性能指标。
当前应用比较广泛的涂层技术为物理气相沉积(PVD)和化学气相沉积(CVD)。
PVD涂层技术涂层质量相对稳定,其厚度均匀性好,且氧化膜较少。
CVD技术具有涂层厚度大、涂层成分均匀和表面质量好等优点。
1.2 表面机械处理技术表面机械处理技术通过对金属材料表面进行拉伸、压缩、剪切、滚压等机械作用,来改善金属材料表面的力学性能。
常规的表面机械处理技术主要包括喷丸、冷弯、压花和滚制等。
喷丸技术以其高效、简便和成本低等优点得到广泛的应用。
冷弯、压花和滚制技术的应用范围比较窄,但在某些领域中应用也非常广泛。
1.3 表面化学处理技术表面化学处理技术通常是通过溶液对金属材料表面进行处理,这种处理方式能够增加金属材料表面的粗糙度,并形成一定的氧化膜层。
该膜层不仅能提高钢铁材料的耐蚀性,还能改善钢铁材料的表面质量、电气性能和降低表面的摩擦系数。
当前应用比较广泛的表面化学处理技术为酸洗、碱洗,以及电化学抛光等。
二、表面强化处理技术的未来趋势随着科技的不断发展,金属材料表面强化处理技术也在不断的演变和更新。
未来的表面强化处理技术将集结多种工艺手段,如物理结构调控、多元复合技术、等离子弧等,以期实现表面强化的可持续性和再生性,并提高其处理技术的抗腐蚀性、耐磨性和机械性能能力。
2.1 多元复合技术目前,多元复合磨料研磨技术是针对高硬度材料表面加工最为有效的处理手段之一。
金属材料表面强化技术新进展
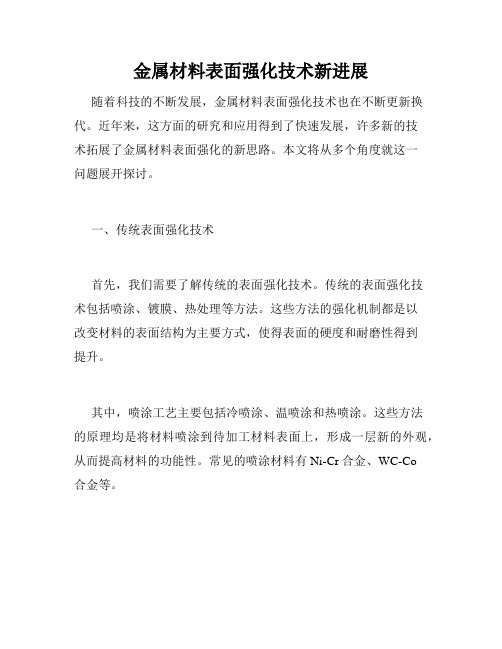
金属材料表面强化技术新进展随着科技的不断发展,金属材料表面强化技术也在不断更新换代。
近年来,这方面的研究和应用得到了快速发展,许多新的技术拓展了金属材料表面强化的新思路。
本文将从多个角度就这一问题展开探讨。
一、传统表面强化技术首先,我们需要了解传统的表面强化技术。
传统的表面强化技术包括喷涂、镀膜、热处理等方法。
这些方法的强化机制都是以改变材料的表面结构为主要方式,使得表面的硬度和耐磨性得到提升。
其中,喷涂工艺主要包括冷喷涂、温喷涂和热喷涂。
这些方法的原理均是将材料喷涂到待加工材料表面上,形成一层新的外观,从而提高材料的功能性。
常见的喷涂材料有Ni-Cr合金、WC-Co合金等。
另外,镀膜技术是通过电化学或物理化学原理将材料在金属表面上形成一层薄膜来达到表面强化的目的。
在这个过程中,要选择同材料或类似材料进行镀膜,以达到良好的复合度。
热处理技术是指在特定的温度、时间和气氛下,将材料进行加热处理,使其表面经过凝固、固定和晶变等作用,以实现表面强化。
尽管这些传统的表面强化技术在一定程度上起到了效果,但是它们存在一些不足。
比如喷涂技术需要高温和高压,会导致质量的不稳定;镀膜技术成本高,有环境污染的风险;而热处理技术只能对表面层进行强化,强化深度和层数都有限制。
二、新兴表面强化技术得益于科技技术的不断进步,在表面强化技术方面也取得了新的突破。
下面我们将介绍一些新兴的表面强化技术。
1、等离子体喷涂技术等离子体喷涂技术是一种新型的表面处理技术,它能够将基材表面与涂层有机的结合,生成均匀致密的涂层。
与传统的喷涂技术相比,它的工艺简单、成本低,而且涂层的耐磨性和粘着性也很强。
在航空、汽车、机械等领域有广泛的应用。
2、激光处理技术激光处理技术是通过激光对金属表面进行处理,使其发生物理和化学变化,从而达到表面强化的目的。
激光处理技术既可以提高表面硬度,又能够控制强化层的厚度和深度。
它不仅能够增加金属材料的表面硬度,还可以改善其表面光泽和表面质量。
金属材料超声表面强化技术的研究与应用进展
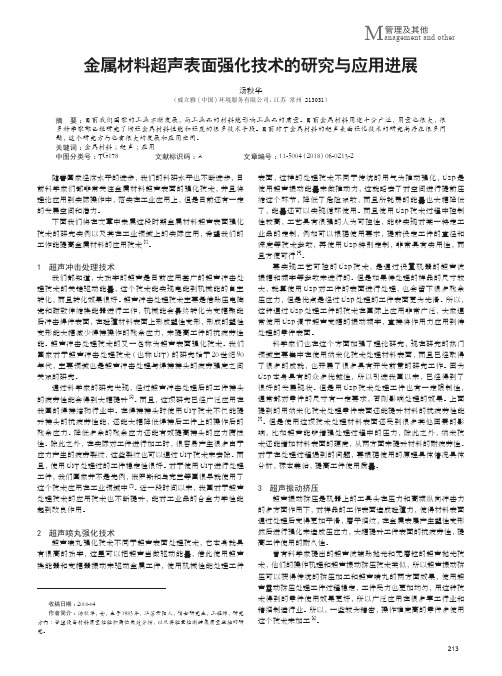
管理及其他M anagement and other 金属材料超声表面强化技术的研究与应用进展汤秋华(威立雅(中国)环境服务有限公司,江苏 常州 213031)摘 要:目前我们国家的工业不断发展,而工业品的材料能影响工业品的质量。
目前金属材料用途十分广泛,用量也很大,很多科学家都已经研究了增强金属材料性能和强度的很多技术手段。
目前对于金属材料的超声表面强化技术的研究尚存在很多问题,这个研究方向也有很大的发展和应用空间。
关键词:金属材料;超声;应用中图分类号:TG178 文献标识码:A 文章编号:11-5004(2018)06-0213-2随着国家经济水平的进步,我们的科研水平也不断进步,目前科学家们都非常关注金属材料超声表面的强化技术,并且将理论应用到实际操作中,落实在工业应用上,但是目前还有一定的发展空间和潜力。
下面我们将在文章中隶属这段时期金属材料超声表面强化技术的研究实例以及其在工业领域上的实际应用,希望我们的工作能提高金属材料的应用技术[1]。
1 超声冲击处理技术我们都知道,大功率的超声是目前应用甚广的超声冲击处理技术的关键驱动能量,这个技术能实现电能到机械能的自主转化,而且转化效果很好。
超声冲击处理技术主要是借助压电陶瓷和磁致伸缩换能器进行工作,机械能会最终转化为变幅聚能后冲击焊件表面,在碰撞材料表面上形成塑性变形,形成的塑性变形能大幅减少焊接操作的残余应力,来提高工件的抗疲劳性能。
超声冲击处理技术的又一名称为超声表面强化技术。
我们国家对于超声冲击处理技术(也称UIT)的研究始于20世纪90年代,主要领域也是超声冲击处理与焊接接头的疲劳强度之间关系的研究。
通过科学家的研究发现,经过超声冲击处理后的工件接头的疲劳性能会得到大幅提升[2]。
而且,这项研究已经广泛应用在我国的焊接结构行业中。
在焊接接头时使用UIT技术不仅能提升接头的抗疲劳性能,还能大幅降低焊接后工件上的操作后的残余应力。
降低多余的残余应力还能有效提高接头的应力腐蚀性。
关于金属材料超声表面强化技术的研究与应用进展

关于金属材料超声表面强化技术的研究与应用进展发布时间:2023-03-01T06:06:13.735Z 来源:《科技新时代》2022年第19期作者:张道[导读] 现今,我国工业发展速度越来越快,对于工业品生产加工质量也会提出较高的要求,要想满足这种高要求,张道维沃移动通信有限公司深圳分公司广东深圳 518000摘要:现今,我国工业发展速度越来越快,对于工业品生产加工质量也会提出较高的要求,要想满足这种高要求,关键任务就是要对金属材料的超声表面强化技术加大研究和创新力度。
本文也会针对当前工业制造中,几种常见的金属材料超声表面强化技术的应用原理进行着重分析,并对其应用进展提出相应的意见和建议,以便为有关人士提供参考。
关键词:金属材料;超声表面强化技术;应用原理;进展分析引言在工业生产中,各类机械设备是不可缺少的重要组成部分,但是设备在长期运行使用后,其零部件就会出现不同程度的磨损、腐蚀以及疲劳等问题,这样就会大大降低机械设备的使用寿命和运行安全,进而在运行期间产生较大的能耗问题,因此,在设备生产制造过程中,积极引入金属材料超声表面强化技术来强化零部件的性能和质量,这样才能使其耐磨性、耐腐蚀性以及疲劳强度等更好地满足机械设备长期运转需求。
1.超声冲击处理技术的应用该金属材料超声表面强化技术主要将大功率超声作为核心驱动能量,在实际运用时,通过压电陶瓷和磁致伸缩换能设备的大力配合,可以很好的实现电能向机械能的有效转化,同时还能借助变幅聚能的力量,对金属材料的焊接表面进行冲击碰撞,以便使材料的表面形成局部塑性变形,这样既可以有效降低工件焊接表面的残余应力,同时也能减小焊接变形问题的发生概率,进而使工件的抗疲劳性能得到最大化提升。
超声冲击处理技术在我国20世纪90年代开始应运而生,主要研究范围围绕超声冲击处理对工件焊接接头的疲劳强度所造成的影响及作用来进行,据相关研究结果可以得知,超声冲击处理技术可以有效改变工件焊接接头的疲劳性能以及抗应力腐蚀性能等,从而使其得到最大化提升,同时还能有效降低焊接面的残余应力,并产生更多有益的残余压应力。
对于表面形变强化技术的现状分析(一)
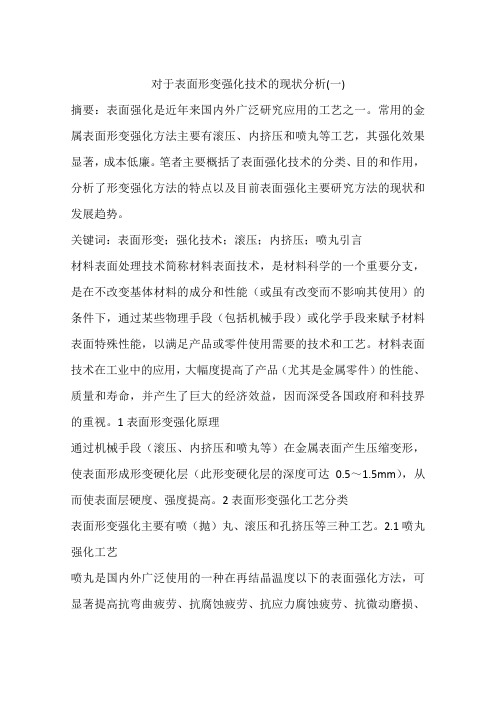
对于表面形变强化技术的现状分析(一)摘要:表面强化是近年来国内外广泛研究应用的工艺之一。
常用的金属表面形变强化方法主要有滚压、内挤压和喷丸等工艺,其强化效果显著,成本低廉。
笔者主要概括了表面强化技术的分类、目的和作用,分析了形变强化方法的特点以及目前表面强化主要研究方法的现状和发展趋势。
关键词:表面形变;强化技术;滚压;内挤压;喷丸引言材料表面处理技术简称材料表面技术,是材料科学的一个重要分支,是在不改变基体材料的成分和性能(或虽有改变而不影响其使用)的条件下,通过某些物理手段(包括机械手段)或化学手段来赋予材料表面特殊性能,以满足产品或零件使用需要的技术和工艺。
材料表面技术在工业中的应用,大幅度提高了产品(尤其是金属零件)的性能、质量和寿命,并产生了巨大的经济效益,因而深受各国政府和科技界的重视。
1表面形变强化原理通过机械手段(滚压、内挤压和喷丸等)在金属表面产生压缩变形,使表面形成形变硬化层(此形变硬化层的深度可达0.5~1.5mm),从而使表面层硬度、强度提高。
2表面形变强化工艺分类表面形变强化主要有喷(抛)丸、滚压和孔挤压等三种工艺。
2.1喷丸强化工艺喷丸是国内外广泛使用的一种在再结晶温度以下的表面强化方法,可显著提高抗弯曲疲劳、抗腐蚀疲劳、抗应力腐蚀疲劳、抗微动磨损、耐蚀点(孔蚀)能力,它具有操作简单、耗能少、效率高、适应面广等优点,是金属材料表面改性的有效方法。
2.1.1喷丸强化的发展状况1908年,美国制造出激冷钢丸,金属弹丸的出现不仅使喷砂工艺获得迅速发展,而且导致了金属表面喷丸强化技术的产生。
1929年,在美国由Zimmerli等人首先将喷丸强化技术应用于弹簧的表面强化,取得了良好的效果1]。
20世纪40年代,人们就发现了喷丸处理可在金属材料表面上产生一种压缩应力层,可以起到强化金属材料、阻止裂纹在受压区扩展的作用。
到了20世纪60年代,该工艺逐步应用于机械零件的强化处理上。
20世纪70年代以来,该工艺已广泛应用于汽车工业,并获得了较大的经济技术效益,如机车用变速器齿轮、发动机及其他齿轮均采用了喷丸强化工艺,大幅度提高了抗疲劳强度。
材料表面强化技术

材料表面强化技术材料表面强化技术是一种通过改变材料表面结构和性质来提高材料性能的技术。
它可以使材料具有更好的耐磨、抗腐蚀、抗疲劳、抗氧化等特性,从而提高材料的使用寿命和性能稳定性。
本文将从材料表面强化技术的原理、应用领域和发展趋势等方面进行探讨。
一、原理材料表面强化技术主要通过改变材料表面的物理、化学和结构特性来提高材料性能。
常见的表面强化技术包括表面沉积、渗碳、涂层、激光熔覆等。
这些技术可以使材料表面形成一层具有特定性能的薄膜,从而提高材料的耐磨、抗腐蚀、导热等性能。
二、应用领域材料表面强化技术在许多领域都有广泛的应用。
在汽车制造领域,表面强化技术可以提高汽车零部件的耐磨性和抗腐蚀性,从而提高汽车的使用寿命和安全性能。
在航空航天领域,表面强化技术可以提高飞机发动机叶片的耐磨性和耐高温性,从而提高发动机的性能和可靠性。
在电子器件制造领域,表面强化技术可以提高电子器件的导电性和耐热性,从而提高电子器件的性能和稳定性。
三、发展趋势随着科学技术的不断进步,材料表面强化技术也在不断发展。
目前,人们对材料表面强化技术的研究主要集中在以下几个方面:1.多功能涂层技术:多功能涂层技术可以在材料表面形成一层具有多种功能的薄膜,例如耐磨、抗腐蚀、导热等。
这种技术可以使材料具有更好的性能和稳定性,从而扩大材料的应用范围。
2.纳米材料表面强化技术:纳米材料具有较大的比表面积和特殊的物理化学性质,可以在材料表面形成一层具有特殊功能的纳米薄膜。
这种技术可以使材料具有更好的导热性、光学性能等,从而提高材料的性能和应用效果。
3.激光表面强化技术:激光表面强化技术可以通过激光束的作用,改变材料表面的结构和性质。
这种技术可以使材料表面形成一层具有特殊功能的薄膜,例如增强材料的硬度、耐磨性等。
4.生物材料表面强化技术:生物材料表面强化技术可以通过改变材料表面的结构和性质,使材料具有良好的生物相容性和生物活性。
这种技术可以使材料在医学领域有更广泛的应用,例如人工骨骼、人工关节等。
金属材料表面强化技术研究及应用

金属材料表面强化技术研究及应用随着科技的不断提升,金属材料表面强化技术也不断得到完善和发展,这种技术可以通过改变金属表面的力学、物理和化学性质,从而提高金属材料的力学性能、耐磨性能、抗腐蚀性能和疲劳寿命等,受到了广泛的关注和应用。
一、金属材料表面强化技术的种类1.化学处理技术金属材料表面化学处理技术是目前应用广泛、经济实用的表面处理技术,它通过在金属表面形成一层化学化合物,使表面的物理特性和化学性质发生变化,从而增加其功能和性能。
2.物理处理技术物理处理技术包括喷砂、喷丸、磨研等,这种方法可以通过表面的机械切削或强制作用去除表面缺陷和杂质,从而优化材料表面的结构,提高材料的表面质量和性能。
3.表面涂层技术表面涂层技术是一种将不同的物质材料涂在金属表面的方法,通过增加表面层的物理、化学性质,来改善金属材料的综合性能和寿命。
4.热处理技术热处理技术是通过加热、淬火、回火等方法,使金属材料的结构和性质发生改变,从而改善其强度、硬度和韧性,提高耐磨性能和疲劳寿命。
二、金属材料表面强化技术的应用领域1.机械制造行业金属材料表面强化技术在机械制造行业中有广泛的应用,可以用于改善机械零件的表面硬度、耐磨性和抗腐蚀性能,从而提高设备的使用寿命和稳定性。
2.航空、船舶等领域在航空、船舶等领域,金属材料表面强化技术可以用于改善飞行器、舰船等设备的表面性能,提升其安全可靠性和性能稳定性。
3.汽车制造行业金属材料表面强化技术在汽车制造行业中也有着广泛的应用,可以用于改善汽车零部件的性能和寿命,提高汽车产品的竞争力和市场占有率。
4.新能源产业在新能源领域,金属材料表面强化技术可以用于提高太阳能电池板、风力发电机组等设备的表面性能和寿命,从而增加其发电效率和稳定性。
三、金属材料表面强化技术的未来发展方向1.绿色环保随着全球环境污染的日益严重,金属材料表面强化技术在未来的发展过程中将越来越重视绿色环保,提高处理工艺的绿色化程度和效率,减少对环境的影响。
探讨表面强化技术在机械零件中的运用

探讨表面强化技术在机械零件中的运用机械零件出现失效的问题大多是从表面开始,因此,表面强化技术在机械零件中运用具有十分重要作用,可以提升零件的性能,比如,耐腐蚀性、耐高温性以及抗疲劳性等。
不但提升材料性能、挖掘材料的潜力,而且可以有效提升零件的寿命。
标签:表面;强化技术;机械零件机械零件在运转过程中出现失效的原因在于零件的材料已经不能适应机械工作的环境,本人总结主要由三方面导致:由于腐蚀导致失效、由于工作强度过大而失效以及由于磨损而失效。
失效总是先从机械零件表面开始,之后在影响到零件的内部结构,进而对机械的使用造成严重的影响。
需要注重机械的零件使用情况,尤其是零件表面的材料,延长零件的使用寿命,提高机械零件性能。
1 表面强化技术的涵义以及意义表面工程主要是指通过一些化学和物理的工艺让机械零件表面的材料以及性能得到改善,提高零件的抗压强度和耐磨性,其工艺内容主要包含了表面改性、表面加工、表面处理、表面涂层等。
表面工程是影响零件成分、性能以及组织结构的关键性技术。
表面强化技术能够通过不同的工艺手段来增强零件材料的硬度、强度、性能、组织结构等,使零件更加耐腐蚀、耐磨,增强零件的使用寿命。
在零件中使用表面强化技术能够达到节约材料、挖掘材料潜力的目的,可以制造出不同的表面强化层,进而使经济效益得以提升。
上个世纪60~70年代时期,在工业领域逐渐引进了激光束、离子束、电子束等技术,致使工业生产开始进行表面处理,同时国家对这方面展开研究,并在表面处理技术上取得一些进展。
90 年代,表面工程技术逐渐系统化,出现表面工程学。
这些都推动了表面工程技术的发展,也推动了其他相关技术的发展和进步。
2 对材料进行表面强化技术的意义(1)可以挖掘材料潜力。
在实际的生产工艺中,传统的表面强化技术,比如淬火技术、热处理技术等,它可以让零件的材料抗强度性更高、耐磨性更高,同时也可以承受更大的冲击力,韧性非常好,进而使零件的寿命得到大幅度提高。
电火花表面强化技术及其应用

电火花表面强化技术及其应用摘要: 电火花表面强化技术是一种具有独特优势的材料表面技术,其在机械零件表面改性和表面修复等方面具有广阔的应用前景。
介绍了电火花表面强化技术的基本原理和工艺特点,阐述了电火花表面强化技术的发展概况,分析了该技术在机械零部件修复、模具强化等方面的实际工程应用,指出了该技术今后的研究方向和发展趋势。
关键词: 电火花表面强化表面改性修复(一)电火花表面强化技术的基本原理与特点电火花表面强化技术的基本原理是储能电源通过电极以10 ~2000Hz 的频率在电极与零部件之间产生火花放电,在10-6~10-5( s) 内电极与零部件接触的部位即达到5000 ~10000℃的高温,使该区域的局部材料熔化、气化或等离子体化,将电极材料高速过渡并扩散到工作表面,形成冶金结合型牢固强化层。
研究表明,强化层主要由白亮层、扩散区和热影响区构成,涂层组织较细密,具有较高硬度及较好的耐高温性、耐腐蚀性和耐磨性。
电火花表面强化技术能有效地改善零部件表面的物理、化学和机械性能,包括硬度、导热和导电性能等,与常规表面强化工艺相比较,具有以下优点。
( 1) 电火花强化是在空气中进行,不需要特殊、复杂的处理装置和设备。
配套装置简单、灵活,投资和运行费用低,强化工艺环保。
( 2) 热输入量小,放电时间很短,放电端点的面积小,放电的热作用只发生在零部件表面的微小区域内,被强化零部件基体不产生退火或热变形。
( 3) 不受零部件形状限制,可以对平面或曲面形状零部件强化; 对需修复局部、有少量损伤、焊接性差以及淬火状态工件的修复更具优势。
( 4) 强化层是电极和零部件材料在放电时的瞬间高温高压条件下重新合金化形成的新合金层,结合非常牢固,不易发生剥落。
( 5) 强化层厚度、表面粗糙度与脉冲电源的电气参数以及强化时间等有关,控制相对简单。
电火花强化处理后可作为最终工序,加工余量少。
( 6) 电极材料来源广,耗量小,容易实现异种材料强化层,同时可以根据强化目的选择电极材料。
金属材料超声表面强化技术的应用进展初探

赵艳艳(渤海船舶职业学院,辽宁葫芦岛125000)摘要:现在我们国家的工业十分发达,工业品的用料直接关系到工业品质量。
现在金属材料的应用非常广泛,使用需求很高,不少科学家已经在探索增强金属材料性能与强度的技术方法。
现在这方面的探究结果显示,问题还很大,因此该研究方向的上升应用空间还很大。
关键词:金属材料;超声表面强化;技术应用中图分类号:TP393文献标识码:A文章编号:1671-1602(2019)19-0041-021前言现在我们国家的经济持续发展,我国科研水平已经居于领先地位,现在科学家们十分重视强化金属材料超声表面的技术,同时理论应用已经融入实际操作,落实到了工业应用,不过现在的应用发展空间还很大。
以下本文将分析实际应用金属材料超声表面强化技术与发展在工业领域,旨在为金属材料的应用技术带来一定的借鉴价值。
2金属材料超声表面强化技术的应用2.1超声冲击处理技术众所周知,超声功率很大,是现在应用比较广泛的超声冲击处理技术的重要驱动,该技术可以自主转化电能与机械能,达到较明显的转化成效。
超声冲击处理技术大致通过压电陶瓷与磁致伸缩换能器开展作业,将机械能最终转变成变幅聚能,冲击焊件表面,碰撞过程中导致塑性变形,变成的塑性变形能极大降低了操作焊接剩下的力量,让工件更能抗疲劳[1]。
处理超声冲击技术又可以叫超声表面强化技术。
国内是从上个世纪九十年代开始研究超声冲击处理技术,主要范围是研究处理超声冲击和焊接接头的抗疲劳能力间影响。
根据科学家探索,超声冲击处理后,工件接头可以更加抗疲劳。
同时,该研究也能够用到我国的焊接结构上。
焊接接头需要用到超声冲击处理技术,可以让接头更加抗疲劳,还可以极大减少焊接后工件操作的剩下力量。
减少多出来的剩余力量还可以大幅提升接头抗腐蚀的能力。
同时,现实中加工工件时,非常有可能发生不少因为应力出现疲劳裂纹,去除他们也能依靠超声冲击处理技术。
同时,通过超声冲击处理技术,工件可以更加稳定。
表面工程学在焊接方面的应用

表面工程学在焊接方面的应用班级:学号:姓名:日期:年月日表面工程学在焊接方面的应用摘要:综述焊接中的表面工程应用及发展历史、方向、前景,介绍目前几个目前应用比较广泛的表面工程技术,并对其性能、经济等方面进行比较。
介绍爆炸焊接中表面工程技术应用。
关键词:表面工程学,焊接,应用Application of surface engineering in weldingAbstract:Surface engineering application of welding and the direction of development, prospect, present the application of surface engineering technology more widely, and compare its performance, economy etc.. The surface engineering techniques in the application of explosive welding.Key Words:Surface engineering. Welding. Application1.前言表面工程学是多学科交叉、综合,多技术融合、集成的新兴学科,表面工程的最大优势是能够以低成本、低能耗制备出优于本体材料性能、多于本体材料功能,更加适宜于服役环境要求的新表面。
表面工程学是材料科学与工程中发展最为迅速的学科之一,在机械制造、冶金、电子、汽车与船舶制造、能源与动力、航空航天等工业领域中起着举足轻重的作用,因此越来越受到广大工程技术人员的重视。
在焊接领域,表面工程学起着极其重要的作用,焊接材料表面经过预处理后,通过表面涂覆、表面改性或多种表面技术复合处理,改变焊接金属或非金属表面的形态、化学成分和组织结构域,以获得所需表面性能的系统工程。
表面强化、表面改性、表面防护以及表面修复在焊接领域的应用已有悠久的历史,但技术手段和技术内涵却在不断发展。
- 1、下载文档前请自行甄别文档内容的完整性,平台不提供额外的编辑、内容补充、找答案等附加服务。
- 2、"仅部分预览"的文档,不可在线预览部分如存在完整性等问题,可反馈申请退款(可完整预览的文档不适用该条件!)。
- 3、如文档侵犯您的权益,请联系客服反馈,我们会尽快为您处理(人工客服工作时间:9:00-18:30)。
表面强化技术在焊接领域中的应用研究
进展
摘要:科技在迅猛发展,社会在不断进步,焊接技术以其成本低、工艺简单等优点被广泛应用于结构和构件的制造。
但是,焊接过程通常会对焊接件施加残余拉伸应力,这往往会对焊接接头的疲劳性能等造成不利影响。
表面强化技术可以显著改善材料的力学性能。
综述了辊轧、高频冲击、喷丸法、激光冲击以及超声冲击法等对焊接接头性能的影响,并对其发展方向进行了展望。
关键词:表面强化;焊接;组织;力学性能
引言
焊接过程中,在形成焊缝的同时,不可避免地在其附近的母材内,经历了一次焊接热循环的特殊热处理,因而形成了一个组织和性能均不同于母材的焊接热循环区。
焊接热影响区本身是一个组织和性能极不均匀的区域;其中一些组织和性能变坏了的部位往往成为整个焊接接头中最薄弱环节,对焊接质量起着控制作用。
很多焊接结构的破坏事故都与其焊接热影响区的性能恶化有关。
国内常用的焊接后处理方法是热处理、过载处理、振动法调整残余应力处理、锤击处理、爆炸消除应力处理、温差拉伸法消除焊接残余应力。
1热喷涂技术
热喷涂是利用一种热源将喷涂材料加热至熔融状态并通过气流吹动使其雾化高速喷射到零件表面以形成喷涂层的表面加工技术。
目前在模具行业中主要发展有火焰喷涂和等离子喷涂等技术。
由于热喷涂层具有耐磨、耐蚀、减摩、抗咬合等性能可为模具提供耐磨而坚韧的热喷涂厚涂层因此特别适用于大型模具以及严重磨损条件下的模具修复。
等离子喷涂是以氮、氩等惰性气体作为工作介质在专用的喷枪内发生电离形成热等离子体再将进入该等离子弧区的粉末状涂层材料熔融、雾化并高速喷送到被涂工件表面形成涂层。
由于整个工艺集熔化、雾化、快
淬、固结等过程为一体且所获组织致密、结合牢固因此在涂层技术中占主导地位。
但等离子喷涂也存在如需要高纯气体且成本较高等缺点。
目前除常压下气稳式喷
涂工艺外又发展出优点更为突出的低压等离子喷涂及液稳式喷涂工艺正逐步推广
使用。
而火焰喷涂与等离子喷涂相比成本较为低廉、操作简便但结合的强度和密
度相对较弱。
近年来通过对此项技术的大力发展和完善目前已开发出性能更为优
良的超音速火焰喷涂并投入了实际应用。
如广州有色金属研究院采用超音速喷涂
硬质合金工艺使Cr12不锈钢拉伸模修模频率从原来的500件1次提高到7000件
1次寿命提高了3~8倍获得了十分可观的经济效益。
2激光冲击对焊接接头的影响研究
激光冲击也称为激光表面硬化或激光喷丸处理,是利用高能脉冲激光在零件
表面产生冲击波,使表面金属材料达到压缩和塑性变形的效果,在零件表面产生
残余压应力,增强了工件对表面疲劳、腐蚀疲劳和应力腐蚀裂纹的抵抗能力。
了
激光冲击处理对45钢-40Cr钢焊接接头组织性能的影响,研究结果表明:经激光
冲击后,接头焊缝区原有的马氏体组织逐渐分解为细小马氏体组织;冲击区域内
焊缝区、热影响区以及母材区的残余拉应力都变为压应力,焊缝中心区域最大平
均残余压应力可达-395MPa;同时,激光冲击使接头各区域的硬度值有不同程度
的提高,热影响区附近和焊缝中心分别提高了约60HV0.3和40HV0.3,影响层
深度约为0.5mm。
激光淬火(LQ)和激光冲击强化(LSP)两种激光强化工艺对钢轨
焊接接头抗磨抗疲劳性能的影响。
LQ工艺显著提高了钢轨焊接接头的抗磨性能,
但抗疲劳性能变差。
LQ处理焊接接头的磨损率降低了91.6%~92.4%,但LQ处
理焊接接头的平均裂纹角(23~25°)和平均裂纹长度(62~74μm)均大于未处理
钢轨焊接接头(分别为13~15°和37~59μm)。
LSP工艺提高了焊接接头的耐磨
性和抗疲劳性能。
LSP处理的焊接接头磨损率降低了5.1%~10.1%。
同时,LSP
处理的焊接接头的裂纹密度(0.9~4.2mm-1)、平均裂纹角(10~13°)和平均
裂纹长度(16~26μm)均小于未处理和LQ处理的焊接接头。
3离子注入技术
离子注入技术是将注入元素的原子电离成离子在获得较高速度后射入放在真
空靶室中的工件表面的一种表面处理技术。
由于被注入离子是以很高的速度强行
注入的所以其不受基体金属中的扩散速率以及固溶度的限制而且注入后既不改变
模具基体表面的几何尺寸又能形成与基体材料完全结合的表面合金不存在有明显
的分界面而产生剥落的问题同时由于大量离子(如氮、碳、硼、钼等)的注入可
使模具基体表面产生明显的硬化效果大大降低了摩擦因数显著地提高了模具表面
的耐磨性、耐腐蚀性以及抗疲劳等多种性能。
因此近年来离子注入技术在模具领
域中如冲裁模、拉丝模、挤压模、拉伸模、塑料模等得到了广泛应用其平均寿命
可提高2~10倍。
表2为离子注入技术在模具中的使用效果。
但是目前离子注入
技术在运用中还存在一些不足如离子注入层较薄、小孔处理困难、设备复杂昂贵
等其应用也受到一定的限制。
4表面强化处理改善焊接接头性能
1999年,金属材料表面纳米化的概念,即在材料表面制备出具有一定厚度的
纳米结构表层,形成从表层到基体梯度变化组织。
通过提高材料表层的组织和性
能均匀性,来改善材料整体的环境服役行为。
近几十年来,一些基于普通喷丸技
术发展起来的超声喷丸(USSP)、表面机械研磨等强烈塑形变形工艺(SSPD),由
于操作简单、成本较低己引起科研工作者的广泛关注。
表面强化处理工艺通过机
械或者弹丸冲击材料表面,使产生剧烈塑性变形,实现晶粒细化,在表面制备出
一层纳米结构层,且硬度明显高于心部。
焊接接头经表面强化处理,在各个区域
表面形成取向随机分布的细晶组织,实现焊接接头各个区域组织和性能的均一化。
表面强化处理消除焊接工艺产生的残余拉应力,并引入残余压应力,降低表面层
存在的微观缺陷密度,提高焊接接头整体力学性能和抗应力腐蚀和疲劳腐蚀行为。
304不锈钢进行表面喷丸处理,研究表明,喷丸处理使表层晶粒明显细化、表层
硬度显著提高。
通过有限元模拟技术分析了喷丸处理对焊缝及近缝区表层残余应
力的影响,结果表明,沿试板厚度方向分布的残余拉应力明显改善。
采用高能喷
丸处理SS400钢焊接接头表面。
结果表明:高能喷丸处理实现了SS400钢焊接接
头表层组织和硬度的均一化,高能喷丸处理引入SS400钢焊接接头表面的残余压
应力是改善应力腐蚀的主要原因,同时表面强化层提高了焊接接头的疲劳寿命。
结语
激光冲击强化处理可以改善焊接接头出金属的力学性能和微观组织,大幅度提高焊缝和热影响区的硬度,消除残余拉应力,提高焊接头疲劳寿命。
对焊接头双面激光冲击强化处理效果优于单面处理。
参考文献
[1]彭云,宋亮,赵琳,等.先进钢铁材料焊接性研究进展[J].金属学报,2020,56(4):601-618.
[2]陈健,苏金花,张毅梅.《中国制造2025》与先进焊接工艺及装备发展[J].焊接,2016(3):1-5.
[3]黄卓笑,张显程,涂善东,等.表面深滚处理对纯镍组织性能及残余应力分布的影响[J].航空材料学报,2016,36(1):39-47.
[4]陈怀宁,陈亮山.微量预应变对焊接接头疲劳性能的影响[J].焊接学报,1992(3):193-197.
[5]许飞,张侃,陈安.残余应力对搅拌摩擦焊接头裂纹扩展速率的影响[J].电焊机,2019,49(9):110-115.。