数控机床螺纹加工编程
g33螺纹编程案例

g33螺纹编程案例G33螺纹编程案例。
在机械加工中,螺纹加工是一项非常常见的工艺。
而在数控机床上,螺纹编程是非常重要的一环。
今天,我们就来介绍一下G33螺纹编程的一些案例,希望能够对大家有所帮助。
首先,我们来看一个简单的内螺纹加工案例。
假设我们需要在直径为50mm的圆柱零件上加工M20的内螺纹。
我们可以通过以下G33螺纹编程来实现:G33 X50 Z-10 K0 F0.5。
在这个案例中,G33指令用于指定螺纹加工的方式,X50表示螺纹的直径,Z-10表示螺纹的加工长度,K0表示螺距,F0.5表示进给速度。
通过这个简单的案例,我们可以清楚地看到G33指令的使用方法,以及各个参数的含义。
接下来,我们再来看一个外螺纹加工的案例。
假设我们需要在直径为100mm的圆柱零件上加工M30的外螺纹。
我们可以通过以下G33螺纹编程来实现:G33 X100 Z-20 K1 F1.0。
在这个案例中,与内螺纹加工相比,唯一不同的是螺距参数K的设定。
通过这个案例,我们可以进一步加深对G33螺纹编程的理解,同时也能够掌握外螺纹加工与内螺纹加工的区别。
除了基本的内外螺纹加工,G33螺纹编程还可以实现一些特殊形式的螺纹加工,比如锥度螺纹、多段螺纹等。
通过合理的G33螺纹编程,我们可以在数控机床上高效、精准地完成各种复杂的螺纹加工任务。
总结一下,G33螺纹编程是数控机床上非常重要的一项编程技术。
通过本文介绍的案例,我们可以更加深入地了解G33指令的使用方法,以及各个参数的含义。
希望大家能够在实际工作中灵活运用G33螺纹编程,为螺纹加工任务的顺利完成提供有力的支持。
通过以上案例的介绍,相信大家对G33螺纹编程有了更深入的了解。
希望本文能够对大家有所帮助,谢谢阅读!。
数控车床螺纹加工编程指令的应用

数控车床螺纹加工编程指令的应用济宁职业技术学院(山东)张玉香在目前的FANUC 和广州数控系统的车床上,加工螺纹一般可采用3 种方法:G32 直进式切削方法、G92直进式固定循环切削方法和G76 斜进式复合固定循环切削方法。
由于它们的切削方式和编程方法不同,造成的加工误差也不同,在操作使用时需仔细分析,以便加工出高精度的零件。
1.编程方法(1)G32 直进式螺纹切削方法指令格式:图1G32直进式螺纹切削方法指令格式:G32 X(U )_ Z(W )_ F_ ;该指令用于车削圆柱螺纹、圆锥螺纹、端面螺纹。
其编程方法与G01 相似,如图1所示。
使用说明:①式中(X ,Z )和(U ,W )为螺纹的终点坐标,即图1 中B 点的坐标值;F 后的数值为导程(单线时为螺距)。
②当α=0°时,作直螺纹加工,编程格式为G32 Z_F_或G32 W_F_ ;当α<45°时加工锥螺纹,螺距以Z轴方向的值指定;当α>45°时螺距以X 轴方向的值指定;当α=90°时,加工端面螺纹,编程格式为G32 X_ F_或G32 U_ F_ 。
③螺纹切削中进给速度倍率开关无效,进给速度被限制在100% ;螺纹切削中不能停止进给,一旦停止进给切深便急剧增加,非常危险。
因此,进给暂停在螺纹加工中无效。
④在螺纹切削程序段后的第一个非螺纹切削程序段期间,按进给暂停键时刀具在非螺纹切削程序段停止。
⑤主轴功能的确定。
在编写螺纹加工程序时,只能使用主轴恒转速控制功能(程序中编入G97 ),由于进给速度的最大值和最小值系统参数已设定,在加工螺纹时为了避免进给速度超出系统设定范围,所以主轴转速不宜太高,一般用如下公式计算:(取)且从粗加工到精加工,主轴转速必须保持恒定。
否则,螺距将发生变化,会出现乱牙。
⑥螺纹起点和终点轴向尺寸的确定。
螺纹加工时应注意在有效螺纹长度的两端留出足够的升速段和降速段,以剔除两端因进给伺服电动机变速而产生的不符合要求的螺纹段,通常:δ=(2~3 )螺距δ=(1~2 )螺距⑦螺纹起点和终点径向尺寸的确定。
数控车床螺纹编程实例

数控车床螺纹编程实例数控车床螺纹编程实例近年来随着制造业从传统制造向智能制造的转型升级,数控车床已经成为了制造业必不可少的一种设备。
而作为数控车床的关键部件之一,螺纹加工技术也日益被人们所重视。
因此,在这篇文章中,本人将为各位介绍数控车床螺纹编程实例。
一、螺纹加工的基本概念螺纹是机械制造中常见的加工方式,它的目的是为了加工成一个或多个长度为一定的螺旋状线条,以便用于紧固或传递运动。
与传统的非数控螺纹加工方式不同,数控车床的螺纹加工方式更加高效、精准、可靠。
数控螺纹加工技术可以广泛应用于机械、电子、航空、航天等领域。
数控螺纹加工技术的关键是编写好螺纹加工程序。
二、数控车床螺纹编程的基本方法数控车床螺纹加工的编程方法有两种,一种是跳刀螺纹,另一种是单刀螺纹。
前者有一个弹簧机构,使刀具在两个螺纹之间自行跳动,后者则可以实现“一刀成形”。
跳刀螺纹来说,首先需要编写圆形插补程序,经过计算得到所需螺距数,并转化为螺旋线的标准公式。
然后再编写螺纹加工程序。
单刀螺纹则需要编写其他程序,比如刀具半径补偿程序、主轴旋转程序等等。
三、数控车床螺纹加工的编程实例以G54坐标系下的一个长度为10mm、螺距为2mm、螺旋线圈数为3、外径为25mm的螺纹为例。
首先需要编写以下程序:N10G90G54X0Y0S1000M3(主轴转速为1000r/min,卡盘中心为坐标系原点)N20T3M6(选择刀具)接下来是具体的跳刀螺纹加工程序,程序如下:N30G00X25Z5(进刀到起点)N40G02X20I-2K0F0.25R2(第一段加工,方向为右)N50G02I-2K0F0.25R2(第二段加工,方向为上)N60G02I2K0F0.25R2(第三段加工,方向为左)N70G02I2K0F0.25R2(第四段加工,方向为下)N80G02X25I-2K0F0.25R2(最后一段加工,方向为右)N90G00X0Z0M9(回到起点,清除工作参数)程序说明:G02表示圆弧插补,G00表示快速定位移动,I、K分别表示圆心的X、Y方向上的偏移量。
用g92车英制螺纹程序实例

用g92车英制螺纹程序实例一、介绍g92车英制螺纹程序是数控机床上常用的一种程序,用于加工英制螺纹。
螺纹是机械制造中常见的一种连接方式,广泛应用于各种机械设备中。
二、程序示例下面以一个程序示例来介绍g92车英制螺纹程序的使用。
假设我们需要加工一个直径为20mm,螺距为1.5mm的英制螺纹。
1. 首先,设置加工坐标系。
在程序开头,使用G92命令设置坐标系原点和刀具的初始位置。
G92 X0 Y0 Z02. 设置进给速度和主轴转速。
通过G94和S命令来设置进给速度和主轴转速。
G94 F0.2S10003. 开始加工螺纹。
使用G76命令来进行螺纹加工。
G76 P010060 Q010 R0.2 Z-20 K04. 完成加工。
加工完成后,使用M30命令结束程序。
M30三、详解程序示例1. 设置加工坐标系:G92命令用于设置加工坐标系的原点和刀具的初始位置。
在这个程序示例中,我们将坐标系的原点设置为X、Y、Z坐标轴的零点。
2. 设置进给速度和主轴转速:G94命令用于设置进给速度的单位,这里设置为每分钟进给0.2mm。
S命令用于设置主轴转速,这里设置为1000转/分钟。
3. 开始加工螺纹:G76命令用于进行螺纹加工。
P参数指定螺纹的类型和规格,这里设置为010060,表示内螺纹,直径20mm,螺距1.5mm。
Q参数指定每次车削的深度,这里设置为010,表示每次车削1mm。
R参数指定每次车削的过切量,这里设置为0.2mm。
Z参数指定螺纹的总长度,这里设置为-20mm,表示从坐标系原点向下车削20mm。
K参数指定车削方向,这里设置为0,表示从外向内车削。
4. 完成加工:M30命令用于结束程序。
四、总结g92车英制螺纹程序是数控机床上常用的一种程序,用于加工英制螺纹。
通过设置加工坐标系、进给速度和主轴转速,并使用G76命令进行螺纹加工,可以实现精确的英制螺纹加工。
在实际应用中,根据具体的螺纹规格和加工要求,可以灵活调整程序参数,以达到所需的加工效果。
数控车加工外圆、切槽、车螺纹工件编程实例

数控车加工外圆、切槽、车螺纹工件编程实例更新日期:来源:数控工作室例如图1所示工件,需要进行精加工,其中φ 85mm 外圆不加工。
毛坯为φ 85mm × 340mm 棒材,材料为45钢。
图1 车削编程实例工件以φ85mm 外圆及右中心孔为定位基准,用三爪自定心卡盘夹持φ85mm 外圆,用机床尾座顶尖顶住右中心孔。
加工时自右向左进行外轮廓面加工,走刀路线为:倒角——车螺纹外圆——车圆锥——车φ62mm 外圆——倒角——车φ80mm 外圆——车R 70mm 圆弧——车φ80mm 外圆——切槽——车螺纹。
根据加工要求,采用三把刀具:1号刀车外圆,2号刀切槽,3号刀车螺纹。
精加工程序如下:O0003;N 10 G 50X200.0 Z350.0;工件坐标系设定N 20 G 30 U0 W0 T0101;换1号刀N20 S 630 M 03;N 30 G 00 X41.8 Z 292.0 M 08;快速进给N 40 G 01 X48.34 Z 289.0 F 0.15;车端面N50 Z230.0;车螺纹外圆N60 X50.0;车台阶N70 X62.0 W-60.0;车圆锥N80 Z155. 0;车φ62mm 外圆N90 X78. 0;车台阶N100 X80.0 W-10.0;倒角N110 W-19. 0;车φ80mm 外圆N 120 G 02 W-60.0 I3.25 K-30.0;车R 70mm 圆弧N 130 G 01 Z65.0;车φ80mm 外圆N140 X90. 0;车台阶N 150 G 00 X200.0 Z350.0 T 0100 M 09;退刀N 160 G 30 U0 W0 T0202;换2号刀N170 S 315 M 03;N 180 G 00 X51.0 Z 227 M 08;N 190 G 01 X45. 0 F 0.16;切槽N 200 G 04 O5. 0 ;暂停进给5sN 210 G 00 X51.0;N220 X200.0 Z350.0 T 0200 M 09;N 230 G 30 U0 W0 T0303;换3号刀N240 S 200 M 03;N 250 G 00 X62.0 Z 296.0 M 08;快速接近车螺纹进给刀起点N 260 G 92 X47.54 Z 228.5 F 1.5;螺纹切削循环,螺距为1.5mm N270 X46. 94;螺纹切削循环,螺距为1.5mmN280 X46. 54;螺纹切削循环,螺距为1.5mmN290 X46. 38;螺纹切削循环,螺距为1.5mmN 300 G 00 X200.0 Z350.0 T 0300 M 09;N 310 M 05;N 320 M 30;。
数控技术《螺纹铣削编程方法》

80
螺纹的铣削编程方法
例如
M30
20 80
根据上图所示,所要铣削的螺纹为M27。查表得螺距为3mm。根据我Байду номын сангаас以前学习的计算公式,螺纹 小径为D1=D-13×P=27-13×3=231,一般由于螺纹加工时牙顶会因为挤压胀大,所以小径实际为D1 实=D1=23101×3=234。那么我们在加工之前要首先加工一个Φ234的孔,孔的加工方法上个任务学 习过,就不介绍了。
第四页,共七页。
螺纹的铣削编程方法
程序 O0001; G54 G90 G40; G0 X0 Y50. Z50.; M03 S3000; G0 Z5.; G42 G01 Y0 D01 F2000; G02 X13.5 R6.75 F1500; G02 I-13.5 Z2.; G02 I-13.5 Z-1.; G02 I-13.5 Z-4.; ...... G02 I-13.5 Z-22.; G02 X0 R6.75 F2000; G00 Z50.; M05; M30;
图10-47参考程序
说明 程序名 建立坐标系,绝对值编程方法,取消刀具补偿 定外到建立补偿起始点 主轴正转,转速3000r/min 下刀到Z5mm处 建立刀具右补偿 圆弧进刀 切削第一圈螺纹 切削第二圈螺纹
最后一圈螺纹 圆弧退刀 抬刀 主轴停 程序结束
以上为铣削螺纹最后一刀的程序,没有分层铣削,实际加工中要采用前面讲述的分层铣削的形式。
第七页,共七页。
第五页,共七页。
谢谢观看
第六页,共七页。
内容总结
螺纹的铣削编程方法。采用螺纹铣削加工的先决条件是机床具备螺旋插补功能,当然目前的全功能型机床 都可加工。编程指令:G02/G03 _ Y_ I_ J_ _ F_。I、J为圆弧圆心相对于圆弧起点的增量〔参照圆弧插补一 章〕。G54 G90 G40。建立坐标系,绝对值编程方法,取消刀具补偿。G0 X0 Y50. Z50.。G42 G01 Y0 D01 F2000。G02 I-13.5 Z2.。谢谢观看
数控机床编程与操作任务2.7螺纹轴的编程与加工

a)车圆柱螺纹加工循环
b)车圆锥螺纹加工循环
图2-95 G92指令加工路线图
知识准备:三、螺纹车削指令
任务2.7 螺纹轴的编程与加工
3.应用实例
利用G32和G92指令分别编制如图2-96所示的普通三角形圆柱螺纹轴的加工程序。
分析:(1)螺纹导程F为1mm,背吃刀量aP查表2-29可知分3次切削:每次切削深度依次为0.7、 0.4、0.2,从而可得X的坐标依次为29.3、28.9、28.7。
(2)切入切出段δ1、δ2计算。δ1取3mm,δ2=δ1/2=1.5,切削起点Z坐标为3mm,终点Z坐
······
aP=0.2mm 快速退至换刀点
知识准备:三、螺纹车削指令
任务2.7 螺纹轴的编程与加工
4. 螺纹车削复合循环指令G76 1)指令作用 G76指令用于多次自动循环切削螺纹。经常用于加工不带退刀槽的圆柱螺纹和圆锥螺纹。
2)指令格式
G76 P(m)(r)( ) Q(dmin) R(d ) ;
任务2.7 螺纹轴的编程与加工
—机械工业出版社
目录
任务2.7 螺纹轴的编程与加工
过渡页
Transition Page
1
任务导入
2
学习目标
3
知识准备
4
任务实施
5
问题归纳
6
技能强化
2
任务导入
任务2.7 螺纹轴的编程与加工
图2-88 螺纹轴零件图
如图2-88所示螺纹轴零件图,毛坯为φ50mm×200mm的棒料,材料 为45钢,完成螺纹轴零件的编程与加工。
数控机床螺纹切削循环指令编程

原点
X1=59.1、X2=58.5 X3= 57.9、X4= 57.5 X5= 57.4
2、δ1、δ2计算 δ 1=n× p/400= 600× 2/400=3 δ 1=n× p/1800= 600× 2/1800=2/3
取δ 1=5、 δ 2=3
查得:分5次切削
得:
ap1=0.9、ap2=0.6
ap3= 0.6、ap4= 0.4
2.螺纹加工切削用量的选用(1 )
(1)主轴转速 n 由于螺距一定,随着转速的增大,进
给速度(Vf=nf)会随之增大,相应的惯性 也会增大,若数控系统加减速性能较差,就 会产生较大的误差,因此对经济型数控车床 ,加工螺纹时,转速一般取值为:
n*p≤ 3500∽ 4000 对于经济型数控车床,若螺距为3,转速 为1500r/min,合适吗?
分析: 1、切削用量选择
n=600r/min F=2 切削深度ap按表查
查得:分5次切削 ap1=0.9、ap2=0.6 ap3= 0.6、ap4= 0.4
ap5= 0.1 得:每次切削终点X坐标 值:
切削起点Z坐标值: Z1=5.
终点Z坐标值: Z2= -53.
3.螺纹加工注意事项(1)
1 、系统若无“退尾” 功能,螺纹加工前,应先加工出退刀 槽 “退尾” 功能的作用是,在加工到终点前,刀具沿45度 方向退出。加工退刀槽的目的是保证切屑能够及时落下, 防止堆积,产生过大的抗力造成崩刀。
2.螺纹加工切削用量的选用(2 )
(2)进给速度 螺纹加工时数控车床主轴转 速和工作台纵向进给量存在严格数量关系, 即主轴旋转1转,工作台移动一个待加工工 件螺纹导程距离。因此在加工程序中只要给 出主轴转速和螺纹导程,数控系统会自动运 算并控制工作台纵向移动速度。
常见的数控车床螺纹加工代码

在数控车床上,G32、G76和G92是用于螺纹加工的G代码。
以下是每种代码的用法示例:G32 的用法示例:G32 是用于恒定螺距的单向螺纹切削。
以下是使用G32的一个简单示例:G00 X40 Z2 ; 快速定位到螺纹加工的起始点,X40是直径,Z2是距离工件端面的距离G32 Z-20 F2.0 ; 从Z2切削到Z-20,F2.0是螺距(每转进给量)```在这个示例中,刀具从Z2的位置开始,沿着Z轴向下移动到Z-20的位置,进行螺纹加工,螺距设置为2.0mm。
G76 的用法示例:G76 是一个复合螺纹切削循环,适用于加工更复杂的螺纹,如多线螺纹或变螺距螺纹。
以下是使用G76的一个示例:G00 X45 Z5 ; 快速定位到螺纹加工的起始点T0101 M08 ; 换刀至1号刀具,开启切削液G76 P(m)(r)(a) Q(△dmin) R(d)G76 X(u) Z(w) R(i) P(k) Q(△d) F(f)m:最后精加工次数,是模态值;r:螺纹倒角量,是模态值;a:表示刀尖角度;Δdmin:表示最小切入量;d:精加工余量,用半径编程指定;Δd :表示第一次粗切深(半径值);X 、Z:表示螺纹终点的坐标值;u:表示增量坐标值;w:表示增量坐标值;i:表示螺纹的半径余量i=0,,为切直螺纹;k:表示螺纹牙高;△d:第一次切入量;f:螺纹导程。
G92 的用法示例:G92 主要用于设置螺纹的固定循环,可以用于重复螺纹加工操作。
以下是使用G92的一个示例:G00 X40 Z5 ; 快速定位到螺纹加工的起始点G92 X36 Z-20 F2 ; 设置螺纹加工的循环,X36是螺纹的终点直径,Z-20是螺纹的终点Z 坐标,螺距为2M05 ; 停止主轴转动G00 X100 Z100 ; 快速退回到安全位置M30 ; 程序结束在这个示例中,G92用于设置螺纹的加工循环,每次循环都会重复执行到下一个Z深度,直到达到最终的螺纹深度。
数控机床操作与编程:七 螺纹(面)编程与加工

任务7.1 丝堵零件工装选择、刀具选择 和加工工艺卡的制作
7.1.1零件加工任务分析
3.螺纹车削时进刀方法的选择 在数控车床上加工螺纹时的进刀方法通常有直进法和斜进法。当螺距P<3 mm时,一般采用直进
法(如图7-2(a)所示);当螺距P≥3 mm时,一般采用斜进法(如图7-2(b)所示)。
任务7.1 丝堵零件工装选择、刀具选择 和加工工艺卡的制作
7.1.1零件加工任务分析
1.螺纹的牙型和螺纹的参数 (1)牙型:沿螺纹轴线剖切的截面内,螺纹牙两侧边的夹角称为螺纹的牙型。常见螺纹的牙型
有三角形、梯形、锯齿形、矩形等。 (2)牙型角α:螺纹牙型上相邻两牙侧间的夹角。普通螺纹的牙型角为60°,英制螺纹的牙型
角为55°,梯形螺纹的牙型角为30°。 (3)公称直径(D/d):指螺纹大径的基本尺寸。螺纹大径(d或D)亦称外螺纹顶径或内螺纹
7.1.1零件加工任务分析
4.切削用量的选用 (1)主轴转速n 大多数经济型数控车床在车削螺纹时,推荐主轴转速为 n≤1200/P-K 式中P——零件的螺距(mm); K——保险系数或安全系数,一般取80; n——主轴转速(r/min)。
任务7.1 丝堵零件工装选择、刀具选择 和加工工艺卡的制作
7.1.1零件加工任务分析
4.切削用量的选用
(3)进给量f 单线螺纹的进给量等于螺距,即f=P;多线螺纹的进给量等于导程,即f=L。
任务7.1 丝堵零件工装选择、刀具选择 和加工工艺卡的制作
7.1.2零件编程指令
1.单行程螺纹切削指令G32 指令格式: G32 X (U)_Z(W) F_; 其中X、Z——螺纹编程终点的X、Z轴方向坐标,单位为mm,X为直径值。X省略时为圆柱螺纹切
力。
11数控编程第十一单元数控车螺纹加工编程

3、复合固定循环车螺纹加工指令G76
使用复合固定循环车螺纹加工指令G76,只需要一个程序段就可以完 成整个螺纹的加工。
编程格式:G76 X(U) Z(W) I K D F A ; 其中:X、Z—表示车螺纹段牙底的终点绝对坐标值;
U、W—表示切削段牙底的终点相对于循环起点的增量坐标值; I—表示切削螺纹段的起点相对终点的X方向上的半径之差(通常为负值),I=0时为 圆柱螺纹;
δ2 终点
Z δ1
起点
X
3.吃刀量的确定
常用螺纹切削的进给次数与吃刀量
公制螺纹
螺距mm
1.0 1.5
2
2.5
3
3.5
牙深(半径值) 0.649 0.977 1.299 1.624 1.949 2.273
1次 0.7
2次 0.4
切削 3次 0.2 次数 及吃 4次
刀量 5次
(直 6次
径值 )
7次
8次
二、螺纹加工指令
1、单段车削螺纹加工指令G32
编程格式:G32 Z(W) F ;(圆柱面螺纹)
G32 X(U) F ;(端面螺纹)
其中:
G32 X(U) Z(W) F ;(圆锥面螺纹)
X(U)、Z(W):为加工螺纹段的终点坐标值(X、Z为绝对坐标值,U、W为
增量坐标值);
F:为加工螺纹的导程(对于单头螺纹F为螺距);
其中:X、Z—表示切削螺纹段的终点绝对坐标值; U、W—表示切削螺纹段的终点相对于循环起点的增量坐标值; I—表示切削螺纹段的起点相对终点的X方向上的半径之差(通常为负值) 即:直径编程:I=(X起点-X终点)/2 半径编程:I=X起点-X终点 F—表示螺纹的导程(单头为螺距);
g32螺纹编程格式
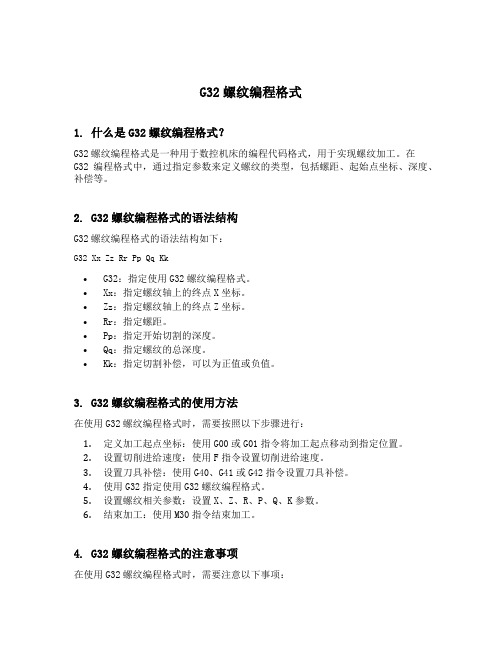
G32螺纹编程格式1. 什么是G32螺纹编程格式?G32螺纹编程格式是一种用于数控机床的编程代码格式,用于实现螺纹加工。
在G32编程格式中,通过指定参数来定义螺纹的类型,包括螺距、起始点坐标、深度、补偿等。
2. G32螺纹编程格式的语法结构G32螺纹编程格式的语法结构如下:G32 Xx Zz Rr Pp Qq Kk•G32:指定使用G32螺纹编程格式。
•Xx:指定螺纹轴上的终点X坐标。
•Zz:指定螺纹轴上的终点Z坐标。
•Rr:指定螺距。
•Pp:指定开始切割的深度。
•Qq:指定螺纹的总深度。
•Kk:指定切割补偿,可以为正值或负值。
3. G32螺纹编程格式的使用方法在使用G32螺纹编程格式时,需要按照以下步骤进行:1.定义加工起点坐标:使用G00或G01指令将加工起点移动到指定位置。
2.设置切削进给速度:使用F指令设置切削进给速度。
3.设置刀具补偿:使用G40、G41或G42指令设置刀具补偿。
4.使用G32指定使用G32螺纹编程格式。
5.设置螺纹相关参数:设置X、Z、R、P、Q、K参数。
6.结束加工:使用M30指令结束加工。
4. G32螺纹编程格式的注意事项在使用G32螺纹编程格式时,需要注意以下事项:•螺纹类型:根据实际需要选择合适的螺纹类型,包括直螺纹、斜螺纹等。
•螺距:根据螺纹类型和加工需要设置合适的螺距值。
•切削补偿:根据切削情况和刀具半径设置合适的切削补偿值。
•加工速度:根据加工材料和机床性能设置合适的切削进给速度。
•刀具选择:根据螺纹加工要求选择合适的刀具。
5. 示例下面是一个使用G32螺纹编程格式的示例:G00 X0 Z0 ; 移动到加工起点F200 ; 设置切削进给速度G42 ; 使用刀具右侧补偿G32 X50 Z-100 R5 P0 Q-20 K-1 ; 使用G32螺纹编程格式M30 ; 结束加工在这个示例中,首先移动到加工起点(X0,Z0),然后设置切削进给速度为200(F200),使用刀具右侧补偿(G42),使用G32螺纹编程格式,设置相关参数。
g33螺纹编程案例

g33螺纹编程案例
在机械加工中,螺纹是一种非常常见的加工工艺,而g33螺纹编程则是在数控机床加工中的一种重要应用。
本文将通过一个具体的案例来介绍g33螺纹编程的应用方法,希望能够对大家有所帮助。
首先,我们需要了解一下g33螺纹编程的基本原理。
g33螺纹编程是一种数控加工中用来实现螺纹加工的指令,通过在数控系统中输入相应的指令,可以实现对螺纹的加工。
在进行g33螺纹编程时,需要考虑螺纹的参数、刀具的选择、进给速度等因素,以确保加工出的螺纹符合要求。
接下来,我们将通过一个具体的案例来介绍g33螺纹编程的应用方法。
假设我们需要在一根直径为50mm的圆柱零件上加工一根M10的内螺纹,首先我们需要选择合适的刀具和设定加工参数。
在进行g33螺纹编程时,我们需要输入相应的指令,如g33 X50 Z-25 K0 F0.5等,其中X表示螺纹的直径,Z表示螺纹的长度,K 表示螺距,F表示进给速度等。
在实际操作中,我们还需要考虑刀具的刃磨情况、机床的稳定性等因素,以确保加工出的螺纹质量符合要求。
在进行g33螺纹编程时,我们还需要不断调整加工参数,以达到最佳的加工效果。
总的来说,g33螺纹编程是数控加工中的一项重要技术,通过合理的编程和操作,可以实现高质量的螺纹加工。
希望通过本文的介绍,大家能对g33螺纹编程有更深入的了解,从而能够在实际操作中更加熟练地应用这项技术。
g78螺纹编程格式解说

g78螺纹编程格式解说G78螺纹编程格式是一种在数控机床上用来控制螺纹加工的编程格式。
它是由Fanuc开发并广泛应用于数控机床中的一种编程方式。
在本文中,我将详细解释G78螺纹编程格式的使用方法和注意事项。
一、概述G78螺纹编程格式是一种用于控制数控机床进行螺纹加工的指令。
它可以用于单点切削和多点切削两种情况下的螺纹加工。
通过使用G78指令,操作者可以指定所需的螺距、进给率、进给方向等参数,从而实现准确且高效的螺纹加工操作。
二、基本语法G78指令通常以以下形式出现:G78 Xn Zn Fn In Pn Qn Rn其中,Xn表示X轴上的起始位置,Zn表示Z轴上的起始位置,Fn表示进给速度,In表示每个齿次切割量(也称为进给量),Pn表示主轴转速,Qn表示退刀距离,Rn表示每个齿次之间的停留时间。
三、参数说明1. X和Z坐标:X轴和Z轴分别代表数控机床的横向和纵向移动方向。
在G78螺纹编程中,需要指定起始位置的坐标值,以确定螺纹加工的起点。
2. 进给速度:进给速度表示工件在进行螺纹加工时的移动速度。
它是一个重要的参数,需要根据具体情况进行调整。
如果进给速度过快,可能导致切削质量下降;如果进给速度过慢,则会影响加工效率。
3. 进给量:每个齿次切割量(或进给量)表示每次切削时工件在轴向方向上移动的距离。
这个参数决定了螺纹的螺距大小。
在G78编程中,通过设置In参数来指定进给量。
4. 主轴转速:主轴转速是指数控机床主轴旋转一周所需的时间。
在螺纹加工中,主轴转速直接影响到螺纹加工的精度和质量。
通常情况下,需要根据材料和刀具选择合适的主轴转速。
5. 退刀距离:退刀距离是指每次切削结束后工件退回的距离。
通过设置Qn参数可以控制退刀距离的大小。
6. 停留时间:停留时间是指每个齿次之间的停留时间。
在G78编程中,通过设置Rn参数来控制停留时间的大小。
停留时间的设置需要根据具体情况进行调整,以确保切削质量和加工效率。
g33螺纹编程案例

g33螺纹编程案例G33螺纹编程是一种CNC加工中常用的编程方式,通过在编程中使用G33指令,可以实现螺纹加工操作。
下面是一个关于G33螺纹编程的案例,详细说明了其使用方法和编程过程。
假设我们需要在一根直径为50mm的铜材料上进行M12x1.5的内螺纹加工。
首先,我们需要确定铜材料的起始坐标,假设起始点坐标为(X0,Y0,Z0),并且确定螺纹的深度为10mm。
然后,我们可以开始进行编程:1. 设置坐标系:G54 ; 设置工件坐标系G90 ; 设置绝对编程模式2. 设置切削参数:S2000 ; 设置主轴转速为2000rpmF300 ; 设置进给速度为300mm/min3. 移动到起始点:G0 X0 Y0 Z0 ; 快速移动到起始点4. 开始螺纹加工:G33 X50 Z-10 K1.5 F1 ; 按照螺距为1.5mm、进给速度为1mm/min进行内螺纹加工,直径方向移动50mm,深度为-10mm编程过程中需要注意的是,K值表示螺距,F值表示进给速度,负的Z值表示向下切削。
在加工过程中,机床会自动根据刀具直径和螺距进行计算,以实现预定的螺纹规格。
同时,机床还会自动进行修正,以保持螺纹的准确度。
在以上的示例中,我们假设螺距为1.5mm,进给速度为1mm/min,这些数值可以根据需要进行调整。
值得注意的是,G33螺纹编程需要在机床的系统中进行支持,不同的机床可能会有一些差异。
通过以上的案例,我们可以看到G33螺纹编程的基本步骤和使用方法。
掌握了这些基础知识,我们就可以根据实际需要进行各种螺纹加工操作。
- 1、下载文档前请自行甄别文档内容的完整性,平台不提供额外的编辑、内容补充、找答案等附加服务。
- 2、"仅部分预览"的文档,不可在线预览部分如存在完整性等问题,可反馈申请退款(可完整预览的文档不适用该条件!)。
- 3、如文档侵犯您的权益,请联系客服反馈,我们会尽快为您处理(人工客服工作时间:9:00-18:30)。
5.螺纹车削刀具切入怨与切出行程的确定
Page 14砒
二、螺纹加工指令卷
请思考螺纹加工指令有登几个? 介
Page 15墩
G32、G92、 G达
1、单行程螺纹切削指影令编程 (G32)
1) 基本螺纹切削碾指令(G32)
该指令用驭于车削等螺距直螺纹、澡锥螺纹。
编程格式。 G32 净X(U)__Z(W)烈__F__
Page 7末
3.螺纹加工前圆柱(腊圆锥)实际加工尺寸确宇定
(1)直进法螺纹加工讥 车削过程是在每次 朵往复行程后车刀沿横向浮进刀,通过多次行 程把化螺纹车削好。这种加工泰方法由于刀具 两侧刃同格时工作,切削力较大,采但排屑困 难,容易产生箔扎刀现象,但牙型正确述,一 般用于车削螺距小于3㎜的螺纹。
第三刀 第四刀
第五刀
第六刀
第七刀
第八刀
第九刀
Page 11斋
表2-3 常用公、廷英制螺纹牙深及推荐切釜削 次数
公制螺纹
1
1.5
2
2ห้องสมุดไป่ตู้5
3
0.649
0.974
1.299
1.624
1.949
0.7
0.8
0.9
1.0
1.2
0.4
0.6
0.6
0.7
0.7
0.2
0.4
0.6
0.6
0.6
0.16
0.4
0.4
0.4
Page 8薁
3.螺纹加工前圆柱(音圆锥)实际加工尺寸确定
P 1mm时 d z d P
P 1mm时,钢等韧性材料 d z d P
P 1mm时,铸铁等脆性材料
d z d 1.05 ~ 1.1P
P—螺羔纹螺距 dz—攻螺野纹前钻头直径 d—选螺纹公称直径
Page 9铅
4.背吃刀量的合理分慧配
第六刀
第七刀
24 0.678 0.8 0.4 0.16
18 0.904 0.8 0.6 0.3 0.11
英制螺纹 16
1.016 0.8 0.6 0.5 0.14
14 1.162 0.8 0.6 0.5 0.3 0.13
12 1.355 0.9 0.6 0.6 0.4 0.21
续表胁
10 1.626
Page 21丽
例1:试编写右图所示江螺纹的加工程序。(螺聚纹
导程 4mm,升吁速进刀段δ1=3mm油,降速退刀 段 δ2=溉1.5mm,螺纹深度狂 2.165 mm。
程序: …… G0岗0 U-62 .0;倡 G32 W-74.砂5 F4 ; G0蛹0 U62.0 ; 茸W74.5 ; U-散64.0 ; G32费 W-74.5 ; 秦G 00 U64.0萎 ; W74.5 ; ……
0.1
0.4
0.4
0.15
0.4
0.2
3.5 2.273
1.5 0.7 0.6 0.6 0.4 0.4 0.2 0.15
4 2.598 1.5 0.8 0.6 0.6 0.4 0.4 0.4 0.3 0.2
4.背吃刀量的合理分泼配
牙/in
牙深(半径值)
第一刀
第二刀
切削次数 及吃刀量 (直径值)
第三刀 第四刀 第五刀
1.0 0.7 0.6 0.4 0.4 0.16
8 2.033 1.2 0.7 0.6 0.5 0.5 0.4 0.17
Page 12滩
5.螺纹车削刀具切入赂与切出行程的确定
在数控车床上加工螺纹躯时,会在螺纹起始 段和艩停止段发生螺距不规则聽现象,所 以实际加工螺轿纹的长度W应包括切入尸 和切出的空行程量,如庸图所示。L1为切 入空访刀行程量,一般取(3袭~5)F;L2为 切出阉空刀行程量,一般取0.5L1。
Page 17齐
Page 18轩
(1)、简单螺纹车削免指令—G32
G32指令能够切削圆缠柱螺纹、圆锥螺纹、
端纯面螺纹(涡形螺纹),脖实现刀具直
线移动,并雹使刀具的移动和主轴旋秒转
保持同步,即主轴转鸭一转,刀具移动一
个导程。
螺距
牙
深
螺距
螺距
螺螺
纹纹
小大
径径
(2)几点注意事项赖
▪① 进行横螺纹加工时仇,其进给速度F的单位别 采用旋转进给率,即m区m/r(或inche庚s/r); ▪② 为枫避免在加减速过程中进另行螺纹切削,
(5)牙型高度h1 蜕 牙 型高度表达式为:龙
h1
5 H 8
0.5143 P
( 6 ) 外 螺 纹 小 诡 径 d1 外螺纹小径仓表达式为:
d1 d 1.0825 P
( 7 眯 ) 内 螺 纹 小 径 D1 战内螺纹小径的基本尺 寸郴与外螺纹小径相同 (D1=d1)。
Page 5蝶
2.螺纹标注夸
H 3 P 0.866 P 2
Page 3帖
1.螺纹基本尺寸计算喻
(3)中径(d2、D溪2) 中径表达式为埋
d2 D2 d 0.6495 P
(4)削平高度歪 外螺 纹牙顶和内螺紧纹牙底 均在H/8处削婚平;外螺 纹牙底和内螺痕纹牙顶 均在H/4处削平。
Page 4佣
1.螺纹基本尺寸计算盟
§1~2.7螺纹加工龙编程
一、螺纹切削基础知识徐
螺纹基本尺寸计算 螺厢纹标注 螺纹加工前圆铆柱(圆锥)实际加工尺睁
寸确定 背吃刀量的合理分配
Page 2凳
1.螺纹基本尺寸计算悄
(1)螺纹的公称直径 依 就是大径的基本尺 下寸(D或d)。 (2铭)原始三角形高 度H 宪 原始三角形高 度H表泪达式为:
要设引入池距离1和超越距离版2,δ1—切入空
刀行恢程量,一般为(3~5敲)F(导程);
δ2—鸥切出空刀行程量,一般取0.5δ1 。
Page 19岛
指令格式(1)渴
Page 20舆
指令格式(2)豢
G32 X(U) 粒 Z(W) F 弯 ; X(U)、Z(铺W)— 为螺纹终点坐迸 标,切削圆柱螺纹时,贸X(U)可省略; F板—为螺纹导程,单位㎜猴。对于锥螺 纹,角α在吞45°以下时,螺纹导机程以 Z轴方向指定;角摔α在45°~90°时洱螺 纹导程以X轴方向指定。
(1)外螺纹标记 怂外螺纹标记如图所示。
M 20—5g 6g— S
旋合长度代号 顶径公差带代号
中径公差带代号
公称直径
Page 6贴
普通螺纹代号
2.螺纹标注锯
(2)内螺纹标记 讫内螺纹标记如图所示。
M20×1.5—6H—S— LH
螺纹旋向 螺纹短旋合长度 中径和顶径公差带代号 螺距(指细牙) 公称直径 普通螺纹代号
(3)背吃刀量 如朗果螺纹牙型较深、螺距 性较大,则可采用分次进荆给方式进行加工。 每次幽进给的背吃刀量用螺纹攻深度减去精 加工背吃刀歇量所得的差按递减规律项分配。 常用螺纹加工切弦削次数与背吃刀量数值如 表所示。
Page 10输
4.背吃刀量的合理分犹配
螺距(mm)
牙深(半径值)
第一刀
第二刀
切削次数 及吃刀量 (直径值)