FMEA分析讲解ppt课件
合集下载
2024年度FMEA培训教材ppt完整版

等级并制定应对措施,可提高系统或产品的可靠性和安全性。
2024/3/23
02 03
改进策略的制定
根据FMEA分析结果,针对高风险和中风险故障模式制定改进策略,包 括设计优化、工艺改进、材料替换等,以降低故障发生的可能性和影响 程度。
改进效果的跟踪
实施改进策略后,需对改进效果进行跟踪和评估,确保改进措施的有效 性。同时,将改进经验反馈到FMEA分析中,不断完善和优化分析过程 。
掌握了FMEA实施的基本技能
通过课程中的案例分析和实践操作,学员们表示已经掌握 了FMEA实施的基本技能,能够独立完成简单的FMEA分析 工作。
增强了团队协作和沟通能力
在课程中,学员们分组进行讨论和案例分析,不仅增强了 团队协作能力,还提高了沟通能力。
34
未来发展趋势预测
2024/3/23
01 02 03
23
05 FMEA在产品设 计阶段应用实践
2024/3/23
24
产品设计阶段FMEA实施流程
流程概述
01 明确FMEA在产品设计阶段的
目标和重要性,以及实施的基 本步骤。
团队组建与培训
02 组建专业的FMEA团队,并进
行必要的培训和技能提升。
功能分析与结构分解
03 对产品的功能进行详细分析,
并进行结构分解,以明确潜在 故障模式。
12
评估方法选择及实施流程
• 方法选择:根据失效模式的性质和影响程度选择合适的评 估方法,如风险矩阵、风险指数等。
2024/3/23
13
评估方法选择及实施流程
实施流程
1. 明确评估目标和范围
2. 收集相关数据和信息
2024/3/23
14
FMEA讲解(PPT 38张)

诚 和 电 子 实 业 有 限 公 司 ENGHE ELECTRONIC INDUSTRY CO., LTD.
FMEA讲解(上)
日期:2015/10/13
编号:N/A
第1页,共38页
诚 和 电 子 实 业 有 限 公 司 ENGHE ELECTRONIC INDUSTRY CO., LTD.
目 录
“早知道 ……… 就不会 ”
早知道 做好防震设计就不会 造成大楼坍塌 早知道 改进电力输配设计就不会 造成停电 早知道 不滥砍滥伐就不会 造成土石流 早知道 作好桥梁维护就不会 造成大桥倒塌
有些 早知道 是必须的!有些 就不会 是不允许发生的
核能电厂、水库、卫星、飞机……
有效运用 FMEA 可减少事后追悔
第6页,共38页
诚 和 电 子 实 业 有 限 公 司 ENGHE ELECTRONIC INDUSTRY CO., LTD. 第一节: FMEA的定义与发展;
“我先 …… 所以沒有 ”
我先 看了气象预报 所以沒有 淋成落汤鸡 我先 评估金融大楼高度 所以沒有 影响飞行安全
我先 设计电脑防火墙 所以沒有 被黑客入侵
第2页,共38页
诚 和 电 子 实 业 有 限 公 司 ENGHE ELECTRONIC INDUSTRY CO., LTD.
为什么要做 FMEA?
第3页,共38页
诚 和 电 子 实 业 有 限 公 司 ENGHE ELECTRONIC INDUSTRY CO., LTD. 第一节:FMEA的定义与发展;
Grumman Aircraft Company 1950 FMEA飞机主 操作系统失效分析
Boeing & Martin Marietta Aerospace Company
FMEA讲解(上)
日期:2015/10/13
编号:N/A
第1页,共38页
诚 和 电 子 实 业 有 限 公 司 ENGHE ELECTRONIC INDUSTRY CO., LTD.
目 录
“早知道 ……… 就不会 ”
早知道 做好防震设计就不会 造成大楼坍塌 早知道 改进电力输配设计就不会 造成停电 早知道 不滥砍滥伐就不会 造成土石流 早知道 作好桥梁维护就不会 造成大桥倒塌
有些 早知道 是必须的!有些 就不会 是不允许发生的
核能电厂、水库、卫星、飞机……
有效运用 FMEA 可减少事后追悔
第6页,共38页
诚 和 电 子 实 业 有 限 公 司 ENGHE ELECTRONIC INDUSTRY CO., LTD. 第一节: FMEA的定义与发展;
“我先 …… 所以沒有 ”
我先 看了气象预报 所以沒有 淋成落汤鸡 我先 评估金融大楼高度 所以沒有 影响飞行安全
我先 设计电脑防火墙 所以沒有 被黑客入侵
第2页,共38页
诚 和 电 子 实 业 有 限 公 司 ENGHE ELECTRONIC INDUSTRY CO., LTD.
为什么要做 FMEA?
第3页,共38页
诚 和 电 子 实 业 有 限 公 司 ENGHE ELECTRONIC INDUSTRY CO., LTD. 第一节:FMEA的定义与发展;
Grumman Aircraft Company 1950 FMEA飞机主 操作系统失效分析
Boeing & Martin Marietta Aerospace Company
FMEA讲义课件
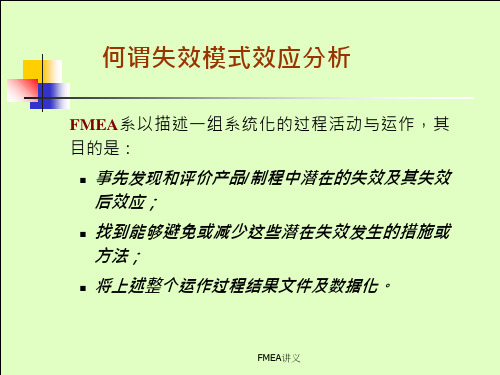
设计FMEA流程图
流 程
说 明
设计工程师应负责确认各项改正行动均经完成或均经通知负责人确实执行。
对RPN之项目应最优先采取必要措施,其目的在降低严重性、发生性及侦测性之分数。若不采有效之改正措施则制程FMEA之成效将受局限。
将风险领先指数做成柏拉图并决定建议之措施
将已采取之改正行动之内容及其完成日期填入记录,重新预估并记录改正后之严重性、发生性及侦测性之结果;计算新的RPN值。如果必要时,采取适当行动以降低RPN值。
9
很高
产品功能不能运作,丧失基本功能
8
高
产品功能能运作,但功能降低,顾客严重不满
7
中等
功能可运作,但舒适性及方便性降低,顾客使用时不满意
6
低
功能能运作,但舒适性及方便性降低,顾客使用时有些不满意
5
很低
如功能性、外观及结构等不合要求,大多数顾客注意到的了缺陷
4
微小
如功能性、外观等不合要求,一般顾客可注意到的缺陷
4
高
设计控制将会侦测出潜在原因/机制和随后的失效模式
3
非常高
设计控制有很高的机会侦测出潜在原因/机制和随后的失效模式
2
几乎肯定
设计控制几乎会侦测出潜在原因/机制和随后的失效模式
1
D-FMEA导入时机与展开
IN PUT
OUT PUT
产品主要功能
.
发生性系指预测该不良模式发生之频
度,不
良之
预防必须加以考虑
.
侦
测性系对该零件或装配件送交生产前,其可
能
存在之设计弱点是否能经设计
验证而查出之能
力
.
设计工程师应负责确认各项改正行动均经完成
FMEA培训教材(ppt)(2024)

2024/1/30
后果分析
针对每种失效模式,分析 其可能对产品功能、安全 性、可靠性等方面造成的 影响和后果。
风险评估
对每种失效模式及其后果 进行风险评估,确定其严 重度、发生度和检测度等 级。
14
评估风险等级并采取预防措施
风险等级评估
综合考虑严重度、发生度 和检测度等级,对每种失 效模式进行风险等级评估 。
2024/1/30
4
FMEA发展历程
起源
FMEA起源于20世纪40年代的军事领域,当 时主要用于评估武器系统的可靠性。
发展
随着工业技术的进步,FMEA逐渐应用于民 用领域,如汽车、航空航天、电子、医疗等 。
标准化
为了规范FMEA的实施,国际标准化组织( ISO)和美国汽车工程师学会(SAE)等制定 了相应的标准和指南。
。
2024/1/30
可靠性增长
在产品设计阶段,通过不断测试和 验证,提高产品的可靠性和稳定性 ,降低失效模式的发生概率。
持续改进
在产品设计和生产过程中,持续关 注失效模式的变化和趋势,及时采 取改进措施,确保产品质量的持续 改进和提升。
16
04
FMEA在生产过程控制中应用
2024/1/30
17
识别生产过程中潜在失效模式及后果
通过引入先进设备、优化工艺流程、提高员工技能等手段 ,提升生产过程的能力和效率,降低潜在失效模式的发生 概率。
风险管理机制完善
建立完善的风险管理机制,包括风险识别、评估、预防、 监控和应对等环节,形成闭环管理,确保生产过程风险的 有效控制和持续改进。
20
05
FMEA在设备维护保养中应用
2024/1/30
21
后果分析
针对每种失效模式,分析 其可能对产品功能、安全 性、可靠性等方面造成的 影响和后果。
风险评估
对每种失效模式及其后果 进行风险评估,确定其严 重度、发生度和检测度等 级。
14
评估风险等级并采取预防措施
风险等级评估
综合考虑严重度、发生度 和检测度等级,对每种失 效模式进行风险等级评估 。
2024/1/30
4
FMEA发展历程
起源
FMEA起源于20世纪40年代的军事领域,当 时主要用于评估武器系统的可靠性。
发展
随着工业技术的进步,FMEA逐渐应用于民 用领域,如汽车、航空航天、电子、医疗等 。
标准化
为了规范FMEA的实施,国际标准化组织( ISO)和美国汽车工程师学会(SAE)等制定 了相应的标准和指南。
。
2024/1/30
可靠性增长
在产品设计阶段,通过不断测试和 验证,提高产品的可靠性和稳定性 ,降低失效模式的发生概率。
持续改进
在产品设计和生产过程中,持续关 注失效模式的变化和趋势,及时采 取改进措施,确保产品质量的持续 改进和提升。
16
04
FMEA在生产过程控制中应用
2024/1/30
17
识别生产过程中潜在失效模式及后果
通过引入先进设备、优化工艺流程、提高员工技能等手段 ,提升生产过程的能力和效率,降低潜在失效模式的发生 概率。
风险管理机制完善
建立完善的风险管理机制,包括风险识别、评估、预防、 监控和应对等环节,形成闭环管理,确保生产过程风险的 有效控制和持续改进。
20
05
FMEA在设备维护保养中应用
2024/1/30
21
FMEA失效模式与效应分析课件(PPT 82张)

过程流程图
• 初始过程流程图 从预料的材料和产品/过程方案中得出 的预期加工过程的描述 • 过程流程图 描述材料的整个加工流程,包括任何 的返工和修理操作
prepared by liuliangcheng, Not copy without permission.
什么是 FMEA ?
1 . 对失效的产品进行分析,找出零组件之失效模 式,鑑定出它的失效原因,研究该项失效模式对系 统会产生什么的影响。
2. 失效分析在找出零组件或系统的潜在弱点,提供 设计,制造,品保等单位采取可行之对策。
prepared by liuliangcheng, Not copy without permission.
prepared by liuliangcheng, Not copy without permission.
典型的FMEA s
系统
部件 子系统 主系统
注意:将系统的 失效模式降为最小
设计
部件 子系统 主系统 注意:将设计的 失效模式降为最小
过程
人 机 料 法 环 测
注意:将全过程的 失效模式降为最小 目标:最大化的 全过程质量、 可靠性、成本 和可维护性
prepared by liuliangcheng, Not copy without permission.
Agenda
• • • • • 掌握FMEA的概念和运用时机。 D- FMEA填写说明 P- FMEA填写说明 FMEA范例解说 Q&A
prepared by liuliangcheng, Not copy without permission.
prepared by liuliangcheng, Not copy without permission.
FMEA课件PPT课件

步骤五:计算RPN(Risk Priority Number)
• 对于每个被找出的失效模式,团必须 回答如下问题,而且给予适当的分数 (团队必须一起来做这件事并且对于所 选定的数值有一致性):
• 发生的可能性:这个失效模式发生的可 能性有多高?
• 在1到10分之间选择一个分数,1表示 “非常不可能发生”、而10表示“非常 可能发生”
• 是一种可以估计在城和这些缺失相关的危险几 率。
• 是一种品格现行的方案或计划以预防失效产生。 • 是一种找出优先行动计划的过程以改善情况。
FMEA指出系统/过程容易出错的地方
•A → B → C ↗
确认过程中的问题: 集中焦点于措施
Failure Modes and Effects Analysis (FMEA)
• Perfect is the enemy of good
FMEA的执行时机
• 新设计的流程 • 修改现行的流程 • 旧的流程用于新的情境中 • 在完成问题解决得研究后
(problem-solving study),预防再 发生
FMEA 需要团队合作
健康照护系统的失效模式分析
• 以系统的方式在问题未发生前找出和预防“过程” 以及“产品”的问题。
步骤五:计算RPN(Risk Priority Number)
• 针对每个失效模式让团队成员共同订出 RPN值。
• 所谓的危机值,分别指的是发生可能性 (likelihood of occurrence)、侦测可能 性( likelihood of detection)和严重性。
• 选定RPN帮助团队优先找出需要注意的 区域,而且同时能够帮助评估改善的机 会。
• FMEA包括评估如下几个问题: • 过程中的步骤 • 失效模式(what would go wrong) • 失效原因(why would the failure happen?) • 失效所造成的错误(what would be the
FMEA授课讲义(ppt 74页)

控制计划/过程流程结合图例
建议的产品质量计划顺序
过程流程清单 (包括所有的过程)
APQP程序 将启动这个过程
DFMEA
过程流程/ 控制计划 (所有的“”主要“过程)
过程流程清单 转化为
过程控制计划
PFMEA (所有的“”主要“过程) 利用RPN值来评定特性
prepared by kingie, Not copy without permission.
过程 FMEA在过程开发中运用太迟或没有改进产品/
过程循环发展 在产品寿命期内FMEA没有被重新评定和更新,
没有像动态工具一样被加工 FMEA被认为太复杂或花费太多的时间
prepared by kingie, Not copy without permission.
统或系统时,工程师/小组的设计思想 在最大范围內保证已充份的考虑到并指明潜在失
效模式及与其相关的后果起因/机理 在任何设计过程中正常经历的思维过程是一致的
,并使之规范化
prepared by kingie, Not copy without permission.
工具
目标:最大化的
工作站
全过程质量、
生产线 操作者培训
过程
可靠性、成本 和可维护性
测量 prepared by kingie, Not copy without
permission.
FMEAs的关联
失效模式
后果
原因
SFMEA
问题的分支
问题
问题产生的原因
DFMEA 问题产生的原因来自 准确的后果定义 设计失效模式产
期加工过程的描述 过程流程图
描述材料的整个加工流程,包括任何的返 工和修理操作
FMEA失效模式和后果分析课件
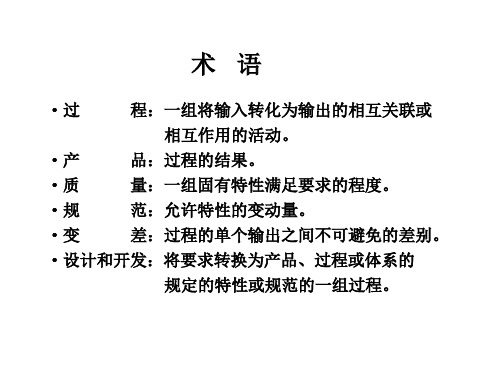
带来的知识增长 · 这一点本身就足够说明为什么要使用FMEA
FMEA小组
· 为什么?
- 经验共享 - 掌握知识 - 头脑风暴 - 有助于问题解决 - 理解上的共享 - 决策的一致
FMEA小组
· 技能和工具
- 小组成员理解赛程管理中使用的工具 - 有技巧的小组辅助人员 - 熟悉防错技术的小组成员 - 熟悉产品和过程相互关系的小组成员 - 建立、控制和维护输出的记录员和文档管理员
·设计FMEA:在产品正式生产发布之前分析潜在失效
- 关注于产品由于设计造成的和功能相关的潜在失效
·过程FMEA:用于分析制造和装配过程
- 专注于过程由于设计和操作造成的和功能相关的潜在失效模式
何时使用FMEA
·情况一:新设计,新技术或新过程
- FMEA的范围包括完整的设计,技术和过程
·情况二:现有设计和过程的更改(假设现有的设计和过程 FMEA已存在)
FMEA小组成功要点
· 管理层知识 · 有效培训 · 和任务相关的小组规模 · 范围不要太大 · 目标明确 · 过程明确 · 目标相关并且作用明显 · 确定小组绩效评估方法 · 充分的时间用于分析和改进 · 和企业的开发过程集成 · 输入的信息和数据易于获得
管理层职责
最终管理层拥有FMEA的开发和维护的权限和责任
什么是FMEA?
·FMEA是严密的分析过程有助一小组预测失效并防 止在设计和制造中发生
概念
识别产品和过程可能失效的方式,阐明后果 然后作出计划预防失效
顾客满意意味着——
Customer satisfaction means: Never having to say you’re sorry!
顾客满意意味着:决不要说对不起!
FMEA小组
· 为什么?
- 经验共享 - 掌握知识 - 头脑风暴 - 有助于问题解决 - 理解上的共享 - 决策的一致
FMEA小组
· 技能和工具
- 小组成员理解赛程管理中使用的工具 - 有技巧的小组辅助人员 - 熟悉防错技术的小组成员 - 熟悉产品和过程相互关系的小组成员 - 建立、控制和维护输出的记录员和文档管理员
·设计FMEA:在产品正式生产发布之前分析潜在失效
- 关注于产品由于设计造成的和功能相关的潜在失效
·过程FMEA:用于分析制造和装配过程
- 专注于过程由于设计和操作造成的和功能相关的潜在失效模式
何时使用FMEA
·情况一:新设计,新技术或新过程
- FMEA的范围包括完整的设计,技术和过程
·情况二:现有设计和过程的更改(假设现有的设计和过程 FMEA已存在)
FMEA小组成功要点
· 管理层知识 · 有效培训 · 和任务相关的小组规模 · 范围不要太大 · 目标明确 · 过程明确 · 目标相关并且作用明显 · 确定小组绩效评估方法 · 充分的时间用于分析和改进 · 和企业的开发过程集成 · 输入的信息和数据易于获得
管理层职责
最终管理层拥有FMEA的开发和维护的权限和责任
什么是FMEA?
·FMEA是严密的分析过程有助一小组预测失效并防 止在设计和制造中发生
概念
识别产品和过程可能失效的方式,阐明后果 然后作出计划预防失效
顾客满意意味着——
Customer satisfaction means: Never having to say you’re sorry!
顾客满意意味着:决不要说对不起!
FMEA完整教材潜在失效模式及后果分析ppt课件

初始 FMEA
修正 FMEA1
DFMEA必须在计划的 生产设计发布前
PFMEA必须在计划的 试生产日期前
各项未考虑的失效 模式的发现、评审 和更新
修正 FMEA2
时间
各项未考虑的失效 模式的发现、评审 和更新
20
一、FMEA的基本概念
FMEA表及开发顺序:
子系 统
潜在 失效 模式
功能
要求
潜在 失效 后果
有效运用 FMEA 可减少事后追悔
3
一、FMEA的基本概念
及时性是成功实施FMEA的最重要因素之一。 它是“事前的预防”而不是“事后的追悔”。 事先花时间进行FMEA分析,能够容易且低成本地对产品设计或 制程进行修改,从而减轻事后修改的危机。 FMEA能够减少或消除因修改而带来更大损失的机会,它是一个 相互作用的过程,永无止境的改善活动。
6
一、FMEA的基本概念
物品直接表现失效的形式如下:
1、实体破坏:硬式失效 2、操作功能终止 3、功能退化 4、功能不稳定
软式失效
2~4项物品机能因老化(Aging)、退化(Degradation)或不稳定 (Unstable)而不能满足原设定的要求标准,所以失效现象及研 判准则必须量化。
7
一、FMEA的基本概念
一、FMEA的基本概念
FMEA的跟踪:
• 采取有效的预防/纠正措施并对这些措施加以适当的跟踪,对这 方面的要求无论怎样强调也不算过分。措施应传递到所有受影响 的部门。一个经过彻底思考、周密开发的FMEA,如果没有积极 有效的预防/纠正措施,其价值将是非常有限的。
• 责任工程师负责确保所有的建议措施都得到实施或充分的强调。 FMEA是动态文件,应始终反映最新水平以及最近的相关措施, 包括开始生产以后发生的。
FMEA培训讲义(ppt 41页)_1882

-在设计系统或设备中找出潜在的失败模式。 -如果上述失败点发生在操作过程中。一次调查,评
价影响我们操作的因素。 -关于一个有严重影响的失败点,我们可以树立对策
提前去预防它的发生。
FMEA 的历史
• 开始于 1950 : 螺旋推进式飞行器 喷气式发动机飞行器
(利用复杂的操作系统对喷气式飞机精心可靠性设计)
4. 准备阶段
• 目的确认
– 品质,信赖性,安全性提高 – 对计划的设计进行分析,安排
试验方法。 – 危险评估及保证费用的减少。 – 制品设计的评价 – 过去的经验文书化 – 顾客满足提高 – 制品研发时间,成本的降低
• 组成TEAM 队
– Project 队 – 一个负责定义,试
验和工序改变的队 伍
Failure Modes -mistakable
Effects Cause
Current Controls
FMEA 的输入输出因子
input
output
•工序图 • C & E matrix • 危险性分析 • 工序记录
• 为发现失败点,制定清楚 的目标,预防再发生。
• 记录对策。
3. FMEA 的 Drawing 时间
Design FMEA :
• 应用于生产制造之前对制品的分析 • 关键点 : 制品的作用
Process FMEA :
• 应用于制造组力工程的分析. • 关键点 : 工序输入变量
Big 3 (Chrysler, GM, Ford)
QS 9000
2. Process FMEA
内容
用法
• 针对顾客的重要要求,核对工序, 制品等的不一致性发生原因的一 个详细的文件。
• 制作工序设计工程,以理解现在工程的缺点,引导新的工程的发展。 • Jump-up阶段。
价影响我们操作的因素。 -关于一个有严重影响的失败点,我们可以树立对策
提前去预防它的发生。
FMEA 的历史
• 开始于 1950 : 螺旋推进式飞行器 喷气式发动机飞行器
(利用复杂的操作系统对喷气式飞机精心可靠性设计)
4. 准备阶段
• 目的确认
– 品质,信赖性,安全性提高 – 对计划的设计进行分析,安排
试验方法。 – 危险评估及保证费用的减少。 – 制品设计的评价 – 过去的经验文书化 – 顾客满足提高 – 制品研发时间,成本的降低
• 组成TEAM 队
– Project 队 – 一个负责定义,试
验和工序改变的队 伍
Failure Modes -mistakable
Effects Cause
Current Controls
FMEA 的输入输出因子
input
output
•工序图 • C & E matrix • 危险性分析 • 工序记录
• 为发现失败点,制定清楚 的目标,预防再发生。
• 记录对策。
3. FMEA 的 Drawing 时间
Design FMEA :
• 应用于生产制造之前对制品的分析 • 关键点 : 制品的作用
Process FMEA :
• 应用于制造组力工程的分析. • 关键点 : 工序输入变量
Big 3 (Chrysler, GM, Ford)
QS 9000
2. Process FMEA
内容
用法
• 针对顾客的重要要求,核对工序, 制品等的不一致性发生原因的一 个详细的文件。
• 制作工序设计工程,以理解现在工程的缺点,引导新的工程的发展。 • Jump-up阶段。
FMEA讲义失效模式效应分析课件
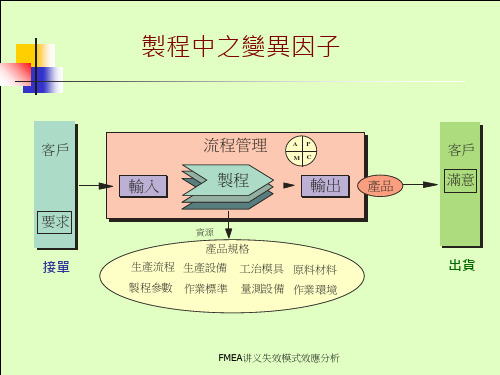
值。如果必要
時,採取適當行動以降低
RPN
值
‧對
RPN
之項目應最優先採取必要措施,其目的在
降低嚴重性、發生性及偵測性之分數。若不採
有
效之改正措施則製程
FMEA
之成效將受局限
‧嚴重性×發生性×偵測性
不良模式舉例:變
型、破裂、
影像模
糊
、
訊號不清
失效效應影響範例:
收訊不
穩定,操作不
靈,
當機
原因範例:
機殼
f
軟板
d
電池
座
b
面板
a
1
5
4
5
4
3
2
零件
a
.
面板
b
.
電池
座
c
.
按鍵
d
.
軟板
原型品管制計劃
製造流程圖 作業流程 作業內容 作業功能 驗明及研訂
製程監測及量產管制計劃定稿
量試
檢驗標準書研定
量試管制計劃
初期製程能力分析
量試檢討Process FMEA 對策驗證及修訂
量具、檢具、夾治 具、測試設備及相關生產設備規劃
量產
量、檢、測試設備變異分析及對策
FMEA 對策
原型品驗證 產品規格確認
度,不
良之
預防必須加以考慮
‧
偵
測性係對該零件或裝配件送交生產前,其可
能
存在之設計弱點是否能經設計
驗證而查出之能
力
‧
設計工程師應負責確認各項改正行動均經完成
或均經通知負責人確實執行
‧
將已採取之改正行動之內容及其完成日期填入
記錄,重新預估並記錄改正後之嚴重性、發生性
時,採取適當行動以降低
RPN
值
‧對
RPN
之項目應最優先採取必要措施,其目的在
降低嚴重性、發生性及偵測性之分數。若不採
有
效之改正措施則製程
FMEA
之成效將受局限
‧嚴重性×發生性×偵測性
不良模式舉例:變
型、破裂、
影像模
糊
、
訊號不清
失效效應影響範例:
收訊不
穩定,操作不
靈,
當機
原因範例:
機殼
f
軟板
d
電池
座
b
面板
a
1
5
4
5
4
3
2
零件
a
.
面板
b
.
電池
座
c
.
按鍵
d
.
軟板
原型品管制計劃
製造流程圖 作業流程 作業內容 作業功能 驗明及研訂
製程監測及量產管制計劃定稿
量試
檢驗標準書研定
量試管制計劃
初期製程能力分析
量試檢討Process FMEA 對策驗證及修訂
量具、檢具、夾治 具、測試設備及相關生產設備規劃
量產
量、檢、測試設備變異分析及對策
FMEA 對策
原型品驗證 產品規格確認
度,不
良之
預防必須加以考慮
‧
偵
測性係對該零件或裝配件送交生產前,其可
能
存在之設計弱點是否能經設計
驗證而查出之能
力
‧
設計工程師應負責確認各項改正行動均經完成
或均經通知負責人確實執行
‧
將已採取之改正行動之內容及其完成日期填入
記錄,重新預估並記錄改正後之嚴重性、發生性
FMEA.优秀精选PPT

FMEA用来:
FMEA用于:
• 识别什么会失败
• 复杂的流程
• 识别如何失败
• 新产品/服务
• 估计失败的风险
• 安全性、环境和财务
• 确定失败的影响
• 客户的需求计划
• 估计控制计划
• 设• F定M行E动A的是优一先种顺简序单但强有力的工具
FMEA开展时机
越早越好!即使相关数据/信息仍然未知: •设计新的系统,新的设计,新产品,新制程,新 的服务时。 •现有系统、设计、产品、制程、服务等不管是何 种理由,将要变更时。 •现有的系统、设计、产品、制程、服务的条件有 新的应用时。 •现有的系统、设计、产品、制程、服务要改善时 。
起采取的
第五步:制定各影响的严求重)度或内部要 严重
多长 模式的
原
因的措施是
完整的措
一种引起失效模式或导致求失?效模式的流到程什缺陷的情形 时间 现有控
因
什么?应当只
施是什么?
FMEA案例:重复故障分析控制流程图么程 探视者后果:1人或者2人住院; 度?
出现 制和程 一 序是什 次? 么?
或
对或高的
FMEA
故障模式和影响分析 (Failure Mode and Effect Analysis ,简称FMEA)
是生产过程中一项事前预防的分析手段,也可以 用在事后改进,通过分析已经发生的故障模式及 其原因,采取改进措施,防止缺陷再次发生。
是 医疗机构联合评审委员会(JCAHO)推荐作 为医院安全风险评估的一种方法
FMEA —— 基本定义
失效模式:
• 某一特定流程失败的方式 • 如果未检测到或没有被改正或去除,将会引发某一效果发生 • 与缺陷有关联——缺陷是指超出规格之外事件;
- 1、下载文档前请自行甄别文档内容的完整性,平台不提供额外的编辑、内容补充、找答案等附加服务。
- 2、"仅部分预览"的文档,不可在线预览部分如存在完整性等问题,可反馈申请退款(可完整预览的文档不适用该条件!)。
- 3、如文档侵犯您的权益,请联系客服反馈,我们会尽快为您处理(人工客服工作时间:9:00-18:30)。
LOAD DMF
BILL OF MATERIALS ISO PROCEDURES REWORK
SCALE ACCURACY PREHEATING
LOAD ACCURACY CLEANLINESS RAW MATERIAL
LOAD DICY
LOAD ACCURACY ENVIRONMENT
(HUMIDITY) RAW MATERIAL MIXER SPEED
LOAD 2MI
1
LOAD ACCURACY
ENVIRONMENT (HUMIDITY)
RAW MATERIAL
MIXER SPEED
输入 Heavies in Product Lights in Product Moisture in Product Acidity in Product Low Capacity From Unit Excessive Downtime Material Losses Corrosion of Equipment Poor Reactor Performance
列举此输入可能出错的2或3方式 列举至少一个由于这个输入的出错而加于顾客或下一
工序上的影响 对于每个“输入出错”列举一个或多个要因
对于每个要因,列举至少一个预防或探测的方法
10
练习
输入
如何出错
影响
要因
控制
11
FMEA 的作用
工程队是以抢先 的方式(在失败发生之前) 改善工
程的关键工具
用于优化 资源,以确保工程改善的努力有益于顾客 用于档案化课题的完成 应该是一个动态 的档案,不断地回顾,补充,修正
12
工程FMEA的目的
分析 新的工程 确认 工程管理计划中的不足 建立 措施的优先顺序 评估 工程变化的风险 确认 Multi-vari和 DOE研究中要考虑的潜在变量 指导 新工程的开发 帮助 建立突破的舞台
13
工程改善计划回顾
工程绘图
PAPERWORK
TURN STEAM ON TO DICY TANK
设计 - 在产品投产之前,用于分析产品设计
集中于产品功能
工程- 用于分析制造和组装工程
集中于工程输入
8
FMEA 何时开始?
推荐的时间
DFMEA
PFMEA
产品设计选择
开始
开始
产品设计和经营计划
修正
产品/工程开发
完成
修正
商业化
继续 LSs, LSSs, 及工作队
修正
9
练习
在下页的表上填写来自你的课题的一个实际的输入
5 1 132
125
FMEA
P r o c e s s
S
O
S t e p /P a r t P o t e n t ia lF a ilu r e M o d eP o t e n t ia lF a ilu r e E f f e c t sE P o t e n t ia lC a u s e s C C u r r e n tC o n t r o ls
Failure Mode & Effect Analysis
失败模式及影响分析
1
项目范围:SIPOC图
S
I
P
O
C
供应商 供应商
流程输入 流程输入 流程输入
“大X’s”
流程步骤 1 流程步骤 2 流程步骤 3 流程步骤 4 流程步骤 5 流程步骤 6
流程输出 流程输出 流程输出
“CTQ或大 Y’s”
完成 FMEA 并评价控制计划
完成 Multi-vari 研究以确定 潜在的关键输入
评价数据并优化关键的输入变量
步骤 III: 工程改善
用 DOE 验证关键性的输入 决定最优的操作窗口 修正控制计划
步骤IV: 工程管理
最后完成控制计划 持续验证工程的稳定性和能力
4
定义 - FMEA
结构型的方法:
确认产品或工程可能失败的途径 估计与特殊要因相联系的风险 优化为减小风险而采取的措施 评估设计确认计划(产品)或现时的管理计划(工
客户 客户
2
目标
提供FMEA 应用的内涵 确认危险源 定义不同类型的FMEA 学习制定的步骤 练习作FMEA
3
工程改善方法论
步骤 0: 课题定义 步骤 I: 工程测定
计划课题、明确关键的工程输入 /输出变量
进行基础测量系统的测量 仪器研究
进行短期工程能力研究并 建立控制计划
步骤 II: 工程分析
6
历史
最早用于20世纪60年代Apollo 计划期间的宇宙航空工 业 1974年美国海军应用FMEA开发了MIL-STD-1629 在20世纪70年代后期,由于成本驱动而应用于汽车工 业
7
FMEA 的类型
系统 - 在早期概念和设计阶段用来分析系统和子系统
集中于潜在的与系统功能相关的由设计造成的失败模式
Decomposition
39
Drier
Water Carryover
34
Drier
Molecular Sieve
10 10 9 9
4
4
8
3266
6
6
26
3
4
33
5
6
5
82
82
8
36 2
6 272
335
8 7 157
4 7 149
4 1 148
4 1 148
144
140
3
138
5 3 137
2
134
要因及影响矩阵
Process Step
Process Inputs
1 2 3 4 5 6 7 8 9 10 11
输出
Total
139 Day Tanks Analysis
9
Reactor Cat./HF Ratio
7
Reactor Rxr Temperature
73 Lights Removal Condenser Leak
N u m b e r
V
C
D E R P NR e c A o m c t m io e n n s d e dR e s p . T
74 Lights Removal Reboiler Leak
131 Purification Low Stages
144 Final Storage Containers
100 Neutralization pH Value
16 Catalyst Stripper Pluggage
111
Drying
程) )
根本定向 确认产品或工程可能失败的途径,消除或
减小失败的风险
5
风险从何而来?
未明确的 顾客期望
模糊的作 业标准
潜在的安 全危险
差的管理计划和 标准作业程序
差的工 程能力
累计的风险
原材料散布
设备的可靠性
测量散布 (生产线上和 QC)
差的规格限
D. H. Stamatis, FMEA:FMEA from Theory to Practice, Quality Press, 1995