DFMEA报告
DFMEA失效模式分析报告-案例

DFMEA失效模式分析报告-案例1. 引言本文档旨在提供针对某一特定产品的DFMEA(设计失效模式及影响分析)报告。
该报告基于针对该产品的失效模式分析的结果,旨在识别和评估潜在的设计失效模式及其潜在影响。
2. 背景信息产品名称:(产品名称)产品型号:(产品型号)报告日期:(报告日期)3. 方法论在分析失效模式之前,我们采用以下方法进行了系统的DFMEA分析:1. 收集产品设计文档和相关技术资料;2. 召开团队会议,对产品进行全面的功能分析;3. 根据功能分析,确定可能存在的失效模式;4. 对每个失效模式进行评估,包括严重程度、频率和发现难度的评估;5. 提出各种可能的故障根本原因;6. 提出相应的纠正措施和预防措施,以减轻潜在的失效模式对产品造成的影响。
4. 失效模式分析及评估在DFMEA分析中,我们发现以下潜在的失效模式及其评估结果:4.1 失效模式1- 描述:(失效模式1的详细描述)- 严重程度:(对产品的影响程度评估,如高、中、低)- 频率:(失效模式发生的频率评估,如高、中、低)- 发现难度:(失效模式的可发现程度评估,如高、中、低)- 根本原因:(该失效模式发生的可能原因)4.1.1 纠正措施- 描述:(纠正该失效模式的措施)4.1.2 预防措施- 描述:(预防该失效模式的措施)4.2 失效模式2- 描述:(失效模式2的详细描述)- 严重程度:(对产品的影响程度评估,如高、中、低)- 频率:(失效模式发生的频率评估,如高、中、低)- 发现难度:(失效模式的可发现程度评估,如高、中、低)- 根本原因:(该失效模式发生的可能原因)4.2.1 纠正措施- 描述:(纠正该失效模式的措施)4.2.2 预防措施- 描述:(预防该失效模式的措施)......5. 结论本报告中,我们对产品的失效模式进行了深入的分析和评估。
通过识别各个失效模式并提出相应的纠正和预防措施,我们能够最大程度地减少潜在的设计失效,并提升产品的质量和可靠性。
DFMEA失效模式分析报告-范本

DFMEA失效模式分析报告-范本1. 引言本报告旨在对产品的DFMEA(Design Failure Mode and Effects Analysis,设计失效模式与影响分析)进行详细分析和评估。
通过DFMEA,我们可以识别潜在的设计问题,并采取相应的改进措施,以确保产品的可靠性和质量。
本范本报告将为您提供一个参考,以便在进行具体的DFMEA分析时提供方向和指导。
2. 设计失效模式与影响分析DFMEA是一种系统化的方法,用于根据设计和工程知识,识别并评估可能的失效模式及其对产品质量和性能的影响。
以下是DFMEA分析的步骤和关键要素:2.1 分析步骤1. 确定分析的设计元素或子系统。
2. 列出可能的失效模式。
3. 对每个失效模式进行评估,包括失效原因、失效对系统功能的影响和失效对其他部件的影响。
4. 根据评估结果,确定和优先级排序失效模式。
2.2 关键要素在DFMEA分析中,以下要素需要特别关注:1. 设计元素:将设计分解为适当的子系统或元素,以便更好地进行分析和识别失效模式。
2. 失效模式:失效模式是指产品在设计元素或子系统中可能发生的故障或失效情况,需要针对每个设计元素列出所有可能的失效模式。
3. 失效原因:为每个失效模式确定可能的原因,例如材料问题、制造过程问题或设计缺陷等。
4. 影响评估:评估失效模式对系统功能和其他部件的影响,包括性能降低、功能丧失或安全风险等。
5. 排序:根据评估结果,对失效模式进行排序,以确定需要采取的优先改进措施。
3. 报告结论通过对产品进行DFMEA分析,我们可以识别潜在的失效模式并确定相应的改进措施。
这有助于减少设计风险,提高产品的可靠性和质量。
然而,请注意,本报告仅为范本,具体的DFMEA分析需要根据实际情况进行定制。
4. 参考资料[1] AIAG. (2019). Potential Failure Mode and Effects Analysis (FMEA) (4th ed.). AIAG.。
车辆白车身DFMEA分析范例

车身工程中心编制人:新严重度新频度新探测度新风险顺序数1零部件无法安装1车身数据未符合边界要求5按《白车身孔位描述书》和《零部件边界条件确认表》进行数据检查152车身无法焊装、车身运动干涉、车身异响、用户抱怨1三维数据检查未全面检查、运动校核未考虑实车精度、相关零部件未考虑到位5按《白车身自相关检查表》和《车身运动件运动校核检查表》进行数据校核6303整车外观效果差,无法满足客户需求,影响销售4设计间隙、面差不合理;装调不到位;公差分配不合理;定位方式设置不合理6参照相关车型合理设置DTS定义值,合理设置公差,合理设置定位方式6144数模校核,定位方案确定车身4增加模具费用,增加整车成本,影响利润1设计结构时未考虑后期开发车型的共用性5编制车身开发模块化说明,预先设计拓展车型结构方案6305零部件冲压起皱,翻边开裂,尖角争料,产品结构弱,易变形,尖角拉延破裂冲压负角,件拉延开裂,模具上修边刃口强度不足,影响车身性能5冲压SE分析未到位,钣金结构不合理4按《白车身SE审查报告》进行反馈及数模修改,合理设计钣金结构6120SE分析车身/制造6车身焊接操作性差,工人抱怨、生产率低,焊接效果差,影响车身性能5焊装SE分析未到位,钣金结构不合理4按《白车身SE审查报告》进行反馈及数模修改,合理设计钣金结构,合理布置焊点位置及层次2407车身电泳底漆厚度不均匀、部分区域未充分覆盖底漆、车身锈蚀、影响整车寿命5涂装SE分析未到位,钣金结构不合理4按《白车身SE审查报告》进行反馈及数模修改,合理设计钣金结构,保证涂装效果2408总装件无法安装;车身总装操作性差,工人抱怨、生产率低;零部件维修操作性差5总装SE分析未到位未分析可维修性4按《白车身SE审查报告》进行反馈及数模修改,合理设计钣金结构,合理考虑安装操作空间,进行安装虚拟验证2409影响用户乘车舒适性,影响内部载货空间,用户抱怨3未合理设计钣金结构,钣金侵占内部空间6进行CAE分析,在保证车身性能、安装结构的前提下尽量增大内部空间,可对比标杆设计7126初期确定目标值,后期按照执行,尽量加大内部空间车身/整车10影响用户乘车舒适性,影响内部装卸货方便性,用户抱怨3未合理设计钣金结构,未按人机要求设计6按人机要求设计数据,在保证车身性能、安装结构的前提下尽量改善,可对比标杆设计6108方案阶段确定各相关尺寸,保证后期数据满足要求。
DFMEA文件

DFMEA 的目的和重要性
目的
DFMEA的目的是通过提前识别和评估产品设计可能出现的故障模式,以及这些故障模式可能带来的 影响,进而采取相应的措施来预防或减轻这些故障模式的影响,以提高产品的质量和安全性。
产品设计的描述:包括产品的功能、用途、结构、 材料等。
故障模式的识别和评估:对产品设计可能出现 的故障模式进行识别和评估,包括故障模式的 原因、发生概率、影响程度等。
改进措施的制定:根据故障模式的评估结果, 制定相应的改进措施,包括设计改进、材料更 换、工艺优化等。
改进措施的实施和验证:对所制定的改进措施 进行实施和验证,以确保其有效性和可靠性。
DFMEA 文件
2023-11-07
目录
• 介绍 • 产品/过程特性分析 • 潜在失效模式分析 • 潜在失效影响分析 • 风险优先级分析 • DFMEA 结果输出 • DFMEA 实施案例分析
01
介绍
DFMEA 是什么
DFMEA,全称为Design Failure Mode and Effects Analysis,即设计故障模式和影响分析。
生产过程改进建议
针对生产过程中的高风险故障模式,提出生产过程改进建议,提 高产品质量和生产效率。
质量管理体系完善建议
根据分析结果,提出完善质量管理体系的建议,提高产品质量保 证能力。
07
DFMEA 实施案例分析
产品开发过程中的 DFMEA 应用案例
案例一
某汽车制造企业在新车型开发过程中应用 DFMEA,通过对设计、生产、使用等环节的分析,成功发现了10余项潜在质量问 题,并提前采取措施予以解决,有效避免了产品上市后可能出现的质量问题。
设计失效模式分析报告(DFMEA)

1. 目的确定与产品相关的设计过程潜在的失效模式,确定设计过程中失效的起因,确定减少失效发生或找出失效条件的过程控制变量并编制潜在失效模式分级表,为采取预防措施提供对策。
2. 适用范围本程序适用于新产品设计、产品设计变更时的样品试验阶段的FMEA分析。
3.职责3.1 项目组:负责设计潜在失效模式和后果分析的工作主导,DFMEA的制定;3.2 APQP跨功能小组:负责设计失效模式和后果分析(DFMEA)结果的评估;3.3 各职能部门:负责各失效模式和后果分析相关工作配合和对策的实施;3.4 管理者代表:负责设计失效模式和后果分析(DFMEA)结果的批准。
4.定义4.1 DFMEA:设计潜在失效模式和后果分析(Design Failure Mode and Effecting Analysis)是指设计人员采用的一门分析技术,在最大范围内保证充分考虑失效模式及其后果、起因和机理,DFMEA以最严密的形式总结了设计技术人员进行产品设计时的指导思想。
4.2 APQP小组:由总经理指定的公司内部从事新产品设计和更改的跨功能组织。
4.3严重度(S):是潜在失效模式对下序组件、子系统、系统或顾客影响后果的严重程度的评价指标。
4.4频度(O):是指某一特定的具体的失效起因/机理发生的可能性/频率。
4.5探测度(D):DFMEA是指在零部件、子系统或系统投产之前,现行过程控制方法找出失效起因/机理(设计薄弱部份)的能力的评价指标,PFMEA是指在零部件离开制造工序或装配工位之前,现行过程方法找出失效起因/机理(过程薄弱部份)的可能性的评价指标。
5.流程图:设计失效模式和后果分析(DFMEA)流程图参见(附件一)。
6.作业程序和内容6.1实施DFMEA的时机6.1.1在设计阶段图面设计之前项目组负责主导DFMEA小组实施DFMEA ,并且在产品图样完成之前全部完成。
6.2 DFMEA小组的构成6.2.1DFMEA小组成员由项目组根据项目需要从APQP小组成员中选择组成。
DFMEA失效模式分析报告

度
O
现行控制
探
测
度
D
RPN
建议
方法
责任
及目
的完
毕日
期
方法成果
防止
探测
采用的方法
S
O
D
RP
N
PCBA
EPON各项
指标合客
户规定
陶瓷电容(C1 C23C24C60源自C46..)影响产品性能、寿命
1
1
1.元器件一致性局限性 2 器件破损
2
1.元件降额使用,最小确保元件使用降额 90%2.规定全部器件严格测试
2
6
无
光模块
(U17)
影响产品性能
3
3
2
零件承认产品试作产品验证
3
54
无
LED灯(LED1-LDE5)
影响产品性能
2
3
1
零件承认产品试作产品验证
3
18
无
PCBA
EPON 各项指标合客户规定
FLASH(U30)
影响产品性能
2
1
1.元器件
一致性局
限性 2.器
件破损
2
1.元件降额使用,最小确保元件使用降额 90%2.规定全部器件严格测试
设计失效模式分析
DESIGNFMEA
产品名称:
NAME:
日期:
DATE:
客户产品型号:
CUSTOMERTYPENO:
批准
Approvedby
审核
Checkedby
拟 制
Madeby
产品EP401M潜在失效模式及后果分析
(设计FMEA)
子系统
功效规定
DFMEA检查报告

现行的控制方法找出失效模式的可能性中上 4
现行的控制方法找出失效模式的可能性高
3
现行的控制方法找出失效模式的可能性很高 2
现行的控制方法几乎肯定能找出失效模式,已知 相似过程的可靠的探测控制方法
1
变更人
时间
负责人/部门/ 计划完成日期
采取措施
7
8
9
10 11 12 13
14 15 16 17 18 19 20
21
22
23 24 25 26 27 28 29 30
31 32 33
34
35
36
评
价
准
则
表
:
①、严重度(S)
序号
后果
评价准则
S
1
无警告的严 这是一种非常严重的失效形式,它是在没有任何失效预兆的情况下影响到作业员、用户
6
后果 很高 高
中等
②、频度(O)
失效发生可 ≥1/2 1/3
经常性失效
1/8 1/20
1/50
偶然性失效
③、探测度(D)
O
探测性
利用过程控制方法可以探测出来的
10
几乎不可能
没有已知的控制方法可以找出失效
9
很微小 现行的控制方法找出失效模式的可能
8
微小
现行的控制方法找出失效模式的可能
产品名称: 编制日期: 团队成员:
版本
修订日期:
DFMEA检查报告
过程责任部门: 版 本:
变更细节
版本变更记录
序 设计项目或功
号
能要求
潜在失效模式
严
潜在失效的 重
后果
度
S
潜在失效的起因/机理
汽车座椅DFMEA校核模板文件

Page19
项目校核报告
座椅-装配要求
Page20
项目校核报告
项目DFMEA截图
项目DFMEA佐证
造型面版本
问题描述:无 新发生度:1
PASS NG
Page21
项目校核报告
座椅-NVH/BSR 要求
Page22
项目校核报告
项目DFMEA截图
项目DFMEA佐证
造型面版本
问题描述:无 新发生度:1
PASS NG
Page40
项目校核报告
头枕-材料要求
Page41
项目校核报告
项目DFMEA截图
项目DFMEA佐证
造型面版本
问题描述:无 新发生度:1
PASS NG
Page42
项目校核报告
头枕-可维修性
Page43
项目校核报告
项目DFMEA截图
项目DFMEA佐证
造型面版本
问题描述:无 新发生度:1
备注
Page10
项目校核报告
座椅系统
• 安全/法规要求(XX条) • 材料要求(XX条) • 功能要求(XX条) • 可靠性/疲劳(XX条) • 可维修性(XX条) • 外观造型(XX条) • 制造可行性要求 (XX条) • 装配要求(XX条) • 人体工程学舒适性(XX条) • NVH/BSR 要求 (XX条)
Page57
项目校核报告
导套-NVH/BSR 要求
Page58
完成DV试验
完全沿用或者DV/PV试验都已完成
法规校核类
初始打分
DV&PV实物验证之前:需要CAE结果,但是结果还没出来
DV&PV实物验证之前:完成CAE,手工样件验证
1.8代泵设计故障模式与效应分析报告(DFMEA)G版

1.8代泵设计故障模式与效应分析报告
(DFMEA)G版
自查报告。
报告标题,1.8代泵设计故障模式与效应分析报告(DFMEA)G版。
报告日期,2023年5月15日。
自查人员,XXX。
自查内容,1.8代泵设计故障模式与效应分析报告(DFMEA)G版。
自查结果:
经过对1.8代泵设计故障模式与效应分析报告(DFMEA)G版的自查,发现以下问题:
1. 在故障模式识别方面,部分潜在故障模式未能被充分考虑到,存在遗漏的情况。
2. 故障效应评估中,部分故障的影响程度未能进行准确的评估,存在一定的主观性。
3. 针对某些故障模式的控制措施不够完善,存在漏洞。
自查结论:
1. 针对发现的遗漏问题,需要对1.8代泵设计故障模式与效应
分析报告(DFMEA)G版进行修订,完善潜在故障模式的识别和故障效
应的评估。
2. 需要加强对故障控制措施的制定和完善,确保针对每个潜在
故障模式都有相应的控制措施。
3. 加强对DFMEA的培训和指导,提高团队对DFMEA的理解和应
用水平。
自查人员签名,XXX。
日期,2023年5月15日。
以上为自查报告,请相关部门注意查阅。
模具开发DFMEA失效模式分析
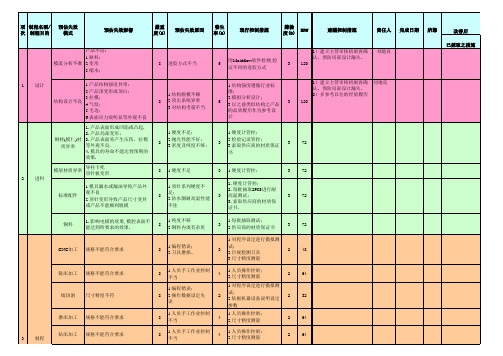
8 8 4
2.人员作业失误 1.人员作业漏失 1.人员作业不当
2 2 6
1.人员模拟实配测试 2.模具制程异常报告 1.专人核对 2.模具制程异常报告 1.专人检查 2.模具制程异常报告 1.专人核对 2.模具制程异常报告
2 2 3
32 32 72
制程尺寸与模 1.产品尺寸不良,导致组装或功 具图面不符 能干涉
刘地良
8
1.硬度不足; 2.抛光性能不好; 3.密度及纯度不够;
3
1.硬度计管控; 2.检验记录管控; 3.索取供应商的材质保证 书.
3
72
8
1.硬度不足 1.项针系列硬度不 足; 2.防水圈耐高温性能 不佳. 1.纯度不够. 2.铜料内混有杂质.
3
1.硬度计管控; 1.硬度计管控; 2.每批抽取2PCS进行耐 高温测试; 3.索取供应商的材质保证 书. 1.每批抽取测试; 2.供应商的材质保证书. 1.对程序设定进行摸拟测 试; 2.目视检测刀具 3.尺寸精度测量 1.人员操作控制; 2.尺寸精度测量 1.对程序设定进行摸拟测 试; 2.依据机器设备说明设定 参数. 1.人员操作控制; 2.尺寸精度测量 1.人员操作控制; 2.尺寸精度测量
8
进胶方式不当
5
用Moldflow软件检测,验 证不同的进胶方式
1)建立主管审核机制再确 认,预防局部设计漏失。 3 120
刘地良
8
1.结构脱模不顺. 2.顶出系统异常. 3.对结构考量不当.
5
1.结构强度遵循行业标 准; 2.摸拟分析设计; 3.以之前类似结构之产品 的品质履历作为参考设 计.
1)建立主管审核机制再确 认,预防局部设计漏失。 2)多参考以往的经验履历 3 120
DFMEA

环境安全
符合
RHOS REACH
不符合ROHS
REACH
不符合法律、法规
使用非环保材料
依据经验评估物料是否满足ROHS\REACH的环境有害物质需求。
审核确认检测报告
10
0
1
0
2
产品安规
符合
UL、3C、CE
认证
不符合UL 3C CE认证
不符合安规
部件未获安规认证
UL 3C CE认证机构认证
审核确认认证报告
6
跌落性能,1m高度自由跌落,功能正常,防水满足IPX7浸泡30分钟,运行噪音30CM距离≦50db
产品跌落损坏
产品跌落易损坏
产品结构设计不合理,易损件没能有效保护
依据经验对产品结构薄弱点、抗跌性能进行评估。
实测验证产品在跌落后的各项表现(如结构、功能、防水、噪音、外观)
7
噪音,30CM距离,≦50db
不符合使用环境要求
产品不能满足40℃环境下运行,或功能失效,或没达到预期目标
依据经验评估40℃环境降温表现
模拟40℃恒温环境下,运行产品进行降温验证。
高温环境DC允许修改目标为30℃
4
储存环境
-20-65℃ 96h
产品损坏
不能满足海运/空运运输环境及其它环境
产品不能满足-20℃与65℃环境下储存
依据经验选择材料、评估物料,装配工艺的环境储存水平。
对产品进行实际试用确认。
9
产品功能
充电
充电方式:磁吸
磁吸平衡保持力≧300g
充电电压:DC5V
最高充电电流:450ma
充电时长≦3.5h
充电时长>3.5h
没满足设计需求
液压离合器DFMEA分析报告
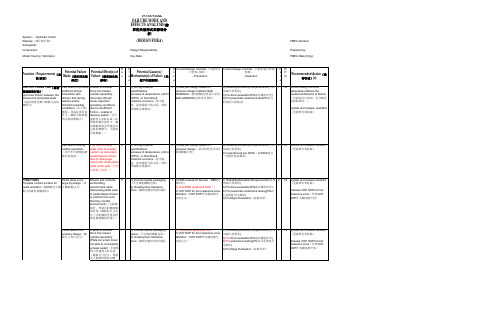
35
Pad falls off during vehicle operation. (在汽车行驶期间踏 板衬套脱落)
Pad falls off pedal 5 plate, able to actuate system via redundant pedal features (driver able to disengage clutch with metal pedal plate under pad) (衬垫从踏板上脱 落,) Drivers foot contacts 5 surrounding environment while depressing pedal (size of pedal allows drivers' to position foot such that they contact environment)(当踩踏 板时,驾驶员的脚接触 的环境(踏板的尺寸决 定了司机脚的位置这样 就是脚接触的环境))
D e t c
R P N
Recommended Action(推 荐行动)(s) Current design controls adequately address the cause/mechanisms of failure.(目前的设计控制,充 分解决失败的原因。) Update and release standard(更新和发布标准)
1) Incorrect pedal packaging 1 1) DMA Clearance Review(DMA间 (不正确的踏板包装) 隙审查) 2) Violating foot clearance 2) CoC/KBE pedal pad SOP() zone(脚的间隙空间的问题) 3) VOP SOP for foot clearance zone definition(VOP SOP作为脚间 隙空间的定义)
DFMEA制程潜在失效分析报告

DFMEA制程潜在失效分析报告一、引言潜在失效模式与效应分析(Failure Mode and Effects Analysis, FMEA)是一种常用的质量管理工具,主要用于识别和评估制程中的潜在失效、确定失效模式的原因和后果,并采取相应的措施,以降低潜在失效对制程质量造成的影响。
本报告主要针对制程进行DFMEA制程潜在失效模式分析,以期发现潜在问题并采取相应措施提升制程可靠性。
二、目标本次DFMEA制程潜在失效模式分析的目标是识别潜在失败模式,评估其可能性、严重性和发现程度,并制定相应的纠正和预防措施,使制程的质量得到提升,达到满足客户需求的标准。
三、方法1.团队组成:本次DFMEA分析由一个由相关岗位的工程师、技术人员和质量管理人员组成的跨职能团队完成。
2.DFMEA流程:按照规定的DFMEA标准流程进行潜在失效模式分析,包括确定分析对象、定义制程概况、制定评分标准、识别失效模式、评估潜在失败的后果和严重性、确定可能性与发现程度、计算风险优先级数(RPN值)、制定改善措施和跟踪实施等步骤。
3.数据收集:通过制程的历史数据、客户反馈、质量记录和操作流程等收集与分析对象相关的数据。
四、DFMEA制程分析结果基于以上方法,我们进行了制程潜在失效模式分析,并汇总如下:1.失效模式分析对象:制程失效模式:a.设备故障;b.人为操作失误;c.材料供应问题;d.环境变化;e.工序流程异常。
2.安全性严重性评估使用DFMEA评分标准将失效模式按照安全性进行评估,得出相应的评分。
3.频率可能性评估结合制程历史数据和操作流程,评估失效模式发生的频率和可能性。
4.检测发现程度评估评估当前制程在对失效模式进行检测并发现的程度,以此得出评分。
五、风险优先级数(RPN值)计算风险优先级数(RPN值)是根据失效模式的严重性、可能性和发现程度得出的综合评分。
计算RPN值,找出风险较高的失效模式。
六、措施制定根据RPN值,针对高风险的失效模式制定相应的预防和纠正措施,以降低制程风险。
DFMEA失效模式分析报告-样板

DFMEA失效模式分析报告-样板这份报告旨在对产品进行失效模式分析 (Design Failure Mode and Effects Analysis。
DFMEA)。
通过对产品设计中可能出现的失效模式进行分析,并评估其对产品质量和性能的影响,我们可以识别潜在的问题并制定相应的改进措施。
通过进行DFMEA分析,我们的目标有以下几点:确定潜在的失效模式和影响因素;评估失效模式对产品的质量和性能的影响;识别潜在问题并提出相应的改进建议;优化产品设计,提高产品的可靠性和性能。
DFMEA分析将采用以下步骤:1.确定分析范围和团队成员:确定要分析的产品和相关过程,并确定参与分析的团队成员;2.确定功能需求:明确产品的功能需求,并列出与功能相关的失效模式;3.评估失效模式的影响:评估每个失效模式对产品质量和性能的影响程度,并给予相应的等级;4.识别潜在原因:分析每个失效模式的潜在原因,并列出可能的原因;5.制定改进措施:提出针对每个失效模式的改进措施,并确定负责人和实施时间;6.执行和验证改进措施:跟踪实施改进措施的进展,并验证改进措施的有效性。
这份报告将包含以下内容:1.引言:介绍DFMEA的目的和方法,以及报告的背景和结构;2.产品描述:提供产品的基本描述和功能需求;3.失效模式和影响因素:列出潜在的失效模式和与之相关的影响因素;4.失效模式的评估:对每个失效模式进行评估,包括影响程度的等级和相应的说明;5.潜在原因分析:针对每个失效模式列出可能的潜在原因;6.改进措施:针对每个失效模式提出相应的改进措施,并确定负责人和实施时间;7.结论:总结分析结果,并强调关键改进措施的重要性;8.附录:包括参与DFMEA分析的团队成员、会议记录等相关信息。
完成这份DFMEA分析报告的时间计划如下:第一阶段:确定分析范围、功能需求和失效模式列表,预计时间为2周;第二阶段:评估失效模式的影响、识别潜在原因和制定改进措施,预计时间为3周;第三阶段:执行和验证改进措施,并编写最终的报告,预计时间为2周。
DFMEA失效模式分析报告-范例

电感(L21
L3 L151)
影响产品性能
4
1
2
零件认可
产品试作
产品验证
2
16
无
电源按键
(S3)
影响产品性能
3
1
1
零件认可
产品试作
产品验证
2
6
无
光模块
(U17)
影响产品性能
3
3
2
零件认可
产品试作
产品验证
3
54
无
LED灯
(LED1-LDE
5)
影响产品性能
2
3
1
零件认可
产品试作
产品验证
3
18
无
PCBA
EPON各项
产品试作
产品验证
3
12
无
电源接口
(J5)
影响产品组装
2
1
1
零件认可
产品试作
产品验证
3
6
无
变压器
(T2)
影响产品性能
3
1
2
零件认可
产品试结构器件
满足外观
及结构要
求
下壳
影响外观及安装
2
1
安装及搬
运过程中
划伤
1
注意操作规
范
零件认可
产品试作
产品验证
3
6
无
上盖
影响外观及安装
2
1
1
零件认可
产品试作
产品验证
3
6
无
产品EP401M潜在失效模式及后果分析
(设计
子系统
功能要求
潜在失效 模式
DFEM评审报告
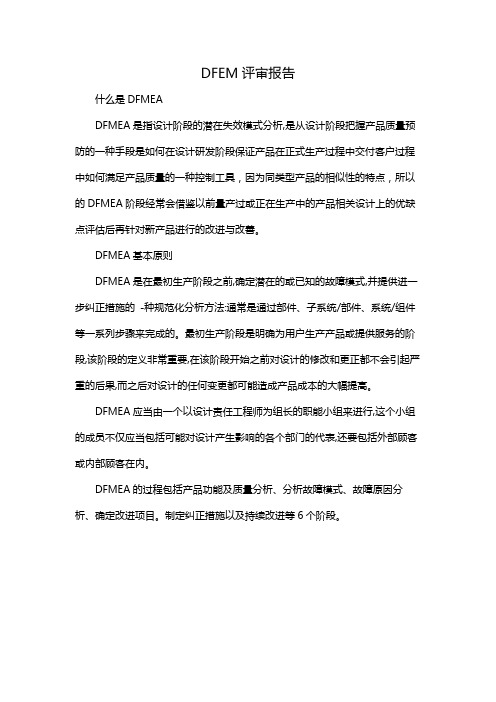
DFEM评审报告
什么是DFMEA
DFMEA是指设计阶段的潜在失效模式分析,是从设计阶段把握产品质量预防的一种手段是如何在设计研发阶段保证产品在正式生产过程中交付客户过程中如何满足产品质量的一种控制工具,因为同类型产品的相似性的特点,所以的DFMEA阶段经常会借鉴以前量产过或正在生产中的产品相关设计上的优缺点评估后再针对新产品进行的改进与改善。
DFMEA基本原则
DFMEA是在最初生产阶段之前,确定潜在的或已知的故障模式,并提供进一步纠正措施的-种规范化分析方法:通常是通过部件、子系统/部件、系统/组件等一系列步骤来完成的。
最初生产阶段是明确为用户生产产品或提供服务的阶段,该阶段的定义非常重要,在该阶段开始之前对设计的修改和更正都不会引起严重的后果,而之后对设计的任何变更都可能造成产品成本的大幅提高。
DFMEA应当由一个以设计责任工程师为组长的职能小组来进行,这个小组的成员不仅应当包括可能对设计产生影响的各个部门的代表,还要包括外部顾客或内部顾客在内。
DFMEA的过程包括产品功能及质量分析、分析故障模式、故障原因分析、确定改进项目。
制定纠正措施以及持续改进等6个阶段。
- 1、下载文档前请自行甄别文档内容的完整性,平台不提供额外的编辑、内容补充、找答案等附加服务。
- 2、"仅部分预览"的文档,不可在线预览部分如存在完整性等问题,可反馈申请退款(可完整预览的文档不适用该条件!)。
- 3、如文档侵犯您的权益,请联系客服反馈,我们会尽快为您处理(人工客服工作时间:9:00-18:30)。
职责及目
严发
标 完成日期
采取措施和 重 生 生效日期 度 率
D
PRN
SO
LECU固定螺钉选型有
误,振动时松动脱
对LECU固定螺钉进
8 落,导致在LECU壳体 4
行材质及尺寸的测 2 64
中滚动,引起板子短
试验证
路BMU固定螺钉选型有
电池系统内
误,振动时松动脱
对BMU固定螺钉进行
电池管理 的高压器件 8 落,导致在BMU壳体 4
2
报警,输入输出
BMU软硬件
控制
版本号读取 8
数据存储错误 2
失败
故障检测错 误
8
故障触发条件判断错 误
2
BMS故障
预警与处 高压互锁功
理
能失效
8
高压互锁采样或控制 电路故障
2
碰撞开关功 能失效
8
碰撞开关检测电路故 障
2
BMS诊断 诊断功能失
功能
效
8
诊断代码错误 2
备注: 在下列三种失效条件下,须制定相应的改善措施: (1)最优原则:S≥9时,必须分析设计控制或建议措施 (2) 严重度S≤8,风险顺序数RPN≥80时(或依顾客需求) (3)关键特性发生失效时。
2 32
拉力试验
2 64
CAN通讯功 8 通讯接插件端子松脱 4
能失效 8
通讯程序bug
2
8 继电器控制电路故障 2 放电回路继
电器失效 管理功能
下降
8
放电启动或停止条件 错误
2
检测电池状态, 计量SOC,整车 通信,电滥用保 护,故障识别及
8 继电器控制电路故障 2 慢充回路继
电器失效
8
慢充启动或停止条件 错误
潜在失效模式及后果分析
BMS
系统
FMEA编号
BCU/BMU 子系统
页码
页
部件
设计职责
编制人
型号/年/项目 功能 要求
严重 度数S 潜在 失效的模式 失效模式 潜在后果
关键日期
失效的潜在要因 起因/机理
FMEA日期(原 始)
(修订)
措施结果
发 生 率
现行设计 控制预防
现行设计控制探测
探
测 率
RPN
D
建议 措施
拉力试验/耐久试验 2 64
对软件代码进行检 查
2
32
对控制电路各组成 单元进行测试
2
32
启动、停止条件代 码检查
2
32
对控制电路各组成 单元进行测试
2
32
启动、停止条件代 码检查
2
32
对存储代码进行检 查
2
32
对故障条件判断的 代码进行检查
2
32
对采样和控制电路 进行功能测试
2
32
对检测电路进行功 能测试
3
绝缘电阻采
绝缘电阻采样检测电
样精度误差 8 路故障或软件算法错 3
较大
误
CAN通讯功 8 能失效 8
通讯电路故障 2 通讯线束断裂 4
BMU外壳采用铝壳材
质,安装时做好接 地设计,并进行测
2 64
试验证
分别测量各模块与 壳体之间绝缘阻 值,判断绝缘失效 点
2 48
对检测电路各组成 单元进行测试,对 2 32 软件代码进行检查
生噪音,抗
电池管理 干扰能力 系统电磁 差,顾客舒 兼容性差 适性变差,
8
结构及线束的排布抗 干扰能力差
4
引起顾客不
满意
电池管理 系统组件 带电部分 与壳体之 间的绝缘 电阻降低
绝缘电阻过 低触发BMS 报警,导致 系统无法正
常工作
8
电池模组与系统壳体 之间绝缘措施失效
3
检测电池状态, 计量SOC,整车 通信,电滥用保 护,故障识别及 报警,输入输出
2
32
对诊断代码进行检 查
2 32
材质及尺寸的测试 2 64
系统组件 、线束等松
中滚动,引起板子短
抗振性能 动,有发生
路
检测电池状态, 计量SOC,整车
差
短路或断路 的风险
8
线束插拔端子选型有 误
4
验证
对插拔端子的拉力 强度进行测试验证
2 64
通信,电滥用保 护,故障识别及 报警,输入输出
8
LECU板上的硬件元器 件抗振性能差
4
对LECU板进行随机 振动测试验证
对BMU电源模块进行 功能验证
2
32
对检测电路各组成 单元进行测试,对 软件代码进行检查
对检测电路各组成 单元进行测试,对 软件代码进行检查
对检测电路各组成 单元进行测试,对 软件代码进行检查
对检测电路各组成 单元进行测试,对 软件代码进行检查
2 48 2 48 2 48 2 48
对通讯电路各组成 单元进行测试264控制8
BMU板板上的硬件元 器件抗振性能差
4
对BMU板进行随机振 动测试验证
2
64
电池系统产 生噪音,抗 电池管理 干扰能力 系统电磁 差,顾客舒 8 BMU板抗干扰能力差 4 兼容性差 适性变差, 引起顾客不 满意
BMU外壳采用铝壳材
质,安装时做好接 地设计,并进行测
2 64
试验证
电池系统产
控制
BMS在供电 电压范围内
8
供电电压检测电路故 障或软件算法错误
2
无法正常工
作
8 BMU电源模块损坏
2
总电压采样 精度误差较
大
8
总电压检测电路故障 或软件算法错误
3
单体电压采
管理功能 样精度误差
下降
较大
8
单体电压检测电路故 障或软件算法错误
3
电流采样精 度误差较大
8
电流采样检测电路故 障或软件算法错误