五轴编程教程.
数控五轴加工中心编程的方法及步骤
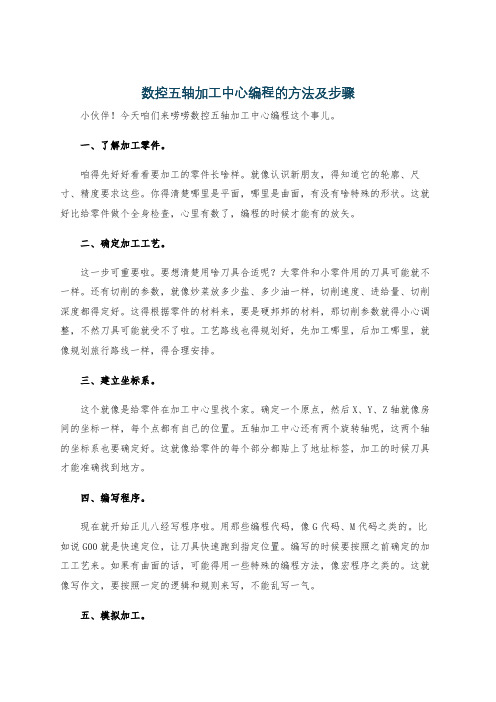
数控五轴加工中心编程的方法及步骤小伙伴!今天咱们来唠唠数控五轴加工中心编程这个事儿。
一、了解加工零件。
咱得先好好看看要加工的零件长啥样。
就像认识新朋友,得知道它的轮廓、尺寸、精度要求这些。
你得清楚哪里是平面,哪里是曲面,有没有啥特殊的形状。
这就好比给零件做个全身检查,心里有数了,编程的时候才能有的放矢。
二、确定加工工艺。
这一步可重要啦。
要想清楚用啥刀具合适呢?大零件和小零件用的刀具可能就不一样。
还有切削的参数,就像炒菜放多少盐、多少油一样,切削速度、进给量、切削深度都得定好。
这得根据零件的材料来,要是硬邦邦的材料,那切削参数就得小心调整,不然刀具可能就受不了啦。
工艺路线也得规划好,先加工哪里,后加工哪里,就像规划旅行路线一样,得合理安排。
三、建立坐标系。
这个就像是给零件在加工中心里找个家。
确定一个原点,然后X、Y、Z轴就像房间的坐标一样,每个点都有自己的位置。
五轴加工中心还有两个旋转轴呢,这两个轴的坐标系也要确定好。
这就像给零件的每个部分都贴上了地址标签,加工的时候刀具才能准确找到地方。
四、编写程序。
现在就开始正儿八经写程序啦。
用那些编程代码,像G代码、M代码之类的。
比如说G00就是快速定位,让刀具快速跑到指定位置。
编写的时候要按照之前确定的加工工艺来。
如果有曲面的话,可能得用一些特殊的编程方法,像宏程序之类的。
这就像写作文,要按照一定的逻辑和规则来写,不能乱写一气。
五、模拟加工。
程序写好可别着急让加工中心干活。
先模拟一下,就像演习一样。
看看刀具的路径对不对,有没有可能撞到零件或者夹具。
要是模拟的时候发现问题,那就赶紧修改程序。
这就像出门前检查一下东西有没有带齐,发现没带钥匙还能及时补上。
六、实际加工。
经过前面的步骤,没问题啦,就可以让加工中心开始干活啦。
不过在加工的时候也不能完全不管,得盯着点。
万一有啥突发情况,像刀具磨损啦,还能及时处理。
数控五轴加工中心编程就是这么个事儿,看起来有点复杂,但是只要一步一步来,多实践,肯定能掌握的。
五轴编程UG教程

1刀轴远离直线(zhíxiàn)-案例1
分层切削(qiēxi āo)
第九页, 共61页。
词语: 如果 拼音: rúguǒ
1刀轴远离(yuǎn l í ) 直线-案例1 解释: 连词。表示假设。《前汉书平话》卷上: “如果不利,截旗营前,以定胜败验之。”《儒林外史》第十六回: “如果文
象
利用网格曲面作为 驱动面能够获得光
顺的刀路
构建网格曲面
面的质量 决定刀轨 的质量
第十九页, 共61页。
词语:指定 拼音:zhǐdìng 解释:确定;认定。唐刘肃《大唐新语·公直》:“銛谬膺驳正,敢废司存,请傍移礼官,以求指定。”宋司马光《起请科场札 子》:“伏乞以臣所奏,及礼部等官所议,榜国子监门,及编下诸州,有州学处榜州学门,令举人限一月内投状,指定何法为善,
旋转刀轨, 获得(huòdé)各个槽的加工程序, 两个刀轨要接起, 否则会有残料
第二十四页, 共61页。
2刀轴插补-案例(àn l ì ) 3
第二十五页, 共61页。
3刀轴侧刃驱动(qū dònɡ)1
部件几何引导刀尖运 动, 驱动面引导刀具
侧刃运动
部件(bù jiàn)选 择底面
驱动(qū dònɡ)面 为周边
第一回:“问其所 以,都是黄河沿上的州县,被河水决了,田庐房舍,尽行漂没。”可与形容词或动词组成名词性词组,仍表示 原因、情由。《庄子·天运》:“彼知矉美,而不知矉之所以美。”《史记·卫康叔世家》:“必求殷之贤人君子长者,问其所以 兴,所以亡,而务爱民。”用以,用来。《庄子·天地》:“是三者,非所以养德也。”《史记·孟尝君列传》:“若急,终无以 偿,上则为君好利不爱士民,下则有离上抵负之名,非所以厉士民彰君声也。”宋苏洵《几策·审势》:“故威与惠者,所以裁节 天下强弱之势也。”连词。表示因果关 系。用在下半句,由因及果。《荀子·哀公》:“君不此问,而问舜冠,所以不对。”北
《五轴编程UG教程》课件

THANKS
汇报人:PPT
UG软件的安装与配置
UG软件的安装步 骤
UG软件的配置参 数
UG软件与其他软 件的兼容性
UG软件的使用技 巧
Part Four
五轴编程基础知识
五轴机床的基本结构
五轴机床的定义和特点 五轴机床的分类和组成 五轴机床的控制系统和编程软件 五轴机床的应用领域和优势
五轴机床的坐标系和运动关系
五轴机床的坐标系 五轴机床的运动关系 五轴机床的编程技巧 五轴机床的应用领域
加工复杂零件:五 轴编程能够加工复 杂零件,满足高精 度、高效率的加工 需求。
提升产品质量:五 轴编程能够减少加 工误差,提高产品 质量和稳定性。
适应市场需求:五 轴编程能够适应市 场需求,满足不同 客户的需求,提高 企业的竞争力。
Part Three
UG软件介绍
UG软件的基本功能
建模功能:支持多种建模方式,包括实体建模、曲面建模等 工程图功能:能够生成符合工程要求的图纸,包括零件图、装配图等 运动仿真功能:可以对机构进行运动仿真,分析机构的运动性能 数控加工功能:支持多种数控加工方式,包括铣削、车削、钻孔等 模具设计功能:支持模具设计,包括分型面设计、型腔设计等
实际加工过 程演示:通 过视频或图 片展示实际 加工过程, 包括机床操 作、刀具选 择等
加工结果评 估:对加工 结果进行评 估,包括尺 寸精度、表 面粗糙度等 方面
总结与展望: 总结叶轮加 工的难点和 解决方案, 并展望未来 五轴编程技 术的发展趋 势
案例二:加工螺旋桨
螺旋桨简介:介 绍螺旋桨的结构、 功能和制造要求。
实际应用案例:介绍UG软件在后处理与工艺规划方面的实际应用案例, 包括复杂零件的加工、多轴联动加工等。
pm五轴编程案例
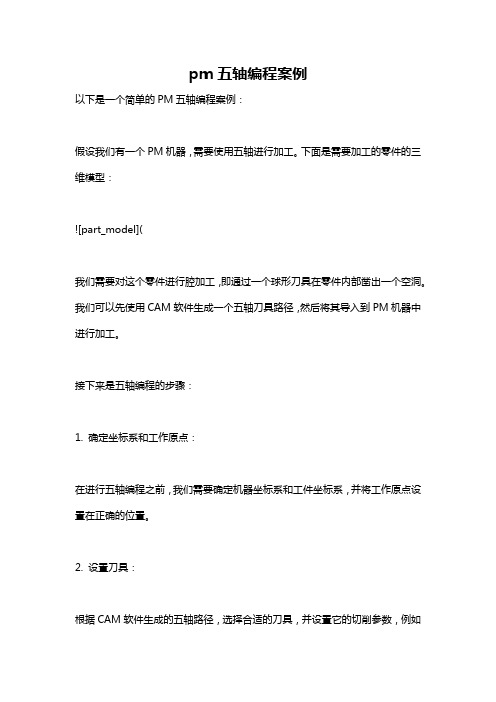
pm五轴编程案例
以下是一个简单的PM五轴编程案例:
假设我们有一个PM机器,需要使用五轴进行加工。
下面是需要加工的零件的三维模型:

WorkNC G3 V19 Training Guide: 5-Axis03/05/07Table of Contents Table of Contents1Prerequisites 1-1 2General Principles for 5-Axis Machining 2-1 35-Axis Machining Parameters 3-1 3.1Machining Zone and Surface Selection for 5-Axis 3-1 3.2Selection of the 5-axis machining method 3-1 3.3Selection of the tool orientation 3-2 3.4Lead-in selection 3-4 3.55-Axis Parameters 3-5 3.6Curve Machining Options 3-7 3.7Selection of the guide curve 3-7 3.8Selection of the change of direction in corners 3-8 3.9Tool Offset Distance 3-10 3.10Tool Offset Angle 3-10 45-Axis Rolling 4-1 4.15-Axis Rolling - Machining Strategy 4-4 4.2Lab: 5-Axis Rolling 4-6 55-Axis Pocketing 5-1 65-Axis Planar Finishing 6-1 6.1Lab: Planar Finishing 6-1 7Z-Level Finishing - Blade Machining 7-1 7.1Lab: Z-Level Finishing - Blade Machining 7-1 85-Axis Parallel to Curve 8-1 8.1Lab: 5-Axis Parallel to Curve 8-1 95-Axis Perpendicular to Surface 9-1 9.1Programming 5 Axis Perpendicular to Surface 9-1 105-Axis Normal to Surface 10-1 10.1Lab: Normal to Surface 10-2 11Grooves 11-1 125-Axis Profiling 12-1 12.15-Axis Profile: Surface Contact Detection 12-1 12.2Lab: Profiling 12-3 134-Axis Profiling 13-1 13.1Programming a 4-Axis Profile toolpath 13-1 14Rolling between Curves 14-1 15Blade Machining 15-1 15.14-Axis Spiral Blade Roughing and Finishing 15-1 15.24-Axis Spiral Blade Remachining 15-4 16Impellers 16-1Table of Contents16.1Programming 5-Axis Impellers Roughing 16-116.2Programming a 5-Axis Impellers Finishing 16-516.3Programming 5-Axis Impeller Remachining 16-6175-Axis Hole Boring 17-117.1Lab: 5-Axis Drilling 17-318Editing Toolpaths 18-118.1General Points 18-118.2Modification of a point 18-218.3Modification of normals 18-518.3.1Normal Selection Types 18-518.3.2Editing Functions for Normals 18-918.4Wizard 18-1019Collision Check 19-119.1General Points 19-119.2Display of the machine 19-219.3Activating Detection and Collision Properties 19-219.4Collision Settings 19-319.5"Toolpath Properties" Panel 19-419.6Representation of Collisions in VisuNC 19-6Prerequisites11 PrerequisitesThis training session and its related manual require that the user has a good working knowledge of WorkNC. He must know how to activate parts, create and edit toolpaths.2 General Principles for 5-Axis MachiningThe G3 V19 version of WorkNC is delivered with twenty 5-axis toolpaths. All of them are milling toolpaths, except a drilling toolpath and a laser cutting toolpath.The surface part construction is very important when using 5-Axis toolpaths. In most cases, the tool orientation is directly linked to the U and V parameters of the surfaces.Most toolpaths require the use of context surfaces to select the surfaces to machine, others require the use of one or more guides curves, etc.For 5-axis machining, a surface is made of a profile and a face. The position of the tool on the surface depends on the selected toolpath, especially for "rolling" and "profiling".E.g.:Surface to machine:Rolling:Profiling:Machining normal to Surface:5-Axis Machining ParametersMachining Zone and Surface Selection for 5-Axis33 5-Axis Machining ParametersAll standard parameters may be used, except boundary curves and machining planes which are never used for 5-axis machining.1. Selection of a machining zone2. Selection of context surfaces3. Selection of the machining method4. Selection of the tool orientation5. Lead-in selection6. Selection of the curve to machine7. Selection of the change of direction in corners 8. Position of the tool on the surface 9. 5-Axis Parameters10. Surface in relation to which the tool is oriented3.1 Machining Zone and Surface Selection for5-AxisIt is not possible to use "Boundary Curves" or "Machining Planes": only Window and View parameters are available. In some cases, the use of a view allows defining which side of the surfaces are machined. This is for example the case for the Perpendicular to surface toolpath.3.2 Selection of the 5-axis machining methodYou can usually choose any of the threeavailable machining methods. This means that the direction of the guide curve as it wascreated has no importance.NOTEStart point of the guide curveWhen using a closed curve, the point used as starting point to create the guide curve is important since the toolpath will start from that exact point.35-Axis Machining Parameters Selection of the tool orientation3.3 Selection of the tool orientation(5-Axis) Machining Direction Dialog BoxSurface definitionFor 5-Axis programming, it is very important that surfaces are correctly defined: the tool orientation depends on the U and V parameters of the surface. Surfaces must have been properly prepared before programming a 5-axis toolpath. E.g.:Surfaces not correctly defined...... wrong toolpath:Surfaces correctly defined... toolpath is OK:The example illustrated with the four images above is a clear representation of the problems that you may encounter. If the U and V surface parameters are not correct and if you choose to follow surface ISO lines, the toolpath may be incomplete or the position of the tool may be wrong. The only solution: change the surface(s) using CAD functions.Other example with wrong positioning of the tool:5-Axis Machining ParametersSelection of the tool orientation3Surfaces not correctly defined...... wrong toolpath:Surfaces correctly defined...... toolpath is OK:The above example shows another type of problem that you may encounter: if the U and V parameters of the surface are not correct and if you chose to follow surface ISO lines, the toolpath may be fully completed but the position of the tool may be wrong. Again, change the surface(s) using CAD functions.In case of problems when following surface ISO lines, you can also try the other option called "Perpendicular to curve": it may give better results.(5-Axis) Machining Direction Dialog Box - Perpendicular to CurveFollow surface ISO lines: Perpendicular to curve:35-Axis Machining Parameters Lead-in selection3.4 Lead-in selectionIf you have enough room to position your tool outside the machining zone without any risk of collision with the part or any clamping equipment, you can choose among different machining lead-ins, depending on your own preferences.Radial lead-in with tangency extensionVertical Lead-inRadial Lead-inLead-in with tangency extension3.55-Axis Machining Parameters35-Axis Parameters 3.6 5-Axis ParametersMaximum head rotationThis parameter is used to specify the rotation amplitude ofthe machine head not to be exceeded. This maximumamplitude directly depends on the technical constraints of themachine. When the inclination angle of a surface to machineis higher than this value, the toolpath does not give anyresult. This parameter does not apply to all 5-axis toolpaths.This parameter allows you to indicate the machine capabilityto reach such angle values or not.1. Vertical head 0°2. Maximum amplitude from – 40 to + 40°The opposite picture illustrates this amplitudeparameter. In this case, a surface to 45° could not bemachined.Vector tolerance for smoothingThis parameter allows defining a maximum angle within which the tool can be adjusted onits axis to obtain a smoother toolpath and avoid vibrations of the machine head. If you setthe value to 3°, each of the vectors can "deviate" by a maximum of 3°. This parameter isalways combined with the smoothing distance.35-Axis Machining Parameters 5-Axis ParametersSmoothing DistanceThis is the length over which WorkNC tries to smooth the toolpath. This value applies both forwards and backwards with respect to each point of the toolpath and in the machining direction.Smoothing vector (5°) Smoothing Distance: 1 mmSmoothing vector (45°) Smoothing Distance: 30 mmsVector toleranceThis parameter offers the possibility of reducing/increasing the number of points in atoolpath. If consecutive point vectors along a longitudinally straight section of the toolpath have vector angle variations within the limit of this user defined tolerance, then these points will be eliminated. This tolerance cannot exceed 5°.Setting this parameter with a small value can be useful when working on recent millingcenters with the latest CN controllers which function better with toolpaths containing a large number of points. Alternatively, a higher value will produce a smaller number of points which is more appropriate to older generation milling centers.Vector tolerancePicture 1: Tolerance = 1° Picture 2: Tolerance = 4° Picture 3: Tolerance = 0.1°5-Axis Machining ParametersCurve Machining Options33.7 Curve Machining OptionsBasically, these options operate in the same way as 2D toolpaths for which he same type of parameters is available.Z-steps are completed to gradually approach the curve to machine.These parameters allow you to machine directly onto the surface or to proceed by level, especially during the roughing phase which requires large quantities of material to be removed.Examples :Approach of the curve from + Z:Approach of the curve in the view plane:Machining order, by level:Machining order, by curve:NOTEMachining OrderMachining by curve is similar to machining by zone in 3D toolpaths. The toolpathmachines an area completely then goes machining the next area. When the "by level" option is selected, the number of retracts in the toolpath is higher.3.8 Selection of the guide curve3 5-Axis Machining ParametersSelection of the change of direction in cornersToolpath Parameters - Curve to machineYou must specify the curve to machine. Note that "Curve to machine" means the drive curve.3.9 Selection of the change of direction incornersThe "non-tangency condition" allows managing changes of direction in sharp corners. Twooptions are possible: radial or by segment.Radial:5-Axis Machining ParametersSelection of the change of direction in corners3 By segment:NOTE By segmentWith the "Segment" option, the edge to machine is protected as the tool does not "roll" on it.35-Axis Machining Parameters Tool Offset Distance3.10 Tool Offset DistanceThe Tool Offset Distance parameter defines the axial distance between the center of the tool tip or tool end and the perpendicular point of the curve on the tool axis. By default, if the value is set to 0, the center of the tool tip or tool end is positioned on the curve during toolpath calculations.Picture 1:Picture 2:1. Surface to machine2. Curve to follow and upper surface (2/2a)3. Lower surface4. Controlled point of the tool (center of the tool)5. Offset distanceThe picture # 1 shows the theoretical position of the tool against the machined curve. The picture # 2 shows the position of the tool with an offset value which corresponds to the tool radius.Toolpath example:With a negative offset3.11 Tool Offset AngleThe forward offset angle allows you to define a lead or lag angle with respect to the normal to surface position along the toolpath trajectory.Defining a positive value will result in a lead angle (forward inclination) and a negative value will give a lag angle (backward inclination).This promotes better cutting conditions and improves surface finish quality.5-Axis Machining Parameters3Tool Offset AngleForward Offset Angle = 10°1 Surface2 Tool trajectory direction3 Toolpath pointA positive value of 10° has been entered for the above example so the tool will be inclined in a forward direction with respect to the tool trajectory direction.This specific parameter is not available in all 5-Axis toolpaths but can be used for 5-Axis Planar Finishing, Normal to Surface, etc.5-Axis Rolling Tool Offset Angle445-Axis RollingThe Rolling strategy is used - among others - for part trimming.5-Axis Rolling machines with the side of the cutter, tangent to the surface and following the user-defined curve as illustrated in the following diagram.5-Axis Rolling Machining Principle1 Surface2 CurveYou can use this toolpath both for the roughing or finishing phase.NOTESurface constructionThe surface construction is very important when using the Rolling strategy: surfaces must be perfectly ruled.E.g.:45-Axis Rolling Tool Offset AngleRolling: lead-in with "tangency extension"1. Machined surface2. Tangency ExtensionSee Also...• Selection of the change of direction in corners [g 3-8]•5-Axis Rolling4Tool Offset Angle Tool Offset Distance [g 3-10]•Tool Offset Angle [g 3-10]4 5-Axis Rolling5-Axis Rolling - Machining Strategy4.1 5-Axis Rolling - Machining StrategyWe will use the following part to illustrate 5-Axis Rolling machining strategies.Example of 5 Axis Rolling ToolpathThe Surface Group, Guide Surfaces and Curves are defined as follows.Surface Selection Group, Guide Surfaces and CurveThe green surface is defined for machining in the Surface Group. The blue surfaces aredefined as the Guide Surfaces and the Curve to Machine is the yellow curve at the base ofthe island.The resulting toolpath is as shown below.Generated 5-Axis Rolling ToolpathLet’s now take a look at a zoomed view of the cutter tip at a point on the toolpath todetermine its position with respect to the flat surface defined for machining in the SurfaceGroup.5-Axis Rolling45-Axis Rolling - Machining StrategyZoom on Cutter TipYou can see in the above screenshot that the extremity of the cutter makes contact with the flat surface defined for machining (the stock allowance = 0 in this toolpath).If we generate the same toolpath but we define the flat surface as ‘ignored’ in the Surface Group, we obtain the following result.Zoom on Cutter Tip - Ignored SurfaceAs the tool is tangent to the inclined Guide Surfaces and the surface below the cutter tip is programmed as ‘Ignored’, the cutter effectively machines this surface.4 5-Axis RollingLab: 5-Axis Rolling4.2 Lab: 5-Axis RollingOpen the 5axes_1 workzone and create "Rolling" toolpaths by machining the undercutgroove.Use the 5-Axis toolpath parameters to create both 5-Axis roughing and finishing cutterpaths.5-Axis Pocketing555-Axis PocketingThis toolpath has been designed for machining tubular forms (e.g. inlet manifolds). You can machine inclined walls and undercuts without having to define different views to access these areas. The toolpath starts at the top of the pocket and mills deeper.Tool Axis ControlAngle and attraction point...When using both an angle and an attraction point, WorkNC draws a dummy cone whose end is the center of the tool tip when in contact with the surface and inclined to the specified angle value .In this case, the tool is oriented to the specified angle, in the direction of the attraction point.This orientation applies for all points on the toolpath, provided however that the attraction point is correctly positioned.Attraction Point...55-Axis PocketingWhen using an attraction point only, the tool is actually oriented with respect to a line going from the center of the tool tip to the attraction point when the tool is in contact with the surface.This orientation applies for all points on the toolpath, provided however that the attraction point is correctly positioned. When the attraction pointis not properly positioned for a given point on the toolpath, a new position is calculated by WorkNC to avoid collision.Z-Step...You can only use a Z-level machining method. The Z-step value can be fixed or variable. The view that you define is very important since each of the Z-steps in the toolpath is made accordingly. Z-steps are calculated in the plane of the view as shown in the picture below.Cutting direction...You can select a curve to indicate the cutting direction.5-Axis Planar Finishing6Lab: Planar Finishing6 5-Axis Planar FinishingThe Planar finishing toolpath is identical to the 3-Axis strategy. You can use it to machinelarge parts using ball-end or flat tools. The 5-Axis strategy offers the advantage that the toolis always normal to the surface machined or some angle inclined from normal.With the 5-Axis strategy, you can also use an inclined tool to avoid having to mill with theend of the tool tip. Use a tool offset angle [g 3-10] to make sure that the tool inclination iskept constant with respect to surface normals.Tool offset angle1 Inclination Angle2 Normal3 Tool4 SurfaceExample of a 5-Axis Planar Finishing toolpath:6.1 Lab: Planar FinishingThe goal of this lab is to show you how to implement planar finishing using related Objectives...parameters.65-Axis Planar Finishing Lab: Planar Finishing(PC) <Installation directory>: \workncxx\surface\assembly 1. Open the workzone called "Assembly". 2. Create lists of surfaces to machine and implement this strategy with differentparameters.Tool normal to Surface:Tool offset:Part required...Instructions...Z-Level Finishing - Blade Machining Lab: Z-Level Finishing - Blade Machining77Z-Level Finishing - Blade MachiningThe 5-Axis "Z-Level Finishing" toolpath allows you to machine by level parts like turbine blades - as in 3-Axis - with the advantage that all undercut areas of the part are machined too.7.1 Lab: Z-Level Finishing - Blade MachiningThe goal of this lab is to illustrate 5-Axis Z-Level Finishing using related parameters.(PC) <Installation directory>: \workncxx\surface\blades 1. Open the workzone called "Blade machining". 2. Apply this strategy and try various parameters.Objectives... Part required... Instructions...5-Axis Parallel to Curve Lab: 5-Axis Parallel to Curve885-Axis Parallel to CurveThis toolpath is similar to "3D Drive Curve Finishing" in 3-Axis. With the 5-Axis strategy, the tool is always normal to the surface being machined. Most specific parameters are the same as in the 3-Axis strategy. However, you can impose a maximum head rotation angle.NOTEContext SurfacesYou do not need to use context surfaces with this toolpath. If a surface is in undercut along the trajectory, it will not be machined.8.1 Lab: 5-Axis Parallel to CurveThe goal of this lab is to illustrate 5-Axis Parallel to Curve Machining using related parameters.(PC) <Installation directory>: \workncxx\surface\turbine_training 1. Open the workzone called "turbine_training". 2.Create a toolpath to machine the lateral side of the part, as shown in both picturesbelow. Start by creating the toolpath using a machining window and check the results.1: Guide curve2: Undercut area machinedObjectives...Part required... Instructions...5-Axis Perpendicular to Surface9Programming 5 Axis Perpendicular to Surface9 5-Axis Perpendicular to SurfaceThe "5-Axis Perpendicular to surface" strategy is used to quickly rough-machine parts made of many curved surfaces such as bumpers. Machining is made between two curves.WorkNC creates a ruled surface between both curves and creates a toolpath with respect to the normals of this surface projected on to the part.9.1 Programming 5 Axis Perpendicular toSurfaceProgramming a 5-Axis Perpendicular to Surface toolpath mainly consists in defining each of the following elements:1. two curves which will be used by WorkNC to create a ruled surface,2. the surfaces to machine,3. the stepover value,4. the maximum depth value and5. the view, which will be used to define which side you want to be machined.We are going to use the following bumper as an example:Bumper ExampleDefining two curves...It is important that you correctly define the curves that will serve as guide curves since theyare used to define the ruled surface. Normals will be oriented in accordance with this surface.If we consider our example, you could define curves on each side of the bumper. Seecurves 1 and 2 in the picture below:9 5-Axis Perpendicular to SurfaceProgramming 5 Axis Perpendicular to SurfaceDrive Curves for Perpendicular to SurfaceSurfaces to machineNow that you have defined the drive curves, you must indicate the surfaces that you want tobe machined. This is done with a surface list and surface group that you then select in theMachining zone parameters. In our example, you can select all part surfaces.Perpendicular to Surface - Surface SelectionStepover valueDefine a stepover value.5-Axis Perpendicular to Surface9Programming 5 Axis Perpendicular to SurfacePerpendicular to Surface - Stepover ValueMaximum depth valueThe maximum depth value is similar to a machining plane. It is used to avoid machining the inner part of the other side:Example: If you define a maximum depth value which is too big, you will obtain the following:Perpendicular to Surface - Maximum DepthAs you can see the tool machines the opposite side of the part.Machining ViewDefine a view which is above the part and covers all surfaces to machine:9 5-Axis Perpendicular to SurfaceProgramming 5 Axis Perpendicular to SurfacePerpendicular to Surface - Machining ViewThe final result should look like the following:Perpendicular to Surface - Final Result5-Axis Normal to SurfaceProgramming 5 Axis Perpendicular to Surface10105-Axis Normal to SurfaceThis toolpath is generally used for engraving and is similar to the 3-Axis toolpath On-Curve Engraving. It has the advantage that the tool position is always normal to the surfaces being machined or some angle inclined from normal to surface. No matter the surface inclination, the depth of the groove is kept constant.Curves to machine are prepared in the CAD environment of WorkNC.When defining curves in the CAD environment of WorkNC, do not forget to merge them.The inclination of the tool against the normals of the surface is defined by the forward offset angle:105-Axis Normal to Surface Lab: Normal to Surface5-Axis Normal to Surface: Forward Offset AngleSee Also...• Selection of the change of direction in corners [g 3-8] • Tool Offset Angle [g 3-10]10.1 Lab: Normal to SurfaceThe goal of this lab is to illustrate 5-Axis Normal to Surface Machining using related parameters.(PC) <Installation directory>: \workncxx\surface\5_axis_training 1. Open the workzone called "5_axis_training". 2. Create a toolpath using the "engraving" curve.Objectives...Part required... Instructions...Grooves 11 11 GroovesThis toolpath is designed to machine complex grooves that are not accessible in 3-Axis. The cutter is always normal to the surface at the bottom of the groove and requires one or twocurves to define the groove. This strategy can be used to rough and finish grooves. It isparticularly adapted to machine door or window rubber profiles.You can machine grooves with a constant or variable width. Use the specific parameters todefine the groove to machine.11 GroovesGroove DefinitionGrooves11Open groove example1: Guide curveOne single curve is enough to machine this groove. It must be defined at the bottom of the wall. You must also indicate the width of the groove.NOTEWidth of the grooveIn this case, you can indicate a groove width that is higher than the theoretical width forthe tool to go beyond the part.Closed groove example5-Axis Profiling5-Axis Profile: Surface Contact Detection12125-Axis ProfilingThe Profile strategy is especially useful for part trimming. This toolpath may be redundant with rolling. Use it for trimming when you do not have any side surface on which you can use rolling.Here, Rolling is possible...Here, only Profiling is possible...Surface to machineProfile to machineIt machines with the tool normal to the selected surface and tangent to the curve which itfollows.5-Axis Profile Toolpath1 Curve to Machine2 Selected Surface3 Tool Offset DistanceSee Also...• Selection of the change of direction in corners [g 3-8]12.1 5-Axis Profile: Surface Contact DetectionWith this option, you can machine tangent to a curve and normal to bottom surface while detecting contact with neighboring surfaces.Automatic surface limitation detectionIntroduction Benefits125-Axis Profiling5-Axis Profile: Surface Contact DetectionThis parameter allows you to define a curve to machine which is ‘hidden’ by an overlayed surface in the Z axis of the View or the Machining Zone. If the perpendicular distance in the Z axis between the edge of the overlayed surface and the curve is less than or equal to the defined value then machining will be performed along the edge of the overlayed surface. The following examples illustrate how this parameter works.Surface Group, Surface Guide and Curve to Machine Definitions1 Curve to machine2+3 Surface selected for machining and as the Guide Surface 4 Inclined surface which ‘hides’ the curveNOTECurve to MachineIn order to orientate the cutter correctly, the Curve to Machine must always be on the Guide Surface.In the following example the Detection Width is set to 0.Toolpath with Detection Width Value = 0The toolpath is generated along the curve where the walls are vertical as the cutter can ‘see’ the curve. However, no trajectory is generated parallel the curve where inclined, overlaying surfaces are located.The next example shows the toolpath with the Detection Width set to an intermediate value.Toolpath with Insufficient Detection Width Value5-Axis Profiling Lab: Profiling12In this case the toolpath trajectory partially machines parallel to the curve ‘hidden’ by the inclined surfaces. The whole section of the curve ‘hidden’ by the inclined surfaces is not machined because the Detection Width value is too small.In the following example the Detection Width value is sufficient to machine parallel to the whole section of the curve which is masked by the inclined surfaces.Toolpath with Sufficient Detection Width Value to Machine the Complete CurveZ Axis View of the ToolpathThe above screenshot shows how the cutter machines parallel to the curve and against the edge of the overlying surface.12.2 Lab: ProfilingThe goal of this lab is to illustrate Profiling using related parameters.(PC) <Installation directory>: \workncxx\surface\part_ladder 1. Open the workzone called "part_ladder". 2. Create toolpaths by following the profile below.1. Surface to select for profiling2. Guide curve to select in order to complete the toolpathTo generate this toolpath and obtain results, you need to specify parameters in a very precise way.Which conclusion can you draw when comparing the obtained result and the rolling toolpath? Do you think you could have used Profiling?Objectives... Part required... Instructions...。
五轴联动加工中心操作与基础编程 第六章 多轴数控加工技术
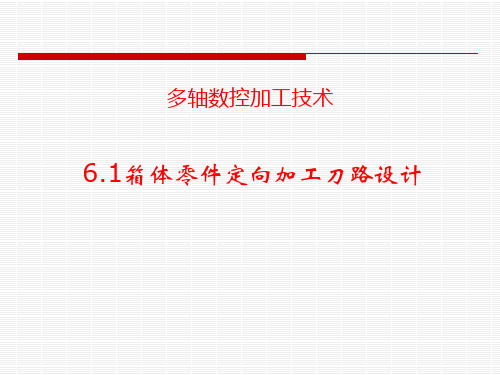
处理等过程进行评价
4.能针对程序中的错误,分析
5.进行本情境工作学习的总结 出错的可能原因,并提出改进意 见
加工仿真检查的类别
1. CAM软件内嵌的仿真检查功能模块 通常可进行线架形式和3D实体形式的仿真验证检查。实体仿真用 于加工结果的直观检查,而线架仿真用于刀路轨迹的细致分析。
2.第三方开发的专业仿真检查软件
刀路程序的优化与调整
曲面加工NC输出的过滤控制
刀路程序的优化与调整
曲面加工大程序输出的分割控制
1)人工分割 注意程序头尾,重新添加提刀和下刀、加刀长补偿、关 停主轴和冷却液等指令。重复小但易出错。 2)刀路分割 调整刀路加工区间范围。包括深度分解、重构边界或调 整边界余量大小。可能有重复但不易出错。
由CAM软件与机床厂家之外的第三方所开发的仿真软件 可面向CAM编制的NC程序,能检查后置的合理性
3.机床厂家开发的在机仿真检查功能模块 作为功能模块内嵌在数控机床控制软件中的在机仿真检查 大多都只能提供线架形式的仿真,只有使用PC-NC及Windows系 统的机床才有3D实体仿真。 在机仿真与机床的实际运动相配合,真实可信度最高。
方法3:使用平行到曲面五轴刀路方法,刀路切削方式参数参照图示设置。
五轴定向加工的CAM刀路设计
六、前侧矩形槽锥壁面五轴加工的刀路设计。
方法3:使用平行到曲面五轴刀路方法,刀轴控制参数参照图示设置。
综合数控加工及工艺应用
单元六 6.2程序仿真检查及优化
单元学习任务与目标
单元学习任务பைடு நூலகம்
单元学习目标
1.学习基于NC程序的仿真检 1.熟悉基于NC程序仿真检查软
CAM内嵌刀路仿真查错不出的案例之二
三轴联动斜向提刀致撞刀,旧版CAM仿真未检出错误!
ug五轴编程教程

ug五轴编程教程五轴编程是机器人技术中非常重要的一部分,它允许机器人在三个平面上进行运动,并且可以通过旋转来改变工具的方向。
在本教程中,我们将学习如何编写五轴编程来控制机器人的动作。
1. 建立工作坐标系在编程之前,我们需要先建立一个工作坐标系。
这个坐标系可以是机器人手臂能够操作的空间范围。
通常情况下,这个坐标系由机器人的基座、手臂和工具构成。
我们需要确定坐标系的原点,以及三个平面的方向。
2. 设定起始位置机器人需要一个起始位置来开始工作。
这个位置可以根据实际需求来设定,比如机器人手臂的位置、工具的方向等。
起始位置一般由坐标值表示,在编程中使用坐标值来设定起始位置。
3. 确定目标位置在编程中,我们通常需要指定一个目标位置,让机器人移动到这个位置。
目标位置可以是一个具体的坐标值,也可以是一个相对于起始位置的偏移量。
根据实际需求来确定目标位置。
4. 编写运动指令一旦我们确定了起始位置和目标位置,我们就可以开始编写运动指令。
这些指令告诉机器人应该如何移动,以及移动的速度和加速度。
编程语言中通常提供了一些指令来实现这些功能,比如直线插补、圆弧插补等。
5. 调试和优化编写完运动指令后,我们需要对程序进行调试和优化。
这包括检查程序中的错误,修改参数以获得更好的运动效果。
通常情况下,我们可以通过机器人模拟器来模拟程序的运行情况,并进行调试和优化。
总结:五轴编程是一项复杂而重要的任务,它允许机器人在三个平面上进行运动,并进行工具方向的调整。
通过建立工作坐标系、设定起始位置、确定目标位置、编写运动指令以及进行调试和优化,我们可以实现机器人的精确控制。
UG五轴编程教程课件成总专业叶轮

UG五轴编程教程课件成总专业叶轮目录一、UG软件简介及安装配置 (3)1. UG软件的发展历程和特点 (4)2. 软件安装与配置要求 (5)3. 用户界面及主要功能模块介绍 (5)二、基础编程概念与技能 (6)1. 编程基础概念解析 (8)1.1 编程定义及作用 (9)1.2 编程与CAD/CAM关系 (10)1.3 数控机床简介 (12)2. 技能要点掌握 (13)2.1 数控加工基本流程了解 (14)2.2 刀具选择及参数设置技巧 (15)2.3 加工工艺路线规划方法 (16)三、UG五轴编程入门 (17)1. 五轴加工概述及优势分析 (20)2. 五轴加工坐标系设置与转换方法 (21)3. 五轴联动数控机床操作界面介绍 (22)4. 五轴编程基本步骤与流程 (23)四、叶轮加工技术要点解析 (24)1. 叶轮结构特点及加工要求 (26)2. 叶轮加工工艺流程规划 (27)3. 专用工具与夹具选择及使用方法 (28)4. 加工过程中的注意事项与常见问题解决方案 (29)五、UG五轴编程进阶技巧与案例实战 (31)1. 编程技巧提升 (32)1.1 优化编程路径,提高加工效率 (33)1.2 复杂曲面加工策略应用实例分享 (34)1.3 刀具路径优化与调整方法 (36)2. 案例实战演练 (37)2.1 实例一 (38)2.2 实例二 (39)2.3 实例三 (40)六、高级功能拓展与探索 (40)1. 高级功能介绍及应用场景分析 (42)2. 拓展模块学习与探索方法建议 (43)3. 行业发展趋势预测与展望 (44)七、课程总结与复习要点 (46)1. 课程重点内容回顾与总结 (47)2. 复习要点提示及学习建议 (48)一、UG软件简介及安装配置UG(Unigraphics)是一款由美国UGS公司推出的强大的CADCAMCAE高端软件,广泛应用于汽车、航空航天、机械、电子等工程领域。
作为一款集成化程度极高的软件,UG不仅提供了强大的建模功能,还集成了仿真、分析、制造等一系列工具,为用户提供了一个从设计到生产的全生命周期解决方案。
UG五轴编程简单教程
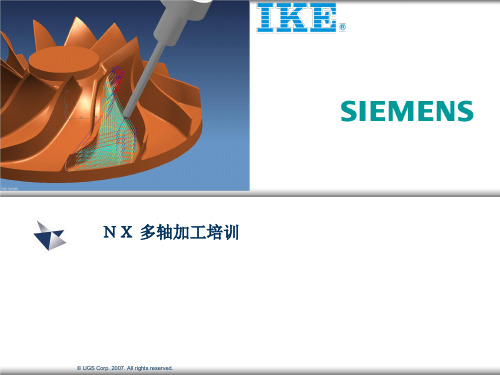
-
© UGS Corp. 2007. All rights reserved.
议程
Tuesday Jan. 22th 9:00 a.m. – 12:00 a.m.
NX加工仿真培训 -CSE仿真 -案例学习
12:00 p.m. – 2:00 p.m. 2:00 p.m. – 5:00 p.m.
休息
NX加工仿真培训 -案例学习 -最佳练习
© UGS Corp. 2007. All rights reserved.
装配加工
实例:m_base\assm_in_m
机床
夹具
刀柄 毛坯
有利于加工中避让, 关联更新,数字化仿真检验各 部分的碰撞的情况,优化加工程式。
© UGS Corp. 2007. All rights reserved.
© UGS Corp. 2007. All rights reserved.
可变轴加工基础 实例:m_base\3_axis\core_profile
m_base\strart\strart_project
零件几何体(part geometry):用于加工的几何体。 检查几何体(check geometry) :检查几何体”使您能够指定刀轨不能干扰的几 何体(如工件壁、岛、夹具等等)。当刀轨遇到检验曲面时,刀具退出,直至到 达下一个安全的切削位置 . 驱动几何体(drive geometry): 用来产生驱动点的几何体。 驱动点( drive point): 从驱动几何体上产生的,将投射到零件几何体上 的 点。
2:00 p.m. – 5:00 p.m.
© UGS Corp. 2007. All rights reserved.
五轴加工中心加工球类带凸台的编程方法

五轴加工中心加工球类带凸台的编程方法
五轴加工中心在加工球类带凸台时,可以通过以下编程方法实现:
1. 定义工件坐标系:首先,需要定义工件坐标系,即球心的坐标以及球的半径等信息。
根据球心坐标和球半径,可以确定球与刀具刀尖的相对位置和距离。
2. 定义刀具坐标系:在五轴加工中心中,刀具坐标系是相对于工件坐标系的坐标系。
刀具坐标系确定了刀具在工件上的位置和姿态。
3. 切削轨迹规划:根据球的形状和凸台的形状,可以确定刀具在球表面的切削路径。
可以使用曲面加工算法来生成刀具的切削轨迹。
同时,还要考虑刀具的刀径补偿和修边等因素。
4. 编写五轴刀具路径程序:根据切削轨迹规划的结果,编写五轴刀具路径程序。
路径程序中需要包含刀具的坐标变换和切削参数等信息。
5. 模拟和调试:在编写好路径程序后,可以使用模拟软件对刀具路径进行模拟和调试。
通过模拟可以检查刀具路径是否正确,并可以预先发现潜在的干涉问题。
6. 加工实施:将调试好的路径程序加载到五轴加工中心上,进行实际的加工操作。
需要注意的是,在五轴加工中心上加工球类带凸台时,需要考虑切削力和切削热的影响,以避免对工件和刀具造成损害。
此外,还需要合理选择刀具和加工参数,以获得更好的加工效果。
数控五轴xza方向的圆弧编程
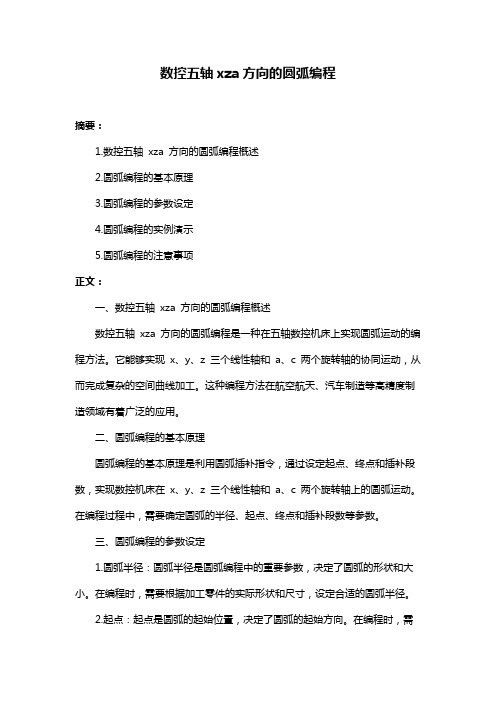
数控五轴xza方向的圆弧编程摘要:1.数控五轴xza 方向的圆弧编程概述2.圆弧编程的基本原理3.圆弧编程的参数设定4.圆弧编程的实例演示5.圆弧编程的注意事项正文:一、数控五轴xza 方向的圆弧编程概述数控五轴xza 方向的圆弧编程是一种在五轴数控机床上实现圆弧运动的编程方法。
它能够实现x、y、z 三个线性轴和a、c 两个旋转轴的协同运动,从而完成复杂的空间曲线加工。
这种编程方法在航空航天、汽车制造等高精度制造领域有着广泛的应用。
二、圆弧编程的基本原理圆弧编程的基本原理是利用圆弧插补指令,通过设定起点、终点和插补段数,实现数控机床在x、y、z 三个线性轴和a、c 两个旋转轴上的圆弧运动。
在编程过程中,需要确定圆弧的半径、起点、终点和插补段数等参数。
三、圆弧编程的参数设定1.圆弧半径:圆弧半径是圆弧编程中的重要参数,决定了圆弧的形状和大小。
在编程时,需要根据加工零件的实际形状和尺寸,设定合适的圆弧半径。
2.起点:起点是圆弧的起始位置,决定了圆弧的起始方向。
在编程时,需要根据加工零件的实际形状和尺寸,设定合适的起点。
3.终点:终点是圆弧的结束位置,决定了圆弧的结束方向。
在编程时,需要根据加工零件的实际形状和尺寸,设定合适的终点。
4.插补段数:插补段数是圆弧编程中的另一个重要参数,决定了圆弧的平滑程度。
在编程时,需要根据加工零件的实际形状和尺寸,设定合适的插补段数。
四、圆弧编程的实例演示假设我们要在x、y、z 三个线性轴和a、c 两个旋转轴上,实现一个半径为50mm 的圆弧运动,起点为(0,0,0),终点为(100,0,0),插补段数为4,可以编写如下圆弧编程代码:```G90 G54 G17 G40 G49G28 G91 Z0G90M6 T1M3 S3000G1 X0 Y0 Z50 F1000G2 X100 Y0 Z0 F1000T2 M8```五、圆弧编程的注意事项1.在编程时,应根据加工零件的实际形状和尺寸,合理设定圆弧半径、起点、终点和插补段数等参数。
五轴数控编程教学-最新教育资料
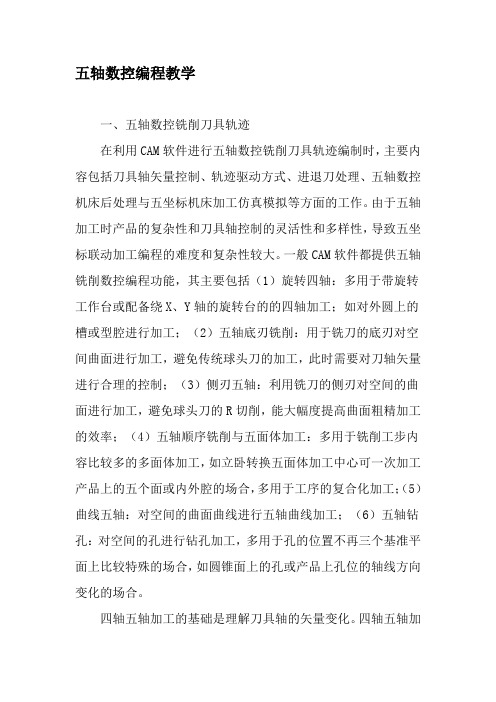
五轴数控编程教学一、五轴数控铣削刀具轨迹在利用CAM软件进行五轴数控铣削刀具轨迹编制时,主要内容包括刀具轴矢量控制、轨迹驱动方式、进退刀处理、五轴数控机床后处理与五坐标机床加工仿真模拟等方面的工作。
由于五轴加工时产品的复杂性和刀具轴控制的灵活性和多样性,导致五坐标联动加工编程的难度和复杂性较大。
一般CAM软件都提供五轴铣削数控编程功能,其主要包括(1)旋转四轴:多用于带旋转工作台或配备绕X、Y轴的旋转台的的四轴加工;如对外圆上的槽或型腔进行加工;(2)五轴底刃铣削:用于铣刀的底刃对空间曲面进行加工,避免传统球头刀的加工,此时需要对刀轴矢量进行合理的控制;(3)侧刃五轴:利用铣刀的侧刃对空间的曲面进行加工,避免球头刀的R切削,能大幅度提高曲面粗精加工的效率;(4)五轴顺序铣削与五面体加工:多用于铣削工步内容比较多的多面体加工,如立卧转换五面体加工中心可一次加工产品上的五个面或内外腔的场合,多用于工序的复合化加工;(5)曲线五轴:对空间的曲面曲线进行五轴曲线加工;(6)五轴钻孔:对空间的孔进行钻孔加工,多用于孔的位置不再三个基准平面上比较特殊的场合,如圆锥面上的孔或产品上孔位的轴线方向变化的场合。
四轴五轴加工的基础是理解刀具轴的矢量变化。
四轴五轴加工的关键技术之一是刀具轴的矢量(刀具轴的轴线矢量)在空间是如何发生变化的,而刀具轴的矢量变化是通过摆动工作台或主轴的摆动来实现的。
对于矢量不发生变化的固定轴铣削场合,一般用三轴铣削即可加工出产品,五轴加工关键就是通过控制刀具轴矢量在空间位置的不断变化或使刀具轴的矢量与机床原始坐标系构成空间某个角度,利用铣刀的侧刃或底刃切削加工来完成。
刀具轴的矢量变化控制一般有固定矢量、曲面法线、固定点、直线导动、直纹面导动、刀具轨迹投影、点位与任意矢量连续插补等方式。
UnigraphicsNX软件在刀具轴矢量控制方面表现得更加灵活,尤其是其提供的插补刀具轴矢量控制和顺序铣削编程功能能够使得用户很轻松得完成所期望的五坐标联动铣削刀具轨迹目标。
五轴联动加工中心操作与基础编程 第二章 五轴联动加工中心操作与基础编程

顺旋为+
逆旋为 -
急停按钮 倍率选择
运动控制---MDI方式操作
当前模态
➢操作方式:
➢操作执行: 开始 暂停
程序编辑时的快捷键
程序编辑修改时可先进行块定义后利用进行块复制、块 粘贴、块移动和块删除的功能实施大范围程序的编辑操 作。
跳段:对行前加“/”的程序行,可通过选择跳段“有效或 无效”控制该行是否执行。
RTCP:W-M变换
轨迹插补 及通道控制器
插补与 运动控
机电 动力
动态补偿
制算法 库接口
学模 型及 力热 补偿
纳米插补 及速度平滑
轴运动控制
实时多
插补与运 动控制
模型
64位运算
高速总线 数据交换
实时多任务 调度
任务的 通用调
度接口
多处理器及实时多任务操作系统软硬件平台
功能类别
CNC功能
CNC编程功能 刀具补偿功能
可在系统界面内建立特性坐标系,然后在程序中使用G68.1指令来选择使 用哪一个特性坐标系。
法向进退刀控制
HNC-848数控系统在通过G68.1使用特性坐标系的基础上,可以指令G53.1 来控制刀具轴摆动到与特性坐标系Z轴平行的方向,从而可实现法向进退 刀控制。
刀具自动测量 (选配)
➢ 工件测量
➢ 刀具测量
➢ HNC-848的自动测量功能
软件界面和菜单操作 机械操作面板功能项
基本操作方法 常见故障处置
程序输入 U盘插口
图文信息 主显示区
程序 显示区 菜单区 菜单键
信息 显示区
✓程 序 操 作 管 理 界 面
加工中心五轴UG编程入门
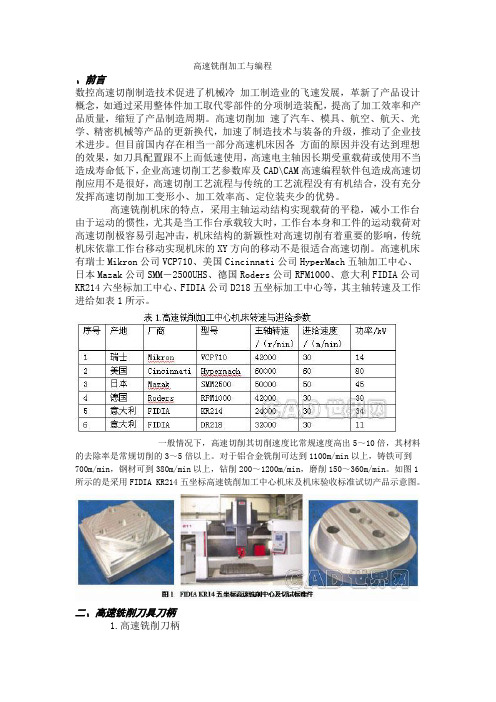
高速铣削加工与编程、前言数控高速切削制造技术促进了机械冷加工制造业的飞速发展,革新了产品设计概念,如通过采用整体件加工取代零部件的分项制造装配,提高了加工效率和产品质量,缩短了产品制造周期。
高速切削加速了汽车、模具、航空、航天、光学、精密机械等产品的更新换代,加速了制造技术与装备的升级,推动了企业技术进步。
但目前国内存在相当一部分高速机床因各方面的原因并没有达到理想的效果,如刀具配置跟不上而低速使用,高速电主轴因长期受重载荷或使用不当造成寿命低下,企业高速切削工艺参数库及CAD\CAM高速编程软件包造成高速切削应用不是很好,高速切削工艺流程与传统的工艺流程没有有机结合,没有充分发挥高速切削加工变形小、加工效率高、定位装夹少的优势。
高速铣削机床的特点,采用主轴运动结构实现载荷的平稳,减小工作台由于运动的惯性,尤其是当工作台承载较大时,工作台本身和工件的运动载荷对高速切削极容易引起冲击,机床结构的新颖性对高速切削有着重要的影响,传统机床依靠工作台移动实现机床的XY方向的移动不是很适合高速切削。
高速机床有瑞士Mikron公司VCP710、美国Cincinnati公司HyperMach五轴加工中心、日本Mazak公司SMM-2500UHS、德国Roders公司RFM1000、意大利FIDIA公司KR214六坐标加工中心、FIDIA公司D218五坐标加工中心等,其主轴转速及工作进给如表1所示。
一般情况下,高速切削其切削速度比常规速度高出5~10倍,其材料的去除率是常规切削的3~5倍以上。
对于铝合金铣削可达到1100m/min以上,铸铁可到700m/min,钢材可到380m/min以上,钻削200~1200m/min,磨削150~360m/min。
如图1所示的是采用FIDIA KR214五坐标高速铣削加工中心机床及机床验收标准试切产品示意图。
二、高速铣削刀具刀柄1.高速铣削刀柄由于高速切削时,主轴、刀柄及刀具在高速旋转情况下,较小的偏心就会产生较大的离心力,由振动引起产品的质量、降低主轴和刀具的使用寿命。
数控五轴xza方向的圆弧编程
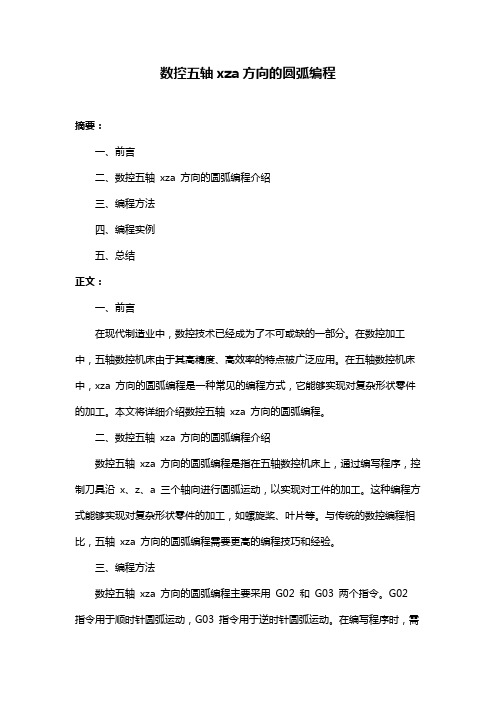
数控五轴xza方向的圆弧编程摘要:一、前言二、数控五轴xza 方向的圆弧编程介绍三、编程方法四、编程实例五、总结正文:一、前言在现代制造业中,数控技术已经成为了不可或缺的一部分。
在数控加工中,五轴数控机床由于其高精度、高效率的特点被广泛应用。
在五轴数控机床中,xza 方向的圆弧编程是一种常见的编程方式,它能够实现对复杂形状零件的加工。
本文将详细介绍数控五轴xza 方向的圆弧编程。
二、数控五轴xza 方向的圆弧编程介绍数控五轴xza 方向的圆弧编程是指在五轴数控机床上,通过编写程序,控制刀具沿x、z、a 三个轴向进行圆弧运动,以实现对工件的加工。
这种编程方式能够实现对复杂形状零件的加工,如螺旋桨、叶片等。
与传统的数控编程相比,五轴xza 方向的圆弧编程需要更高的编程技巧和经验。
三、编程方法数控五轴xza 方向的圆弧编程主要采用G02 和G03 两个指令。
G02 指令用于顺时针圆弧运动,G03 指令用于逆时针圆弧运动。
在编写程序时,需要根据零件的形状和加工要求,选择合适的指令。
编程时,还需要考虑刀具的半径补偿和长度补偿。
半径补偿用于补偿刀具直径引起的加工误差,长度补偿用于补偿刀具磨损引起的加工误差。
在编写程序时,需要根据刀具的实际参数进行设置。
四、编程实例下面以一个简单的数控五轴xza 方向的圆弧编程实例进行说明。
假设我们要加工一个直径为100mm、高度为50mm 的圆柱形零件,刀具的直径为20mm。
1.首先,开启数控机床,并设置好刀具的半径补偿和长度补偿。
2.编写G00 指令,将刀具移至加工起点。
3.编写G02 指令,进行顺时针圆弧运动,加工直径为100mm 的圆弧。
4.编写G01 指令,进行直线运动,加工高度为50mm 的部分。
5.编写G02 指令,进行逆时针圆弧运动,加工直径为100mm 的圆弧。
6.编写G00 指令,将刀具移至加工终点。
五、总结数控五轴xza 方向的圆弧编程是一种常见的编程方式,能够实现对复杂形状零件的加工。
- 1、下载文档前请自行甄别文档内容的完整性,平台不提供额外的编辑、内容补充、找答案等附加服务。
- 2、"仅部分预览"的文档,不可在线预览部分如存在完整性等问题,可反馈申请退款(可完整预览的文档不适用该条件!)。
- 3、如文档侵犯您的权益,请联系客服反馈,我们会尽快为您处理(人工客服工作时间:9:00-18:30)。
1刀轴控制-朝向直线
朝向直线: 刀背指向某 条直线产生 刀具轨迹, 用于4轴加工
朝向直 线
1刀轴远离直线-案例1
零件 切削区 域 驱动曲线: 刀具沿着曲 线走 远离直线:刀 尖指向直线
1刀轴远离直线-案例1
分层切削
1刀轴远离直线-案例1
如果导轨异常,则不 选择部件 零件和驱 动面均选 择侧壁面
生成刀具轨迹,刀 轴偏摆量越小,加 工效率越高。
2刀轴插补-案例2
旋转刀轨,获得各个槽的加工程序, 两个刀轨要接起,否则会有残料
2刀轴插补-案例3
3刀轴侧刃驱动1
部件几何引导刀尖 运动,驱动面引导 刀具侧刃运动 部件选 择底面
驱动面 为周边 刀轴
3刀轴侧刃驱动1
切削方向。 选择驱动面的开始位置 决定切削起点位置,所 以把这个零件的一侧壁 切开,希望刀具从中间 进刀在 刀轴方向。
构造辅助面, 使刀路延伸一段距离 辅助面构造: 扩大—分割—抽取
刀具移动方向
4刀轴相对矢量1
正侧倾角:沿刀具移动 方向看刀具右倾
负侧倾角:沿刀具移动 方向看刀具左倾
4刀轴相对矢量2
部件选 择整个 零件 驱动面 选择叶 片型面
4刀轴相对矢量2
螺旋走刀 提高加工 表面质量
4刀轴相对矢量2
四轴加工,只 有A轴转动,没 有B轴和C轴
4刀轴相对矢量2
五轴加工,五轴 联动程序
5外形轮廓铣1
创建多轴操作: 外形轮廓铣
部件选 择整个 零件 底面选择 零件槽内 底面
5外形轮廓铣1
5外形轮廓铣1
宽度分层
深度分层
5外形轮廓铣2
5外形轮廓铣2
设置切入切出
5外形轮廓铣3
扫掠建模辅助底面
5外形轮廓铣3
复制一个零件 用于辅助造型
5外形轮廓铣3
删除面, 处理拐角
5外形轮廓铣3
主讲:Gavin liu QQ:545421169
五轴编程学习提要(30H)
学习目的: 了解并会使用UG软件对复杂零件进行五 轴编程
学习内容: 1、刀轴控制—远离点,朝向点 远离直线,朝向直线。(4H) 2、刀轴控制—插补(4H) 3、刀轴控制—侧刃驱动(4H) 4、刀轴控制—相对矢量(4H) 5、外形轮廓加工(2H) 6、综合件练习(4H) 6、后处理构造及VERICUT加工仿真(8H)
沿驱动面的 法向投影产 生刀轨到零 件面上 远离直线:刀 尖指向直线
1刀轴远离直线-案例1
分层切削
1刀轴远离直线-案例2
当零件表面较复杂时,无法选 取加工驱动表面,必须做辅助 面.驱动面可以不是零件面 平行刀轨 粗加工
零部件
驱动面
远离直线:刀 尖指向直线
1刀轴远离直线-案例2
选择单个 曲面为驱 动面
以上条件 时,投影 矢量要设 置为垂直 于驱动, 不能用刀 轴
3刀轴侧刃驱动3
分层切削
3刀轴侧刃驱动3
控制进退刀 和移刀动作
4ቤተ መጻሕፍቲ ባይዱ轴相对矢量1
意义: 一、四轴加工 二、有效避让夹具体。
部件选 择整个 零件 驱动面 选择上 表面
4刀轴相对矢量1
正前倾角:刀具拉着走
刀具移动方向
负前倾角:刀具铲着走
2刀轴插补-案例2
箭头朝向表面 外侧,如果箭 头朝向内侧就 点击材料反向, 使其朝向外侧
2刀轴插补-案例2
根据需要编辑各点的刀轴方向,也可以在 需要的地方添加新的刀轴控制点
视图方向定义矢量。刀轴控制不需要很精确,只要不干涉,机床能实现就 可以了,所以这是定义刀轴方向非常方便的功能。
2刀轴插补-案例2
1刀轴控制-远离点
创建多轴操作
零件
驱动面
远离点
1刀轴控制-远离点
远离点:刀 尖指向某个 点产生刀具 轨迹,用于5 轴加工
远离点
1刀轴控制-朝向点
朝向点:刀 背指向某个 点产生刀具 轨迹,用于5 轴加工
朝向点
1刀轴控制-远离直线
离开直线: 刀尖指向某 条直线产生 刀具轨迹, 用于4轴加工
远离直 线
在曲面上构建 曲线
2刀轴插补-案例2
辅 助 造 型
旋转曲线构建曲面
在旋转曲面上构建 曲线网格
构建网格曲面
如果直接在原 来的曲面上构 建曲线会出现 异常现象
利用网格曲面 作为驱动面能 够获得光顺的 刀路
面的质量 决定刀轨 的质量
2刀轴插补-案例2
不指定部件, 利用检查体 防止过切碰 撞 如果曲面质量 不好,指定部 件后得到的刀 轨质量不好
平行刀轨 精加工
1刀轴朝向点-案例3
零件
驱动面
朝向点
1刀轴朝向点-案例3
调整曲面百分比,使加工区域减小,获 得光滑刀轨 这 两 处 刀 具 干 涉, 刀 轨 下 不 去
2刀轴插补-案例1
不需要指 定部件
驱动面
修改刀 具矢量 方向
2刀轴插补-案例1
设 置 切 入 切 出
2刀轴插补-案例2
辅 助 造 型
4刀轴相对矢量3
部件选 择整个 零件
驱动面 选择叶 片型面
4刀轴相对矢量3
4刀轴相对矢量3
进退刀控制
4刀轴相对矢量3
部件和驱动 面均选择辅 助曲面
4刀轴相对矢量3
4刀轴相对矢量3
固定轴切削叶片 端面
4刀轴相对矢量3
部件选 择整个 零件
切削区域 选择端面 部分
4刀轴相对矢量3
4刀轴相对矢量3
3刀轴侧刃驱动1
分层切削
3刀轴侧刃驱动2
部件选 择底面
驱动面 为周边 刀轴
3刀轴侧刃驱动2
切削方向。 刀轴方向。
3刀轴侧刃驱动2
轴向分层
3刀轴侧刃驱动2
只要底部 产生一条 刀轨,此 处设置为0
如果不是0 会有多余的 刀轨
放大
3刀轴侧刃驱动3
底面作为检查 面,避免过切 碰撞 部件和驱动面 均选择侧壁