氧化铝生产工艺流程简介
氧化铝生产工艺流程

氧化铝生产工艺流程氧化铝(Al2O3)是一种重要的无机化合物,广泛应用于陶瓷、耐火材料、磨料、催化剂等领域。
氧化铝的生产工艺流程通常包括以下几个步骤:矿石的选矿、氧化铝的制备和精炼。
下面将详细介绍氧化铝的生产工艺流程。
一、矿石的选矿氧化铝的主要原料是铝土矿(bauxite)。
矿石的选矿过程是将含铝矿石从其他杂质中提取出来,使其含铝量达到一定标准。
矿石的选矿流程包括以下几个步骤:矿石碎磨、物理选矿、化学选矿和浸出。
1.矿石碎磨:将原矿经过破碎设备进行粗碎和细碎,使其达到适合后续处理的粒度要求。
2.物理选矿:利用物理性质的差异,采用重选方法分离矿石中的杂质。
常用的重选设备有重介分离机、离心分选机和震动筛等。
3.化学选矿:通过化学方式改变矿石中各种成分的化学性质,使其在溶液中呈现不同的溶解度,从而达到分离杂质的目的。
常用的化学选矿方法有酸洗、碱洗和氧化等。
4.浸出:将经过选矿的矿石用稀硫酸浸出,使铝氧化物溶解在浸出液中。
二、氧化铝的制备经过选矿的矿石中含有一定数量的铝氧化物(Al2O3),但还存在有机质、杂质和无机结合物等。
所以,经过矿石的选矿后还需要进行炼制和制备氧化铝,常用的工艺流程有碳酸钠法、铝盐法和氨法等。
1.碳酸钠法:将经过选矿的矿石和合适比例的碳酸钠与水一起混合,并加热,使其反应生成碳酸盐。
然后,将碳酸盐与酸进行反应,使铝氧化物在溶液中析出。
最后,将沉淀分离出来,通过烘干和高温煅烧得到氧化铝。
2.铝盐法:将经过选矿的矿石先进行煅烧,使其进行脱水。
然后,将矿石与酸反应,生成铝酸盐。
再通过晶体分离和干燥得到氧化铝。
3.氨法:将经过选矿的矿石煅烧,使其脱除水分。
然后,将矿石与氧化铝碳酸铵溶液进行反应,生成氨铝酸盐。
再通过结晶和煅烧得到氧化铝。
三、氧化铝的精炼经过上述制备后得到的氧化铝还存在一定的杂质,如硅酸盐、铁、钠和镁等。
因此,还需要进行氧化铝的精炼,提高其纯度。
常用的精炼方法有硫酸法、溶剂萃取法和氟化法等。
氧化铝生产工艺技术规程

1氧化铝生产工艺流程1.1工艺流程概述我厂氧化铝生产采用拜尔法。
矿山来的铝土矿在卸矿站卸入矿仓后转运到均化库布料。
石灰石经竖式石灰炉煅烧后送到石灰仓,用于石灰消化和原料磨配料。
均化库内的碎铝土矿用双斗轮取料机横向取料后经皮带运输机送至磨头仓。
铝土矿、石灰和蒸发来的循环母液按一定配比进入由棒、球二段磨和水旋器组成的磨矿分级系统。
分级溢流(原矿浆)进入原矿浆槽,然后泵送至高压溶出工序的溶出前槽。
溶出前槽内矿浆用G E H O泵送入溶出系统。
首先由单套管和压煮器组成的十级预热器预热,再用约60巴新蒸汽间接加热压煮器内矿浆到溶出温度,保温溶出45-60分钟,经十级自蒸发器闪蒸降温后,溶出矿浆用赤泥洗液稀释。
闪蒸产生的二次蒸汽用于十级预热,新蒸汽冷凝水经闪蒸成6巴蒸汽并入全厂低压蒸汽管网,新蒸汽不含碱冷凝水返回热电厂。
二次蒸汽冷凝水及新蒸汽含碱冷凝水送热水站。
稀释矿浆在Ф40m单层平底沉降槽内进行液固分离,底流进入洗涤沉降槽进行三次赤泥反向洗涤,再送入赤泥过滤机进行过滤洗涤,热水分别加入过滤机和末次洗涤,滤饼经螺旋输送进入再浆化槽,用离心泵向G E H O泵喂料,然后压送到赤泥堆场进行干法堆存。
分离沉降槽中添加由絮凝剂工序制备好的合成絮凝剂和天然絮凝剂。
一次、二次洗涤槽加合成絮凝剂。
分离沉降槽溢流经泵送粗液槽,再用泵送往385m2凯利式叶滤机或226m2立式叶滤机进行控制过滤,过滤时加入助滤剂(石灰乳或苛化渣)。
滤饼送二次洗涤槽,精液送板式热交换器。
精液经三级板式热交换器与分解母液和冷却水进行热交换冷却到设定温度。
再与种子过滤滤饼(晶种)在晶种槽内混合后用晶种泵送至由13台平底机械搅拌槽组成的分解系列的首槽(1#和2#槽)。
经连续分解后从11#(或10#)槽顶用立式泵抽取分解浆液去进行旋流分级,分级前加入部分过滤母液稀释,分级溢流进12#(或11#)分解槽。
底流再用部分母液冲稀后自压至产品过滤。
分解末槽(12#或11#)的分解浆液从槽上部出料自流至种子过滤机,滤饼用精液冲入晶种槽,滤液入锥形母液槽。
氧化铝的生产工艺流程
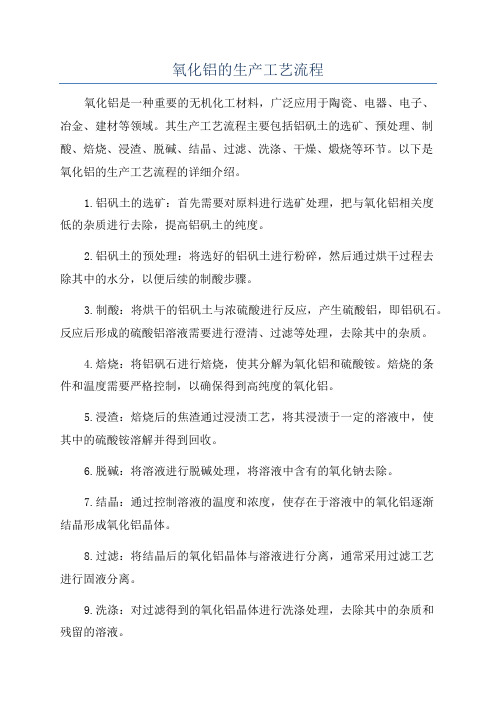
氧化铝的生产工艺流程氧化铝是一种重要的无机化工材料,广泛应用于陶瓷、电器、电子、冶金、建材等领域。
其生产工艺流程主要包括铝矾土的选矿、预处理、制酸、焙烧、浸渣、脱碱、结晶、过滤、洗涤、干燥、煅烧等环节。
以下是氧化铝的生产工艺流程的详细介绍。
1.铝矾土的选矿:首先需要对原料进行选矿处理,把与氧化铝相关度低的杂质进行去除,提高铝矾土的纯度。
2.铝矾土的预处理:将选好的铝矾土进行粉碎,然后通过烘干过程去除其中的水分,以便后续的制酸步骤。
3.制酸:将烘干的铝矾土与浓硫酸进行反应,产生硫酸铝,即铝矾石。
反应后形成的硫酸铝溶液需要进行澄清、过滤等处理,去除其中的杂质。
4.焙烧:将铝矾石进行焙烧,使其分解为氧化铝和硫酸铵。
焙烧的条件和温度需要严格控制,以确保得到高纯度的氧化铝。
5.浸渣:焙烧后的焦渣通过浸渍工艺,将其浸渍于一定的溶液中,使其中的硫酸铵溶解并得到回收。
6.脱碱:将溶液进行脱碱处理,将溶液中含有的氧化钠去除。
7.结晶:通过控制溶液的温度和浓度,使存在于溶液中的氧化铝逐渐结晶形成氧化铝晶体。
8.过滤:将结晶后的氧化铝晶体与溶液进行分离,通常采用过滤工艺进行固液分离。
9.洗涤:对过滤得到的氧化铝晶体进行洗涤处理,去除其中的杂质和残留的溶液。
10.干燥:洗涤后的氧化铝晶体需要进行干燥处理,以去除残留的水分。
11.煅烧:将干燥后的氧化铝晶体进行煅烧,使其变成具有特定晶态结构和物理化学性能的氧化铝颗粒。
以上便是氧化铝的生产工艺流程。
整个工艺流程中,各个环节的控制和操作对于提高氧化铝的纯度、晶态和物理化学性能至关重要。
目前,随着科技的不断进步和工艺的创新,氧化铝的生产工艺也在不断完善和优化,以提高生产效率和产品质量。
氧化铝冶炼工艺流程简介
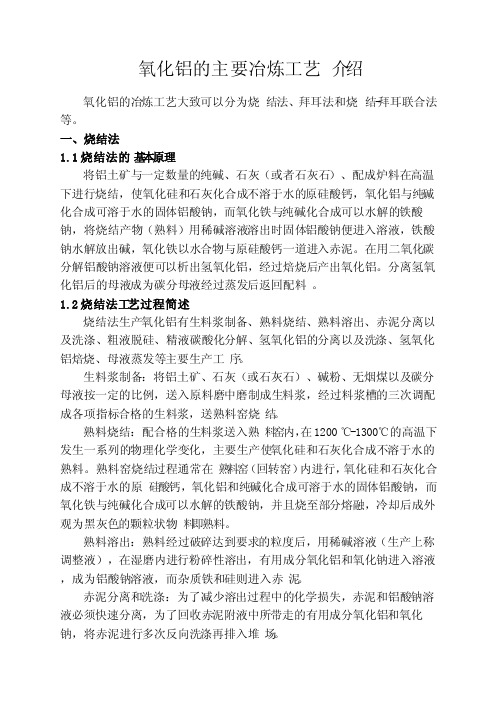
氧化铝的主要冶炼工艺介绍氧化铝的冶炼工艺大致可以分为烧结法、拜耳法和烧结-拜耳联合法等。
一、烧结法1.1烧结法的基本原理将铝土矿与一定数量的纯碱、石灰(或者石灰石)、配成炉料在高温下进行烧结,使氧化硅和石灰化合成不溶于水的原硅酸钙,氧化铝与纯碱化合成可溶于水的固体铝酸钠,而氧化铁与纯碱化合成可以水解的铁酸钠,将烧结产物(熟料)用稀碱溶液溶出时固体铝酸钠便进入溶液,铁酸钠水解放出碱,氧化铁以水合物与原硅酸钙一道进入赤泥。
在用二氧化碳分解铝酸钠溶液便可以析出氢氧化铝,经过焙烧后产出氧化铝。
分离氢氧化铝后的母液成为碳分母液经过蒸发后返回配料。
1.2烧结法工艺过程简述烧结法生产氧化铝有生料浆制备、熟料烧结、熟料溶出、赤泥分离以及洗涤、粗液脱硅、精液碳酸化分解、氢氧化铝的分离以及洗涤、氢氧化铝焙烧、母液蒸发等主要生产工序。
生料浆制备:将铝土矿、石灰(或石灰石)、碱粉、无烟煤以及碳分母液按一定的比例,送入原料磨中磨制成生料浆,经过料浆槽的三次调配成各项指标合格的生料浆,送熟料窑烧结。
熟料烧结:配合格的生料浆送入熟料窑内,在1200℃-1300℃的高温下发生一系列的物理化学变化,主要生产使氧化硅和石灰化合成不溶于水的熟料。
熟料窑烧结过程通常在熟料窑(回转窑)内进行,氧化硅和石灰化合成不溶于水的原硅酸钙,氧化铝和纯碱化合成可溶于水的固体铝酸钠,而氧化铁与纯碱化合成可以水解的铁酸钠,并且烧至部分熔融,冷却后成外观为黑灰色的颗粒状物料即熟料。
熟料溶出:熟料经过破碎达到要求的粒度后,用稀碱溶液(生产上称调整液),在湿磨内进行粉碎性溶出,有用成分氧化铝和氧化钠进入溶液,成为铝酸钠溶液,而杂质铁和硅则进入赤泥。
赤泥分离和洗涤:为了减少溶出过程中的化学损失,赤泥和铝酸钠溶液必须快速分离,为了回收赤泥附液中所带走的有用成分氧化铝和氧化钠,将赤泥进行多次反向洗涤再排入堆场。
氧化铝生产工艺流程

氧化铝生产工艺流程氧化铝是一种重要的工业原料,广泛用于陶瓷、磨料、电子材料等领域。
其生产工艺流程主要包括矿石选矿、氧化铝的制备和氧化铝的精炼三个步骤。
一、矿石选矿氧化铝的主要原料是铝土矿,其主要成分是氧化铝矿石。
矿石选矿是生产氧化铝的第一步,其目的是从矿石中提取出氧化铝。
首先将铝土矿石经过破碎、磨矿等工艺处理,得到粉碎后的矿石。
然后通过重选、浮选等方法,将矿石中的氧化铝和其他杂质进行分离,得到含氧化铝较高的矿石精矿。
二、氧化铝的制备1. 煅烧矿石精矿经过煅烧处理,将其转化为氧化铝。
煅烧是将矿石精矿在高温下进行煅烧,使其发生化学反应,氧化铝矿石中的氢氧化铝转化为氧化铝。
煅烧的温度一般在1000℃以上,煅烧时间根据矿石的性质和工艺要求而定。
2. 碳酸化经过煅烧后的氧化铝矿石,其颗粒度较大,不利于后续的加工和应用。
因此需要进行碳酸化处理,将氧化铝矿石进行粉碎,并与碳酸钠进行反应,生成碳酸铝钠。
然后将碳酸铝钠进行水解,生成氢氧化铝沉淀。
经过过滤、洗涤等工艺处理,得到氢氧化铝产品。
三、氧化铝的精炼1. 氢氧化铝的煅烧将氢氧化铝进行煅烧,使其转化为氧化铝。
煅烧温度一般在1100℃以上,煅烧时间根据产品要求而定。
煅烧后的氧化铝颗粒度较大,需要进行粉碎和分级处理,得到符合要求的氧化铝产品。
2. 氧化铝的提纯经过煅烧后的氧化铝产品中可能还含有一定的杂质,需要进行提纯处理。
常用的方法包括盐酸法、碱法和氧化法等,通过这些方法可以将氧化铝产品中的杂质去除,得到高纯度的氧化铝产品。
以上就是氧化铝生产的主要工艺流程。
通过矿石选矿、氧化铝的制备和氧化铝的精炼三个步骤,可以生产出符合工业需求的氧化铝产品。
随着工艺技术的不断进步,氧化铝生产工艺也在不断优化,以提高产品质量和降低生产成本。
希望通过不断的研究和改进,能够进一步完善氧化铝生产工艺,为工业生产提供更优质的原料。
氧化铝生产工艺

氧化铝生产工艺氧化铝是一种重要的工业原料,广泛应用于陶瓷、建材、电子、化工等领域。
下面我将从原料准备、工艺流程、设备和能耗等方面全面介绍氧化铝的生产工艺。
原料准备:氧化铝主要的原料是含铝矿石,如赤铁矿、高岭土、脱硅白云石等。
此外,还需要使用含碱矿石、氯化铝、铝氧化物等作为助熔剂和助矿剂。
原料在使用前需要经过破碎、磨矿、筛分等工艺处理,以确保原料的颗粒度和成分合格。
工艺流程:氧化铝的生产工艺主要可以分为电解氧化法和氢氧化法两种。
1.电解氧化法:首先,将矿石与碱矿石、助熔剂和助矿剂混合后,在高温电炉中进行熔炼。
熔炼后的铝渣经过冷却和破碎后,得到铝渣粉末。
然后,将铝渣粉末与氯化铝等混合物放入电解槽中,进行电解氧化反应。
在电解槽中,阳极是铝阳极,阴极是石墨或铝带,电解质是熔融氯化铝。
通过施加适当的电压和电流,铝阳极上的氧化铝逐渐析出,并经过相应的处理后得到氧化铝产品。
反应公式如下:2Al(阳极)+3H2O->Al2O3+6H++6e-2.氢氧化法:氢氧化法是一种相对低能耗的生产工艺。
首先,将矿石经过碳酸钠焙烧后得到氧化铝。
然后,将氧化铝与钠氢氧化物溶液反应生成氢氧化铝。
接着,通过煮沸和沉淀处理,得到粗氢氧化铝。
最后,将粗氢氧化铝通过煅烧处理,得到氧化铝产品。
设备:氧化铝的生产设备主要包括熔炼炉、电解槽、沉淀槽等。
其中,熔炼炉一般采用电炉,电解槽为密封结构,以防止电解质的挥发和溢出,沉淀槽为反应容器。
能耗:总结:氧化铝的生产工艺包括电解氧化法和氢氧化法,其中电解氧化法能耗较高,而氢氧化法能耗较低。
原料准备需要对矿石进行破碎、磨矿等处理,设备主要包括熔炼炉、电解槽和沉淀槽。
为了减少能耗,可以采用电能、燃料能的节约措施,并优化工艺参数。
希望通过以上介绍,您对氧化铝的生产工艺有更全面的了解。
氧化铝生产工艺及计算
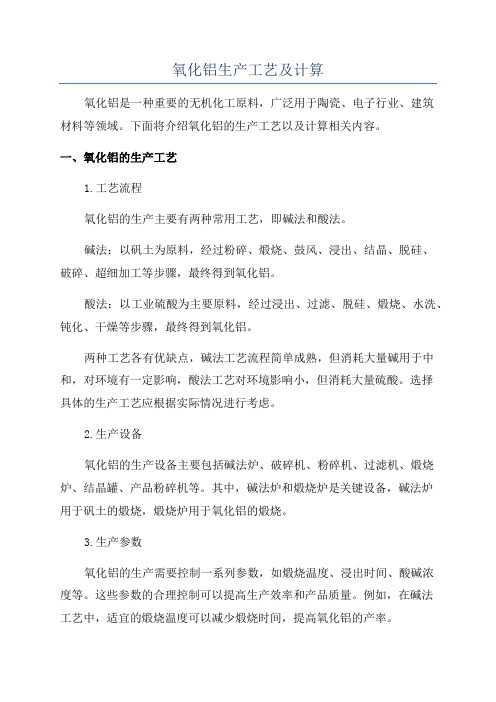
氧化铝生产工艺及计算氧化铝是一种重要的无机化工原料,广泛用于陶瓷、电子行业、建筑材料等领域。
下面将介绍氧化铝的生产工艺以及计算相关内容。
一、氧化铝的生产工艺1.工艺流程氧化铝的生产主要有两种常用工艺,即碱法和酸法。
碱法:以矾土为原料,经过粉碎、煅烧、鼓风、浸出、结晶、脱硅、破碎、超细加工等步骤,最终得到氧化铝。
酸法:以工业硫酸为主要原料,经过浸出、过滤、脱硅、煅烧、水洗、钝化、干燥等步骤,最终得到氧化铝。
两种工艺各有优缺点,碱法工艺流程简单成熟,但消耗大量碱用于中和,对环境有一定影响,酸法工艺对环境影响小,但消耗大量硫酸。
选择具体的生产工艺应根据实际情况进行考虑。
2.生产设备氧化铝的生产设备主要包括碱法炉、破碎机、粉碎机、过滤机、煅烧炉、结晶罐、产品粉碎机等。
其中,碱法炉和煅烧炉是关键设备,碱法炉用于矾土的煅烧,煅烧炉用于氧化铝的煅烧。
3.生产参数氧化铝的生产需要控制一系列参数,如煅烧温度、浸出时间、酸碱浓度等。
这些参数的合理控制可以提高生产效率和产品质量。
例如,在碱法工艺中,适宜的煅烧温度可以减少煅烧时间,提高氧化铝的产率。
二、氧化铝的计算1.确定产品质量指标氧化铝的质量指标主要包括氧化铝含量、比表面积、晶型等。
根据产品的具体要求和应用领域,确定相应的质量指标。
2.计算产率氧化铝的产率是衡量生产效果的重要指标,通常通过计算可得。
产率=(实际产量/理论产量)×100%其中,实际产量是指实际生产得到的氧化铝的质量,理论产量是根据原料的理论含量计算出来的氧化铝的质量。
3.浓度计算碱法工艺中,浸出液中的铝离子浓度是关键参数之一、可以通过测定浸出液中铝的含量,再根据浸出液体积计算浓度。
4.脱硅率计算氧化铝产品中的硅含量对产品质量有一定影响,因此需要计算脱硅率。
脱硅率=(进料硅含量-产物硅含量)/进料硅含量×100%总结:氧化铝的生产工艺包括碱法和酸法,选择适合的工艺应根据实际情况进行考虑。
氧化铝生产流程

THANKS
汇报人:XX
熟料破碎与筛分:将冷却后的熟料破碎 至一定粒度,并进行筛分,得到不同粒 度的熟料产品
包装与运输:将筛分后的熟料进行包装 和标识,并进行运输和储存
氧化铝的冷却与输送
氧化铝焙烧后的冷却方式:自然冷 却、强制风冷、水冷等
输送设备选择依据:产量、物料特 性、地形等
添加标题
添加标题
添加标题
添加标题
输送方式:皮带输送、斗式提升机、 刮板输送等
赤泥的分离:采用沉淀池或 沉降槽进行分离
赤泥的利用:作为建筑材料、 土地改良剂等资源化利用
赤泥的处置:合理堆放、填 埋等无害化处理方式
苛化产物的用途
氧化铝:用于制造陶瓷、 玻璃等
氢氧化铝:用于制造药物、 化妆品等
硫酸铝:用于制造肥料、 纸张等
硝酸铝:用于制造炸药、 染料等
Part Six
氧化铝焙烧与冷却
氧化铝的用途
用于制造耐火材料
用于制造陶瓷和玻璃
用于制造铝盐和催化剂
用于制造电池和电子器件
氧化铝生产流程简介
原料准备: 选用合适的 铝土矿,进 行破碎、磨 细和调配等 处理,以便 进行下一阶 段的反应。
熟料烧成: 将处理后的 原料与石灰 石、白云石 等添加剂混 合,经过高 温烧结,形 成熟料。
熟料溶出: 将熟料放入 高压釜中, 用硫酸、硝 酸等酸类溶 剂进行溶出, 使氧化铝从 矿石中溶解 出来。
氧化铝焙烧工艺流程
原料准备:将铝土矿破碎至一定粒度, 并进行筛分和除杂处理
配料与混合:按照一定比例将破碎后的 铝土矿和其他添加剂进行混合,确保成 分均匀
熟料烧成:将混合料送入回转窑中进行 焙烧,在高温下进行固相反应,生成铝 酸三钙等化合物
氧化铝生产工艺简介

氧化铝生产工艺简介氧化铝(Aluminium oxide,简称Al2O3)是一种广泛应用的工程材料,具有耐高温、耐腐蚀、绝缘性能良好等特点,广泛用于电子、陶瓷、建筑、化工等行业。
氧化铝的生产工艺主要分为两种,即碳酸铝法和氨铝石法。
以下将对这两种生产工艺进行详细介绍。
碳酸铝法是一种常用的氧化铝生产工艺。
具体步骤如下:1.起始原料准备:将铝酸盐(如氢氧化铝)和碳酸盐(如氢碳酸铝)作为起始原料。
碳酸盐是还原剂,可以将铝酸盐还原为氧化铝。
2.溶液制备:将起始原料溶解在水或其他溶剂中,形成氧化铝浆料。
3.沉淀反应:通过加入碱液或调整溶液pH值,使溶液中的铝离子发生沉淀反应,生成氢氧化铝沉淀物。
4.过滤和洗涤:将沉淀物过滤得到固体,然后进行洗涤,去除杂质。
5.烘干和焙烧:将洗涤后的固体烘干,然后进行焙烧处理,将氢氧化铝转化为氧化铝。
6.磨碎和筛分:将焙烧后的氧化铝块磨碎成粉末,并进行筛分,调整粒度和颗粒形状。
氨铝石法是另一种常用的氧化铝生产工艺。
具体步骤如下:1.起始原料准备:将铝金属或铝化合物作为起始原料。
铝金属是常用的起始原料,可以通过冶炼等方法获得。
2.粉碎和磨矿:将起始原料粉碎和磨细,以增大其表面积,有利于反应进行。
3.水解反应:将粉碎后的铝原料与氨气在一定温度下反应,发生水解反应,生成氨铝石。
4.过滤和洗涤:将水解后的氨铝石过滤得到固体,然后进行洗涤,去除杂质。
5.烘干和焙烧:将洗涤后的固体烘干,然后进行焙烧处理,将氨铝石转化为氧化铝。
6.磨碎和筛分:将焙烧后的氧化铝块磨碎成粉末,并进行筛分,调整粒度和颗粒形状。
以上是氧化铝的两种常用生产工艺的简介。
在实际应用中,根据不同的需求,还可以对生产工艺进行调整和改进,以提高产品质量和生产效率。
氧化铝的工艺流程

氧化铝的工艺流程
氧化铝是一种重要的工业原料,广泛应用于陶瓷、电子材料、
磨料、耐火材料等领域。
氧化铝的生产工艺主要包括氧化铝矿石的
选矿、粉碎、浸出、结晶、过滤、煅烧等步骤。
下面将详细介绍氧
化铝的生产工艺流程。
1. 氧化铝矿石的选矿
氧化铝矿石主要包括赤铁矿、脱水铝石、石英石等。
在选矿过
程中,需要根据矿石的成分和性质,采用物理方法(如重选、磁选)或化学方法(如浮选)进行选矿,以提高氧化铝的品位和回收率。
2. 氧化铝矿石的粉碎
经过选矿的氧化铝矿石需要经过粉碎工艺,将矿石破碎成适当
的颗粒大小,以便后续的浸出和结晶工艺。
3. 氧化铝矿石的浸出
粉碎后的氧化铝矿石经过浸出工艺,将氧化铝矿石中的氧化铝
和其他杂质溶解出来,得到含氧化铝的浸出液。
4. 氧化铝的结晶
浸出液经过结晶工艺,通过控制温度、浓度等条件,使溶液中的氧化铝结晶沉淀,得到氧化铝的结晶产品。
5. 氧化铝的过滤
经过结晶的氧化铝产品需要进行过滤工艺,将结晶产品中的液相分离出来,得到干燥的氧化铝产品。
6. 氧化铝的煅烧
过滤后的氧化铝产品需要进行煅烧工艺,将氧化铝产品在高温条件下进行煅烧,以去除残余的水分和有机物质,提高氧化铝的结晶度和颗粒度。
以上就是氧化铝的生产工艺流程,通过选矿、粉碎、浸出、结晶、过滤、煅烧等步骤,可以生产出高品质的氧化铝产品,满足不同工业领域的需求。
随着工艺技术的不断进步,氧化铝的生产工艺也在不断优化和改进,以提高生产效率和降低生产成本。
希望通过
不断的研究和实践,能够进一步完善氧化铝的生产工艺,为工业生产提供更好的原料支持。
氧化铝的生产工艺流程
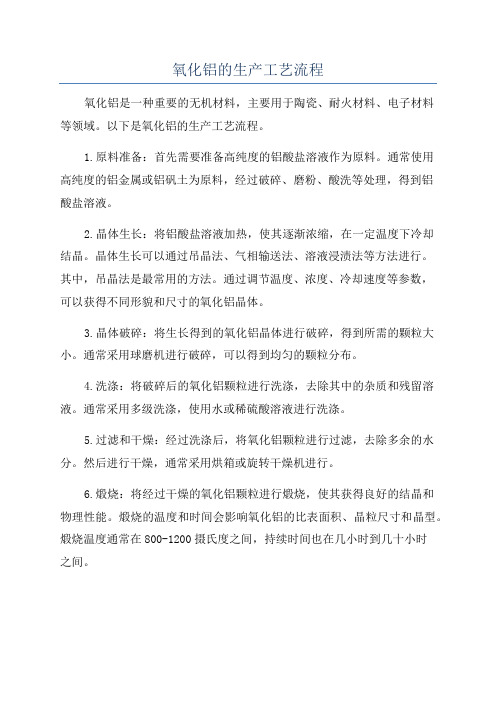
氧化铝的生产工艺流程氧化铝是一种重要的无机材料,主要用于陶瓷、耐火材料、电子材料等领域。
以下是氧化铝的生产工艺流程。
1.原料准备:首先需要准备高纯度的铝酸盐溶液作为原料。
通常使用高纯度的铝金属或铝矾土为原料,经过破碎、磨粉、酸洗等处理,得到铝酸盐溶液。
2.晶体生长:将铝酸盐溶液加热,使其逐渐浓缩,在一定温度下冷却结晶。
晶体生长可以通过吊晶法、气相输送法、溶液浸渍法等方法进行。
其中,吊晶法是最常用的方法。
通过调节温度、浓度、冷却速度等参数,可以获得不同形貌和尺寸的氧化铝晶体。
3.晶体破碎:将生长得到的氧化铝晶体进行破碎,得到所需的颗粒大小。
通常采用球磨机进行破碎,可以得到均匀的颗粒分布。
4.洗涤:将破碎后的氧化铝颗粒进行洗涤,去除其中的杂质和残留溶液。
通常采用多级洗涤,使用水或稀硫酸溶液进行洗涤。
5.过滤和干燥:经过洗涤后,将氧化铝颗粒进行过滤,去除多余的水分。
然后进行干燥,通常采用烘箱或旋转干燥机进行。
6.煅烧:将经过干燥的氧化铝颗粒进行煅烧,使其获得良好的结晶和物理性能。
煅烧的温度和时间会影响氧化铝的比表面积、晶粒尺寸和晶型。
煅烧温度通常在800-1200摄氏度之间,持续时间也在几小时到几十小时之间。
7.表面处理:经过煅烧后的氧化铝颗粒表面可能会存在一些有害物质或氧化层,需要进行进一步的表面处理。
通常采用酸洗、碱洗或离子交换等方法,去除表面杂质,以提高氧化铝的纯度和质量。
8.精细处理:根据不同的用途和要求,可以对氧化铝进行进一步的处理。
例如,对氧化铝颗粒进行球形化处理,获得更好的流动性和储存性能;或者进行表面改性,增加氧化铝的特殊功能,如吸附、离子交换等。
9.质量检验:对生产得到的氧化铝产品进行质量检验,检测其化学成分、晶体形貌、比表面积、物理性能等。
质量检验是确保产品达到规定标准的重要环节。
以上就是氧化铝的生产工艺流程。
根据具体的生产要求和用途,工艺流程可能会有所不同,但整体上都是遵循上述的基本步骤。
氧化铝生产工艺流程

氧化铝生产工艺流程氧化铝是一种重要的工业原料,广泛应用于陶瓷、耐火材料、电子材料等领域。
下面是氧化铝的生产工艺流程的详细介绍。
1.原料准备:氧化铝的主要原料是铝矾土,其主要成分是氧化铝和杂质。
在生产中,需要对原料进行破碎、筛分、干燥等处理,以获得满足要求的颗粒度和含水率的原料。
2.破碎和球磨:将破碎后的铝矾土送入球磨机中进行球磨处理。
通过球磨,原料中的氧化铝和杂质得以更好地混合,并且颗粒尺寸得到进一步细化。
3.水洗和筛分:将球磨后的原料送入水洗机中进行水洗处理,以将其中的杂质和不溶于水的物质去除。
然后,通过筛分设备对洗涤后的原料进行筛分,以得到所需的粒度级配。
4.酸洗:将筛分后的原料送入酸洗器中进行酸洗处理,主要目的是去除铁、钙、镁等杂质。
在酸洗过程中,使用稀盐酸或硫酸进行处理,将杂质溶解掉,并通过水洗去除残留的酸液。
5.煅烧:酸洗后的原料送入煅烧炉进行煅烧处理。
煅烧过程中,将原料加热至高温,使其中的水分和一些有机物质蒸发和分解,同时将铝矾土中的氧化铝转化为晶体形式。
煅烧温度和时间的控制对产品的性能和质量有着重要的影响。
6.水洗和沉淀:在煅烧后,产品需要进行水洗和沉淀处理。
首先,将煅烧后的大颗粒破碎成合适的粒径范围,然后将颗粒送入水洗设备中进行洗涤。
洗涤过程中,通过水力和湍流作用,将杂质和细小颗粒从氧化铝颗粒中去除。
然后,通过离心沉淀机将洗净的氧化铝进行沉淀分离。
7.结晶和分级:将沉淀后的氧化铝送入结晶槽中进行结晶处理。
通过控制槽内的温度和浓度,使溶液中的氧化铝结晶成颗粒状,并沉淀到底部。
随后,使用分级设备对结晶过程中产生的颗粒进行分级,以获得所需粒度的氧化铝产品。
8.焙烧:分级后的氧化铝送入焙烧炉进行焙烧处理。
焙烧目的是除去分级过程中残留的水分和有机物,同时使氧化铝颗粒中的杂质进一步还原和挥发。
焙烧温度和时间的控制对产品质量和性能具有重要影响。
9.研磨和包装:焙烧后的氧化铝需要进行研磨处理,以获得所需的细度和颗粒形态。
氧化铝生产工艺流程
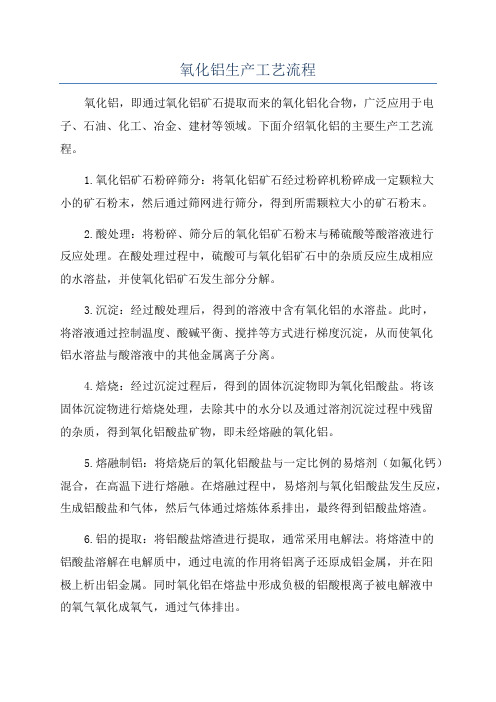
氧化铝生产工艺流程氧化铝,即通过氧化铝矿石提取而来的氧化铝化合物,广泛应用于电子、石油、化工、冶金、建材等领域。
下面介绍氧化铝的主要生产工艺流程。
1.氧化铝矿石粉碎筛分:将氧化铝矿石经过粉碎机粉碎成一定颗粒大小的矿石粉末,然后通过筛网进行筛分,得到所需颗粒大小的矿石粉末。
2.酸处理:将粉碎、筛分后的氧化铝矿石粉末与稀硫酸等酸溶液进行反应处理。
在酸处理过程中,硫酸可与氧化铝矿石中的杂质反应生成相应的水溶盐,并使氧化铝矿石发生部分分解。
3.沉淀:经过酸处理后,得到的溶液中含有氧化铝的水溶盐。
此时,将溶液通过控制温度、酸碱平衡、搅拌等方式进行梯度沉淀,从而使氧化铝水溶盐与酸溶液中的其他金属离子分离。
4.焙烧:经过沉淀过程后,得到的固体沉淀物即为氧化铝酸盐。
将该固体沉淀物进行焙烧处理,去除其中的水分以及通过溶剂沉淀过程中残留的杂质,得到氧化铝酸盐矿物,即未经熔融的氧化铝。
5.熔融制铝:将焙烧后的氧化铝酸盐与一定比例的易熔剂(如氟化钙)混合,在高温下进行熔融。
在熔融过程中,易熔剂与氧化铝酸盐发生反应,生成铝酸盐和气体,然后气体通过熔炼体系排出,最终得到铝酸盐熔渣。
6.铝的提取:将铝酸盐熔渣进行提取,通常采用电解法。
将熔渣中的铝酸盐溶解在电解质中,通过电流的作用将铝离子还原成铝金属,并在阳极上析出铝金属。
同时氧化铝在熔盐中形成负极的铝酸根离子被电解液中的氧气氧化成氧气,通过气体排出。
7.产出氧化铝:在铝的电解过程中,反应产生的铝金属定期收集,通过特定的处理方法,得到纯度高的氧化铝颗粒。
以上是氧化铝主要的生产工艺流程。
不同的生产工艺流程可能因厂家、设备和技术等因素有所不同,因此在实际生产中还需要根据具体情况进行工艺调整和优化,以确保氧化铝的质量和产量。
氧化铝生产工艺

氧化铝生产工艺
氧化铝(Aluminum Oxide,Al2O3)是一种广泛应用的陶瓷材料,用于制备金属铝、耐火材料、陶瓷、磨料等。
以下是氧化铝的生产工艺的主要步骤:
1.铝矾土的提取:
原料:铝矾土是氧化铝的主要矿石,主要成分是氧化铝和含铝的硅酸盐。
提取过程:铝矾土通过矿石的选矿和矿石的酸法提取,得到含铝的物质。
2.氧化铝的制备:
预处理:含铝物质经过预处理,去除杂质和松散物。
氧化:预处理后的物质通过高温氧化反应,将含铝的物质转化为氧化铝。
3.氧化铝的结晶:
结晶反应:通过化学反应使氧化铝结晶成微小颗粒。
结晶分离:将结晶的氧化铝颗粒从反应液中分离出来。
4.水洗和烘干:
水洗:将结晶的氧化铝颗粒通过水洗去除残留的溶液。
烘干:将洗净的氧化铝颗粒进行烘干,去除水分。
5.氧化铝的精炼:
精炼:通过各种物理和化学方法对氧化铝进行精炼,提高其纯度。
细磨:对氧化铝进行细磨,得到所需颗粒大小的产品。
6.成品包装:
检验:对精炼后的氧化铝进行质量检验。
包装:符合质量标准的氧化铝产品被包装成成品,准备发往市场。
这是一个简化的氧化铝生产工艺的概述,实际的生产过程可能会有更多的细节和精密的控制。
此外,为了保护环境,工业生产过程通常会采取环保措施,例如废气处理和资源回收。
详细的生产工艺和技术参数可以在专业的工艺手册或相关文献中找到。
氧化铝生产工艺pdf

氧化铝生产工艺pdf一、氧化铝生产工艺概述氧化铝是一种重要的工业原材料,具有广泛的应用领域。
其生产工艺主要分为碱法、拜耳法和烧结法等。
碱法是最常用的方法,通过氢氧化钠溶液与铝土矿反应,生成氢氧化铝,再经过焙烧得到氧化铝。
拜耳法是一种较为先进的工艺,通过高温高压下的溶出和晶种分解,得到氧化铝。
烧结法是将铝土矿与碳酸钠混合后进行烧结,再经过溶解和分离得到氧化铝。
二、原料准备氧化铝生产所需的主要原料包括铝土矿、碱(氢氧化钠或碳酸钠)等。
铝土矿是氧化铝的主要来源,其质量和性质对氧化铝的生产工艺和产品质量有着重要影响。
碱是氧化铝生产中的重要化学试剂,其选择和使用对生产效率和能源消耗有着重要影响。
三、碱法生产氧化铝流程碱法生产氧化铝主要包括以下步骤:铝土矿与碱反应生成氢氧化铝,经过过滤分离出固体杂质;焙烧氢氧化铝得到氧化铝;最后进行产品洗涤和干燥。
该工艺具有较高的生产效率和较低的生产成本,是目前应用最广泛的氧化铝生产工艺。
四、拜耳法生产氧化铝流程拜耳法是一种较为先进的氧化铝生产工艺,主要包括以下步骤:高温高压下将铝土矿溶出得到溶出液;经过晶种分解得到氧化铝;过滤分离出固体杂质;最后进行产品洗涤和干燥。
该工艺具有产品质量高、能耗低等优点,但生产成本较高。
五、烧结法生产氧化铝流程烧结法是将铝土矿与碳酸钠等试剂混合后进行烧结,再经过溶解和分离得到氧化铝。
该工艺具有设备简单、投资少等优点,但生产效率和产品质量相对较低。
六、赤泥分离与洗涤赤泥是氧化铝生产过程中产生的废弃物,含有较多的铁、硅等杂质。
赤泥分离与洗涤是氧化铝生产过程中的重要环节,主要通过物理和化学方法将赤泥中的有用成分分离出来,同时对赤泥进行洗涤和干燥。
该过程对环境保护和资源利用具有重要意义。
七、氧化铝总回收率与氧化铝总工艺能耗氧化铝总回收率和氧化铝总工艺能耗是衡量氧化铝生产工艺的重要指标。
总回收率反映了生产过程中氧化铝的回收效率,总工艺能耗反映了生产过程中的能源消耗情况。
氧化铝生产工艺简介

氧化铝生产工艺简介1. 氧化铝的概述氧化铝(Aluminium Oxide,化学式:Al2O3)是一种重要的无机化合物,广泛应用于工业生产中。
氧化铝具有高硬度、高熔点、耐火性强等特点,在陶瓷、电子材料、磨料、催化剂等领域有广泛的应用。
2. 氧化铝生产工艺氧化铝可以通过不同的工艺来生产,常见的生产工艺主要有以下几种:2.1 工业氧化铝工艺工业氧化铝工艺是目前应用最广泛的一种氧化铝生产工艺。
该工艺主要包括以下步骤:2.1.1 氧化铝矿石选矿首先,从氧化铝矿石中进行选矿,去除其中的杂质,得到纯净的氧化铝矿石。
2.1.2 熔炼将选矿后的氧化铝矿石与碳质物料进行熔炼,生成氧化铝的金属铝。
2.1.3 氧化将金属铝氧化,生成氧化铝粉末。
这个过程可以采用火法氧化、湿法氧化和电解法氧化等不同方法。
2.1.4 粉碎和筛分将氧化铝粉末进行粉碎和筛分,得到粒径合适的氧化铝颗粒。
2.1.5 烘干和包装把粒径合适的氧化铝颗粒进行烘干处理,然后进行包装,以便储存和运输。
2.2 溶胶-凝胶法溶胶-凝胶法是一种常用的氧化铝生产工艺,它主要包括以下几个步骤:2.2.1 制备氧化铝溶胶将适量的铝源与溶剂混合,形成氧化铝溶胶。
2.2.2 凝胶化经过特定的酸碱调节和水解反应,溶胶内的氧化铝物质逐渐聚集形成胶状凝胶。
2.2.3 干燥将胶状凝胶进行烘干,使其脱去溶剂。
2.2.4 煅烧对干燥后的凝胶进行高温煅烧处理,使其形成坚硬的氧化铝。
2.2.5 粉碎和筛分将煅烧后的氧化铝进行粉碎和筛分,得到所需粒径的氧化铝粉末。
2.3 氧化铝晶体生长法氧化铝晶体生长法主要是通过溶液中的化学反应和结晶生长过程来制备氧化铝晶体。
这种工艺主要用于生产高纯度的氧化铝,包括以下步骤:2.3.1 制备溶液根据反应所需的组分,将适量的溶剂和反应物混合,形成溶液。
2.3.2 晶体生长将溶液置于适宜的温度和环境条件下,通过化学反应和结晶生长过程,使氧化铝逐渐形成晶体。
2.3.3 筛分和洗涤将生长的氧化铝晶体进行筛分和洗涤,去除其中的杂质。
氧化铝生产工艺流程
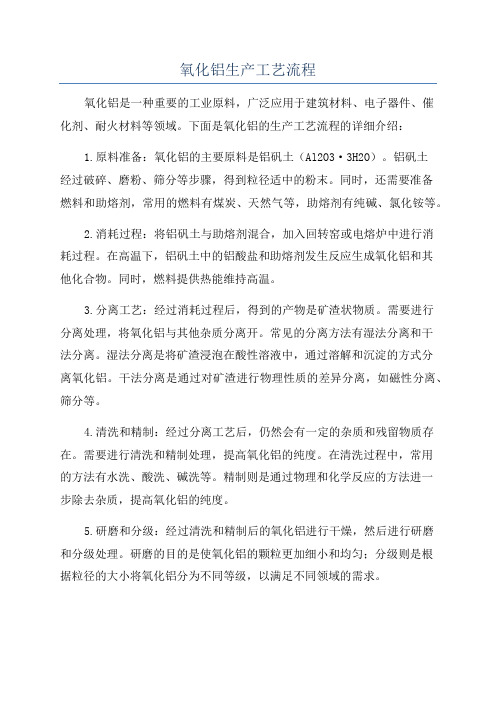
氧化铝生产工艺流程氧化铝是一种重要的工业原料,广泛应用于建筑材料、电子器件、催化剂、耐火材料等领域。
下面是氧化铝的生产工艺流程的详细介绍:1.原料准备:氧化铝的主要原料是铝矾土(Al2O3·3H2O)。
铝矾土经过破碎、磨粉、筛分等步骤,得到粒径适中的粉末。
同时,还需要准备燃料和助熔剂,常用的燃料有煤炭、天然气等,助熔剂有纯碱、氯化铵等。
2.消耗过程:将铝矾土与助熔剂混合,加入回转窑或电熔炉中进行消耗过程。
在高温下,铝矾土中的铝酸盐和助熔剂发生反应生成氧化铝和其他化合物。
同时,燃料提供热能维持高温。
3.分离工艺:经过消耗过程后,得到的产物是矿渣状物质。
需要进行分离处理,将氧化铝与其他杂质分离开。
常见的分离方法有湿法分离和干法分离。
湿法分离是将矿渣浸泡在酸性溶液中,通过溶解和沉淀的方式分离氧化铝。
干法分离是通过对矿渣进行物理性质的差异分离,如磁性分离、筛分等。
4.清洗和精制:经过分离工艺后,仍然会有一定的杂质和残留物质存在。
需要进行清洗和精制处理,提高氧化铝的纯度。
在清洗过程中,常用的方法有水洗、酸洗、碱洗等。
精制则是通过物理和化学反应的方法进一步除去杂质,提高氧化铝的纯度。
5.研磨和分级:经过清洗和精制后的氧化铝进行干燥,然后进行研磨和分级处理。
研磨的目的是使氧化铝的颗粒更加细小和均匀;分级则是根据粒径的大小将氧化铝分为不同等级,以满足不同领域的需求。
6.包装和储存:经过研磨和分级后的氧化铝需要进行包装和储存。
包装一般采用密封的包装材料,以保证产品质量和使用效果。
储存需要注意避免潮湿和高温等有害环境因素,以确保产品的稳定性和保存期限。
总结起来,氧化铝的生产工艺流程包括原料准备、消耗过程、分离工艺、清洗和精制、研磨和分级以及包装和储存等环节。
每个环节的操作和控制都对最终产品的质量和性能有重要影响。
因此,对于氧化铝生产企业来说,优化工艺流程和提高工艺技术水平是非常关键的。
氧化铝的生产工艺流程

氧化铝的生产工艺流程氧化铝是一种重要的无机化工产品,广泛应用于化妆品、建材、电子、食品、陶瓷等多个领域。
下面将详细介绍氧化铝的生产工艺流程。
1.矿石选矿:氧化铝的原料主要是赤铝石、泡沫铝石等。
首先进行矿石的开采和选矿过程,选取高品位的矿石用于后续的处理。
2.破碎和磨粉:将选矿后的矿石进行破碎和磨粉,使得颗粒达到一定的细度,便于后续的处理和反应。
3.酸浸提取:将粉煜铝矿放入酸浸槽中,用稀硫酸或氢氟酸进行浸出反应。
酸性条件下,铝石中的氧化铝会与酸反应,生成可溶性的铝酸盐。
4.脱硅处理:将酸浸提取后的溶液进行脱硅处理,一般采用氢氟酸法或石灰法。
通过加入适量的氟化钠或氧化钙等物质,反应生成难溶性的氟铝酸盐或氢氧化铝,随后沉淀分离。
5.氧化反应:将分离得到的氟铝酸盐或氢氧化铝进行氧化反应,通常采用高温氧化炉。
在高温(900-1200℃)下,氟铝酸盐或氢氧化铝经过氧化反应生成氧化铝颗粒。
6.分离和洗涤:将氧化铝颗粒从氧化炉中取出,进行分离和洗涤。
分离一般采用离心机或其他分离装置,将氧化铝颗粒和气体分离。
洗涤则是为了去除残留的杂质和酸性物质,提高氧化铝的纯度。
7.烘干和筛分:将洗涤后的氧化铝颗粒进行烘干处理,通常采用回转干燥机。
烘干后的氧化铝颗粒通过筛分,分离出不同粒径的颗粒,以满足不同应用领域的需求。
8.精细处理:根据不同的要求,进一步对氧化铝进行精细处理。
可以采用磁选、搅拌、过滤等方法,去除细小的杂质和残留物质。
9.包装和储存:将处理好的氧化铝颗粒进行包装,通常采用塑料袋或密封桶进行包装。
包装后的氧化铝颗粒存放在防潮、防尘的储存设施中,以确保产品质量。
以上是氧化铝的生产工艺流程。
在具体的生产过程中,还会根据不同的生产设备和工艺要求,进行一些微调和改进。
但总体来说,通过矿石选矿、酸浸提取、氧化反应和后续处理等步骤,可以获得高质量的氧化铝产品。
氧化铝生产工艺流程

氧化铝生产工艺流程氧化铝,即二氧化铝,是一种重要的无机化合物,在多个领域有着广泛的应用。
氧化铝的生产工艺流程涉及多个步骤,包括矿石选矿、矿石煅烧、铝酸法制取和氢氧化法制取等。
本文将详细介绍氧化铝的生产工艺流程。
1. 矿石选矿氧化铝的主要原料是铝土矿,其中含有较高比例的氧化铝。
矿石选矿是将铝土矿经过粉碎、浮选等工艺,提高氧化铝的含量,同时去除杂质。
该过程通常包括矿石的碎石、磨矿和浮选等步骤。
选矿后的矿石进行下一步的处理。
2. 矿石煅烧矿石煅烧是将经过选矿的铝土矿在高温条件下进行煅烧,使其发生化学反应,转变成含有高纯度氧化铝的物质。
该过程主要分为预煅和炼煅两个步骤。
预煅是将矿石在较低温度下进行煅烧,以去除矿石中的有机物和水分,并使得矿石结构发生改变。
而炼煅是将经过预煅的矿石在高温下进行进一步的煅烧,使其转变成高纯度的氧化铝。
3. 铝酸法制取铝酸法是目前氧化铝生产中最常用的方法之一。
该方法主要包括铝土矿浸出、铝含量的提纯、氢氧化铝的沉淀和氢氧化铝的煅烧等步骤。
首先,将经过选矿和煅烧的铝土矿与浸取剂(如石灰石)混合,进行浸出反应,将铝含量提取出来。
然后,通过提纯工艺,去除浸出液中的杂质,提高铝的纯度。
接下来,将纯化的溶液加入沉淀剂,使氢氧化铝沉淀出来。
最后,将沉淀的氢氧化铝进行煅烧,转变成氧化铝产品。
4. 氢氧化法制取氢氧化法是另一种常用的氧化铝生产方法。
该方法主要包括铝土矿的浸取、氢氧化铵的制备和氧化铝的煅烧等步骤。
首先,将经过选矿和煅烧的铝土矿与浸取剂进行浸取反应,将铝含量提取出来。
然后,将浸出液与氨水等反应,制备氢氧化铵。
最后,将氢氧化铵进行煅烧,转变成氧化铝产品。
总结氧化铝的生产工艺流程涉及矿石选矿、矿石煅烧、铝酸法制取和氢氧化法制取等多个步骤。
无论是铝酸法还是氢氧化法,都需要经过多个反应和处理过程,才能获得高纯度的氧化铝产品。
这些工艺的运用使得氧化铝的生产更加经济高效,广泛应用于建筑材料、电子器件等领域。
氧化铝生产工艺

氧化铝生产工艺氧化铝是一种重要的工业原材料,在许多行业中都有广泛的应用。
它通常通过氧化铝生产工艺来制备,以下是氧化铝的生产工艺的简要介绍。
氧化铝生产工艺主要包括矿石提取、粉煤灰制备、氧化铝制备和精细处理四个主要步骤。
首先,矿石提取是氧化铝生产的第一步。
氧化铝的主要矿石有脱水铝土矿和熔融铝土矿。
脱水铝土矿经过开采、破碎和磨粉等处理,得到的矿石经过采矿车运输到选矿场,在选矿场经过一系列的工艺,如洗选、磁选、重选等,将矿石中的杂质除去,得到纯度较高的氧化铝矿石。
其次,粉煤灰制备是氧化铝生产的重要步骤之一。
煤矸石是煤炭生产过程中产生的废弃物,经过粉碎、分级等工艺处理,得到粉煤灰。
粉煤灰中含有丰富的氧化铝资源,可以作为氧化铝生产的原料。
接下来,氧化铝制备是氧化铝生产的关键步骤。
氧化铝制备主要分为两个过程,即氧化和还原。
首先,将矿石和粉煤灰按一定比例混合,并加入一定量的石灰石作为催化剂。
然后,将混合物放入氧化反应釜中,在高温下进行氧化反应。
氧化反应使矿石中的氧化铝与其他金属氧化物分离,并生成氧化铝产物。
接着,将产物经过洗涤、沉淀和干燥等工艺处理,得到纯度较高的氧化铝。
最后,精细处理是氧化铝生产的最后一个步骤。
精细处理主要是对氧化铝的粒度、物理性质和化学性质进行调整,以满足不同行业的需求。
精细处理的方法包括研磨、筛分、分类、电磁分选等工艺。
总的来说,氧化铝的生产工艺包括矿石提取、粉煤灰制备、氧化铝制备和精细处理四个主要步骤。
通过这些工艺的处理,可以得到纯度较高的氧化铝产品,广泛应用于建筑材料、电子产业、化工等行业中。
随着科技的不断发展,氧化铝生产工艺也在不断改进,以提高产能、降低成本和减少环境污染。
- 1、下载文档前请自行甄别文档内容的完整性,平台不提供额外的编辑、内容补充、找答案等附加服务。
- 2、"仅部分预览"的文档,不可在线预览部分如存在完整性等问题,可反馈申请退款(可完整预览的文档不适用该条件!)。
- 3、如文档侵犯您的权益,请联系客服反馈,我们会尽快为您处理(人工客服工作时间:9:00-18:30)。
氧化铝工艺流程简介
一、生产工艺简介
公司采用国际先进的拜耳法生产工艺,主要设备从德国、法国、荷兰、澳大利亚等国进口;生产指挥系统采用美国Rockwell公司的DCS控制系统。
公司还建有庞大的生产ERP系统及信息管理系统,集生产调度、控制、信息采集、管理于一体。
二、生产工艺流程图
铝土矿
氧化铝
三、工艺流程简述
1、原料工序
原料矿石堆场在建厂初期,为方便装卸矿石及避免大量杂质在倒运过程进入生产流程,堆场使用原矿石将地基提升50cm压实后用于储存铝土矿。
原矿石由汽车运进厂的铝土矿经地磅站称重后和原矿堆场的铝土矿经破碎后一起倒入卸矿站,经胶带输送机送往均化堆场堆存,为避免斗轮取料机将杂质当做矿石取走,取料机斗轮离地面30cm,其间用矿石进行填充,再由胶带输送机将铝土矿送往原料磨的磨头仓。
外购石灰由汽车运进厂,卸入石灰卸矿站,经胶带输送机送往石灰仓,一部分石灰通过胶带输送机送往原料磨磨头仓,另一部分石灰送往石灰消化工段。
在石灰消化工段,石灰与热水一同加入化灰机中,制备的石灰乳流进石灰乳槽,石灰乳用泵送往蒸发车间苛化工序和沉降车间控制过滤工序。
在原料磨工段,铝土矿、石灰及循环母液按比例加入原料磨中磨制原矿浆,原矿浆用水力漩流器进行分级,分级机溢流为合格的原矿浆,送入原矿浆槽,分级机底流返回原料磨。
为应对磨机突发故障及流程稳定,矿浆槽必须保持一定液位。
2、溶出工序
来自原料磨已研磨好的原矿浆首先进入溶出预脱硅槽,矿浆通过预脱硅槽的压差进行自溢流至末槽,同时为消除矿浆中的SiO2对溶出过程的影响,根据车间操作规程,矿浆在预脱硅槽首槽加热至100℃,且原矿浆在脱硅槽中停留8h以上,以达到预脱硅的目的。
在预脱硅末槽通过出料泵进入高压隔膜泵,再由高压隔膜泵注入溶出机组。
矿浆首先经过六级
单管预热器被来自相应闪蒸槽的二次蒸汽间接加热到160℃左右,后进入六级带机械搅拌间接加热的预热压煮器,由来自相应级别的闪蒸槽的二次蒸汽预热到200℃左右,再进入带机械搅拌间接加热反应压煮器内,用来自热电的6.0Mpa新蒸汽加热到溶出温度256℃左右,最后经过反应停留压煮器停留反应45~60分钟,溶出后料浆经过十一级闪蒸槽降压降温后,进入稀释槽。
在稀释槽内,根据料浆的密度和浓度,确定一次洗液的加入量,在稀释槽内混成合格的稀释浆液,送往溶出后槽储存,并停留4小时以上,保持高液位运行,以进一步脱除溶液中的硅、铁、锌等杂质,再送往沉降作业区。
各级矿浆自蒸发器产生的二次蒸汽用于相对应的套管预热器中预热原矿浆,二次汽冷凝后从预热器排出进冷凝水罐,冷凝水经逐级闪蒸降压后,汇总到末级冷凝水罐,送往热水站制备热水。
3、沉降工序
从溶出后槽送来的稀释料浆与从絮凝剂制备工段来的絮凝剂一同进入分离沉降槽中,进行液固分离,底流用泵送往洗涤沉降槽,采用三到四次反向洗涤,洗水从末槽加入,末次洗涤后底流送至赤泥过滤,经过滤机过滤后用隔膜泵送往赤泥堆场堆存。
为降低分离槽和洗涤槽溢流中固体的含量,根据车间操作规程,分离槽和洗涤槽的清液层高度,必须保持在5m以上,以确保分离和洗涤槽中外送的溢流中固体含量降低最低。
分离沉降槽溢流送控制过滤工段的粗液槽中进行液位缓冲,输送至控制过滤,控制过滤采用立式叶滤机,同时将少量石灰乳也加进粗液槽中作为助滤剂,叶滤得到的精液在精液槽中进行缓冲后送分解车间的精液板式热交换工段,叶滤渣进滤渣槽中,用泵返回沉降槽。
4、分解工序
控制过滤工段送来的精液进分解车间的精液热交换工序,精液在此工段经三级换热,精液温度从100~105℃降为61~62℃,然后送种子过滤冲晶种。
第一、二级为精液与分解母液换热,第三级为精液与水换热。
精液冲晶种后,在晶种槽中停留搅拌均匀后,制备成固含为800g/L 的氢氧化铝料浆,用晶种泵送往分解首槽中,从分解首槽槽顶溢流口依次溢流至分解末槽,经过50h左右的梯度降温制备砂状氢氧化铝,在分解槽尾部经过水力漩流器分级机组,分级后的粗颗粒氢氧化铝料浆,送往焙烧车间成品过滤工序,分级溢流返回分解槽中,分解倒数第二槽为种子出料槽,在槽上部适当位置出料自流进种子过滤工段,经过滤后晶种流进晶种槽中,过滤母液进锥形母液槽进行液固沉淀分离,溶液进入母液槽进行缓冲,固含较大的料浆送至分解溢流槽后转至分解末槽继续分解循环。
母液槽母液用泵输送,一部分送氢氧化铝分级,调配料浆固含,另一部分送精液热交换工序与精液换热,换热后母液温度从50~55℃升至85~90℃,送蒸发车间的蒸发原液槽。
为使分解产出率较高,在分解槽顶部适当位置设有宽流道板式换热器作为中间降温设备。
5、蒸发工序
从分解车间送来的母液进入蒸发车间的蒸发原液槽,为确保生产稳定及生产液量平衡,蒸发原液槽需保持一定的液位。
蒸发工段采用分解母液部分蒸发工艺,一部分母液进蒸发器中浓缩,另一部分母液直接送往循环母液槽调配成合格的循环母液。
蒸发站由一组六效降膜蒸发器和一台强制循环结晶蒸发器及三级闪蒸组成,蒸发采用逆流流程。
原液由末效逐级送到前效蒸发,最后到I 效。
I效的出料温度为140℃,此溶液进入三级闪蒸系统,逐级闪蒸降温,三闪出料温度92℃左右,三闪出料即为蒸发母液,送往循环母液调配槽制备循环母液。
由蒸发三闪出料引一定数量的母液进强制效,使其蒸浓到Na2Ok 320g/L以上,并从盐沉降槽底流中引入部分Na2CO3固体颗料做为晶种,温度控制在103℃,加热蒸汽用I效产生的部分二次汽(或新蒸汽)做热源,控制好结晶条件,使从强制效母液中析出的碳酸钠主要为颗粒粗大、沉降及过滤性能较好的无水碳酸钠,结晶器出料去盐沉降槽,底流进盐过滤机,经过滤后的Na2CO3滤饼稀释后进苛化槽。
苛化料浆送苛化过滤机过滤,滤饼送赤泥沉降车间的沉降槽。
溢流称为强碱液,其返回三闪,经闪蒸后送循环母液调配槽制备循环母液。
生产补碱用液体或固体烧碱,循环母液配制区域设有补碱设备。
6、焙烧工序
由分解分级来的氢氧化铝浆液经氢氧化铝浆液贮槽进行液位缓冲,用泵送水平盘式过滤机,对氢氧化铝进行分离及洗涤,洗涤后滤饼含水率6~8%,用胶带输送机送往焙烧炉喂料箱或氢氧化铝仓,过滤后母液和滤液在各自的储槽缓冲后送种子过滤的锥形母液槽。
从成品过滤或氢氧化铝仓来的氢氧化铝卸入焙烧工序的喂料箱内,喂料箱下设有皮带计量给料机,控制焙烧炉进料量。
含水6-8%的氢氧化铝经胶带输送机,螺旋喂料机送入文丘里干燥器内,干燥后的氢氧化铝被气流带入第一级旋风预热器中,烟气和干燥的氢氧化铝在此进行分离,一级旋风出来的氢氧化铝进入第二级旋风预热器,并与从热分离器来的温度约为1000℃的烟气混合进行热交换,氢氧化铝的温度达320-360℃,附着水基本脱除,预焙烧过的氧化铝在第二级旋风预热器内与烟气分离卸入焙
烧炉的锥体内,焙烧炉所用的燃烧空气预热到600-800℃从焙烧炉底进入,燃料、预焙烧的氧化铝及热空气在炉底充分混合并燃烧,氧化铝的焙烧在炉内约1.4秒钟的时间内完成。
焙烧好的氧化铝和热烟气在热分离器中分离。
热烟气经上述的两级旋风预热器,文丘里干燥器与氢氧化铝进行热交换后,温度降为145℃,进入电除尘器,净化后的烟气用排风机送入烟囱排入大气。
热分离器出来的氧化铝经两段冷却后温度降至80℃,第一段冷却采用四级旋风冷却器,在四级旋风冷却过程中,氧化铝温度从1050℃降为260℃,燃料燃烧所需的空气温度预热到800℃,第二段冷却采用沸腾床冷却机,用水间接冷却,使氧化铝温度从260℃降为80℃。
从沸腾床冷却机出来的氧化铝用风动流槽送入氧化铝仓储存,仓底设有吨包机和散装机,氧化铝包装采用1.0或1.5吨的大袋包装,包装好的氧化铝用汽车运出厂。
电收尘器收下的粉尘,用螺旋输送泵送入第二级旋风冷却器中。