金属变形特性
金属的变形特性

大多数金属材料经冶炼浇注后大多数要进行各种压力加工:1. 铸态组织:晶粒粗大且不均匀,组织不致密,成分偏析等缺陷2. 各种压力加工:轧制锻造挤压拉丝冲压金属经压力加工后不仅改变外形尺寸内部组织和性能也发生变化:1. 冷轧冷拉等冷塑性变形后,金属强度显著提高而塑性下降2. 热轧锻造等热塑性变形后,强度提高不明显,塑性韧性有所改善3. 若压力加工工艺不当,变形量超过塑性值,将产生裂纹或断裂第一节金属的变形特性金属在外力载荷的作用下1. 弹性变形阶段:首先发生弹性变形2. 弹塑性变形阶段:载荷增加到一定值,还发生塑性变形即弹塑性变形3. 断裂阶段:继续增加载荷,塑性变形继续增加,直至金属发生断裂一,工程应力应变曲线或载荷变形曲线低碳钢的应力应变曲线6.1所示:工程应力应变曲线 应力或工程应力或名义应力0A F=σ 应变或工程应变或名义应变00L L L -=ε 工程应力应变曲线和载荷变形曲线相似,只是坐标不同在应力应变曲线上分析低碳钢的变形过程特点:1. 当应力低于e σ时:应力应变成正比,应力去除变形消失,弹性极限表示材料保持完全弹性变形时的最大应力2. 当应力超过e σ后:应力应变直线关系破坏,出现屈服平台或屈服齿,应力或载荷去除变形恢复一部分,屈服极限或屈服点表示材料对起始微量塑性变形的抗力3. 当应力超过s σ后:明显均匀塑性变形,要想使试样应变增加,必须增加应力值,这种随塑性变形增加塑性变形抗力增加的现象称为加工硬化或者形变强化4. 当应力达到b σ时:均匀变形阶段终止,强度极限或抗拉强度表示材料对最大均匀塑性变形的抗力5. 当应力超过b σ后:不均匀塑性变形,出现缩颈,应力下降,最后应力达到Kσ时试样断裂,条件断裂强度表示材料对塑性变形的极限抗力试样断裂的非突发性:塑性断裂:产生一定塑性变形后的断裂材料的塑性: 断裂前的塑性变形量伸长率00L L L f -=δ和断面收缩率00A A A f -=ψ材料的韧性:表征断裂抗力,可由曲线下的面积进行度量材料不同应力应变曲线不同:1. 铜铝及其合金或经热处理的钢材:没有明显的屈服平台2. 铝青铜和某些奥氏体钢:断裂前产生一定量得塑性变形,没有缩颈3. 某些脆性材料如淬火状态下的中高碳钢:拉伸时几乎没有明显的塑性变形二,真应力真应变曲线 真实应力:瞬时载荷除以瞬时截面积AF t =σ 真实应变 0ln 0L L L dL LL t ==⎰ε 真应力真应变曲线图6.3所示两条曲线的比较:1. 工程应力应变曲线:载荷达到最大值后转而下降2. 真应力应变曲线:a) 载荷不断上升直至断裂b) 不断发生加工硬化外力需不断增加才能使变形继续,即使是缩颈之后,缩颈处的真应力仍然在增加c) 没有应力下降阶段流变曲线:均匀塑性变形阶段的真应力真应变曲线均匀塑性变形时的真实应力计算公式:加工硬化指数:1. 加工硬化指数表征:均匀塑性变形阶段的加工硬化能力2. 大多数金属材料的加工硬化指数:0.10~0.503. 取决于:材料晶体结构和加工状态三,金属的弹性变形 金属弹性变形的实质:1. 一句话描述就是:弹性畸变2. 从双原子模型角度进行说明:3.当未加外力时:4.当受到外力后:5.当外力去除后:胡克定律:弹性变形阶段应力应变呈线性关系正弹性模量和切变模量:1.应力应变曲线上直线部分的斜率2.模量越大,弹性抗力越大,弹性变形越不容易进行3.表征弹性变形抗力构件的刚度:1.表征弹性变形难易程度2.拉伸件的刚度:3.材料选材时的重要意义:镗床的镗杆弹性变形越小加工精度越高影响弹性模量的因素:1.对组织不敏感2.取决于原子间结合力3.只与金属本性晶体结构晶格常数4.材料合金化加工过程热处理等影响小第二节单晶体的塑性变形常温或低温下金属的塑性变形方式:主要是通过滑移方式,此外还有孪生等其他方式滑移带滑移带:金相显微镜下在抛光的表面观察到的许多相互平行的线条滑移线:电子显微镜下观察滑移带时可以观察到每条滑移带都许多相互平行的滑移线组成滑移线和滑移带的关系:1.塑性变形以后晶体表面出现的一个个的小台阶2.相互靠近的一组小台阶在宏观上就是一个大台阶也就是滑移带晶体塑性变形前后的晶体结构:晶体的塑性变形:1.晶体的一部分相对于另一部分沿某些晶面和晶向发生滑动2.当发生滑移的晶面移出晶体表面时,在滑移晶面与晶体表面相交处形成滑移台阶3.一个滑移台阶就是一条滑移线4.每条滑移线所对应的台阶高度表示滑移面的滑移量5.台阶的累积就造成了宏观的塑性变形效果滑移:晶体的一部分相对于另一部分沿某些晶面和晶向发生滑动孪生:晶体的一部分相对于另一部分沿某些晶面和晶向作均匀切变塑性变形的不均匀性:1.在滑移带内每条滑移线间的距离约为100个原子间距,而滑移带间的距离约为10000个原子间距2.说明滑移集中发生在某些晶面上,滑移带之间或滑移线之间的晶体层片并没有变形滑移带和滑移线的发展:1. 首先出现滑移线,然后发展呈带2. 滑移线的数目总是随变形程度的增加而增加,滑移线之间的距离随变形程度增加而减小晶面指数和晶向指数晶向族:原子排列相同空间位向不同的所有晶向晶面族:原子排列相同空间位向不同的所有晶面100:[][][]001010100和与之相反的晶向[][][]100010001110:[][][]011101110[][][]110011101和与之相反的晶向111:[][][][]111111111111和与之相反的晶向{}100:()()()001010100{}110:()()()()()()110011101011101110{}111:()()()()111111111111{}112:滑移系滑移面和滑移方向:晶体在滑移面上的滑移方向滑移系:滑移系和金属的塑性:空间位向越多塑性越好晶体结构和滑移系:晶体结构不同滑移系不同滑移面和滑移方向总是原子排列最密的晶面和晶向:1. 面心立方金属:密排面{}111密排晶向110,12个滑移系,塑性较好 2. 体心立方金属:密排面{}110密排晶向111,12个滑移系,塑性较好 3. 密排六方金属:室温时{}0001密排晶向2011,塑性较差金属塑性的好坏:1. 滑移系的多少2. 滑移面上原子的密排程度和滑移方向的数目:3. Fe -α的塑性比铜铝金银的差些:a) 滑移方向的个数:b) 滑移面上原子排列密集程度:c) 滑移面的间距:d) 原子间结合力:滑移的临界分切应力滑移是在切应力的作用下发生的什么是临界分切应力:1. 并不是所有的滑移系同时开动2. 晶体中的滑移系是否滑移取决于:力在滑移面内沿滑移方向上的分切应力的大小3. 最小分切应力:分切应力的计算:φλτcos cos AF =临界分切应力的计算:φλστcos cos s K =临界分切应力K τ的大小取决于:1. 晶体结构纯度加工状态实验温度和加载速度2. 外力大小方向及作用方式单晶体的屈服极限S σ与取向因子之间的关系图6.7:外力大小方向作用方式有关1. 当外力与滑移面滑移方向的夹角都是45度时:最容易滑移,软取向2. 当外力与滑移面平行90=φ或垂直90=λ时:根本无法滑移,硬取向3. 当取向因子介于0~0.5之间时:单系滑移时晶体的转动说明滑移时晶体发生转动的结论:1. 金属在单纯切应力的作用下滑移,晶体的取向不改变2. 金属在任意一个力的作用下滑移,总是分解为沿滑移方向的分切应力和垂直于滑移面的分正应力3. 晶体在滑移的同时发生滑移面和滑移方向的转动只有一个滑移面的密排六方金属为例说明滑移时晶体发生转动现象:1. 假如拉伸机的夹头可自由移动,这时滑移面的滑移方向保持不变,而拉伸轴的方向发生变化2. 假如拉伸机的夹头固定,则拉伸轴的方向不变,而晶体的取向发生变化a) 试样中部滑移面朝着与拉伸轴平行的方向转动,使φ角增加λ角减小,从而晶体位向发生变化说明滑移时晶体发生转动的分析图6.91. 滑移面发生转动:将作用在21O O ''和上的外加应力分解,滑移面上最大切应力方向上的切应力21ττ和,滑移面法线方向上的正应力21n n σσ和,这时21n n σσ和就会组成一个力偶使滑移面发生转动2. 滑移方向发生转动:当最大切应力方向与滑移方向不一致时,晶体还会以滑移面法线方向为轴发生转动,将最大切应力21ττ和分解:滑移方向上的21ττ''和,垂直于滑移方向上的b b ττ'和,这时b b ττ'和组成的力偶将使晶体的滑移方向发生变化3. 同理,在压缩时晶体的滑移面则趋向于与压力方向垂直的位置,而滑移面的法线趋向于与压力轴重合说明滑移时晶体发生转动的结论:1. 滑移时不仅滑移面发生转动2. 滑移方向也在发生变化3. 即晶体的位向在发生变化4. 取向因子也在发生变化a) 如果某一滑移系的取向处于软取向:那么拉伸时晶体取向发生变化,滑移面的法向与外力方向远离45度,滑移越来越困难,几何硬化b) 如果某一滑移系的取向处于硬取向:那么拉伸时晶体取向发生变化,滑移面的法向与外力方向趋于45度,滑移越来越容易,几何软化多系滑移晶体的转动规律是在单系滑移条件下讨论的晶体的转动规律多出现于滑移系较少的密排六方结构的金属中立方晶系的金属滑移时晶体的转动:1.滑移首先发生在取向最有利的滑移系上——滑移过程中晶体发生转动——动或者交替开动2.如果外力轴的方向合适,滑移一开始就在一个以上的滑移系上同时进行3.在两个或更多的滑移系上进行的滑移,我们称之为多系滑移多滑移所产生的滑移带通常呈交叉型如图6.11所示交滑移所产生的滑移带会出现曲折或波纹状单滑移和多滑移的加工硬化效果可以从图6.12看出:交滑移1.第一阶段:只有一个滑移系,加工硬化效果很小2.第二阶段:晶体转动发生多滑移,滑移系间相互交割,加工硬化效果突然上升3.第三阶段:晶体取向改变,滑移面可能沿一个滑移方向滑移,加工硬化效果下降4.。
学习情境三金属材料塑性变形对组织性能的影响
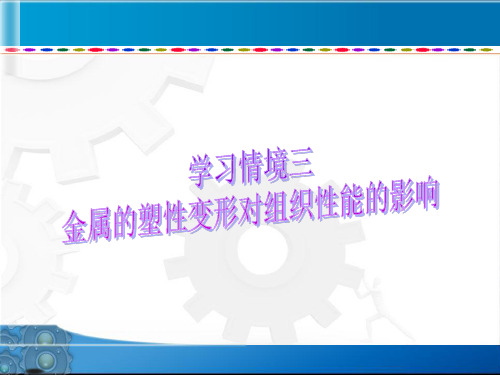
2. 晶粒位向的影响
由于各相邻晶粒位向不同,当一处利于滑移方向晶粒发生滑 移时,必然受到周围位向不同的其他晶粒的约束,使滑移受 到阻碍,从而提高金属塑性变形抗力。
(二) 晶粒大小的影响 晶粒越细,其强度和硬度越高。
细晶强化
晶粒越细晶界越 ,不同位向的晶粒也越 滑 移抗力 强度
晶粒越细晶粒数目越 变形均匀性 应力集 中,裂纹过早产生、扩展 塑性、韧性
一、金属材料变形特性
材料在外力的作用下,变形过程一般可分三个阶段:弹性 变形、塑性变形和断裂。其中对组织和性能影响最大的是 塑性变形阶段。
单晶体的滑移
多晶体
二、单晶体的塑性变形
单晶体塑性变形基本形式:滑移和孪生。
(一)滑移
1、滑移定义
滑移:指晶体在切应力的作用下, 晶体的一部分沿一定的晶面 (滑移面)上的一定方向(滑移方向)相对于另一部分发生滑动。 滑移带:当试样经过塑性变形后,在显微镜下观察,可在表面 看到许多相互平行的线条,称之为滑移带。 若干条滑移线组成一个滑移带。
三、 多晶体的塑性变形
单个晶粒变形与单晶体相似。
而多晶体变形是一个不均匀的塑性变 形过程。
(一)晶界及晶粒位向差的影响
1. 晶界的影响
当位错运动到晶界附近时,由于 晶界处的原子排列紊乱,缺陷和 杂质多,能量高,对位错的滑移
起阻碍作用,位错受到晶界的阻
碍而堆积起来,称位错的塞积。使 位错运动阻力增大,从而使金属 的变形抗力提高。
位错运动使其由冷塑性变形时的 无序状态变为垂直分布,形成亚 晶界,这一过程称多边形化。
回复带来的组织性能变化 (1) 宏观应力基本去除,微观应
力仍然残存;
(2)力学性能,如硬度和强度稍 有降低,塑性稍有提高;
《金属的变形特性》课件
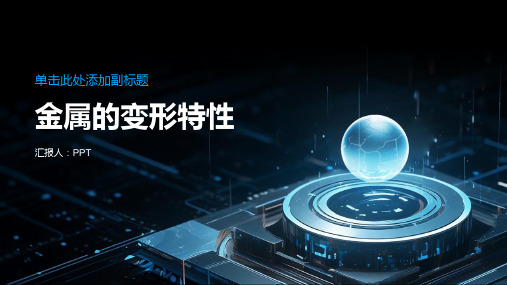
蠕变:金属在高温下缓 慢发生的塑性变形
金属变形的分类
塑性变形:金属在外力作用 下发生形变,外力消失后不 能完全恢复原状
弹性变形:金属在外力作用 下发生形变,外力消失后恢 复原状
脆性变形:金属在外力作用 下发生断裂,无法恢复原状
蠕变变形:金属在高温下缓 慢发生塑性变形,无法恢复
原状
金属变形的影响因素
拉伸:将金属拉伸成各种 形状和尺寸的零件
弯曲:将金属弯曲成各种 形状和尺寸的零件
焊接:将金属焊接在一起 形成整体结构
在结构设计和制造中的应用
结构设计:利用金属的变形特性,设计出更坚固、更轻便的结构 制造工艺:利用金属的变形特性,提高制造效率和质量 材料选择:根据金属的变形特性,选择合适的材料进行加工 性能优化:通过调整金属的变形特性,提高产品的性能和耐用性
在新材料的开发中的应用
提高材料的强度 和韧性
改善材料的耐磨 性和耐腐蚀性
优化材料的热处 理性能
提高材料的疲劳 寿命和疲劳强度
感谢观看
汇报人:PPT
添加标题
添加标题
添加标题
添加标题
应力-应变关系:金属在塑性变形 过程中,应力与应变的关系遵循 胡克定律
塑性变形的恢复:金属在塑性变 形后,可以通过热处理等方式恢 复其原始形状
04
金属的弹性变形
弹性变形的定义和分类
定义:金属在外力作用下产生的可恢复的变形 分类:分为线弹性变形、面弹性变形和体弹性变形 线弹性变形:金属在轴向或径向受到外力作用时产生的变形 面弹性变形:金属在平面内受到外力作用时产生的变形 体弹性变形:金属在三维空间内受到外力作用时产生的变形
单击此处添加副标题
金属的变形特性
汇报人:PPT
金属材料强度及变形性能分析

金属材料强度及变形性能分析简介:金属材料的强度和变形性能是决定材料使用和应用范围的重要性能指标。
强度指材料抵抗外力破坏的能力,而变形性能则表征材料在外力作用下的形变特性。
本文将重点分析金属材料的强度和变形性能,并对其影响因素进行深入探讨。
一、金属材料的强度分析:1. 抗拉强度:金属材料的抗拉强度是指材料在拉伸力作用下抵抗破坏的能力。
抗拉强度取决于材料的原子结构、晶粒尺寸、晶体缺陷等因素。
常见的金属材料如钢、铝、铜等具有不同的抗拉强度。
2. 屈服强度:屈服强度是金属材料在拉伸过程中,从线性弹性阶段到非线性弹性阶段的临界点。
屈服强度是材料首次发生可见塑性变形的应力水平。
屈服强度反映了金属材料在外力作用下的抗变形能力。
3. 延伸率和断裂伸长率:延伸率和断裂伸长率是反映材料延展性能的重要参数。
延伸率指的是材料在断裂前的拉伸程度,断裂伸长率是指材料在断裂时相对于原始长度的变化程度。
较高的延伸率和断裂伸长率意味着材料具有良好的可塑性和变形能力。
二、金属材料的变形性能分析:1. 弹性变形:弹性变形是指金属材料在外力作用下具有恢复性的形变。
弹性变形区域内,材料的形状通过去除外力而恢复到初始状态。
弹性变形的特点是应变与应力呈线性关系,且应力和应变之间的关系服从胡克定律。
2. 塑性变形:塑性变形是指金属材料在外力作用下发生的不可逆形变,形变后无法完全恢复到初始状态。
金属材料的塑性变形可以通过冷加工、热加工等方式实现。
塑性变形主要由材料内部的晶格滑移、位错等现象引起。
3. 硬化和回弹:硬化是指金属材料在塑性变形过程中变得更加坚硬和脆性的现象。
在连续塑性变形中,材料会经历晶格被位错锁定的过程,导致材料的硬度增加。
回弹是指金属材料在去除外力后,部分形变恢复到原始状态的现象。
三、影响金属材料强度和变形性能的因素:1. 材料的组成和制备工艺:不同元素的添加和不同的制备工艺会对金属材料的强度和变形性能产生重要影响。
2. 晶体结构和晶粒尺寸:晶体结构的不同会导致材料的强度和塑性发生变化,较大的晶粒尺寸能够提高材料的强度,但会降低塑性。
多晶体金属变形的特性

多晶体金属变形的特性
多晶体金属变形的一个重要特点是构成多晶体金属的
所有晶体变形具有非同时性。
由无数同相晶粒或不同相晶粒构成的金属。
由于各晶体的取向不同,在外力作用下,它们的变形不可能同时开始,而是那些滑移面阳适宜滑动的晶粒最先开始发生塑性变形,因此变形总是从那些比较弱的晶粒率先开始。
多晶体拉伸变形曲线变形的不均一性是多晶体塑性变形的第二个特点。
这种变形的不均一性不仅体现在同相不同晶粒之间,也表现在不同相之间。
即基体金属晶粒和第二相晶粒之间。
更进一步说,即使在同一晶粒几部变形也不均匀。
多晶体模型
时间性是多晶体金属塑性变形的第三个特点。
正国为多晶体金属塑性变形行为具有时间性,因此,对高温条件下服役的金属,通常采用应力、应变和时间三个变形来来描述金属的失效行为。
多晶体塑性变形模型
多晶体金属在塑性变形过程中,金属的机械性能和其它性能变化是多金属晶体变形的第四个特点,最突出的现象就是加工硬化现象。
位错的透射电镜形貌多晶体塑性变形的第五个特点是晶界所表现的行为,在低温条件多晶体金属发生塑性变形时,变形通常在晶内进行。
高温时晶粒会沿着晶界动力,甚至导致开裂。
多晶体金属塑性变形开裂,孪晶界开裂。
金属的冷变形和热变形的含义和特点
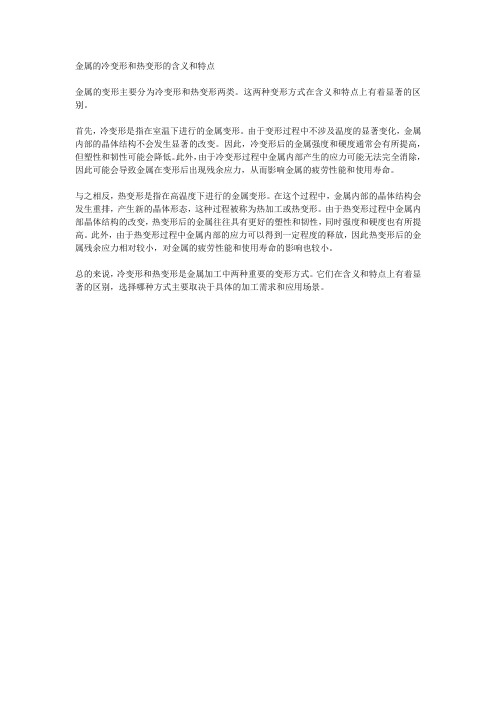
金属的冷变形和热变形的含义和特点
金属的变形主要分为冷变形和热变形两类。
这两种变形方式在含义和特点上有着显著的区别。
首先,冷变形是指在室温下进行的金属变形。
由于变形过程中不涉及温度的显著变化,金属内部的晶体结构不会发生显著的改变。
因此,冷变形后的金属强度和硬度通常会有所提高,但塑性和韧性可能会降低。
此外,由于冷变形过程中金属内部产生的应力可能无法完全消除,因此可能会导致金属在变形后出现残余应力,从而影响金属的疲劳性能和使用寿命。
与之相反,热变形是指在高温度下进行的金属变形。
在这个过程中,金属内部的晶体结构会发生重排,产生新的晶体形态,这种过程被称为热加工或热变形。
由于热变形过程中金属内部晶体结构的改变,热变形后的金属往往具有更好的塑性和韧性,同时强度和硬度也有所提高。
此外,由于热变形过程中金属内部的应力可以得到一定程度的释放,因此热变形后的金属残余应力相对较小,对金属的疲劳性能和使用寿命的影响也较小。
总的来说,冷变形和热变形是金属加工中两种重要的变形方式。
它们在含义和特点上有着显著的区别,选择哪种方式主要取决于具体的加工需求和应用场景。
第六章材料科学基础
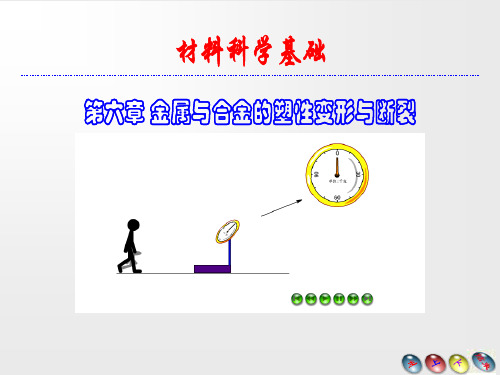
§6.1.1 普弹性
图 弹性变形与塑性变形
普弹性:应力与应变间符合线性关系,即满足虎克定律;
加上或去除应力时应变都能瞬时达到平衡
弹性的实质是原子作用势 的不对称性。
可以用双原子模型来解释。
图 双原子模型
弹性变形的主要特点是: (1)可逆性 去掉外力,变
s k s cos cos
τk称为临界分切应力,与金属 的晶体结构、纯度、加工状 态、试验温度与加载速度有 关,而与外力的大小、方向 及作用方式无关。
图 镁单晶屈服应力与晶体取向的关系
k取决于金属的本性,不受,的影响; 或=90时,s ;
k=scoscos s的取值 ,=45时,s最小,晶体易滑移;
形就消失。 (2)线性 应力和应变间满
足直线关系。 (3)弹性变形量小 一般说
来,金属材料和陶瓷材料 的弹性变形很小,高聚物 材料的弹性变形可以比较 大。
E G
G E
2(1 )
弹性模量是材料结合强度的标志之一。主要的影响因素有: (1)结构 弹性模量与原子序数呈周期性变化趋势。 (2)温度的影响 T升高,热振动加剧,晶格势能发生变
螺位错的双交滑移:交滑移后的螺位错再转回到原滑移面的过程。
9. 滑移的表面痕迹 单滑移:
单一方向的滑移带; 多滑移:
相互交叉的滑移带; 交滑移:
波纹状的滑移带。
滑移的位错机制
① 位错的运动是晶体的滑移 滑移是位错在切应力作用下沿着滑移面逐步移动形成的。
② 位错的增殖——弗兰克-瑞德位错源 ③ 位错的交割与塞积
图 工业纯铜中的滑移线
滑移:在切应力作用下,晶体的一部分相 对于另一部分沿着一定的晶面(滑移面) 和晶向(滑移方向)产生相对位移,且不 破坏晶体内部原子排列规律性的塑变方式。
金属材料的变形机制从弹性到塑性的转变
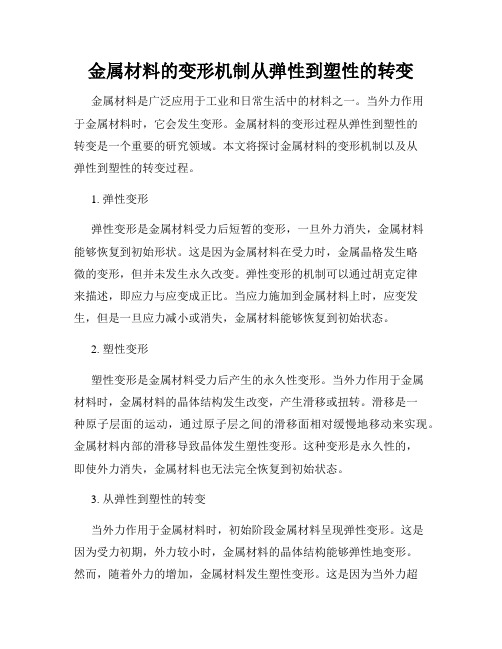
金属材料的变形机制从弹性到塑性的转变金属材料是广泛应用于工业和日常生活中的材料之一。
当外力作用于金属材料时,它会发生变形。
金属材料的变形过程从弹性到塑性的转变是一个重要的研究领域。
本文将探讨金属材料的变形机制以及从弹性到塑性的转变过程。
1. 弹性变形弹性变形是金属材料受力后短暂的变形,一旦外力消失,金属材料能够恢复到初始形状。
这是因为金属材料在受力时,金属晶格发生略微的变形,但并未发生永久改变。
弹性变形的机制可以通过胡克定律来描述,即应力与应变成正比。
当应力施加到金属材料上时,应变发生,但是一旦应力减小或消失,金属材料能够恢复到初始状态。
2. 塑性变形塑性变形是金属材料受力后产生的永久性变形。
当外力作用于金属材料时,金属材料的晶体结构发生改变,产生滑移或扭转。
滑移是一种原子层面的运动,通过原子层之间的滑移面相对缓慢地移动来实现。
金属材料内部的滑移导致晶体发生塑性变形。
这种变形是永久性的,即使外力消失,金属材料也无法完全恢复到初始状态。
3. 从弹性到塑性的转变当外力作用于金属材料时,初始阶段金属材料呈现弹性变形。
这是因为受力初期,外力较小时,金属材料的晶体结构能够弹性地变形。
然而,随着外力的增加,金属材料发生塑性变形。
这是因为当外力超过某个临界值时,滑移开始在金属材料中发生,导致塑性变形。
一旦滑移开始,金属材料将不可逆地发生形状改变,即从弹性变形转变为塑性变形。
在金属材料的变形机制中,还存在一些影响因素。
其中一个重要因素是温度。
在高温下,金属材料的滑移速率增加,塑性变形更容易发生。
另一个因素是晶粒结构和晶界。
细小的晶粒和多晶晶界可以促进滑移的发生,从而导致更容易的塑性变形。
总结起来,金属材料的变形机制从弹性到塑性的转变是一个复杂的过程。
弹性变形是一种可逆的临时变形,而塑性变形则是永久性的变形。
当外力作用于金属材料时,初始阶段呈现弹性变形,随着外力的增加,金属材料发生塑性变形。
这种转变通常受温度和晶粒结构等因素的影响。
金属的塑性变形

二、金属的塑性变形材料受力后要发生变形,变形可分为三个阶段:弹性变形;弹-塑性变形;断裂。
外力较小时产生弹性变形,外力较大时产生塑性变形,而当外力过大时就会发生断裂。
在整个变形过程中,对材料组织、性能影响最大的是弹-塑性阶段的塑性变形部分。
如:锻造、轧制、拉拔、挤压、冲压等生产上的许多加工方法,都要求使金属产生变形,一方面获得所要求的形状及尺寸,另一方面可引起金属内部组织和结构的变化,从而获得所要求的性能。
因此研究塑性变形特征与组织结构之间相互关系的规律性,具有重要的理论和实际意义。
弹性变形(Elastic Deformation)1.1 弹性变形特征(Character of Elastic Deformation)1.变形是可逆的;2.应力与应变保持单值线性函数关系,符合Hooke定律:σ=Eε,τ=Gγ,G=E/2(1-ν) 3.弹性变形量随材料的不同而异。
1.2 弹性的不完整性(Imperfection of Elastane)工程上应用的材料为多晶体,内部存在各种类型的缺陷,弹性变形时,可能出现加载线与卸载线不重合、应变的发展跟不上应力的变化等现象,称为弹性的不完整性,包括包申格效应、弹性后效、弹性滞后等。
1.包申格效应(Bauschinger effect)现象:下图为退火轧制黄铜在不同载荷条件下弹性极限的变化情况。
曲线A:初次拉伸曲线,σe=240Pa曲线B:初次压缩曲线,σe=178Pa曲线C:B再压缩曲线,σe↑,σe=278Pa曲线D:第二次拉伸曲线,σe↓,σe=85Pa可见:B、C为同向加载,σe↑;C、D为反向加载,σe↓。
定义:材料经预先加载产生少量塑性变形,然后同向加载则σe升高,反向加载则σe降低的现象,称为包申格效应。
对承受应变疲劳的工件是很重要的。
2.弹性后效(Anelasticity)理想晶体(Perfect crystals):实际金属(Actual metal):弹性后效示意图这种在弹性极限范围内,应变滞后于外加应力,并和时间有关的现象称为弹性后效。
金属的冷变形和热变形的含义和特点。

一、金属的冷变形和热变形的含义金属的变形是指通过外力使金属产生形状、尺寸或结构上的改变。
金属的变形可以分为冷变形和热变形两种类型。
冷变形是指在常温下进行金属加工,而热变形则是在高温下对金属进行加工。
两者各有其特点和应用范围,对于金属加工工艺具有重要意义。
二、冷变形的特点1. 需要较大的变形压力:在常温下,金属的变形抗力较大,需要较大的变形压力才能使金属发生塑性变形。
冷变形通常需要采用较大的压力设备,如压力机、滚压机等。
2. 变形后金属强度提高:冷变形可以使金属晶粒细化并产生变形硬化效应,提高金属的强度和硬度。
在一些对强度要求较高的零部件制造中,常采用冷变形工艺来提高材料的性能。
3. 变形过程产生热量少:冷变形过程中,由于变形速度较快,变形所产生的热量较少,大部分会随着金属的散热而失去,因此变形温度相对稳定。
4. 加工硬化效应明显:在冷变形过程中,金属材料会产生加工硬化现象,使材料的强度和硬度得到提高。
冷变形还会改善金属材料的力学性能和物理性能,提高材料的综合性能。
三、热变形的特点1. 变形易:在高温下,金属材料的塑性较好,变形抗力较小,因此比冷变形更容易进行金属加工。
通过热变形可以得到复杂形状的零部件,提高产品的精密度和成型性。
2. 变形后金属强度降低:热变形会使金属晶粒得到再结晶,使材料的强度和硬度降低,但同时也改善了金属材料的延展性和韧性,提高材料的成形性能。
3. 变形过程产生大量热量:在高温下进行金属加工时,金属的变形会产生大量的热量,需要及时采取降温措施对金属进行冷却,以防止过热和热裂现象的发生。
4. 加工硬化效应不明显:在热变形过程中,金属材料的加工硬化效应较小,因此通常需要通过热处理等方法来提高材料的强度和硬度,以满足实际使用要求。
四、冷变形与热变形的应用领域1. 冷变形在精密五金加工、汽车零部件制造、航空航天制造等领域得到广泛应用,可以有效提高产品的强度和硬度,提高零部件的精密度和表面质量。
金属及合金的塑性变形与断裂
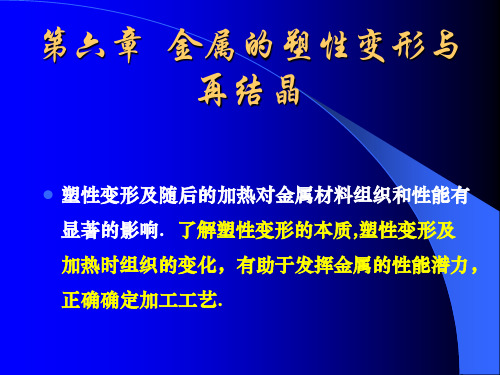
晶粒。
工业纯铁在塑性变形前后的组织变化
(a) 正火态
(b) 变形40%
(c) 变形80%
5%冷变形纯铝中的位错网
塑性变形对金属组织的影响
晶粒拉长,纤维组织 → 各向异性 (沿纤维方向的强度、塑性最大)
变形10% 100×
变形80% 纤维组织
100×
变形40% 100×
工业纯铁 不同变形度 的显微组织
2.位错的增殖
位错增值模型.swf 螺位错双交滑移增殖模型.swf
3.位错的交割与塞积
位错在障碍物前的塞积
位错:AB 、CD (固定不动)
mn⊥b2
位错
当两条位错线交割时,每条位错线上都可能出 现长度相当于另一条位错线b的割阶,这就增加
了位错长度,是位错能量升高,是变形所需的
总能量升高; 另外,当割阶垂直于滑移面时, 此割阶有阻止位错运动的作用,会使晶体进一 步滑移的抗力增加,这是加工硬化的主要原因。
量和分布有关。第二相
可以是纯金属、固溶体
或化合物,工业合金中
第二相多数是化合物。
+钛合金(固溶体第二相)
当在晶内呈颗粒状弥散分布时,第二相颗粒越细, 分布越均匀,合金的强度、硬度越高,塑性、韧性 略有下降,这种强化方法称弥散强化或沉淀强化。 弥散强化的原因是由于硬的颗粒不易被切变,因而 阻碍了位错的运动,提高了变形抗力。
固溶强化的实质是溶质原子与位错的弹性交互作用阻碍了位错 的运动。即溶质原子与位错弹性交互作用的结果,如下图所示,使 溶质原子趋于聚集在位错的周围,以减小畸变,使系统更加稳定, 此即称为柯氏(cotrell)气团。显然,柯氏气团对位错有“钉扎”作用。 为了使位错挣脱气团而运动,必须施加更大的外力。因此,固溶体 合金的塑性变形抗力要高于纯金属。
金属的塑性变形

五、金属变形程度
常用锻造比表示 Y=F0/F F0表示变形前面积 F表示变形后面积
钢锭Y=2-3 合金钢Y=3-4 高速钢Y=5-12
六、冷、热变形比较
热变形特点:
(1)均匀、细化晶粒 (2)消除加工硬化
(3)高温、塑性好 (4)氧化严重
(5)精度差
(6)设备贵,维修费高
冷变形特点:
(1)不加热
(2)精度、表面质量好
单晶体的滑移
多晶体
二、冷变形后的金属组织与性能 塑Байду номын сангаас变形后:
(1)产生纤维组织,引起各向异性 (2)晶格扭曲 (3)晶粒间产生碎晶 使金属的强度、硬度增加,塑性、韧性 下降,即加工硬化。增加滑移阻力,使金 属形变强化
1.纤维组织 2.加工硬化 3.残余内应力
2.加工硬化(形变硬化、冷作硬化)
(3)硬度、强度高 (4)材料有方向性
(5)设备贵,存在残余应力,易产生裂纹。
§1-2 锻前加热与锻后冷却
一、锻造前加热目的及方法
目的: 提高金属塑性,降低变形抗力.易于锻造成形 并获得好的锻后组织.
按加热热源不同可分为:
1.火焰加热,燃料来源方便,炉子修造简单,加热费 用低适应范围广。用于各种大、中、小型坯料的加热。 劳动条件差,加热速度慢,加热质量难于控制。
§1-1 金属的塑性变形
压力加工:在外力作用下,使金属产生塑性变形,获得一定几 何形状、尺寸和力学性能毛坯,原材料或零件的加工方法。压 力加工有自由锻、模锻、板料冲压、轧制、挤压、拉拔等。
一、塑性变形实质 1、单晶体塑性变形 (1)当无外力,晶格正常排列。 (2)外力作用使原子离开平衡位置,晶格变形。 (3)当剪应力足够大,沿晶面移动一个或几个原子距离。 2、多晶体塑性变形 多晶体是多个位向不同变形总和。特点: (1)变形过程复杂。 (2)变形抗力比单晶体大的多。
金属及合金的塑性变形
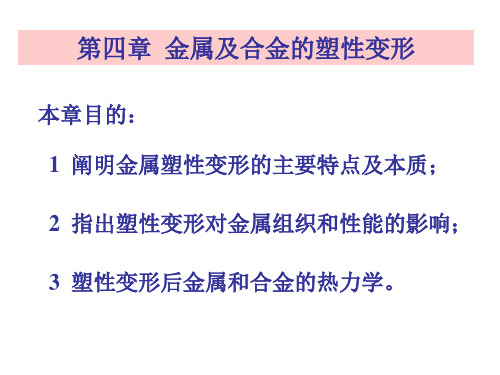
§4-5 多晶体与合金的塑性变形
晶界
一 多晶体塑性变形特点
⑴ 单个晶粒与单晶体一致; ⑵ 各晶粒的变形具不同时性: 分批、逐次。 原因:取向不同 ⑶ 变形具不均匀性 晶粒内部与边界、 晶粒之间(取向)。
⑷ 多晶体变形抗(阻)力> 单晶体
原因: ① 晶界阻碍位错运动;
② 位向差→晶粒之间须协调
意义: 晶界强化——金属材料强化机制之一 霍耳—配奇公式: ζs = ζ0+Kd-1/2
〔111 〕 (110)
面心立方 (f.c.c) 滑移面:{111} (111), (111), (111), (111); 滑移方向:〈110〉 滑移系数: 4×3=12
(111) 〔110〕
密排六方:
滑移面{0001}
滑移方向〈1120 〉 滑移系数目: 1×3=3
Hale Waihona Puke (3)滑移系数目的实际意义 —判断塑性变形能力 ① 滑移系数目愈多,塑性愈好; ② 滑移系数相同时,滑移方向多者塑性较好 塑性排序:f.c.c>b.c.c>h.c.p
§4-2 弹性变形
一、弹性形变的宏观定律
E G 21
二、弹性变形能
三、影响弹性变形的因素
§4-3 塑性形变的表象
一、塑性形变的宏观特征
二、塑性形变在纤维组织中的反映
1. 晶粒外形的变化
2. 晶粒内部的变化
§4-4 单晶体的塑性变形
F
塑性变形研究思路: ① 基本单元——单晶体变形特性 ② 晶界影响——多晶体变形特性 ③ 相界——合金变形特性 塑性变形方式:滑移;孪生
孪生与滑移变形比较
1.孪生:均匀切变。滑移:塑性变形是不均勺的。
2.孪生:各晶面移动量与其离孪晶面距离成正比,相邻晶团相
- 1、下载文档前请自行甄别文档内容的完整性,平台不提供额外的编辑、内容补充、找答案等附加服务。
- 2、"仅部分预览"的文档,不可在线预览部分如存在完整性等问题,可反馈申请退款(可完整预览的文档不适用该条件!)。
- 3、如文档侵犯您的权益,请联系客服反馈,我们会尽快为您处理(人工客服工作时间:9:00-18:30)。
思考:为什么会出现屈服现象?
金属变形特性
16
塑性变形过程--屈服
屈服强度:表示材料对
开始发生微量塑性变形
的抗力,也称为屈服极
限,用σs表示。对具有 屈服现象的材料用屈服
现象发生时对应的应力
表示;对屈服现象不明
显的材料,则以所产生
的塑性应变变0.2%时的
应力值表示。
金属变形特性
17
塑性变形过程--均匀变形
21
塑性变形过程--断裂
脆性断裂:断裂前因并未经过明显塑性变形,故其断口 常具有闪烁的光泽,这种断裂叫“脆性断裂”。脆性断 裂可沿晶界发生,称为“晶间断裂”,断口凹凸不平; 脆性断裂也可穿过各个晶粒发生,称为“穿晶断裂”, 断口比较平坦。
金属变形特性
沿晶脆性断口 22
➢ 材料的最大弹性变形量随材料的不同而不同。
金属变形特性
10
弹性模量
在弹性变形范围内,应力与应变服从虎克定律。
式中,σ、τ分别为正应力和 σ
切应力,ε、γ分别为正应变和
切应变;比例系数E称为弹性
模量(杨氏模量),G称为切 σe
变模量,它反映材料对弹性变
形的抗力,代表材料的“刚
度” 。
o
ε
金属变形特性
11
弹性模量代表着使原子离开平衡位置的难易程度,是 表征晶体中原子间结合力强弱的物理量。
弹性模量是表征材料在发生弹性变形时所需要施加力 的大小。
在给定应力下,弹性模量大的材料只发生很小的弹性 应变,而弹性模量小的材料则发生比较大的弹性应变。
结合能是影响弹性模量的主要因素,结合键之间的结 合键能越大,则弹性模量越大,结合键能与弹性模量 之间有很好的对应关系。
金属变形特性
12
金刚石具有最高的弹性模量,E=1000GPa
工程陶瓷如碳化物、氮化物、氧化物等结合键能 也比较高,它们的弹性模量为250~600GPa
金属键结合的金属材料弹性模量要抵一些,常用 金属材料的弹性模量约为70~350GPa
聚合物由于二次键的作用,弹性模量仅为0.7~ 3.5GPa
前承受最大载荷时的应力。 F F b
b
σb =Fb/S0 (MPa)
它表征了材料在拉伸条 件下所能承受的最大应力。 o
l
抗拉强度 — 是脆性材料选材的依据。
Байду номын сангаас
金属变形特性
8
常用 δ 和 ψ 作为衡量塑性的指标。
伸长率: lk l0 100% F
l0
断面收缩率: s0 sk 10% 0
s0
d0
F
l0
塑性:是指材料能发生塑性变形的量或能力,用伸 长率(δ%)或断面减缩率(ψ%)表示。
实质:塑性变形的实质是在应力的作用下,材料内
部原子相邻关系已经发生改变,故外力去除后,原
子回到另一平衡位置,物体将留下永久变形。
金属变形特性
15
塑性变形过程--屈服
屈服:材料开始发生塑性变形。
屈服现象:即使外力不 再增加,试样也会继续 变形,这种变形属于塑 性变形,在拉伸曲线上 会出现锯齿状的平台。 这是部分材料所具有的 特征。
F'
F
(MPa)
σ= F’ /S
SS
外力 —— 内力 —— 应力
金属变形特性
5
拉伸实验
F
d0 l0
F
F S0
F
Fs
Fe
Fb
s e
b
k
L
dk
o
缩颈
l
l l0
lk
拉伸曲线 应力—应变曲线
e — 弹性极限点 K — 断裂点
S — 屈服点
b — 极限载荷点
金属变形特性
6
强度 材料在外力作用下,抵抗塑性变形和断裂的能力。
L dk
lk
良好的塑性是金属材料进行塑性加工的必要条件。
金属变形特性
9
(1)两种基本变形
弹性变形
材料受外力作用时产生变形,当外力去除后恢复 其原来形状,这种随外力消失而消失的变形,称为 弹性变形。
特点
➢ 变形是可逆的,在外力去除后它便可以完全恢复,变 形消失。
➢ 在弹性变形范围内,应力与应变之间保持单值线性函 数关系。
金属变形特性
13
弹性变形的本质
弹性变形的实质是在应力的作用下,材料内部原
子间距就偏离了平衡位置,但未超过其原子间的结合
力。晶体材料反映为晶格发生了伸长(缩短)或歪扭。
原子的相邻关系还未发生改变,故外力去除后,原子
间结合力便可以使变形完全恢复。
金属变形特性
14
塑性变形
定义:不能恢复的永久性变形叫塑性变形。当应力 大于弹性极限时,材料不但发生弹性变形,而且还 发生塑性变形,即在外力去除后,其变形不能得到 完全的恢复,而具有残留变形或永久变形。
金属变形特性
20
塑性变形过程--断裂
断裂:变形量大至K点,试样发生断裂。
实质:断裂的实质原子间承受的力超出最大吸引力,原 子间的结合破坏而分离。
韧性断裂:在断裂前有明 显塑性变形后发生的断裂 叫“韧性断裂”。在晶体 构成的材料中,内部的晶 粒都被拉长成为细条状, 断口呈纤维状,灰暗无光。
金属变形特性
(a) 屈服强度(σS) 指材料在外力作用下,产生屈服现象时的应力。 σS =Fs/S0 (MPa) 它表征了材料抵抗微量塑性变形的能力。
当材料单位面积上所受的应力σe<σ<σs时, 只产生微量的塑性变形。当σ>σs时,材料将产生
明显的塑性变形。
金属变形特性
7
(b)抗拉强度(σb )
抗拉强度是材料在拉断
金属变形特性
18
塑性变形过程--颈缩
颈缩:试样将开始发生不均匀的塑性变形,产生了颈缩, 即塑性变形集中在一局部区域进行。
特点:颈缩发生后,宏观表现为外力在下降,工程应力 在减小,但颈缩区的材料承受的真实应力依然在上升。
金属变形特性
19
塑性变形过程--颈缩
开始发生颈缩时对应 的工程应力σb ,这 时试样出现失稳,颈 缩真实应力依然在上 升,但能承受的总外 力在下降。
第6章
金属及合金的塑性变形
金属变形特性
1
本章知识结构
金属的变形特性 晶体的塑性变形 组织与性能的变化
单晶体的塑性变形 多晶体的塑性变形 合金的塑性变形
金属变形特性
2
6.1 金属的变形特性
纳米铜的室温超塑性
金属变形特性
3
金属变形特性
4
静载荷 作用在机件上的外力——载荷
动载荷
F
F
F’
F
F = F’
均匀变形:在屈服后的变形阶段,试样整体进行均 匀的塑性变形。如果不再增加外力,材料的变形将 不能继续下去。
原因:维持材料均匀变形的原因是材料发生了加工 硬化。 已经发生变形处的强度提高,进一步变形困 难,即变形要在更大的应力作用下才能进行。下一 步的变形发生在未变形或变形相对较小的位置,达 到同样变形后,在更大的应力作用下发生变形。