金属基复合材料(MMC)
[材料科学]金属基复合材料
![[材料科学]金属基复合材料](https://img.taocdn.com/s3/m/bd12e168f121dd36a22d8208.png)
33
三种热等静压工艺
• 先升压后升温:其特点是无需将工作压力 开到最高压力,随着温度升高,气体膨胀, 压力不断升高,直至达到需要压力,适用 于金属包套的工艺制备;
• 先升温后升压:适用于玻璃包套制备复合 材料;
• 同时升温升压:适合于低压成形、装入量 大、保温时间长的工件制备。
34
热等静压工艺优缺点
混合
热压 冷压-烧结
坯或零件
封装除氧
挤压
粉末冶金法的工艺流程
23
粉末冶金法的优缺点
• 粉末冶金复合法的工艺主要优点是:基体金属或合金 的成分可自由选择,基体金属与强化颗粒之间不易发 生反应;可自由选择强化颗粒的种类、尺寸,还可多 种颗粒强化;强化颗粒添加量的范围大;较容易实现 颗粒均匀化。
• 但材料的成本较高,制备大尺寸的零件和坯料有一定 困难,而且粉末混合和防止氧化是工艺的关键,必须 采取有效措施加以控制,以及微细强化颗粒的均匀分 散困难;颗粒与基体的界面不如铸造复合材料等。
密封袋材的设计较困难
(HIP)
温下,高压气体加压烧结
超高压烧结 用超高压装置在高温下加压 可不用烧结助剂
制品尺寸不能过大
(UHP)
烧结
冲击加压烧结 置粉末于容器中,利用机械 短时间内可以烧结
不易控制
(Dina-Pac) 或炸药产生瞬时高温高压
液相烧结 烧结助剂发挥烧结作用
较低温度下可以进行高密度 若液相以玻化状态残留,
19
不连续增强相复合材料的制备工艺
颗粒 晶须 短纤维
铝合金—固态、液态、原位生长、喷射成型法 镁合金—液态法 钛合金—固态、液态法、原位生长法 高温合金—原位生长法 金属间化合物—粉末冶金、原位生长法
【技术干货】一文简要了解金属基复合材料的常见种类、典型特性及应用

【技术干货】一文简要了解金属基复合材料的常见种类、典型特性及应用金属基复合材料(Metal Matrix Composite,MMC)是由金属基体与陶瓷(氧化物,碳化物)、金属(铅,钨,钼)或纤维(陶瓷纤维、碳纤维)等分散相结合而成的材料。
按照增加金属基体的种类,金属基复合材料可以分为铝基复合材料、镁基复合材料、钛基复合材料、铜基复合材料等。
铝基复合材料铝基复合材料(Aluminum Matrix Composites,AMC )是金属基复合材料的最大种类。
AMC基体通常是基于铝硅(Al-Si)合金以及2xxx和6xxx系列的合金。
AMC主要制造方法包括粉末冶金、搅拌铸造和渗透等,而通常使用的增强体包括:▪颗粒:氧化铝或碳化硅颗粒,含量为15-70%(体积);▪连续纤维:氧化铝、碳化硅、石墨纤维(即:高强高模碳纤维)等连续纤维;▪短切纤维:氧化铝的不连续纤维(短纤维增强复合材料)。
AMC复合材料的典型特性:▪高温下也具有高强度;▪高刚度(弹性模量);▪低密度;▪高导热系数 ;▪优异的耐磨性。
▪铝基复合材料(AMC)可用于制造汽车零件(活塞、推杆、制动部件)、高速火车的制动转子、自行车、高尔夫球杆、电子基板、高压电缆的芯材等领域。
镁基复合材料镁基复合材料主要由碳化硅(SiC)颗粒增强,其典型特性包括:▪低密度;▪高刚度;▪高耐磨性▪高温下也具有良好的强度;▪良好的抗蠕变性。
镁基复合材料用于制造赛车部件、轻型汽车制动系统、飞机零件,以及用于变速箱、变速器、压缩机和发动机。
钛基复合材料钛基复合材料主要制造工艺为粉末冶金,其常用增强体包括:▪连续碳化硅纤维(长纤维增强复合材料);▪硼化钛(TiB2)和碳化钛(TiC)颗粒(颗粒复合材料)。
Ti-SiC金属基复合材料钛基复合材料的典型特性如下所示:▪高强度;▪高刚度;▪高抗蠕变性;▪高热稳定性;▪高耐磨性。
钛基复合材料可用于制造F-16飞机起落架的结构部件、涡轮发动机部件(风扇叶片、执行器活塞、同步环、连接连杆、轴、盘)、汽车发动机部件、传动系统部件、通用机械部件等。
金属基复合材料
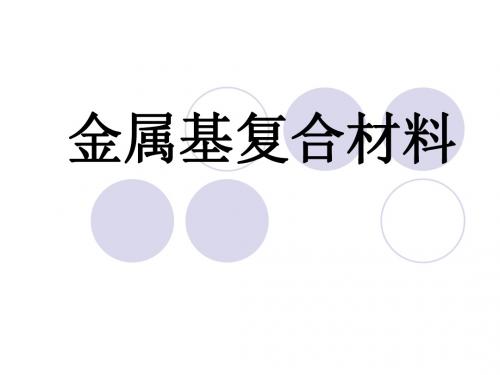
四、挤压铸造法
挤压铸造法是制造金属基复合材料较理 想的途径,此工艺先将增强体制成预成型 体,放入固定模型内预热至一定温度,浇 人金属熔体,将模具压下并加压,迅速冷 却得到所需的复合材料。
挤压铸造法特点:可以制备出增强相非常 高体积分数(40 %~50 %)的金属基复合 材料,由于在高压下凝固,既改善了金属 熔体的浸润性,又消除了气孔等缺陷,因 此,挤压铸造法是制造金属基复合材料质 量较好,可以一次成型。
六、熔体浸渗法
熔体浸渗工艺包括压力浸渗和无压浸渗。 当前是利用惰性气体和机械装置作为压力 媒体将金属熔体浸渗进多气孔的陶瓷预制 块中,可制备体积分数高达50 %的复合材 料,随后采用稀释的方法降低体积分数。
三、原位生成法
原位生成法指增强材料在复合材料制造 过程中,并在基体中自己生成和生长的方 法,增强材料以共晶的形式从基体中凝固 析出,也可与加入的相应元素发生反应、 或者合金熔体中的某种组分与加入的元素 或化合物之间的反应生成。前者得到定向 凝固共晶复合材料,后者得到反应自生成 复合材料。
原位生成复合材料的特点:增强体是 从金属基体中原位形核、长大的热力学稳 定相,因此,增强体表面无污染,界面结 合强度高。而且,原位反应产生的增强相 颗粒尺寸细小、分布均匀,基体与增强材 料间相容性好,界面润湿性好,不生成有 害的反应物,不须对增强体进行合成、预 处理和加入等工序,因此,采用该技术制 备的复合材料的综合性能比较高,生产工 艺简单,成本较低。
一、搅拌铸造法
搅拌铸造法制备金属基复合材料起源于 1968年,由S.Ray在熔化的铝液中加入氧化 铝,并通过搅拌含有陶瓷粉末的熔化状态 的铝合金而来的。
搅拌铸造法的特点是:工艺简单,操作 方便,可以生产大体积的复合材料(可到 达500 kg),设备投入少,生产成本低, 适宜大规模生产。但加入的增强相体积分 数受到制,一般不超过20 %,并且搅拌后 产生的负压使复合材料很容易吸气而形成 气孔,同时增强颗粒与基体合金的密度不 同易造成颗粒沉积和微细颗粒的团聚等现 象。
金属基复合材料的字母缩写
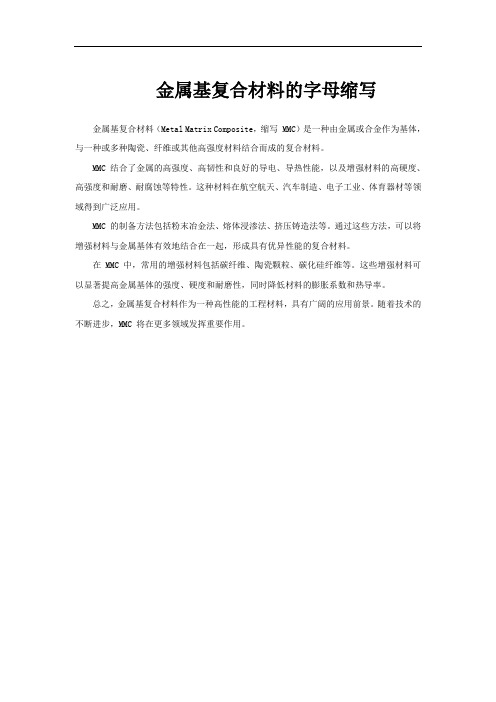
金属基复合材料的字母缩写
金属基复合材料(Metal Matrix Composite,缩写 MMC)是一种由金属或合金作为基体,与一种或多种陶瓷、纤维或其他高强度材料结合而成的复合材料。
MMC 结合了金属的高强度、高韧性和良好的导电、导热性能,以及增强材料的高硬度、高强度和耐磨、耐腐蚀等特性。
这种材料在航空航天、汽车制造、电子工业、体育器材等领域得到广泛应用。
MMC 的制备方法包括粉末冶金法、熔体浸渗法、挤压铸造法等。
通过这些方法,可以将增强材料与金属基体有效地结合在一起,形成具有优异性能的复合材料。
在 MMC 中,常用的增强材料包括碳纤维、陶瓷颗粒、碳化硅纤维等。
这些增强材料可以显著提高金属基体的强度、硬度和耐磨性,同时降低材料的膨胀系数和热导率。
总之,金属基复合材料作为一种高性能的工程材料,具有广阔的应用前景。
随着技术的不断进步,MMC 将在更多领域发挥重要作用。
金属基复合材料
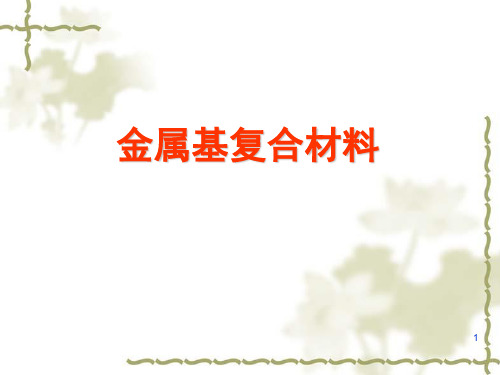
压铸成型法的具体工艺
将包含有增强材料的金属 熔体倒入预热摸具中后,迅 速加压,压力约为70-100MPa, 使液态金属基复合材料在压 力下凝固。 复合材料完全固化后顶出, 制得所需形状及尺寸的复合 材料的坯料或压铸件。
31
压铸成型法的特点
压铸工艺中,影响金属基复合材料性能的工艺因素主要 有四个:①熔融金属的温度、 ②模具预热温度、 ③使用的 最大压力、 ④加压速度。 在采用预制增强材料块时,为了获得无孔隙的复合材料, 一般压力不低于50MPa,加压速度以使预制件不变形为宜, 一般为1-3cm/s。 对于铝基复合材料,熔融金属温度一般为700-800℃,预 制件和模具预热温度一般可控制在500-800℃,并可相互补 偿,如前者高些,后者可以低些,反之亦然。 采用压铸法生产的铝基复合材料的零部件,其组织细化、 无气孔,可以获得比一般金属模铸件性能优良的压铸件。 与其他金属基复合材料制备方法相比,压铸工艺设备简 单,成本低,材料的质量高且稳定,易于工业化生产。 32
20
粉末冶金法的优点
① 热等静压或烧结温度低于金属熔点,由于高温引起的增 强材料与金属基体的界面反应少,减小了界面反应对复合材 料性能的不利影响。同时可以通过热等静压或烧结时的温度、 压力和时间等工艺参数来控制界面反应。 ② 可根据性能要求,使增强材料(纤维、颗粒或晶须)与 基体金属粉末以任何比例混合,纤维含量最高可达75%,颗粒 含量可达50%以上,这是液态法无法达到的。 ③ 降低增强材料与基体互相湿润及密度差的要求,使颗粒 或晶须均匀分布在金属基复合材料的基体中。 ④ 采用热等静压工艺时,其组织细化、致密、均匀,一般 不会产生偏析、偏聚等缺陷,可使孔隙和其他内部缺陷得到 明显改善,提高复合材料的性能。 ⑤ 金属基复合材料可通过传统的金属加工方法进行二次加 21 工,得到所需形状的复合材料构件毛坯。
金属基复合材料(MMC)制备工艺课件

VS
详细描述
机械合金化法是一种制备金属基复合材料 的有效方法。在球磨机中,将金属粉末与 增强相(如碳纳米管、陶瓷颗粒等)混合 ,在高能球磨过程中,金属粉末与增强相 在剧烈的机械力作用下发生合金化及复合 。该方法具有制备工艺简单、成本低、可 批量生产的优点。
扩散焊接法
总结词
通过在高温和压力作用下,使金属基体与增 强相之间发生相互扩散,实现冶金结合。
用于制备高尔夫球杆、滑 雪板等轻质、高强度的运 动器材。
05 喷射沉积法制备mmc
喷射沉积法的原理
喷射沉积法是一种制备金属基复合材料 的方法,其原理是将两种或多种材料通 过高速喷射流混合,并在快速凝固条件
下形成复合材料。
在喷射沉积过程中,各种材料的颗粒或 液体在高速运动中相互碰撞、混合和分
散,形成均匀的复合材料。
为了获得均匀分布的增强相, 需要采用合适的分散剂和分散
工艺。
常用的分散剂包括表面活性剂 、偶联剂、高分子聚合物等。
分散工艺可以采用球磨、超声 波振动、搅拌等方式。
压制与烧结
压制是将混合分散后的粉末压制成一 定形状和尺寸的预制件。
烧结是使预制件在高温下致密化的过 程,通过物质迁移和组织转变来实现 。
除了上述两种方法外,还有化学沉积法、物理气相沉 积法、熔融浸渗法等方法制备金属基复合材料。
详细描述
化学沉积法是通过化学反应在金属基体上沉积增强相 ,实现复合。物理气相沉积法是利用物理过程,在金 属基体上沉积增强相,制备金属基复合材料。熔融浸 渗法是将增强相(如碳纤维、陶瓷颗粒等)与金属基 体混合,经过熔融、浸渗后冷却固化,制备出金属基 复合材料。这些方法各有特点,适用范围也不同,可 根据实际需求选择合适的制备方法。
金属基复合材料(MMC)
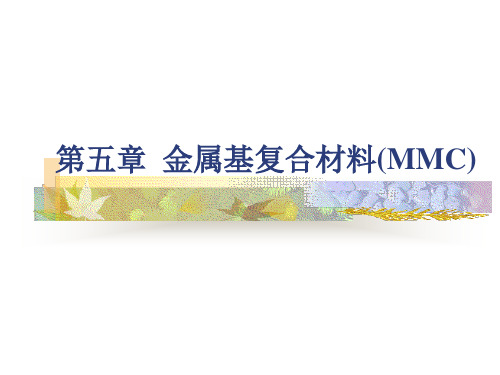
3.熔渗
将增强材料制成多孔预制体,置基体金属熔 体的上方或内部,利用毛细力的使熔体作用渗 入预制中。也可将预制体和基体金属坯料装入 一可通入流动氮气的加热炉中。通过加热,基 体金属熔化,自发渗透入网络状增强材料预制 体中
三、喷涂与喷射沉积
喷涂沉积主要应用于纤维增强金属基复合材 料的须制层的制备,也可以获得复合层状复合 材料的坯料。喷射沉积则主要用于制备颗粒增 强金属基复合材料。喷射与喷涂沉积工艺的最 大特点是增强材料与基体金属的润湿性要求低; 增强材料与熔融金属基体的接触时间短,界面 反应量少。喷涂沉积制备纤维增强金属基复合 材料时,纤维的分布均匀,获得的薄单层纤维 增强预制层可以很容易地通过扩散结合工艺形 成复合材料结构形状和板材。喷涂与喷射沉积 工艺,可以与各种陶瓷纤维或颗粒复合,即基 体金属的选择范围广。
高温性能优良。合金化后的耐热性显著提高,可以作为 高温结构材料使用,如航空发动机的压气机转子叶片等, 长期使用最高温度已达540℃
在大气和海水中有优异的耐蚀性.在硫酸、盐酸、硝酸 相氢氧化纳等介质中都很稳定
导电与导热性差.导热系数只有铜的1/l 7和铝的l/10, 比电阻为铜的25倍
常用钛合金的性能
第五章 金属基复合材料(MMC)
第一节 概 述
一、MMC的沿革与发展
二、MMC的分类
1、按增强材料形态分类 纤维增强金属基复合材料 颗粒和晶须增强金属基复合材料 2、按金属基体分类 铝基复合材料 钛基复合材料 镁基复合材料 高温合金复合材料 金属间化合物复合材料
第二节 金属基体
热压
在真空或保护气氛下直接放入热压模 或平板进行热压合热压工艺参数主要为: 热压温度、压力和时间
扩散结合的优缺点:
金属复合材料的优势和应用前景
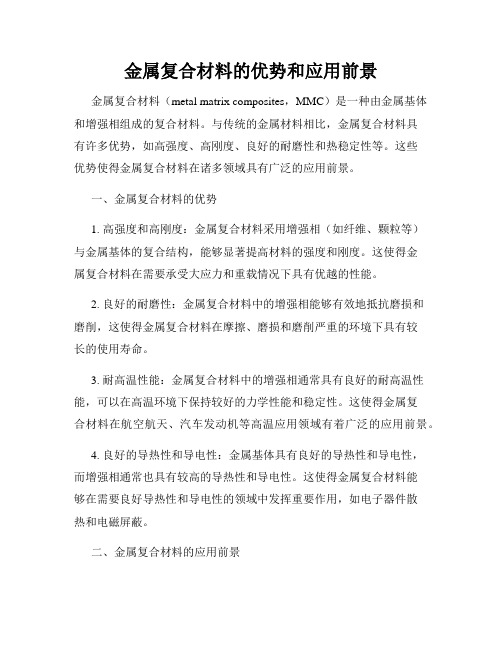
金属复合材料的优势和应用前景金属复合材料(metal matrix composites,MMC)是一种由金属基体和增强相组成的复合材料。
与传统的金属材料相比,金属复合材料具有许多优势,如高强度、高刚度、良好的耐磨性和热稳定性等。
这些优势使得金属复合材料在诸多领域具有广泛的应用前景。
一、金属复合材料的优势1. 高强度和高刚度:金属复合材料采用增强相(如纤维、颗粒等)与金属基体的复合结构,能够显著提高材料的强度和刚度。
这使得金属复合材料在需要承受大应力和重载情况下具有优越的性能。
2. 良好的耐磨性:金属复合材料中的增强相能够有效地抵抗磨损和磨削,这使得金属复合材料在摩擦、磨损和磨削严重的环境下具有较长的使用寿命。
3. 耐高温性能:金属复合材料中的增强相通常具有良好的耐高温性能,可以在高温环境下保持较好的力学性能和稳定性。
这使得金属复合材料在航空航天、汽车发动机等高温应用领域有着广泛的应用前景。
4. 良好的导热性和导电性:金属基体具有良好的导热性和导电性,而增强相通常也具有较高的导热性和导电性。
这使得金属复合材料能够在需要良好导热性和导电性的领域中发挥重要作用,如电子器件散热和电磁屏蔽。
二、金属复合材料的应用前景1. 航空航天领域:金属复合材料由于其高强度、高刚度和耐高温的特点,在航空航天领域具有广泛的应用前景。
例如,金属复合材料可以用于制造飞机结构件、发动机零部件和航天器热防护材料等。
2. 汽车工业:随着汽车行业对轻量化和节能环保要求的提升,金属复合材料作为一种重要的替代材料,其在汽车工业中的应用也越来越广泛。
金属复合材料可以应用于汽车发动机、底盘和车身结构等部件,以减轻整车重量、提高燃油效率和降低尾气排放。
3. 电子行业:金属复合材料具有良好的导热性和导电性,因此在电子行业中具有广泛的应用前景。
金属复合材料可以用于制造散热片、电磁屏蔽材料、半导体基底等,以提高电子器件的性能和稳定性。
4. 能源领域:金属复合材料的高强度、良好的耐高温性能和导热性,使其在能源领域具有潜在的应用前景。
金属基复合材料(MMC)
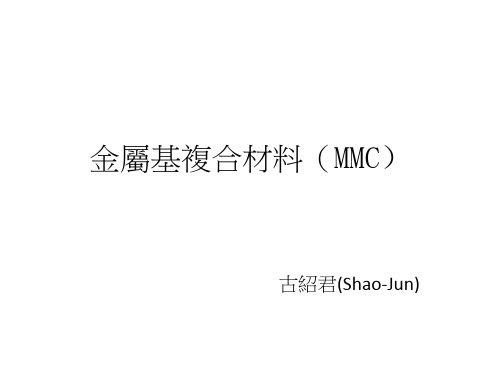
2. 液相複合法
– 該方法(特別是攪拌複合鑄造法)可以規模生產, 顆粒 金屬熔體 成本相對較低,但顆粒體積分數一般不超過 25%,成形過程與製品品質較難控制。
機械攪拌 3. 熔體噴霧與顆粒共噴射沉澱 擠壓鑄造法 壓力滲透法 混和澆鑄
– 壓力作用下通過噴嘴送入霧化器,在高速惰性 氣體射流的作用下,液態金屬被分散為細小的 液滴,形成“霧化錐”;同時通過一個或多個 胚料 複合材料錠材 噴嘴向“霧化錐”噴射入增強顆粒,使之與金 屬霧化液滴一齊在一基板(收集器)上沉積並 超塑 轧製 快速凝固形成顆粒增強金屬基複合材料。 擠出 鍛造 旋壓 機械加工
2. 藉外力強制克服結合不良之情形
1. 攪拌渦旋強迫顆粒納入鋁湯中 2. 採以加壓型式的鑄造方式成型
飛灰顆粒-鋁基(反應)
R. Q. Guo, P. K. Rohatgi, 1998, “Chemical Reactions between Aluminum and Fly Ash during Synthesis and Reheating of Al–Fly Ash Composite”, Metallurgical and Materials Transactions B, Vol. 29B, pp. 519-525.
鍵提供結合力。
• 物理結合
– 由兩相間原子中電子的交互作用的行為,即以凡得瓦力來結合。
• 擴散結合
– 某些複合體系的基體與增強體雖無界面反應,但可藉由原子間會 相互擴散作用。
• 機械結合
– 主要依靠補強材料粗糙表面的機械「錨固」力和基材的收縮力, 來抱緊補強材料產生摩擦力而結合。
一般情況,皆以化學結合為主,或者以兩種或兩種以上界面結合方式並存之的情況。
4. 靜電作用理論
金属基复合材料
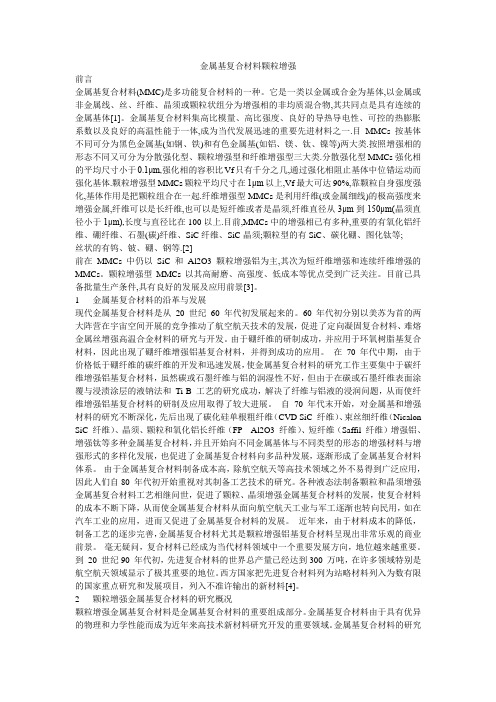
金属基复合材料颗粒增强前言金属基复合材料(MMC)是多功能复合材料的一种。
它是一类以金属或合金为基体,以金属或非金属线、丝、纤维、晶须或颗粒状组分为增强相的非均质混合物,其共同点是具有连续的金属基体[1]。
金属基复合材料集高比模量、高比强度、良好的导热导电性、可控的热膨胀系数以及良好的高温性能于一体,成为当代发展迅速的重要先进材料之一.目MMCs按基体不同可分为黑色金属基(如钢、铁)和有色金属基(如铝、镁、钛、镍等)两大类.按照增强相的形态不同又可分为分散强化型、颗粒增强型和纤维增强型三大类.分散强化型MMCs强化相的平均尺寸小于0.1μm,强化相的容积比Vf只有千分之几,通过强化相阻止基体中位错运动而强化基体.颗粒增强型MMCs颗粒平均尺寸在1μm以上,Vf最大可达90%,靠颗粒自身强度强化,基体作用是把颗粒组合在一起.纤维增强型MMCs是利用纤维(或金属细线)的极高强度来增强金属,纤维可以是长纤维,也可以是短纤维或者是晶须,纤维直径从3μm到150μm(晶须直径小于1μm),长度与直径比在100以上.目前,MMCs中的增强相已有多种,重要的有氧化铝纤维、硼纤维、石墨(碳)纤维、SiC纤维、SiC晶须;颗粒型的有SiC、碳化硼、图化钛等;丝状的有钨、铍、硼、钢等.[2]前在MMCs中仍以SiC和Al2O3颗粒增强铝为主,其次为短纤维增强和连续纤维增强的MMCs。
颗粒增强型MMCs以其高耐磨、高强度、低成本等优点受到广泛关注。
目前已具备批量生产条件,具有良好的发展及应用前景[3]。
1 金属基复合材料的沿革与发展现代金属基复合材料是从20 世纪60 年代初发展起来的。
60 年代初分别以美苏为首的两大阵营在宇宙空间开展的竞争推动了航空航天技术的发展,促进了定向凝固复合材料、难熔金属丝增强高温合金材料的研究与开发。
由于硼纤维的研制成功,并应用于环氧树脂基复合材料,因此出现了硼纤维增强铝基复合材料,并得到成功的应用。
金属基复合材料(MMC)制备工艺

contents
目录
• 引言 • 金属基复合材料的制备方法 • 金属基复合材料的制备工艺流程 • 金属基复合材料的应用与发展前景
01 引言
金属基复合材料的定义与重要性
金属基复合材料是由两种或两种以上材料组成的新型材料,其中一种材料为金属 ,其他材料为增强体(如陶瓷、玻璃、碳纤维等)。这种材料具有优异的力学性 能、物理性能和化学性能,广泛应用于航空航天、汽车、能源、电子等领域。
电子工业
用于制造电子产品的外壳、散 热器、连接器等,以提高导热 、导电和绝缘性能。
医疗器械
用于制造医疗器械,如牙科植 入物、手术刀等,以提高生物
相容性和耐腐蚀性能。
金属基复合材料的发展趋势与挑战
发展趋势
随着科技的进步,金属基复合材料的 应用领域不断扩大,新型的制备技术 和复合材料不断涌现,如纳米增强复 合材料、自修复复合材料等。
制备工艺中的问题与解决方案
界面反应控制
在制备过程中,金属基体与增强相之间可能发生界面反应, 影响材料性能。通过选择合适的金属基体和增强相、控制 制备工艺参数等措施来控制界面反应。
增强相分散
为了获得均匀的复合材料,需要确保增强相在基体中均匀 分散。采用适当的分散剂和搅拌方式,提高增强相的分散 效果。
挑战
金属基复合材料的制备成本较高,性 能稳定性有待提高,同时环保法规对 材料生产和废弃处理提出了更高的要 求。
金属基复合材料的前景展望
THANKS FOR WATCHING
感谢您的观看
激光熔覆法
利用激光束将增强体与金属基体 熔化混合,快速冷却固化后形成 复合材料。
03 金属基复合材料的制备工 艺流程
原材料的选择与处理
金属基复合材料

4、应用
➢ MMCs在陆上运输领域的应用
MMCs进入汽车行业的动力是它耐磨性和耐热性高、重 量轻的优点,因此MMCs主要用于需要减轻重量的刹车系统 和发动机系统。
碳化硅和氧化铝加强MMCs 制造的刹车转子重量仅为一 般材料的33 %~60 %,同时, 这种刹车转子具有卓越的耐 磨性,其使用期限甚至可以 与车本身的寿命一样长。
AlSiC微处理器盖板(a), AlSiC光电封装基座(b)
4、应用
➢ MMCs在航空航天领域的应用
MMCs最初发展的原动力来自于航空工业领域。
目前已用于军机和民机的MMCs主要是铝基和钛基复合 材料。NASA和DOD均在投资开发钛基复合材料(TMC)喷气涡 轮发动机。
MMCs 也用在航天飞机和火箭上。NASA采用硼连续纤 维增强的MMCs制成管材, 用作航天飞机的结构桁条, 性能 十分优越。
MMC的发展和应用
目录
MMC概述 MMC的性能特点
MMC的发展
MMC的应用
1、概述
1、金属基复合材料
金属基复合材料(Metal Matrix Composite,简称 MMC)是以金属及其合金为基体,与一种或几种金属或非 金属增强相人工结合而成的复合材料。
其增强体大多为 无机非金属,如 陶瓷、炭、石墨 及硼,也可以用 金属丝。
➢ 涡轮发动机的各个部件对于高温高效性材料的不断需求, 触发了对金属基复合材科特别是钛基材料的广泛兴趣的复 苏。
➢ 近年,功能和纳米金属基复合材料成为研究热点。
4、应用
据预测, 2013年以前全球MMCs市场将保持5.9%的 年增长率。根据应用领域不同, MMCs市场可细分为陆上 运输、电子/热控、航空航天、工业、消费产品等5个部 分。其中, 陆上运输(包括汽车和轨道车辆)和高附加值 散热组件仍然是MMCs的主市场, 用量占比分别超过60% 和30%。
金属基复合材料
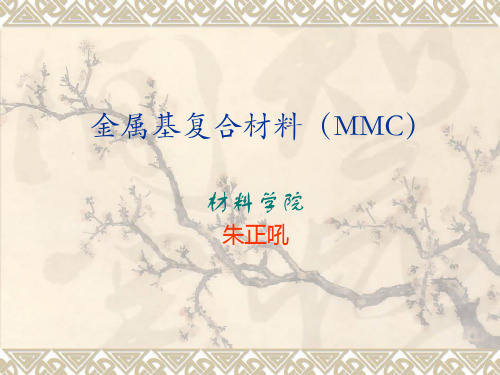
2)界面的形成及机制,界面产物的控制及界面设计; 3)增强剂在基体中的均匀分布: 在选择制备方法时,应选择那些使得增强剂更均匀、均质排 布(分布)的方法。在这方面,液态法与固态法相比较差。 4)制备工艺方法及参数的选择和优化; 5)制备成本的控制和降低,工业化应用的前景。
图9-11 粉末(冶金)法制备金属 基复合材料示意图
3 - 6 固态法制备工艺方法及参数的选择和优化固态法工艺的 主要参数:
1) 温度、时间: D = D0 exp (- Q / RT) D:扩散系数;Q: 扩散激活能。
X = k t 1/2 X:反应层厚度; k:反应速度常数。 2) 压力:促进结合 面的接触及在一定 温度下的金属基体 的塑性流动。 3) 结合面的清洁度:
合材料时,主要是基体
与基体之间的扩散结合,
有利于材料界面的改善;
同时通过控制基体沉积
层的厚度可控制纤维的 体积比。
图 9-4 PVD法纤维表面金属基体沉积层
2 - 4 粉末法纤维/基体复合丝
首先将金属基体粉末与聚合物 粘接剂混合制成基体粉末/聚合 物粘接剂胶体,然后将纤维通 过带有一定孔径毛细管的胶槽, 在纤维表面均匀地涂敷上一层 基体粉末胶体,干燥后形成一 定直径的纤维/基体粉末复合丝。 复合丝的直径取决于胶体的粘 度、纤维走丝速度以及胶槽的 毛细管孔径等。
业化生产。铝基复合材料单坯可达250公斤。
4 - 4 无压浸渗法(Lanxide法)
金属基复合材料(MMC)
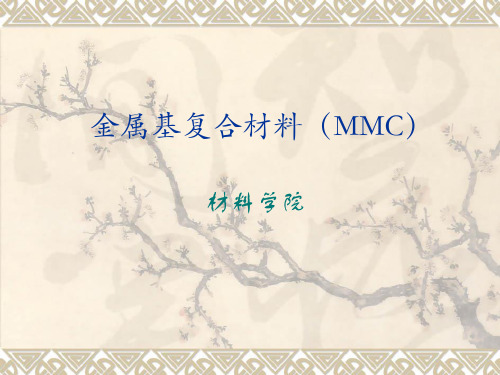
图 9-4 PVD法纤维表面金属基体沉积层
2 - 4 粉末法纤维/基体复合丝
图9-5 粉末法纤维/基体复合丝示意图
2 - 6 熔池法纤维 / 基体复合丝
图 9-6 熔池法纤维 / 基体复合丝示意图
这种复合丝制备方法主要是应用于碳纤维或石墨纤维增强铝基复合材料。 由于碳纤维或石墨纤维与铝液接触会反应生成Al4C3界面生成物。过量的脆性相Al4C3生成会严重影响复合材料的性能。 如图9-6所示,对纤维进行Ti-B或(液态)金属钠表面涂层处理可以增加纤维与铝液的润湿性,防止过量的脆性相Al4C3生成。
图 9-9 模压成型制备金属基复合材料示意图 模压成型也是扩散结合的一种手段。将纤维/基体预制体放置在具有一定形状的模具中进行扩散结合,最终得到一定形状的最终制品。常用这种工艺制备各种型材(图9-9)。
3-4 超塑性成型/ 扩散结合 (SPF / DB)
超塑性:材料在低负载作用下,拉伸变形时不发生缩颈,也不发生断裂,延伸率可达 100% 到 2000% 的现象。塑性流变和应变速度的关系如下: = K (e ) m 式中 :流变应力;e:应变速度;K:常数;m:应变速度敏感指数,衡量超塑性的重要参数。 影响超塑性的因素: 1) 形变速度:10 -4 ~10 -1 /分 2) 温度:> 0. 5T m ,达到相变临界点以下的某一温度可得到最大的m值和延伸率。 3) 晶粒度: 稳定、等轴、复相直径为0.5 5 m的细晶粒。
金属基复合材料MMC课件

高性能结构件
金属基复合材料具有高强度、高刚性和轻量化的特点,适用于制 造航空航天领域的高性能结构件。
耐高温性能
金属基复合材料能够承受高温环境,适用于制造飞机和火箭的燃烧 室和喷嘴等部件。
减振降噪性能
金属基复合材料的减振降噪性能较好,可用于制造飞机和火箭的起 落架和机身等部件。
电子封装材料的应用
散热性能
新材料与新技术的研发
1 2 3
高性能增强相的研发 利用新材料如碳纳米管、陶瓷纳米颗粒等,提高 金属基复合材料的力学性能和热稳定性。
金属基复合材料的制备技术 研究新的制备方法,如原位合成、喷射沉积、激 光熔覆等,以实现高效、低成本的生产。
多功能金属基复合材料 开发具有导电、导热、磁性等功能的新型金属基 复合材料,满足不同领域的应用需求。
分类
根据增强体的不同,金属基复合材料可分为连续增强金属基复合材料和非连续 增强金属基复合材料。
金属基复合材料的特性
高比强度和比模量
可设计性强
金属基复合材料具有较高的比强度和 比模量,能够满足轻量化设计的需求。
通过选择不同的增强体和金属基体, 可以定制金属基复合材料的性能,满 足各种应用需求。
良好的热稳定性和耐磨性
车、高尔夫球杆等。
医疗器械
用于制造医疗器械,如 手术刀、牙科工具等, 提高医疗器械的耐用性
和可靠性。
02
金属基复合材料的制备方法
粉末冶金法
粉末冶金法是一种常用的制备金属基复合材料的方法,通过将增强体(如碳纤维、陶瓷颗粒 等)与金属粉末混合,经过压制、烧结和热等静压等工序,制备出具有优异性能的金属基复 合材料。
界面设计与优化
01
02
03
界面类型
金属基复合材料原位复合工艺
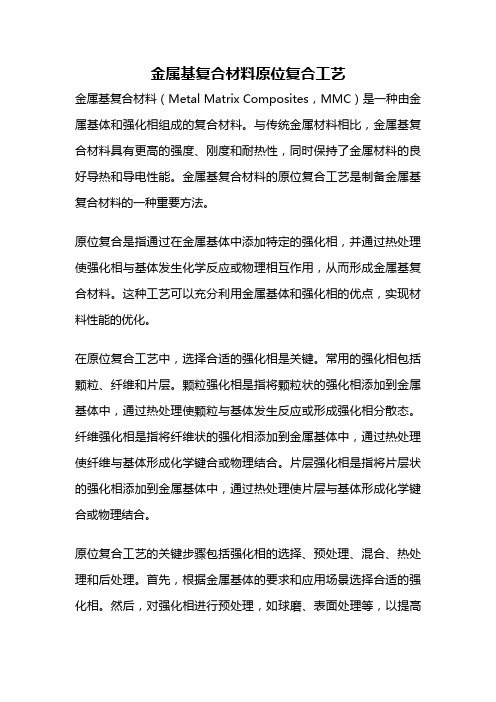
金属基复合材料原位复合工艺金属基复合材料(Metal Matrix Composites,MMC)是一种由金属基体和强化相组成的复合材料。
与传统金属材料相比,金属基复合材料具有更高的强度、刚度和耐热性,同时保持了金属材料的良好导热和导电性能。
金属基复合材料的原位复合工艺是制备金属基复合材料的一种重要方法。
原位复合是指通过在金属基体中添加特定的强化相,并通过热处理使强化相与基体发生化学反应或物理相互作用,从而形成金属基复合材料。
这种工艺可以充分利用金属基体和强化相的优点,实现材料性能的优化。
在原位复合工艺中,选择合适的强化相是关键。
常用的强化相包括颗粒、纤维和片层。
颗粒强化相是指将颗粒状的强化相添加到金属基体中,通过热处理使颗粒与基体发生反应或形成强化相分散态。
纤维强化相是指将纤维状的强化相添加到金属基体中,通过热处理使纤维与基体形成化学键合或物理结合。
片层强化相是指将片层状的强化相添加到金属基体中,通过热处理使片层与基体形成化学键合或物理结合。
原位复合工艺的关键步骤包括强化相的选择、预处理、混合、热处理和后处理。
首先,根据金属基体的要求和应用场景选择合适的强化相。
然后,对强化相进行预处理,如球磨、表面处理等,以提高其与金属基体的相容性。
接下来,将预处理后的强化相与金属基体进行混合,并形成均匀分散的体系。
混合过程中可采用机械混合、溶液共沉淀等方法。
混合后的体系经过热处理,使强化相与金属基体发生反应或结合。
最后,对原位复合材料进行后处理,如热处理、机械加工等,以获得所需的性能和形态。
金属基复合材料的原位复合工艺具有以下优点:首先,可以在金属基体中实现强化相的均匀分散,避免了强化相的聚集和团聚现象。
其次,原位复合工艺可以改善金属基体的力学性能,提高材料的强度、刚度和耐热性。
同时,金属基复合材料还保持了金属材料的导热和导电性能,具有良好的综合性能。
此外,原位复合工艺还可以实现对金属基体材料的改性,满足特定应用的需求。
金属基复合材料简介
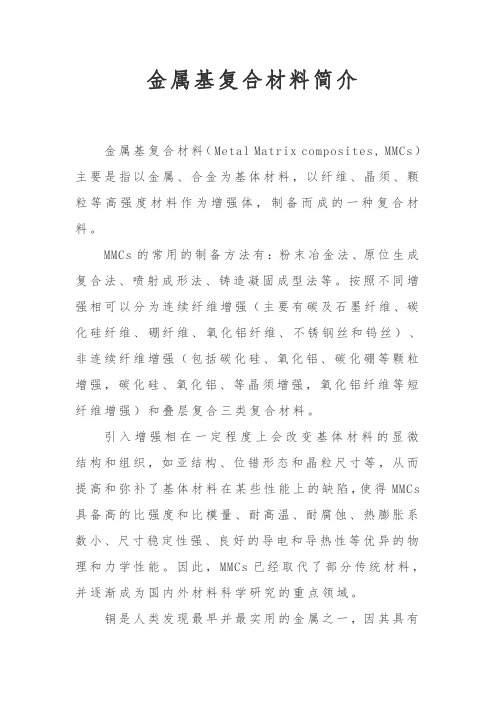
金属基复合材料简介金属基复合材料(Metal Matrix composites,MMCs)主要是指以金属、合金为基体材料,以纤维、晶须、颗粒等高强度材料作为增强体,制备而成的一种复合材料。
MMCs的常用的制备方法有:粉末冶金法、原位生成复合法、喷射成形法、铸造凝固成型法等。
按照不同增强相可以分为连续纤维增强(主要有碳及石墨纤维、碳化硅纤维、硼纤维、氧化铝纤维、不锈钢丝和钨丝)、非连续纤维增强(包括碳化硅、氧化铝、碳化硼等颗粒增强,碳化硅、氧化铝、等晶须增强,氧化铝纤维等短纤维增强)和叠层复合三类复合材料。
引入增强相在一定程度上会改变基体材料的显微结构和组织,如亚结构、位错形态和晶粒尺寸等,从而提高和弥补了基体材料在某些性能上的缺陷,使得MMCs 具备高的比强度和比模量、耐高温、耐腐蚀、热膨胀系数小、尺寸稳定性强、良好的导电和导热性等优异的物理和力学性能。
因此,MMCs已经取代了部分传统材料,并逐渐成为国内外材料科学研究的重点领域。
铜是人类发现最早并最实用的金属之一,因其具有优良的延展性,仅次于银的电导率,仅次于金银的热导率,一直以来备受重视。
但是,铜的力学性能(耐磨性、硬度、强度、抗蠕变性等)较差,限制了铜在工业和军事等领域的应用。
在众多MMCs中,铜基复合材料以其优异的导电、导热性能、耐腐蚀性以及良好的加工性而被广泛关注。
从二十世纪六十年代开始,铜基复合材料的相关研究逐渐开展,许多科学家在铜基体中加入了不同的增强体,发现该复合材料既保持了铜的优点,又弥补了铜力学性能上的不足。
时至今日,铜基复合材料的研究已经持续了几十年,形成了以颗粒增强铜基复合材料、纤维增强铜基复合材料、晶须增强铜基复合材料三大类别。
1、颗粒增强铜基复合材料颗粒增强铜基复合材料目的是将性能优异的颗粒均匀分散于铜基体,提高铜基复合材料的综合性能。
颗粒增强相产生的钉扎作用能够极大的阻碍位错的运动从而增强复合材料的强度,使铜基复合材料的力学性能、耐磨以及高温性能大幅提高。
第五章 金属基复合材料(MMC)

MMC制备工艺(续)
• 粉末冶金(Powder Metallurgy)
• 既可适用于连续、长纤维增强.又可用于短纤维、颗 粒或晶须增强的金属基复合材料。
MMC制备工艺
• MCC制备工艺的重要性
其不但对金属基复合材料的性能有很大的影响,而且 由于制造工艺复杂,是导致金属基复合材料成本居高 不下的重要原因,影响着金属基复合材料的广泛使用, 因此制备工艺一直是金属基复合材料的重要研究内容 之一。
• 目前常用的MCC的制备工艺方法
制备金属基复合材料的方法是多样化的。为了便于介 绍金属基复合材料的制备工艺,根据各种制备方法的 基本特点,主要把金属基复合材料的制备工艺分为三 大类,即(1)固态法;(2)液态法;(3)喷射与喷射沉积 法及原位复合法等新技术。
• 除上述外,还有铜基、锌基和金属间化合物基复合材料等。
各类MMC简介(续)
• 各种不同增强体增强的MCC
• 颗粒增强MCC
• 指增强体为颗粒形态的金属基复合材料,一般它是指 弥散的硬质增强相的体积超过20%的复合材料,而不 包括那种弥散质点体积比很低的弥散强化金属。
• 硬质增强相造成的对基体的束缚作用能阻止基体屈服。 颗粒复合材料的强度通常取决于颗粒的直径、间距和 体积比,但基体性能也很重要。
MMC制备工艺(续)
MMC制备工艺(续)
• 三个关键步骤:
• (1)纤维的排布;(2)复合材料的叠合和真空封 装;(3)热压。
• 扩散结合工艺中的最关键步骤是热压为了保证 性能符合要求,热压过程中要控制好热压工艺 参数。热压工艺参数主要为:热压温度、压力 和时间。
- 1、下载文档前请自行甄别文档内容的完整性,平台不提供额外的编辑、内容补充、找答案等附加服务。
- 2、"仅部分预览"的文档,不可在线预览部分如存在完整性等问题,可反馈申请退款(可完整预览的文档不适用该条件!)。
- 3、如文档侵犯您的权益,请联系客服反馈,我们会尽快为您处理(人工客服工作时间:9:00-18:30)。
2.粉末冶金
适用于连续、长纤维 增强.也可用于短纤 维、颗粒或晶须增强 的金属基复合材料
长纤维增强:将纤维和 金属粉末按比例混合,密 封在容器中,然后进行热 等静压
整理ppt
18
其它增强相
整理ppt
19
粉末冶金的优点
工艺过程温度低,可以控制界面反应
增强材料(纤维、颗粒或晶须)与基体金属粉末 可以任何比例混合,纤维含量最高可达75%, 颗粒含量可达50%以上
高温性能优良。合金化后的耐热性显著提高,可以作为
高温结构材料使用,如航空发动机的压气机转子叶片等, 长期使用最高温度已达540℃
在大气和海水中有优异的耐蚀性.在硫酸、盐酸、硝酸 相氢氧化纳等介质中都很稳定
导电与导热性差.导热系数只有铜的1/l 7和铝的l/10, 比电阻为铜的25倍
整理ppt
7
对浸润性和密度差的要求较小
采用热等静压工艺时,其组织细化、细密、均 匀,一般不会产生偏析、偏聚等缺陷,可使空 隙和其它内部缺陷得到明显改善,从而提高复 合材料的性能
可以用传统的加工方法进行二次加工
整理ppt
20
粉末冶金的缺点
工艺过程比较复杂,金属基体必须制 成金属粉末,增加了工艺的复杂性和 成本
22
普通压铸工艺过程
将包含有增强材料的金属熔体倒入预热模 具中后迅速加压,压力约为70—l00MPa, 使液态金属基复合材料在压力下凝固。待 复合材料完全固化后顶出,即制得所需形 状及尺寸的金属基复合材料的坯料或压铸 件。
整理ppt
23
增强材料预制体的压铸工艺过程
将熔融金属注入装有增强材料(长、短纤维, 颗粒或晶须)的预制件模具中,并在压力下使 之渗入预制件的间隙,在高压下迅速凝固成金 属基复合材料
采用等离子喷涂。即先在金属基体箔片上用排 布好一层纤维,然后再喷涂一层与基体金属相 同的金属
纤维表面经化学或物理处理,在基体金属熔池 中充分地浸渍形成金属基复合丝
整理ppt
14
叠合与封装
为了防止复合材料在热压中的氧化,叠 合好的复合材料坯科应真空封装于金属 模套中。为了便于复合材料在热压后与 金属模套的分离,在金属模套的内壁徐 上云母粉类的涂料以利分离,注意不能 涂与金属基体发生反应的涂料。
整理ppt
26
整理ppt
27
3.熔渗
将增强材料制成多孔预制体,置基体金属熔 体的上方或内部,利用毛细力的使熔体作用渗 入预制中。也可将预制体和基体金属坯料装入 一可通入流动氮气的加热炉中。通过加热,基 体金属熔化,自发渗透入网络状增强材料预制 体中
整理ppt
28
三、喷涂与喷射沉积
喷涂沉积主要应用于纤维增强金属基复合材 料的须制层的制备,也可以获得复合层状复合 材料的坯料。喷射沉积则主要用于制备颗粒增 强金属基复合材料。喷射与喷涂沉积工艺的最 大特点是增强材料与基体金属的润湿性要求低; 增强材料与熔融金属基体的接触时间短,界面 反应量少。喷涂沉积制备纤维增强金属基复合 材料时,纤维的分布均匀,获得的薄单层纤维 增强预制层可以很容易地通过扩散结合工艺形 成复合材料结构形状和板材。喷涂与喷射沉积 工艺,可以与各种陶瓷纤维或颗粒复合,即基 体金属的选择范围广。艺
根据各种制备方法的基本特点,金 属基复合材料的制备工艺分为四大类, 即 (1)固态法; (2)液态法; (3)喷涂与喷射沉积法; (4)原位复合法。
整理ppt
11
一、固态法
1.扩散结合 在一定温度的压力下,把新鲜清洁
表面的相同或不相同的金届,通过表面 原子的互相扩散而连接在一起。
第五章 金属基复合材料(MMC)
整理ppt
1
第一节 概 述
一、MMC的沿革与发展
整理ppt
2
二、MMC的分类
1、按增强材料形态分类 纤维增强金属基复合材料 颗粒和晶须增强金属基复合材料 2、按金属基体分类 铝基复合材料 钛基复合材料 镁基复合材料 高温合金复合材料 金属间化合物复合材料
整理ppt
15
热压
在真空或保护气氛下直接放入热压模 或平板进行热压合热压工艺参数主要为: 热压温度、压力和时间
整理ppt
16
扩散结合的优缺点:
工艺相对复杂,纤维排布、叠合以及封 装手工操作多,成本高。
能按照复合材料的铺层要求排布。 在热压时可通过控制工艺参数的办法来
控制界面反应
整理ppt
17
整理ppt
3
第二节 金属基体
一、铝及铝合金
铝的基本特点:熔点660℃ ,密度 2.7g/cm3
具有面心立方结构.所以其塑性优异,适合各 种形式的冷、热加工
导电、导热性能好,约为铜的60%左右 化学活性高,在大气中铝表面与氧形成一层薄
而又致密的氧化铝膜,防止铝继续氧化
强度低
整理ppt
4
铝合金的分类
常用钛合金的性能
整理ppt
8
三、镁及镁合金
特点:密度1.74g/cm3
由于其密度低,比强度、比刚度较高, 镁具有密排六方结构,室温和低温塑性较低,
但高温塑性好可进行各类形式的热变形加工。 减震性能好,能承受较大的冲击振动负荷
整理ppt
9
四、金属间化合物
具有反常的温度 强度效应
脆性很大
铝合金的热处理:淬火和时效
整理ppt
5
铝合金的力学性能
整理ppt
6
二、钛及钛合金
钛的特点:熔点1678℃ ,密度4.51g/cm3
重量轻、比强度高。纯钛的强度可通过冷作硬化和合金
化而得到显著的提高.如50%的冷变形可使强度提高60 %,适当合金化和热处理,则抗拉强度可达1200— 1400MPa,含有氢、碳、氧、铁和镁等杂质元素的工业 纯钛抗拉强度可提高到700MPa,并仍能保持良好的塑 性和韧性。
在制备铝基复合材料时,还要防止铝 金属粉末引起的爆炸
整理ppt
21
二、液态法
1.压铸 压铸成型(Squeeze casting),是指在压
力的作用下,将液态或半液态金属基复 合材料或金属以一定速度充填压铸模型 腔或增强材料须制体的孔隙中,在压力 下快速凝固成型而制备金属基复合材料 的工艺方法。
整理ppt
整理ppt
24
压铸法的优点
其组织细化、无气孔,可以获得比一般 金属模铸件性能优良的压铸件。
工艺设备简单,成本低,材料的质量高 且稳定
易于工业化生产。
整理ppt
25
2.半固态复合铸造
将颗粒加入处于半固态的金属基体中, 通过搅拌使颗粒在金属基体中均匀分布, 并取得良好的界面结合,然后浇注成型 或将半固态复合材料注入摸具进行压铸 成型。
整理ppt
12
工艺流程
整理ppt
关键步骤 纤维的排布; 复合材料的
叠台和真空 封装; 热压
13
纤维排布
采用有机粘接剂。将增强纤维的单丝或多丝的 条带分别浸溃加热后易挥发的有机粘接剂,按 复合材料的设计要求的间距排列在全属基体的 薄板或箔上,形成预制件
采用带槽的薄板或箔片,将纤维排布在其中