复合涂层
关于波形护栏表面处理——环氧锌基聚酯复合涂层的介绍

关于波形护栏表⾯处理——环氧锌基聚酯复合涂层的介绍1材料环氧锌基聚酯复合涂层⽤第⼀层(底涂层)为环氧锌基粉末涂层,由环氧树脂和⽚状锌粉组成,应分别符召GD/T 1G30.1和GD/T 2603S的规定;笫⼆层(⾯涂层)为纯聚酯粉⽊涂层,由纯聚酯粉未涂料经静电喷涂⼯艺形成,其理化性能应符合JT/T 600.4的规定。
2构件⼯艺要求2.1钢板构件在防腐处理前的边、⾓应采⽤1 mmX45°倒⾓处理或i?l mm圆弧化处理。
2.2钢板构件表⾯应经过抛丸、喷丸或喷砂清理,除锈等级⾄少达到Sa2K级。
3厚度在GB/T 15957规定的⼤⽓腐蚀环境、等级条件下,构件的各层质量或厚度应符合表13的要求;在GB/T 15957规定的⼤⽓腐蚀环境ffl、F、V、Y 等级条件下,构件的各层质量或厚度应不低于表14的要求。
4环氧锌基涂层4.1外观质量涂层应均匀、光滑、连续,⽆⾁眼可分辨的缩孔、针眼、凹坑、裂缝、脱⽪等表⾯缺陷。
4.2 厚度应不低于表13或表14的规定。
4.3附着性按拉开法测试涂层附宥⼒,涂层与⾦属底材的结合拉⼒不^⼩于40 MPa,4.4抗弯曲性能经多3圆柱轴弯曲试验后,试样应⽆⾁眼可见的裂纹、剥离、脱落等现象。
4.5耐冲击性经过90 kg . on的冲击试验后,涂塑层应⽆碎裂、开裂、剥离、脱落等现象。
4.6耐盐雾腐蚀性能经1 500 h的中性盐雾试验后,涂层表⾯应⽆起泡、⽣锈、脱落、剥离等现象;划痕部位两侧英延距离不⼤于1mm。
4.7耐湿热性经1 000 h湿热试验后,涂层表⾯应⽆起泡、脱落、⽣锈、剝离等现象;划痕部位两侧荽延距离不⼤于 1 mm。
5环氣锌基聚酯复合涂层5.1 外观涂层应均勻光滑、连续,⽆⾁眼可分辨的缩孔、针眼、凹坑、裂缝、脱⽪等表⾯缺陷。
5.2 厚度应不低于表13或表14的规定。
5.3附着性按拉开法测试涂层附着⼒,涂层层间的结合拉⼒不⼩于40 MPa。
5.4湿附着性按拉开法测试涂层湿附着⼒,涂层层间的结合拉⼒不⼩于12 MPa。
涂层和复合的区别【一文搞懂】
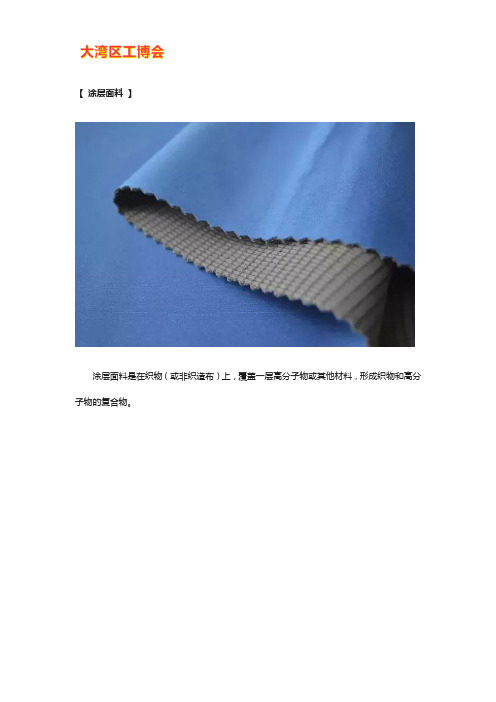
【涂层面料】涂层面料是在织物(或非织造布)上,覆盖一层高分子物或其他材料,形成织物和高分子物的复合物。
涂层面料利用溶剂或水将所需要的涂层胶粒(有PU胶,A/C胶,PVC,PE胶)等溶解成流涎状,再以一种某种方式(圆网,刮刀或者滚筒)均匀的涂在布料上(有棉,涤纶,锦纶等基材),然后再经过烘箱内温度的固着,使在面料表面形成一层均匀的覆盖胶料。
【复合面料】复合面料可以理解为,不同成分、不同组织或不同染整工艺两种(或多种)面料通过特殊的工艺组织在一起的新的面料。
复合面料应用了“新合纤”的高技术和新材料,具备很多优异的性能(与普通合纤相比),如织物表现细洁、精致、文雅、温馨,织物外观丰满、防风、透气,具备一定的防水功能。
它的主要特点是保暖、透气性好。
该织物还有一个特点是:耐磨性好,超细纤维织物手感柔软、透气、透湿,所以在触感和生理的舒适性方面,具有明显优势,超细纤维织物的抗皱性较差(这是因为纤维柔软,折皱后弹性回复差所致);为了克服这一缺点,故采取了“复合”工艺,这样就大大地改善了超细纤维织物抗皱性差的缺点。
复合面料是欧美流行外套面料。
扩展资料:涂层面料主要产品:当前涂层整理的种类大致如下PA涂层又叫AC胶涂层,即丙烯酸涂层,是最普通最常见的一种涂层,涂后可增加手感,防风,有垂感。
PU涂层即聚氨酯涂层,涂后织物手感丰满,有弹性,表面有膜感。
防绒涂层即指防羽绒涂层,涂后能防止羽绒跑绒,适合做羽绒服面料。
但现在涂层中凡有水压要求的PA涂层也叫防绒涂层。
PA白胶涂层即在织物表面涂一层白色的丙烯酸树脂,能增加布面的遮盖率,不透色,并使布面颜色更鲜艳。
PU白胶涂层即在织物表面涂一层白色聚氨酯树脂,作用基本同PA白胶,但是PU白胶涂后手感更丰满,织物更有弹性,牢度更好。
PA银胶涂层即在织物表面涂一层银白色胶,使织物具有遮光,防辐射的功能,一般多用于窗帘、帐篷、服装。
PU银胶涂层基本功能同PA银胶涂层。
但PU涂银织物具有更好的弹性、更好的牢度,对于帐篷等要求高水压的面料,PU涂银相对PA涂银更好。
复合涂层材料

复合涂层材料复合涂层材料是一种由多种不同材料组合而成的涂层,具有多种优异性能和广泛的应用领域。
复合涂层材料通常由底漆、中间涂层和面漆组成,每一层都具有特定的功能和作用,共同构成了高性能的涂层系统。
在工业、建筑、航空航天等领域中,复合涂层材料发挥着重要的作用,为材料提供了保护、美化和功能增强等多种功能。
首先,复合涂层材料具有优异的防腐蚀性能。
由于复合涂层材料通常由多种材料组合而成,其在防腐蚀性能上具有独特的优势。
底漆层通常具有优异的附着力和防腐蚀性能,能够有效地防止金属材料的腐蚀。
中间涂层则能够提供额外的保护和增强功能,例如耐磨、耐化学腐蚀等性能。
面漆层则能够提供美观的外观和额外的保护。
这些性能使得复合涂层材料成为各种金属制品的理想选择,例如汽车零部件、建筑结构、船舶和航空器等。
其次,复合涂层材料具有优异的耐候性能。
在室外环境中,材料往往要经受日晒、雨淋、风吹等自然环境的侵蚀,因此需要具有良好的耐候性能。
复合涂层材料通过不同层次的组合,能够有效地提高材料的耐候性能。
底漆层通常具有优异的抗紫外线和氧化性能,中间涂层能够提供额外的保护和增强功能,面漆层则能够提供额外的防护和美观。
这些性能使得复合涂层材料成为室外金属制品的首选,例如户外家具、广告牌、桥梁和建筑外墙等。
此外,复合涂层材料还具有优异的功能增强性能。
通过不同材料的组合和设计,复合涂层材料能够为材料提供额外的功能增强,例如耐磨、耐化学腐蚀、防火等功能。
这些功能增强性能使得复合涂层材料在特定领域具有重要的应用,例如航空航天领域的航空器外壳、汽车领域的车身涂装等。
综上所述,复合涂层材料具有优异的防腐蚀性能、耐候性能和功能增强性能,广泛应用于工业、建筑、航空航天等领域。
随着材料科学和涂料技术的不断发展,复合涂层材料将会在更多领域展现出其独特的优势和潜力。
锌铬酸盐复合涂层介绍
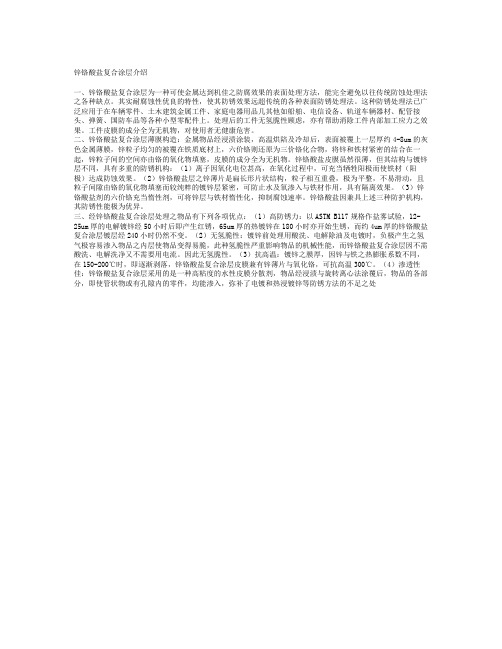
锌铬酸盐复合涂层介绍一、锌铬酸盐复合涂层为一种可使金属达到机佳之防腐效果的表面处理方法,能完全避免以往传统防蚀处理法之各种缺点。
其实耐腐蚀性优良的特性,使其防锈效果远超传统的各种表面防锈处理法。
这种防锈处理法已广泛应用于在车辆零件、土木建筑金属工件、家庭电器用品几其他如船舶、电信设备、轨道车辆器材、配管接头、弹簧、国防车品等各种小型零配件上。
处理后的工件无氢脆性顾虑,亦有帮助消除工件内部加工应力之效果。
工件皮膜的成分全为无机物,对使用者无健康危害。
二、锌铬酸盐复合涂层薄膜构造:金属物品经浸渍涂装,高温烘陪及冷却后,表面被覆上一层厚约4-8um的灰色金属薄膜,锌粒子均匀的被覆在铁质底材上,六价铬则还原为三价铬化合物,将锌和铁材紧密的结合在一起,锌粒子间的空间亦由铬的氧化物填塞,皮膜的成分全为无机物。
锌铬酸盐皮膜虽然很薄,但其结构与镀锌层不同,具有多重的防锈机构:(1)离子因氧化电位甚高,在氧化过程中,可充当牺牲阳极而使铁材(阳极)达成防蚀效果。
(2)锌铬酸盐层之锌薄片是扁长形片状结构,粒子相互重叠,极为平整,不易滑动,且粒子间隙由铬的氧化物填塞而较纯粹的镀锌层紧密,可防止水及氧渗入与铁材作用,具有隔离效果。
(3)锌铬酸盐剂的六价铬充当惰性剂,可将锌层与铁材惰性化,抑制腐蚀速率。
锌铬酸盐因兼具上述三种防护机构,其防锈性能极为优异。
三、经锌铬酸盐复合涂层处理之物品有下列各项优点:(1)高防锈力:以ASTM B117规格作盐雾试验,12-25um厚的电解镀锌经50小时后即产生红锈,65um厚的热镀锌在180小时亦开始生锈,而约4um厚的锌铬酸盐复合涂层镀层经240小时仍然不变。
(2)无氢脆性:镀锌前处理用酸洗、电解除油及电镀时,负极产生之氢气极容易渗入物品之内层使物品变得易脆,此种氢脆性严重影响物品的机械性能,而锌铬酸盐复合涂层因不需酸洗、电解洗净又不需要用电流。
因此无氢脆性。
(3)抗高温:镀锌之膜厚,因锌与铁之热膨胀系数不同,在150-200℃时,即逐渐剥落,锌铬酸盐复合涂层皮膜兼有锌薄片与氧化铬,可抗高温300℃。
金属材料的表面涂层工艺研究
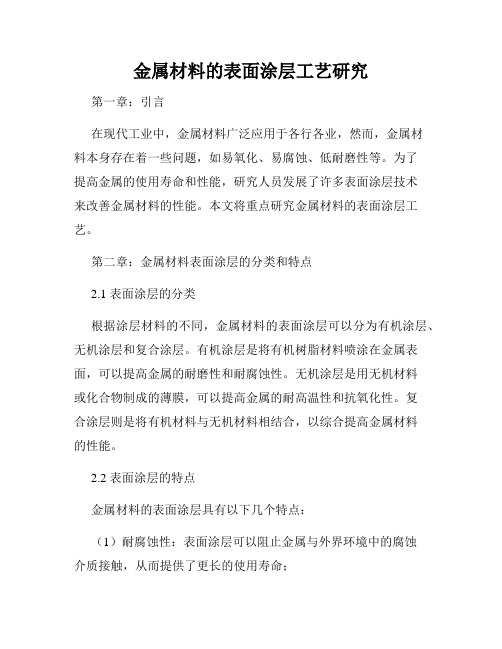
金属材料的表面涂层工艺研究第一章:引言在现代工业中,金属材料广泛应用于各行各业,然而,金属材料本身存在着一些问题,如易氧化、易腐蚀、低耐磨性等。
为了提高金属的使用寿命和性能,研究人员发展了许多表面涂层技术来改善金属材料的性能。
本文将重点研究金属材料的表面涂层工艺。
第二章:金属材料表面涂层的分类和特点2.1 表面涂层的分类根据涂层材料的不同,金属材料的表面涂层可以分为有机涂层、无机涂层和复合涂层。
有机涂层是将有机树脂材料喷涂在金属表面,可以提高金属的耐磨性和耐腐蚀性。
无机涂层是用无机材料或化合物制成的薄膜,可以提高金属的耐高温性和抗氧化性。
复合涂层则是将有机材料与无机材料相结合,以综合提高金属材料的性能。
2.2 表面涂层的特点金属材料的表面涂层具有以下几个特点:(1)耐腐蚀性:表面涂层可以阻止金属与外界环境中的腐蚀介质接触,从而提供了更长的使用寿命;(2)改善机械性能:表面涂层可以增加金属材料的硬度、耐磨性和抗刮擦性;(3)改善热性能:表面涂层可以提高金属的耐高温性和导热性能;(4)美观效果:表面涂层可以改变金属材料的外观,使之更美观。
第三章:常见的金属材料表面涂层工艺3.1 电镀电镀是一种通过电解的方式将金属离子沉积在金属表面的工艺。
它具有成本低、效果好、镀层均匀等优点,可以提高金属的耐腐蚀性和耐磨性。
常见的电镀方法包括镀铬、镀镍、镀锌等。
3.2 喷涂喷涂是将有机涂料均匀喷涂在金属表面的工艺。
喷涂具有简单、成本低、施工方便等特点,可以提高金属的耐腐蚀性、耐热性和耐磨性。
常见的喷涂材料包括聚氨酯漆、聚酯漆等。
3.3 真空镀膜真空镀膜是一种在真空环境下将金属蒸汽沉积在金属表面的工艺。
它能够制备出均匀、致密的薄膜,可以提高金属的耐氧化性和耐高温性。
常见的真空镀膜方法包括物理气相沉积(PVD)和化学气相沉积(CVD)等。
第四章:金属材料表面涂层工艺的发展趋势4.1 高效、环保随着环境保护意识的提高,金属材料表面涂层工艺越来越注重减少对环境的污染。
热浸镀锌聚酯复合涂层工艺

热浸镀锌聚酯复合涂层工艺热浸镀锌聚酯复合涂层工艺是一种常用的表面处理技术,主要用于金属制品的防腐蚀和美化。
本文将介绍该工艺的基本原理、工艺流程以及应用范围。
一、基本原理热浸镀锌聚酯复合涂层工艺的基本原理是通过将金属制品浸入含锌的熔融液中,在金属表面形成一层锌层。
同时,在锌层上再涂覆一层聚酯涂料,形成一种具有双重保护作用的复合涂层。
锌层可以提供良好的防腐蚀性能,而聚酯涂层则可以提供优异的耐候性和美观效果。
二、工艺流程热浸镀锌聚酯复合涂层工艺的主要工艺流程包括准备工作、表面处理、热浸镀锌、涂覆聚酯涂料、固化和检验等步骤。
1. 准备工作:包括设备和原材料的准备,确保工艺的顺利进行。
2. 表面处理:金属制品在进行热浸镀锌前需要进行表面处理,通常包括除油、除锈和酸洗等步骤,以确保金属表面的洁净度和粗糙度符合要求。
3. 热浸镀锌:将经过表面处理的金属制品浸入熔融的锌液中,使锌与金属的表面发生化学反应,形成一层均匀的锌层。
热浸镀锌工艺中,温度和时间是影响镀层质量的重要因素。
4. 涂覆聚酯涂料:在形成锌层后,将聚酯涂料涂覆在锌层上,然后进行固化处理。
聚酯涂料可以根据需要选择不同的颜色和光泽度,以达到美观的效果。
5. 固化:将涂覆了聚酯涂料的金属制品进行固化处理,使涂层能够充分附着在金属表面,并提供良好的耐候性。
6. 检验:对热浸镀锌聚酯复合涂层进行质量检验,包括涂层的厚度、附着力、耐腐蚀性等指标的测试。
三、应用范围热浸镀锌聚酯复合涂层工艺广泛应用于建筑、汽车、家电等行业。
在建筑行业中,常用于屋面、墙面、钢结构等金属制品的防腐蚀和装饰;在汽车行业中,常用于车身及零部件的防腐蚀和外观美化;在家电行业中,常用于冰箱、洗衣机等产品的外壳防腐蚀和颜色涂装。
总结:热浸镀锌聚酯复合涂层工艺是一种常用的表面处理技术,通过在金属制品表面形成锌层和聚酯涂层,实现了双重保护效果。
该工艺具有良好的防腐蚀性能和耐候性,广泛应用于建筑、汽车、家电等行业中的金属制品。
2023年功能性涂层复合材料行业市场调研报告

2023年功能性涂层复合材料行业市场调研报告近年来,随着人们对复合材料行业的重视,功能性涂层复合材料市场也在不断地发展壮大。
在市场竞争日趋激烈的背景下,制定科学的市场营销策略可以使企业在市场中占据更有优势的地位。
本文对功能性涂层复合材料行业市场进行了调研分析,旨在了解市场现状和趋势,为企业决策提供参考。
一、市场概况功能性涂层复合材料是由涂层和基材组成的复合材料,以增强材料性能为主要目的。
它具有优良的防腐、抗氧化、耐磨、耐高温等性能,广泛应用于航空航天、汽车、电子、建筑等领域。
目前,全球功能性涂层复合材料行业市场规模已经达到了1000亿美元,年复合增长率为5%左右。
随着科技的不断进步和产业的升级,功能性涂层复合材料的市场前景十分广阔。
二、市场分析1. 行业竞争格局功能性涂层复合材料市场具有较高的市场集中度,市场前几位的企业占据了市场的大部分份额。
全球领先的企业包括PPG、AkzoNobel、Axalta、Valspar等,它们拥有多年的技术积累和完善的营销网络,具有较高的市场竞争力。
2. 市场需求趋势功能性涂层复合材料的应用范围不断扩大,应用领域的需求也在不断地增加。
其中,建筑和汽车产业的需求量最大。
随着人们对建筑环保和汽车轻量化的关注程度提高,涂层复合材料的需求也将不断增长。
3. 市场驱动因素随着人民生活水平的提高和全球经济的发展,人们对产品的性能和体验的要求越来越高。
这加速了各行业对功能性涂层复合材料的需求。
同时,全球气候变暖和环境污染,给各行业的产品带来了更高的环保要求,这也推动了功能性涂层复合材料的市场需求。
三、市场发展趋势1. 市场规模持续扩大全球功能性涂层复合材料市场规模将在未来10年内继续扩大,年复合增长率将超过5%。
这一增长主要受到建筑和汽车产业的需求增加、对环保和性能要求的提高以及新兴产业的逐渐崛起等多种因素的影响。
2. 技术革新引领市场发展涂层复合材料的研发和应用技术不断地更新,新技术的应用将更好地满足市场需求。
羟基磷灰石及其复合涂层的研究现状

羟基磷灰石及其复合涂层的研究现状段希夕 高钦钦(新余学院机电工程学院 江西新余 338004)摘要:钛及其合金金属有良好的机械性能,羟基磷灰石是有优异生物性能的活性陶瓷,因而羟基磷灰石/钛(HA/Ti)复合涂层结合二者优势性能被广泛应用于人体骨组织和牙齿的修复中,以提高材料的医用价值。
该文采用冷喷涂、等离子喷涂、磁控溅射、激光熔覆、溶胶-凝胶、电化学沉积等其他技术制备HA/Ti复合粒子,并适当掺入其他金属合金,完善性能,探究其实验后的涂层特征、表面形态对力学性能和生物性能的影响。
关键词:羟基磷灰石 钛 喷涂 复合涂层中图分类号:TG146文献标识码:A 文章编号:1672-3791(2023)17-0087-07 Research Status of Hydroxyapatite and Its Composite CoatingsDUAN Xixi GAO Qinqin(School of Electrical and Mechanical Engineering, Xinyu University, Xinyu, Jiangxi Province, 338004 China) Abstract: Titanium and its alloy metals have good mechanical properties. Hydroxyapatite is an active ceramic with excellent biological properties, so hydroxyapatite/titanium ( HA/Ti ) composite coatings are widely used in the re‐pair of human bone tissue and teeth in combination with the advantages of the two to improve the medical value of materials. HA/Ti composite particles are prepared by cold spraying, plasma spraying, magnetron sputtering, laser cladding, sol-gel, electrochemical deposition and other technologies, other metal alloys are added to improve prop‐erties, and the effects of their coating characteristics and surface morphology after the experiment on mechanical properties and biological properties are explored.Key Words: Hydroxyapatite; Titanium; Spraying; Composite coatings21世纪以来,需要人工骨治疗患者的数量在全球约有3 000万人次[1-2]。
WCp(Co+Cr)复合材料涂层的组织及耐磨性能
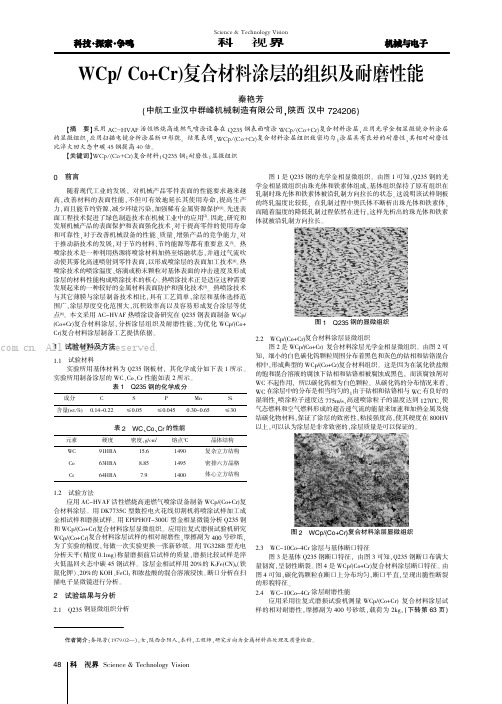
Science &Technology Vision科技视界0前言随着现代工业的发展,对机械产品零件表面的性能要求越来越高,改善材料的表面性能,不但可有效地延长其使用寿命,提高生产力,而且能节约资源,减少环境污染,加强稀有金属资源保护[1]。
先进表面工程技术促进了绿色制造技术在机械工业中的应用[2]。
因此,研究和发展机械产品的表面保护和表面强化技术,对于提高零件的使用寿命和可靠性,对于改善机械设备的性能、质量,增强产品的竞争能力,对于推动新技术的发展,对于节约材料、节约能源等都有重要意义[3]。
热喷涂技术是一种利用热源将喷涂材料加热至熔融状态,并通过气流吹动使其雾化高速喷射到零件表面,以形成喷涂层的表面加工技术[4]。
热喷涂技术的喷涂温度、熔滴或粉末颗粒对基体表面的冲击速度及形成涂层的材料性能构成喷涂技术的核心。
热喷涂技术正是适应这种需要发展起来的一种较好的金属材料表面防护和强化技术[5]。
热喷涂技术与其它薄膜与涂层制备技术相比,具有工艺简单,涂层和基体选择范围广,涂层厚度变化范围大,沉积效率高以及容易形成复合涂层等优点[6]。
本文采用AC-HVAF 热喷涂设备研究在Q235钢表面制备WCp/(Co+Cr)复合材料涂层,分析涂层组织及耐磨性能,为优化WCp/(Co+Cr)复合材料涂层制备工艺提供依据。
1试验材料及方法1.1试验材料实验所用基体材料为Q235钢板材,其化学成分如下表1所示。
实验所用制备涂层的WC、Co、Cr 性能如表2所示。
表1Q235钢的化学成分表2WC、Co、Cr 的性能1.2试验方法应用AC-HVAF 活性燃烧高速燃气喷涂设备制备WCp/(Co+Cr)复合材料涂层。
用DK7735C 型数控电火花线切割机将喷涂试样加工成金相试样和磨损试样。
用EPIPHOT-300U 型金相显微镜分析Q235钢和WCp/(Co+Cr)复合材料涂层显微组织。
应用往复式磨损试验机研究WCp/(Co+Cr)复合材料涂层试样的相对耐磨性,摩擦副为400号砂纸,为了实验的精度,每做一次实验更换一张新砂纸。
热喷涂WC复合耐磨涂层制备的开题报告

热喷涂WC复合耐磨涂层制备的开题报告一、研究背景及意义随着工业化的发展和经济的增长,耐磨材料的需求量不断增加。
传统的钢材、铸铁等金属材料虽然具有较高的强度和硬度,但在高温、高压和高速等复杂环境下容易磨损和腐蚀,影响其使用寿命和性能。
因此,研发新型的高强度、高韧性和具有较好的耐磨性能的材料是当前的一个热点和难点问题。
近年来,热喷涂技术被广泛应用于制备各种复合涂层,该技术具有简单、灵活、可控性与环保等优点。
其中,WC复合涂层是一种具有高硬度、高强度和良好耐磨性能的涂层材料。
其主要原料为碳化钨(WC)和金属粉末,通过热喷涂技术在基材表面制备而成。
此种复合涂层不仅能提高基材的硬度和强度,还能有效降低基材在磨损、腐蚀和疲劳等方面的破坏,提高其使用寿命和性能。
因此,WC复合耐磨涂层具有广阔的应用前景和市场价值。
二、研究内容和方法本文的研究目标是制备一种高质量的WC复合耐磨涂层,并研究其在不同工况下的性能表现。
具体的研究内容如下:1.研究WC复合涂层制备工艺。
对不同喷枪、喷嘴、气体和喷粉参数等因素进行优化,制备出具有一定厚度和较好结合效果的WC复合涂层。
2.研究WC复合涂层的微观结构和组成。
通过扫描电子显微镜(SEM)、能量散布谱(EDS)和X射线衍射(XRD)等分析手段,对涂层的微观结构和组成进行观察和分析。
3.研究WC复合涂层的力学性能和耐磨性能。
利用硬度测试机、万能试验机、摩擦磨损试验机等测试手段,对涂层的力学性能和耐磨性能进行测试和分析。
4.研究WC复合涂层在不同工况下的应用性能。
通过对涂层在高温、高压、高速等不同工况下的应用情况进行测试和分析,探究其在实际使用中的表现和问题。
三、预期成果和意义1.成功制备出一种高质量、高结合度的WC复合涂层,对其制备工艺进行了优化和改进。
2.通过对涂层的微观结构和组成进行分析,在深入了解其材料特性的同时,为其性能表现提供了科学的解释和分析。
3.在涂层力学性能和耐磨性能的测试中,得到了涂层的力学参数和耐磨性能指标,为其应用领域的扩展和优化提供了实验基础。
复合涂层材料

复合涂层材料
复合涂层材料是一种由多种不同材料组合而成的新型材料,具有优异的性能和
广泛的应用前景。
它由基材、粘结剂和功能性涂层三部分组成,通过特定的工艺方法将它们结合在一起,形成具有特定功能和性能的复合涂层材料。
复合涂层材料可以在不同的领域得到应用,如建筑、汽车、航空航天、电子等行业,其性能和功能也因应用领域的不同而有所差异。
首先,复合涂层材料具有优异的耐腐蚀性能。
由于其表面涂层通常采用防腐蚀
材料,能够有效地防止金属基材受到腐蚀和氧化的影响,从而延长了材料的使用寿命。
在海洋工程、化工设备等领域,复合涂层材料得到了广泛的应用,有效地提高了设备的耐腐蚀性能,降低了设备的维护成本。
其次,复合涂层材料还具有优异的耐磨性能。
在一些需要经常受到磨损的场合,如汽车发动机部件、工程机械零部件等,复合涂层材料能够有效地提高材料的耐磨性能,延长了零部件的使用寿命,减少了更换零部件的频率,降低了维护成本。
另外,复合涂层材料还具有优异的导热性能和绝缘性能。
在一些需要具有导热
性能和绝缘性能的场合,如电子器件、电力设备等,复合涂层材料能够满足这些特殊要求,提高了设备的工作效率和安全性。
此外,复合涂层材料还具有良好的外观性能和装饰性能。
由于其表面涂层可以
采用各种颜色和图案,可以满足不同客户的个性化需求,提高了产品的市场竞争力。
综上所述,复合涂层材料具有优异的性能和广泛的应用前景,可以满足不同领
域的特殊需求,为各行各业的发展提供了新的可能性。
随着科技的不断进步和工艺的不断改进,相信复合涂层材料将会在未来得到更广泛的应用,并为人类社会的发展做出更大的贡献。
金属基复合材料涂层
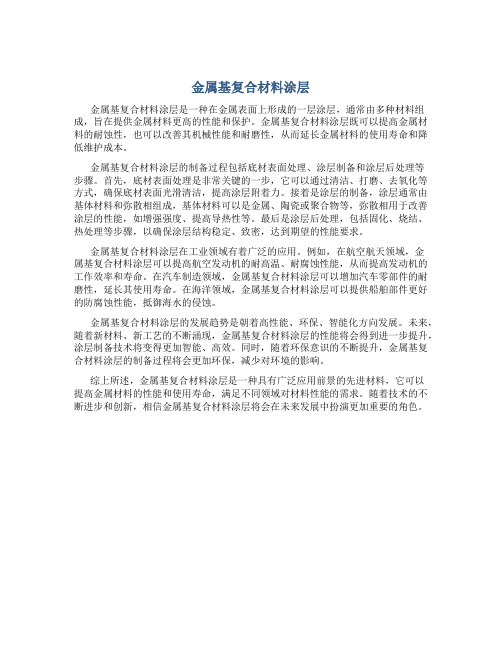
金属基复合材料涂层金属基复合材料涂层是一种在金属表面上形成的一层涂层,通常由多种材料组成,旨在提供金属材料更高的性能和保护。
金属基复合材料涂层既可以提高金属材料的耐蚀性,也可以改善其机械性能和耐磨性,从而延长金属材料的使用寿命和降低维护成本。
金属基复合材料涂层的制备过程包括底材表面处理、涂层制备和涂层后处理等步骤。
首先,底材表面处理是非常关键的一步,它可以通过清洁、打磨、去氧化等方式,确保底材表面光滑清洁,提高涂层附着力。
接着是涂层的制备,涂层通常由基体材料和弥散相组成,基体材料可以是金属、陶瓷或聚合物等,弥散相用于改善涂层的性能,如增强强度、提高导热性等。
最后是涂层后处理,包括固化、烧结、热处理等步骤,以确保涂层结构稳定、致密,达到期望的性能要求。
金属基复合材料涂层在工业领域有着广泛的应用。
例如,在航空航天领域,金属基复合材料涂层可以提高航空发动机的耐高温、耐腐蚀性能,从而提高发动机的工作效率和寿命。
在汽车制造领域,金属基复合材料涂层可以增加汽车零部件的耐磨性,延长其使用寿命。
在海洋领域,金属基复合材料涂层可以提供船舶部件更好的防腐蚀性能,抵御海水的侵蚀。
金属基复合材料涂层的发展趋势是朝着高性能、环保、智能化方向发展。
未来,随着新材料、新工艺的不断涌现,金属基复合材料涂层的性能将会得到进一步提升,涂层制备技术将变得更加智能、高效。
同时,随着环保意识的不断提升,金属基复合材料涂层的制备过程将会更加环保,减少对环境的影响。
综上所述,金属基复合材料涂层是一种具有广泛应用前景的先进材料,它可以提高金属材料的性能和使用寿命,满足不同领域对材料性能的需求。
随着技术的不断进步和创新,相信金属基复合材料涂层将会在未来发展中扮演更加重要的角色。
VCI复合涂层技术分析

VCI复合涂层技术分析一、基本情况VCI复合涂层技术就是将VCI(气相缓蚀剂)技术与片状锌粉相结合的一种涂料技术,主要面向高速公路护栏、灯杆、电器等钢构件的高强度防腐。
VCI技术发明于二战期间,最初用于武器装备的保护,但VCI易挥发水解,目前多应用于封闭空间对易生锈金属的保护。
片状锌粉的电化学保护性能和覆盖性能优于球状锌粉,两者结合作为金属防腐的复合涂料,必须要求涂层有着良好的屏蔽与封闭性。
从专利库中搜索,VCI复合涂层技术相关专利共有4件,全部为发明专利,拥有者均为中国航空工业集团公司百慕新材料技术工程股份有限公司。
该公司为中国航发控股的高新技术公司,于2009年在新三板挂牌,曾参与6项国家及行业标准编制。
VCI复合涂层技术曾于2012年获得中国腐蚀与防护学会科技进步一等奖,也是工信部与国防科工局2015年度《军用技术转民用推广目录》中的10项重点推荐项目之一。
二、技术分析VCI复合涂层技术作为一项军转民技术,可查阅的文献资料较少。
从现有资料看,包括该技术在内的缓蚀防护封存技术从上世纪90年代开始已逐渐军用装备领域,而VCI的复配以及与无机材料的结合研究,也是学界普遍认同的未来VCI的主要研究方向。
目前,热镀锌因为生产效率高,应用场景灵活仍然是金属防腐领域应用最广泛的技术。
相较于热浸锌,2015年度《军用技术转民用推广目录》中认定,VCI复合涂层技术所得产品,金属锌节省了近30%,材料总成本节约了25%左右。
其中45微米厚度VCI复合涂层盐雾寿命超过10000h,相当于热浸锌的10倍以上,附着力、耐温和涂层电阻指标均与热镀锌技术相近。
三、效益分析目前中航百慕新材料的VCI新型涂料生产基地共有4个,其中已竣工投产2个。
江苏高邮作为首个示范基地,一期建筑面积80000平方米,已于15年建成投产,目前产品主要销往光伏支架、金属灯杆、电缆桥架等金属防腐涂装领域,其中包括全球首个“熊猫光伏电站”的彩色支架的供货安装。
防腐涂层分类

防腐涂层分类
防腐涂层是一种应用广泛的涂层,用于保护金属表面免受腐蚀和氧化的影响。
根据涂层的成分和用途,防腐涂层可以分为以下几类:
1. 金属涂层:金属涂层是一种将金属颗粒或金属化合物涂覆在金属表面上的涂层。
金属涂层可以提供优异的耐腐蚀性能,例如铝、锌、铬等金属涂层可以提供防锈和防腐蚀的保护。
2. 有机涂层:有机涂层是一种含有有机物的涂层。
有机涂层可以提供优异的耐化学腐蚀性能,例如环氧树脂涂层、聚氨酯涂层等。
3. 无机涂层:无机涂层是一种含有无机物的涂层。
无机涂层可以提供优异的耐高温、耐腐蚀性能,例如陶瓷涂层、磷化涂层、硅酸盐涂层等。
4. 复合涂层:复合涂层是一种由多种涂层组合而成的涂层。
复合涂层可以综合利用各种涂层的优点,提供更加优异的防腐性能。
5. 阳极保护涂层:阳极保护涂层是一种利用阳极保护原理来保护金属表面的涂层。
阳极保护涂层可以提供优异的耐腐蚀性能,例如铝阳极保护涂层、锌阳极保护涂层等。
以上是防腐涂层的主要分类,不同类型的涂层在不同的应用场合具有不同的优缺点,需要根据具体情况选择合适的涂层。
摩擦学涂层分类
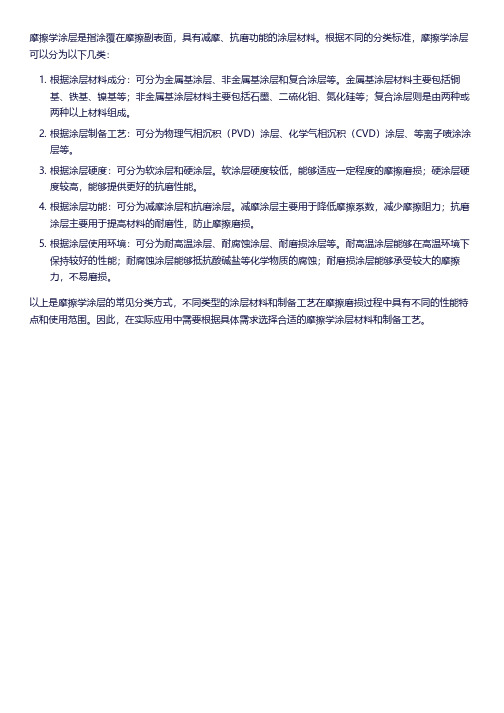
摩擦学涂层是指涂覆在摩擦副表面,具有减摩、抗磨功能的涂层材料。
根据不同的分类标准,摩擦学涂层可以分为以下几类:
1. 根据涂层材料成分:可分为金属基涂层、非金属基涂层和复合涂层等。
金属基涂层材料主要包括铜
基、铁基、镍基等;非金属基涂层材料主要包括石墨、二硫化钼、氮化硅等;复合涂层则是由两种或两种以上材料组成。
2. 根据涂层制备工艺:可分为物理气相沉积(PVD)涂层、化学气相沉积(CVD)涂层、等离子喷涂涂
层等。
3. 根据涂层硬度:可分为软涂层和硬涂层。
软涂层硬度较低,能够适应一定程度的摩擦磨损;硬涂层硬
度较高,能够提供更好的抗磨性能。
4. 根据涂层功能:可分为减摩涂层和抗磨涂层。
减摩涂层主要用于降低摩擦系数,减少摩擦阻力;抗磨
涂层主要用于提高材料的耐磨性,防止摩擦磨损。
5. 根据涂层使用环境:可分为耐高温涂层、耐腐蚀涂层、耐磨损涂层等。
耐高温涂层能够在高温环境下
保持较好的性能;耐腐蚀涂层能够抵抗酸碱盐等化学物质的腐蚀;耐磨损涂层能够承受较大的摩擦力,不易磨损。
以上是摩擦学涂层的常见分类方式,不同类型的涂层材料和制备工艺在摩擦磨损过程中具有不同的性能特点和使用范围。
因此,在实际应用中需要根据具体需求选择合适的摩擦学涂层材料和制备工艺。
复合涂层分类

复合涂层分类复合涂层是指由两种或两种以上的涂料、材料或涂层组成的涂层。
复合涂层通常由基层、中间层和表层三部分组成,每层都可以选择不同的材料或涂料。
根据涂料的性质,可以将复合涂层分为以下几类。
1. 有机涂层与无机涂层复合涂层有机涂层是指由含有碳、氢、氧、氮等元素的高分子材料组成的涂层,如涂料、树脂等。
无机涂层是指由非有机化合物组成的涂层,如陶瓷、金属等。
有机涂层与无机涂层可以组合在一起形成复合涂层。
该种复合涂层的基层通常选用无机涂层,中间层可选用有机涂层,表层则采用有机涂层。
这样可以兼顾基层的实力和表层的颜色效果。
2. 溶液涂层与粉末涂层复合涂层溶液涂层是指溶于溶剂中的涂层,常见的有羧基树脂、醇酸树脂、脂肪族醇树脂等。
粉末涂层是指粉末状的涂层,通常是填料或树脂以及功能添加剂的粗粉混合物。
溶液涂层与粉末涂层可以组合在一起形成复合涂层。
该种复合涂层的基层通常选用粉末涂层,中间层可选用溶液涂层,表层仍然是粉末涂层。
这样可以降低基层表面的粗糙度和增强表层的颜色效果。
3. 热喷涂涂层与冷喷涂涂层复合涂层热喷涂涂层是指将熔融状态的材料通过喷嘴喷射在基层表面形成涂层,如高速火焰喷涂、高速电弧喷涂、等离子喷涂等。
冷喷涂涂层是指通过喷射压缩空气或氮气等气体将细颗粒物质喷射在基层表面形成涂层,如喷砂、喷丸、电磁喷涂等。
热喷涂涂层与冷喷涂涂层可以组合在一起形成复合涂层。
用热喷涂涂层作为基层,表层采用冷喷涂涂层,中间层可以使用其他的涂层形成。
这样可以兼顾基层的强度和表层的保护性能。
4. 电化学涂层与无电化学涂层复合涂层电化学涂层是指在电解质中通过电解处理形成的涂层,如电沉积、阳极氧化、电镀等。
无电化学涂层是指不通过电解处理而形成的涂层,如溅射、浸涂、喷涂等。
电化学涂层与无电化学涂层可以组合在一起形成复合涂层。
该种复合涂层的基层通常选用电化学涂层,中间层使用无电化学涂层,表层还是电化学涂层。
这样既能减少基层表面的开裂现象,又能兼顾表层的防腐功能。
两种复合涂层性能的对比研究
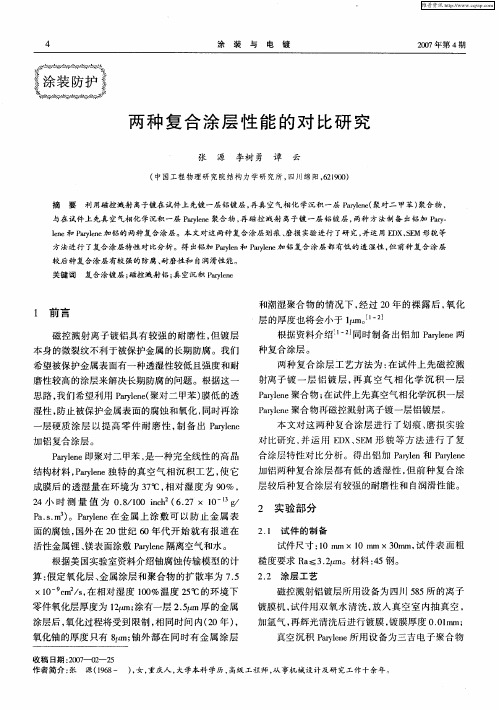
5
Z
-
Z
-
・
. R
R
蜷 世
瓣 登
涂 层 1 L与 切 向 力 变 化 曲 线 与
涂 层 2 L 与 切 向 力 变 化 曲 线 与
图 1 两 种 涂 层 的 划 痕 实 验 曲线
图2 涂层 1 和涂 层 2在 F= 0 =0 0时的 ~ 、 .3 ,N 5 0 一 三维 图 ( 摩擦力修正系数 3 8 .)
真空 沉积 Prl e所用 设 备为 三吉 电 子聚 合物 a e yn
作者简介 : 张
源(9 8 )女 , 16 一 , 重庆人 , 大学本科学历 , 高级 工程师, 从事机械设计及研 究工作 十余年
维普资讯
20 07年 8月
张 源等 : 种 复 合 涂 层 性 能 的 对 比研 究 两
维普资讯
4
涂
装
与
电
镀
20 年第 4期 07
两 种 复 合 涂 层 性 能 的 对 比研 究
张 源 李树 勇 谭 云
( 中国工程物理研 究院结构 力学研 究所 , 四川绵阳,290 61 ) 0
摘
要
利 用磁控 溅射 离子镀在试件上先镀一层铝镀层 , 再真 空气相化 学沉积一层 Prl e 聚对二 甲苯 ) ay n ( e 聚合物 ,
与在 试 件 上 先 真 空 气 相 化 学 沉积 一层 Prl e聚合 物 , 磁 控 溅 射 离子 镀 一 层 铝 镀 层 , 种 方 法制 备 出铝 加 Pr— a e yn 再 两 ay l e Prl e 铝 的 两 种 复合 涂 层 。本 文 对 这 两 种 复 合 涂 层 划 痕 、 损 实验 进 行 了研 究 , e 和 a e 加 n yn 磨 并运 用 E X、E 形 貌等 D SM 方 法进 行 了复 合 涂 层特 性对 比分 析 。得 出铝 加 Pr e al y n和 P 'ee 铝 复 合 涂 层 都 有 低 的 透 湿性 , 前 种 复 合 涂 层 ml 加 yn 但 较 后 种 复 合 涂 层 有 较 强 的 防 腐 、 磨 性和 自润 滑性 能 。 耐 关键词 复 合 涂镀 层 ; 磁控 溅 射 铝 ; 空沉 积 Prl e 真 ay n e
金属陶瓷复合涂层的定义

属陶瓷复合涂层的定义
嘿,咱来说说啥是金属陶瓷复合涂层哈。
我记得有一回,我去一个工厂参观。
哇,那里面有好多奇奇怪怪的机器和材料。
我就看到一个工人拿着一个喷枪,对着一个金属零件喷来喷去。
我好奇地凑过去看,就问他:“大哥,你这是干啥呢?”那工人说:“这是在给零件喷金属陶瓷复合涂层呢。
”我就懵了,啥是金属陶瓷复合涂层啊?
工人大哥就给我解释起来。
他说啊,这金属陶瓷复合涂层呢,就是把金属和陶瓷两种材料结合在一起,涂在零件表面上。
这样可以让零件变得更结实、更耐磨、更耐腐蚀啥的。
我听了还是有点迷糊,这金属和陶瓷咋能结合在一起呢?
工人大哥就接着说,他们用一种特殊的工艺,把金属粉末和陶瓷粉末混合在一起,然后用喷枪喷到零件上。
在高温下,这些粉末就会熔化,然后凝固在一起,形成一层坚硬的涂层。
我就想象着那个画面,觉得好神奇啊。
有一次,我看到一个喷好金属陶瓷复合涂层的零件。
哇,那表面亮晶晶的,可好看了。
我用手摸了摸,感觉很光滑,很坚硬。
工人大哥说,这种涂层可以保护零件不受磨损和腐蚀,延长零件的使用寿命。
我就想,这可真是个好东西啊。
总之啊,金属陶瓷复合涂层就是一种把金属和陶瓷结合在一起的涂层,可以让零件变得更厉害。
以后要是看到那种亮晶晶的零件,说不定就是喷了金属陶瓷复合涂层呢。
嘿嘿。
- 1、下载文档前请自行甄别文档内容的完整性,平台不提供额外的编辑、内容补充、找答案等附加服务。
- 2、"仅部分预览"的文档,不可在线预览部分如存在完整性等问题,可反馈申请退款(可完整预览的文档不适用该条件!)。
- 3、如文档侵犯您的权益,请联系客服反馈,我们会尽快为您处理(人工客服工作时间:9:00-18:30)。
SiO2 + RO2 → RSiO4
原位反应法制备硅酸钇涂层(续)
玻璃外涂层
microcrack 复合涂层截面图 硅酸钇涂层 涂层之间的界面 涂层之间结合十分良好, 界面上相之间自然连接, 说明各层很好的相容性 玻璃 硅酸钇 SiC C/C
Si/Y2O3=6:4制备的涂层试样表面及断面SEM照片
原位反应法制备硅酸钇涂层(续)
硅酸盐涂层 等离子喷涂制备梯度硅酸钇涂层 通过设计成分梯度的涂层结构,成功地解决了硅酸钇与C/C 复合材料热膨胀失配的问题。
典型的三层涂层结构
Glass sealant layer SiO2 • Y2O3 1.5SiO2 •Y2O3 2SiO2• Y2O3 SiC bonding layer
C/C
SiC-CrSi2涂层
B
Si, Cr Si, C
A
100 80 weight loss/% 60 40 20 0 0 5 10 15 20 25 30 35 oxidation time/hour
SiC-CrSi2 coated C/C SiC coated C/C C/C
SiC-CrSi2涂层在1500℃ 下的防氧化寿命比单层 SiC延长近十倍
涂层的高温防氧化性能
8 7 6 C1 C2 C3 C4 C5 C6 C7
Weight loss/%
5 4 3 2 1 0 0 50 100 150
200
Time/h
Si/Y2O3=6:4的涂层试样在1600℃下氧化202小时后失重小于0.7%
梯度复合涂层
由于碳/碳复合材料基体与涂层之间不可避免的热膨胀差 异,故在涂层中易产生裂纹。裂纹除了可以采用前述的密 封层愈合外,还可以通过功能梯度材料原理制作热膨胀系 数梯度变化的涂层消除裂纹。
by sintering
SiC
by plasma spray
硅酸钇
by pack cementation
玻璃
梯度复合涂层的结构示意图
SiC/硅酸钇/玻璃复合涂层断面形貌
晶须增韧复合涂层
由于碳/碳复合材料需要在燃气冲刷剪切力作用下 服役,因此,涂层与基体之间结合力以及涂层本身 内聚力的提高是一个比较现实的问题。为了提高这 种结合力和增强涂层的韧性,提出了一种新型的晶 须增韧陶瓷复合涂层技术。
50
0% 15%
0% 15%
2 1 0 0 10 20 30 40 Oxidation time/ hour 50
1 μm
1μm
(a)
200nm 200nm
(b)
(c)
(d)
•
讨论:
1. 你认为哪一种复合涂层有发展潜力?说出理由。 2. 多层复合涂层的设计思路是什么?
目前,与基体结合牢固、稳定的多相镶嵌复合涂层的形成 主要有两种方式。一是粉料经扩散、熔融流动、蒸发、凝 聚、溶解沉淀等渗透作用进入基体与基体发生反应而形成 的;二是首先制备多孔的SiC内涂层,然后将其他耐高温 陶瓷材料通过扩散及传质作用渗透进入SiC内涂层的孔隙 中,从而形成致密的多相镶嵌复合涂层。从断面上看,多 组分之间没有明显的层间界面,这样可以有效解决相或多 项材料之间热膨胀系数不匹配的问题。
晶须增韧陶瓷涂层
拨出桥连
裂纹转向
晶须增韧陶瓷涂层
陶瓷基体 SiC晶须
C/C
SiC晶须增韧SiC涂层 首先采用料浆法在C/C复合材料表面制备含有SiC晶须的 多孔涂层,再采用包埋法填充涂层中的孔隙。
料浆法制备多孔涂层
包埋法填充涂层中的孔隙
SiC晶须增韧SiC涂层(续)
Weight loss/%
0.4 0.2 0.0 -0.2 0 50
涂层试样氧化失重曲线
SiC-莫来石-Al2O3涂层
采用两次包埋技术在C/C复合材料表面制备了SiC-Al2O3-莫来 石复合涂层,克服了国外采用热喷涂、溶胶-凝胶等方法制备 莫来石涂层致密度低,且涂层与基体界面结合差等问题 。
一次包埋制备疏松的SiC内涂层 二次包埋制备致密的复相外涂层
SiC-Al2O3-莫来石复合涂层试样的截面(a)与表面(b)形貌
多相镶嵌复合涂层
许多高温陶瓷材料(如MoSi2,AI2O3等)由于与SiC之 间热膨胀系数相差很大,不能直接应用于SiC表面而形成 多层涂层。为了解决此问题,曾燮榕、黄剑锋等人提出 了多相镶嵌复合涂层模式。多相镶嵌复合涂层组分之间 采用互相镶嵌方式有机组合,提高涂层致密度的同时也 缓解了热膨胀不匹配问题。
30 25 Weight loss/% 20 15 10 5 0 0
5 4 Weight loss/% 3 2 1 0 -10 0 10 20 30 40 50 60 70 80 Oxidation time/h
Weight loss/ % 3
0% 15%
10
20 30 40 Oxidation time/h
-0.1 -0.2 -0.3 -0.4 -0.5 0
1500℃氧化315小时 后仍未失重
100μm
50
100 150 200 250 300 350
Oxidation time/h
SiC-MoSi2-CrSi2-Si涂层
采用两步包埋法制备的SiCMoSi2-CrSi2-Si涂层在1500和 1600静态空气环境中可对C/C 复合材料有效保护1000小时 和500小时。
0.3
1.0
Wight gain/%
0.2
Wight loss/%
1500 ℃
0.1
0.8 0.6 0.4 0.2 0.0
1600 ℃
1000 hrs
0.0 0 250 500 750 1000
500 hrs
0 100 200 300 400 500
Oxidation time/h
Oxidation time/h
碳/碳复合材料高温 抗氧化复合涂层
复合涂层的优异性能
复合材料各组分之间可以取长补短、协同作用, 弥补了单相材料的缺点,改进了单相材料的性 能,甚至可产生单一材料所不具有的新性能。
可以根据表面涂层的性能需求进行设计, 使表面涂层具有更加优异的性能。
¾ 多相镶嵌复合涂层 ¾ 多层复合涂层 ¾ 梯度复合涂层 ¾ 晶须增韧复合涂层
-20 -40 -60 -80 100 150 200 250 300 350 Time/hour
1500℃静态空气中防护寿 命超过310小时。
SiO2 glass layer transition layer
Weight loss rate/ -5 -2 -1 (×10 ) /g⋅cm ⋅h
0.6
SiC-MoSi2-WSi2涂层
氧化前
Intensity / a.u.
6000
c
4000
a b a c a c
a-α− SiC b-Si c-(W x Mo 1-x )Si2
c
2000
a
ac a aa
0
50μm
0.1
20
30
40
50
60
o70802θ / ( )0.0
氧化后
Weight loss%
多相镶嵌涂层
利用多相镶嵌互补原理,构造多相涂层结构,并通过 调整各相含量及分布,解决了硅化物、莫来石等涂层与 C/C热膨胀不匹配、涂层易开裂和剥落等问题。
Si、氧化铝 硅化物、莫来石 SiC
C/C
SiC-CrSi2、SiC-MoSi2/MoSi2、SiC-MoSi2/WSi2 、SiC-Al2O3-莫来石
多层复合涂层
最简单的复合涂层是双层复合涂层。由于SiC与C/C基体 良好的物理化学相容性,双层复合涂层目前大多采用 SiC为内涂层,外层材料则选用耐火氧化物、高温玻璃 或高温合金作为密封层。该种涂层利用密封层对SiC内 涂层的裂纹和孑L隙进行愈合,从而提高复合涂层的抗 氧化能力。
在双层复合涂层研究的基础上,以SiC为内涂层,采用 耐高温陶瓷材料(如ZrO2,MoSi2,Al2O3,莫来石和硅 酸钇等)为热障涂层,以氧气渗透率低的玻璃、硅酸盐等 为外层的三层复合涂层可将高温陶瓷材料的优点结合起 来,发挥各自的作用,达到更满意的抗氧化效果。
0
SiC晶须增韧MoSi2-SiC-Si涂层
由料浆法与包埋法制备
3.0 2.5 Weight loss/% 2.0 1.5 1.0 0.5 0.0 0 50 100 150 Oxidation time/hour 200 0% 10%
SiC晶须增韧SiC-CrSi2涂层
在SiC-CrSi2涂层中加入SiC晶须后,涂层在1200-1500℃空气中的防护能力明显提高
原位反应法制备硅酸钇涂层
开发了一种在氧化性气氛下制备硅酸盐涂层的新方法—原位反 应法,打破了C/C高温涂层仅能在真空或保护性气氛下制备的传统 观念。该方法解决了硅酸盐涂层内部结合力弱的问题,同时实现 了高致密度硅酸钇涂层的制备。
原位反应法制备硅酸盐涂层的形成原理
Si + O2 → SiO2
SiO 2 + RO → RSiO 3 SiO 2 + R2 O3 → R2 SiO5