清洁煤燃烧器的技术
洁净煤技术

浅谈洁净煤技术1.洁净煤技术的背景1.1煤炭利用过程的危害煤炭是世界重要能源,我国更是世界最大的煤炭生产国和消费国,而发电用煤占原煤的很大比列。
我国煤炭消费的一个主要特点是大量原煤直接燃烧,大约占原煤总量的62%。
由于大量煤炭直接燃烧,燃煤质量差,且燃烧效率低,对环境也造成了破坏。
煤炭燃烧后会产生二氧化硫、一氧化碳、烟尘、放射性飘尘、氮氧化物、二氧化碳等。
这些产物会造成很大的危害:二氧化硫、二氧化氮会形成酸雨,严重影响地球生态环境和人类社会;燃烧后排放的二氧化碳会造成全球气候变暖和温室效应,威胁着全球生态系统及人类生存;烟尘会以颗粒物形式漂浮在大气中,危害生物健康及气候;人类长期吸入氮氧化物会影响呼吸系统造成疾病,同时氮氧化物达到一定浓度后也会和其他物质反应形成光化学烟雾,损害生态系统。
1.2针对煤炭利用造成污染的一些措施有关专家提出开发清洁和可再生能源,改善电力工业结构,降低煤炭消费量。
清洁和可再生能源主要包括核能、水能、风能、天然气等。
目前我国清洁能源发电的比例也在逐年提高,生态环境得到了改善。
虽然其他能源消费比例有所提高,但煤炭仍是我国主要的消费能源,针对这一情况,提高煤炭使用效率提高使用技术就变得尤为重要。
近些年,我国正逐步进行工业锅炉大型化,减小煤耗提高效率,以热电联产、集中供热取代分散小锅炉。
再有就是实施城市煤气化以提高煤炭整体利用效率。
1.3洁净煤技术的提出及意义洁净煤技术一词源于美国。
洁净煤技术贯穿于开发即利用整个过程,是减少污染提高利用效率的加工、燃烧、转化及污染控制等高新技术的总称。
洁净煤技术主要分为煤炭燃烧前处理、燃烧中处理、燃烧后处理和转化技术。
而且各个部分越往后越难,成本及投资也越来越多。
各国在分阶段进行各环节净化技术同时,也分阶段进行技术经济优化。
我国煤炭大部分用于直接燃烧,造成各种问题,可再生能源发展缓慢。
我国可再生能源利用量明显低于发达国家平均水平,可再生能源与新能源发展滞后。
煤炭清洁燃烧技术减少排放和提高效能

煤炭清洁燃烧技术减少排放和提高效能煤炭作为全球最主要的能源之一,其使用对环境造成的影响不容忽视。
传统的煤炭燃烧往往伴随着大量的二氧化碳、硫化物和氮氧化物的排放,这些废气不仅对空气质量造成污染,也加剧了全球变暖的问题。
为了应对这一挑战,研究人员不断努力开发新的煤炭清洁燃烧技术,以减少排放并提高能源利用效率。
一、煤炭气化技术煤炭气化是一种将煤转化为合成气(主要为一氧化碳和氢气)的技术。
通过对煤炭进行气化处理,可以将固体煤转化为气体燃料,从而减少燃烧产生的污染物的排放。
此外,煤炭气化还可以通过气化废热回收系统,提高能源的利用效率。
二、煤炭洁净燃烧技术煤炭洁净燃烧技术是指在煤炭燃烧过程中采用一系列的措施来减少废气排放。
例如,通过对煤粉细度的控制和煤粉干燥预热处理,可以增加煤粉的燃烧速率,降低燃烧温度,从而减少氮氧化物的生成。
此外,还可以通过添加燃烧辅助剂,如石灰石和硫化钙,来吸收燃烧过程中产生的硫化物,减少硫化物的排放。
三、燃烧废气处理技术煤炭燃烧产生的废气中含有大量的污染物,例如二氧化碳、一氧化碳、氮氧化物和颗粒物等。
为了减少这些污染物的排放,研究人员开发了多种燃烧废气处理技术。
例如,烟气脱硫技术可以通过喷射石灰浆或氨水来吸收烟气中的二氧化硫,从而减少硫化物的排放。
此外,烟气除尘技术可以通过静电除尘器或布袋除尘器等设备,将烟气中的颗粒物捕集下来,达到净化烟气的目的。
四、高效利用煤炭能源除了减少煤炭燃烧过程中的排放物外,提高煤炭能源的利用效率也是降低环境影响的重要途径。
研究人员利用高效的燃烧器和热交换器等设备,设计出更加节能高效的煤炭燃烧系统。
此外,结合余热回收技术,可以降低煤炭燃烧过程中的能量损失,提高能源利用效率。
综上所述,煤炭清洁燃烧技术的发展对于减少煤炭燃烧过程中的排放物,并提高能源利用效率具有重要意义。
在未来,我们需要继续加大对煤炭清洁燃烧技术的研究和应用,以促进能源的可持续发展,实现经济与环境的双赢。
清洁燃烧技术最后整理

1,燃烧技术有几种NOx? 影响因素?答:煤在燃烧过程中产生的NOx分为三类,即热力型NOx、燃料型NOx和快速型NOx,由于快速型NOx的生成量很小,故不考虑,可以认为热力型NOx和燃料型NOx生成量之和即为燃烧产生它们的NOx的总量。
热力型NOx与燃烧温度、氧气的浓度及气体在高温区停留的时间有关;燃料型NOx的生成机制为:燃料中的氮化合物首先发生热分解形成中间产物,然后再经氧化生成NO,燃料型NOx主要是NO。
NOx中以燃料型为主,占NOx 的总生成量60~80%,热力型占20%。
2,低NOx 的燃烧技术有那几种?举例?目的?答:燃煤锅炉低NOx燃烧技术的主要目的就是根据NOx的生成机理,在煤的燃烧过程中通过改变燃烧条件或合理组织燃烧方式来遏制NOx生成的燃烧技术。
目前常见的低NOx燃烧技术有低NOx的燃烧器技术、空气分级燃烧技术(又称再燃技术)和烟气再循环技术3,我国能源结构、能源利用及其环境与世界其他国家相比有以下特点:1)初级能源以煤为主;2)人均能源消费水平低;3)煤炭生产以地方和集体煤矿为主;4)原煤入选率低;5)煤炭消费构成复杂;6)能耗高、利用率低、浪费严重;7)煤烟型大气污染严重;8)硫酸型酸雨问题严重;9)CO2排放量迅速增长。
4,工业煤的主要特点?答:工业型煤的主要特点有:1)在块煤燃烧或气化领域,型煤燃烧可以提高煤炭的利用率,节约能源。
2)在配置过程中添加固硫剂,可以有效地控制粉尘和SO2的污染排放。
文献报道,型煤中如果添加3.3%的石灰石可以在燃烧中脱去87%的硫。
3)通过型煤制备过程中的配料或成型可以改善热稳定性差或难燃煤(贫煤、无烟煤、煤泥等)的燃烧特性,扩大煤炭资源的利用。
4)更为重要的是,型煤技术投资少、见效快,是经济性很好的洁净煤技术。
5,SOx主要有几种形态?主要形成是什么?哪些属于可燃S?哪些不属于可燃S?答:SOx主要有四种形态,即黄铁矿硫、硫酸盐硫、有机硫和元素硫。
洁净煤技术

洁净煤技术A12化工一班120702107 吕荣青摘要我国是一个多煤、少油、少气的国家,未来能源发展的政策仍是“煤为基础,多元发展”。
提高煤炭利用率、降低污染率,是我国能源工业发展的紧迫而现实的任务。
而完成这一任务,就需要大力发展洁净煤技术。
关键词:煤炭能源洁净煤技术1. 洁净煤技术的特点洁净煤技术是洁净、高效利用煤炭的先导性技术,最早由美国学者提出,主要是为了解决美国和加拿大边境的酸雨问题。
洁净煤技术是指从煤炭开发到利用全过程中,旨在减少污染物排放和提高利用效率的煤炭加工、转化、燃烧及污染控制等一系列新技术的总称,是使煤作为一种能源应达到最大限度的潜能利用,而将释放的污染控制在最低水平,实现煤的高效、洁净利用的技术体系。
洁净煤技术具有以下几个显著特点:首先,洁净煤技术以高硫煤为原料,以一碳化学为基础,采用多样化工艺,实现煤炭资源的优化配置、高效和清洁利用;其次,洁净煤技术涉及物理学、化学、生物学、地质学等多学科,化工、热工、环境等多技术,是一项多层次、多学科、综合性很强的系统工程;第三,洁净煤技术注重综合效益,实现了环境友好和经济发展的双重效益,即经济和环境的双赢。
传统意义上的洁净煤技术主要是指煤炭的净化技术及一些加工转换技术,即煤炭的洗选、配煤、型煤以及粉煤灰的综合利用技术,国外煤炭的洗选及配煤技术相当成熟,已被广泛采用;意义上洁净煤技术是指高技术含量的洁净煤技术,发展的主要方向是煤炭的气化、液化、煤炭高效燃烧与发电技术等等。
2.技术工艺洁净煤技术包括两个方面,一是直接烧煤洁净技术,二是煤转化为洁净燃料技术。
2.1直接烧煤洁净技术这是在直接烧煤的情况下,需要采用的技术措施:①燃烧前的净化加工技术,主要是洗选、型煤加工和水煤浆技术。
②燃烧中的净化燃烧技术,主要是流化床燃烧技术和先进燃烧器技术。
③燃烧后的净化处理技术,主要是消烟除尘和脱硫脱氮技术。
2.2煤转化为洁净燃料技术主要有四种:①煤的气化技术②煤的液化技术③煤气化联合循环发电技术④燃煤磁流体发电技术。
煤炭的洁净燃烧与高效利用技术

煤炭的洁净燃烧与高效利用技术【收藏本页】【打印】2009-8-18 来源:中煤网1、引言未来几十年内,煤炭在我国一次能源结构中的主导地位是不可动摇的,这已是无需争辩的事实。
因此,在未来几十年内,煤炭能源仍将是我国国民经济高速、健康、持续发展的重要支柱。
然而总体上说,我国目前的煤炭加工环节还相当薄弱,煤炭利用仍以传统、落后的技术为主,环保设施亦不配套、不健全。
因而,不仅煤炭利用效率较低,煤炭资源浪费严重,而且排放大量污染物,使得生态环境的恶化加剧。
人类社会的可持续发展首先要求经济、能源、环境必须协调发展。
根据我国国情,并总结一些工业发达国家的经验和教训,得出的结论是:大力发展洁净煤技术是我们切实可行的战略选择。
煤炭洁净加工与高效利用是我国洁净煤技术的重要组成部分,对提高煤炭利用效率、减少污染物排放具有十分重要的现实意义。
因此,应对其研究开发和技术推广给予足够的重视。
2、国内外技术现状2.1 国外情况国外一些国家,特别是工业发达国家消费的煤炭,绝大部分或大部分要经过洗选,因而商品煤质量较好。
目前,商品煤入洗率日本为100%,德国和加拿大为95%,英国和澳大利亚为75%,前苏联和南非为60%,美国为55%。
近年来,随着洁净煤技术在全球范围内的迅速发展,国外不断推出更加先进的煤炭洁净加工与高效利用新技术,这些技术不仅大幅度提高了煤炭利用效率,而且具有卓越的环保特性。
但目前普遍存在的问题是技术与设备造价昂贵,而且工程建设投资和运行费用也太高,因此,较难大量推广应用。
2.2 国内情况我国是世界上少数几个一次能源以煤为主的国家之一。
过去、现在和未来几十年内,煤炭在我国一次能源消费结构中一直占主要地位,见表1。
表1 煤炭在我国一次能源消费结构中所占比例年份1952 1960 1970 1980 1990 1997 2010 2050比例,% 95.00 93.90 80.89 72.15 76.20 73.50 64 47.7我国的煤炭消费结构与国外也有较大差别。
煤炭清洁燃烧技术

一、技术概述我国是世界耗煤第一大国,主要用于火力发电燃煤锅炉,由于大部分火电厂未对燃煤排气中的SO2、NOX采取措施脱除,因此造成对环境的污染越来越严重。
目前主要有两类方式对燃煤排放气体中的SO2、NOX进行处理。
一类是在炉内通过燃烧技术的改进,降低SO2、NOX排放量,这种技术主要应用于常规燃煤发电厂,称之为煤清洁发电技术。
目前已有商业应用。
煤的清洁发电技术主要有:循环流化床燃烧技术(CFBC)、增压流化床燃烧联合循环技术(PFBC-CC)、整体煤气化蒸汽-燃气联合循环技术(IGCC)。
另一类是在炉后,尾部烟气中进行脱硫脱硝。
采用的主要的技术和方法主要有:1.湿法烟气脱硫技术、2.旋转喷雾半干烟气脱硫技术、3.炉内喷钙尾部增湿脱硫技术、4.电子束照射法、5.磷铵肥法、6.活性焦法等,统称为脱硫(脱硝)技术。
二、现状及国内外发展趋势1.煤清洁发电技术(1)国外发展趋势①国外CFBC锅炉正向大型化方向迅速发展,循环流化床锅炉的炉型较多,各家公司都有自己独特的流派,竞争很激烈。
目前国外已运行的CFBC锅炉的容量等级已达到100-1 80MW,且技术上比较成熟并正在设计和研制200-300MW的CFBC锅炉,1995年由法国stein公司制造的250MWCFBC锅炉的投运,其容量上已接近300MW等级。
②在八十年代中期国外已开始建设PFBC-CC示范电站。
瑞典ABB-Carbon公司在PFBC -CC的商业化进程中处于领先地位,开发的输入热功率为200MW的P200装置首批五套已先后在瑞典、西班牙、美国和日本的电站投入运行。
首台输入功率为800MW的P800装置也正在日本 Karita电站建设中。
③经过净化处理的合成煤气为燃料的IGCC发电系统是目前最清洁高效的燃煤发电方式。
目前国外已建成工业装置5套,正在建设和计划建设的电站超过24座,总容量超过820 0MW,首台工业装置是1972年在德国克曼电厂建成的为170MW机组。
清洁煤技术

清洁煤技术是指在煤炭从开发到利用全过程中,旨在减少污染排放与提高利用效率的加工、燃烧、转化和污染控制等新技术的总称。
清洁煤技术主要包括两个方面:一是直接烧煤洁净技术。
这是在直接烧煤的情况下,需要采用相应的技术措施:①燃烧前的净化加工技术,主要是洗选、型煤加工和水煤浆技术。
②燃烧中的净化燃烧技术,主要是流化床燃烧技术和先进燃烧器技术。
③燃烧后的净化处理技术,主要是消烟除尘和脱硫脱氮技术。
二是煤转化为洁净燃料技术。
主要是煤的气化以及液化技术、煤气化联合循环发电技术和燃煤磁流体发电技术。
清洁煤技术是当前国际上解决环境问题的主导技术之一,也是高技术国际竞争的重要领域之一。
多年来,我国围绕提高煤炭开发利用效率、减轻对环境污染进行了大量的研究开发和推广工作,并随着国家宏观发展战略的转变,已把清洁煤技术作为可持续发展和实现两个根本转变的战略措施之一,得到了中央政府的大力支持。
目前,我国的清洁煤技术在四个领域: 煤炭加工、煤炭高效洁净燃烧、煤炭转化、污染排放控制与废弃物处理)的十多项技术方面,通过引进技术和自主开发、创新已建设了一大批示范工程,有效地促进丁我国洁净煤技术的发展和应用,个别方面已领先于国际水平。
但是,由于相关政策的不配套,以及清洁煤技术重在社会效益和长远的综合经济效益的结合,一般都具有投入大、回收期长的特点,各级地方政府推进的积极性不高,使得这些技术的推广运用情况并不理想。
清洁煤概念是20世纪80年代中期美国首先提出的,是指在煤炭开发和加工利用全过程中旨在减少污染与提高利用效率的加工﹑燃烧﹑转换及污染控制等技术的总称,是使煤作为一种能源应达到最大限度潜能的利用,而释放的污染物控制在最低水平,达到煤的高效清洁利用的技术。
采用煤炭加工技术,可有效降低原料煤的灰分和硫分,实现煤炭燃前脱硫降灰,大幅度减少大气污染物排放,减少煤炭利用的外部成本。
发展煤基合成燃料可以促进能源供应来源的多样性,改善单一的能源结构,在相当程度上缓解我国石油、天然气供应不足的问题,且经济投入和运行成本大大低于采用石油和天然气,有利于我国清洁能源的发展及长远的能源安全。
洁净煤技术概述

洁净煤技术概述1.能源1.1能源的概念能源亦称能量资源或能源资源。
是指可产生各种能量(如热量、电能、光能和机械能等)或可做功的物质的统称。
是指能够直接取得或者通过加工、转换而取得有用能的各种资源,包括煤炭、原油、天然气、煤层气、水能、核能、风能、太阳能、地热能、生物质能等一次能源和电力、热力、成品油等二次能源,以及其他新能源和可再生能源。
1.2能源的分类能源种类繁多,根据不同的划分方式,可分为不同的类型:(1)按来源分为3类:①来自地球外部天体的能源(主要是太阳能)。
除直接辐射外,并为风能、水能、生物能和矿物能源等的产生提供基础。
②地球本身蕴藏的能量。
如原子核能、地热能等。
③地球和其他天体相互作用而产生的能量。
如潮汐能。
(2)按能源的基本形态分类,有一次能源和二次能源。
前者即天然能源,指在自然界现成存在的能源。
如煤炭、石油、天然气、水能等。
后者指由一次能源加工转换而成的能源产品。
如电力、煤气、蒸汽及各种石油制品等。
一次能源又分为可再生能源(水能、风能及生物质能)和非再生能源(煤炭、石油、天然气、油页岩等)。
根据产生的方式可分为一次能源(天然能源)和二次能源(人工能源)。
一次能源是指自然界中以天然形式存在并没有经过加工或转换的能量资源,一次能源包括可再生的水力资源和不可再生的煤炭、石油、天然气资源,其中包括水、石油和天然气在内的三种能源是一次能源的核心,它们成为全球能源的基础;除此以外,太阳能、风能、地热能、海洋能、生物能以及核能等可再生能源也被包括在一次能源的范围内;二次能源则是指由一次能源直接或间接转换成其他种类和形式的能量资源,例如:电力、煤气、汽油、柴油、焦炭、洁净煤、激光和沼气等能源都属于二次能源。
(3)按能源性质分,有燃料型能源(煤炭、石油、天然气、泥炭、木材)和非燃料型能源(水能、风能、地热能、海洋能)。
(4)根据能源消耗后是否造成环境污染可分为污染型能源和清洁型能源。
污染型能源包括煤炭、石油等,清洁型能源包括水力、电力、太阳能、风能以及核能等。
洁净煤技术第05章 洁净燃烧技术

第五章洁净燃烧技术第一节概述一、洁净燃烧技术所涉及的领域我国煤利用的主要形式是直接燃烧,直接燃煤量占用煤总量的80%以上。
燃煤设备的容量差异很大,由小到大依次为民用(含商用)炉灶,工业(含供暖)锅炉和工业窑炉,热电站及自备电站锅炉,大型火力发电锅炉,小时燃煤量由几百克到数百吨。
目前的中小燃煤设备(小时燃煤量5吨以下)燃用着总用煤量的40%以上。
它们的燃烧效率及热效率不高,民用炉灶热效率约为16%左右,工业炉窑热效率仅40%左右,工业及供暖锅炉热效率也仅50%~65%。
以高效技术改造后该领域可节约我国总用煤量的10%左右。
大型燃煤设备指电站锅炉,我国大型电站几乎全部使用低于临界参数的蒸汽循环机组,平均供电效率仅为32%左右,如用高效技术使之达40%~45%,则电站可节约我国总用煤量的7%~10%。
直接燃煤也是我国大气污染物的主要来源。
目前除对尘排放有一定治理外,SO x、NO x、CO和CO2、C n H m等污染均有待治理。
实现高效洁净燃煤有两条路,一个是在现有设备上改进,包括燃用型煤,烟气净化等;另一条路就是采用新燃烧技术,其中包括循环流化床燃烧(CFBC)、煤气、蒸汽联产(CFBG-C)、增压流化床联合循环(PFBC)、整体气化联合循环(1GCC)和部分气化联合循环(PGCC),本章将介绍新燃烧技术。
二、实现高效洁净燃烧新燃烧技术与旧有层燃和室燃技术不同,其特点是煤被部分和完全气化,即使是直接燃烧固体燃料也是在流化床内进行。
气化和流化床燃烧均是高效洁净燃烧。
除改变燃烧方式外新燃烧方式还可构成燃气、蒸汽联合循环发电技术,以提高循环效率。
新燃烧技术将引起一系列变化;首先可使居民和小型设备燃料煤气化,特别令人感兴趣的是它利用我国富产的高挥发分非强粘结性粉末煤,新气化工艺的投资和成本较现有技术均有显著降低;所列技术将更适于发展热电联供,使工业及城市用热(冷)效率更高;将既可使用优质燃料又可使用劣质燃料,使地产的或加工副产的可燃物物尽其用;所列技术将以低的投资和运行费大幅度降低SO x、NO x的污染,是难得的,可减少CO2的有效途径,灰渣特别是固硫后的灰渣有良好的可用性;所包括的联合循环发电技术与超临界技术一起是发电领域近期可大幅度提高供电效率的现实途径。
《清洁燃烧技术》PPT课件

2.燃料完全燃烧的条件
燃料完全燃烧的条件是适量的空气、足够的温度 、必要的燃烧时间、燃料与空气的充分混合。
• (1) 空气条件:按燃烧不同阶段供给相适应 的空气量。
• (2) 温度条件:只有达到着火温度,才能与 氧化合而燃烧。
• 着火温度:在氧存在下可燃质开始燃烧必须达 到的最低温度。各种燃料的着火温度见表2-4 。
【任务二】煤燃烧大气污染物排放量的计算
某电厂烟气温度为473k,压力为105kpa,湿烟气量 V=10400m3,水蒸气的体积分数为6.25%,二氧化碳为 10.7%,氧气为8.2%,不含一氧化碳。排放的污染物质流 量为22.7kg/min。求1.污染物排放的流量(单位:t/d)2. 污染物在干烟气中的浓度。3.烟气中的过剩系数。4.空气 过度系数a=1.8时,污染物在烟气中的浓度。
• 高位:包括燃料燃烧生成物中水蒸汽的汽化潜
热。
• 低位:指燃料燃烧生成物中水蒸汽仍以气态存
在时,完全燃烧释放的热量。
(2) 热损失
• 排烟热损失:热损失为6—12%: • 不完全燃烧热损失:化学不完全燃烧、机械不完全燃烧。 • 散热损失:由于设备管道温度高于周围空气温度造成热损失。
• 在充分混合的条件下,热损失在理论空气量条件下最低
化过程 ③烟煤 烟煤是炭化程度较高的煤,仅次于无烟煤。 ④无烟煤 无烟煤是含碳量最高、炭化时间最长的煤。(煤炭分类见表2-1)
(2)液体燃料 液体燃料包括石油及石油制品、煤炭加工制取的燃料油和生物液体燃料。
(3)气体燃料 由可燃气体组成燃料称为气体燃料。可分为天然气体燃料、工业生产过
程副产气体燃料和人造气体燃料等。
《清洁燃烧技术》PPT课 件
循环流行化床锅炉技术是近十几年来迅速发展的一项高效低污染清洁燃
洁净煤燃烧技术

沧州炼油厂熄灭火炬系统顺利通过集团公司验收1999年8月底沧州炼油厂顺利通过了集团公司熄灭火炬验收小组对我厂熄灭火炬系统和工作的全面检查和验收,达到了集团公司要求的熄灭火炬的标准。
为早日实现熄灭火炬,从1997年开始,沧州炼油厂就成立了由环保、生产、技术等职能部门参加、并由生产副厂长挂帅的熄灭火炬领导小组,制定了严格的监督、考核管理制度,研究制定了周密的熄灭火炬计划:包括系统瓦斯产需平衡、瓦斯系统优化操作、技术改造、系统量化管理等。
对各套生产装置和公用系统逐一分析研究,找出了影响熄灭火炬的包括催化重油掺炼比例过大、干气产率高、催化装置蝶阀关闭不严、瓦斯发电系统操作不够灵活等各方面原因,并分别制订出了整改措施。
尤其在瓦斯发电、发汽方面进行了技术改造,对消灭火炬起到了重要作用。
在运行管理方面,在彻底查清瓦斯用量的前提下制订出了高低压瓦斯的供需平衡方案和切实可行的运行管理规定,像调度油品一样调度瓦斯;组织技术攻关,解决了丙烷压缩机长周期运行、冬季管线积液影响正常操作和液化气排放瓦斯系统聚丙烯颗粒带入火炬等问题。
在硬件方面,新上自动点火系统,在排放压力和流量超过给定值时能够实现自动点火;在软件方面,对与排放火炬有关的一催化、二催化、气体分馏、聚丙烯、管网系统等全部制定了熄灭火炬的操作规程以及同经济责任制挂钩的奖惩办法。
环保处,综合管理处严格按照经济责任制考核办法对各相关单位进行考核。
经过努力,瓦斯产、存、用系统实现了规范管理,瓦斯利用率提高到98%以上,至1999年7月基本消灭了长明灯,继而通过了集团公司熄灭火炬的验收。
(以上由沧州炼油厂环保处沈志刚供稿)用磷石膏制新型墙体砖铜陵化学工业集团公司近日研制成功利用工业废渣磷石膏制新型建筑墙体砖技术。
这是该公司继利用磷石膏制建筑用石膏板、高水材料、水泥缓凝剂等产品之后取得的又一重大科研成果。
磷石膏是磷酸化工产品生产过程中产生的一种工业废渣。
据了解,目前我国现有大型磷酸二铵生产装置5套,生产能力达100万t a左右,磷石膏排放量约为300万t a。
洁净煤燃烧技术.

降低NOx生成与排放根本在于控制燃烧区域
的温度不能太高,但低温燃烧又影响煤粉的 燃烧率,协调好这两项技术的应用使之达到 综合最佳效果是目的,实际上就要求对煤粉 燃烧的全过程加以控制。既能够保证煤粉着 火的稳定性,又有较低的燃烧温度,同时有 足够长的并在一定温度下的燃烧时间保证燃 烬。
煤粉低尘燃烧技术
优点: 1、燃烧连续稳定、易于调节、燃烧气氛可控等,克服 了煤粉火焰含灰量高的缺点; 2、其火焰的洁净度高于水煤浆火焰,可与重油火焰相 媲美; 3、不须对煤进行特殊处理,只须将煤磨成煤粉,所要 求的煤粉平均粒径可以比一般煤粉燃烧炉要求的粗。 4、煤粉可通过管道进行气力输送,整个燃烧给煤系统 是封闭式的。现场没有一般燃煤窑炉附近煤尘飞扬 的缺点。
第一节 粉煤燃烧
粉煤粒径:50-100um 燃烧效率:96%-99.5% 粉煤燃烧过程:
1、粉煤气流着火 2、粉煤气流燃烧 3、粉煤气流燃尽 4、粉煤燃烧结渣
粉煤气流着火
粉煤炉安全经济运行的重要条件;
不同煤种具有不同的着火温度,见表9-1; 着火热:粉煤达到着火温度所需要的热量,
与着火温度、灰分、水分和一次风量有关; 着火热越小,着火越容易; 一次风量尽量小,满足挥发份烧尽即可; 一次风速率:r1=Vdaf/100 一次风温度:400℃左右
什么是洁净煤燃烧技术
洁净煤利用技术包括从煤炭开发到利 用的所有技术领域,其基本领域包括煤炭 加工、煤炭燃烧、煤炭转化、污染物及CO2 排放控制、固体废弃物处理和利用。 洁净煤燃烧技术是洁净煤利用技术中 的一个重要内容,旨在煤的燃烧过程中提 高效率、减少污染物排放,达到煤的高效、 清洁利用。
煤粉高效燃烧技术与低NOx燃烧技术
能源行业清洁煤技术改造方案
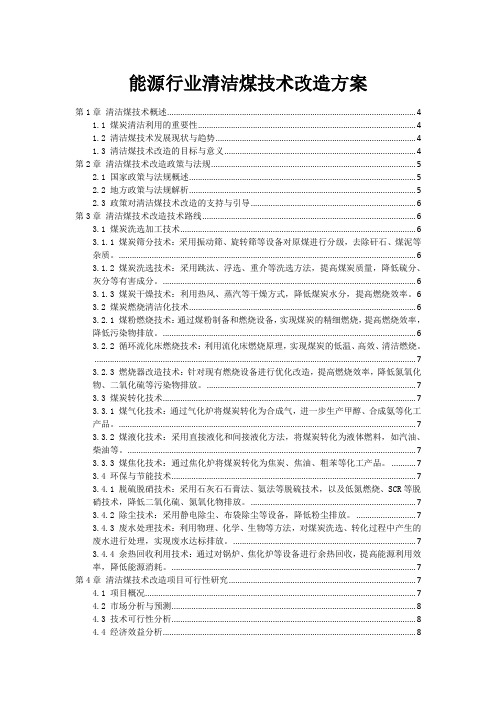
能源行业清洁煤技术改造方案第1章清洁煤技术概述 (4)1.1 煤炭清洁利用的重要性 (4)1.2 清洁煤技术发展现状与趋势 (4)1.3 清洁煤技术改造的目标与意义 (4)第2章清洁煤技术改造政策与法规 (5)2.1 国家政策与法规概述 (5)2.2 地方政策与法规解析 (5)2.3 政策对清洁煤技术改造的支持与引导 (6)第3章清洁煤技术改造技术路线 (6)3.1 煤炭洗选加工技术 (6)3.1.1 煤炭筛分技术:采用振动筛、旋转筛等设备对原煤进行分级,去除矸石、煤泥等杂质。
(6)3.1.2 煤炭洗选技术:采用跳汰、浮选、重介等洗选方法,提高煤炭质量,降低硫分、灰分等有害成分。
(6)3.1.3 煤炭干燥技术:利用热风、蒸汽等干燥方式,降低煤炭水分,提高燃烧效率。
63.2 煤炭燃烧清洁化技术 (6)3.2.1 煤粉燃烧技术:通过煤粉制备和燃烧设备,实现煤炭的精细燃烧,提高燃烧效率,降低污染物排放。
(6)3.2.2 循环流化床燃烧技术:利用流化床燃烧原理,实现煤炭的低温、高效、清洁燃烧。
(7)3.2.3 燃烧器改造技术:针对现有燃烧设备进行优化改造,提高燃烧效率,降低氮氧化物、二氧化硫等污染物排放。
(7)3.3 煤炭转化技术 (7)3.3.1 煤气化技术:通过气化炉将煤炭转化为合成气,进一步生产甲醇、合成氨等化工产品。
(7)3.3.2 煤液化技术:采用直接液化和间接液化方法,将煤炭转化为液体燃料,如汽油、柴油等。
(7)3.3.3 煤焦化技术:通过焦化炉将煤炭转化为焦炭、焦油、粗苯等化工产品。
(7)3.4 环保与节能技术 (7)3.4.1 脱硫脱硝技术:采用石灰石石膏法、氨法等脱硫技术,以及低氮燃烧、SCR等脱硝技术,降低二氧化硫、氮氧化物排放。
(7)3.4.2 除尘技术:采用静电除尘、布袋除尘等设备,降低粉尘排放。
(7)3.4.3 废水处理技术:利用物理、化学、生物等方法,对煤炭洗选、转化过程中产生的废水进行处理,实现废水达标排放。
煤清洁燃烧技术工艺流程

煤清洁燃烧技术工艺流程一、煤清洁燃烧技术的背景。
咱都知道,煤可是个重要的能源,工业生产、发电啥的都离不开它。
但是呢,传统的煤燃烧会带来好多问题。
比如说,会排放出大量的污染物,像二氧化硫、氮氧化物和颗粒物这些,这对环境可不好啦,空气变得脏脏的,还会影响我们的健康呢。
所以呀,煤清洁燃烧技术就应运而生啦。
这技术就像是给煤燃烧穿上了一件干净的衣服,让它在发挥能量的同时,尽量少地产生污染。
二、煤的预处理。
在煤进入燃烧环节之前,得先对它进行预处理。
这就好比给煤做个小小的美容。
有一种预处理方式是洗煤,就像给煤洗个澡一样。
把煤放在专门的洗煤设备里,用水或者其他溶液把煤里面的杂质,像灰分、硫分这些尽可能地去掉。
这样处理之后的煤呢,质量更好,燃烧的时候产生的污染物也会少一些。
还有一种是把煤加工成煤粉,把大块的煤磨得细细的,这样在燃烧的时候就更容易充分燃烧啦。
就像把食物切得碎碎的,更容易煮熟是一个道理呢。
三、燃烧环节。
说到燃烧环节呀,这里面的学问可大了。
有一种比较先进的燃烧技术叫循环流化床燃烧技术。
想象一下,煤在一个像大容器一样的床里面燃烧,这个床里还有很多像沙子一样的颗粒在不停地翻滚,就像在跳舞一样。
煤就在这些颗粒的陪伴下燃烧。
这种燃烧方式有个好处,就是燃烧的温度比较均匀,不会出现局部温度过高或者过低的情况。
而且呀,在燃烧过程中,还可以往里面加入一些石灰石,石灰石就像一个小卫士一样,它可以和煤燃烧产生的二氧化硫发生反应,把二氧化硫固定住,不让它跑到空气中去污染环境。
四、尾气处理。
煤燃烧完了之后,产生的尾气可不能就这么直接排出去。
这时候就需要进行尾气处理啦。
比如说,对于氮氧化物的处理,可以采用选择性催化还原法。
简单来说呢,就是在尾气通过的管道里,放上一些特殊的催化剂,然后再往里面喷入一些还原剂,就像给尾气做个小手术一样,让氮氧化物变成氮气和水,氮气可是空气里本来就有的成分,水也不会污染环境。
还有对于颗粒物的处理,可以用静电除尘器或者布袋除尘器。
煤的清洁燃烧技术

煤的先进清洁燃烧技术介绍【摘要】中国作为世界上最大的发展中国家,每年都需要燃烧大量的煤。
据可靠统计,2013年中国煤的燃烧量达到了36亿吨,比世界其他国家燃煤量的总和还要多。
大量煤的燃烧不仅使中国煤炭资源急剧减少,而且严重污染了大气环境,所以发展煤的清洁燃烧技术迫在眉睫。
本文从煤的污染物的产生原因和防止措施出发,详细介绍了当前比较先进的煤炭清洁燃烧技术。
【关键词】煤燃烧清洁一、引言燃烧是当今世界的主要能源来源,超过85%的全球一次能源消费都是由化石燃料的燃烧提供的。
然而,全球能源需求量的不断增长与有限的化石能源储量之间存在着严重的矛盾,从而引发了一系列政治、经济和社会问题;化石燃料燃烧所排放的大量颗粒物、二氧化碳、二氧化硫、氮氧化物等大气污染物还会影响环境安全和人类健康。
因此,如何实现高效清洁的燃烧已经成为包括我国在内的世界各国所面临的重大问题。
二、直接燃煤是我国城乡大气污染的主要原因由于传统的燃煤方式和煤炭加工过程中产生大量的污染物,必然会导致严重的大气污染、酸雨和水污染,甚至造成生态环境与自然植物的破坏,特别是以煤为主要能源的动力燃料的消耗。
每年我国电站锅炉、工业炉窑与工业锅炉,仅发电与其它工业耗煤就占了煤炭总消费量的2/3左右,而用于民用生活仅占1/10左右,用于城市供热的占不到1/20。
因此,长期以来我国在能源生产与消费中,以煤炭作为主要能源而直接燃烧,又正是造成我国严重大气污染的主要原因之一。
三、煤粉富氧燃烧技术燃烧中碳捕集即富氧燃烧技术,它是在现有电站锅炉系统基础上,用高纯度的氧气代替助燃空气,同时辅助以烟循环的燃烧技术,可获得高达富含80%体积浓度的C02烟气,从而以较小的代价冷凝压缩后实现C02的永久封存或资源化利用:具有相对成本低、易规模化、可改造存量机组等诸多优势,被认为是最可能大规模推广和商业化的CCUS技术之一。
其系统流程:由空气分离装置(ASU)制取的高纯度氧气(02纯度95%以上),按一定的比例与循环回来的部分锅炉尾部烟气混合,完成与常规空气燃烧方式类似的燃烧过程,锅炉尾部排出的具有高浓度C02的烟气产物,经烟气净化系统(FGCD)净化处理后,再进入压缩纯化装置(CPU),最终得到高纯度的液态C02,以备运输、利用和埋存。
读懂这些,秒变“煤粉清洁燃烧技术”专家
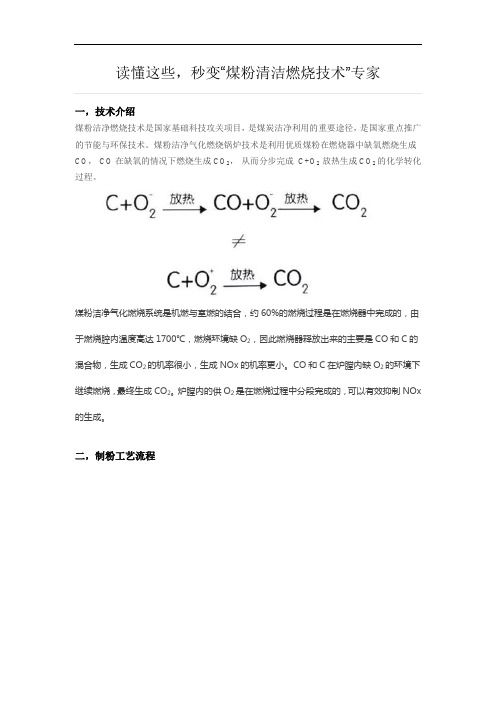
读懂这些,秒变“煤粉清洁燃烧技术”专家一,技术介绍煤粉洁净燃烧技术是国家基础科技攻关项目,是煤炭洁净利用的重要途径,是国家重点推广的节能与环保技术。
煤粉洁净气化燃烧锅炉技术是利用优质煤粉在燃烧器中缺氧燃烧生成CO,CO在缺氧的情况下燃烧生成CO2,从而分步完成C+O2放热生成CO2 的化学转化过程。
煤粉洁净气化燃烧系统是机燃与室燃的结合,约60%的燃烧过程是在燃烧器中完成的,由于燃烧腔内温度高达1700℃,燃烧环境缺O2,因此燃烧器释放出来的主要是CO和C的混合物,生成CO2的机率很小,生成NOx的机率更小。
CO和C在炉膛内缺O2的环境下继续燃烧,最终生成CO2。
炉膛内的供O2是在燃烧过程中分段完成的,可以有效抑制NOx的生成。
二,制粉工艺流程1燃烧技术燃烧技术采用机燃与室燃在缺O2条件下相结合完成燃烧过程的。
机燃过程:煤粉在缺氧条件下在燃烧器的燃烧腔内进行高温燃烧,在极短时间内完成干燥、气化、裂解、燃烧的全过程并产生CO,这一过程实现了大部分固体燃料向气体燃料的转化。
室燃过程:CO和部分C颗粒伴随高温烟气从锅炉顶部进入燃烧室,在分段风的辅助下完成燃烧全过程。
燃烧不完全的CO和C在燃烬室完成最终燃烧的过程。
分室燃烧技术可以使煤粉的燃烧效率>99%。
2锅炉技术锅炉结构采用国际上最先进的角管式全膜式水冷壁锅炉技术,燃烧器采用顶置式。
锅炉设有燃烧室和燃烬室两个燃烧空间,采取多点分段送风形式。
对流管束采用蛇形管对流受热面,中间预留SCR法脱硝空间。
为保证在变负荷情况下不影响脱硝烟气温度及防止对流受热面低温腐蚀,锅炉回水方式采用了模拟法分段回水技术。
热水锅炉无锅筒,水循环采用强制循环方式;蒸汽锅炉设置汽包,水循环采用自然循环方式。
通过科学设置炉膛结构及控制燃烧温度,实现固态排渣。
3环保技术煤粉洁净燃烧系统环保技术的核心是确保低硫煤在高温缺O2条件下完成分步燃烧。
在第一个燃烧过程,由于缺O2,C与O2反应只能生成CO,由于CO的活性比N2强,即使瞬间局部富氧,也只能生成CO2,而不能生成NOx。
煤炭资源的清洁燃烧与能效提升
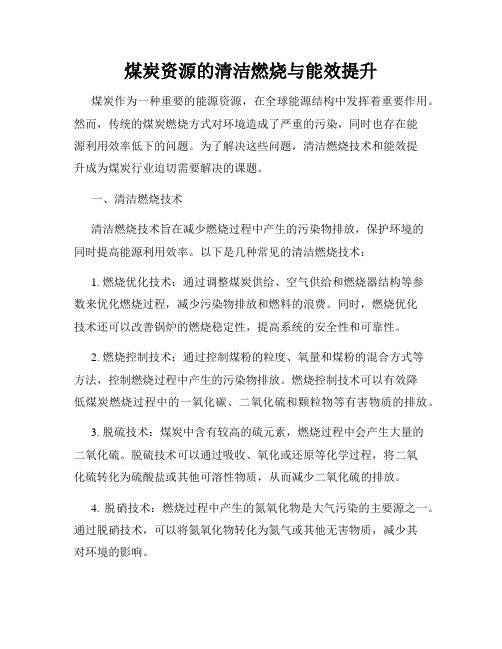
煤炭资源的清洁燃烧与能效提升煤炭作为一种重要的能源资源,在全球能源结构中发挥着重要作用。
然而,传统的煤炭燃烧方式对环境造成了严重的污染,同时也存在能源利用效率低下的问题。
为了解决这些问题,清洁燃烧技术和能效提升成为煤炭行业迫切需要解决的课题。
一、清洁燃烧技术清洁燃烧技术旨在减少燃烧过程中产生的污染物排放,保护环境的同时提高能源利用效率。
以下是几种常见的清洁燃烧技术:1. 燃烧优化技术:通过调整煤炭供给、空气供给和燃烧器结构等参数来优化燃烧过程,减少污染物排放和燃料的浪费。
同时,燃烧优化技术还可以改善锅炉的燃烧稳定性,提高系统的安全性和可靠性。
2. 燃烧控制技术:通过控制煤粉的粒度、氧量和煤粉的混合方式等方法,控制燃烧过程中产生的污染物排放。
燃烧控制技术可以有效降低煤炭燃烧过程中的一氧化碳、二氧化硫和颗粒物等有害物质的排放。
3. 脱硫技术:煤炭中含有较高的硫元素,燃烧过程中会产生大量的二氧化硫。
脱硫技术可以通过吸收、氧化或还原等化学过程,将二氧化硫转化为硫酸盐或其他可溶性物质,从而减少二氧化硫的排放。
4. 脱硝技术:燃烧过程中产生的氮氧化物是大气污染的主要源之一。
通过脱硝技术,可以将氮氧化物转化为氮气或其他无害物质,减少其对环境的影响。
二、能效提升提高能源利用效率是煤炭资源清洁燃烧的关键环节。
通过提升燃烧系统的能效,不仅可以减少煤炭资源的消耗,减少对环境的影响,还可以降低能源成本,提高能源利用效益。
以下是几种能效提升的方式:1. 高效锅炉技术:采用高效锅炉技术可以提高燃烧系统的热效率,减少能量的浪费。
高效锅炉通常采用先进的燃烧控制技术、余热回收技术和节能降耗设备等,使燃烧系统的能效得到大幅提升。
2. 能量管理系统:能量管理系统能够对燃烧系统进行全面的监控和调控,实现热力过程的优化。
通过对燃烧过程中能源的输入和输出进行精确计量和分析,找出能量消耗的瓶颈和浪费点,采取相应的措施进行节能改造,进一步提高能源的利用效率。
第六章燃烧设备和洁净煤燃烧技术

三次风对燃烧及汽温调节的不利影响: (1) 使火焰温度降低,燃烧不稳定。 (2) 火焰拖长,炉膛出口烟温升高,使过热汽温与再热汽 温偏高,汽温调节幅度增大。同时增大过热器热 偏差。 (3) 三次风高速射入,使火焰残余旋转增大,同时飞灰可 燃物增加; (4) 三次风量较大时,风速也增大,易扰乱炉正常的空气 流动,引起火焰贴墙结渣。
煤粉气流卷吸高温烟气而被加热的过程; 射流的相互撞击、射流两侧的补气及压力平衡过程; 煤粉气流的着火过程; 煤粉与二次风空气的混合过程; 四股气流形成的切圆旋转过程; 焦碳的燃尽过程。
2、“自点燃”作用
四、四角切圆燃烧的气流偏斜及切圆直径
1、气流偏斜问题
引起燃烧器出口气流偏斜的主要原因是: (1)邻角气流的撞击是气流偏斜的主要原因。 (2)射流偏斜还受射流两侧“补气”条件的影响。 (3)燃烧器的高宽比(hr/b)对射流弯曲变形影响较大。 (4)当燃烧器多层布置时,上层气流不断的被卷吸到下层气 流中,加上气流受热膨胀的影响,使气流容积流量增大, 旋涡直径相应增大,一般可使实际切圆直径膨胀到假想 切圆直径的8~10倍。
*燃烧器的作用
作用:将煤粉与空气混合气流按有利的方式送入炉膛,造成有利 的空气动力场,保证煤粉气流及时着火、强烈燃烧、洁净燃烧、 良好燃尽。 分类: 直流燃烧器 旋流燃烧器
第二节
直流式煤粉燃烧器
一、直流式煤粉燃烧器的特性
1.不旋转,射流扩展角小,卷吸能力小,单只燃烧器的着火性 能差,炉膛充满度差; 2.射流衰减慢,射程远,后期混合好,有利于煤粉燃尽; 3.采用四角布置,相互配合时,相互点燃,着火好,混合强烈; 4.多层布置(不少于三层)。
(3) 一次风集中布置的问题 着火区煤粉高度集中,可能造成着火区供氧不足,延 缓燃烧进程; 一次风喷嘴附近为高温区,喷嘴易变形,使喷嘴出口 附近气流速度分布不均,容易出现空气、煤粉分层现 象。
- 1、下载文档前请自行甄别文档内容的完整性,平台不提供额外的编辑、内容补充、找答案等附加服务。
- 2、"仅部分预览"的文档,不可在线预览部分如存在完整性等问题,可反馈申请退款(可完整预览的文档不适用该条件!)。
- 3、如文档侵犯您的权益,请联系客服反馈,我们会尽快为您处理(人工客服工作时间:9:00-18:30)。
清洁煤燃烧器的技术摘要循环流化床燃烧技术是国际80年代在锅炉上得到成功应用的清洁煤燃烧技术。
提高可靠性、经济性和文明生产程度贯穿了循环流化床燃烧技术的发展历史。
围绕分离器的形式和整体布置,循环床燃烧技术已经历了三代的发展,作者认为冷却型紧凑布置的循环床燃烧技术是未来的发展方向。
关键词循环流化床锅炉分离器发展方向引言循环流化床锅炉(CFB)燃烧技术是一项近20年来发展起来的燃煤技术。
它具有燃料适应性广、燃烧效率高、氮氧化物排放低、负荷调节比大和负荷调节快等突出优点。
自循环流化床燃烧技术出现以来,循环流化床锅炉已在世界范围内得到广泛的应用,大容量的循环流化床电站锅炉已被发电行业所接受。
世界上最大容量的250MW循环流化床锅炉已在1997年投运,多台200~250MW大容量循环流化床锅炉也已投产。
我国集中于中型CFB的研制与开发,目前已完全商业化。
到1998年底,我国已投运及订货的35t/h以下的循环流化床锅炉共计约600台,已开始走向电力市场,并且开始大型CFB的研制工作。
主循环回路是循环流化床锅炉的关键,其主要作用是将大量的高温固体物料从气流中分离出来,送回燃烧室,以维持燃烧室的稳定的流态化状态,保证燃料和脱硫剂多次循环、反复燃烧和反应,以提高燃烧效率和脱硫效率。
主循环回路不仅直接影响整个循环流化床锅炉的总体设计、系统布置,而且与其运行性能有直接关系。
分离器是主循环回路的主要部件,因而人们通常把分离器的形式,工作状态作为循环流化床锅炉的标志。
1 循环流化床的发展现状气固分离器是CFB系统的核心部件之一。
其之所以关键,从运行机理上来讲,只有当分离器完成了含尘气流的气固分离并连续地把收集下来的物料回送至炉膛,实现灰平衡及热平衡,才能保证炉内燃烧的稳定与高效;就系统结构而言,分离器设计、布置得是否合理直接关系着锅炉系统制造、安装、运行、维修等各方面的经济性与可靠性。
虽然分离器是CFB必不可少的关键环节,但它又具有相对的独立性和灵活性,在结构与布置上回旋余地很大。
从某种意义上讲,CFB锅炉燃烧技术的发展也取决于气固分离技术的发展,分离器设计上的差异标志着不同的CFB技术流派。
1.1 第一代循环流化床燃烧技术——绝热旋风分离循环流化床锅炉旋风分离器在化工、冶金等领域具有悠久的使用历史,是比较成熟的气固分离装置,因此在CFB领域应用最多。
德国Lurgi公司较早地开发出了采用保温、耐火及防磨材料砌装成筒身的高温绝热式旋风分离器的CFB锅炉[1]。
分离器入口烟温在850℃左右。
应用绝热旋风筒作为分离器的循环流化床锅炉称为第一代循环流化床锅炉,目前已经商业化。
Lurgi公司、Ahlstrom公司、以及由其技术转移的Stein、ABB-CE、AEE、EVT等公司设计制造的循环流化床锅炉均采用了此种形式。
这种分离器具有相当好的分离性能,使用这种分离器的循环流化床锅炉具有较高的性能。
据统计,目前除中国大陆外,有78%的CFB全部采用了高温绝热旋风分离器,但这种分离器也存在一些问题,主要是旋风筒体积庞大,因而钢耗较高,锅炉造价高,占地较大,旋风筒内衬厚、耐火材料及砌筑要求高、用量大、费用高,见图1;启动时间长、运行中易出现故障;密封和膨胀系统复杂;尤其是在燃用挥发份较低或活性较差的强后燃性煤种时,旋风筒内的燃烧导致分离后的物料温度上升,引起旋风筒内或回料腿回料阀内的超温结焦。
这些问题在我国的实际生产条件下显得更为突出。
Circofluid的中温分离技术在一定程度上缓解了高温旋风筒的问题,炉膛上部布置了较多数量的受热面,降低了旋风筒入口处的烟气温度和体积,旋风筒的体积和重量有所减小,因此相当程度上克服了绝热旋风筒技术的缺陷,使其运行可靠性提高,但炉膛上部布置有过热器和高温省煤器等,需要采用塔式布置,炉膛比较高,钢耗量大,使锅炉造价提高。
同时,它的CO排放及检修问题在一定程度上限制了该技术的发展。
1.2 第二代CFB燃烧技术——水(汽)冷分离循环流化床锅炉为保持绝热旋风筒循环流化床锅炉的优点,同时有效地克服该炉型的缺陷,Foster Wheeler公司设计出了堪称典范的水(汽)冷旋风分离器[2],其结构如图2。
应用水(汽)冷分离器的循环流化床锅炉被称为第二代循环流化床锅炉。
该分离器外壳由水冷或汽冷管弯制、焊装而成,取消绝热旋风筒的高温绝热层,代之以受热面制成的曲面及其内侧布满销钉涂一层较薄厚度的高温耐磨浇注料。
壳外侧覆以一定厚度的保温层,内侧只敷设一薄层防磨材料,见图3。
水(汽)冷旋风筒可吸收一部分热量,分离器内物料温度不会上升,甚至略有下降,较好地解决了旋风筒内侧防磨问题。
该公司投运的循环流化床锅炉从未发生回料系统结焦的问题,也未发生旋风筒内磨损问题,充分显示了其优越性。
这样,高温绝热型旋风分离循环床的优点得以继续发挥,缺点则基本被克服。
当然,任何一种设计都难以尽善尽美,FW式水(汽)冷旋风分离器的问题是制造工艺复杂,生产成本过高,缺乏市场竞争力,这使其商业竞争力下降,通用性和推广价值受到了限制[3]。
1.3 水冷方形分离器为克服汽冷旋风筒制造成本高的问题,芬兰Ahlstrom公司创造性地提出了Pyroflow Compact设计构想[4,5], Pyroflow Compact型循环流化床锅炉结构简图。
Pyroflow Compact循环床锅炉采用其独特专利技术的方形分离器,分离器的分离机理与圆形旋风筒本质上无差别,壳体仍采用FW式水(汽)冷管壁式,但因筒体为平面结构而别具一格。
这就是第三代循环流化床锅炉。
它与常规循环流化床锅炉的最大区别是采用了方形的气固分离装置,分离器的壁面作为炉膛壁面水循环系统的一部分,因此与炉膛之间免除热膨胀节。
同时方形分离器可紧贴炉膛布置从而使整个循环床锅炉的体积大为减少,布置显得十分紧凑。
此外,为防止磨损,方形分离器水冷表面敷设了一层薄的耐火层,这使得分离器起到传热表面的作用,并使锅炉启动和冷却速率加快。
从国内许多已投入运行的流化床锅炉来看,普遍都存在有床内的燃烧工况组织不好、床温偏高以及旋风分离器内CO和残碳后燃造成数十度甚至上百度温升的现象,加上流化床中的结焦温度比较低,因此结焦的可能在运行中始终是一个很大的隐患。
如果采用有冷却的旋风筒,分离器内的温度就可以得到控制,从而消除了结焦的危险。
水冷或汽冷的方形旋风分离器与不冷却的钢板卷成的旋风筒制造成本基本相当,考虑到前者所节省的大量的保温和耐火材料,最终的实际成本有所下降。
此外它还减少了散热损失,提高了锅炉效率。
另外由于保温厚度的减少,可以提高启停速度,启停过程中床料的温升速率不再取决于耐火材料,而主要取决于水循环的安全性,使得启停时间大大缩短。
以一台高温绝热旋风筒的75t/h锅炉为例,采用两根油枪床下点火,一般设计每小时耗油量为600kg左右,启动时间8h以上,如果将分离器做成汽冷或水冷,只要2~3h就足够了,这样每次启动都可以节省2~3t的轻柴油。
2 循环流化床锅炉的发展方向分析Ahlstrom公司的方形分离器紧凑型设计推出之后,立即引起了广泛的重视,人们对该技术一直持观望态度。
但经过5年的多台锅炉运行实践,已被人们所接受,其标志为:在1999年5月第15届国际流化床燃烧会议上,该专利持有人Timo荣获唯一的ASME贡献奖。
Foster wheeler公司和Ahlstrom公司合并后即将方形分离器循环流化床锅炉作为大型化方向予以重点发展。
时至今日,Foster Wheeler 公司采用方形分离器技术的紧凑型循环流化床锅炉已有68t/h至410t/h多台锅炉成功运行,150MW机组正在建设中,300MW和600MW 容量的紧凑布置CFB已经完成设计。
图5给出了方形分离器循环流化床锅炉单台容量的发展历史。
采用方形分离器的紧凑型布置循环床锅炉的市场份额逐年增加,该技术在Foster Wheeler的定单总数与其它形式的技术比较。
目前各循环流化床锅炉制造厂家和研究机构都十分重视循环流化床锅炉的大型化,方形分离器在大型化方面具有很大的优势。
1993年清华大学在实验室对国外方形分离器专利进行了验证实验,初步实验发现其分离效率并非如国外公司宣传的那么好,特别是在200~400mm的粒径范围存在一个低效区。
经分析表明这个低效区是由于分离器进口颗粒加速不良造成的,为此改进了入口段设计,实验表明此改进是完全正确的,这个改进最终取得了中国专利——“水冷异型分离器”。
为进一步优化分离器的效果和验证改进可靠性,在实验室冷态实验、热态实验的基础上应用到75t/h完善化循环流化床锅炉上,并取得成功。
该分离器是四周用膜式水冷壁组成的方形分离器,但烟气入口和水冷壁管弯制成圆弧形段,这一结构使分离器的造价降低,有效地克服了绝热旋风筒的后燃结焦问题和圆形汽(水)冷旋风筒的制造成本问题,被认为达到了90年代国际先进水平。
采用方形分离器的循环流化床锅炉市场发展情况。
清华大学等单位已对几种不同当量尺寸的方形分离器进行了一些卓有成效的试验和较为深入的研究,取得了许多有价值的结果[6]。
对这些成果进行较全面的分析、整理和比较,可以更多的了解方形分离器的放大性能,有助于开发研制大型化分离器和解决循环流化床锅炉大型化所面临的难题。
这些研究结果表明,方型分离器的放大性能要优于圆形旋风分离器,至少绝不逊于后者,特征尺寸在10m以内的方型分离器大型化的前景相当乐观[7]。
清华大学在该方面的研究成果得到国际同行的充分肯定和高度评价,在15届FBC国际会议上被评为最佳论文[8]。
采用方形分离器的220t/h、410t/h循环流化床锅炉设计已完成。
3 结论采用第三代技术的循环流化床锅炉除了具有常规循环流化床锅炉的优点外,还具有结构紧凑、占地面积小、钢耗量小、制造成本低、分离器内无磨损等突出优点,因此第三代循环流化床锅炉将成为燃烧技术发展的主流,并且在大型化方面将发挥其优势。