刀具材料与切削加工技术27~52W
数控刀具基础知识
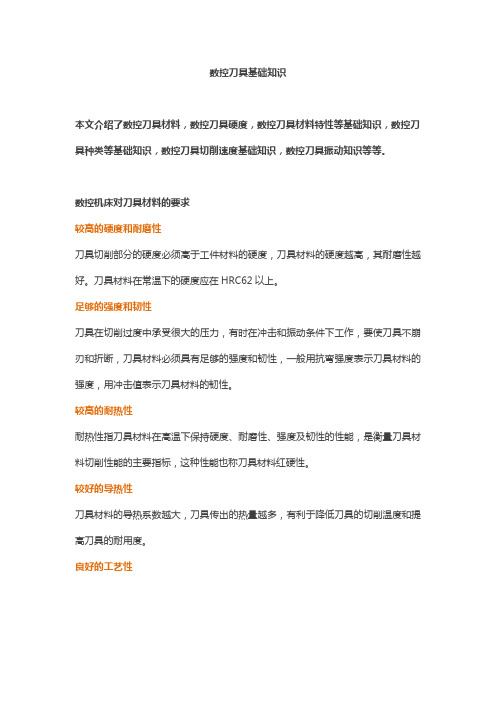
数控刀具基础知识本文介绍了数控刀具材料,数控刀具硬度,数控刀具材料特性等基础知识,数控刀具种类等基础知识,数控刀具切削速度基础知识,数控刀具振动知识等等。
数控机床对刀具材料的要求较高的硬度和耐磨性刀具切削部分的硬度必须高于工件材料的硬度,刀具材料的硬度越高,其耐磨性越好。
刀具材料在常温下的硬度应在HRC62以上。
足够的强度和韧性刀具在切削过度中承受很大的压力,有时在冲击和振动条件下工作,要使刀具不崩刃和折断,刀具材料必须具有足够的强度和韧性,一般用抗弯强度表示刀具材料的强度,用冲击值表示刀具材料的韧性。
较高的耐热性耐热性指刀具材料在高温下保持硬度、耐磨性、强度及韧性的性能,是衡量刀具材料切削性能的主要指标,这种性能也称刀具材料红硬性。
较好的导热性刀具材料的导热系数越大,刀具传出的热量越多,有利于降低刀具的切削温度和提高刀具的耐用度。
良好的工艺性为便于刀具的加工制造,要求刀具材料具有良好的工艺性能,如刀具材料的锻造、轧制、焊接、切削加工和可磨削性、热处理特性及高温塑性变形性能,对于硬质合金和陶瓷刀具材料还要求有良好的烧结与压力成形的性能。
刀具材料种类高速钢高速钢是由W、Cr、Mo等合金元素组成的合金工具钢,具有较高的热稳定性,较高的强度和韧性,并有一定的硬度和耐磨性,因而适合于加工有色金属和各种金属材料,又由于高速钢有很好的加工工艺性,适合制造复杂的成形刀具,特别是粉沬冶金高速钢,具有各向异性的机械性能,减少了淬火变形,适合于制造精密与复杂的成形刀具。
硬质合金硬质合金具有很高的硬度和耐磨性,切削性能比高速钢好,耐用度是高速钢的几倍至数十倍,但冲击韧性较差。
由于其切削性能优良,因此被广泛用作刀具材料。
切削刀具用硬质合金分类及标志涂层刀片1)CVD气相沉积法涂层涂层物质为TiC,使硬质合金刀具耐用度提高1-3倍。
涂层厚;刃口钝;利于提高速度寿命。
2)PVD物理气相沉积法涂层涂层物质为TiN、TiAlN和Ti(C,N),使硬质合金刀具耐用度提高2-10倍。
刀具材料
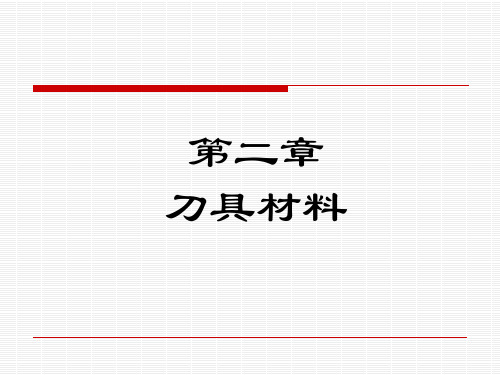
补充一些常用牌号: 高碳高速钢: W18Cr4V(9W18) , W6Mo5Cr4V2(CM2) 其碳的质量分数从普通高速钢的0.7%~0.8%增加 到0. 9%~l .0%,使常温硬度提高到66~68HRC, 600°c时高温硬度提高到51~52HRC。适用于耐磨 性要求高的铰刀、锪钻,丝锥以及加工较硬材料 (220~250HBS)的刀具。
含铝高速钢
铝高速钢W6M05cr4V2A1(简称501)和 W10M04Cr4V3Al(简称5F一6)是我国独创的新钢 种,这种钢常温硬度为67~69HRC,600°C高温 时硬度为54~55HRc,切削性能相当于钻高速钢 M42,刀具寿命比W18cr4V显著提高(至少1~2 倍),而价格却相差不多,用这种钢做的齿轮滚刀 允许l 67m/s的切削速度。
2、 高速钢
概念:高速钢是一种含钨(w)、钼(Mo)、铬(cr)、钒 (V)等合金元素较多的合金工具钢。 以重量计其碳的质量分数为0.7%~1.5%,铬 的质量分数约为4%,钨的质量分数和钼的质量分 数为10%~20%,钒的质量分数为1%~5%。 由于合金元素与碳化合形成较多的高硬度碳化 物,如碳化钒,硬度高达2800HV,且晶粒细小, 分布均匀。而且合金元素和碳原子结合力很强,提 高了马氏体受热时的稳定性。
高钒高速钢 W6Mo5Cr4V3、W12Cr4V4Mo 高钒高速钢质量分数在3%~5%,由于形成 大量高硬度耐磨的碳化钒弥散在钢中,提高 了高速钢的耐磨性,且能细化晶粒和降低钢 的过热敏感性。
3) 粉末冶金高速钢 是20世纪70年代开发的新型刀具材料, 其工艺方法是用高压惰性气体(氩气 或氮气)或高压水雾化高速钢水得到 细小的高速钢粉末,再经热压制成刀 具毛坯。
钴高速钢
M42(W2MO9Cr4VCO8) 和 W10MO4Cr4V3CO10
机加工常见材料加工参数
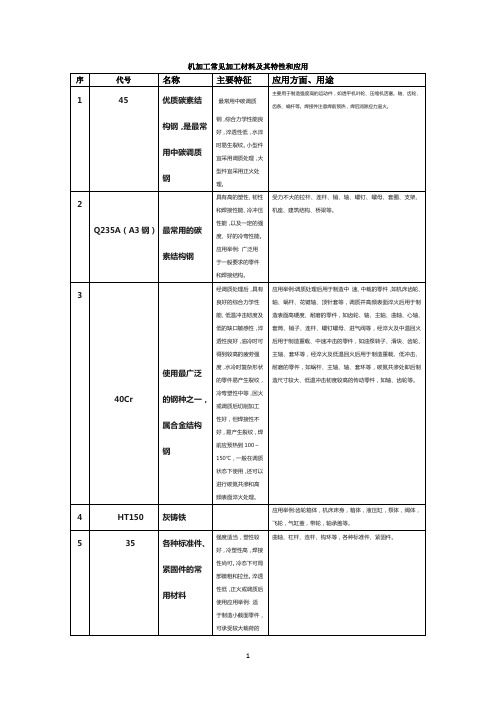
机加工常见加工材料及其特性和应用镜面抛光塑胶模具硬度HRC52。
21 H13 普通常用压铸模用于铝,锌,镁及合金压铸.热冲压模,铝挤压模,22 SKD61 高级压铸模日本日立株式产,经电碴重溶技术,在使用寿命上比H13有明显的提高. 热冲压模,铝挤压模, 23 8407 高级压铸模瑞典产. 热冲压模,铝挤压模。
24 FDAC 添加了硫加强其易削性出厂预硬硬度338-42HRC,可直接进行刻雕加工,无须淬火,回火处理用于小批量模,简易模,各种树脂制品,滑动零部件,交期短的模具零件.拉链模,眼镜框模。
25POM称赛钢,非标机械中最常用的材料该材料表面比较润滑,耐磨,使用温度在-40°至100℃中持续使用,加工尺寸较好,工精度在恒温下能保证在0.03mm以内,一般用于轻质化轴或齿轮等零件。
聚四氟乙烯是一种高分子材料。
很耐高低温,可达到-180℃至260℃,摩擦系数极低,与钢材料产生一般在机械设计中用于耐磨损零件,比如链条导轨,w型密封圈等。
26PTFE塑料王,特氟龙摩擦可达0.04,与滚动摩擦接近,也是世界上最耐腐蚀材料之一。
可以抵抗任何的有机溶物。
该材料较为软,不易加工易变形,无法加工高精度零件。
27尼龙尼龙用是非标机械中用的较为多的材料之一,该材料耐磨自润滑,可高温拍打润滑油,使其摩擦系数极低,该材料几何精度较高,可加工齿轮轴承等零件。
耐高温可达到160℃,持续使用,但在水中浸泡容易吸水膨胀导致精度影响。
28pvc聚乙烯该材料价格便宜使用特别广泛,也是非标机械常用的材料之一,PVC有防静电与不防静电的材料,在电子产品中,使用的皮如工装板等,该材料的熔点是75-90°在与食品接触时不能使用该产品,因为高温会释放致癌物质。
带就是防静电。
也有pvc 硬料与软料的区别,一般承受载荷的基本是硬料29 PU聚氨酯也称优力胶具有良好的耐油性、韧性、耐磨性、耐老化性和粘合性;具有塑料的刚性,又有橡胶的弹性。
刀具切削进给参数表
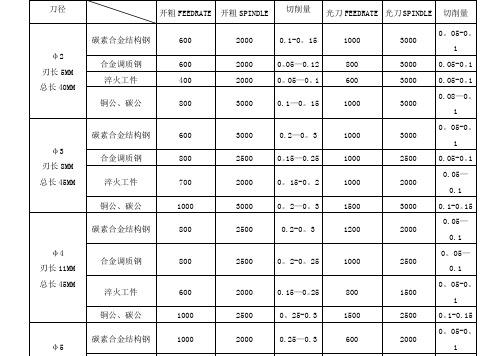
参数材料刀具切削进给参数表:
碳素合金结构钢(HRC<20) 合金调质钢(HRC30~40)淬火工件(HRC46~52) 1
碳素合金结构钢(HRC <20= 合金调质钢(HRC30~40) 淬火工件(HRC46~52) 2 碳素合金结构钢(HRC <20) 合金调质钢(HRC30~40) 淬火工件(HRC46~52) 3
材料
刀具切削进给参数表: 刀具切削进给参数表:
碳素合金结构钢(HRC<20=合金调质钢(HRC30~40) 淬火工件(HRC46~52) 4
刀具切削进给参数表:
碳素合金结构钢(HRC<20)合金调质钢(HRC30~40)淬火工件(HRC46~52) 5
刀具切削进给参数表:
碳素合金结构钢(HRC<20) 合金调质钢(HRC30~40) 淬火工件(HRC46~52) 6
刀具切削进给参数表:
碳素合金结构钢(HRC<20) 合金调质钢(HRC30~40)淬火工件(HRC46~52) 7
碳素合金结构钢(HRC <20)
合金调质钢(HRC30~40) 淬火工件(HRC46~52) 8 刀具切削进给参数表: 刀具切削进给参数表:
碳素合金结构钢(HRC<20) 合金调质钢(HRC30~40)淬火工件(HRC46~52) 9
碳素合金结构钢(HRC<20=合金调质钢(HRC30~40)淬火工件(HRC46~52) 10。
铣削不同材料的切削参数

合金铣刀 2(3刃) 3(3刃) 4(4刃) 5(4刃) 6(4刃) 45# 8(4刃) 10(4刃) 12(4刃) 16(4刃) 可转位铣刀 63R6(5刃) 0.60d0 0.8 237 1200 2500 0.4 0.5d0 0.5d0 0.5d0 0.5d0 0.75d0 0.75d0 0.75d0 0.75d0 0.75d0 0.1 0.2 0.3 0.3 0.4 0.5 0.6 0.8 1 19 24.5 30 35 38 45 50 57 60 3000 2600 2400 2200 2000 1800 1600 1500 1200 300 400 600 600 800 1000 1000 1200 1200 0.033 0.053 0.063 0.07 0.1 0.14 0.15 0.2 0.25 0.5d0 0.5d0 0.5d0 0.75d0 0.75d0 0.75d0 0.75d0 0.75d0 0.75d0 0.05 0.05 0.05 0.05 0.05 0.1 0.1 0.1 0.1 1 1.5 2 2.5 3 4 5 6 8 25 33 38 39 47 50 63 68 75 4000 3500 3000 2500 2500 2000 2000 1800 1500 300 400 400 500 500 500 600 720 600 0.025 0.04 0.033 0.05 0.05 0.06 0.075 0.1 0.1
刀径 加工材料 d0(mm) 4(4刃) 5(4刃) 6(4刃) 8(4刃) 10(4刃) 不锈钢 12(4刃) 16(4刃) 10R5(2刃) 6R3(2刃) 可转位铣刀 22R0.8(2刃)山特 0.75d0 20R5(2刃)山特 0.70d0 2.5 0.5 3 138 200 160 2000 3200 1600 600 1500 400 0.15 0.23 0.125 0.2 0.15 0.15 160 3000 1500 0.25 aw(mm) ap(mm) V(m/min) S(r/min) 0.5d0 0.5d0 0.75d0 0.75d0 0.75d0 0.75d0 0.75d0 0.5 0.8 1 1.5 2 2.5 3 38 39 38 38 47 45 50 3000 2500 2000 1500 1500 1200 1000 F(mm/min) 300 400 400 420 420 480 420 Fz(mm/z) 0.025 0.04 0.05 0.07 0.07 0.1 0.1 aw(mm) 0.5d0 0.75d0 0.75d0 0.75d0 0.75d0 0.75d0 0.75d0 0.2 0.2 粗铣(根据设备选择转速) 侧壁余量 (mm) 0.05 0.05 0.05 0.1 0.1 0.1 0.1 0.15 0.1 精铣A(根据具体要求可进行适当调整) ap(mm) 2 2.5 3 4 5 6 8 0.15 0.1 V(m/min) S(r/min) 38 39 47 50 56 56 75 94 57 3000 2500 2500 2000 1800 1500 1500 3000 3000 F(mm/min) 300 400 400 400 420 400 400 1500 1500 Fz(mm/z) 0.025 0.04 0.04 0.05 0.06 0.07 0.07 0.25 0.25
加工中心新刀具常用切削参数参照表1

刀具名称
φ16圆鼻刀 φ20圆鼻刀 φ25圆鼻刀 φ25圆鼻刀 φ40圆鼻刀 φ40圆鼻刀 φ63圆鼻刀 φ63圆鼻刀 φ25圆鼻刀 φ32圆鼻刀 φ40圆鼻刀
用途
精加工 精加工 粗加工 精加工 粗加工 精加工 粗加工 精加工 粗加工 粗加工 粗加工
转速 (r/min)
3300 3300 1800 3000 1500 3000 1300 2500 2000 3300 1800
进给量 (mm/min)
3800 3800 3800 3800 3800 3800 3800 3800 2500 3800 3800
切削深度 (mm) 0.1 0.1 0.6 0.3 0.8 0.3 1 0.3 0.5 0.6 0.6
切削宽度 (mm)
刀具材料
10 涂层合金
10
10
涂层合金
备注:此表仅供加工中心车间(使用新刀具时)参考
800
60
钻孔
800
20
扩孔
700
50
钻孔
400
60
钻孔
400
80
扩孔
120
40-50
精铰孔
120
40-50
精铰孔
高速钢 合金 高速钢 高速钢 高速钢 合金 焊刃
φ68-72/T型刀
8
120-140
10-20 粗铣T型槽
焊刃
40Cr/滑块 φ68-72/T型刀
8
120-150
20-30 半精铣T型槽
12
φ16高速钢立铣 3刃
400-600
50-70
16
16
高速钢
φ20高速钢立铣 3刃
300-400
切削力与切削功率

切削力与切削功率切削力与切削功率切削力与切削功率计算切削力及其分解、切削功率(1)切削力产生与切削力分解切削加工时,刀具作用下,被切削层金属、切屑和工件已加工表面金属都要产生弹性变形和塑性变形,这些变形所产生抗力分别作用前刀面和后刀面上:同时,切屑沿前刀面流出,刀具与工件之间有相对运动,还有摩擦力作用刀面和后刀面上。
这些作用刀具上合力就是总切削力F,简称切削力。
F受很多因素影响,,其大小和方向都是不固定。
便于分析切削力作用和测量切削力大小,常常将总切削力F分解为如图1-9所示三个互相垂直切削分力:1)切削力F c是总切削力主运动方向上分力。
,它垂直与基面,是切削力中最大一个切削分力。
其所消耗功率占总功率95%~99%。
它是计算机床动力,校核刀具、夹具强度与刚度主要依据之一。
2) 背向力F p是总切削力切削深度方向上分力。
它基面内,与进给运动方向垂直。
图1-9 切削力分解此力作用机床一夹具一工件一刀具系统刚度最弱方向上,容易引起振动与加工误差,它是设计和校验系统刚度和精度基本参数。
3) 进给力F f是总切削力进给运动方向上分力。
它基面内,与进给运动方向一致。
F f作用机床进给机构上,是计算和校验机床进给系统动力、强度及刚度主要依据之一。
由图1-9可知,总切削力F与三个切削分力之间关系为(1-1)(2)切削功率消耗切削过程中功率称为切削功率p m。
切削功率为切削力F c--和进给力F f所消耗功率之和,因背向力F p没有位移,不消耗功率。
切削功率(W)为(1-2)式中:F c—切削力(N)υc—切削速度(m/s)F f—进给力(N)υf—进给速度(mm/s)。
一般情况下,F f所消耗功率(约占p m1%~2%)远小于F c所消耗功率,,式(1-2)可简化为(1-3)按上式求P m后,如要计算机床电动机功率P E,还应将P m除以机床传动效率ηm(一般取ηm=0.75~0.85),即(1-4)2.切削分力经验公式目前,生产中计算切削分力经验公式可分为两类:一类是按单位切削力进行计算。
各材料常用刀具转速进给参数对照表

各材料常用刀具转速进给参数对照表在机械加工领域,刀具的转速和进给参数对于加工质量、效率和成本都有着至关重要的影响。
不同的材料具有不同的物理和机械性能,因此需要根据材料的特性来选择合适的刀具转速和进给参数。
下面是一份常见材料的刀具转速进给参数对照表,希望能为您的加工工作提供一些参考。
一、铝合金铝合金是一种广泛应用于航空航天、汽车制造和电子工业等领域的轻质材料。
由于其良好的导热性和较低的强度,加工时需要较高的转速和较快的进给速度。
1、粗加工刀具:硬质合金立铣刀转速:3000 5000 rpm进给速度:800 1500 mm/min切削深度:2 5 mm切削宽度:刀具直径的 70% 80%2、半精加工刀具:硬质合金立铣刀转速:5000 8000 rpm进给速度:500 1000 mm/min切削深度:05 15 mm切削宽度:刀具直径的 50% 60%3、精加工刀具:硬质合金球头铣刀转速:8000 12000 rpm进给速度:200 500 mm/min切削深度:01 03 mm切削宽度:刀具半径的 20% 30%二、钢材钢材是机械加工中最常见的材料之一,其种类繁多,性能各异。
以下是常见钢材的加工参数。
1、低碳钢粗加工刀具:硬质合金涂层立铣刀转速:1500 2500 rpm进给速度:300 600 mm/min切削深度:3 6 mm切削宽度:刀具直径的 60% 70%半精加工刀具:硬质合金涂层立铣刀转速:2500 4000 rpm进给速度:200 400 mm/min切削深度:1 2 mm切削宽度:刀具直径的 40% 50%精加工刀具:硬质合金涂层球头铣刀转速:4000 6000 rpm进给速度:100 200 mm/min切削深度:01 02 mm切削宽度:刀具半径的 15% 20% 2、中碳钢粗加工刀具:硬质合金涂层立铣刀转速:1000 1800 rpm进给速度:200 400 mm/min切削深度:2 4 mm切削宽度:刀具直径的 50% 60%半精加工刀具:硬质合金涂层立铣刀转速:1800 3000 rpm进给速度:150 300 mm/min切削深度:05 10 mm切削宽度:刀具直径的 30% 40%精加工刀具:硬质合金涂层球头铣刀转速:3000 5000 rpm进给速度:80 150 mm/min切削深度:005 015 mm切削宽度:刀具半径的 10% 15% 3、高碳钢粗加工刀具:硬质合金涂层立铣刀转速:800 1200 rpm进给速度:100 200 mm/min切削深度:1 3 mm切削宽度:刀具直径的 40% 50%半精加工刀具:硬质合金涂层立铣刀转速:1200 2000 rpm进给速度:80 150 mm/min切削深度:03 08 mm切削宽度:刀具直径的 20% 30%精加工刀具:硬质合金涂层球头铣刀转速:2000 3500 rpm进给速度:50 100 mm/min切削深度:003 008 mm切削宽度:刀具半径的 8% 12%三、不锈钢不锈钢具有良好的耐腐蚀性和耐磨性,但加工难度较大,需要较低的转速和较慢的进给速度。
切削加工技术综述

切削加工技术综述切削加工技术是一种通过物理力学原理和工具与工件之间的相对运动来改变工件形状和尺寸的方法。
它是制造业中最常用的一种加工方法,广泛应用于各个领域,如机械、汽车、航空航天等。
切削加工技术的基本原理是利用切削工具对工件进行削除材料的操作,以达到所需的形状和尺寸。
切削工具一般由硬质材料制成,如高速钢、硬质合金等,具有较高的硬度和耐磨性。
在切削加工过程中,切削工具与工件之间的相对运动产生剪切力,使工件表面的材料被削除,从而形成所需的形状。
切削加工技术包括多种方法,常见的有车削、铣削、钻削、刨削等。
车削是利用车床上的主轴和刀具对工件进行旋转切削的方法,常用于加工圆柱形工件。
铣削是通过铣床上的刀具进行旋转切削的方法,常用于加工平面和复杂曲面形状的工件。
钻削是利用钻床上的钻头对工件进行旋转切削的方法,常用于加工孔洞。
刨削是利用刨床上的刀具对工件进行直线切削的方法,常用于加工平面和棱角。
切削加工技术的优点是加工精度高、表面质量好、适用于各种材料和形状的工件。
然而,切削加工也存在一些限制和挑战。
首先,切削加工需要专业的设备和工具,成本较高。
其次,切削加工过程中产生的切屑和废料需要处理和清理,对环境造成一定影响。
此外,切削加工对工件的形状和尺寸有一定限制,无法加工过于复杂和小尺寸的工件。
随着科技的不断进步,切削加工技术也在不断发展。
近年来,随着数控技术的应用,切削加工实现了自动化和智能化,提高了加工效率和精度。
同时,切削工具的材料和结构也得到了改进和创新,提高了切削效果和工具寿命。
切削加工技术的发展为制造业的进步和发展提供了坚实的基础。
切削加工技术是一种重要的制造工艺,具有广泛的应用前景和发展空间。
随着科技的不断进步,切削加工技术将会更加高效、精确和智能化,为制造业的发展做出更大贡献。
同时,我们也需要不断学习和掌握新的切削加工技术,以适应市场需求和技术发展的变化。
高速钢铣刀切削用量选择表
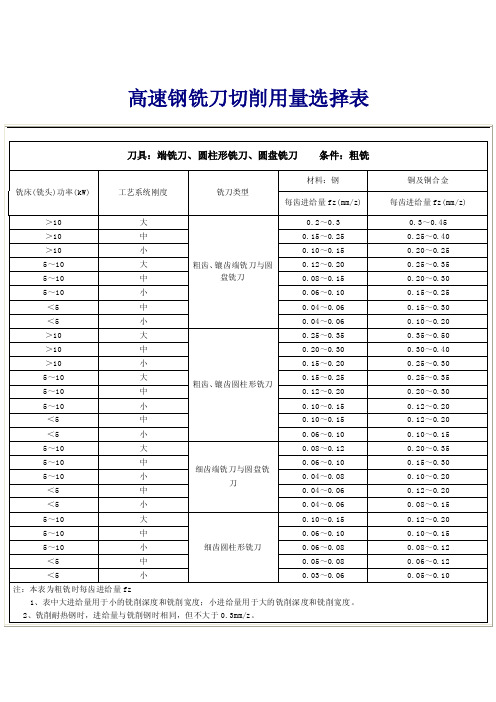
高速钢铣刀切削用量选择表刀具:端铣刀、圆柱形铣刀、圆盘铣刀条件:半精铣要求表面粗糙度Ra(μm)铣刀类型铣刀直径do(mm)加工材料进给量f(mm/r)6.3圆盘和镶齿端铣刀 1.2~2.73.2圆盘和镶齿端铣刀0.5~1.21.6圆盘和镶齿端铣刀0.23~0.53.2圆柱形铣刀40~80 1.0~2.71.6圆柱形铣刀40~80钢及铸铁0.6~1.53.2圆柱形铣刀100~125钢及铸铁 1.7~3.81.6圆柱形铣刀100~125钢及铸铁 1.0~2.13.2圆柱形铣刀160~250钢及铸铁 2.3~5.01.6圆柱形铣刀160~250钢及铸铁 1.3~2.83.2圆柱形铣刀40~80铸铁、铜及铝合金 1.0~2.31.6圆柱形铣刀40~80铸铁、铜及铝合金0.6~1.33.2圆柱形铣刀100~125铸铁、铜及铝合金 1.4~3.01.6圆柱形铣刀100~125铸铁、铜及铝合金0.8~1.73.2圆柱形铣刀160~250铸铁、铜及铝合金 1.9~3.71.6圆柱形铣刀160~250铸铁、铜及铝合金 1.1~2.1注:本表为半精铣时每转进给量f,使用圆柱形铣刀1、表中大进给量用于小的铣削深度和铣削宽度;小进给量用于大的铣削深度和铣削宽度。
2、铣削耐热钢时,进给量与铣削钢时相同,但不大于0.3mm/z。
刀具:立铣刀 条件:粗铣材料铣削平面及凸台铣削槽铣削深度(mm ) 铣削速度 v(m/min)铣刀直径d0 mm 每齿进给量af(mm/z) 铣削深度(mm ) 铣削速度 v(m/min)槽宽d0(mm) 每齿进给量fz(mm/z) 低碳钢HB:125~2250.5 52-64 10 0.025 0.75 30~34 10 0.025 1.5 38-49 10 0.05 3 29~32 10 0.038 d0/4 34-43 10 0.025 d0/2 26~29 10 0.018~0.025d0/2 20-37 10 0.018 d0 21~24 10 0.013 0.5 52-64 12 0.05 0.75 30~34 12 0.038 1.5 38-49 12 0.075 3 29~32 12 0.063 d0/4 34-43 12 0.05 d0/2 26~29 12 0.038 d0/2 20-37 12 0.025 d0 21~24 12 0.025 0.5 52-64 18 0.075-0.102 0.75 30~34 18 0.075 1.5 38-49 18 0.102-0.13 3 29~32 18 0.102 d0/4 34-43 18 0.075-0.102 d0/2 26~29 18 0.063 d0/2 20-37 18 0.05-0.075 d0 21~24 18 0.05 0.5 52-64 25~50 0.102-0.13 0.75 30~34 25~50 0.102 1.5 38-49 25~50 0.13-0.15 3 29~32 25~50 0.13 d0/4 34-43 25~50 0.102-0.13 d0/2 26~29 25~50 0.089 d0/2 20-37 25~50 0.075-0.102d0 21~24 25~50 0.075 中碳钢175~275 0.5 34-49 10 0.025 0.75 26~29 10 0.018 1.5 26-37 10 0.05 3 24~27 10 0.025 d0/4 23-32 10 0.025 d0/2 21~24 10 0.013 d0/2 20-27 10 0.018 d0 18~20 10 0.5 34-49 12 0.05 0.75 26~29 12 0.025-0.038 1.526-37 12 0.075 3 24~27 12 0.05-0.063 d0/4 23-32 12 0.05 d0/2 21~24 12 0.025 d0/2 20-27 12 0.025 d0 18~20 12 0.018 0.5 34-49 18 0.075 0.75 26~29 18 0.05-0.075 1.5 26-37 18 0.102 3 24~27 18 0.075-0.102d0/4 23-32 18 0.075 d0/2 21~24 18 0.05 d0/2 20-27 18 0.05 d0 18~20 18 0.038 0.5 34-49 25~50 0.102 0.75 26~29 25~50 0.075-0.102 1.5 26-37 25~50 0.13 3 24~27 25~50 0.102-0.13 d0/4 23-32 25~50 0.102 d0/2 21~24 25~50 0.075 d0/220-27 25~50 0.075 d0 18~20 25~50 0.063 高碳钢175~2750.5 32-46 10 0.025 0.75 24~27 10 0.018 1.524-34100.05323~26100.025d0/218-24100.018d017~18100.532-46120.050.7524~27120.0251.524-34120.075323~26120.05 d0/421-29120.05d0/220~23120.025 d0/218-24120.025d017~18120.0180.532-46180.0750.7524~27180.0631.524-34180.102323~26180.089 d0/421-29180.075d0/220~23180.05 d0/218-24180.05d017~18180.0380.532-4625~500.1020.7524~2725~500.0891.524-3425~500.13323~2625~500.102 d0/421-2925~500.102d0/220~2325~500.075 d0/218-2425~500.075d017~1825~500.063合金钢(低碳)125~2250.537-38100.0250.7527~30100.0251.527-29100.05326~29100.025 d0/424-26100.038d0/223~26100.018 d0/221-23100.025d018~21100.0130.537-38120.050.7527~30120.0381.527-29120.075326~29120.063 d0/424-26120.05d0/223~26120.038 d0/221-23120.038d018~21120.0250.537-38180.075-0.1020.7527~30180.0751.527-29180.102-0.13326~29180.102 d0/424-26180.075-0.102d0/223~26180.063 d0/221-23180.05-0.075d018~21180.050.537-3825~500.102-0.130.7527~3025~500.1021.527-2925~500.13-0.15326~2925~500.13 d0/424-2625~500.102-0.13d0/223~2625~500.089 d0/221-2325~500.075-0.102d018~2125~500.075合金钢(中碳)175~2750.530-37100.0250.7520~23100.0181.523-27100.05318~21100.025d0/420-24100.038d0/215~18100.013d0/218-21100.025d012~14100.530-37120.050.7520~23120.0381.523-27120.075318~21120.05d0/420-24120.05d0/215~18120.025d0/218-21120.038d012~14120.013-0.0180.530-37180.0750.7520~23180.05-0.0751.523-27180.102318~21180.075-0.102d0/2 18-21 18 0.05 d0 12~14 18 0.038 0.5 30-37 25~50 0.102 0.75 20~23 25~50 0.075-0.102 1.5 23-27 25~50 0.13 3 18~21 25~50 0.102-0.13 d0/4 20-24 25~50 0.102 d0/2 15~18 25~50 0.075 d0/2 18-21 25~50 0.075 d0 12~14 25~50 0.063 合金钢(高碳)175~275 0.5 30-34 10 0.025 0.75 18~20 10 0.018 1.5 23-26 10 0.05 3 17~18 10 0.025 d0/4 20-21 10 0.025 d0/2 14~15 10 0.013 d0/2 18 10 0.018 d0 12 10 0.5 30-34 12 0.05 0.75 18~20 12 0.038 1.5 23-26 12 0.075 3 17~18 12 0.05 d0/4 20-21 12 0.05 d0/2 14~15 12 0.025 d0/2 18 12 0.025 d0 12 12 0.018 0.5 30-34 18 0.075 0.75 18~20 18 0.05-0.075 1.5 23-26 18 0.102 3 17~18 18 0.075-0.102d0/4 20-21 18 0.075 d0/2 14~15 18 0.05 d0/2 18 18 0.05 d0 12 18 0.038 0.5 30-34 25~50 0.102 0.75 18~20 25~50 0.075-0.102 1.5 23-26 25~50 0.13 3 17~18 25~50 0.102-0.13 d0/4 20-21 25~50 0.102 d0/2 14~15 25~50 0.075 d0/2 18 25~50 0.075 d0 12 25~50 0.063 高强度钢225~350 0.5 18-26 10 0.018 0.75 15~18 10 0.013-0.018 1.5 14-20 10 0.025 3 14~17 10 0.018-0.025 d0/4 12--17 10 0.018 d0/2 12~14 10 0.013 d0/2 11--15 10 0.013 d0 11~12 10 0.5 18-26 12 0.038-0.05 0.75 15~18 12 0.025 1.5 14-20 12 0.05-0.075 3 14~17 12 0.038-0.05 d0/4 12--17 12 0.038-0.05 d0/2 12~14 12 0.025 d0/2 11--15 12 0.025-0.038 d0 11~12 12 0.013 0.5 18-26 18 0.075 0.75 15~18 18 0.05 1.5 14-20 18 0.102 3 14~17 18 0.075 d0/4 12--17 18 0.075 d0/2 12~14 18 0.038 d0/2 11--15 18 0.05 d0 11~12 18 0.025 0.5 18-26 25~50 0.102 0.75 15~18 25~50 0.075 1.5 14-20 25~50 0.13 3 14~17 25~50 0.102 d0/4 12--17 25~50 0.102 d0/2 12~14 25~50 0.063 d0/211--15 25~50 0.075 d0 11~12 25~50 0.05 高速钢200~2750.5 18-26 10 0.013-0.018 0.75 9~15 10 0.013 1.514-20100.018-0.02538~14100.018d0/211--15100.013d05~11100.518-26120.0250.759~15120.0381.514-20120.025-0.0538~14120.05d0/412--17120.013-0.025d0/26~12120.018-0.025 d0/211--15120.013d05~11120.0130.518-26180.038-0.050.759~15180.051.514-20180.038-0.07538~14180.075d0/412--17180.025-0.05d0/26~12180.038-0.05 d0/211--15180.013-0.025d05~11180.0250.518-2625~500.05-0.0750.759~1525~500.0751.514-2025~500.063-0.10238~1425~500.102d0/412--1725~500.05-0.075d0/26~1225~500.075d0/211--1525~500.025-0.05d05~1125~500.05工具钢150~2500.520-30100.013-0.0180.7512~17100.013-0.0181.515-23100.025311~15100.018d0/412--20100.013-0.018d0/29~12100.013d0/211--18100.013d08~9100.520-30120.0250.7512~17120.0381.515-23120.038-0.05311~15120.05d0/412--20120.025d0/29~12120.025-0.038 d0/211--18120.013d08~9120.013-0.0250.520-30180.038-0.050.7512~17180.051.515-23180.05-0.075311~15180.075d0/412--20180.038-0.05d0/29~12180.038-0.05 d0/211--18180.025d08~9180.025-0.050.520-3025~500.05-0.0750.7512~1725~500.075-0.1021.515-2325~500.075-0.102311~1525~500.102-0.13 d0/412--2025~500.05-0.075d0/29~1225~500.075-0.102 d0/211--1825~500.038-0.05d08~925~500.05-0.075不锈钢(奥氏体)135~2750.527-34100.0250.7512~18100.013-0.0181.520-24100.05311~17100.018-0.025 d0/417-21100.025d0/29~15100.013d0/215-18100.025d08~12100.527-34120.050.7512~18120.0251.520-24120.075311~17120.038-0.05 d0/417-21120.05d0/29~15120.025d0/215-18120.025-0.038d08~12120.0130.527-34180.1020.7512~18180.051.520-24180.13311~17180.063-0.075d0/2 15-18 18 0.075 d0 8~12 18 0.025 0.5 27-34 25~50 0.13 0.75 12~18 25~50 0.075 1.5 20-24 25~50 0.15 3 11~17 25~50 0.102 d0/4 17-21 25~50 0.13 d0/2 9~15 25~50 0.063-0.075 d0/2 15-18 25~50 0.102 d0 8~12 25~50 0.038-0.05 不锈钢(马氏体175~325 0.5 21-40 10 0.018-0.025 0.75 12~20 10 0.013 1.5 17-30 10 0.025-0.05 3 11~18 10 0.018 d0/4 14-27 10 0.018-0.025 d0/2 9~15 10 0.013 d0/2 12--23 10 0.013-0.025 d0 8~12 10 0.5 21-40 12 0.025-0.05 0.75 12~20 12 0.025-0.038 1.5 17-30 12 0.05-0.075 3 11~18 12 0.038-0.05 d0/4 14-27 12 0.025-0.05 d0/2 9~15 12 0.025-0.038 d0/2 12--23 12 0.018-0.025 d0 8~12 12 0.013 0.5 21-40 18 0.05-0.075 0.75 12~20 18 0.05 1.5 17-30 18 0.075-0.102 3 11~18 18 0.063-0.075 d0/4 14-27 18 0.05-0.075 d0/2 9~15 18 0.038-0.05 d0/2 12--23 18 0.038-0.05 d0 8~12 18 0.018-0.025 0.5 21-40 25~50 0.075-0.102 0.75 12~20 25~50 0.075 1.5 17-30 25~50 0.102-0.13 3 11~18 25~50 0.102 d0/4 14-27 25~50 0.075-0.102 d0/2 9~15 25~50 0.05-0.075 d0/2 12--23 25~50 0.063-0.075 d0 8~12 25~50 0.025-0.05 灰铸铁160~260 0.5 27-43 10 0.025 0.75 14~23 10 0.038 1.5 21-35 10 0.05 3 12~21 10 0.05 d0/4 18-29 10 0.038 d0/2 11~18 10 0.025-0.038 d0/2 15-24 10 0.025 d0 9~14 10 0.013-0.018 0.5 27-43 12 0.038-0.05 0.75 14~23 12 0.038-0.05 1.521-35 12 0.063-0.0753 12~21 12 0.05-0.075 d0/4 18-29 12 0.05 d0/2 11~18 12 0.038-0.05 d0/2 15-24 12 0.038 d0 9~14 12 0.025 0.5 27-43 18 0.05-0.102 0.75 14~23 18 0.05-0.102 1.5 21-35 18 0.075-0.13 3 12~21 18 0.075-0.13 d0/4 18-29 18 0.063-0.102 d0/2 11~18 18 0.05-0.075 d0/2 15-24 18 0.05-0.075 d0 9~14 18 0.036-0.05 0.5 27-43 25~50 0.075-0.15 0.75 14~23 25~50 0.075-0.13 1.5 21-35 25~50 0.102-0.18 3 12~21 25~50 0.102-0.15 d0/4 18-29 25~50 0.089-0.13 d0/2 11~18 25~50 0.075-0.13 d0/215-24 25~50 0.075-0.102 d0 9~14 25~50 0.05-0.102 可锻铸铁160~0.5 34-43 10 0.025 0.75 18~21 10 0.018 1.527-34100.05317~20100.025d0/218-24100.018d011~14100.0130.534-43120.050.7518~21120.0251.527-34120.075317~20120.038-0.05 d0/421-23120.05d0/214~17120.025d0/218-24120.025d011~14120.0180.534-43180.075-0.1020.7518~21180.05-0.0631.527-34180.102-0.13317~20180.063-0.075 d0/421-23180.075-0.102d0/214~17180.05d0/218-24180.05-0.075d011~14180.025-0.0380.534-4325~500.102-0.150.7518~2125~500.063-0.0751.527-3425~500.13-0.18317~2025~500.075-0.102 d0/421-2325~500.102-0.13d0/214~1725~500.063-0.075 d0/218-2425~500.075-0.102d011~1425~500.038-0.05铝合金30~1500.5245-305100.0750.75115~150100.0751.5185-245100.1023100~135100.102 d0/4150-185100.075d0/284~120100.075 d0/2120-150100.05d069~105100.050.5245-305120.1020.75115~150120.131.5185-245120.153100~135120.15 d0/4150-185120.102d0/284~120120.13 d0/2120-150120.075d069~105120.0750.5245-305180.130.75115~150180.151.5185-245180.23100~135180.2 d0/4150-185180.15d0/284~120180.15 d0/2120-150180.13d069~105180.130.5245-30525~500.180.75115~15025~500.251.5185-24525~500.253100~13525~500.3 d0/4150-18525~500.2d0/284~12025~500.2 d0/2120-15025~500.15d069~10525~500.15铜合金0.546-150100.025-0.050.7530~87100.025-0.051.538-120100.038-0.075326~79100.05-0.075 d0/430-105100.025-0.05d0/223~72100.025-0.05 d0/223-90100.018-0.038d020~64100.025-0.0380.546-150120.025-0.0750.7530~87120.051.538-120120.038-0.13326~79120.063-0.075 d0/430-105120.025-0.075d0/223~72120.038-0.05 d0/223-90120.018-0.075d020~64120.025-0.038 0.546-150180.102-0.130.7530~87180.0751.538-120180.13-0.2326~79180.102-0.13 d0/430-105180.075-0.103d0/223~72180.063-0.075 d0/223-90180.05-0.102d020~64180.050.546-15025~500.13-0.180.7530~8725~500.102-0.131.538-12025~500.18-0.25326~7925~500.13-0.18 d0/430-10525~500.102-0.15d0/223~7225~500.089-0.102 d0/223-9025~500.075-0.13d020~6425~500.063-0.075钛合金300~3500.515-34100.0250.7511~20100.018-0.0251.514-30100.035-0.0539~18100.018-0.025 d0/48--17100.025d0/28~15100.013-0.018d0/26--12100.018-0.025d06~12100.0130.515-34120.050.7511~20120.025-0.051.514-30120.07539~18120.025-0.05 d0/48--17120.038-0.05d0/28~15120.018-0.038 d0/26--12120.025-0.038d06~12120.013-0.0250.515-34180.1020.7511~20180.05-0.0751.514-30180.1339~18180.05-0.075 d0/48--17180.05-0.075d0/28~15180.05d0/26--12180.038-0.05d06~12180.0380.515-3425~500.102-0.130.7511~2025~500.075-0.1021.514-3025~500.13-0.1539~1825~500.075-0.102 d0/48--1725~500.075-0.13d0/28~1525~500.063-0.075 d0/26--1225~500.05-0.075d06~1225~500.05-0.075高温合金200~4750.53--12100.0250.75 2.1~1.6100.013-0.0181.52.4-9100.038-0.053 1.8~1.55100.013-0.025 d0/4 2.1-8100.025-0.038d0/2 1.5~510d0/22--6100.013-0.025d0100.53--12120.0250.75 2.1~1.6120.013-0.051.52.4-9120.038-0.053 1.8~1.55120.018-0.038 d0/4 2.1-8120.025-0.038d0/2 1.5~5120.018-0.025 d0/22--6120.018-0.025d0120.53--12180.038-0.050.75 2.1~1.6180.018-0.051.52.4-9180.05-0.0753 1.8~1.55180.025-0.075。
铣削不同材料的切削参数

33
3500
200
第 2 页,共 3 页
0.02
铣削不同材料的切削参数
加工材料
刀径 d0(mm) 4(4刃)
粗铣(根据设备选择转速)
aw(mm) ap(mm) V(m/min) S(r/min) F(mm/min)
0.5d0 0.5
38
3000
300
Fz(mm/z) 0.025
aw(mm) 0.5d0
6
150-188 4000-5000 1000-1500 0.06-0.075
0.75d0 2.5 200-251 4000-5000 4000 0.2-0.25 0.75d0 0.1-0.3
8
200-251 4000-5000 1000-1500 0.06-0.075
0.75d0 3 251-314 4000-5000 4000 0.2-0.25 0.75d0 0.1-0.3
铣削不同材料的切削参数
粗铣(根据设备选择转速) aw(mm) ap(mm) V(m/min) S(r/min) F(mm/min)
Fz(mm/z)
aw(mm)
精铣A(根据具体要求可进行适当调整)
侧壁余量 (mm)
ap(mm) V(m/min) S(r/min)
F(mm/min)
Fz(mm/z)
0.5d0 0.05 19-25 6000-8000 400-500
56
1500
400
16(4刃)
0.75d0 3
50
1000
420
0.1 0.75d0 0.1
8
75
1500
400
10R5(2刃)
0.2
0.15
金属切削加工基础课件

Kr’:使已加工表面残留密集的高度减小,降低工件 的表面粗糙度。
选择:在不产生振编动辑的版pp前t 提下,取小值。
22
5 . 刃倾角( S )
编辑版ppt
23
作用
①影响切削刃的锋利程度; ②影响切屑流出方向; ③影响刀头强度和散热条件; ④影响切削力的大小和方向。
选择: 精加工:取 正(+S )
介质: 5%
编辑版ppt
43
2.影响切削温度的因素
v ① 切削用量: c 、f 、a p愈大,切削温度愈高。但 vc的影响最大 、f 次之、a p最小。
② 工件材料:材料的强度、硬度越高,塑性、韧性越好, 切削温度越高。 刀具角度: 增大 0 ,切削温度降低;减小kr 、kr’,
③ 刀具 切削温度降低。
⑷ 硬质合金
碳化物+粘结剂——粉末冶金
碳化物:WC、TiC、等
粘结剂:Co
HRC≈76~84 耐热温度 —1000℃
允许的切削速度是高速钢的4~10倍。
编辑版ppt
27
① 钨钴类(YG)(K):WC+Co ② 钨钴钛类(YT)(P):WC+TiC+Co ③ 通用(YW)(M):TaC、NbC ④ 表面涂层: TiC、TiN、TiCN、TiAlN
0
0
编辑版ppt
19
选择: 加工塑性材料和精加工—取大后角( 0 ) 加工脆性材料和粗加工—取小后角( 0 )
后角( 0)只能是正的。
精加工: 0= 80~120 粗加工: 0= 40~80 3 . 主偏角(kr)
作用:改善切削条件,提高刀具寿命。
减小kr:当ap、f 不变时, 则 bD 、hD —
积屑瘤的形成
金属切削原理和刀具教学大纲

金属切削原理和刀具教学大纲一、引言金属切削是制造业中常见的一种加工方式,通过使用刀具对金属材料进行切削,实现对工件形状和尺寸的精确加工。
本教学大纲旨在介绍金属切削的基本原理和常用刀具的分类、特点及应用,以帮助学生全面理解金属切削加工的基本知识和技术。
二、金属切削原理1. 金属切削的定义和作用金属切削是指通过刀具对金属材料进行切削,以改变工件的形状和尺寸,达到加工要求的一种加工方法。
金属切削可以实现高效、精确和重复性加工,广泛应用于制造业各个领域。
2. 金属切削的基本原理金属切削的基本原理是通过刀具对金属材料施加切削力,使切削刃与工件接触并产生相对运动,从而移除工件上的金属层,实现加工目标。
切削过程中,刀具的切削刃与工件之间形成一定的切削角度,刀具在切削过程中产生切削力和切削热,同时也会产生切削振动和切削噪声。
3. 金属切削的影响因素金属切削的质量和效率受到多个因素的影响,包括切削速度、进给速度、切削深度、刀具材料和刀具几何形状等。
合理选择这些参数,可以提高切削效率和加工质量,减少切削力和切削热。
三、刀具分类及特点1. 刀具分类根据刀具的用途和结构特点,刀具可以分为以下几类:- 轴向刀具:如平面铣刀、立铣刀,用于平面加工和开槽加工。
- 径向刀具:如钻头、铰刀,用于孔加工和外圆加工。
- 侧面刀具:如刀片、车刀,用于车削加工和切槽加工。
- 特殊刀具:如刃磨刀具、切槽刀具,用于特殊形状的加工。
2. 刀具特点不同类型的刀具具有不同的特点和适用范围,主要包括以下几个方面:- 刀具材料:刀具材料应具有较高的硬度、耐磨性和热稳定性,常用材料有高速钢、硬质合金和陶瓷等。
- 刀具几何形状:刀具的几何形状包括刀片的前角、后角、刃倾角、切削角等参数,不同的形状适用于不同的切削任务。
- 刀具涂层:刀具涂层可以提高刀具的耐磨性和切削性能,常用涂层有涂层碳化物、涂层氮化物和涂层氧化物等。
四、刀具教学内容安排1. 金属切削原理的介绍- 金属切削的定义和作用- 金属切削的基本原理- 金属切削的影响因素2. 刀具分类及特点的讲解- 轴向刀具的分类和特点- 径向刀具的分类和特点- 侧面刀具的分类和特点- 特殊刀具的分类和特点3. 刀具选择和使用的技巧- 刀具选择的原则和方法- 刀具使用的注意事项- 刀具的保养和维护4. 刀具故障分析和排除- 常见刀具故障的原因和表现- 刀具故障的排查和排除方法- 刀具寿命的评估和提高方法五、教学方法和评价方式1. 教学方法本教学大纲推荐采用多种教学方法,包括理论讲解、实例演示、实验操作和案例分析等。
各材料常用刀具转速进给参数对照表

各材料常用刀具转速进给参数对照表在机械加工领域,刀具的转速和进给参数的选择对于加工质量、效率和刀具寿命都有着至关重要的影响。
不同的材料具有不同的物理和机械性能,因此需要相应的不同刀具转速和进给参数来实现最佳的加工效果。
下面我们将为您详细介绍一些常见材料的刀具转速进给参数对照。
一、钢材钢材是机械加工中最常见的材料之一,包括低碳钢、中碳钢和高碳钢等。
对于低碳钢,如 A3 钢,在使用硬质合金刀具进行粗加工时,转速一般可设置在 800 1200 转/分钟,进给速度为 02 03 毫米/转;而在进行精加工时,转速可提高到 1200 1800 转/分钟,进给速度则降低至 01 015 毫米/转。
中碳钢,例如 45 号钢,粗加工时转速通常在 600 1000 转/分钟,进给速度 015 025 毫米/转;精加工时,转速调整为 1000 1500 转/分钟,进给速度 008 012 毫米/转。
高碳钢由于硬度较高,加工时转速相对较低。
粗加工时转速约为400 800 转/分钟,进给速度 01 02 毫米/转;精加工时转速提升到 800 1200 转/分钟,进给速度为 005 01 毫米/转。
二、铝材铝材具有良好的导电性和导热性,相对较软,加工难度较低。
在使用高速钢刀具加工铝材时,粗加工转速可达到 1500 2000 转/分钟,进给速度 03 05 毫米/转;精加工时,转速进一步提高到 2000 3000 转/分钟,进给速度则减小至 01 02 毫米/转。
如果采用硬质合金刀具,粗加工转速能达到 2000 3000 转/分钟,进给速度 04 06 毫米/转;精加工时转速可高达 3000 5000 转/分钟,进给速度 01 02 毫米/转。
三、铜材铜材包括黄铜和紫铜等。
对于黄铜,在粗加工时,使用硬质合金刀具,转速可设定在 800 1500 转/分钟,进给速度 02 03 毫米/转;精加工时,转速提高到 1500 2500 转/分钟,进给速度降至 008 015 毫米/转。
钛合金材料及其加工刀具参数选择
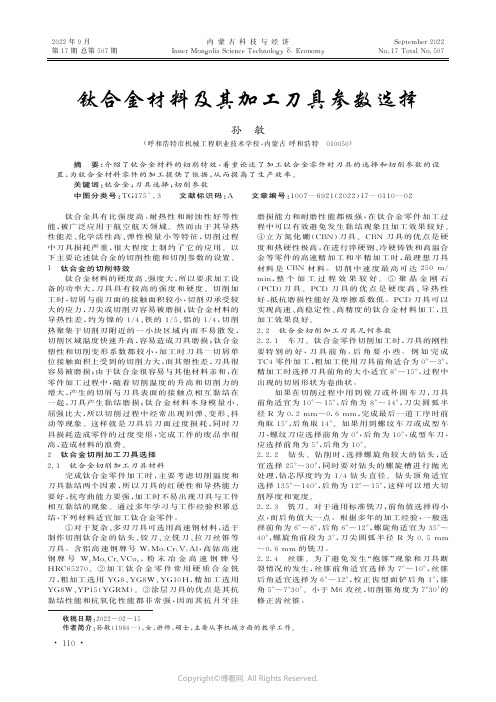
5 mm。
3
削 TC
根据 进 给 量 的 大 小 确 定 切 削 深 度 和 切 削
4 时,
速度,
见表 2,
表内个参数值均是工作中的经验值。
钛合金的切削用量
3.
1
3.
2
车削
用硬质合金 YG8 车 刀 加 工 表 面 被 氧 化 形 成 硬
膜的钛合金毛坯 件 时,粗 加 工 时,切 削 速 度、切 削 深
°~1
0
°,丝 锥
后角适宜选择为 6
°~1
2
°,校 正 齿 型 面 铲 后 角 1
°,锥
收稿日期:
2022-02-15
作者简介:孙敏(
1984—),女,讲师,硕士,主要从事机械方面的教学工作。
· 110 ·
Copyright©博看网. All Rights Reserved.
孙敏 · 钛合金材料及其加工刀具参数选择
1.
5~3
20~24
7~14
8~5
11~22
7~14
0.
08~0.
10
0.
10~0.
13
0.
10~0.
13
0.
06~0.
08
0.
07~0.
1
≤0.
6D
1.
5~6
钛合金工件进行攻丝时,
最 适 合 采 用 跳 牙 丝 锥,
0.
1
44
3
0.
2
30
0.
3
26
精铣
切削速度
/mm
每齿
进给量
/mm
轴向切深
/mm
30~45
动等现象。这样就 是 刀 具 后 刀 面 过 度 损 耗,同 时 刀
各材料常用刀具转速进给参数对照表

各材料常用刀具转速进给参数对照表一、铝合金铝合金是一种轻质、高强度且具有良好导热性的材料,常用于航空航天、汽车制造和电子设备等领域。
对于普通铝合金(如 6061、6063),在使用硬质合金刀具进行粗加工时,转速一般可设置在 1500 2500 转/分钟,进给速度约为 015 03 毫米/转。
而在进行精加工时,转速可提高到 3000 5000 转/分钟,进给速度降低至 005 015 毫米/转。
当使用涂层刀具时,由于其耐磨性更好,转速和进给速度可以适当提高。
粗加工时,转速可达 2000 3000 转/分钟,进给速度 02 04 毫米/转;精加工时,转速 4000 6000 转/分钟,进给速度 008 012 毫米/转。
二、铜合金铜合金具有良好的导电性、导热性和延展性,常见于电气、电子和模具制造等行业。
对于黄铜(如 H62),粗加工时,使用硬质合金刀具,转速约为800 1500 转/分钟,进给速度 01 02 毫米/转。
精加工时,转速提升到1500 2500 转/分钟,进给速度降至 005 01 毫米/转。
对于青铜(如 QSn65-01),由于其硬度相对较高,粗加工时,转速在 600 1200 转/分钟,进给速度 008 015 毫米/转;精加工时,转速1000 2000 转/分钟,进给速度 003 008 毫米/转。
三、碳钢碳钢是机械制造中应用最广泛的材料之一,其强度和硬度因含碳量的不同而有所差异。
对于低碳钢(如 A3 钢),使用硬质合金刀具进行粗加工,转速可设定在 800 1500 转/分钟,进给速度 015 03 毫米/转。
精加工时,转速提高到 1500 2500 转/分钟,进给速度减小为 008 015 毫米/转。
中碳钢(如 45 钢)在粗加工时,转速一般为 600 1200 转/分钟,进给速度 01 02 毫米/转;精加工时,转速 1000 1800 转/分钟,进给速度005 01 毫米/转。
切削力与切削功率

刀尖圆弧半径 λ∈ λ∈对 Fc 影响不大。λ∈增大时,Fp 将增大。
刀具材料
刀具与被加工材料间摩擦因数,直接影响着切削力大小。同样切削条件下,高速钢刀具切 削力最大,硬质合金次之,陶瓷刀具最小。
切削液 刀具磨损
切削液润滑性能越高,切削力降低越明显。
刀具后 刀面磨损后,接触摩擦增大,切削力增大:刀具前刀面上因磨损而形成月牙洼时, 增大了前角,切削力减小。
υc=1.83m/s(110m/min), ap=2~6mm,f=0.1~0.5mm/r
无卷屑槽
у0=20°κr =90°λs=0°byl= 0.15mm,y01=5°,前刀面上带
卷屑槽
υc=40m/min,ap=1~5mm,f= 0.1~0.4mm/r
注:1、切削各种钢,用 YT15刀片:切削不锈钢、各种铸铁与铜、铝,用 YG8或 YG6刀片: 用 YW2刀片。
影响切削力因素(见表1-2) 切削力测量
测量切削分力方法有两类:一类是间接测量法,例如把应变片贴滚动轴承外环上、用为移计测 量主轴或刀架变形量、测量驱动电动机耗电功率或转差率、测量静压轴承压力等,利用这些方 法便可间接测量切削力大小:另一类是直接测量法,主利用各种测力仪来进行测量。常用测量
仪是应变片式和压电式两种,其工作原理是利用切削力作用测力仪弹性元件上所产生变形,或 作用压电晶体上产生电荷转换后,来测量各切削分力。
刀具及切削原理
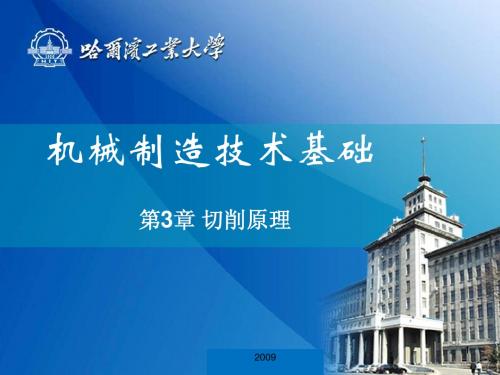
3.2.1切削力的产生与分解
2009
26
3.2.2切削力公式 根据力学知识有切削力理论公式为: 指数形式的切削力经验公式为: xFc yFc Fc c Fc P
F C a f v K Fc 式中 C 决定于被加工金属和切削条件的系数 Fc
xF
c
yF
c
F
c
分别
aP f
v
的指数
一般 Φ≈π/4 – β+γ0
2009
γ0↑
,Φ↑
12
3.1.5前刀面上的摩擦与积屑瘤
2009
13
3.1.5前刀面上刀-屑的摩擦与积屑瘤
积屑瘤
在速度不高切削塑性金属形成
带状切屑的情况下,滞流层金 属粘接在前刀面上,形成硬度
很高的硬块,称为积屑瘤。
积屑瘤对切削过程有什么 影响?是利是弊?如何控 制?
2009
40
3.3切削热与切削温度
切削热是切削过程中的重要物理现象之一。 切削温度的作用: 影响工件材料的性能 前刀面上的摩擦系数和切削力的大小; 影响刀具磨损和刀具使用寿命; 影响积屑瘤的产生和加工表面质量; 也影响工艺系统的热变形和加工精度。
2009
41
3.3.1切削热的产生与传出
33
3.2.3切削力的影响因素 切削力理论公式
由上式知:在切削面积一定的情况下,切削力大小取决于 工件材料的强度和硬度和切屑变形程度。工件材料强度和 硬度高-切削力大,但工件材料强度和硬度高-变形小。 所以工件材料强度和硬度越高,切削力越大。但不成正 比。 在同等强度与硬度情况下,材料的塑性越大,切削力越 大
2009 43
自然热电偶法
自然热电偶法测量切削温度示意图
各类钢制车刀的热处理工艺
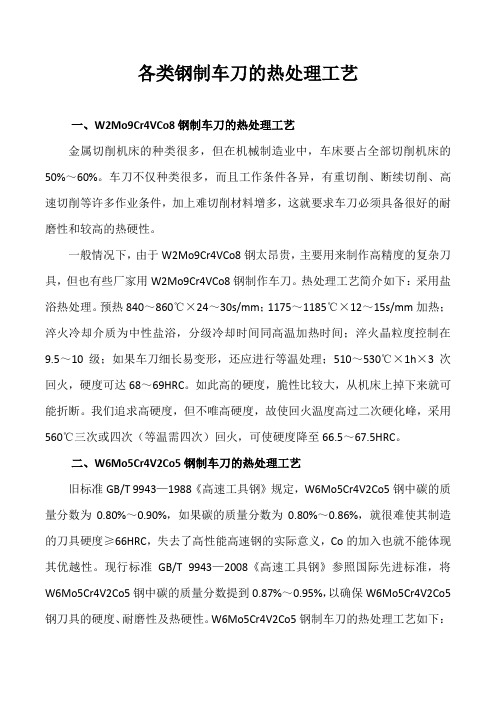
各类钢制车刀的热处理工艺一、W2Mo9Cr4VCo8钢制车刀的热处理工艺金属切削机床的种类很多,但在机械制造业中,车床要占全部切削机床的50%~60%。
车刀不仅种类很多,而且工作条件各异,有重切削、断续切削、高速切削等许多作业条件,加上难切削材料增多,这就要求车刀必须具备很好的耐磨性和较高的热硬性。
一般情况下,由于W2Mo9Cr4VCo8钢太昂贵,主要用来制作高精度的复杂刀具,但也有些厂家用W2Mo9Cr4VCo8钢制作车刀。
热处理工艺简介如下:采用盐浴热处理。
预热840~860℃×24~30s/mm;1175~1185℃×12~15s/mm加热;淬火冷却介质为中性盐浴,分级冷却时间同高温加热时间;淬火晶粒度控制在9.5~10级;如果车刀细长易变形,还应进行等温处理;510~530℃×1h×3次回火,硬度可达68~69HRC。
如此高的硬度,脆性比较大,从机床上掉下来就可能折断。
我们追求高硬度,但不唯高硬度,故使回火温度高过二次硬化峰,采用560℃三次或四次(等温需四次)回火,可使硬度降至66.5~67.5HRC。
二、W6Mo5Cr4V2Co5钢制车刀的热处理工艺旧标准GB/T 9943—1988《高速工具钢》规定,W6Mo5Cr4V2Co5钢中碳的质量分数为0.80%~0.90%,如果碳的质量分数为0.80%~0.86%,就很难使其制造的刀具硬度≥66HRC,失去了高性能高速钢的实际意义,Co的加入也就不能体现其优越性。
现行标准GB/T 9943—2008《高速工具钢》参照国际先进标准,将W6Mo5Cr4V2Co5钢中碳的质量分数提到0.87%~0.95%,以确保W6Mo5Cr4V2Co5钢刀具的硬度、耐磨性及热硬性。
W6Mo5Cr4V2Co5钢制车刀的热处理工艺如下:(1)预热840~860℃×24~30s/mm盐浴预热。
(2)加热1190~1210℃×12~15s/mm高温盐浴加热。
lnmu0303刀片切削参数

lnmu0303刀片切削参数摘要:1.刀片切削参数的概念和重要性2.刀片切削参数的分类3.刀片切削参数的选择与优化4.刀片切削参数对切削性能的影响5.结论正文:1.刀片切削参数的概念和重要性刀片切削参数是指在切削过程中,刀片与工件之间的各种物理量和几何参数。
这些参数对于切削过程的顺利进行和切削质量的保证具有重要意义。
合理的刀片切削参数可以提高生产效率、降低加工成本,同时保证产品的加工质量。
2.刀片切削参数的分类刀片切削参数主要分为以下几类:(1)切削速度:刀片在切削过程中的线速度,单位为米/分钟(m/min)。
(2)进给速度:刀片在切削过程中的线性进给速度,单位为米/分钟(m/min)。
(3)切削深度:刀片在切削过程中的最大切削深度,单位为米(mm)。
(4)刀片材料:刀片的材质,如高速钢、硬质合金等。
(5)刀片形状:刀片的几何形状,如平刀、球头刀等。
(6)刀片尺寸:刀片的尺寸,如直径、长度等。
3.刀片切削参数的选择与优化在选择和优化刀片切削参数时,需要考虑以下因素:(1)工件材料:不同材料的切削性能差异较大,需要根据具体材料选择合适的切削参数。
(2)工件形状和结构:复杂的形状和结构需要选用合适的刀片形状和尺寸。
(3)切削机床:切削机床的性能和稳定性影响切削参数的选择。
(4)刀片耐用性:在保证切削性能的同时,要考虑刀片的耐用性,以降低刀具磨损和更换成本。
4.刀片切削参数对切削性能的影响刀片切削参数对切削性能有重要影响,主要表现在以下几个方面:(1)切削速度:切削速度过快会导致刀片过热、磨损加剧,甚至出现断刀现象;切削速度过慢则会降低生产效率。
(2)进给速度:进给速度过快会导致刀片磨损加剧,降低刀具寿命;进给速度过慢则会降低生产效率。
(3)切削深度:切削深度过大会导致刀片承受的切削力增大,降低刀具寿命;切削深度过小则会降低生产效率。
(4)刀片材料和形状:不同的刀片材料和形状对切削性能有较大影响,需要根据具体情况选择合适的刀片。
- 1、下载文档前请自行甄别文档内容的完整性,平台不提供额外的编辑、内容补充、找答案等附加服务。
- 2、"仅部分预览"的文档,不可在线预览部分如存在完整性等问题,可反馈申请退款(可完整预览的文档不适用该条件!)。
- 3、如文档侵犯您的权益,请联系客服反馈,我们会尽快为您处理(人工客服工作时间:9:00-18:30)。
TH03
H1H2
KG03
K05
YD05
YS8
YD051
YG3X
YG3
YG610
YG643
作
业
ISO分类
分组代号
株洲钻石
自贡764
山特维克
肯纳公司
伊斯卡
公司
三菱公司
东芝公司
住友公司
山高公司
黛杰公司
车削
K
K10
YD15
YS8
YS10
YD201
YG6X
YG6A
ZK10UF
YG6X
YG6A
YG610
产地
牌号
对应于ISO
化学成分(%>
WC粒度um
物理机械性能
主要用途
WC
Co
TiC,TaC/NbC
密度(g/cm3>
硬度(HRA>
抗弯强度(N/mm2>
株硬型材
YU06
K05-K10
94.0
6
0.4
14.75
94.3
≥3000
加工铝镁合金及塑料,用于制作微型铣刀及铰刀。
YL10.2
K20-K30
89.5
H15
H25
CR1
KG20
N30
G13
THR
H25
KG30
S
S01
RT9005
KG03
S10
YS8
YD15
YT726
H10A
H10F
H13A
H10
K10
K313
THM
RT9005
RT9010
TH10
EH10
EH510
890
F205
KG10
S20
YT767
YT758
K715
KMF
RT9010
TF15
KS20
YW2
YW3
YS25
YS30
YW2
YW2A
YT798
K313
UTi20T
A30N
DX25
UMS
M30
YS25
YS30
YC30S
YC30T
SM30
KFM
K600
1C28
UTi20T
UX30
A30N
DX25
UMS
M40
YC40T
YC40
1C28
TU40
K
K01
YG3X
YD05
YG3X
YG610
HTi05T
YG643
H1P
H10
HM
K10
K313
KF1
KM1
K110
MTH
MTHM-U
1C20
HTi10
G1FTH10
EH10
EH510
890
KG10
KT9
CR1
K20
YG6
YG8N
YD15
YD201
ZK20UF
ZK20
YG6
YG813
H13A
K715
KMF
K600
1C20
1C10
UTi20T
G2F
G2K
S20
YG8
YDS15
YG6
YG643
YG813
K20UF
HM
KFM
1C20
1C10
UTi20T
G10E
HX
KT9
CR1
KG20
K30
YG8
YG8N
YDS15
YG8
YG813
2K30UF
1C10
1C28
UTi20T
KG30
注:上表摘自各公司样本和刊物,没有取得各公司的认可。
表3-2国内外部分硬质合金棒材性能及用途对照表
M
M10
YW1
YW3
YD201
YT726
YW1
ZM15
ZCP1F
YT767
H10A
K313
TU10
EH510
U10E
890
UMN
UM10
M20
YW2
YW3
YM20
YW2
YW2A
2CP1A
YG522
R1P
H13A
K68
KMF
K125M
TTM
1C08
UTi20T
TU20
EH520
U2
HX
883
DX25
UM20
EH20
EH520
890
883
HX
H25
F215
KG20
S30
G13
K600
THR
TF15
KG30
铣削
P
P10
YT15
YC10
YT15
S1P
SRT
P20
YT14
YC10
YS25
ZP25
YT798
YT14
SMA
K125
1C50M
1C28
UTi20T
TX25
A30N
SRT
DX30
作
业
ISO分类
分组代号
株洲钻石
自贡764
山特维克
肯纳公司
伊斯卡
公司
三菱公司
东芝公司
住友公司
山高公司
黛杰公司
铣削
P
P30
YT5
YS25
YC30S
YS30
ZP35
YT5
SM30
GX
K600
1C50M
1C28
UTi20T
UX30
A30N
SR30
DX30
P40
YC40
YT535
1C28
SR30
M
M10
YW1
YW3
YW1
K110M
UMN
M20
G10E
EH20
EH520
890
HX883
KT9
CR1
KG20
K30
YG8
YG8N
YS2T
YD201
ZK30UF
ZK30
YG8
THR
1C10
1C28
UTi20T
G3
G10E
883
KG30
N
N01
YD101
H10
H13A
K605
H1H2
KG03
N10
YD101
YS8
YS10
ZK10UF
K10
K313
KF1
KM1
K110M
THM
THM-U
HTi10
TH10
H10T
KS05F
EH10
EH510
890
H15
KC10
KT9
作
业
ISO分类
分组代号
株洲钻石
自贡764
山特维克
肯纳公司
伊斯卡
公司
三菱公司
东芝公司
住友公司
山高公司
黛杰公司
车削
N
N20
YD201
K715
KMF
K600
G10E
EH20
EH520
HX
KX
883
表1-3,五国十厂硬质合金刀具材料对照表
作
业
ISO分类
分组代号
株洲钻石
自贡764
山特维克
肯纳公司
伊斯卡
公司
三菱公司
东芝公司
住友公司
山高公司
黛杰公司
车削
P
P01
YN05
YT30
YT30
F02
SRN
P05
YN10
YT05
YC10
YT30
ZP01
S1P
P10
YT15
YC10
ZP10
YT715
YT15
S1P
UMS
M30
YM30
YC30T
YG813
ZM30
YG532
H10F
H20
H13A
SM30
K600
TTR
1C08
1C28
UTi20T
UX30
A30
A30N
DX25
UM30
UMS
M40
YC40T
YG640
S6R4
G13
1C28
TU40
UM40
K
K01
YG3
YG3X
YD05
YG3X
YG3
YG610
H1P
H605
P10
1C70
TX10S
ST10P
ST15E
SRT
P20
YT14
YC20.1
ZP20
YT14
YT758
YT798
SMA
S2
K125M
TTM
1C70
1C50M
UTi20T
TX20
TX25
ST20E
SRT
DX30
P30
YT5
YC30
YC35
YC40
ZP35
ZP30
YT730
YT535
YT5
S4
SM30
GK
KG03
K05
YD05
YD051
YG610
H1P
K10
YG6
YG6X
YD051
YG6
YG6X