电子教案与课件:《陶瓷工艺学》 6烧成
陶艺 陶瓷烧成课件
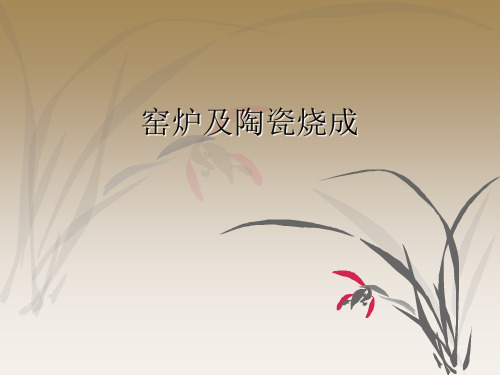
(2).龙窑——一般都是依山坡而建,坡的大 小缓急直接影响烧成时间和产量。
一般窑头坡度大,易上火,窑尾坡度小,易 存火,低的一端为火膛,高的一端有排烟 口。
龙窑的只要特点是升温快、降温也快,维持 火焰和还原时间长。使用的材料为松柴。
在我国南方比较多见。(如浙江龙泉、福建 德化、在景德镇的湖田也多出发现了龙 窑。)
一次烧成和二次烧成
一次烧成:是指经过成型、干燥或施釉后的 生坯,在烧成窑内一次烧成陶瓷产品的工艺 路线。 二次烧成:是指经过成型干燥的生坯,先在 素烧窑内进行第一次烧成(素烧)后的产品, 经拣选,施釉等工序后,再进行第二次烧成 (釉烧)的工艺路线。
设置烧制曲线
釉下烧成曲线
釉上烧成曲线
(三)升温曲线
使之变成“形如覆瓮”的蛋型, 所以也叫瓮形 窑或蛋形窑,景德镇人把这各独具地方特色, 独具技术优势的属于平焰式的窑叫镇窑。
电窑认识
以此款八边形顶 开盖窑炉为例。
此款窑为顶开 盖,小且轻便。 0.07立方、6kw、 220v、接线为4m ㎡以上的全铜 线。
窑炉结构
采用五层不同结构层完美结合。 最里层为高温砖,然后以高保温耐火棉保
150~500℃:坯体可快速升温,比较安全,失去结合 水,碳酸盐、黑云母的分解,气体很容易溢出。
500~700℃:较松散,石英在573℃有突变,膨胀系数 较大。
700~900℃:可快速加热坯体,比较安全,碳化物燃 烧成气体,并排出,坯体气孔增多,可不限制加热速 度,因为坯体很薄,可渗透性强。
• 900~1100℃:在烧成收缩很严重之前要减小制品间 的温差,在900度是升温较慢,盐酸盐分解许多气泡 在釉面玻化之前必须排出,快速升温会导致石膏混入 坯体或已干燥的可溶性盐类集中到一起,坯体炸裂。
陶瓷工艺学第十章烧成与窑具分析课件(1).ppt

(2) 充分利用原料资源 随着低温快速烧成的实现,大量的耐火度较低的
原料可以大量应用于陶瓷生产。如 硅灰石、透辉石、 霞石正长岩、含锂矿物以 及一些尾矿等劣质原料。 (3)减少窑具的使用量
隔焰、明焰辊道窑的使用大幅度减少了窑具的用 量, (4)缩短生产周期,提高生产效率 (5)低温快速烧成有利于色釉的显色,提高某些瓷 坯的强度。
线膨胀
热分析综合图谱
粘土
石英
ITE TE
长石
DTA
200
400 600 800 1000 1200 ℃
利用热分析综合图谱绘制理论烧成曲线
1400 1000
600 200
ITE
脆性生坯
热塑性范围
脆性瓷器
DTA
TE
-石英
脱OH
-石英 碳素燃烧
脱吸附水
时间
(2)烧结曲线(气孔率、烧成线收缩率、吸 水率及密度变化曲线)和高温物相分析, 是确定烧成温度的主要依据。
例如:(熟料)>(基质)
莫来石 堇青石
5.6
2×10-6
熟料表面基质切向受到压
应力,径向受到张应力。
压应力 张应 力
压应力
反之,基质切向受到张应力,产生微裂纹, 能够抑制裂纹的扩散
上述两种情况,控制得好都可以提高制品 的抗热震性能。
(3)重复使用时窑具的体积稳定性(不可逆变化)
※ 二次莫来石化引起体积膨胀
倒焰窑装窑示意图
(3)装隧道窑车特点 匣钵柱排列应当有利于窑内焰气有规律
流动;坯体大小、形状、厚度差别不能太大。
(4)无匣钵装烧 隧道窑
陶瓷工艺学第8章-烧成课件

第八章 烧 成
第三篇 陶瓷工艺学
2、分解反应 a. 结构水的分解、排除
坯料中各种粘土原料和其它含水矿物,在此阶段进行结构水 的排除,升温速度对脱除结构水有直接影响,快速升温时,结构
水的温度移向高温,而且比较集中。 b. 碳酸盐的分解 陶瓷坯体中含碳酸盐类物质,其分解温度一般<1050℃。 c. 硫酸盐的分解 陶瓷坯体中的硫酸盐,分解温度一般在650℃左右。
第八章 烧 成
第三篇 陶瓷工艺学
烧成 对陶瓷坯体按一定规律加热至高温,经过一系列物理化学
反应,然后再冷却至室温,坯体的矿物组成与显微结构发生 显著变化,外形尺寸固定,强度提高,最终成为人们预期的、 具有某种特定使用性能的陶瓷制品的过程。
烧结 是一种利用热能使粉末坯体致密化的技术。其具体的定义
是指多孔状陶瓷坯体在高温条件下,表面积减小、孔隙率降 低、机械性能提高的致密化过程。
第八章 烧 成
第三篇 陶瓷工艺学
3、石英的多晶转化和少量液相的生成 石英在配方中一般用量较多,本阶段将发生多晶转化。
573℃ ,β-石英转化为a-石英,伴随体积膨胀0.82%; 900 ℃附近,长石与石英,长石与分解后的粘土颗粒,在
接触位置处有共熔体的液滴生成。
本阶段发生的物理变化: 随着结构水和分解气体的排除, 坯体质量急速减少,密度减小,气孔增加。
第三篇 陶瓷工艺学
一次烧成的特点
1. 干生坯直接上釉,入窑烧成,工艺流程简化。 2. 劳动强度下降,操作人员减少,劳动生产率提高。 3. 由于减少了素烧窑、素检及其附属设施,占地面积小,基
建投资减少,烧成设备投资及占地可减少1/3~2/3。 4. 节约能源。因为只需烧成一次,燃料消耗和电耗下降。
我国生产的瓷器,除青瓷和薄胎瓷外,一般采用一次烧 成工艺。但在国外,瓷器绝大多数是二次烧成。
第七章 陶瓷工艺学 烧成

烧成时,氧化分解期要求强氧化气氛;玻化成瓷期,
要注意气氛转换温度。强氧化物 前150℃左右,强还原 强还原,釉始熔
铁少、有机物、碳素多用氧化气氛;南方瓷,还原气氛, 弱还原,1200℃左右。
3.压力制度: 影响窑内温度和气氛。 倒焰窑:窑底处于零压,窑内处于微正压,烟道 内微负压。 隧道窑:预热带负压(—29.4Pa),烧成带正压
按照一次烧成法进行烧成。世界各国硬质精
细日用白瓷多采用此法。
低温素烧、高温釉烧
有 高温素烧、低温釉烧
低温素烧即用低温700-960℃左右,将已经干 燥的生坯烧成,然后施釉,再入窑用高温烧成。如 有些薄胎瓷、艺术瓷、釉下彩绘的日用瓷等。 高温素烧是先将坯高温素烧(1260-1280℃), 再进行低温釉烧(950-1050℃),如一般精陶和英国 骨灰瓷等多采用此法。
第二节 坯体在烧成过程中的主要物理化学变化
一、低温阶段 (室温~300℃)
入窑水分低于5%以下,排除残余机械结合水和 吸附水,质量减轻,坯体体积收缩,坯体强度和气孔 率增加。
主要是物理变化,干燥过程的继续。使坯体入窑 水分降低,提高窑炉生产效率。一般隧道窑的坯体入 窑水分<1%,辊道窑0.5%以下。
(19.6~29.4Pa),冷却带正压(0~19.6Pa),零压
位在预热带与烧成带之间。
第四节
快速烧成
一、传统烧成制度周期长的原因
1. 坯釉反应需要一定的时间;
2. 外部原因:如窑炉温差大、装窑密度、燃料、窑 具性能等条件所限制。
二、快速烧成的意义 烧成周期10h以上为常规烧成;4~10h以内称为加 速烧成;4h以下为快速烧成。 1.节约能源(燃料) 2.充分利用原料资源 3.提高窑炉和窑具的使用寿命 4.缩短生产周期,提高生产效率
《陶瓷的烧成》课件

烧成的条件
1 温度
2 时间
烧成温度是决定陶瓷烧成质量的重要因素之一, 不同类型的陶瓷材料对应不同的烧成温度范围。
烧成时间取决于陶瓷材料的性质和尺寸,较小的 制品通常烧成时间较短,而较大的制品需要更长 的时间。
3 空气循环
4 烧成环境
适当的空气流动可以使烧成过程中产生的有害气 体逸散,同时促进陶瓷制品中的化学反应和结构 形成。
烧成失误与解决方法
1 烧结
2 烧焦
烧结是指陶瓷材料在烧成过程中出现的不完全烧 结现象,导致制品强度低、水分渗透等问题。解 决方法包括调整烧成温度和时间。
烧焦是指陶瓷制品在烧成过程中过烧,导致制品 表面出现焦痕和颜色异常等问题。解决方法包括 调整烧成温度、增加保护层等。
3 爆炸
4 解决方法
爆炸是指陶瓷制品在烧成过程中由于内部应力过 大而发生破裂。解决方法包括增加排气孔、减少 烧成温度梯度等。
《陶瓷的烧成》PPT课件
陶瓷的烧成是一门重要的工艺,它通过恰当的温度和时间控制,使陶瓷材料 获得理想的性能和装饰效果。
什么是陶瓷烧成
陶瓷烧成是指将陶瓷材料加热至充分成熟的过程,以使其变成瓷质体并获得所需的性能。 陶瓷烧成在制作陶瓷制品过程中发挥着关键作用,其主要目标是提高陶瓷的密度和硬度,并赋予其特殊的性质和装 饰效果。 根据烧成温度和时间的不同,陶瓷烧成可以分为低温烧成、中温烧成和高温烧成等不同的分类。
烧成过程
1
成型
2
将原料制备好的陶瓷糊料进行成型,可以通
过注塑、转盘成型、手工成型等方法实现。
3
烧成
4
将干燥后的陶瓷制品放入专用的烧成设备中, 按照一定的温度和时间条件进行加热烧结处
理,使其成为坚硬的瓷质体。
陶瓷工艺学PPT课件
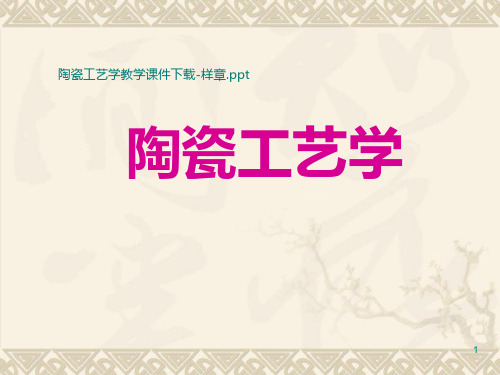
各窑代表产品的特点 官窑:北宋在河南开封,南宋在浙江临安(杭州)
主要为青釉瓷。 越窑:在浙江余姚,秘色瓷(青瓷)。 定窑:北定,河北曲阳,定州。南定,江西景德镇
白釉瓷 钧窑:河南禹县。钧红(铜红)釉,窑变花釉,其
特点,颜色不一,变化多,有千钧万变之说。 汝窑:河南临汝。青釉。属乳浊釉,无裂纹。色泽
二、普通陶瓷(不带釉)的岩相成分
是由晶相,玻璃相,气相构成的不均匀多相系统。 1、晶相:(以长石质瓷为例)莫来石,石英,方石英, 少量原料残骸,熟料粒。 2、玻璃相:25—70%(少数大于70%)
玻璃相少,只够粘接晶粒,胎体气孔多。[陶器] 3
玻璃相增多,除粘接晶粒外,还填充部分晶粒间隙,胎 体气孔减少。[不致密炻器]
9
一. 无釉陶器时期 (新石器时期 ---- 殷商 )
1. 我国最早的陶器:公元前8000年,江西万年仙人洞 出土的泥质陶,夹砂陶,夹炭陶。
这些陶器大部分为灰,红色。含Fe,Mn 等天然矿物, 起装饰作用,其烧成温度为800 c~1000 c。
2. 新石器时代晚期:彩陶,黑陶 彩陶代表“仰韶文化”,也称“彩陶文化”。最初
从出土的文物看:郑州二里冈出土商代一件豆青釉布纹
陶尊,内外施釉。洛阳出土西周灰青釉陶两件。战国时期有
胎质近瓷的带釉陶器。说明商周以来釉陶的出现和由陶到瓷
转变的萌芽。
随烧窑技术的发展,到两汉时期,有了早期的瓷器出现,
称为原始瓷。
河南板桥水库和洛阳有西汉四耳罐和盘的出土,河南信
阳东汉墓有青瓷壶,洗,碗等。此时的瓷器质地坚硬外施釉,
玻璃相很多,胎体几乎无气孔。[致密炻器,瓷器] 3、气孔
闭气孔:与大气不通,不吸水。 开气孔:与大气相通,吸水。气孔率越大,吸水越大。
郑州大学陶瓷工艺原理第六章t354页PPT

(5)大型产品的热压烧结温度要高些,保温时间要长些。
(6)冷却速度和材料的抗热震性及制品的大小、形状有关。
14.01.2020
国家精品课程——陶瓷工艺原理
14.01.2020
国家精品课程——陶瓷工艺原理
6.7.2.4 热压烧结的特点
1. 可降低坯体的成型压力 2. 可以显著提高坯体的致密度
14.01.2020
国家精品课程——陶瓷工艺原理
6.7.8 爆炸烧结(Explosion Sintering)
爆炸粉末烧结是利用 炸药爆轰产生的能量,以 冲击波的形式作用于金属 或非金属粉末,在瞬态、 高温、高压下发生烧结的 一种材料加工或合成的新 技术。
14.01.2020
国家精品课程——陶瓷工艺原理
(3)热压后期
外加压力作用已经很不明显,主要传质推动力与普通烧结相似。
14.01.2020
国家精品课程——陶瓷工艺原理
6.7.2.2 热压设备(热压机) 1 加热炉 热源:电
加热元件:SiC、MoSi2、镍铬丝、 白金丝、钼丝、导电的模具石墨等 2 加压装置 杠杆式压机、液压机
3 模具 要求:机械强度高;高温下能抗氧 化;热膨胀性接近于所热压的材料, 且二者之间不反应或粘结。
在微波烧结技术中使用的频率主要为915 MHz和2.45 GHz两种波段。
14.01.2020
国家精品课程——陶瓷工艺原理
6.7.5.1 微波烧结的优点 (1)微波与材料直接耦合导致整体加热。 (2)微波烧结升温速度快,烧结时间短。 (3)安全无污染。 (4)能实现空间选择性烧结。
14.01.2020
3. 可以显著降低烧成温度和缩短烧 成时间。 4. 可以有效地控制坯体的显微结构
陶瓷工艺学 电子教案[1]
![陶瓷工艺学 电子教案[1]](https://img.taocdn.com/s3/m/17285f62f121dd36a32d82ef.png)
陶瓷工艺学电子教案[1]《陶瓷工艺学》电子教案绪论陶瓷工艺学是无机非金属材料重要的专业课程,它以陶瓷材料的性质─结构─工艺之间的关系为纲,阐明材料的组成,键性,结构与性能的内在联系,讨论工艺方法对产品性能的影响。
将技术基础的有关原理与生产工艺,性能控制融合在一起。
因此,广义的陶瓷概念已延伸到无机非金属材料的概念范畴内。
此外,陶瓷作为中国古老文明与艺术的象征,使得日用瓷具有最广泛的实用性和欣赏性,也是陶瓷科学技术与工艺美术有机结合的产物,陶瓷从作为日用品开始,已逐步发展为国民经济领域中的重要材料。
陶瓷已从古老的艺术宫殿走出来,跨进了现代科学技术的行列之中。
璀璨的历史文明给我们留下了大量的陶瓷艺术珍品,这些历代名瓷或从造型,或从色彩,或从雕琢,从技术难度上创造了一个又一个的神奇,历久弥新,有强烈的视觉效果,能有效的调动学生的兴趣 ,在课程内容上,我们将另辟一章,结合专业知识着重介绍我国历代名瓷,不但可显著提高学生听课效果,而且符合当前在自然学科中加强人文修养的要求。
一、陶瓷的概念1、传统陶瓷:陶器,炻器,瓷器等以粘土为主要原料的制品的通称。
按吸水率分类2、现在陶瓷:无机非金属固体材料的通称。
从概念上可以看出陶瓷内涵的扩大二、陶瓷的发展史概述1、陶器的起源和演变2、由陶到瓷的发展3、我国历代瓷器的成就三、陶瓷在现代化建设中的作用四、现代陶瓷技术1、新技术与新工艺的采用:(1)原料制备:最初采用天然原料,不加任何处理。
现在为适应特殊材料的特殊要求,对原料进行精选,分等级处理,在纯度、粒度、性质等各方面加以控制。
(2)粉料制备:传统的半机械,机械球磨,兑打粉磨等粉碎方法。
现在为制备超细粉末,采用化学气(液)相沉淀,溶胶-凝胶法,气流粉碎,超声波粉碎等方法来制备(胶体颗粒10-7~10-9m)。
一些半干压成型的建筑陶瓷,铁氧体及电子陶瓷普遍地采用喷雾干燥法进行坯料加工和造粒。
在特种陶瓷粉末制备中将详细介绍如何用固、液、气相法合成超细粉末。
【大学课件】陶瓷工艺学ppt-精品文档

docin/sundae_meng
釉用原料 瘠性原料
电解质
塑性、半 塑性原料
球 磨 精 选 干 燥 称量配料 修坯及检查 过筛除铁 调制池 过筛除铁 调制桶 燃料 CMC 水
电解质
球 磨 过筛除铁 调浆池 压滤脱水 陈 腐 粗精练泥 成 型
水
施 釉 白坯检查 烧 成 白瓷检查 釉上装饰 釉、彩烧 彩瓷检查 包装入库 docin/sundae_meng 图1-1 日用陶瓷生产工艺流程
docin/sundae_meng
陶瓷制品种类繁多,目前国内外尚无统一的分类方法。较普遍 的分类方法有两种,一是根据陶瓷的概念和用途分类;二是根据陶 瓷的基本物理性能(如吸水率、透明性、色泽等)分类。 (1)按陶瓷的概念和用途分类 按这种分类方法可将陶瓷制品分为两大类,即普通陶瓷和特种 陶瓷。 普通陶瓷即传统陶瓷:根据传统陶瓷使用领域不同,又可分为 日用陶瓷、艺术陶瓷、建筑卫生陶瓷和工业陶瓷等。 日用陶瓷:如餐具、茶具、缸、坛、盆、罐等; 艺术陶瓷:如花瓶、雕塑品、陈设品等; 建筑卫生陶瓷:如卫生洁具、墙地砖、排水管等; 工业陶瓷:如化工用陶瓷、化学瓷、电瓷等。 特种陶瓷:分为高温结构陶瓷、功能陶瓷、生物陶瓷和原子能 陶瓷。高温结构陶瓷,如氧化铝陶瓷、氧化锆陶瓷、氮化硅陶瓷、 碳化硅陶瓷等;功能陶瓷,如敏感陶瓷、导电陶瓷、超导陶瓷、铁 电陶瓷等。
日用器皿、建筑外墙砖、 陈设品等 日用器皿、卫生洁具、 地砖、电瓷、化学瓷等
高频和超高频绝缘材料、 磁性材料、耐高温和高 强度材料、其它功能材 料等
1.2陶瓷工艺技术的内容及陶瓷生产工艺 陶瓷工艺技术的内容:包括由陶瓷原材料到制成陶瓷制品的整 个工艺过程中的技术及其基本原理。随着陶瓷生产技术的进步,陶 瓷工艺技术作为一门应用科学,也广泛汇集了生产经验和科学技术 理论,而逐步得到发展。 陶瓷制品的基本生产工艺过程有:原料选定(进厂)、配料、 坯釉料制备、成型、干燥、施釉、烧成等工序。 从整个陶瓷工业制造工艺技术的内容来分析,它的错综复杂与 牵涉之广,显然不是仅用无机化学的理论所能概括的。因此,学习 陶瓷工艺技术首先应学好基础科学和专业基础课程,广泛吸收新的 理论知识、新的科学技术和先进经验。同时更重要的是要重视在生 产一线的实习、实践环节。在学习陶瓷工艺技术前要通过参观认识 实习,对陶瓷生产工艺有一个基本认识。
《陶瓷制作工艺》课件

环保陶瓷
环保陶瓷如生物陶瓷、可降解陶瓷等,符合绿色环保理念,具有可持续发展的潜力。
陶瓷与金属的结合可以发挥各自的优势,如金属的强度和耐腐蚀性与陶瓷的耐磨性和耐高温性相结合,广泛应用于刀具、发动机部件等领域。
陶瓷与金属的结合
陶瓷与玻璃的结合可以创造出独特的艺术效果和功能性,如玻璃陶瓷、微晶玻璃等,在建筑、装饰和光学领域有广泛的应用。
陶瓷与玻璃的结合
陶瓷与塑料的结合可以使产品具有轻便、不易碎等特点,如陶瓷涂层塑料餐具、陶瓷增强塑料等,在日常生活和工业生产中得到广泛应用。
陶瓷与塑料的结合
05
陶瓷制作工艺的传承与保护
在家族中,父母将陶瓷制作技术传授给子女,代代相传。
家庭传承
徒弟跟随师傅学习,通过实践掌握陶瓷制作技艺。
师徒传承
一些民间组织或协会组织陶瓷制作技艺的传承活动,吸引年轻人参与。
上釉方法有多种,如浸釉、喷釉、刷釉等。不同的上釉方法适用于不同的陶瓷制品和釉料。在上釉过程中,需要注意控制釉料的浓度、涂覆量和涂覆次数等参数,以确保陶瓷制品表面的美观性和耐久性。
总结词
详细描述
总结词
烧成是将上釉后的陶瓷坯体在高温下烧结成瓷的过程。
详细描述
烧成是陶瓷制作工艺中的重要环节,需要在高温下进行长时间烧结,使陶瓷坯体中的水分、有机物和挥发物等充分排出,同时使釉料与坯体紧密结合在一起形成致密的瓷器。在烧成过程中,需要注意控制烧成温度、烧成时间和气氛等因素,以确保陶瓷制品的质量和性能符合要求。
总结词
配料过程中需要根据陶瓷种类和性能要求,选择合适的原料和添加剂,并按照一定比例混合,以获得所需的陶瓷材料。配料过程中需要注意原料的湿度、温度、粒度等参数,以确保配料的准确性和均匀性。
- 1、下载文档前请自行甄别文档内容的完整性,平台不提供额外的编辑、内容补充、找答案等附加服务。
- 2、"仅部分预览"的文档,不可在线预览部分如存在完整性等问题,可反馈申请退款(可完整预览的文档不适用该条件!)。
- 3、如文档侵犯您的权益,请联系客服反馈,我们会尽快为您处理(人工客服工作时间:9:00-18:30)。
r P ( 1 1 )
r1 r2
3、空位差:颗粒表面上的空位浓度与内部浓度之差
C
3 k T
C0
固相烧结 1.固相烧结现象 粉料经压制成为具有一定外形的坯体,含百分之几十的气
孔,颗粒间为点接触。 在高温的作用下发生了颗粒间接触面积的扩大,颗粒聚集,
体积收缩; 颗粒中心距离的逼近,逐渐形成晶界; 气孔形状变化,体积缩小,从连通的气孔逐渐变成孤立的气
6烧成
概述 烧成(sintering)是一种利用热能使粉末坯体致密化的技术。
其具体的定义是指多孔状陶瓷坯体在高温条件下,表面积减小、 孔隙率降低、机械性能提高的致密化过程。
烧成是陶瓷制造工艺中最重要的工序之一。陶瓷烧成所需 时间约占整个生产周期的1/3~1/4,所需费用约占产品成本的 40%左右。因此,正确的设计与选择窑炉,科学地制定和执行 烧成制度并进行严格的执行装烧操作规程,是提高产品质量和 降低燃料消耗的必要保证。
ln P1 M ( 1 1 ) P0 dRT x
x r
P1——曲率半径为ρ处的蒸气压; P0——球形颗粒表面的蒸气压; ——表面张力;d——密度; M——分子量; x——接触颈部半径; ρ ——颈部表面曲率半径
由上式说明,蒸发-凝聚传质产生的原因是曲率半径的差异;传质的条件是颗粒
尺寸足够小。
当压力差ΔP=P0-P1很小时,且x>>ρ,
对这类传质过程用延长时间不能达到促进烧结的结果。而应从原料的起始 粒度(r)和烧结温度(T)考虑。
x 0.3 r 0.2
0.1
0 10 20 30
时间(min)
NaCl在750 ℃时球形颗粒之间颈部生长
蒸发-凝聚传质的特点: 1、烧结时颈部区域扩大;颗粒形状改变;气孔形状改变;但颗粒间中心 距 不变,即坯体不收缩。 2、粉末的起始粒度越小,烧结速率越大;温度升高,蒸气压增大,对烧 结有利。 3、蒸发-凝聚传质的烧结过程,只有在高温下蒸气压较大的系统中才能明 显表现出来。一般蒸气压需在1~10Pa。例如SiO2,在7000K时蒸气压 0.1Pa;Al2O3在1200K时蒸气压10-41Pa。对于这些蒸气压低的系统,不适 合气相传质机理,而是扩散传质。
烧结开始阶段,在这种局部的应力和流体静压力影响下,颗粒 间出现重新排列,从而使坯体堆积密度提高,气孔率降低,坯体 出现收缩,但晶粒形状没有变化,颗粒重排不可能导致气孔完全 消除。
粒度为1m的材料烧结后,G降低约8.3J/g(无机材料等效于0.5 1.5 KJ/mol);
α-石英与β-石英之间的多晶转变时,G为1.7 KJ/mol; 一般化学反应前后能量变化超过200 KJ/mol。
烧结的难易可以用GB晶界能/SV表面能比值来衡量: GB/SV越大,烧结越困难
2、压力差:颗粒的弯曲表面上存在有压力差
孔,逐渐缩小,以至排除,最终成为致密体。
烧结现象示意图 a-晶粒重排; b1-疏松堆积的颗粒系 统中颗粒中心靠近; b2-紧密堆积的系统中, 颗粒中心的靠近。
固相烧结传质机理 (1)蒸发-凝聚
烧结时颈部区域的扩大,球的形状逐步变为椭圆,气孔形状发生了变化 两个球形颗粒中心间的距离不变。 不导致坯体的收缩和气孔率的降低
(2)扩散传质 在大多数固体材料中,由于高温下蒸气压低,则传质更易
通过固态内质点扩散过程来进行。
烧结的推动力是如何使质点在固态中发生迁移的呢?
1. 颈部应力模型 (假定晶体是各向同性的)。
在烧结前的粉末体如果是由同径颗粒堆积而成的理想紧密堆积,颗粒接触 点上最大压应力相当于外加一个静压力。在真实系统中,由于球体尺寸不一, 颈部形状不规则,堆积方式不相同等原因,使接触点上应力分布产生局部剪 应2RT
当凝聚速率等于颈部体积增加时即有:
Um——凝聚速率; a ——调节系数; ΔP——凹面与平面的蒸气 压之差
Um A dV
d
dt
由烧结模型,将颈部曲率半径ρ、表面积A和体积V代入上式,分离变量积分,得颈部 生长速率公式:
x Kr 2/ 3t1/ 3 r
烧结初期,接触颈部的增长x/r随时间t的1/3次方而变化。由图可见,颈部增 长(x/r)开始比较显著,随着烧结的进行,颈部增长速率减小直至停止。
球形颗粒间颈部长大改变气孔形状与中心距
在球形颗粒表面有一正曲率半径,在二个颗粒连接处有一小的负曲率半径 的颈部。
根据开尔文公式:
ln P 2M P0 dRTr
x r
凸表面蒸气压>平表面蒸气压>凹表面蒸气压 质点从凸表面蒸发向凹表面(颈部)迁移、凝 聚,使颈部逐渐被填充。
蒸发-凝聚传质
球形颗粒连接处曲率半径ρ和接触颈部半径x之间的开尔文公式:
目前我国日用陶瓷工业广泛采用隧道窑、辊道窑和推板窑,并 保留少量的倒焰窑继续用于生产。
烧结定义: 经过成型的粉末在加热到一定温度后开始收缩,在低于物质
熔点温度之下变成致密、坚硬烧结体的过程称为烧结。 烧结程度的衡量指标:
坯体收缩率、气孔率、吸水率 相对密度(烧结体密度/理论密度)
烧成与烧结的区别:
烧结:粉料经加热致密化的简单物理过程;宏观上出 现体积收缩、致密度提高和强度增加
烧成:脱水、坯体内气体分解、多相反应、溶解、烧 结等一系列过程。
烧成的含义和范围比烧结更宽,可以表述多相系统的 变化,烧结仅是其中的一个部分。
烧结和熔融的区别
烧结和熔融-原子热振动引起的。 熔融时全部组元都是液相, 烧结在远低于固态物质熔融温度进行,至少有一个组 元处于固态。
烧结温度TS和熔融温度Tm之间的关系: 金属粉末TS≈(0.3~0.4) Tm, 盐类TS≈0.57Tm, 硅酸盐TS ≈(0.3~0.4) Tm。
烧结的推动力
1、能量差 粉状物料的表面能大于多晶烧结体的晶界能,即能量差是烧结的推 动力,但较小。烧结不能自发进行,必须对粉料加以高温,才能促 使粉末体转变为烧结体。 例如:
上式为:P MP0 dRT
∵ lnP1/P0=ln(1+ ΔP/ P0) ≈ ΔP/ P0
ΔP——负曲率半径的颈部与接近于平面的颗粒表面上的饱和蒸气压之差。
蒸发-凝聚传质烧结初期动力学方程 (双球模型,中心距不变) 根据气体分子运动论,推出物质在单位面积上凝聚速率的朗格缪尔(Langmuir)公式: