冲压成形工艺流程及零件成形常见问题.pptx
冲压成形工艺流程及零件成形常见问题PPT文档36页
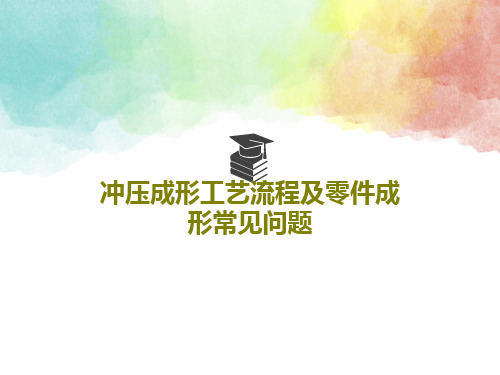
谢谢!
36
冲压成形工艺流程及零件成 形常见问题
26、机遇对于有准备的头脑有特别的 亲和力 。 27、自信是人格的核心。
28、目标的坚定是性格中最必要的力 量泉源 之一, 也是成 功的利 器之一 。没有 它,天 才也会 在矛盾 无定的 迷径中 ,徒劳 无功。- -查士 德斐尔 爵士。 29、困难就是机遇。--温斯顿.丘吉 尔。 30、我奋斗,所以我快乐。--格林斯 潘。
▪
26、要使整个人生都过得舒适、愉快,这是不可能的,因为人类必须具备一种能应付逆境的态度。——卢梭
▪
27、只有把抱怨环境的心情,化为上进的力量,才是成功的保证。——罗曼·罗兰
▪
28、知之者不如好之者,好之者不如乐之者。——孔子
▪
29、勇猛、大胆和坚定的决心能够抵得上武器的精良。——达·芬奇
冲压质量分析常见冲压质量问题及解决PPT模板
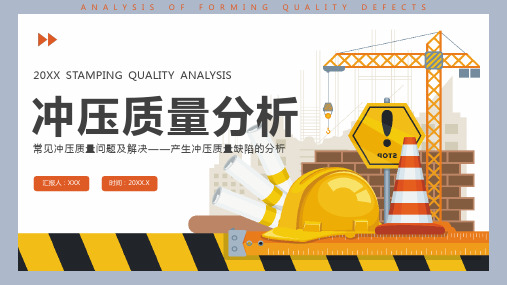
• 2.2.1制件的冲压工艺性差,冲压方向和压料面形状确定不当,很难控制材料的流动速度,引起皱纹。 • 2.2.2压料面的进料阻力太小,进料过多而起皱。这时可调节外滑块压力或改变拉深毛坯局部形状,增加压
料面积来消除,或局部增加拉深筋来增大进料阻力。 • 2.2.3压料面接触不好,严重时形成里松外紧。材料通过外紧区域后压料圈就失去压料作用,造成进料过多,
弯曲件的常见缺陷及原因分析
3、表面擦(拉)伤
表面擦伤的主要原因是模具工作部分选材不当,热 处理硬度低,凹模圆角磨损、光洁度差,弯曲毛坯 表面质量差(有锈、结疤等),材料厚度超差,工 艺方案选择不合理,缺少润滑等。
4、挠度和扭曲
ANALYSIS OF FORMING QUALITY DEFECTS
冲裁件的常见缺陷及原因分析
制件翘曲产生的原因
2.1、冲裁间隙大
间隙过大,则在冲裁过程中,制件的拉伸、弯曲力大,易产生翘曲。改善的办法可在冲裁时用凸模和压料板紧紧 地压住,以及保持锋利的刃口,都能受到良好的效果。
2.2、材料内部应力产生的翘曲
材料在轧制卷绕时产生的内部应力,在冲裁后移到表面,制件将出现翘曲。解决的方法时开卷时通过矫平机矫平。
均。因此,控制材料的流向及流速极为重要。 • 大型曲面制件的局部既易起皱,又易开裂。
大型曲面拉深件的常见缺陷及原因分析
1、大型曲面制件的拉深特点
1.2要有足够稳定的压边力 大型曲面制件不仅要求一定的拉深力,而且要求在其拉深过程中具有足够的稳定的压边力。 此类制件往往是轮廓尺寸较大,深度较深的空间曲面,所以需用变形力和压边力都较大。 在普通带气垫的单动压力机上,压边力只有名义吨位的1/6左右,而且压边力也不稳定,难以满足
板料冲压成形工艺课件
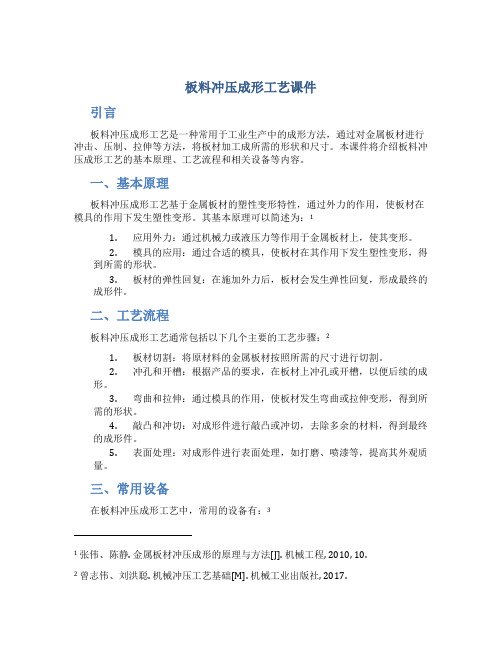
板料冲压成形工艺课件引言板料冲压成形工艺是一种常用于工业生产中的成形方法,通过对金属板材进行冲击、压制、拉伸等方法,将板材加工成所需的形状和尺寸。
本课件将介绍板料冲压成形工艺的基本原理、工艺流程和相关设备等内容。
一、基本原理板料冲压成形工艺基于金属板材的塑性变形特性,通过外力的作用,使板材在模具的作用下发生塑性变形。
其基本原理可以简述为:11.应用外力:通过机械力或液压力等作用于金属板材上,使其变形。
2.模具的应用:通过合适的模具,使板材在其作用下发生塑性变形,得到所需的形状。
3.板材的弹性回复:在施加外力后,板材会发生弹性回复,形成最终的成形件。
二、工艺流程板料冲压成形工艺通常包括以下几个主要的工艺步骤:21.板材切割:将原材料的金属板材按照所需的尺寸进行切割。
2.冲孔和开槽:根据产品的要求,在板材上冲孔或开槽,以便后续的成形。
3.弯曲和拉伸:通过模具的作用,使板材发生弯曲或拉伸变形,得到所需的形状。
4.敲凸和冲切:对成形件进行敲凸或冲切,去除多余的材料,得到最终的成形件。
5.表面处理:对成形件进行表面处理,如打磨、喷漆等,提高其外观质量。
三、常用设备在板料冲压成形工艺中,常用的设备有:31张伟、陈静. 金属板材冲压成形的原理与方法[J]. 机械工程, 2010, 10.2曾志伟、刘洪聪. 机械冲压工艺基础[M]. 机械工业出版社, 2017.1.冲床:用于施加冲击力和压力,将金属板材塑性变形。
2.模具:用于加工金属板材的工具,决定成形件的形状和尺寸。
3.剪切机:用于板材的切割,将金属板材按照所需尺寸进行切割。
4.折弯机:用于将金属板材进行弯曲,得到所需的形状。
5.敲料机:用于敲凸和冲切,去除多余的材料。
四、注意事项在进行板料冲压成形工艺时,需要注意以下几个事项:41.板材的选择:选择合适的板材材料和厚度,以满足产品的要求。
2.模具的设计:合理设计模具,确保成形件的质量和尺寸准确。
3.工艺参数的控制:控制冲床的冲击力、压力等工艺参数,以达到最佳的成形效果。
冲压零件常见缺陷分析PPT课件

A、提高压料力,调整拉延筋; Add the pressure of binder, adjust the draw bead,
B、工艺补充增加吸皱造型; Add shape of the suction in addendum
C、检查拉延毛坯、局部材料流动情况的合理性,调整压料面 Check material enter speed, adjust the binder.
• 材料堆集起皱。进入凹模腔内材料过多变成的皱纹。 Material gathered. The material enter dies too more caused the wrinkle
• 失稳起皱 Instability A.板料厚度方向增厚失稳。 Thickness direction less sanction force, increasation. B.拉伸应力不均匀而产生的皱纹。(例如:门把手区域) Strain asymmetrical (For example: Door handle area)
14
第14页/共40页
Cases anaylse
15
第15页/共40页
一、冲压负角(1) Undercut(1)
A
A
min3°
[SECTION A-A]
缺陷:在冲压方向有负角,如采用侧整形工艺, 增加大量模具成本。
Risk: Undercut in press direction, Use CAM-
9
第9页/共40页
回弹问题 Spring back
回弹 Spring back:零件在冲压成形后,材料由于弹性卸载,导致 局部或整体发生变形。 After form, uninstall the stress, parts deformed
冲压培训冲压工艺及缺陷分析ppt课件
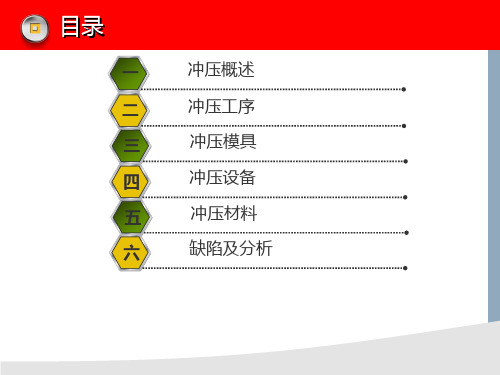
一、冲压概述
热成形工艺是将初始强度为500~600MPa 的钢板加热到奥氏体温度范围(850℃),然 后在压机上冲压成所需形状,同时以20~30 ℃ /秒的冷却速度进行淬火,保压一段时间以 保证充分淬透,最后零件随室温冷却,成形 后的零件的强度可以达到1500MPa左右。
落料
预成形
加热
成形
一、冲压概述
2. Байду номын сангаас压三要素
设备
冲压设备
• 机械压力机 • 液压机
冲压材料
• 板材 • 带材 • 管材及其他型材
材料
冲压零件
模具
冲压模具
• 冲压加工的主要工艺装备 • 冲压件质量与模具关系最大
冲压概述
3.冲压加工特点
• 产品尺寸稳定,重量轻,刚度好 • 表面质量和精度较好 • 操作简单,易于实现自动化 • 生产效率高 • 适于大批量生产 • 大批量生产时加工费用较低 • 依赖设备与模具 • 投产周期较长,初始投入大
2.3整形
为了提高已成形零件的尺寸精度或获得小的圆角半径而采 用的成形方法。
二、冲压工序
2.4翻孔
在预先冲孔的板料或半成品上或未经冲孔的板料制成竖立 的边缘。
二、冲压工序
2.5弯曲
把板料沿直线弯成各种形状,可以加工形状极为复杂的零 件。
二、冲压工序
3.冲压工艺流程图
二、冲压工序
冲压工艺流程图示例-F6左侧围外板
高的塑性应变比r值(各向异性性能); 高的加工硬化指数n值; 高的延伸率δ; 低的屈强比(σs/σb); 低的时效指数。
五、冲压材料
1.2良好的表面质量 钢板表面不得有结疤、裂纹、夹杂和划痕等明显缺陷。其 中车身内板允许存在不影响成型性及涂漆附着力的缺陷, 如小气泡、小划痕、小辊印、轻微的刮伤及轻微氧化色等; 外板须符合FD(O5)的质量级别即两面中较好的一面不得 有任何缺欠,即不能影响涂漆后的外观质量或电镀后的外 观质量,另一面应达到FB(O3)的要求。
冲压工艺技术培训资料全解PPT教学课件
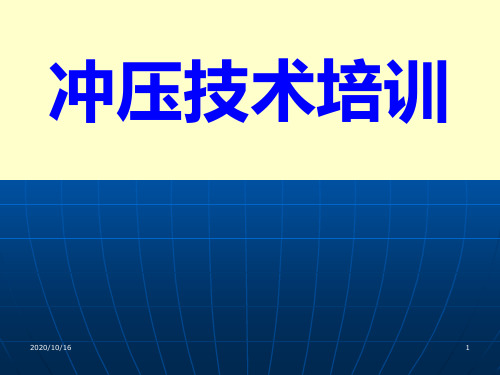
B、调整拉延筋参数
C、增加辅助工艺(垫薄膜等)
D、改善润滑条件
E、修改工艺补充面
F、调整压料力
2020/10/16
11
表面质量产生原因
主要类型:冲击线、滑移线、塌陷、暗坑、 表面扭曲等
对于外板零件来说,外表面产生的缺陷是不 允许的。
冲击线、滑移线主要是由于在冲压过程中,
板料和模具接触后,在应力集中处摩擦造 成的表面划痕。
2020/10/16
13
(二):操作工应掌握基础知识
A:冲压操作工掌握“三好”“四会”基本内容 a:三好:管好、用好、修好。
1; 管理好设备:操作工管好车间分配责任机台,每天对机 台点检;记好点检记录并保持记录清洁不得丢失。
2;用好设备:严格遵守操作规程,正确使用、合理润滑。 做好下班设备“无脏乱差”、填好规定记录。
2、冲压工艺方面: A、合理安排工序 B、检查压料面和拉延补充面的合理性; C、检查拉延毛坯、压料力、局部材料流动情况的合理性。 D、用内筋方式舒皱 E、提高压料力,调整拉延筋、冲压方向,增加成形工序、 板料厚度,改变产品及工艺造型以吸收多余材料等方法
3、材料方面:在满足产品性能的情况下,对于一些易起皱 的零件,采用成形性较好的材料
塌陷、暗坑、表面扭曲主要是由于零件变形
不充分,局部材料应变较小,外力释放后
出现的缺陷。
2020/10/16
12
表面质量问题解角,增加拉延深度,更改压料面 等方法。
消除滑移线,可以通过改变产品形状 (左右对称)、增大阻力等方式。
消除塌陷、表面扭曲,应了解零件在变 形区所产生应力梯度的等级,尽量保证 产品塑性变形的均匀性。同时通过增大 阻力,提高局部形状应变等手段。
冲压成形工艺流程及零件成形常见问题详解(行业讲座教学培训课件)

11
(行业讲座教学培训课件)
起皱解决办法
1、产品设计方面: A、检查原始产品模型设计的合理性; B、避免产品出现鞍形形状; C、产品易起皱部位增加吸料筋等等;
2、冲压工艺方面: A、合理安排工序 B、检查压料面和拉延补充面的合理性; C、检查拉延毛坯、压料力、局部材料流动情况的合理性。 D、用内筋方式舒皱 E、提高压料力,调整拉延筋、冲压方向,增加成形工序、 板料厚度,改变产品及工艺造型以吸收多余材料等方法
14
(行业讲座教学培训课件)
开裂解决办法
1、材料方面:采用拉延性能较好的材料 2、减少应变方面: A、选择合理的坯料尺寸和形状 B、调整拉延筋参数 C、增加辅助工艺(切口等) D、改善润滑条件 E、修改工艺补充面 F、调整压料力 G、………….
15
(行业讲座教学培训课件)
回弹问题
回弹:零件在冲压成形后,材料由于弹性卸载, 导致局部或整体发生变形。
CAE技术解决的问题
材料移动
拼焊线的确定
25
(行业讲座教学培训课件)
CAE分析结果的影响原因
模拟结果的影响原因: 1、材料参数是影响模拟结果的主要原因。 材料性质的不一致导致分析结果和现场调 试结果的不一致。 2、模拟用参数以及润滑条件不同造成的 误差。
26
(行业讲座教学培训课件)
CAE分析结果的评判
(行业讲座教学培训课件)
冲压成形工艺流程及零件成形常见问题
一、冲压成形工艺流程 二、MP的制作方法 三、应用实例
1
(行业讲座教学培训课件)
模具开发基本流程
产品 设计
冲压 工艺 分析
冲压成型工艺ppt

THANKS
感谢观看
操作人员需保持与冲压机械及其模具的安全 距离,避免因过于接近而导致的伤害事故。
操作人员需遵守各项安全规定,不违章操作 ,避免因不规范操作导致的安全事故。
06
冲压成型工艺的未来发展
冲压成型工艺的发展趋势
高效化生产
随着汽车制造业的发展,冲压成型工艺需要进一步提高生产效率,以满足汽车生产的需求 。
自动化与智能化
冲压成型工艺的应用范围
汽车制造
覆盖件、车身后翼子板、车门等。
家用电器
洗衣机外壳、空调室外机等。
仪器仪表
外壳、面板等。
医疗器械
不锈钢冲压成型手术器械等。
03
冲压成型工艺流程
冲压成型工艺的基本流程
材料准备
模具设计
选择合适的材料,进行材料清洗、干燥和切 割等准备工作。
根据产品需求,设计相应的模具结构,确定 模具的闭合高度、压力大小等参数。
工艺改进
通过对冲压成型工艺的不断研究和 改进,提高生产效率、降低生产成 本。
自动化提升
采用自动化设备替代传统的手工操 作,提高生产过程的稳定性和效率 。
信息化整合
通过引入生产管理系统等信息化手 段,优化生产计划和物料管理,提 高整体运营效率。
环境友好性
注重环保和节能,采用环保材料和 设备,降低生产过程中的能耗和废 弃物排放。
冲压成型工艺ppt
xx年xx月xx日
contents
目录
• 冲压成型工艺简介 • 冲压成型工艺的原理 • 冲压成型工艺流程 • 冲压成型工艺的影响因素 • 冲压成型工艺的安全性 •艺简介
冲压成型工艺的定义
冲压成型工艺是一种金属加工方法,通过施加压力将金属板 材或管材变形、剪切或成型为所需形状和尺寸的零件或组件 。
冲压成型工艺ppt

未来发展趋势与挑战
01
高强度材料的应用
随着高强度材料的不断发展和应用,冲压成型工艺将面临更高的挑战
,需要解决成型难度大、模具磨损严重等问题。
02
智能化和自动化
未来冲压成型工艺将更加智能化和自动化,提高生产效率和产品质量
。
03
可持续发展
随着环保意识的提高,冲压成型工艺需要朝着可持续发展的方向发展
,减少能源消耗和环境污染。
特点
高精度、高效率、低成本、适用范围广。
冲压成型工艺的重要性
1 2
满足工业需求
冲压成型工艺是工业生产中的重要环节,尤其 在汽车、电子、航空等领域,能够满足大量且 多样化的零件需求。
提升产品质量
通过冲压成型工艺,可以制造出高精度的零件 ,从而提高产品质量和稳定性。
3
提高生产效率
冲压成型工艺具有高效的特点,能够实现自动 化生产,提高生产效率。
技术创新与可持续发展方向
材料创新
工艺创新
研究和开发新的高强度材料,以满足产品轻 量化、高性能的要求。
研究和开发新的冲压成型工艺,以提高生产 效率、降低成本、提高产品质量。
技术融合
环保技术
将信息技术、人工智能等技术与传统冲压成 型工艺相结合,实现智能化和自动化生产。
研究和开发环保的冲压成型技术,如废料回 收、能源节约等,以减少对环境的影响。
03
冲压成型工艺材料与设备
材料选择与要求
冲压成型材料
通常选择金属薄板或带材作为 冲压材料,如低碳钢、不锈钢
、铝合金等。
材料厚度
根据产品要求和工艺特点选择合 适的厚度,通常在0.1~2mm之间 。
材料表面质量
要求材料表面平整、无锈蚀、氧化 皮等缺陷。
- 1、下载文档前请自行甄别文档内容的完整性,平台不提供额外的编辑、内容补充、找答案等附加服务。
- 2、"仅部分预览"的文档,不可在线预览部分如存在完整性等问题,可反馈申请退款(可完整预览的文档不适用该条件!)。
- 3、如文档侵犯您的权益,请联系客服反馈,我们会尽快为您处理(人工客服工作时间:9:00-18:30)。
CAE技术解决的问题
• 利用计算机数字化模拟,能预测零件在生产 过程中的所有问题,例如:开裂、起皱、塌 陷、滑移和冲击等缺陷。
• 通过成形的切线位移场可以了解材料的流动 情况,为更好的解决零件成形时产生的缺陷 提供帮助。
• 同时可以通过和产品的同步开发,确定零件 的局部形状以及一些重要特征状态。
• 通过对拉延、切边、翻边等各种工艺环境的 仿真,模拟实际的冲压过程,预测及修正设 计模型、工艺参数。
3、材料方面:在满足产品性能的情况下,对于一些易起皱的零件, 采用成形性较好的材料
零件开裂问题
开裂原因
开裂:主要是由于材料在拉伸过程中,应变超过其 极限,而形成失稳。 1、材料抗拉强度不足而产生的破裂,如靠凸、凹 模园角处,局部受力过大而破裂。 2、材料变形量不足而破裂,在胀形变形时,靠凸 模顶部产生的破裂,或凸缘伸长变形流入引起的破 裂。 3、时效裂纹:即严重成形硬化部分,经应变时效 脆化又加重,并且成形时的残余应力作用引起的制 件晚起破裂。 4、材料受拉伸弯曲既而又弯曲折回以致产生破裂 ,多产生于凸筋或凹摸口处。 5、条纹状裂纹。由于材料内有杂质引起的裂纹, 一般平行于板料扎制方向。
MP制订
一、传统的制作方法(国内) 1、按照产品形状,制订出合理的冲压
工艺(BMP); 2、制作3D数据(UG)(用于模具设
计和NC加工); 3、制作详细的2D数据(指导设计和会
签)
MP制订
二、国外的制作方法 1、按照产品形状,制订出合理的冲压
工艺(BMP); 2、制作3D数据(UG格式、设计用); 3、制作详细的2D数据(指导设计和会
CAE技术解决的问题
Skid mark 滑移线
Impact mark 冲击线
塌陷
起皱
CAE技术解决的问题
材料移动
拼焊线的确定
CAE分析结果的影响原因
模拟结果的影响原因: 1、材料参数是影响模拟结果的主要原因。 材料性质的不一致导致分析结果和现场调 试结果的不一致。 2、模拟用参数以及润滑条件不同造成的 误差。
表面质量问题解决办法
• 消除冲击线,可以通过改变冲压圆角、 凹模圆角,增加拉延深度,更改压料面 等方法。
• 消除滑移线,可以通过改变产品形状 (左右对称)、增大阻力等方式。
• 消除塌陷、表面扭曲,应了解零件在变 形区所产生应力梯度的等级,尽量保证 产品塑性变形的均匀性。同时通过增大 阻力,提高局部形状应变等手段。
开裂解决办法
1、材料方面:采用拉延性能较好的材料 2、减少应变方面: A、选择合理的坯料尺寸和形状 B、调整拉延筋参数 C、增加辅助工艺(切口等) D、改善润滑条件 E、修改工艺补充面 F、调整压料力 G、………….
回弹问题
回弹:零件在冲压成形后,材料由于弹性卸载, 导致局部或整体发生变形。
应变
起皱解决办法
1、产品设计方面: A、检查原始产品模型设计的合理性; B、避免产品出现鞍形形状; C、产品易起皱部位增加吸料筋等等;
2、冲压工艺方面: A、合理安排工序 B、检查压料面和拉延补充面的合理性; C、检查拉延毛坯、压料力、局部材料流动情况的合理性。 D、用内筋方式舒皱 E、提高压料力,调整拉延筋、冲压方向,增加成形工序、板 料厚度,改变产品及工艺造型以吸收多余材料等方法
CAE模拟技术在冲压工艺中的应用
一、CAE技术的应用 二、利用CAE模拟可以解决的问题 三、应用实例
CAE模拟技术的应用
• 随着计算机技术的不断发展,CAE 数字模拟技术被广泛的应用到实际 生产中。
• 主要应用软件: • PAMSTAMP(法国);
AUTOFORM(瑞士); DYNAFORM(美国);KMAS(J 金网格);FASTAMP(华中科大)
冲压成形工艺流程及零件成形常见问题
一、冲压成形工艺流程 二、MP的制作方法 三、应用实例
模具开发基本流程
产品 设计
冲压 工艺 分析
模具 同步 分析
DL图 设计
CAE CAE分
同步 析(运 分析 动干涉)
产品、 冲压工 艺、模 具结构、
NC
冲压工艺基本流程
产品数模
生产纲领
参考工艺
技术标准 设备参数
零件工艺 性分析 CAE 拉延
修冲
工艺制订 CAE
冲压方向
内容分配
编制冲压 制作 CAE 作业书 数模 分析
解析 技术
模具材料 定位方式
PB
拉延 间隙
确定
PC 全工序
翻边
模具结构 取料方式.. PD…
CAM…..
分模线….
冲压工艺制订
主要原则和步骤: 1、详细了解产品的功能和形状 2、合理安排工序内容 3、BMP制订 4、工序数模制作 5、CAE模拟 6、MP制订
应力
回弹解决办法
由于影响回弹的因素很多,例如:材料、压 力、模具状态等等,实际生产中很难解决。 目前,解决回弹常用下面几种方法:
1、补偿法。其原理是根据弯曲成形后板料的 回弹量的大小预先在模具上作出等于工件 回弹量的斜度,来补偿工件成形后的回弹 (经验和CAE模拟);
2、拉弯法。是在板料弯曲的同时施加拉力来 改变板料内部的应力状态和分布情况,使 应力分布较为均匀,减少回弹量;
零件常见问题
1、起皱问题
起皱原因
• 主要原因:由于板料的厚度方向的尺寸和 平面方向上的尺寸相差较大,造成厚度方 向不稳定,当平面方向的应力达到一定程 度时,厚度方向失稳,从而产生起皱现象。
• 1、材料堆集起皱。进入凹模腔内材料过多 变成的皱纹。
• 2、失稳起皱 a.板料厚度方向约束力弱的压缩凸缘失稳。 b.在不均匀的拉伸部位失稳而产生的皱纹。
签) (MP)(OFFICE文件) 4、制作3D数据(UG格式、NC用)
冲压工艺案例
零件名称:左右纵梁 材料:SP121BQ 料厚:1。2MM
冲压工艺案例
PB:拉延 PD:整形
PC:修冲 PE:修冲
零件常见问题
• 零件成形时常见问题: • 1、起皱 • 2、开裂 • 3、回弹 • 4、表面质量(塌陷、滑移、冲击)
3、采用成形性较好的材料。
表面质量问题
表面质量产生原因
主要类型:冲击线、滑移线、塌陷、暗坑、 表面扭曲等
对于外板零件来说,外表面产生的缺陷是不 允许的。
冲击线、滑移线主要是由于在冲压过程中, 板料和模具接触后,在应力集中处摩擦造 成的表面划痕。
塌陷、暗坑、表面扭曲主要是由于零件变形 不充分,局部材料应变较小,外力释放后 出现的缺陷。