换型动作时间分析表
动作分析与时间研究-20071221145624311

动作分析与时间研究3. 时间研究3.1 时间研究概述3.2 作业测定的方法及基本程序3.3 标准工时设定3.4 工作抽样3.4.1 工作抽样概述3.4.2 工作抽样的原理3.4.3 工作抽样的方法和步骤3.5 预定动作时间标准3.5.1 预定动作时间标准概述3.5.2 模特排时法 (MOD3.5.2.1 MOD 法的特点3.5.2.2 模特排时法的动作分类3.5.2.3 模特法的动作分析3.5.2.4 动作的改进3.6 生产线平衡分析3. 时间研究3.1 时间研究概述1.时间研究的意义时间研究是基础工业工程的两大技术之一, 他是由泰勒首创并发展起来的, 也称为“ 作业测定” , 或是“ 工作衡量” 。
生产现场,日常消耗的总时间大致可以分为:基本需要作业时间与由于工作进度不妥而造成的多余时间,以及完全浪费的无效时间三种。
• 基本需要作业时间当产品设计、制造工序及作业方法都不再更改时所使用的生产时间, 也可以说是不能降低到这以下的理想时间, 唯有这项作业内容才视为真正是“ 有效工作” 。
• 多余时间由于设计及制造方法不当多耗费的作业时间,其内容本质上是“ 无效工作” 。
• 无效时间由于工厂管理上的各种缺陷所引起的中断时间,作业人员与机械设备在此期间没有工作成效而浪费掉的时间, 其内容可以说是“ 浪费工作” 。
在制造的总过程中, 这些多余因素与无效因素, 所谓非生产因素与真正需要的基本作业内容相比, 其值相当大。
因此,依靠时间研究在对工作潜在的非生产因素内容定向的分析的同时,还必须进行定量的评价,以便使我们能够极力排除或减少它。
作业测定的首要目的在于明确非生产因素,以便有助于方法研究。
在把可能避免的非生产因素全部排除之后,按照正确的、通行的某种测定来确定使用可行的最佳作业方法时的标准作业时间。
这样一来,一次确定了的标准时间可作为推进生产的管理计划,且作为控制和评价的基本尺度而得以应用。
此外,在日常的现场管理中,利用标准时间的效果与在质量管理中使用管理图一样。
SMED(快速换模)
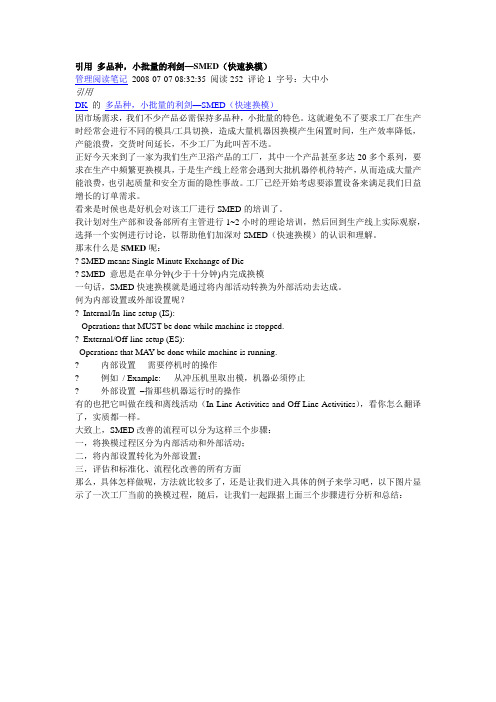
引用多品种,小批量的利剑—SMED(快速换模)管理阅读笔记2008-07-07 08:32:35 阅读252 评论1 字号:大中小引用DK的多品种,小批量的利剑—SMED(快速换模)因市场需求,我们不少产品必需保持多品种,小批量的特色。
这就避免不了要求工厂在生产时经常会进行不同的模具/工具切换,造成大量机器因换模产生闲置时间,生产效率降低,产能浪费,交货时间延长,不少工厂为此叫苦不迭。
正好今天来到了一家为我们生产卫浴产品的工厂,其中一个产品甚至多达20多个系列,要求在生产中频繁更换模具,于是生产线上经常会遇到大批机器停机待转产,从而造成大量产能浪费,也引起质量和安全方面的隐性事故。
工厂已经开始考虑要添置设备来满足我们日益增长的订单需求。
看来是时候也是好机会对该工厂进行SMED的培训了。
我计划对生产部和设备部所有主管进行1~2小时的理论培训,然后回到生产线上实际观察,选择一个实例进行讨论,以帮助他们加深对SMED(快速换模)的认识和理解。
那末什么是SMED呢:? SMED means S ingle M inute E xchange of D ie? SMED 意思是在单分钟(少于十分钟)内完成换模一句话,SMED快速换模就是通过将内部活动转换为外部活动去达成。
何为内部设置或外部设置呢?? Internal/In-line setup (IS):Operations that MUST be done while machine is stopped.? External/Off-line setup (ES):Operations that MAY be done while machine is running.? 内部设置- 需要停机时的操作? 例如/ Example: ---从冲压机里取出模,机器必须停止? 外部设置–指那些机器运行时的操作有的也把它叫做在线和离线活动(In-Line Activities and Off-Line Activities),看你怎么翻译了,实质都一样。
动作分析
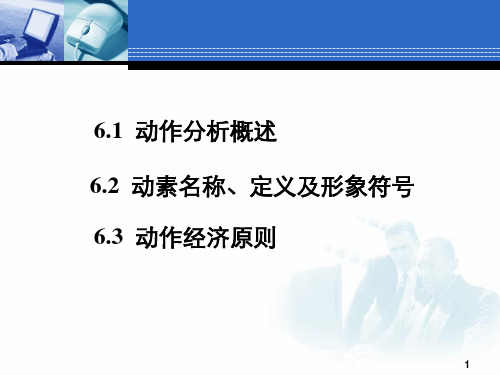
11
3.抓取(Grasp-G):利用手指充分控制物体,也称“握取”。
起点:当手指或手掌环绕一物体,欲控制该物体的瞬间;终点:当 物体被充分控制的瞬间结束
特性:物体已经被充分控制后的“持住”;要点是用手控制物体; 任何用工具的控制应视为“使用”;“抓取”常在“伸手”和“移 物”之间发生
起点:两个物体开始接触瞬间;终点:两个物体完全配合瞬间 特性:较简单的“装配”几乎和“定位”无区别时,应以“定位” 视之;常在“定位”或“预对”之后,而在“释放”之前发生
(14) 应有适当的照明设备,使视觉舒适。
(15) 工作台及椅之高度,应使工作者坐立适宜。 (16) 工作椅式样及高度,应可使工作者保持良好的姿势。
27
3.与工具设备有关的原则 (17)尽量解除手的工作负担,代之以夹具或脚踏装置进行 工作。 (18)尽可能用两个或两个以上功能的组合工具。
(19)工具和物料应尽可能预放在工作位置。
29
动作经济原则的应用
实例1:通过固定电烙铁减少动作数
30
实例2:用定量容器取消计数动作
31
实例3:利用反射镜减少眼的移动角度
32
实例4:用透明有机玻璃观看窗口减少眼的活动
33
实例5:合并两个印章减少盖印动作
34
实例6:用双管注射器减少涂覆树脂动作
35
实例7:指定工具、物料的放置位置
36
18
17.故延(Avoidable Delay-AD):由于故意
或疏忽而使工作中断
起点:开始停顿的瞬间;终点:恢复工作的瞬
间
特性:此动素发生时,不需考虑工序调整;通
常是由于工人的工作方法错误,不注意或疏忽
精益生产-SMED(快速换模)
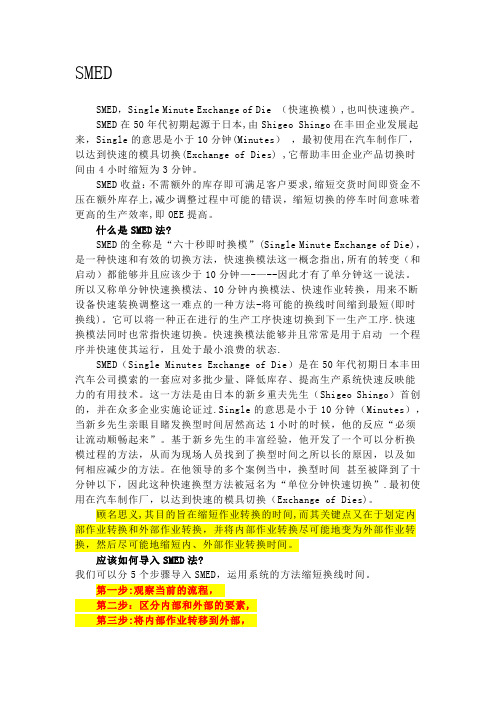
SMEDSMED,Single Minute Exchange of Die (快速换模),也叫快速换产。
SMED在50年代初期起源于日本,由Shigeo Shingo在丰田企业发展起来,Single的意思是小于10分钟(Minutes),最初使用在汽车制作厂,以达到快速的模具切换(Exchange of Dies) ,它帮助丰田企业产品切换时间由4小时缩短为3分钟。
SMED收益:不需额外的库存即可满足客户要求,缩短交货时间即资金不压在额外库存上,减少调整过程中可能的错误,缩短切换的停车时间意味着更高的生产效率,即OEE提高。
什么是SMED法?SMED的全称是“六十秒即时换模”(Single Minute Exchange of Die),是一种快速和有效的切换方法,快速换模法这一概念指出,所有的转变(和启动)都能够并且应该少于10分钟—-—--因此才有了单分钟这一说法。
所以又称单分钟快速换模法、10分钟内换模法、快速作业转换,用来不断设备快速装换调整这一难点的一种方法-将可能的换线时间缩到最短(即时换线)。
它可以将一种正在进行的生产工序快速切换到下一生产工序.快速换模法同时也常指快速切换。
快速换模法能够并且常常是用于启动一个程序并快速使其运行,且处于最小浪费的状态.SMED(Single Minutes Exchange of Die)是在50年代初期日本丰田汽车公司摸索的一套应对多批少量、降低库存、提高生产系统快速反映能力的有用技术。
这一方法是由日本的新乡重夫先生(Shigeo Shingo)首创的,并在众多企业实施论证过.Single的意思是小于10分钟(Minutes),当新乡先生亲眼目睹发换型时间居然高达1小时的时候,他的反应“必须让流动顺畅起来”。
基于新乡先生的丰富经验,他开发了一个可以分析换模过程的方法,从而为现场人员找到了换型时间之所以长的原因,以及如何相应减少的方法。
在他领导的多个案例当中,换型时间甚至被降到了十分钟以下,因此这种快速换型方法被冠名为“单位分钟快速切换”.最初使用在汽车制作厂,以达到快速的模具切换(Exchange of Dies)。
快速换型SMED

快速換型SMED 主講:劉波EVERLASTING 說明:本文所有圖片及內容均於本人個人版權,未經本人允許不得轉載.簡介什麼是SMED?-S ingle M inute E xchange of D ie 單分鐘快速換模(<10分鐘)什麼是OTED?-O ne-T ouch E xchange of D ie 一觸即發快速換模(<100秒)概述SMED在50年代初期起源於日本由Shigeo Shingo在豐田企業發展起來S ingle的意思是小於10分鐘(M inutes)最初使用在汽車制造廠,以達到快速的模具切換(Exchange of Die)它幫助豐田企業產品切換時間由4小時縮短為3分鐘SMED的創造者Shigeo Shingo生平:於1909年生於日本1930年--機械工程專業的學位1943-48年軍需部空氣啟動魚雷深度機製1950年形成SMED的階段使安裝操作分裂成內部和建立的外部有關換型時間的定義換型時間:在同一條生產線或同一臺設備生產的前一种產品的最後一件良品與下一种產品的第一件良品之間的間隔時間.最后一件良品第一件良品在換型過程中設備作業停滯沒有產品產出沒有任何增值活動(NVA)停滯的設備不能創造任何效益內部時間VS 外部時間內部時間:生產停滯時所進行的換型作業(只有當機器停下來才能進行的操作所需要的時間.(例如,裁斷換斬刀的取放時間,針車換線,大底換型時變換膠藥水的時間).外部時間:生產進行的同時所進行的換型作業.(可以在機器運行的情況下進行的操作的需要的時間)換模的現場舉例 准備課裁斷換線動作視頻電腦班換線動作視頻大底課換線動作視頻快速換模的定義用最短的時間完成在同一條生產線或同一臺設備生產的前一种產品的最后一件良品與下一种產品的第一件良品之間的換型過程切換過程中時間的損失損失時間停產時間調整時間生產速度時間訂單一訂單二為什麼要快速換型精益生產-即小批量,混合型的生產模式要求整個生產過程能夠非常快速的由一個品种的生產轉換到另一個品种的生產,認達到最少的生產時間損失.*提高换线的频率是采用SMED的主要目的提高產能提高換線的頻率*之前采用SMED之后需要加班的時間總共可以工作的時間321213要求有產出的時間換線時間和頻率需求增加•縮短換線時間•不需要加班213縮小批量的大小降低存儲量提高靈活性縮短備貨時間提高品質減少浪費提高換線的頻率SMED可以為生產帶來兩方面的好處SMED的好處換型過程中的常見作業關機工作站清潔及整理取新產品作業的指導文件取新產品所需的治具更換治具新產品的原材料和設備就位校準與對位測試設備及治具確保對位準確典型的切換基本過程30%準備和清理-準備部件和工具,並檢查其狀況-移走部件和工具,並進行清理5%裝配和移開機器15%測量,設置和校正50%試運行和調整生產過程中的一些可變因素過程輸入換型過程輸入:溫度,原材料,濕度,等.客戶生產過程換型過程中常見的作業•關機•工作站清潔及整理•取新產品作業的指導文件•取新產品所需的治具•更換治具•新產品的原材料和設備就位•校准與對位•測試設備及治具以確保對位准确F1賽車進維修站的啟示1.F1賽車進維修站過程視頻欣賞搞笑進站視頻欣賞2.分組討論對F1進站過程的優點和可借鑒之處大家不妨數一數有多少人,每個都在做什麼呢?減少換型時間的黃金法則1.去除,簡化,自動化---只按照此順序進行;2.一種方法,正確的方法,相同的方法-始終如一﹔3.在系統中建立所要求的精度-無需調整﹔4.內轉外-把內部時間作業轉至外部時間進行.去除,簡化,自動化---只按照此順序進行去除對於換型過程中的每一步作業,觀察是否必須還是有機會去除該步驟﹔簡化如果不能夠去除某一步驟,就盡量簡化它,以求更快,更簡便以及更完美﹔自動化自動化是為了更好地得以過程控制。
快速切换培训教材(ppt 78页)
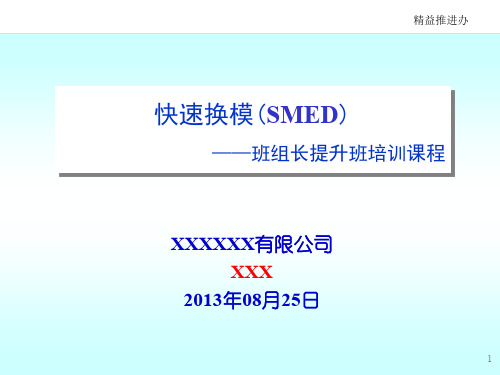
精益推进办
26
精益推进办
SMED的基本法则:事前准备
1、尽量将内部作业时间转换为外部作业时间,缩短停机换模时间: 将内部作业时间转换为外部作业时间,做好前期准备。在还没有停机的时候
就做好前期准备,比如:如工装夹具准备、零部件准备、作业指导书准备、升降 工具、作业台准备等。
将取拿新模具,清洁新模具,取拿试产部件等活动在不需要停机时准备好。 然后,进行一些与模具有关的预备工作,比如:预装配、预设定、预清洁、 预热等等。
—— 新乡重夫( Shigeo Shingo )
9
精益推进办
快速换模的境界:
境界一:No concept of Quick Changeover 没有快速换模观念 境界二:Single Minutes Exchange Die 单分钟换模 境界三:Zero Exchange Die 零换模 境界四:One Touch Exchange Die 一触换模 境界五:One Cycle Exchange Die 一周换模 境界六:No Need Exchange Die 无需换模
快速换模法同时也指快速切换。快速换模法能够并且常常是用于启动一个程 序并快速使其运行,且处于最小浪费的状态。
19
精益推进办
如何理解 SMED:
工业工程IE 方法应用: SMED 是通过工业工程的方法,将模具的产品换模时间、生产启动时间或调整 时间等尽可能减少的一种过程改进方法。
高度可调式 换模车
20
精益推进办
如何理解 SMED:
团队工作 是基础: SMED 是一种以团队工作为基础的工作改进方式,可显著地缩短设备、模具安 装、调整,即换模所需的时间。
大家不妨数一数有 多少人,每个人都 在做什么呢?
换模作业分析表

工序:
换模作业动作、时间分析表
设备:
换模时间:
编号 切换作业项目
作业具体内容 (李志明)
开始时间
1 停机 2
操作电脑屏幕 控制行程限位 回移机架 拆下模水管(4根) 松下模锁 松下模锁环 离开 敲下模模锁环 清理工具和螺丝 松下模锁环 拆滑牙最后一颗螺丝 寻求滑牙处理方法:打锁环
停止时间
花费 时间 (秒)试产 首件 人数
调整 检查
问题点说明
机架同时在移动,操作不当 操作顺序不对造成重复作业
中间有换人操作,
螺丝滑牙 没有固定位置导致多余动作, 失败作业。滑牙原因? 寻求滑牙处理方法
设备老化导致需要的补救措施 补救措施也没有事前标准化,导致现场寻找铝 块,铝块的大小形状都无要求,安装后易脱落, 工装化检讨?
有失败作业铝块镶嵌取不出来,快速的方法是?
与等模具的平行作业 叉车使用方法:旧去新来?这样一定会等待。
清渣 工作的延续 动作比较熟练,有无更快速的方法? 两人配合作业?
可否加快速度?
无固定位置摆放,浪费时间
无编号导致需要挑选 还是挑选的浪费动作 安装水管的时间各有不同,原因是?
进水管不够长导致的问题 如何提前发现问题,水管的问题、安装的问题? 提前加工的可能性?
借铁锤是外换模,可以提前准备
提起的高度有无标准,如何加快速度?
补救措施也没有事前标准化,导致现场寻找铝 块,铝块的大小形状都无要求,安装后易脱落,
工装化检讨?
提前准备,对此张经理有新思路不用叉车。 行车使用规定?排除铁钩干涉的问题
提前到达指定位置、保持指定姿态 预定位的位置精确化、模具底板位置精确化
6S问题,机台周边的整理整顿
前面没有清理干净
工业工程导论-预定动作时间标准法

9.2.3 MTM动作要素说明
9.对准(Position)一一符号P 对准是指使目的物与另一目的物对准整齐的动作。例如对准钢笔与笔套之动作等。其影响因素有三: (1)啮合(Engage)程度。 (2)对称性。 (3)操作的难易程度。 10.拆卸(Disengage)一一符号D 拆卸是指将两啮合的物体拆开并有反动力发生之动作。如拆开钢笔套时的动作。 拆卸影响因素有二: (1)啮合程度。 (2)操作难易程度。
预定动作时间标准法概述
9.1.1 预定动作时间标准法的产生
1934年,美国无线电公司的奎克(J.H.Quick)等人在动作研究的基础上创立了工作因素体系(Work Factor System),简称WF。该方法将操作分解为移动、抓取、放下、定向、装配、使用、拆卸及精神作用等8种动作要素,并制定出8种动作要素的时间标准。 1948年,美国西屋电气公司梅纳德(H.B.Maynad)、斯坦门丁(G.J.S tegemerteh)和斯克互布(J.L.Schwab)公开了他们研制的方法时间衡量(Methods Time Measurement),简称MTM。该方法是把操作分解为:伸向、移动、抓取、定位、放下、拆卸、行走等动作要素,并且预先排成表,确定出完成每种动作要素所需要的时间。
预定动作时间标准法概述
9.2 方法时间衡量(MTM)
9.2.1 方法时间衡量(MTM)系统 9.2.2 MTM的时间单位 9.2.3 MTM动作要素说明 9.2.4 MTM法制定标准时间的步骤 9.2.5 MTM法分析举例
第九章 预定动作时间标准法
9.2.1 方法时间衡量(MTM)系统
方 法 时 间 衡 量 (MTM)
9.2.3 MTM动作要素说明
快速换型技术

快速换型技巧大多数制造企业生产的产品不会仅是一二种而已,少则数十种,多则数万种也有。
不同类别的产品在生产的过程中必定有其不同的制造条件。
举倒来说:温度不同,工具、模具、胎具的不同,材料、零部作的不同甚至工作方法也有不同。
因此,在不同类别的产品更换时,生产线必须暂时停止生产活动,以便能更换并设定新的工作条作,这种更换设定的动作就称为“切换”。
“切换”时,因生产停顿所耗费的时间就称为“切换时间”。
“切换”的次数会因生产线产品种类的增多,或生产批量减少而相应增多。
每次“切换”耗费的时间,对工厂而言是损失。
为了减少这种损失,许多人想到的解决方式就是加大每一种产品的生产批量,以及减少产品的种类,这样每一个产品所分摊的平均切换损失就会减少。
换句话说,生产的批量越大,分摊的切换成本就越低。
但是如果批量超过了市场的需要量,多余的产品就必须储存起来保管。
储存时必然使用到仓库以及相关的防护保管及管理,所以每次生产的批量越大,“保管”的成本也就越高。
就“保管”成本而言,希望每次生产的批量越少越好。
到底该怎么办呢.如上所述为了避免“切换时间”的损失,许多人倾向于加大生产的批量数,以减少切换次数。
但是这种做法,仅仅考虑到切换本身成本的减少,却忽略工厂的整体效率。
例如:制造过多的浪费、等待的浪费、不良品的浪费、生产交付时间过长、物流混浊等等,尤其目前市场的趋势是走向少批量多品种、高品质、短交付期的新竞争的优势,就必须尽量缩短“切换时间”,这就是“快速换模(线)”的意义。
一.何为快速换模技术快速换模技术是由日本现场改善专家新乡重夫先生于1969年在丰田汽车以1000顿的压床由4小時的换线(模)时间,历经六个月的改善降到1.5小时换线(模)时间,再经3个月的改善,换线(模)时间再降至3分钟內完成的实际换线(模)案例所提倡的技术.其发展是从1950年即有换线(模)作业的设定预备工作有"內设定(线內作业)"和"外设定(线外作业)"之分的想法开始,历经19年时间所孕育出來。
动作要素分析(共6张PPT)

RWF——(Ready Work-Factor)WF简便法。为非专业作业研究者开发的。一般情况下,
13
15
9
11
13
15
17
摘型
握型
平均动作数
2
3
4
主要寸法 mm
6
-6
直径 mm 厚 mm
6 1.2
-6 -1.2
全部
1
2
3
5
4
6
8
复 杂 抓 +2, (e)、 (n)、 (slp)+1
单手
双手
主 要 寸 法 (mm)
10-100 -250
-10
-250
250
1
2
2
3
4
3
4
5
5
6
4
5
6
7
8
+50%
—
22+10步 数
上下楼每一台阶 10,起立 13,着席 9
注:红色字为动作要素时间值。1Ru=0.06秒
2
第2页,共6页。
RWF法的时间
1、普通熟练程度的作业者从事熟悉的工作; 2、作业者精神或肉体上没有感到难以承受;
3、良好的努力(无特别的物质刺激、精神刺激、威胁、强迫、强制手段等); 4、正常的作业环境; 5、按规定的作业方法和品质要求进行作业; 6、完成1个作业周期所需要的作业时间。
扳手换手(若有必要)
SMED,Single Minute Exchange of Die (快速换模)培训

目标:消除换模时间!
我们有没有信心, 做好?
快速换模的四大原则
• 区分内部作业转换与外部作业转换 • 内部作业转换尽可能转换成外部作业 • 排除一切调整过程 • 完全取消作业转换操作
5S 是快速换模的关键 !
• 花费在寻找刀、模、夹、治、工具或其它材 料原料所需的时间,会增加换模设定时间。
• 5S做得好,将可以确保所有需要用到的物料, 在当我们有需求时、均在设定位置而且已经 清理,以及是能够被使用的状态下。
•
15% 测量、设置和校正
•
50% 试运行和调整
快速换模(SMED)法则
1. SMED 从头到尾都与 5S 有关。 2. 把内部换模设定变更为外部换模设定,然后
去改善剩下来的内部换模设定时间。 3. 螺丝是我们的敌人。 4. “设定基准原点永远不变”. 假如你必须用你的手,先确认你的脚原地不动。 5. 不要依赖特殊的微调技术。 6. 标准就是标准:它们是没有弹性可伸缩的。 7. 把所有的换型动作标准化。
快速换模
—— 方法比埋头苦干更有效
上批 尾件 良品
下批 首件 良品
换模设定时间
换模设定时间 ( Set-up time ) 是指上批最终一 件良品完成起至下批首件良品完成止所需之时间 。
快速换型的专家,新乡重夫先生(SHIGEO SHINGO):
任一换模设定时间可以
被减少 59/60
换模时间有可以分为以下二类:
冲压机
工具车
模具间
工具间
切记以下八种浪费:
• 超量生产 • 待料或等待 • 运输搬运 • 过多的制程工序 • 库存 • 过多的动作 • 不良品及波动 • 未被采用的创造力/好点子
典型的切换基本过程
动作及时间分析

动作改善的目标和顺序
三 动作改善的顺序
1 问题的发生 发现——时常拥有问题意识 在生产制造的现场;每天都有新的问题在发生 有些 人可能视若无睹;觉得一切都很正常;因而也就缺少 改善的动因;效率也就日复一日地停留在同一水平 上 改善往往源于问题的发生和发现;管理者如果能 带着疑问审视现场所发生的一切;特别对细节的地 方加以留意;就更容易找到改善的对象
用最少的动作投入; 达到最大的工作效果
动作改善的目标和顺序
二 动作经济原则
2 人体的动作应尽量应用最低等级而能得到满意结果; 人身体的动作可按其难易度划分等级;具体如下表:
等级 动作
1
以手指为中心的动作:手指
2
以手腕为中心的动作:手指 及手腕
3
以肘部为中心的动作:手指 手腕及小臂
4
以肩部为中心的动作:手指 手腕 小臂及大臂
动作分析
三 作业人员工序分析法
1 加工作业:使对象发生物理性 的或者化学性的变化;可组装 分解; 是真正的生产性的工作或作业 2 搬运:将对象体从一地点搬到另一 地点的行为 3 检查:调查对象是否和标准一样;并 对其重量和数量进行计算核对的行为 4 停滞待工:指作业人员或机器没 有进行真正的生产性的工作的现象;因 此在进行改善作业时;尽量取消这一现象
动作改善的目标和顺序
一 动作改善的目标
消除不经济 不均衡和不合理的现象
动作改善的目标和顺序
二 动作经济原则
动作经济原则又称省工原则;是使作业动作的组成能以 最少的工的投入;产生最有效率的效果;达成作业目的 的原则
1 双手的动作应同时而对称;
能熟练应用双手同时进行作业;对提高作业速度 大有裨益 单手动作不但是一种浪费;同时也会造成一 只手负担过重;动作不平衡 从动作经济的原则出发;双 手除休息外不能闲着 另外;双手的动作最好同时开始; 同时结束;这样会更加协调
MTM测时法

一、方法时间衡量(MTM法)方法时间测量把人的动作分解为多种基本动作,如足动、腿动、转身、俯屈、跪、坐、站、行及手握等。
在工业中,用手臂动作的操作最多,手臂动作又可分为伸向、移动、转动、加压、抓取、释放、定位及拆卸等动素,将每个基本动作加上宽限,再将这些推算出来的各个时间相加,即可得出完成一项工作所必须的时间,作为建立标准时间的依据。
1.MTM动作的时间单位MTM时间单位称为TMU(Time Measurement Unit),其与普通时间单位换算公式如下:1 TMU=== 1 s=1min=1667 TMU 1 h=100000 TMU2.MTM动素说明(1)伸手(Reach) 符号R1)定义手向目的物移动的基本动作。
2)变动因素。
①手或手指的移动距离。
②伸手的条件:条件A:伸向固定位置或另一手的目的物的情况。
条件B:伸向无固定位置的目的物的情况。
条件C:伸向放置杂乱的目的物的情况。
这时会发生选择的因素,如向零乱的零件伸向的动作等。
条件D:伸向小型目的物或需要适当抓取的目的物的情况。
条件E:伸向身体的自然位置的情况,如手回到自然的工作位置等。
③动作形态A、伸手的开始和伸手的终止均为静止态。
B、伸手的开始或终止为静止态。
C、伸手的开始和终止均为移动态。
向桌上的钢笔伸手5cm,记为R5B。
1) 动素R 的时间标准表。
伸向(R)(2)移动(Move) 符号M1)定义 为某种预定的目的移动某物至一特定的地点。
2)变动因素 ①移动距离; ②移动条件:条件A :将目的物移动到另一手或停止位置的情况。
条件B :将目的物移动到大概位置的情况。
条件C :将目的物移动到精确位置的情况。
③动作形态与伸向的形态相同。
④移动物体重量。
如单手搬运5kg 的货物移动15cm ,表示为M15B ——5;若双手则为:M15B ——5/2 3)动素M 的时间标准表。
表11-31 移动 (M)移动距离 (英寸)时间(TMU) 重量宽限情况和说明A B C 手动B重量达到 (磅) 系数 常数 TMU 3/4或小于0 0 A.移动物体到另一手或从静止状态移动物体1 2(3)转动(Turn) 符号T1)定义以前臂为轴,回转其手、手腕及前臂的旋转动作。
精益生产-快速换型
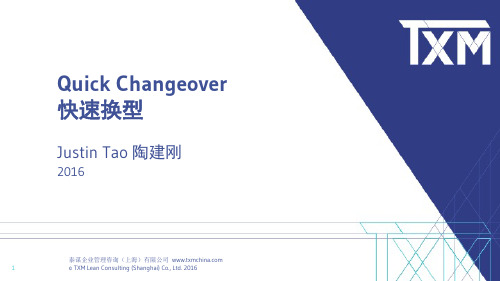
Quick Changeover 快速换型Justin Tao 陶建刚2016Produce Large Lot Size? 大批量生产?• It is a reality still used by many companies to produce, and the main objective is to smooth the setup time.事实上很多企业使用大批量生产方式进行生产,并且主要目标是使换型时间更加平稳• This is the key of the “Mass Production”, it means:这点是“大规模生产”意思的关键所在:– “Produce a large amount of a only product”“生产大批量的单一产品”Heijunka Process 均衡化进程Too early 过早,inventory 库存Too late 过晚,out of stock 缺货ChangeoverConsequence of Long Setup Time 长换型时间导致的结果All these factors increase the wastes in the workshop!!!所有这些因素都在车间中增加了浪费!!!Long Setup Time 长的换型时间Long Production Cycle time 长的生产周期 Large amount of WIP 大量的在制品Equipment to transport and to storage需要设备搬运和存储 Increase manpower need 增加所需人员Require space in the shop floor and area to storage 需要空间存储Definition of Setup Time and Its Structure换型时间的定义和构成:Setup time: The last qualified product in production run and the first qualified product in thenext production run换型时间:指介于一个生产作业的最后一件合格品和下一个生产作业的首件合格品之间的时间 Definition of setup in lean manufacturing: The last qualified product of one type to the firstqualified product of next type精益生产的换型定义:为从前一品种最后一个合格产品,到下一品种第一个合格产品之间的时间间隔。
TPS理论知识考试题库

第一部分TPS知识试题一、填空题1。
标准作业指在指在节拍时间内,以有效的操作顺序,在同一条件下反复进行的操作。
2.合格工位要求1个作业循环中,作业部位不能超过3个,这样的目的是避免多余的步行。
3.生产中的七种浪费:制造过剩的浪费、库存的浪费、搬运的浪费、等待的浪费、加工的浪费、动作的浪费、不良品的浪费。
4.精益生产的两大支柱:自働化和准时化生产。
5.准时化生产的前提条件:平准化包含种类平准化、数量平准化两个面。
6.解决问题与改进流程必须追溯源头、亲自观察,然后验证所得数据.7.评价合格工位的五项内容为:作业区域、作业干涉、部品的放置区域、作业部位、往返次数。
8.标准作业的前提条件应考虑①作业方面②人的方面③设备及生产线方面④品质方面。
9.决定标准手持时有哪些注意点:①作业顺序②有无设备自动加工③完成品不计入④有无自动取出装置⑤温度⑥检查作业。
10.没有问题是最大的问题!管理者需要跳出现场去观察现场。
11. 全员生产保全涵盖四大内容:预防保全;事后保全;改良保全;设备设计。
12.5S是通过整理、整顿、清扫来强化管理,通过清洁来巩固效果。
13.解决问题的八个步骤为:明确问题、分解问题、设定目标、把握真因、制定对策、贯彻实施对策、评价结果和过程、巩固成果。
14。
改善的顺序作业改善、设备改善、工序改善。
15。
现场监察的观察点: 1、瓶颈作业2、堆积 3、材料流动 4、等待5、步行6、身体的动作7、手的动作 8、眼睛的动作.16。
时间观测表要求至少连续观测 10 个循环。
17。
实现“准时化生产”的方式看板方式、后工序取用方式、单个流动方式、平准化生产.18.平准化生产的优点使工人操作更容易、更熟练,提高了对市场的反应速度,降低了库存,缩短了每台产品的制造周期。
19.QC小组活动的主要特点明显的自主性、广泛的群众性、高度的民主性、严密的科学性。
20。
T。
T=1日的生产时间/1日的必要生产量,不是根据设备能力和人员来定的。
PIE制造系统的设计与改进程序

制造系统的设计与改进1、目的:本程序规定了制造系统的设计与改进的步骤及方法,以便有效收集,整理并分析相关资料,达到不断改进的目的。
2、范围:本公司的制造系统3、职责:制造工程师负责设备选型,提出相关技术要求;编制工艺流程,工厂布局的设计,设备及操作动作分析生产部经理负责行动计划的审批生产主管负责库存期量标准的制定4、相关部门:生产部 质量部 采购部 工程部5、程序5.1 制造系统设计内容/使用工具表格 负责人/相关人员见APQP 程序公司经营计划制定指标,TAKT Tim 分析表R-OP-052 制造工程师作出从零件到成品的加工工艺流程, 制造工程师包括成本,机器周期时间,工序时间设备故障率,废品率等(相关数据可 参考类似产品的经验数据)过程流程框图 R-OP-053作出设备平衡分析表(R-OP-054) 制造工程师 包括设备运行时间,故障时间,换型时间上下料时间等.(相关数据参考类似设备的经验数据)制订新设备,工装开发计划(R-OP-056)草拟设备技术协议流程 内容/使用工具表格 负责人/相关人员/装配过程中的动作分析:包括增值动作 制造工程师R-OP-005)R-OP-057)之前R-OP-056A )建议批量=1,建立在制品库存期量标准 生产主管 考虑工位器具的标准化,小型化 制造工程师制造工程师行动计划表R-OP-060包括各项计划内容,进度,日期,负责人5.2 制造系统改进流 程 内容/使用工具表格 负责人。
相关人员公司目标做设备平衡分析表(R-OP-054) 制造工程师 操作动作分析图PFP 图(针对每个人) 制造工程师做浪费分析汇总:包括人员、材料, 物料等,表R-P-058也可用LEAD TIME 分析图R-OP-05行动计划表R-OP-060操作动作分析图R-OP-055A 制造工程师做LEAD TIME分析图(R-OP-059)制造工程师包括设备摆放位置,操作工的走动路线,物料的存放及流动方式等详细内容,修改工厂布局图行动计划R-OP-060与计划目标比较可参考Delphi-GAP评估标准7、编制生产部8、审核质量部采购部生产部工程部9、批准总经理/副总经理HUBEI DELPHI文件编号:R-OP-054A 版本:01 批准:HUBEI DELPHIMACHINE BALANCE SHEET设备平衡分析表PEOPLE FOCUSED PRACTICE SHEET操作动作分析表PROJECT项目: DATA日期:PRODUCT产品名称: PART NO型号:文件编号:R-OP 版本:01 批准:湖北德尔福汽车电机有限公司Hubei Del phi Automotive Generator CO.,Ltd采购设备技术协议书编号:文件编号:R-OP-057 版本号:01 批准:HUBEI DELPHIBLOCK DIAGRAM FORM 过程流程框图PROJECT 主题: DATE 日期: 共 页第 页文件编号:R-OP-053 版本号:01 批准:HUBEI DELPHITAKT TIME ANALYSIS TAKT TIME分析PROJECT项目: DATA日期:Total Available Minutes/Day工作总时间/日Less Contractual休息时间Less Planned Maintenance计划维修时间Total Available Minutes(1)实际工作总时间(1)Year annual Scheduled Daily TAKT Time TAKT Time 年份 Customer Days/Yr Volume(2) Per Moduld Per Module Voiume年产量计划工作日/年日产量 TAKT时间分钟/件 Seconde/PcTakt Time Per Module=(Total Availabie Minutes(1)×60(Sec/Min)/Daily Volume(2)) ×NO.of Modules(3)Take Time/模=(实际工作总时间(1)×60(Min)/Daily Volume(2))×模文件编号:R-OP-052 版本号:01 批准:HUBEI DELPHIPEOPLE FOUSED PRACTICE CHARTProject项目: Data日期:文件编号:R-OP-055A 版本:01 批准:。