CAE领域八大热点
cae发展现状
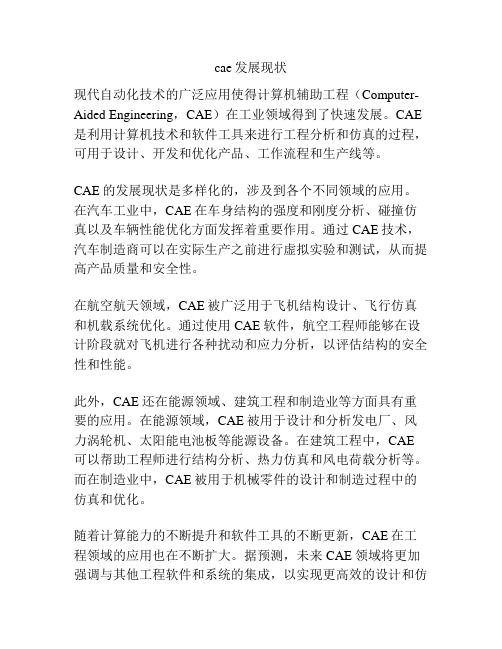
cae发展现状现代自动化技术的广泛应用使得计算机辅助工程(Computer-Aided Engineering,CAE)在工业领域得到了快速发展。
CAE 是利用计算机技术和软件工具来进行工程分析和仿真的过程,可用于设计、开发和优化产品、工作流程和生产线等。
CAE的发展现状是多样化的,涉及到各个不同领域的应用。
在汽车工业中,CAE在车身结构的强度和刚度分析、碰撞仿真以及车辆性能优化方面发挥着重要作用。
通过CAE技术,汽车制造商可以在实际生产之前进行虚拟实验和测试,从而提高产品质量和安全性。
在航空航天领域,CAE被广泛用于飞机结构设计、飞行仿真和机载系统优化。
通过使用CAE软件,航空工程师能够在设计阶段就对飞机进行各种扰动和应力分析,以评估结构的安全性和性能。
此外,CAE还在能源领域、建筑工程和制造业等方面具有重要的应用。
在能源领域,CAE被用于设计和分析发电厂、风力涡轮机、太阳能电池板等能源设备。
在建筑工程中,CAE 可以帮助工程师进行结构分析、热力仿真和风电荷载分析等。
而在制造业中,CAE被用于机械零件的设计和制造过程中的仿真和优化。
随着计算能力的不断提升和软件工具的不断更新,CAE在工程领域的应用也在不断扩大。
据预测,未来CAE领域将更加强调与其他工程软件和系统的集成,以实现更高效的设计和仿真过程。
此外,随着人工智能和机器学习技术的普及,CAE 还将更好地支持自动化和智能化的工程设计和分析。
总之,CAE在工程领域的发展前景广阔,其应用范围涵盖了许多不同的行业和领域。
由于CAE能够提供准确、高效和经济的工程分析和仿真解决方案,预计它将继续在未来的工程实践中发挥重要作用。
CAE在各个行业概况

CAE在各个行业概况摘要:随着计算机辅助工程(CAE)技术的发展,CAE在各个行业中已经得到了广泛的应用。
本文将对CAE在航空航天、汽车、医疗、电子、建筑、能源等行业的应用情况进行调研和分析。
本文将介绍CAE技术在这些行业中的应用和发展趋势,并分析它们在这些行业中的优点和挑战。
一、简介随着计算机技术的不断发展和迅速普及,计算机辅助工程(CAE)技术在工程领域中得到了广泛应用,大大提高了工程设计的效率和准确性。
CAE是指利用计算机仿真和模拟等技术进行工程设计、分析和验证的方法。
它不仅可以用于设计过程中的仿真和测试,还可以用于产品的研发、生产和维护。
在过去几年中,CAE技术已经得到了广泛的应用,并在各个行业中取得了显著的成就。
本文将分析CAE在航空航天、汽车、医疗、电子、建筑、能源等行业的应用情况和发展趋势,并探讨它们在这些行业中的优点和挑战。
二、航空航天在航空航天领域中,CAE技术已经成为必不可少的工具。
飞行器的设计和开发是一项非常复杂的工程,需要进行大量的计算和验证。
CAE 技术可以在设计过程中进行仿真和测试,以验证设计的正确性和可行性。
例如,可以使用CAE技术进行气动性能、结构强度、疲劳寿命等方面的仿真和测试。
据统计,使用CAE技术可以将飞机研发的时间和成本降低30%以上。
目前,航空航天领域中最热门的CAE技术是CFD(计算流体力学)和结构分析。
CFD技术可以用于模拟飞机飞行时的气动流场状况,分析飞机的气动性能和优化设计。
结构分析可以用于确定飞机的结构强度和疲劳寿命,并提供改善设计的建议。
此外,CAE技术在航空航天领域中的应用还包括发动机设计、飞行控制和航空电子。
三、汽车汽车是CAE技术的另一个重要应用领域。
汽车的设计和开发也是一项非常复杂的工程,需要进行大量的计算和验证。
CAE技术可以用于模拟汽车的运行和碰撞,以评估汽车的安全性和性能。
例如,可以使用结构分析技术来确定汽车的强度和疲劳寿命,以及优化车身设计;可以使用动力学仿真技术来模拟汽车的悬挂系统和其他运动部件的运动,并对其进行优化。
中国CAE行业现状及发展前景分析

中国CAE⾏业现状及发展前景分析中国CAE⾏业现状及发展前景分析CAE指⼯程设计中的计算机辅助⼯程,指⽤计算机辅助求解分析复杂⼯程和产品的结构⼒学性能,以及优化结构性能等,把⼯程(⽣产)的各个环节有机地组织起来,其关键就是将有关的信息集成,使其产⽣并存在于⼯程(产品)的整个⽣命周期。
⽽CAE软件可作静态结构分析,动态分析;研究线性、⾮线性问题;分析结构(固体)、流体、电磁等。
CAE⼴泛应⽤于汽车、航空航天、国防军⼯、电⼦装备等制造业,下游⾏业的产品研发对于CAE具有较⼤的市场需求,有助于驱动业内CAE软件⽔平的提升、CAE⾏业解决⽅案及相关服务的持续完善。
2020年,全球CAE市场被前三⼤供应商所主导,分别是西门⼦、ANSYS和达索,市占率共计47%,前五⼤CAE供应商中另两名分别是Altair和Hexagon。
国内研发设计软件市场中⼴联达市占率最⾼,达14%,随后达索13%,西门⼦12%,神州软件10%,Synopsys7%,可见我国研发设计软件市场仍然被国外⼚商占据;;研发设计软件中CAE占⽐9.57%,近10%,其中主要⼚商为ANSYS、达索、西门⼦、中望和安怀信等,国内三家公司市占⽐均不⾜5%,总占⽐仅6%。
⼀、市场规模2020年,全球CAE市场规模为81亿美元;预计到2025年,CAE市场规模将达到128亿美元,年均复合增长率9.6%。
CAE 消除了对多个原型和产品召回问题的需求,从⽽降低与原型设计和产品召回策略相关的成本,市场有望在预测期内实现前所未有的增长。
运⽤CFD分析电池模块温度的情况增多,延长了电池寿命和性能,将有效推动CAE市场发展。
越来越多的⼯程制造任务被外包给中国、印度、俄罗斯等新兴经济体。
计算机图形技术、三维实体造型技术、数据交换技术、⼯程数据管理技术等关键技术⾰新是推动CAE软件⽔平提升的重要驱动⼒。
“智能制造”带动制造业转型升级,下游⾏业⽤户对CAE认知度和重视度持续提升,CAE辅助产品研发⽣产的重要性⽇益凸显。
世界CAE行业综述
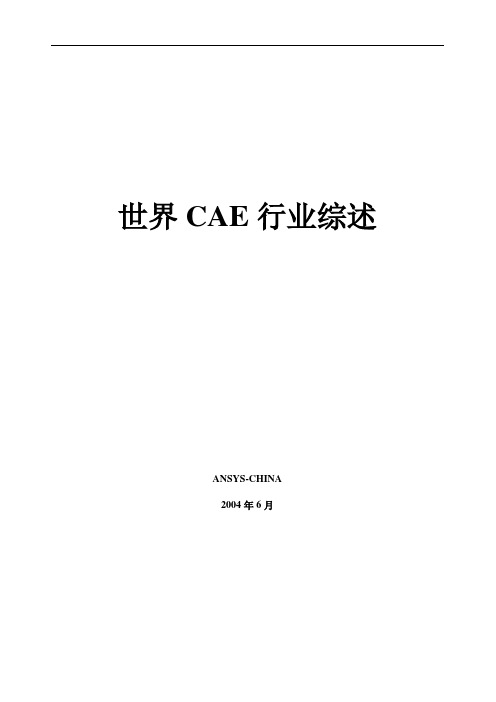
世界CAE行业综述ANSYS-CHINA2004年6月目录一. CAE的定义 (4)二. CAE软件的分类 (4)2.1 MCAE类: (4)2.2 CFD类: (4)2.3 CEM类: (4)三. 世界CAE领域的主要竞争者 (5)3.1 ANSYS公司 (5)3.2 MCAE领域 (5)3.3 CFD领域 (5)3.4 CEM领域 (5)3.5 其他公司 (5)3.6 主流CAE软件一览表 (6)四. ANSYS公司 (6)4.1 核心技术体系 (7)4.1.1 MCAE体系 (7)1. Mechanical模块 (7)2. LS-DYNA模块 (8)3. Motion模块 (8)4. Fe-safe模块 (8)4.1.2 CFD体系 (8)1. CFX模块 (8)2. CART3D模块 (8)4.1.3 CEM体系 (8)1. EMAG模块 (9)2. FEKO模块 (9)4.2 ANSYS协同仿真环境 (9)4.2.1 CAD技术与数据的协同 (9)4.2.2 CAE技术与数据的协同 (10)4.2.3 CAD与CAE的协同 (10)4.3 ANSYS公司的优势特征 (11)4.3.1 ANSYS总体优势 (12)1. 仿真类型全面 (12)2. 多场耦合仿真 (12)3. 协同仿真环境 (12)4. 研发全过程仿真 (12)5. 高效并行计算 (13)4.3.2 细节技术优势 (13)2. 自动探测装配 (14)3. “死网格”再生术 (14)4. 解读仿真模型 (15)5. 变分优化技术 (15)6. 顶级网格雕塑 (15)五. MSC.Software公司 (16)5.1 核心产品 (17)1. MSC.Nastran (17)2. MSC.Marc (17)3. MSC.Dytran (17)4. MSC.ADAMS (18)5. MSC.Fatigue (18)6. MSC.Patran (18)7. MSC.Enterprise Mvision (18)5.2 与ANSYS的比较 (18)5.2.1 MSC的优势 (18)1. 行业市场 (18)2. 机构运动学 (18)3. 线性动力学 (19)4. 工程材料库 (19)5.2.2 ANSYS的优势 (19)1. 总体优势 (19)2. 行业市场 (19)3. 动力学与非线性的集成 (19)4. 显式动力学 (20)5. 复合材料计算 (20)6. 疲劳计算 (20)六. Fluent公司 (20)6.1 核心产品 (21)6.1.1 前处理 (21)6.1.2 求解器 (21)6.1.3 专用软件 (22)6.2 与ANSYS CFD的比较 (22)6.2.1 FLUENT的优势 (22)1. 行业市场 (22)2. 物理模型 (23)6.2.2 ANSYS CFD的优势 (23)1. 总体优势 (23)2. 行业市场 (23)3. 网格前处理 (23)4. 数值方法 (23)5. 收敛性能 (23)7. 物理模型 (24)8. 流固耦合 (24)七. ANSOFT公司 (24)7.1 核心产品 (24)1. HFSS (24)2. Designer (24)3. Nexxim (25)7.2 与ANSYS的比较 (25)7.2.1 Ansoft的优势 (25)1. 行业市场 (25)2. HFSS (25)3. Designer (26)7.2.2 ANSYS的优势 (26)1. 总体优势 (26)2. 行业市场 (26)3. 电大尺寸问题分析能力 (26)4. 天线分析与设计 (26)5. 天线布局分析 (27)6. 电磁隐身分析(RCS) (27)7. EMC/EMI (27)八. 总结 (27)8.1 CAE产品竞争系数 (27)8.2 结论 (28)一.CAE的定义计算机辅助工程(Computer Aided Engineering,CAE) 主要指用计算机对工程和产品进行性能与安全可靠性分析,对其未来的工作状态和运行行为进行仿真,及早发现设计缺陷,并证实未来工程、产品功能和性能的可用性与可靠性。
汽车开发过程中CAE技术的五大主要应用方向
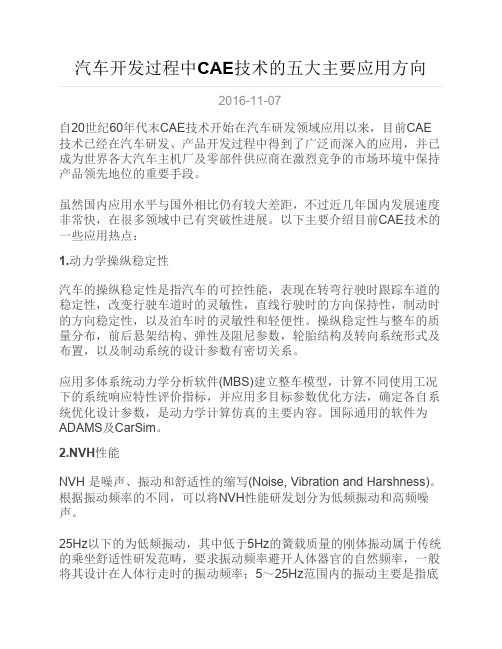
汽车开发过程中CAE技术的五大主要应用方向2016-11-07自20世纪60年代末CAE技术开始在汽车研发领域应用以来,目前CAE 技术已经在汽车研发、产品开发过程中得到了广泛而深入的应用,并已成为世界各大汽车主机厂及零部件供应商在激烈竞争的市场环境中保持产品领先地位的重要手段。
虽然国内应用水平与国外相比仍有较大差距,不过近几年国内发展速度非常快,在很多领域中已有突破性进展。
以下主要介绍目前CAE技术的一些应用热点:1.动力学操纵稳定性汽车的操纵稳定性是指汽车的可控性能,表现在转弯行驶时跟踪车道的稳定性,改变行驶车道时的灵敏性,直线行驶时的方向保持性,制动时的方向稳定性,以及泊车时的灵敏性和轻便性。
操纵稳定性与整车的质量分布,前后悬架结构、弹性及阻尼参数,轮胎结构及转向系统形式及布置,以及制动系统的设计参数有密切关系。
应用多体系统动力学分析软件(MBS)建立整车模型,计算不同使用工况下的系统响应特性评价指标,并应用多目标参数优化方法,确定各自系统优化设计参数,是动力学计算仿真的主要内容。
国际通用的软件为ADAMS及CarSim。
2.NVH性能NVH 是噪声、振动和舒适性的缩写(Noise, Vibration and Harshness)。
根据振动频率的不同,可以将NVH性能研发划分为低频振动和高频噪声。
25Hz以下的为低频振动,其中低于5Hz的簧载质量的刚体振动属于传统的乘坐舒适性研发范畴,要求振动频率避开人体器官的自然频率,一般将其设计在人体行走时的振动频率;5~25Hz范围内的振动主要是指底盘零部件、转向系统及发动机刚体的振动。
25Hz以上的振动及噪声,要解决的是车身的局部共振,制动器制动时产生的不稳定噪音,以及整车在路面(Road Noise)、传动系(Powertrain Noise),及高速驾驶时的风流(Wind Noise)激励下的共振现象,从而避免激励起乘员空腔的声学模态。
3.疲劳耐久性能疲劳耐久性能是指汽车在正常的使用条件下,各主要结构部件在功能失效前所经历的时间,评价指标为失效时的行驶里程数。
cae方面的好书

cae方面的好书
在CAE(计算机辅助工程)领域,有许多优秀的书籍可以作为学习和参考的资料。
这些书籍涵盖了从基础理论到实际应用的各个方面,对于想要深入了解CAE技术的读者来说,它们都是不可或缺的宝贵资源。
首先,我要推荐的是《有限元分析及应用》。
这本书是CAE领域的一部经典之作,系统介绍了有限元方法的基本原理和应用技术。
它通过丰富的实例和详细的步骤,引导读者逐步掌握有限元分析的核心内容,包括模型的建立、网格的划分、边界条件的设置以及结果的后处理等。
无论是初学者还是有一定基础的读者,都能从这本书中获得深刻的启发和实用的指导。
另一本值得一读的CAE好书是《计算流体力学基础及其应用》。
计算流体力学是CAE 领域的一个重要分支,广泛应用于航空航天、汽车工程、水利工程等领域。
这本书从流体力学的基本原理出发,详细介绍了计算流体力学的数值方法、离散化技术、湍流模型等关键内容。
同时,它还结合了大量的实际案例,帮助读者更好地理解计算流体力学在实际工程中的应用。
此外,对于对多物理场耦合分析感兴趣的读者,我推荐阅读《多物理场耦合分析方法及应用》。
多物理场耦合分析是近年来CAE领域的一个研究热点,它涉及多个物理场之间的相互作用和耦合效应。
这本书系统地介绍了多物理场耦合分析的基本原理、数值方法、软件实现等方面的内容,并通过具体的工程案例展示了多物理场耦合分析在实际应用中的巨大潜力。
总的来说,这些CAE方面的好书不仅为我们提供了丰富的理论知识和实践技能,还帮助我们更好地理解和应用CAE技术在实际工程中的价值。
无论你是初学者还是资深工程师,阅读这些书籍都将对你的职业发展和技能提升产生积极的影响。
2024年CAE软件市场调查报告
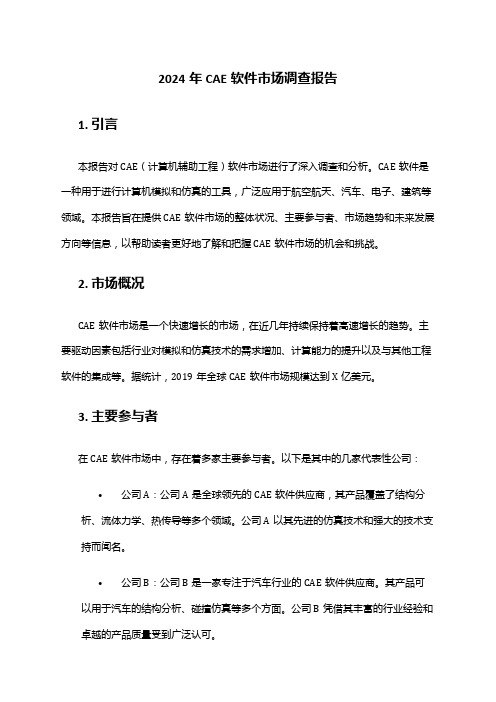
2024年CAE软件市场调查报告1. 引言本报告对CAE(计算机辅助工程)软件市场进行了深入调查和分析。
CAE软件是一种用于进行计算机模拟和仿真的工具,广泛应用于航空航天、汽车、电子、建筑等领域。
本报告旨在提供CAE软件市场的整体状况、主要参与者、市场趋势和未来发展方向等信息,以帮助读者更好地了解和把握CAE软件市场的机会和挑战。
2. 市场概况CAE软件市场是一个快速增长的市场,在近几年持续保持着高速增长的趋势。
主要驱动因素包括行业对模拟和仿真技术的需求增加、计算能力的提升以及与其他工程软件的集成等。
据统计,2019年全球CAE软件市场规模达到X亿美元。
3. 主要参与者在CAE软件市场中,存在着多家主要参与者。
以下是其中的几家代表性公司:•公司A:公司A是全球领先的CAE软件供应商,其产品覆盖了结构分析、流体力学、热传导等多个领域。
公司A以其先进的仿真技术和强大的技术支持而闻名。
•公司B:公司B是一家专注于汽车行业的CAE软件供应商。
其产品可以用于汽车的结构分析、碰撞仿真等多个方面。
公司B凭借其丰富的行业经验和卓越的产品质量受到广泛认可。
•公司C:公司C是一家提供综合CAE解决方案的供应商,其产品涵盖了结构、流体、电磁等多个领域。
公司C凭借其全面的产品线和灵活的定制服务受到了众多客户的青睐。
除了这些公司外,还有许多其他的CAE软件供应商也在市场中扮演着重要角色。
4. 市场趋势CAE软件市场中存在着多种市场趋势,以下是其中几个主要趋势:•云计算:随着云计算技术的发展,越来越多的CAE软件开始采用云计算模式。
云计算能够提供更高的计算能力和灵活性,使得CAE软件在效率和成本方面都得到了改善。
•人工智能:人工智能在CAE软件领域的应用也日益增多。
通过引入机器学习和深度学习等人工智能技术,CAE软件能够自动化模型构建和参数优化等过程,提高工程师的工作效率。
•行业应用拓展:除了传统的航空航天、汽车等行业外,CAE软件在其他行业中的应用也在不断扩大。
CAE技术及其航天领域的应用

CAE技术及其航天领域的应用CAE(计算机辅助工程)技术是一种通过计算机模拟和分析技术,用来帮助工程师在设计、开发和优化产品或系统过程中进行性能预测和验证的技术手段。
在航天领域,CAE技术发挥着重要作用,帮助解决了许多挑战,并提升了航天器的设计、制造和性能。
首先,CAE技术在航天领域的应用非常广泛。
航天器的设计和制造通常涉及复杂的物理学、力学和流体力学问题。
通过使用CAE软件,工程师可以通过建立数值模型,模拟航天器的运行环境和物理行为,预测和分析不同条件下的性能表现,如结构强度,热力学效应和空气动力学特性等。
这有助于工程师快速优化设计,减少试验成本,并提高工作效率。
其次,CAE技术在飞行动力学模拟、轨道设计和飞行控制方面也起着关键作用。
航天器的飞行特性、轨道选择、姿态控制和交会对接等问题需要进行复杂的计算和分析。
CAE技术可以通过数值模拟和仿真,评估不同飞行模式和控制策略的效果,帮助工程师制定合理的方案。
这有助于提高航天器的安全性和飞行效率,并减少操作风险。
此外,CAE技术还在航天器结构和材料方面发挥重要作用。
航天器需要经受极端的温度、压力和振动等环境,因此在设计航天器的结构时需要考虑到材料的力学性能和疲劳寿命等问题。
CAE技术可以通过建立数值模型,分析不同材料和结构设计对应力、应变和振动等因素的影响,预测和优化航天器的结构性能。
这有助于提高航天器的耐久性和可靠性,并减少结构故障的风险。
最后,CAE技术在航天器系统工程中也具有重要作用。
航天器的系统工程涉及多个子系统和组件之间的协调和集成,要求对整个系统进行综合性能分析和评估。
通过使用CAE软件,工程师可以建立整体的数值模型,模拟和预测不同子系统和组件之间的相互影响,以及整体系统在不同操作条件下的性能表现。
这有助于发现潜在的问题和优化点,并改进系统的整体性能。
总之,CAE技术在航天领域的应用可以帮助工程师进行航天器的设计、分析和优化,在结构、力学、热力学和飞行动力学等方面提供关键支持。
汽车开发中CAE技术的应用热点
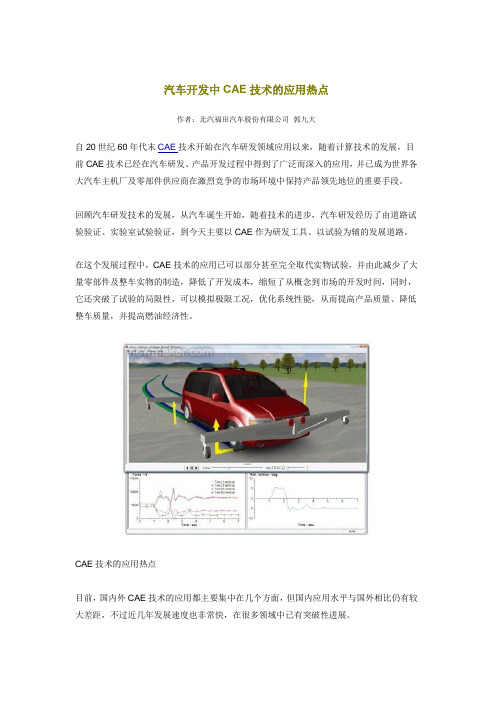
汽车开发中CAE技术的应用热点作者:北汽福田汽车股份有限公司郭九大自20世纪60年代末CAE技术开始在汽车研发领域应用以来,随着计算技术的发展,目前CAE技术已经在汽车研发、产品开发过程中得到了广泛而深入的应用,并已成为世界各大汽车主机厂及零部件供应商在激烈竞争的市场环境中保持产品领先地位的重要手段。
回顾汽车研发技术的发展,从汽车诞生开始,随着技术的进步,汽车研发经历了由道路试验验证、实验室试验验证,到今天主要以CAE作为研发工具、以试验为辅的发展道路。
在这个发展过程中,CAE技术的应用已可以部分甚至完全取代实物试验,并由此减少了大量零部件及整车实物的制造,降低了开发成本,缩短了从概念到市场的开发时间,同时,它还突破了试验的局限性,可以模拟极限工况,优化系统性能,从而提高产品质量、降低整车质量,并提高燃油经济性。
CAE技术的应用热点目前,国内外CAE技术的应用都主要集中在几个方面,但国内应用水平与国外相比仍有较大差距,不过近几年发展速度也非常快,在很多领域中已有突破性进展。
以下主要介绍目前CAE技术的一些应用热点:1. 动力学操纵稳定性汽车的操纵稳定性是指汽车的可控性能,表现在转弯行驶时跟踪车道的稳定性,改变行驶车道时的灵敏性,直线行驶时的方向保持性,制动时的方向稳定性,以及泊车时的灵敏性和轻便性。
操纵稳定性与整车的质量分布,前后悬架结构、弹性及阻尼参数,轮胎结构及转向系统形式及布置,以及制动系统的设计参数有密切关系。
应用多体系统动力学分析软件(MBS)建立整车模型,计算不同使用工况下的系统响应特性评价指标,并应用多目标参数优化方法,确定各自系统优化设计参数,是动力学计算仿真的主要内容。
国际通用的软件为ADAMS及CarSim。
2. NVH性能NVH 是噪声、振动和舒适性的缩写(Noise, Vibration and Harshness)。
根据振动频率的不同,可以将NVH性能研发划分为低频振动和高频噪声。
CAE技术的应用和发展趋势-大米的博客-中华工程师网
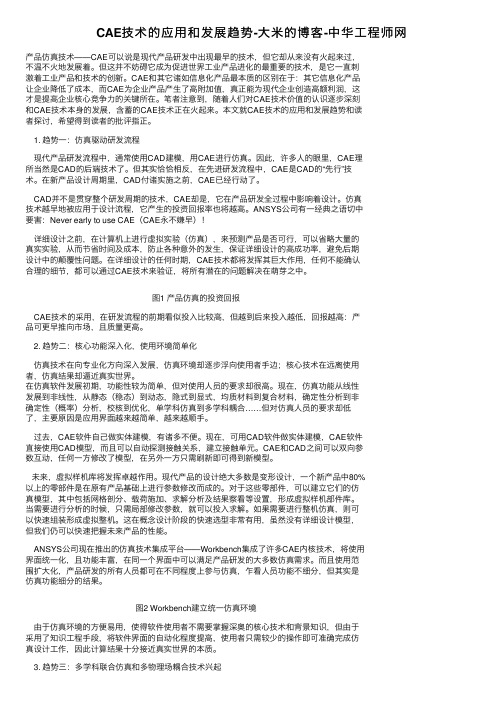
CAE技术的应⽤和发展趋势-⼤⽶的博客-中华⼯程师⽹产品仿真技术——CAE可以说是现代产品研发中出现最早的技术,但它却从来没有⽕起来过,不温不⽕地发展着。
但这并不妨碍它成为促进世界⼯业产品进化的最重要的技术,是它⼀直刺激着⼯业产品和技术的创新。
CAE和其它诸如信息化产品最本质的区别在于:其它信息化产品让企业降低了成本,⽽CAE为企业产品产⽣了⾼附加值,真正能为现代企业创造⾼额利润,这才是提⾼企业核⼼竞争⼒的关键所在。
笔者注意到,随着⼈们对CAE技术价值的认识逐步深刻和CAE技术本⾝的发展,含蓄的CAE技术正在⽕起来。
本⽂就CAE技术的应⽤和发展趋势和读者探讨,希望得到读者的批评指正。
1. 趋势⼀:仿真驱动研发流程现代产品研发流程中,通常使⽤CAD建模,⽤CAE进⾏仿真。
因此,许多⼈的眼⾥,CAE理所当然是CAD的后端技术了。
但其实恰恰相反,在先进研发流程中,CAE是CAD的“先⾏”技术。
在新产品设计周期⾥,CAD付诸实施之前,CAE已经⾏动了。
CAD并不是贯穿整个研发周期的技术,CAE却是,它在产品研发全过程中影响着设计。
仿真技术越早地被应⽤于设计流程,它产⽣的投资回报率也将越⾼。
ANSYS公司有⼀经典之语切中要害:Never early to use CAE(CAE永不嫌早)!详细设计之前,在计算机上进⾏虚拟实验(仿真),来预测产品是否可⾏,可以省略⼤量的真实实验,从⽽节省时间及成本,防⽌各种意外的发⽣,保证详细设计的⾼成功率,避免后期设计中的颠覆性问题。
在详细设计的任何时期,CAE技术都将发挥其巨⼤作⽤,任何不能确认合理的细节,都可以通过CAE技术来验证,将所有潜在的问题解决在萌芽之中。
图1 产品仿真的投资回报CAE技术的采⽤,在研发流程的前期看似投⼊⽐较⾼,但越到后来投⼊越低,回报越⾼:产品可更早推向市场,且质量更⾼。
2. 趋势⼆:核⼼功能深⼊化,使⽤环境简单化仿真技术在向专业化⽅向深⼊发展,仿真环境却逐步浮向使⽤者⼿边;核⼼技术在远离使⽤者,仿真结果却逼近真实世界。
计算机辅助工程三大市场热点

计算机辅助工程市场三大热点CAE(ComputerAidedEngineering),即计算机辅助工程,是广泛应用于工业制造业产品研发设计过程中的一种技术工具。
近5年来,中国CAE行业市场容量持续稳定释放,市场规模从2014年的23.4亿元增长至2018年的43.2亿元,年复合增长率为16.6%。
在“智能制造”所带动的制造业转型升级以及下游行业用户对CAE认知度和重视度持续提升的大背景下,CAE市场容量有望持续扩大,预计到2023年将达到112.5亿元。
热点一:CAE应用广泛、市场潜力大:CAE广泛应用于汽车、航空航天、国防军工、电子装备等制造业。
下游制造业的转型升级,为产品研发的效率、成本、可控性提出了更高的要求,消费者对于产品安全性、经济性、美观性等各方面性能指标的需求有助于推动CAE软件在功能性、可理解性、稳定性、可用性等方面性能的革新以及行业解决方案的专业度和定制化程度的提升。
热点二:关键技术的革新推动CAE软件水平提升:计算机图形技术、三维实体造型技术、数据交换技术、工程数据管理技术的革新是推动CAE软件水平提升的重要驱动力。
关键技术的革新持续推动了CAE软件水平的提升,主要体现在:(1)软件操作界面更加用户友好,用户可理解性和可交互性更强;(2)软件建模仿真时,模型的颗粒度更高、精细度更佳,保证了仿真分析的精确性和可参考性;(3)软件的数据处理和求解能力愈加强大,可满足愈加严苛的仿真需求等。
热点三:本土CAE软件发展未得到充分重视:本土CAE软件研发水平较低,在与外资CAE软件的竞争中处于下风,这与中国工业制造业水平受限、CAE软件发展未得到充分重视等因素有关。
外资CAE软件在业内具有较强的领先优势,主要得益于美国、德国等国的工业制造业水平进步,对于计算机仿真在国家制造业发展中的重视程度较高,以及政府主体在CAE软件开发方面资金、时间投入高等因素。
中国的制造业水平尚待提高,在精密设备、高端轴承、精密电机等高端领域的核心技术、工艺水平相对受限,这限制了工业知识、成果的代码化、软件化,制约了CAE的研发水平的提升。
CAE领域高性能计算发展分析
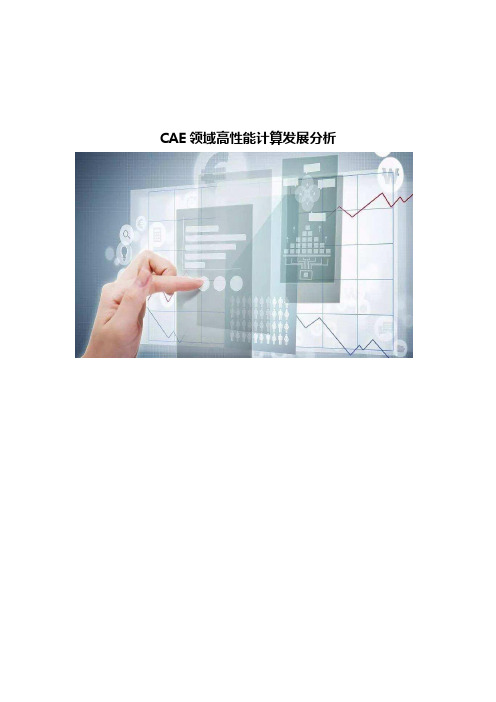
CAE领域高性能计算发展分析目录一、CAE简介 (1)1.1 什么是CAE (1)1.2 CAE产业链 (1)二、国外CAE技术发展历程 (2)三、国内CAE技术发展历程 (4)四、CAE软件发展历程 (6)4.1 CAE软件分类 (6)4.2 CAE软件基本框架 (7)4.3 CAE软件发展历程 (8)4.3.1 CAE软件发展历程 (8)4.3.2 CAE主要软件发展历程 (18)五、不同领域CAE仿真基本原理和相关软件介绍 (20)5.1力学仿真计算 (20)5.1.1计算固体力学 (20)5.1.2计算流体力学 (25)5.2电磁仿真计算 (29)5.2.1电磁仿真基本理论 (30)5.2.2常用电磁计算软件介绍 (33)5.3电子设计自动化 (34)5.3.1电子设计自动化仿真基本理论 (34)5.3.2常用电子自动化软件介绍 (36)六、CAE目前发展情况和发展趋势 (37)6.1 CAE技术发展趋势 (37)6.1.1 CAE技术相关功能发展趋势 (38)6.1.2 CAE技术的相关计算性能发展趋势 (39)6.1.3 CAE技术相关的软件技术的发展趋势 (40)6.1.4 CAE技术相关的用户界面的发展趋势 (41)6.1.5 CAE技术集成化、专业化与属地化的发展趋势 (41)6.2中国CAE市场现状分析 (41)七、CAE在高性能计算领域的需求分析 (44)7.1CAE高性能计算的计算节点需求分析 (44)7.1.1 通用高性能计算节点 (44)7.1.2胖节点 (46)7.1.3 GPU协处理器加速计算节点 (48)7.1.4 Intel Xeon Phi 协处理器计算节点 (50)7.2 CAE高性能计算对计算网络需求 (51)7.3 CAE高性能计算对存储系统需求 (53)7.4 CAE高性能计算对Portal及可视化作业需求 (53)7.5 CAE高性能计算对协同环境需求 (54)7.6 CAE高性能计算对远程3D虚拟桌面的需求 (54)一、CAE简介1.1 什么是CAE计算机辅助工程(CAE),从字面上讲它包括工程和制造业信息化的所有方面,但是传统的CAE主要指用计算机对工程和产品的功能、性能与安全可靠性进行计算、优化设计,对未来的工作状态和运行行为进行模拟仿真,及早发现设计缺陨,改进和优化设计方案,证实未来工程/产品的可用性与可靠性。
CAE技术的发展、应用及我国推广现状

CAE技术的发展、应用及我国推广现状[引言]:模具是生产各种工业产品的重要工艺装备,随着塑料工业的迅速发展以及塑料制品在航空、航天、电子、机械、船舶和汽车等工业部门的推广应用,产品对模具的要求越来越高,传统的模具设计方法已无法适应产品更新换代和提高质量的要求。
计算机辅助工程(CAE)技术已成为塑料产品开发、模具设计及产品加工中这些薄弱环节的最有效的途经。
同传统的模具设计相比,CAE技术无论在提高生产率、保证产品质量,还是在降低成本、减轻劳动强度等方面,都具有很大优越性。
近几年,CAE技术在汽车、家电、电子通讯、化工和日用品等领域逐步地得到了广泛应用。
一、CAE技术--模具设计的发展趋势目前,世界塑料成型CAE软件市场由美国上市公司Moldflow公司主导,该公司是专业从事注塑成型CAE软件和咨询公司,自1976年发行了世界上第一套流动分析软件以来,一直在此领域居领先地位。
利用CAE技术可以在模具加工前,在计算机上对整个注塑成型过程进行模拟分析,准确预测熔体的填充、保压、冷却情况,以及制品中的应力分布、分子和纤维取向分布、制品的收缩和翘曲变形等情况,以便设计者能尽早发现问题,及时修改制件和模具设计,而不是等到试模以后再返修模具。
这不仅是对传统模具设计方法的一次突破,而且对减少甚至避免模具返修报废、提高制品质量和降低成本等,都有着重大的技术经济意义。
在今天,塑料模具的设计不但要采用CAD技术,而且还要采用CAE技术。
这是发展的必然趋势。
注塑成型分两个阶段,即开发/设计阶段(包括产品设计、模具设计和模具制造)和生产阶段(包括购买材料、试模和成型)。
传统的注塑方法是在正式生产前,由于设计人员凭经验与直觉设计模具,模具装配完毕后,通常需要几次试模,发现问题后,不仅需要重新设置工艺参数,甚至还需要修改塑料制品和模具设计,这势必增加生产成本,延长产品开发周期。
采用CAE技术,可以完全代替试模,CAE技术提供了从制品设计到生产的完整解决方案,在模具制造之前,预测塑料熔体在型腔中的整个成型过程,帮助研判潜在的问题,有效地防止问题发生,大大缩短了开发周期,降低生产成本。
工程仿真CAE领域未来的三大技术趋势

工程仿真CAE领域未来的三大技术趋势计算机辅助工程(CAE)的世界在不断发展。
下一步该怎么办?与其他行业一样,大数据、物联网(IoT)、机器学习和数字孪生技术将给CAE领域带来重大转变。
(1)云计算技术将推动高性能仿真计算HPC的平民化以前只有通过大量的前期投资才能获得高性能计算机和仿真计算资源,现在工程师们更容易获得。
云计算技术在仿真软件的平民化中扮演着重要的角色,因为它可以远程访问这种强大的计算能力。
基于云的HPC资源还消除了对昂贵硬件和软件的投资需求,同时提供了比传统(通常昂贵)软件许可更灵活的定价模式。
云计算技术将对CAE的市场商业模式、软件应用模式产生重大影响。
云计算可能会引起所有人的注意,但软件容器的引入也推动了HPC更广泛的接受。
容器完全将操作系统、库和工具以及应用程序代码和用户数据捆绑在一起。
他们甚至可以持有工具来支持整个复杂的工程和科学工作流程。
这些容器设计为部署在本地或云中,大大减少了部署时间。
容器技术的下一个阶段可能会带来简化的用户界面和集成的仿真工作流程,使软件更加用户友好。
随着软件公司从传统的定价模式中走得更远,他们很可能会提供对培训和模板等资源的开放访问。
(2)机器学习技术超越现在的基于物理的仿真计算传统的基于物理的仿真模型是基于预先设定的原理或规则。
但是,获取大数据(例如物联网设备产生的)意味着有可能训练人工神经网络,产生预测性仿真模型。
将机器学习应用于仿真环境将有助于大大缩短求解时间,同时保持与传统解算器的大部分精度水平。
在未来几年,我们无疑将看到深度学习组件集成到仿真中,既可以为真实系统建模,也可以训练额外的人工智能组件。
同时,由于机器学习需要大量的数据,组织也很可能会处理与这些数据的生成和管理相关的问题。
最近的案例研究探讨了使用深度学习预测稳态流体流动的机理。
研究表明,较大的数据集可以加快神经网络的训练速度,提高人工神经网络预测能力的准确性。
虽然生成如此大量的数据需要大量的开销,但是可以通过在云中并行运行许多HPC模拟来抵消这一开销。
CAE技术及其航天领域的应用
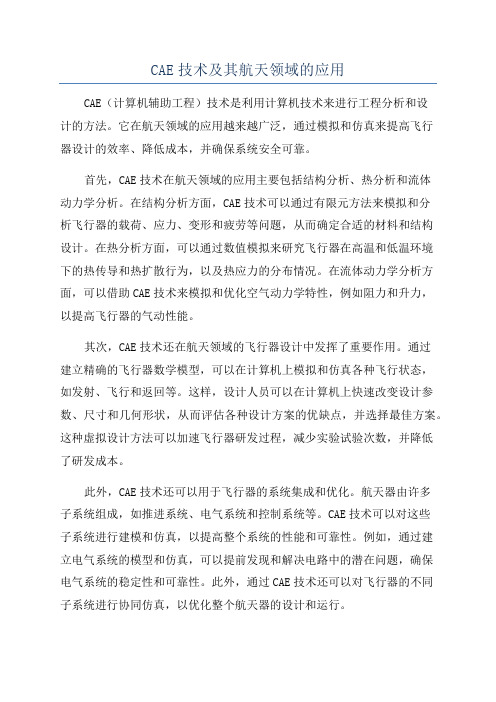
CAE技术及其航天领域的应用CAE(计算机辅助工程)技术是利用计算机技术来进行工程分析和设计的方法。
它在航天领域的应用越来越广泛,通过模拟和仿真来提高飞行器设计的效率、降低成本,并确保系统安全可靠。
首先,CAE技术在航天领域的应用主要包括结构分析、热分析和流体动力学分析。
在结构分析方面,CAE技术可以通过有限元方法来模拟和分析飞行器的载荷、应力、变形和疲劳等问题,从而确定合适的材料和结构设计。
在热分析方面,可以通过数值模拟来研究飞行器在高温和低温环境下的热传导和热扩散行为,以及热应力的分布情况。
在流体动力学分析方面,可以借助CAE技术来模拟和优化空气动力学特性,例如阻力和升力,以提高飞行器的气动性能。
其次,CAE技术还在航天领域的飞行器设计中发挥了重要作用。
通过建立精确的飞行器数学模型,可以在计算机上模拟和仿真各种飞行状态,如发射、飞行和返回等。
这样,设计人员可以在计算机上快速改变设计参数、尺寸和几何形状,从而评估各种设计方案的优缺点,并选择最佳方案。
这种虚拟设计方法可以加速飞行器研发过程,减少实验试验次数,并降低了研发成本。
此外,CAE技术还可以用于飞行器的系统集成和优化。
航天器由许多子系统组成,如推进系统、电气系统和控制系统等。
CAE技术可以对这些子系统进行建模和仿真,以提高整个系统的性能和可靠性。
例如,通过建立电气系统的模型和仿真,可以提前发现和解决电路中的潜在问题,确保电气系统的稳定性和可靠性。
此外,通过CAE技术还可以对飞行器的不同子系统进行协同仿真,以优化整个航天器的设计和运行。
总的来说,CAE技术在航天领域的应用有助于提高飞行器设计的效率和可靠性,并降低研发成本。
它可以通过模拟和仿真来优化结构设计、热分析和流体动力学分析,帮助设计人员选择最佳的设计方案。
此外,CAE 技术还可以用于飞行器的系统集成和优化,提高整个航天器的性能和可靠性。
随着计算机技术的不断发展和提高,CAE技术在航天领域的应用前景将会更加广阔。
CAE行业发展趋势分析(2021年)
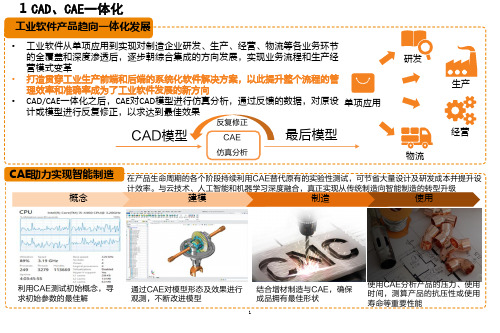
利用CAE测试初始概念,寻求初始参数的最佳解通过CAE对模型形态及效果进行观测,不断改进模型结合增材制造与CAE,确保成品拥有最佳形状使用CAE分析产品的压力、使用时间,测算产品的抗压性或使用寿命等重要性能12 兼并收购23 上云成为趋势工业软件发展阶段软件自身发展阶段软件协同应用工业云(软件+服务)目前,国外工业软件行业发展已经处于第三阶段,外资企业以达索、欧特克、西门子为代表已实现软件本身的技术积累,并在国家工业化的实践中实现软件的应用协同,实现流程串通和优化。
目前上述巨头均在向“软件+服务”的整体解决方案转型升级。
而中国的工业软件行业目前仍处于第一阶段,大量的设计、制造等核心工业软件均为国外品牌所占领,中国企业仍屈指可数,并且总体可以概括为“管理软件强、工程软件弱;低端软件多,高端软件少”。
在中国制造业转型升级的大背景下,工业企业均开始加快两化融合(工业化与信息化的融合)的步伐,逐步转变发展模式。
中国工业软件迅速实现第一阶段发展,向第二阶段转型成为大势所趋•由专业服务商提供云服务,无需自建服务器,省去了对服务器的维护成本•云服务器按需收费,按年收费,不需要为用不到的功能付费•便于进入新市场,实现新应用•新兴市场应用预测38-54亿美元配置的时间,真正做到即插即用•云服务器在云上具有无限可扩展性,数据空间不受限团队和更可靠的安全保障系统•几大云服务商在各个地区都有分散部署的服务器,且各服务器之间当遭遇灾祸时,可以进行及时的服务器切换,保证客户数据不丢失,灾备能力强交互管理,而企业上云之后,公司和不同工厂之间的数据都在云端。
云服务器可以统一对这些数据进行管理,实现厂间协同34中国特色发展模式:好风凭借力,送我上青云4风险因素:➢核心技术人员流失风险工业软件行业是技术密集型行业,非常依赖核心技术人员对行业发展趋势及研发方向的把控,同时也依赖于技术人员的研发落地能力。
若出现竞争对手恶意争抢,或其他因素导致核心技术人员流失,则可能导致公司无法保持技术领先性,对公司经营产生不利影响。
目前工程仿真热点
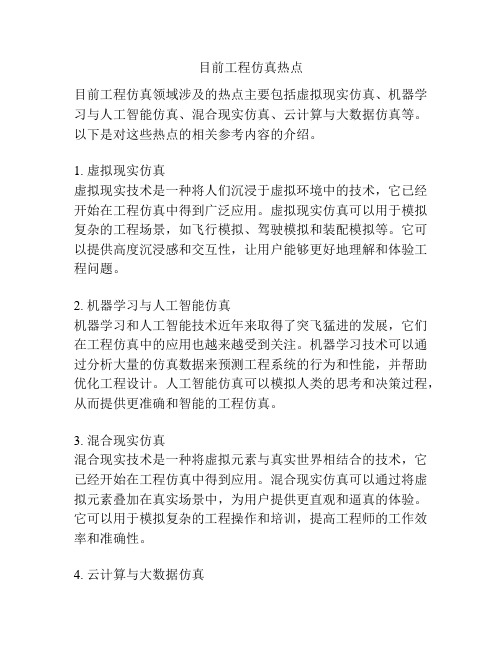
目前工程仿真热点目前工程仿真领域涉及的热点主要包括虚拟现实仿真、机器学习与人工智能仿真、混合现实仿真、云计算与大数据仿真等。
以下是对这些热点的相关参考内容的介绍。
1. 虚拟现实仿真虚拟现实技术是一种将人们沉浸于虚拟环境中的技术,它已经开始在工程仿真中得到广泛应用。
虚拟现实仿真可以用于模拟复杂的工程场景,如飞行模拟、驾驶模拟和装配模拟等。
它可以提供高度沉浸感和交互性,让用户能够更好地理解和体验工程问题。
2. 机器学习与人工智能仿真机器学习和人工智能技术近年来取得了突飞猛进的发展,它们在工程仿真中的应用也越来越受到关注。
机器学习技术可以通过分析大量的仿真数据来预测工程系统的行为和性能,并帮助优化工程设计。
人工智能仿真可以模拟人类的思考和决策过程,从而提供更准确和智能的工程仿真。
3. 混合现实仿真混合现实技术是一种将虚拟元素与真实世界相结合的技术,它已经开始在工程仿真中得到应用。
混合现实仿真可以通过将虚拟元素叠加在真实场景中,为用户提供更直观和逼真的体验。
它可以用于模拟复杂的工程操作和培训,提高工程师的工作效率和准确性。
4. 云计算与大数据仿真随着云计算和大数据技术的发展,它们在工程仿真中的应用也逐渐扩大。
云计算技术可以提供强大的计算和存储能力,使得工程仿真可以在云端进行,并提供更高效和灵活的仿真服务。
大数据技术可以分析和处理海量的仿真数据,从中挖掘有价值的信息,为工程设计和决策提供支持。
以上是目前工程仿真领域的一些热点研究方向和应用领域的简单介绍。
随着技术的不断进步和应用的深入,工程仿真将会在更广泛的领域得到应用,为工程设计和决策提供更强大的支持。
汽车工业中的CAE技术

汽车工业中的CAE技术张早明,邸建卫,肖杰,李思远上海同济同捷科技有限公司,上海(201206)E-mail: zhangzm1982@摘要:本文总结了汽车设计和汽车制造中的八大CAE技术的应用内容、常用软件及应用实例,进一步提出了未来汽车工业中CAE技术的发展趋势。
关键词:汽车;CAE;发展中图分类号:TP391.731 引言汽车行业是一个高速发展的行业,其竞争也日趋激烈,在这种情况下,新产品推出的速度也越来越快,这也对行业的CAE应用提出了越来越高的要求[1]。
CAE技术为汽车行业的高速发展提供了具有中心价值地位的技术保障,CAE在产品设计的质量、寿命、性能和成本等方面发挥着重要的作用,可以为企业带来巨大的技术经济效益[2]。
CAE技术在国内汽车工业的应用经历了入门、推广、普及等阶段,目前已经到了取得实质效益的阶段[3,4]。
本文从汽车设计和汽车制造两大方面介绍了汽车工业中八大CAE技术的应用。
2 CAE在汽车工业中的应用领域汽车设计和汽车制造是汽车工业中的两个重要组成部分,是一个有机整体,是一个系统工程;汽车设计是前提和基础,汽车制造将设计完成的汽车转化为实物,制造能力很大程度上决定了汽车设计的方式、水平。
如果没有优秀的汽车设计,即使拥有再好的汽车制造能力,也没办法生产出高质量的汽车;反之,无论设计多么优秀的汽车,没有与之匹配的制造工艺,能力,那也只能是一堆没有用的数据而已。
同样地,汽车工业中的CAE技术应该包含两大类:汽车设计CAE技术和汽车制造CAE 技术,两者是组成一个有机系统,相互促进,缺一不可。
2.1. 结构、疲劳、NVH分析结构、疲劳分析主要包含整车,各子系统,各零部件的模态、刚度、强度、疲劳分析。
例如:白车身,副车架,后桥、吊挂、安全带支架等零部件的模态,刚度,强度[5,6]。
NVH是指影响汽车乘坐和使用环境等重要因素的振动噪声性能[7,8]。
主要的分析软件有:nastran,abaqus,fatigue等。
CAE技术的应用热点

CAE技术的应用热点
郭九大
【期刊名称】《汽车制造业》
【年(卷),期】2008(000)019
【摘要】随着CAE技汽车研发领域的广泛应用,目前它已成为世界各大汽车主机厂及零部件供应商在竞争中保持产品领先地位的重要手段。
随着计算技术的发展以及汽车主机厂在CAE分析验证方面经验的不断积累,CAE分析将可以完全取代试验,使整个汽车研发在虚拟环境下的完成成为可能。
【总页数】3页(P90,92,93)
【作者】郭九大
【作者单位】北汽福田汽车股份有限公司工程研究院
【正文语种】中文
【中图分类】TQ320.662
【相关文献】
1.CAE技术系列应用案例(8)--大连重工CAE技术系列应用案例 [J], 李春亭
2.CAE技术系列应用案例(7)--大连重工CAE技术系列应用案例 [J], 李春亭
3.CAE技术系列应用案例(2)--大连重工CAE技术系列应用案例 [J],
4.CAE技术系列应用案例(7)--大连重工CAE技术系列应用案例 [J], 李春亭
5.“2011大连市计算机辅助工程(CAE)技术与应用研讨会暨第1届英特仿真CAE 技术与应用年会”通知 [J],
因版权原因,仅展示原文概要,查看原文内容请购买。
- 1、下载文档前请自行甄别文档内容的完整性,平台不提供额外的编辑、内容补充、找答案等附加服务。
- 2、"仅部分预览"的文档,不可在线预览部分如存在完整性等问题,可反馈申请退款(可完整预览的文档不适用该条件!)。
- 3、如文档侵犯您的权益,请联系客服反馈,我们会尽快为您处理(人工客服工作时间:9:00-18:30)。
2007CAE领域八大热点7月28~29日,第三届CAE工程分析年会在大连举行,参会人数大大超过往届年会,这从一个侧面反映出CAE正受到业界越来越多的关注,预计CAE应用的广度和深度也都将扩大。
通过此次年会以及后续的采访和沟通我们发现,当前CAE在产品、技术、应用等方面表现出一些值得关注的热点。
●CAE与CAD的集成●多物理场耦合●仿真数据的管理●专业化软件的发展●CAE知识积累●有限元模型越来越大●中低端市场升温●自主开发之痛汽车行业是当前国内参与国际化市场竞争最充分的行业之一,奇瑞公司则成为该行业自主创新的排头兵。
在国内同行中,奇瑞率先成立了CAE部门。
得益于此,奇瑞大大缩短了产品开发周期,提高了产品开发质量,这使得奇瑞每年能够推出数款全新的产品。
展望未来,奇瑞每年推出数十款新的汽车产品也并不是没有可能。
奇瑞汽车有限公司总经理助理、汽车工程研究院院长顾镭说:“由于引入CAE技术,我们能够避免在设计中走弯路,在开发初期就预测未来的产品性能,这是做好正向开发的前提。
通过计算机仿真替代样车试验,节省了大量样车和试验费用。
模拟过程具备再现性,可帮助工程师发现实车试验无法观察的细节问题。
而对于设计方案选择和多目标优化,CAE技术更是效果显著。
”应用永远是产品技术发展方向的风向标。
在CAE深化和普及的状态下,CAE软件在市场、技术等方面的一些特点值得用户共同关注,比如,第一飞机设计研究院研究员宁振波在分析CAE领域的一系列收购事件后认为,CAE产业将迎来一次整合的浪潮,他说:“三维普及以后解决了几何模型的问题,那么解决性能和功能的CAE软件将会得到大范围应用,我认为今后10到15年是将CAE软件整合的过程。
”本次综合报道,我们采访了7位专家,并以问答的形式,向读者展示了CAE八个方面的热点。
这7位专家分别是:第一飞机设计研究院研究员宁振波、中国铁道科学研究院研发中心机车车辆部常务副主任王成国、奇瑞汽车有限公司总经理助理/汽车工程研究院院长顾镭、中科院数学与系统科学研究院研究员/飞箭软件总工程师梁国平、ANSYS-FluentChina总经理蒋辉国、UGS PLM Software亚太区市场副总裁Ron Close和澳汰尔总经理戚国焕。
CAE与CAD的集成《e制造》:CAE与CAD的集成是当前CAE应用中亟需解决的问题,那么目前集成的现状如何?是否存在一些挑战?宁振波:CAD与CAE的集成是一个必然的发展趋势。
以前的CAE分析仅限于非常简单的计算,如果要知道产品的功能和性能的话,必须要造出样品,然后才能进行试验,从而进一步把产品的功能和性能确定下来。
而现在三维设计已经比较普遍了。
通过三维设计生成数字化模型之后,就比较接近于真实的物理模型,模型中可以加入材料数据,外形也比较精准。
以飞机为例,就可以利用数字化模型在计算机上进行数字风洞试验,代替了以前的物理样车。
这些的基础是三维设计。
从软件角度,分析软件主要集中在三大类,首先是流体,包括大气、气流、水流等,然后是结构,包括可靠性和安全性等,第三块是电磁场,光场是很小的一块。
CAD与CAE的集成中,流场已经集成得非常好了,比如Fluent专门开发了一款产品Fluent for CATIA,我们用CA TIA设计飞机外形之后,可以直接用Fluent进行流体计算。
结构方面,CATIA中有几款网格画分的模块,包括面单元,体单元,装配体单元,设计的CAD模型可以直接画分网格,这之后,可以用其他软件直接分析,进行后台计算。
王成国:高速列车是现代工业的标致性产品。
我曾经参观过国外高速列车制造企业,其车厢制造加工已经实现CAE与CAD的集成技术,对其保证产品质量发挥重要作用。
但是我认为,CAE与CAD的集成是当前CAE应用中亟需解决的问题之一,原因有三:第一,CAE与CAD的集成有利于推动我国机械行业CAE应用技术的整体发展。
CAD不仅是CAE的重要组成部分,而且是CAE发展的基石。
CAD与有限元的集成可以提高计算精度,CAD与自动加工设备的集成可以提高制造精度,CAD与生产过程控制的集成可以提高产品质量。
CAE与CAD的集成可以借助CAD已有的技术平台,整合技术队伍,提高技术水平,推动我国机械行业CAE的迅速发展。
其次,有利于降低我国机械行业实施CAE技术的成本。
目前,机械工程领域的企业,已经普遍认识到CAE技术是现代企业核心竞争力的重要组成部分。
然而,企业领导层必须考虑实施CAE的经济成本和实际生产效益。
CAE与CAD的集成有利于降低企业采购、应用、维护和升级费用,这对于发展中的我国机械行业尤其具有现实意义。
第三,有利于CAE技术的理论方法进一步发展和提高。
在CAE与CAD的集成过程中,会碰到许多新问题。
企业根据自己具体的产品特点和生产情况,要求CAE的使用更方便、运行更快捷、理论更完备、模型更可靠、结果更实用。
大量实际工程要求是CAE技术进一步发展的强大推动力。
国际一流机械制造企业与CAE商业软件公司紧密合作,在CAE与CAD的集成应用方面已经取得实效并不断深入。
福特汽车公司与MDI关于ADAMS软件开发和应用的成功合作是一个非常典型的事例。
国内机械行业面临机构设置、技术队伍、实际应用等诸多问题急需解决。
我认为,CAE与CAD的集成在最近十年内将有显著的进展。
相信我国机械制造行业会抓住目前的有利发展时机。
顾镭:CAE与CAD的集成是当前CAE应用中亟需解决的问题,因为CAD数据更新必须在CAE模型中及时体现出来,这样才能够给设计人员有效地提供支持。
传统的、相互割裂的方法往往会导致CAE工作一定的滞后,即便做一个很小的设计更改也必须去做一个新的计算模型,人工设定一次新的运算,不仅有时效性问题,而且还会带来数据存储方面的问题。
二者的集成,可以实现CAD与CAE之间工程数据的共享,使耗时较大的CAE建模工作量大大减少,提高分析效率,而且让设计师也能够做简单的分析工作,从而更好地发挥设计创意。
目前,应该说一部分工作已经实现集成了。
有的是通过客户化方法来定义批处理流程手段,有的是基于参数化方法,有的是面向单个零件的分析与优化,但从严格意义上来说,两者之间完整的(能够面向整车的)集成还是没有能够达到。
由于CAE和CAD两者的侧重点是不同的——CAD主要侧重于几何信息表达,CAE是运用力学与数学方法描述事物性能,CAE分析必须有一个提炼和生成模型的过程,需要综合CAD 数据与应用工况以及边界状态等信息,这其中涉及对几何、材料、物理与力学等抽象与集成,特别是整车系统必须考虑各种复杂工况,所以需要通过人的大量的思维活动来完成,实现CAD-CAE集成是一个长期的过程。
两者完全融合今后也是难以达到的。
梁国平:CAD与CAE的集成的确是一个很大的趋势。
过去采用的CAE,实际上是一个CAD 再加上一个通用CAE软件,这是很初级的,其趋势是应该集成到一块,二者应该是无缝连接的。
不同的行业不同的企业,采用的CAD软件也都不同,因此很多软件厂商在集成方面的努力市场前景还不确定。
企业也越来越要求在整个PLM过程中进行CAE分析。
用户一般在集成时进行二次开发。
但是中国的用户本身的开发能力很有限,所以一般是采用与软件提供商合作的方式,这种方式比较容易成功。
另外,企业在旧有的CAE软件基础上进行集成恐怕会很困难,因为旧软件不一定支持二次开发。
所以,集成的挑战,主要在于用户自己的技术力量。
Ron:以往的CAE分析与CAD设计割裂,导致了以下三个主要问题:1、CAD设计发生变化时,部件或装配件的CAE模型更新变得十分困难;2、CAE结果不能反映最新的CAD设计特征;3、得到CAE计算的时间太晚,结果CAE不能及时地用于优化产品设计。
这些问题导致时间、人力和物力的浪费。
市场竞争的压力要求厂商进一步缩短产品设计时间,并节省成本,因此CAD与CAE的集成势在必行。
国内的一些汽车厂商发现自己的CAE工程师花费大量的时间在CAE模型准备上,这不但造成资源的严重浪费,而且严重的影响设计进度,使得工程师失去了产品创新的时间。
造成这种现象的根本原因就是,CAE分析和CAD设计的割裂。
现在的应用情况是,CAE分析工程师所需的几何数据和CAD部门的原始几何数据不能建立直接的联系,这打破了CAD和CAE数据的关联性,造成了不必要的浪费。
因此只有把CAD与CAE集成起来,然后有一个统一的数据管理平台,比如UGS Teamcenter,进行集中管理,保持CAD和CAE数据的关联性,才可以使CAE的分析结果及时的指导产品设计。
因为NX可以在Multi-CAD环境下工作,所以在CAE环境下访问,创建、修改和修补几何体,是我们与其他仿真软件供应商的主要区别。
蒋辉国:集成主要解决的是CAE的方便性和普及性的问题。
作为复杂的专业性领域,目前大多数分析问题还是由专业性软件来解决。
在工程设计中,也有这种集成在CAD软件中的普及型CAE软件,比如说我们的Fluent for CATIA,这套软件基本上Fluent的全套功能都集成在CATIA中了,在设计的时候,如果需要初步检验设计是否合理,只需要点击Fluent的一些功能就可以进行相应的流体力学分析。
还有一些其他的软件具有或多或少的CAD与CAE集成功能。
在结构分析领域,与CAD结合的CAE软件相对多一些,因为结构分析的技术相对成熟,矛盾的焦点集中在怎么样方便使用。
对流体力学分析领域,有些问题已经可以实现非常准确的模拟,对于此类问题,CAD与CAE的集成将有利于提高效率和推广CAE的应用。
而对于一些复杂的流体力学问题,模拟的精度即物理问题的数学描述模型的准确性是目前亟待解决的主要问题。
戚国焕:CAD与CAE的集成目前是一个很大的问题。
CAD与CAE,和CAD与CAM,这两种集成,差距非常大,后者的集成现在做得非常好,真正体现了设计工艺的一体化。
由于CAD几何模型到CAE中做网格的时候,并不是直接使用,而是要先进行几何清理,目的是达到一个平衡,就是在网格质量足够好的情况下,使网格数量适当少一些。
几何清理对CAE非常重要,但对一体化却造成影响,因为几何清理之后,网格关联性就被破坏了,那么一体化就不存在了。
现在二者的联系存在两种状态,第一种,从有限元角度来说,CAD与CAE割裂的状态没有改变,有些厂商宣称可以做到一体化,我认为实际上有一定的误导。
因为一体化牺牲了单元和求解的质量,这样使得分析的实用性大大降低,因此就没有价值了。
为了解决这个问题,我们发展了一些另外的技术来弥补这个问题,就是我们的“自动网格变更”。
当CAD大致定稿之后,做CAE分析实际上还要进行一些结构等方面的变更,这种变化我们不把它反映到CAD中,而是直接在网格上进行,在变化的过程中进行分析,当分析结果比较合理以后,再把定稿的结果抽取出来,返回到CAD中进行调整。