喷丸强化标准
喷丸处理规范

NOV 喷丸处理规范
一、喷丸处理类型
喷丸处理型号喷丸尺寸强度(mm) 试片类型是否遮盖NSPS-100-2 S-110 0.28-0.33 A 是
二、预处理
1.喷丸零件需去除污渍如油脂,污垢,油腐蚀,以及防腐镀层如阳极涂层,镀层或者油漆。
2.喷丸硬度不得低于45HRC。
三、质量保证及过程控制
1.测试片与其它喷丸件一起进行喷丸处理,用来检测喷丸强度。
此测试需在喷丸开始和结束以及者喷丸过程中每隔8小时进行,以较短时间为准。
更换零件种类时也要在开始和结束时分别喷试片。
2.喷丸介质必须大小形状统一(理论为球形),同时保证有锐边或者损坏.定时检查喷丸过程,需保证喷丸的均匀性,从而保证小于10%的砂球变形或者损坏。
3.为每个零件号和能够生产出合格件的控制因素参数建立档案.同时,控制因素必须记录在案,除过程的参数变化外,还包括下列数据:
机器类型(气动型或者离心型);
喷嘴或转轮数目;
喷嘴或者转轮大;
喷嘴或喷丸口位置;;
空气压力或者转轮速度rpm(转/分钟);
喷嘴(或转轮)-到-工件距离(或者控制程序参考数目)
喷丸介质类型,硬度,大小
工件平移和旋转速度
工作过程中测试片位置
喷丸时间
计量孔大(仅限于气动机器)
测试片类型( A,N,C)
夹紧和遮蔽装置
六、文件
文件须记录零件已据最新版本的规范要求进行了喷丸处理以及相关检验,并需遵循认可的检测要求. 报告需包括下列各项:
1.采购订单号
2.批号
3.零件号
4.零件数量
5.零件系列号
6.过程控制参数报告(参照3.3)。
(喷丸标准)jbt10174
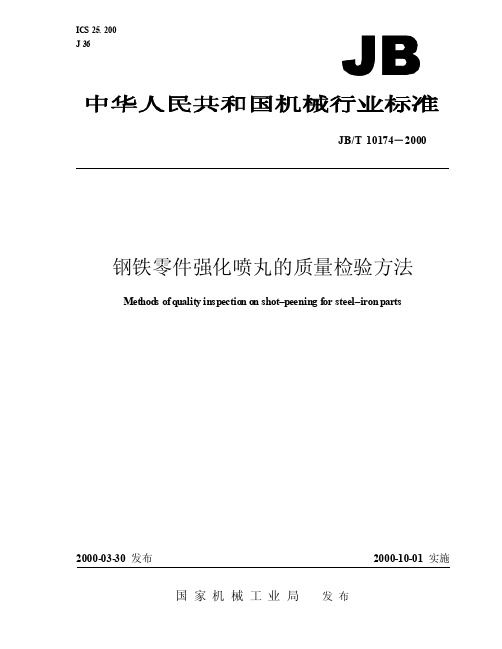
YB/T 5058—1993 弹簧钢、工具钢冷轧钢带
YB/T 5149—1993 铸钢丸
3 定义
本标准采用下列定义。 3. 1 强化喷丸 shot–peening
将高速弹丸喷射到钢铁零件表面,使其表面层在弹丸的冲击作用下发生塑性变形,由此产生强化 及表面压应力,使钢铁零件的抗疲劳性能及耐应力腐蚀抗力均得到改善。 3. 2 弧高度试片 almen 弧高度试片是综合测量强化喷丸工艺参数的一种专用量规,用弹簧钢(应符合 YB/T 5058 的有关 规定)制成,共有三种尺寸,其型号分别是:N、A、C。 3. 3 弧高值 arc high value 将标准的阿尔门试片固定在夹具上,进行单面强化喷丸,弧高度试片在弹丸的冲击下,表面发生 塑性变形,导致试片向喷丸面呈球面状弯曲,再用弧高度测量仪测量试片弯曲弧高度。 3. 4 喷射时间 shot time 受喷零件在喷丸过程中,从开始喷丸到受喷部位达到 100%覆盖率时所需的喷丸时间。 3. 5 喷丸强度 shot strength 计量弹丸冲击金属表面程度的一项指标,它是许多工艺参数(如零件材料、弹丸大小、弹丸性能、 喷射速度和喷丸时间等)的函数。喷丸强度一般是以弧高度试片(阿尔门试片)在双倍喷射时间 下产生的弧高增加值小于或等于 10% 所对应的覆盖率至少为 100% 时,所产生的弧高增加值来 表示。
—
—
—
—
—
—
全通 过 止 10% (max)
—
— 止 85% (min) 止 97% (min)
—
80
0.180
—
—
—
—
—
100
0.125
—
—
—
—
—
注 1 ZG100、 ZG85表 示铸 钢弹 丸尺寸 分别 为φ 1.0 mm 和 φ0.85 mm 的 弹丸 。 2 max、min 表 示应留 方孔 筛网 上丸 粒积累 量的 最大 值和 最小值 。
如何选用喷(抛)丸强化介质

如何选用喷(抛)丸强化介质Keynes khu喷(抛)丸强化工艺技术与锻、铸、焊、热处理、切削等工艺技术一样是用于对金属零部件加工的一种制造工艺技术.但它与上述常规加工工艺不同的是,它既不对工件表面进行切削,更不使工件发生几何形状与尺寸变化,它只是在工件外表层(厚约0.2-1.0mm )发生非均匀的循环塑性变形的过程中,使工件表层发生①显微组织结构改性;②引入残余压应力场.喷丸强化是高速运动(70~90m/s)弹丸流冲击工件表面的过程.此间表层循环塑性变形过程中材料发生循环硬/软化,导致表层显微组织结构改性(晶粒,亚晶粒以及位错组态等变化)同时引入残余压应力场.循环硬化的组织结构与残余压应力是提高零部件表面完整性(Surface Integrity- SI)的两个极为重要的因素.喷丸强化处理有三大要素:1.喷丸强化设备及其附件;2.喷丸强化介质-各种类型的弹丸;3.喷丸强化工艺:强化工艺参数与疲劳强度(寿命)间的关系。
我们可将磨料大致分为金属磨料和非金属磨料,金属磨料有以下几种:铸钢丸、钢丝制强化钢丸、不锈钢丸;非金属磨料有陶瓷丸、玻璃丸等。
今天我们一起来探讨一下如何正确选用喷(抛)丸强化的磨料:在选择磨料时我们除了关注它们是否满足尺寸、硬度、形状的要求之外,我们一般还遵循以下三个原则:1.满足喷(抛)丸强化的规范要求;2.能维持喷(抛)丸强化的强度;3.要防止喷(抛)丸强化时工件的表面受损;我们对照此三项原则,将以上几种的磨料一一和大家做个分析:铸钢丸铸钢丸的价格便宜,但由于它的制造工艺决定了它本身很多无法改变的缺点:内部空心多、重叠的双球面、形状不规则球多,所以如果选择用铸钢丸作为喷(抛)丸强化的介质的话前期要先去除这些不规则的钢丸,而且在使用过程中要及时不断地清理出已经破碎的钢丸或已变小的钢丸,这样才能维持好喷(抛)丸强化的强度,所以钢丸用量会比较大,而且设备维修清理的频率较高。
有的客户甚至只将铸钢丸用1-2次,就清空换新的一批钢丸。
强力喷丸检测标准
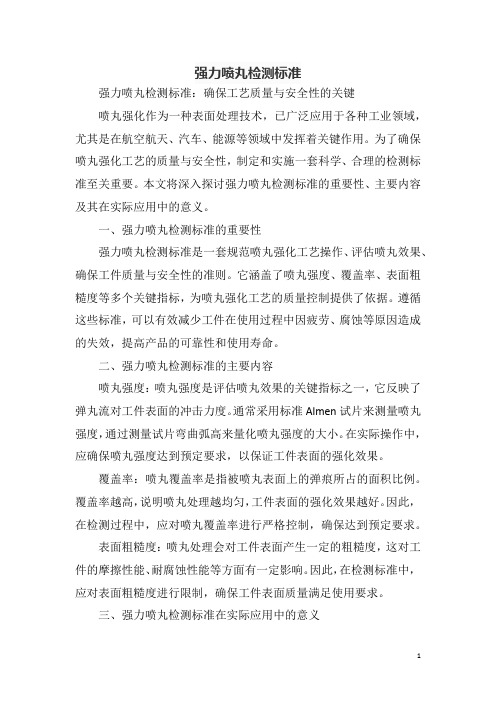
强力喷丸检测标准强力喷丸检测标准:确保工艺质量与安全性的关键喷丸强化作为一种表面处理技术,已广泛应用于各种工业领域,尤其是在航空航天、汽车、能源等领域中发挥着关键作用。
为了确保喷丸强化工艺的质量与安全性,制定和实施一套科学、合理的检测标准至关重要。
本文将深入探讨强力喷丸检测标准的重要性、主要内容及其在实际应用中的意义。
一、强力喷丸检测标准的重要性强力喷丸检测标准是一套规范喷丸强化工艺操作、评估喷丸效果、确保工件质量与安全性的准则。
它涵盖了喷丸强度、覆盖率、表面粗糙度等多个关键指标,为喷丸强化工艺的质量控制提供了依据。
遵循这些标准,可以有效减少工件在使用过程中因疲劳、腐蚀等原因造成的失效,提高产品的可靠性和使用寿命。
二、强力喷丸检测标准的主要内容喷丸强度:喷丸强度是评估喷丸效果的关键指标之一,它反映了弹丸流对工件表面的冲击力度。
通常采用标准Almen试片来测量喷丸强度,通过测量试片弯曲弧高来量化喷丸强度的大小。
在实际操作中,应确保喷丸强度达到预定要求,以保证工件表面的强化效果。
覆盖率:喷丸覆盖率是指被喷丸表面上的弹痕所占的面积比例。
覆盖率越高,说明喷丸处理越均匀,工件表面的强化效果越好。
因此,在检测过程中,应对喷丸覆盖率进行严格控制,确保达到预定要求。
表面粗糙度:喷丸处理会对工件表面产生一定的粗糙度,这对工件的摩擦性能、耐腐蚀性能等方面有一定影响。
因此,在检测标准中,应对表面粗糙度进行限制,确保工件表面质量满足使用要求。
三、强力喷丸检测标准在实际应用中的意义遵循强力喷丸检测标准,不仅可以提高喷丸强化工艺的质量与安全性,还有助于降低生产成本、提高生产效率。
在实际应用中,企业应结合自身生产需求和工艺特点,制定适合自己的喷丸检测标准,并加强员工培训,确保操作规范、检测准确。
总之,强力喷丸检测标准是确保喷丸强化工艺质量与安全性的关键。
通过遵循这些标准,企业可以生产出更可靠、更耐用的产品,提高客户满意度和市场竞争力。
金属零件喷丸标准AMS

金属零件喷丸标准AMS-S-13165(中文翻译)发布时间:2018/10/14 15:00:24金属零部件喷丸这项标准直接引用美国军方标准:MIL-S-13165c ,修正1 ,在编辑和形式上做了一些微小的变动,从而与 SAE 公开出版的技术标准达到一致。
经SAE 技术标准管理委员会的决定,原来的军方技术说明才被采纳为 SAE 标准。
1范围1.1范围这份说明包括喷丸的加工要求, 在物体表面产生残余压力,目的是为了提高物体抗疲劳寿命, 抗压性和耐磨性(见 6.1 )。
2应用文件以下文件,在文件生效期内构成了该标准的一部分。
2.1 美国官方出版的文件来源于PA 19111-5094 费城700罗宾大街4楼,期刊订阅服务中心,DODSSP 。
钢砂,钢丸,钢丝切丸,铁砂 ,抛丸清理和喷砂。
武器装备的金属表面处理和无机涂层 用来清理和喷砂的玻璃丸 校准系统要求 筛网,检测2.2 SAE 出版的文件来源于SAE , 400联合装置,沃伦, PA15096-0001 J441 钢丝切丸 J1830喷砂用的瓷丸3要求MIL-S-851 MIL-S-5002 MIL-G-9954 MIL-STD-45662 RR-S-3663.1.1 材质。
丸子用铸铁,铸钢,钢丝、不锈钢丝、玻璃或塑料等允许的材质制成。
由不同方法测出的硬度都可转化成洛式硬度。
钢丸和铁丸应符合MIL-S-851 标准。
对于强度大于200 000Psi的钢部件,如果没有特别说明,使用的钢丸硬度范围应在55-65HRC 之间,或者硬度在57-63HRC 之间的瓷丸。
302或304 (B条件回火弹簧)材质的不锈钢丝切丸和碳钢丝切丸应该与SAE J441 标准一致。
玻壬^珠应满足SAE J1830 标准的要求。
3.1.2 规格。
如果购货方没有具体要求,装入机器里的丸子规格,无论是新的,使用过的,或是再提炼的丸子,应与表n中(铸钢丸规格)、表出(切丸规格)、表W (玻璃珠规格)和表v (瓷丸的规格)的要求一致。
齿轮强化喷丸残余应力要求

齿轮强化喷丸残余应力要求
齿轮强化喷丸的残余应力要求主要包括以下几个方面:
1. 残余压应力:喷丸处理后,齿轮表面应形成一定的残余压应力。
根据不同的应用要求和工艺条件,残余压应力的范围应在50μm处-700MPa至-900MPa之间。
2. 深度范围:在某个深度范围内,应至少达到产品规定的最小残余应力值。
3. 检测方法:残余应力的检测通常采用X射线衍射法。
这种方法是非破坏性的,可测定表层10~35um内的应力。
此外,还可以采用机械法、电阻法、声学法等其他方法进行检测。
4. 检测位置:残余应力检测的位置应按照用户规定的零件要求进行选择。
5. 稳定性控制:在生产过程中,通常通过检测试片弧高值的稳定性来进行控制。
总的来说,这些要求是为了确保齿轮强化喷丸处理能够达到所需的表面质量和性能,以满足各种应用场景的需求。
具体的参数和要求应根据实际工艺条件和用户需求进行确定。
金属表面处理—喷丸、抛丸、喷砂
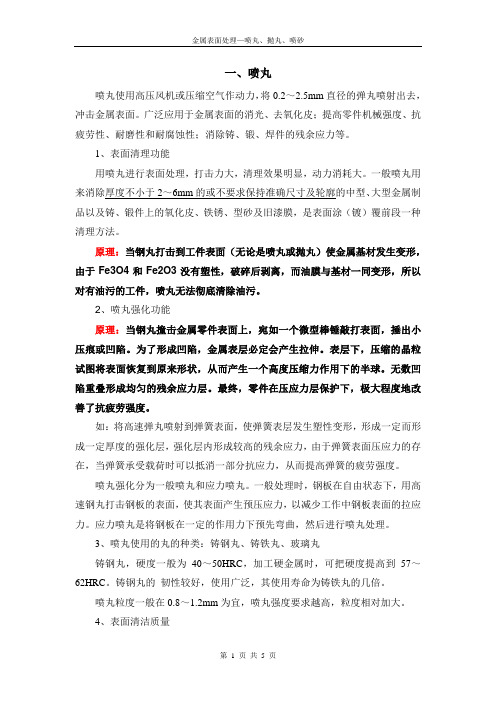
一、喷丸喷丸使用高压风机或压缩空气作动力,将0.2~2.5mm直径的弹丸喷射出去,冲击金属表面。
广泛应用于金属表面的消光、去氧化皮;提高零件机械强度、抗疲劳性、耐磨性和耐腐蚀性;消除铸、锻、焊件的残余应力等。
1、表面清理功能用喷丸进行表面处理,打击力大,清理效果明显,动力消耗大。
一般喷丸用来消除厚度不小于2~6mm的或不要求保持准确尺寸及轮廓的中型、大型金属制品以及铸、锻件上的氧化皮、铁锈、型砂及旧漆膜,是表面涂(镀)覆前段一种清理方法。
原理:当钢丸打击到工件表面(无论是喷丸或抛丸)使金属基材发生变形,由于Fe3O4和Fe2O3没有塑性,破碎后剥离,而油膜与基材一同变形,所以对有油污的工件,喷丸无法彻底清除油污。
2、喷丸强化功能原理:当钢丸撞击金属零件表面上,宛如一个微型棒锤敲打表面,捶出小压痕或凹陷。
为了形成凹陷,金属表层必定会产生拉伸。
表层下,压缩的晶粒试图将表面恢复到原来形状,从而产生一个高度压缩力作用下的半球。
无数凹陷重叠形成均匀的残余应力层。
最终,零件在压应力层保护下,极大程度地改善了抗疲劳强度。
如:将高速弹丸喷射到弹簧表面,使弹簧表层发生塑性变形,形成一定而形成一定厚度的强化层,强化层内形成较高的残余应力,由于弹簧表面压应力的存在,当弹簧承受载荷时可以抵消一部分抗应力,从而提高弹簧的疲劳强度。
喷丸强化分为一般喷丸和应力喷丸。
一般处理时,钢板在自由状态下,用高速钢丸打击钢板的表面,使其表面产生预压应力,以减少工作中钢板表面的拉应力。
应力喷丸是将钢板在一定的作用力下预先弯曲,然后进行喷丸处理。
3、喷丸使用的丸的种类:铸钢丸、铸铁丸、玻璃丸铸钢丸,硬度一般为40~50HRC,加工硬金属时,可把硬度提高到57~62HRC。
铸钢丸的韧性较好,使用广泛,其使用寿命为铸铁丸的几倍。
喷丸粒度一般在0.8~1.2mm为宜,喷丸强度要求越高,粒度相对加大。
4、表面清洁质量⑴、Sa1—手工刷除清理级(或清扫级)Sa1级处理的技术标准:工件表面应不可见油污、油脂、残留氧化皮、锈斑和残留油漆等污物;处理后表面上出现大量分别均匀的金属斑点。
材料表面喷丸强化技术概论
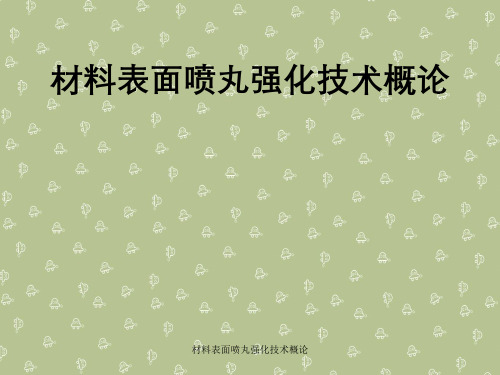
材料表面喷丸强化技术概论
早在1948年美国宇航材料规范中制定了喷丸 强化工艺规范(AMS-2430)。
1959年美国军用标准(MIL-C-26074A)中,规 定军用产品电镀前零件构必须进行喷丸处理。
+σr
δc
残
余
应 δc
力
-σr
材料表面喷丸强化技术概论
距表面
深度δ
当喷丸强度恒定 时,材料强度越高 则δc 值越小
当材料强度不变 时,喷丸强度越高 则δc 越大
通 常 情 况 下 , δc 在0.1~0.8mm的范 围内
材料表面喷丸强化技术概论
下图是300M高强钢 (σb=1900MPa)喷丸残余应力 分布曲线,可见喷丸强度由 0.13Amm增高至 0.75Amm,导致δc由0.15mm增至0.55mm,但表 面残余应力和最大残余应力变化不明显。
但喷丸后引起的表面粗糙度增加,有时对其 疲劳性能不利。
生产中,可以通过控制喷丸工艺参数,避免 零件表面粗糙度的增加。
也可通过二次喷丸或喷丸后表面精加工,来 削弱粗糙度的不利影响。
材料表面喷丸强化技术概论
1、应力强化
喷丸引人材料表层的残余应力沿表层深度的分 布如图。其中,残余压应力的深度δc 随着材料 强度和喷丸工艺参数而变化。
喷丸过程中,弹丸反复打击材料的表面,最终 在材料表面附近造成一塑性变形层即强化层的 深度,其深度为0.1~0.8mm
强化层
材料表面喷丸强化技术概论
合理利用引入表面塑性变形层的 1、残余压应力场(应力强化) 2、变形显微组织(组织强化) 3、残余奥氏体向马氏体转变(相变强化)
抛丸强化标准
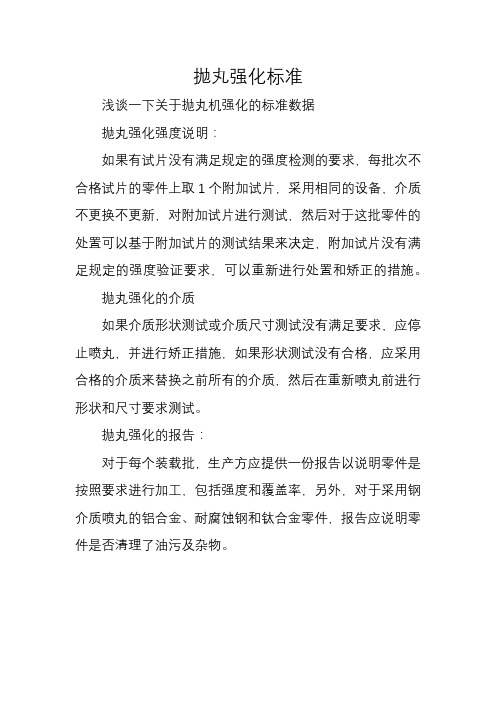
抛丸强化标准
浅谈一下关于抛丸机强化的标准数据
抛丸强化强度说明:
如果有试片没有满足规定的强度检测的要求,每批次不合格试片的零件上取1个附加试片,采用相同的设备,介质不更换不更新,对附加试片进行测试,然后对于这批零件的处置可以基于附加试片的测试结果来决定,附加试片没有满足规定的强度验证要求,可以重新进行处置和矫正的措施。
抛丸强化的介质
如果介质形状测试或介质尺寸测试没有满足要求,应停止喷丸,并进行矫正措施,如果形状测试没有合格,应采用合格的介质来替换之前所有的介质,然后在重新喷丸前进行形状和尺寸要求测试。
抛丸强化的报告:
对于每个装载批,生产方应提供一份报告以说明零件是按照要求进行加工,包括强度和覆盖率,另外,对于采用钢介质喷丸的铝合金、耐腐蚀钢和钛合金零件,报告应说明零件是否清理了油污及杂物。
不同材料零件的喷丸强化

不同材料零件的喷丸强化高强度钢由抛丸/喷丸强化引入的残余压应力是最终拉应力强度的一个百分比,该比率随着零件材料本身强度/硬度增加而增加。
高强度/硬度的金属更脆,且对表面缺陷更敏感。
对其进行抛丸/喷丸强化,能让这些高强度金属可以应用在易发生疲劳的工作条件下。
飞机起落架通常设计的疲劳强度为300 ksi (2068 MPa),结合抛丸/喷丸强化。
没经过抛丸/喷丸强化的,机加工后的钢制零件在硬度为30 HRC.左右能取得最佳的疲劳属性。
如材料强度/硬度超过这个水平,其疲劳强度会由于对表面缺口的敏感性和脆性增加而降低。
通过导入的压应力,疲劳强度与增加的强度/硬度成比率提高。
当材料硬度为52 HRC,强化后的疲劳强度可达144 ksi (993 MPa),比未经过强化的同样材料抗疲劳强度增加了2倍多。
利用抛丸/喷丸强化改善高强度/硬度零件的典型应用包括对扳手和冲击工具等。
此外,表面的浅刮痕对于经过抛丸/喷丸强化的高强度钢的疲劳强度影响不大,而对于未经强化的则破坏性很大。
渗碳钢渗碳和渗氮都是热处理过程,能让钢表面具有非常高的硬度。
通常在55~62 HRC。
渗碳钢强化的好处在于:?在~200 ksi (1379 MPa)或更高的高应力水平下,能提供卓越的疲劳属性?减少表面晶格间因氧化而造成渗碳异常情况对于完全渗碳和渗氮处理过的零件,要取得最佳的抗疲劳属性,建议使用硬度为55-62 HRC 的丸料。
脱碳钢脱碳是在热处理过程,铁合金表面碳含量减少。
脱碳会降低高强度钢(240 ksi, 1650 MPa 或以上)的疲劳强度70-80%;能降低低强度钢(2140-150 ksi, 965-1030 MPa)的疲劳强度45-55%。
脱碳对于疲劳属性的破坏力与脱碳层深度并无特别的关系。
脱碳层在0.003英寸深度,其破坏力与0.030英寸深度是一样的。
强化工艺被证实为一种有效的方法,能恢复大部分由于脱碳过程损失的疲劳强度。
喷丸处理规程 (喷丸)

喷丸处理一般应用在汽车的弹簧钢板的加工上.是为了减少被加工材料的塑性变形.喷丸强化分为一般喷丸和应力喷丸.一般处理时,钢板在自由状态下,用高速钢丸打击钢板的里面,使其表面产生预压应力.以减少工作中钢板表面的拉应力,增加使用寿命.应力喷丸处理是将钢板在一定的作用力下的预先弯曲,然后进行喷丸处理.汽车钢板弹簧喷丸处理规程1 主要内容与适用范围本规程规定了汽车钢板弹簧喷丸处理的适用范围、术语、喷丸处理的分类、喷丸处理条件的确定、技术要求和检验方法。
本规程适用于以提高汽车钢板弹簧使用寿命为目的的喷丸处理。
2 术语2.1 喷丸是一种将丸粒以适当的加速装置加速,并用适当的方式喷向工件的一种冷加工方法。
2.2 喷丸强化用喷丸的方法使其表层发生塑性变形并形成应变层,在应变层内发生组织结构和残余应力的变比。
合理地控制应变层内的这些变化可以提高零件的疲劳断裂抗力和应力腐蚀开裂抗力。
2.3 饱和以同一条件继续喷丸而不改变受喷区域的喷丸特性时,这一受喷区域就达到了饱和状态。
2.4 标准弧高度试片[即ALMEN片]标准弧高度试片是测定喷丸强度的专用试片。
标准试片有三种,分别用英文字母N、A、C表示,所用材料均为70号冷轧带钢,其尺寸参数及技术要求按表1的规定。
表 1试 片 代 号项 目 名 称N A C厚度,mm 0.8±0.025 1.3±0.025 2.4±0.025×75±0.2宽×长,mm 190-0.1平面度公差,mm ±0.025表面粗糙度,μm表面硬度 HRA 73~76 HRC 44~50 HRC 44~502.5 弧高度曲线试片在丸料冲击下,表面层发生塑性流变,由此导致试片向喷射面呈球面状弯曲(见图1),切入球面的特定基准面至球面最高点之间的距离称为弧高度。
试片的弧高度是喷丸工艺参数(包括丸粒直径、速度、流量、喷丸时间、角度等)的函数。
喷丸强化技术

一、喷丸强化技术原理
高速喷射的弹丸颗粒连续不断撞击齿面的过程,如同无数小锤对齿面进行锤击,使齿面产生极为强烈的塑性形变,使齿面产生一定厚度的冷作硬化层,这一硬化层即齿面的强化层,由此产生强化及表面压应力,达到提高齿轮疲劳强度和提高使用寿命的一项表面冷处理强化技术。
喷丸强化也称之为强化喷丸或受控喷丸。
齿轮喷丸强化是一种受控的喷丸技术,是将高速的弹丸流连续不断撞击齿面,使齿面在弹丸流的撞击作用下发生塑性变形(塑性变形层的厚度通常处于0.1-0.8mm之间)。
这一影响延伸到齿轮材料的表层,在表层下产生较高的残余压应力、加工硬化和组织细化等有利的变化,抵消不良的拉应力,该残余压应力延缓了的疲劳断裂的形成,有效的提高了齿轮的疲劳强度,延长了齿轮的使用寿命。
二、齿轮喷丸强化的工艺参数
青岛丰东热处理有限公司专业提供热处理服务,可为客户提供化学热处理(渗碳、渗氮、碳氮共渗)、真空热处理、等离子热处理(离子渗氮)、常规热处理(含深冷处理)等四大领域的热处理加工服务。
欢迎新老客户来电咨询,电话:4006577217。
“青岛丰东热处理”微信公众号提供热“新鲜”的处理行业动态及资讯,如果您对热处理相关知识感兴趣,欢迎关注我们,青岛丰东期待与您共同进步!。
喷丸强化
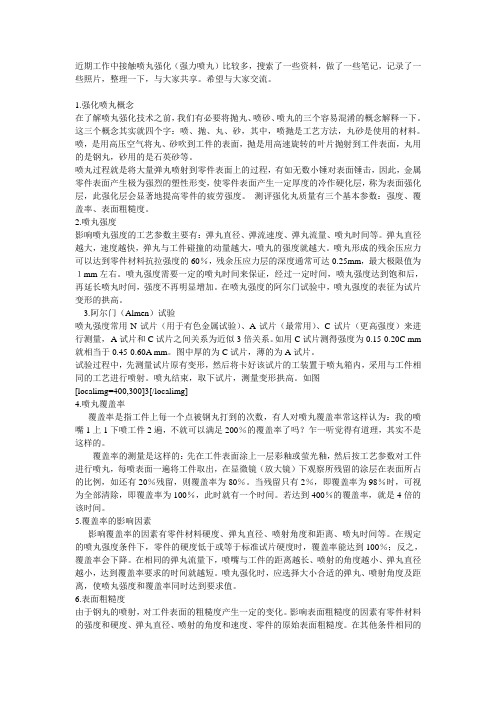
近期工作中接触喷丸强化(强力喷丸)比较多,搜索了一些资料,做了一些笔记,记录了一些照片,整理一下,与大家共享。
希望与大家交流。
1.强化喷丸概念在了解喷丸强化技术之前,我们有必要将抛丸、喷砂、喷丸的三个容易混淆的概念解释一下。
这三个概念其实就四个字:喷、抛、丸、砂,其中,喷抛是工艺方法,丸砂是使用的材料。
喷,是用高压空气将丸、砂吹到工件的表面,抛是用高速旋转的叶片抛射到工件表面,丸用的是钢丸,砂用的是石英砂等。
喷丸过程就是将大量弹丸喷射到零件表面上的过程,有如无数小锤对表面锤击,因此,金属零件表面产生极为强烈的塑性形变,使零件表面产生一定厚度的冷作硬化层,称为表面强化层,此强化层会显著地提高零件的疲劳强度。
测评强化丸质量有三个基本参数:强度、覆盖率、表面粗糙度。
2.喷丸强度影响喷丸强度的工艺参数主要有:弹丸直径、弹流速度、弹丸流量、喷丸时间等。
弹丸直径越大,速度越快,弹丸与工件碰撞的动量越大,喷丸的强度就越大。
喷丸形成的残余压应力可以达到零件材料抗拉强度的60%,残余压应力层的深度通常可达0.25mm,最大极限值为1mm左右。
喷丸强度需要一定的喷丸时间来保证,经过一定时间,喷丸强度达到饱和后,再延长喷丸时间,强度不再明显增加。
在喷丸强度的阿尔门试验中,喷丸强度的表征为试片变形的拱高。
3.阿尔门(Almen)试验喷丸强度常用N试片(用于有色金属试验)、A试片(最常用)、C试片(更高强度)来进行测量,A试片和C试片之间关系为近似3倍关系。
如用C试片测得强度为0.15-0.20C mm 就相当于0.45-0.60A mm。
图中厚的为C试片,薄的为A试片。
试验过程中,先测量试片原有变形,然后将卡好该试片的工装置于喷丸箱内,采用与工件相同的工艺进行喷射。
喷丸结束,取下试片,测量变形拱高。
如图[localimg=400,300]3[/localimg]4.喷丸覆盖率覆盖率是指工件上每一个点被钢丸打到的次数,有人对喷丸覆盖率常这样认为:我的喷嘴1上1下喷工件2遍,不就可以满足200%的覆盖率了吗?乍一听觉得有道理,其实不是这样的。
- 1、下载文档前请自行甄别文档内容的完整性,平台不提供额外的编辑、内容补充、找答案等附加服务。
- 2、"仅部分预览"的文档,不可在线预览部分如存在完整性等问题,可反馈申请退款(可完整预览的文档不适用该条件!)。
- 3、如文档侵犯您的权益,请联系客服反馈,我们会尽快为您处理(人工客服工作时间:9:00-18:30)。
TASK 70-47-01-380-0161. 概述。
A. 喷丸是利用金属丸,玻璃丸,陶瓷丸来达到工件表面强化的工艺。
实质上,它在表面形成残余压应力,从而提高了抗压力腐蚀和和抗击循环疲劳的能力。
特定零件表面修整所需的介质的成分,尺寸,强度和覆盖率都在发动机/车间手册中有具体规定。
B. 喷丸介质通过高压风冲击工作表面。
喷丸射流有直接冲击和反射冲击两种方法。
直接冲击是使用标准喷嘴,偏转喷嘴或者长矛枪喷嘴与零件表面成35度角冲击而成的线状气流。
反射冲击是非线状冲击,工件表面通过另一表面反射的喷丸射流而完成喷丸。
C. 喷丸主要使用干介质。
然而,湿玻璃丸喷丸法可以用作干玻璃丸喷丸法的替代方法。
不同的介质用不同的范围来表征喷丸强度。
金属丸主要用来表征阿尔门A范围的喷丸强度。
陶瓷丸和玻璃丸介质用阿尔门N范围指定的强度来喷射零件。
注意:低强度喷丸可以使用金属喷丸,用阿尔门N试片来测量。
D. 在喷丸操作的阿尔门N范围内,陶瓷丸可以用作玻璃丸的替代品。
因为质量和尺寸上的差别,陶瓷丸和玻璃丸介质在喷丸时的参数也不一样。
当使用陶瓷介质时,喷丸机的参数需要重新设定。
对于指定的阿尔门强度,陶瓷丸比起玻璃丸能产生更深的应力层。
因此,当在含有薄片状(比如叶片前缘)的工件上进行喷丸程序时,喷丸强度最好定在允许强度范围的前半部分。
E. 喷丸操作通常由计算机控制,自动控制或人工设备控制以及加工来完成。
参考,设备。
F. 替代喷丸介质的使用,参考,,和,材料。
G. 不同种类,硬度,尺寸的喷丸介质不能混合在一起。
2. 设备。
Subtask 70-47-01-380-161A. 喷丸机包括使喷丸射流受控的可移动喷嘴,使工件通过喷丸射流的的转动和回转工作台,使喷丸介质输送至喷嘴的机构,去除设备运转过程中产生的破损丸粒的筛分装置和控制喷丸时间的记时装置。
一些特殊设备,比如在孔里、槽里或凹陷工件上喷丸的矛枪和偏转仪需要具备。
同样也需要提供一个延伸喷嘴来达到这些难以达到的区域。
(1) 通用喷丸设备。
所有的喷丸设备应满足以下基本要求:(a) 喷丸机通过空气压力驱动喷丸介质。
轮式喷丸是不允许的。
(b) 当喷丸机将工件以平移或者旋转(或者两者兼有)的方式通过喷射气流时,工件或者喷嘴要受控且重复移动。
警告:使用防护装备。
出自某些材料的粉尘,比如镍,对人员有吸入性危害。
警告:防止粉尘的堆积。
出自某些材料的粉尘,比如钛,容易引起火灾和爆炸。
(c) 喷丸机应该具备控制喷丸过程中粉尘的装置。
这些粉尘包含喷丸介质,出自工件、工装和其他一些和空气或喷丸介质接触的材料。
采取措施保护工作人员,避免接触这些粉尘。
(d) 避免使用能造成工件划伤的夹具(直接划伤或者是因为残留在夹具上的喷丸带来的划伤)。
除非设备充分接地,否则木质、可降解材料或金属-金属的夹具是不允许用的。
由高密度聚合体构成的夹具是符合要求的。
如果工件定位器由硬橡胶或聚亚安酯构成,此夹具也可用。
像硬橡胶这种有柔韧性的材料在夹具的重复使用中能体现出较好的优越性,能防止丸粒留在夹具上而造成工件划伤。
警告:遵守接地指示,避免对人员和工件造成伤害。
(e) 喷丸时能产生给人员和工件带来伤害的强大静电荷。
按如下通过传导介质或人工施加探针来接地。
1 用来接地的材料可以是软金属,它和工件接触的剖面需平滑。
2 用来接地的材料和探针在与工件接触的区域不能含有银、黄铜、青铜、铜、锌、石墨等物质。
3 静电荷同样会在喷嘴和装喷丸介质的容器内堆积,所以接地来释放电荷。
提醒:在喷丸过程中或喷丸结束后,如果出现比较大的电弧,需检查工件。
工件如果出现熔化或凹坑,则不可用。
(f) 在喷丸过程中或喷丸结束后,如果出现比较大的电弧,按如下做目视检查:1 检查探针与工件接触的区域是否出现熔化或凹坑。
2 参照,打磨步骤。
用打磨方式修理熔化或凹坑区域。
提醒:确保每个材料都使用正确级别的蚀刻剂。
根据,酸洗步骤,表1或者咨询当地GEAE代表选择正确的蚀刻剂。
3 根据,酸洗步骤,酸洗打磨区域。
4 根据,荧光渗透检查,检查酸洗区域。
5 根据发动机/车间门手册重新喷丸。
(g) 喷嘴和空气射流的磨损会影响工艺质量。
喷丸厂家需要制定喷嘴控制方案。
喷嘴控制方案应考虑如下情况:1 使用前先目视检查喷嘴和空气射流是否可用。
2 确保喷嘴和空气射流在肉眼观察下没有明显损伤和不均匀的磨损。
3 喷嘴磨损不能超过公称直径的15%,空气射流磨损不能超过公称直径的10%。
4 如果发生磨损,重新建立饱和曲线来测试喷丸强度,确保喷嘴能达到所需的强度。
(h) 磨损或损坏的的喷嘴会影响喷丸射流对工件的对准。
需要检查喷丸后的覆盖范围。
(2) 手动喷丸设备。
基于手动重复性差,手动喷丸(手握和移动喷嘴)不建议使用。
(a) 手动喷丸设备需要提供可控的空气压力,还能让操作者安全看到工件和要喷丸的表面,而且要保证喷丸介质被稳定地送到喷嘴机构。
(b) 对于有时限要求的的转动件和在高压涡轮上的叶片不允许使用手动喷丸。
对于局部修理,手动喷丸有相应规定且只能在如下情况下允许使用:1 一些组件,比如管路组件,它们的构造使之比起自动喷丸,手动喷丸更容易达到均匀覆盖。
2 根据,旋片喷丸。
对一些在固定大零件上金属切削下的小区域或焊接区域用手动喷嘴或旋片喷丸的方式。
3 只有在工艺文件上具体说明且在工件上有授权的具体位置才能给有时限要求的的转动件和在高压涡轮上的叶片实施手动喷丸。
(3) 自动喷丸设备。
自动喷丸设备需要手动安装和配置工件、喷嘴位置和工艺参数。
另外,工艺参数的监测需要操作者来管理,不过,操作过程中就不需要操作者的任何参与。
(a) 自动喷丸机须装有计时装置或循环计数器,保证重复喷丸。
(b) 为了防止喷丸射流在一个地方意外停留,自动喷丸机应具备启动-关断互锁开关的装置,保持当空气压力供给时转台的连续转动。
注意:在对准工件表面以前,喷丸机应具备使喷丸射流保持稳定的装置。
如果喷嘴在喷丸循环结束后仍然对准零件,最好的关断顺序是,先关断空气压力供给,再关断喷丸射流。
(c) 自动喷丸机应具备自动去除运转过程中产生的破损丸粒的筛分装置。
推荐使用整套的筛分装置。
(d) 喷丸车间的角色很重要,要保证喷丸射流对准工件以获得所需的强度和覆盖面。
提醒:不允许转动物体碰触工件表面。
必须控制公差避免损伤工件以提供良好覆盖。
(e) 必须要控制喷射气流,偏转、喷嘴设置角度、位置和角度重复性来防止不正确的喷丸结果。
转台轴承严重磨损将造成零件位置变化而影响均匀覆盖。
当转动的物体离工件表面比较近时,受控尤其重要(如在螺栓孔里使用矛枪时)。
在这些情况下,更要严格受控防止零件磨损。
(4) 计算机控制喷丸设备。
计算机控制喷丸设备利用计算机(或可编程逻辑控制器或数控型控制器)来储存丸粒、设定和控制参数。
这个设备应该具备筛选、控制和监控的能力。
喷丸空气压力喷射气流速度喷丸时间,进料速度,循环次数工件和喷嘴的位置、方向和速度矛枪转动速度(在使用时)(a) 喷丸机应具备保证对零件重复喷丸的记时装置和循环计时器。
(b) 为了防止喷丸射流在一个地方意外停留,自动喷丸机应具备启动-关断互锁开关的装置,保持当空气压力供给时转台的连续转动。
注意:在对准工件表面以前,喷丸机应具备使喷丸射流保持稳定的装置。
如果喷嘴在喷丸循环结束后仍然对准零件,最好的关断顺序是,先关断空气压力供给,再关断喷丸射流。
(c) 当检测到如下任何参数有变化而造成强度和覆盖在修理要求范围之外时,喷丸机应具备持续控制和终止设备的能力。
空气压力喷射气流速度工件/喷嘴的位置和速度(d) 喷丸机应具备自动去除运转过程中产生的破损丸粒、超尺寸丸粒、小尺寸丸粒的筛分装置。
所有的喷丸在重新使用前必须都通过筛分装置。
筛分装置通常有振动筛来筛选出超尺寸的和小尺寸丸粒。
螺旋分离器可以更进一步的去除不规则丸粒,但是没必要让所有的丸粒都通过螺旋分离器。
(e) 喷丸厂家的角色很重要,要保证喷丸射流对准工件以获得所需的强度和覆盖。
提醒:不允许转动物体碰触工件表面。
必须控制公差避免损伤工件以提供良好覆盖。
(f) 必须要控制喷射气流,偏转、喷嘴设置角度、位置和角度重复性来防止不正确的喷丸结果。
转台轴承严重磨损将造成零件位置变化而影响均匀覆盖。
当转动的物体离工件表面比较近时,受控尤其重要(如在螺栓孔里使用矛枪时)。
在这些情况下,更要严格受控防止零件磨损。
B. 阿尔门试片夹具。
阿尔门试片是用来评估喷丸效果的工件构造复制品,它需要和工件在轮廓和遮光效果方面的误差不超过0.060 inch (1.5mm),试片应和它代表的工件表面硬度类似,这样才能使弹跳在表面上的丸粒和在真实工件上的效果一样。
3. 材料。
Subtask 70-47-01-380-162A. 金属丸和玻璃丸都是球形的,不需要丸粒的过度压裂就能产生所需的喷丸强度。
有多种种类和尺寸的金属丸和玻璃丸可供选择,来满足发动机/车间手册规定的喷丸强度。
注意:符合表2的同等尺寸的丸粒型号在满足表3时可以互相代替。
举一个尺寸同等的例子,丸粒CCW 14可以作为S110的替代品(它的公称直径接近表1中使S110最少通过50%的筛网直径)。
当可调质切丝丸替代铸钢丸时,破损丸粒的数量必须要符合表1要求,但不适用表2关于观察区域不可接受丸粒的最大数量的规定。
这个规定使喷丸机上能残留铸钢丸,已调质切丝丸也是一样的情况。
任何种类的丸粒替代品都要重新绘制符合段落4.E.(1)(g)的饱和曲线图和测量覆盖度。
(1) 铸钢丸。
(a) 铸钢丸,其高硬度应满足AMS 2431/2,喷丸介质(ASH)铸钢丸,高硬度(55-62 HRc)的要求。
参看表1关于丸粒尺寸定义的参考。
Cast Steel Shot Sizes and Screening Tolerances (inches) - Table 1Shot Size All PassU.S.ScreenSize(inches)Max 2% onU.S.Screen(inches)Max 50%on U.S.Screen(inches)Cumula-tive Min 90%on U.S.Screen(inches)Cumula-tive Min98% onU.S.Screen(inches)Max Numberof BrokenandDeformed1ShotAcceptableperInspectionArea(inches)780 6(0.132) 7(0.111) 8(0.0937) 10(0.0787) 12(0.0661) 11 per 1.0 x 1.0660 7(0.111) 8(0.0937) 10(0.0787)12(0.0661)14(0.0555)16 per1.0 x 1.0550 8(0.0937) 10(0.0787)12(0.0661)14(0.0555)16(0.0469)22 per1.0 x 1.0460 10(0.0787) 12(0.0661)14(0.0555)16(0.0469)18(0.0394)32 per1.0 x 1.0390 12(0.0661) 14(0.0555)16(0.0469)18(0.0394)20(0.0331)45 per1.0 x 1.0330 14(0.0555) 16(0.0469)18(0.0394)20(0.0331)25(0.0280)16 per0.5 x 0.5230 18(0.0394) 20(0.0331)25(0.0280)30(0.0232)35(0.0197)32 per0.5 x 0.5170 25(0.0280) 30(0.0232)35(0.0197)40(0.0165)45(0.0138)16 per0.25 x 0.25130 30(0.0232) 35(0.0197)40(0.0165)45(0.0138)50(0.0117)23 per0.25 x 0.25110 35(0.0197) 40(0.0165)45(0.0138)50(0.0117)80(0.0070)32 per0.25 x 0.2570 40(0.0165) 45(0.0138)50(0.0117)80(0.0070)120(0.0049)45 per0.25 x 0.25注意:参考Figure 14。