50万吨年产甲醇合成工艺初步设计
年产60万吨石油制甲醇初步工艺设计

年产60万吨石油制甲醇初步工艺设计1. 引言本文档旨在提供一份关于年产60万吨石油制甲醇初步工艺设计的详细说明。
石油制甲醇工艺设计主要包括石油预处理、蒸馏与分离、合成气制备、甲醇合成以及甲醇精制等工艺步骤。
通过合理的工艺设计,可确保高效、稳定地生产出预期的年产60万吨甲醇。
2. 工艺流程以下是年产60万吨石油制甲醇的初步工艺设计流程:1. 石油预处理:首先,经过石油分离、脱硫、脱氮等预处理步骤,将原油中的杂质和有害物质去除,以提高后续工艺步骤的稳定性和效率。
石油预处理:首先,经过石油分离、脱硫、脱氮等预处理步骤,将原油中的杂质和有害物质去除,以提高后续工艺步骤的稳定性和效率。
2. 蒸馏与分离:经过真空蒸馏和分离步骤,将预处理后的石油分离为轻质石油和重质石油。
轻质石油用于合成气的制备,而重质石油则用于后续的甲醇合成工艺。
蒸馏与分离:经过真空蒸馏和分离步骤,将预处理后的石油分离为轻质石油和重质石油。
轻质石油用于合成气的制备,而重质石油则用于后续的甲醇合成工艺。
3. 合成气制备:轻质石油经过催化重整和变换等步骤,生成含有一定比例的一氧化碳和氢气的合成气。
合成气是甲醇合成过程的重要原料。
合成气制备:轻质石油经过催化重整和变换等步骤,生成含有一定比例的一氧化碳和氢气的合成气。
合成气是甲醇合成过程的重要原料。
4. 甲醇合成:在甲醇合成反应器中,采用适当的催化剂和反应条件,使合成气中的一氧化碳和氢气进行反应,生成甲醇。
通过控制反应参数,可以获得高纯度的甲醇产品。
甲醇合成:在甲醇合成反应器中,采用适当的催化剂和反应条件,使合成气中的一氧化碳和氢气进行反应,生成甲醇。
通过控制反应参数,可以获得高纯度的甲醇产品。
5. 甲醇精制:生产得到的初级甲醇通过蒸馏和洗涤等工艺步骤,去除其中的杂质和不纯物质,提高甲醇的纯度和质量。
甲醇精制:生产得到的初级甲醇通过蒸馏和洗涤等工艺步骤,去除其中的杂质和不纯物质,提高甲醇的纯度和质量。
年产30万吨合成甲醇项目初步设计说明书
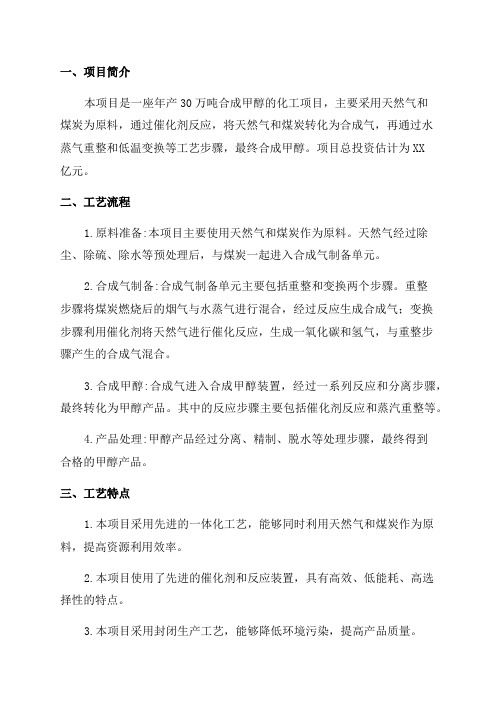
一、项目简介本项目是一座年产30万吨合成甲醇的化工项目,主要采用天然气和煤炭为原料,通过催化剂反应,将天然气和煤炭转化为合成气,再通过水蒸气重整和低温变换等工艺步骤,最终合成甲醇。
项目总投资估计为XX亿元。
二、工艺流程1.原料准备:本项目主要使用天然气和煤炭作为原料。
天然气经过除尘、除硫、除水等预处理后,与煤炭一起进入合成气制备单元。
2.合成气制备:合成气制备单元主要包括重整和变换两个步骤。
重整步骤将煤炭燃烧后的烟气与水蒸气进行混合,经过反应生成合成气;变换步骤利用催化剂将天然气进行催化反应,生成一氧化碳和氢气,与重整步骤产生的合成气混合。
3.合成甲醇:合成气进入合成甲醇装置,经过一系列反应和分离步骤,最终转化为甲醇产品。
其中的反应步骤主要包括催化剂反应和蒸汽重整等。
4.产品处理:甲醇产品经过分离、精制、脱水等处理步骤,最终得到合格的甲醇产品。
三、工艺特点1.本项目采用先进的一体化工艺,能够同时利用天然气和煤炭作为原料,提高资源利用效率。
2.本项目使用了先进的催化剂和反应装置,具有高效、低能耗、高选择性的特点。
3.本项目采用封闭生产工艺,能够降低环境污染,提高产品质量。
4.本项目设计了完善的废物处理装置,实现了废物的资源化利用,减少了对环境的影响。
五、经济效益分析1.本项目年产30万吨甲醇,主要销售给化工企业作为原材料。
根据市场调研和产品定价,预计年销售收入为XX亿元。
2.本项目投资估计为XX亿元,预计投资回收期为X年,静态投资回收率为X%。
3.本项目能够提供大量的就业机会,促进当地经济发展。
六、风险分析1.天然气和煤炭市场价格波动风险。
2.环保政策和法规调整风险。
3.技术创新和市场需求变化风险。
4.合作伙伴风险及市场竞争风险。
七、总结本项目的初步设计说明书详细介绍了年产30万吨合成甲醇的工艺流程、工艺特点、经济效益分析和风险分析等方面。
该项目将利用先进的工艺装置和催化剂,通过合成气制备和反应步骤,将天然气和煤炭转化为合成甲醇,可提供大量就业机会和促进当地经济发展。
甲醇化工厂毕业设计1部分

甲醇化工厂毕业设计1部分1. 简介本文档是甲醇化工厂毕业设计的第一部分,旨在介绍甲醇化工厂的工艺流程及设备配置。
甲醇是一种重要的化工原料,在化工领域具有广泛的应用,因此本设计旨在搭建一个高效、可持续的甲醇化工厂。
2. 工艺流程甲醇化工厂的工艺流程包括甲醇生产、提纯和储存三个主要步骤。
2.1 甲醇生产甲醇生产的主要步骤是甲烷转化成合成气,然后合成气通过甲醇合成反应转化成甲醇。
具体的流程如下:1.原料准备:甲烷作为甲醇的原料,需要经过脱水、聚合等预处理步骤,以提高甲烷的纯度和反应效率。
2.合成气生产:甲烷经过蒸汽重整后生成合成气,合成气主要由一氧化碳和氢气组成。
3.甲醇合成反应:合成气经过甲醇合成反应,通常使用铜催化剂,在高温高压的条件下将一氧化碳和氢气转化成甲醇。
4.分离和提纯:甲醇合成反应产生的混合物需要进行分离和提纯,通常采用蒸馏和萃取等方法。
2.2 提纯甲醇合成后的产物需要进行进一步的提纯,以满足工业使用要求。
主要的提纯过程包括:1.蒸馏:将甲醇原液进行蒸馏,去除其中的杂质和水分。
2.萃取:采用一系列溶剂的萃取操作,进一步提高甲醇纯度。
3.结晶:对纯度较高的甲醇进行结晶分离,得到最纯净的甲醇产品。
2.3 储存甲醇提纯之后需要进行储存和包装,以便运输和销售。
常见的储存方式包括储罐和压力容器,储存温度通常保持在零下20摄氏度以防止甲醇的挥发。
3. 设备配置甲醇化工厂的设备配置主要包括反应器、分离设备、储存设备等。
3.1 反应器反应器是甲醇生产的核心设备,其主要功能是提供合适的反应条件并促进反应的进行。
在甲醇合成反应中,常采用固定床反应器和流化床反应器。
3.2 分离设备分离设备主要用于分离甲醇和其他物质,以提高甲醇的纯度。
常见的分离设备有蒸馏塔、萃取塔、结晶器等。
3.3 储存设备储存设备主要用于储存甲醇产品,常见的储存设备包括储罐和压力容器。
储存设备需要具备密封性和耐腐蚀性,以确保甲醇的质量和安全性。
年产60万吨甲醇制烯烃初步设计
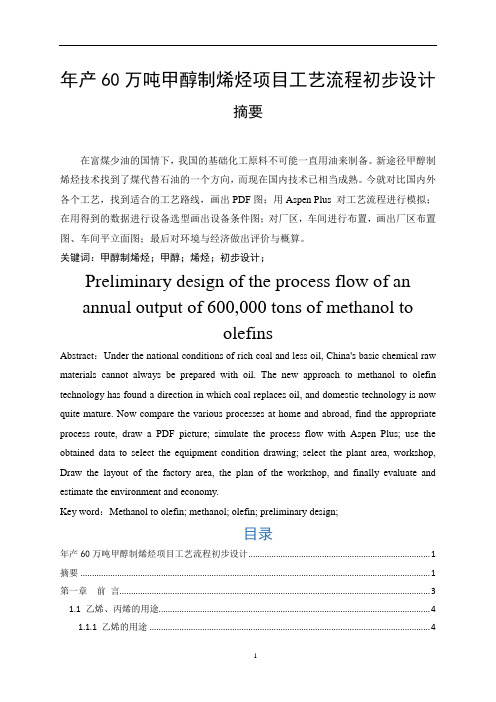
年产60万吨甲醇制烯烃项目工艺流程初步设计摘要在富煤少油的国情下,我国的基础化工原料不可能一直用油来制备。
新途径甲醇制烯烃技术找到了煤代替石油的一个方向,而现在国内技术已相当成熟。
今就对比国内外各个工艺,找到适合的工艺路线,画出PDF图;用Aspen Plus 对工艺流程进行模拟;在用得到的数据进行设备选型画出设备条件图;对厂区,车间进行布置,画出厂区布置图、车间平立面图;最后对环境与经济做出评价与概算。
关键词:甲醇制烯烃;甲醇;烯烃;初步设计;Preliminary design of the process flow of anannual output of 600,000 tons of methanol toolefinsAbstract:Under the national conditions of rich coal and less oil, China's basic chemical raw materials cannot always be prepared with oil. The new approach to methanol to olefin technology has found a direction in which coal replaces oil, and domestic technology is now quite mature. Now compare the various processes at home and abroad, find the appropriate process route, draw a PDF picture; simulate the process flow with Aspen Plus; use the obtained data to select the equipment condition drawing; select the plant area, workshop, Draw the layout of the factory area, the plan of the workshop, and finally evaluate and estimate the environment and economy.Key word:Methanol to olefin; methanol; olefin; preliminary design;目录年产60万吨甲醇制烯烃项目工艺流程初步设计 (1)摘要 (1)第一章前言 (3)1.1 乙烯、丙烯的用途 (4)1.1.1 乙烯的用途 (4)1.2 乙烯、丙烯的国内外市场供需情况 (5)1.3 主要方法 (7)1.4 课题研究的目的,意义和内容 (8)第二章工艺方案选择 (9)2.1 概述 (9)2.2 煤基甲醇制烯烃工艺对比 (9)2.2.1 MTO反应工艺对比 (9)2.2.2 MTP工艺对比 (11)2.4 工艺流程简述 (13)第三章工艺流程模拟 (14)3.1 工艺流程叙述与模拟 (14)3.1.1 反应工段 (14)3.1.2 预反应工段 (16)3.2.3后续分类工段模拟 (18)3.2.4裂化回收工段 (19)第四章物料衡算 (20)4.1概述 (20)4.2 物料衡算的目的 (21)4.3 物料衡算的方法 (21)4.4 物料衡算的任务 (21)4.5 系统物料衡算 (21)第五章热量衡算 (22)5.1 概述 (22)5.2热量衡算的方法 (22)5.3 热量衡算的任务 (22)5.4 系统热量衡算 (23)第六章设备选型 (23)6.1 反应器设计 (23)6.1.1 反应再生工段反应器 (23)6.1.2预分离工段加氢反应器 (25)6.2 分离器设计 (26)第七章总图与车间布置 (27)7.1 总图布置 (27)7.2 车间布置 (28)第八章环境保护 (29)8.1 概述 (29)8.2 各个工段污染物 (29)8.2.1 废水处理 (29)8.2.2 废气处理 (29)8.2.3 废渣处理 (30)第九章项目概算 (30)9.1 工程概括 (30)9.2 项目总投资概算 (30)结论 (31)致谢 ......................................................................................................................... 错误!未定义书签。
年产60万吨煤制甲醇合成工艺设计说明书 (1)

《过程装备成套技术》课程设计煤制甲醇合成工段工艺流程及典型题目设备的设计组别第四组姓名学号院(系) 化学与化工学院专业过程装备与控制工程指导教师高勇日期2016年6月27日至2016年7月3日目录1甲醇的合成 (1)1.1甲醇合成的基本原理 (1)1.1.1甲醇合成反应步骤 (1)1.1.2合成甲醇的化学反应 (1)1.2甲醇合成催化剂的选用 (2)1.3铜基催化剂的中毒和寿命 (2)1.4甲醇合成的工艺条件 (2)1.4.1反应温度 (2)1.4.2压力 (2)1.4.3空速 (3)1.4.4气体组成 (3)1.5甲醇合成的工艺流程 (3)1.5.1甲醇合成的方法 (3)1.5.2本设计的合成工艺 (4)1.5.3甲醇合成塔的选择 (4)1.5.4甲醇合成工艺流程 (5)2列管式换热器设计及相关计算 (6)2.1设计任务及操作条件 (6)2.2方案简介 (6)2.3设计方案 (6)2.3.1.确定设计方案 (6)2.3.2确定物性数据 (7)2.3.3计算总传热系数 (7)2.3.4计算传热面积 (8)2.3.5工艺结构尺寸 (9)2.3.6换热器核算 (11)3参考文献 (17)1甲醇的合成1.1甲醇合成的基本原理1.1.1甲醇合成反应步骤对甲醇合成而言,无论是锌铬催化剂还是铜基催化剂,其多相(非匀相)催化过程按下列过程进行:a)扩散——气体自气相扩散到催化剂的界面;b)吸附——各种气体在催化剂的活性表面进行化学吸附,其中CO在Cu2+上吸附,H2在Zn2+上吸附并异裂;c)表面反应——化学吸附的反应物在活性表面上进行反应,生成产物;d)解析——反应产物脱附;e)扩散——反应产物气体自催化剂界面扩散到气相中去;以上五个过程中a、e(扩散)进行得最快,b(吸附)、d(解析)进行的速度较快,而过程c(表面反应)分子在催化剂活性界面的反应速度最慢,因此,整个反应过程取决于表面反应的进行速率[1]。
年产60万吨煤制甲醇初步工艺设计
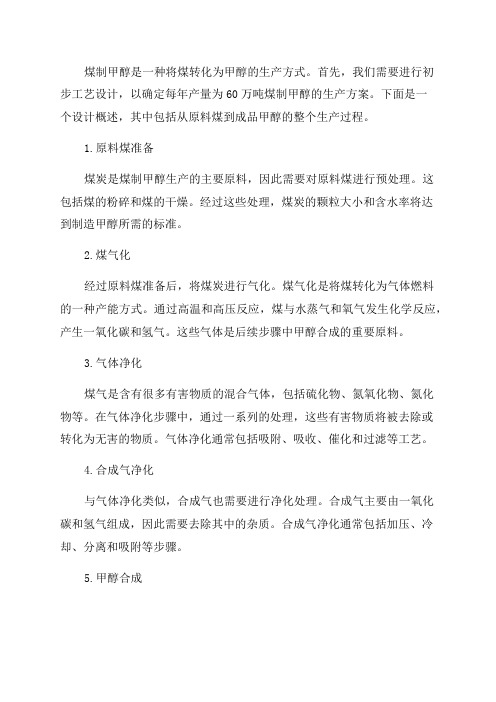
煤制甲醇是一种将煤转化为甲醇的生产方式。
首先,我们需要进行初步工艺设计,以确定每年产量为60万吨煤制甲醇的生产方案。
下面是一个设计概述,其中包括从原料煤到成品甲醇的整个生产过程。
1.原料煤准备煤炭是煤制甲醇生产的主要原料,因此需要对原料煤进行预处理。
这包括煤的粉碎和煤的干燥。
经过这些处理,煤炭的颗粒大小和含水率将达到制造甲醇所需的标准。
2.煤气化经过原料煤准备后,将煤炭进行气化。
煤气化是将煤转化为气体燃料的一种产能方式。
通过高温和高压反应,煤与水蒸气和氧气发生化学反应,产生一氧化碳和氢气。
这些气体是后续步骤中甲醇合成的重要原料。
3.气体净化煤气是含有很多有害物质的混合气体,包括硫化物、氮氧化物、氮化物等。
在气体净化步骤中,通过一系列的处理,这些有害物质将被去除或转化为无害的物质。
气体净化通常包括吸附、吸收、催化和过滤等工艺。
4.合成气净化与气体净化类似,合成气也需要进行净化处理。
合成气主要由一氧化碳和氢气组成,因此需要去除其中的杂质。
合成气净化通常包括加压、冷却、分离和吸附等步骤。
5.甲醇合成经过气体净化后,一氧化碳和氢气被送入甲醇合成反应器中。
在甲醇合成反应器中,通过一系列催化反应,一氧化碳和氢气发生化学反应,产生甲醇。
这个过程通常是在高温和高压下进行的。
6.甲醇精制在甲醇合成后,产生的甲醇含有一定量的杂质,如水分、重质烃和酸等。
在甲醇精制过程中,这些杂质将通过蒸馏、吸附、萃取等步骤被去除。
最终得到的是高纯度的甲醇产品。
7.甲醇储存和出口在甲醇精制后,将产生的甲醇储存于储罐中,并进行包装和标记。
根据客户需求,可以选择将甲醇产品出口到国内或国际市场。
需要指出的是,以上只是一个初步工艺设计的概述,具体的工艺细节将根据实际情况进行优化和调整。
同时,在生产过程中需要考虑的因素还包括环境保护、能源消耗和安全生产等方面。
因此,在具体的工艺设计中,需要进行细致的分析和评估,以确保生产过程的可行性和经济性。
以上是一个大致的初步工艺设计,简要介绍了从原料煤到成品甲醇的生产过程。
久泰能源建设年产50万吨甲醇技改项目

久泰能源建设年产50万吨甲醇技改项目
汪家铭
【期刊名称】《大氮肥》
【年(卷),期】2013(36)3
【摘要】久泰能源集团三期甲醇技改项目由久泰化工科技股份有限公司投资兴建.位于山东省临沂市罗庄区北区工业园,总投资36亿元,建设年产50万吨甲醇生产装置。
该项目建设年限2012年12月至2014年底,前期手续办理、场地平整已经完成,厂区道路施工全面展开,锅炉、空分、土建、安装、监理等招标工作陆续进行。
【总页数】1页(P171-171)
【关键词】甲醇生产装置;技改项目;能源建设;化工科技;项目建设;手续办理;场地平整;道路施工
【作者】汪家铭
【作者单位】
【正文语种】中文
【中图分类】TQ223.121
【相关文献】
1.湖北宜化集团100万吨/年硫铁矿采矿基地动工兴建/恒通联创年产15万吨PVC 项目竣工/年产85万吨甲醇工程 [J],
2.年产40万吨甲醇装置合成气利用技改项目 [J], ;
3.内蒙古久泰能源年产60万吨烯烃项目建成投产 [J], 本刊
4.内蒙古久泰能源建设年产50万吨乙二醇项目 [J], 汪家铭
5.久泰能源建设三期年产50万吨甲醇技改项目 [J], 汪家铭
因版权原因,仅展示原文概要,查看原文内容请购买。
年产55万吨粗甲醇合成精馏毕业设计
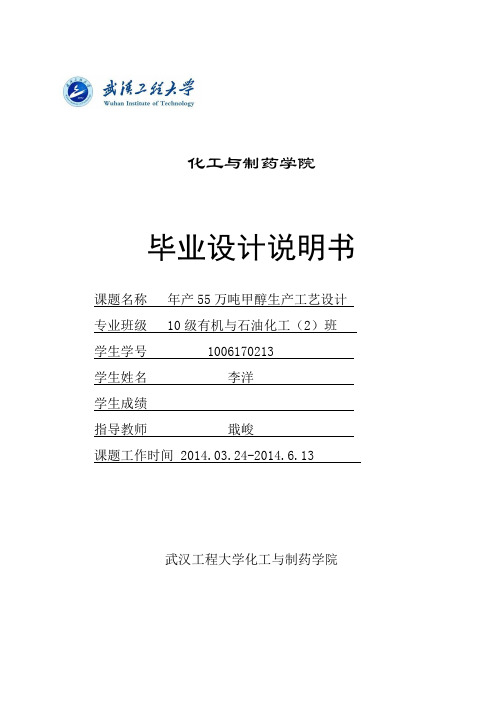
年产50万吨甲醇合成的任务书

年产50万吨甲醇合成的任务书任务书一、背景介绍甲醇是一种重要的有机化工产品,广泛应用于化工、能源、医药等领域。
随着全球经济的发展和能源需求的增加,甲醇的需求量也在不断增长。
为了满足市场需求,我公司决定建设年产50万吨甲醇合成装置。
二、任务目标1. 建设规模:年产50万吨甲醇合成装置。
2. 技术要求:采用先进的合成工艺,确保产品质量达到国家标准。
3. 安全要求:严格遵守相关安全法规和操作规程,确保生产过程安全可靠。
4. 环境要求:采取有效的环境保护措施,减少对环境的影响。
三、项目计划1. 前期准备阶段(6个月)a) 进行市场调研,确定项目可行性。
b) 编制项目建设方案和预算,并进行审批。
c) 确定项目建设地点,并进行土地征收和手续办理。
d) 开展技术研究和工艺设计。
2. 设备采购阶段(12个月)a) 编制设备采购计划,并进行审批。
b) 开展设备招标工作,选择合适的供应商。
c) 签订合同,进行设备生产和交付。
3. 建设施工阶段(18个月)a) 编制施工方案和施工图纸,并进行审批。
b) 进行土建施工、设备安装和调试。
4. 试生产阶段(6个月)a) 完成装置的调试和试运行。
b) 对产品质量进行检验和测试。
5. 正式投产阶段a) 完成所有验收手续,取得相关证照。
b) 正式投入生产,实现年产50万吨甲醇的目标。
四、技术要求1. 选择先进的甲醇合成工艺,确保产品质量达到国家标准。
2. 优化反应装置结构,提高反应效率和甲醇收率。
3. 采用高效的催化剂,降低能耗和催化剂用量。
4. 配备先进的控制系统,实现自动化控制和远程监测。
五、安全要求1. 设计合理的安全防护措施,确保操作人员的人身安全。
2. 建立健全的安全管理体系,加强对操作人员的培训和监督。
3. 定期进行设备检修和维护,确保设备安全可靠。
六、环境要求1. 采用清洁能源作为原料,减少二氧化碳和有害气体的排放。
2. 配备先进的废气处理装置,实现废气的净化和排放达标。
年产60万吨煤制甲醇定稿稿

毕业设计题目:年产60万吨煤制甲醇生产工艺初步设计学号:**********名:***系别:地质测量系专业:应用化工技术指导教师:***2012.6.8题目:年产60万吨煤制甲醇生产工艺初步设计摘要甲醇是一种极重要的有机化工原料,是碳一化学的基础产品,在国民经济中占有十分重要的地位。
近年来,随着甲醇下属产品的开发,特别是甲醇燃料的推广应用,甲醇的需求大幅度上升。
为了满足经济发展对甲醇的需求,开展了此60万t/a的甲醇项目。
设计的主要内容是进行工艺论证,物料衡算和热量衡算等。
本设计本着符合国情、技术先进和易得、经济、环保的原则,采用煤炭为原料;利用GSP气化工艺造气;NHD净化工艺净化合成气体;低压下利用列管均温合成塔合成甲醇;三塔精馏工艺精制甲醇;此外严格控制三废的排放,充分利用废热,降低能耗,保证人员安全与卫生。
关键词:甲醇、合成、精馏目录1.总论 (4)1.1概述 (4)2.工艺流程设计 (5)2.1煤气化技术路线的选择 (5)2.2净化工艺方案的选择 (7)2.3合成甲醇工艺的选择 (8)2.4粗甲醇的精馏 (11)3.工艺流程 (14)3.1GSP气化工艺流程 (14)3.2净化装置工艺流程 (15)3.3甲醇合成工艺流程 (19)3.4甲醇精馏工艺流程 (20)3.5氨吸收制冷流程 (22)4.工艺计算 (23)4.1物料衡算 (23)4.1.1精馏工段 (23)4.1.2合成工段 (24)4.1.3变换净化工段 (30)4.1.4气化工段 (33)4.2能量衡算 (33)5.主要设备的计算和选型 (38)5.1甲醇合成塔的设计 (38)5.2水冷器的工艺设计 (40)5.3循环压缩机的选型 (43)5.4气化炉的选型 (43)6.合成车间设计 (45)6.1厂房的整体布置设计 (45)6.2合成车间设备布置的设计 (45)7.三废处理 (46)7.1甲醇生产对环境的污染和处理方法 (46)致谢 (48)参考文献 (48)1.总论1.1概述1.1.1甲醇性质OH。
年产20万吨煤制甲醇合成工艺初步设计煤化工毕业设计
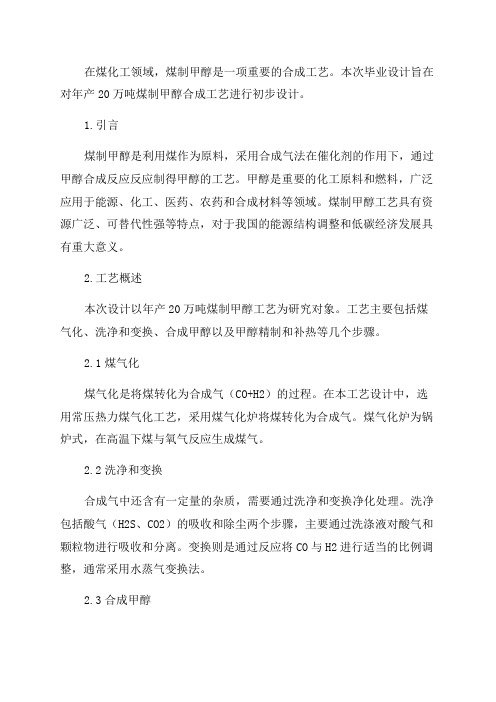
在煤化工领域,煤制甲醇是一项重要的合成工艺。
本次毕业设计旨在对年产20万吨煤制甲醇合成工艺进行初步设计。
1.引言煤制甲醇是利用煤作为原料,采用合成气法在催化剂的作用下,通过甲醇合成反应反应制得甲醇的工艺。
甲醇是重要的化工原料和燃料,广泛应用于能源、化工、医药、农药和合成材料等领域。
煤制甲醇工艺具有资源广泛、可替代性强等特点,对于我国的能源结构调整和低碳经济发展具有重大意义。
2.工艺概述本次设计以年产20万吨煤制甲醇工艺为研究对象。
工艺主要包括煤气化、洗净和变换、合成甲醇以及甲醇精制和补热等几个步骤。
2.1煤气化煤气化是将煤转化为合成气(CO+H2)的过程。
在本工艺设计中,选用常压热力煤气化工艺,采用煤气化炉将煤转化为合成气。
煤气化炉为锅炉式,在高温下煤与氧气反应生成煤气。
2.2洗净和变换合成气中还含有一定量的杂质,需要通过洗净和变换净化处理。
洗净包括酸气(H2S、CO2)的吸收和除尘两个步骤,主要通过洗涤液对酸气和颗粒物进行吸收和分离。
变换则是通过反应将CO与H2进行适当的比例调整,通常采用水蒸气变换法。
2.3合成甲醇通过将洗净和变换后的合成气进入反应器,在催化剂的作用下进行甲醇合成反应。
本设计中选用Cu-Zn-Al催化剂,并采用固定床反应器进行反应。
在适宜的反应温度和压力下,合成气中的CO和H2与催化剂发生反应生成甲醇。
2.4甲醇精制和补热合成甲醇后,通过分离、蒸馏和精制等过程,将甲醇纯化得到符合质量标准的甲醇产品。
同时也需要对合成反应产生的热量进行回收利用,提高热能利用率。
3.工艺流程4.工艺经济分析进行工艺经济分析是评估该工艺可行性的关键环节。
通过对投资、生产能力、原料消耗和产品收益等方面的计算和估算,可以评估工艺的经济效益,为项目决策提供依据。
5.结论本次毕业设计对年产20万吨煤制甲醇合成工艺进行了初步设计,从工艺概述、工艺流程和工艺经济分析等方面对该工艺进行了详细的研究。
煤制甲醇工艺的应用有助于推动我国能源结构调整和低碳经济发展,具有重要的实际意义。
产万吨煤制甲醇生产工艺初步设计
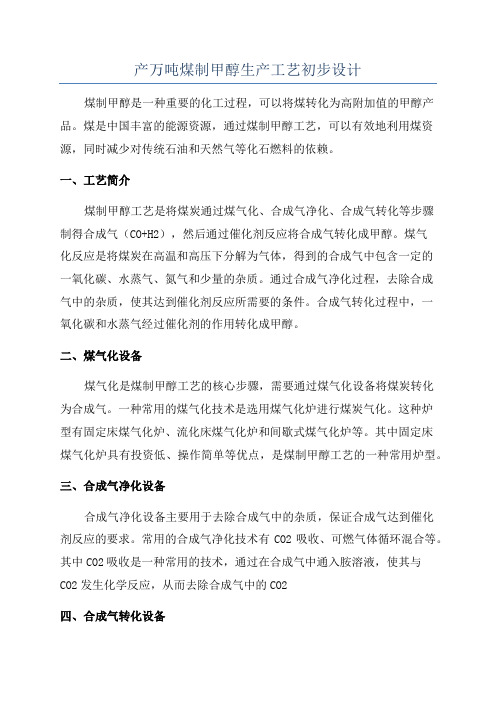
产万吨煤制甲醇生产工艺初步设计煤制甲醇是一种重要的化工过程,可以将煤转化为高附加值的甲醇产品。
煤是中国丰富的能源资源,通过煤制甲醇工艺,可以有效地利用煤资源,同时减少对传统石油和天然气等化石燃料的依赖。
一、工艺简介煤制甲醇工艺是将煤炭通过煤气化、合成气净化、合成气转化等步骤制得合成气(CO+H2),然后通过催化剂反应将合成气转化成甲醇。
煤气化反应是将煤炭在高温和高压下分解为气体,得到的合成气中包含一定的一氧化碳、水蒸气、氮气和少量的杂质。
通过合成气净化过程,去除合成气中的杂质,使其达到催化剂反应所需要的条件。
合成气转化过程中,一氧化碳和水蒸气经过催化剂的作用转化成甲醇。
二、煤气化设备煤气化是煤制甲醇工艺的核心步骤,需要通过煤气化设备将煤炭转化为合成气。
一种常用的煤气化技术是选用煤气化炉进行煤炭气化。
这种炉型有固定床煤气化炉、流化床煤气化炉和间歇式煤气化炉等。
其中固定床煤气化炉具有投资低、操作简单等优点,是煤制甲醇工艺的一种常用炉型。
三、合成气净化设备合成气净化设备主要用于去除合成气中的杂质,保证合成气达到催化剂反应的要求。
常用的合成气净化技术有CO2吸收、可燃气体循环混合等。
其中CO2吸收是一种常用的技术,通过在合成气中通入胺溶液,使其与CO2发生化学反应,从而去除合成气中的CO2四、合成气转化设备合成气转化设备是煤制甲醇工艺的关键设备,通过催化剂的作用将合成气转化为甲醇。
催化剂是合成气转化过程中一个重要的因素,常用的催化剂有铜-锌-铝催化剂和高选择性催化剂等。
催化剂的活性和选择性对甲醇的合成效果具有较大的影响。
五、甲醇分离和纯化设备合成甲醇中常含有杂质和水分,需要进行进一步的分离和纯化。
常用的分离技术有精馏、吸收和萃取等。
甲醇的纯化主要通过精馏等方法,将甲醇中的杂质和水分进行分离,得到高纯度的甲醇产品。
六、废水处理设备煤制甲醇生产过程中会产生大量的废水,其中含有一些有机物和杂质。
为了保护环境,需要对废水进行处理。
产万吨甲醇合成工艺设计方案

设计任务书设计<论文)题目:年产40万吨甲醇合成工艺设学院:内门古化工职业学院专业:应用化工技术班级:应化09-4班学生:张琦指导教师:杨志杰李秀清1.设计<论文)的主要任务及目标(1> 结合专业知识和工厂实习、分析选定合适的工艺参数。
(2> 进行工艺计算和设备选型能力的训练。
(3> 进行工程图纸设计、绘制能力的训练。
2.设计<论文)的基本要求和内容(1> 本车间产品特点及工艺流程。
(2> 主要设备物料、热量衡算、结构尺寸计算及辅助设备的选型计算。
(3> 参考资料3.主要参考文献[1] 谢克昌、李忠.甲醇及其衍生物.北京.化学工业出版社.2002.5~7[2] 冯元琦.联醇生产.北京.化学工业出版社.1989.257~268.[3] 柴诚敬、张国亮。
化工流体流动与传热。
北京。
化学工业出版社。
2000.525-5304.进度安排设计<论文)各阶段名称起止日期1 收集有关资料20181-01-28~2018-02-112 熟悉资料,确定方案2018-02-12~2018-02-263 论文写作2018-02-27~2018-03-194 绘制设计图纸2018-03-20~2018-04-035 准备答辩2018-4-10目录摘要 (1)第1章甲醇精馏的工艺原理 (2)第1.1节基本概念 (2)第1.2节甲醇精馏工艺 (3)1.2.1 甲醇精馏工艺原理 (3)1.2.2 主要设备和泵参数 (3)1.2.3膨胀节材料的选用 (6)第2章甲醇生产的工艺计算 (7)第2.1节甲醇生产的物料平衡计算 (7)第2.2 节生产甲醇所需原料气量 (9)2.2.1生产甲醇所需原料气量 (9)第2.3节联醇生产的热量平衡计算 (15)2.3.1甲醇合成塔的热平衡计算 (15)2.3.2甲醇水冷器的热量平衡计算 (18)第2.4节粗甲醇精馏物料及热量计算 (21)2.4.1 预塔和主塔的物料平衡计算 (21)2.4.2 预塔和主塔的热平衡计算 (25)第3章精馏塔的设计计算 (33)第3.1节精馏塔设计的依据及任务 (33)3.1.1设计的依据及来源 (33)3.1.2设计任务及要求 (33)第3.2节计算过程 (34)3.2.1塔型选择 (34)3.2.2操作条件的确定 (34)3.2.2.1 操作压力 (34)3.2.2.2进料状态 (35)3.2.2.3 加热方式 (35)3.2.2.4 热能利用 (35)第3.3节有关的工艺计算 (36)3.3.1 最小回流比及操作回流比的确定 (36)3.3.2 塔顶产品产量、釜残液量及加热蒸汽量的计算 (37)3.3.3 全凝器冷凝介质的消耗量 (37)3.3.4热能利用 (38)3.3.5 理论塔板层数的确定 (38)3.3.6全塔效率的估算 (39)3.3.7 实际塔板数 (40)第3.4节精馏塔主题尺寸的计算 (40)3.4.1 精馏段与提馏段的体积流量 (40)3.4.1.1 精馏段 (40)3.4.1.2 提馏段 (42)第3.5节塔径的计算 (43)第3.6节塔高的计算 (45)第3.7节塔板结构尺寸的确定 (46)3.7.1 塔板尺寸 (46)3.7.2弓形降液管 (47)3.7.2.1 堰高 (47)3.7.2.2 降液管底隙高度h0 (47)3.7.3进口堰高和受液盘 (47)3.7.4 浮阀数目及排列 (47)3.7.4.1浮阀数目 (48)3.7.4.2排列 (48)3.7.4.3校核 (49)第3.8节流体力学验算 (49)3.8.1 气体通过浮阀塔板的压力降(单板压降> (49)3.8.1.1 干板阻力 (49)3.8.1.2板上充气液层阻力 (49)3.8.1.3由表面张力引起的阻力 (50)第3.9节漏液验算 (50)第3.10节液泛验算 (50)第3.11节雾沫夹带验算 (51)第3.12节操作性能负荷图 (51)3.12.1雾沫夹带上限线 (51)3.12.2液泛线 (52)3.12.3 液体负荷上限线 (52)3.12.4漏液线 (52)3.12.5 液相负荷下限线 (52)第3.13节操作性能负荷图 (53)第3.14节各接管尺寸的确定 (54)3.14.1 进料管 (54)3.14.2釜残液出料管 (55)第3.15节回流液管 (55)第3.16节塔顶上升蒸汽管 (55)第3.17节水蒸汽进口管 (56)第4章辅助设备的计算及选型 (57)第4.1节水冷排设计计算 (58)第4.2节水冷排的设计选型 (59)第4.3节预塔进料泵的选型 (60)参考文献 (62)附录 (63)致谢 (64)年产40万吨甲醇合成工艺设计摘要目前,我国的甲醇市场随着国际市场的原油价格在变化,总体的趋势是走高。
年产60万吨煤制甲醇初步工艺设计
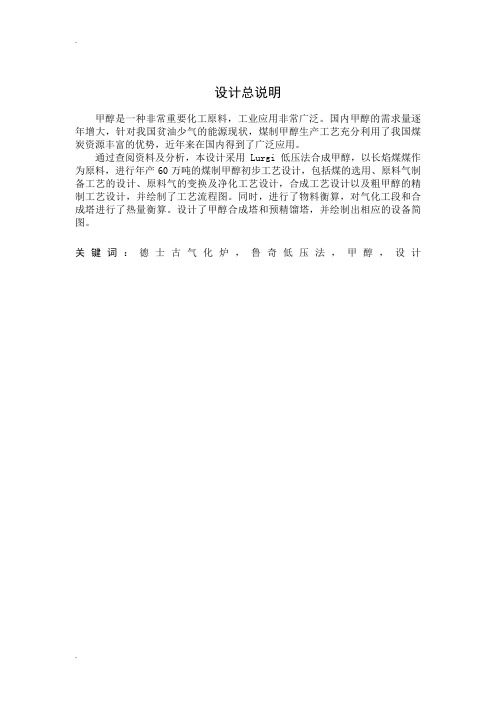
设计总说明甲醇是一种非常重要化工原料,工业应用非常广泛。
国内甲醇的需求量逐年增大,针对我国贫油少气的能源现状,煤制甲醇生产工艺充分利用了我国煤炭资源丰富的优势,近年来在国内得到了广泛应用。
通过查阅资料及分析,本设计采用Lurgi低压法合成甲醇,以长焰煤煤作为原料,进行年产60万吨的煤制甲醇初步工艺设计,包括煤的选用、原料气制备工艺的设计、原料气的变换及净化工艺设计,合成工艺设计以及粗甲醇的精制工艺设计,并绘制了工艺流程图。
同时,进行了物料衡算,对气化工段和合成塔进行了热量衡算。
设计了甲醇合成塔和预精馏塔,并绘制出相应的设备简图。
关键词:德士古气化炉,鲁奇低压法,甲醇,设计Design DescriptionMethanol is a very important chemical raw material, which is widely used in industrial applications. The demand for the domestic methanol increased year by year, in view of the current situation of our country less oil and less gas in the energy, coal to methanol production process makes full use of the advantage of abundant coal resources in our country, in recent years in domestic has been widely used.By means of data and analysis, the design uses Lurgi low-pressure synthesis to produce methanol,taking long flame coal as raw material, designing preliminary process of the coal to methanol with the annual output of 600000 tons ,Including the selection of coal, raw material gas preparation process design, raw gas transformation and purification process design, synthesis process design and crude methanol refining process design, and drawing the process flow chart.At the same time, it finished the material balance calculation, the heat value calculation of the gasification process and the Synthetic tower .it completed the design of the methanol synthesis reactor and distillation distillation tower, finally drawed the corresponding diagram of equipment. Key word:Texaco gasifier, Lurgi low pressure, methanol, design目录1 绪论 (1)1.1甲醇简介 (1)1.1.1物化性质 (1)1.1.2包装及储运 (1)1.1.3毒性和防护 (2)1.1.4质量要求 (2)1.2甲醇的用途 (4)1.3甲醇合成工艺技术 (5)1.3.1.DAVY甲醇技术特点 (5)1.3.2.Lurgi甲醇技术 (5)1.3.3.TOPSOE的甲醇技术特点 (5)1.3.4.TEC甲醇技术特点 (5)1.3.5.三菱重工业公司甲醇技术特点 (6)1.3.6.林德公司甲醇技术的特点 (6)1.4甲醇的生产工艺 (6)1.4.1生产工艺的发展历史 (6)1.4.2天然气制甲醇 (7)1.4.3油制甲醇 (9)1.4.4联醇生产 (9)1.4.5煤制甲醇 (10)1.4.6甲醇生产的发展趋势 (12)1.5 本次设计的目的和意义 (14)2 设计要求及设计依据 (15)2.1 设计题目 (15)2.2 设计原则 (15)2.3 设计要求 (15)2.4 设计依据 (15)3.1煤气化工段 (16)3.1.1煤的选用 (16)3.1.2煤气化过程 (17)3.1.3气化工艺原理 (17)3.1.4气化工艺流程 (19)3.2煤气变换工段 (21)3.2.1煤气变换原理 (21)3.2.2变换工艺流程 (22)3.3煤气净化工段 (23)3.3.1煤气净化方法 (23)3.3.2工艺流程概述 (25)3.4甲醇合成工段 (28)3.4.1合成原理 (28)3.4.2合成工艺流程 (30)3.5甲醇精制工段 (32)3.5.1精制工艺 (32)3.5.2精制要求 (32)3.5.3三塔精馏工艺流程 (33)4 工艺计算 (35)4.1.物料衡算 (35)4.1.1精馏工段物料衡算 (35)4.1.2合成工段物料衡算 (36)4.1.3变换工段物料衡算 (42)4.1.4气化工段物料衡算 (42)4.1.5综合计算 (47)4.2热量衡算 (48)4.2.1气化工段热量衡算 (48)4.2.2合成塔热量衡算 (53)5.1 甲醇合成反应器的设计 (57)5.1.1催化剂的使用量 (57)5.1.2 换热面积的确定 (57)5.1.3换热管数的确定 (57)5.1.4合成塔直径 (58)5.1.5合成塔的壁厚设计 (58)5.1.6壳体设计液压强度校核 (58)5.1.7合成塔封头设计 (59)5.1.8折流板和管板的选择及设计 (59)5.1.9支座 (59)5.2 甲醇精馏工段预精馏塔的设计 (59)5.2.1 进料组成 (60)5.2.2 加碱量的计算 (60)5.2.3 清晰分割法取出二甲醚 (60)5.2.4 预精馏塔塔釜温度计算 (62)5.2.5 理论板数的计算 (63)6 总结 (64)参考文献 (65)致谢 (67)1 绪论1.1甲醇简介1.1.1物化性质甲醇(Methanol ,dried ,CH 3OH )是结构最为简单的饱和一元醇,因在干馏木材中首次发现,故又称“木醇”或“木精”。
年产50万吨甲醇合成工艺初步设计
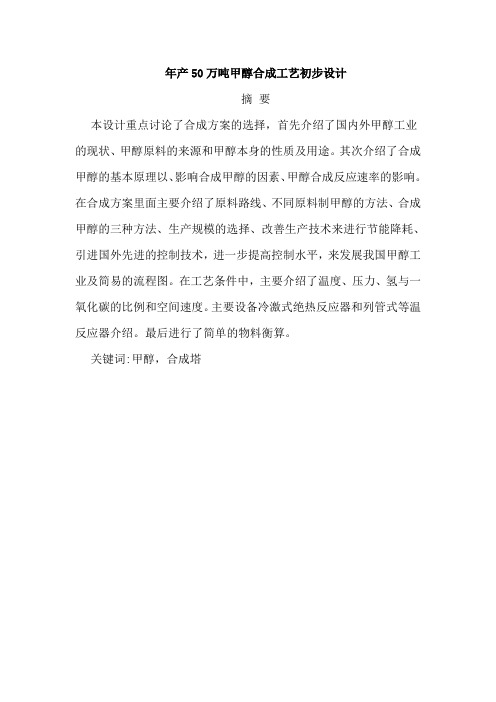
年产50万吨甲醇合成工艺初步设计摘要本设计重点讨论了合成方案的选择,首先介绍了国内外甲醇工业的现状、甲醇原料的来源和甲醇本身的性质及用途。
其次介绍了合成甲醇的基本原理以、影响合成甲醇的因素、甲醇合成反应速率的影响。
在合成方案里面主要介绍了原料路线、不同原料制甲醇的方法、合成甲醇的三种方法、生产规模的选择、改善生产技术来进行节能降耗、引进国外先进的控制技术,进一步提高控制水平,来发展我国甲醇工业及简易的流程图。
在工艺条件中,主要介绍了温度、压力、氢与一氧化碳的比例和空间速度。
主要设备冷激式绝热反应器和列管式等温反应器介绍。
最后进行了简单的物料衡算。
关键词:甲醇,合成塔一、综述(一)国内外甲醇工业现状甲醇是重要的化工原料,应用广泛,主要用于生产甲醛,其消耗量约占甲醇总量的30%~40%;其次作为甲基化剂,生产甲胺、丙烯酸甲酯、甲基丙烯酸甲酯、甲基叔丁基醚、对苯二甲酸二甲酯;甲醇羰基化可生产醋酸、酸酐、甲酸甲酯、碳酸二甲酯等。
其次,甲醇低压羰基化生产醋酸,近年来发展很快。
随着碳化工的发展,由甲醇出发合成乙二醇、乙醛、乙醇等工艺正在日益受到重视。
国内甲醇装置规模普遍较小,且多采用煤头路线,以煤为原料的约占到78%;单位产能投资高,约为国外大型甲醇装置投资的2倍,导致财务费用和折旧费用高,这些都会影响成本。
据了解,我国有近200家甲醇生产企业,但其中10万吨/年以上的装置却只占20%,最大的甲醇生产装置产能也就是60万吨/年,其余80%都是10万吨/年以下的装置。
根据这样的装置格局,业内普遍估计,目前我国甲醇生产成本大约在1400,1800元/吨(约200美元/吨),一旦出现市场供过于求的局面,国内甲醇价格有可能要下跌到约2000元/吨,甚至更低。
这对产能规模小,单位产能投资较高的国内大部分甲醇生产企业来讲会加剧增。
而以中东和中南美洲为代表的国外甲醇装置普遍规模较大。
目前国际上最大规模的甲醇装置产能以达到170万吨/年。
年产50万吨煤制甲醇生产的工艺设计
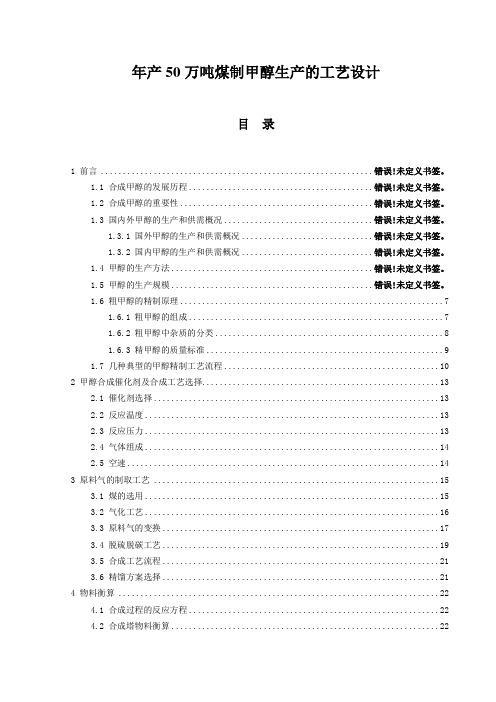
年产50万吨煤制甲醇生产的工艺设计目录1 前言 .............................................................. 错误!未定义书签。
1.1 合成甲醇的发展历程.......................................... 错误!未定义书签。
1.2 合成甲醇的重要性............................................ 错误!未定义书签。
1.3 国内外甲醇的生产和供需概况.................................. 错误!未定义书签。
1.3.1 国外甲醇的生产和供需概况.............................. 错误!未定义书签。
1.3.2 国内甲醇的生产和供需概况.............................. 错误!未定义书签。
1.4 甲醇的生产方法.............................................. 错误!未定义书签。
1.5 甲醇的生产规模.............................................. 错误!未定义书签。
1.6 粗甲醇的精制原理 (7)1.6.1 粗甲醇的组成 (7)1.6.2 粗甲醇中杂质的分类 (8)1.6.3 精甲醇的质量标准 (9)1.7 几种典型的甲醇精制工艺流程 (10)2 甲醇合成催化剂及合成工艺选择 (13)2.1 催化剂选择 (13)2.2 反应温度 (13)2.3 反应压力 (13)2.4 气体组成 (14)2.5 空速 (14)3 原料气的制取工艺 (15)3.1 煤的选用 (15)3.2 气化工艺 (16)3.3 原料气的变换 (17)3.4 脱硫脱碳工艺 (19)3.5 合成工艺流程 (21)3.6 精馏方案选择 (21)4 物料衡算 (22)4.1 合成过程的反应方程 (22)4.2 合成塔物料衡算 (22)4.3 合成反应中各气体消耗和生产量 (24)4.4 新鲜气和驰放气量的确定 (25)4.5 循环气气量的确定 (26)4.6 入塔气和出塔气组成 (26)4.7 甲醇分离器出口气体组成 (28)4.8 贮罐气组成 (29)5 热量衡算 (30)5.1 合成塔热量衡算相关计算式 (30)5.1.1 合成塔入塔热量计算 (30)5.1.2 合成塔的反应热 (31)5.1.3 合成塔出塔热量计算 (31)5.2 合成塔热量损失 (32)5.3 蒸汽吸收的热量 (32)5.4 合成气换热器的热量衡算 (33)5.4.1 合成气入换热器的热量 (33)5.4.2 合成气出换热器的热量 (33)5.5 换热器的热量衡算 (33)5.5.1 入换热器的出合成塔气热量 (33)5.5.2 出换热器的出合成塔气热量 (33)5.6 水冷器的热量衡算 (34)5.6.1 入水冷器的热量 (34)5.6.2 出水冷器的热量 (34)5.6.3 冷却水的用量 (35)5.7 甲醇分离器的热量衡算 (35)6 合成工段的设备选型 (35)6.1 催化剂的使用量 (35)6.2 合成塔的设计 (35)6.2.1 换热面积的确定 (35)6.2.2 换热管数的确定 (36)6.2.3 合成塔直径 (36)6.2.4 合成塔的壁厚设计 (36)6.2.5 壳体设计液压强度校核 (37)6.2.6 合成塔封头设计 (37)6.2.7 折流板和管板的选择及设计 (38)6.2.8 支座 (38)6.3 合成气进塔换热器的选型 (38)6.4 水冷器的选型 (41)6.5 汽包的选型 (42)6.6 加热器的选型 (42)6.7 分离器的设计 (43)6.8 合成气压缩机选型 (43)6.9 出塔气离心泵 (44)6.10 冷却水离心泵 (44)6.11 粗产品泵 (44)7 甲醇精馏工段的设计 (45)7.1 预精馏塔的设计 (45)7.1.1 进料组成 (45)7.1.2 加碱量的计算 (45)7.1.3 清晰分割法取出二甲醚 (46)7.1.4 预精馏塔塔釜温度计算 (47)7.1.5 理论板数的计算 (47)7.2 加压精馏塔设计 (48)7.2.1 清晰分割法分离物系 (48)7.2.2 塔顶、进料、塔釜温度计算 (49)7.2.3 回流比及理论板数计算 (50)7.3 加压精馏塔工艺尺寸设计 (51)7.3.1 平均摩尔质量、密度、表面张力计算 (51)7.3.2 精馏段塔径设计 (52)7.3.3 提馏段塔径设计 (53)7.3.4 塔板工艺尺寸计算 (54)7.3.5 热量衡算 (56)7.4 常压精馏塔设计 (58)7.4.1 清晰分割法分离物系 (58)7.4.2 塔顶、进料、塔釜温度计算 (59)7.4.3 回流比及理论板数计算 (60)7.5 常压精馏塔工艺尺寸设计 (61)7.5.1 平均摩尔质量、密度、表面张力计算 (61)7.5.2 精馏段塔径设计 (63)7.5.3 提馏段塔径设计 (63)7.5.4 精馏段塔板工艺尺寸计算 (64)7.5.5 精馏段塔板负荷性能图 (66)7.5.6 提馏段塔板工艺尺寸计算 (69)7.5.7 提馏段塔板负荷性能图 (71)7.6 热量衡算 (73)8 安全技术与环境保护................................................. 错误!未定义书签。
- 1、下载文档前请自行甄别文档内容的完整性,平台不提供额外的编辑、内容补充、找答案等附加服务。
- 2、"仅部分预览"的文档,不可在线预览部分如存在完整性等问题,可反馈申请退款(可完整预览的文档不适用该条件!)。
- 3、如文档侵犯您的权益,请联系客服反馈,我们会尽快为您处理(人工客服工作时间:9:00-18:30)。
酒泉职业技术学院
毕业设计(论文)2009 级应用化工技术专业
题目:50万吨/年产甲醇合成工艺初步设计
毕业时间:2012年6月
学生姓名:田红梅
指导教师:白老师
班级:2009应化(5)班
2011年6月20日
酒泉职业技术学院2012 届各专业
毕业论文(设计)成绩评定表
姓名田红梅班级2009应化(5)班专业应用化工技术
指导教师第一次指导意见题目的确定,内容的审核与要求,以及图表的要求,封面设计的修正,成绩评定表的给定,摘要重新,标点的改正,关键词的修改,目录标点符号的修改,章节的修改与确定以及其排版的修改。
2011 年3 月20 日
指导教师第二次指导意见内容的确定,摘要的修改,目录标点再一次的修改,内容的修改与流程图的修改和表格的确定,计算结果的修改与意见,致谢词的要求,参考文献的要求。
2011年4 月10 日
指导教师第三次指导意见字体撰写不符合规范要求,图和表的表示方法不准确,整个内容需再一次审查,致谢词字数太少,参考文献格式部分有误,继续修改,文章中目录字体要求统一,整个篇章的进行细化和修改。
2011年5 月1 日
指导教师评语及评分
田红梅同学做的50万吨/年产甲醇合成工艺初步设计,能够跟当前煤化工结合起来,较为全面的考虑和设计了甲醇生产工艺,选择的生产方案较为先进,跟所学专业进行了有效的结合和联系,取得了较为好的效果。
在整个设计过程中任务完成良好,态度好,谦虚认真,顺利地完成了毕业设计。
同意推荐答辩。
成绩:良好签字(盖章)2011年6月16日
答辩小
组评价
意见及
评分
成绩:签字(盖章)年月日教学系
毕业实
践环节
指导小
组意见
签字(盖章)年月日学院毕
业实践
环节指
导委员
会审核
意见
签字(盖章)年月日说明:1、以上各栏必须按要求逐项填写。
2、此表附于毕业论文(设计)封面之后。
摘要
本设计重点讨论了合成方案的选择,首先介绍了国内外甲醇工业的现状、甲醇原料的来源和甲醇本身的性质及用途。
其次介绍了合成甲醇的基本原理以、影响合成甲醇的因素、甲醇合成反应速率的影响。
在合成方案里面主要介绍了原料路线、不同原料制甲醇的方法、合成甲醇的三种方法、生产规模的选择、改善生产技术来进行节能降耗、引进国外先进的控制技术,进一步提高控制水平,来发展我国甲醇工业及简易的流程图。
在工艺条件中,主要介绍了温度、压力、氢与一氧化碳的比例和空间速度。
主要设备冷激式绝热反应器和列管式等温反应器介绍。
最后进行了简单的物料衡算。
关键词:甲醇,合成塔,煤
一、综述
我国是一个少油多煤的国家,煤炭贮量非常丰富,煤种齐全。
但到目前为止,我国煤炭资源的综合利用水平还很低,基本上处于小型化、分散化、产品单一化、浪费大、污染严重和低效益的状态。
因此建设大型煤炭综合利用的焦化基地,实现煤炭资源的综合利用,生产高附加值的深加工产品,调整产业结构,保护环境,带动区域经济乃至行业经济的发展已成为必然趋势。
(一)国内外甲醇工业现状
国内甲醇装置规模普遍较小,且多采用煤头路线,以煤为原料的约占到78%;单位产能投资高,约为国外大型甲醇装置投资的2倍,导致财务费用和折旧费用高,这些都会影响成本。
据了解,我国有近200家甲醇生产企业,但其中10万吨/年以上的装置却只占20%,最大的甲醇生产装置产能也就是60万吨/年,其余80%都是10万吨/年以下的装置。
根据这样的装置格局,业内普遍估计,目前我国甲醇生产成本大约在1400~1800元/吨(约200美元/吨),一旦出现市场供过于求的局面,国内甲醇价格有可能要下跌到约2000元/吨,甚至更低。
这对产能规模小,单位产能投资较高的国内大部分甲醇生产企业来讲会加剧增。
而以中东和中南美洲为代表的国外甲醇装置普遍规模较大。
目前国际上最大规模的甲醇装置产能以达到170万吨/年。
2008年4月底,沙特甲醇公司170万吨/年的巨型甲醇装置在阿尔朱拜勒投产,使得该公司5套大型甲醇装置的总产能投资大幅下降,成本竞争力大为增强。
据石油和化工规划院分析,目前国外天然气产地在建的大型甲醇生产装置成本只有60~80美元/吨。
不仅如此,国外大型甲醇装置多以天然气为原料,采用天然气两端转化技术,包括德国鲁奇公司,丹麦托普索公司,英国卜内门化工公司和日本三菱公司等企业的技术。
相对煤基甲醇技术,天然气转化技术成熟可靠,转化规模受甲醇规模影响较小,装置紧凑,占地面积小。
尽管近年来国际
市场天然气价格也在上涨。
但国外甲醇生产企业依靠长期供应协议将价格影响因素将至最低。
而我国大部分甲醇生产以煤为原料,气化装置规模有限和占地面积大的先天缺陷制约着甲醇生产装置向大型化发展。
同时近年来煤炭价格的大幅度上涨对本来还具有一定成本优势的煤基甲醇生产较大影响,再加上煤基甲醇大多建在西部地区,运输费用较高。
种种因素进一步削弱了煤基甲醇的价格竞争力。
国外大型甲醇装置集中投产后,传统的销售渠道无法消化聚然增多的甲醇。
2010年之前,国外甲醇以低价冲击中国市场几无悬念。
现实是:国外甲醇生产规模大,技术先进,管理严格,能耗低,产品质量稳定;国内大甲醇装置的产品质量已经达到国际水平,但许多小甲醇或联醇装置产品质量尚不稳定。
据全国化学工程技术委员会副主席,中石化宁波工程有限公司副总工程师唐宏吉介绍,国内煤基甲醇每吨产品能耗为50~60焦,耗煤1.6吨左右,耗水22~30吨。
以天然气为原料生产的甲醇每吨产品能耗约为40焦,耗天然气900~1150
立方米,耗水15~20吨。
我国小型联醇装置每吨产品耗能则高达70焦。
而国外大型甲醇装置基本都以天然气为原料,并且每吨产品能耗只有25~30焦,耗天然气760~920立方米,耗水10~15吨。
另外,由于我国甲醇生产大多采用煤基路线,酸性气体和灰渣排放量最大,需投入较多资金建设环保处理设施。
而国外以天然气为原料的大型甲醇装置,基本属于清洁生产,对环境影响较小,环境投入也相应较小。
许多业内专家都向记者提到了国内甲醇生产的一个先天不足;我国甲醇生产所需原料煤炭、天然气主要集中在经济较落后、交通不便的西部,而我国甲醇市场消费中心在华东和华南地区。
西部甲醇运到华东和华南地区铁路和公路的长途运输,运输费用最高达400元/吨(约55美元/吨)。
甲醇产地与消费地相距较远,导致交通运输成为今后我国甲醇发展的主要瓶颈。