自动换刀系统
数控机床的自动换刀系统操作指南

数控机床的自动换刀系统操作指南数控机床的自动换刀系统是现代机床中重要的工具,它的作用是实现多种刀具的自动切换,提高生产效率和加工精度。
本文将为您介绍数控机床的自动换刀系统的操作指南。
1. 系统概述数控机床的自动换刀系统由控制单元、刀库、刀臂、刀具以及相关传感器组成。
通过控制单元的指令,刀库中的刀具可以自动切换到刀臂上,实现刀具的自动更换。
2. 操作前的准备在操作数控机床的自动换刀系统之前,首先要进行以下的准备工作:- 确认机床的电源是否正常,机床内部是否处理干净。
- 确认自动换刀系统的刀库是否存放有足够的刀具。
- 确认程序中的执行代码是否正确,不会发生刀具碰撞。
3. 操作步骤以下是数控机床的自动换刀系统的操作步骤:(1) 手动操作模式:首先将机床设置为手动操作模式,确保机床处于不会自动运行的状态。
(2) 加载刀具:通过控制单元的操作指令,将所需刀具从刀库中选取出来。
(3) 位置定位:使用机床的控制面板或相关软件对刀臂进行位置定位,使其准确匹配刀具的安装位置。
(4) 刀具安装:将选取的刀具正确安装到刀臂上,确保刀具牢固固定,避免出现松动的情况。
(5) 参数设定:在机床的控制面板或相关软件中设定刀具的相关参数,如切削速度、进给速度等。
(6) 刀具校对:在刀具安装完成后,进行刀具校对的操作,确保刀具位置的准确性。
(7) 确认操作:在进行自动换刀操作之前,要仔细确认刀具的安装是否正确,刀具是否符合加工要求。
(8) 运行程序:确认刀具安装正确后,将机床切换到自动运行模式,在控制单元中选择相应的程序,运行自动换刀操作。
(9) 监测切换:在自动换刀操作过程中,通过机床的控制面板或相关软件实时监测刀具的切换过程,确保刀具的准确切换。
(10) 完成切换:当刀具切换完成后,机床会自动停止,并显示切换完成的提示信息。
4. 常见问题及解决方法在使用数控机床的自动换刀系统时,可能会遇到以下的问题,下面为您提供一些建议的解决方法:- 刀具松动:检查刀具安装是否正确,确保刀具紧固螺母牢固固定。
数控铣床自动换刀化改造(刀库式加工中心)

第一章绪论1.1 数控设备的发展历史>第一代数控系统:1952年至1959年,采川电子管元件。
>第二代数控系统:1959年开始,采刖晶体管元件。
>第三代数控系统:1965年开始,采川集成电路。
>第四代数控系统:1970年开始,采刖人规模集成电路及小型通用计算机。
>第五代数控系统:1974年开始,采用微处理机和微型计算机。
1.2 自动换刀系统的意义从换刀系统发展的历史米看,1956年日本富士通研究成功数控转塔式冲床,美国IBM公司同期也研制成功了“APT”(刀具程序控制装置)。
1958年美国K&T公司研制出带ATC(自动刀具交换装置)的加工中心。
1967年出现了FMS(柔性制造系统)。
1978年以后,加工中心迅速发展,带有ATC装置,可实现多种工序加工的机床,步入了机床发展的黄金时代。
1.1.1 加工中心加工中心机床的出现,加之CAD技术、信息技术、网络控制技术以及系统工程学的发展,为单机数控自动化向计算机控制的多机制造系统自动化方向发展,创造了必要的条件.计算机群控系统即直接数控(Direct NC-DNC)系统,就是这一发展趋向的具体体观。
DNC系统使用一台较大的计算机,控制与管理多台数控机床和数控加工中心,能进行多品种、多工序的加工。
加工中心机床配备有装载多把刀具的刀具库,有自动更换刀具的功能,一次装夹中可以完成钻、镗、铣、铰等工序,特别适用于箱体类零件的多面、多工序加工。
它能完成车削加工的同时,兼有铣、镗、钻孔、攻丝等功能。
1.1.2 柔性制造单元柔性制造单元(FMC)是由中心控制计算机、加工中心与自动交换工件(AWC,APC)装置所组成。
工件一次装夹后可在柔性制造单元中的加工中心上加工,使得加工的柔性(可编程性)、加工精度和生产效率更高。
在柔性制造单元中,中心控制计算机负责作业调度、自动检测与工况自动监控等功能。
工件装在自动交换工件装置(工作台)上在中心控制计算机控制下传送到加工中心上加工;加工中心接收中心控制计算机传送来的数控程序进行加工,并将工况数据送中心控制计算机处理,如工件尺寸自动检测和补偿,刀具损坏和寿命躲控等。
加工中心自动换刀系统设计(盘式)
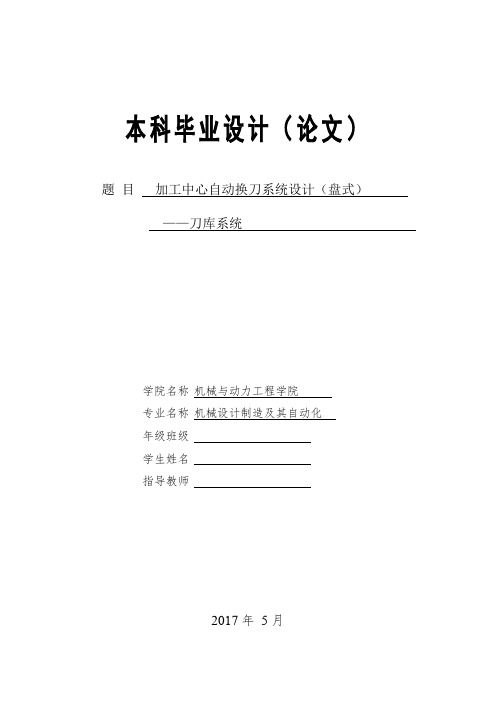
本科毕业设计(论文)题目加工中心自动换刀系统设计(盘式)——刀库系统学院名称机械与动力工程学院专业名称机械设计制造及其自动化年级班级学生姓名指导教师2017年5月目录前言1.加工中心概述 (1)1.1加工中心发展现状和发展趋势 (1)1.2加工中心的特点 (2)1.3加工中心的分类 (3)1.4加工中心的结构 (5)1.5加工中心刀库及自动换刀装置 (6)1.5.1加工中心刀库形式 (6)1.5.2加工中心的自动换刀装置 (8)1.5.3刀库结构及换刀过程 (9)2.刀库传动设计…………………………………………………………………2.1电动机的选择…………………………………………………………2.1.1初选电动机………………………………………………………2.1.2校核电动机………………………………………………………2.2运动和动力参数计算……………………………………………2.3蜗杆传动设计…………………………………………………………2.3.1蜗杆传动的选择…………………………………………………2.3.2蜗杆传动的主要参数及几何尺寸计算…………………………2.3.3校核齿根弯曲疲劳强度…………………………………………2.3.4验算蜗杆传动的效率、润滑及热平衡……………………………2.3.5蜗杆和蜗轮的结构设计…………………………………………2.4传动轴设计…………………………………………………………2.4.1轴的材料…………………………………………………………2.4.2蜗杆轴的结构设计………………………………………………2.4.3蜗轮轴的结构设计………………………………………………2.4.4轴系零、部件的校核………………………………………………3.刀库结构设计………………………………………………………………3.1刀盘设计………………………………………………………………3.2刀库设计………………………………………………………………4.液压系统的设计……………………………………………………………4.1液压缸的载荷计算…………………………………………………4.2液压缸的主要参数计算……………………………………………结论…………………………………………………………………………………致谢…………………………………………………………………………………参考文献…………………………………………………………………………前言目前机床发展的主要趋势是加工中心,其在机械制造业中得到了大规模的应用,而且加工中心还在不断地向高速化、高效率、高精度的目标发展着,在机床结构方面,多轴化、复合加工等方面的创新也日趋活跃。
数控机床自动换刀装置
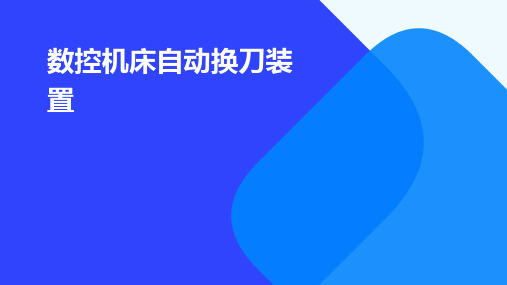
02
数控机床自动换刀装置 的结构与设计
刀库设计
刀库容量
根据数控机床的加工需求, 合理设计刀库容量,确保 能够存放足够数量的刀具。
刀具存放方式
采用合适的刀具存放方式, 如刀具架、刀具套等,以 便于刀具的存取和管理。
刀库布局
根据数控机床的整体布局 和加工要求,合理布置刀 库的位置和方向,以提高 换刀效率和加工精度。
例如,在发动机缸体的加工中,需要使用不同种类的刀具进行粗加工、半精加工和精加工。数控机床 自动换刀装置可以在加工过程中自动识别需要更换的刀具,并快速、准确地完成换刀操作,保证了加 工过程的连续性和稳定性。
应用案例二:航空航天业
航空航天业对零部件的加工精度和效率要求极高,数控机床自动换刀装置在航空 航天业中也有着广泛的应用。例如,在飞机机身和机翼的制造中,需要使用大型 五轴数控机床进行加工,而大型五轴数控机床的换刀时间较长,影响了加工效率 。
数控机床自动换刀装置的应用,可以大大缩短换刀时间,提高加工效率。同时, 由于航空航天业对零部件的加工精度要求极高,数控机床自动换刀装置的精确性 和稳定性也得到了充分验证,为航空航天业的发展提供了有力支持。
应用案例三:模具制造业
模具制造业是数控机床自动换刀装置的重要应用领域 之一。在模具的制造过程中,需要使用不同种类的刀 具进行粗加工、半精加工和精加工。数控机床自动换 刀装置的应用,可以大大提高模具的加工效率和精度 。
分类与比较
按换刀方式分类
数控机床自动换刀装置可分为机械手换刀和机器人换刀两种 方式。机械手换刀方式具有结构简单、成本低等优点,但换 刀速度较慢;机器人换刀方式具有换刀速度快、精度高等优 点,但结构复杂、成本较高。
按刀库类型分类
数控机床自动换刀装置可分为固定刀库和旋转刀库两种类型 。固定刀库具有容量大、换刀速度快等优点,但结构复杂、 成本较高;旋转刀库具有结构简单、成本低等优点,但容量 较小、换刀速度较慢。
FANUCOiMD数控系统斗笠式刀库实现自动换刀

N 1 M 9 9
%
( 换刀结束 ,返回主程序)
( 2)P MC 与NC 程序的配合 。斗笠式 刀库 实 现 自动换 刀是P MC与NC 程 序 的配合 来完成 的 。
P M C在 整 个 换 刀 过 程 中 主 要 控 制 刀 库 的 正 /反
转 、刀库的前进 /后退、松 刀 /紧刀阀的动作以及 换 刀动作 顺序 。主轴 的上 升 、下 降和定 位都是 由
N C系统 程序 控 制 的 。
( 8 )刀库向远离 主轴 中心位置侧平移如附图f
所示 ,直  ̄ J I P L C 接 收 到 传 感 器A发 出 的 反馈 确认 信
步。
斗
换取 ,根据 刀库选取的不同 ,换刀系统 的控制方式 也不同。加 工中心常用的刀库有斗笠式 、凸轮式、 链条式 等 ,斗笠式 刀库是加工中, Ol : k 较常见的一种 换刀装置 ,换 刀过程简单 ,体积小、安装方便 、易 于控制和维护等优点 ,因此在中小型加工 中心上得 到了广 泛的应用 。但对 刀库的定位要求高 ,而且在 换刀过 程中需要轴配合其动作 ,而P L C 是无法直接 参与数控轴的控制。基于F A NUC 0 i MD数控 系统 利用NC 宏程序可以把轴控制与P MC 控制有机地结 合 ,它可以按一定的逻辑控制P Mc 和进给轴 ,从而 实现 包含轴移动的换 刀控制。在本文 中,笔者 结合
后 ,这 时 刀库 转 动 , 当 目标 刀具 对 正 主 轴 正 下 方 时 ,主 轴 下 移 ,使 刀具 进 入主 轴 锥 孔 内 ,刀具 夹 紧 后 ,刀库 退 回原 来 的 位 置 ,换 刀结 束 。 刀库 具 体 动 作过程如下 :
数控加工中心自动换刀系统的研究
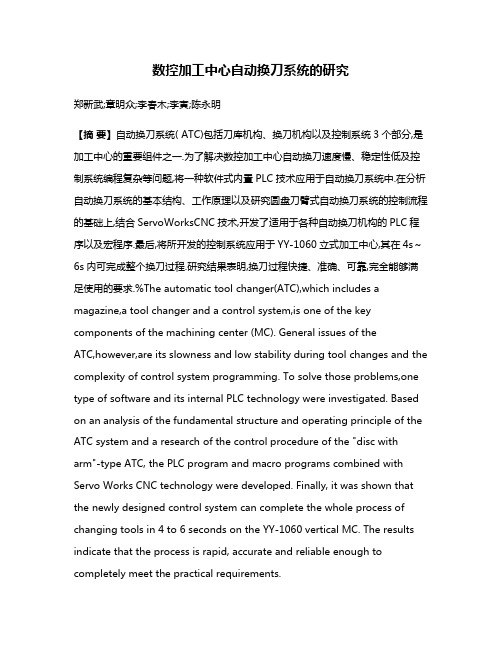
数控加工中心自动换刀系统的研究郑新武;章明众;李春木;李寅;陈永明【摘要】自动换刀系统( ATC)包括刀库机构、换刀机构以及控制系统3个部分,是加工中心的重要组件之一.为了解决数控加工中心自动换刀速度慢、稳定性低及控制系统编程复杂等问题,将一种软件式内置PLC技术应用于自动换刀系统中.在分析自动换刀系统的基本结构、工作原理以及研究圆盘刀臂式自动换刀系统的控制流程的基础上,结合ServoWorksCNC技术,开发了适用于各种自动换刀机构的PLC程序以及宏程序.最后,将所开发的控制系统应用于YY-1060立式加工中心,其在4s~6s内可完成整个换刀过程.研究结果表明,换刀过程快捷、准确、可靠,完全能够满足使用的要求.%The automatic tool changer(ATC),which includes a magazine,a tool changer and a control system,is one of the key components of the machining center (MC). General issues of theATC,however,are its slowness and low stability during tool changes and the complexity of control system programming. To solve those problems,one type of software and its internal PLC technology were investigated. Based on an analysis of the fundamental structure and operating principle of the ATC system and a research of the control procedure of the "disc with arm"-type ATC, the PLC program and macro programs combined with Servo Works CNC technology were developed. Finally, it was shown that the newly designed control system can complete the whole process of changing tools in 4 to 6 seconds on the YY-1060 vertical MC. The results indicate that the process is rapid, accurate and reliable enough to completely meet the practical requirements.【期刊名称】《机电工程》【年(卷),期】2011(028)012【总页数】4页(P1457-1460)【关键词】加工中心;自动换刀;可编程逻辑控制器【作者】郑新武;章明众;李春木;李寅;陈永明【作者单位】厦门大学机电工程系,福建厦门361005;厦门大学机电工程系,福建厦门361005;厦门大学机电工程系,福建厦门361005;厦门大学机电工程系,福建厦门361005;厦门大学机电工程系,福建厦门361005【正文语种】中文【中图分类】TG71;TH39;TD2730 引言利用刀库(MAG)实现自动换刀是目前加工中心大量使用的换刀方式,独立的刀库大大增加了刀具的存储数量,有利于扩大机床的功能,并能较好地隔离各种影响加工精度因素的干扰[1]。
自动换刀系统
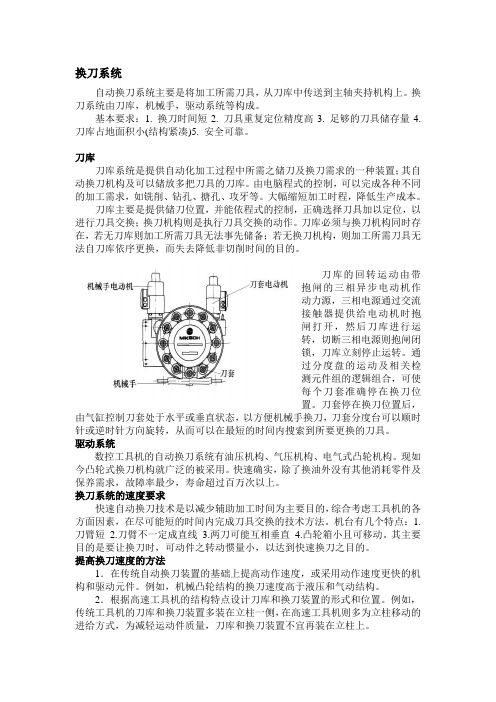
换刀系统自动换刀系统主要是将加工所需刀具,从刀库中传送到主轴夹持机构上。
换刀系统由刀库,机械手,驱动系统等构成。
基本要求:1. 换刀时间短2. 刀具重复定位精度高3. 足够的刀具储存量4. 刀库占地面积小(结构紧凑)5. 安全可靠。
刀库刀库系统是提供自动化加工过程中所需之储刀及换刀需求的一种装置;其自动换刀机构及可以储放多把刀具的刀库。
由电脑程式的控制,可以完成各种不同的加工需求,如铣削、钻孔、搪孔、攻牙等。
大幅缩短加工时程,降低生产成本。
刀库主要是提供储刀位置,并能依程式的控制,正确选择刀具加以定位,以进行刀具交换;换刀机构则是执行刀具交换的动作。
刀库必须与换刀机构同时存在,若无刀库则加工所需刀具无法事先储备;若无换刀机构,则加工所需刀具无法自刀库依序更换,而失去降低非切削时间的目的。
刀库的回转运动由带抱闸的三相异步电动机作动力源,三相电源通过交流接触器提供给电动机时抱闸打开,然后刀库进行运转,切断三相电源则抱闸闭锁,刀库立刻停止运转。
通过分度盘的运动及相关检测元件组的逻辑组合,可使每个刀套准确停在换刀位置。
刀套停在换刀位置后,由气缸控制刀套处于水平或垂直状态,以方便机械手换刀,刀套分度台可以顺时针或逆时针方向旋转,从而可以在最短的时间内搜索到所要更换的刀具。
驱动系统数控工具机的自动换刀系统有油压机构、气压机构、电气式凸轮机构。
现如今凸轮式换刀机构就广泛的被采用。
快速确实,除了换油外没有其他消耗零件及保养需求,故障率最少,寿命超过百万次以上。
换刀系统的速度要求快速自动换刀技术是以减少辅助加工时间为主要目的,综合考虑工具机的各方面因素,在尽可能短的时间内完成刀具交换的技术方法。
机台有几个特点:1.刀臂短2.刀臂不一定成直线 3.两刀可能互相垂直 4.凸轮箱小且可移动。
其主要目的是要让换刀时,可动件之转动惯量小,以达到快速换刀之目的。
提高换刀速度的方法1.在传统自动换刀装置的基础上提高动作速度,或采用动作速度更快的机构和驱动元件。
数控机床自动换刀系统
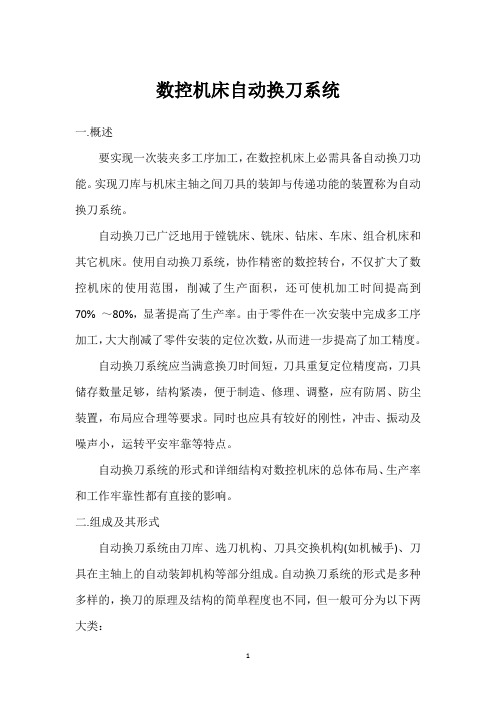
数控机床自动换刀系统一.概述要实现一次装夹多工序加工,在数控机床上必需具备自动换刀功能。
实现刀库与机床主轴之间刀具的装卸与传递功能的装置称为自动换刀系统。
自动换刀已广泛地用于镗铣床、铣床、钻床、车床、组合机床和其它机床。
使用自动换刀系统,协作精密的数控转台,不仅扩大了数控机床的使用范围,削减了生产面积,还可使机加工时间提高到70% ~80%,显著提高了生产率。
由于零件在一次安装中完成多工序加工,大大削减了零件安装的定位次数,从而进一步提高了加工精度。
自动换刀系统应当满意换刀时间短,刀具重复定位精度高,刀具储存数量足够,结构紧凑,便于制造、修理、调整,应有防屑、防尘装置,布局应合理等要求。
同时也应具有较好的刚性,冲击、振动及噪声小,运转平安牢靠等特点。
自动换刀系统的形式和详细结构对数控机床的总体布局、生产率和工作牢靠性都有直接的影响。
二.组成及其形式自动换刀系统由刀库、选刀机构、刀具交换机构(如机械手)、刀具在主轴上的自动装卸机构等部分组成。
自动换刀系统的形式是多种多样的,换刀的原理及结构的简单程度也不同,但一般可分为以下两大类:由刀库和主轴的相对运动实现刀具交换。
用这种形式交换刀具时,主轴上用过的刀具送回刀库和从刀库中取出新刀,这两个动作不能同时进行,选刀和换刀由数控定位系统来完成,因此换刀时间长,换刀动作也较多。
由机械手进行刀具交换。
由于刀库及刀具交换方式的不同,换刀机械手也有多种形式。
图1 换刀机械手的形式图1(a),(b),(c)为双臂回转机械手,能同时抓取和装卸刀库和主轴(或中间搬运装置)上的刀具,动作简洁,换刀时间短。
图(d)虽然不是同时抓取刀库和主轴上的刀具,但换刀预备时间及将刀具还回刀库的时间与机加工时间重复,因而换刀时间也很短。
抓刀运动可以是旋转运动,也可以是直线运动。
图1(a)为钩手,抓刀运动为旋转运动;图(b)为抱手,抓刀运动为两个手指旋转;(c)和(d)为叉手,抓刀运动为直线运动。
浅谈基于PLC的刀库自动换刀控制系统设计

图6 整体臂架第四阶模态振型图图7 整体臂架第五阶模态振型图图8 整体臂架第六阶模态振型图144中国设备工程 2024.03(上)图1 电源接线图3.2 控制系统的电路设计为了方便绘制PLC接线图和编写PLC程序,将每个输入/输出设备与PLC的输入/输出点相对应。
3.2.1 PLC的IO接线在这个设计里,首先设计了已有的PLC的输入点和输出点,接下来,按照目前的项目流程需求,为目前的设备设置了特定的PLC连接线,在程序设计中,这样就可以更清楚地看到当前设备的输入点和输出点。
3.2.2 电机接线三相电机运转时,装置的工作部件,必须使用三相电源,而且还会出问题,此时,若在装置的进电线上加装一组防风开关,那么在电动机发生故障的时候,而不会影响其他部件的工作,对现有设备马达进行保护。
三相电源通过交流保护空气开关的上端进入后,把它的下端头和AC接触器的上端头连接起来,当220V的电力供应完毕后。
电动机在PLC的控制下运转,在接触器绕组通电和常开度连接处,电动机就能正常运转。
4 控制系统的程序设计4.1 程序主流程图按照设计要求,本文给出了该控制系统的主要程序流程图,如图2所示。
它将目前的位置2传递给数据寄存器地址D100,以执行随后的目前的程序比较。
图3 位置传送块程序 4.2.2 当前刀号位置传送程序如图4所示,在程序在向网络72自动执行时,程序会自动判断输入继电器X14的状态,如果接受了这个任务,PLC将常数2自动转移到了目前的数据寄存器D102上,在同一时间内,输入继电器X15被激活,此时,数据寄存器常数3也被转移到了数据寄存图4 刀库位置传送程序电机正反转判断程序在程序开始的时候,要判断所选刀具编号D100当前刀具编号D102的尺寸,当D100大于D102时,M10表示,把它打开,并计算其差异,然后把它放到的数据寄存器里,再次判定D300中的数据是否大于图5 故障指示灯4.3 程序设计转刀装置的基础工作是转刀。
自动换刀系统设计

自动换刀系统设计摘要数控车床将向中高档发展,对数控刀架需求量将大大增加。
随着数控车床的发展,数控刀架也向快速换刀、电液组合驱动和伺服驱动方向发展。
本设计采用电液组合驱动,主要完成了八工位卧式刀架的机械结构设计和利用三菱FX2N可编程控制器(PLC)对自动换刀系统的控制系统进行设计。
机械设计主要包括分度机构及定位机构的选择和刀架主轴的设计等。
控制部分为自动和手动换刀两种工作方式。
关键词数控刀架,PLC控制,液压控制ABSTRACTNumerical Control lathe will be developed to middle and senior grade in the future. It is estimated that the demand for NC tool carrier will be much greater. NC tool start to the rapid tool change, electrohydraulic servo driving and portfolio-driven direction with the development of NC lathes.The paper takes electrohydraulic driving. It was discussed that mechanical design and control system design by Mitsubishi FX2N programmable logic controller (PLC) of the eight engineering automatic tool change. Machinery part includes the positioning tools and the degree of positioning choices and tool spindle design. Control part is divided into auto control and manual control.Key words ATC,PLC control,Hydraulic control目录摘要 (I)ABSTRACT (II)1 绪论 (1)1.1 课题背景 (1)1.2 研究的主要内容 (1)2 自动换刀系统机械部分设计 (3)2.1刀座的设计 (3)2.1.1 刀座基本形状及尺寸的确定 (3)2.1.2 刀座强度的校核 (6)2.2 刀盘主要尺寸的确定 (7)2.3 传动齿轮的设计 (8)2.4 刀架主轴的设计 (8)2.4.1 初步确定轴的最小直径 (8)2.4.2 轴的结构设计 (9)2.4.3 校核键的强度 (11)2.5 共轭分度凸轮机构基本参数的确定 (11)2.5.1 共轭分度凸轮的介绍 (11)2.5.2 主要运动参数的选择 (12)2.5.3 主要几何尺寸的确定 (12)2.6 端齿盘的选择 (12)2.6.1 端齿盘的介绍 (13)2.6.2 端齿盘的特点 (13)2.6.3 端齿盘主要参数的设计计算 (13)2.6.4 螺栓组强度校核 (17)2.7 液压缸的结构及主要尺寸的设计 (18)2.8 箱体的基本形状及尺寸确定 (19)2.9 液压马达及接近开关的选择 (19)2.9.1 液压马达的选择 (19)2.9.2 接近开关的选择 (19)2.10 润滑剂的选择 (20)2.11 对压力油的要求 (20)3 PLC控制的硬件设计 (21)3.1 换刀系统的工作原理 (21)3.2 PLC简介 (22)3.2.1 PLC的分类 (22)3.2.2 PLC的特点及主要功能 (23)3.3 PLC控制系统的硬件选择和资源配置 (25)3.3.1 自动换刀控制系统要求 (25)3.3.2 PLC型号的选择 (26)3.4 控制系统元件列表 (27)3.5 PLC I/O地址的分配 (28)3.6 PLC外围接线图 (29)4 控制系统PLC程序设计 (29)4.1 系统流程图的确设计 (30)4.2 PLC程序设计 (31)4.2.1程序结构设计 (31)4.2.2 自动换刀的程序设计 (31)4.2.3 手动换刀程序设计 (35)4.2.4 数据传送程序的设计 (37)4.3 程序的调试 (38)5 结论 (39)参考文献 (40)致谢 (41)1 绪论1.1 课题背景从自动换刀系统发展的历史来看,1956年日本富士通研究成功数控转塔式冲床,美国IBM公司同期也研制成功了“APT”(刀具程序控制装置)。
自动换刀装置的结构原理与维修

自动换刀装置的结构原理与维修8.4.1 自动换刀装置的形式自动换刀装置是加工中心的重要执行机构,它的形式多种多样,目前常见的有以下几种。
1.回转刀架换刀数控机床使用的回转刀架是最简单的自动换刀装置,有四方刀架、六角刀架,即在其上装有四把、六把或更多的刀具。
回转刀架必须具有良好的强度和刚度,以承受粗加工的切削力:同时要保证回转刀架在每次转位的重复定位精度。
图8-17为数控车床六角回转刀架,它适用于盘类零件的加工。
在加工轴类零件时,可以用四方回转刀架。
由于两者底部安装尺寸相同,更换刀架十分方便。
图8-17 数控车床六角回转刀架1-活塞 2-刀架体 3、7-齿轮 4-齿圈 5-空套齿轮6-活塞 8-齿条 9-固定插销 10、11-推杆 12-触头回转刀架的全部动作由液压系统通过电磁换向阀和顺序阀进行控制,它的动作分为4个步骤:(1)刀架抬起当数控装置发出换刀指令后,压力油由a孔进入压紧液压缸的下腔,活塞1上升,刀架体2抬起,使定位用的活动插销10与固定插销9脱开。
同时,活塞杆下端的端齿离合器与空套齿轮5结合。
(2)刀架转位当刀架抬起后,压力油从c孔进入转位液压缸左腔,活塞6向右移动,通过联接板带动齿条8移动,使空套齿轮5作逆时针方向转动。
通过端齿离合器使刀架转过60º。
活塞的行程应等于齿轮5分度圆周长的1/6,并由限位开关控制。
(3)刀架压紧刀架转位之后,压力油从b孔进入压紧液压缸上腔,活塞1带动刀架体2下降。
齿轮3的底盘上精确地安装有6个带斜楔的圆柱固定插销9,利用活动插销10消除定位销与孔之间的间隙,实现反靠定位。
刀架体2下降时,定位活动插销10与另一个固定插销9卡紧,同时齿轮3与齿圈4的锥面接触,刀架在新的位置定位并夹紧。
这时,端齿离合器与空套齿轮5脱开。
(4)转位液压缸复位刀架压紧之后,压力油从d孔进入转位液压缸的右腔,活塞6带动齿条复位,由于此时端齿离合器已脱开,齿条带动齿轮3在轴上空转。
数控机床自动换刀系统的使用方法

数控机床自动换刀系统的使用方法数控机床自动换刀系统是一种现代化的工艺装备,它能够自动完成刀具的安装和拆卸,极大地提高了机床的工作效率和自动化水平。
在这篇文章中,我们将详细介绍数控机床自动换刀系统的使用方法,以帮助读者更好地了解和应用这一技术。
首先,数控机床自动换刀系统的基本原理是通过刀库来存放各种不同类型的刀具,并且能够根据加工程序的要求自动选择并安装适当的刀具。
在使用之前,我们需要先对刀具进行合理的编码和分类,并将其放置在刀库中。
接下来,我们需要进行合适的设置和调整。
首先,通过数控系统进入自动换刀的菜单界面,选择相应的刀库和刀具编号。
然后,根据加工零件的要求,选择适当的刀具参数和加工工艺参数,如切削速度、进给速度等。
最后,将设定好的加工程序加载到数控系统中。
在机床开始加工前,我们需要执行一次预热功能,以确保刀库、刀具和机床处于最佳状态。
同时,还需要检查刀具的完好程度,如刀片的磨损情况、刀具的固定性等。
如果存在问题,及时更换和调整刀具,以保证加工质量和安全。
在实际操作中,数控机床自动换刀系统的使用方法还需注意以下几点。
首先,严禁在机床运行状态下打开刀库门,以防止刀库和刀具的损坏。
其次,操作人员必须经过专业的培训和熟悉使用手册,掌握换刀系统的操作要领和注意事项。
再次,要定期对刀具和机床进行保养和维护,以延长其使用寿命。
此外,数控机床自动换刀系统的使用方法还需要根据具体的机床类型和加工要求进行灵活调整。
例如,在加工不同材料的零件时,需要选择适宜的刀具材质和切削参数;在进行复杂轮廓和曲线加工时,需要使用特殊形状的刀具,并调整切削路径和刀具补偿等。
总结起来,数控机床自动换刀系统的使用方法是一个复杂而重要的技术,它能够提高机床的生产效率和一致性。
通过合理设置和调整刀具参数,以及进行正确的操作和维护,可以确保刀具的安全性和加工质量。
然而,在使用过程中还需要注意刀具的选择和切削参数的调整,以适应不同的加工需求。
简述自动换刀系统的基本要求
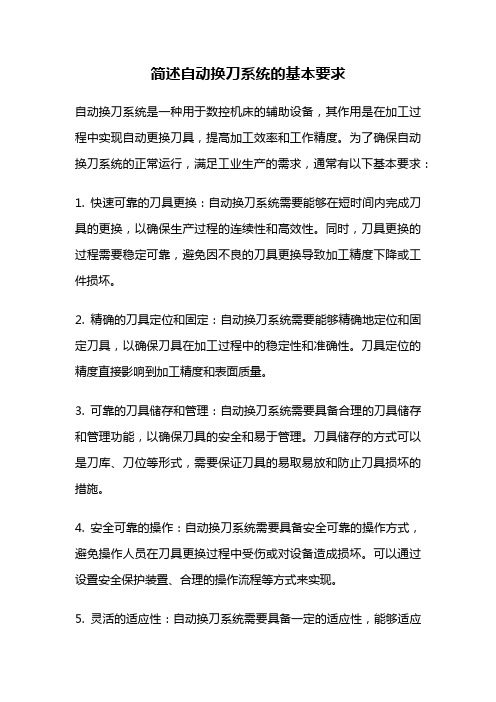
简述自动换刀系统的基本要求自动换刀系统是一种用于数控机床的辅助设备,其作用是在加工过程中实现自动更换刀具,提高加工效率和工作精度。
为了确保自动换刀系统的正常运行,满足工业生产的需求,通常有以下基本要求:1. 快速可靠的刀具更换:自动换刀系统需要能够在短时间内完成刀具的更换,以确保生产过程的连续性和高效性。
同时,刀具更换的过程需要稳定可靠,避免因不良的刀具更换导致加工精度下降或工件损坏。
2. 精确的刀具定位和固定:自动换刀系统需要能够精确地定位和固定刀具,以确保刀具在加工过程中的稳定性和准确性。
刀具定位的精度直接影响到加工精度和表面质量。
3. 可靠的刀具储存和管理:自动换刀系统需要具备合理的刀具储存和管理功能,以确保刀具的安全和易于管理。
刀具储存的方式可以是刀库、刀位等形式,需要保证刀具的易取易放和防止刀具损坏的措施。
4. 安全可靠的操作:自动换刀系统需要具备安全可靠的操作方式,避免操作人员在刀具更换过程中受伤或对设备造成损坏。
可以通过设置安全保护装置、合理的操作流程等方式来实现。
5. 灵活的适应性:自动换刀系统需要具备一定的适应性,能够适应不同类型和规格的刀具,并能够满足不同加工工艺和产品的需求。
可以通过采用标准化的刀具接口和灵活的刀具夹持方式来实现。
6. 可靠的故障检测和报警功能:自动换刀系统需要具备可靠的故障检测和报警功能,及时发现和排除可能出现的故障,以保证设备的正常运行和生产的连续性。
7. 易于维护和保养:自动换刀系统需要具备易于维护和保养的特点,便于设备的日常维护和保养工作。
可以通过合理的设计和使用优质的材料来降低设备的维修频率和成本。
8. 合理的成本和效益:自动换刀系统需要具备合理的成本和效益,能够在提高生产效率和产品质量的同时,降低生产成本和人力投入。
自动换刀系统的基本要求包括刀具更换的快速可靠性、刀具定位和固定的精确性、刀具储存和管理的可靠性、操作的安全可靠性、适应不同需求的灵活性、故障检测和报警功能的可靠性、易于维护和保养的特点,以及合理的成本和效益。
加工中心自动换刀系统设计说明书
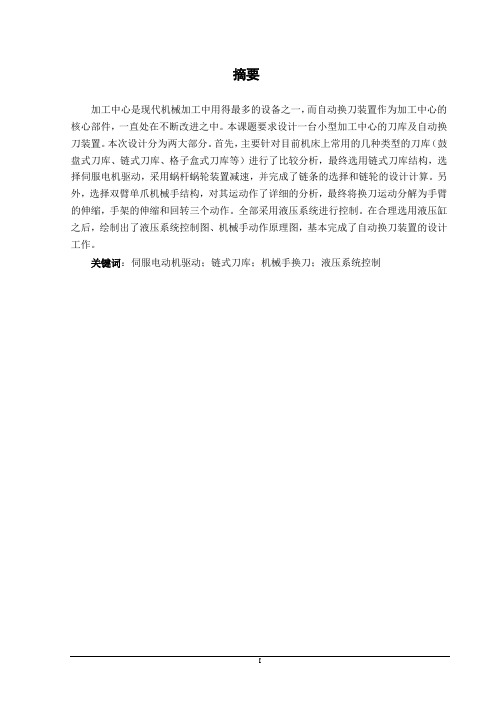
摘要加工中心是现代机械加工中用得最多的设备之一,而自动换刀装置作为加工中心的核心部件,一直处在不断改进之中。
本课题要求设计一台小型加工中心的刀库及自动换刀装置。
本次设计分为两大部分。
首先,主要针对目前机床上常用的几种类型的刀库(鼓盘式刀库、链式刀库、格子盒式刀库等)进行了比较分析,最终选用链式刀库结构,选择伺服电机驱动,采用蜗杆蜗轮装置减速,并完成了链条的选择和链轮的设计计算。
另外,选择双臂单爪机械手结构,对其运动作了详细的分析,最终将换刀运动分解为手臂的伸缩,手架的伸缩和回转三个动作。
全部采用液压系统进行控制。
在合理选用液压缸之后,绘制出了液压系统控制图、机械手动作原理图,基本完成了自动换刀装置的设计工作。
关键词:伺服电动机驱动;链式刀库;机械手换刀;液压系统控制AbstractProcessing Center is a modern mechanical processing equipment used in one of the largest and automatic tool change device as the core parts processing center, has been in the continuous improvement of. The topics designed a small knife processing center for devices and automatic tool change. The design is divided into two parts. First of all, the main view of the current machine, commonly used for several types of knives (knives drum disc library, the chain knife, knife lattice cassette library, etc.) a comparative analysis, the final choice of the chain knife structure, choice of servo motor Driver, a worm worm deceleration devices, and completed the chain and sprocket of the choice of design and calculation. In addition, the choice of single-claw manipulator arms structure, its movement made a detailed analysis will eventually ATC campaign for the decomposition of the telescopic arm, hand-stretching and rotating the three movements. All the hydraulic system used to control. A reasonable choice of hydraulic cylinders, to map out plans of the hydraulic control systems, mechanical hand movements schematics, basically completed the installation of automatic tool change the design work.Keywords:The servo motor actuates; Chain knife storehouse; The manipulator trades the knife; The hydraulic system controls目录目录摘要 (I)Abstract (Ⅲ)1 绪论1.1 本课题的来源、目的及意义 (1)1.1.1 课题的来源 (1)1.1.2 本课题研究的目的 (1)1.1.3 本课题研究的意义 (1)1.2 课题背景及国内外研究现状 (2)1.3 本课题研究的主要内容 (3)2 刀库及换刀机构总体结构设计2.1 刀库的结构设计 (3)2.1.1 方案分析比较 (3)2.1.2 刀库容量的确定 (6)2.1.3 刀库选刀方式的确定 (6)2.1.4 刀库的设计及计算 (6)2.2 自动换刀装置设计 (13)2.2.1 方案分析比较 (13)2.2.2 机械手自动换刀工作流程设计 (13)2.2.3 换刀机械手结构设计 (22)2.2.4 换刀手手臂和手爪结构设计 (23)2.2.5 液压缸、活塞杆的选择 (24)2.2.6 液压系统工作原理 (26)设计总结 (27)致谢 (29)参考文献 (30)1 绪论1.1课题的来源及研究目的和意义1.1.1课题的来源刀库和机械手是加工中心稳定可靠运行的关键功能部件。
基于PLC的刀库自动换刀控制系统设计

此 次 题 的 研 究 埘 象 足 皖 『萄 ● 式 JJ1] } 心 VMC1000L的 『】动 换 j装 簧 , 其 J库 J
!I盘 式 ,J J车 i{=fJ, nl】I I、 l 2 ÷, 、 住 180r am, 度 为 250turn,最 多 町 容 纳 6把 ,J jI。 } 垧II队I斜 丁L J、 }{J的 足 7:24 I 内钎 I耵, J 的 ft』℃址 MSA403 BT-40, 最 人 uJ.以 承 受 : 为 9KG 的 /JljI.最 人 『IJ容 纳 的 /Jj}J 寸为 ‘D1 50X450mm.换 时 I'tlJ 10—30S之 I't TJ
- 过 特 制 容 埸… 观 战 障 ,所 以必 须 一耍按 严 格 标 准 的 辑 ,行 ,Jjlll ̄)i) 求使 个机 构 的 } 动 刺1 ’i协调 IIlj‘ 数 控 ll I l11心 Il, f】动 换 j系
.
统 址 · 【成 fl}lj分之 ‘,所 以 I,J‘以 说 它 的 效 就 址 机 床 的 J J【】I.效 。 小 逻删:究 的 址 数 ;加 l: III心 f内恻 黜 J J年以及 机 械 r换 J, 系统 的 艘 什 、换 Jll,J的 行 eOjllldi) 及 软 什 编 ,j’ 进 行 J 1 嘤 n勺研 究 分 , J 刚 l. 今干II传 统 的 { 『 换 /J系 统 , 然 ^ 改 J 以 l,j-绷 制 系统
3 PLO控 制 系 统要 求
存 找 们 ,1 产 JJI1 l: 个 零 件 的 时 候 , 往 往 小能 次 加 l:完成 ,需 要 多 个上 序 米 充 成 加 上 。 『面 ‘舣 的 或 足 通 的 机 J术I}I部 足 {能 完 成 一 个 的 加 】., t-'.IJ使 足功 能 ‘的 数 控 机 床 也 足 如 此 征 JJi】1 过 中 最 人 茕的 时 足 化 征 J,换 川 而 今 {{:会 r1动 化 度 越 术越 高 超 , r动 的 换 J 经 人 人 的影 响 J 生 产 的 效 率 , 可 以 醣 fJ动 的 换 系统 的作 川 加【l:II 终 足 划 /f 缓 。 本 次 改 汁就 足针 划此 种 情 况 对 },1 J J 门控 制 系统 进 行 设 汁 ,j 体 要 求 如 :
数控机床的自动换刀装置

《数控机床编程与操作》
山东华宇职业技术学院实训中心
数控机床的自动换刀装置
单元三
刀具系统及刀具选择 一、刀具系统 二、刀具的选择方式 三、刀具识别装置
Exit
《数控机床编程与操作》
山东华宇职业技术学院实训中心
数控机床的自动换刀装置
单元三
刀具系统及刀具选择
刀柄 编码环 销紧螺母
二、刀具的选择方式 1、顺序选择刀具 2、任意选择刀具 a)刀具编码方式 b)刀座编码方式 c)编码附件方式
二、更换主轴换刀
三、更换主轴箱换刀 四、带刀库的自动换刀系统
Exit
《数控机床编程与操作》
山东华宇职业技术学院实训中心
数控机床的自动换刀装置
单元一
自动换刀装置的形式
内装信号盘 上齿盘 开 合 下齿盘 n 螺母 蜗轮副 (a) 刀架 弹簧安全离合器 (b) 转位 刀架 端齿盘定位 电动机 销钉 刀架 销钉
《数控机床编程与操作》
山东华宇职业技术学院实训中心
数控机床的自动换刀装置
单元四
刀具交换装置
1、无机械手换刀 2、机械手换刀
刀库 刀库 (a) 主轴 (b)
一、刀具交换方式
主轴
主轴
主轴 刀库 (c) 刀库
(d)
图6-17 双臂机械手常见的结构形式
Exit
《数控机床编程与操作》
山东华宇职业技术学院实训中心
拉杆
刀座编码块 刀座识别装置
图6-10
刀具编码的结构
图6-11
刀座编码的结构
弹性接触片 导向突起 代码突起 炭刷
钥匙代码凹凸处 弹性接触片
炭刷 代码突起 钥匙代码凹凸处
图6-12 编码钥匙
机械加工自动换刀的工作原理

机械加工自动换刀的工作原理机械加工中,自动换刀系统的使用可以大幅度提高生产效率和降低操作风险。
通过自动换刀系统,机床可以实现自动完成工件加工过程中所需要的刀具更换操作,而无需人工干预。
本文将介绍机械加工自动换刀的工作原理。
1. 自动换刀系统的组成机械加工自动换刀系统一般包括以下几个主要部分:- 刀库:用于存放各种类型的刀具;- 刀柄:刀柄与刀具连接,用于固定刀具的位置;- 自动换刀装置:通过控制系统,实现刀具的自动更换;- 控制系统:用于控制自动换刀装置的运行。
2. 工作原理机械加工自动换刀系统的工作原理可以分为以下几个步骤:步骤一:刀具选择根据加工要求,通过控制系统选择合适的刀具。
控制系统中存储了各类刀具的信息,可以根据加工要求进行刀具的选择。
步骤二:刀具传递控制系统将选定的刀具信息传递给自动换刀装置。
自动换刀装置根据接收到的指令,通过刀库和刀柄将相应的刀具传递到机床的刀具安装位置。
步骤三:刀柄固定刀柄将刀具固定在机床上的刀具位置。
刀柄通常通过夹紧等方式,确保刀具在加工过程中的稳定性。
步骤四:加工操作一旦刀具安装完成,机床可以进行加工操作。
自动换刀系统不会影响机床的正常工作,它只是在需要更换刀具时提供自动化的支持。
步骤五:刀具退回当刀具不再需要使用时,控制系统会发送退回信号。
自动换刀装置会将刀具退回到刀库中的相应位置,以备下次使用。
3. 自动换刀系统的优势自动换刀系统在机械加工中具有以下几个优势:- 提高生产效率:自动换刀系统可以在加工过程中快速、准确地更换刀具,节省了手动换刀的时间,提高了加工效率。
- 降低操作风险:自动换刀系统减少了人工干预的需求,降低了因操作错误而引起的风险,提高了操作安全性。
- 多样化加工:自动换刀系统可以容纳多种类型的刀具,机床可以根据加工要求自由切换不同的刀具,实现多样化的加工操作。
总结:机械加工自动换刀系统通过控制系统的指令,实现刀具的选择、传递、固定和退回。
它的工作原理简单明了,优势明显。
数控加工中的自动换刀系统原理与操作要点

数控加工中的自动换刀系统原理与操作要点随着科技的不断进步,数控加工技术在工业生产中的应用越来越广泛。
而自动换刀系统作为数控加工中的重要组成部分,对于提高加工效率和保证产品质量起着至关重要的作用。
本文将介绍数控加工中的自动换刀系统的原理与操作要点。
一、自动换刀系统的原理自动换刀系统是指通过机械装置和控制系统,实现数控机床上刀具的自动更换。
其原理主要包括以下几个方面:1. 传感器检测:自动换刀系统通常会配备传感器,用于检测当前刀具的状态。
传感器可以检测刀具的长度、直径、磨损程度等参数,以及刀具是否安装正确。
2. 控制系统:自动换刀系统的核心是控制系统,它通过接收传感器的反馈信息,并根据预设的程序进行判断和操作。
控制系统可以根据刀具的使用寿命、加工工艺等因素,自动切换到合适的刀具。
3. 刀库和换刀装置:数控机床上通常会配备一个刀库,用于存放各种规格的刀具。
自动换刀系统通过换刀装置,将需要更换的刀具从刀库中取出,并安装到机床上。
二、自动换刀系统的操作要点在使用自动换刀系统时,需要注意以下几个操作要点:1. 刀库管理:刀库是存放各种规格刀具的地方,因此需要进行刀具的分类和管理。
刀具应按照规格和用途进行分类,并进行编号或标记。
同时,刀具的使用寿命也需要进行记录和管理,及时更换磨损严重的刀具。
2. 刀具安装:在进行刀具更换时,需要确保刀具的正确安装。
刀具的长度、直径等参数应与加工工艺要求相符合。
同时,刀具的固定方式也需要正确,以确保刀具在加工过程中不会松动或脱落。
3. 检测与调试:在使用自动换刀系统前,需要进行系统的检测和调试。
检测主要包括传感器的工作状态和刀具的识别功能是否正常。
调试则包括刀具的安装和换刀过程的调整,以确保换刀的准确性和稳定性。
4. 故障处理:在使用自动换刀系统过程中,可能会遇到一些故障,如刀具卡住、刀具识别错误等。
此时,操作人员需要及时处理故障,并进行相应的维修和调整。
5. 定期维护:自动换刀系统需要定期进行维护,以确保其正常工作。
- 1、下载文档前请自行甄别文档内容的完整性,平台不提供额外的编辑、内容补充、找答案等附加服务。
- 2、"仅部分预览"的文档,不可在线预览部分如存在完整性等问题,可反馈申请退款(可完整预览的文档不适用该条件!)。
- 3、如文档侵犯您的权益,请联系客服反馈,我们会尽快为您处理(人工客服工作时间:9:00-18:30)。
2004。09。
自动换刀装置的调整
数控机床自动换刀装置的形式
▪ 多转塔头自动换刀装置 ▪ 具有刀库和机械手的自动换刀装置
▪ 刀库类型 1) 转塔式刀库 2) 圆盘式刀库 3) 链式刀库 4) 格子式刀库
▪ 机械手 1) 单臂单手式机械手 2) 回转式单臂双手机械手
▪ 排屑器 ▪ 经常清理铁屑 ▪ 检查有无卡住
▪ 清理废油池 ▪ 及时取油池中废油,以免 外溢
▪ 调整主轴驱动带松紧 ▪ 按机床说明书调整
2004。09。
数控机床的维护
数控机床使用中应注意的问题
▪ 使用环境: ▪ 避免阳光的直射和其他辐射 ▪ 避免太潮湿或粉尘过多的场所 ▪ 避免有腐蚀气体的场所 ▪ 要远离振动大的设备
2004。09。
第二章 数控机床的调整
主轴部件的结构与调整
▪ CK7815型数控车床主轴部件的结构与调整 ▪ NT-J320A型数控铣床主轴部件的结构与调整 ▪ THK6380加工中心主轴部件的结构与调整
进给传动系统部件的调整 回转运动部件的调整 自动换刀装置的调整 位置检测装置的调整 床身导轨的调整
数控机床维修
第一章 数控机床的安装、调试及验收
数控机床的选用 数控机床的安装 数控机床的调试 数控机床的验收
2004。09。
数控机床的验收
开箱检验和外观检查 机床性能及数控功能的检验 机床精度的验收
2004。09。
机床性能的检验
主轴系统性能 进给系统性能 自动换刀系统 机床噪声 电气装置 数控装置 安全装置 润滑装置 气、液装置 附属装置
2004。09。
进给传动系统部件的调整
数控机床进给传动系统布置形式
▪ 水平布置和垂直布置
水平布置时和普通机床布置形式相同,大多采用滚珠丝杠取代滑动丝 杠。布置形式有:
1) 一端装推力轴承 2) 两端装推力轴承 3) 一端装推力轴承、另一端装深沟球轴承 4) 两端装推力轴承及深沟球轴承
▪ 数控机床与普通机床进给传动系统结构布置的不同之处:
2004。09。
机床切削精度的检验
机床的切削精度是一项综合精度
▪ 切削精度检验可分为: 1) 单项加工精度检验 2) 加工一个标准的综合性试件精度检验
▪ 卧式加工中心切削精度检验内容: 1) 镗孔精度-圆度、圆柱度 2) 端铣刀铣平面精度-平面度、阶梯差 3) 端端铣刀铣侧面精度-垂直度、平行度 4) 镗孔孔距精度——X轴方向、 Y轴方向、对角线方向、孔 径偏差 5) 立铣刀铣四周面精度——直线度、平行度、厚度差、垂直 度 6)两轴联动铣削直线精度——直线度、平行度、垂直度 7)立铣刀铣削圆弧精度——圆度
2004。09。
位置检测装置的调整
位置检测装置的作用
▪ 闭环伺服系统中的位置反馈 ▪ 开环或闭环伺服系统的误差补偿 ▪ 测量机、机床工作台等的坐标测量及数字显示 ▪ 齿轮、螺纹加工机床的同步电子传动 ▪ 直线-回转运动相互变换用的精密伺服系统
数控机床对位置检测装置的基本要求:
▪ 工作可靠 ▪ 能满足机床精度和速度的要求 ▪ 抗干扰能力强 ▪ 使用方便 ▪ 成本低
2004。09。
位置检测装置的分类
回转型:测角度、角位移
▪ 增量式 ▪ 脉冲编码器 ▪ 旋转变压器 ▪ 圆感应同步器 ▪ 圆光栅 ▪ 圆磁栅
▪ 绝对式 ▪ 多速旋转变压器 ▪ 绝对值脉冲编码器 ▪ 三速圆感应同步器
直线型:测长度、直线位移
▪ 增量式 ▪ 直线圆感应同步器 ▪ 计量光栅、磁尺
▪ 主轴润滑恒温油箱
每年
▪ 检查并更换直流伺服电机碳刷 ▪ 检查换向器表面,吹净碳 粉,去毛刺
▪ 更换长度过短的电刷,跑 合后使用
▪ 润滑液压泵、滤油器清洗 ▪ 清理池底,更换滤油器
不定期
▪ 检查各轴轨道上镶条、压紧滚 轮松紧状态 ▪ 按机床说明书调整
▪ 冷却水箱 ▪ 检查液面高度 ▪ 太脏、更换 ▪ 清理水箱底部 ▪ 经常清洗过滤器
分析 ▪ 分类:
▪ 日常点检:对机床一般部件的点检,处理和检查机床在运行过程中出现的 故障,由机床操作人员进行
▪ 专职点检:对机床关键部位和重要部件按周期进行重点点检和设备状态 监测与故障诊断,制定点检计划,做好诊断记录,分析维修结果,提出改善 设备维护管理的建议,由专职维修人员进行
2004。09。
1) 数控机床进给传动链首端件是伺服电动机 2) 传动机构大多采用滚珠丝杠取代滑动丝杠 3) 垂直布置的进给传动系统结构中,设置有制动装置 4) 齿轮副采用了消除齿轮啮合间隙结构
2004。09。
进给传动系统伺服电动机的形式及安装
伺服电动机的主要类型及结构
▪ 直流伺服电动机 1) 小惯量直流电动机 a) 转动惯量小 b) 机电时间常数小 c) 低速平稳,无爬行现象,换向性能好 2) 宽调速直流伺服电动机 又叫大惯量直流电动机,调速范围宽,可直接驱动滚珠丝杠, 减少了传动损失及传动误差,提高了传动精度 a) 低速性能好,转矩大,可和机床丝杠直接连接 b) 转子惯量大 c) 过载性能好 d) 用永久磁铁作为磁极,提高了电机效率,在重切削过载情况 下,加减速特性好 3) 缺点:尺寸较大,容量和使用环境受限,电刷和整流子要经常维修
▪ 斜齿圆柱齿轮传动间隙的消除 ▪ 垫片调整法 ▪ 轴向压簧调整法
▪ 锥齿轮传动间隙的消除 ▪ 轴向压簧调整法 ▪ 周向弹簧调整法
▪ 齿轮齿条传动间隙的消除 ▪ 双薄片齿轮错齿调整法 ▪ 预紧装置----P43图2-18
2004。09。
滚珠丝杠螺母副的结构及间隙调整
滚珠丝杠螺母副的特点:
▪ 传动效率高 ▪ 传动灵敏,不易产生爬行 ▪ 随动精度和定位精度高 ▪ 同步性好 ▪ 传动具有可逆性 ▪ 磨损小,使用寿命长 ▪ 施加预紧后,可消除轴向间隙,反向时无空程,轴向运动精度和刚
的维修档案 ▪ 建立维修协作网,开展专家诊断系统工作 数控机床维修管理应强调的内容: ▪ 选择合理的维修方式
▪ 维修方式有:事后维修、预防维修、改善维修、预知维修或状态监测 维修、维修预防
▪ 从修理费用、停产损失、维修组织工作和修理效果等方面去衡量 ▪ 建立专业维修组织和维修协作网 点检管理:按有关文件的规定,对设备进行定点、定时的检查和维护 ▪ 点检的内容:定点、定标、定期、定项、定人、定法、检查、记录、处理、
▪ 滚动导轨
▪ 优点:
1) 导轨面之间为滚动摩擦,摩擦因数小,是滑动导轨的1/10,工作所需牵引力小,移动轻 便
2) 运动平稳,灵敏度高,定位精度高,无承载油膜,重复定位精度达0.2um
3) 磨损小,使用寿命长
▪ 缺点:抗振性差,防护要求高,结构复杂,制造成本高,主要用于高精度数控机床和坐标镗床 等
某加工中心的维护点检表
每天
▪ 导轨润滑油箱 ▪ 油标 ▪ 油量 ▪ 及时添加润滑油 ▪ 润滑泵能定时启动及停止
▪ XYZ轴导轨面 ▪ 清除切屑及脏物 ▪ 检查润滑油是否充分 ▪ 导轨面有划伤损坏
▪ 压缩空气气源压力 ▪ 检查压力是否在正常范围
▪ 气源自动分水滤水器和自动空气干 燥器
▪ 及进清理分水器中滤出的水分, 自动保持空气干燥器正常工作
2004。09。
机床几何精度检验
常用检测工具:
精密水平仪 精密方箱 直角尺 平行尺 平行光管 精度检测必须在机床精调之后一次完成,不允许调整一项检测一项, 因为几何精度有些项目是相互联系相互影响的。
2004。09。
机床定位精度检验
▪ 结构形式:
1) 滚针导轨
2) 滚珠导轨
3) 滚柱导轨
▪ 静压导轨:将压力油经节流器输送到导轨面上的油腔中,形成承载油膜,将互相接触的导轨面隔开, 实现液体摩擦
▪ 优点:
1) 摩擦因数小,机械效率高,能长期保持导轨导向精度
2) 承载油膜吸振性好,低速下不易产生爬行
▪ 缺点:结构复杂,需配置一套专门的供油系统
度高
滚珠丝杠螺母副的结构形式
▪ 外循环 ▪ 内循环
滚珠丝杠螺母副的轴向间隙的调整方法
▪ 垫片调整法 ▪ 螺母调整法 ▪ 齿差式调整法
滚珠丝杠螺母副的预紧
▪ 预紧力计算公式:FV=1/3Fmax
2004。09。
回转运动部件的调整
回转运动部件:
▪ 分度工作台:按最小分度角的整数倍分度 ▪ 回转工作台:回转进给运动,实现任意角度分度及控制
▪ 分类:开式和闭式两大类
2004。09。
数控机床的维修管理及维护
数控机床维修管理及维护中与普通机床相同的内容:
▪ 必须坚持设备使用上的定人、定机、定岗制度 ▪ 开展岗位培训,严禁无证操作 ▪ 严格执行设备点检和定期、定级保养制度 ▪ 对维修者实行派工卡,认真做好故障现象、原因、维修的记录,建立完整
2004。09。
机床精度验收
几何精度 定位精度 切削精度
2004。09。
机床几何精度检验
以普通立式加工中心为例:
工作台面的平面度 各坐标方向移动的相互垂直度; X、Y坐标方向移动时工作台面的平行度; X坐标方向移动时工作台面T形槽侧面的平行度; 主轴的轴向窜动; 主轴孔的径向跳动; 主轴箱沿Z坐标方向移动时主轴轴心线的平行度; 主轴回转轴心线对工作台面的垂直度; 主轴箱沿Z坐标方向移动的直线度。
定义:是指机床各坐标轴在数控装置控制下运动所能达到的位 置精度。
定位精度决定于数控系统和机械传动误差。 定位精度的主要检测内容:
▪ 各直线运动轴的定位精度和重复定位精度; ▪ 各直线运动轴机械原点的复归精度; ▪ 各直线运动轴的反向误差; ▪ 各回转运动轴(回转工作台)的定位精度和重复定位精度; ▪ 各回转运动轴原点的复归精度; ▪ 各回转运动轴的反向误差;