冲压、脱脂废气方案
废气治理工程方案设计范本
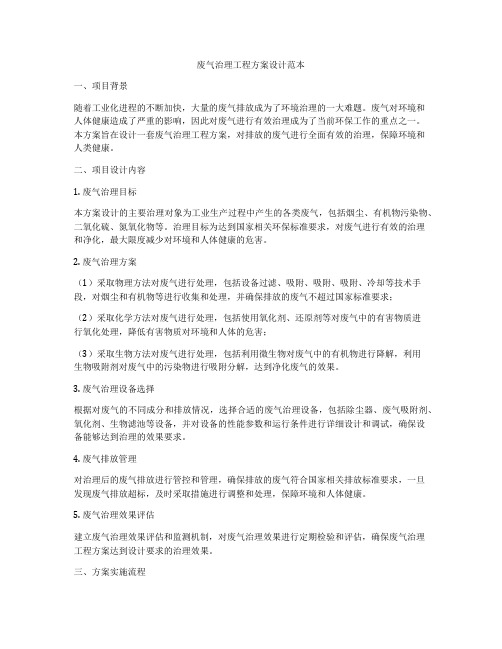
废气治理工程方案设计范本一、项目背景随着工业化进程的不断加快,大量的废气排放成为了环境治理的一大难题。
废气对环境和人体健康造成了严重的影响,因此对废气进行有效治理成为了当前环保工作的重点之一。
本方案旨在设计一套废气治理工程方案,对排放的废气进行全面有效的治理,保障环境和人类健康。
二、项目设计内容1. 废气治理目标本方案设计的主要治理对象为工业生产过程中产生的各类废气,包括烟尘、有机物污染物、二氧化硫、氮氧化物等。
治理目标为达到国家相关环保标准要求,对废气进行有效的治理和净化,最大限度减少对环境和人体健康的危害。
2. 废气治理方案(1)采取物理方法对废气进行处理,包括设备过滤、吸附、吸附、吸附、冷却等技术手段,对烟尘和有机物等进行收集和处理,并确保排放的废气不超过国家标准要求;(2)采取化学方法对废气进行处理,包括使用氧化剂、还原剂等对废气中的有害物质进行氧化处理,降低有害物质对环境和人体的危害;(3)采取生物方法对废气进行处理,包括利用微生物对废气中的有机物进行降解,利用生物吸附剂对废气中的污染物进行吸附分解,达到净化废气的效果。
3. 废气治理设备选择根据对废气的不同成分和排放情况,选择合适的废气治理设备,包括除尘器、废气吸附剂、氧化剂、生物滤池等设备,并对设备的性能参数和运行条件进行详细设计和调试,确保设备能够达到治理的效果要求。
4. 废气排放管理对治理后的废气排放进行管控和管理,确保排放的废气符合国家相关排放标准要求,一旦发现废气排放超标,及时采取措施进行调整和处理,保障环境和人体健康。
5. 废气治理效果评估建立废气治理效果评估和监测机制,对废气治理效果进行定期检验和评估,确保废气治理工程方案达到设计要求的治理效果。
三、方案实施流程1. 确定治理对象和治理目标首先对废气排放情况进行调查和分析,确定治理对象和治理目标,对废气排放进行详细分析和监测。
2. 废气治理方案设计设计废气治理方案,包括废气治理技术路线、治理设备选择、综合治理效果评估等,确保废气得到有效治理。
青岛工厂废气治理方案
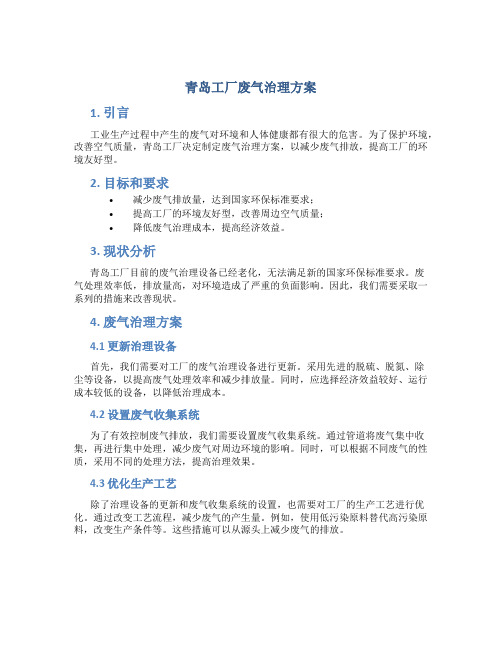
青岛工厂废气治理方案1. 引言工业生产过程中产生的废气对环境和人体健康都有很大的危害。
为了保护环境,改善空气质量,青岛工厂决定制定废气治理方案,以减少废气排放,提高工厂的环境友好型。
2. 目标和要求•减少废气排放量,达到国家环保标准要求;•提高工厂的环境友好型,改善周边空气质量;•降低废气治理成本,提高经济效益。
3. 现状分析青岛工厂目前的废气治理设备已经老化,无法满足新的国家环保标准要求。
废气处理效率低,排放量高,对环境造成了严重的负面影响。
因此,我们需要采取一系列的措施来改善现状。
4. 废气治理方案4.1 更新治理设备首先,我们需要对工厂的废气治理设备进行更新。
采用先进的脱硫、脱氮、除尘等设备,以提高废气处理效率和减少排放量。
同时,应选择经济效益较好、运行成本较低的设备,以降低治理成本。
4.2 设置废气收集系统为了有效控制废气排放,我们需要设置废气收集系统。
通过管道将废气集中收集,再进行集中处理,减少废气对周边环境的影响。
同时,可以根据不同废气的性质,采用不同的处理方法,提高治理效果。
4.3 优化生产工艺除了治理设备的更新和废气收集系统的设置,也需要对工厂的生产工艺进行优化。
通过改变工艺流程,减少废气的产生量。
例如,使用低污染原料替代高污染原料,改变生产条件等。
这些措施可以从源头上减少废气的排放。
4.4 建立废气监测系统为了确保废气治理效果的有效实施,应建立废气监测系统。
监测系统可以实时监测废气的排放情况,并记录数据,以便后续分析和评估。
监测系统的建立还可以提高治理的透明度,方便监管部门进行监督。
4.5 培训和宣传最后,青岛工厂应加强废气治理相关知识的培训和宣传。
通过培训,提高员工对废气治理的认识和意识,使其积极参与废气治理工作。
同时,通过宣传,向社会公众普及废气治理的重要性,形成全社会共同关注环境保护的氛围。
5. 实施计划为了顺利实施废气治理方案,我们制定了以下实施计划:1.进行废气治理设备更新,选购适合的设备;2.设置废气收集系统,建立管道网络;3.对生产工艺进行优化,减少废气排放;4.建立废气监测系统,对治理效果进行评估;5.开展废气治理知识培训和宣传活动。
氧气管道脱脂方案及过程控制表格
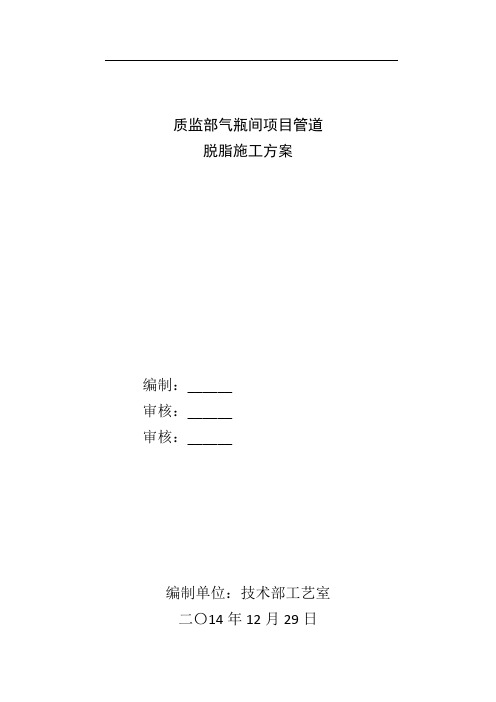
质监部气瓶间项目管道脱脂施工方案编制:______审核:______审核:______编制单位:技术部工艺室二〇14年12月29日一、编制说明氧气等管线按工艺要求在管道安装之前必须进行管道脱脂。
为了保证管线的脱脂质量,特编制本方案,鉴于安装时间及各方面条件的限制,故本项目在施工完毕后统一对管线进行脱脂处理:二、编制依据1、《脱脂工程施工及验收规范》(HG20202-2000)2、《工业金属管道工程施工及验收规范》GB50235-20103、《污水综合排放标准》,GB8978-2002三、脱脂安全规定1、脱脂应在晴天室外进行,应露天作业,应在通风良好的环境中进行。
2、脱脂现场应清除一切易燃易爆物及其他杂物,划分脱脂专责区域,无关人员不得进入。
严禁烟火,并设置“严禁烟火!”、“有毒物品!”标示牌。
3、参加脱脂的工作人员应有必要的保护措施和防护用品。
4、脱脂剂存放应分别贮存于于通风良好、干燥、凉爽的仓库中。
5、严禁不同的溶剂混合使用,或不按适用范围使用。
6、脱脂剂必须具有产品质量证明书。
7、脱脂应根据工作介质、管材、管径、脏污程度制定脱脂措施。
8、脱脂时,脱脂物件上不得含有水分。
9、脱脂后的脱脂件采用氮气或干燥的空气吹干。
10、脱脂件经脱脂后,由专职检查人员检查合格,方可进行下道工序。
11、脱脂合格的管子应及时封闭管口,保证以后的工序施工中不再被污染。
12、管道脱脂时应认真填写《管道系统脱脂记录》。
13、应防止脱脂剂溅出和溢到地面上。
溢出的溶剂应立即用木屑、砂子等吸干并和脱脂用过的织物一起收集在专用的密闭金属容器内。
14、脱脂残液及污染物的排放,应按国家相关标准的规定执行。
15、脱脂完毕剩余的溶剂应退回仓库并妥善保管。
四、脱脂溶剂本工程氧气管道脱脂采用溶剂为HG20202中附录A碱性脱脂液配方及使用条件中第一种复配剂,具体要求以标准中规定为准。
五、管道脱脂方法本系统管道脱脂采用循环冲洗法作业,具体方法为:从气瓶间气体管线接头处往室内进行冲洗,每次两条管线;首尾相接组成一个闭式循环冲洗系统,循环时间不低于30min;六、合格检验标准1、用清洁干燥的白色滤纸在被测表面用力往返擦拭一次,目测纸上无油脂痕迹为合格。
冲压过程中的节能环保技术

单击此处输入你的正文,请阐述观点
冲压工艺能耗:与冲压工艺参数、模具结构、材料等因素有关
单击此处输入你的正文,请阐述观点
设备维护与保养能耗:定期维护和保养设备,确保设备正常运行,减少故障停机时间
单击此处输入你的正文,请阐述观点
生产管理能耗:通过优化生产计划、提高生产效率等方式降低能耗 冲压过程中的环保问题
节能环保技术对冲压行业的影响
节能环保技术在冲压行业的应用
PART FOUR
减少冲压次数:通过合理的模具设计和优化工艺流程,减少冲压次数,降低能耗和减少废料
高效冲压设备:采用高效、低能耗的冲压设备,提高生产效率,减少能源消耗
冲压自动化:通过自动化技术,减少人工操作,提高生产效率,同时减少因人为因素导致的能源浪费
实施效果及经济效益分析
经验总结及未来发展规划
实施效果及经济效益分析
未来发展规划及前景展望
公司背景及概况
冲压生产线及设备介绍
节能环保技术应用方案
高效节能技术:采用先进的节能设备和技术,提高冲压生产效率,降低能源消耗。
环保材料应用:使用环保材料替代传统材料,减少对环境的污染。
智能化生产:通过引入人工智能、大数据等先进技术,实现冲压生产的智能化和自动化,提高生产效率和产品质量。
家电行业:冰箱、洗衣机、空调等的外壳和零部件
电子行业:手机、电脑等的外壳和零部件
航空航天:飞机、火箭等的外壳和零部件
其他行业:建筑、家具、玩具等的外壳和零部件
添加标题
添加标题
添加标题
添加标题
自动化:实现自动化生产,减少人工干预
高效化:提高生产效率,降低成本
智能化:利用人工智能技术,实现智能化生产
氧气管道脱脂试压吹扫检修规定

氧气管道脱脂试压吹扫检修规定1、前言为了确保氧气管道在运行过程中的安全性,避免发生意外事故,保障人身和财产安全,制定了本规定。
2、管道脱脂氧气管道在运输过程中,管道内壁可能会附着一些油脂物质,因此必须对管道进行脱脂处理。
如不进行脱脂处理,氧气管道的使用可能会对人员造成危险。
具体操作如下:(1)先关闭氧气管道总阀门和支管阀门,接通气源设备和埋地管道连通管线。
(2)用电动或手动管道清洗泵将清水从管道的支管阀门中注入管道内,开启管道排放阀,将水从管道排放阀中排出。
(3)止水后,使用油剂泵将管道内壁喷涂上适量的油剂。
(4)放置3至4小时,使管道内壁的油脂物质充分润湿。
(5)开启管道排放阀,将油剂从管道内用清水冲洗干净,直到有清水流出为止。
(6)关闭冲洗阀,将管道内的水排出。
在排水的过程中,需要开启管道连通管线。
(7)确认管道内壁干燥后,进行下一步操作。
3、管道试压为了避免氧气管道在操作过程中出现泄漏,必须对管道进行试压,确保其在运行过程中的安全性。
具体操作如下:(1)确定试压设备,包括试压泵、计量设备和管道连接阀门。
(2)将在试压前所需检测的所有管道、疏水器、阀门关闭,注意检查各接口是否连接牢固。
(3)开启试压泵和氧气管道的试压阀门,将管道的压力逐渐提高到设计压力,并保持1-2小时。
(4)对管道进行泄露检查,检查管道是否有明显的裂缝、漏气等状况。
(5)关闭试压泵和试压阀门,排放管道内的氧气,确认管道没有氧气残留后,进行下一步操作。
4、管道吹扫管道吹扫是为了清除管道内的尘土和杂物,保障管道运行的畅通性。
具体操作如下:(1)将吹扫气源设备接通到管道的支管阀门上。
(2)打开管道的排放阀门,调整吹扫气源设备的气源压力,将气流从管道的支管阀门进入管道中。
(3)将气流逐渐放大,清除管道内的尘土和杂物,将排泄物从管道的排放阀门排出。
(4)对管道进行检查,确认管道无尘土和杂物残留。
(5)关闭气源设备和排放阀门,确认管道无氧气残留后,进行下一步操作。
处理废气的设计方案
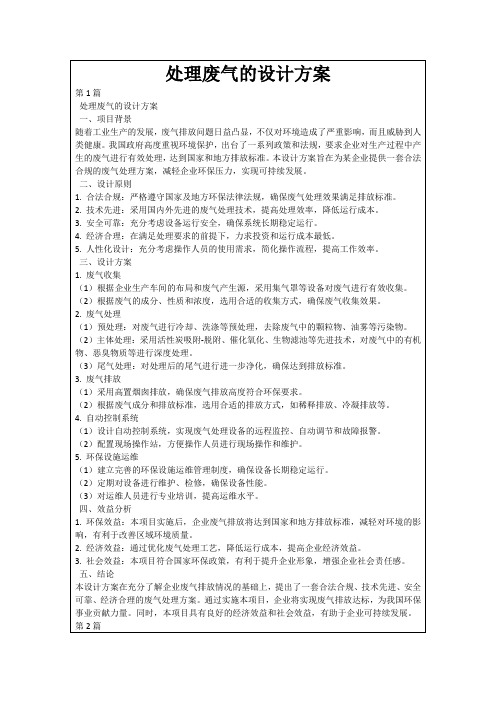
-提升企业的环保形象,增强企业社会责任感。
-推动行业绿色发展,助力生态文明建设。
六、结论
本设计方案从废气收集、预处理、处理工艺、尾气排放、自动控制及运维管理等环节进行了详细规划。在确保合法合规的基础上,力求实现高效、经济、安全的废气处理目标。通过实施本项目,企业将有效降低废气排放对环境的影响,为我国环保事业作出贡献。同时,本项目具有良好的经济效益和社会效益,有助于企业可持续发展。
二、设计原则
1.合法合规:严格遵守国家及地方环保法律法规,确保废气处理效果满足排放标准。
2.技术先进:采用国内外先进的废气处理技术,提高处理效率,降低运行成本。
3.安全可靠:充分考虑设备运行安全,确保系统长期稳定运行。
4.经济合理:在满足处理要求的前提下,力求投资和运行成本最低。
5.人性化设计:充分考虑操作人员的使用需求,简化操作流程,提高工作效率。
3.社会效益:本项目符合国家环保政策,有利于提升企业形象,增强企业社会责任感。
五、结论
本设计方案在充分了解企业废气排放情况的基础上,提出了一套合法合规、技术先进、安全可靠、经济合理的废气处理方案。通过实施本项目,企业将实现废气排放达标,为我国环保事业贡献力量。同时,本项目具有良好的经济效益和社会效益,有助于企业可持续发展。
处理废气的设计方案
第1篇
处理废气的设计方案
一、项目背景
随着工业生产的发展,废气排放问题日益凸显,不仅对环境造成了严重影响,而且威胁到人类健康。我国政府高度重视环境保护,出台了一系列政策和法规,要求企业对生产过程中产生的废气进行有效处理,达到国家和地方排放标准。本设计方案旨在为某企业提供一套合法合规的废气处理方案,减轻企业环保压力,实现可持续发展。
氧气管道脱脂施工方案
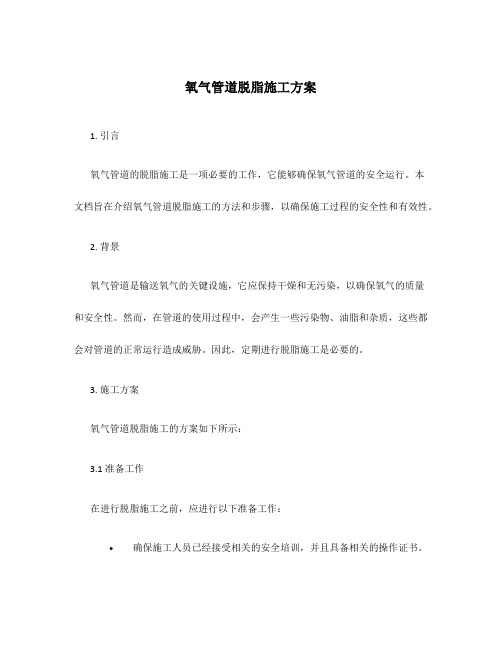
氧气管道脱脂施工方案1. 引言氧气管道的脱脂施工是一项必要的工作,它能够确保氧气管道的安全运行。
本文档旨在介绍氧气管道脱脂施工的方法和步骤,以确保施工过程的安全性和有效性。
2. 背景氧气管道是输送氧气的关键设施,它应保持干燥和无污染,以确保氧气的质量和安全性。
然而,在管道的使用过程中,会产生一些污染物、油脂和杂质,这些都会对管道的正常运行造成威胁。
因此,定期进行脱脂施工是必要的。
3. 施工方案氧气管道脱脂施工的方案如下所示:3.1 准备工作在进行脱脂施工之前,应进行以下准备工作:•确保施工人员已经接受相关的安全培训,并且具备相关的操作证书。
•确保所有的施工设备、工具和材料已经准备齐全,并且处于良好的工作状态。
•检查施工区域是否存在安全隐患,如裂缝、漏水等,并及时处理。
3.2 施工步骤氧气管道脱脂施工的步骤如下所示:3.2.1 清洁管道表面首先,使用合适的清洁剂和工具清洁管道表面,以去除表面的污染物和油脂。
在清洁过程中,应注意安全,避免使用易燃、易爆或有毒的清洁剂。
3.2.2 脱脂处理采用适当的脱脂剂对氧气管道进行脱脂处理。
脱脂剂的选择应符合相关的标准和规范,并且要求不会对管道本身产生损害。
脱脂剂的使用应按照厂家的使用说明进行,并且应注意安全使用,避免直接接触皮肤。
3.2.3 清洗管道内部使用适当的清洗设备,将清洗剂送入管道内部,进行内部清洗。
清洗的时间和流量应根据实际情况进行调整,确保清洗效果的达到要求。
3.2.4 检查施工质量在完成脱脂施工后,应进行质量检查。
检查的内容包括清洁度、管道连接和阀门的密封性等。
如发现问题,应及时进行修复,并再次进行检查确认。
3.3 安全注意事项在进行氧气管道脱脂施工时,应注意以下安全事项:•施工人员应穿戴安全防护设备,如手套、眼镜和防护服等。
•施工现场应设置明显的警示标志,以避免他人进入施工区域。
•严禁在氧气管道附近使用明火或其他火源。
•在脱脂剂的选择和使用中,应严格按照相关标准和规范进行,避免使用不合适的脱脂剂。
废气治理设计及施工方案

废气治理设计及施工方案一、废气治理的需求及目标随着工业发展和城市化进程的加快,废气污染成为了一个不可忽视的环境问题。
废气的排放不仅对大气造成了污染,还给人们的健康带来了威胁。
因此,废气治理成为了一项紧迫的任务。
废气治理的主要目标是减少废气排放量,降低废气污染物含量,改善环境质量,从而保护人们的身体健康。
二、废气治理设计的原则1.合理利用和消除废气源头2.选择合适的废气治理技术3.优化废气治理方案,提高治理效果4.保证废气治理设施的可持续运营5.符合当地相关法律法规及环保要求三、废气治理设施的选择及设计1.预处理设备:根据废气的不同特性选择适当的预处理设备,如除尘器、沉降器、过滤器等。
预处理设备的设计要考虑静态压力、流速、过滤面积等因素。
2.废气治理装置:根据废气的成分和排放浓度选择相应的治理装置,如湿式净化装置、干式净化装置、燃烧装置等。
治理装置的设计要考虑处理效率、可靠性、运行成本等因素。
3.辅助设备:根据废气治理装置的需要选择合适的辅助设备,如风机、泵阀、管道等。
辅助设备的设计要考虑耐腐蚀性、密封性、风量等因素。
4.安全设施:对于高温、高压、有毒废气,需要配置相应的安全设施,如防火防爆设备、监测报警设备等。
安全设施的设计要考虑安全性、可靠性、灵敏度等因素。
四、废气治理施工方案1.施工准备:包括工程方案编制、组织设计方案评审、材料采购、施工人员培训等。
2.设备安装:按照设计方案进行设备的安装、调试和试运行。
3.管道连接:根据设计方案进行管道的连接和密封工作。
4.电气安装:根据设计方案进行电气设备的安装、接线和调试。
5.防腐处理:对于易受腐蚀的设备和管道,进行防腐处理。
6.安全设施安装:根据设计方案进行安全设施的安装和调试。
7.施工验收:对已完成的废气治理设施进行验收,确保其满足设计要求和相关标准。
8.运维管理:对废气治理设施进行定期检查、维修和保养,确保其长期稳定运行。
五、废气治理效果的评估和改进1.监测评估:对废气治理设施的治理效果进行监测和评估,包括废气排放浓度、治理效率等指标。
双氧水管道脱脂处理施工方案
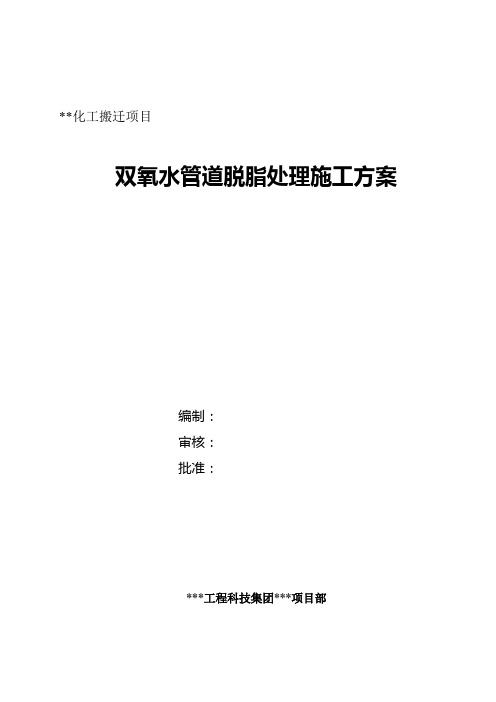
**化工搬迁项目双氧水管道脱脂处理施工方案编制:审核:批准:***工程科技集团***项目部一、工程概况:**化工项目***车间双氧水管道需做脱脂处理。
管道材质为304不锈钢,管径Φ57、Φ32、Φ18共三种。
二、编制依据:1、《脱脂工程施工及验收规范》HG20202—20002、《工业金属管道工程施工及验收规范》(GB50235-2010);三、施工方案:1、施工准备⑴、施工人员应认真学习本方案,掌握清洗、脱脂方法。
施工前,技术员须向作业施工人员进行安全、技术交底,所有被交底人员;⑵、准备好绸布, 塑料布、胶带、脱脂棉等消耗物品;⑶、准备好施工中应用的各种工、器具,安全防火、防毒器材。
⑷、施工前必须严格核查所要脱脂的管线、管件、阀门的规格、型号、材质,以防出错。
(5)、脱脂的管线及附件做好记录及记号,专人负责发放。
(6)、场地选择:脱脂工作应在通风良好的场地(所)进行;场地平整;用水、排水方便,不受雨水、尘土的侵染;脱脂剂应不受阳光直射。
本方案选址在甲氨基车间北侧12-15轴(此处为阴凉)。
⑺、检查脱脂剂的合格证书。
2、脱脂的一般规定⑴、管子、管件、阀门等的脱脂应在安装前完成。
⑵、有明显油迹和污垢的零部件,在脱脂前可先用煤油等清除油迹和污垢,然后再用脱脂液脱脂。
⑶、脱脂、检验及安装所用的工具、量具、仪表等必须按脱脂件的要求预先脱脂。
未经脱脂,不得使用。
工作服、鞋、手套等劳保用品必须干净无油。
保护用塑料布应无油。
⑷、管子、管件、阀门等在脱脂后,必须按要求进行报验,经相关人员检查认为合格签字后,用塑料布、胶带及时封堵敞口,防止污染及杂物进入。
此时方可进行下道工序。
⑸、经检查合格的脱脂件,由专人负责封闭,并加标志,妥善存放。
要把脱脂合格与不合格的或未脱脂件隔离存放,严禁相混。
3、脱脂方法⑴、脱脂方法选用Φ32、Φ18管灌注浸泡法;Φ57管拖试法。
脱脂剂为工业四氯化碳。
⑵、所购脱脂剂必须具有合格的质量证明文件,并按程序进行材料报验。
天润氧气管道脱脂方案(精)
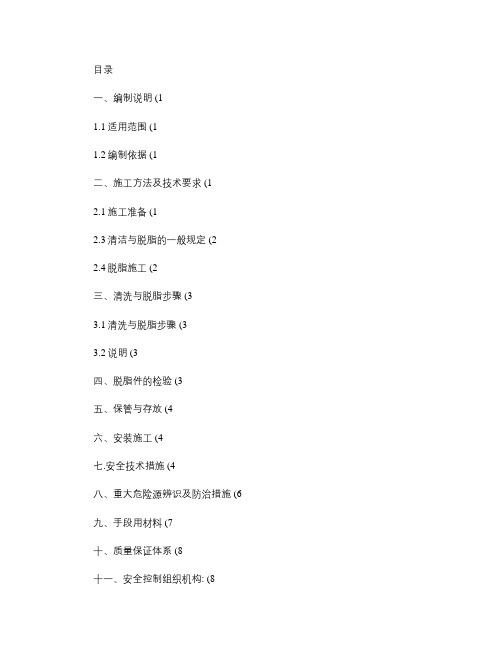
目录一、编制说明 (11.1适用范围 (11.2编制依据 (1二、施工方法及技术要求 (12.1施工准备 (12.3清洁与脱脂的一般规定 (22.4脱脂施工 (2三、清洗与脱脂步骤 (33.1清洗与脱脂步骤 (33.2说明 (3四、脱脂件的检验 (3五、保管与存放 (4六、安装施工 (4七.安全技术措施 (4八、重大危险源辨识及防治措施 (6九、手段用材料 (7十、质量保证体系 (8十一、安全控制组织机构: (8十二、项目组织机构 (9十三、(附件清洗脱脂检查记录表 (10一、编制说明1.1适用范围本方案适用于内蒙古XXX合成氨尿素工程气化(703装置及装置内管廊(709氧气管道的脱脂工作。
氧气管道的脱脂施工除执行本方案外,同时执行业已批准的《工艺管道安装施工方案》和《氧气管道施工方案》的一般规定。
1.2 编制依据1气化(703管道布置图05034-703-F2装置内管廊(709管道布置图05034-709-I3管道施工设计说明05034-708-F-24《脱脂工程施工及验收规范》(HG20202-2000;5《氧气站设计规范》(GB50030-91中第9.0.16“氧气管道设计对施工及验收的要求”。
6《工业“三废”排放执行标准》GBJ4-73二、施工方法及技术要求2.1施工准备(1 熟悉图纸和相关规范,掌握施工特点、技术要求。
施工人员应认真学习本方案,掌握清洗、脱脂方法;(2制作清洗槽1个进行清洗;(3准备好绸布, 塑料布等消耗物品;(4准备好紫光灯、试纸等检测用具;(5 施工前必须进行技术交底和安全交底。
(6 准备好施工中应用的各种工、器具,安全防火、防毒器材。
(7 施工前必须严格核查所要脱脂的管线、管件、阀门的规格、型号、材质,以防出错。
(8 脱脂的管线及附件做好记录及记号,专人负责发放。
(9 场地选择:脱脂工作应在通风良好的场地(所进行;场地平整;用水、排水方便,不受雨水、尘土的侵染;脱脂剂应不受阳光直射。
氧气管道脱脂施工方案
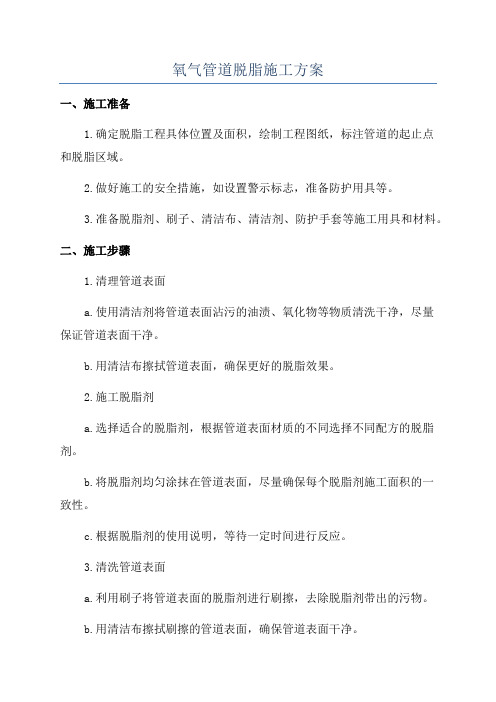
氧气管道脱脂施工方案一、施工准备1.确定脱脂工程具体位置及面积,绘制工程图纸,标注管道的起止点和脱脂区域。
2.做好施工的安全措施,如设置警示标志,准备防护用具等。
3.准备脱脂剂、刷子、清洁布、清洁剂、防护手套等施工用具和材料。
二、施工步骤1.清理管道表面a.使用清洁剂将管道表面沾污的油渍、氧化物等物质清洗干净,尽量保证管道表面干净。
b.用清洁布擦拭管道表面,确保更好的脱脂效果。
2.施工脱脂剂a.选择适合的脱脂剂,根据管道表面材质的不同选择不同配方的脱脂剂。
b.将脱脂剂均匀涂抹在管道表面,尽量确保每个脱脂剂施工面积的一致性。
c.根据脱脂剂的使用说明,等待一定时间进行反应。
3.清洗管道表面a.利用刷子将管道表面的脱脂剂进行刷擦,去除脱脂剂带出的污物。
b.用清洁布擦拭刷擦的管道表面,确保管道表面干净。
c.重复以上步骤,直到脱脂剂完全清除干净。
4.检查和修复a.检查管道表面是否有脱脂不彻底或遗留的污物,如有需要进行修复。
b.对有损坏的管道进行修复,如有漏水或裂缝等情况,需要进行相关的维修工作,并确保修复后的管道表面干净。
5.筛查和放气a.筛查管道是否有堵塞或残留物,确保管道畅通。
b.确认管道内不再有氧气残留,进行放气处理。
6.清洁和消毒a.使用清洁剂和消毒剂对管道进行清洁和消毒处理。
b.清洗管道内部,确保管道内部干净无污染。
7.安全检查和质量验收a.进行安全检查,确保管道脱脂施工过程中没有发生安全事故。
b.进行质量验收,对管道脱脂施工进行全面检查,确保工程的质量符合相关标准。
三、施工注意事项1.根据氧气管道的特殊性,施工时要特别注意安全,防止火源的引入,严禁吸烟,使用防爆手套、防毒面具等防护用具。
2.选择适宜的脱脂剂,根据管道表面材质的不同选择合适的脱脂剂。
3.施工期间要注意通风,避免脱脂剂的蒸发造成污染。
4.刷擦管道表面时要注意力度和频率,确保脱脂剂与管道表面充分接触。
5.尽量避免在高温、潮湿或雨天施工,避免脱脂效果不佳。
脱脂方案
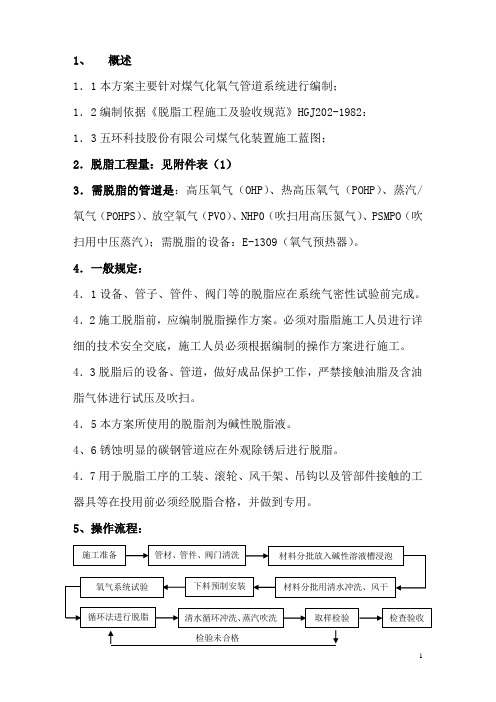
1、概述1.1本方案主要针对煤气化氧气管道系统进行编制;1.2编制依据《脱脂工程施工及验收规范》HGJ202-1982:1.3五环科技股份有限公司煤气化装置施工蓝图;2.脱脂工程量:见附件表(1)3.需脱脂的管道是:高压氧气(OHP)、热高压氧气(POHP)、蒸汽/氧气(POHPS)、放空氧气(PVO)、NHP0(吹扫用高压氮气)、PSMPO(吹扫用中压蒸汽);需脱脂的设备:E-1309(氧气预热器)。
4.一般规定:4.1设备、管子、管件、阀门等的脱脂应在系统气密性试验前完成。
4.2施工脱脂前,应编制脱脂操作方案。
必须对脂脂施工人员进行详细的技术安全交底,施工人员必须根据编制的操作方案进行施工。
4.3脱脂后的设备、管道,做好成品保护工作,严禁接触油脂及含油脂气体进行试压及吹扫。
4.5本方案所使用的脱脂剂为碱性脱脂液。
4、6锈蚀明显的碳钢管道应在外观除锈后进行脱脂。
4.7用于脱脂工序的工装、滚轮、风干架、吊钩以及管部件接触的工器具等在投用前必须经脱脂合格,并做到专用。
5、操作流程:6.管子、管件和阀门的脱脂6.1脱脂方法采用循环法和擦洗法,不锈钢和碳钢应分别单独脱脂。
6.2对已安装完成的管道采用循环脱脂法进行,循环时间为1小时,要确保碱性脱脂液在管道低点进入,并由高点排出,以确保管道内壁被脱脂液冲洗到。
对不能拆卸或循环脱脂有困难的管道,应在安装前进行脱脂。
6.3管材在未切割下料前对管材内表面进行脱脂,可将管材放入脱脂剂槽内进行浸泡,浸泡时间以4个小时为宜。
脱脂液温度以60-90度为宜,当温度达不到要求时,可用点燃后的木材加热脱脂剂槽,并设专人进行看护,以检测温度的变化和防止火灾事故的发生。
当施工现场有低压蒸汽时,可将低压蒸汽通与脱脂剂槽内,以起到加热作用,达到良好的脱脂效果。
6.4管子外表面的脱脂可用擦洗法擦洗脱脂。
6.5阀门脱脂前应经试验合格。
并清除阀门内的铁锈等杂物,浸入溶剂槽内浸泡2个小时。
脱脂废水处理技术方案

脱脂废水处理技术方案关键信息项:1、处理技术及工艺流程2、处理设备规格与型号3、处理效果标准4、项目实施时间节点5、费用及支付方式6、售后服务与质保期限1、引言本协议旨在明确脱脂废水处理技术方案的相关事宜,确保废水处理达到环保要求和预期效果。
11 背景随着工业生产的发展,脱脂废水的产生量逐渐增加。
为保护环境,实现可持续发展,需对脱脂废水进行有效处理。
12 目标通过采用先进的处理技术,使脱脂废水达到国家规定的排放标准。
2、处理技术及工艺流程21 技术选择采用物理化学法与生物处理相结合的综合处理技术。
211 预处理阶段通过格栅、沉砂池等设备去除大颗粒杂质和悬浮物。
212 化学处理阶段加入化学药剂,进行破乳、混凝、沉淀等反应,去除废水中的油脂和部分有机物。
213 生物处理阶段利用好氧生物处理工艺,进一步降解废水中的有机物。
22 工艺流程描述脱脂废水首先进入预处理单元,经过初步处理后进入化学处理单元,完成化学处理后进入生物处理单元,最后经过深度处理达标排放。
3、处理设备规格与型号31 预处理设备格栅:具体规格型号沉砂池:具体规格型号32 化学处理设备反应池:具体规格型号沉淀池:具体规格型号33 生物处理设备曝气池:具体规格型号生物膜反应器:具体规格型号34 深度处理设备过滤装置:具体规格型号消毒设备:具体规格型号4、处理效果标准41 水质指标处理后的脱脂废水应满足以下主要水质指标:化学需氧量(COD):具体数值生化需氧量(BOD):具体数值悬浮物(SS):具体数值油脂含量:具体数值pH 值:具体数值42 排放标准符合国家具体排放标准名称及地方相关环保要求。
5、项目实施时间节点51 设计阶段开始时间结束时间,完成处理方案的设计和优化。
52 设备采购与安装开始时间结束时间,完成设备采购和安装调试。
53 试运行开始时间结束时间,进行系统试运行和性能测试。
54 正式运行开始时间,系统正式投入运行。
6、费用及支付方式61 项目总费用包括设备采购、安装调试、工程设计、技术服务等费用,总计具体金额。
冲压车间环保整改方案

冲压车间环保整改方案背景描述随着人们环保意识的不断提高,企业环保问题也日益引起了人们的关注,其中冲压车间作为企业生产环节中的主要源头,环保问题尤为突出。
本文对于冲压车间的环保问题提出了整改方案,以期改善企业的环境质量,达到环保、持续发展的目标。
现状分析主要环保问题冲压车间的生产活动会产生大量的噪音、粉尘和废水等危害环境的物质,如果不加以妥善处理就会造成极大的环境污染,甚至可能影响员工健康。
除此之外,冲压车间作为企业生产流程中的重要环节,其环保情况也直接关系到企业在社会中的形象和信誉度。
因此,对于冲压车间的环保问题进行整改显得十分必要。
环保整改难点针对冲压车间当前存在的环保问题,主要的整改难点在于如何采取科学、有效的方法,对车间内的废气、废水和噪声等环保问题进行有效控制,同时对车间内的生产设备、物品等进行管理和铺设,从而达到环保整改的效果。
环保整改方案设备管理冲压车间生产中常用到切割机、焊接机等设备,这些设备如果没有安装合适的管道和过滤装置,就会对环境造成危害。
因此,我们需要对这些设备进行专业的管理和维护。
具体的措施如下:•对已有的设备进行检查,确保各种排放口畅通并安装合规的过滤装置。
•针对新购置的设备,从环保角度考虑,选购能够符合相关标准的设备,并根据企业实际情况进行合理铺设,减少污染源。
•所有设备安装专业的检测设备,及时对环境问题进行监控和报警。
废气治理冲压车间生产过程中会产生含油烟、尘埃等高污染废气,如果不对其进行治理,会对车间内环境和外部环境造成不良影响。
因此,我们需要制定合理的废气治理方案。
具体的措施如下:•废气控制系统在安装过滤设备的前提下,进行经济集成设计、选用合适的材料和设备,确保废气排放符合相关标准。
•升级部分废气控制装置,例如,对于较老旧的废气控制装置,采取新型设备进行改造或替换。
废水治理冲压车间生产过程中产生大量含有油、污泥的废水,如果不加以处理,就会影响周边环境的水质及生态。
废气治理方案(精选6篇)

废气治理方案废气治理方案(精选6篇)为了确保事情或工作扎实开展,时常需要预先制定一份周密的方案,方案是书面计划,是具体行动实施办法细则,步骤等。
那么问题来了,方案应该怎么写?以下是小编为大家整理的废气治理方案(精选6篇),欢迎大家借鉴与参考,希望对大家有所帮助。
废气治理方案1为贯彻落实《国务院关于印发打赢蓝天保卫战三年行动计划的通知》有关要求,指导各地加强工业炉窑大气污染综合治理,协同控制温室气体排放,促进产业高质量发展,制定本方案。
一、重要意义工业炉窑是指在工业生产中利用燃料燃烧或电能等转换产生的热量,将物料或工件进行熔炼、熔化、焙(煅)烧、加热、干馏、气化等的热工设备,包括熔炼炉、熔化炉、焙(煅)烧炉(窑)、加热炉、热处理炉、干燥炉(窑)、焦炉、煤气发生炉等八类(见附件1)。
工业炉窑广泛应用于钢铁、焦化、有色、建材、石化、化工、机械制造等行业,对工业发展具有重要支撑作用,同时,也是工业领域大气污染的主要排放源。
相对于电站锅炉和工业锅炉,工业炉窑污染治理明显滞后,对环境空气质量产生重要影响。
京津冀及周边地区源解析结果表明,细颗粒物(PM2.5)污染来源中工业炉窑占20%左右。
从工业炉窑装备和污染治理技术水平来看,我国既有世界上最先进的生产工艺和环保治理设备,也存在大量落后生产工艺,环保治理设施简易,甚至没有环保设施,行业发展水平参差不齐,劣币驱逐良币问题突出。
尤其是在砖瓦、玻璃、耐火材料、陶瓷、铸造、铁合金、再生有色金属等涉工业炉窑行业,“散乱污”企业数量多,环境影响大,严重影响产业转型升级和高质量发展。
实施工业炉窑升级改造和深度治理是打赢蓝天保卫战重要措施,也是推动制造业高质量发展、推进供给侧结构性改革的重要抓手。
各地要充分认识全面加强工业炉窑大气污染综合治理的重要意义,深入推进相关工作。
二、总体要求(一)主要目标。
到20xx年,完善工业炉窑大气污染综合治理管理体系,推进工业炉窑全面达标排放,京津冀及周边地区、长三角地区、汾渭平原等大气污染防治重点区域(以下简称重点区域,范围见附件2)工业炉窑装备和污染治理水平明显提高,实现工业行业二氧化硫、氮氧化物、颗粒物等污染物排放进一步下降,促进钢铁、建材等重点行业二氧化碳排放总量得到有效控制,推动环境空气质量持续改善和产业高质量发展。
冲压车间环境保护导则

冲压车间环境保护导则背景随着工业化进程的不断推进,冲压车间作为一个重要的生产场所,其产生的废气、废水和废弃物对环境的影响日益凸显。
为了促进企业可持续发展,保障员工身体健康,保护环境,制定一套相应的环境保护导则非常必要。
目的本文档的目的是为冲压车间相关人员提供一套规范化、可操作的环境保护指南,以降低企业对环境及员工的不良影响,提高环境意识和环保能力。
责任生产部门1.生产部门要全面贯彻国家相关的环保法规和企业内部的环保政策,制定可行的环境保护方案,按时完成各项环保指标,确保生产活动不对环境造成危害。
2.生产部门要加强对设备的维护保养,确保设备运行稳定,不会发生故障等影响环境的问题。
管理部门1.管理部门要监督生产部门的环保工作,并对其执行环保方案的效果进行跟踪、评估以及纠正措施。
2.管理部门要制定、修订并完善企业的环保政策与管理制度,确保环保工作与企业管理相互协调。
3.管理部门要加强员工环保意识的教育与培训,提高员工对环保的认识和参与度。
员工1.员工要认真熟悉企业的环保政策和管理制度。
2.员工要严格按照规定,正确地使用、操作设备、工具和仪器,保证废气、废水、废物等污染物的减排。
3.员工要积极参与环保意识教育和培训,提高环保知识水平,提高环保自觉性。
要求1.压缩和减少废气、废水的排放。
管理部门要制定排放标准,并对生产部门进行监督和管理。
生产部门要依据排放标准科学设计工艺流程、选用优质的材料和设备,减少废气、废水的排放。
2.废物的妥善处理。
废物必须尽可能被回收再利用,如不能回收利用的,必须采用环保的处理方法,如分类存放、严格封存、定期清理、专业机构处理等。
3.安全环保设施的建设。
加强环保设施的建设,如垃圾桶、油水分离器、隔油池等,及时检测维护设施的性能,防止出现环保事故。
4.行为规范。
加强员工的环保意识,要求员工在工作中要注意环保,如减少喧哗、节约用水、节约用电等。
效果1.降低企业排放的废气、废水和废弃物,达到国家和地方环保标准。
氧气管线蒸汽脱脂方案

氧气管线所接氮气管线、阀门脱脂方案一、目的:对氧气管线上所接氮气管线、阀门,进行吹扫、脱脂。
二、吹扫介质:雾化空气 1.0MPa 蒸汽三、吹扫安全注意事项:1、拆装阀门注意保护填料、密封圈等阀门零部件。
2、阀门回装之前确认脱脂合格,并防止灰尘等杂物落入管道。
3、阀门的确认必须到位。
4、吹扫注意安全,穿长袖工作服。
5、蒸汽吹扫前注意管线暖管、排液。
6、做好管线吹扫记录。
三、吹扫准备:1、配临时管线,从煤浆管线LS1蒸汽吹扫管线止逆阀处,接临时管线至氧气管线上置换用的N3管线第一道闸阀处。
2、拆除XV1320后止逆阀阀芯,XV1306后止逆阀阀芯、XV1341后氮气管线止逆阀阀芯、拆除煤浆管线LS1管线上止逆阀,N3管线上第一道闸阀。
3、断开以下仪表取压管线的根部连接:PT1345、FT1321、PT1303、FT1307、PT1308、PT1343。
4、拆除以下压力表:PG13006、PG13007。
5、拆除以下阀门阀芯进行化洗:XV1320后手阀、止逆阀阀芯;XV1306 后手动阀、止逆阀阀芯;XV1341后氮气管线上后手动阀、止逆阀阀芯,化洗完成后全部复位。
四、吹扫方法1、所有被吹扫的管线的吹扫方法为:每次吹扫两个小时,冷却半小时,间歇吹扫四次,共计八小时。
2、吹扫开始时,应逐步缓慢开大蒸汽吹扫阀门,保证氧气管线受热均匀膨胀以及吹扫完时的均匀冷却。
五、吹扫路线1、吹扫煤浆管线上炉头吹扫LS1管线,包括临时管线的吹扫。
2、确认氧气炉头阀,XV1304关闭,XV1320打开,XV1320前、后阀打开。
确认到位后打开N3手阀吹扫1号管线,从N3管线所配临时管线通过XV1320然后到氮气缓冲罐。
3、确认氧气炉头阀打开,XV1320后手法关闭,PT1345取压管线根部断开,PG13007拆除,氧气管线至烧嘴加临时盲板,FV1321关闭。
吹扫2号管线,从N3管线所配临时管线通过PT1345、PG13007。
冲压车间环保整改措施

冲压车间环保整改措施背景随着环保意识的抬头,越来越多的企业开始重视环境保护,对环保法规的遵守也越来越严格。
冲压车间在生产过程中,排放出的废气、废水和废渣等都对环境造成了一定的污染。
为了满足环保法规要求,本文将介绍冲压车间的环保整改措施。
废气处理冲压车间排放的废气主要来自喷漆设备、焊接设备等。
针对这些设备,我们采取以下措施:1.安装废气净化设备。
喷漆设备和焊接设备安装空气净化器,对排放的废气进行净化和处理,确保达到排放标准。
2.加强检查。
定期进行设备检查和维护,并对设备运行情况进行监测和记录,及时发现异样情况并处理。
3.限制车间产生的二手烟。
在车间中明确禁止吸烟,通过管理制度、宣传以及制定相应的处罚措施,使员工自觉遵守并减少二手烟的产生。
废水处理冲压车间产生的废水主要有冷却水和洗涤废水等。
针对这些废水,我们采取以下措施:1.废水回收。
将洗涤废水进行处理,回收其中有价值的物质,如铁、铜等,达到资源与环保的双重目的。
2.排放前处理。
将废水通过化学处理、调节pH值等措施,使其达到国家规定的排放标准,确保废水不会对环境造成污染。
3.内部循环利用。
对于冷却水,我们采用循环利用方法,通过循环使用和进行适量补充,达到节约用水的目的。
垃圾处理冲压车间产生的垃圾主要有生活垃圾、废弃物料和废旧设备器材等。
针对这些垃圾,我们采取以下措施:1.分类投放。
在车间内设置分类垃圾桶,明确标识各类垃圾的投放位置及种类,通过分类投放,减少可再生资源的浪费。
2.安排定期清理。
针对冲压车间产生的垃圾,安排定期清理,确保环境卫生。
3.做好设备报废处理。
对于冲压车间已经报废的设备器材,进行分类处理,将可回收的部分进行回收利用,确保环保与资源利用。
员工培训为了确保整个冲压车间环保整改工作的实施,我们将对员工进行培训,组织环境保护教育和技能培训,严格让每一位员工遵守环保法规和操作规程,树立环保意识,贯彻落实环保措施,共同关注环保,为保护环境、推动单位可持续发展做出员工应有的贡献。
- 1、下载文档前请自行甄别文档内容的完整性,平台不提供额外的编辑、内容补充、找答案等附加服务。
- 2、"仅部分预览"的文档,不可在线预览部分如存在完整性等问题,可反馈申请退款(可完整预览的文档不适用该条件!)。
- 3、如文档侵犯您的权益,请联系客服反馈,我们会尽快为您处理(人工客服工作时间:9:00-18:30)。
冲压油挥发有机废气治理技术方案一、项目概述目前需要治理的环节为高速冲床车间内挥发性冲压油的常温自然挥发排气,以及脱脂炉高温下工件表面的挥发性冲压油受热挥发排气。
目前针对该两股废气进行有组织收集或有效的处理,大量的挥发性废气(带恶臭)需进行治理,通过废气处理,可以收集冷凝冲压油,该油通过适当处理,可以部分回用至工艺,产生客观的经济效益。
二、设计依据(1)《中华人民共和国环境保护法》(1989年)(2)《中华人民共和国大气污染防治法》(2004年4月修订)(3)《采暖通风与空气调节设计规范》(GB50019-2003)(4)《通用用电设备配电设计规范》(GB5055-2011)(5)《低压配电设计规范》(GB50054-2011)(6)《大气环境质量标准》(GB3095-1996)(7)《大气污染物综合排放标准》(GB 16297-1996)(8)《恶臭污染物排放标准》(GB 14554-93)(9)《工业企业设计卫生标准》(GBZ 1-2010)(10)《浙江省挥发性有机物污染整治方案》(11)《宁波奥克斯空调有限公司年产126万套变频空调及配套设施生产线技改项目》环评报告及批复(12)提供的生产设备相关资料。
三、设计范围方案设计对象:位于A3车间内的4台脱脂炉及12个高速冲床;位于C4车间内的3台脱脂炉及12个高速冲床。
方案的设计范围:包括废气收集装置、处理装置、配套机电设备以及电器控制在内的整套系统。
四、设计标准废气排放执行《大气污染物综合排放标准》(GB16297-1996)中的二级标准,见表4.1;废气排放的臭气浓度标准为:2000(无量纲)。
另外根据《浙江省挥发性有机物污染整治方案》的相关要求,有机废气的净化效率应达到90%以上。
由于挥发性冲压油的挥发分中,非甲烷总烃仅占一部分比例,且非甲烷总烃的分子量较小,不易通过冷凝进行去除,故非甲烷总烃的进出口净化效率不能直接反映环保设备对废气中的总有机物的净化效率。
可以通过处理回收下来的废冲压油量进行物料核算,从而更准确地推算系统对废气中有机废气的去除效果。
表4.1 大气污染物排放标准五、设计原则⑴采用技术成熟、安全、可靠的工艺和先进、简单、处理效果好的设备,确保环保设施运行正常;⑵整个工程做到布局合理、占地空间小、外形结构美观;净化系统投资最经济,运行费用低为原则;⑶以工艺简单合理,设备使用寿命长,维护简单、方便,并且处理效果稳定,确保处理后废气达到排放标准;⑷有一定的灵活性,在环保要求提高后经过少量的调整即可满足新的要求。
六、净化工艺设计(一)企业基本资料及设计参数(1)企业基本情况分析企业有脱脂炉产生的脱脂废气,该股废气的温度在80度左右,单台脱脂炉的废气强制排风量约为5000 m3/h;冲压车间废气含自然挥发的有机气体,该股废气的温度在25度左右,单个冲压车间的废气风机排放量为约为3000 m3/h。
其中企业在最大生产负荷下每日冲压油用量为2m3,约1.5吨。
其中跑冒滴漏及无组织挥发量约占15%。
冲压车间自然挥发量约占5%,脱脂炉受热挥发量约占80%。
企业共有19台冲床,每个冲床车间的冲压油挥发量约为4kg/d,每天工作24小时,折合废气排放浓度约为56mg/m3;企业现有脱脂炉5台,每台脱脂炉的冲压油挥发量约为240kg/d,每天工作24小时,折合废气排放浓度约为2000mg/m3。
(2)设计参数拟对每个车间的脱脂炉废气和冲压废气做合并处理。
其中A3车间有4台脱脂炉,同时生产时的废气总排放量为20000 m3/h;12个冲床车间同时生产时的废气总排放量约为36000 m3/h;其他车间废气总排放量分别为15000 m3/h和36000 m3/h。
表6.1 A3车间废气产生量分析表表6.2 C4车间废气产生量分析表(二)处理工艺及说明废气处理首先考虑企业现有场地比较紧张,在净化工艺设计上优先考虑废气合并处理,节约场地。
此外废气合并处理可以有效降低投资和运行成本。
脱脂炉废气的特点为:高温、高浓度有机废气,冲床废气的特点为:常温、含有机废气。
以A3车间4台脱脂炉同时工作时的废气排放情况进行分析,工艺选择采用二级间接水冷换热串联冷冻水湿式旋流板塔串联处理。
工艺选择分析如下:脱脂炉排放的废气通过管道输送至车间外以后进行合并,首先经过二级常温水冷后与冲压废气管道合并进入主风机,然后进入冷冻水二级旋流塔处理直接接触热交换及捕捉,最后后高空排放。
脱脂炉废气的最高温度约为80度,预目标处理温度为40度。
以20000m3/h的干空气冷却热交换功率计算为221kw,20kg冲压油的冷凝热功率约15kw。
由于废气中的有机废气成分为挥发性冲压油的全挥发份,该有机物的饱和蒸气压较低,需要对其进行冷凝,通过冷凝可以从废气中分离出大部分冲压油。
由于常温水冷的冷却介质为水,在夏天水温较高,导致传热效果差,难以对废气进行非常有效降温冷凝,故需在后段设置冷冻水旋流板塔处理,冷冻水系统的制冷功率设置120kw,使循环水温度可以降低10度左右,可以在常温水间接冷凝的基础上进一步降低废气温度,对废气中的冲压油进行有效分离和捕捉。
通过一级间接热交换冷凝(热交换功率120kw),将废气温度降至50度,去除冲压油约占总排放量的35%;通过二级间接热交换冷凝(热交换功率100kw),将废气温度降至40度,去除冲压油约占总排放量的35%;合并废气通过冷冻水旋流板塔(总热交换功率140kw),将废气温度降至20度,去除冲压油约占总排放量的30%。
通过以上组合工艺处理,对挥发性冲压油的净化效率有90%以上。
排放废气中的非甲烷总烃浓度可以控制在120mg/m3以下。
废气可以满足《大气污染物综合排放标准》,通过15m排气筒排放。
整个系统通过PLC自动控制,当生产负荷降低时,自动控制相应管道风阀开关,并调节主风机频率,降低运行能耗;通过温度监控系统可以控制冷冻水制备系统的开关,从而在冬季水温及气温较低时智能减少设备运行能耗。
夏季极端高温气候,可以通过零时性投放冰块,降低预冷却系统水温度,从而更好地控制系统温度,降低系统负荷。
由于废气中的挥发性冲压油大部分经过冷凝被分离回收,故需设置专人对系统分离出来的油品进行回收处置。
其中一级间接冷凝、二级间接冷凝以及冷冻水旋流板塔3处处理单元均有冷凝冲压油产生,产生的冲压油通过专门管道输送至废油储罐中,并通过适当处理进行部分回用。
废气处理工艺流程如图6.1所示。
图6.1 废气处理工艺流程图七、治理设备选型A3车间废气处理系统设备选型:(1)一级水冷换热器,碳钢材质,长1.7m,宽1.7m,高度1.2m,螺旋片管150m,循环水量40m3/h,换热功率120kw,一台;(2)换热系统中间水池,PP材质,有效容积2m3,一座;(3)二级水冷换热器,碳钢材质,长1.7m,宽1.7m,高度1.2m,螺旋片管150m,循环水量40m3/h,换热功率100kw,一台;(4)一级水冷换热管道离心泵,流量40m3/h,扬程25m,功率5.5kw,两台(一用一备);(5)二级水冷换热管道离心泵,流量40m3/h,扬程25m,功率5.5kw,两台(一用一备);(6)冷却塔,直径2000mm,高度2200mm,设计流量40m3/h,功率1.1kw,一座;(7)旋流板塔,碳钢材质,3级旋流板,直径2.4m,高度7m,处理风量56000 m3/h,循环水量50m3/h,数量1台;(8)管道离心泵,流量50 m3/h,扬程12m,功率3.7kw,两台(一用一备);(9)冷冻水系统,长2.2m,宽1.7m,高2m,制冷功率120kw,运行功率50kw,一套;(10)离心风机:碳钢材质,4-72-12C/45kw,风量56000 m3/h,全压2200pa,一台;(11)PLC控制系统,1台风机,4台水泵,1台冷却塔,1套制冷系统,4个废气温控点,一套;(12)油水分离器,有效容积3m3,一套;C4车间废气处理系统设备选型:(13)一级水冷换热器,碳钢材质,长1.5m,宽1.5m,高度1m,螺旋片管100m,循环水量30m3/h,换热功率100kw,一台;(14)换热系统中间水池,PP材质,有效容积2m3,一座;(15)二级水冷换热器,碳钢材质,长1.5m,宽1.5m,高度1m,螺旋片管100m,循环水量30m3/h,换热功率80kw,一台;(16)一级水冷换热管道离心泵,流量30m3/h,扬程24m,功率4kw,两台(一用一备);(17)二级水冷换热管道离心泵,流量30m3/h,扬程24m,功率4kw,两台(一用一备);(18)冷却塔,直径2000mm,高度2200mm,设计流量30m3/h,功率1.1kw,一座;(19)旋流板塔,碳钢材质,3级旋流板,直径2.2m,高度7m,处理风量51000 m3/h,循环水量40m3/h,数量1台;(20)管道离心泵,流量50 m3/h,扬程12m,功率3.7kw,两台(一用一备);(21)冷冻水系统,长2m,宽1.5m,高2m,制冷功率100kw,运行功率40kw,一套;(22)离心风机:碳钢材质,4-72-12C/45kw,风量51000 m3/h,全压2300pa,一台;(23)PLC控制系统一套,1台风机,4台水泵,1台冷却塔,1套制冷系统,4个废气温控点;(24)油水分离器,有效容积3m3,一套;八、配电A3车间废气处理系统:配套最大功率:106kw。
夏季运行功率约106kw,冬季运行功率约84kw;C4车间废气处理系统:配套最大功率:98kw。
夏季运行功率约98kw,冬季运行功率约78kw;九、平面布置本项目处理装置初步考虑布置在车间外,具体另见平面布置图。
十、工程清单A3车间废气处理系统C4十一、工程其它说明1、系统配置统一配电箱,配电箱的外部供电(包括电缆连接)由甲方负责;2、施工时需甲方提供380V或220V电源及设备进线电源;3、施工时,甲方和乙方均设一名现场负责人,方便联系;4、设备安装在室外,厂房采取适当措施,对机电设备进行一定的保护。
5、夏季极端高温天气会导致废气处理系统冷却效果下降,建议对冷冻水喷淋系统投加冰块应急,以确保处理效果。
十二、售后服务及保养(一)施工现场服务在工程施工中保持密切联系,解决施工问题。
各专业设计人员根据施工进度要求首先到现场进行施工交底,在施工高峰期将派现场代表,平时根据甲方要求确保3小时内到达施工现场,解决施工中发生的各种问题,及时做出图纸修改和变更。
乙方必须遵守甲方厂纪厂规,要在施工时注意甲方生产现场,下班后现场及时清理干净。
乙方在甲方工厂内须严格按照甲方的各项规章制度执行,否则,甲方将有权对乙方按甲方公司规章制度进行处理。
由于乙方原因所导致的乙方人员在甲方工厂内发生的一切事故均由乙方自行承担,与甲方无关;改造过程中因为乙方原因造成的甲方设备损坏和人员伤亡由乙方全部承担。