轴类零件的工艺路线实例
轴类零件加工2012

2013-8-13
21
(4)次要表面加工的安排。
轴上的花键、键槽、螺纹等次要表面加工,通常均安排
在外圆精车或粗磨之后、精磨外圆之前进行。
如果精车前就铣出键槽,精车时因断续切削而易产生振动, 既影响加工质量,又容易损坏刀具,也难控制键槽的深度。 次要表面加工也不能放到主要表面精磨之后,否则会破坏 主要表面已获得的精度。
2013-8-13
11
二、轴类零件机械加工的主要工艺问题
轴类零件在机械中起着突出的作用,工作中受弯曲、
扭转和交变载荷,有时还得承受一定冲击性载荷。支承轴
颈处还要承受磨擦,产生摩擦热。为了保证轴件的正常工 作,轴件的加工质量至关重要。这就需要解决好轴件加工
的工艺问题。
工艺的关键问题在于防止弯曲变形、残余内应力和微 观裂纹的产生。为了保证轴件的质量,机械加工中必须解 决好以下主要工艺问题:
同,穿插于粗加工、半精加工、精加工各加工阶段之间。
2013-8-13
23
4.轴类零件的热处理及其安排
轴类零件的使用性能除与所选钢材种类有关外,还与所 采用的热处理关系密切。 作用:改善切削性能 去除内应力 提高机械性能
(1)锻造毛坯在机加工前,均需安排正火或退火处理(含碳 量大于ω (C)=0.7%的碳钢和合金钢),以使钢材内部晶粒细 化,消除锻造应力,降低材料硬度,改善切削加工性能。 (2)为了获得较好的综合力学性能,轴类零件常要求调质处 理,一般分两种情况:
需在渗氮之前进行调质和低温时效处理。对调质的质 量要求也很严格,不仅要求调质后索氏体组织要均匀细 化,而且要求离表面0.8~0.10mm层内铁素体含量不超过 ω(C)=5%,否则会造成氮化脆性而影响其质量。
2013-8-13
轴类零件加工工艺

轴类零件加工工艺机床主轴机床主轴是典型的受扭转—弯曲复合作用的轴件,它受的应力不大(中等载荷),承担的冲击载荷也不大,假如使用滑动轴承,轴颈处要求耐磨。
因此大多采纳45钢制造,并进行调质处理,轴颈处由表面淬火来强化。
载荷较大时则用40Cr等低合金结构钢来制造。
车床主轴的选材结果如下:材料:45钢。
热处理:整体调质,轴颈及锥孔表面淬火。
性能要求:整体硬度NB220~HB240;轴颈及锥孔处硬度HRC52。
工艺路线:锻造→正火→粗加工→调质→精加工→表面淬火及低温回火→磨削。
该轴工作应力专门低,冲击载荷不大,45钢处理后屈服极限可达400MPa以上,完全可满足要求。
现在有部分机床主轴差不多能够用球墨铸铁制造。
拖拉机半轴汽车半轴是典型的受扭矩的轴件,但工作应力较大,且受相当大的冲击载荷,其结构如图5所示。
最大直径达50mm左右,用45钢制造时,即使水淬也只能使表面淬透深度为10%半径。
为了提高淬透性,并在油中淬火防止变形和开裂,中、小型汽车的半轴一样用40Cr制造,重型车用40CrMnMo等淬透性专门高的钢制造。
例:铁牛45半轴材料:40Cr。
热处理:整体调质。
性能要求:杆部HRC37~HRC44;盘部外圆HRC24~HRC34。
工艺路线:下料→锻造→正火→机械加工→调质→盘部钻孔→磨花键。
机床齿轮机床齿轮工作条件较好,工作中受力不大,转速中等,工作平稳无强烈冲击,因此其齿面强度、心部强度和韧性的要求均不太高,一样用45钢制造,采纳高频淬火表面强化,齿面硬度可达HRC52左右,这对弯曲疲劳或表面疲劳是足够了。
齿轮调质后,心部可保证有HB220左右的硬度及大于4kg?m/cm2的冲击韧性,能满足工作要求。
关于一部分要求较高的齿轮,可用合金调质钢(如40Cr等)制造。
这时心部强度及韧性都有所提高,弯曲疲劳及表面疲劳抗力也都增大。
例:一般车床床头箱传动齿轮。
材料:45钢。
热处理:正火或调质,齿部高频淬火和低温回火。
介绍轴类锻件加工工艺
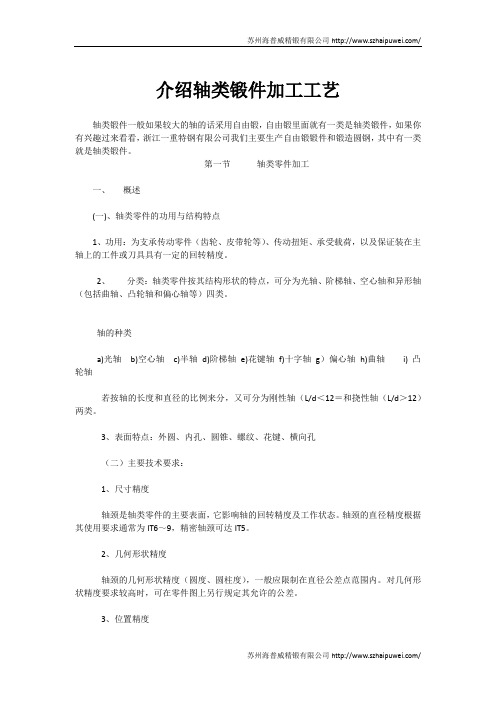
介绍轴类锻件加工工艺轴类锻件一般如果较大的轴的话采用自由锻,自由锻里面就有一类是轴类锻件,如果你有兴趣过来看看,浙江一重特钢有限公司我们主要生产自由锻锻件和锻造圆钢,其中有一类就是轴类锻件。
第一节轴类零件加工一、概述(一)、轴类零件的功用与结构特点1、功用:为支承传动零件(齿轮、皮带轮等)、传动扭矩、承受载荷,以及保证装在主轴上的工件或刀具具有一定的回转精度。
2、分类:轴类零件按其结构形状的特点,可分为光轴、阶梯轴、空心轴和异形轴(包括曲轴、凸轮轴和偏心轴等)四类。
轴的种类a)光轴b)空心轴c)半轴d)阶梯轴e)花键轴f)十字轴g)偏心轴h)曲轴i) 凸轮轴若按轴的长度和直径的比例来分,又可分为刚性轴(L/d<12=和挠性轴(L/d>12)两类。
3、表面特点:外圆、内孔、圆锥、螺纹、花键、横向孔(二)主要技术要求:1、尺寸精度轴颈是轴类零件的主要表面,它影响轴的回转精度及工作状态。
轴颈的直径精度根据其使用要求通常为IT6~9,精密轴颈可达IT5。
2、几何形状精度轴颈的几何形状精度(圆度、圆柱度),一般应限制在直径公差点范围内。
对几何形状精度要求较高时,可在零件图上另行规定其允许的公差。
3、位置精度主要是指装配传动件的配合轴颈相对于装配轴承的支承轴颈的同轴度,通常是用配合轴颈对支承轴颈的径向圆跳动来表示的;根据使用要求,规定高精度轴为0.001~0.005mm,而一般精度轴为0.01~0.03mm。
此外还有内外圆柱面的同轴度和轴向定位端面与轴心线的垂直度要求等。
4.表面粗糙度根据零件的表面工作部位的不同,可有不同的表面粗糙度值,例如普通机床主轴支承轴颈的表面粗糙度为Ra0.16~0.63um,配合轴颈的表面粗糙度为Ra0.63~2.5um,随着机器运转速度的增大和精密程度的提高,轴类零件表面粗糙度值要求也将越来越小。
(三)、轴类零件的材料和毛坯合理选用材料和规定热处理的技术要求,对提高轴类零件的强度和使用寿命有重要意义,同时,对轴的加工过程有极大的影响。
工艺流程编排:轴类零件一
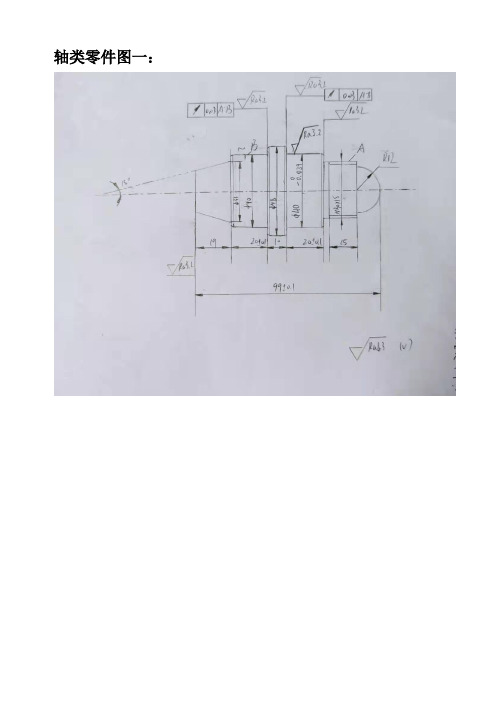
轴类零件图一:一、计算年生产纲领、确定生产类型计划期内应当生产的产品产量和进度计划成为生产纲领。
计划期定为1年,所以年生产纲领也就是年产量,零件的生产纲领计算如下:N=Qn(1+a+b)其中,Q-产品的年产量,94台/年n-每台产品中该零件的数量,1件/台a-备品的百分率,2%b-废品的百分率,2%代入数据有:N=94×1×(1+2%+2%)=94×1.04=97.76≈98件二、零件图分析由零件图可分析得,该工件由:两个端面,台阶,外圆柱面,半球体和外螺纹组成,15°圆锥面表面是实心刚性轴,轴上轴径φ45×20mm是轴的装配基准面A B,由此可见,该轴的技术要求中,分多次精度,指标是以A B为基准进行制定。
几何公差如下:①端面粗糙度Ra3.2μm;②轴套零件总长度公差±0.05mm;③基准圆A,B粗糙度Ra3.2μm;④轴肩轴径φ48*10mm两端面圆跳动量为0.03mm;⑤尺寸精度要求为IT8,且需要加工半球面,适合使用数控机床进行加工。
根据以上分析可知:该零件的结构比较简单,加工精度和表面质量要求不高,比较容易完成加工。
三、选择毛坯平常常用的毛坯种类有:铸件/锻件/型材/焊接件等,在加工时我们选择铝制型材作为毛坯,铝在加工后会生成三氧化二铝,形成保护膜,使零件不易生锈。
毛坯的形状何尺寸主要由零件组成表面的形状、结构、尺寸和加工余量等因素决定的,并尽量与零件接近,以达到减少机械加工的劳动量,考虑到加工余量、面及加工情况来选择,该工件选用毛坯定为大小为φ52×103mm 铝制型材。
四、工艺方案根据零件图综合分析,采取如下工艺方案:1.半球体→数控机床编程加工;2.外圆→粗车→半精车→精车;3.外螺纹→铣削;4.15°圆锥面→粗车→半精车→精车。
五、确定各工序的加工余量,计算公式工序尺寸及公差确定φ40外圆表面各工序尺寸及偏差1.根据技术要求,确定加工路线。
典型轴类零件的加工工艺

典型轴类零件的加工工艺典型轴类零件的加工工艺设计能通过运用机械制造工艺学课程中的基本理论以及在生产实习中学到实践知识,正确的解决一个零件在加工过程中的定位.夹紧以及工艺路线安排.工艺尺寸确定等问题,保证零件的加工质量本文选择了轴的加工工艺设计这一课题,主要阐述了对轴类零件的加工工艺过程,主要表现在从毛坯到成品的的过程它分为零件的热处理,大部分采用的是常见的四把火和调制处理.对典型的轴比如机床主轴、汽车半轴、内燃机曲轴、阶梯轴和CA6140主轴的热处理和加工工艺都有很明确的方案及选材。
对轴的加工工艺流程分为:下料→锻造→正火→机械加工→调质→粗车—半精车—精车—粗磨—精磨—光整加工—终检。
对工件的装夹都采取一次性装夹满足基准重合和基准统一或者互为基准。
对不同的工件采取的加工工艺有所不同。
以上此法操作简便、工效提高、节省材料,能保证加工精度。
对它的工艺性能也有明显的提高和使用寿命长等优点。
关键词:热处理工艺轴加工工艺轴的装夹定位Through the use of machinery manufacturing technology courses in basic theory and practice in the production of learned practical knowledge, the correct solution to a part in the positioning process. Clamping and routing process. Process to determine issues such as size, to ensure that the processing of parts qualityThis article has chosen the design process of the axis of the subject, the main shaft of the machining process, mainly in the finished product from rough to divide it into parts of the process of heat treatment, most commonly used is the four - to deal with fire and modulation. For example, a typical machine tool spindle axis, automotive axle, the internal combustion engine crankshaft, stepped shaft and spindle CA6140 process of heat treatment and processing of the program are very clear and material selection.Processing process of the axis is divided into: forging → → Cutting machining normalizing → → → Rough quenched - semi-refined car - Finish - coarse grinding - Grinding - Finishing - the end of the seizure. Clamping of the work piece clamping has been taken to meet the benchmark one-time overlap and complement each other or to benchmark thebenchmark reunification. Different parts of the process taken to be different. Above this method is simple, to improve work efficiency, saving materials, can guarantee the processing precision. The performance of its technology has improved and the advantages of long life.Key words: heat treatment process processing shaft axis positioning of the clamping目录第一章前言 (1)第二章轴类零件的分类和技术要求 (2)第一节轴类零件的功用与结构特点 (2)第二节主要技术要求 (3)第三节轴类零件的材料和毛坯 (3)第四节轴类零件的预加工 (4)第三章典型主轴类零件加工工艺分析 (5)第一节轴类零件加工的工艺路线 (5)第二节轴类零件加工的定位基准和装夹 (5)第四章轴类零件选材及工艺设计 (7)第一节机床主轴 (7)第二节汽车半轴 (9)第三节内燃机曲轴 (10)第四节阶梯轴的加工工艺过程 (10)第五节CA6140主轴加工工艺过程 (11)第五章检验 (17)第一节加工中的检验 (17)第二节加工后的检验 (17)结束语 (18)谢辞 (19)参考文献 (20)[1]邱宣怀.机械设计[M].北京:高等教育出版社,1997.. (20)[2]范文慧谭建荣.基于图形单元技术的轴类零件的设计[J].机械设计2001 (20)[3]西北工业大学机械原理及机械零件教研室.机械原理[M].北京:高等教育出版社,1987. 20 [4]机械设计手册编委会.机械设计册[M].北京:接写工业出版社2004 (20)第一章前言在机床、汽车、拖拉机等制造工业中,轴类零件是另一类用量很大,且占有相当重要地位的结构件。
典型轴类零件加工实用工艺分析报告
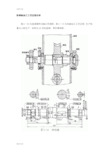
阶梯轴加工工艺过程分析图6—34为减速箱传动轴工作图样。
表6—13为该轴加工工艺过程。
生产批量为小批生产。
材料为45热轧圆钢。
零件需调质。
(一)结构及技术条件分析该轴为没有中心通孔的多阶梯轴。
根据该零件工作图,其轴颈M、N,外圆P,Q及轴肩G、H、I有较高的尺寸精度和形状位置精度,并有较小的表面粗糙度值,该轴有调质热处理要求。
(二)加工工艺过程分析1.确定主要表面加工方法和加工方案。
传动轴大多是回转表面,主要是采用车削和外圆磨削。
由于该轴主要表面M,N,P,Q的公差等级较高(IT6),表面粗糙度值较小(Ra0.8μm),最终加工应采用磨削。
其加工方案可参考表3-14。
2.划分加工阶段该轴加工划分为三个加工阶段,即粗车(粗车外圆、钻中心孔),半精车(半精车各处外圆、台肩和修研中心孔等),粗精磨各处外圆。
各加工阶段大致以热处理为界。
3.选择定位基准轴类零件的定位基面,最常用的是两中心孔。
因为轴类零件各外圆表面、螺纹表面的同轴度及端面对轴线的垂直度是相互位置精度的主要项目,而这些表面的设计基准一般都是轴的中心线,采用两中心孔定位就能符合基准重合原则。
而且由于多数工序都采用中心孔作为定位基面,能最大限度地加工出多个外圆和端面,这也符合基准统一原则。
但下列情况不能用两中心孔作为定位基面:(1)粗加工外圆时,为提高工件刚度,则采用轴外圆表面为定位基面,或以外圆和中心孔同作定位基面,即一夹一顶。
(2)当轴为通孔零件时,在加工过程中,作为定位基面的中心孔因钻出通孔而消失。
为了在通孔加工后还能用中心孔作为定位基面,工艺上常采用三种方法。
①当中心通孔直径较小时,可直接在孔口倒出宽度不大于2mm的60o内锥面来代替中心孔;②当轴有圆柱孔时,可采用图6—35a所示的锥堵,取1∶500锥度;当轴孔锥度较小时,取锥堵锥度与工件两端定位孔锥度相同;③当轴通孔的锥度较大时,可采用带锥堵的心轴,简称锥堵心轴,如图6—35b所示。
典型零件的选材及加工工艺路线分析讲解材料

轻量化
减轻材料重量,提高产品机动性,降低能源 消耗和排放。
环保化
发展可再生、可回收、可降解的材料,减少 对环境的污染。
智能化
研究具有自适应、自修复、自感应等功能的 智能材料。
新材料的研究与开发
碳纤维复合材料
具有高强度、轻质、耐高温等优点,广 泛应用于航空航天、汽车等领域。
高分子合成材料
具有优良的化学稳定性、绝缘性、耐 磨性等,在建筑、电子、化工等领域
03
材料的应用与发展趋势
材料的应用领域
01
航空航天
用于制造飞机、火箭等高强度、轻 质材料。
建筑领域
用于制造桥梁、高层建筑等高强度、 高耐久性材料。
03
02
汽车工业
用于制造发动机、变速器等耐磨、 耐高温材料。
电子产品
用于制造集成电路、晶体管等精密、 小型化材料。
04
材料的发展趋势
高性能化
提高材料的强度、硬度、耐高温等性能,以 满足更高要求的工业应用。
可加工性原则
材料应具有良好的可加工性, 以便于零件的制造和加工。
可维修性原则
材料应易于维修和更换,以提 高零件的使用寿命和降低维修 成本。
常用材料介绍
钢铁
钢铁是机械制造业中应用最广泛的材料之一,具 有高强度、良好的韧性和耐磨性。
铜及铜合金
铜及铜合金具有良好的导电性、导热性、耐腐蚀 性和加工性能,广泛应用于电气、电子、化工等 领域。
实例二:齿轮类零件的选材与加工工艺
灰铸铁
用于制造一般用途的齿轮,如减速器齿轮等。
球墨铸铁
用于制造高强度、高耐磨性的齿轮,如汽车变速毛坯准备
根据零件材料和尺寸要求,准备毛坯。
粗加工
零件的加工工艺路线

零件的加工工艺路线1、轴类零件典型工艺路线对于7级精度、表面粗糙度Ra0.8~0.4μm的一般传动轴,其典型工艺路线是:正火-车端面钻中心孔-粗车各表面-精车各表面-铣花键、键槽-热处理-修研中心孔-粗磨外圆-精磨外圆-检验。
轴类零件一般采用中心孔作为定位基准,以实现基准统一的方案。
在单件小批生产中钻中心孔工序常在普通车床上进行。
在大批量生产中常在铣端面钻中心孔专用机床上进行。
中心孔是轴类零件加工全过程中使用的定位基准,其质量对加工精度有着重大影响。
所以必须安排修研中心孔工序。
修研中心孔一般在车床上用金刚石或硬质合金顶尖加压进行。
对于空心轴(如机床主轴),为了能使用顶尖孔定位,一般均采用带顶尖孔的锥套心轴或锥堵。
若外圆和锥孔需反复多次、互为基准进行加工,则在重装锥堵或心轴时,必须按外圆找正或重新修磨中心孔。
轴上的花键、键槽等次要表面的加工,一般安排在外圆精车之后,磨削之前进行。
因为如果在精车之前就铣出键槽,在精车时由于断续切削而易产生振动,影响加工质量,又容易损坏刀具,也难以控制键槽的尺寸。
但也不应安排在外圆精磨之后进行,以免破坏外圆表面的加工精度和表面质量。
在轴类零件的加工过程中,应当安排必要的热处理工序,以保证其机械性能和加工精度,并改善工件的切削加工性。
一般毛坯锻造后安排正火工序,而调质则安排在粗加工后进行,以便消除粗加工后产生的应力及获得良好的综合机械性能。
淬火工序则安排在磨削工序之前。
2、齿轮的加工工艺路线(以45号钢为例):(1)、毛坯下料(2)、粗车(3)、调质处理(提高齿轮轴的韧性和轴的刚度)(4)、精车齿坯至尺寸(5)、磨齿(6)、若轴上有键槽时,可先加工键槽等(7)、滚齿(8)、齿面中频淬火(小齿轮用高频淬火),淬火硬度HRC48-58(具体硬度值需要依据工况、载荷等因素而定)(9)、成品的最终检验3、箱体的加工工艺路线箱壳体要求加工的表面很多。
在这些加工表面中,孔系加工精度是工艺关键问题。
传动轴机械加工工艺实例分析
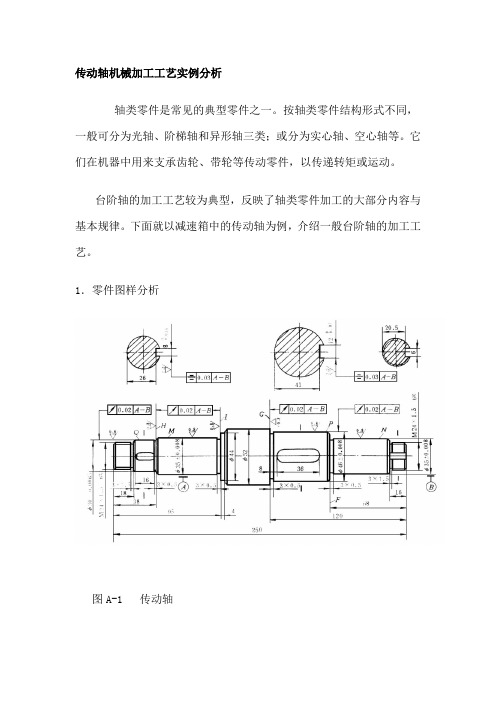
传动轴机械加工工艺实例分析轴类零件是常见的典型零件之一。
按轴类零件结构形式不同,一般可分为光轴、阶梯轴和异形轴三类;或分为实心轴、空心轴等。
它们在机器中用来支承齿轮、带轮等传动零件,以传递转矩或运动。
台阶轴的加工工艺较为典型,反映了轴类零件加工的大部分内容与基本规律。
下面就以减速箱中的传动轴为例,介绍一般台阶轴的加工工艺。
1.零件图样分析图A-1 传动轴图A-1所示零件是减速器中的传动轴。
它属于台阶轴类零件,由圆柱面、轴肩、螺纹、螺尾退刀槽、砂轮越程槽和键槽等组成。
轴肩一般用来确定安装在轴上零件的轴向位置,各环槽的作用是使零件装配时有一个正确的位置,并使加工中磨削外圆或车螺纹时退刀方便;键槽用于安装键,以传递转矩;螺纹用于安装各种锁紧螺母和调整螺母。
根据工作性能与条件,该传动轴图样(图A-1)规定了主要轴颈M,N,外圆P、Q以及轴肩G、H、I有较高的尺寸、位置精度和较小的表面粗糙度值,并有热处理要求。
这些技术要求必须在加工中给予保证。
因此,该传动轴的关键工序是轴颈M、N和外圆P、Q的加工。
2.确定毛坯该传动轴材料为45钢,因其属于一般传动轴,故选45钢可满足其要求。
本例传动轴属于中、小传动轴,并且各外圆直径尺寸相差不大,故选择¢60mm的热轧圆钢作毛坯。
3.确定主要表面的加工方法传动轴大都是回转表面,主要采用车削与外圆磨削成形。
由于该传动轴的主要表面M、N、P、Q的公差等级(IT6)较高,表面粗糙度Ra 值(Ra=0.8 um)较小,故车削后还需磨削。
外圆表面的加工方案(参考表A-3)可为:粗车→半精车→磨削。
4.确定定位基准合理地选择定位基准,对于保证零件的尺寸和位置精度有着决定性的作用。
由于该传动轴的几个主要配合表面(Q、P、N、M)及轴肩面(H、G)对基准轴线A-B均有径向圆跳动和端面圆跳动的要求,它又是实心轴,所以应选择两端中心孔为基准,采用双顶尖装夹方法,以保证零件的技术要求。
粗基准采用热轧圆钢的毛坯外圆。
第一部分 定位销轴零件加工工艺路线

第一部分定位销轴零件加工工艺路线定位销轴机械加工工艺实例轴类零件是常见的典型零件之一。
按轴类零件结构形式不同,一般可分为光轴、阶梯轴和异形轴三类;或分为实心轴、空心轴等。
它们在机器中用来支承齿轮、带轮等传动零件,以传递转矩或运动。
台阶轴的加工工艺较为典型,反映了轴类零件加工的大部分内容与基本规律。
下面就以定位销轴零件为例,介绍一般台阶轴的加工工艺。
1.零件图样分析图A-1图A-1所示为定位销轴零件。
它属于异形轴类零件,由圆柱面、轴肩和车槽等组成。
轴肩一般用来确定安装在轴上零件的轴向位置,各环槽的作用是使零件装配时有一个正确的位置,并使加工中磨削外圆时退刀方便。
2.确定毛坯该定位销轴轴材料为45钢,因其属于一般传动轴,故选45钢可满足其要求。
本例传动轴属于中、小传动轴,并且各外圆直径尺寸相差不大,故选择¢40mm的热轧圆钢作毛坯。
3.确定主要表面的加工方法传动轴大都是回转表面,主要采用车削与外圆磨削成形。
由于该传动轴的主要表面的公差等级(IT6)较高,表面粗糙度Ra值(Ra=1.6 um)较小,故车削后还需磨削。
外圆表面的加工方案可为:粗车→半精车→磨削。
4.确定定位基准合理地选择定位基准,对于保证零件的尺寸和位置精度有着决定性的作用。
由于该传动轴的几个主要配合表面对基准轴线均有径向圆跳动和端面圆跳动的要求,它又是实心轴,所以应选择两端中心孔为基准,采用双顶尖装夹方法,以保证零件的技术要求。
粗基准采用热轧圆钢的毛坯外圆。
中心孔加工采用三爪自定心卡盘装夹热轧圆钢的毛坯外圆,车端面、钻中心孔。
但必须注意,一般不能用毛坯外圆装夹两次钻两端中心孔,而应该以毛坯外圆作粗基准,先加工一个端面,钻中心孔,车出一端外圆;然后以已车过的外圆作基准,用三爪自定心卡盘装夹(有时在上工步已车外圆处搭中心架),车另一端面,钻中心孔。
如此加工中心孔,才能保证两中心孔同轴。
5.划分阶段对精度要求较高的零件,其粗、精加工应分开,以保证零件的质量。
数控车床零件加工编程实例
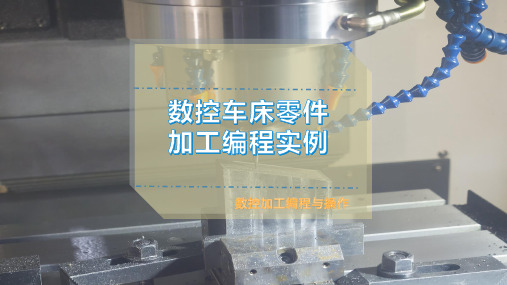
• G01 X20. F50;
• G00 Z100.;
• X100.;
ቤተ መጻሕፍቲ ባይዱ
• T0404;
换4号刀
• G00 X18. Z2.;
• G90 X21.6 Z-41. F300; 粗车φ22mm内孔,留径向余量0.4mm
• G01 X26. Z1. F50;
• X22. Z-1.;
倒角1×45°
• Z-39.;
数控车床零件加工编程实例
• 轴类零件编程 • 套类零件编程 • 轴套类零件编程
1.1 轴类零件编程
对图所示的零件进行精加工。图中φ85mm不加工,要求编制精加工程序。
1. 确定工艺路线
• 1)先从左至右切削外轮廓面。 • 其路线为:倒角—切削螺纹的实际外圆—切削锥度部分—
车削φ62mm外圆—倒角—车φ80mm外圆—切削圆弧部分— 车φ80mm外圆。 • 2)切3mm×φ45mm的槽。
快速退到Z为100的位置
• X100.;
• M05;
• M30;
1.3 轴套类零件编程
毛坯直径为φ50 mm,长为55 mm,材料为45钢。
确定工艺路线
• 手动加工出φ25mm的孔,装夹φ45 mm的外圆部分。以φ49 mm部 分的端面作为工作原点。先加工φ49 mm外径及φ30 mm内孔,车 外圆用外圆车刀T01, 加工孔用镗刀T02。
切槽加工
• G04 X3.;
槽底停留3秒
•
X45.;
退刀
• G00 Z-42.5;
• G01 X-1. F50;
切断
• G00 X100. Z100.;
• M05;
主轴停止
• M03;
程序结束
数控车加工实例

数控车床加工实例——螺纹车削加工
工艺分析及处理
(3)零件的装夹及夹具的选择 采用该机床本身的标准卡盘,毛坯伸出三爪卡盘外
70mm,并找正夹紧。
数控车床加工实例——螺纹车削加工
工艺分析及处理
(4)刀具和切削用量的选择 1)刀具的选择:选择1号刀具为90 °硬质合金机夹偏刀,用于
粗、精车削加工。选择2号刀具为硬质合金机夹切断刀,其刀片宽度 为5mm,用于切槽、切断车削加工。选择3号刀具为硬质合金机夹螺 纹刀,用于螺纹车削加工。
N80 X50.0;
车削台阶
N90 G00 Z1.0;
快速点定位
N100 X43.5;
N110 G01 Z-25.0;
粗车外圆柱台阶面为¢43.5 mm ×L25 mm
N120 X46.5;
车削台阶
N130 G00 Z1.0;
快速点定位
N140 X40.5;
数控车床加工实例——轴类零件
参考程序
N150 G01 Z-10.0;
粗镗内圆柱面为¢39.5mm
N90 X37.5;
切削台阶
N100 G00 Z2.0;
快速点定位
N110 X40.0;
数控车床加工实例——套类零件
参考程序
N120 G01 Z-25.0 F0.1;
精镗¢40 mm内圆柱面
N130 X37.5;
切削台阶
N140 G00 Z2.0;
快速点定位
N150 G00 X100.0 Z100.0 T20; 快速退回刀具起始点,取消2号刀的刀具补偿
N360 G01 X0.0 F0.1;
切断
N370 G00 X30.0;
退刀
N380 X100.0 Z100.0 T20; 快速退回刀具起始点,取消2号刀的刀具补偿
机械轴类零件的加工工艺PPT课件

一、概述 二、轴类零件的主要技术要求 三、轴类零件机械加工的主要工艺问题 四、轴类零件加工实例
一、概述
1.轴类零件的功用
(1)轴类零件的功用 支承传动零件(如齿轮、带轮、凸轮等)传递转矩、 承受载荷并保证装在轴上的零件(或刀具)具有一定的 回转精度。
正是因为轴类零件多用于变速箱、减速箱、发动 机、离合器、差速器一些动力转动机构中,所以 轴类零件是机械加工中非常重要的零件。
(3)轴类零件的加工表面
内、外圆柱面 内、外圆锥面 台阶平面和端平面 螺纹、花键、键槽和沟槽
2.轴类零件的材料和毛坯
(1)材料 碳素结构钢 合金结构钢
(2)毛坯 圆棒料 锻件 铸钢件
3.几何形状精度
主要指轴颈表面、外圆锥面、锥孔等重要表面的圆度、 圆柱度。其误差一般应限制在尺寸公差范围内,对于 精密轴,需在零件图上另行规定其几何形状精度。
4.相互位置精度
包括内、外表面、重要轴面的同轴度、圆的径向跳 动、重要端面对轴心线的垂直度、端面间的平行度等。
5.其它 热处理、倒角、倒棱及外观修饰等要求。
三、轴类零件机械加工的主要工艺问题
1.定位基准
中心孔 外圆表面和内孔表面
2.加工顺序的安排
粗、精加工分开进行 粗加工外圆表面时,应先加工直径大的外圆,后加
工直径小的外圆 空心轴的深孔加工应安排在工件经调质处理后和外
圆经粗车或半精车之后进行 轴上的花键、键槽应安排在外圆经精车或粗磨后、
磨削或精磨前加工 轴上螺纹应在轴颈经表面淬火后进行加工 主要表面经精磨以后不宜再安排其他表面的加工
3.热处理工序的安排
毛坯锻造后安排正火热处理 粗加工后安排调质热处理 工作中与配合零件有相对运动的轴颈和需要经常拆
- 1、下载文档前请自行甄别文档内容的完整性,平台不提供额外的编辑、内容补充、找答案等附加服务。
- 2、"仅部分预览"的文档,不可在线预览部分如存在完整性等问题,可反馈申请退款(可完整预览的文档不适用该条件!)。
- 3、如文档侵犯您的权益,请联系客服反馈,我们会尽快为您处理(人工客服工作时间:9:00-18:30)。
轴类零件的工艺路线实例
一、材料选择
轴类零件常用的材料为锻造或轧制的碳素钢或合金钢。
轴类零件之所以选用碳素钢和合金钢制造,是因为轴属于较为重要、较为精密的零件。
它本身要求足够的强度和刚度(包括变形刚度和接触刚度),足够精确的尺寸和较高的表面粗糙度,与滑动轴承配合处的轴颈表面还应有高的硬度。
因而材料应具有优良的综合机械性能。
而碳素钢和合金钢则能满足这些要求。
尤其是碳素钢,因其价格低廉,锻造工艺性能良好,对应力集中没有合金钢敏感,所以应用尤为广泛。
近年来,采用球墨铸铁或合金铸铁制造形状复杂的轴已获得很大的成功。
估计随着铸铁质量的进一步提高,“以铁代钢”将取得更加飞速的发展。
在选择轴的材料时,对载荷不大或不太重要的场合,可用Q235A、Q255A钢;对载荷较大,较为重要的场合,以45钢最为常用;重载,且轴的尺寸和重量受到限制时,或轴的工作条件恶劣时,则采用合金钢,如此40Cr、38CrMoAl等。
根据上述分析,本传动轴以选45号钢为宜。
二、毛坯的选择
该轴尺寸不大,但最大直径与最小直径的差值较大,因此不宜选择圆钢毛坯,应选择锻造毛坯。
考虑到轴的尺寸和重量采用模型锻造是可行的。
若批量较大,应选择模型锻造。
若批量较小,则应采用自由锻造。
三、工艺路线的拟定
在拟定工艺路线之前,先分析轴的结构和精度要求。
从结构上分析,轴由七段圆柱组成,上面有两个键槽和两个中心孔(其中一个中心孔带螺孔,以便安装轴端挡圈)。
从精度和粗糙度分析,有四段圆柱要求达到IT6级精度,其中安装联轴器的55段和要安装齿轮的80段两段要求粗糙度在1.6以下,安装轴承的65两段要求粗糙度在0.8以下。
以上四段圆柱之间又要求有较高的位置精度。
根据该轴主要由圆柱构成和多数段均要求较高的加工精度和较小的粗糙度这一特点,在拟定工艺路线时,应以外圆表面的加工贯穿始终,将全轴的加工分成粗、半精和精加工三个阶段,而将键槽和螺纹的加工穿插于各加工阶段中。
至于中心孔,其作用是为加工时提供安装定位基准。
根据“基准先行”的原则,应该在一开始就将其加工出来。
现将大批量生产时,该轴的主要加工工艺路线安排如表32-1所示,以供参考。
表
热处理的质量。
安排在半精加工之前(有时也安排在精加工之前),是为了通过半精加工(或精加工)修正热处理产生的变形。
在精车后铣键槽,易保证键槽深度,同时可防止精车时产生断续切削以影响精车质量。
左端螺纹孔放在精磨后加工,可防止加工螺纹孔时破坏中心孔精度,从而影响精磨质量。