911-锌浸出渣挥发窑生产工艺与节能
锌系统矿粉浸出渣挥发工艺操作规程(二)

锌系统矿粉浸出渣挥发工艺操作规程(二)1 范围本标准规定了锌系统挥发窑二工段矿粉浸出渣挥发工艺流程、基本原理、原材料及质量要求、工艺操作条件、岗位操作法、产出物料及质量要求、主要技术经济指标和主要设备。
本标准适用于锌系统挥发窑二工段矿粉浸出渣挥发的工艺操作过程。
2 规范性引用文件下列文件对于本文件的应用是必不可少的。
凡是注日期的引用文件,仅注日期的版本适用于本文件。
凡事不注日期的引用文件,其最新版本(包括所有的修改单)适用于本文件。
Q/ZYJ06.05.01.07 挥发窑氧化锌Q/ZYJ06.05.01.08 挥发窑液Q/ZYJ06.05.02.11 矿粉浸出渣Q/ZYJ13.01.04 煤气使用岗位通用安全环保操作流程Q/ZYJ15.02.01 工业煤气3 工艺流程4 基本原理在1100℃~1300℃的高温下,浸出渣中的锌、铅、铟、锗等有价金属(主要呈氧化物状态、部分呈硫化物状态存在)被一氧化碳还原为金属而挥发进入烟气,在烟气中被氧化成氧化锌等,随烟气离开挥发窑,被收集在收尘器内。
主要化学反应如式:在料层内:C+O2=CO2CO2+C=2COZnO+CO=Zn+CO2ZnO+C=Zn+COFe2O3+CO=2FeO+CO2FeO+CO=Fe+CO2ZnO+Fe=FeO+Zn在料层上空:Zn+1/2O2=ZnOCO+1/2O2=CO25 原材料及质量要求5.1 矿粉浸出渣:应符合Q/ZYJ06.01.02.11的规定5.2 焦粉5.2.1 化学成分(%):C≥75%,挥发物:4~6,灰分≤205.2.2 粒度:<5mm5.3 工业煤气:应符合Q/ZYJ15.02.01的规定6 工艺操作条件6.1 挥发窑6.1.1 窑转速:60s/r~120s/r(4#窑),90s/r~120s/r(5#窑)6.1.2 压缩风风压:0.10~0.14MPa(4#窑),0.16~0.20MPa(5#窑)6.1.3 窑尾温度:500℃~800℃6.1.4 窑尾负压:0~40Pa6.1.5 焦比:50%~60%(即100Kg浸出渣配50~60Kg焦粉)6.1.6 离窑烟气量:28000~40000Nm³3/h〃台(4#窑),35000~50000Nm³3/h〃台(5#窑)6.2 布袋收尘6.2.1 布袋入口温度:110℃~200℃6.2.2 布袋出口温度:70℃~110℃6.2.3 布袋箱负压:入口:1000~1400Pa,出口:2000~2400Pa6.3 电收尘6.3.1 烟气温度:进口:260℃~350℃,出口:230℃~320℃6.3.2 烟气含尘量:40g/Nm³~55g/Nm³6.3.3 进、出口负压差:280~320Pa6.3.4 漏风率:≤3%6.3.5 收尘效率:≥99.7%6.3.6 排风机出口烟气含尘:≤0.30g/Nm³7 岗位操作法8 产出物料及质量要求挥发前氧化锌(混合)应符合Q/ZYJ06.05.01.07的规定,Zn≥54%,Pb≤12%9 主要技术经济指标9.1 窑流含锌:≤2.5%9.2 锌回收率:≥92%9.3 铅吸收率:≥80%9.4 收尘效率:≥99%9.5 焦粉单耗:≤1800Kg/tZnO9.6 布袋单耗:≤0.05条/tZnO10 主要设备1 4#挥发窑 1附:减速机 1万向联轴节 1主电机 1事故电机 1悬挂齿轮箱 12 5#挥发窑 1主电机 2事故电机 1事故减速机 1万向联轴节 2悬挂齿轮箱 23 1#、3#抓斗起重机 2 附:大车电机 4小车电机 2卷扬电机 4大车减速机 2小车减速机 1卷扬减速机 24 3#抓斗吊车 1附:大车电机 2小车电机 1卷扬电机 2大车减速机 2小车减速机 1卷扬减速机 25 4#抓斗吊车 1附:大车电机 2小车电机 1卷扬电机 2大车减速机 2小车减速机 1卷扬减速机 26 配料圆盘配料机 2电机(焦粉圆盘)1 电机(浸出渣圆盘)1 减速机 1减速机 17 配料皮带运输机 2 附:减速机 2电机 28 43#皮带运输机 1 附:减速机 1电机 1减速机9 44#皮带运输机 1 附:减速机 1电机 1减速机10 45#皮带运输机 1电机 1减速机11 4#进料圆盘 1附:减速机 1电机 1减速机12 3#进料圆盘 1附:减速机 1电机 1减速机13 连续斗式运输机 1附:减速机 1电机 114 46#皮带运输机 1附:减速机 1电机 1减速机15 4#余热锅炉 1附:吹灰机 1816 锅炉给水泵 2附:电机 217 锅炉饮水泵 2附:电机 218 蒸汽往复泵19 螺旋除尘机(长) 1附:减速机 120 螺旋除尘机(短) 1附:减速机 121 5#余热锅炉 1附:吹灰机 2022 锅炉给水泵 2附:电机 223 锅炉饮水泵 2附:电机 224 螺旋除尘机(长) 1附:减速机 125 螺旋除尘机 1附:减速机 126 冲渣泵 6附:电机 627 表面冷却器 2附:振打电机 628 螺旋输送机(冷却) 229 螺旋输送机(布袋)4附:电机 430 电除尘器 131 螺旋输送机(电收尘) 2附:电机 232 1#锅炉引风机 1附:电机 1液力耦合器 1油冷却器 133 2#锅炉引风机 1附:电机 1液力耦合器 134 强风机循环水泵 4附:电机 435 水环式真空泵 3附:电机 336 罗茨泵 4附:电机 437 空气压缩机 1附:电机 138 空气压缩机 2附:电机 239 空气压缩机 3附:电机 340 空气压缩机 241 空气压缩机 1附:电机 142 电动单梁起重机 1附:行走电机 1运行电机 1起升电机 143 空压机循环热水泵 2附:电机 244 空压机循环冷水泵 2附:电机 245 离子循环冷水泵 2附:电机 246 离子循环热水泵 2附:电机 247 污水冷却风机 5附:电机 548 脉冲布袋收尘器 449 钟罩阀(4#窑) 150 钟罩阀(5#窑) 151 冷却塔风机 4。
锌浸出渣的处理
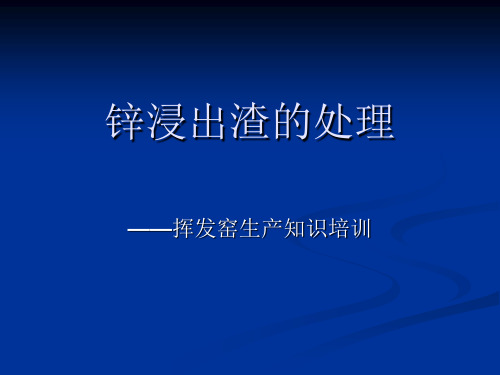
2.浸出渣的组成及各组分在处理过 程中的行为
浸出渣的组成: 锌在浸出渣中主要以铁酸锌(ZnO· Fe2O3)、 硫化锌(ZnS)、硫酸锌(ZnSO4)、氧化锌 (ZnO)及硅酸锌(ZnO· SiO2)等形态存在 铅主要以硫酸铅(PbSO4)及硫化铅(PbS) 形态存在。
锌、铅化合物在处理过程中的变化
2、停窑操作
1)停窑前,先要把料仓内的料全部进完, 待窑内物料中的锌基本挥发完后,再抽出 风管,关钟罩阀,停止收尘。将窑密封起 来,让其自然冷却,以防窑内衬砖炸裂。 2)停料后,在窑内没有冷却下来之前,必 须继续转窑,当窑尾温度降到100℃以下, 方可停窑。
八、主要技术经济指标
2、其他注意事项 窑头回火 拆除窑砖 打粘帮
十、新技术应用
低温带整体浇筑技术 富氧的运用
锌直接回收率:92~95% 铅直接回收率:85~95% 窑生产能力:1.1~1.3t混合料/(m3· d) 窑渣含锌:<1.5% 窑渣含铅:0.5~0.7% 窑渣含碳:15~25% 窑渣率:64~68% 收尘效率:>99%
九、安全注意事项
1、 回转窑烘炉油枪使用安全注意事项
(1).油枪必须保证明火点燃。 (2)用油枪烘窑时,必须经常观察喷油及燃烧情况,保证油的正常燃烧。 如出现油灭火时,立即关闭油路阀门和油泵,防止发生爆炸。 (3)观察油枪燃烧情况时必须戴好口罩,要从观察孔侧面观察,不能正 对观察孔。 (4)出现回火现象时(风机停转、钟罩突然落下等造成),迅速离开窑 头罩观察孔、人孔门等位置,并关闭油泵,待处理好后,再按点油 枪作要求重新点火。 (5)使用油枪时,调整油、风阀门,确保油的充分燃烧,观察烟囱不能 冒黑烟。 (6)按升温曲线进行升温。
湿法炼锌浸出渣处理工艺研究
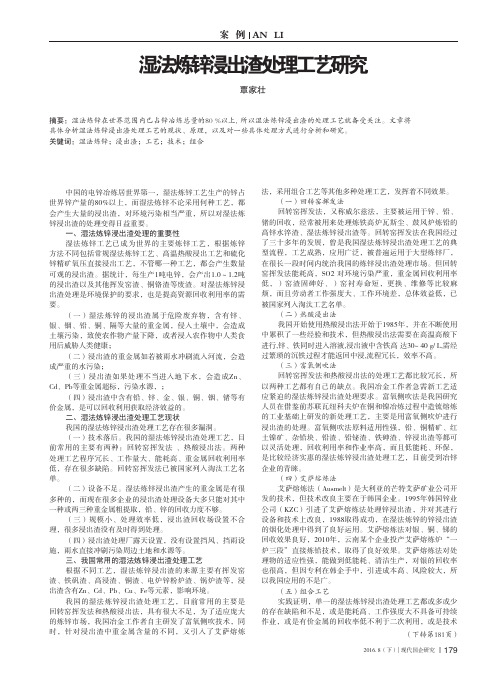
摘要:湿法炼锌在世界范围内已占锌冶炼总量的80 %以上, 所以湿法炼锌浸出渣的处理工艺就备受关注。
文章将具体分析湿法炼锌浸出渣处理工艺的现状、原理,以及对一些具体处理方式进行分析和研究。
关键词:湿法炼锌;浸出渣;工艺;技术;组合中国的电锌冶炼居世界第一,湿法炼锌工艺生产的锌占世界锌产量的80%以上,而湿法炼锌不论采用何种工艺,都会产生大量的浸出渣,对环境污染相当严重,所以对湿法炼锌浸出渣的处理变得日益重要。
一、湿法炼锌浸出渣处理的重要性湿法炼锌工艺已成为世界的主要炼锌工艺,根据炼锌方法不同包括常规湿法炼锌工艺、高温热酸浸出工艺和硫化锌精矿氧压直接浸出工艺,不管哪一种工艺,都会产生数量可观的浸出渣。
据统计,每生产1吨电锌,会产出1.0~1.2吨的浸出渣以及其他挥发窑渣、铜铬渣等废渣。
对湿法炼锌浸出渣处理是环境保护的要求,也是提高资源回收利用率的需要。
(一)湿法炼锌的浸出渣属于危险废弃物,含有锌、银、铟、铅、铜、隔等大量的重金属,侵入土壤中,会造成土壤污染,致使农作物产量下降,或者浸入农作物中人类食用后威胁人类健康;(二)浸出渣的重金属如若被雨水冲刷流入河流,会造成严重的水污染;(三)浸出渣如果处理不当进入地下水,会造成Zn、Cd、Pb等重金属超标,污染水源,;(四)浸出渣中含有铅、锌、金、银、铜、铟、锗等有价金属,是可以回收利用获取经济效益的。
二、湿法炼锌浸出渣处理工艺现状我国的湿法炼锌浸出渣处理工艺存在很多漏洞。
(一)技术落后。
我国的湿法炼锌浸出渣处理工艺,目前常用的主要有两种:回转窑挥发法 、热酸浸出法。
两种处理工艺程序冗长、工作量大、能耗高、重金属回收利用率低,存在很多缺陷。
回转窑挥发法已被国家列入淘汰工艺名单。
(二)设备不足。
湿法炼锌浸出渣产生的重金属是有很多种的,而现在很多企业的浸出渣处理设备大多只能对其中一种或两三种重金属粗提取,铅、锌的回收力度不够。
(三)规模小、处理效率低,浸出渣回收场设置不合理,很多浸出渣没有及时得到处理。
底吹炉处理锌浸出渣工艺设想
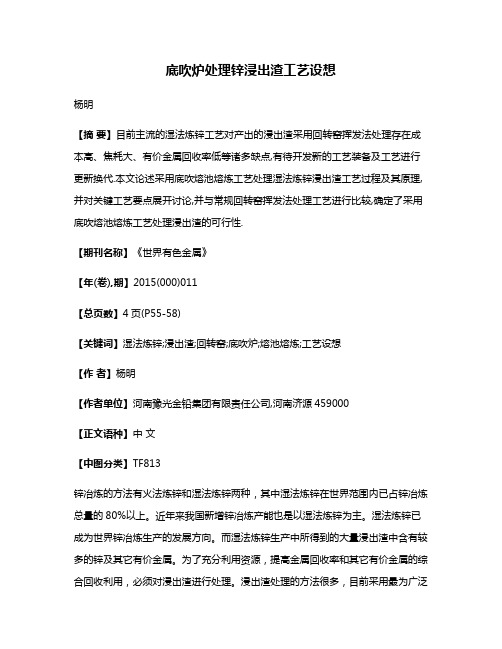
底吹炉处理锌浸出渣工艺设想杨明【摘要】目前主流的湿法炼锌工艺对产出的浸出渣采用回转窑挥发法处理存在成本高、焦耗大、有价金属回收率低等诸多缺点,有待开发新的工艺装备及工艺进行更新换代.本文论述采用底吹熔池熔炼工艺处理湿法炼锌浸出渣工艺过程及其原理,并对关键工艺要点展开讨论,并与常规回转窑挥发法处理工艺进行比较,确定了采用底吹熔池熔炼工艺处理浸出渣的可行性.【期刊名称】《世界有色金属》【年(卷),期】2015(000)011【总页数】4页(P55-58)【关键词】湿法炼锌;浸出渣;回转窑;底吹炉;熔池熔炼;工艺设想【作者】杨明【作者单位】河南豫光金铅集团有限责任公司,河南济源459000【正文语种】中文【中图分类】TF813锌冶炼的方法有火法炼锌和湿法炼锌两种,其中湿法炼锌在世界范围内已占锌冶炼总量的80%以上。
近年来我国新增锌冶炼产能也是以湿法炼锌为主。
湿法炼锌已成为世界锌冶炼生产的发展方向。
而湿法炼锌生产中所得到的大量浸出渣中含有较多的锌及其它有价金属。
为了充分利用资源,提高金属回收率和其它有价金属的综合回收利用,必须对浸出渣进行处理。
浸出渣处理的方法很多,目前采用最为广泛的是回转窑挥发法,该法处理存在成本高、焦耗大、有价金属回收率低等诸多缺点,有待开发新的工艺装备及工艺进行更新换代。
1.1 锌浸出渣来源某电锌生产厂设计产能20万t/a,采用典型的“焙烧—浸出—电积—铸型”湿法炼锌工艺生产。
在这种常规湿法炼锌流程中,焙砂中几乎全部的铅、金、银、铟、锗、镓,60%的铜、30%的镉、15%的锌都进入浸出渣中。
锌精矿的锌品位处于47.5%~49%之间,按每生产1t电锌可以产出1.0~1.05t浸出渣,电锌产能20万t/a规模,则每年产出浸出渣约为20~21万t。
1.2 浸出渣的成份及属性锌浸出渣的化学组成和锌物相组成分别见表1和表2。
从分析结果可知,锌浸出渣中锌的含量较高,并含有Pb、Cu、Fe、Au、Ag等有价金属与贵金属。
浅谈回转窑法处理锌浸出渣工艺中燃料对生产的影响
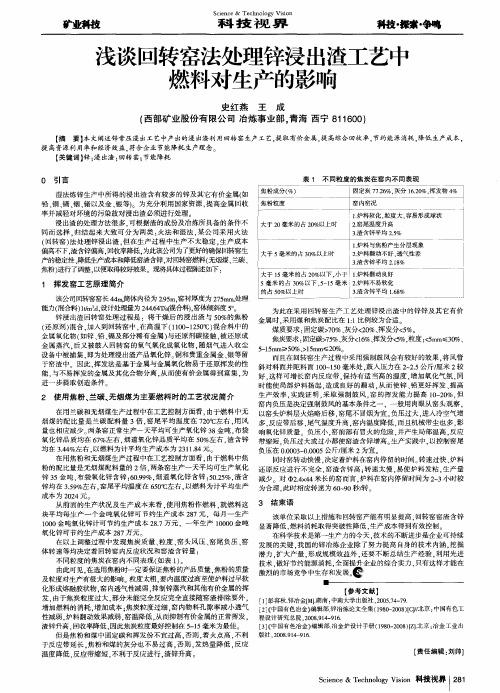
表 1 不同粒 度的焦炭在窑 内不同表现
固定炭 7 7 . 2 6 %. 灰分 1 6 2 0 %. 挥发物 4 %
窑 内窑况
湿法炼 锌生产 中所得 的浸 出渣含有较多 的锌及其 它有 价金属f 如 铅、 铜、 镉、 铟、 锗 以及金 、 银等) 。为充分利用 国家资源 , 提高金属 回收 焦粉粒度 率并 减轻对 环境的污染故对 浸出渣必须进 行处 理。 浸 出渣 的处理方法很 多. 可根据渣 的成份及冶炼所具备 的条件不 大于 2 0 毫米 的占 2 0 %以上时 同而选择 . 归结起 来大致 可分为 两类 : 火 法和湿 法 , 某公 司采用 火法 ( 回转窑 ) 法处理锌浸 出渣 . 但在生产 过程 中生产 不太稳定 , 生产成本 偏高不下 。 渣含锌偏高 . 回收率降低, 为此 该公司为了更好的确保回转窑生 大于 5毫米的 占 3 0 %1 ) 2 上时 产的稳定性、 降低生产或 本和降低窑渣含锌. 对回转窑燃料( 无烟煤、 兰碳 、 焦粉) 进行了调整 . 以便取得较好效果。现将具体过程陈述如下 :
【 摘 要】 本 文阐述锌 常压浸 出工艺中产出的浸出渣利用回转窑生产工艺, 提取有价金属 , 提 高综合回收率 , 节约能源消耗 , 降低 生产成本
提 高资源利 用率和经济效益, 符合企业节能降耗生产理念 。
锌浸出渣回转窑富氧烟化工艺研究
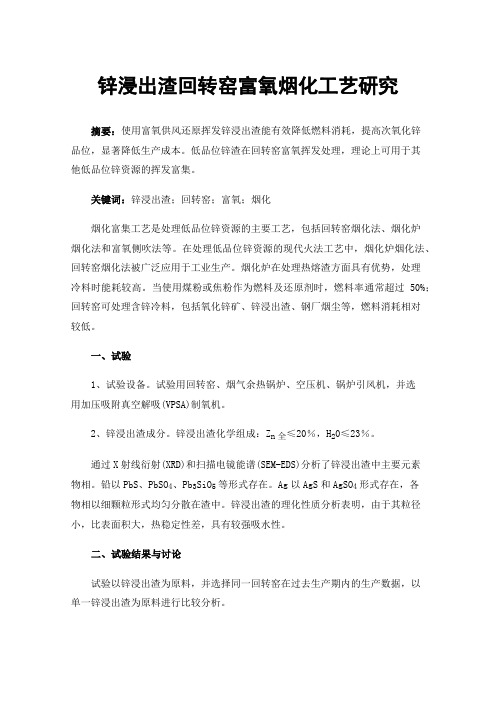
锌浸出渣回转窑富氧烟化工艺研究摘要:使用富氧供风还原挥发锌浸出渣能有效降低燃料消耗,提高次氧化锌品位,显著降低生产成本。
低品位锌渣在回转窑富氧挥发处理,理论上可用于其他低品位锌资源的挥发富集。
关键词:锌浸出渣;回转窑;富氧;烟化烟化富集工艺是处理低品位锌资源的主要工艺,包括回转窑烟化法、烟化炉烟化法和富氧侧吹法等。
在处理低品位锌资源的现代火法工艺中,烟化炉烟化法、回转窑烟化法被广泛应用于工业生产。
烟化炉在处理热熔渣方面具有优势,处理冷料时能耗较高。
当使用煤粉或焦粉作为燃料及还原剂时,燃料率通常超过50%;回转窑可处理含锌冷料,包括氧化锌矿、锌浸出渣、钢厂烟尘等,燃料消耗相对较低。
一、试验1、试验设备。
试验用回转窑、烟气余热锅炉、空压机、锅炉引风机,并选用加压吸附真空解吸(VPSA)制氧机。
2、锌浸出渣成分。
锌浸出渣化学组成:Z n全≤20%,H20≤23%。
通过X射线衍射(XRD)和扫描电镜能谱(SEM-EDS)分析了锌浸出渣中主要元素物相。
铅以PbS、PbSO4、Pb3SiO5等形式存在。
Ag以AgS和AgSO4形式存在,各物相以细颗粒形式均匀分散在渣中。
锌浸出渣的理化性质分析表明,由于其粒径小,比表面积大,热稳定性差,具有较强吸水性。
二、试验结果与讨论试验以锌浸出渣为原料,并选择同一回转窑在过去生产期内的生产数据,以单一锌浸出渣为原料进行比较分析。
1、氧浓度对锌回收率的影响。
在不改变原料和燃料性质及燃料配比情况下,将回转窑供风氧浓度分别调整为24±0.5%、26±0.5%、29±0.5%。
受限于制氧设备产能,未在较高氧浓度下对生产进行试验。
试验运行条件为:回转窑转速2.5~3min,鼓风压力150~160kPa,抽风压力48~49kPa;混合料投入量约250t/d。
随着供风氧浓度的增加,产品次氧化锌中的锌含量增加。
可解释为:随着鼓入空气中氧含量的增加,鼓风量减少,烟气流速降低,烟气带入烟尘中的生料减少,从而增加了次氧化锌的锌含量。
锌浸出渣的处理
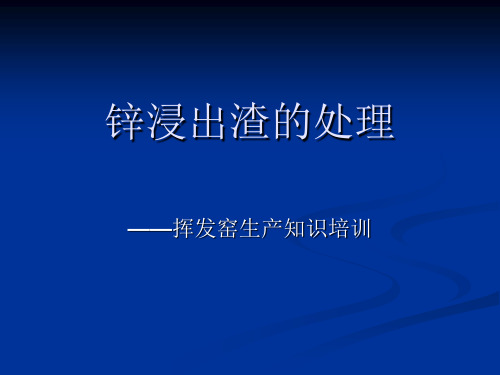
4、窑身转动 窑身的转速对于炉料在窑内停留时间,反 应速度及反应的完成程度有很大影响。转 速太大,炉料在窑内停留时间短,虽然翻 动良好,但反应不完全,渣含锌升高。转 速太慢,炉料在窑内停留时间长,焦粉 (无烟煤)燃烧完全,但处理量低。一般 来说,炉料在窑内的停留时间为2~3h, 窑身转速在60~120s/r。
注意!
硫化铅可与其他金属硫化物形成底熔点冰 铜,PbO与SiO2形成底熔点硅酸铅。所以, 当炉料中含PbS过高时,产生的金属铅、冰 铜、底熔点硅酸盐,由于其渗透力很强, 会渗入窑衬而侵蚀炉衬,当其聚集时使炉 料形成炉结,阻碍锌、铅的挥发,恶化操 作等。因此,应当在配料时配加更多的焦 粉(碎煤),以吸收溶体产物。另外采用 强制鼓风、延长高温区,提高废气出口温 度,也有利于铅、锌的挥发,减少熔渣。
硫酸铅:
铅在浸出渣中大部分以硫酸铅形态存在, 也有少量的硫化铅、氧化铅及硅酸铅。硫 酸铅在窑内被还原成硫化铅,氧化铅被还 原成金属铅,硫酸铅、硫化铅和氧化铅也 可能进行交互反应形成金属铅: PbSO4+PbS=2Pb+SO2 PbS+2PbO=3Pb+SO2 过程中不论PbS、PbO还是Pb都能挥发,且 以PbS、PbO挥发为主。
铁酸锌:由于锌精矿中含有较多的铁,在焙烧是形成铁 酸锌。在常规浸出条件下,铁酸锌几乎不溶解而残留在 渣中,约占渣含锌量的50~60%,它在窑内发生的反应: 3(ZnO· Fe2O3)+C=2 Fe3O4+3ZnO+CO ZnO· Fe2O3+ CO= ZnO+2 FeO+CO2 ZnO+ CO=Zn+CO2 当窑内温度在1050℃以上时,上述反应进行很快, 且有部分氧化铁被还原为金属铁,促使氧化锌的还原。 ZnO+Fe=Zn(气)+FeO ZnO· Fe2O3+Fe=Zn(气)+4FeO
锌冶炼浸出渣资源化回收工艺分析

锌冶炼浸出渣资源化回收工艺分析谈应飞;王浩宇【摘要】本文简要介绍目前国内外锌浸出渣处理工艺,对比挥发窑工艺与烟化炉工艺、Ausmelt法工艺的投资、成本、金属回收率、工艺成熟性等方面的对比分析,为提高锌冶炼浸出渣综合回收效益最大化提供依据.【期刊名称】《世界有色金属》【年(卷),期】2016(000)010【总页数】2页(P79-80)【关键词】锌冶炼;资源化;处理工艺【作者】谈应飞;王浩宇【作者单位】株洲冶炼集团股份有限公司,湖南株洲412000;株洲冶炼集团股份有限公司,湖南株洲412000【正文语种】中文【中图分类】X820.4湿法炼锌工艺中,锌系统采用沸腾炉-常规浸出(部分高温高酸浸出)工艺,常规法锌浸出渣含锌一般在17~20%左右、含铅5%左右、含铜0.6%左右、含铟250~350g/t、银80~120g/t,具有很好的资源价值和经济价值。
目前处理锌浸出渣主要有两个目的:①使锌浸出渣无害化,避免其中的硫酸根离子和重金属离子进入地表土壤和水体而造成环境污染;②回收其中的有价金属如铅、锌、金、银、铜、铟、锗等,最大限度地提高资源的综合利用水平[1]。
锌浸出渣火法处理方法很多种:回转窑法、烟化炉法、Ausmelt法、Kivcet搭配处理法、富氧侧吹法、电热法、硫酸化焙烧法、氯化硫酸焙烧法、旋涡炉熔炼法等。
目前几种工业化应用相对广泛的工艺有回转窑法、烟化炉法、Ausmelt法等三种方法[2]。
2.1 行业挥发窑生产成本分析降低挥发窑生产成本主要集中在两个方面:一是提高挥发窑作业率和作业效率;二是通过工艺优化和设计改造,降低渣的燃料单耗,近年来同行业挥发窑逐步开始使用富氧熔炼技术,使用效果也有差异。
表1为同行业挥发窑生产成本分析。
从表1分析可知,目前处理浸出渣的挥发窑燃料成本控制400~700之间,其差异比较大。
个别企业使用物料有差别,其成本很低只有200~300元/t,目前处理浸出渣的挥发窑主要以使用筛下焦和焦米为主,这与浸出渣特性有关,富氧技术仍然还有探索的过程。
锌冶炼渣综合利用与节能减排的工艺解析
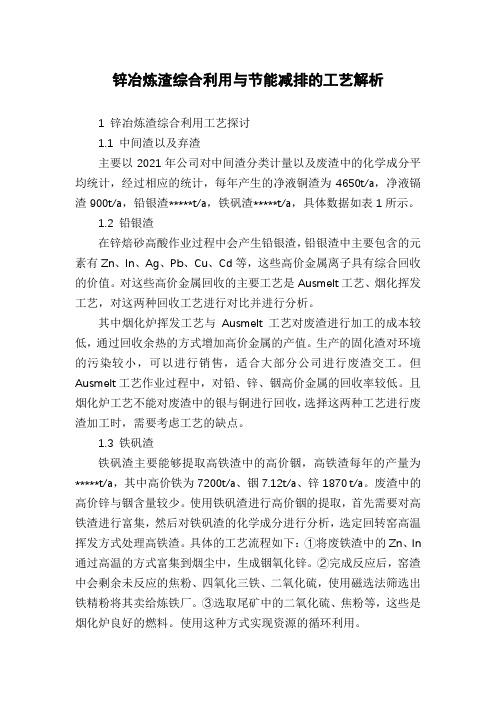
锌冶炼渣综合利用与节能减排的工艺解析1 锌冶炼渣综合利用工艺探讨1.1 中间渣以及弃渣主要以2021年公司对中间渣分类计量以及废渣中的化学成分平均统计,经过相应的统计,每年产生的净液铜渣为4650t/a,净液镉渣900t/a,铅银渣*****t/a,铁矾渣*****t/a,具体数据如表1所示。
1.2 铅银渣在锌焙砂高酸作业过程中会产生铅银渣,铅银渣中主要包含的元素有Zn、In、Ag、Pb、Cu、Cd等,这些高价金属离子具有综合回收的价值。
对这些高价金属回收的主要工艺是Ausmelt工艺、烟化挥发工艺,对这两种回收工艺进行对比并进行分析。
其中烟化炉挥发工艺与Ausmelt工艺对废渣进行加工的成本较低,通过回收余热的方式增加高价金属的产值。
生产的固化渣对环境的污染较小,可以进行销售,适合大部分公司进行废渣交工。
但Ausmelt工艺作业过程中,对铅、锌、铟高价金属的回收率较低。
且烟化炉工艺不能对废渣中的银与铜进行回收,选择这两种工艺进行废渣加工时,需要考虑工艺的缺点。
1.3 铁矾渣铁矾渣主要能够提取高铁渣中的高价铟,高铁渣每年的产量为*****t/a,其中高价铁为7200t/a、铟7.12t/a、锌1870 t/a。
废渣中的高价锌与铟含量较少。
使用铁矾渣进行高价铟的提取,首先需要对高铁渣进行富集,然后对铁矾渣的化学成分进行分析,选定回转窑高温挥发方式处理高铁渣。
具体的工艺流程如下:①将废铁渣中的Zn、In 通过高温的方式富集到烟尘中,生成铟氧化锌。
②完成反应后,窑渣中会剩余未反应的焦粉、四氧化三铁、二氧化硫,使用磁选法筛选出铁精粉将其卖给炼铁厂。
③选取尾矿中的二氧化硫、焦粉等,这些是烟化炉良好的燃料。
使用这种方式实现资源的循环利用。
1.4 铜镉钴渣铜镉钴渣是Cu、Cd、Co的富集物,通过净液渣经置换得到净液镉渣混合物。
我国每年产生的净液铜渣为4690t/a,净液镉渣为900t/a。
其中主要包含铜离子1100t/a,锌离子1090t/a,一氧化碳40t/a。
锌浸出渣挥发窑系统设备的优化
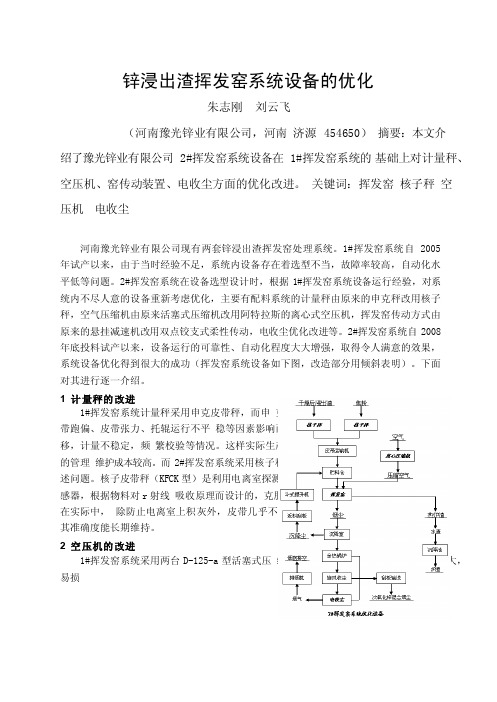
锌浸出渣挥发窑系统设备的优化朱志刚刘云飞(河南豫光锌业有限公司,河南济源454650)摘要:本文介绍了豫光锌业有限公司 2#挥发窑系统设备在 1#挥发窑系统的基础上对计量秤、空压机、窑传动装置、电收尘方面的优化改进。
关键词:挥发窑核子秤空压机电收尘河南豫光锌业有限公司现有两套锌浸出渣挥发窑处理系统。
1#挥发窑系统自2005年试产以来,由于当时经验不足,系统内设备存在着选型不当,故障率较高,自动化水平低等问题。
2#挥发窑系统在设备选型设计时,根据 1#挥发窑系统设备运行经验,对系统内不尽人意的设备重新考虑优化,主要有配料系统的计量秤由原来的申克秤改用核子秤,空气压缩机由原来活塞式压缩机改用阿特拉斯的离心式空压机,挥发窑传动方式由原来的悬挂减速机改用双点铰支式柔性传动,电收尘优化改进等。
2#挥发窑系统自 2008年底投料试产以来,设备运行的可靠性、自动化程度大大增强,取得令人满意的效果,系统设备优化得到很大的成功(挥发窑系统设备如下图,改造部分用倾斜表明)。
下面对其进行逐一介绍。
1 计量秤的改进1#挥发窑系统计量秤采用申克皮带秤,而申克秤常由于皮带跑偏、皮带张力、托辊运行不平稳等因素影响而造成零点飘移,计量不稳定,频繁校验等情况。
这样实际生产中,申克秤的管理维护成本较高。
而 2#挥发窑系统采用核子秤却能克服上述问题。
核子皮带秤(KFCK 型)是利用电离室探测器作为称重传感器,根据物料对r 射线吸收原理而设计的,克服了上述缺点,在实际中,除防止电离室上积灰外,皮带几乎不需要进行维护,其准确度能长期维持。
2 空压机的改进1#挥发窑系统采用两台D-125-a 型活塞式压缩机,存在结构复杂笨重,震动和噪音大,易损件较多,维修量大,日常维护成本较高等缺点。
而在 2#挥发窑系统从国外引进先进的ZH7000 型离心式压缩机。
该压缩机采用先进的机组整体化设计, 机内内置进口空气过滤器、放空阀、放空消音器和进口导叶等, 采用无基础安装方式, 大大降低占地面积;电机功率从原来的550kW 改为现在450kW,功率消耗少;采用功能强大的PLC 控制器, 对压缩机的运行进行全面的监控和保护。
- 1、下载文档前请自行甄别文档内容的完整性,平台不提供额外的编辑、内容补充、找答案等附加服务。
- 2、"仅部分预览"的文档,不可在线预览部分如存在完整性等问题,可反馈申请退款(可完整预览的文档不适用该条件!)。
- 3、如文档侵犯您的权益,请联系客服反馈,我们会尽快为您处理(人工客服工作时间:9:00-18:30)。
烟尘
窑渣
图 1 挥发窑生产工艺流程示意图
5 5一 5 9. 8 6一 1 2
Z F n P C b e u 4. 36
A C ‘ s S b
0. 3 42 0. 2 54
A S 2 S g G a i C O I d n
F2 3 O=2 e e +C 0 FO+C q F O+C e O=F +C 2 e 0 Z O+F =Z 个+FO n e n e
生产实践中, 锌精矿品位处于 4.%-4%之间, 75 9 每生产I电锌可以产出 10 10t t .- 5浸出渣, . 以一 个年产 1 万t 0 的炼锌厂来计, 则一年产出浸出渣约 为1- 05 , 挥发窑系统回收锌金属量大 0 1.万t 其中 致为 17 o .万t
图 2 改进后的挥发窑生产工艺流程示意图
表 5 国内某炼锌厂不同规格挥发窑 余热锅炉的烟气条件和工作参数
挥发窑规格 余热锅炉烟气条件
0 . x m 6 8 5 似 . x m X . x m 4 4 4 2 9 2 5
4 5
2. 5 7
2. 5 7
4 4
2.4 4 230
2. 9 3. 6
窑体长度, m 有效容积, 3 m
3 0
.
3 8
4 4
5 2 5 8 3 3 4 52 9
9 4 14 8
窑体斜度, %
31 挥发窑热平衡和工艺流程的改进 .
311 挥发窑的热平衡 ..
X.x 24 4 4m挥发窑热平衡表如表 4 所示。
锌浸出渣挥发窑生产工艺与节能—
易 文
表 4 4 4 P.x 4m挥发窑热平衡表( 测定周期:h 6)
热收入
项目
热支出
百分 比% 项目
数值 x U/ 1' h 0
7 0 7 2. 3 2 7 1 1
数值 x k/ 13 0 Jh
2 9 0 6 .7 642 68
3 9 5 7. 4 0 6 4 1 3 5 3. 5 4 2 9 1 3 5 7 3. 2 7 98 1
百分 比%
.6 2
9 2 1. 1 6
4. 2 2
『j 2 。 .. 卫 1 井 月 呀 . d. 弃 } 0 C 内J 2 。 4 n 0 。 r
PRODUCTI ON TECHNOLOGY AND ENERGY AVI S NG OF NC ZI LEACHI NG RES DUES OLATI I V LE LN KI
Yi e W n
( h zo S e e ) Z uhu l r m t y
A S R C T ippr lnd bi o te h i l c lo z c h g i e vli BT A T h ae ep i i rf h t n a pi ie i l ci r d s al s x a e n e n e c r p f e n e u o te c n n a s k n c s it dcd bs cn io o eeg cnu pi o vl i k n T ippr i poe ad r ue te i od i n ry sm t n o te . s e ao l r s n no h a c t n n o o f al i l h a l s ep r a y ip v t ee y i o vli k n Sm vl b sge i f ee y - xl e w t m r e nr s n f t i . e u l ugso o nr s o d a o o h e g a g o l l o a a e tn v a e r g a v i o vli kn e n f w r. n f t i hv be pt a g a l l a e u o d a e r
似. X 7 4m与 1 24 m的总和。焦率是指 5 4 台¥.X 4 4 10g 0k 干浸出渣所搭配的焦粉数量。一般炼锌厂焦
率维持在 5 %左右, 0 有些炼锌厂焦率虽然 只有
在80 00 0一10 元。因此, 节约能源在挥发窑的生产
实践中具有十分重要的意义, 有利于降低成本、 节约
资源。
1 2 4 4. 1 1 51 8 9
7
内‘
, 山
0 丹
窑体表面散热
其它 合计
8 0 85 5 9 2 3 0.
3 6 0 7. 3 82 1 8 8085 5 9 2 3 0.
合计
根据对挥发窑热平衡的测定数据表明, 烟气及
烟尘带走热占到整个体系热支出的 3%-4%, 0 0 挥 发窑窑尾温度可达 60 5r, 5 一70 热能资源十分丰 -
生的 10 -10℃高温条件下, 00- 30 - 浸出渣中锌、 铅、 锢、 锗等有价元素被一氧化碳还原进人烟气, 在烟气 中被氧化成氧化锌等氧化物随烟气离开挥发窑。挥 发窑内主要的化学反应如下: 在料层内 十 C q = C q
C2 0 +C=2 O C
锌浸出渣挥发窑生产工艺与节能—
易 文
1 1
锌浸出渣挥发窑生产工艺与节能
文 易
( 株洲冶炼厂)
摘 要 本文简述了锌浸出渣挥发窑生产过程的工艺原理, 介绍了挥发窑能源消耗的基本状况, 并就挥发窑的节
能途径间题进行了探讨, 提出了挥发窑的节能措施。 关镶词 挥发回转窑 热平衡 余热 焦粉粒度
0. 5 15
34
.8l
0 17 .3
0. 4 7
0 0 6 2. 4 . 5 5
0. 5 2 3 0 0. 5
2. 8 5
0. 2 0 2
2. 3一 2. 8
0. 6 78
0. 5 0 4
0. 2 8 09
2 0 4. 3 1. 2 8
0. 6 9 0. 0 1 0 1 0 6
表3 生产 1 吨氛化锌所消耗的能源费用( %)
能源品种 工序 I
工序 I
3 , 0 但另需增加重油或天然气或粉煤进行加热, 便
于窑温维持在 10 一100。随着窑体的大型化, 00 30 焦率也可适当提高到 5%一6 %. 5 0
电
1 3 6. 2
水
焦粉
煤气
13 .2
压缩空气
.
合计
10 0
2 9 9 4 . 7 . 6
4. 3 8 3 3 5. 6
3 挥发窑的节能
在挥发窑的生产过程中需要消耗大量能源, 如 电、 焦粉、 水、 重油、 压缩空气等。电主要用于驱动风 机、 水泵等各类传动机械设备; 水用于设备的冷却和
1 7 . 9 0 0. 1 1 0
焦率, % 温度, ℃ 窑衬材料
2 3 9.
3 3. 8 3 0
4 5一 5 5
另加重油
15 1 0一 1 0 3 0
另加重油
10 0一 1 0 3 0
10 1 0一 1 0 30
镁尖晶砖
镁砖、 高铝砖、 粘土砖
1 0 3 1 0 3 1 5 1 26 0
处理渣量, d t /
挥发回转窑的长度与内径的比值称为长径比。 从表2 中可知, 国内外长径比一般都在 1-2 之 3 0 间, 长径比若太小, 会造成窑尾温度升高, 窑的热效 率降低, 而长径比太大, 则窑尾温度低, 不利于生产。 在设计挥发回转窑时, 较多地考虑长径 比在 1 一 5 1。随着窑体内衬材料的改进、 8 电收尘工艺的完善 和窑体机械传动的改进, 回转窑更趋向于大型化, 如 表2 国内某厂 19 年投入生产的5 回转窑规格达 96 # 到帕. 8 , 日处理 浸出渣量相当于 2台 6X5m 其
冲窑渣; 焦粉主要作为燃料使用, 同时兼作还原剂; 重油则配合焦粉用于加热( 一些炼锌厂不用)压缩 ;
空气用于窑头的强制鼓风, 一是使窑尾产生负压, 二
是使窑内反映带增长, 三是将炉料吹起, 造成良 好的 翻动, 提高挥发能力, 一些炼锌厂在挥发窑工序单独 设立空压机站直接供给压缩空气, 另一些则由炼锌 厂统一供给压缩空气。表 3 为国内某炼锌厂挥发窑 IH I 工序生产 1 吨氧化锌所消耗能源费用。根据 有关资料, 挥发窑每生产 1 吨氧化锌, 能源费用一般
在料层上空 Z( + 2 2n 2n气) 0 = ZO
2 挥发窑生产工艺特性
21 生产原理与工艺流程 .
挥发窑生产原理: 在挥发回转窑内燃料燃烧产
2 O+ = C 2 C q 2O 挥发窑系统处理锌浸出渣时, 被处理的物料浸 出渣与焦粉混合均匀, 通过加料溜子进入到具有一 定倾斜度的回转窑内, 当窑体转动时, 炉料从一端翻 滚着流向另一端, 所加入燃料产生的高温炉气与物 料反向流动, 炉料中的金属氧化物与还原剂产生较 好的接触而被还原成蒸汽进入烟气中, 烟气通过冷 却、 收尘净化后, 气体排空, 氧化锌烟尘则回收利用.
富, 要达到烟气收尘的技术条件, 烟气温度须降到
含尘等多项因素。表 5 是国内某炼锌厂不同规格挥 发窑余热锅炉的烟气条件和工作参数。
30 0℃左右。对烟气的冷却多采用以下几种方法: 一 是直接使用烟气冷却器, 其缺点是不能有效利用烟 气的温差, 造成热能损失又污染环境; 二是出窑烟气
经过一定装置预热空气, 可返回到窑头作为强制鼓 风使用, 此法的缺点在于热效率低, 烟气的余热资源 利用不充分, 造成能源浪费; 三是在挥发窑尾端设 计、 建造余热锅炉, 其特点是可以提高热能利用率, 节约能源, 同时可为烟气的收尘创造良好条件。 焦粉在挥发窑内的燃烧是属于一种不完全燃
环境保护方面的问题并流失大量有价金属, 所以, 必
须对浸出渣进行适当处理以回收有价金属, 减轻环
境污染。根据复浸出工艺所得浸出渣成分和冶炼条 件的许可, 国内外许多炼锌厂选择传统的威尔兹法 处理浸出渣, 即通过挥发窑系统处理湿法炼锌的浸 出渣来回收锌、 锢、 铅、 锗等有价金属。在湿法炼锌