冲压模具设计及其工艺分析
冲压模具的设计与制造分析

冲压模具的设计与制造分析冲压模具是一种用于将金属板材或金属片材进行冲压加工的工具。
它由模具座、冲头、模座、定位销等部件组成,通过对材料施加压力来使材料发生变形,最终得到所需的产品。
冲压模具设计的目标是提高冲压产品的质量、生产效率和经济效益。
在进行冲压模具设计时,需要考虑以下几个方面:1. 产品材料的特性:不同材料具有不同的物理性质和加工特性,冲压模具的设计要根据产品材料的特性来确定合适的冲头形状、模具座结构和模座材料等。
2. 产品的结构形式:冲压产品的结构形式决定了模具的形状和加工工艺。
对于复杂的产品结构,需要设计多工位的冲压模具,以实现一次冲压完成多个工序。
3. 模具的寿命和耐用性:冲压模具在生产过程中需要承受高压力和频繁的运动,因此需要选择高硬度和高韧性的材料来制作模具,以提高模具的寿命和耐用性。
4. 模具的工艺性:冲压模具的设计要考虑到产品的成型精度和表面质量要求,确定合适的冲床和冲头尺寸,以及适当的冲压工艺参数。
在进行冲压模具制造时,需要进行以下分析和步骤:1. 材料选择和加工工艺的确定:根据冲压产品的要求和模具设计要求,选择合适的材料进行制造,并确定适当的加工工艺和工艺参数。
2. 模具结构的制造:根据模具设计要求,将模具座、冲头、模座等部件进行制造,并进行必要的热处理和表面处理。
3. 模具装配和调试:将各个部件进行装配,并进行必要的调试和检测,确保模具的稳定性和性能。
4. 模具使用和维护:在模具制造完成后,进行模具的使用和维护,定期进行润滑、清洁和检修,以延长模具的使用寿命。
冲压模具的设计和制造是一个复杂而重要的工作,需要综合考虑材料特性、产品结构形式、模具寿命和工艺性等方面的要求。
只有合理设计和制造冲压模具,才能实现高质量、高效益的冲压加工。
冲压工艺及模具设计
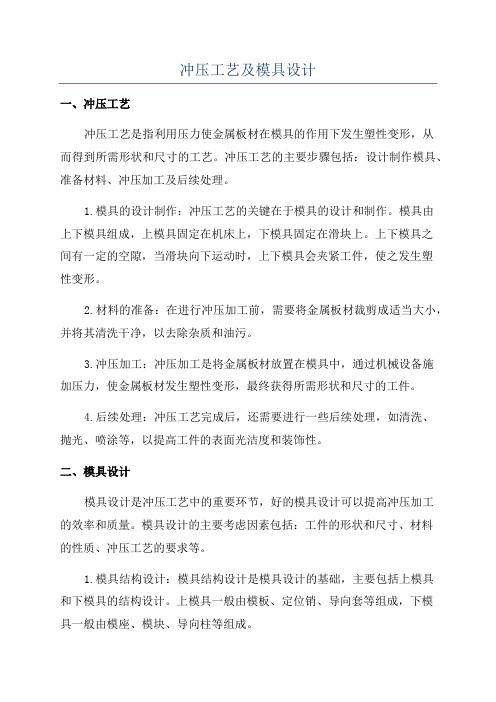
冲压工艺及模具设计一、冲压工艺冲压工艺是指利用压力使金属板材在模具的作用下发生塑性变形,从而得到所需形状和尺寸的工艺。
冲压工艺的主要步骤包括:设计制作模具、准备材料、冲压加工及后续处理。
1.模具的设计制作:冲压工艺的关键在于模具的设计和制作。
模具由上下模具组成,上模具固定在机床上,下模具固定在滑块上。
上下模具之间有一定的空隙,当滑块向下运动时,上下模具会夹紧工件,使之发生塑性变形。
2.材料的准备:在进行冲压加工前,需要将金属板材裁剪成适当大小,并将其清洗干净,以去除杂质和油污。
3.冲压加工:冲压加工是将金属板材放置在模具中,通过机械设备施加压力,使金属板材发生塑性变形,最终获得所需形状和尺寸的工件。
4.后续处理:冲压工艺完成后,还需要进行一些后续处理,如清洗、抛光、喷涂等,以提高工件的表面光洁度和装饰性。
二、模具设计模具设计是冲压工艺中的重要环节,好的模具设计可以提高冲压加工的效率和质量。
模具设计的主要考虑因素包括:工件的形状和尺寸、材料的性质、冲压工艺的要求等。
1.模具结构设计:模具结构设计是模具设计的基础,主要包括上模具和下模具的结构设计。
上模具一般由模板、定位销、导向套等组成,下模具一般由模座、模块、导向柱等组成。
2.模具材料选择:模具的材料选择直接影响到模具的使用寿命和加工质量。
一般情况下,模具材料应具有高硬度、高强度、良好的热导性和耐磨性等特性。
3.模具零件设计:模具零件的设计应考虑到工件的形状和尺寸,以及冲压工艺的要求。
模具零件的设计应尽量简化,减少加工难度,提高生产效率。
4.模具配合设计:模具零件之间的配合关系直接影响到模具的精度和稳定性。
模具配合设计应确保零件的定位准确、运动平稳,并充分考虑到热膨胀等因素。
综上所述,冲压工艺及模具设计是一项复杂的工程,它涉及到材料、结构、流程等多个方面。
通过合理的冲压工艺和精心的模具设计,可以实现高效、高质量的冲压加工,为生产制造提供有力支持。
冲压工艺及模具设计

冲压工艺及模具设计冲压工艺及模具设计是现代工业制造中常用的一种技术,它通过将金属板材或者其他形状的金属件置于模具中,然后通过冲压机的动作使得金属材料发生塑性变形以得到所需的形状和尺寸。
冲压工艺及模具设计是一门综合性强的工艺技术,以下将介绍其包括冲压工艺流程、模具设计原则、模具结构设计、模具构件选用等相关内容。
一、冲压工艺流程冲压工艺分为单道冲压和多道冲压两种。
单道冲压是指在一个冲压过程中完成产品的全体造型,多道冲压是指通过多次冲压工艺来完成产品的全体造型。
下面将以多道冲压为例介绍冲压工艺流程。
1.材料准备:选择合适的板材材料,进行剪切、铺料等准备工作。
2.模具设计:根据产品的形状和尺寸要求,设计合适的冲压模具。
3.上料:将材料板厚按照模具规格要求剪切成对应尺寸,然后放置在模具上。
4.开模:通过冲压机的动作,使得模具上的凸模与凹模对压,使材料发生塑性变形。
5.去杂及模具保养:在冲压过程中会产生一些杂质,需要及时清理,并对模具进行保养和维护。
二、模具设计原则模具设计是冲压工艺的核心环节,它直接影响着产品的质量和成本。
在进行模具设计时,需要遵循以下原则:1.合理性原则:模具结构要合理,能够满足产品的形状和尺寸要求,并且易于加工和调整。
2.稳定性原则:模具要具有足够的刚性和稳定性,能够承受冲压机的冲击力和振动。
3.高效原则:模具设计要考虑工作效率,设计出能够实现快速冲压的模具结构。
4.经济原则:模具的设计和制造成本要较低,以降低产品的制造成本。
三、模具结构设计模具的结构设计是模具设计的重要环节,它包括模具的整体结构、分段结构、导向结构等。
下面将介绍常用的模具结构设计方法:1.整体结构设计:将模具设计为一个整体结构,具有较好的刚性和稳定性。
2.分段结构设计:根据产品的形状和尺寸要求,将模具分为多个部分,通过连接件进行连接。
3.导向结构设计:模具需要具有良好的导向性,避免材料在冲压过程中发生歪斜和偏移。
4.其他辅助结构设计:模具还需要考虑各种辅助结构,如剪断边缘结构、定位结构、脱模结构等。
冲压模具工艺(3篇)
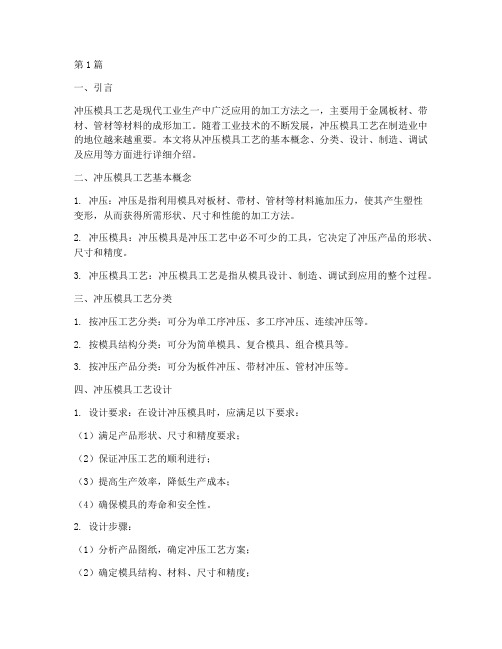
第1篇一、引言冲压模具工艺是现代工业生产中广泛应用的加工方法之一,主要用于金属板材、带材、管材等材料的成形加工。
随着工业技术的不断发展,冲压模具工艺在制造业中的地位越来越重要。
本文将从冲压模具工艺的基本概念、分类、设计、制造、调试及应用等方面进行详细介绍。
二、冲压模具工艺基本概念1. 冲压:冲压是指利用模具对板材、带材、管材等材料施加压力,使其产生塑性变形,从而获得所需形状、尺寸和性能的加工方法。
2. 冲压模具:冲压模具是冲压工艺中必不可少的工具,它决定了冲压产品的形状、尺寸和精度。
3. 冲压模具工艺:冲压模具工艺是指从模具设计、制造、调试到应用的整个过程。
三、冲压模具工艺分类1. 按冲压工艺分类:可分为单工序冲压、多工序冲压、连续冲压等。
2. 按模具结构分类:可分为简单模具、复合模具、组合模具等。
3. 按冲压产品分类:可分为板件冲压、带材冲压、管材冲压等。
四、冲压模具工艺设计1. 设计要求:在设计冲压模具时,应满足以下要求:(1)满足产品形状、尺寸和精度要求;(2)保证冲压工艺的顺利进行;(3)提高生产效率,降低生产成本;(4)确保模具的寿命和安全性。
2. 设计步骤:(1)分析产品图纸,确定冲压工艺方案;(2)确定模具结构、材料、尺寸和精度;(3)绘制模具装配图和零件图;(4)进行模具强度、刚度和耐久性计算。
五、冲压模具工艺制造1. 模具材料:模具材料应具有良好的耐磨性、耐冲击性、耐热性、耐腐蚀性等性能。
常用的模具材料有Cr12、Cr12MoV、CrWMn等。
2. 模具加工:模具加工主要包括以下步骤:(1)毛坯加工:根据模具图纸,加工出模具毛坯;(2)热处理:对模具毛坯进行热处理,提高其性能;(3)机械加工:对模具进行机械加工,达到图纸要求的尺寸和精度;(4)装配:将模具零件装配成完整的模具。
六、冲压模具工艺调试1. 调试目的:调试冲压模具的目的是使模具在正常生产条件下,达到规定的生产速度、精度和产品质量。
冲压模具设计及其工艺分析
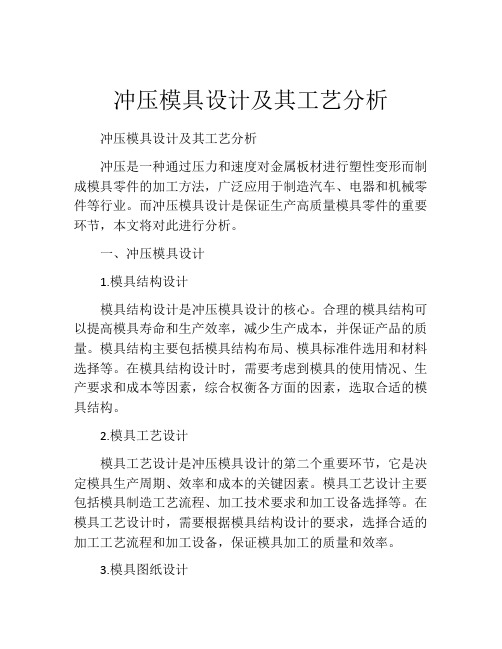
冲压模具设计及其工艺分析冲压模具设计及其工艺分析冲压是一种通过压力和速度对金属板材进行塑性变形而制成模具零件的加工方法,广泛应用于制造汽车、电器和机械零件等行业。
而冲压模具设计是保证生产高质量模具零件的重要环节,本文将对此进行分析。
一、冲压模具设计1.模具结构设计模具结构设计是冲压模具设计的核心。
合理的模具结构可以提高模具寿命和生产效率,减少生产成本,并保证产品的质量。
模具结构主要包括模具结构布局、模具标准件选用和材料选择等。
在模具结构设计时,需要考虑到模具的使用情况、生产要求和成本等因素,综合权衡各方面的因素,选取合适的模具结构。
2.模具工艺设计模具工艺设计是冲压模具设计的第二个重要环节,它是决定模具生产周期、效率和成本的关键因素。
模具工艺设计主要包括模具制造工艺流程、加工技术要求和加工设备选择等。
在模具工艺设计时,需要根据模具结构设计的要求,选择合适的加工工艺流程和加工设备,保证模具加工的质量和效率。
3.模具图纸设计模具图纸是冲压模具设计的具体内容,它包括三维图纸、二维图纸和工艺流程图等。
在模具图纸设计时,需要准确地表达模具的各种尺寸、形状和位置等信息,同时还需要表达模具加工工艺中的细节和要求,保证模具加工的准确性和一致性。
二、冲压模具工艺分析1.材料特性分析冲压模具制造材料的选择是影响模具品质和寿命的重要因素,而材料特性分析是选择模具材料的关键。
材料特性分析主要包括材料力学性能、耐磨性、韧性等方面的特性分析。
2.冲压工艺分析冲压工艺分析是决定模具加工周期、效率和成本的关键因素,它是确定冲压过程各环节的激励和反力,分析冲压过程中产生的变形和应力情况。
冲压工艺分析需要根据冲压模具的特性和材料特性、产品要求等综合考虑,选择合适的冲压工艺参数。
3.模具加工工艺分析模具加工工艺分析是决定模具加工成本和周期的重要因素,它是确定模具加工过程中加工工艺的某些细节和要求。
模具加工工艺分析需要根据模具结构和加工工艺的要求,选择合适的加工工艺流程和加工设备,保证模具加工的质量和效率。
冲压工艺及模具设计方案

冲压工艺及模具设计方案冲压工艺是一种常用的金属成形工艺,适用于大批量生产,具有高效、精确、稳定的特点。
模具是冲压工艺的核心部件,其设计方案直接影响产品的质量和生产效率。
本文将就冲压工艺及模具设计方案进行探讨。
一、冲压工艺分析冲压工艺的核心是模具设计,其主要过程包括:材料选择、冲剪线设计、工序计算、模具设计、模具制造和装配等。
在模具设计过程中,需要考虑产品的尺寸、形状、材料及生产批量等因素。
1.材料选择:根据产品的要求,选择适宜的材料进行冲压。
常见的材料有冷轧钢板、不锈钢板、铝板等。
材料的选择应考虑产品的应用环境、强度、耐磨性等因素。
2.冲剪线设计:冲剪线是产品的外形轮廓线,在模具设计中,需要绘制出产品的冲剪线。
冲剪线的设计应合理,保证产品的精度和质量。
3.工序计算:根据产品的结构和尺寸,进行工序计算。
工序计算主要包括模具开数、冲头设计、压力计算等。
通过合理的工序计算,可以提高生产效率和降低生产成本。
4.模具设计:模具设计是冲压工艺的核心。
在模具设计中,需要考虑产品的形状、尺寸、材料、模具材料、模具开数、冲头设计等因素。
模具设计应以满足产品要求为主要目标,同时考虑制造成本和交货周期。
5.模具制造和装配:根据模具设计方案进行模具制造和装配。
模具的制造应严格按照模具设计要求进行,保证模具的精度和质量。
模具装配时,需要注意各组件之间的配合和调试,确保模具能够正常运行。
在模具设计方案中,需要考虑以下几个方面:1.产品的形状和尺寸:根据产品的形状和尺寸,确定模具的结构和尺寸。
模具的结构应简单、合理,并能够满足产品的要求。
2.模具材料:模具的材料应具有良好的切削性能、硬度和耐磨性。
常见的模具材料有合金工具钢、硬质合金等。
模具的材料选择应根据产品的要求和生产批量来确定。
3.模具开数:模具开数是指一次生产中所需要的模具的数量。
模具开数的选择应根据产品的生产批量和生产效率来确定。
开数过多不利于模具制造和管理,开数过少会降低生产效率。
冲压模具的设计与制造分析
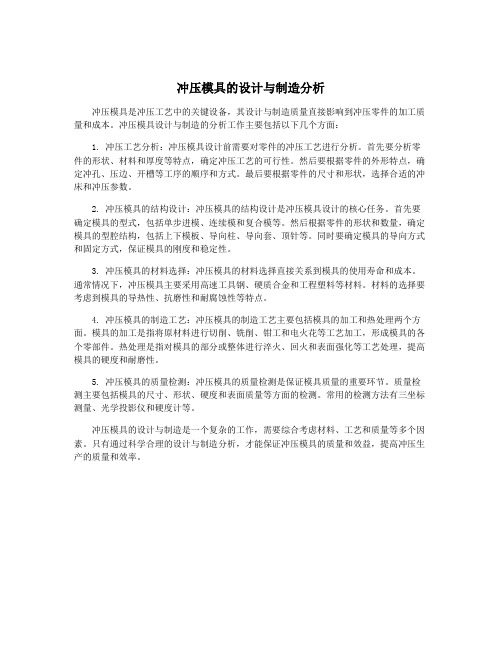
冲压模具的设计与制造分析冲压模具是冲压工艺中的关键设备,其设计与制造质量直接影响到冲压零件的加工质量和成本。
冲压模具设计与制造的分析工作主要包括以下几个方面:1. 冲压工艺分析:冲压模具设计前需要对零件的冲压工艺进行分析。
首先要分析零件的形状、材料和厚度等特点,确定冲压工艺的可行性。
然后要根据零件的外形特点,确定冲孔、压边、开槽等工序的顺序和方式。
最后要根据零件的尺寸和形状,选择合适的冲床和冲压参数。
2. 冲压模具的结构设计:冲压模具的结构设计是冲压模具设计的核心任务。
首先要确定模具的型式,包括单步进模、连续模和复合模等。
然后根据零件的形状和数量,确定模具的型腔结构,包括上下模板、导向柱、导向套、顶针等。
同时要确定模具的导向方式和固定方式,保证模具的刚度和稳定性。
3. 冲压模具的材料选择:冲压模具的材料选择直接关系到模具的使用寿命和成本。
通常情况下,冲压模具主要采用高速工具钢、硬质合金和工程塑料等材料。
材料的选择要考虑到模具的导热性、抗磨性和耐腐蚀性等特点。
4. 冲压模具的制造工艺:冲压模具的制造工艺主要包括模具的加工和热处理两个方面。
模具的加工是指将原材料进行切削、铣削、钳工和电火花等工艺加工,形成模具的各个零部件。
热处理是指对模具的部分或整体进行淬火、回火和表面强化等工艺处理,提高模具的硬度和耐磨性。
5. 冲压模具的质量检测:冲压模具的质量检测是保证模具质量的重要环节。
质量检测主要包括模具的尺寸、形状、硬度和表面质量等方面的检测。
常用的检测方法有三坐标测量、光学投影仪和硬度计等。
冲压模具的设计与制造是一个复杂的工作,需要综合考虑材料、工艺和质量等多个因素。
只有通过科学合理的设计与制造分析,才能保证冲压模具的质量和效益,提高冲压生产的质量和效率。
冲压模具的设计与制造分析

冲压模具的设计与制造分析冲压模具是用于金属冲压加工中的一种工艺设备,主要用于将金属板材通过冲压工艺加工成所需的形状和尺寸。
冲压模具的设计与制造分析是为了确保冲压过程的稳定性和产品质量的一项重要工作。
下面将对冲压模具的设计与制造分析进行详细介绍。
冲压模具的设计首先需要根据产品的尺寸和形状要求确定模具的结构形式,常见的有单工位模具、多工位模具和进模式模具等。
然后需要进行模具的布局设计和模具零件的选择。
模具的布局设计包括冲床的选择、上模槽和下模槽的位置安排、导向装置的设计等。
模具零件的选择包括上模、下模、模板、导向柱等零件的选择和设计。
冲压模具的制造分析主要包括模具材料的选择、模具结构强度分析和模具加工工艺的确定。
模具材料的选择需要考虑模具耐磨性、抗拉强度和导热性等因素,一般常用的模具材料有合金工具钢、硬质合金和工程塑料等。
模具结构强度分析是为了保证模具在冲压过程中不发生变形或损坏,需要进行有限元分析或计算强度校核。
模具加工工艺的确定需要根据模具结构和形状复杂程度进行加工工艺的选择,包括粗加工、热处理、精加工和装配等工艺。
冲压模具的设计与制造分析中还需要考虑模具的寿命和维修问题。
模具的寿命是指模具可以保持稳定工作状态的时间,直接影响到模具的经济效益。
模具维修是指在模具使用过程中出现的损坏或故障需要进行修复和维护,以延长模具的使用寿命和保证产品质量。
在设计和制造冲压模具时需要考虑模具的易维修性,合理布置模具的加工余量和保护装置,以便于模具的维修和保养。
冲压模具的设计与制造分析是一项复杂而重要的工作,需要综合考虑多个因素,包括模具的结构形式、材料选择、强度分析、加工工艺、寿命和维修等问题。
只有在设计和制造过程中充分考虑这些因素,才能保证模具的稳定性和产品质量。
冲压模具设计及其工艺分析
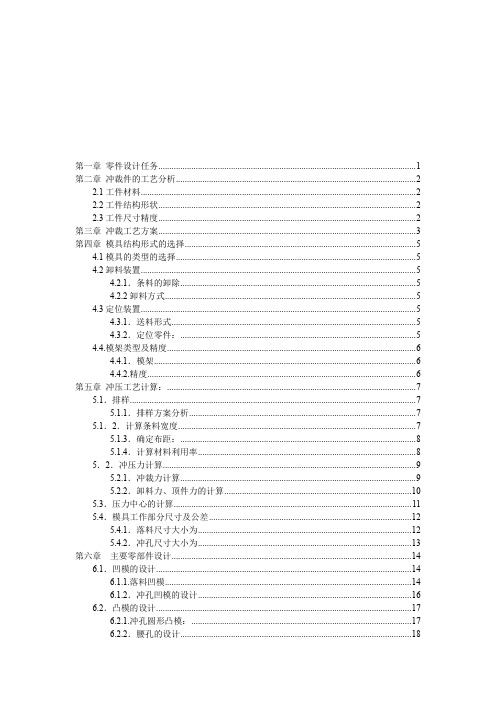
第一章零件设计任务 (1)第二章冲裁件的工艺分析 (2)2.1工件材料 (2)2.2工件结构形状 (2)2.3工件尺寸精度 (2)第三章冲裁工艺方案 (3)第四章模具结构形式的选择 (5)4.1模具的类型的选择 (5)4.2卸料装置 (5)4.2.1.条料的卸除 (5)4.2.2卸料方式 (5)4.3定位装置 (5)4.3.1.送料形式 (5)4.3.2.定位零件: (5)4.4.模架类型及精度 (6)4.4.1.模架 (6)4.4.2.精度 (6)第五章冲压工艺计算: (7)5.1.排样 (7)5.1.1.排样方案分析 (7)5.1.2.计算条料宽度 (7)5.1.3.确定布距: (8)5.1.4.计算材料利用率 (8)5.2.冲压力计算 (9)5.2.1.冲裁力计算 (9)5.2.2.卸料力、顶件力的计算 (10)5.3.压力中心的计算 (11)5.4.模具工作部分尺寸及公差 (12)5.4.1.落料尺寸大小为 (12)5.4.2.冲孔尺寸大小为 (13)第六章主要零部件设计 (14)6.1.凹模的设计 (14)6.1.1.落料凹模 (14)6.1.2.冲孔凹模的设计 (16)6.2.凸模的设计 (17)6.2.1.冲孔圆形凸模: (17)6.2.2.腰孔的设计 (18)6.2.3.落料凸模 (18)6.2.4.凸模的校核: (19)6.3.卸料板的设计 (20)6.4.固定板的设计 (21)6.4.1. 凹模固定板: (21)6.4.2.凸模固定板: (22)6.5.模架以及其他零部件的选用 (23)第7章校核模具闭合高度及压力机有关参数 (24)7.1 校核模具闭合高度 (24)7.2 冲压设备的选定 (24)第8章设计并绘制模具总装图及选取标准件 (25)第9章结论 (26)参考文献 (27)第一章零件设计任务零件简图:如图1-1 所示材料:10号钢材料厚度:2mm未标注尺寸按照IT10级处理.第二章冲裁件的工艺分析2.1工件材料由图1-1分析知:10#钢为优质碳素结构钢,具有良好的塑性性、焊接性以及压力加工性,主要用于制作冲击件、紧固件,如垫片、垫圈等。
冲压工艺与模具设计

冲压工艺与模具设计冲压工艺是一种通过对金属板材进行压制或冲剪,以改变其形状和尺寸的制造工艺。
在冲压过程中,需要使用模具来对金属板材施加确定的压力,使其发生塑性变形。
模具设计是冲压工艺的关键环节,合理的模具设计可以保证冲压过程的精度和效率。
一、金属材料的选择冲压工艺中常用的金属材料有钢板、铝板、铜板等。
不同金属材料的机械性能和加工性能不同,选择合适的金属材料对冲压工艺的成功至关重要。
二、冲压工艺的确定冲压工艺主要包括件的外形确定、孔位置的布置、切缘的设计等。
通过工艺确定,可以确定冲压工序的顺序、模具的需求以及操作要求。
三、模具设计要点1.模具结构的设计:模具结构设计要满足零件的加工要求,并在生产中方便拆卸、更换。
2.模具材料的选择:模具材料需要具有较高的硬度、强度和耐磨性,常用的模具材料有合金工具钢、硬质合金等。
3.模具配套设备的选择:根据冲压工艺的要求,选择合适的配套设备,如冲压机等。
4.压力分布的设计:模具在冲压过程中需要对板材施加一定的压力,合理的压力分布可以避免产生变形和裂纹。
5.模具的预紧力设计:预紧力是指模具在冲压过程中需承受的力量,需要合理设置预紧力以保证冲压过程的稳定性和精度。
6.附件的设计:模具附件是模具的辅助部件,如导向柱、定位销等,合理的设计可以提高模具的使用寿命和加工效率。
7.考虑模具的便于制造性和可维护性:在模具设计中,需要考虑到模具的制造难度和维护难度,合理的设计可以降低成本和提高效率。
总之,冲压工艺与模具设计是密不可分的,合理的模具设计可以保证冲压过程的精度和效率,最终提高产品的质量和生产效益。
在进行冲压工艺与模具设计时,需要考虑金属材料的选择、工艺的确定以及模具结构、材料等方面的要点。
只有全面考虑这些因素,才能设计出合理、高效的模具,实现优质的冲压加工。
冲压模具的设计与制造分析

冲压模具的设计与制造分析冲压模具是制造零部件的重要设备之一,其设计与制造直接影响着工件的质量和生产效率。
本文将从设计原则、制造工艺等方面进行分析,探讨冲压模具的设计与制造过程。
冲压模具的设计应遵循以下原则:1. 合理确定冲压工艺参数:冲压模具设计的第一步是确定冲压工艺参数,包括材料的特性、板料厚度、冲裁力等。
这些参数直接影响着冲压模具的结构和尺寸,因此必须合理确定。
2. 确定冲压工艺路线:根据工件的形状、尺寸和加工要求,确定最优的冲压工艺路线,包括冲裁次序、冲裁方式等。
这有助于降低模具的复杂性和加工难度,提高生产效率。
3. 优化模具结构:冲压模具的结构应简洁、紧凑,以减少材料的浪费和制造成本。
要考虑工件的加工难度和生产效率,合理设计模具的导向元件、定位元件等部件,保证模具的稳定性和精度。
4. 考虑模具的易制造性:在设计模具时,要充分考虑模具的制造工艺和加工设备的能力,合理确定模具的尺寸、精度和加工工艺,以确保模具能够顺利制造并具有良好的性能。
5. 重视模具的可维修性:冲压模具在使用过程中可能会出现磨损、损坏等情况,因此设计时应考虑模具的可维修性。
要合理选择材料、加工工艺和装配方式,以便方便维修和更换模具的损坏部件。
冲压模具的制造主要包括以下几个步骤:1. 材料选择和准备:根据模具的要求和使用条件,选择合适的模具材料,一般为工具钢或高速钢。
材料的准备包括切割、锻造、热处理等工艺,以获得合适的模具坯料。
2. 基础件的加工:冲压模具的基础件包括模板、模架、模座等,它们的加工主要包括铣削、钻孔、车削等工艺。
这些基础件的加工精度直接影响着模具的精度和稳定性。
3. 零部件的制造:冲压模具的零部件包括导向元件、定位元件、护套、松套等,它们的制造主要包括车削、铣削、磨削等工艺。
这些零部件必须具备良好的加工精度和表面质量,以保证模具的准确性和稳定性。
4. 模具的装配和调试:在模具制造完成后,将各个零部件组装在一起,进行精确的定位和调试。
冲压模具的设计与制造分析

冲压模具的设计与制造分析随着工业的发展和技术的提升,冲压模具的应用越来越广泛,是现代制造业中不可缺少的一部分。
因此,对冲压模具的设计和制造分析具有重要的意义。
下面将对冲压模具的设计和制造分析进行探讨。
1.1 冲压模具的结构设计冲压模具结构设计的主要目的是确保模具精度、强度和耐用性。
模具应尽可能简洁,零件数目较少,这样有利于降低制造成本,并有助于维护和修理。
根据压力等级的不同,冲压模具的结构类型包括单站模、多站模、复合模等。
冲压模具的材料应具有高强度、高硬度、高耐磨性能和较好的加工性能。
主要有工具钢、硬质合金和陶瓷等材料。
其中,工具钢是目前应用最广泛的材料,而硬质合金和陶瓷等材料主要用于高精度、高效率、高要求的冲压模具。
冲压模具的设计程序一般包括产品设计、模具设计、零件加工、组装和调整等步骤。
设计人员需要了解冲压件的形状、大小、性质等信息,进行分析和计算,确定模具的结构和尺寸,绘制图纸和进行仿真分析等。
2.1 冲压模具制造工艺冲压模具的制造工艺主要包括材料处理、零件加工、组装和调整等。
为确保模具精度和质量,制造过程需要经过多道工序,从零件加工到组装,每个步骤都需要严格的质量控制。
冲压模具的制造技术包括铣削、电火花加工、线切割、抛光等,其中最主要的技术为数控加工技术。
数控加工技术可以大大提高加工精度和效率,并且可以在不同阶段实现自动化控制。
综上所述,冲压模具的设计和制造是一项极为复杂的工作,需要设计人员和制造人员具备一定的专业知识和技能,加之开发新产品的需求与对生产效率和商品质量不断提高的要求,冲压模具的应用领域将会越来越广泛,冲压模具制造业还有很大发展的潜力。
冲压模具的设计与制造分析

冲压模具的设计与制造分析冲压成型技术是一种高效的制造工艺,广泛应用于汽车、机械、电子等领域。
而冲压模具的设计和制造直接影响冲压零件的质量和效率。
本文将对冲压模具的设计与制造进行分析。
一、冲压模具的工作原理冲压模具是一种利用冲压机械对金属材料进行冲压成型加工的工具,在其工作中,需要通过模具的几何形状将金属材料切割、冲孔、弯曲、拉伸等加工操作。
冲压模具通常包括上模板、下模板、模具座、弹性元件、导向机构、排屑器、润滑系统等组成部分。
其中,上模板和下模板通过模具座进行固定,模具座上设置弹性元件和导向机构,以保持上下模板的位置准确。
排屑器则用于清理冲压时产生的废料,润滑系统则用于减小模具零件之间的磨损。
1.冲压件形状的确定冲压件的形状通常是按所需要的功能和前后工艺进行设计的。
模具的设计需要根据冲压件的形状进行模拟,并根据模拟结果进行模具结构的优化。
在模具的设计过程中,需要考虑材料的加工性能,包括抗拉、抗压强度、塑性变形等因素。
2.材料的选择模具制造材料常用的有工具钢、高速钢、硬质合金、大形高温合金等多种材料。
在选择材料时,需要综合考虑材料的耐磨、硬度、导热性、抗应力和耐腐蚀等性能,以符合模具的使用条件。
3.模具的结构设计冲压模具的结构设计需要保证其刚度和稳定性。
一般来说,模具的刚度越高,其工作效率和生产能力越高,质量也越稳定。
同时,在模具的设计中,还需要考虑模具的导向和平衡机构、夹持、位置检测等方面的问题,以确保模具配合的精度和生产效率。
在冲压模具制造过程中,需要选择高质量的合金钢材料才能确保其准确和稳定性。
一些高端模具通常使用精密或工作钢材料,如硬质合金和高速钢等。
在选择制造工艺的过程中,需要考虑到模具的材质、形状及制造要求等因素。
例如,钳工加工工艺及CNC加工工艺通常用于简单模具的生产,而走丝加工工艺或电火花加工则用于制造复杂模具的部分。
3.制造工艺的优化为了保证冲压模具的质量和生产效率,需要在制造过程中对工艺进行优化。
冲压模具的设计与制造分析
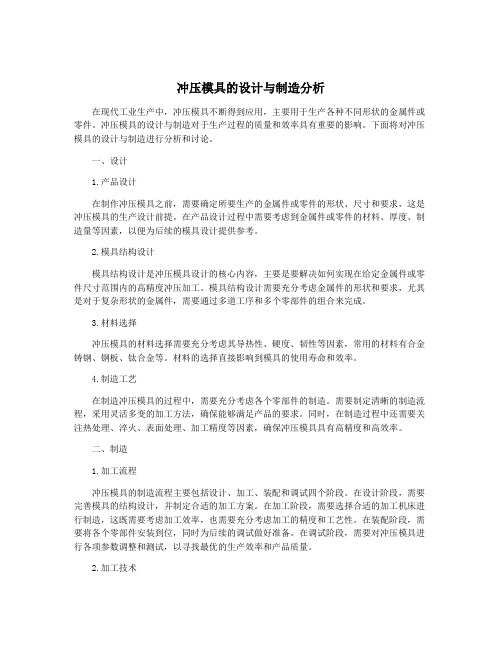
冲压模具的设计与制造分析在现代工业生产中,冲压模具不断得到应用,主要用于生产各种不同形状的金属件或零件。
冲压模具的设计与制造对于生产过程的质量和效率具有重要的影响。
下面将对冲压模具的设计与制造进行分析和讨论。
一、设计1.产品设计在制作冲压模具之前,需要确定所要生产的金属件或零件的形状、尺寸和要求,这是冲压模具的生产设计前提。
在产品设计过程中需要考虑到金属件或零件的材料、厚度、制造量等因素,以便为后续的模具设计提供参考。
2.模具结构设计模具结构设计是冲压模具设计的核心内容,主要是要解决如何实现在给定金属件或零件尺寸范围内的高精度冲压加工。
模具结构设计需要充分考虑金属件的形状和要求,尤其是对于复杂形状的金属件,需要通过多道工序和多个零部件的组合来完成。
3.材料选择冲压模具的材料选择需要充分考虑其导热性、硬度、韧性等因素,常用的材料有合金铸钢、钢板、钛合金等。
材料的选择直接影响到模具的使用寿命和效率。
4.制造工艺在制造冲压模具的过程中,需要充分考虑各个零部件的制造。
需要制定清晰的制造流程,采用灵活多变的加工方法,确保能够满足产品的要求。
同时,在制造过程中还需要关注热处理、淬火、表面处理、加工精度等因素,确保冲压模具具有高精度和高效率。
二、制造1.加工流程冲压模具的制造流程主要包括设计、加工、装配和调试四个阶段。
在设计阶段,需要完善模具的结构设计,并制定合适的加工方案。
在加工阶段,需要选择合适的加工机床进行制造,这既需要考虑加工效率,也需要充分考虑加工的精度和工艺性。
在装配阶段,需要将各个零部件安装到位,同时为后续的调试做好准备。
在调试阶段,需要对冲压模具进行各项参数调整和测试,以寻找最优的生产效率和产品质量。
2.加工技术在冲压模具加工过程中,需要采用不同的加工技术以满足各个零部件的加工要求,这既需要考虑到加工效率,也需要充分考虑到加工的质量和精度。
常使用的加工技术包括铣削、钻孔、线切割、焊接等。
在使用这些加工技术时,需要特别关注制造过程中的各个环节,确保待加工的零部件的精度和质量得到保障。
冲压模具的设计与制造分析
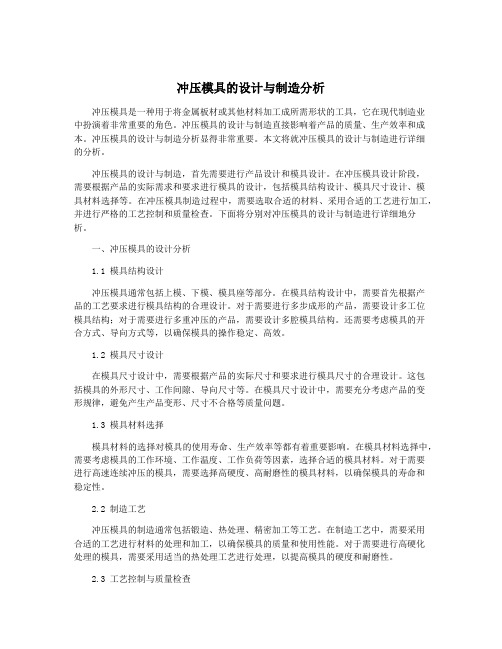
冲压模具的设计与制造分析冲压模具是一种用于将金属板材或其他材料加工成所需形状的工具,它在现代制造业中扮演着非常重要的角色。
冲压模具的设计与制造直接影响着产品的质量、生产效率和成本。
冲压模具的设计与制造分析显得非常重要。
本文将就冲压模具的设计与制造进行详细的分析。
冲压模具的设计与制造,首先需要进行产品设计和模具设计。
在冲压模具设计阶段,需要根据产品的实际需求和要求进行模具的设计,包括模具结构设计、模具尺寸设计、模具材料选择等。
在冲压模具制造过程中,需要选取合适的材料、采用合适的工艺进行加工,并进行严格的工艺控制和质量检查。
下面将分别对冲压模具的设计与制造进行详细地分析。
一、冲压模具的设计分析1.1 模具结构设计冲压模具通常包括上模、下模、模具座等部分。
在模具结构设计中,需要首先根据产品的工艺要求进行模具结构的合理设计。
对于需要进行多步成形的产品,需要设计多工位模具结构;对于需要进行多重冲压的产品,需要设计多腔模具结构。
还需要考虑模具的开合方式、导向方式等,以确保模具的操作稳定、高效。
1.2 模具尺寸设计在模具尺寸设计中,需要根据产品的实际尺寸和要求进行模具尺寸的合理设计。
这包括模具的外形尺寸、工作间隙、导向尺寸等。
在模具尺寸设计中,需要充分考虑产品的变形规律,避免产生产品变形、尺寸不合格等质量问题。
1.3 模具材料选择模具材料的选择对模具的使用寿命、生产效率等都有着重要影响。
在模具材料选择中,需要考虑模具的工作环境、工作温度、工作负荷等因素,选择合适的模具材料。
对于需要进行高速连续冲压的模具,需要选择高硬度、高耐磨性的模具材料,以确保模具的寿命和稳定性。
2.2 制造工艺冲压模具的制造通常包括锻造、热处理、精密加工等工艺。
在制造工艺中,需要采用合适的工艺进行材料的处理和加工,以确保模具的质量和使用性能。
对于需要进行高硬化处理的模具,需要采用适当的热处理工艺进行处理,以提高模具的硬度和耐磨性。
2.3 工艺控制与质量检查在冲压模具的制造过程中,需要对制造工艺进行严格控制,并进行系统的质量检查。
冲压模具的设计与制造分析
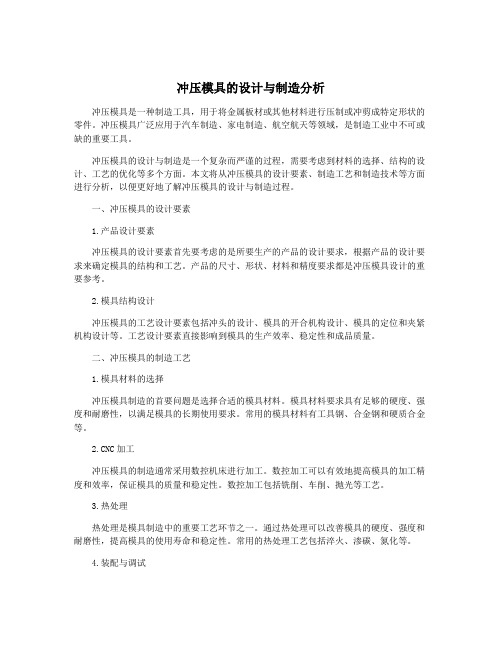
冲压模具的设计与制造分析冲压模具是一种制造工具,用于将金属板材或其他材料进行压制或冲剪成特定形状的零件。
冲压模具广泛应用于汽车制造、家电制造、航空航天等领域,是制造工业中不可或缺的重要工具。
冲压模具的设计与制造是一个复杂而严谨的过程,需要考虑到材料的选择、结构的设计、工艺的优化等多个方面。
本文将从冲压模具的设计要素、制造工艺和制造技术等方面进行分析,以便更好地了解冲压模具的设计与制造过程。
一、冲压模具的设计要素1.产品设计要素冲压模具的设计要素首先要考虑的是所要生产的产品的设计要求,根据产品的设计要求来确定模具的结构和工艺。
产品的尺寸、形状、材料和精度要求都是冲压模具设计的重要参考。
2.模具结构设计冲压模具的工艺设计要素包括冲头的设计、模具的开合机构设计、模具的定位和夹紧机构设计等。
工艺设计要素直接影响到模具的生产效率、稳定性和成品质量。
二、冲压模具的制造工艺1.模具材料的选择冲压模具制造的首要问题是选择合适的模具材料。
模具材料要求具有足够的硬度、强度和耐磨性,以满足模具的长期使用要求。
常用的模具材料有工具钢、合金钢和硬质合金等。
C加工冲压模具的制造通常采用数控机床进行加工。
数控加工可以有效地提高模具的加工精度和效率,保证模具的质量和稳定性。
数控加工包括铣削、车削、抛光等工艺。
3.热处理热处理是模具制造中的重要工艺环节之一。
通过热处理可以改善模具的硬度、强度和耐磨性,提高模具的使用寿命和稳定性。
常用的热处理工艺包括淬火、渗碳、氮化等。
4.装配与调试冲压模具的装配与调试是模具制造的最后阶段。
在装配与调试过程中,需要对模具的各个零部件进行组装与调整,以保证模具的精度、稳定性和可靠性。
1.模具CAD/CAM技术模具CAD/CAM技术是现代模具制造的重要技术手段。
通过CAD/CAM技术可以实现模具的设计、工艺规划、数控加工程序生成等全过程数字化,提高设计效率和生产精度。
2.先进制造技术冲压模具的制造技术在不断发展与进步,涌现了许多新的制造技术。
冲压工艺及模具设计

冲压工艺及模具设计冲压工艺及模具设计是一种应用广泛的金属加工方法,它通过将金属材料置于模具中,施加外力使其产生塑性变形来实现加工目的。
冲压工艺及模具设计在日常生活中被广泛应用于汽车制造、家电制造、建筑结构等领域。
本文将详细介绍冲压工艺及模具设计的基本原理、流程以及注意事项。
一、冲压工艺的基本原理冲压工艺是利用模具的上下凸模与下模的活套孔进行压力传递,从而给金属材料施加一定的压力,使其发生塑性变形,最终获得所需形状的零件。
冲压工艺的基本原理包括:所需零部件的模具设计、材料的选用、设备的调整和操作、冲压力的控制等。
二、冲压工艺的流程1.设计模具:根据所需加工的零件形状和尺寸,设计相应的冲压模具。
模具的设计考虑要点包括:模具结构、零件加工顺序、模具寿命等。
2.材料选用:根据所需加工的零件的要求,选择合适的金属材料。
常用的金属材料有冷轧钢板、不锈钢板、铝合金板等。
3.材料切割:将金属材料按照所需零件的形状和尺寸切割成相应的板料。
4.模具调整:将上下模具安装在冲床上,并进行调整,使得上下模具对齐、平衡。
5.进料:将切割好的板料放置在模具上,通过上模的压力传递给下模,使金属材料发生塑性变形。
6.成型:通过上下模具的周期性运动,使金属材料依次进行冲击、拉伸、弯曲等工艺,最终获得所需形状的零件。
7.完成零件:将成型好的零件从模具中取出,并进行后续处理,如清洗、打磨、表面处理等。
三、冲压工艺及模具设计的注意事项1.模具的设计:模具的设计应符合所需零件的形状和尺寸要求,且要考虑模具的寿命和成本问题。
模具设计时,需注意加工顺序的合理性,以提高生产效率。
2.材料的选用:选择合适的金属材料是冲压工艺的关键,需考虑零件的材质要求、成本和加工性能等因素。
3.设备的调整和操作:正确调整冲床的压力、速度和行程等参数,保证冲压工艺的稳定进行。
操作时,需注意安全,确保操作人员的人身安全。
4.增加冲压辅助工艺:根据所需零件的形状和要求,可以增加冲压辅助工艺,如冲孔、拉伸、弯曲、压花等,以提高零件的加工质量和寿命。
冲压模具的设计与制造分析

冲压模具的设计与制造分析1. 引言1.1 冲压模具的设计与制造分析冲压模具的设计与制造分析是现代制造业中至关重要的一环。
冲压模具作为生产加工中的关键装备,在各种行业中都扮演着不可或缺的角色。
通过对冲压模具的设计与制造进行深入分析,可以更好地理解其在生产制造中的作用和意义。
冲压模具的设计与制造是一个综合性强、工艺性较强的领域。
在设计过程中,需要考虑材料的选择、模具结构的设计、工艺参数的确定等诸多因素;在制造过程中,要注重工艺的精细化、设备的先进性、质量的稳定性等方面。
只有将设计与制造紧密结合,才能保证冲压模具的性能和精度达到要求。
冲压模具的设计与制造也是一个不断创新和发展的过程。
随着科技的不断进步和市场需求的不断变化,冲压模具的设计与制造技术也在不断更新迭代。
必须与时俱进,不断学习和掌握最新的技术和方法,才能在激烈的市场竞争中立于不败之地。
冲压模具的设计与制造分析是一个复杂而又充满挑战的领域。
只有不断总结经验、研究新技术、提高自身素质,才能在这个领域中获得成功。
2. 正文2.1 冲压模具的概念与分类冲压模具是一种用于在金属板或带材上施加力量,使其产生塑性变形并最终成型为所需形状的工具。
它是冲压加工中必不可少的重要设备,广泛应用于汽车制造、电子设备、家电产品等行业。
根据不同的使用需求和工艺要求,冲压模具可以分为以下几类:1.单操作模具:单操作模具是最基本的一种冲压模具,其结构简单,适用于对称或简单形状的产品加工。
2.复合模具:复合模具包括多个工作站,可以同时进行多道工序的加工,提高生产效率和产品质量。
3.连续模具:连续模具适用于对冲压速度要求较高的产品加工,能够实现高速连续冲压。
4.特殊形状模具:特殊形状模具适用于特殊形状产品的加工,如异形孔、凹凸结构等。
5.逐次成型模具:逐次成型模具适用于需要多次冲压工序才能完成的产品加工,通常用于复杂形状的产品制造。
不同类型的冲压模具在设计和制造上有各自特点,但都是为了实现产品的快速、精准成型而存在的重要工具。
冲压工艺与冲压模具设计
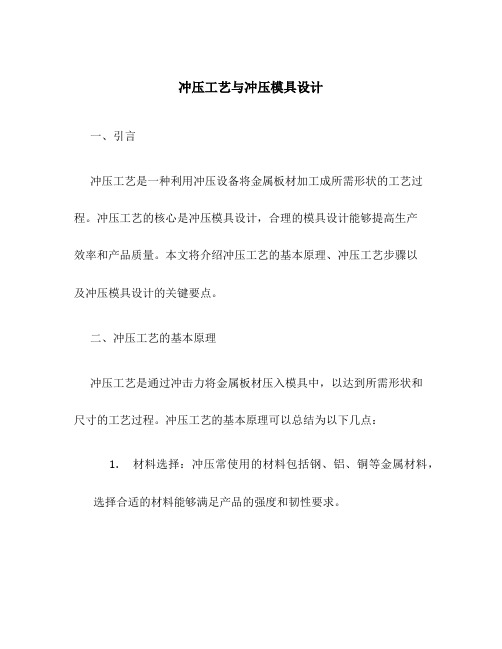
冲压工艺与冲压模具设计一、引言冲压工艺是一种利用冲压设备将金属板材加工成所需形状的工艺过程。
冲压工艺的核心是冲压模具设计,合理的模具设计能够提高生产效率和产品质量。
本文将介绍冲压工艺的基本原理、冲压工艺步骤以及冲压模具设计的关键要点。
二、冲压工艺的基本原理冲压工艺是通过冲击力将金属板材压入模具中,以达到所需形状和尺寸的工艺过程。
冲压工艺的基本原理可以总结为以下几点:1.材料选择:冲压常使用的材料包括钢、铝、铜等金属材料,选择合适的材料能够满足产品的强度和韧性要求。
2.板料形状设计:根据产品的设计要求,确定金属板材的形状和尺寸。
常见的板料形状包括平板、弯曲板、拉伸板等。
3.模具设计:根据产品的形状和尺寸,设计合适的冲压模具。
冲压模具包括上模、下模和剪切模等。
模具的设计需要考虑产品的结构、工艺要求和生产效率。
4.工艺参数选择:冲压工艺中需要选择合适的工艺参数,如压力、速度、冲头形状等。
合理的工艺参数能够保证产品的质量和生产效率。
三、冲压工艺步骤冲压工艺通常包括以下几个步骤:1. 材料准备首先需要准备合适的金属板材,根据产品的要求选择合适的材料。
然后对金属板材进行切割、修边等预处理工作,以准备好冲压加工。
2. 模具设计和制造根据产品的形状和尺寸,设计合适的冲压模具。
模具的设计要考虑产品的结构、工艺要求和生产效率。
设计完成后,制造相应的模具。
3. 模具调试和试产制造完成的模具需要进行调试和试产。
通过调试,调整模具的参数和结构,使其能够满足产品的要求。
试产时,对模具进行试运行和试制品的生产,以验证模具的可行性和稳定性。
4. 生产加工调试完成后,模具即可投入正式生产。
生产时,将金属板材放入模具中,通过冲压设备施加压力,将板材加工成产品的形状和尺寸。
5. 检验和修磨生产完成后,需要对产品进行检验。
对于不合格品,需要进行修磨到合格尺寸。
修磨工艺要求较高,需要保持产品的精度和表面质量。
四、冲压模具设计的关键要点冲压模具设计是冲压工艺中最关键的环节,其设计质量直接关系到产品的质量和生产效率。
冲压工艺及模具设计(3篇)

第1篇一、引言冲压工艺是一种常见的金属成形工艺,广泛应用于汽车、家电、电子、航空等行业。
冲压工艺具有生产效率高、成本低、精度高、尺寸稳定性好等优点。
模具是冲压工艺中的关键设备,其设计质量直接影响到冲压产品的质量和生产效率。
本文将对冲压工艺及模具设计进行简要介绍。
二、冲压工艺概述1. 冲压工艺原理冲压工艺是利用模具对金属板材施加压力,使其产生塑性变形,从而获得所需形状、尺寸和性能的零件。
冲压工艺的基本原理是金属的塑性变形,即金属在受到外力作用时,产生塑性变形而不破坏其连续性的过程。
2. 冲压工艺分类(1)拉深:将平板金属沿模具凹模形状变形,形成空心或实心零件的过程。
(2)成形:将平板金属沿模具凸模形状变形,形成具有一定形状的零件的过程。
(3)剪切:将平板金属沿剪切线剪切成一定形状和尺寸的零件的过程。
(4)弯曲:将平板金属沿模具凸模形状弯曲,形成具有一定角度的零件的过程。
三、模具设计概述1. 模具设计原则(1)满足产品精度和尺寸要求:模具设计应保证冲压产品具有高精度和尺寸稳定性。
(2)提高生产效率:模具设计应优化工艺流程,减少不必要的加工步骤,提高生产效率。
(3)降低生产成本:模具设计应选用合适的材料,降低模具成本。
(4)确保模具寿命:模具设计应考虑模具的耐磨性、耐腐蚀性等性能,延长模具使用寿命。
2. 模具设计步骤(1)产品分析:分析产品的形状、尺寸、材料等,确定模具设计的基本要求。
(2)工艺分析:根据产品形状和尺寸,确定冲压工艺类型,如拉深、成形、剪切、弯曲等。
(3)模具结构设计:根据工艺要求,设计模具结构,包括凸模、凹模、导向装置、压边装置等。
(4)模具零件设计:根据模具结构,设计模具零件,如凸模、凹模、导向装置、压边装置等。
(5)模具加工:根据模具零件设计,进行模具加工。
(6)模具调试:完成模具加工后,进行模具调试,确保模具性能符合要求。
四、冲压工艺及模具设计要点1. 冲压工艺要点(1)合理选择材料:根据产品形状、尺寸、性能要求,选择合适的金属材料。
- 1、下载文档前请自行甄别文档内容的完整性,平台不提供额外的编辑、内容补充、找答案等附加服务。
- 2、"仅部分预览"的文档,不可在线预览部分如存在完整性等问题,可反馈申请退款(可完整预览的文档不适用该条件!)。
- 3、如文档侵犯您的权益,请联系客服反馈,我们会尽快为您处理(人工客服工作时间:9:00-18:30)。
第一章零件设计任务 (1)第二章冲裁件的工艺分析 (2)2.1工件材料 (2)2.2工件结构形状 (2)2.3工件尺寸精度 (2)第三章冲裁工艺方案 (3)第四章模具结构形式的选择 (5)4.1模具的类型的选择 (5)4.2卸料装置 (5)4.2.1.条料的卸除 (5)4.2.2卸料方式 (5)4.3定位装置 (5)4.3.1.送料形式 (5)4.3.2.定位零件: (5)4.4.模架类型及精度 (6)4.4.1.模架 (6)4.4.2.精度 (6)第五章冲压工艺计算: (7)5.1.排样 (7)5.1.1.排样方案分析 (7)5.1.2.计算条料宽度 (7)5.1.3.确定布距: (8)5.1.4.计算材料利用率 (8)5.2.冲压力计算 (9)5.2.1.冲裁力计算 (9)5.2.2.卸料力、顶件力的计算 (10)5.3.压力中心的计算 (11)5.4.模具工作部分尺寸及公差 (12)5.4.1.落料尺寸大小为 (12)5.4.2.冲孔尺寸大小为 (13)第六章主要零部件设计 (14)6.1.凹模的设计 (14)6.1.1.落料凹模 (14)6.1.2.冲孔凹模的设计 (16)6.2.凸模的设计 (17)6.2.1.冲孔圆形凸模: (17)6.2.2.腰孔的设计 (18)6.2.3.落料凸模 (18)6.2.4.凸模的校核: (19)6.3.卸料板的设计 (20)6.4.固定板的设计 (21)6.4.1. 凹模固定板: (21)6.4.2.凸模固定板: (22)6.5.模架以及其他零部件的选用 (23)第7章校核模具闭合高度及压力机有关参数 (24)7.1 校核模具闭合高度 (24)7.2 冲压设备的选定 (24)第8章设计并绘制模具总装图及选取标准件 (25)第9章结论 (26)参考文献 (27)第一章零件设计任务零件简图:如图1-1 所示材料:10号钢材料厚度:2mm未标注尺寸按照IT10级处理.第二章冲裁件的工艺分析2.1工件材料由图1-1分析知:10#钢为优质碳素结构钢,具有良好的塑性性、焊接性以及压力加工性,主要用于制作冲击件、紧固件,如垫片、垫圈等。
适合冲裁加工。
2.2工件结构形状工件结构形状相对简单,有四个圆孔,孔与边缘之间的距离满足要求,料厚为2mm满足许用壁厚要求(孔与孔之间、孔与边缘之间的壁厚),可以冲裁加工。
2.3工件尺寸精度根据零件图上所注尺寸,工件要求不高,尺寸精度要求较低,采用IT14级精度,普通冲裁完全可以满足要求。
根据以上分析:该零件冲裁工艺性较好,综合评比适宜冲裁加工。
第三章冲裁工艺方案完成此工件需要冲孔、落料两道工序。
其加工工艺方案分为以下3种:1.方案一:单工序模生产。
先冲孔,后落料;2.方案二:级进模生产。
冲孔—落料级进冲压;3.方案三:复合模生产。
冲孔—落料复合冲压。
各模具结构特点及比较如下表3-1:表 3-1 各类模具结构及特点比较根据分析结合表分析:方案一模具结构简单,制造周期短,制造简单,但需要两副模具,成本高而生产效率低,难以满足大批量生产的要求。
方案二只需一副模具,生产效率高,操作方便,精度也能满足要求,模具制造工作量和成本在冲裁简单的零件时比复合模低。
方案三只需一副模具,制件精度和生产效率都较高,且工件最小壁厚大于凸凹模许用最小壁厚模具强度也能满足要求。
冲裁件的内孔与边缘的相对位置精度较高,板料的定位精度比方案二低,模具轮廓尺寸较小。
综上对上述三种方案的分析比较,该工件的冲压生产采用方案二为佳。
第四章模具结构形式的选择4.1模具的类型的选择由冲压工艺分析可知,采用级进模方式冲压,所以模具类型为级进模。
4.2卸料装置4.2.1.条料的卸除因采用级进模生产,故采用向下落料出件。
4.2.2卸料方式考虑零件尺寸较大,厚度较高,采用固定卸料方式,为了便于操作,提高生产率。
4.3定位装置4.3.1.送料形式因选用的冲压设备为开式压力机且垂直于送料方向的凹模宽度B小于送料方向的凹模长度L故采用横向手动送料方式,即由右向左(或由左向右)送料既能满足生产要求,又可以降低生产成本,提高经济效益。
4.3.2.定位零件:零件尺寸较大,厚度较高,保证孔的精度及较好的定位,宜采用导料板导向,导正销导正,为了提高材料利用率采用始用挡料销和固定挡料销。
4.4.模架类型及精度4.4.1.模架1.若采用中间导柱模架,则导柱对称分布,受力平衡,滑动平稳,但只能一方送料;2. 若采用对角导柱模架,则受力平衡,滑动平稳,可纵向或横向送料;3. 若采用后侧导柱导柱模架,可三方送料,操作者视线不被阻挡,结构比较紧凑的,但模具受力不平衡,滑动不平稳。
综上,结合本冲孔、落料级进模的特点,决定采用后侧导柱模架。
4.4.2.精度由于零件材料较厚,尺寸较大,冲裁间隙较小,又是级进模因此采用导向平稳的中间导柱模架,考虑零件精度要求不是很高,冲裁间隙较小,因此采用Ⅰ级模架精度。
第五章 冲压工艺计算:5.1.排样5.1.1.排样方案分析方案一:有废料排样 沿冲件外形冲裁,在冲件周边都留有搭边。
冲件尺寸完全由冲模来保证,因此冲件精度高,模具寿命高,但材料利用率低。
方案二:少废料排样 因受剪切条料和定位误差的影响,冲件质量差,模具寿命较方案一低,但材料利用率稍高,冲模结构简单。
方案三:无废料排样 冲件的质量和模具寿命更低一些,但材料利用率最高。
通过上述三种方案的分析比较,综合考虑模具寿命和冲件质量,该冲件的排样方式选择方案一为佳。
考虑模具结构和制造成本有废料排样的具体形式选择直排最佳。
5.1.2.计算条料宽度根据零件形状,查<<冲压模具设计手册>>工件之间搭边值a=1.2mm, 工件与侧边之间搭边值a 1=1.5mm, 条料是有板料裁剪下料而得,为保证送料顺利,规定其上偏差为零,下偏差为负值—△11max 0)22(∆∆⨯+⨯+=b a D B 公式(5-1)式中:Dmax —条料宽度方向冲裁件的最大尺寸;a 1---冲裁件之间的搭边值;b 1---侧刃冲切得料边定距宽度;(其值查表6)可得△=2.0mm 。
△—板料剪裁下的偏差;(其值查表5)可得△=0.6mm 。
B 0△=75+2×1.5+2×2.0=82.00-0.60mm故条料宽度为82.0mm 。
5.1.3.确定布距:送料步距S :条料在模具上每次送进的距离称为送料步距,每个步距可冲一个或多个零件。
进距与排样方式有关,是决定侧刃长度的依据。
条料宽度的确定与模具的结构有关。
级进模送料步距S1max a D S += 公式(5-2)D max 零件横向最大尺寸,a 1搭边S =75+1.5=76.5mm排样图如图2所示。
5.1.4.计算材料利用率一个步距内的材料利用率η=A/BS ×100% 公式(5-3) 式中 A —一个步距内冲裁件的实际面积;B —条料宽度;S —步距;一个步距内冲裁件的实际面积A=π×37.52-π×13.52-3×π×3.752-3(π×302×34/360-π×26.252×34/360)= 3807.73539mm 2所以一个步距内的材料利用率Η=A/BS ×100%= 3807.73539/(76.5×82)×100%=60.7%考虑料头 、尾料和边角余料消耗,一张板材上的总利用率η总为η总= nA 1/LB ×100% 公式(5-4)式中 n —一张板料上冲裁件的总数目;A 1—一个冲裁件的实际面积; L —板料长度;B —板料宽度。
查板材标准,宜选用850mm ×1700mm 的钢板,每张钢板可剪裁为11张条料(82mm ×1700mm ),每张条料可以冲25个工件,所以每张钢板的材料利用率η总= nA 1/LB ×100%=25×3807.73539/82×1700×100% =68.3%根据计算结果知道选用直排材料利用率可达68.3%,满足要求。
5.2.冲压力计算5.2.1.冲裁力计算用平刃冲裁时,其冲裁力F一般按下式计算:b KLt F τ= 公式(5-5)式中:F —冲裁力;L —冲裁周边长度; t —材料厚度;τb —材料抗剪强度;10钢τb的值查《《冲压成型工艺与模具设计》》附录表2为255-333Mpa,取τb =300MpaK—系数;一般取K=1.3。
1、冲孔力计算冲孔周长:L=π×27+3π×3.75×2+3π(26.25+33.75)×34/360+2×76.5+2×12 =764.98mm 所以冲孔力F=KLt τb =1.3×764.98×2×300=596.69kN2.落料力的计算落料周长75⨯=⨯=ππd L落料冲裁力F2= KLt τb =1.3×π×75×2×300=183.78kN 。
5.2.2.卸料力、顶件力的计算一般按以下公式计算: 卸料力kNF K F X x 35.778.18304.0 (2)=⨯=∙= 公式(5-6)顶件力kNkN F F K F d D 83.46.....)78.18369.596(06.0.....)(2=+⨯=+= 公式(5-7)(d X K K 为卸料力系数,其值查表5-1可得)所以总冲压力kNF F F F F DX Z 65.834.....83.4635.778.18369.596.....2=+++=+++= 公式(5-8)表5-1 卸料力、推件力和顶件力系数由ZF P >-0%)60%50(,即冲压时工艺力的总和不能大于压力机公称压力的50%-60%,取ZF P ⨯=8.10,则公称压力kNF P Z 37.15028.10=⨯=. 初选压力机的公称压力为1600Kn,即JA21-160型压力机。
5.3.压力中心的计算用解析计算法求出冲模压力中心。
X 0=(L 1x 1+L 2x 2+…L n x n )/(L 1+L 2+…L n ) 公式(5-9) Y 0=(L 1y 1+L 2y 2+……L n y n )/(L 1+L 2+…+Ln )用解析法计算压力中心时,先画出凹模形口图,如图5-3所示。
在图中将XOY 坐标系建立在建立在图示对称中心线上,将冲裁轮廓线按几何图形分解成L 1~L 5共 3组基本线段 (注:由于图中3个圆弧形孔均以一个点为圆心的等分列阵排列,所以其几何图形为一组) ,用解析法求得该模具压力中心的坐标。