冲压模具设计
冲压模具设计全套步骤和流程

冲压模具设计全套步骤和流程1.零件设计:根据产品的功能要求和外观要求,进行零件的设计。
确定零件的几何形状、尺寸和所需的表面质量等。
2.材料选择:根据零件的要求和产品的使用环境,选择合适的材料。
考虑材料的强度、塑性和可加工性等因素。
3.模具结构设计:根据零件的几何形状和加工要求,设计模具的结构。
包括模具的底座、上模、下模、模具导向装置、顶针等部分。
4.模具零件设计:根据模具结构设计的要求,对模具的各个零部件进行设计。
包括模具的滑块、顶出装置、顶出销等。
5.模具总成设计:将各个模具零件组装成一个整体。
进行模具总成的设计,确定各个模具零件的安装位置、尺寸等。
6.模具加工工艺设计:根据模具结构和零件的加工要求,设计模具的加工工艺。
包括模具的加工工艺路线、加工顺序、机床设备等。
7.模具调试和试产:根据模具的设计和加工工艺,进行模具的组装和调试。
包括模具的调试、调整、测试以及初次试产。
根据试产结果,对模具进行优化和改进。
8.模具使用和维护:对模具进行使用和维护。
包括模具的防护、清洁、润滑和定期维护等。
9.模具性能评价:对模具进行性能评价。
包括模具的使用寿命、生产效率、加工精度等方面的评价。
10.模具改进和更新:根据使用中的问题和需求,对模具进行改进和更新。
包括模具的结构改进、材料选择和加工工艺的优化等。
以上是冲压模具设计的全套步骤和流程。
在进行设计的过程中,需要考虑零件的功能要求、材料的选择、模具的结构设计、加工工艺的确定等因素。
通过设计和优化,能够获得满足产品要求的冲压模具,提高生产效率和产品质量。
冲压模具设计流程

冲压模具设计流程冲压模具是制造工业中常见的一种模具,它广泛应用于汽车、电子、家电等行业。
冲压模具的设计流程对产品的质量和生产效率有着重要的影响。
下面将介绍冲压模具设计的流程。
首先,冲压模具设计的第一步是需求分析。
在这一阶段,设计师需要与客户充分沟通,了解客户对产品的要求和需求,包括产品的形状、尺寸、材料等。
只有充分了解客户的需求,才能设计出符合客户要求的冲压模具。
接着,设计师需要进行产品设计和结构设计。
在产品设计阶段,设计师需要根据客户的需求,绘制产品的草图和三维模型,确定产品的形状和尺寸。
在结构设计阶段,设计师需要设计模具的结构,确定模具的各个零部件的结构和尺寸,以及各个零部件之间的配合关系。
然后,设计师需要进行材料选型和工艺规划。
在材料选型阶段,设计师需要根据产品的要求和模具的结构,选择合适的材料,包括模具的主要材料和辅助材料。
在工艺规划阶段,设计师需要确定模具的加工工艺和生产工艺,包括模具的加工工艺和装配工艺。
接着,设计师需要进行模具零部件的设计和加工。
在这一阶段,设计师需要根据模具的结构和尺寸,设计模具的各个零部件,并将零部件的图纸和工艺文件传递给模具加工车间进行加工。
最后,设计师需要进行模具的装配和调试。
在这一阶段,模具加工车间将加工好的模具零部件进行装配,然后进行模具的调试,包括模具的合模性能、产品的成型性能等。
综上所述,冲压模具设计流程包括需求分析、产品设计和结构设计、材料选型和工艺规划、模具零部件的设计和加工、模具的装配和调试。
只有严格按照这些流程,才能设计出高质量的冲压模具,满足客户的需求,提高产品的质量和生产效率。
冲压模具设计方法与步骤

冲压模具设计方法与步骤冲压模具是制造行业中常用的一种模具,用于在金属板材上进行冲裁、压制、成形等工艺。
冲压模具的设计是冲压工艺的关键环节之一,合理的设计可以提高产品质量和生产效率。
以下是冲压模具设计的方法与步骤。
一、冲压模具设计方法1.分析产品要求:首先需要仔细分析产品要求,了解产品的形状、尺寸、材质等要求,以及要求的生产效率和成本等因素。
2.选择合适的材料:根据产品的要求选择合适的模具材料,常用的材料有合金工具钢、合金冷作工具钢等。
3.制定冲压工艺:根据产品要求,制定冲压工艺,包括冲剪顺序、成形方式、冲压力、冲头形状等因素。
4.设计模具结构:根据产品要求和冲压工艺,设计模具的结构,包括上模、下模、导向机构等部分。
5.进行模具布局:进行模具布局,合理安排模具零件的形状、位置和尺寸,以确保模具的强度和稳定性。
6.进行模具零件设计:根据模具布局,设计模具的零件,包括冲头、导柱、导套、导向板等部分。
7.进行模具装配:根据模具设计,进行模具的装配,确保各个零件之间的配合和精度。
8.进行模具调试:进行模具调试,调整模具的尺寸和位置,确保模具在冲压过程中的稳定性和精度。
9.进行模具试产:进行模具试产,对模具进行试模和试产,检验产品的质量和模具的性能。
10.进行模具改进:根据试产结果,对模具进行改进和优化,提高模具的性能和生产效率。
二、冲压模具设计步骤1.初步设计:根据产品要求,进行初步的模具设计,包括模具结构和布局。
2.详细设计:对初步设计的模具进行详细设计,包括各个零件的形状、尺寸和材料等。
3.模具制造:根据详细设计,进行模具的制造,包括加工模具零部件和进行模具装配。
4.模具调试:对制造完成的模具进行调试,调整模具的尺寸和位置,确保模具的性能和精度。
5.模具试产:进行模具的试模和试产,检验产品的质量和冲压工艺的可行性。
6.模具改进:根据试产结果,对模具进行改进和优化,提高模具的性能和生产效率。
7.模具验收:对改进后的模具进行验收,确保模具达到产品要求和生产效果。
毕业设计冲压模具设计

毕业设计冲压模具设计冲压模具设计是指根据零部件的形状和要求,通过模具设计软件对压制工艺和模具结构进行详细设计并完成加工制造的过程。
本文将以零部件的冲压模具设计为例,详细介绍冲压模具设计的步骤和关键技术。
一、冲压模具设计的步骤1.零件分析与加工工艺确定:首先对待设计的零件进行分析,了解其形状、材料及加工工艺要求。
通过对零件的尺寸测量、材料分析和工艺流程确定,确定适宜的冲压模具设计方案。
2.模具结构确定:根据零件形状和工艺要求,确定模具的基本结构形式,包括上、下模块的形状和结构、导向方式以及顶出装置的设计。
3.模具零件设计:根据模具的结构形式,对上、下模板、定位销、导柱、导套、顶出器等模具零件进行详细设计,并确定其尺寸、形位公差和表面粗糙度。
4.模具装配设计:根据模具零件的设计,进行模具的装配设计,确定模具各零件的加工工艺和装配工艺。
5.3D模型的建立:采用模具设计软件对模具的各个零件进行建模,并对其进行装配,实现模型的全面展示和动态演示。
6.模具结构的强度分析:采用有限元分析法对模具结构进行强度分析,确定模具零件的受力状态,从而提高模具的刚度和寿命。
7.模具工艺文件的编制:编制模具的工艺文件,包括工艺流程、工装设计和使用说明,为模具的制造和使用提供详细的技术支持。
二、冲压模具设计的关键技术1.零件厚度均衡设计:保证冲压零件的均衡受力,在模具的设计中尽量避免出现片厚不均的问题,从而避免在冲压过程中产生变形或裂纹等缺陷。
2.弹性顶出设计:在模具设计中合理设置顶针或顶出器,以保证冲压零件在顶出过程中不会卡死或破碎,从而提高冲压的质量和效率。
3.导向方式优化设计:合理选择导向方式,减小模具的摩擦阻力,从而提高模具的导向精度和工作寿命。
4.材料选择与热处理:合理选择模具材料,并根据工艺要求进行适当的热处理,以提高模具的硬度和耐磨性,延长模具的使用寿命。
5.模腔润滑与冷却设计:在模具设计中设置合理的润滑和冷却装置,以提高冲压的质量和效率,并减少模具的磨损和热变形。
冲压模具设计

冲压模具设计一、冲压模具设计的步骤1.确定需求:首先要明确冲压件的形状、尺寸和质量要求,以及加工工艺的要求,包括材料选材、工艺流程等。
2.分析冲压过程:了解冲压过程中的受力情况,确定冲压件的受力情况,考虑冲压件的结构和形状。
分析完成后,可以确定模具的结构和工作原理。
3.制定设计方案:设计方案是根据需求和分析决策,形成的模具设计的主要思路,包括模具的结构形式、材料选材、零件加工工艺等。
4.细化设计:在设计方案的基础上,进一步细化设计,包括每个零件的尺寸、形状和工艺要求,确保每个零件都符合设计要求。
5.制作样品:制作模具样品,进行试验和调试,验证设计方案的可行性,确定调整和改进方案。
6.定稿设计:根据试验结果,对设计方案进行调整和优化,形成最终的设计方案。
二、冲压模具设计的关键要点1.良好的受力结构:冲压模具在工作过程中要经受巨大的冲击力和挤压力,因此必须具备良好的受力结构,包括合理的分布受力、合理的受力传递和合理的受力集中。
2.优秀的耐磨材料:冲压模具的工作环境往往十分恶劣,耐磨材料可以大大延长模具的使用寿命,提高生产效率。
3.精密的加工工艺:冲压模具的加工精度直接影响到冲压件的质量,因此必须采用精密的加工工艺,确保模具的精密度和可靠性。
4.优化的结构设计:冲压模具的结构设计要尽可能简单,降低成本,提高生产效率。
同时也要考虑模具的易维护性,方便维修和更换零件。
5.可靠的试验与调试:为了保证冲压模具的质量和可靠性,必须进行全面的试验和调试,包括模具的运行测试、冲压件的检测评价等。
三、结语冲压模具设计是一个复杂而细致的工程,需要综合运用材料学、结构设计、机械加工、模具试验等多方面的知识。
只有具备扎实的理论基础和丰富的实践经验,才能设计出高质量的冲压模具。
希望以上内容对冲压模具设计有所帮助,能够指导相关行业的人士更好地进行冲压模具设计工作。
冲压模具设计是一个复杂的过程,需要设计人员深入且全面地了解冲压工艺、材料特性、机械结构、模具加工工艺等多方面知识,并且需要经验丰富的工程师进行设计。
冲压模具设计的主要内容及步骤

冲压模具设计的主要内容及步骤冲压模具设计是指根据产品的形状、尺寸和工艺要求,设计出适合于冲压成型的模具。
它是冲压工艺的关键环节之一,对于冲压成品的质量、生产效率和成本等方面具有重要影响。
下面将从主要内容和步骤两个方面来详细介绍冲压模具的设计过程。
一、主要内容1.产品分析:了解产品的形状、尺寸、材料以及加工工艺要求等,包括产品的外观和内部结构等方面。
根据产品的特点来确定模具的种类和结构。
2.材料选择:根据冲压工艺要求和模具的使用条件,选择合适的模具材料,包括工作模具和凸模、活塞等配件的材料选择。
3.结构设计:确定模具的分型方式和结构形式,包括模具的基本结构、操作方式、传动方式、冷却系统和脱模系统等。
还需要考虑模具的可拆卸性、装配性以及模具的厚度和尺寸等。
4.零件设计:根据产品的形状和尺寸,设计出模具的主要零件,包括模具座、滑块、压料板、导向套等。
需要考虑模具的刚度和强度等。
5.工艺设计:根据冲压工艺要求,确定模具的工作步骤和工艺参数,包括下料、冲孔、冲凸、整形等工序,并合理安排模具的工作顺序和加工工艺。
6.零件布局:根据结构设计和工艺要求,将各个零件合理布局,包括确定零件之间的相对位置和相互之间的配合关系等。
7.工装设计:根据冲压工艺要求,设计出合适的工装夹具和模板,用于固定和定位工件,保证冲压过程中的精度和稳定性。
二、主要步骤1.产品分析及材料选择:仔细分析产品的形状、尺寸和工艺要求,根据产品的材料选择合适的模具材料。
2.结构设计:根据产品的特点和生产要求,确定模具的结构形式和基本结构,包括模具的分型方式、操作方式、冷却系统和脱模系统等。
3.零件设计:根据产品的形状和尺寸,设计出模具的主要零件,包括模具座、滑块、压料板、导向套等。
4.工艺设计:根据冲压工艺要求,确定模具的工作步骤和工艺参数,合理安排模具的工作顺序和加工工艺。
5.零件布局:将各个零件合理布局,确定零件之间的相对位置和相互之间的配合关系。
冲压模具通用设计规范

冲压模具通用设计规范
一、基本概念
1、冲压模具:是一种利用冲压设备加热,表面处理等减轻金属模具表面机械应力,以实现金属零件加工的模具。
2、冲压模具的目的:通过冲压模具实现零件加工加工,能够有效减少工件的材料浪费,节约加工时间,提高加工质量,减轻加工成本,提高产品质量,提升竞争力。
二、冲压模具的分类
根据结构形式,冲压模具可以分为单片式模具,双片式模具,多片式模具,拼接式模具和复合式模具等。
根据工件的制造方法,冲压模具可以分为成型模具,连接模具,混合模具,拼接模具,拉伸模具,精加工模具和切削模具等。
三、冲压模具的制造工艺
1、机械加工:常用车削、铣削和锻造等机械加工来制作冲压模具。
2、冲压:在模具制造过程中,需要用到冲压机来冲压模具。
3、热处理:热处理可以改善模具的硬度和强度,延长模具的使用寿命。
4、表面处理:主要手段有镀锌,进行阳极氧化,其采用的颜色有金色,银色,暗色和白色等,以便满足客户的不同需求。
四、冲压模具通用设计要求
1、冲压模具尺寸的选择:冲压模具尺寸的选择应该充分考虑材料的尺寸要求。
冲压模具设计

冲压模具设计1. 引言冲压模具是指用于进行金属冲压工艺的模具,用于在金属工件上施加力量以将其形状改变。
冲压模具设计在制造业中扮演着重要的角色,它直接影响到产品的质量和生产效率。
本文将介绍冲压模具设计的基本概念、设计过程和一些常用的设计原则。
2. 冲压模具设计的基本概念2.1 冲压工艺冲压工艺是指将薄板金属材料经过剪切、冲孔、弯曲等工艺加工,以获得所需形状和尺寸的工件。
冲压工艺具有高效、精确和重复性好等特点,广泛应用于汽车制造、电子设备和机械制造等行业。
2.2 冲压模具冲压模具是用于进行冲压工艺的工具,通常由上模、下模和导向装置等部件组成。
上模和下模通过导向装置进行定位,形成模腔,金属材料在模腔中受力产生变形,从而得到所需形状的工件。
3. 冲压模具设计的过程冲压模具设计通常包括以下几个步骤:3.1 零件分析在进行冲压模具设计之前,需要对待加工的零件进行分析。
分析包括对零件的形状、材料和尺寸等方面进行研究,以确定合适的冲压工艺和模具结构。
3.2 模具结构设计根据零件的形状和要求,设计冲压模具的结构。
模具结构设计包括上模、下模、导向装置、顶出装置等部分的设计,以保证模具具有足够的刚度和稳定性。
3.3 模具零部件设计根据模具结构设计的结果,对各个零部件进行详细设计。
包括绘制各个零部件的草图、确定材料和尺寸,以及进行结构优化和强度计算等工作。
3.4 工艺路线设计根据零件的要求和工艺特点,设计出适合的工艺路线。
包括冲孔位置和尺寸、切削方式、顶出顺序等方面的确定。
3.5 模具制造和试模根据模具设计的结果,进行模具制造和试模工作。
包括制造各个零部件、装配模具、进行调试和试模等过程。
通过试模,检验模具的设计和制造是否符合要求,提出改进和优化的意见。
4. 冲压模具设计的常用原则4.1 简化结构冲压模具的结构尽量简化,以减少制造成本和提高生产效率。
避免使用复杂的零部件和工艺过程,尽量采用标准件或通用部件,方便制造和维护。
冲压模具 毕业设计

冲压模具毕业设计冲压模具毕业设计导言:冲压模具是一种重要的工业制造工具,广泛应用于汽车、家电、电子产品等行业。
本文将探讨冲压模具的设计与应用,以及在毕业设计中的相关问题。
一、冲压模具的概述冲压模具是一种用于金属板材加工的工具,通过将金属板材置于模具中,施加压力使其形成所需的形状。
冲压模具分为单工位模具和多工位模具,根据产品的复杂程度和生产需求选择合适的模具类型。
二、冲压模具的设计原理1. 材料选择:冲压模具通常使用高强度、耐磨损的工具钢材料,以确保模具的寿命和稳定性。
2. 结构设计:冲压模具的结构应考虑产品的形状和尺寸,采用合理的分段设计,以便于加工和维护。
3. 工艺分析:在设计冲压模具时,需要进行工艺分析,确定每个工序的加工顺序和参数,以提高生产效率和产品质量。
4. 模具寿命预测:通过模具寿命预测分析,可以评估模具的使用寿命,及时进行维护和更换,以避免生产中的故障和延误。
三、冲压模具的应用领域1. 汽车制造:冲压模具在汽车制造中扮演着重要角色,用于生产车身、车门、引擎盖等零部件。
2. 家电制造:冲压模具广泛应用于家电制造过程中,如冰箱、洗衣机、空调等产品的外壳和内部零部件。
3. 电子产品:手机、电脑等电子产品的外壳和内部结构也需要通过冲压模具进行加工。
四、冲压模具在毕业设计中的应用1. 模具设计:在毕业设计中,学生可以选择冲压模具设计作为课题,通过学习和实践,掌握模具设计的基本原理和技术。
2. 模具制造:毕业设计中的冲压模具制造过程可以锻炼学生的实际操作能力,提高他们的制造技术水平。
3. 模具应用:通过将冲压模具应用于具体产品的制造中,学生可以了解模具在实际生产中的应用效果和问题,并提出改进方案。
五、冲压模具的发展趋势1. 自动化生产:随着科技的进步,冲压模具的生产过程将越来越趋向自动化,提高生产效率和质量。
2. 数字化设计:利用计算机辅助设计软件进行冲压模具设计,可以提高设计效率和精度。
3. 精密化加工:冲压模具的加工精度将继续提高,以满足高精度产品的需求。
冲压模具设计的方法与步骤
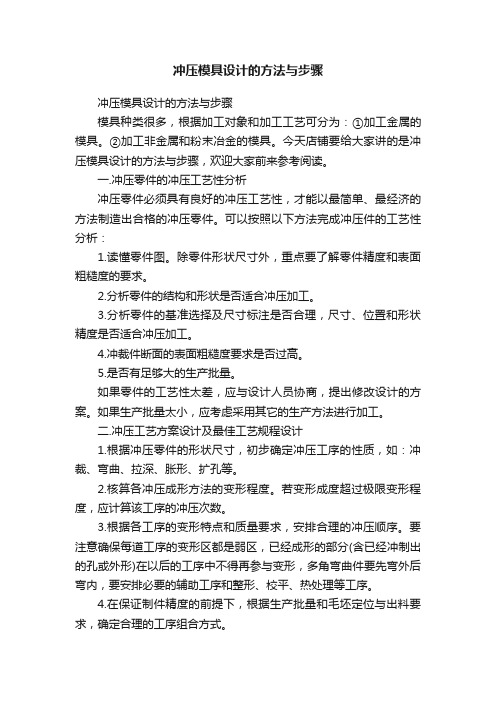
冲压模具设计的方法与步骤冲压模具设计的方法与步骤模具种类很多,根据加工对象和加工工艺可分为:①加工金属的模具。
②加工非金属和粉末冶金的模具。
今天店铺要给大家讲的是冲压模具设计的方法与步骤,欢迎大家前来参考阅读。
一.冲压零件的冲压工艺性分析冲压零件必须具有良好的冲压工艺性,才能以最简单、最经济的方法制造出合格的冲压零件。
可以按照以下方法完成冲压件的工艺性分析:1.读懂零件图。
除零件形状尺寸外,重点要了解零件精度和表面粗糙度的要求。
2.分析零件的结构和形状是否适合冲压加工。
3.分析零件的基准选择及尺寸标注是否合理,尺寸、位置和形状精度是否适合冲压加工。
4.冲裁件断面的表面粗糙度要求是否过高。
5.是否有足够大的生产批量。
如果零件的工艺性太差,应与设计人员协商,提出修改设计的方案。
如果生产批量太小,应考虑采用其它的生产方法进行加工。
二.冲压工艺方案设计及最佳工艺规程设计1.根据冲压零件的形状尺寸,初步确定冲压工序的性质,如:冲裁、弯曲、拉深、胀形、扩孔等。
2.核算各冲压成形方法的变形程度。
若变形成度超过极限变形程度,应计算该工序的冲压次数。
3.根据各工序的变形特点和质量要求,安排合理的冲压顺序。
要注意确保每道工序的变形区都是弱区,已经成形的部分(含已经冲制出的孔或外形)在以后的工序中不得再参与变形,多角弯曲件要先弯外后弯内,要安排必要的辅助工序和整形、校平、热处理等工序。
4.在保证制件精度的前提下,根据生产批量和毛坯定位与出料要求,确定合理的工序组合方式。
5.要设计两个以上的'工艺方案,并从质量、成本、生产率、模具的刃磨与维修、模具寿命及操作安全性等各个方面进行比较,从中选定一个最佳的工艺方案。
6.初步确定各个工序的冲压设备。
三.冲压零件毛坯设计及排样图设计1.按冲压件性质尺寸,计算毛坯尺寸,绘制毛坯图。
2.按毛坯性质尺寸,设计排样图,进行材料利用率计算。
要设计多种排样方案,经过比较选择其中的最佳方案。
冲压模具设计的一般流程
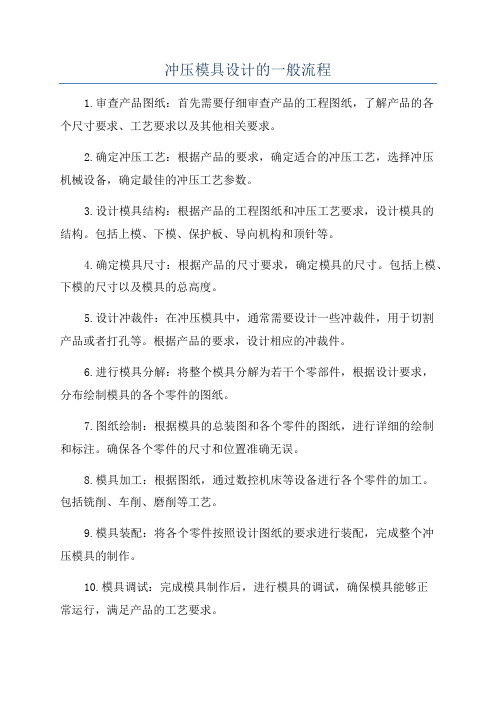
冲压模具设计的一般流程
1.审查产品图纸:首先需要仔细审查产品的工程图纸,了解产品的各
个尺寸要求、工艺要求以及其他相关要求。
2.确定冲压工艺:根据产品的要求,确定适合的冲压工艺,选择冲压
机械设备,确定最佳的冲压工艺参数。
3.设计模具结构:根据产品的工程图纸和冲压工艺要求,设计模具的
结构。
包括上模、下模、保护板、导向机构和顶针等。
4.确定模具尺寸:根据产品的尺寸要求,确定模具的尺寸。
包括上模、下模的尺寸以及模具的总高度。
5.设计冲裁件:在冲压模具中,通常需要设计一些冲裁件,用于切割
产品或者打孔等。
根据产品的要求,设计相应的冲裁件。
6.进行模具分解:将整个模具分解为若干个零部件,根据设计要求,
分布绘制模具的各个零件的图纸。
7.图纸绘制:根据模具的总装图和各个零件的图纸,进行详细的绘制
和标注。
确保各个零件的尺寸和位置准确无误。
8.模具加工:根据图纸,通过数控机床等设备进行各个零件的加工。
包括铣削、车削、磨削等工艺。
9.模具装配:将各个零件按照设计图纸的要求进行装配,完成整个冲
压模具的制作。
10.模具调试:完成模具制作后,进行模具的调试,确保模具能够正
常运行,满足产品的工艺要求。
11.产出产品:经过模具调试后,使用冲压机械设备进行批量生产,产出满足产品要求的冲压件。
12.模具维护和修理:冲压模具在使用过程中,需要进行定期的维护和修理,确保模具长时间稳定运行。
冲压模具设计规范
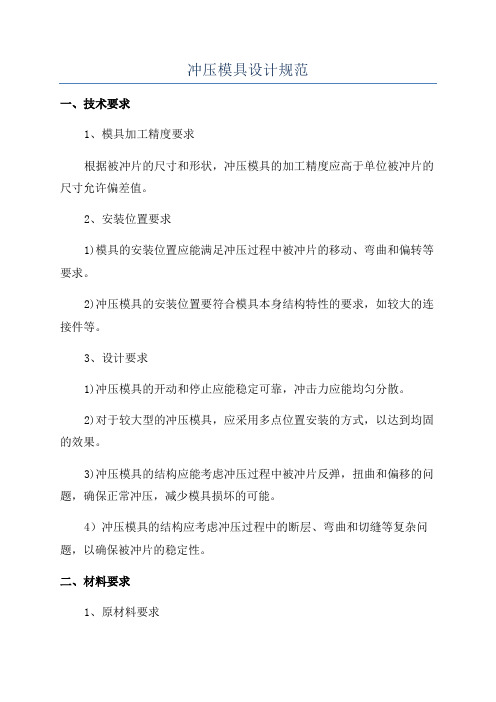
冲压模具设计规范
一、技术要求
1、模具加工精度要求
根据被冲片的尺寸和形状,冲压模具的加工精度应高于单位被冲片的尺寸允许偏差值。
2、安装位置要求
1)模具的安装位置应能满足冲压过程中被冲片的移动、弯曲和偏转等要求。
2)冲压模具的安装位置要符合模具本身结构特性的要求,如较大的连接件等。
3、设计要求
1)冲压模具的开动和停止应能稳定可靠,冲击力应能均匀分散。
2)对于较大型的冲压模具,应采用多点位置安装的方式,以达到均固的效果。
3)冲压模具的结构应能考虑冲压过程中被冲片反弹,扭曲和偏移的问题,确保正常冲压,减少模具损坏的可能。
4)冲压模具的结构应考虑冲压过程中的断层、弯曲和切缝等复杂问题,以确保被冲片的稳定性。
二、材料要求
1、原材料要求
1)冲压模具原材料应根据被冲片的材料特性、冲压工艺及模具的使用
寿命等因素确定,一般采用合金钢等。
2)冲压模具的原材料应考虑冲压过程中对其断裂、变形、冲击力以及
模具热处理等要求。
3)冲压模具的原材料质量应符合国家标准要求,保证模具的正常使用。
2、表面处理要求
冲压模具的表面处理要根据不同应用环境确定。
冲压模具设计

冲压模具设计1. 引言冲压模具是指在冲压加工过程中用于将金属材料加工成所需形状的专用模具。
冲压加工具有高效率、高精度、低材料消耗等优点,是广泛应用于汽车、家电、航空航天等制造行业的关键工艺。
冲压模具的设计是冲压加工过程中不可或缺的一环,在模具设计过程中需要考虑多个因素,包括材料的选择、模具结构的设计、加工工艺的确定等。
2. 冲压模具的基本概念和工作原理冲压模具主要由上模、下模和导向系统组成。
上模与下模配合后形成一个封闭的腔体,腔体中通过金属材料进行冲压加工,使其变形成所需要的形状。
冲压模具的工作原理是通过将上模与下模进行闭合,并施加一定的压力,使金属材料产生弹性变形或塑性变形,从而得到目标形状。
3. 冲压模具的设计步骤冲压模具的设计过程可以分为以下几个步骤:3.1 确定产品形状和尺寸在冲压模具设计之前,首先需要明确产品的形状和尺寸要求。
这可以从产品的图纸和技术要求中获取,也可以通过与产品设计师的沟通来确认。
3.2 材料选择根据产品的特性和工艺要求,选择适合的材料作为冲压模具的材料。
常见的冲压模具材料包括合金工具钢、高速钢等,具体选择需要综合考虑材料的强度、耐磨性、导热性等因素。
3.3 模具结构设计根据产品形状和尺寸要求,设计模具的结构。
模具一般分为上模和下模,根据需要还可以增加一些辅助结构,如导向柱、导向套等。
模具的结构设计需要考虑到产品的加工过程和模具的使用寿命,确保模具具有足够的强度和刚度。
3.4 模具零件设计根据模具的结构设计,对各个零部件进行详细设计。
主要包括上模、下模、导向柱、导向套、导向销等部件。
在设计过程中,需要考虑到各个零件的功能需求,如导向柱的导向精度、导向套的磨损等。
3.5 加工工艺确定根据产品的加工要求和模具的结构特点,确定模具的加工工艺。
主要包括不同零件的加工顺序、加工方法、加工设备的选择等。
加工工艺的确定需要综合考虑加工效率、加工精度和加工成本等因素。
4. 冲压模具设计的注意事项在冲压模具设计过程中,需要注意以下几个方面:•结构合理性:冲压模具的结构应尽可能简洁,确保模具的强度和刚度满足要求;同时要尽量避免零部件的干涉和冲突,以提高模具的稳定性和寿命。
冲压模具设计

冲压模具设计1. 简介冲压模具是冲压工艺中的重要工具,用于将金属板材通过冲击和压力形成所需形状的工件。
冲压模具的设计和制造直接影响着冲压工艺的质量、效率和成本。
本文将介绍冲压模具设计的基本原理和步骤,帮助读者了解冲压模具设计的要点。
2. 冲压模具设计的基本原理冲压模具设计的基本原理是根据产品的形状和尺寸要求,确定合理的冲压工艺,并设计出相应的模具结构。
冲压模具包括上模和下模,上模安装在冲床上方,下模则安装在冲床的工作台上。
冲压过程中,上模通过冲击和压力作用于工件,使得工件在下模的引导下形成所需形状。
3. 冲压模具设计的步骤3.1 确定产品要求冲压模具设计的第一步是确定产品的形状和尺寸要求。
根据产品的技术要求和设计图纸,确定产品的尺寸、公差和表面质量等指标。
3.2 确定冲压工艺冲压工艺的确定包括冲床的选择、冲孔顺序、冲头的选择等。
根据产品的形状和材料的特性,选择合适的冲压工艺,确保冲压过程中能够达到理想的成形效果。
3.3 设计模具结构根据产品的形状和冲压工艺,设计模具的结构。
模具结构主要包括上模、下模和导向装置等。
上模和下模的形状和尺寸应根据产品的形状和尺寸要求确定,确保能够正确引导工件形成所需形状。
3.4 设计冲头和冲具根据冲压工艺的要求,设计冲头和冲具。
冲头的形状和尺寸应根据冲床的要求和产品的形状确定,确保能够正确施加冲击和压力作用于工件。
冲头的材料应选择具有耐磨性和强度的材料,以确保其使用寿命满足要求。
3.5 完成模具设计根据以上步骤完成模具的设计,包括模具结构和冲头、冲具的设计图纸。
设计图纸应包含模具的三维模型、尺寸要求和加工工艺等信息,以便于制造和检验。
4. 冲压模具设计的要点•合理选择冲压工艺,确保冲压过程能够满足产品的成形要求。
•设计稳定、刚性良好的模具结构,以确保冲压过程中模具的稳定性和使用寿命。
•选择耐磨性和强度好的材料制造冲头和冲具,以确保其使用寿命满足要求。
•设计合理的导向装置,确保工件能够正确引导并形成所需形状。
冲压模具设计标准
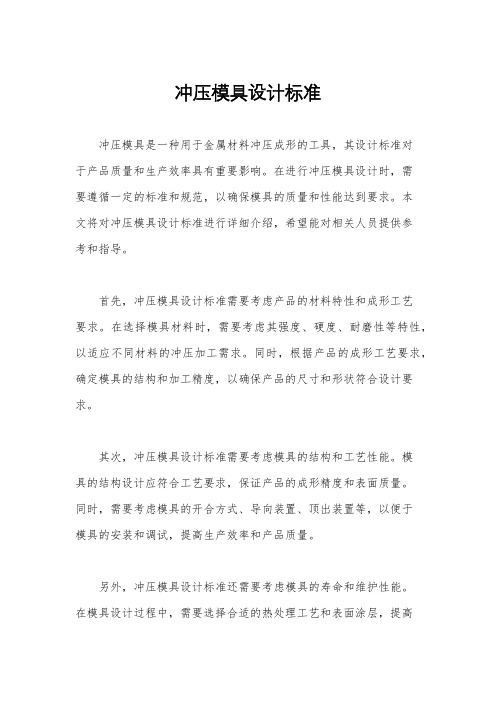
冲压模具设计标准冲压模具是一种用于金属材料冲压成形的工具,其设计标准对于产品质量和生产效率具有重要影响。
在进行冲压模具设计时,需要遵循一定的标准和规范,以确保模具的质量和性能达到要求。
本文将对冲压模具设计标准进行详细介绍,希望能对相关人员提供参考和指导。
首先,冲压模具设计标准需要考虑产品的材料特性和成形工艺要求。
在选择模具材料时,需要考虑其强度、硬度、耐磨性等特性,以适应不同材料的冲压加工需求。
同时,根据产品的成形工艺要求,确定模具的结构和加工精度,以确保产品的尺寸和形状符合设计要求。
其次,冲压模具设计标准需要考虑模具的结构和工艺性能。
模具的结构设计应符合工艺要求,保证产品的成形精度和表面质量。
同时,需要考虑模具的开合方式、导向装置、顶出装置等,以便于模具的安装和调试,提高生产效率和产品质量。
另外,冲压模具设计标准还需要考虑模具的寿命和维护性能。
在模具设计过程中,需要选择合适的热处理工艺和表面涂层,提高模具的耐磨性和使用寿命。
同时,需要考虑模具的易损件和易损部位,设计合理的维护通道和更换方式,以便于模具的维护和保养。
最后,冲压模具设计标准还需要考虑模具的安全性和可靠性。
在模具设计过程中,需要考虑模具的安全保护装置、操作人员的人身安全和设备的可靠性,以确保生产过程安全稳定。
综上所述,冲压模具设计标准涉及产品的材料特性、成形工艺要求、模具的结构和工艺性能、模具的寿命和维护性能、模具的安全性和可靠性等方面。
只有严格按照设计标准进行模具设计,才能确保模具的质量和性能达到要求,提高生产效率,降低生产成本,保证产品质量,提升企业竞争力。
希望本文能够对冲压模具设计提供一定的参考和指导,促进模具设计水平的提高。
冲压模具设计课题简介

冲压模具设计课题简介冲压模具设计是机械制造工程中的一项重要技术,涉及到金属板材的加工和成型。
冲压模具设计的主要目标是确保在特定的生产条件下,通过一系列的工艺步骤,将原材料转化为具有所需形状、尺寸和质量的成品。
一、课题背景与意义随着制造业的快速发展,冲压模具设计在汽车、电子、家电、航空航天等领域得到了广泛应用。
由于冲压模具设计直接影响到产品的质量、生产效率和成本,因此对于模具设计师来说,掌握冲压模具设计的基本原理和方法至关重要。
本课题旨在介绍冲压模具设计的基本概念、原理和方法,通过实际案例的分析,使读者深入了解冲压模具设计的全过程。
同时,本课题还探讨了冲压模具设计中的一些常见问题及其解决方案,以帮助读者在实际工作中避免类似问题的发生。
二、研究内容与方法研究内容本课题将重点介绍以下内容:(1)冲压模具的基本结构及各部件功能;(2)冲压模具设计的基本原理和方法,包括冲裁、弯曲、拉伸等基本工艺;(3)冲压模具设计的步骤和方法,包括模具结构设计、材料选择、热处理工艺等;(4)冲压模具设计中常见的问题及其解决方案;(5)冲压模具设计的实例分析。
研究方法本课题将采用以下研究方法:(1)理论分析:通过对冲压模具设计的基本原理和方法进行深入研究,建立相应的理论模型;(2)实验研究:通过实验验证理论模型的正确性,并探索最佳的工艺参数;(3)案例分析:通过对实际案例的分析,使读者深入了解冲压模具设计的全过程;(4)归纳总结:通过对研究内容的归纳总结,提出相应的结论和建议。
三、预期成果与价值本课题预期能够为读者提供一套完整的冲压模具设计理论和方法,并通过实际案例的分析,使读者深入了解冲压模具设计的全过程。
同时,本课题还能够为读者在实际工作中提供一些实用的解决方案和建议,以帮助其更好地完成冲压模具设计工作。
四、研究计划与进度本课题的研究计划分为以下几个阶段:第一阶段:收集和整理相关文献资料,对冲压模具设计的基本原理和方法进行深入研究;第二阶段:进行实验研究,验证理论模型的正确性,并探索最佳的工艺参数;第三阶段:通过实际案例的分析,深入了解冲压模具设计的全过程;第四阶段:对研究内容进行归纳总结,提出相应的结论和建议。
冲压模具设计步骤

冲压模具设计步骤第一步呢,得先把产品的要求搞清楚。
就像你要给一个人做衣服,得知道人家想要啥样的衣服风格、尺寸啥的。
对于冲压模具,你得知道要冲压出来的零件长啥样,尺寸精度要求多高,是啥材质的,这些信息就像设计的指南针 。
第二步,开始构思模具的大概结构啦。
这就好比搭积木,你得想好用哪些“积木块”,也就是模具的各个部件。
是用单工序模呢,还是复合模或者级进模。
这得根据产品的形状、产量这些因素来决定哦。
要是产品形状简单,产量又不大,单工序模可能就够啦;要是产量大,形状复杂,复合模或者级进模可能更合适呢。
第三步,计算各种参数。
这可不能马虎呀,就像厨师做菜得掌握好调料的量一样。
像冲压力得算准咯,这关系到模具的强度能不能承受。
还有模具的闭合高度,也得精心计算,不然和冲压设备不匹配可就麻烦啦。
第四步,画草图。
这就像是给模具画个简单的画像,把各个部件的位置关系大概表示出来。
草图不用画得特别精美,但得能让人看明白各个部分是咋回事。
第五步,详细设计。
这时候就像给画像上颜色、加细节啦。
把每个部件的尺寸、形状都精确地确定下来,还要考虑到加工工艺性哦。
比如说,有些形状在理论上可以设计出来,但是加工起来特别困难,那可不行,得调整设计,让它既满足功能要求,又好加工。
第六步,选择合适的模具材料。
这就像给战士选武器一样重要。
不同的冲压工艺、不同的产品要求,得选不同的材料。
要是冲压硬的材料,那模具材料就得更耐磨、更抗压才行呢。
最后呀,就是审核校对啦。
自己检查完了,最好再找个有经验的人帮忙看看,就像考试做完题要检查一样。
看看有没有啥不合理的地方,有没有计算错误啥的。
冲压模具设计岗位职责
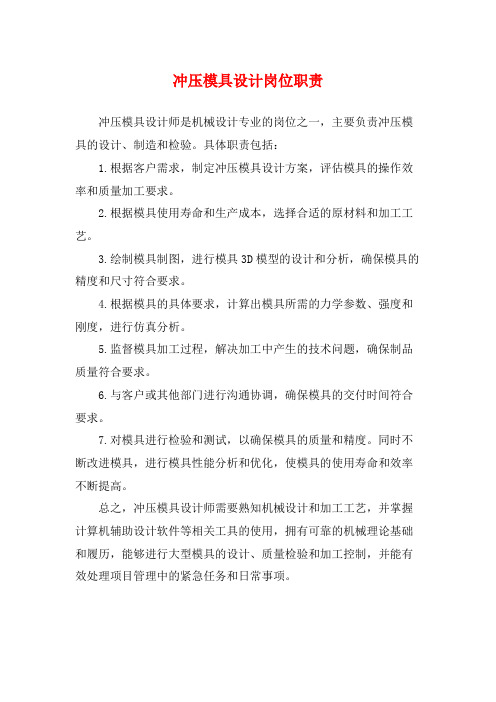
冲压模具设计岗位职责
冲压模具设计师是机械设计专业的岗位之一,主要负责冲压模具的设计、制造和检验。
具体职责包括:
1.根据客户需求,制定冲压模具设计方案,评估模具的操作效率和质量加工要求。
2.根据模具使用寿命和生产成本,选择合适的原材料和加工工艺。
3.绘制模具制图,进行模具3D模型的设计和分析,确保模具的精度和尺寸符合要求。
4.根据模具的具体要求,计算出模具所需的力学参数、强度和刚度,进行仿真分析。
5.监督模具加工过程,解决加工中产生的技术问题,确保制品质量符合要求。
6.与客户或其他部门进行沟通协调,确保模具的交付时间符合要求。
7.对模具进行检验和测试,以确保模具的质量和精度。
同时不断改进模具,进行模具性能分析和优化,使模具的使用寿命和效率不断提高。
总之,冲压模具设计师需要熟知机械设计和加工工艺,并掌握计算机辅助设计软件等相关工具的使用,拥有可靠的机械理论基础和履历,能够进行大型模具的设计、质量检验和加工控制,并能有效处理项目管理中的紧急任务和日常事项。
冲压工艺及模具设计(3篇)

第1篇一、引言冲压工艺是一种常见的金属成形工艺,广泛应用于汽车、家电、电子、航空等行业。
冲压工艺具有生产效率高、成本低、精度高、尺寸稳定性好等优点。
模具是冲压工艺中的关键设备,其设计质量直接影响到冲压产品的质量和生产效率。
本文将对冲压工艺及模具设计进行简要介绍。
二、冲压工艺概述1. 冲压工艺原理冲压工艺是利用模具对金属板材施加压力,使其产生塑性变形,从而获得所需形状、尺寸和性能的零件。
冲压工艺的基本原理是金属的塑性变形,即金属在受到外力作用时,产生塑性变形而不破坏其连续性的过程。
2. 冲压工艺分类(1)拉深:将平板金属沿模具凹模形状变形,形成空心或实心零件的过程。
(2)成形:将平板金属沿模具凸模形状变形,形成具有一定形状的零件的过程。
(3)剪切:将平板金属沿剪切线剪切成一定形状和尺寸的零件的过程。
(4)弯曲:将平板金属沿模具凸模形状弯曲,形成具有一定角度的零件的过程。
三、模具设计概述1. 模具设计原则(1)满足产品精度和尺寸要求:模具设计应保证冲压产品具有高精度和尺寸稳定性。
(2)提高生产效率:模具设计应优化工艺流程,减少不必要的加工步骤,提高生产效率。
(3)降低生产成本:模具设计应选用合适的材料,降低模具成本。
(4)确保模具寿命:模具设计应考虑模具的耐磨性、耐腐蚀性等性能,延长模具使用寿命。
2. 模具设计步骤(1)产品分析:分析产品的形状、尺寸、材料等,确定模具设计的基本要求。
(2)工艺分析:根据产品形状和尺寸,确定冲压工艺类型,如拉深、成形、剪切、弯曲等。
(3)模具结构设计:根据工艺要求,设计模具结构,包括凸模、凹模、导向装置、压边装置等。
(4)模具零件设计:根据模具结构,设计模具零件,如凸模、凹模、导向装置、压边装置等。
(5)模具加工:根据模具零件设计,进行模具加工。
(6)模具调试:完成模具加工后,进行模具调试,确保模具性能符合要求。
四、冲压工艺及模具设计要点1. 冲压工艺要点(1)合理选择材料:根据产品形状、尺寸、性能要求,选择合适的金属材料。
- 1、下载文档前请自行甄别文档内容的完整性,平台不提供额外的编辑、内容补充、找答案等附加服务。
- 2、"仅部分预览"的文档,不可在线预览部分如存在完整性等问题,可反馈申请退款(可完整预览的文档不适用该条件!)。
- 3、如文档侵犯您的权益,请联系客服反馈,我们会尽快为您处理(人工客服工作时间:9:00-18:30)。
目录一、工艺性分析 (2)二、工艺方案的确定 (3)三、模具结构形式的确定 (3)四、工艺设计 (3)(1)计算毛坯尺寸 (3)(2)画排样图 (3)(3)计算材料利用率 (4)(4)计算冲压力 (5)(5)初选压力机 (6)(6)计算压力中心 (7)(7)计算凸凹模刃口尺寸 (8)五、模具结构设计 (8)(1)模具类型的选择 (8)(2)定位方式的选择 (8)(3)凹模设计 (8)(4)凸模设计 (9)(6)选择模架及确定其他冲模零件尺寸 (10)六、装配图和零件图 (12)七、结束语 (12)致谢 (13)参考文献 (14)设计内容一、工艺性分析此工件只有落料和冲孔两个工序。
材料为08F,具有良好的冲压性能,适合冲裁。
工件结构相对简单。
有一个Φ6的孔和两个非圆孔:孔与孔.孔与边缘之间的距离也满足要求,最小壁厚为4mm(小孔与边缘之间的距离)。
工件的尺寸全部为自由公差,可看作IT14级,尺寸精度较低,普通冲裁完全能满足要求。
但应注意::图1(1)有一定批量,应重视模具材料和结构的选择,保证一定的模具寿命。
(2)冲裁间隙,凸凹模间隙的确定应符合制件的要求。
(3)各工序凸凹模动作行程的确定应保证各工序动作稳妥、连贯。
二、工艺方案确定该工件包括落料.冲孔两个基本工序,可有以下三种方案:方案一:先落料,后冲孔.采用单工序模生产.方案二:落料------冲孔复合冲压.采用复合模生产.方案三:冲孔-------落料级进冲压.采用级进生产.方案一模具结构简单,但需要两道工序两副模具,成本高而生产效率低,难以满足中批量生产要求,方案二只需要一副模具,工件精度及生产效率都能满足,模具轮廓尺寸较小,制造成本低。
方案三也只需一副模具,生产效率高,操作方便,工件精度也能满足要求。
通过对上述三种方案的分析比较,该工件冲压生产采用方案二为佳。
三、模具结构形式的确定。
因制件材料较薄,为保证制件平整,采用弹性卸料装置。
为方便操作和取件可初选双立柱可倾压力机,横向送料。
采用圆柱头式挡料销。
综上所述:由《冲压手册》[1]表5—3,5—8选用弹性卸料横向送料典型组合结构形式,后侧导柱滑动导向模架。
四、工艺设计。
(1)计算毛坯尺寸。
制件长尺寸如图一。
(2)排样方式的确定及尺寸确定。
排样方式的选择方案一:有废料排样沿冲件外形冲裁,在冲件周边都留有搭边。
冲件尺寸完全由冲模来保证,因此冲件精度高,模具寿命高,但材料利用率低。
方案二:少废料排样因受剪切条料和定位误差的影响,冲件质量差,模具寿命较方案一低,但材料利用率稍高,冲模结构简单。
方案三:无废料排样冲件的质量和模具寿命更低一些,但材料利用率最高。
通过上述三种方案的分析比较,综合考虑模具寿命和冲件质量,该冲件的排样方式选择方案一为佳。
考虑模具结构和制造成本有废料排样的具体形式选择直排最佳。
制件排样如图2:(3)计算材料利用率η。
由参考书《冲压手册》[2] P45表2-18表2-18 最小工艺搭边值(单行排列) (单位为mm)材料厚度t圆件及r >2t 的圆角矩形边长L ≤50矩形边长L >50或圆角 r ≤2t工件间a 1侧边a 工件间a 侧边a 1 工件间a 1 侧边a 0.25以下 1.8 2.0 2.2 2.5 2.8 3.0 0.25~0.5 1.2 1.5 1.8 2.0 2.2 2.5 0.5~0.8 1.0 1.2 1.5 1.8 1.8 2.0 0.8~1.2 0.8 1.0 1.2 1.5 1.5 1.8 1.2~1.6 1.0 1.2 1.5 1.8 1.8 2.0 1.6~2.01.21.51.82.52.02.2选a=1.5mm,a 1=1.2mm.由《冲压工艺学》P45,无侧压装置有:条料宽度 0ΔB = [D+2 (a+Δ)+c1)]0 -Δ 导尺间距离 S=b+c1=D+2(a+Δ+c1) 其中:b —条料板公称宽度(mm )D —冲裁件垂直于送料方向的尺寸(mm )a—侧搭边的最小值,见表2-18(mm)c1—导尺与最宽条料之间的单面小间隙,其值见表2-21(mm)Δ—条料宽度的单向偏差,见表2-19、表2-20(mm)查表2-19,有Δ=0.6mm,表2-21,有c1=0.5mm则;B = D+2×(a+Δ)+c1)= 50.3 mm条料步距S=14+a1=15.2 mm.查参考书《冲压手册》P506表8-12,选板料规格为600mm×1200mm×1.2mm。
由零件图算得一个零件的面积为S=14×[48-2×(14-7×1.732)]+(14×14×3.14÷6-7×1.732×14÷2) ×2-3.14×3×3-5×2×2-3.14×2×2=510.7㎜2采用横裁时,剪切条料尺寸为50.3。
一块板可裁的条料为23,每条可冲零件个数39个零件。
则一块板材的材料利用率为:η=(n×A0/A)×100﹪η=(23×39×510.7/600×1200)×100﹪=63.6﹪采用纵裁时,剪切条料尺寸为50.3。
一块板可裁的条料为11,每条可冲零件个数78个零件,则一块板材的材料利用率为:η=(n×A0/A)×100﹪η=(11×78×510.7/600×1200)×100﹪=60.9﹪根据以上分析,横裁比纵裁时的板材材料利用率高,因此采用横裁。
每块裁成50.3mm × 1200mm ×1.2mm的条料。
(4)计算冲压力。
1)、冲裁力的计算用平刃冲裁时,其冲裁力F一般按下式计算:F=KLt τb式中F—冲裁力;L—冲裁周边长度;t—材料厚度;τb—材料抗剪强度;K—系数,系数K是考虑到实际生产中,模具间隙值的波动和不均匀,刃口磨损、板料力学性能和厚度波动等原因的影响而给出修正系数,一般取K=1.3。
计算冲裁件轮廓尺寸L=[48-(14-7×1.732) ×2] ×2+3.14×2×14÷3=117.8mm 由参考书《冲压手册》查得08F的抗剪强度为τb=300MPa由参考书《冲压手册》[2]表2-37表2-37 卸料力、推件力和顶件力系数则:采用弹性卸料装置冲裁力为F总= F冲+F顶+ F卸=1.3Ltτb=55130.4N①F冲裁②F推=n K推F落由表查出K推=0.055,查得凹模刃口直壁高度h=8mm,则n=h/t=6.67F推=nK推F落=20224.6N顶件力:F2=K2F卸料力:F3=K3F查表:K2 =0.06 K3 =0.04F2=0.06×55130.4=3307.824NF3=0.04×55130.4=2205.216N总冲裁力F总=F冲+F顶+ F卸=55130.4+3305.824+2205.216=60644.048N=60.6KN (5)初选压力机。
冲模闭合高度H(Hmax-5)≥H ≥(Hmin+10) 165mm ≥H ≥140mm(6)计算凸凹模刃口尺寸。
对于形状复杂或薄材料的冲裁件,为了保证凸凹模之间的间隙值,并使其分布均匀,必须采用配合加工,这种方法是先加工好凸模或凹模作为基准件,然后以此基准件为标准加工凹模或凸模,使二者保持一定间隙。
外形48mm ,14mm 由落料获得 圆孔Φ6及两个非圆孔由冲孔同时获得 查表:Zmin =0.126mm ,Zmax =0.180mm磨损系数x 尺寸025.048-,28±0.2,5±0.12,R ﹢0.2502 x=0.75 尺寸043.014-,R 043.014- x=0.5 尺寸Φ16.006+ x=1基准制造偏差δ 尺寸5±0.12 δ=0.03 尺寸28±0.2 δ=0.05 尺寸025.048- δ=0.0325尺寸Φ16.006+ δ=0.04尺寸043.014-,R 043.014- δ=0.1075尺寸R ﹢0.2502 δ=0.0625 磨损后变大的尺寸(A 类)有025.048- ,043.014-,R 043.014- j A =(max A -x Δ)δ0+1A =(48-0.75*0.25)0.06250+=47.81250.06250+ 2A =(14-0.5*0.43)0.10750+=47.81250.10750+3A =(14-0.5*0.43)0.10750+=47.81250.10750+磨损后变小的尺寸(B 类)有Φ16.006+,5±0.12 ,R ﹢0.252 j B =(min B +x Δ)0δ-1B =(6+1*0.16)004.0-=6.16004.0- 1B =(5+0.75*0.24)003.0-=5.18003.0- 1B =(2+0.75*0.25)00625.0-=2.187500625.0-孔距尺寸:Ld =L ±Δ/8=28±0.05 (7)计算压力中心。
由于此冲裁件属于中心对称件,故其压力中心位于冲裁件轮廓图形的几何中心。
五、模具结构设计:(1)模具类型的选择由冲压工艺分析可知,需落料冲孔两个工序,所以模具类型落料冲孔复合模。
(2)定位方式的选择因为该模具采用的是条料,控制条料的送进方向采用导料板,无侧压装置。
控制条料的送进步距采用挡料销。
而第一件的冲压位置因为条料长度有一定余量,可以靠操作工目测来定。
(3)凹模设计。
①凹模结构形式因制件材料简单,总体尺寸不大,选用整体式矩形凹模较为合理。
因生产批量较大,由文献《冲压手册》[1]表3-5选用T10A 为凹模材料。
由该文献表2-39得凹模壁厚c=30mm 。
凹模高度h=22mm 。
②凹模刃口与边缘的距离由文献《冲压手册》P68表2—41得a=33mm ③凹模长度: L=s1+2s2s1 -----送料方向凹模刃壁间最大距离 14mms2 -----送料方向凹模刃壁到凹模边缘最小距离33mmL=80mm凹模宽度:B=s+(2.5~4)cs----垂直于送料方向的凹模刃壁间最大距离48mmc----凹模厚度30mmB=123~168mm 取B=125mm凹模轮廓尺寸为80mm×123mm×30mm⑷凸模设计①凸模的结构形式与固定方法落料凸模刃口尺寸为非圆形,为了便于凸模和固定板的加工,将落料凸模设计成台阶式。
为了保证强度、刚度及便于加工与装配,圆形凸模常做成圆滑过渡的阶梯形,小端圆柱部分。