冲裁中常见不良
冲压入门知识
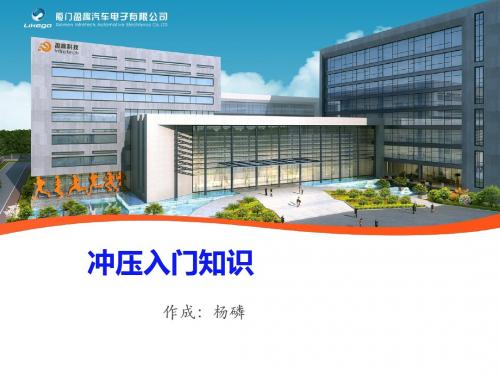
5.少孔→冲头折断,冲头长度不→凸凹模R角半径过小,压边力过大,材料成型性能差或材料尺寸 偏大,凸凹模间隙小,润滑不当。定位不准、凸凹模R角或拉伸筋不顺 拉毛等。 2.起皱→凸凹模R角半径过大,压边力过小,材料尺寸偏小。凸凹模间隙
过大;润滑过甚;定位不准;拉伸筋布置不良,高度不够等。
12
Thank you
我们期望与目标
Our expectation and goal
快速成长、持续改进,成为最好的合作伙伴
Grow quickly, improve continuously,be the best partner for our customers.
13
3
4
5
6
7
8
9
常见不良——落料冲孔
1.毛刺过大→凸凹模间隙过大或过小,刃口磨损、导向精度差、凸凹模不同心等。 2.变形→孔距太小,压料板与凹模型面配合不好,间隙过大等。 3.表面划伤→操作时有拖、拉等现象。板料在剪切过程中划伤等。 4.尺寸不符→上料不到位、定位装置损坏或松动、位置窜动等。
冲压入门知识
作成:杨磷
1
冲压的定义
利用安装在压力机上的冲模对材料施加压力,使其产生分离或塑形 性变形,从而获得所需要的零件。
冲压的工艺流程
开卷线→大件清洗涂油、小件开卷剪切→冲压生产线→安装模具→ 调试首件合格→批量生产→防锈处理→入库
2
冲压的基本工序
• 冲裁:使板料实现分离的冲压工序(包括冲孔、落料、修边等) • 弯曲:将板料沿弯曲线弯成一定的角度和形状。 • 拉伸:将平面板料编成各种开口空心零件,或把空心件的形状、 尺寸作进一步的改变。 • 局部成形:用各种不同性质的局部变形来改变毛坯或冲压件(包 括翻边、膨胀、校平、整形)
连续模常见的设计缺陷

连续模常见的设计缺陷一. 冲裁中常见不良1. 跳屑2. 金属丝3. 冲子蹦4. 模仁裂与堵料5. 接刀毛头6. 尺寸超差7. 压板断8. 啃刀口9. 接刀设计错(粗定位无效果)二.折弯成形常见不良1.违反先压料后成形原则2.冲子断差太大3.框口磨损4.拉毛5.两次折弯折弯线设计错6.折弯成形尺寸不稳定7.成形尺寸不到位8.浮动模仁定位段太短,晃动幅度大9.浮动模仁或Lifter,易跳出来(危险性大),或者设计强度太差10.KINK的成形问题11.尺寸不良的几个因素:1)角度2)圆角3)展开长度4)折弯线处之逃料三.整形机构1. 斜面整形的适用范围及常见问题点2. 摆块整形机构的适用范围及常见问题点3. 斜面整形机构的适用范围及常见问题点4. 一次折弯整形机构的局限性四.翻边打卡荀等起伏成形工站常见问题点1. 翻边口部裂纹2. 翻边高度小3. 扭力不足4. 翻边起皱5. 卡荀断6. 起伏成形对相邻已成形尺寸的影响7. 撕破成形高度偏低五.下料时常见问题:(下料不畅)1. 废料留在模面(821-762N1)2. 下料不畅,加吹气,顶杆3. 混料4. 下产品改为下废料(吹气方式)六.抽引中常见问题点1. 毛坯太大2. 毛坯太小3. 抽引拉裂4. 抽引起皱5. 壁部拉毛6. Carry相互挤压7. 定位不可靠8. 大肚子七.结构设计中常见问题:1. 定位针固定在冲子固定板上2. 剥料套设计不良3. 料条定位不好(追加导板)4. 压板,弹簧断裂(改冲子固定方式)5. 背板螺丝太靠外6. 抽引第一抽不分开7. 缺少整形工站8. 定位针太少,太细9. Lifter无爬坡(模仁太短)八.料条设计问题:1. 刚性太差2. 前后工序排配不合理3. 粗定位无效4. 定位针孔太靠后九.几种常见的典型机构十.其它常见问题:1. 大平面的平面度问题2. SMT PAD的共面度问题3. 铆合中的一些问题及解决措施4. 料带式产品的扇形(波浪形)第一章冲裁中常见不良一.跳屑一)跳屑的几种情况:1.切边时的跳屑:原因:系不完整的冲孔废料难以有效卡在模仁里,故易跳屑改善措施:修边结构复杂化2.小方孔,小圆孔跳屑原因:1)间隙太大2)有较多的油3)料太薄改善措施:1)收紧间隙2)减少用油3)加向下吹气,在废料下面形成负压4)设变模仁加工方式(改为PG加工),提高刃口段光洁度5)对冲子结构作重新设计6)对铁材产品模具备品须退磁干凈)3.细小废屑:(常见于有撕破的模具,有重切时尤为时显,821-220模)4.大片废屑的跳屑原因: 同2改善措施:1)加顶杆2)加吹气3)对其形状复杂化(和carry相连一侧)5.其它状况的跳屑:原因:工序排配设计不合理改善措施:重新调整工序排配(重新设计接刀)二)跳屑的危害:1.产生模痕,压伤等不良2.对间歇性跳屑,不易发现,极易流出不良品3.维修不易(常采用异形冲子,刃口披覆等有损备品寿命和产品断面质量的方式)致生产效率和稼动率低4.不良品产生时常需大量的人工进行挑选二.金属丝一)危害:1.组装成成品后,极易造成短路(SHORT),是要绝对禁止的严重一种不良2.脱落时易在产品上产生模痕3.当有发生时须耗费大量的人力对其重工二)产出原因:常见于有撕破的模具,比如:1.先向下撕破,后又被向上拍平,撕破切口处产生二次挤压,形成金属丝2.先向一个方向撕破后又向相反方向折弯成形3.一次撕破折弯不到位时,让设计不合理三)改善措施:1.撕破处后面工站闪开(放电)避免撕破和被反复拍打。
冲压过程中容易产生的各种缺陷分析及预防措施

A.孔的位置尺寸不对,(弯曲受拉变薄)措施:
♦严格控制弯曲半径,弯曲角度以及材料厚度;对材料的中性层进行修整和凸模进入凹模 的深度以及凸凹模适当均匀。
B孔不同心原因
♦弯曲高度不够
♦毛坯发生滑动
♦回弹
♦弯曲平面上出现起伏现象 措施:
♦确保左右弯曲高度正确。
B.多角弯曲使弯曲部位变薄加大,为了减少变薄尽量采用单角多工序的压弯办法。
C.采用尖角凸模时凸模进入凹模太深使弯曲部位厚度明显减少。
十二.拉深件凸缘在拉深过程中起皱的原因及预防 原因:凸缘部位压边力太小,无法抵制过大的切向压应力;而引起切向变形,因而失去稳 定后形成皱纹。材料较薄也较易形成皱纹
措施:
E.凸凹模间隙不应太小,间隙太小会引起变薄擦伤。在冲压过程中要时刻检查模具的间隙 的变化情况。
F.凸模进入凹模的深度太大时会产生零件表面擦伤,因此在保证不受回弹的影响的情况下, 应适当的减少凸模进入凹模的深度。
G.为了使制件符合精度的要求往往使用在底部压料的弯曲模,则在弯曲时压料板上的弹簧,
定位销孔、托板和退料孔等都会压制成压痕,故应给予调整。
十七.拉深件表面产生拉痕的原因及预防措施 原因:
A.凸模或凹模表面有尖利的压伤,致使工件表面相应的产生拉痕,此时应将压伤表面进行 修磨或抛光即可。
B.凸凹模间隙过小或者间隙不均匀,使其在啦深时工件表面被刮伤,此时应修整凸凹模间 隙直至合适为止。
C.凹模圆角表面粗糙,拉深时工件表面被刮伤,此时应将凹模圆角半径进行修磨打光;
A.材料的回弹造成产品不合格
减少回弹的措施:
♦.选用弹性模数大屈服点小的力学性能较稳定的冲压材料;
♦.增加校正工序,采用校正弯曲代替自由弯曲;
冲床常见故障及其处理方法大全
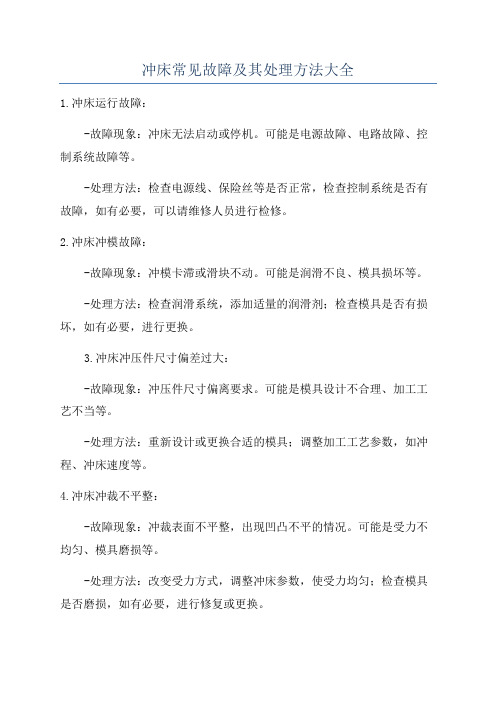
冲床常见故障及其处理方法大全1.冲床运行故障:-故障现象:冲床无法启动或停机。
可能是电源故障、电路故障、控制系统故障等。
-处理方法:检查电源线、保险丝等是否正常,检查控制系统是否有故障,如有必要,可以请维修人员进行检修。
2.冲床冲模故障:-故障现象:冲模卡滞或滑块不动。
可能是润滑不良、模具损坏等。
-处理方法:检查润滑系统,添加适量的润滑剂;检查模具是否有损坏,如有必要,进行更换。
3.冲床冲压件尺寸偏差过大:-故障现象:冲压件尺寸偏离要求。
可能是模具设计不合理、加工工艺不当等。
-处理方法:重新设计或更换合适的模具;调整加工工艺参数,如冲程、冲床速度等。
4.冲床冲裁不平整:-故障现象:冲裁表面不平整,出现凹凸不平的情况。
可能是受力不均匀、模具磨损等。
-处理方法:改变受力方式,调整冲床参数,使受力均匀;检查模具是否磨损,如有必要,进行修复或更换。
5.冲床噪音过大:-故障现象:冲床运行时噪音过大。
可能是润滑不良、零部件磨损等。
-处理方法:检查润滑系统,添加适量的润滑剂;检查零部件是否需要更换,如有必要,更换磨损的零部件。
6.冲床冲压速度过慢:-故障现象:冲床冲压速度明显减慢。
可能是油压不足、电机故障等。
-处理方法:检查油压系统,确保油压正常;检查电机是否正常工作,如有必要,更换电机。
7.冲床冲床速度不稳定:-故障现象:冲床冲床速度时快时慢。
可能是电路故障、控制系统故障等。
-处理方法:检查电路连接是否正常,检查控制系统是否有故障,如有必要,可以请维修人员进行检修。
8.冲床冲床精度不高:-故障现象:冲压件尺寸偏差较大。
可能是冲模精度不高、冲床压力不稳定等。
-处理方法:重新设计或更换合适的冲模;调整冲床压力参数,使其稳定。
冲压生产中不良产品产生的原因及防止对策

.. 料 被 冲 子 带 上来 则 称 为带 废料 ;堵 废 料 则 是 由于 冲压 时 废 料 涨 2 1 6设 计人 员的经验 不足 设计时刀 口的间隙不合理 , 或单面切料 , 另一面悬空 , 而未 大 或 细 屑 粘 在人 块侧 壁 上 而 卡 住废 料 ,废 料 不 能 顺 利 从 人 块 孔
● —
£ —- L —
l 刚 吾
材 料 材 质 比较 软 的 ,如 黄 铜 、青铜 、铝 材 等 更 容 易 产 生 细
模 具 中的 跳 屑 、跳 废 料 与 堵 废 料 的 现象 一 直 以来 是 困扰 企 屑 ;不 锈 钢 、冷 轧 钢 板 、热 轧 钢 板 及 黑 皮 铁 板 类 就 不 易 产 生 细 屑 。 是 因 为 软 料 的粘 性 比较 好 , 易 粘在 冲 子上 。 薄 的 材 料 这 更 较 业 五 金 续 模 生 产 的 一 道 难 题 。 所谓 跳 屑 ,主要 是 因为 材 料 在 剪 和 废 料 外 形 较 小 、 规 则 的 形状 , 本 身较 轻 , 口的 摩 擦力 较 较 其 切 切 时 上 下 模具 存 在 间 隙 ,被 切 材料 本身 晶粒 细小 产 生 断裂 ,脱 小, 整个废料 容易被冲子带上来产生跳废料 。 离 原来 的 材 料本 体 ,粘 在 冲子 上 一 起 带 离模 面 ;如 果 是 整 个 废
这种情况在小企业最为普遍 。 爆 脱板 。 这些 都 会 直 接 影 响到 生产 速 度 和产 品 品 质 ,有 时 不 得 依靠现场模具师傅去想办法 ,
. 不 停 机 维 修 清理 废 料 ,有 的企 业 在 模 具 外 面 加 风 枪 等 方 法 ,效 2 2跳屑 和 跳废 料 的 防止 对 策 针对 以上原 因 ,我们尽量在设计和制造中可采取 以下一些 果 均 不 理想 。这里 提 供 一种 有 效 的解 决 方案 旨在 能 解 决 此 问题 。
常见冲压质量问题及解决之冲裁件的常见缺陷及原因分析

常见冲压质量问题及解决之冲裁件的常见缺陷及原因分析冲裁件的常见缺陷及原因分析冲裁是利用模具使板料分离的冲压工序。
冲裁件常见缺陷有:毛刺、制件表面翘曲、尺寸超差。
1、毛刺在板料冲裁中,产生不同程度的毛刺,一般来讲是很难避免的,但是提高制件的工艺性,改善冲压条件,就能减小毛刺。
产生毛刺的原因主要有以下几方面:1.1 间隙冲裁间隙过大、过小或不均匀均可产生毛刺。
影响间隙过大、过小或不均匀的有如下因素:a 模具制造误差-冲模零件加工不符合图纸、底板平行度不好等;b 模具装配误差-导向部分间隙大、凸凹模装配不同心等;c 压力机精度差—如压力机导轨间隙过大,滑块底面与工作台表面的平行度不好,或是滑块行程与压力机台面的垂直度不好,工作台刚性差,在冲裁时产生挠度,均能引起间隙的变化;d 安装误差—如冲模上下底板表面在安装时未擦干净或对大型冲模上模的紧固方法不当,冲模上下模安装不同心(尤其是无导柱模)而引起工作部分倾斜;e 冲模结构不合理-冲模及工作部分刚度不够,冲裁力不平衡等;d 钢板的瓢曲度大-钢板不平。
1.2 刀口钝刃口磨损变钝或啃伤均能产生毛刺。
影响刃口变钝的因素有:a 模具凸、凹模的材质及其表面处理状态不良,耐磨性差;b 冲模结构不良,刚性差,造成啃伤;c 操作时不及时润滑,磨损快;d 没有及时磨锋刃口。
1.3 冲裁状态不当如毛坯(包括中间制件)与凸模或凹模接触不好,在定位相对高度不当的修边冲孔时,也会由于制件高度低于定位相对高度,在冲裁过程中制件形状与刃口形状不服帖而产生毛刺。
1.4 模具结构不当1.5 材料不符工艺规定材料厚度严重超差或用错料(如钢号不对)引起相对间隙不合理而使制件产生毛刺。
1.6 制件的工艺性差-形状复杂有凸出或凹入的尖角均易因磨损过快而产生毛刺。
小结:毛刺的产生,不仅使冲裁以后的变形工序由于产生应力集中而容易开裂,同时也给后续工序毛坯的分层带来困难。
大的毛刺容易把手划伤;焊接时两张钢板接合不好,易焊穿,焊不牢;铆接时则易产生铆接间隙或引起铆裂。
常见的冲裁件缺陷有哪些_冲裁件为什么会有缺陷
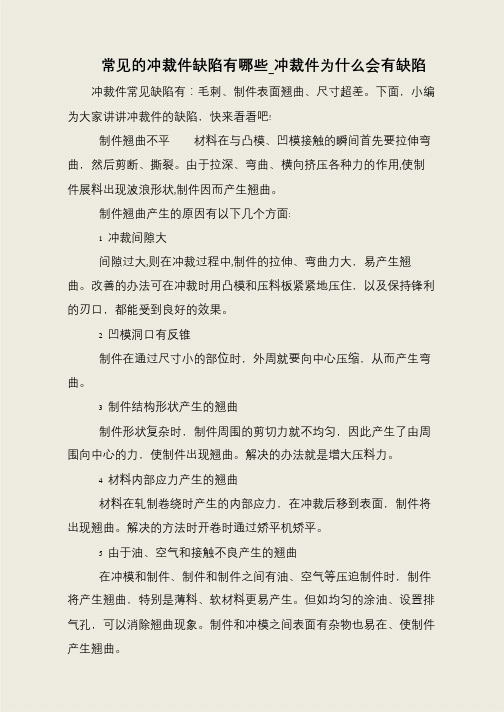
常见的冲裁件缺陷有哪些_冲裁件为什么会有缺陷冲裁件常见缺陷有:毛刺、制件表面翘曲、尺寸超差。
下面,小编为大家讲讲冲裁件的缺陷,快来看看吧!
制件翘曲不平材料在与凸模、凹模接触的瞬间首先要拉伸弯曲,然后剪断、撕裂。
由于拉深、弯曲、横向挤压各种力的作用,使制件展料出现波浪形状,制件因而产生翘曲。
制件翘曲产生的原因有以下几个方面:
1 冲裁间隙大
间隙过大,则在冲裁过程中,制件的拉伸、弯曲力大,易产生翘曲。
改善的办法可在冲裁时用凸模和压料板紧紧地压住,以及保持锋利的刃口,都能受到良好的效果。
2 凹模洞口有反锥
制件在通过尺寸小的部位时,外周就要向中心压缩,从而产生弯曲。
3 制件结构形状产生的翘曲
制件形状复杂时,制件周围的剪切力就不均匀,因此产生了由周围向中心的力,使制件出现翘曲。
解决的办法就是增大压料力。
4 材料内部应力产生的翘曲
材料在轧制卷绕时产生的内部应力,在冲裁后移到表面,制件将出现翘曲。
解决的方法时开卷时通过矫平机矫平。
5 由于油、空气和接触不良产生的翘曲
在冲模和制件、制件和制件之间有油、空气等压迫制件时,制件将产生翘曲,特别是薄料、软材料更易产生。
但如均匀的涂油、设置排气孔,可以消除翘曲现象。
制件和冲模之间表面有杂物也易在、使制件产生翘曲。
冲压件缺陷产生原因【干货分析】

冲压件缺陷产生原因分析内容来源网络,由“深圳机械展(11万㎡,1100多家展商,超10万观众)”收集整理!更多cnc加工中心、车铣磨钻床、线切割、数控刀具工具、工业机器人、非标自动化、数字化无人工厂、精密测量、3D打印、激光切割、钣金冲压折弯、精密零件加工等展示,就在深圳机械展.1. 冲压废品1)原因:原材料质量低劣;冲模的安装调整、使用不当;操作者没有把条料正确的沿着定位送料或者没有保证条料按一定的间隙送料;冲模由于长期使用,发生间隙变化或本身工作零件及导向零件磨损;冲模由于受冲击振动时间过长紧固零件松动使冲模各安装位置发生相对变化;操作者的疏忽,没有按操作规程进行操作。
2)对策:原材料必须与规定的技术条件相符合(严格检查原材料的规格与牌号,在有条件的情况下对尺寸精度和表面质量要求高的工件进行化验检查。
);对于工艺规程中所规定的各个环节应全面的严格的遵守;所使用的压力机和冲模等工装设备,应保证在正常的工作状态下工作;生产过程中建立起严格的检验制度,冲压件首件一定要全面检查,检查合格后才能投入生产,同时加强巡检,当发生意外时要及时处理;坚持文明生产制度,如工件和坯件的传送一定要用合适的工位器具,否则会压伤和擦伤工件表面影响到工件的表面质量;在冲压过程中要保证模具腔内的清洁,工作场所要整理的有条理加工后的工件要摆放整齐。
2. 冲裁件毛刺1)原因:冲裁间隙太大、太小或不均匀;冲模工作部分刃口变钝;凸模和凹模由于长期的受振动冲击而中心线发生变化,轴线不重合,产生单面毛刺。
2)对策:保证凸凹模的加工精度和装配质量,保证凸模的垂直度和承受侧压力及整个冲模要有足够的刚性;在安装凸模时一定要保证凸凹模的正确间隙并使凸凹模在模具固定板上安装牢固,上下模的端面要与压力机的工作台面保持相互平行;要求压力机的刚性要好,弹性变形小,道轨的精度以及垫板与滑块的平行度等要求要高;要求压力机要有足够的冲裁力;冲裁件剪裂断面允许毛刺的高度冲裁板材厚度>0.3>0.3-0.5>0.5-1.0>1.0-1.5>1.5-2.0新试模毛刺高度≤0.015≤0.02≤0.03≤0.04≤0.05生产时允许的毛刺高度≤0.05≤0.08≤0.10≤0.13≤0.153. 冲裁件产生翘曲变形1)原因:有间隙作用力和反作用力不在一条线上产生力矩。
五金冲压加工件不良原因及解决办法
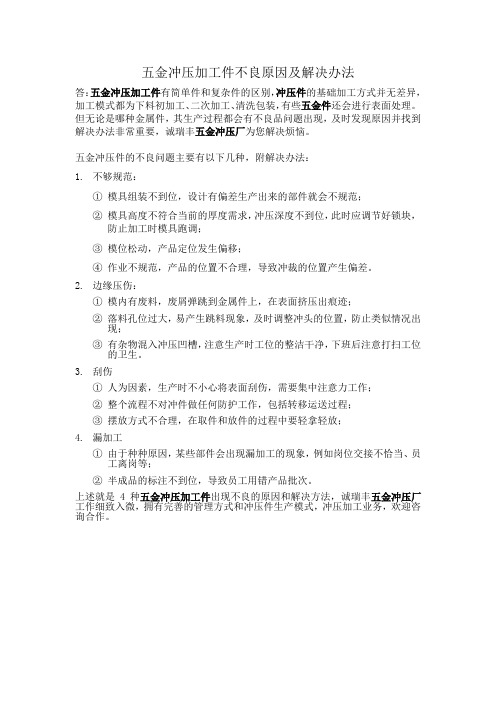
五金冲压加工件不良原因及解决办法
答:五金冲压加工件有简单件和复杂件的区别,冲压件的基础加工方式并无差异,加工模式都为下料初加工、二次加工、清洗包装,有些五金件还会进行表面处理。
但无论是哪种金属件,其生产过程都会有不良品问题出现,及时发现原因并找到解决办法非常重要,诚瑞丰五金冲压厂为您解决烦恼。
五金冲压件的不良问题主要有以下几种,附解决办法:
1.不够规范:
①模具组装不到位,设计有偏差生产出来的部件就会不规范;
②模具高度不符合当前的厚度需求,冲压深度不到位,此时应调节好锁块,
防止加工时模具跑调;
③模位松动,产品定位发生偏移;
④作业不规范,产品的位置不合理,导致冲裁的位置产生偏差。
2.边缘压伤:
①模内有废料,废屑弹跳到金属件上,在表面挤压出痕迹;
②落料孔位过大,易产生跳料现象,及时调整冲头的位置,防止类似情况出
现;
③有杂物混入冲压凹槽,注意生产时工位的整洁干净,下班后注意打扫工位
的卫生。
3.刮伤
①人为因素,生产时不小心将表面刮伤,需要集中注意力工作;
②整个流程不对冲件做任何防护工作,包括转移运送过程;
③摆放方式不合理,在取件和放件的过程中要轻拿轻放;
4.漏加工
①由于种种原因,某些部件会出现漏加工的现象,例如岗位交接不恰当、员
工离岗等;
②半成品的标注不到位,导致员工用错产品批次。
上述就是4种五金冲压加工件出现不良的原因和解决方法,诚瑞丰五金冲压厂工作细致入微,拥有完善的管理方式和冲压件生产模式,冲压加工业务,欢迎咨询合作。
五金连续冲模常见不良及其改善措施

五金连续冲模常见不良及其改善措施一、冲裁中常见不良(一)跳屑1.跳屑的几种情况:(1)切边时的跳屑:原因:系不完整的冲孔废料难以有效卡在模仁里,故易跳屑。
改善措施:修边结构复杂化。
(2)小方孔,小圆孔跳屑:原因:a、间隙太大b、有较多的油c、料太薄改善措施:a、收紧间隙b、减少用油c、加向下吹气,在废料下面形成负压d、设变模仁加工方式(改为PG加工),提高刃口段光洁度e、对冲子结构作重新设计f、对铁材产品模具备品须退磁干净(3)细小废屑:(常见于有撕破的模具,有重切时尤为时显,821-220模)(4)大片废屑的跳屑原因:同(2)改善措施:a、加顶杆b、加吹气c、对其形状复杂化(和carry相连一侧)(5)其他状况的跳屑:原因:工序排配设计不合理。
改善措施:重新调整工序排配(重新设计接刀)2.跳屑的危害(1)产生模痕,压伤等不良(2)对间歇性跳屑,不易发现,极易流出不良品。
(3)维修不易(常采用异性冲子,刃口披覆等有损备品寿命和产品断面质量的方式)致生产效率和稼动率低(4)不良品产生时常需要大量的人工进行挑选(二)金属丝危害1、组装成成品后,极易造成短路(short),是要绝对禁止的严重一种不良2、脱落时易在产品上产生模痕3、当有发生时须耗费大量的人力对其重工产生原因常见于有撕破的模具,比如:1、先向下撕破,后又被向上拍平,撕破切口处产生二次挤压,形成金属丝2、先向一个方向撕破后又向相反方向折弯成形3、一次撕破折弯不到位时,让设计不合理改善措施1、撕破处后面工站闪开(放电)避免撕破和被反复拍打。
(抽引毛坯的准备)2、对抽引,有撕破准备毛坯的后面各工站,均应闪开撕破缝隙处,或是重新对carry进行设计,以改善其变形,防止接缝段太长。
3、撕破方向应和后续**进行的成形方向一致,能采用一次撕破折弯成形方案的要尽可能采用。
4、在撕破处须进行二次forming,要合理设计穿过缝隙的冲子和模仁与撕破口间的间隙>0.02(三)冲子蹦根源:结构设计不合理1、直刀面太长为(大于10mm)2、该用PG加工(光学研磨)的未用,由于压板槽的影响,使用强度大大削弱(820-380N1)3、采用PG加工时结构设计不合理,PG槽对其削弱很多,822-173U形冲子4、弧量的部分太过细长5、太过细小冲子的导向段送样不合理(入子加工方式不好)改善措施:1、PG加工的冲子直刀面应小于10mm2、长*宽<3*3者应采用PG加工方式来设计和加工3、对大多数改U形结构冲子来讲,尽量采用PG加工,也应采用分体式结构,以尽量减小对其强度的削弱。
五金冲压模具常见问题点及不良原因与对策)

五金冲压模具常见问题点及不良原因与对策发布时间:2011-7-22 10:21:50 来源:本站原创作者:佚名冲件毛边不良原因:1.刀口或冲头磨损 2.间隙过大(研磨修刀口后效果不明显) 3.刀口崩角.4.导柱/导套磨损对策:1.研磨刀口. 2.依产品断面调整下料间隙. 3.研修刀口. 4. 调整站裁间隙(确保模板穴孔磨损或成形加工精度等问题. 5. 更换导向件或重新组装跳屑压伤不良原因:1. 间隙偏大. 2. 送料不当. 3. 五金冲压油滴太快,油粘 , 4.模具末退磁, 5.冲子磨损,屑料压附于冲子上. 6.冲子太短,刃入下模长度不足, 7.材质较硬,冲切形状简单.对策:1控制冲子及下模加工精度或修改设计间隙; 2送至适当位置时修剪料带并及时清理模具;3控制五金冲压油滴油量,或更换油种降低粘度;4零件研修后必须退磁;5研修冲刀口. 6调整冲子刃入子下模长度;7修改设计,冲子刃部端面装顶出或修出斜面或弧形(注意方向)减小冲子刃部端面与屑料之贴合面积,可防真空跳屑;8减小下模刃口的锋利度,减小下模刃口的研修量,增加下模刃部表面粗糙度,采用吸尘器吸屑料.降低冲速屑料阻塞不良原因:1.漏料孔偏小, 2.漏料孔偏大,屑料翻滚,3.刀口磨损,毛边较大, 4五金冲压油滴太快,油粘 5.下模直刃部表面粗糙,粉屑烧结附着于刃部. 6.材质较软. 对策:1.修改漏料孔,2.修改漏料孔 3.研修刀口, 4. 控制滴油量,更换油种, 5.表面处理抛光加工时注意降低表面粗糙度. 6.更改材料修改冲裁间隙, 7. 冲子刃部端面修出斜度或弧形,使用吸尘器下料偏位尺寸变异不良原因:1.冲子及下模刀口磨损,产生毛边(外形偏大,内孔偏小)2. 设计尺寸及间隙不当,加工精度差. 3.下料位冲子及下模镶块等偏位,间隙不均, 4.导料针磨损,定经不够. 5.导向件磨损. 6.送料机送距,压料,放松调整不当,7.模具合模深度不当, 8. 脱料镶块压料位磨损,无压料功能(材料牵引发翻料冲孔小), 9.脱料镶块强压太深,冲孔偏大. 10.五金冲压材质机械性能变异(强度延伸率等不稳定), 11.冲切时冲切力对材料牵引,引发尺寸变异.对策:1.研修刀口, 2.修改设计,控制加工精度, 3.调整其位置精度, 4.更换导料销, 5.更换导柱,导套, 6.重新调整送料机,7.重新调整合模深度, 8.重新研磨或更换脱料镶块,增加压功能调整压料. 9.减小强压深度, 10.更换材料,控制进料质量. 11.冲子端部修出斜面或弧形,以改善冲切时受力状况,许可时,下料部位于脱料镶块上加设导位功能卡模不良原因:1.送料送距,压料,放松,调整不当, 2.生产中送距产生变异, 3.送料机故障, 4.材料弧形,宽度超差,毛边较大, 5.模具五金冲压异常,镰刀弯引发, 6.导料孔经不足,上模拉料, 7.折弯或撕切位上下脱料不顺, 8.导料板之脱料功能设置不当,料带上带, 10.材料薄,送进中翘曲对策:1.重新调整,2.重新调整. 3.调整及维修, 4. 更换材料, 控制进料质量, 5.消除料带镰刀弯, 6.研修冲导孔冲子下模, 7.调整脱料弹簧力量等, 8.修改导料板,防料带上带, 9.送料机与模具间加设上下压料,加设上下挤料安全开关, 10.重新架设模具料带镰刀不良原因:1.五金冲压毛边, 2.材料毛边模具无切边. 3.冲床深度不当. 4.冲件压伤模内在屑料,5.局部压料太深或压至部局损伤对策:1.研修下料刀口,2. 更换材料,模具加设切边装置, 3.重调冲床深度. 4.清理模具,解决跳屑, 5.检查并调整各位脱料及下模镶块高度尺寸损伤位研修, 6.采用整弯机构调整冲子断裂崩刃不良原因:1.跳屑,屑料阻塞,卡模等倒致,2.送料不当,切半料, 3.冲子强度不足.4.大小冲子相距太近,冲切时材料牵引引发小冲断.5. 冲子及下模局部过于尖角, 6.冲裁间隙偏小, 7.无五金冲压油或使用的五金冲压油挥发性较强.8.冲裁间隙不均,偏移,冲子,上模发生干涉,9.脱料镶件精度差或磨损,失去精密导向功能,10.模具导向不准,磨损,11.冲子,下模材质选用不当,硬度不当,12.导料件(销)磨损,13.垫片加设不当,引发冲子与下模断裂,对策:1.解决跳屑,屑料阻塞,,卡模等问题,2.注意送料,及时修剪料带,及时清理模具,3.修改设计,增加冲子整体强度,减短下模直刃部尺寸,注意冲子刃部端面修出斜度,细小部后切, 4.小冲子长度磨短大冲子一个料厚以上, 5.修改设计, 6.控制冲子下模加工精度或修改设计间隙,细小部位冲切间隙适当加大,7.调整五金冲压油滴油量或更换油种,8.松查各成形悠扬精度,并施以调整或更换,控制加工精度,9.研修或更换,10.更换导柱,导套,注意日常保养,11.更换使用材质使用合适硬度,12.修正,垫片数画量少,尽可使用权用钢垫.且垫在漏料垫块之下面.折弯变形尺寸变异不良原因: 1.导料销尺寸不准,磨损, 2.折弯导位部精度差,磨损,3. 折弯冲子,下模磨损(压损), 4.模具让位不足, 5.材料滑移,折弯冲子,下模无导位功能,折弯时未施以预压, 6.模具结构及设计尺寸不良,7.冲件毛边引发折弯不良, 8.折率位冲子,下模加设垫片较多,造成尺寸不稳定, 9.材料厚度尺寸不变异, 10.材料机械性能变异对策:1.更换导料销, 2.重新研磨或更换, 3.重新研磨或更换. 4.检查,修正, 5.修改设计,增设导位功能,增设预压功能, 6.修改设计尺寸,分解折弯,增加折弯整形等, 7.研修下料位刀口, 8.调整,采用整体钢垫, 9.换料,控制进料质量, 10.换料控制进料质量冲件高低(一模多件)不良原因:1.冲件毛边. 2.冲件有压伤,模内有屑料,3.冲子,下模(折弯位)压损或损伤.4.冲剪时翻料, 5.相关压料部位磨损压损, 6.相关撕切位撕切尺寸不一致,刀口磨损,7.相关易断位,预切深度不一致,冲子下模有磨损事崩刃, 8.相关打凸部位冲子及下模有崩刃事磨损较为晋重, 9.模具设计缺陷,对策:1.研修下料刀口,2.清理模具,解决屑料上浮问题, 3.重新研修或更换新件, 4.研修冲切刀口,调整或增设强压功能, 5.检查实施维护或更换, 6.维修或更换保证切的状况一致辞, 7.检查预切之冲子,下模状况实施维护或更换. 8.检查冲子,下模状况实施维修或更换, 9.修改设计加设高低调整事增设整形工位维护不当不良原因:1.模具无防呆功能组模时疏忽导致装反向,错位(指不同工位)等已经偏移过间隙之镶件未按原状复原对策:1.修改模具,增防呆功能,采用模具上作记号等方法,并在组模后对照料带作必要的检查,确认等特别提醒:东莞禾聚塑胶五金有限公司是珠三角最专业的精密五金冲压件/贴片LED支架厂家,有绝对的优势!。
冲压常见缺陷及措施

破裂的改善措施
01
优化模具设计和加工工艺,避免 应力集中和脆化现象。
02
控制冲压材料的厚度和硬度,避 免过薄或过硬的材料导致破裂。
采用润滑剂和脱模剂等辅助材料 ,减少摩擦和粘结,降低破裂风 险。
03
采用先进的冲压设备和工艺技术 ,提高设备和工艺的精度和稳定
性,降低破裂风险。
04
起皱的改善措施
01
汽车制造中,许多零部件如车 门、车座、车盖等都需要经过
冲压工艺加工。
电子行业中,一些精密零件也 需要通过冲压工艺制造。
家用电器中,许多外观件和结 构件也是通过冲压工艺制造的
。
02
冲压常见缺陷
表面粗糙
原因
模具表面粗糙度低,冲压速度过 快,导致冲压件表面质量差。
措施
提高模具表面粗糙度,降低冲压 速度,改善冲压件表面质量。
05
06
解决方案:提高模具表面质量,选用合适 的润滑剂,控制冲压速度和压力。
案例三:不锈钢零件冲压缺陷及解决方案
缺陷一:粘结
解决方案:选用合适的润滑 剂,控制冲压速度和压力, 避免材料之间发生粘结。
缺陷二:变形
在冲压过程中,由于不锈钢 材料具有高粘性,导致材料
之间发生粘结现象。
由于不锈钢材料具有较高的 变形抗力,在冲压过程中容 易发生变形。
工艺问题
总结词
工艺问题也是冲压缺陷的原因之一。
详细描述
工艺问题包括工艺流程不合理、工艺参数不准确、工 艺操作不当等。这些问题可能导致产品形状变形、模 具磨损加剧、生产效率降低等不良影响。
04
冲压常见缺陷的措施
表面粗糙的改善措施
选用适宜的冲压材料和模具材料,提 高材料的质量和硬度。
连续冲模常见的模具设计缺陷

连续冲模常见的模具设计缺陷引言连续冲模是一种常见的模具类型,广泛应用于汽车零部件、电子产品、家电和医疗器械等制造行业。
然而,由于设计不当或缺陷,连续冲模可能会导致产品质量不稳定、生产效率低下甚至模具损坏等问题。
本文将讨论连接冲模的常见设计缺陷及其对模具性能和产品质量的影响,并提供相应的解决方案。
1. 模腔设计缺陷1.1 腔型结构不合理在连续冲模的模具设计中,腔型结构的设计是至关重要的。
不合理的腔型结构可能导致产品成形精度低、变形、裂纹等问题。
常见的腔型设计缺陷包括: - 壁厚不均匀:不合理的壁厚分布会导致金属在冲击过程中的流动不均匀,影响产品的成形精度。
- 毛刺和划痕:腔型表面的毛刺和划痕会在冲压过程中留下痕迹,降低产品表面质量。
- 冲裁不良:腔型设计不当可能导致冲裁不完全或边缘残留,影响产品的结构完整性。
解决方案: - 合理设计腔型结构,确保壁厚分布均匀,避免毛刺和划痕。
- 使用高硬度、高耐磨损的材料制作模具,提高模具的使用寿命。
- 定期检查模具,及时修复或更换受损的部件。
1.2 腔型温度控制不当连续冲模的腔型温度对产品成形质量有着重要影响。
腔型温度过高或过低都会导致产品尺寸不稳定、变形等问题。
常见的腔型温度控制缺陷包括: - 温度不均匀:腔型温度不均匀会导致产品在冷却过程中出现温度差异,从而影响成形质量。
- 温度过高:过高的腔型温度会导致产品热胀冷缩不均匀,引起尺寸变化和变形。
- 温度过低:过低的腔型温度会导致产品冷却速度过快,增加应力和残余应力,容易导致开裂或收缩不均。
解决方案: - 使用合适的冷却系统,确保腔型温度均匀,并进行及时调整。
-使用温度传感器对腔型温度进行监控,及时调整冷却系统的工作状态。
- 对于过高或过低的腔型温度,适当调整冲压参数,控制冲压速度和冷却速度。
2. 引导部件设计缺陷连续冲模的引导部件设计是确保模具正常运行的关键。
不合理的引导部件设计可能导致模具寿命短、生产效率低下等问题。
常见冲压质量问题及解决方法

常见冲压质量问题及解决方法摘要:冲压行业是一个涉及领域极其广泛的行业,深入到了制造业的方方面面。
故在近三十年受到大力推广及应用。
在我国汽车生产过程,如汽车车身、车架等零部件都是冲压加工出来的,而且汽车冲压件产品种类日趋丰富、形状日趋复杂,在冲压加工过程中,易产生各种不良质量问题,给公司带来损失。
本文首先对造成冲压产品质量问题的几种原因进行了概述,详细探讨了提高冲压模具零件精加工的注意事项,旨在推动现代冲压模具的广泛运用。
关键词:冲压质量问题;解决方法冲压是现代机械零件精加工的最常用的一种加工方法,采用冲床和模具对不同材料施加压力,使其发生分离或者是形变,最终生产出所需的机械零件。
零件加工是机械生产过程中必要的步骤,在传统的零件加工过程中仅能够实现粗加工,生产后的零件还需要在车床上进行人工的修整,以保证其符合生产规格的要求。
但随着现代机械加工技术的不断进步,也使得零件加工技术不断提升,冲压模具的应用使得精加工成为了可能,降低了人力资源的消耗,提高了机械零件生产的速率。
1 造成冲压产品质量问题的几种原因1.1 模具隙不合理引起的冲裁件质量问题对于冲裁件影响产品质量的重要因素就是冲裁间隙。
冲裁模间隙过大与过小或者间隙不均匀都会引起制件产生毛刺。
而产生不合理的冲裁间隙原因有:(1)模具问题:冲裁模具零件不合格,尺寸精度不达标。
模具装配精度不够,导向间隙大,上下模具同心度差等问题都会导致间隙不合理。
(2)设计问题:模具设计间隙不合理,设计人员缺乏实际经验,给出的间隙值过大或者过小。
(3)冲压设备问题:压力机精度差、滑块与工作台面平行度不好、滑块行程方向与压力机台面垂直度不好等原因都会造成模具间隙问题。
(4)操作者问题:模具安装过程中未能严格遵守操作规程,工作台表面没有清理干净,安装紧固螺栓顺序错误等也会造成间隙问题产生。
在生产过程中,冲压件精度要求、生产的条件不同,在实际加工时,无法确定一个统一的间隙值。
数控冲床加工时常见的问题及处理方法
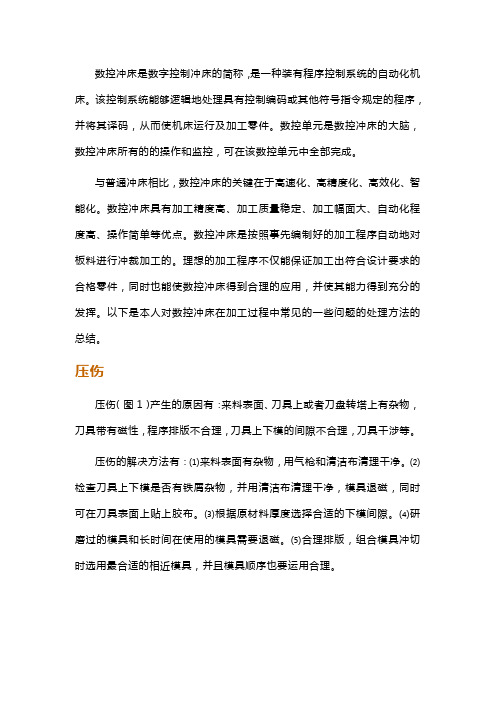
数控冲床是数字控制冲床的简称,是一种装有程序控制系统的自动化机床。
该控制系统能够逻辑地处理具有控制编码或其他符号指令规定的程序,并将其译码,从而使机床运行及加工零件。
数控单元是数控冲床的大脑,数控冲床所有的的操作和监控,可在该数控单元中全部完成。
与普通冲床相比,数控冲床的关键在于高速化、高精度化、高效化、智能化。
数控冲床具有加工精度高、加工质量稳定、加工幅面大、自动化程度高、操作简单等优点。
数控冲床是按照事先编制好的加工程序自动地对板料进行冲裁加工的。
理想的加工程序不仅能保证加工出符合设计要求的合格零件,同时也能使数控冲床得到合理的应用,并使其能力得到充分的发挥。
以下是本人对数控冲床在加工过程中常见的一些问题的处理方法的总结。
压伤压伤(图1)产生的原因有:来料表面、刀具上或者刀盘转塔上有杂物,刀具带有磁性,程序排版不合理,刀具上下模的间隙不合理,刀具干涉等。
压伤的解决方法有:⑴来料表面有杂物,用气枪和清洁布清理干净。
⑵检查刀具上下模是否有铁屑杂物,并用清洁布清理干净,模具退磁,同时可在刀具表面上贴上胶布。
⑶根据原材料厚度选择合适的下模间隙。
⑷研磨过的模具和长时间在使用的模具需要退磁。
⑸合理排版,组合模具冲切时选用最合适的相近模具,并且模具顺序也要运用合理。
图 1 压伤划伤划伤(图2)产生的原因有:来料不良有划伤,人员上下料摆放不到位,模具划伤等。
图2 划伤划伤的解决方法有:⑴来料不良有划伤可拒收,如有烤漆、拉丝产品加工时,必须要考虑烤漆的位置和划伤的严重性,再决定是否采用。
⑵上下料时,工作人员必须同时垂直抬起和放下,且必须把机台的滚珠包起来,严禁上料时在原材料上摩擦、拖动。
⑶产品摆放时严禁在纸板上拖动,同时纸板上不能有铁屑等杂物;摆放要平稳、整齐,同时产品不能摆放太高。
⑷调整刀盘里的毛刷,特殊成形模具下模较高时要把毛刷抬高,尽量使模具远离其他的模具或采用装拆方式。
⑸程序优化,减少工件在刀盘上面的拖动。
常见冲压不良分析
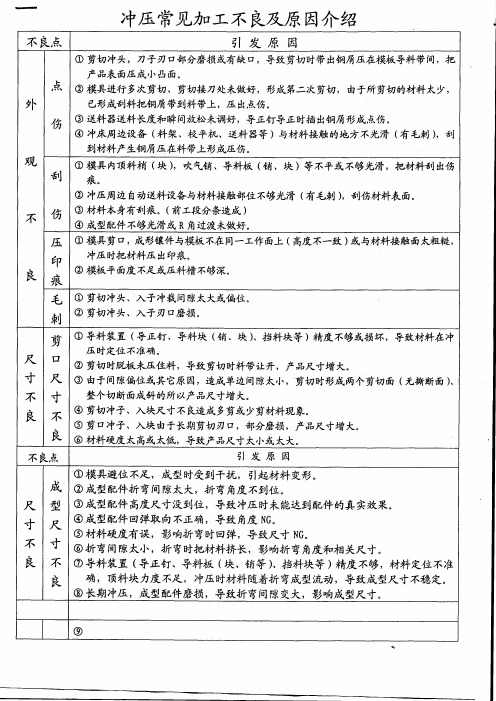
5000
6050
20
150ˉ 600
20
100ˉ 500
30
lO0ˉ 350
⒈6
1.6
2
闭合 工作高度 (D。 H)Ⅱ m 冲头调整量
210
50
205
250
50
340× 280
245
325 50
320
(⑶ nlm
8。 L。
冲头底面面积
冲头孔径深度
× RB.)nm
230*189
φ 38.1x70
470x390
φ50.8× 70
印 痕
毛
,
丶 艮
冲压 时把材料压 出印痕 。 ② 模板平 面度不足或压料槽 不够深 。
① 剪切 冲头 、入 子 冲裁间隙太大或偏位。 刺 ② 剪切 冲头 、入 子刃 口磨损 。
尺 寸
不 丶 艮
导料装置 (导 正钉 、导料块 (销 、块 挡料块等 )精 度不够或损坏 ,导 致材料在冲 口 压 时定位不准确。 尺 ② 剪切时脱板 未压住料 ,导 致剪切时料带让开 ,产 品尺寸增 大。 ③ 由于间隙偏位或其它原因,造 成单边间隙太小,剪 切时形成两个剪切面 (无 撕断面 寸 整个切断面成斜的所以产 品尺寸增大。 不 ④ 剪切冲子 、入块尺寸不良造成多剪或少剪材料现象。 良 ⑤ 剪 口冲子 、入块由于长期剪切刀 口,部 分磨损 ,产 品尺寸增 大。 ⑥ 材料硬度太高或太低 ,导 致产品尺寸太小或太大。
850× 520
nlm G× D
lnm
φ50.8k70
720× 420
平板面积
平板厚度
1径 平板孑
500× 300
(T,mm
△ σ L× F.B)lnm
冲压作业伤害分析及标识管理(4篇)

冲压作业伤害分析及标识管理冲压作业是指通过冲裁、剪裁、拉伸等方式,将金属板材加工成所需形状的工艺。
由于冲压作业涉及到各种复杂的冲击、挤压和拉伸过程,工人在进行冲压作业时往往面临着一定的伤害风险。
本文将对冲压作业的伤害问题进行分析,并提出相应的标识管理措施。
冲压作业的伤害问题主要有以下几个方面:1. 机械伤害:在冲压作业中,机械设备的运动部件如冲头、刀具等可能造成工人的损伤。
例如,当金属板材被冲头冲击时,如果操作不规范,很容易夹伤手指或者手部其他部位。
此外,由于冲压作业速度较快,工人也可能被冲击产生的金属屑或者碎片击伤。
2. 物理伤害:冲压作业时,金属板材的弯曲、挤压和拉伸等过程会产生大量的能量释放,如切割时产生的淋巴浮沫等。
这些能量释放会导致工人受到切、割、挤、夹等物理伤害。
3. 化学伤害:在冲压作业中,涉及到的金属板材和润滑油等材料可能对工人造成化学伤害。
例如,金属板材中可能含有有害物质,如铅、氟等,长期接触这些物质可能对工人的健康产生不良影响。
此外,冲压作业中所使用的润滑油等化学物质也可能对工人造成伤害。
为了防止冲压作业中的伤害问题,可以采取以下标识管理措施:1. 设置警示标识:对于可能造成机械伤害的设备和工作区域,应设置明显的警示标识,警示工人注意安全。
标识应清晰明了,易于辨认,并应进行定期检查和维护,确保其有效性。
2. 安装安全护栏:对于冲压作业中涉及到的危险区域,应设置安全护栏或隔离带,阻止未经授权人员进入,并用明显的标识标明危险区域。
3. 提供个人防护装备:为了防止工人在冲压作业中受伤,应提供适当的个人防护装备,如安全帽、防护眼镜、手套等。
同时,应对工人进行相应的培训,确保其正确使用个人防护装备。
4. 定期维护设备:对于用于冲压作业的设备,应定期进行维护和检修,确保其正常运行。
设备维护记录应详细记录,包括维护时间、内容以及维护人员等信息。
5. 使用安全材料:为了防止冲压作业中的化学伤害问题,应选用符合相关标准的金属板材和润滑油等材料,并确保其质量和供应来源可靠。
模具冲压十大问题,以及对应十大解决方案

在级进模的冲压生产中,针对冲压不良现象必须做到具体分析,采取行之有效的处理对策,从根本上解决所发生之问题,如此才能降低生产成本,达到生产顺畅。
以下就生产中常见的冲压不良现象其产生的原因及处理对策分析如下,供模具维修人员参考。
1.冲件毛边(1)原因:a、刀口磨损; b、间隙过大研修刀口后效果不明显;c、刀口崩角; d、间隙不合理上下偏移或松动; e、模具上下错位。
(2)对策:a、研修刀口;b、控制凸凹模加工精度或修改设计间隙;c、研修刀口;d、调整冲裁间隙确认模板穴孔磨损或成型件加工精度等问题;e、更换导向件或重新组模。
2.跳屑压伤(1)原因:a、间隙偏大; b、送料不当;c、冲压油滴太快,油粘;d、模具未退磁;e、凸模磨损,屑料压附于凸模上;f、凸模太短,插入凹模长度不足;g、材质较硬,冲切形状简单;h、应急措施。
(2)对策:a、控制凸凹模加工精度或修改设计间隙;b、送至适当位置时修剪料带并及时清理模具;c、控制冲压油滴油量,或更换油种降低粘度;d、研修后必须退磁(冲铁料更须注意);e、研修凸模刀口; f、调整凸模刃入凹模长度;g、更换材料,修改设计。
凸模刃入端面装顶出或修出斜面或弧性(注意方向)。
减少凸模刃部端面与屑料之贴合面积;h、减小凹模刃口的锋利度,减小凹模刃口的研修量,增加凹模直刃部表面的粗糙度(被覆),采用吸尘器吸废料。
降低冲速,减缓跳屑3.屑料阻塞(1)原因:a、漏料孔偏小;b、漏料孔偏大,屑料翻滚;c、刀口磨损,毛边较大;d、冲压油滴太快,油粘;e、凹模直刃部表面粗糙,粉屑烧结附着于刃部;f、材质较软;g、应急措施。
(2)对策:a、修改漏料孔;b、修改漏料孔;c、刃修刀口;d、控制滴油量,更换油种;e、表面处理,抛光,加工时注意降低表面粗糙度;更改材料,f、修改冲裁间隙;g、凸模刃部端面修出斜度或弧形(注意方向),使用吸尘器,在垫板落料孔处加吹气。
4.下料偏位尺寸变异(1)原因:a、.凸凹模刀口磨损,产生毛边(外形偏大,内孔偏小);b、设计尺寸及间隙不当,加工精度差;c、下料位凸模及凹模镶块等偏位,间隙不均;d、导正销磨损,销径不足;e、导向件磨损;f、送料机送距、压料、放松调整不当;g、模具闭模高度调整不当;h、卸料镶块压料位磨损,无压料(强压)功能(材料牵引翻料引发冲孔小);i、卸料(2)对策:a、研修刀口; b、修改设计,控制加工精度;c、调整其位置精度,冲裁间隙;d、更换导正销;e、更换导柱、导套;f、重新调整送料机;g、重新调整闭模高度;h、研磨或更换卸料镶块,增加强压功能,调整压料;i、减小强压深度;j、更换材料,控制进料质量;k、凸模刃部端面修出斜度或弧形(注意方向),以改善冲切时受力状况。
冲裁模具生产中的不规范行为对产品质量的不良影响

行 为
来 源
为通用工艺规则 , 这些不规范生产行为 , 或多或少 地“ 解决” 了一些生产实际问题 。 人们 自学或不 自
觉地 将 它运用 于生产 中。 一 方面 , 另 放任 这些 不规
模具 在维修 时 , 困难 的工作 是拆 卸整 体模具 。拆 较 卸 过程 , 位销 的拆 卸格外 费工 。当维修 的频 率增 定 大 之后 ,部 分模 具 的制造 者不 再将 模 具 的定位 销 安 装得那 么规 范 , 是将 销子 磨小 0O . 2 而 .10O mm, 0
金 中 的共 晶 硅 ,使 铸 态 合 金 中 的 共 晶 硅 由 长 针 片
’ 寸问题存在着微微的螺动现象。检测人员认定该 /
曼
i
I 、 一 、、 . 0、 _ \ | \ \
,
。
j
, -
,
.
/ ,
I
5 :1
I
5 :1
I
5 :1
螺 钉 与螺 母 加 工 正 常
螺母 加 工 不 正 常 时 的 紧 固 配 合状 况
滑动现象。大型冲裁模具中, 拉紧的螺栓很多 , 定
位 销较 少 , 般 也不会 出现 凹 、 一 凸模在 固定板 上滑 动现 象 。然 而 ,在生 产 现场 ,一 副 约 凸模 尺寸 为
材料的凹、 凸模具上 , 手工攻丝变得较容易。螺孔
钻 削孔 径 加大值 越 大 , 手工 攻丝 越快 。更有 甚者 , 直 接用 机床 在 Cl r2材料 的凹 、 凸模 具 上采 用机 攻
螺 钉与螺母加工均 不正常 时 的紧固配合不稳定状况 螺钉与螺母 的配合出现间隙
时的紧固配合状况
- 1、下载文档前请自行甄别文档内容的完整性,平台不提供额外的编辑、内容补充、找答案等附加服务。
- 2、"仅部分预览"的文档,不可在线预览部分如存在完整性等问题,可反馈申请退款(可完整预览的文档不适用该条件!)。
- 3、如文档侵犯您的权益,请联系客服反馈,我们会尽快为您处理(人工客服工作时间:9:00-18:30)。
连续冲模常见设计缺陷及其解决措施一.冲裁中常见不良1.跳屑2.金属丝3.冲子蹦4.模仁裂与堵料5.接刀毛头6.尺寸超差7.压板断8.啃刀口9.接刀设计错(粗定位无效果)二.折弯成形常见不良1.违反先压料后成形原则2.冲子断差太大3.框口磨损4.拉毛5.两次折弯折弯线设计错6.折弯成形尺寸不稳定7.成形尺寸不到位8.浮动模仁定位段太短,晃动幅度大9.浮动模仁或Lifter,易跳出来(危险性大),或者设计强度太差10.KINK的成形问题11.尺寸不良的几个因素:1)角度2)圆角3)展开长度4)折弯线处之逃料三.整形机构1.斜面整形的适用范围及常见问题点2.摆块整形机构的适用范围及常见问题点3.斜面整形机构的适用范围及常见问题点4.一次折弯整形机构的局限性四.翻边打卡荀等起伏成形工站常见问题点1.翻边口部裂纹2.翻边高度小3.扭力不足4.翻边起皱5.卡荀断6.起伏成形对相邻已成形尺寸的影响7.撕破成形高度偏低五.下料时常见问题:(下料不畅)1.废料留在模面(821-762N1)2.下料不畅,加吹气,顶杆3.混料4.下产品改为下废料(吹气方式)六.抽引中常见问题点1.毛坯太大2.毛坯太小3.抽引拉裂4.抽引起皱5.壁部拉毛6.Carry相互挤压7.定位不可靠8.大肚子七.结构设计中常见问题:1.定位针固定在冲子固定板上2.剥料套设计不良3.料条定位不好(追加导板)4.压板,弹簧断裂(改冲子固定方式)5.背板螺丝太靠外6.抽引第一抽不分开7.缺少整形工站8.定位针太少,太细9.Lifter无爬坡(模仁太短)八.料条设计问题:1.刚性太差2.前后工序排配不合理3.粗定位无效4.定位针孔太靠后九.几种常见的典型机构十.其它常见问题:1.大平面的平面度问题2.SMT PAD的共面度问题3.铆合中的一些问题及解决措施4.料带式产品的扇形(波浪形)第一章冲裁中常见不良一.跳屑一)跳屑的几种情况:1.切边时的跳屑:原因:改善措施:2.小方孔,小圆孔跳屑原因:1)间隙太大2)有较多的油3)料太薄改善措施:1)收紧间隙2)减少用油3)加向下吹气,在废料下面形成负压4)设变模仁加工方式(改为PG加工),提高刃口段光洁度5)对冲子结构作重新设计6)对铁材产品模具备品须退磁干凈)3.细小废屑:(常见于有撕破的模具,有重切时尤为时显,821-220模)4.大片废屑的跳屑原因: 同2改善措施:1)加顶杆2)加吹气3)对其形状复杂化(和carry相连一侧)5.其它状况的跳屑:原因:工序排配设计不合理改善措施:重新调整工序排配(重新设计接刀)二)跳屑的危害:1.产生模痕,压伤等不良2.对间歇性跳屑,不易发现,极易流出不良品3.维修不易(常采用异形冲子,刃口披覆等有损备品寿命和产品断面质量的方式)致生产效率和稼动率低4.不良品产生时常需大量的人工进行挑选二.金属丝一)危害:1.组装成成品后,极易造成短路(SHORT),是要绝对禁止的严重一种不良2.脱落时易在产品上产生模痕3.当有发生时须耗费大量的人力对其重工二)产出原因:常见于有撕破的模具,比如:1.先向下撕破,后又被向上拍平,撕破切口处产生二次挤压,形成金属丝2.先向一个方向撕破后又向相反方向折弯成形3.一次撕破折弯不到位时,让设计不合理三)改善措施:1.撕破处后面工站闪开(放电)避免撕破和被反复拍打。
(抽引毛坯的准备)2.对抽引,有撕破准备毛坯的后面各工站,均应闪开撕破缝隙处,或是重新对carry进行设计,以改善其变形,防止接缝段太长。
3.撕破方向应和后续**进行的成形方向要一致,能采用一次撕破折弯成形方案的要尽可能采用。
4.在撕破处须进行二次forming,要合理设计穿过缝隙的冲子和模仁与撕破口间的间隙>0.02.三.冲子蹦根源:1.结构设计不合理1)直刀面太长为(大于10mm)2)该用PG加工的未用,由于压板槽的影响,使用强度大大削弱(820-380N1)3)采用PG加工时结构设计不合理,PG槽对其削弱很多,822-173 U形冲子4)弧量的部分太过细长5)太过细小冲子之导向段送样不合理(入子加工方式不好)改善措施:1.PG加工之冲子直刀面应小于10mm2.长*宽<3*3者应采用PG方式来设计和加工3.对大多改U形结构冲子来讲,尽量采用PG加工,也应采用分体式结构,以尽量减小对其强度的削弱。
分体和整体式加工时的差异:因分体式时可采用垂直于深槽的方向进刀,可减小许多切削量。
4.当有弧悬的细小部位存在时,1)排样时尽量避免(排样重新考虑)2)无法避免时,应采用PG方式设计5.当有细长的冲子存在时(<直径1.0时)冲子导向段和工作段应分开(工作段长度应<2.0)(长径比不大于3),其结构如下:五.毛头1.现象2.原因:1)接刀设计不良:在圆弧顶点或平面上接刀→无2)垂切3)间隙不合理4)冲子模仁材质选择不合理5)刀口保养做得不确实3.改善措施:1)接刀设计不改善2)避免在圆弧顶点或平面上接刀增加工艺逃料(避免垂切)3)采用合理日冲裁间隙4)尽量将冲子和模仁选用不同的材质(冲子V3,则模仁用ASP23或SKD11),反之易可。
六.冲裁的尺寸超差1.原因:1)材料有翻转2)材料有流动3)成形与下料工序排配不当4)打COIN的影响5)打倒角的影响6)下料的侧边的成形设计不合理2.改善措施:1)对材料作强压(不允压痕者除外2)作限位,防止材料流动3)据试模作修正4)调整成形和下料工序的先后排配(不影响模仁强度的状况下)5)据经验值修正因打COIN,打倒角,而会引起变异的量,0.05~0.10)6)不会引起细小废屑的时候加精切,通常不用)7)后工序段加调整原则:首先使成形尺寸稳定后再修正下料,*七.压板断:(螺丝断)1.原因:压板不足以承受剥料力,常见设计缺陷:1)大冲子只有一个压板2)压板悬臂太长,A太大,A≦9mm为宜2.改善措施:1)增加压板2)改压板固定冲子为键固定冲子3)改用螺纹吊(Mini Din产品的翻边冲子)八.接刀设计错误:1.粗定位无效果1)A>P+0.22) A<P2.接刀时垂切3.精切的量太少4.接刀的先后顺序反第二章折弯成形常见设计不良一.角度不到位二.表面拉毛三.尺寸不到位四.变形五.尺寸不稳定六.包料一.角度不到位1.原因分析:1)折弯高度小于最小折弯高度2)间隙不合理3)无整形工站4)压料不确实(弧形)5)框口磨损6)冲子刚性太差7)无后角2.解决措施:(洽制工,产生更改规格)1)追加整形工站(成二次折弯工站)(斜向,滑块,摆块……)2)调整折弯间隙3)打Coin(允许时)作用:减小料厚===减小最小折弯高度(圆角,料厚)4)改善压料:A.增大Lifter面积B.磨加强筋C.换强力弹簧D.下死点时迭死E.收冲子成形为剥料扳成形(下死点迭死)5)追加模板入子6)下模加冲子挡块7)模仁闪后角二.表面拉毛1.原因:1)间隙太小2)冲子材质和零件材质存在亲和力3)润滑不良4)冲子表面光洁度不够2.改善措施:1)调整间隙至0~0.012)改冲子材质(与零件材质有关:WC,B,Tic,C,陶瓷)3)适当加油4)生产试模时抛光冲子表面3.对镀后成形产品的折弯工序排配建议:1)采用两次折弯成形工艺2)采用折弯加整形工站3)冲子尽可能的采用嵌件结构4)生产时加油的考虑和种类须严格控制5)冲压工艺难以解决时协商制工产发工程师共同解决三.尺寸不到位:1.原因:1)角度不到位2)展开长度不良3)圆角R尺寸不良4)有变形5)COIN的影响6)折弯线位置不对7)折弯力不够3.改善措施:1)先修正角度到位2)CHK折弯线位置有无错误3)CHK展开长度4)CHK折弯有无变形5)是否有打COIN(对尺寸是否会造成影响)6)消除以上所有不良之后,再决定是否要修正下料*试模修模小技巧:调整折弯圆角(模仁)可对折弯成形尺寸作一定范围的微调。
7)弹簧力不足以提供折弯力。
(料厚,折弯线长时,尤其明显)有时也采用剥料板成形也不足以到达要求的折弯力(S02A和P01A间有0.10的间隙),可以追加迭死冲子。
四.变形(不包含闪位不够的变形)2.原因:1)压料不好2)折弯间隙太小(对细小折弯影响很明显)3)折弯冲子断差太大3.解决措施:1)改善压料2)适当放松间隙(采用二次折弯或加整形工站等使角度到位3)减小冲子断差至(6+0.05~0.10)<0.5此类改善做得极多,约占以前总改善量的30%断差的作用:1.下死点时对折弯圆角作整形,增塑性变形,减小回弹2.方便生产中对折弯间隙作调整,(可位移)五.尺寸不稳定1.材质有变化2.折弯线不稳定原因:1)冲子无入子,框口或冲子磨损2)折弯模仁晃动(尤其是浮动折弯模仁)3)浮动折弯模仁定位段短4)浮动模仁或框口磨损解决措施:1)加大模仁,增加定位段2)加入子,沉入下垫板六.包料与折弯裂纹1.原因:1)折弯模仁圆角小于最小折弯圆角3)折弯角度小于90∘(外侧伸长量大于材料的延伸率)4)材料的性能变异2.模具设计时注意点:1)CHK折弯圆角,是否小于最小折弯圆角2)折弯模仁圆角不能取得过小3)对两次折弯或(一次折弯+整形)中的第一次折弯模仁不要与第二次折弯(或整形模仁作成整体)当料硬度低,折弯圆角小时,第一次折弯极易形包料第一次折弯模仁不闪后角则不会包料七.几种典型折弯整形机构的优缺点:一)斜面整形1.优点:结构简单,成本低,所需模具空间小效果有限,同时有如下问题:受力点不在折弯线附近1)产生弧形当折弯面上有孔等其它减其弱度的情形存在时,整形屈服点将不在我们所希望折弯线处,而在最薄弱处2)形成毛头3.适用范围:1)尺寸与角度要求均不高的埸合2)料厚与折弯线均不大的场合3)折弯高度不大于5mm的场合4.设计要点:α<20∘L值要合理二)侧推滑块整形1.优点:稳定。
可靠,可将折弯角度整形至小于90∘,在实际设计中适用最广泛的机构2.缺点:结构复杂,零件多,成本高,占有模具空间大,使用场合受到一定的限制。
3.适用范围:广泛运用于尺寸和角度要求高或角度要求90∘时折弯整形工站,只要模具结构空间允许,均可大胆采用。
4.设计要点:1)防止滑块跳出a.用压板压b.用导板压c.用T形槽2)α1<α23)H不能太高,25 OR30厚下模板时最好采用一个垫块4)行程要足够,不能和产品的已成形部分干涉,须L1>L2否则:产品(料条)上行时会和滑块干涉5.调整量要合适,原则:设计时:调整到最内时,滑块和折弯模仁间的最小间隙应不小于0.5否则:当调整适量时会造成滑块或模仁损坏三)摆块机构。