铝合金半固态成形工艺的研究现状
铝合金半固态挤压成形工艺及理论研究
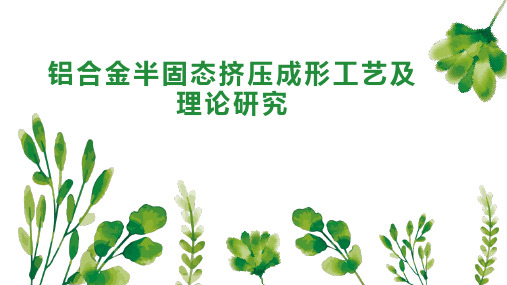
最后,对实验结果进行分析,并基于实验结果进行了理论研究,包括半固态 挤压成形工艺的理论基础、工艺优化方法和挤压力计算等。本次演示的研究成果 表明,铝合金半固态挤压成形工艺具有诸多优点,相比传统液态挤压成形工艺, 半固态挤压成形工艺可以获得更高的制品质量、更优的力学性能和更好的表面完 整性。因此,本次演示的研究为铝合金半固态挤压成形工艺的应用和推广提供了 理论支持和实践指导。
半固态铝合金的制备工艺
半固态铝合金的制备工艺主要包括熔炼、球磨、热处理等步骤。其中,熔炼 是制备半固态铝合金的关键步骤,需要将铝、铜、镁等合金元素熔化在一起,并 控制好熔炼温度和时间,以保证合金的成分和组织稳定性。球磨是制备半固态铝 合金的另一个关键步骤,通过将合金粉末进行球磨处理,可以细化合金的晶粒尺 寸,提高合金的力学性能。热处理则是为了进一步优化合金的组织和性能,使合 金达到最佳的使用效果。
(1)制品质量更稳定:由于半固态浆料具有较好的流动性和稳定性,使得模 具内的材料更加均匀,减少了流体流动和不稳定性对制品质量的影响。
(2)力学性能更优:半固态挤压成形过程中,材料在模具内可以迅速达到高 密度,同时由于半固态材料的特性,使得制品内部晶粒更细小,力学性能更优。
(3)表面完整性更好:由于半固态挤压成形过程中模具内的材料分布更加均 匀,减少了模具表面的摩擦和划痕,使得制品表面更加完整。
铝合金半固态挤压成形工艺及 理论研究
摘要
本次演示主要介绍了铝合金半固态挤压成形工艺及其相关理论研究。首先, 简要介绍了铝合金半固态挤压成形工艺的研究背景和现状,阐明了本次演示研究 的重要性和意义。其次,详细阐述了铝合金半固态挤压成形工艺的基本原理和流 程,包括铝合金半固态制备、挤压成形工艺及其原理。接着,介绍了实验方法, 包括实验材料、实验设备和实验过程。
A356铝合金半固态流变成形中的凝固行为及组织控制

A356铝合金半固态流变成形中的凝固行为及组织控制A356铝合金半固态流变成形中的凝固行为及组织控制摘要: A356铝合金是一种广泛应用于航空、汽车等领域的热处理铝合金,半固态流变成形是一种有效改善A356铝合金成形性能的技术。
本文通过研究A356铝合金半固态流变成形过程中的凝固行为及组织控制,旨在探索其对材料性能的影响,为铝合金半固态流变成形工艺的优化提供理论依据。
1. 引言随着工业技术的不断发展,高性能铝合金逐渐成为替代传统材料的理想选择。
A356铝合金作为一种常用的铝合金,具有优异的机械性能和耐腐蚀性能,在航空、汽车及其他工业领域被广泛应用。
然而,传统的铸造工艺制备A356铝合金存在着铸件缺陷、微观组织不均匀等问题,严重制约了其进一步发展。
半固态流变成形技术通过控制铝合金在半固态状态下的流变特性,可以有效改善铝合金的成形性能和材料的微观组织,成为铝合金加工的重要方法之一。
2. A356铝合金半固态流变成形的基本原理A356铝合金在半固态状态下的流变行为受到凝固行为的影响较大。
凝固是指熔融金属在冷却过程中由液态向固态转化的过程。
在半固态流变成形过程中,凝固过程会影响材料的流变性能和组织形成,因此对凝固行为的研究是研究A356铝合金半固态流变成形的重要前提。
3. A356铝合金半固态凝固行为的研究现状目前,对于A356铝合金半固态凝固行为的研究主要集中在以下几个方面:凝固曲线的测定与分析、凝固过程中的晶粒生长和凝固组织形成机制的研究、凝固活动能和凝固时间的计算等。
通过对凝固行为的研究,可以揭示铝合金在半固态状态下的变形行为,并为合理控制材料的组织形成提供理论基础。
4. A356铝合金半固态流变成形中的组织控制半固态流变成形过程中,通过合理控制A356铝合金的凝固行为,可以实现对材料组织的精确控制,进而影响材料的性能。
常见的组织控制方法包括凝固速率控制、液固相体积分数控制、添加剂控制等。
通过组织控制,可以调节材料的晶粒尺寸、相分布、亚稳相含量等,进而实现优化材料性能的目的。
半固态加工技术研究现状与应用前景

凝固论文半固态加工技术研究现状及应用前景Research Situation and Application Prospect of Semi-solid Processing Technology课程:金属凝固理论半固态加工技术研究现状及应用前景Research Situation and Application Prospect of Semi-solid Processing Technology摘要:半固态金属成形技术具有高效、节能、近终形生产和成形件性能高等许多优点,是近年来金属加工技术研究的热点。
该工艺在钢铁及有色金属加工中都受到了相当的重视,关于这方面的专著、论文等也大量的涌现。
本文在众多的文献资料基础上通过作者的整合,思考将从半固态加工简介,基本原理,研究现状及应用前景四个方面进行阐述。
关键词:半固态加工;浆料制备;成形技术;数值模拟;应用前景Abstract: There are many advantages of semi-solid metal forming technology such as high efficiency, energy saving, and net-shaped processing. Thixo-formed products also have fine mechanical properties, it’s the hot topic of metal processing technology research in recent years. The process in iron and steel, non-ferrous metal processing is given great attention, a large number of monographs, papers about this aspect emerge very quickly. Based on lots of documentations, the author will discuss these aspects, introduction of semi-solid processing, basic principle, research situation and application prospect through her integration and thinking.Key Words: semi-solid processing; slurry making; forming technology; numerical simulation; application prospect.液体与固体是我们比较熟悉的两种物质存在形态,而液体与固体之间尚存在一种软物质,称为半固态物质或半固态金属,其流动时表现为粘塑性行为,结果产生永久变形。
铝合金半固态压铸成形过程的模拟

成明显的温度梯度。
凝固过程
随着温度的下降,铝合金逐渐凝固, 凝固顺序与温度分布密切相关。
热节与冷隔
在温度场模拟中,可以发现热节 (局部高温区域)和冷隔(局部低 温区域)现象,这些区域对铸件质 量有重要影响。
流场模拟结果分析
充填过程
流动前沿与流动末端
本研究成果有助于推动铝合金半固态压铸技术的发展,提 高其在工业生产中的应用水平,促进相关产业的进步。
未来研究方向与展望
01
完善模拟方法,提高 模拟精度
未来可以进一步完善铝合金半固态压 铸成形过程的模拟方法,提高模拟精 度和效率,以更好地指导实际生产。
02
拓展应用领域,探索 新工艺
可以探索将铝合金半固态压铸技术应 用于更多领域,如航空航天、汽车制 造等,并研究新工艺,以满足不同领 域的需求。
成形精度高
半固态铝合金具有良好的流动性和触 变性,能够精确填充模具型腔,减少 飞边和毛刺等缺陷,提高零件的成形 精度。
组织性能好
半固态铝合金在成形过程中经历了固 液共存状态,有利于晶粒细化和均匀 化,提高材料的力学性能和耐蚀性。
铝合金半固态压铸成形技术原理及特点
生产效率高
铝合金半固态压铸成形技术具有 高效、自动化的特点,可大幅缩 短生产周期和降低成本,适用于 大规模生产。
优化后工艺参数的确定
1 2
综合评估
根据正交试验、数值模拟和人工智能算法的分析 结果,综合评估各工艺参数对成形质量的影响, 确定最优工艺参数组合。
实验验证
通过实际压铸实验对优化后的工艺参数进行验证, 确保优化结果的准确性和可靠性。
3
参数调整
在实际生产过程中,根据设备状况、原材料批次 等因素对工艺参数进行适当调整,以保证生产稳 定性和产品质量的稳定性。
铝合金半固态成形技术发展现状

铝合金半固态成形技术发展现状
修磊;张之荣;金飞翔
【期刊名称】《科技风》
【年(卷),期】2024()10
【摘要】铝合金半固态成形技术是一种新型的金属成形技术,广泛应用于航空、汽车、船舶、电子、建筑和机械等领域。
本文首先介绍了铝合金半固态成形技术的概念、分类和特点;其次,分别从成形方法、成形工艺、设备和模具等方面对其发展现状进行了阐述;最后,对其未来发展进行了展望。
【总页数】4页(P1-4)
【作者】修磊;张之荣;金飞翔
【作者单位】合肥学院先进制造工程学院
【正文语种】中文
【中图分类】F764.3
【相关文献】
1.铝合金半固态成形工艺及力学性能的研究现状
2.A356铝合金半固态成形触变成形力的计算
3.铝合金半固态成形工艺及力学性能的研究现状
4.铝合金与镁合金半固态成形技术研究进展:当前中国的发展现状、机遇与挑战
5.铸造ZL109铝合金和变形7050铝合金半固态成形过程组织演变的对比研究
因版权原因,仅展示原文概要,查看原文内容请购买。
半固态成形发展概况及研究进展

半固态成形利用金属材料在固液共存状态下所特有的流变特性进行成形的技术。
首先要制造含有一定体积比例的非枝晶固相的固液混合浆料,成形方法有流变成形和触变成形两种。
优点:1、在工艺方面:成型温度低,延长模具寿命(热冲击小);节省能源;改善生产条件和环境。
2、在产品方面:铸件质量提高(减少气孔和凝固收缩);减少加工余量;零件的尺寸和精度能达到近终形;扩大压铸合金的范围并可以发展金属复合材料。
所谓半固态加工是指金属在凝固过程中,对其施以剧烈的搅拌作用或扰动作用,得到一种液态金属母液,其中均匀悬浮着一定量的球状初生固相或退化的枝晶固相的固2液混合浆料(也称流变浆料) ,对这种浆料进行的加工成型的方法。
半固态成型包括半固态流变成型和半固态触变成型两类,前者是将制备好的半固态浆料直接用于成型,如压铸成型(称为半固态流变压铸成型) ;后者是对制备好的半固态坯料进行重新加热使其达到半熔融状态,然后进行成型,如挤压成型(称为半固态触变挤压)[1]。
1半固态金属成形的发展及现状(半固态成形铝合金材料研究)半固态金属(SSM)成形技术自DavidSpencer于1971年首次提出至今,已有30多年历史【2-5】。
综观整个历史过程,其发展可以分为实验研究、应用研究和工程化应用三个阶段。
从20世纪70年代初开始,实验研究工作大约延续了15年。
这一阶段的研究主要集中在探索具有流变性和触变性的有色金属合金半固态试样的组织特征与制备方法上。
主要成果包括:①揭示了流变性和触变性坯料的组织特征;②提出了枝晶组织向非枝晶组织转变的物理模型:③研究了搅拌速度、强度以及温度等工艺参数对非枝晶化过程的影响规律:④初步探讨了半固态微观组织与流变性能的关系;⑤测试了半固态合金流变性能,并建立了相关的数学模型。
上世纪80年代中期是半固态成形技术应用研究的迅速发展阶段,并且从早期的有色金属合金扩展到高熔点合金以及复合材料的半固态成形。
这期间,开发与研制了包括电磁搅拌在内的多种半固态制坯技术与连铸设备;利用计算机模拟技术揭示了半固态合金充型过程;深入细致研究了成形工艺对产品组织性能影响的规律。
半固态加工技术的发展及其研究现状
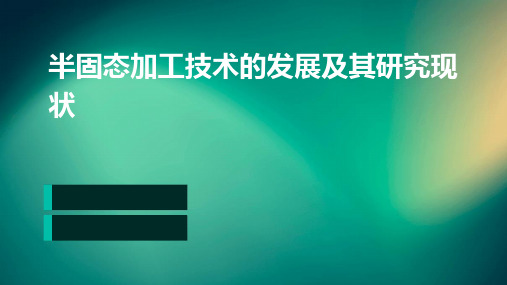
技术瓶颈与挑战
流变行为复杂
半固态加工过程中,材料的流变行为受多种因素影响,如温度、 应变速率等,导致加工过程难以控制。
界面问题
在半固态加工过程中,由于固液两相的存在,界面问题成为一大挑 战,如固液界面稳定性、颗粒分散等。
设备与工艺匹配
半固态加工需要特殊的设备和工艺,如何实现设备和工艺的匹配, 提高加工效率是亟待解决的问题。
未来发展前景与展望
拓展应用领域
随着半固态加工技术的不断成熟, 其应用领域将进一步拓展,如航 空航天、汽车、新能源等领域。
绿ቤተ መጻሕፍቲ ባይዱ可持续发展
半固态加工技术具有节能减排的潜 力,未来将在绿色可持续发展领域 发挥重要作用。
智能化与自动化
随着智能制造技术的发展,半固态 加工将实现智能化与自动化,提高 加工效率和产品质量。
01
02
03
汽车工业
研究半固态加工技术在汽 车零部件制造中的应用, 提高零部件的性能和轻量 化水平。
航空航天工业
探索半固态加工技术在航 空航天领域的应用,满足 高性能、轻质材料的需求。
电子产品
研究半固态加工技术在电 子产品外壳、连接器等制 造中的应用,实现产品的 小型化、轻薄化。
04 半固态加工技术的挑战与 前景
输标02入题
应用领域:航空航天业
01
03
优势特点:半固态加工技术能够控制零件的内部结构 和微观组织,提高零件的疲劳寿命和可靠性,满足航
空航天器的高性能要求。
04
技术应用:半固态加工技术用于制造航空航天器的关 键零部件,如发动机叶片、机翼结构件等。
成功应用的案例三
案例名称
医疗器械制造
应用领域
医疗器械制造业
半固态加工及其在铝镁合金中的应用

1.引言我国的铸造业有着悠久的历史,随着铸造技术的发展以及对铸造品品质的更高要求, 传统的铸造方式表现出了在环保和轻量化等方面的不足, 这就要求我们采取更为先进的铸造技术。
为满足新的铸造要求, 半固态铸造应运而生, 并且因为其表现出来的更为高效、更加节能以及更高品质等特性, 得到了广泛的认可和关注。
1.1半固态加工的定义自从20世纪70年代初,美国麻省理工学院MC Flemings 教授及其领导的科研小组发现半固态金属的触变性能以来,现已成功地应用于多种有色金属及黑色金属。
半固态加工指在金属凝固过程中,把金属保持在固-液两相温度区间内,进行剧烈搅拌,将凝固过程中形成的枝晶打碎,然后直接进行流变铸造或先制备半固态铸造,后进行局部重熔和触变成形。
这样得到的产品具有一次相为球形颗粒的组织。
1980年,DOW 化学公司首创了镁合金半固态成形工艺,激发了该技术的研究热潮。
其基本原理是利用非枝晶半固态金属(Semi-Solid Metals,SSM)独有的流变性和搅熔性控制铸件的质量,典型的枝晶组织和非枝晶组织,如图1 [1]所示。
图1 典型的枝晶组织与非枝晶组织1.2 半固态加工工艺半固态加工工艺分两种:流变铸造和触变成形。
流变铸造(Rheocasting)是麻省理工学院的研究人员于1972年提出的一种制备方法,它是将液态金属一边搅拌一边冷却至固液两相共存区,而后将此半固态黏奖浆直接传送至冷室压铸机铸造成工件,亦称搅动铸造(Stir Casting),如图2所示。
由于半固态金属浆液的保存和输送不方便,该成形方法实际投入应用的较少。
触变铸造(Thixocasting),它是将经搅拌等工艺获得的具有非枝晶组织的半固态坯料冷却凝固后,制成所需要的尺寸,重新加热到半固态温度,然后进行压铸或挤压成形,如图2[1]所示。
由于半固态金属坯料的加热、输送很方便,并且成形过程容易控制,便于实现自动化,因此触变铸造是当今半固态铸造的主要工艺方式。
- 1、下载文档前请自行甄别文档内容的完整性,平台不提供额外的编辑、内容补充、找答案等附加服务。
- 2、"仅部分预览"的文档,不可在线预览部分如存在完整性等问题,可反馈申请退款(可完整预览的文档不适用该条件!)。
- 3、如文档侵犯您的权益,请联系客服反馈,我们会尽快为您处理(人工客服工作时间:9:00-18:30)。
铝合金半固态成形工艺的研究现状
作者:上海大学 余忠土 张恒华 邵光杰 许珞萍
新型的成形技术─―半固态成形
技术(SSM )是一种近终成形(Near-net-shape )的成形工艺。
与传统的成形工艺相比,它有一系列突出的优点:成形温度低,成形件力学性能好,并较好地综合了固态金属模锻与液态压铸成形的优点。
本文阐述了铝合金半固态成形技术的主要工艺方法,其工艺参数与传统液态压铸成形的差异,以及半固态成形件在不同状态下的力学性能
图1 半固态金属压铸流程图
20世纪70年代初,美国麻省理工学院Flemings 等人在实验中发现了半固态金属的流变性能,到70年代中期,Joly 等人进一步探索了半固态金属的这种性能,并出现了半固态金属加工的概念。
所谓半固态金属加工技术即在金属凝固过程中,进行剧烈搅拌,将凝固过程中形成的枝晶打碎或完全抑制枝晶的生长,然後直接进行流变铸造或制备半固态坯锭後,根据产品尺寸下料,再重新加热到半固态温度,然後进行成形加工。
铝合金的半固态加工技术主要有三道工序:半固态坯料的制备、二次重熔和触变成形。
触变成形作为半固态加工技术的最後一道工序,是影响半固态成形件组织和性能的关键工序,直接影响着半固态成形件的组织和性能。
自该技术被开发以来,已经历了30馀年的研究发展,并已召开了六次有关半固态的国际会议,发达国家已经进入生产实用阶段。
因为半固态成形技术有一系列突出的优点:半固态金属成形技术具有高效、优质、节能和近终成形等优点,可以满足现代汽车制造业对有色合金铸件高致密度、高强度、高可靠性、高生产率和低成本等要求,因此倍受汽车制造厂商以及零部件配套生产厂商的重视。
半固态金属加工工艺
SSM成形是介乎铸造和锻造之间的一种工艺过程,是针对固、液态共存的半熔化或半凝固金属进行成形加工的工艺方法的总称,使用於很多常规的成形方法。
半固态金属加工技术主要有两种工艺:一种是将经搅拌获得的半固态金属浆料在保持其半固态温度的条件下直接进行半固态加工,即流变成形(Rheoforming);另一种是将半固态浆料冷却凝固成坯料後,根据产品尺寸下料,再重新加热到半固态温度,然後进行成形加工,即触变成形(Thixoforming),後者在目前的生产条件下占主导地位。
目前,应用在工业上的半固态金属触变方法主要有:半固态压铸、半固态挤压、半固态模锻和半固态压射成形等。
半固态压铸工艺
半固态压铸工艺是目前半固态金属成形的主要成形工艺。
典型的半固态压铸工艺流程图见图1。
半固态铝合金压铸是将半固态坯料二次加热至坯料组织恢复到40%~60%球状初生固相颗粒和共晶液相共存的固液混合态,随即用夹持工具夹持到压铸机压射室中压铸成形,其主要的工艺参数包括压射比压、压射速度、压射时间、模腔温度以及留模时间等。
压射压比是压射室内半固态坯料所受的静压力,是半固态铝合金压铸最重要的工艺参数之一。
由於半固态铝合金压铸时,坯料粘度较大,流动性较液态金属差,为了充分利用半固态铝合金坯料的流变性,在成形时,压射比压一般比液态金属压铸时高20%~30%。
压射速度为压射室内压塞的推进速度。
由於半固态坯料具有一定的粘度,因此在低速压射阶段,其流动相对液态更平稳,也不存在液态金属压射时的喷射、紊流和卷气现象,因此该阶段的压射速度可比液态金属压铸时快,有利於提高充型速度,缩短充型时间,提高铸件表面质量。
压铸机的料缸尺寸应根据半固态坯料的大小来设计,由於半固态坯料在二次加热时表面有一层薄薄的氧化膜,为了除去这一层氧化膜,料缸的直径必须比坯料的直径稍小,并充分考虑半固态坯料在二次加热时的膨胀系数。
料缸在压铸前要适当的预热,以保证半固态坯料压射前在料缸中不会冷却凝固,并保持稳定。
除了要预热外,还要在料缸表面涂上一层润滑剂,以保证坯料不会和料缸表面粘在一起,但选择润滑剂时,要考虑其对半固态成形件性能的影响。
半固态铝合金压铸时模具内的温度也比液态金属压铸时要高,且要求温度稳定,一般应控制在200℃~350℃。
其型腔内浇注系统常采用开放式浇注系统、浇道流程
短、浇道位置不远离铸件。
留模时间是指半固态坯料被压入模腔直到模腔被打开时成形件在模腔所停留的时间。
留模时间直接影响这成形件的冷却速度,以及铸件的组织状况。
因为留模时间长,即更长的保压时间会使铸件中没来得及填充的部位在保压下由浆料来填充。
但时间太长,则会引起粘模现象。
半固态金属锻造
半固态金属锻造与半固态金属触变压铸实质上并无明显差别,其主要不同之处在於前者是用半固态金属在锻造设备上加工成形。
锻造半固态金属可以在较低的压力下进行,这使得一些传统锻造无法成形的形状复杂构件可以在半固态金属锻造方法来生产,其锻造设备可分为立式和卧式压力机两种。
半固态锻造是将加热到半固态的坯料,在锻模中进行以压缩变形为主的模锻以获得所需形状、性能制品的加工方法。
半固态锻造可以成形变形力较大的高固相率的半固态材料,并达到一般锻造难以达到的复杂形状。
而且,可以用於制造用普通锻造难以成形的许多超合金,有可能用半固态锻造技术制造出特殊材料的耐热零件。
锻造速度每秒几百mm到一千多mm,模压从几Mpa到十多Mpa,甚至更高。
半固态锻造零件的总量可从20g~13.6kg,锻造速率可达120~360件/分,并能实现自动化。
目前,已经利用半固态锻造技术进行了联轴节、齿轮等机械零件制造的研究。
半固态金属挤压成形
半固态挤压成形即将坯料加热到半固态,然後放入挤压模腔,用凸模施加压力,通过凹模口挤出所需制品。
半固态坯料在挤压模腔内处於密闭状态,流动变形的自由度低,内部的固相、液相成分不易单独流动,除挤压开始时若干液相成分有先行流出的倾向外,在进入正常挤压状态後,两者一起从模口挤出,在长度方向上得到稳定、均一的制品。
其他半固态金属成形
除了上述半固态金属成形方法外,还有一些正处於开发状态下的半固体金属成形法:如半固态压射成形以及半固态铸造和锻造复合法等。
半固态成形件的力学性能。