FCS和DCS的结构特点与区别
PLC、DCS、FCS三大工业控制系统的区别

PLC›DCS、FCS三大工业控制系统的区别随着工业技术的快速发展,相继出现了集散控制系统和现场总线控制系统,一些行业当中有的人认为FCS是由PLC发展而来的;另一些行业的人认为FCS又是由DCS发展而来的。
FCS与PLC及DCS之间既有密不可分的关联,又存在着本质的区别。
在工业过程控制中的三大控制系统,分别是PLC、DCS、FCSoPLC控制器是一种数字运算操作的电子系统,专为工业环境下的应用而设计。
它采用一类可编程的存储器,用于其内部存储程序、执行逻辑运算、顺序控制、定时、计数与算术操作等面向用户的指令,并通过数字式或模拟式输入或输出,控制各种类型的机械或生产过程。
DCS集散控制系统,又叫计算机分布式控制系统,它是20世纪70年代中期迅速发展起来的,它把控制技术、计算机技术、图像显示技术以及通信技术结合起来,也称作4C技术,实现了对生产过程的监视、控制和管理。
它既打破了常规控制仪表功能的局限性,又较好的解决了早期计算机系统对于信息、管理和控制作用过于集中带来的危险性。
FCS现场总线控制系统的核心是总线协议,基础是数字智能现场设备,本质是信息处理现场化。
1、大型PLC构成的过程控制系统的基本特点⑴从上到下的结构,PLC既可以作为独立的DCS,也可以作为DCS的子系统。
(2)PID放在控制站中,可实现连续PID控制等各种功能。
⑶可用一台PC为主站,多台同类型PLC为从站;也可用一台PLC为主站,多台同类型PLC为从站,构成PLC网络。
⑷主要用于工控中的顺序控制,新型PLC也兼有闭环控制功能。
2、DCS控制系统的基本特点⑴从上到下的树状系统,其中通信是关键。
(2)PID在控制器中,连接计算机与现场仪器仪表。
⑶是树状拓扑和并行连续的链路结构,有大量电缆从中继站并行到现场仪器仪表。
⑷信号系统包括开关量信号和模拟信号。
(5)DCS一般是由现场仪表层、控制装置单元层、工厂(车间)层、和企业管理层构成。
传统DCS-现场级设备与控制器之间连接采用一对一I/O连线方式3、FCS控制系统的基本特点(I)FCS是3C技术的融合。
PLC、DSC、FCS三大控制系统的特点和差异
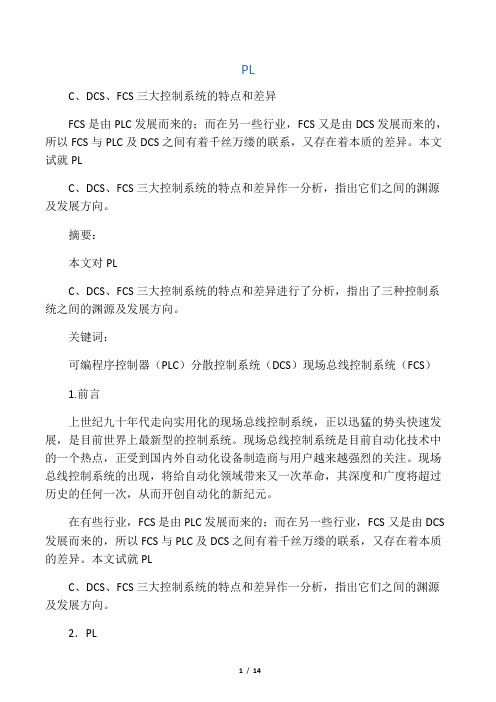
PLC、DCS、FCS三大控制系统的特点和差异FCS是由PLC发展而来的;而在另一些行业,FCS又是由DCS发展而来的,所以FCS与PLC及DCS之间有着千丝万缕的联系,又存在着本质的差异。
本文试就PLC、DCS、FCS三大控制系统的特点和差异作一分析,指出它们之间的渊源及发展方向。
摘要:本文对PLC、DCS、FCS三大控制系统的特点和差异进行了分析,指出了三种控制系统之间的渊源及发展方向。
关键词:可编程序控制器(PLC)分散控制系统(DCS)现场总线控制系统(FCS)1.前言上世纪九十年代走向实用化的现场总线控制系统,正以迅猛的势头快速发展,是目前世界上最新型的控制系统。
现场总线控制系统是目前自动化技术中的一个热点,正受到国内外自动化设备制造商与用户越来越强烈的关注。
现场总线控制系统的出现,将给自动化领域带来又一次革命,其深度和广度将超过历史的任何一次,从而开创自动化的新纪元。
在有些行业,FCS是由PLC发展而来的;而在另一些行业,FCS又是由DCS 发展而来的,所以FCS与PLC及DCS之间有着千丝万缕的联系,又存在着本质的差异。
本文试就PLC、DCS、FCS三大控制系统的特点和差异作一分析,指出它们之间的渊源及发展方向。
2.PLC、DCS、FCS三大控制系统的基本特点目前,在连续型流程生产自动控制(PA)或习惯称之谓工业过程控制中,有三大控制系统,即PLC、DCS和FCS。
它们各自的基本特点如下:2.1 PLC(1)从开关量控制发展到顺序控制、运送处理,是从下往上的。
(2)连续PID控制等多功能,PID在中断站中。
(3)可用一台PC机为主站,多台同型PLC为从站。
(4)也可一台PLC为主站,多台同型PLC为从站,构成PLC网络。
这比用PC机作主站方便之处是:有用户编程时,不必知道通信协议,只要按说明书格式写就行。
(5)PLC网格既可作为独立DCS/TDCS,也可作为DCS/TDCS的子系统。
现场控制系统FCS 和集散控制系统DCS的对比

现场控制系统FCS 和集散控制系统DCS 的对比1 引言当今的时代是一个信息化的时代,自动控制技术发展日新月异。
随着网络技术的不断发展,因特网把全世界的计算机信息系统,通信系统逐渐集成起来,形成信息高速公路和公用数据网络[1]。
现场总线(field bus)是用于最终控制设备与上层自动化控制设备之间的双向串行通信链络,目前主要的现场总线标准有HART、LonWorks、PROFIBUS、InterBus、FF、CAN 即控制器局域网技术[2]。
现场总线是应运而生的,作为工业系统控制技术领域划时代的标志,它的出现必将对该领域的发展产生重要影响。
现场总线技术以其高速、可靠、布线简单,费用低廉等优点得到越来越广泛的应用,特别是在制造业自动化、过程控制自动化、电力、楼宇、铁路交通等方面[3]。
现场总线技术将专用微处理器置入传统的测量控制仪表,使它们各自具有了数字计算和数字通讯能力,采用可进行简单连接的双绞线等作为总线,把多个测量控制仪表连接成网络系统,并按公开、规范的通信协议,在位于现场的多个微机化测量控制设备之间及现场仪表与远程监控计算机之间,实现数据传输与信息交换,形成各种适应实际需要的自动控制系统[4]。
2 现场总线的简介现场总线(field bus)是应用在生产现场、在微机化测量控制设备之间实现双向串行多节点的数字通信系统,也被称为开放式、数字化、多点通信的底层控制网络[5,11]。
IEC 对现场总线的定义是:“安装在制造和过程区域的现场装置与控制室内的自动控制装置之间的数字式,双向串行传输,多点通信的数据总线称为现场总线。
”[6]这种总线是用做现场控制系统的、直接与所有受控(设备)节点进行串行相连的通信网络[7],按ISO 的OSI 标准提供网络服务,可靠性高,稳定性好。
它采用了三层网络结构——物理层,数据链路层和应用层[8]。
这种网络结构具有结构简单,执行协议直观,价格低廉等优点,同时性能又中国设计师网自控频道w w w ..z k .s h e j i s .c o m能令人满意[9]。
dcs与fcs的区别

(2)DCS系统是封闭式系统,各公司产品基本不兼容。而FCS系统是开放式系统,用户可以选择不同厂商、不同品牌的各种设备连入现场总线,达到最佳的系统集成。
(3)DCS系统的信息全都是二进制或模拟信号形成的,必须有D/A与A/D转换。而FCS系统是全数字化,就免去了D/A与A/D变换,高集成化高性能,使精度可以从±0.5%提高到±0.1%。
现在一些带现场总线的现场仪表本身装了许多功能块,虽然不同产品同种功能块在性能上会稍有差别,但一个网络支路上有许多功能雷同功能块的情况是客观存在。选用哪一个现场仪表上的功能,是系统组态要解决的问题。
考虑这个问题的原则是:尽量减少总线上的信息往返。一般可以选择与该功能有关的信息输出最多的那台仪表上的功能块。
2、FCS
FCS的关键要点有以下三点。
(1)FCS系统的核心是总线协议,即总线标准。
一种类型的总线,只要其总线协议一经确定,相关的关键技术与有关的设备也就被确定,就其总线协议的基本原理而言,各类总线都是一样的,都以解决双向串行数字化通信传输为基本依据。但是由于各种原因,各类总线的总线协议存在很大的差异。文章来源:中国自动化网社区
通过上述,我们是否可以得出这样一种映象:开放的现场总线控制系统的互操作性,就一个特定类型的现场总线而言,只要遵循该类型现场总线的总线协议,对其产品是开放的,并具有互操作性,换句话说,不论什么厂家的产品,也不一定是该现场总线公司的产品,只要遵循该总线的总线协议,产品之间是开放的,并具有互操作性,就可以组成总线网络。
(9)用于过程控制的FCS设计开发要点。这一点并不作为DCS比较,只是说明用于过程控制或者说用于模拟连续过程类的FCS在设计开发中应重点考虑的问题。
①要求总线本安防爆功能,而且是头等重要的。文章来源:中国自动化网社区
再说DCS和FCS区别

再说DCS和FCS区别
(1).开放性和可互操作性
开放性FCS将打破DCS大型厂家的垄断,给中小企业发展带来了平等竞争的机遇。
可互操作性实现控制产品的“即插即用”功能,从而使不同厂家的工控产品可以互换和替换。
(2).分散性
彻底的分散性意味着系统具有较高的可靠性和灵活性,系统很容易进行重组和扩建,且易于维护。
(3).低成本
衡量一套控制系统的总体成本,不仅考虑其造价,而且应该考察系统安装调试尤其是运行维护整个生命周期内总投入。
相对DCS而言,FCS开放的体系结构和OEM技术将大大缩短开发周期,降低开发成本,且彻底分散的分布式结构将1对1模拟信号传输方式变为1对N的数字信号传输方式,节省了模拟信号传输过程中大量的A/D、D/A转换装置,网络协议传输取代大量的信号线布线中的安装成本,可靠的性能降低了维护费用。
因此从总体上来看,FCS的成本大大低于DCS的成本。
从维护角度看,FCS以其协议统一、互相兼容、合理可靠方便生产;从成本角度,更是FCS取代DCS的理由。
来补充:
FCS的结构比 DCS简单,FCS系统中没有了控制器,其控制功能已有现场仪表及设备来实现。
二者的传输介质差别很大,DCS每个检测点需要1根传输4-20mA标准信号的导线,而 FCS 全部检测信号的传输仅需 1根传输数字信号的双绞线
FCS系统比 DCS系统更好地体现了“信息集中,控制分散”的思想
FCS可做到系统从上到下全开放;DCS只能做到操作站以上开放,而控制层不可能开放
由于结构上的改变,FCS比DCS更节约硬件设备,仪表精度得到极大的提高,控制周期大为缩短,改善了调节性能。
1集散控制系统DCS与现场总线控制系统FCS的比较
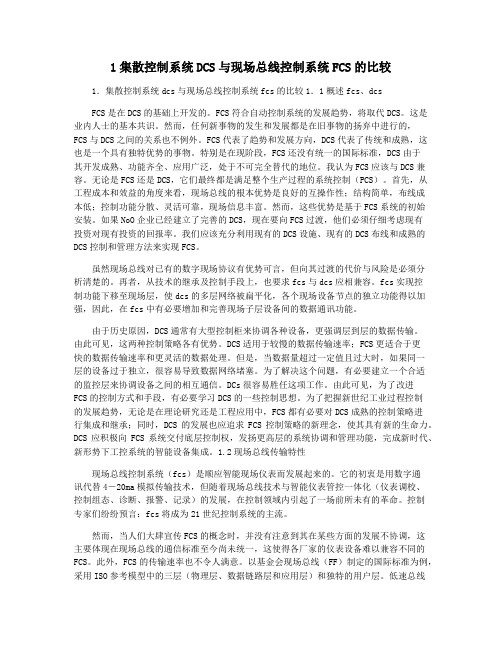
1集散控制系统DCS与现场总线控制系统FCS的比较1.集散控制系统dcs与现场总线控制系统fcs的比较1.1概述fcs、dcsFCS是在DCS的基础上开发的。
FCS符合自动控制系统的发展趋势,将取代DCS。
这是业内人士的基本共识。
然而,任何新事物的发生和发展都是在旧事物的扬弃中进行的,FCS与DCS之间的关系也不例外。
FCS代表了趋势和发展方向,DCS代表了传统和成熟,这也是一个具有独特优势的事物。
特别是在现阶段,FCS还没有统一的国际标准,DCS由于其开发成熟、功能齐全、应用广泛,处于不可完全替代的地位。
我认为FCS应该与DCS兼容。
无论是FCS还是DCS,它们最终都是满足整个生产过程的系统控制(PCS)。
首先,从工程成本和效益的角度来看,现场总线的根本优势是良好的互操作性;结构简单,布线成本低;控制功能分散、灵活可靠,现场信息丰富。
然而,这些优势是基于FCS系统的初始安装。
如果NoO企业已经建立了完善的DCS,现在要向FCS过渡,他们必须仔细考虑现有投资对现有投资的回报率。
我们应该充分利用现有的DCS设施、现有的DCS布线和成熟的DCS控制和管理方法来实现FCS。
虽然现场总线对已有的数字现场协议有优势可言,但向其过渡的代价与风险是必须分析清楚的。
再者,从技术的继承及控制手段上,也要求fcs与dcs应相兼容。
fcs实现控制功能下移至现场层,使dcs的多层网络被扁平化,各个现场设备节点的独立功能得以加强,因此,在fcs中有必要增加和完善现场子层设备间的数据通讯功能。
由于历史原因,DCS通常有大型控制柜来协调各种设备,更强调层到层的数据传输。
由此可见,这两种控制策略各有优势。
DCS适用于较慢的数据传输速率;FCS更适合于更快的数据传输速率和更灵活的数据处理。
但是,当数据量超过一定值且过大时,如果同一层的设备过于独立,很容易导致数据网络堵塞。
为了解决这个问题,有必要建立一个合适的监控层来协调设备之间的相互通信。
DCS与FCS在控制系统中比较
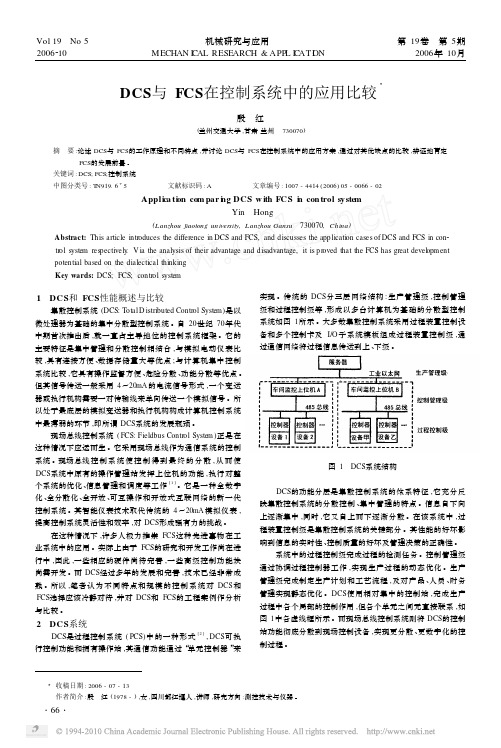
DCS 与FCS 在控制系统中的应用比较3殷 红(兰州交通大学,甘肃兰州 730070)摘 要:论述DCS 与FCS 的工作原理和不同特点,并讨论DCS 与FCS 在控制系统中的应用方案,通过对其优缺点的比较,辨证地肯定FCS 的发展前景。
关键词:DCS;FCS;控制系统中图分类号:T N919.6+5 文献标识码:A 文章编号:1007-4414(2006)05-0066-02Appli ca ti on com par i n g DCS w ith FCS i n con trol syste mYin Hong(L anzhou jiaotong university,L anzhou Gansu 730070,China )Abstract:This article intr oduces the difference in DCS and FCS,and discusses the app licati on cases of DCS and FCS in con 2tr ol syste m res pectively .V ia the analysis of their advantage and disadvantage,it is p r oved that the FCS has great devel opment potential based on the dialectical thinking .Key wards:DCS;FCS;contr ol syste m1 DCS 和FCS 性能概述与比较集散控制系统(DCS:Total D istributed Contr ol Syste m )是以微处理器为基础的集中分散型控制系统。
自20世纪70年代中期首次推出后,就一直占主导地位的控制系统框架。
它的主要特征是集中管理和分散控制相结合,与模拟电动仪表比较,具有连接方便、数据存储量大等优点;与计算机集中控制系统比较,它具有操作监督方便、危险分散、功能分散等优点。
DCS和FCS两大控制系统的区别

DCS和FCS两大控制系统的区别DCS和FCS两大控制系统的区别 DCS、FCS两大控制系统的区别及比较,DCS、FCS控制系统的基本要点。
1引言过程控制以计算机控制作为主流。
近年来,计算机技术的飞速发展正迅速改变着工业自动化的现状,传统的生产过程计算机控制系统已仅仅是一个狭义的概念,现代计算机控制系统的含义已被大大扩展,它不仅包含我们最熟悉的各种自动控制系统、各种顺序逻辑控制系统、各种自动批处理控制系统及联锁保护系统,还包括了各生产工段和各生产车间的优化调度系统,以及整个企业的决策系统和管理系统。
本文重点分析作为现代工业顺序逻辑控制的可编程逻辑控制PLC、现代工业主流的集散型控制系统(DCS)和未来工业主流的现场总线控制系统(FCS)及其相互关系。
2 DCS、FCS控制系统的基本要点目前,在连续型流程生产自动控制(PA)或习惯称之为工业过程控制中,有两大控制系统,即DCS和FCS。
它们的各自基本要点如下:2.1DCS或TDCS (1)分散控制系统DCS与集散控制系统是集通讯、计算、控制、显示4C(Communication,Computer,Control,CRT)技术于一身的监控技术。
(2)从上到下的树状拓扑大系统,其中通信(Communication)是关键。
(3)PID在中继站中,中继站联接计算机与现场仪器仪表与控制装置。
(4)模拟信号A/D-D/A带微处理的混合。
(5)一台仪表一对线接到I/O,由控制站挂到局域网LAN。
(6)DCS是控制(工程师站)、操作(操作员站)、现场仪表(现场控制站)的三级结构。
(7)缺点是成本高,各公司产品不能互换,不能互操作,大DCS系统是各家不同的。
(8)用于大规模的连续过程控制,如石化等。
(9)制造商:Bailey(美)、Westinghouse(美)、HITACH(日)、LEEDS&NORTHRMP(美)、Siemens(德)、Foxboro(美)、ABB(瑞士)2.2FCS (1)基本任务是:本质(本征)、安全、危险区域、易变过程、难于对付的非常环境。
现场总线控制系统FCS和集散控制系统DCS的差异

现场总线控制系统FCS和集散控制系统DCS的差异发表时间:2018-07-02T11:19:27.703Z 来源:《电力设备》2018年第7期作者:盛佳[导读] 摘要:现场总线具有高性能和高可靠性特点,现已形成国际标准。
(山西漳电同达热电有限公司山西省大同市 037003)摘要:现场总线具有高性能和高可靠性特点,现已形成国际标准。
现场控制总线系统比传统的集散控制系统的能力好,准确度高,误码率低。
本论文通过对集散控制系统(DCS)与现场总线控制系统(FCS)的研究,阐述了集散控制系统发展到现场总线控制系统的进步性。
同时,论文分析现场总线的体系结构、功能、类型,比较集散控制系统与现场总线控制系统的区别。
本文从系统可靠性、管理维护要求、信息传输精度等方面进行了的对比分析,认为DCS在维持一定的活跃性同时,FCS也将成为工业控制领域发展的主流。
关键词:集散控制系统(DCS);现场总线控制系统(FCS);比较研究集散控制系统DCS的本质是以微处理为基础,综合4C技术(计算机技术、测量控制技术、通信网络技术、屏幕显示技术)成果,对生产过程进行集中监视、操作、管理和分散控制的综合计算机控制系统。
从80年代中期起,在集散控制系统蓬勃发展的基础上,一种更为开放的现场总线开始出现。
现场总线是一种适用于工业现场控制的网络集成式全分布控制系统FCS。
本文对集散控制系统DCS与现场总线控制系统FCS的构成和特点进行比较和分析,分析了两种系统之间的优劣并阐述了二者之间的联系和发展趋势。
一、FCS的特点研究现场总线控制系统FCS(Field Bus Con-trol System)是基于现场总线技术的控制系统。
现场总线是用于现场仪表与控制系统之间的一种分散、全数字化、智能、双向互联、多变量、多点、多站的通信网络系统。
现场总线控制系统由于采用了智能现场设备,把控制功能直接置于现场设备之中,各输入输出模块置入现场设备,现场设备具有通信能力,现场的测量变送仪表可以与阀门等执行机构直接传送信号,实现了彻底的分散控制。
DCS与FCS间的区别
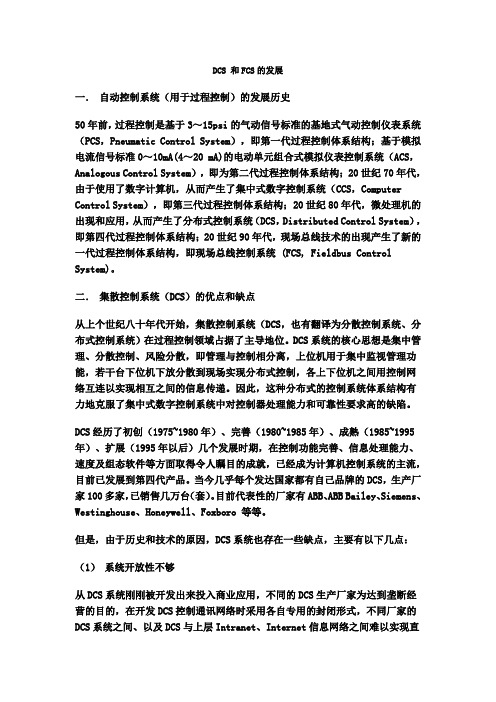
DCS 和FCS的发展一.自动控制系统(用于过程控制)的发展历史50年前,过程控制是基于3~15psi的气动信号标准的基地式气动控制仪表系统(PCS,Pneumatic Control System),即第一代过程控制体系结构;基于模拟电流信号标准0~10mA(4~20 mA)的电动单元组合式模拟仪表控制系统(ACS,Analogous Control System),即为第二代过程控制体系结构;20世纪70年代,由于使用了数字计算机,从而产生了集中式数字控制系统(CCS,Computer Control System),即第三代过程控制体系结构;20世纪80年代,微处理机的出现和应用,从而产生了分布式控制系统(DCS,Distributed Control System),即第四代过程控制体系结构;20世纪90年代,现场总线技术的出现产生了新的一代过程控制体系结构,即现场总线控制系统 (FCS, Fieldbus Control System)。
二.集散控制系统(DCS)的优点和缺点从上个世纪八十年代开始,集散控制系统(DCS,也有翻译为分散控制系统、分布式控制系统)在过程控制领域占据了主导地位。
DCS系统的核心思想是集中管理、分散控制、风险分散,即管理与控制相分离,上位机用于集中监视管理功能,若干台下位机下放分散到现场实现分布式控制,各上下位机之间用控制网络互连以实现相互之间的信息传递。
因此,这种分布式的控制系统体系结构有力地克服了集中式数字控制系统中对控制器处理能力和可靠性要求高的缺陷。
DCS经历了初创(1975~1980年)、完善(1980~1985年)、成熟(1985~1995年)、扩展(1995年以后)几个发展时期,在控制功能完善、信息处理能力、速度及组态软件等方面取得令人瞩目的成就,已经成为计算机控制系统的主流,目前已发展到第四代产品。
当今几乎每个发达国家都有自己品牌的DCS,生产厂家100多家,已销售几万台(套)。
三大控制系统PLC、DCS和FCS的特点介绍
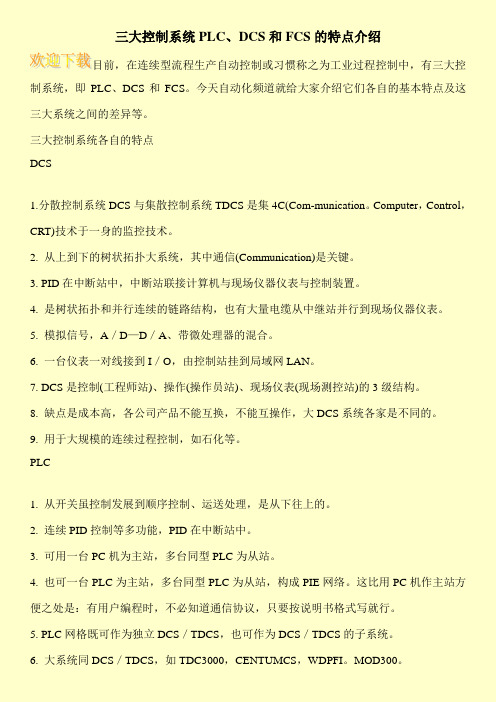
三大控制系统PLC、DCS和FCS的特点介绍目前,在连续型流程生产自动控制或习惯称之为工业过程控制中,有三大控制系统,即PLC、DCS和FCS。
今天自动化频道就给大家介绍它们各自的基本特点及这三大系统之间的差异等。
三大控制系统各自的特点DCS1.分散控制系统DCS与集散控制系统TDCS是集4C(Com-munication。
Computer,Control,CRT)技术于一身的监控技术。
2. 从上到下的树状拓扑大系统,其中通信(Communication)是关键。
3. PID在中断站中,中断站联接计算机与现场仪器仪表与控制装置。
4. 是树状拓扑和并行连续的链路结构,也有大量电缆从中继站并行到现场仪器仪表。
5. 模拟信号,A/D—D/A、带微处理器的混合。
6. 一台仪表一对线接到I/O,由控制站挂到局域网LAN。
7. DCS是控制(工程师站)、操作(操作员站)、现场仪表(现场测控站)的3级结构。
8. 缺点是成本高,各公司产品不能互换,不能互操作,大DCS系统各家是不同的。
9. 用于大规模的连续过程控制,如石化等。
PLC1. 从开关虽控制发展到顺序控制、运送处理,是从下往上的。
2. 连续PID控制等多功能,PID在中断站中。
3. 可用一台PC机为主站,多台同型PLC为从站。
4. 也可一台PLC为主站,多台同型PLC为从站,构成PIE网络。
这比用PC机作主站方便之处是:有用户编程时,不必知道通信协议,只要按说明书格式写就行。
5. PLC网格既可作为独立DCS/TDCS,也可作为DCS/TDCS的子系统。
6. 大系统同DCS/TDCS,如TDC3000,CENTUMCS,WDPFI。
MOD300。
PLC,DCS,FCS的区别联系特点及应用场合分析

PLC,DCS,FCS的区别联系,特点及应用场合分析物联网工程学院自动化在冶金、石化、纺织、电力、汽车制造等多个行业的设备安装工程中都涉及自动化控制系统。
本文对比分析了P L C 、D C S 、FCS 三大自动控制系统的特点和差异,介绍了系统的应用及其发展前景。
1 PLC、DCS、FCS 三大类型控制系统的基本特点1.1 可编程序控制器(Programmable LogicController,PLC)的特点(1)从开关量控制发展到顺序控制、运算处理。
( 2 ) 逻辑控制、定时控制、计数控制、步进(顺序)控制、连续PID 控制、数据控制—— PLC 具有数据处理能力、通信和联网等多功能。
(3)可用一台PC 机为主站,多台同型PLC为从站。
(4)也可一台PLC 为主站,多台同型PLC为从站, 构成P L C 网络。
(5)PLC 网络既可作为独立DCS,也可作为D C S 的子系统。
(6)主要用于工业过程中的顺序控制,新型P L C 也兼有闭环控制功能。
1.2 集散控制系统 (Distributed Control System,DCS)的特点(1)集散控制系统DCS 集4C(Communication,Computer, Control,CRT)技术于一身的监控技术,是第四代过程控制系统。
既有计算机控制系统控制算式先进、精度高、响应速度快的优点,又有仪表控制系统安全可靠、维护方便的优势。
(2)从上到下的树状拓扑大系统,其中通信(Communication)是关键。
(3)是树状拓扑和并行连续的链路结构,有大量电缆从中继站并行到现场仪器仪表。
(4)模拟信号,A/D — D / A 、带微处理器的混合。
是由几台计算机和一些智能仪表智能部件组成,并逐渐地以数字信号来取代模拟信号。
(5)一台仪表一对线接到I / O,由控制站挂到局域网L A N 。
1.3 现场总线控制系统(Fieldbus Control System,FCS)的特点FCS 是第五代过程控制系统, 由PLC 或DCS 发展而来,它是21 世纪自动化控制系统的方向。
DCSFCS工业以太网之间的区别和联系
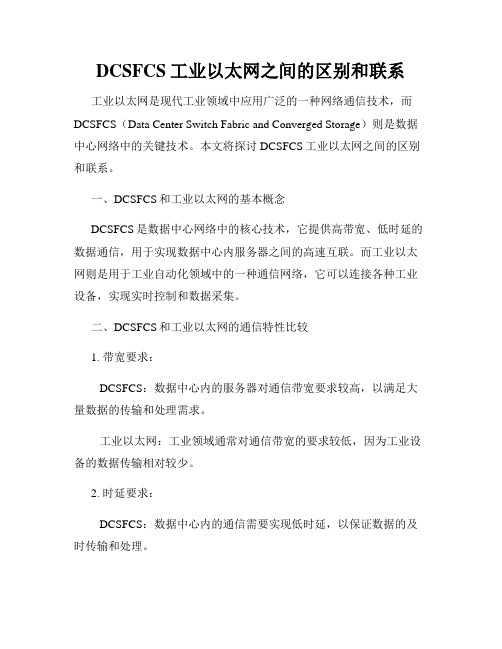
DCSFCS工业以太网之间的区别和联系工业以太网是现代工业领域中应用广泛的一种网络通信技术,而DCSFCS(Data Center Switch Fabric and Converged Storage)则是数据中心网络中的关键技术。
本文将探讨DCSFCS工业以太网之间的区别和联系。
一、DCSFCS和工业以太网的基本概念DCSFCS是数据中心网络中的核心技术,它提供高带宽、低时延的数据通信,用于实现数据中心内服务器之间的高速互联。
而工业以太网则是用于工业自动化领域中的一种通信网络,它可以连接各种工业设备,实现实时控制和数据采集。
二、DCSFCS和工业以太网的通信特性比较1. 带宽要求:DCSFCS:数据中心内的服务器对通信带宽要求较高,以满足大量数据的传输和处理需求。
工业以太网:工业领域通常对通信带宽的要求较低,因为工业设备的数据传输相对较少。
2. 时延要求:DCSFCS:数据中心内的通信需要实现低时延,以保证数据的及时传输和处理。
工业以太网:工业自动化过程通常对通信时延要求较宽松,因为一些控制指令的响应时间可以接受较高的延迟。
3. 可靠性要求:DCSFCS:数据中心的通信需要很高的可靠性,以保证数据传输过程中不出现错误或丢失的情况。
工业以太网:工业领域对通信可靠性的要求较高,以保证工业设备的正常运行和数据的准确采集。
4. 网络拓扑结构:DCSFCS:数据中心网络通常采用多层结构,包括核心层、汇聚层和接入层,以实现高可靠性和高性能的数据通信。
工业以太网:工业自动化网络通常采用总线型或星型拓扑结构,用于连接各个工业设备。
三、DCSFCS和工业以太网的应用领域比较1. 应用范围:DCSFCS:主要应用于数据中心网络中,用于实现服务器之间的高速互联和大规模数据的传输。
工业以太网:主要应用于工业自动化领域,用于连接各种工业设备和实现实时控制。
2. 应用场景:DCSFCS:常见的应用场景包括云计算、大数据处理、虚拟化等领域,旨在提高数据中心的性能和可扩展性。
FCS-DCS两种控制系统比较

流. 在一定程度上成为 ” 孤岛” 信息 。现场 总线是 将专用
微处 理器置入测 量控制 仪表 、 执行器 、 能 马达 控制器 智 等现场 设备之 内 .使 这些 现场设备各 自都具有数 字计 算、 逻辑判断 、 数字通信和智能功能 , 将这些现场智能设 备用于生产对 象就构 成一个 现场控制设备 . 这个现场控
与节点 间 . 点与过程监控计 算机乃至 Itme 之间的 节 ne t 数据传输 、 信息交换 、 远程登录和远程访 问等 。 总 之 .C F S是 以 现 场 总 线 为 基 础 应 用 于 生 产 现 场. 在测 量和控 制设 备之 间实现 双 向 、 串行 、 节点 数 多
逐步完善 、 熟2 世 纪八 、 成 o 九十年代在控制 领域 中 占主 导地位 其 基本思想是分散控制集中管理 D S系统的 C
维普资讯
来 江 , 王 宝 渝 , 边 江 ,祁 玉梅 佟
( . 津水 泥工 业设 计研究 院 ,天津 3 0 0 ;. 1 天 0 4 0 2中国建材 装 备有 限公 司 , 北京 10 3 ; 0 0 7 3中 国建材 工业 对外 经济 技术合 作公 司 , 京 10 3 ) . 北 0 8 1 当前现场总线控制系统(c ) rs 是控 制领域 中的热点.
3 F S n S 比较 C  ̄ DC 的
首先 .C F S的结 构 比 D S简单,C C F S系统 中没有 了 控制器. 其控制功能 已有现场仪表及设备 来实现。更 明 显 的是二 者 的传输 介质 差别很大 ,C D S需要 多根导 线 ,
2 0 . 0 7 8 CHI NA CEMENT 4 9
的缺陷 , 把基于封闭 、 用的解决方案变成 了基于开放 、 专
DCS、FCS、工业以太网之间的区别和联系

DCS、FCS与工业以太网的区别和联系摘要:本文对DCS(集散控制系统/分布式控制系统/distributed control system)、FCS(现场总线控制系统)和工业以太网三种工业自动化控制系统进行了简要的介绍,结合其各自的特点对它们之间的区别和联系进行了论述。
希望读者能够通过本文,对这三种控制系统有一定的认识和了解。
关键词:DCS FCS 工业以太网区别联系1 概述DCS是20世纪70年代随着微处理器的出现而逐渐发展起来的一种计算机控制系统。
因其控制功能分散、操作监视与管理功能集中的特点,称为分布式控制系统。
它是目前在工业控制领域应用最广的计算机控制系统。
由于DCS存在生产厂商专有技术造成的硬件与软件的封闭性,20世纪90年代出现了现场总线技术FCS,它是连接智能测量与控制设备的全数字式、双向传输、具有多节点分支结构的通信链路,是工业自动化领域近年来的热点。
以太网是最著名的几种局域网之一,应用范围很广,它不仅是一种主要的办公自动化局域网,在工业控制网中也得到一定的应用。
以太网在工业控制网络结构中有两种不同的应用,一类是把以太网用在复合型结构的通信网络中作为管理子网,传递生产管理信息;另一类是把以太网当作控制网络使用,即把所有的工作站直接挂在以太网上传递过程数据。
2 三类控制系统的特点2.1DCS的特点典型DCS系统的体系结构一般为三层,即管理级、监控级(工程师站/操作站)和过程控制级,有三级网络连接各层相应的设备。
DCS因而具有三种类型的产品,即仪表型分散控制系统;以PLC为基础的分散控制系统;以PC总线为基础的分散控制系统。
DCS过程控制器与现场变送器的直接连接采用一对一的设备连接方式,需消耗大量的连接电缆且安装和维护费时费力。
DCS属于半数字系统,还需大量的AI/ AO、DI/DO和PI/ PO等中间模板来完成模拟量与数字量间的信息转换。
DCS系统的特点如下:1)集4C(Communication,Computer,Control,CRT)技术与一身;2)是从上到下的树状拓扑系统,其中通信是关键;3)PID功能在中继站中,中继站连接计算机、现场仪器仪表与控制装置;4)是树状拓扑和并行连续的链路结构,也有大量电缆从中继站并行到现场仪器仪表;5)与现场仪器仪表间使用模拟信号进行通信;6)成本高,各公司产品不能互换和互操作;7)常用于控制精度要求高的大规模连续过程控制。
PLC、DCS、FCS三大控制系统的基本特点及区别
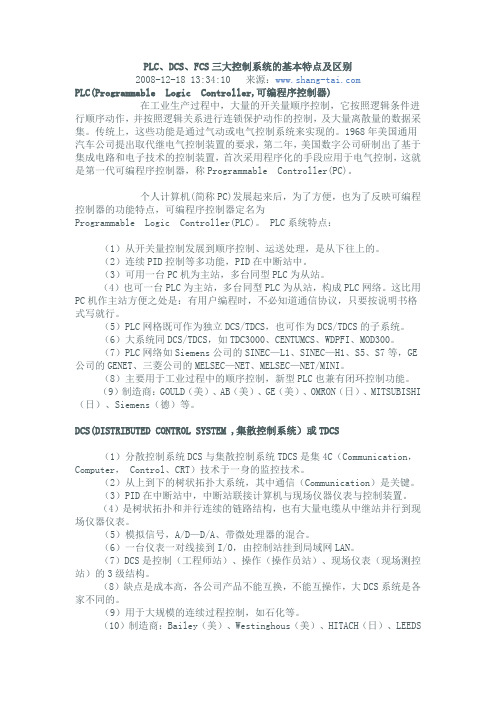
PLC、DCS、FCS三大控制系统的基本特点及区别2008-12-18 13:34:10 来源:PLC(Programmable Logic Controller,可编程序控制器)在工业生产过程中,大量的开关量顺序控制,它按照逻辑条件进行顺序动作,并按照逻辑关系进行连锁保护动作的控制,及大量离散量的数据采集。
传统上,这些功能是通过气动或电气控制系统来实现的。
1968年美国通用汽车公司提出取代继电气控制装置的要求,第二年,美国数字公司研制出了基于集成电路和电子技术的控制装置,首次采用程序化的手段应用于电气控制,这就是第一代可编程序控制器,称Programmable Controller(PC)。
个人计算机(简称PC)发展起来后,为了方便,也为了反映可编程控制器的功能特点,可编程序控制器定名为Programmable Logic Controller(PLC)。
PLC系统特点:(1)从开关量控制发展到顺序控制、运送处理,是从下往上的。
(2)连续PID控制等多功能,PID在中断站中。
(3)可用一台PC机为主站,多台同型PLC为从站。
(4)也可一台PLC为主站,多台同型PLC为从站,构成PLC网络。
这比用PC机作主站方便之处是:有用户编程时,不必知道通信协议,只要按说明书格式写就行。
(5)PLC网格既可作为独立DCS/TDCS,也可作为DCS/TDCS的子系统。
(6)大系统同DCS/TDCS,如TDC3000、CENTUMCS、WDPFI、MOD300。
(7)PLC网络如Siemens公司的SINEC—L1、SINEC—H1、S5、S7等,GE 公司的GENET、三菱公司的MELSEC—NET、MELSEC—NET/MINI。
(8)主要用于工业过程中的顺序控制,新型PLC也兼有闭环控制功能。
(9)制造商:GOULD(美)、AB(美)、GE(美)、OMRON(日)、MITSUBISHI (日)、Siemens(德)等。
DCS、PLC、FCS三大系统比较
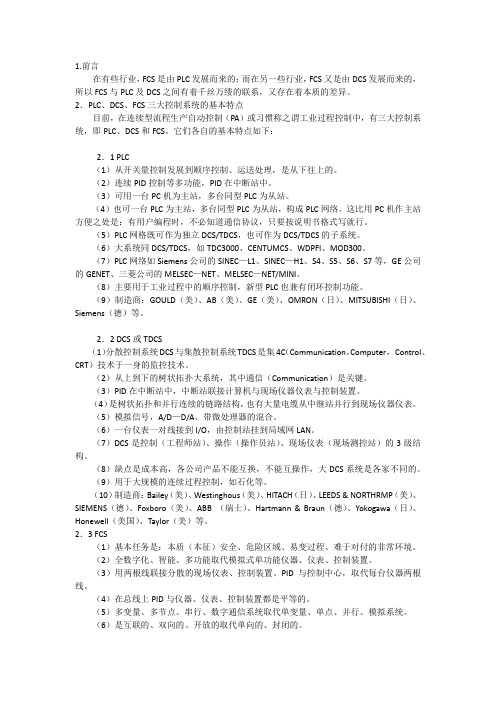
1.前言在有些行业,FCS是由PLC发展而来的;而在另一些行业,FCS又是由DCS发展而来的,所以FCS与PLC及DCS之间有着千丝万缕的联系,又存在着本质的差异。
2.PLC、DCS、FCS三大控制系统的基本特点目前,在连续型流程生产自动控制(PA)或习惯称之谓工业过程控制中,有三大控制系统,即PLC、DCS和FCS。
它们各自的基本特点如下:2.1 PLC(1)从开关量控制发展到顺序控制、运送处理,是从下往上的。
(2)连续PID控制等多功能,PID在中断站中。
(3)可用一台PC机为主站,多台同型PLC为从站。
(4)也可一台PLC为主站,多台同型PLC为从站,构成PLC网络。
这比用PC机作主站方便之处是:有用户编程时,不必知道通信协议,只要按说明书格式写就行。
(5)PLC网格既可作为独立DCS/TDCS,也可作为DCS/TDCS的子系统。
(6)大系统同DCS/TDCS,如TDC3000、CENTUMCS、WDPFI、MOD300。
(7)PLC网络如Siemens公司的SINEC—L1、SINEC—H1、S4、S5、S6、S7等,GE公司的GENET、三菱公司的MELSEC—NET、MELSEC—NET/MINI。
(8)主要用于工业过程中的顺序控制,新型PLC也兼有闭环控制功能。
(9)制造商:GOULD(美)、AB(美)、GE(美)、OMRON(日)、MITSUBISHI(日)、Siemens(德)等。
2.2 DCS或TDCS(1)分散控制系统DCS与集散控制系统TDCS是集4C(Communication,Computer,Control、CRT)技术于一身的监控技术。
(2)从上到下的树状拓扑大系统,其中通信(Communication)是关键。
(3)PID在中断站中,中断站联接计算机与现场仪器仪表与控制装置。
(4)是树状拓扑和并行连续的链路结构,也有大量电缆从中继站并行到现场仪器仪表。
(5)模拟信号,A/D—D/A、带微处理器的混合。
DCS、PLC、FCS三大系统比较
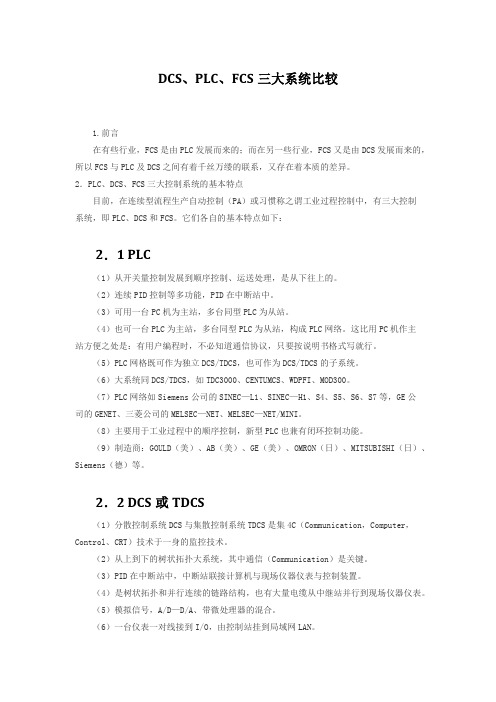
DCS、PLC、FCS三大系统比较1.前言在有些行业,FCS是由PLC发展而来的;而在另一些行业,FCS又是由DCS发展而来的,所以FCS与PLC及DCS之间有着千丝万缕的联系,又存在着本质的差异。
2.PLC、DCS、FCS三大控制系统的基本特点目前,在连续型流程生产自动控制(PA)或习惯称之谓工业过程控制中,有三大控制系统,即PLC、DCS和FCS。
它们各自的基本特点如下:2.1 PLC(1)从开关量控制发展到顺序控制、运送处理,是从下往上的。
(2)连续PID控制等多功能,PID在中断站中。
(3)可用一台PC机为主站,多台同型PLC为从站。
(4)也可一台PLC为主站,多台同型PLC为从站,构成PLC网络。
这比用PC机作主站方便之处是:有用户编程时,不必知道通信协议,只要按说明书格式写就行。
(5)PLC网格既可作为独立DCS/TDCS,也可作为DCS/TDCS的子系统。
(6)大系统同DCS/TDCS,如TDC3000、CENTUMCS、WDPFI、MOD300。
(7)PLC网络如Siemens公司的SINEC—L1、SINEC—H1、S4、S5、S6、S7等,GE公司的GENET、三菱公司的MELSEC—NET、MELSEC—NET/MINI。
(8)主要用于工业过程中的顺序控制,新型PLC也兼有闭环控制功能。
(9)制造商:GOULD(美)、AB(美)、GE(美)、OMRON(日)、MITSUBISHI(日)、Siemens(德)等。
2.2 DCS或TDCS(1)分散控制系统DCS与集散控制系统TDCS是集4C(Communication,Computer,Control、CRT)技术于一身的监控技术。
(2)从上到下的树状拓扑大系统,其中通信(Communication)是关键。
(3)PID在中断站中,中断站联接计算机与现场仪器仪表与控制装置。
(4)是树状拓扑和并行连续的链路结构,也有大量电缆从中继站并行到现场仪器仪表。
PLC,DCS,FCS厂家,特点与区别

PLC的特点
• 结构灵活
– 不受环境的限制,有电即可组建网络,同时可 以灵活扩展接入端口数量,使资源保持较高的 利用率,在移动性方面可与WLAN媲美。
• 范围广
– 无所不在的电力线网络也是这种技术的优势。虽然 无线网络可以做到不破墙,但对于高层建筑来说, 其必需布设N多个AP才能满足需求,而且同样不能 避面信号盲区的存在。而电力线是最基础的网络, 它的规模之大,是其他任何网络无法比拟的。由此, 运营商就可以轻松地把这种网络接入服务渗透到每 一处有电力线的地方。这一技术一旦全面进入商业 化阶段,将给互联网普及带来极大的发展空间。终 端用户只需要插上电力猫,就可以实现因特网接入, 电视频道接收节目,打电话或者是可视电话。
DCS是一个系统包括上位软件、网络与控制器,而PLC只是一个控制 器,要构成系统还需要上位SCADA系统和与之相连的网络。对PID回 路控制,现在三菱的过程控制器也可以实现象SAMA组态一样的FBD 编程;DCS系统更大,控制的回路数目更多,有比较多的控制和算法, 可以完成比较复杂的回路间的控制。硬件可靠性差不多。DCS可以做 到I/O的冗余,PLC则不可以。相对而言,PLC构成的系统成本更低。 —— 三菱电机自动化精密控制部经理宋葭晖
DCS的特点
• (1)高可靠性
– 由于DCS将系统控制功能分散在各台计算机上 实现,系统结构采用容错设计,因此某一台计 算机出现的故障不会导致系统其它功能的丧失。 此外,由于系统中各台计算机所承担的任务比 较单一,可以针对需要实现的功能采用具有特 定结构和软件的专用计算机,从而使系统中每 台计算机的可靠性也得到提高。
• 日本OMRON公司
– CPM1A型机,P型机,H型机,CQM1、CVM、CV型 机,Ha型、F型机等
- 1、下载文档前请自行甄别文档内容的完整性,平台不提供额外的编辑、内容补充、找答案等附加服务。
- 2、"仅部分预览"的文档,不可在线预览部分如存在完整性等问题,可反馈申请退款(可完整预览的文档不适用该条件!)。
- 3、如文档侵犯您的权益,请联系客服反馈,我们会尽快为您处理(人工客服工作时间:9:00-18:30)。
FCS结构特点
现场总线打破了传统控制系统的结构形式。传统模拟控制系统采 用一对一的设备连线,按控制回路分别进行连接。
FCS由于采用了智能现场设备,能够把原先DCS系统中处于控制 室的控制模块、各输入模块置入现场设备中,加上现场设备具有 通信能力,因而控制系统功能能够不依赖控制室的计算机或控制 仪表,直接在现场完成,实现了彻底的分散控制。 FCS与传统控制系统的对比图:
FCS典型应用
连续的工艺过程自动控制如石油化工
分立的工艺动作自动控制如汽车制造机器人、汽车 多点控制如楼宇自动化
FCS 和 DCS 的 比 较
FCS
结构 可靠性 失控状态 一对多:一对传输线接多台仪表,双 向传输多个信号 可靠性好:数字信号传输抗干扰能力 强,精度高 操作员可以再控制室了解现场设备的 工作状态,也可以对设备进行参数调 整,还可以预测或寻找故障。 用户可以选择不同制造商提供的性能 价格比最优的现场设备和仪表。不同 品牌的仪表可以互连。 智能仪表除了具有模拟仪表的检测、 变换、补偿等功能外,还具有数字通 信能力,并且具有控制和运算能力 控制功能分散在各个智能仪表中
FCS概述
FCS的全称是现场总线控制系统,属于第五代过程控制系统,它 是21世纪自动化控制系统的方向。
FCS是3C技术(Communication,Computer,Control)的融 合。是用于现场智能化装置与控制室自动化系统之间的一个标准 化数字式通信链路,可进行全数字化、双向、多站总线式的信息 数字通信,实现相互操作以及数据共享。 基本任务是:本质(本征)安全、危险区域、易变过程、难于对 付的非常环境。 主要目的是:用于控制、报警和事件报告等工作。
控制
DCS
一对一:一对传输线接一台仪表,单向 传输一个信号 可靠性差:模拟信号传输不仅精度低, 而且容易受干扰 操作员在控制室不能了解模拟仪表的工 作状况,也不能调整参数和排除故障, 导致操作员对仪表处于“失控”状态 不同品牌的仪表无法互换
互换性
仪表
模拟仪表只具有检测、变换、补偿等功 能 所有的控制功能集中在控制站中
DCS概述
DCS采用标准化、模块化和系列化设计,由过程控制单元、过程 接口单元、管理计算机以及高速通道等五个主要部分组成。
DCS是4C( Communication,Computer,Control ,CRT) 技术的融合。 DCS以计算机的CRT、键盘、鼠标、轨迹球代替仪表盘形成系统 人机界面,人机界面由操作员站实现,系统可有多台操作员站。 DCS是以回路控制为主要功能的系统。回路控制功能由现场控制 站完成,系统可有多台现场控制站,每台控制一部分回路。 系统中所有现场控制站、操作员站均通过数字通信网络实现连接。
பைடு நூலகம்
FCS产生的背景
在过程控制领域,从20世纪50年代开始,都在使用一种信号标 准——4~20mA的模拟信号标准。
20世纪70年代,数字计算机引入到测控系统中,而此时的计算机 提供的是集中式控制处理。 20世纪80年代,微处理器在控制领域得到应用,微处理器被嵌入 到各种仪器设备中,形成了分布式控制系统。 随着微处理器的发展和广泛应用,产生了以IC代替常规电子线路, 以微处理器为核心,实施信息采集、显示、处理、传输及优化控 制等功能的智能设备,由此产生了现场总线。
FCS和DCS的结构特点与区别
副标题
目录
FCS产生的背景
FCS概述 FCS典型应用 DCS发展历程 DCS概述
FCS和DCS的比较
DCS发展历程
20世纪70年代,各大公司推出第一代DCS产品,其中代表的产品有: Honeywell的TDC-2000、横河的CENTUM
20世纪80年代,随着各种高新技术,特别是信息处理技术和计算机网 络技术的飞速发展,现场控制站的功能大为增强。开发了高层次的综合 信息管理系统,以适应企业发展的需要。DCS的应用开始广泛起来。 20世纪90年代,DCS把过程控制、监督控制、管理调度有机地结合起 来,并继续加强逻辑控制功能。这个时期的特点是系统功能综合化和系 统网络开放性水平不断提高。 21世纪初,新一代DCS采用微型无引线元器件和软印制线路板、表面 贴装技术新工艺,体积小、可靠性高。能使用C、FORTRAN等高级语 言作为编程工具。