铁路货车转K2型转向架主要故障的探讨及分析
既有铁路货车换装转K2型转向架改造中存在的质量问题与改进措施

铁道车辆 第57卷第6期2019年6月
文章编号:1002-7602(2019)06-0040-02
既有铁路货车换装转K2型转向架
存在2质量问题7-8措施
魏周江
(中国铁路兰州局集团有限公司兰州西车辆段质检验收室,甘肃 兰州730070)
摘 要:对既有铁路货车换装转K2型转向架改造检修过程中容易发生的质量问题进行了分析,并提出了相应的改
(7) 油漆标记要求落实不到位。经常发现车型标
记后缀“T”未改为“K”、“已改造”标记未保留、各种新 组焊及换装的配件油漆涂刷不到位等问题#
3改进措施
(1) 检修时应进一步加强对利旧配件的使用管 理。对于报废车的利旧配件,应采用严格检测标识、上 下工序间质量互控等方式加强检测质量#对摇枕、侧 架等大部件要按厂修标准进行抛丸、除锈、探伤,并做 好相应探伤标识后方可进入换装工作流程#
(5) 改造制动管系存在的主要问题,一是部分管 系制作不符合图样要求,再加上底架附属件定位偏差 等因素,造成管系组装存在抗力的现象;二是在进行管 系组装时存在使用火焰加热进行调修的现象,这不符 合制动管系组装技术要求。制动管系抗力、别劲组装, 易造成运行中管系漏风甚至折断等安全风险#
(6) 底架附属件焊接质量不高#检查发现,部分 车辆的吊架、上旁承等存在焊缝开裂等问题。另外,受 改造车辆检修场地、工装等综合因素的影响,部分检修 车辆如棚车等无法实施翻转焊接,也容易对焊接质量 造成不利影响。
从故障部位的分布以及具体表现来看,改造车辆 检修发生的故障主要集中在转向架、车体底架、制动装 置等部件,故障原因主要为: »»»»»»»»»»»»»»»»»»»»»»»»»»»»»»»»»»»»»»»»»»»»»»»»»
3改造的实施
浅析转K2型转向架存在的问题

浅析转K2型转向架存在的问题为了提高运能,我国铁路成功地进行了客运提速,主要干线的客运列车最高速度已达140km/h-160km/h。
除极少数的快运专列外,绝大多数货物列车的最高运行速度仅有70km/h-80km/h,旅客列车的速度仅有150km/h,还远远不能满足铁路跨越式发展新形势的需要。
为此,铁道部为解决因货运列车运行速度慢,限制铁路运输发展的问题,提出了,在三年内对既有货车进行120km/h的提速改造,而既有货车120km/h提速改造所采用的转向架就是K2型转向架。
因此,转K2型转向架就成为了铁路货车车辆所采用的主型转向架。
为确保铁路运输的安全运营,就有必要对其主导产品进行研究分析找出不足,进行整改,使其达到能保证铁路运输安全的需要。
通过我在列检现场一线的调研,下面我谈谈对转K2型转向架的故障类型分析和改进意见。
一、转K2型转向架的技术状态转K2型转向架系齐车公司引进美国交叉支撑技术生产的新型快速货车转向架。
该转向架在传统三大件式转向架的两个侧架间增加了交叉支撑装臵,,以提高三大件式转向架的抗菱钢度,选用大静挠度的,内外枕簧有一定高度差的两级钢度弹簧组,使车辆的减振性能得到了较大的提高,特别是平车及轻体罐车等自重较轻的车辆,空车减振性能得到了较大提高,避免了原有货车因装配件转8A型转向架在空车减振性能得以较大的提高,避免了原有货车因装配转8A型转向架在空车减振性能较差或失效情况下,造成车辆脱线或颠覆的现象。
采用常接触弹性旁承和新型斜楔,提高了转向架的抗蛇行运动能力,减少了轮缘与钢轨间的接触摩擦,延长了车轮的使用寿命。
由此可见转K2型转向架与原有转向架相比相比其动力学性能得到了较大的提高,各项技术参数的结果也显示出该型转向架基本上能满足我国货车提速的需要。
二、转K2型转向架在运用中存在的一些问题:因该转向架加装了弹性交叉支撑装臵,增大了转向架的簧下质量及自重,轮轨间作用力加大,摇枕中间开孔较大,影响了摇枕的强度。
转K2型转向架承载鞍和侧架导框异常磨耗原因分析及措施

期处 于欠超 高 的运 行 工况 , 车辆 动 力 学 性 能有 一 对
定 的不 利 影 响 。
4 改 进 措 施
针对 以上原 因 , 取 了 以下改进 措施 : 采
良 ,使 空 车 动 挠 度 减 小 ,同 时 增 大 斜 楔 横 向摩 擦 力 , 轮轨横 向力作 用下 ,出现侧 架 和 承载 鞍 之 间 在
相 对 移 动 ,是 造 成 承 载 鞍 顶 面 和 侧 架 导 框 异 常 磨 耗 的另一个 原 因 。
( ) G 型 罐 车罐 体 与底 架 的 连接 部 位进 行 1对 检修 , 同时换装 组合 式斜 楔 、 承载鞍 和 弹性 旁 承 。 ( ) N 型平 车 进行 检 修 并换 装 组 合 式斜 2对 X
摘 要 : 对 转 K 针 2型 转 向 架在 环行 线 试 验 q 出现 的 磨 耗 问题 进 行 了原 因分 析 , - 并提 出 改 进措 施 。
关键词 : 行线试验 ; K 环 转 2型 转 向架 ; 耗 磨
中 图分 类 号 : 7 u2 2 文 献标 识 码 : B
1 问题 的提 出
率和脱 轨 系数 的最 大影 响分别 达到 6 6 和 34 。 .% .% 试 验 车 约 7 % 里 程 的 运 行 速 度 为 10k / , 辆 长 0 2 m h 车
会增 大承 载鞍 先发 生相对 运 动的可 能性 。但根 据动
力 学分析 , 回转 阻 力 矩 的 过 小 将 引 起 蛇 行 临 界 速 度
20 0 6年 , 公 司 在 环 行 线 进 行 了 提 速 货 车 10 某 2
大 , 分 间隙 已经超 过 了段修 限度 , 且横 向 间隙较 部 并
大 的 导 框 对 应 的 承 载 鞍 顶 面 磨 耗 也 较 严 重 , 明 侧 说
转K2型转向架主要运用故障分析
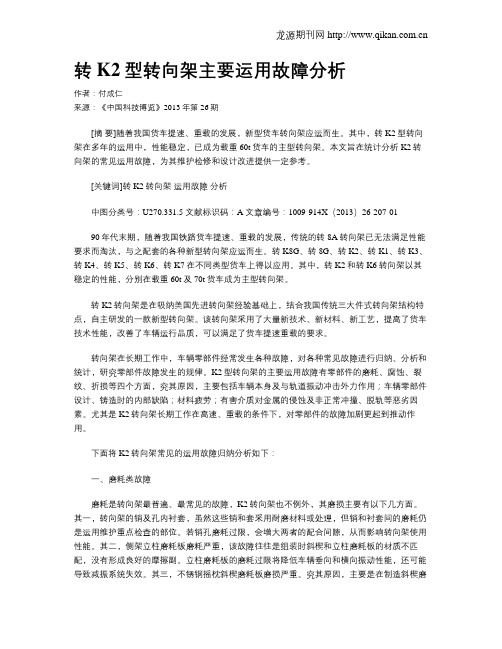
转K2型转向架主要运用故障分析作者:付成仁来源:《中国科技博览》2013年第26期[摘要]随着我国货车提速、重载的发展,新型货车转向架应运而生。
其中,转K2型转向架在多年的运用中,性能稳定,已成为载重60t货车的主型转向架。
本文旨在统计分析K2转向架的常见运用故障,为其维护检修和设计改进提供一定参考。
[关键词]转K2转向架运用故障分析中图分类号:U270.331.5 文献标识码:A 文章编号:1009-914X(2013)26-207-0190年代末期,随着我国铁路货车提速、重载的发展,传统的转8A转向架已无法满足性能要求而淘汰,与之配套的各种新型转向架应运而生。
转K8G、转8G、转K2、转K1、转K3、转K4、转K5、转K6、转K7在不同类型货车上得以应用。
其中,转K2和转K6转向架以其稳定的性能,分别在载重60t及70t货车成为主型转向架。
转K2转向架是在吸纳美国先进转向架经验基础上,结合我国传统三大件式转向架结构特点,自主研发的一款新型转向架。
该转向架采用了大量新技术、新材料、新工艺,提高了货车技术性能,改善了车辆运行品质,可以满足了货车提速重载的要求。
转向架在长期工作中,车辆零部件经常发生各种故障,对各种常见故障进行归纳、分析和统计,研究零部件故障发生的规律。
K2型转向架的主要运用故障有零部件的磨耗、腐蚀、裂纹、折损等四个方面,究其原因,主要包括车辆本身及与轨道振动冲击外力作用;车辆零部件设计、铸造时的内部缺陷;材料疲劳;有害介质对金属的侵蚀及非正常冲撞、脱轨等恶劣因素。
尤其是K2转向架长期工作在高速、重载的条件下,对零部件的故障加剧更起到推动作用。
下面将K2转向架常见的运用故障归纳分析如下:一、磨耗类故障磨耗是转向架最普遍、最常见的故障,K2转向架也不例外,其磨损主要有以下几方面。
其一,转向架的销及孔内衬套,虽然这些销和套采用耐磨材料或处理,但销和衬套间的磨耗仍是运用维护重点检查的部位。
转K2转向架摇枕裂纹原因分析及改进措施
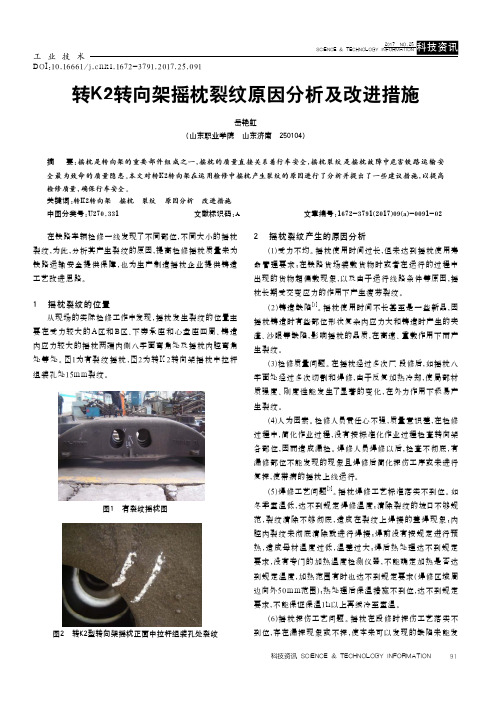
工 业 技 术91科技资讯 SCIENCE & TECHNOLOGY INFORMATIONDOI:10.16661/j.c n k i.1672-3791.2017.25.091转K2转向架摇枕裂纹原因分析及改进措施岳艳虹(山东职业学院 山东济南 250104)摘 要:摇枕是转向架的重要部件组成之一,摇枕的质量直接关系着行车安全,摇枕裂纹是摇枕故障中危害铁路运输安全最为致命的质量隐患。
本文对转K2转向架在运用检修中摇枕产生裂纹的原因进行了分析并提出了一些建议措施,以提高检修质量,确保行车安全。
关键词:转K2转向架 摇枕 裂纹 原因分析 改进措施中图分类号:U270.331文献标识码:A文章编号:1672-3791(2017)09(a)-0091-02在铁路车辆检修一线发现了不同部位,不同大小的摇枕裂纹,为此,分析其产生裂纹的原因,提高检修摇枕质量来为铁路运输安全提供保障,也为生产制造摇枕企业提供铸造工艺改进思路。
1 摇枕裂纹的位置从现场的实际检修工作中发现,摇枕发生裂纹的位置主要在受力较大的A区和B区、下旁承座和心盘座四周、铸造内应力较大的摇枕两端内侧八字面弯角处及摇枕内腔弯角处等处。
图1为有裂纹摇枕,图2为转K 2转向架摇枕中拉杆组装孔处15mm裂纹。
图1 有裂纹摇枕图图2 转K2型转向架摇枕正面中拉杆组装孔处裂纹 2 摇枕裂纹产生的原因分析(1)受力不均。
摇枕使用时间过长,但未达到摇枕使用寿命管理要求;在铁路货场装载货物时或者在运行的过程中出现的货物超偏载现象,以及由于运行线路条件等原因,摇枕长期受交变应力的作用下产生疲劳裂纹。
(2)铸造缺陷[1]。
摇枕使用时间不长甚至是一些新品,因摇枕铸造时有些部位形状复杂内应力大和铸造时产生的夹渣、沙眼等缺陷,影响摇枕的品质,在高速、重载作用下而产生裂纹。
(3)检修质量问题。
在摇枕经过多次厂、段修后,如摇枕八字面处经过多次切割和焊修,由于反复加热冷却,使局部材质强度、刚度性能发生了显著的变化,在外力作用下极易产生裂纹。
关于K13NT型铁路货车在换装转K2型转向架改造中有关问题的分析和建议

关于K13NT型铁路货车在换装转K2型转向架改造中有关问题的分析和建议摘要:阐述K13NT型铁路货车在换装转K2型转向架改造工作中遇到的问题,并提出改进建议。
关键词:货车;换装;K2;建议1引言为适应铁路货车提速重载要求,提高车辆运行品质,中国铁路总公司组织对装用转8B(转8AB)型转向架铁路货车进行了换装转K2型转向架改造工作。
2017年下半年,我段陆续组织对管内十余辆K13NT型铁路货车按照改造工艺进行转K2型转向架改造。
在改造过程中,我们发现了一些问题,笔者对这些问题进行了分析,并提出改进建议,以便和大家共同讨论和解决。
2改造中出现的问题在底架附属件改造中,要求切除原有测重机构,在中梁下翼板两侧分别重新焊装测重机构安装座(图2-1),以便安装KZW-A型空重车自动调整装置。
在焊装测重机构安装座时,我们发现安装座与中梁下翼板的横向焊接搭接量过少,仅为5mm(图2-2),不能满足焊接强度需求,且在焊接过程中,测重机构安装座无法呈现水平状态,在补强板与中梁翼板过渡区域出现上倾(图2-3),导致安装座螺栓孔过高,测重机构无法正常组装。
图2-1 测重机构安装座图2-2 安装座与中梁下翼板焊接搭载量图2-3 安装座上倾图3-1补强板与中梁下翼板横向间隙图3-2 测重机构安装座焊接尺寸3原因分析K13NT型铁路货车在设计中,为增强梁的强度,在牵引梁及中梁下翼板焊装有补强板,补强板与中梁下翼板横向有45mm间隙(图3-1),而测重机构安装座焊接部位尺寸宽度为50mm(图3-2),因此,只留有5mm的安装座与中梁下翼板补强板结合部位,其余要求焊接的45mm均不能与中梁下翼板接触,处于悬空状态,造成焊接搭载量不足。
4解决方案方案一:对测重机构安装座尺寸进行调整,延长安装座焊接部位长度,将50mm的焊接长度加长至100mm(图4-1),在去除补强板与中梁下翼板横向45mm间隙后,可实现测重机构安装座与中梁下翼板补强板的焊接搭接量55mm,可以确保焊接强度及焊后水平状态。
转K2与转K6型转向架故障与检修

转K2与转K6型转向架故障与检修【摘要】本文针对转K2与转K6转向架几个常见故障进行分析,并给出故障检测的方法及检修措施;【关键词】转向架;故障;检修1 转K2、转K6型转向架侧架常见故障检修1.1 侧架容易有裂纹部位以及A、B区的区分铸钢侧架裂纹多发生在A区、B区,如图1.一般多发生在承载鞍导框弯角处,侧架立柱的上下弯角处及制动梁滑槽下方。
其中A区为侧架导框的内侧弯角处如图2;B区为侧架的底面平面及向上倾斜延伸至导框下弯角处。
裂纹也发生在支撑座、弹簧承台及弹簧承台与立柱弯角处等部位。
图1 转K2、转K6型侧架A、B区示意图图2 侧架A区(上弦梁弯角)裂纹1.2 侧架容易磨损的部位侧架磨损多发生在承载鞍支承面,内、外导框,转K2型侧架立柱与摇枕挡内表面配合处等部位。
1.3 重点注意检查部位主要检查侧架的A、B区;检查导框弯角处A区部位;承载鞍承台园脐上平面与侧架结合处;导框三角孔周边;三角孔内腔铆钉孔及立柱弯角处;摇枕弹簧承台周边;侧架立柱及立柱磨耗板;中央方框上弦梁;下斜弦梁内外侧;制动梁滑槽磨耗板、斜楔档、交叉杆支撑座及周边焊缝、横跨梁托,对接近20年及以上的侧架以到疲劳期,裂纹故障较多,要重点检查。
1.4 检查方法采用外观检查的方式。
通过外观检查方法对有异状部位,铸造工艺粗糙部位,经常磨耗部位,检查有无锈线或透锈现象,如有锈线或透锈现象先去除表面锈迹或漆面(注意不要将痕迹盖住),振动痕迹附近,看是否有迹象增大或铁锈透出。
对有油垢处注意有无细线痕迹,可采用手电光线斜交照射的方法检查。
采用探伤方式进行检查,对存在裂纹疑问的侧架进行整体抛丸除锈,采用专用探伤设备对存在裂纹疑问部位进行探伤检查。
1.5 裂纹故障检修侧架弯角处横裂纹长度不大于裂纹处断面周长的30%,其他位的横裂纹长度不大于裂纹处断面周长的50%时焊修,大于时报废。
1.6 磨耗故障检修(1)导框两侧摩擦面单侧磨耗(含局部磨耗)深度大于2mm、两侧磨耗深度之和大于3mm,内侧面磨耗(含局部磨耗)深度大于3mm或组装间隙超限时,堆焊后加工。
转K2与转K6型转向架故障与检修

Science &Technology Vision 科技视界1转K2、转K6型转向架侧架常见故障检修1.1侧架容易有裂纹部位以及A、B 区的区分铸钢侧架裂纹多发生在A 区、B 区,如图1.一般多发生在承载鞍导框弯角处,侧架立柱的上下弯角处及制动梁滑槽下方。
其中A 区为侧架导框的内侧弯角处如图2;B 区为侧架的底面平面及向上倾斜延伸至导框下弯角处。
裂纹也发生在支撑座、弹簧承台及弹簧承台与立柱弯角处等部位。
图1转K2、转K6型侧架A、B 区示意图图2侧架A 区(上弦梁弯角)裂纹1.2侧架容易磨损的部位侧架磨损多发生在承载鞍支承面,内、外导框,转K2型侧架立柱与摇枕挡内表面配合处等部位。
1.3重点注意检查部位主要检查侧架的A、B 区;检查导框弯角处A 区部位;承载鞍承台园脐上平面与侧架结合处;导框三角孔周边;三角孔内腔铆钉孔及立柱弯角处;摇枕弹簧承台周边;侧架立柱及立柱磨耗板;中央方框上弦梁;下斜弦梁内外侧;制动梁滑槽磨耗板、斜楔档、交叉杆支撑座及周边焊缝、横跨梁托,对接近20年及以上的侧架以到疲劳期,裂纹故障较多,要重点检查。
1.4检查方法采用外观检查的方式。
通过外观检查方法对有异状部位,铸造工艺粗糙部位,经常磨耗部位,检查有无锈线或透锈现象,如有锈线或透锈现象先去除表面锈迹或漆面(注意不要将痕迹盖住),振动痕迹附近,看是否有迹象增大或铁锈透出。
对有油垢处注意有无细线痕迹,可采用手电光线斜交照射的方法检查。
采用探伤方式进行检查,对存在裂纹疑问的侧架进行整体抛丸除锈,采用专用探伤设备对存在裂纹疑问部位进行探伤检查。
1.5裂纹故障检修侧架弯角处横裂纹长度不大于裂纹处断面周长的30%,其他位的横裂纹长度不大于裂纹处断面周长的50%时焊修,大于时报废。
1.6磨耗故障检修(1)导框两侧摩擦面单侧磨耗(含局部磨耗)深度大于2mm、两侧磨耗深度之和大于3mm,内侧面磨耗(含局部磨耗)深度大于3mm 或组装间隙超限时,堆焊后加工。
论转K2型转向架交叉支撑装置中卡子断裂的原因及防止措施

论转K2型转向架交叉支撑装置中卡子断裂的原因及防止措施目录内容:一、我国交叉支撑转向架的产生与应用;二、转K2型转向架技术性能参数;三、结构特点;四、交叉支撑转向架在我国铁路上的初步运用状况。
引言:目前,随着铁路跨越式的发展,为了提高货车运行速度和车辆的稳定性,货车车辆不段更新,带有交叉支撑装置的提速转向架以成为铁路货车的主型转向架。
交叉支撑装置是用以提高转向架的抗菱刚度,从而减少轮对与转向架蛇行运动,提高转向架的蛇行失稳临界速度,增大货车直线运行的稳定性,同时交叉支撑装置可有效保持转向架的正位状态,从而减小了车辆在直线和曲线运动时轮对对钢轨的冲击,改善转向架的曲线通过性能,显著减少轮轨磨耗。
正文:随着铁路运输企业的改革和发展不断深入,铁路运输设备不断更新,管理方法也在创新,铁路运输生产中的新技术、新设备、新方法与新工艺不断涌现,大大提高了铁路运输的效率,保证了运输生产的安全。
一、我国交叉支撑转向架的产生与应用交叉支撑转向架的产生中交叉支撑转向架的研制开始于1990年,齐齐哈尔车辆厂为了解决转8A型转向架抗菱刚度不足等缺点,决定探索采用交叉支撑技术对转8A型转向架的运行性能进行改进的可行性,他们以转8A型转向架为基础创造性地改进了一辆份中交叉支撑式转向架。
采用2根交叉杆通过摇枕侧壁开孔把左右侧架连接起来,交叉杆与侧架的连接点位于侧架三角孔部位,位置的高度接近于侧架的中部,所以称为中交叉支撑转向架。
通过车辆线路动力学性能等一系列试验表明,该转向架的强度、刚度和各项动力学性能指标符合我国有关国标和铁标的规定要求,具有优良的动力学性能,可以满足最高运行速度达120km/h的运用要求。
1994年该新型中交叉支撑2D轴转向架装于C64型敞车交哈尔滨铁路局海拉尔铁路分局进行运用考验。
运用表明,该转向架运用安全可靠,轮缘磨耗少,深受运用检修部门好评。
1997年,美国标准车辆转向架公司(SCT公司)为改造北美铁路BarberS-2-HD型三大件式货车转向架,研制了下交叉支撑转向架技术,并获得了良好的动力学性能。
转K2型转向架轮对偏磨故障分析

转K2型转向架轮对偏磨故障分析转K2型转向架作为目前货车提速改造的主型转向架,其性能的好坏对铁路运输安全至关重要。
2006年8月一11月,郑州北车辆段连续发现了3起转K2型转向架轮对偏磨故障,严重危及行车安全,这说明目前该型转向架在组装和检修上可能还存在一些问题。
1概况2006年7月15日,在技检33191次列车时,发现机后22位C62BK4641177号车(定检:O5.3齐厂、O5.3齐厂、4.22店)的2位和4位车轮踏面、轮缘等部位磨耗严重。
表1和图1分别为C62BK4641177号车车轮各部尺寸及磨耗情况。
2006年8月8日,在技检83133次列车时,发现机后43位C64 K4960699号车(定检:O5.4齐厂、O5.4齐厂、取消辅修)的1位转向架2位和4位车轮踏面、轮缘等部位磨耗严重,出现严重偏磨现象,轮缘立面紧贴钢轨内侧。
车轮各部尺寸的测量结果见表2。
2006年11月13日,25079次列车机后42位C64K4835979号车(定检:04.6柳厂、O5.12呼包西)的2位、4位车轮圆周磨耗严重,达11 mm,相对应的1位、3位车轮圆周磨耗为7 mm,其他尺寸均正常。
2 原因分析总的来看,转K2型转向架运行品质稳定,运行速度高,大幅度地减少了车轮的磨耗。
但是由于提速改造任务紧,工作量大,使得转K2型转向架可能存在配件质量、组装质量和公差配合等方面的隐患。
虽然只是个别现象,但对行车安全危害极大,必须引起高度重视。
这3起故障均是由于车轮的非正常磨耗而引起的,而且都是车轮偏磨。
经分析,可能是由以下几个方面的原因引起的:转向架组装尺寸不当或侧架、摇枕等有关尺寸加工不当,造成落成后的转向架在运用中逐步呈“八”字形或菱形,从而加剧了转向架一侧车轮的磨耗。
特别是C62BK4641177和C64K4960699号车的2起故障,轮缘垂直磨耗过限,踏面圆周磨耗过限,同一轮对两车轮直径差过限。
车辆组装改造后运行仅1年多的时间久发生了如此严重的车轮磨偏,说明转向架组装存在问题的可能性非常大。
转K2型转向架异常磨耗

浅谈转K2型转向架异常磨耗张一莹(上海铁路局杭州北车辆段,浙江杭州311100)摘要:本文针对转K2型货车转向架在日常检修中发现的摇枕端部(与侧架立柱磨耗板相对处)异常磨耗的情况,通过对转向架各部的配合情况以及各配件的尺寸、磨耗情况进行检测,并对检测结果进行了分析,查找发生转向架异常磨耗的原因,同时针对原因分析,提出了该问题的解决方法与建议。
关键词:转K2型货车转向架;立柱磨耗板;摇枕端部;斜楔;磨耗中图分类号:U270文献标识码:A 文章编号:1003-5168(2012)24-0001-01一、问题提出转K2型转向架作为我国货车转向架家族中最主要的成员,在我国的保有量非常大,抓好转K2型转向架检修质量,对我国货运列车的运行安全有着非常大的作用。
而在2012年以来,杭州北车辆段乔司检修车间在转向架日常检修过程中,发现了多起转K2型货车转向架摇枕端部(与侧架立柱磨耗板)相对处异常磨耗情况的发生(具体磨耗异常部位见图1与图2),磨耗产生主要表现为摇枕端部与侧架立柱磨耗板在转向架运行过程中发生了接触摩擦,摇枕端部该部位磨耗较为严重,磨耗深度达到1-4mm,影响到了转向架的运行安全,对车辆的行车安全带来了安全隐患。
二、分解检测情况为了分析查找出产生转向架异常磨耗的原因,我们抽出了3个故障转K2型转向架进行检测,对其进行了正位检测,并进行了分解检测,重点对斜楔、枕簧等部件的磨耗、限度尺寸进行了全面的检测,并对检测结果进行了分类统计,具体检测情况如下:2.1 转向架正位检测情况对转向架正位情况进行了检测。
检测结果表明,这3个故障转向架在正位检测这个项目中都为合格,由此可见,其转向架组装正位情况符合要求,货车在运行过程中的蛇形运动在可控范围之内。
2.2 摇枕、侧架其他部位尺寸情况对摇枕、侧架的其他部分尺寸进行了检测,未发现有磨耗过限及铸造缺陷存在,侧架铲豆保持一致。
2.3 斜楔检测情况此3个故障转向架都为整体式斜楔,对斜楔的主摩擦面与副摩擦面进行了检测,发现有两个故障转向架的斜楔主摩擦面存在较大的磨耗过限情况,磨耗深度达到了8.2mm及7.9mm(段修标准为6.4mm),且这两个斜楔都位于摇枕端部异常磨耗侧。
转K2与转K6型转向架故障与检修

转K2与转K6型转向架故障与检修作者:陆嘉来源:《科技视界》2013年第24期【摘要】本文针对转K2与转K6转向架几个常见故障进行分析,并给出故障检测的方法及检修措施;【关键词】转向架;故障;检修1 转K2、转K6型转向架侧架常见故障检修1.1 侧架容易有裂纹部位以及A、B区的区分铸钢侧架裂纹多发生在A区、B区,如图1.一般多发生在承载鞍导框弯角处,侧架立柱的上下弯角处及制动梁滑槽下方。
其中A区为侧架导框的内侧弯角处如图2;B区为侧架的底面平面及向上倾斜延伸至导框下弯角处。
裂纹也发生在支撑座、弹簧承台及弹簧承台与立柱弯角处等部位。
图1 转K2、转K6型侧架A、B区示意图图2 侧架A区(上弦梁弯角)裂纹1.2 侧架容易磨损的部位侧架磨损多发生在承载鞍支承面,内、外导框,转K2型侧架立柱与摇枕挡内表面配合处等部位。
1.3 重点注意检查部位主要检查侧架的A、B区;检查导框弯角处A区部位;承载鞍承台园脐上平面与侧架结合处;导框三角孔周边;三角孔内腔铆钉孔及立柱弯角处;摇枕弹簧承台周边;侧架立柱及立柱磨耗板;中央方框上弦梁;下斜弦梁内外侧;制动梁滑槽磨耗板、斜楔档、交叉杆支撑座及周边焊缝、横跨梁托,对接近20年及以上的侧架以到疲劳期,裂纹故障较多,要重点检查。
1.4 检查方法采用外观检查的方式。
通过外观检查方法对有异状部位,铸造工艺粗糙部位,经常磨耗部位,检查有无锈线或透锈现象,如有锈线或透锈现象先去除表面锈迹或漆面(注意不要将痕迹盖住),振动痕迹附近,看是否有迹象增大或铁锈透出。
对有油垢处注意有无细线痕迹,可采用手电光线斜交照射的方法检查。
采用探伤方式进行检查,对存在裂纹疑问的侧架进行整体抛丸除锈,采用专用探伤设备对存在裂纹疑问部位进行探伤检查。
1.5 裂纹故障检修侧架弯角处横裂纹长度不大于裂纹处断面周长的30%,其他位的横裂纹长度不大于裂纹处断面周长的50%时焊修,大于时报废。
1.6 磨耗故障检修(1)导框两侧摩擦面单侧磨耗(含局部磨耗)深度大于2mm、两侧磨耗深度之和大于3mm,内侧面磨耗(含局部磨耗)深度大于3mm或组装间隙超限时,堆焊后加工。
转K2型转向架常见故障及原因分析

的反馈信息 ,并且使板子本身的质量得 受力不均, 降低了动力学性能并导致热 本 文研 究 的附属 件都 是转 向架 的, 可以发 明一个铁路货车转向架摇枕斜楔与减振
方式一般采取换件修 ,检修的目的是恢 复设计原型或保证各零部件及配合间隙 在规定的限度以内,保证整车在到达下
责任 编辑 : 王
华
辆各 部 受力 状况 发生 了很大 变化 , 零 单位努力维修 的同时 ,相关部 门也要及 各
来稿 日期 :0 2 0 — 7 2 1— 2 1
部件 的故障率也明显增加。转 K 型转 时提 出整改措 施 。 2
12件 , 3 占全部 检修车辆 的 5 过多 的 %,
铸钢侧架承载鞍支承面磨耗以侧架 磨耗故障, 严重影响了货车的运行品质。 [ 中华 人民共 和 国铁 道部 .铁路 货 车段修 规 3 】 《 承载鞍支承面未磨耗部位为基准,测量 承载鞍支撑面的磨耗问题长期存在 , 其 磨耗处最大深度 ;偏磨检测 以侧架承载 中 9 年生产的一批侧架尤为突出, 9 这也 【] 4 中华 人 民共 和 国铁 道部 .铁路 货 车辅修 规 《 鞍支承面未磨耗部位为基准 , 测量磨耗 充 分说 明造成 这种 问题 的主要 原 因在 于 程》中国铁道 出版社.04 . 20.
次相应 修程 之前 运行 良好 ,确 保铁 路运
输安全。
磨耗板连接装置 ,解决传统磨耗板在修
理换 件过程 中 因热切 割和焊 接对 摇枕 产
生的热损伤问题 ,以及转向架其它运动 部件对摇枕产生的磨耗问题 。其必须结
构简单 、 装配方便 , 摇枕斜楔磨耗板无磨 耗,满足减振磨耗板无焊接切割的换件 修理要求 , 提高摇枕组成的工作寿命 、 修 理作业质量及工效。 2 . 3承载 鞍支 撑面 的故 障及原 因
关于对转K2型转向架旁承滚子异向的调查分析及改进建议_唐才栋

2. 2 理论计算分析 假设同一转向架两侧旁承磨损量相同且达到最大
限度, 设上旁承下平面工作位置与滚子顶距离 A d 为 6 mm, 滚子 径向磨耗 Mg 为 2 mm , 上旁承下平 面磨损 Ms为 2 m m, 发生侧滚时旁承压死, 实测旁承座滚子凹 槽深度 H 为 14 mm , 则相对应的另一侧上旁承下平面 工作位置与滚子顶面间的距离为: A = 2 @ ( A d+ M g + Ms ) , 即 20 mm 。
1 存在的问题
( 1) 微合金奥- 贝球铁 ( ADI) 侧架立 柱磨耗板断 裂。
( 2) 侧架支撑座焊缝焊接质量差。 ( 3) 上旁承及底架附属件焊接质量差。 ( 4) 侧架支撑座组对后划线检查精度低。 ( 5) 侧架立柱磨耗板组装后紧固力矩无法校核。
收稿日期: 2005-08-26 作者简介: 王建军( 1968- ) , 男, 工程师。
由此可知, 车辆通过曲线时, 只要磨损达到一定成 度, A > H 这一条件就可能成立, 滚子就可能出现异 向故障。随着转 K2 型转向架运用时间的增加, 其滚 子异向故障出现的概率会逐渐加大。
3 改进建议
3. 1 换用 JC 型旁承
JC 型弹性旁承从结构上避免了滚子由横向转为 纵向的可能性, 是解决转 K2 型转向架旁承滚子纵向 故障 最 为 得 力 的 措 施。 建 议 对 新 造 车 和 既 有 120 km/ h改造提速车一律安装新型 JC 型旁承, 从根 本上解决这一难题。
既有的转 K2 旁承与转 8G、转 8AG 等旁承相比, 具有检修难度小、滚子磨损少、使用寿命长等优点, 如 果解决了其旁承滚子异向问题, 仍不失为一种好旁承。 建议对该旁承座进行改进, 在车辆检修时对已安装了 这类旁承的车辆更换旁承座, 避免浪费。改进方法是 增加旁承座滚子凹槽深度 H , 使约束滚子转向的高度 增加, 在极限条件下保持 A < H 成立。建议安全余量 取 5 mm, H 由 14 mm 改为 25 mm, 见图 1。
铁路货车转K2型转向架主要故障的探讨及分析

铁路货车转K2型转向架主要故障的探讨及分析摘要:根据我国铁路建设快速发展,我国铁路先后经过多次提速,目前我国铁路货车速度已达到120km/h,现在铁路货车普遍使用的60t级K2型转向架,转向架一般随整车同时进行定期检修,检修的目的是恢复其原设计原型或保证各零部件及配合间隙在规定的限度以内,保证整车在到达下次相应修程之前作用良好,确保铁路运输安全。
关键词:货车;转向架;故障;分析;探讨1.转K2型转向架的主要特点转K2型转向架是采用交叉支撑转向架,车辆在运行过程中,存在点头运动、摇头(蛇形)运动、侧滚运动等六个自由度的运动方式,控制好该六种运动方式,是保证运行安全、提高运行品质的基本原理。
交叉支撑转向架通过采用新技术,优化转向架抗菱刚度、转向架回转力矩、转向架正位状态、摩擦减振装置的相对摩擦系数、空重车状态下弹簧静挠度等性能参数,有效地控制车辆的摇头、侧滚运动,提高了车辆运行时的平稳性和稳定性。
转K2型转向架采用新技术有:侧架弹性下交叉支撑装置、JC型双作用常接触弹性旁承、中央悬挂系统两级刚度弹簧、新型减振摩擦副、心盘磨耗盘、耐磨销套。
2.交叉支撑装置中交叉杆裂损、开焊图1 交叉杆杆体(压窝处)裂损图2 交叉杆焊缝开裂2.1原因分析:2.1.1在检修过程中,时常发现交叉杆裂损、焊缝开焊,原因之一是车辆在运行或整体翻转卸货时,容易造成交叉杆受力不均或碰撞交叉杆,其次交叉杆支撑座与侧架组对焊接时定位不准确,有安装误差。
交叉杆端头紧固螺栓在紧固时,未严格执行工艺标准和工艺要求,在车辆使用过程中,车辆在通过曲线或车辆产生蛇行运动,由于交叉杆纠正其运行偏态时,容易在应力比较集中的地方发生断裂。
2.1.2焊接工水平参差不齐,焊后形成的焊缝有夹渣、气泡或焊缝高度达不到工艺要求,而且由于交叉杆属于簧下装置,在运行中承受的振动力和冲击力均很大,使有缺陷的焊缝在剧烈的振动作用下产生裂纹,最终导致裂损、开焊,造成交叉杆脱落而引发车辆事故。
转K2、转K6型转向架故障分析与维修建议

毕业设计(论文)中文题目:转K2、转K6型转向架故障分析与维修建议专业:铁路运输工程(机车车辆方向)姓名:学号:指导教师:北京交通大学远程与继续教育学院2022年4月毕业设计(论文)承诺书与版权使用授权书本人所呈交的毕业论文是本人在指导教师指导下独立研究、写作的成果。
除了文中特别加以标注和致谢之处外,论文中不包含其他人已经发表或撰写过的研究成果,也不包含为获得北京交通大学或其他教育机构的学位或证书而使用过的材料。
本毕业论文是本人在读期间所完成的学业的组成部分,同意学校将本论文的部分或全部内容编入有关书籍、数据库保存,并向有关学术部门和国家相关教育主管部门呈交复印件、电子文档,允许采用复制、印刷等方式将论文文本提供给读者查阅和借阅。
论文作者签名: 2021 年 12 月 1 日指导教师签名: 2021 年 12 月 1 日毕业设计(论文)成绩评议毕业设计(论文)任务书本任务书下达给:铁路运输工程专业准考证号姓名(机车车辆方向)设计(论文)题目:转K2、K6型转向架故障分析与维修建议一、毕业设计(论文)基本内容本文对转K2、K6型转向架运行当中出现的减振内簧折断、侧架立柱磨耗板断裂、制动梁滑槽磨耗板裂损或丢失等故障进行了归纳总结,对故障产生的原因进行了认真剖析,找出了其设计、制造中存在的缺陷和不足,并提出了改进建议。
二、基本要求了解转k2和转k6型转向架的故障及检修措施,了解转k2、转k6型转向架的重点检查部位及检修工艺。
三、重点研究的问题本文重点研究转K2、K6转向架的用途和转K2、K6转向架常见故障分析及维修建议以及转K2、K6 型转向架落成技术要求。
四、主要技术指标无五、其他要说明的问题无下达任务日期:2020年12 月01 日要求完成日期:2021年01 月20 日指导教师:开题报告题目:转K2、K6型转向架故障分析与维修建议学生姓名:学号:2020年 12月 20日一、文献综述为满足我国铁路货车提速和重载的要求,近年来我国开发研制了K2、K6型下交叉支撑转向架,该转向架自上世纪末在P65型行包快运棚车上装用以来,已基本取代了转8A型铸钢三大件式转向架,成为我国2lt轴重货车的主型转向架。
铁路货车K2型转向架交叉支撑装置故障原因分析及改进建议

铁路货车K2型转向架交叉支撑装置故障原因分析及改进建议摘要:本文对交叉支撑装置进行了简要的介绍,通过本人在工作中接触和了解的交叉支撑转向架故障多发部位和情况,针对交叉支撑转向架在实际运用中发生的故障进行详细介绍与分析,提出与实际情况相符的建议方案,从而减少转向架交叉支撑装置故障对铁路行车安全的影响。
关键词:铁路货车,交叉支撑装置,故障,建议为了适应我国铁路运输高速重载要求,提高运输效率,采用交叉支撑装置的转向架能够较大的增加转向架的抗凌刚度,从而提高转向架临界速度和货车直线运行稳定性;有效保持转向架正位状态,减少在曲线运行时轮对与钢轨冲角,从而改善转向架曲线通过性能,显著降低车轮轮缘磨耗。
转K2型转向架属于铸钢三大件式转向架,在两侧架之间安装了弹性下交叉支撑机构,交叉杆从摇枕下面穿过,4个端点轴向橡胶垫与侧架连接。
侧架弹性交叉支撑装置由1个下交叉杆、1个上交叉杆、8个轴向橡胶垫、4个双耳垫圈、4个锁紧板、4个标志板、4个紧固螺栓(强度等级10.9级)组成。
在上、下交叉杆中部焊有夹板,利用2组M12螺栓、螺母、垫圈将夹板紧固,同时把螺母用电焊点焊加固,夹板间有4处塞焊点和2条平焊缝,把上、下交叉杆连接成一个整体。
1.交叉支撑装置交叉杆磨耗原因分析1.1侧架上的横跨梁安装座焊装位置偏差较大,与侧架顶面的距离较小,当车轮直径较大,下心盘无垫板时,重车枕簧压缩情况下,上旁承也随之下降。
此外,横跨梁安装座立面翼板宽度尺寸过大,车辆通过曲线时上旁承最下部的磨耗板就会碰横跨梁安装座使之弯曲变形。
1.2交叉杆压痕前后位置设计不合理,现压痕前后位置没有完全躲开闸瓦托底部过渡圆弧,随着车辆的长时间运行,闸瓦托底部与交叉杆不断产生摩擦,最终导致交叉杆磨耗超限。
1.3货车车辆运行中受到的振动和冲击较大,而交叉杆属于簧下装置,振动更为严重。
剧烈的振动导致马蹄环螺栓松动,马蹄环随之与杆体间接触产生碰撞,使交叉杆横向以及马蹄环弧面根部产生较为严重的磨损。
转K2型转向架故障分析及改进建议

李春燕
科 技论 坛 Ij 1
霍 秀峰
转K 2型转 向架故障分析及改进建议
( 黑龙 江第二技 师学院 黑龙 江 绥化 12 5 ) 5 01
摘 要: 针对转 K 型转向架因其结构原 因造成摇枕 、 2 侧架 内腔积水, 轮对偏磨 , 从各方面分析原 因, 并提 出了改进 建议 。
关键词 : K 转 2型 转 向 架 ; 枕 ; 架 ; 盘座 加 强筋 ; 水 ; 对偏 磨 摇 侧 心 积 轮
达 2 m。 a r
责 任编 辑 : 雨 张
一ห้องสมุดไป่ตู้
— 一
量较小, 可以忽略不计, 因此可以认为摇枕的强度 没有变化, 即改动后仍可保证摇枕的运行安全。 3 . 2侧架下水孔改进。3. .1将侧架下弦面上 2 的下水孔下移 , 使孔的内弧边起始于下边平面上。 3 .将侧架 的两个下水孔 内面的内侧加强筋突 .2 2 起,在侧架下边纵向中心处各 留出一处宽 3r 0m a 的缺 口, 缺口底面与侧架内腔下平面平齐 , 内腔 使 内的水能全部 自 然流出。3 . .3将侧架的W i 2 " Y ̄ 孔周围的加强筋突起高度增加 2 倍。 3 3摇枕J 盘座加强筋的改进。 K 型转 向 转 2 架摇 枕心盘 销座底 面 至心盘 座上 平面距 离为 1 1 m 心盘座的中心孔处 的厚度为 4 r , 6m , 5 m 因此 a 中 心销座的孔高为 1 6 m 铸造摇枕时 , m 。 1 将心盘加 强筋的高度增加 l 6 m 即改进后心盘座加强筋 m , 1 高度为 2 7 m, 7 m 从距心盘座上平面 4 m 5 m起向下 留—个 1 , 孔 这个孔 的大小 、 位置与心盘座 E 的中 心孔相同。这样改动可方便地从摇枕两端中心销 座情况, 也便于在车辆落成后清理其 中的异物。 3 _ 4列检所作业加强对转 K 型转向架检查。 2 列检所作业要加强对转 K 型转向架轮对 、 2 摇枕、 交叉支撑装置和基础制动的检查。重点检查摇枕 是否有裂损, 交叉支撑装置是否弯曲变形 , 轮对是 否存在偏磨 , 基础制动装置是否别劲, 是否存在闸 瓦严重偏磨现象等。列检所必须及时更换到限合 成闸瓦。从运用检查看, 是合成闸瓦过限 , 凡 瓦背 钢板磨到车轮踏面的车轮均出现 了不规则磨耗 , 将车轮踏面沿圆周方向磨成很深凹槽 , 个别深度
铁道车辆机械装置检修 转K2型转向架

铁道车辆机械装置检修转K2型转向架介绍铁道车辆是运输系统中的重要组成部分,其中机械装置的正常运行对于保障运输安全和行车效率至关重要。
转向架作为车辆的重要组件之一,在运行过程中扮演着关键的角色。
本文将以K2型转向架为例,介绍铁道车辆机械装置检修的相关内容。
K2型转向架K2型转向架是常见的铁道车辆转向架之一,广泛应用于铁路运输中。
它具有结构简单、重量轻、承载能力大、操作灵活等特点,在铁路运输中得到了广泛应用。
K2型转向架由转向架架架体、负重弹簧装置、液压支承装置、制动器装置等部分组成。
它以转向架架体为基础,通过负重弹簧装置、液压支承装置和制动器装置的配合工作,实现车辆的转向和制动。
检修流程1. 检查转向架整体情况首先,需要对转向架的整体情况进行检查。
检查的内容包括转向架的外观是否有明显破损或变形,各连接处是否松动,零部件是否完好等。
如果发现有明显的问题,需要及时进行修复或更换。
2. 检查负重弹簧装置负重弹簧装置是转向架的重要组成部分,用于承载车辆的重量。
检查时,需要确认弹簧是否完好,是否存在变形或断裂等情况。
同时,要检查弹簧固定装置是否牢固,防止松动导致转向架失去稳定性。
3. 检查液压支承装置液压支承装置用于调节和稳定转向架的工作状态。
在检查时,需要检查液压缸是否正常工作,油路是否畅通,密封件是否完好等。
如发现问题,及时进行维修或更换。
4. 检查制动器装置制动器装置用于控制车辆的制动。
在检查时,需要检查制动器片是否磨损严重,制动器液压缸是否正常工作,制动盘是否平整等。
如果发现问题,应及时进行修复或更换。
5. 清洁和润滑在检修过程中,还需要进行清洁和润滑工作。
通过清洁可以去除转向架上的尘土和杂物,保持转向架的工作环境清洁。
润滑工作则可以减少零部件的摩擦和磨损,延长转向架的使用寿命。
安全注意事项在进行铁道车辆机械装置检修时,需要注意以下安全事项:1.检修时要确保车辆停稳并切断电源,防止意外启动导致伤害。
转K2型转向架常见故障的分析及采取的对策

转K2型转向架常见故障的分析及采取的对策随着铁路货车提速改造的进行,转K2型转向架在货车运用中所占的比例越来越高,作为60t提速货车转向架,以其稳定的性能,良好的运行品质为我国的铁路货车的发展做出了很大的贡献。
但是随着车辆运用时间的延长,转K2型转向架一些零部件的破损故障和整体结构的不合理问题应引起我们的重视。
常见故障:(一)侧架磨耗板故障1侧架磨耗板断裂转K2型转向架立柱磨耗板是通过这头螺栓、垫圈和防松螺母与侧架连接在一起的,如图1所示。
立柱磨耗板的状态对车辆运行中转向架的性能起着重要的作用,立柱磨耗板裂损将导致斜楔主摩擦面损伤,摩擦副性能降低,甚至失效,致使车辆动力性能降低,造成车辆运输安全隐患。
原因分析:侧架立柱磨耗板的加工质量是由多方面因素决定的,如材料的化学成分及加工工艺,材料的金相组织,磨耗板的具体设计以及质量控制等等。
影响磨耗板的组装质量取决与侧架立柱磨耗板安装面的平整程度、磨耗板的平整程度和他们之间的装配关系状况。
此外,磨耗板上的锥形沉孔的加工质量,折头螺栓底椎部与磨耗板锥形沉孔的配合状态也有很大关系。
2侧架磨耗板磨耗转K2型转向架侧架立柱面与磨耗板接触状态不良是发生磨耗板裂损的重要原因。
由于在侧架面没有进行机加工的要求,在铸造可以满足技术要求的条件下,不进行加工。
在实际生产中,部分工厂为了保证侧架立柱面的平面度和侧架的组装质量,对侧架立柱面进行了加工。
一些单位只是为了保证侧架的组装质量,对侧架立柱面上的铸造凸起进行了打磨,以满足磨耗板与侧架立柱四周的接触符合要求,但是磨耗板与侧架立柱中间出现间隙,形成如图所示的情况,此处的间隙很难被发现和检查测量。
在侧架组装后,由于磨耗板与侧架立柱中间存在间隙,连接磨耗板与侧架的折头螺栓紧固后(扭矩为500-550Nm),使磨耗板在沉孔出存在很大应力。
车辆落成后,车体的部分自重、重载和车辆动载荷等通过斜楔作用到磨耗板上,两者叠加,造成磨耗板裂损。
- 1、下载文档前请自行甄别文档内容的完整性,平台不提供额外的编辑、内容补充、找答案等附加服务。
- 2、"仅部分预览"的文档,不可在线预览部分如存在完整性等问题,可反馈申请退款(可完整预览的文档不适用该条件!)。
- 3、如文档侵犯您的权益,请联系客服反馈,我们会尽快为您处理(人工客服工作时间:9:00-18:30)。
铁路货车转K2型转向架主要故障的探讨及分析
摘要:根据我国铁路建设快速发展,我国铁路先后经过多次提速,目前我国铁
路货车速度已达到120km/h,现在铁路货车普遍使用的60t级K2型转向架,转向架一般随整车同时进行定期检修,检修的目的是恢复其原设计原型或保证各零部
件及配合间隙在规定的限度以内,保证整车在到达下次相应修程之前作用良好,
确保铁路运输安全。
关键词:货车;转向架;故障;分析;探讨
1.转K2型转向架的主要特点
转K2型转向架是采用交叉支撑转向架,车辆在运行过程中,存在点头运动、摇头(蛇形)运动、侧滚运动等六个自由度的运动方式,控制好该六种运动方式,是保证运行安全、提高运行品质的基本原理。
交叉支撑转向架通过采用新技术,
优化转向架抗菱刚度、转向架回转力矩、转向架正位状态、摩擦减振装置的相对
摩擦系数、空重车状态下弹簧静挠度等性能参数,有效地控制车辆的摇头、侧滚
运动,提高了车辆运行时的平稳性和稳定性。
转K2型转向架采用新技术有:侧架弹性下交叉支撑装置、JC型双作用常接
触弹性旁承、中央悬挂系统两级刚度弹簧、新型减振摩擦副、心盘磨耗盘、耐磨
销套。
2.交叉支撑装置中交叉杆裂损、开焊
图1 交叉杆杆体(压窝处)裂损图2 交叉杆焊缝开裂
2.1原因分析:
2.1.1在检修过程中,时常发现交叉杆裂损、焊缝开焊,原因之一是车辆在运行或整体翻转卸货时,容易造成交叉杆受力不均或碰撞交叉杆,其次交叉杆支撑
座与侧架组对焊接时定位不准确,有安装误差。
交叉杆端头紧固螺栓在紧固时,
未严格执行工艺标准和工艺要求,在车辆使用过程中,车辆在通过曲线或车辆产
生蛇行运动,由于交叉杆纠正其运行偏态时,容易在应力比较集中的地方发生断裂。
2.1.2焊接工水平参差不齐,焊后形成的焊缝有夹渣、气泡或焊缝高度达不到工艺要求,而且由于交叉杆属于簧下装置,在运行中承受的振动力和冲击力均很大,使有缺陷的焊缝在剧烈的振动作用下产生裂纹,最终导致裂损、开焊,造成
交叉杆脱落而引发车辆事故。
2.2改进建议:
2.2.1加强对交叉杆支撑座与侧架组对、焊接的质量检查、验收工作。
要求职工在作业时应严格执行厂、段修工艺规程,保证组对焊接质量,端头螺栓平均紧固,四条螺栓紧固力矩在675~700N.M范围内应尽量保持一致。
2.2.2加强焊接工的培训,提高焊接工的技术水准,对焊后的交叉杆严格执行探伤工艺要求,杜绝有缺陷的交叉杆组装到车辆上,提高车辆检修质量。
3.交叉杆杆体磨耗和弯曲、变形
3.1原因分析:
交叉杆杆体磨耗和杆体变形是比较严重的问题。
其中,杆体磨耗更为普遍,
在交叉杆杆体磨耗的交叉杆中磨耗量小于1mm的占70%,磨耗量为1mm~2mm
的占20%,磨耗量大于2mm的占10%。
有关规程规定,交叉杆磨耗量不应该超
过1mm。
按照这项规定,则有近30%的交叉杆不合格,这个比例是相当高的。
交叉杆臂厚为6mm,如果磨耗量超过1mm后,则极易形成应力集中,同时产生腐
蚀问题,大大降低该部位的疲劳可靠性。
鉴于交叉杆的重要性,对该问题必须引
起足够的重视,车辆运行中制动梁的闸瓦托经常磨损交叉杆的压形处,造成磨耗
过限较多,在组装交叉杆时未按工艺要求正确使用定位胎具组装,使转向架出现
菱形现象,造成交叉杆弯曲、变形。
3.2改进建议:
按照检修规程的要求,段修中对交叉杆磨损不超过限度者需要磨修清除缺陷,磨修面与非磨修面需平滑过渡,超限的要进行更换,由于受工装设备、检修手段
和配件供应等因素的制约,检修结果往往达不到技术要求。
平时应加强检修设备
的日常检查,均匀调整制动杠杆,使制动拉杆能拉住制动梁不碰到交叉杆,按要
求正确使用交叉杆定位胎具。
4.JC型双作用弹性下旁承组成裂损、变形
4.1原因分析
在检修过程中,时常发现JC型双作用弹性下旁承组成裂损、橡胶弹性旁承变形等故障,原因为在组装JC型双作用弹性下旁承时未使用专用工具、组装方法不正确,没有采用垂直面力平行压入,另外为使旁承磨耗板上平面至滚子上部的垂
直距离达到规定要求;允许在弹性旁承体与旁承座间加装调整垫板,调整垫板厚
度为2~5mm,数量为1块,但是在验收转向架时,经常发现加装的调整垫板有
时未安装入槽内,或者数量超限。
4.2改进建议
要严格执行工艺标准,旁承体与旁承座的拆、装应使用经铁道部批准定型专
用工装,旁承体与旁承座组装(拆卸)时,弹性旁承须纵向压缩旁承体两侧板后垂
直向下(上)平行装入(取出),旁承体侧板与旁承座定位槽内侧面应密贴,旁
承体顶板和侧板不得产生永久变形;旁承磨耗板与旁承体组装时,磨耗限度凹槽
应向上,采用垂直面力平行压入。
组装后旁承磨耗板不得松动,测量磨耗板的上
表面平面度应不大于0.5mm,用0.5mm厚度(宽度为10mm)塞尺检查旁承磨耗板与顶板间的周向局部间隙,插入深度不得大于30mm。
5.减振内簧折断
段修过程中分解检测枕簧时发现,减振内簧衰弱、折断现象时有发生,且裂
纹和折损多发生在1圈—2圈内,裂纹一般自簧杆内侧开始,断口全新,呈扭断状。
大量减振内簧折断,既增加了检修单位材料费用的支出,又影响了转向架性
能的发挥和车辆运行安全。
减振内簧折断后,一方面使摇枕和车体倾斜,另一方面又使相应的外簧受力
增大,外簧的弹塑性也随之增大,轮对出现减载现象,影响车辆运行安全。
若超
出外簧弹性强度极限,则有可能使之折断,造成斜楔与侧架立柱磨耗板之间的压
力减小或者降为零,降低了转向架的减振性能。
同时,整个转向架斜楔、侧架立
柱磨耗板偏磨,摇枕错位,转向架正位刚度变差,摇枕、侧架间的抗菱刚度变小,交叉杆轴向、径向受力增加,进一步发展可导致交叉杆变形,严重的可能会危及
行车安全。
5.1原因分析:
5.1.1转K2型转向架斜楔副摩擦面与底面夹角为32°,与其他几种斜楔相比,对应夹角有所减小,因此相同摇枕压力通过斜楔时对减振弹簧的压力将有所增加。
5.1.2、从折断的内簧断口可以看出,在簧杆由圆截面过渡到矩形截面处存在着凸台及波形不平现象。
内簧卷制时,端部支撑圈和工作圈不光滑,有毛刺,且有刻伤、刻痕、裂纹、折叠、尖锐边缘和夹具伤痕;弹簧支撑圈端部与工作圈之间的间隙太大,运用过程中端头和工作圈之间磨出沟槽。
以上缺陷在运用中极易形成应力集中,导致裂纹的产生。
5.2改进建议
5.2.1保持原减振外簧设计标准不变,将减振内簧圆钢直径和减振内簧外径适当增加;严格控制热处理后减振弹簧单边脱碳层的深度,必要时可以渗碳处理。
4.2.2圆弹簧圆钢受到腐蚀、磨耗超过原形8%、圆弹簧支承圈不足5/8时应更换;检修中,对弹簧支撑圈端部与工作圈之间容易磨出沟槽的地方要注意详细检查,发现凹坑超限时及时更换。
6.结论
在铁路货车主要配件中,转向架是车辆的走行部分,同时也是故障率较高的配件之一,是铁路货车安全防范的重点。
在铁路货物运输提速、重载发展的形式下,随着列车速度进一步的提高,转向架的可靠性问题变得更加突出。
因此,要保证转向架具有较高的安全可靠性,必须严格执行检修工艺标准,并根据各制造单位的实际情况,认真分析,细化工艺,多做试验,摸索规律。
降低转向架故障率。
参考文献
[1]张进德.《铁路货车交叉支撑转向架》.中国铁道出版社.2002年
[2]严隽耄.《车辆工程》.中国铁道出版社.2003年
[3]陈雷杨绍清.《铁路货车段修技术与管理》.中国铁道出版社.2004年
[4]黄毅陈雷.《铁路货车检修技术》.中国铁道出版社.2010年。