切削加工技术发展史
刀具材料论文

金属切削刀具的发展历史与现状前言刀具是机械制造中用于切削加工的工具,又称切削工具。
广义的切削工具既包括刀具,还包括磨具。
刀具技术的进步,体现在刀具材料、刀具结构、刀具几何形状和刀具系统四个方面,刀具材料新产品更是琳琅满目。
当代正在应用的刀具材料有高速钢、硬质合金、陶瓷、立方氮化硼和金刚石。
其中,高速钢和硬质合金是用得最多的两种刀具材料,分别约占刀具总量的30%~40%和50%~60%。
本文将介绍刀具的发展历程,发展现状,并对未来刀具的发展法相作出分析。
刀具的发展历史刀具的发展在人类进步的历史上占有重要的地位。
中国早在公元前28~前20世纪,就已出现黄铜锥和紫铜的锥、钻、刀等铜质刀具。
战国后期(公元前三世纪),由于掌握了渗碳技术,制成了铜质刀具。
当时的钻头和锯,与现代的扁钻和锯已有些相似之处。
然而,刀具的快速发展是在18世纪后期,伴随蒸汽机等机器的发展而来的。
1783年,法国的勒内首先制出铣刀。
1792年,英国的莫兹利制出丝锥和板牙。
有关麻花钻的发明最早的文献记载是在1822年,但直到1864年才作为商品生产。
那时的刀具是用整体高碳工具钢制造的,许用的切削速度约为5米/分。
1868年,英国的穆舍特制成含钨的合金工具钢。
1898年,美国的泰勒和.怀特发明高速钢。
1923年,德国的施勒特尔发明硬质合金。
在采用合金工具钢时,刀具的切削速度提高到约8米/分,采用高速钢时,又提高两倍以上,到采用硬质合金时,又比用高速钢提高两倍以上,切削加工出的工件表面质量和尺寸精度也大大提高。
由于高速钢和硬质合金的价格比较昂贵,刀具出现焊接和机械夹固式结构。
1949~1950年间,美国开始在车刀上采用可转位刀片,不久即应用在铣刀和其他刀具上。
1938年,德国德古萨公司取得关于陶瓷刀具的专利。
1972年,美国通用电气公司生产了聚晶人造金刚石和聚晶立方氮化硼刀片。
这些非金属刀具材料可使刀具以更高的速度切削。
1969年,瑞典山特维克钢厂取得用化学气相沉积法,生产碳化钛涂层硬质合金刀片的专利。
《金属切削原理与刀具》课程授课教案
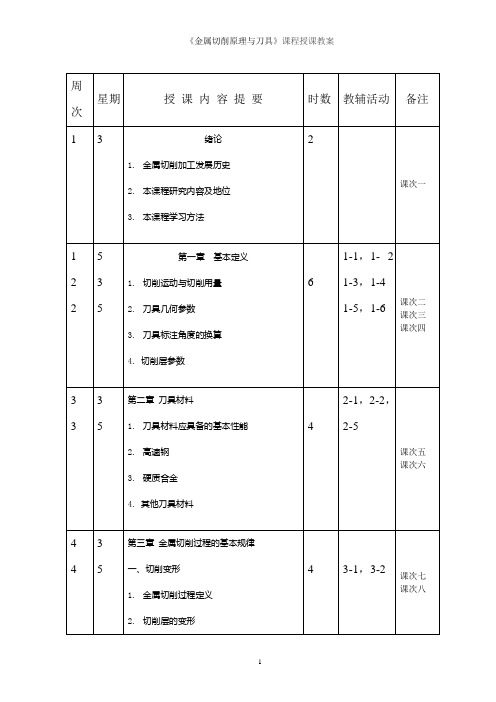
13
3
5
第七,八章孔加工刀具
1.孔加工刀具的种类及用途
2.麻花钻
3.深孔钻
4.铰刀
4
7-2 7-4
7-8 8-1
课次二十四、五
14ห้องสมุดไป่ตู้
3
第九章拉刀
1.拉刀的种类及用途
2.拉刀的结构
3.圆孔拉刀的设计
2
9-1 9-2
9-3
课次二十六
14
15
5
3
第十章铣刀
1.铣刀的种类及用途
2.铣刀的几何角度
3.铣削力及铣削方式
其次,要根据机器的结构和技术要求,把某些零件装配成部件。部件是由若干组件、套件和零件在一个基准上装配而成的。部件在整个机器中能完成一定的、完整的功能。这种把零件和组件、套件装配成部件的过程称为部装过程。部装过程是依据部件装配工艺,应用相应的装配工具和技术完成的。部件装配的质量直接影响整个机器的性能和质量。
1.刀具材料应具备的基本性能
2.高速钢
3.硬质合金
4.其他刀具材料
4
2-1,2-2,
2-5
课次五
课次六
4
4
3
5
第三章金属切削过程的基本规律
一、切削变形
1.金属切削过程定义
2.切削层的变形
3.第一变形区
4.第二变形区
5.第三变形区
6.切削变形的变化规律
4
3-1,3-2
课次七
课次八
5
5
3
5
二、切削力
1.切削力的来源
0.4本课程的内容与学习方法
金属切削原理与刀具是研究金属切削过程基本规律、刀具设计与使用的一门科学,是机械制造专业的重要课程。
切削加工与刀具技术的历史

切削加工与刀具技术的历史介绍了中国远古时期石器时代铁器时代的切削加工与刀具技术中国领先于全世界从第一次工业革命以后阐述了欧美各国和俄罗斯在切削加工技术解放后工件与刀具双方交替发展关键词它在国民经济中占有重要地位刀具用坚硬的材料制成切削加工的任务是利用刀具切除被加工对象毛坯上的多余材料精度和表面质量都符合预定要求的表面是由古代切削加工本文将阐述古代1 古代的切削加工和刀具在切削加工方面旧石器时代距今约50~60万年的北京猿人制造和使用了各种带刃的石器刮削器和尖状器(图1)¿³ÔÒÆ÷ÓÒ²¿Ô²Íº×ó²¿ÓзæÈйÎÏ÷Æ÷ºÍ¼â×´Æ÷ÉÏÔò¾ù¾ßÓÐÃ÷ÏԵķæÀûÈв¿µ«ËüÊÇÒ»ÇÐÈËΪ¼Ó¹¤µÄ¿ªÊ¼到了新石器时代石刀石锛刀体比较匀称有凸刃圆刃等这是钻孔技术的开端制作形状和用途各异的切削工具新石器时代的人类曾把坚硬的石片镶嵌在骨把上石器时代的切削工具加工对象也多为非金属材料(如石材兽骨等)ÒѾ-¾ß±¸ÁËÈý¸ö»ù±¾ÒªËص¶¾ß(带刃部的工具)被加工对象(生产或生活用品)切削运动(人用手握持住刀具与被加工对象 刀具的发明和切削加工的应用历史学家认为它是人类登上历史舞台的重要标志(1) 砍砸器(约为原大的1/2) (2) 刮削器(约为原大的2倍) (3) 尖状器(约为原大的2倍)图1 砍砸器图2 新石器时代的石刀图3 新石器时代的石刃骨刀(甘肃永昌鸳鸯池出土)从青铜器时代开始早在齐家文化时期已用天然铜制造器具已经有了相当发达的青铜冶铸业图4所示为商代的青铜钻锯这些刀锉的结构和形状似于现代的切削工具而包括了金铜等金属材料当时这些切削工具发挥了多么大的作用图4 商代的青铜钻(郑州二里冈出土)图5 春秋时代的青铜刀锉(河南汲县山彪镇出土)商代还会制作过铁刃铜钺(图6)ÏâǶÔÚÍ-ÖÊîáÌåÉÏÈпڵĻùÌåΪÌú含镍1.76%ÎýîܹèËùÒÔÈв¿²ÄÁÏʵ¼ÊÉÏÊÇÒ»ÖÖº¬ÓжàÖֺϽðÔªËØµÄ¸Ö²Ä图6 商代的铁刃铜钺(河北藁城出土)石刃骨刀和铁刃铜钺说明当时已经认识到刀具刃部的重要作用刀刃取稀缺刀体取价值较低但韧性较好的材料青铜器时代的大量出土文物表明生产工具和生活用品磨削加工或研磨实质上也是一种切削加工我国发明了生铁冶铸技术渗碳为制造坚硬锋利的工具提供了有利的条件使切削加工进入了一个新阶段分工比较细致出现了用金属刀具刻镂的纹饰和钻孔的痕迹有一部手工艺专著上面记载了各种兵器介绍了关于战车的制造工艺金工等30个专业的技术知识材美工巧所谓指采用优良的材质工巧是指采取合理由此可见包括一部分切削加工当时的实战兵器很多矛钺镞制作十分精致光亮无锈经化验含锡21.38%锌0.041%º¬Îý11.10%锌0.098%解放后在河北满城一号汉墓(中山靖王之墓)中出土的五铢钱(图7)µ¶»¨¾ùÔÈÍÖÔ²¶ÈºÜСȻºó×°¼ÐÔÚľ֯µÄ³µ´²ÉÏÐýתͬĹ³öÍÁµÄÆ÷ÎïÖÐÌúÔä¾-¹ýÉøÌ¼´¦ÀíµÄÌú½£ºÍÊéµ¶ÆäÖе«¼Ó¹¤¾«¶ÈºÍ±íÃæÖÊÁ¿ºÜ¸ß˵Ã÷µ±Ê±µÄÇÐÏ÷¼Ó¹¤¼¼ÊõÒѾ-´ïµ½ÁËÒ»¶¨µÄˮƽ图7 西汉时代的五铁钱(河北满城一号汉墓出土)(1)青铜弩机(2)青铜箭头图8 西汉时代的青铜弩机和箭头(河北满城一号汉墓出土)在西安出土的唐代文物中银制造的盘在这些器具上有明显的车削痕迹刀痕细密体现出当时较高的加工精度我国最晚在8世纪时已有原始的切削车床北宋在一百年内先后制造了五座浑仪分度读数能精确到四分之一度明制造精度进一步提高仪器上直径达两米多的大铜环内孔上刻度的加工精度和表面质量都已达到了相当高的水平大铜环的端面是用图9和图10所示的方法[1,9]½øÐÐϳÏ÷ºÍÄ¥Ï÷¶øÖƳɵÄ图12为大铜环制造过程中划线在长期的实践中明代张自烈著[2] (图13)中对刃挤都写出了明确的含义刃为用古谓之芒又说刃从坚则钝古人十分强调刃部的重要性利坚对切削原理已有了一些朴素的唯物辩证的认识图9 清代天文仪器上大铜环的加工(铣削)图10 清代天文仪器上大铜环的加工(磨制)图11 清代铣刀的刃磨图12 清代天文仪器上大铜环的加工(划线和检测)图13 明代上有关刀及刃的论述从以上资料可以看出有着光辉的成就特别是铁器时代2 近代的切削加工机械工程迅猛发展成为一个独立的工程和学科1847年而美国则到1880年才成立了机械工程师协会是和从英国开始的工业革命密切相关的蒸汽机的出现和纺织工业军事工业的兴起每一种新产品的发明和设计才能付诸实现推动着机械制造(包括切削加工)技术迅速提高最早的蒸汽机在很大的程度上是用手工方法加工出来的英国有一位叫理查德它的内孔直径为28È»ºóÇëÀ´Ò»Î»Ç¦½³ËûÓÃľ°åºÍÄàɰµ²×¡Æû¸×µÄÁ½¶ËÕâÑù¾Í¼Ó¿ìÁËÄ¥¹âÆû¸×µÄ¹¤×÷ÌúÌõÉÏϵÉÏÉþ×ÓÀ-סÉþ×ÓÔÚÆû¸×ÌåÄÚÍ¿ÉϽð¸ÖɰºÍ¾¨ÓÍǦ¿éÏÂÃæµÄÆû¸×Äڿ׾ͱ»Ä¥¹âÁËÄÚ¿×µÄÁíÒ»²¿·ÖҲѸËÙ±»Ä¥¹â¾-¹ý¼è¿àµÄŬÁ¦ºÍ·±ÖصÄÀͶ¯Ö®ºó¼´ËüµÄ×î´óÖ±¾¶Óë×îСֱ¾¶Ö®²î²»´óÓÚÎÒµÄСÊÖÖ¸µÄºñ¶ÈÒòΪÕâÊÇÆù½ñËùÖªµÀµÄ×îºÃµÄ¼Ó¹¤·½·¨¸ù¾ÝÕâÒ»¶ÎÈÕ¼ÇÈçͼ14所示图14 1760年英国加工汽缸内孔的情形由此可知铸铁但由于缺少先进的机床和工具因而工作效率很低1776年詹姆斯遇到的最大困难是由于镗孔加工方法落后漏汽严重皮革或油脂也无济于事威尔金森(John Wilkinson)帮助瓦特解决了汽缸加工的问题可以加工直径达1.8 m的内孔它的刀杆有4.5 m长可以加工蒸汽机的汽缸并满足精度要求瓦特的蒸汽机才得以顺利制成他为瓦特铸造和加工汽缸达20年之久提高工艺水平和加工技术在18世纪中叶以前当时切削加工所用的机床多数是木制的由于工业革命的推动大约经过一百年的努力解决了各种各样加工问题西奥(Antoine Thiout)在车床上装了一个刀架比过去用手握持车刀进给前进了一大步英国工程师杰西1818年用单齿铣刀进行工作苏格兰詹姆斯1836年1835年)设计了第一次由丝杠同时驱动纵向和横向进给的车床美国的罗宾斯和劳伦斯(Robbins & Lawrence)公司制造出转塔车床轮流进行8道工序的加工在巴黎举行的国际博览会上标志着机床和切削加工已经发展到一个崭新的历史阶段1892年美国诺顿(Norton W. P.)发明了用手柄换档的变速箱这种变速机构很快被应用到各种机床上1887年美国格兰特(Grant G)发明滚齿机1895年发明伞齿刨床泰勒(Taylor F)发明齿轮磨床万能铣床已经基本完善制成座标镗床世界上各主要工业国家的机床工业已具有相当规模工作母机又被称为业的发展 自从切削加工技术发展到一定水平后研究切削理论研究工作主要是从19世纪最早研究切削加工机理的人要数英国的罗姆福德(Rumford)1851年)直接测量了钻削时切除单位体积金属所需的功德国的哈蒂格(Hartig E1770年俄国的基麦(Tème и)和1873年法国的特雷沙(Tresca H1881年)正确指出还强调刀具前刀面上摩擦作用的重要性腐蚀进行观察刀刃锋利性对切削过程的影响以及切削过程中引起颤振的原因)于1900年提出在刀具的刃前区工件材料存在一个裂纹这种认识是错误的19世纪后斯至20世纪初期W1856 ̄1915)对金属切削加工的规律1906年他发表了一篇著名的科学论文1941年and Merchant M)发表了关于金属切削过程力学的著名论文 前苏联很重视科学技术史的研究经常写入一些名人的传略1870至1877年A但未考虑摩擦和塑性变形的影响俄国科学家慈伏雷金(3âîðûêèн K )在切削力的主要问题上作了许多研究工作制作了直接测定切削力的测力仪在实验基础上只知道切削力与切削面积的大小有关当然是一件了不起的事情彼得堡工业学院主任技师乌沙乔夫(Óñà÷åâ ß)进行了很多研究工作创造了用热电偶测量切削温度的方法用金相方法研究切削过程寻求切削规律的方法契留斯金(×åлþñòêèí A )进一步建立了多因素的切削力公式0.7525.0z )(sin 1 60ts øäk P = 式中 k 常数δ 切削角ϕ 主偏角t 切削深度s 进给量 俄国和苏联的科学家们虽然有过很多贡献做过多方面深入研究还应首推美国工程师泰勒世纪末到20世纪初美国机械制造行业的发明家和科学管理家(1) 研究了切削条件和刀具材料对于刀具寿命的影响规律从而优选切削条件得到T¼´Ëùν»òm与刀具材料至今还在应用刀具上的切削温度控制着刀具磨损的速率)于1898年研制成功了高速钢系统的切削试验他们确定的高速钢最佳成分为W18.91%Mn0.11%Fe余量高速钢可用30m/min的速度切削钢材合金工具钢提高了好几倍引起了切削加工的重大变革当时伯利恒钢铁公司的机械加工车间使用了高速钢曾使生产提高了5倍美国机械制造行业从而增加了80亿美元的产值高速钢的成分和性能有了很多变化但当今用得较多的一种钨系高速钢W18Cr4V的化学成分仍然同泰勒(4)泰勒首创(Time Study)和(Motion Study)1911年他发表了(Principle of Scienitific Management)一书泰勒把身体最健壮精确地计算出该工人每一动作所花费的时间找出时间最省资本家曾使之成为一种固定制度这种制度后来被称为泰勒制曾有过各种不同观点的评论泰勒制被资产阶级所利用列宁对泰勒制有过全面的论述[6]Ò»·½ÃæÊÇ×ʲú½×¼¶°þÏ÷µÄ×îÇÉÃîµÄ²Ð¿áÊÖ¶ÎÁíÒ»·½ÃæÊÇһϵÁеÄ×î·á¸»µÄ¿ÆÑ§³É¾Íʡȥ¶àÓàµÄ±¿×¾µÄ¶¯×÷ʵÐÐ×îÍêÉÆµÄ¼ÆËãºÍ¼à¶½ÖƵȵÈÁÐÄþÓÖÖ¸³öÔÚÕâ·½ÃæÎÞÂÛÈçºÎ¶¼Òª²ÉÓÿÆÑ§ºÍ¼¼ÊõÉÏÒ»Çб¦¹óµÄ³É¾ÍÒò´ËÓ¦¸ÃÔÚ¶í¹úÑо¿Óë´«ÊÚÌ©ÀÕÖÆ²¢ÇÒʹËüÊÊÓ¦ÏÂÀ´Óɴ˿ɼû¶øÊÇ×÷Á˿͹۵Ä总之是不容抹煞的惠特沃思泰勒等人见诸历史的教授在历史长河中如工人也曾对切削加工技术作出过重要贡献但是应该同样地怀着崇敬的心情来纪念他们自19世纪中叶起由三方面组成外国人经营的船舶修造厂和铁路工厂等清朝政府兴办的机械工业金陵机器局天津机器局等民族资本家经营的机器制造厂值得写记的有由江南制造局发展而成的江南造船所于1921~1922年间曾为美国建造过4艘万吨运输船1916年上海王岳记机器厂造出我国第一台3号万能铣床抗日战争前自成体系战争作准备实力很弱七事变后国民党在大后方(主要在重庆成都解放区为了抗战需要从事军械修理炮等武器到1947年职工10.7万人年用电量1.4 亿多度有少数的机床修造厂和工具厂能自制一些普通车床铣床丝锥等简单刀具和量具旧中国的切削加工技术是非常落后的中国约比欧美先进国家落后了近一百年3 解放后中国切削加工与刀具技术大发展1949年机械工业迅速发展在前苏联援建的156项重点企业中如汽车制造厂飞机制造厂硬质合金制造厂等又改建新建了许多制造工厂文革特别是国民经济改革开放以后加强对外交流在数量和质量水平上都步入了国际先进行列全国机床有300余万台唯数控机床所占的比例尚低于工业先进国家中工具厂遍布全国刀具结构加工效率大幅度增长铣床的切削速度由解放初的10 m/min提高到现在500~1000 m/min(切削普通钢铝合金)半个世纪以来目前如硬质合金年产7 000~10 000 t均为世界第一铣刀已采用了先进的机夹可转位结构内外排屑的深孔钻及改进结构后的麻花钻也得到普遍应用数控机床和加工中心上所用的刀具系统也实现了完善与进步热加工)者达200所以上很多学校对切削加工和刀具的理论与实践进行科学研究如华南理工大学在已加工表面质量哈尔滨工业大学在超精密切削哈尔滨理工大学在断屑方面西安交通大学在齿轮刀具方面新型刀具材料及机械加工发展史方面华侨大学在石材加工方面华中科技大学在极薄层切削北京航空航天大学在并联机床及钻头刃磨方面车铣机床与超高速铣床的研制(主轴达3 000~6 000 r/min)方面合肥工业大学在绿色制造方面河北理工学院在切削液方面南京航空航天大学在难加工材料高速切削及CVD金刚石镀膜刀具方面等等成果丰硕实用在解放初期做出了很大贡献北京永定机械厂的倪志福上海锅炉厂的李福祥北京人民机器厂的桂育鹏使用了强力切削车刀可转位铣刀长春第一汽车制造厂的张国良创造了超细长杆的车削工作法哈尔滨的孙茂松创造了高速挑蜗杆先进工作法沈阳全福长对强力车刀等等带动和培养了大量现场工作人员全国劳动模范在20世纪50年代就建立起来的机床研究所兵器55所等均为有关切削加工的专业研究单位做出了很大贡献积累了丰富的经验例如高锰钢的切削方面航天工厂在高温合金电子行业在有色金属的切削方面冶金行业在高硬度钢与铸铁轧辊的切削方面高校与工厂还实践了多种新型切削加工方法等离子体加热)Õæ¿Õ»·¾³ÏÂÇÐÏ÷Ê©¼Ó¸÷ÖÖÇÐÏ÷ÒºµÄÇÐÏ÷Ê©¼ÓÅçÎíÀäÈ´µÄÇÐÏ÷µÈµÈÓеÄÒѸ¶ÖîÓ¦ÓÃĿǰÖйúÒÑÓµÓÐÇ¿´óµÄ»úÐµÖÆÔì¹¤ÒµÒ²ÕÆÎÕÁËÏȽøµÄÇÐÏ÷Óëµ¶¾ß¼¼ÊõÄÜÖÆÔìÎÀÐÇÄܽ¨ÉèÈýÏ¿¹¤³ÌºÍ´óÐ͵çÕ¾ÄÜÖÆÔìËùÓеij£¹æÓëÏȽøµÄ±øÆ÷»¯¹¤ÄÜÖÆÔìËùÓеÄÏȽø»ú´²ºÍµ¶¾ßÖйúÒѳÉΪ»úÐµÖÆÔìµÄ´ó¹úºÍÇ¿¹úÒÙÁ¢ÓÚå¾Çò¼¼ÊõÂäºóµÄ¾ÉÖйúÒѾ-һȥ²»¸´·µÁ˵¶¾ßË«·½½»Ìæ·¢Õ¹µ¶¾ßÓ빤¼þÓÐ×ŶÔÁ¢ºÍͳһµÄ¹ØÏµ¾-³£Íƶ¯ÁíÒ»·½·¢Õ¹Ç°½øÓÉÓÚÉú»î¹¤¼þÒ»·½µÄÇé¿ö¾-³£·¢Éú±ä»¯¹¤¼þ²ÄÁϵĻúеÐÔÄÜ(如强度产品的品种和批量逐渐增多工件的结构等等就不断向刀具提出更新当刀具不能满足这些要求时提高其性能刀具性能提高了接着工件又推动刀具继续前进工件材料多为灰铸铁它们较易加工19世纪中叶以后钢的产量迅速增加熟铁等钢的加工要难一些只能采有5~10 m/min的切削速度于是高碳工具钢已不能适应新的加工要求英国的罗伯特使切削速度提高到8~12 m/minÈÔÊǺÜÓкܵÄÇÐÏ÷ÆÕͨ¸Ö²ÄʱËÙ¶ÈÒ»ÏÂ×ÓÌá¸ßµ½30 m/min³ÉΪÇÐÏ÷¼¼ÊõÀúÊ·ÉϵÄÒ»´ÎÖØ´ó±ä¸ïµ¶¾ß²ÄÁ϶ÔÓÚµ±Ê±¼Ó¹¤µÄÐèÒª´óÌåÉÏÊÇÊÊÓ¦µÄ½øÈë20世纪以来其机械性能日益提高各种高强度钢高硬耐磨铸铁钛合金等难加工材料相继出现或者根本切不动人们又改进高速钢的化学成分与热处理方法出现了很多新型高速钢高钒超硬高速钢等20世纪20年代至30年代初并逐步用于生产可比高速钢提高4~10倍可以切削高速钢所加工不了的材料硬质合金脆性较大因此只能在部分加工范围内代替高速钢使用又出现了陶瓷人造金刚石等更为先进的刀具材料然而加上价昂直到最近它们的使用面均尚受到局限切削加工仍处在大量使用高速钢与硬质合金的时代硬质合金约占50%~60%ÌմɵÈÏȽøµ¶¾ß²ÄÁÏ硬铸铁正因为如此而在19世纪或20世纪初是根本不可想象的维持切削性能的最高温度以及切削速度的大致比值可以预期加工效率要求进一步提高高速切削即所谓超精密切削数控技术主导的和环保要求的所有这些而刀具材料更是关键是既有高的硬度和耐磨性刀具对于被加工工件和工作条件再适应交替发展这就是切削加工与刀具技术发展的历史规律17131665ɽ¶«¿ÆÑ§¼¼Êõ³ö°æÉçÐìºëɽÒë. 北京19805 Taylor F, W. On tne art of cutting metals. Trans. ASME, 1906, 28:13~206 [苏]列宁. 列宁选集. 中文译本第三卷. 北京19727 于启勋. 论现代刀具材料的新进展. 中国高校切削与先进制造技术研究会第六届年会论文集. 北京1999Öйú´ó°Ù¿ÆÈ«Êé³ö°æÉç¸ßµÈ½ÌÓý³ö°æÉç。
先进制造工艺--高速切削技术
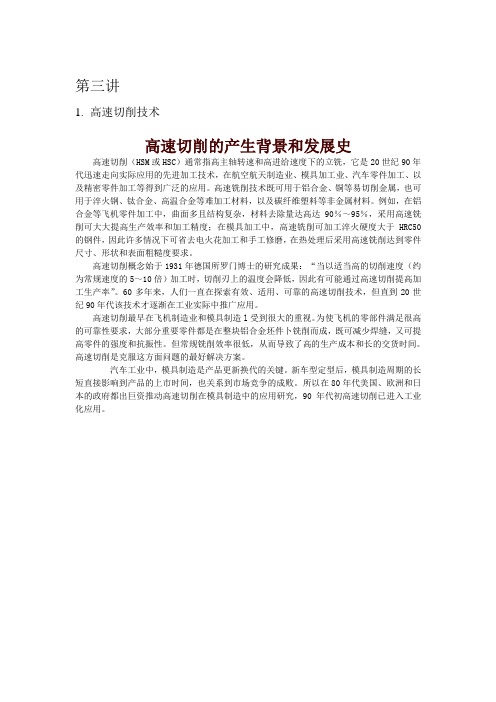
第三讲1.高速切削技术高速切削的产生背景和发展史高速切削(HSM或HSC)通常指高主轴转速和高进给速度下的立铣,它是20世纪90年代迅速走向实际应用的先进加工技术,在航空航天制造业、模具加工业、汽车零件加工、以及精密零件加工等得到广泛的应用。
高速铣削技术既可用于铝合金、铜等易切削金属,也可用于淬火钢、钛合金、高温合金等难加工材料,以及碳纤维塑料等非金属材料。
例如,在铝合金等飞机零件加工中,曲面多且结构复杂,材料去除量达高达90%~95%,采用高速铣削可大大提高生产效率和加工精度;在模具加工中,高速铣削可加工淬火硬度大于HRC50的钢件,因此许多情况下可省去电火花加工和手工修磨,在热处理后采用高速铣削达到零件尺寸、形状和表面粗糙度要求。
高速切削概念始于1931年德国所罗门博士的研究成果:“当以适当高的切削速度(约为常规速度的5~10倍)加工时,切削刃上的温度会降低,因此有可能通过高速切削提高加工生产率”。
60多年来,人们一直在探索有效、适用、可靠的高速切削技术,但直到20世纪90年代该技术才逐渐在工业实际中推广应用。
高速切削最早在飞机制造业和模具制造l受到很大的重视。
为使飞机的零部件满足很高的可靠性要求,大部分重要零件都是在整块铝合金坯件卜铣削而成,既可减少焊缝,又可提高零件的强度和抗振性。
但常规铣削效率很低,从而导致了高的生产成本和长的交货时间。
高速切削是克服这方面问题的最好解决方案。
汽车工业中,模具制造是产品更新换代的关键。
新车型定型后,模具制造周期的长短直接影响到产品的上市时间,也关系到市场竞争的成败。
所以在80年代美国、欧洲和日本的政府都出巨资推动高速切削在模具制造中的应用研究,90年代初高速切削已进入工业化应用。
图16 高速切削在生产应用中的发展历程图17 采用高速切削后产品质量提高的历程a一硬质合金切钢 b一硬质合金切铸铁c—CBN切铸铁图16是德国宝马公司(BMW)采用高速切削的历程。
数控机床的发展历史和趋势
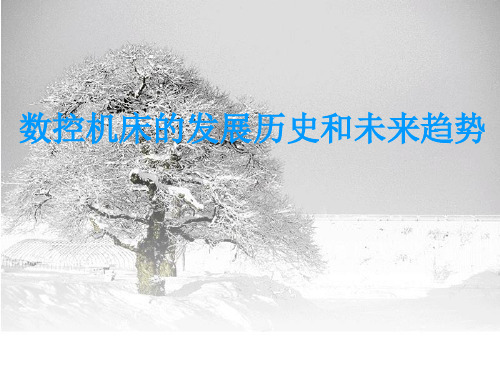
未来的数控机床
智能化、 3.智能化、网络化: 智能化 网络化:
追求加工效率的智能化,如自适应控制; 追求加工效率的智能化,如自适应控制;提高驱动性 能及使用连接方便的智能化,如电机参数的自适应运 能及使用连接方便的智能化, 算等;简化编程、简化操作的智能化, 算等;简化编程、简化操作的智能化,如智能化的自 动编程、智能诊断等。 动编程、智能诊断等。 数控装备的网络化实现了新的制造模式如敏捷制造、 数控装备的网络化实现了新的制造模式如敏捷制造、 虚拟企业等。 虚拟企业等。
数控机床的发展先后 经历了电子管( 经历了电子管(1952 )、晶体管 晶体管( 年)、晶体管(1959 )、小规摸集成电 年)、小规摸集成电 路(1965年)、大规 年)、大规 模集成电路及小型计 算机( 算机(1970年)和微 年 处理机或微型机算机 (1974年)等五代数 年 控系统。 控系统。
高精度、高可靠性 高精度、高可靠性: 普通级数控机床的加工精度已由±10μm提高 普通级数控机床的加工精度已由±10μm提高 5μm; 到±5μm; 精密级加工中心的加工精度则从± 5μm, 精密级加工中心的加工精度则从±3~5μm, 提高到± 1.5μm。 提高到±1~1.5μm。 数控装置的平均无故障时间值已达6000小时 数控装置的平均无故障时间值已达6000小时 平均无故障时间值已达6000 以上,驱动装置达30000小时以上。 30000小时以上 以上,驱动装置达30000小时以上。
2.复合化、多轴化: 2.复合化、多轴化: 复合化 一次装夹,整体加工。 一次装夹,整体加工。 在加工自由曲面时, 在加工自由曲面时,5轴联动控制对球头 铣刀的数控编程比较简单, 铣刀的数控编程比较简单,并且能使球头铣 刀在铣削3 刀在铣削3维曲面的过程中始终保持合理的切 从而提高加工效率。 速,从而提高加工效率。
我国数控系统的发展史
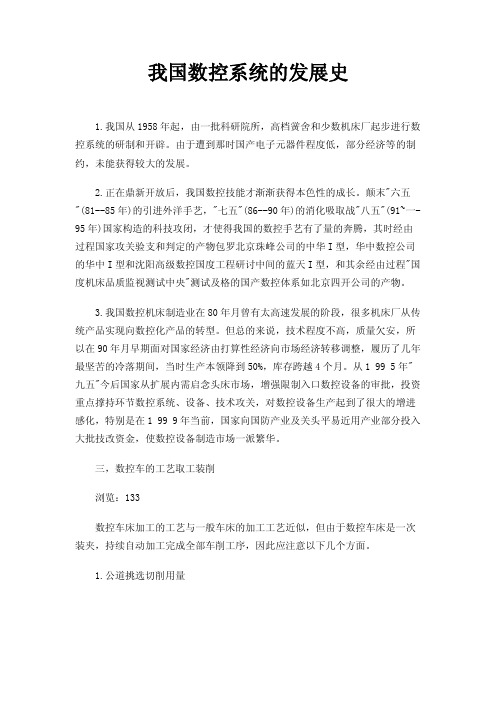
我国数控系统的发展史1.我国从1958年起,由一批科研院所,高档黉舍和少数机床厂起步进行数控系统的研制和开辟。
由于遭到那时国产电子元器件程度低,部分经济等的制约,未能获得较大的发展。
2.正在鼎新开放后,我国数控技能才渐渐获得本色性的成长。
颠末"六五"(81--85年)的引进外洋手艺,"七五"(86--90年)的消化吸取战"八五"(91~一-95年)国家构造的科技攻闭,才使得我国的数控手艺有了量的奔腾,其时经由过程国家攻关验支和判定的产物包罗北京珠峰公司的中华I型,华中数控公司的华中I型和沈阳高级数控国度工程研讨中间的蓝天I型,和其余经由过程"国度机床品质监视测试中央"测试及格的国产数控体系如北京四开公司的产物。
3.我国数控机床制造业在80年月曾有太高速发展的阶段,很多机床厂从传统产品实现向数控化产品的转型。
但总的来说,技术程度不高,质量欠安,所以在90年月早期面对国家经济由打算性经济向市场经济转移调整,履历了几年最坚苦的冷落期间,当时生产本领降到50%,库存跨越4个月。
从1 99 5年"九五"今后国家从扩展内需启念头床市场,增强限制入口数控设备的审批,投资重点撑持环节数控系统、设备、技术攻关,对数控设备生产起到了很大的增进感化,特别是在1 99 9年当前,国家向国防产业及关头平易近用产业部分投入大批技改资金,使数控设备制造市场一派繁华。
三,数控车的工艺取工装削浏览:133数控车床加工的工艺与一般车床的加工工艺近似,但由于数控车床是一次装夹,持续自动加工完成全部车削工序,因此应注意以下几个方面。
1.公道挑选切削用量对付下服从的金属切削加工来讲,被加工质料、切削东西、切削条件是三大体素。
这些决议着加工时间、刀具寿命和加工质量。
经济有用的加工体式格局一定是公道的选择了切削前提。
切削前提的三因素:切削速度、进给量和切深间接引发刀具的毁伤。
先进制造技术 第2章 高速切削技术2-1
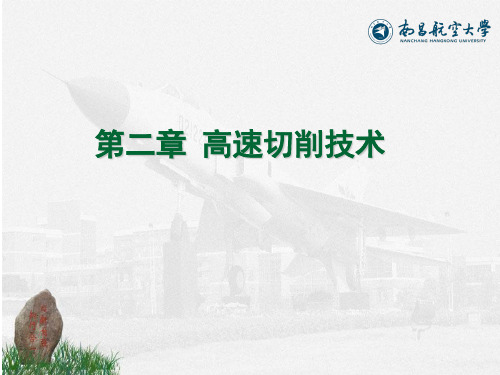
萨洛蒙在l924一1931年间,进行了一系列的高速切削实验: 在非黑色金属材料,如铝、铜和青铜上,用特大直径的刀 盘进行锯切,最高实验的切削速度曾达到14000m/min, 在各种进给速度下,使用了多达20齿的螺旋铣刀。l931年 申请了“超极限速度”专利,随后卖给了“Krupp钢与工 具制造厂”。 萨洛蒙和他的研究室实际上完成了大部分有色金属的切削 试验研究,并且推断出铸铁材料和钢材的相关曲线。 萨洛蒙理论提出了一个描述切削条件的区域或者是范围, 在这个区域内是不能进行切削的。萨洛蒙没有提出可靠的 理论解释,而且他的许多实验细节也没有人知道。
刀具磨损曲线
三、高速切削切屑形成
高速切削试验表明,工件材料及 性能对切屑形态 有决定性影响。
低硬度和高热物理性能的工件材料(铝合金、低碳钢、未 淬硬钢等)易形成连续带状切屑。 高硬度和低热物理性能的工件材料(钛合金钢、未淬硬钢 等)易形成锯齿状切屑。
切削速度对切屑形态有重要影响。对钛合金,在 (1.5~4800)m/min的切削速度范围内形成锯齿状 切屑,随切削速度的增加,锯齿程度(锯齿的齿 距)在增加,直至成为分离的单元切屑。
不同切削速度下车削45钢件的切削形态。
一方面,切削速度增加,应变速度加大,导致脆 性增加,易于形成锯齿状切屑;另一方面,切削 速度增加,切屑温度增加,导致脆性降低,不易 形成锯齿状切屑;
绝热剪切理论(Adiabatic Shear Theory) 周期脆性断裂理论(Periodic brittle fracture theoty)
萨洛蒙(Salomon)曲线
1600
切削温度/℃
钢
1200
青铜
铸铁 硬质合金980℃ Stelite合金850℃ 高速钢650℃ 碳素工具钢450℃
精密加工的发展史及趋势
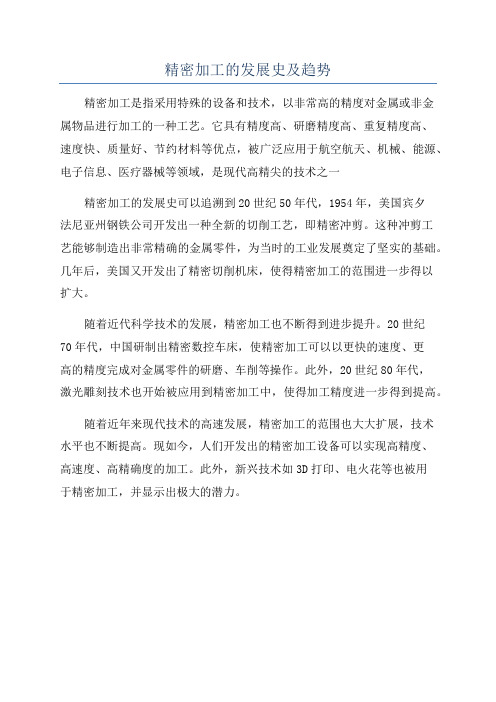
精密加工的发展史及趋势
精密加工是指采用特殊的设备和技术,以非常高的精度对金属或非金
属物品进行加工的一种工艺。
它具有精度高、研磨精度高、重复精度高、
速度快、质量好、节约材料等优点,被广泛应用于航空航天、机械、能源、电子信息、医疗器械等领域,是现代高精尖的技术之一
精密加工的发展史可以追溯到20世纪50年代,1954年,美国宾夕
法尼亚州钢铁公司开发出一种全新的切削工艺,即精密冲剪。
这种冲剪工
艺能够制造出非常精确的金属零件,为当时的工业发展奠定了坚实的基础。
几年后,美国又开发出了精密切削机床,使得精密加工的范围进一步得以
扩大。
随着近代科学技术的发展,精密加工也不断得到进步提升。
20世纪
70年代,中国研制出精密数控车床,使精密加工可以以更快的速度、更
高的精度完成对金属零件的研磨、车削等操作。
此外,20世纪80年代,
激光雕刻技术也开始被应用到精密加工中,使得加工精度进一步得到提高。
随着近年来现代技术的高速发展,精密加工的范围也大大扩展,技术
水平也不断提高。
现如今,人们开发出的精密加工设备可以实现高精度、
高速度、高精确度的加工。
此外,新兴技术如3D打印、电火花等也被用
于精密加工,并显示出极大的潜力。
切削技术发展的回顾与展望
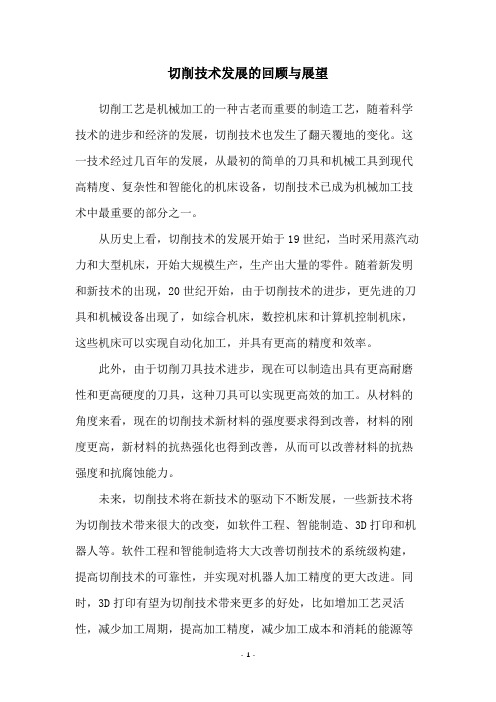
切削技术发展的回顾与展望切削工艺是机械加工的一种古老而重要的制造工艺,随着科学技术的进步和经济的发展,切削技术也发生了翻天覆地的变化。
这一技术经过几百年的发展,从最初的简单的刀具和机械工具到现代高精度、复杂性和智能化的机床设备,切削技术已成为机械加工技术中最重要的部分之一。
从历史上看,切削技术的发展开始于19世纪,当时采用蒸汽动力和大型机床,开始大规模生产,生产出大量的零件。
随着新发明和新技术的出现,20世纪开始,由于切削技术的进步,更先进的刀具和机械设备出现了,如综合机床,数控机床和计算机控制机床,这些机床可以实现自动化加工,并具有更高的精度和效率。
此外,由于切削刀具技术进步,现在可以制造出具有更高耐磨性和更高硬度的刀具,这种刀具可以实现更高效的加工。
从材料的角度来看,现在的切削技术新材料的强度要求得到改善,材料的刚度更高,新材料的抗热强化也得到改善,从而可以改善材料的抗热强度和抗腐蚀能力。
未来,切削技术将在新技术的驱动下不断发展,一些新技术将为切削技术带来很大的改变,如软件工程、智能制造、3D打印和机器人等。
软件工程和智能制造将大大改善切削技术的系统级构建,提高切削技术的可靠性,并实现对机器人加工精度的更大改进。
同时,3D打印有望为切削技术带来更多的好处,比如增加工艺灵活性,减少加工周期,提高加工精度,减少加工成本和消耗的能源等等。
另外,机器人技术将使切削技术更加智能化,有助于减少制造过程中的人为因素,提高加工效率,实现精确的制造。
总的来说,从过去的发展历程来看,切削技术取得了非常重大的发展,形成了一种完整的技术体系。
未来,切削技术将继续得到深入发展,随着新技术的推广,切削技术将会发挥更大的作用,为提高制造业的竞争力和可持续发展贡献力量。
数控加工技术的发展方向
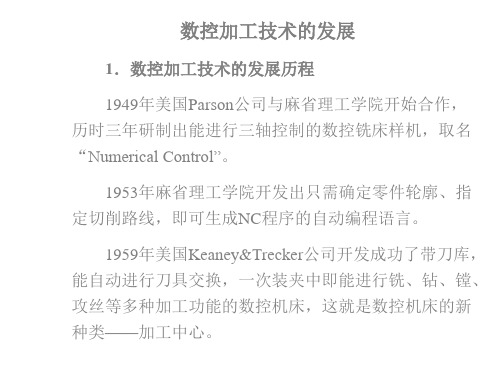
4) 高一体化
CNC系统与加工过程作为一个整体,实现机电光 声综合控制,测量造型、加工一体化,加工、实时检 测与修正一体化,机床主机设计与数控系统设计一体 化。 5) 网络化 实现多种通讯协议,既满足单机需要,又能满足 FMS(柔性制造系统)、CIMS(计算机集成制造系统)对基 层设备的要求。配置网络接口,通过Internet可实现远 程监视和控制加工,进行远程检测和诊断,使维修变 得简单。建立分布式网络化制造系统,可便于形成 “全球制造”。
代变得非常容易。充分利用现有PC机的软硬件资源,
使远程控制、远程检测诊断能够得以实现。
我国早在1958年就开始研制数控机床,但由于历史 原因,一直没有取得实质性成果。20世纪70年代初期, 曾掀起研制数控机床的热潮,但当时是采用分立元件, 性能不稳定,可靠性差。1980年北京机床研究所引进 日本FANUC5、7、3、6数控系统,上海机床研究所引 进美国GE公司的MTC-1数控系统,辽宁精密仪器厂 引进美国Bendix公司的Dynapth LTD10数控系统。在引 进、消化、吸收国外先进技术的基础上,北京机床研 究所又开发出BS03经济型数控和BS04全功能数控系统, 航天部706所研制出MNC864数控系统。“八五”期间 国家又组织近百个单位进行以发展自主版权为目标的 “数控技术攻关”,从而为数控技术产业化建立了基 础。20世纪90年代末,华中数控自主开发出基于PCNC的HNC数控系统,达到了国际先进水平,加大了我 国数控机床在国际上的竞争力度。
数控加工技术的发展
1.数控加工技术的发展历程 1949年美国Parson公司与麻省理工学院开始合作, 历时三年研制出能进行三轴控制的数控铣床样机,取名 “Numerical Control”。
1953年麻省理工学院开发出只需确定零件轮廓、指
高速切削加工

高速切削机理
•
高速切削技术的应用和发展是以高速切削机理为理论基础的。通过对高速加 工中切屑形成机理、切削力、切削热、刀具磨损、表面质量等技术的研究, 也为开发高速机床、高速加工刀具提供了理论指导。 高速切削机理的研究主要有以下几个方面: 1、高速切削过程和切削成形机理的研究对高速切削加工中切屑成形机理、 切削过程的动态模型、基本切削参数等反映切削过程原理的研究,采用科学 实验和计算机模拟仿真两种方法。 2、高速加工基本规律的研究对高速切削加工中的切削力、切削温度、刀具 磨损、刀具耐用度和加工质量等现象及加工参数对这些现象的影响规律进行 研究,提出反映其内在联系的数学模型。 3、各种材料的高速切削机理研究由于不同材料在高速切削中表现出不同的 特性,所以,要研究各种工程材料在高速切削下的切削机理,包括轻金属材 料、钢和铁、复合材料、难加工合金材料等。通过系统的实验研究和分析, 建立高速切削数据库,以便指导生产。 4、高速切削虚拟技术研究在实验研究的基础上,利用虚拟现实和防真技术, 虚拟高速加工过程中刀具和工件相对运动的作用过程,对切屑形成过程进行 动态防真,显示加工过程中的热流、相变、温度及应力分布等,预测被加工 工件的加工质量,研究切削速度、进给量、刀具和材料以及其他切削参数具 2.1涂层刀具 涂层在刀具基体上涂复硬质耐磨金属化合物薄膜以达到提高刀具表面的硬 度和耐磨性的目的。 2.2金属陶瓷刀具 金属陶瓷主要包括高耐磨性能的TiC基硬质合金(TiC+Ni或Mo)、高韧性的 TiC基硬质合金( TiC+TaC+WC)、强韧的TiN基硬质合金和高强韧性的TiCN基 硬质合金(TiCN+NbC)等。 2.3陶瓷刀具 陶瓷刀具可在υc=200m/min~1000m/min范围内切削软钢、淬硬钢和铸铁 υc=200m/min 1000m/min 等材料。 2.4CBN刀具 CBN刀具是高速精加工或半精加工淬硬钢、冷硬铸铁和高温合金等的理想 对具材料,可以实现“以车代磨”。 2.5PCD刀具 PCD刀具可实现有色金属、非金属耐磨材料的高速加工。 • 2.6性能优异的高速钢和硬质合金复杂刀具 用高性能钴高速钢、粉末冶金高速钢和硬质合金制造的齿轮刀具,可用于 齿轮的高速切削。
高速切削加工技术介绍

美国于 1960 年前后开始进行超高速切削试验。试验将刀具装在加农炮里,从滑台上射向工件;或将工件当作子弹射向固定的刀具。 1977 年美国在一台带有高频电主轴的加工中心上进行了高速切削试验,其主轴转速可以在 180 ~ 18000r / min 范围内无级变速,工作台的最大进给速度为 7 . 6m / min。
1979 年美国防卫技术研究总署( DARPA )发起了一项“先进加工研究计划”,研究切削速度比塑性波还要快的超高速切削,为快速切除金属材料提供科学依据。
在德国, 1984 年国家研究技术部组织了以 Darmstadt 工业大学的生产工程与机床研究所 PTW )为首,包括 41 家公司参加的两项联合研究计划,全面而系统地研究了超高速切削机瓜刀具、控制系统以及相关的工艺技术,分别对各种工件材料(钢、铸铁、特殊合金、铝合金、铝镶铸造合金、铜合金和纤维增强塑料等)的超高速切削性能进行了深入的研究与试验,取得了切削热的绝大部分被切屑带走国际公认的高水平研究成果,并在德国工厂广泛应用,获得了好的经济效益。日本于 20 世纪 60 年代就着手超高速切削机理的研究。日本学者发现在超高速切削时,工件基本保持冷态,其切屑要比常规切屑热得多。日本工业界 35善于吸取各国的研究成果并及时应用到新产品开发中去,尤其在高速切削机床的研究和开发方面后来居上,现已跃居世界领先地位。进人 20 世纪 90 年代以来,以松浦( Matsuora )、牧野 ( Makino )、马扎克( Mazak )和新泻铁( Niigata )等公司为代表的一批机床制造厂,陆续向市场推出不少超高速加工中心和数控铣床,日本厂商现已成为世界上超高速机床的主要提供者.
2 高速切削刀具
刀具是实现高速加工的关键技术之一。生产实践证明,阻碍切削速度提高的关键因素是刀具能否承受越来越高的切削温度在萨洛蒙高速切理研究和高速切削试验的不断深人,证明高速切削的最关键技术之一就是所用的刀具。舒尔兹教授在第一届德国 ― 法国高速切削年会( 1997 年)上做的报告中指出:目前,在高速加工技术中有两个基本的研究发展目标,一个是高速引起的刀具寿命问题,另一个是具有高精度的高速机床.
超精密切削加工

研发节能技术和设备,降低切削加工的能耗和排放,提高资源利用效率。
THANK YOU
智能化与自动化
智能切削参数优化
通过智能化技术,实现切削参数的实时优化,提高加工效率和降 低能耗。
自动化监控与补偿
利用传感器和机器视觉技术,实现切削过程的自动化监控和补偿, 提高加工精度和稳定性。
智能切削决策支持系统
开发智能切削决策支持系统,为切削加工提供科学依据和优化建议。
切削过程建模与仿真
切削力模型
清洗作用
03
切削液可以清除切屑和磨粒,防止其粘附在刀具和工件上,影
响加工精度和质量。
切削参数优化
切削深度优化
根据工件材料和加工要求,选择合适的切削深度,以实现高效、 高精度的加工效果。
切削速度优化
根据刀具材料和工件材料,选择合适的切削速度,以提高加工效 率、减小刀具磨损和防止工件热变形。
进给量优化
04
超精密切削加工的挑战与解决 方案
刀具磨损
总结词
刀具磨损是超精密切削加工中常见的问题,它会影响 加工精度和表面质量。
详细描述
在超精密切削加工过程中,刀具与工件的高速摩擦会 导致刀具磨损,进而影响切削刃的锋利度和切削深度 ,最终导致工件表面粗糙度增加或产生加工误差。为 了解决这一问题,可以采用高硬度、高耐磨性的刀具 材料,如金刚石或立方氮化硼等,以提高刀具的耐磨 性和使用寿命。此外,优化切削参数、加强刀具冷却 和润滑也是减轻刀具磨损的有效措施。
韧性决定了材料抵抗切削应力的能力。韧性较好的材料在切 削过程中不易开裂或崩刃,能够获得较好的表面质量。在超 精密切削加工中,应选择具有较好韧性的材料,以减小切削 过程中的振动和热变形。
材料热导率
高速切削技术要点及其在我国的发展趋势
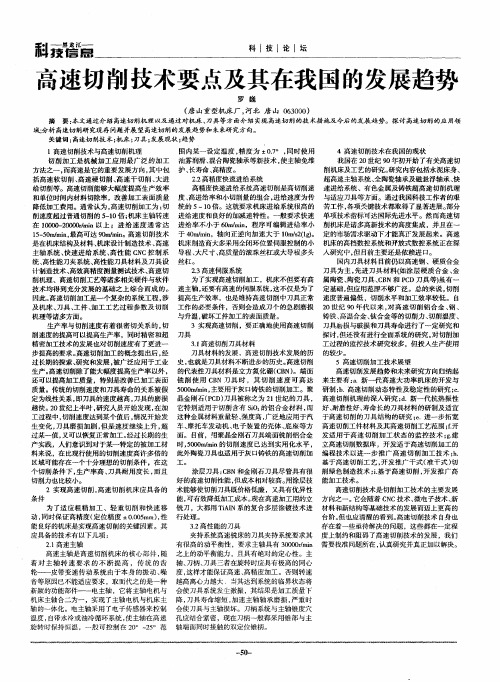
科 技论 坛 III
罗 巍
高速切 削技术要点及其在我 国的发展趋势
( 山重 型机 床 厂 , 北 唐 山 0 3 0 ) 唐 河 6 0 0
摘 要: 本文通过介 绍高速切 削机理 以及通过对机床 、 刀具等方 面介绍 实现 高速切 削的技 术措施及今后 的发展趋势 。探讨 高速切 削的应 用领 域; 高速切 削研究现存问题 并展 望高速切 削的发展趋势和未来研究方向。 分析 关键词 : 高速切削技 术; 机床 ; 刀具 ; 发展现状 ; 理 围内某一设定 温度 , 精度 为 ± . , 0 。 同时使 用 7 4 高速切削技术在我国的现状 切削加 工是机械 加工应用 最广 泛 的加 工 油雾润滑、 混合陶瓷轴承等新技术 , 使主轴免维 我国在 2 世纪 9 年初 开始 了有关 高速切 0 o 长寿命 、 高精度 。 削机床及工艺 的研究。 研究 内容包括水泥床身、 方法之一 , 而高速是它 的重要发展方向 , 其中包 护 、 括高速软切削 、 高速硬切削 、 速干切削 、 进 高 大 2 高精度快速进给系统 . 2 超高速 主轴系统 、 全陶瓷轴承及磁悬浮轴 承、 快 给切削等 。高速切削能够大幅度提高生产效 率 高精度快速进给系统高速切 削是 高切 削速 速进给系统 、有色金属 及铸铁超 高速切 削机理 和单位时间内材料切除率 ,改善 加工 表面质量 度 、 高进给率和小切削量的组合 , 进给速 度为传 与适应刀具等方面。通过我 国科技工作者 的艰 降低加工 费用 。通常认 为 , 高速切 削加工为 : 切 统的 5~1 。这就要求 机床进 给系统很高 的 苦 工作 , 0倍 各项关键技术都取得 了显著进展 。 部分 削速度超过普通切削的 5 1 倍 ; — 0 机床主轴转速 进给速度和良好的加减速特性 。一般要求快速 单项技术指标 可达 国际先进水平 。然而高速切 在 10 0 2 0 0 r n以 上 ;进给 速度 通 常 达 进给率不小于 6 mr n 00-00r i / a 0 / i,程序 可编辑进给率小 削机床是诸多高新技术 的高度集成 ,并且在一 a 1 — 0 / i, 5 5 m rn 最高可达 9 r m n 高速 切削技术 于 4 nm n a 0 d i。 t 0d i,轴 向正逆 向加速 大于 1 ms ( ) 定 的市场需求 驱动下才能真 发展起来 。高速 0/ 1 。 2 g 是 在机床结构及材料、 机床设计制造技术 、 高速 机床制造商大多采用全 闭环位置伺服控制的小 机床的高档数控 系统和开放式数控系统正在深 主轴系统 、 速进给系统 、 快 高性能 C C控制 系 导程 、 N 大尺寸 、 高质量的滚珠丝杠或大导程多头 人研究中 , 目 但 前主要还是依赖进 口。 统、 高性能刀夹系统、 高性 能刀具材料及刀具设 丝 杠 。 国内刀具材料 目 前仍 以高速钢 、硬质合金 2 高速伺服系统 - 3 计制造技术 、 高效高精度测量测试技术 、 高速切 刀具为 主 , 先进刀具 材料( 如涂层硬 质合金 、 金 削机理 、高速切 削工艺等诸多相关硬件与软件 为 了实现高速切削加工 ,机床不但要有高 属陶瓷 、 陶瓷刀具 、 B C N和 P D刀具等) C 虽有 一 技术 均得到充分发展的基础之 上综合 而成 的 。 速 主轴 , 还要有高速 的伺服系统 , 这不仅是为了 定基础 , 但应用范 围不够广泛。总的来 说 , 切削 因此 。 高速切削加工是 一个复杂 的系统工程 , 涉 提高生产效率 ,也是维持高速切削中刀具正常 速度普遍偏低 ,切削水平和加工效率较低。 自 及机 床、 刀具 、 工件 、 加工工艺 过程参数及 切削 工作 的必要条件,否则会造成刀个的急剧磨损 2 世纪 9 年代 以来 , 高速切 削铝合 金 、 、 O O 对 钢 与升温 , 破坏工件加工 的表面质量。 铸铁、 高温合金、 钛合金等的切削力 、 切削温度 、 机理等诸多方面。 生产率与切削速度有着很密切关 系的 , 切 3实现高速切削 ,要正确地使用 高速切 削 刀具 损与破损和刀具寿命进行 了一定研究 和 削速度的提高可 以提高生产率 ,同时精 密和超 刀 具 探讨 , 但还没有进行全面系统 的研究 。 对切削加 31高速切削刀具材料 . 工过程的监控技术 研究较 多,但投入生产使用 精密加工技术 的发展也对切削速度有了更 进一 步提高的要求 。 高速切削加工 的概念提出后 , 经 刀具材料的发展 ,高速切削技术发展 的历 的较少 。 也就是刀具材料不断进 步的历史 。 高速切削 5高速切 削加工技术展望 过长期的探索 、 研究和发展 , 泛应用 于工业 史 , 被广 生产。 高速切 削除了能大幅度提高生产率以外 , 的代表性 刀具材料是立方氮化硼 ( B ) C N 。端 面 高速切削发展趋势和未来研究方 向归纳起 B 还可以提高加工质量 ,特别是改善 已加工表 面 铣 削使 用 C N刀具 时 ,其 切 削 速 度 可 高达 来主要有 : 新一 代高速大功率 机床的开发与 n 0 0 / i, b 高速切削动态特性 及稳 定性的研究 ; e . 质量。传统 的切削速度和刀具 寿命 的关 系被假 50 mm n 主要用 于灰 口铸铁的切削加工 。聚 研制 ;. 定 为线性关系 , 即刀具 的速度越高 , 刀具 的磨损 晶金刚石( C 刀具被称之为 2 世 纪的刀具 , 高速切削机理的深入研究 ;. P D) 1 d 新一代 抗热振性 越 快。2 O世纪上半叶 。 研究人 员开始发 现, 在加 它特别适用 于切 削含有 S i 的铝合金 材料 , O 而 好 、 耐磨性好 、 寿命长的刀具材料的研制及适 宜 工过程 中, 切削速度达 到某个值后 , 情况开始发 这种金属材料重量 轻、 强度高 , 广泛地应用于汽 于高速切削的刀具结构 的研究 ;. 一步拓宽 e进 生 变化 , 刀具磨损加剧 , 是速度继续上 升 , 但 超 车、 摩托车发动机 、 电子装置 的壳体 、 底座 等方 高速切削工件材料及其高速切削工艺范围 ;开 £ g 建 过某一值 , 又可以恢复正常加工 。 经过 长期 的生 面。目前 ,用聚晶金刚石刀具端 面铣削铝合金 发适用 于高速切 削加工 状态 的监控技 术 ;- 产实践 ,人们意识 到对于某一特定的被加工材 时,0 0 / i 5 0 m mn的切削速度 已达到实用化水 平 , 立高速切削数据库 ,开发适于高速切 削加工的 h 料来说 ,在比现行使用的切削速度高许多倍的 此外 陶瓷刀具也适用于灰 口铸铁 的高速切 削加 编程技术 以进 一步推 广高速 切削加 工技术 ;. 区域可能存 在一个十分理想的切削条件 ,在这 工 。 基于高速切削工艺 , 发推广干式 ( 开 准干式 ) 切 涂层 刀具 :B C N和金 刚石刀具 尽管具 有很 削绿色制造技术 ;基 于高速切削 , 个切 削条 件下 , 生产率高 、 刀具 耐用度长 , 而且 j . 开发推广高 切 削 力 也 比较 小 。 好的高速切 削性能 , 但成本相对较高 。 用涂层技 能加工技术 。 2实现高速切 削 , 高速切削机床应具 备的 术能够使切 削刀具既价格 低廉,又具有优异性 高速切削技术 是切 削加工技术 的主要发展 条件 能, 可有效 降低加工成本。 现在高速加工用 的立 方 向之一。 它会随着 C C技术 、 电子技术 、 N 微 新 为 了适应 粗精加 工 、轻重 切削 和快速 移 铣刀 , 大都用 TAN系的复合多层涂镀技术进 材料 和新结构等基 础技术 的发展而迈上更高的 iI 动, 同时保证高精度 ( 位精度 ± . 5 m , 定 0 0 r )性 行 处 理 。 0 a 台阶。 但也应清醒的看到。 高速切 削技术 自身也 能 良好的机床是实现高速切 削的关键 因素 。其 3 . 2高性 能 的 刀具 存在着一些亟待解决 的问题 ,这些都在一定程 应具备的技术有以下几项 : 夹持系统高速铣床的刀具夹持系统要求其 度上制约和阻碍 了高速切削技术 的发展 ,我们 有很高的动平衡性 , 要求 主轴具 有 30 0/ i 需要找准问题所在 , 00 r n m 认真研究并真正加以解决 。 21 速 主 轴 .高 高速主轴是高速切削机床 的核心部件 , 随 之上 的动平衡能力 , 且具有绝对的定心性 。主 着对 主 轴 转 速要 求 的不 断 提 高 ,传 统 的齿 轴 、 刀柄 、 刀具三者在旋转时应具有极高的同心 轮——皮带变 速传 动系统 由于本身 的振 动 、 噪 度 , 这样才能保证高速 、 高精度加工 。否则转速 音等 原因已不能适应要求 ,取而代之的是一种 越 高离心力越大 当其达到系统的临界状态将 新颖 的功能部件—— 电主轴 ,它将主轴电机与 会使刀具系统发生 激振 ,其结果 是加工质量下 刀具寿命缩短 , 加速 主轴轴 承磨损 , 重时 严 机床 主轴合二为一 ,实现 了主轴 电机与机床主 降, 轴 的~体化。电主轴采用 了电子传感器来控制 会使 刀具与主轴损坏 。刀柄系统与主轴锥 度穴 温度 , 自带水冷或 油冷循环系统 , 使主轴在高速 孔应结合紧密,现在 刀柄一般都采用锥部 与主 旋转时保持恒温 ,一般可控制在 2 。 ~ 5 0 2 。范 轴端面同时接触 的双定位锥柄。
切削技术发展史

切削技术发展史1古代的切削加工切削加工是机械制造中最基本的加工方法之一,它在国民经济中占有重要地位.切削加工的任务是利用刀具切除被加工对象上的多余材料,从而得到形状、精度和表面质量都符合预定要求的表面.切削加工所用的工具叫刀具,刀具一般用坚硬的材料制成,并具有锋利的切削刃.现代的金属切削加工及其刀具,也是由当时具有世界领先地位的中国古代切削加工、原始带刃工具和兵器发展演变而来的.在切削加工和金属切削加工方面,我国有着悠久的历史.旧石器时代,距今约170万年的云南元谋猿人就使用过石砍砸器.距今约50~60万年的北京猿人,在与大自然搏斗的过程中,制造和使用了各种带刃的石器,如砍砸器、刮削器和尖状器。
砍砸器右部圆秃,可作砸用;左部有锋刃,可作砍用.刮削器和尖状器上则均具有明显的锋利刃部.这些古老的原始工具虽然十分粗糙,但它是一切人为加工的开始,也是研究切削加工起源和发展的宝贵历史资料.到了新石器时代,生产工具有了很大进步.石刀、石斧、石锛、石镰等都已制造得相当精致.刀体比较匀称,刃部锋利适用,有凸刃、凹刃、圆刃等.在石器上能打出圆度较高的孔,这是钻孔技术的开端.当时人类已能根据不同的加工对象和需要,制作形状和用途各异的切削工具.出土文物表明,新石器时代的人类会把坚硬的石片镶嵌在骨把上,制成了夹固式的石刃骨刀。
.石器时代的切削工具,多为石质和骨质,加工对象也多为非金属材料(如石头、木头、兽骨等).一个原始的切削加工过程,已经具备了3个基本要素:(1)刀具;(2)被加工对象;(3)切削运动.刀具的发现和切削加工的应用,在人类历史上具有十分重要的意义.历史学家认为,刀和火的发现和应用是两项伟大的发明,它是人类登上历史舞台的重要标志.春秋战国时期,我国发明了生铁冶铸造技术,比西欧要早1800年以上.渗碳、淬火和炼钢技术的发明,为制造坚硬锋利的工具提供了有利的条件.铁质工具的出现,使切削加工进入了一个新阶段.这一时期出土的切削工具,分工比较细致.许多青铜器上,出现了用金属刻镂的纹饰和钻孔的痕迹.春秋中晚期,有一部手工艺专著《考工记》,它是我国现存的一部最早的工程技术著作.其上面记载了各种兵器、生产工具和生活用品的制作规范,介绍了关于战车的制造工艺,简述了土木、金工等30个专业的技术知识.这本书指出“材美工巧”是制成良器的必要条件.所谓“材美”,是指采用优良的材质;“工巧”,是指采取合理、先进的加工工艺.由此可见,这一时期已能比较熟练地掌握各种加工方法,包括一部分切削加工。
数控机床发展史

数控机床发展史一、引言数控机床是指通过计算机控制系统,实现机床的自动化加工操作的一种高精度、高效率的机床。
它的出现彻底改变了传统机床的加工方式,极大地提高了加工精度和生产效率。
本文将从数控机床的发展历程、关键技术和应用领域等方面介绍数控机床的发展史。
二、数控机床的发展历程数控机床的发展可以追溯到20世纪40年代,当时以美国为代表的工业发达国家开始研究数控技术。
1947年,美国麻省理工学院的数学家维茨尔(W.H.Witzel)提出了数控机床的概念,并设计出第一台数控铣床。
此后,数控技术得到了迅速发展,出现了一系列划时代的技术突破。
1952年,美国麻省理工学院的尤金·W·伯里(Eugene W.Berry)教授成功开发出世界上第一台数控车床。
此后,数控机床开始广泛应用于航空航天、军工、汽车等领域,并逐渐取代了传统机床。
1960年代,计算机技术的飞速发展为数控机床的进一步发展提供了坚实的基础。
计算机数控(CNC)系统的出现,使得数控机床的编程更加灵活方便,加工精度也得到了大幅提高。
此后,数控机床的发展进入了一个新的阶段。
1980年代,随着微电子技术和信息技术的不断进步,数控机床的性能得到了大幅提升。
高速切削技术、高精度测量技术等先进技术的应用,使得数控机床在加工效率和加工精度上达到了前所未有的水平。
到了21世纪,数控机床的发展进入了智能化阶段。
人工智能、云计算、大数据等技术的应用,使得数控机床具备了更高的自动化程度和智能化水平。
现如今,数控机床已经成为工业制造中不可或缺的设备。
三、数控机床的关键技术数控机床的发展离不开一系列关键技术的突破。
首先是数控系统技术,包括硬件和软件两个方面。
硬件方面,数控系统需要具备高性能的计算机、精密的运动控制装置和灵敏的传感器等。
软件方面,数控系统需要具备强大的编程和控制功能,能够实现复杂的加工操作。
其次是伺服控制技术,伺服系统是数控机床实现高精度加工的关键。
中国机床发展史
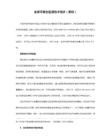
现代化的重要标志,代表着一个国家的科学水平、创新能力和综合能力,中国要成为
”
中国机床工具行业一直在党和国家领导人的关爱中不断发展壮大。如今,中国数控机床的
2000余种。通过突破国外多年的技术封锁,相继开发出国民经济急需且具有自
11m的数控龙门镗铣床;加工直径
的数控立车;加工直径20m、22m超重型数控立车;φ5m×20m加工件重500吨超重型
25m和28m的超重型数控立车和加工直径达6.3m的超重型数控卧
260吨、φ5m×14.5m的大型船用柴油机曲轴旋风切
φ2.5m×15m,承重150吨数控轧辊磨床;加工直径达8m的数
年周恩来总理在访问前苏联时指示,国家进口的各类机床11115台,首先用在机床
1952年
国家决定在第一机械工业部设立第二机器工业管理局,成为全国机床工具行业的统一领
当时,在前苏联的援助下,改造和新建18个机床厂和四个工具厂,
“十八罗汉、四大金刚”,形成了行业的骨干。在国民经济恢
30个品种,24500余台机床。
累计出口83.1亿美元,其中金切机床23.4亿美元、数控机床4.98亿美元。2005年我
45.7万台,其中金切数控机床5.96万台,分别是2000年的2.55倍和
倍。2005年产品销售收入1212.46亿元,是2001年销售收入578.74亿元的2.1倍。2005
29.95亿美元,其中数控机床2.31亿美元。
0.0015mm.
四是功能部件、数控系统、刃量具等方面产品研发。已经制造了三自由度并联主轴头,主
±40°行程达345mm,主轴快速移动速度50m/min,加速度1g,转速24000r/min,主轴功率
金属切削加工技术论文

金属切削加工技术探析据统计,在国民生产总值中相当多的产业与机械制造技术密切相关。
在大多数情况下,切削加工仍是能耗小、效益高的加工方法。
虽然也有一些特殊加工技术,如电加工、激光加工、超声加工等,但90%以上的机械加工是由切削加工完成的。
本文现从以下几方面分析金属切削技术的发展趋势。
一、金属切削加工自动化技术的发展伴随着微电子与信息技术的发展,cad、capp、cam、cae、mrpii 等关键技术为迅速提高制造工程领域的管理水平、显著降低制造过程中的大量辅助工时、推动设计制造一体化及产品质量提高等起到巨大的作用。
同时,这些技术也给传统的金属切削理论与技术提出了新的要求与发展方向。
推动了它在柔性自动化生产条件下的发展和进步,其中较重要的发展领域和技术成果有:1、切削数据库与工艺数据库。
微机辅助数据库技术迅速发展,克服了过去全靠人的经验或查阅手册来获得切削技术数据的困难,补充了在信息量、获取信息速度和信息准确性等方面的不足,为capp、cam、cims等奠定了坚实的基础。
2、切削技术专家系统。
人工智能技术在金属切削领域的应用,产生了切削技术专家系统,它为解决切割技术中的若干决策、咨询、诊断、管理等问题提供了有效的工具。
3、切削用量和工艺过程优化。
传统的优化理论多以单刀,单工序,单目标,单参数的优化为主,而在现代化加工系统中,大量的优化工作需要在多刀、多工序、多优化目标、多优化参数等条件下进行,这就是相应的优化理论与技术的进步。
4、刀具寿命及其可靠性。
在现代自动化加工系统中,由于设备昂贵、自动化程度和灵活性要求高,对刀具提出了一系列新要求,如:刀具的切削速度高,以便充分利用设备的效率,弥补其昂贵的缺陷,刀具通用性好,耐用度,以避免频繁换刀,刀具几何状态和切削性能一致性好,可靠性高,以保证整个自动加工过程的可操作性和稳定性。
因此,对刀具材料与结构提出了新的要求。
5、切削过程检测与监控。
在制造系统无人管理的情况下,对切削工程的各种状态和各种故障应有完善的检测和监控系统,以便及时报警,停机或自适应调节,有效的减少废品率,降低加工成本。
数控加工工艺
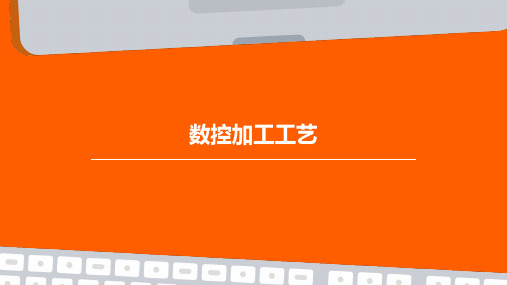
切削用量的优化
01
切削深度与宽度
切削深度与宽度是影响切削用 量的重要因素。在保证加工质 量和刀具寿命的前提下,合理 增大切削深度与宽度可以提高 加工效率。
02
切削路径规划
合理的切削路径规划可以减少 空行程时间和提高材料去除率 ,进而优化切削用量。常用的 切削路径规划方法包括往复式 切削、螺旋式切削等。
03
冷却与润滑
04
切削过程中的冷却与润滑对切削 用量也有影响。合适的冷却润滑 方式可以减小切削力、降低刀具 磨损,并提高加工表面的质量。
工艺系统刚性
工艺系统的刚性对切削用量有较 大影响。在切削过程中,如果工 艺系统刚性不足,可能会导致振 动、过切等问题,影响加工质量 。因此,在选择切削用量时,需 充分考虑工艺系统的刚性。
数控加工的重要性
提高加工精度和效率
促进制造业转型升级
数控加工可以实现高精度和高效率的 加工,提高生产效率和产品质量。
数控加工技术的应用可以推动传统制 造业的转型升级,提高制造业的技术 水平和市场竞争力。
适应个性化生产需求
数控加工可以快速调整工艺参数和加 工过程,适应个性化生产需求,缩短 产品研发周期。
螺纹车削
切槽加工
用于加工各种螺纹,通过调整刀具的角度 和切削参数,实现高质量螺纹车削。
用于在轴类零件上加工各种槽形,通过选 择合适的刀具和切削参数,实现高效切槽 加工。
线切割加工工艺
快走丝线切割
采用快速往复运动的电极丝进行切割,适用于加 工厚度较大的工件。
大锥度线切割
适用于加工大锥度或非圆形工件,能够实现复杂 形状的切割。
质量控制
建立严格的质量控制体系,对加工过 程进行实时监测和记录,确保产品质 量的稳定性和可靠性。
高速切削加工技术及应用论文

浅谈高速切削加工技术及应用摘要:高速切削(high speed cutting,hsc)是近年来迅速崛起的一项先进制造技术。
本文就高速切削加工技术的发展、特点、关键技术及其应用作一简要的研究与阐述。
关键词:高速切削加工;技术;研究;应用中图分类号:tg659 文献标识码:a 文章编号:1006-3315(2011)11-175-0011931年4月德国物理学家carl.j.saloman最早提出了高速切削(high speed cutting)的理论,并于同年申请了专利。
他指出:在常规切削速度范围内,切削温度随着切削速度的提高而升高,但切削速度提高到一定值之后,切削温度不但不会升高反而会降低,且该切削速度vc与工件材料的种类有关。
对于每一种工件材料都存在一个速度范围,在该速度范围内,由于切削温度过高,刀具材料无法承受,切削加工不可能进行。
要是能越过这个速度范围,高速切削将成为可能,从而大幅度地提高生产效率。
由于实验条件的限制,当时高速切削无法付诸实践,但这个思想给后人一个非常重要的启示。
一、高速切削加工概述1.高速切削历史和现状高速切削的起源可追溯到20世纪20年代末期。
德国的切削物理学家萨洛蒙博士于1929年进行了超高速切削模拟试验。
1931年4月发表了著名的超高速切削理论,提出了高速切削假设。
我国早在20世纪50年代就开始研究高速切削,但由于各种条件限制,进展缓慢。
近10年来成果显著,至今仍有多所大学、研究所开展了高速加工技术及设备的研究。
2.切削速度的划分根据高速切削机理的研究结果,高速切削不仅可以大幅度提高单位时间材料切除率,而且还会带来一系列的其他优良特性。
高速切削的速度范围定义在这样一个给切削加工带来一系列优点的区域。
这个切削速度区比传统的切削速度高得多,因此也称超高速切削。
通常把切削速度比常规高出5~10倍以上的切削加工叫做高速切削或超高速切削。
3.高速切削的优势高速切削具有以下特点:①可提高生产效率;②降低了切削力;③提高加工质量;④高速切削的切削热对工件的影响小;⑤加工能耗低,节省制造资源;⑥高速切削可以加工难加工材料;⑦简化了加工工艺流程;⑧可降低加工成本。