汽车尺寸工程 -尺寸工程公差设计流程
汽车车身冲压件尺寸工程尺寸质量接收和监控
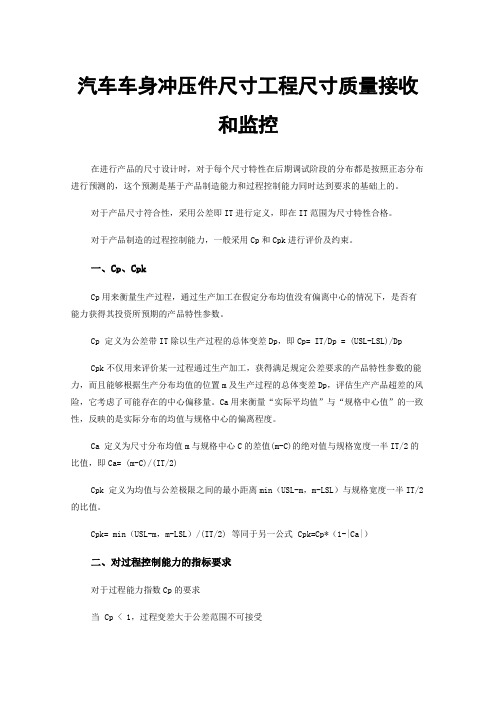
汽车车身冲压件尺寸工程尺寸质量接收和监控在进行产品的尺寸设计时,对于每个尺寸特性在后期调试阶段的分布都是按照正态分布进行预测的,这个预测是基于产品制造能力和过程控制能力同时达到要求的基础上的。
对于产品尺寸符合性,采用公差即IT进行定义,即在IT范围为尺寸特性合格。
对于产品制造的过程控制能力,一般采用Cp和Cpk进行评价及约束。
一、Cp、CpkCp用来衡量生产过程,通过生产加工在假定分布均值没有偏离中心的情况下,是否有能力获得其投资所预期的产品特性参数。
Cp定义为公差带IT除以生产过程的总体变差Dp,即Cp= IT/Dp = (USL-LSL)/DpCpk不仅用来评价某一过程通过生产加工,获得满足规定公差要求的产品特性参数的能力,而且能够根据生产分布均值的位置m及生产过程的总体变差Dp,评估生产产品超差的风险,它考虑了可能存在的中心偏移量。
Ca用来衡量“实际平均值”与“规格中心值”的一致性,反映的是实际分布的均值与规格中心的偏离程度。
Ca 定义为尺寸分布均值m与规格中心C的差值(m-C)的绝对值与规格宽度一半IT/2的比值,即Ca= (m-C)/(IT/2)Cpk 定义为均值与公差极限之间的最小距离min(USL-m,m-LSL)与规格宽度一半IT/2的比值。
Cpk= min(USL-m,m-LSL)/(IT/2)等同于另一公式Cpk=Cp*(1-|Ca|)二、对过程控制能力的指标要求对于过程能力指数Cp的要求当Cp < 1,过程变差大于公差范围不可接受当 Cp = 1 时,过程有产生不合格品的风险,且不能再遭受任何中心偏离Cp越大,产生超差尺寸的风险越小,对中心偏移带来的超差防范能力也就越强。
对于考虑中心偏移的过程能力指数Cpk的要求如果 Cpk < 1,过程的变差大于公差或其偏差不可接受Cpk = 0 表明均值位于公差上限或下限Cpk 为负值表明过程的均值位于公差上下限之外当 Cpk = 1,过程有生产不合格品的风险,且不允许有任何偏离均值中心发生。
汽车研发常用专业术语详细汇总与解释!

汽车研发常⽤专业术语详细汇总与解释!汽车研发过程中,有⼤量的专业术语,每个术语都有其特殊的含义,且不同的主机⼚还有不同的叫法!今天漫谈君全⾯总结了⼀版汽车研发常⽤专业术语和⼤家⼀起交流学习⼀、研发阶段1、商品计划阶段1)完成项⽬前期研究,管理层评审预研阶段定义的所有初期⽬标、评审并批准市场分析、技术⽅案、造型⽅向、资源获得⽅案、项⽬综合可⾏性分析、正式启动项⽬。
2)批准初步项⽬⽅案,包括所有的产品⽬标和商业计划⽬标的最初符合性,⼯程/制造/物流/采购等项⽬⽅案。
为项⽬批准做准备。
3)综合评审产品开发状态,包括造型冻结,对产品、制造、物流和销售计划进⾏评审和批准,所有的⽬标在项⽬的经济架构中都必须是可⾏的,正式批准项⽬。
2、产品开发阶段1)通过对数模的⼯程可⾏性确认和pertest试验,通过CAE和制造可⾏性分析,完成整车数据发放。
2)对设计样车进⾏相关验证试验,检查评估产品设计及⼯艺的正确性。
完成试⽣产准备。
3、量产准备阶段1)使⽤⼯装零件按⼯艺要求在总装线上制造样车,验证⼯装模具和供应商的制造能⼒,完成⼯程的最终验证和制造的早期⼯艺调试。
2)调试整车⼚的⽣产设备,验证⽣产⼯艺,验证全⼯装和⼯艺条下件批量提供的零部件质量,完成样车数据更改,冻结变更数据。
3)验证整车⼚在⼀定节拍下的⽣产能⼒。
4)按整车⽣产节拍的提升计划,投⼊批量⽣产。
4、量产维持阶段1)新产品预研⽴项GATE#0(KO)项⽬⽴项研究。
成⽴项⽬团队,开始对项⽬进⾏研究分析。
2)预可研评审(SI)完成产品初步可⾏性分析后,通过预可研评审确定开发平台。
3)产品开发决策(SC)进⼀步细化产品⽅案,通过评审后,初步确定项⽬开发⽬标。
4)新产品开发项⽬认可GATE#1(OD)完成各项性能指标的细化,形成产品的最终设计⽅案和⽬标并获得批准。
5)设计数据发布(DR)⾸轮设计数据经过评审确认后,进⾏发布⽤于相关部门的设计样车制作。
6)设计样车验证完成(CP)对设计样车进⾏相关试验验证,检查及评审产品设计和⼯艺的正确性。
汽车尺寸工程 -DTS断面介绍
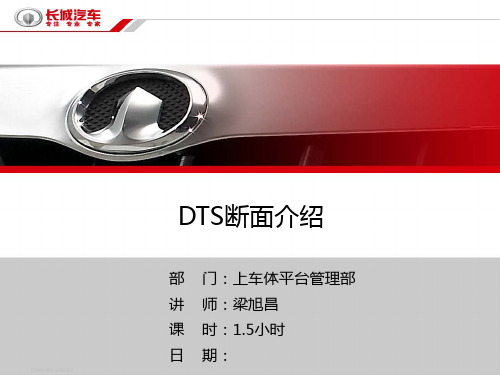
GWM-PPT V2012.2
17
汇报人:×××
GWM-PPT V2012.2
18
GWM-PPT V2012.2
12
针对DTS断面间隙段差定义方式存在分歧的几类断 面,现统一定义方式如下:
1、翻边与翻边
a、以最靠内侧的圆弧起点到配合件的最小距离为间隙
b、对于内饰件夹角较大的位置,尤其是软质仪表板, 可特殊处理,定义分型线端点到另一件的最小距离为 间隙
GWM-PPT V2012.2
GWM-PPT V2012.2
DTS断面介绍
部 门:上车体平台管理部 讲 师:梁旭昌 课 时:1.5小时 日 期:
目录
1 DTS 断面介绍
2 DTS 断面设计主要内容
3 DTS 断面定义主要存在的问题
4
DTS 断面统一测量方式
GWM-PPT V2012.2
2
DTS断面介绍
1、DTS断面的定义
DTS断面能够表达结构配合关系、用来指导结构设计工作的二维图样。
前保与中网
GWM-PPT 度不同会出现不同的测量值
尾灯与背门
4、后门外板与水切,间隙段差的测量位置模糊
GWM-PPT V2012.2
7
5、三个件的间隙段差如何定义测量,彼此都有间隙段差, 特别是下护板,按照倒角后的制作方案,下护板的边界在拐 角处会很扭曲。
GWM-PPT V2012.2
6、玻璃与周圈件(前风挡玻璃与侧围,前风挡玻璃与 顶盖,侧门玻璃与窗框,后风挡玻璃与侧围),侧围与 背门,侧围与门框这类的断面,分别以玻璃,背门,门 框为基准,根据具体情况以被测件到基准件主面切线延 长线的垂直距离为段差
GWM-PPT V2012.2
汽车开发流程1
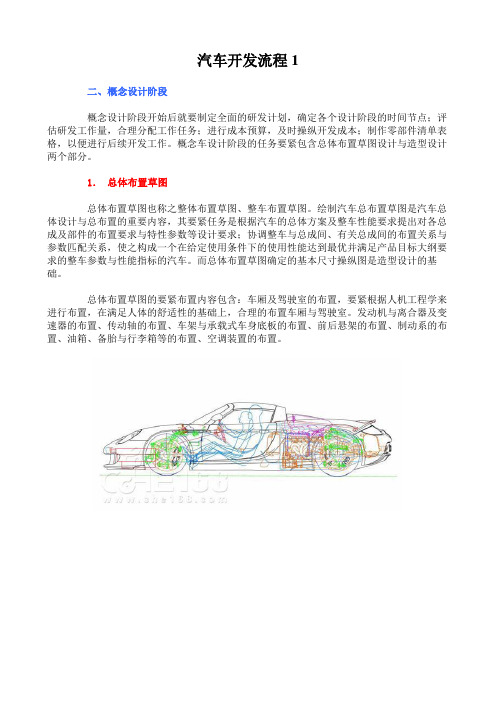
汽车开发流程1二、概念设计阶段概念设计阶段开始后就要制定全面的研发计划,确定各个设计阶段的时间节点;评估研发工作量,合理分配工作任务;进行成本预算,及时操纵开发成本;制作零部件清单表格,以便进行后续开发工作。
概念车设计阶段的任务要紧包含总体布置草图设计与造型设计两个部分。
1.总体布置草图总体布置草图也称之整体布置草图、整车布置草图。
绘制汽车总布置草图是汽车总体设计与总布置的重要内容,其要紧任务是根据汽车的总体方案及整车性能要求提出对各总成及部件的布置要求与特性参数等设计要求;协调整车与总成间、有关总成间的布置关系与参数匹配关系,使之构成一个在给定使用条件下的使用性能达到最优并满足产品目标大纲要求的整车参数与性能指标的汽车。
而总体布置草图确定的基本尺寸操纵图是造型设计的基础。
总体布置草图的要紧布置内容包含:车厢及驾驶室的布置,要紧根据人机工程学来进行布置,在满足人体的舒适性的基础上,合理的布置车厢与驾驶室。
发动机与离合器及变速器的布置、传动轴的布置、车架与承载式车身底板的布置、前后悬架的布置、制动系的布置、油箱、备胎与行李箱等的布置、空调装置的布置。
测量得到的点云数据某轿车白车身侧围部分设计图5.底盘工程设计底盘工程设计的内容就是对底盘的4大系统进行全面的设计,包含:传动系统设计、行驶系统设计、转向系统设计与制动系统设计。
要紧工作包含:(1)对各个系统零部件进行包含尺寸、结构、工艺、功能与参数等方面的定义(2)根据定义进行结构设计与计算,完成3维数模(3)零部件样件试验(4)完成设计图与装配图其中传动系统的要紧设计内容为离合器、变速器、驱动桥,行驶系统的要紧设计内容为悬架设计,转向系统的要紧设计内容为转向器与转向传动机构的设计,制动系统的设计内容包含制动器与ABS的设计。
底盘部分系统3维设计图国内某汽车企业试验场在奇瑞,一个全新的车型的开发,通常有10个节点,P0到P9,通常要45个月。
P0阶段:立项建议书。
工程图纸尺寸大全
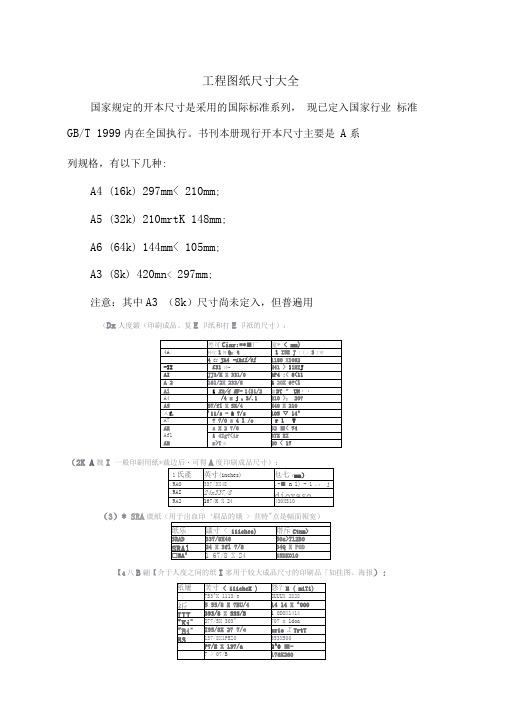
工程图纸尺寸大全国家规定的开本尺寸是采用的国际标准系列,现已定入国家行业标准GB/T 1999内在全国执行。
书刊本册现行开本尺寸主要是A系列规格,有以下几种:A4 (16k) 297mm< 210mm;A5 (32k) 210mrtK 148mm;A6 (64k) 144mm< 105mm;A3 (8k) 420mn< 297mm;注意:其中A3 (8k)尺寸尚未定入,但普遍用(Dx人度鍛(印刷成品、复E卩纸和打E卩祇的尺寸):(2K A魏I 一般印刷用紙*裁边后・可得A度印刷成品尺寸):(3)* SRA虞紙(用于出血印‘刷品的娥 > 苴特"点是幅面報宽)【4八B翩【介于人度之间的纸I寥用于较大成品尺寸的印刷品「如挂图、海报):我们日常生活中说说的A4复印纸,8K纸就是指这些尺寸,即A4纸(16K纸)的尺寸为:297mm< 210mm, 32K笔记本(A5笔记本)规格为:21cm xi4.8cm。
纸张尺寸介绍:a2纸的尺寸(大4开)594mm< 420mma3 纸尺寸(大8 开)420mn< 297mma4 纸尺寸(大16 开)297mm<210mmb4纸尺寸(16开)b5纸的尺寸(32开)8开纸尺寸纸张按种类可分为新闻纸、凸版印刷纸、胶版纸、有光铜版纸、哑粉纸、字典纸、地图纸、凹版印刷纸、周报纸、画报纸、白板纸、书面纸、特种纸等。
普通纸张按克重可分为60gsm、80gsm、100gsm 105gsm> 120gsm、157gsm 200gsm 250gsm> 300gsm 350gsm> 400gsm。
8开就是8开的,尺寸是390X270mm,要是word里面没有,那就自行设定。
全开,载成8张,你量一下.纸张的规格是指纸张制成后,经过修整切边,裁成一定的尺寸。
过去是以多少"开"(例如8开或16开等)来表示纸张的大小,现在我采用国际标准,规定以AO、A1、A2、B1、B2……等标记来表示纸张的幅面规格。
汽车工程学-图文-1-7 汽车总体布置
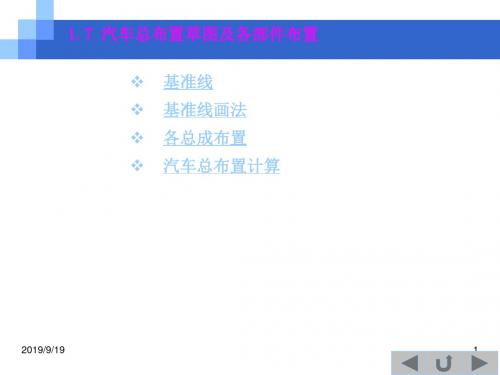
A”
a
向前为“-”, 向后为“+” ;0x
O1 Rr1 地面线Ⅰ
汽车中心线:横向尺寸的基准线。
A
向右为“-”, 向左为“+” 。0y
L
地面线:标注车高、货台高度、接
B’
B”
b
O2 Rr2
B
近角、离去角和离地间隙的尺寸的基准线
前轮垂直线:标注汽车轴距和前悬的基准线,当车架与地面平行时,
前轮垂直线与前轮中心线重合,如乘用车。
2019/9/19
2
0号图纸尺寸: 841*1189 一般加长不加宽 主视图:汽车行驶的侧面 俯视图:汽车顶盖 左视图:汽车车头(可以从对称面分别画汽车前后视图) 右视图:汽车尾部 网格线:400mm一格,用4X,8X,12X,16X……表示.
②总布置图格式
2019/9/19
4
2019/9/19
1.7 汽车总布置草图及各部件布置
基准线 基准线画法 各总成布置 汽车总布置计算
2019/9/19
1
基准线
车架上平面线:垂直方向尺寸的基
准线。向上为“+”, 向下为“-”;
O
但当车架上表面是复杂面时,也可
Ⅴ 前轮垂直线Ⅱ
以用车身地板主平面作基准线;0z
前轮中心线:纵向尺寸的基准线。 Ⅳ A’
5
2019/9/19
6
2019/9/19
7
2019/9/19
8
2019/9/19
9
室布置 货厢布置 客厢布置
制动系布置 转向系布置 悬架布置 其他总成布置 空调布置
2019/9/19
10
1.发动机布置
汽车总布置尺寸

汽车总布置尺寸——SAE J1100 JUN93 SAE推荐实施本报告在1973年9月由人体工程委员会核准,1984年6月修订,在1993年6月由人体放置和设计装置标准委员会全面修订目录1.范围2.参考3.概述4.基准标记尺寸5.内部尺寸5.1 前排座椅空间尺寸5.2 第二座椅空间尺寸5.3 卡车卧铺空间尺寸5.4第三座椅空间尺寸5.5座椅入口和出口尺寸5.6视野和控制尺寸6.外部尺寸6.1 外宽尺寸6.2 外高尺寸6.3 长度尺寸6.4 离地间隙尺寸7.货箱尺寸8.行李厢容积9.货箱容积目录10.ISO货箱容积11.车窗面积12.踏板13.H点设计移动轨迹14.尺寸数值索引15.尺寸字母索引16. 注释1.适用范围——本SAE推荐实施标准定义了一系列关于客车,多用途车,货车的一些统一的内部和外部尺寸。
2.参考2.1 参考文档——下面的刊物在本文特定范围内组成了部分的文档规范,应采用最新的SAE规范文档。
2.1.1 SAE刊物——Available from SAE,400 CommonweathDrive,Warrendle.PA 15096-0001.SAE J182——汽车基准标记SAE J826——用于定义和测量汽车座椅放置的装置SAE J941——汽车驾驶员眼点范围SAE J1052——汽车驾驶员和乘员头部位置SAE E-72.2 术语定义2.2.1汽车——根据车辆使用定义和内部座椅数量分类。
2.2.1.1客车——载客10人以下的带动力的机动车,不包括多用途客车,摩托车,挂车。
2.2.1.1.1旅行车——有较大的空间,上面可携带货物及载客车。
2.2.1.1.2后背门式汽车—倒车灯间有尾部检修门的客车。
2.2.1.2多用途客车(MPV)——载客10人以下,带动力,一般采用卡车底盘并具有一定越野性能的机动车,不包括挂车。
2.2.1.3卡车——带动力,主要用于运输货物和专用设备的车辆。
2.2.1.3.1轻型卡车——主要用于运输货物和专用设备的机动车,汽车总重率(GVWR)不大于4536kg(10000lb), GVWR是由生产厂家给出的单车装载重量值。
汽车整车开发流程图
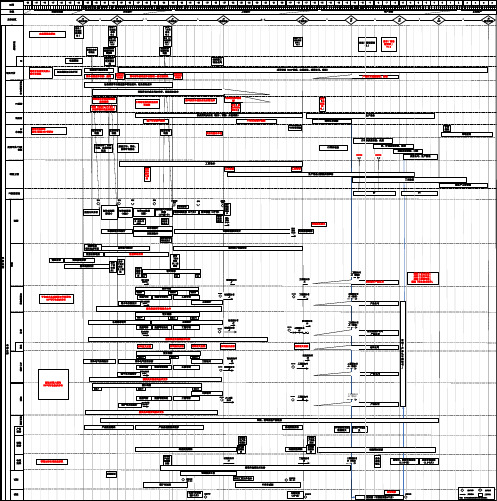
发 动 机 系 统
设计审查
平台动力总成选型可行性研究 USP可行性初步分析 骡子车方案设计
造型可研
骡子车试制通 知书JT
造型可研细化
工程可研 工程设计
试制通知书 JT
设计审查
工程通知书 JE
工程通知书 JE(修改)
产品认可
提供供应商咨询技术文件 设计构想
编制JP1 编制JP2 编制JP3
产品认可进度管控、协调
成 本 分 析 平 台
协助项目平台制定整车目标成本、组块目标成本 零部件设计成本同步分析、目标成本发布 造型相关长周期制造供 应商选择 底盘(含骡子车开发)/ 关键零部件供应商选择 冲压件供应商选 择
发布「底 盘件采购 通知书」 发布
PV采购
中周期零部件制造供应 商选择
除冲压件外的其余供应商选择
「采
购通 知 书」
供应商同步开发(设计、试制、开发试验) 供应商 骡子车零部件试制 FT样车零部件试制 PCC市场调查 配合市场 调查 配合市场 调查 配合市场 调查 商业化新车命名 零件认可试验
生产准备
PV 市场部
销售目标市场 量价/配置/USP等研讨
价格 提案 市场宣传 白车身质量检验、改进
质量平台/PV质 量部
产品认可
提供供应商咨询技术文件 新技术导入研究 USP可行性初步分析
编制JP1
设计构想
编制JP2 编制JP3
工程设计 底 盘 骡子车方案设计 造型可研
骡子车试制 通知书JT
造型可研细化
工程可研
设计审查
JT/JE通 知书
设计审查
工程通知书 JE
工程通知书 JE(修改)
汽车整车开发流程
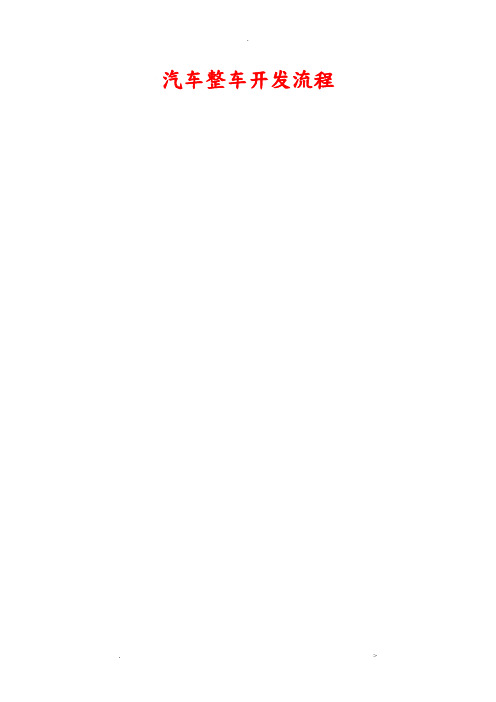
汽车整车开发流程目录一、方案筹划阶段1二、概念设计阶段11.总体布置草图12.造型设计2三、工程设计阶段31.总布置设计32.车身造型数据生成43.发动机工程设计44.白车身工程设计45.底盘工程设计46.外饰工程设计57.电器工程设计5四、样车试验阶段5五、投产启动阶段6六、国自主品牌6本文主要向大家介绍汽车研发中的核心流程,也就是专业的汽车设计开发流程,这一流程的起点为工程立项,终点为量产启动,主要包括5个阶段:一、方案筹划阶段一个全新车型的开发需要几亿甚至十几亿的大量资金投入,投资风险非常大,如果不经过周密调查研究与论证,就草率上马新工程,轻则会造成产品先天缺乏,投产后问题成堆;重则造成产品不符合消费者需求,没有市场竞争力。
因此市场调研和工程可行性分析就成为了新工程至关重要的局部。
通过市场调研对相关的市场信息进展系统的收集、整理、纪录和分析,可以了解和掌握消费者的汽车消费趋势、消费偏好和消费要求的变化,确定顾客对新的汽车产品是否有需求,或者是否有潜在的需求等待开发,然后根据调研数据进展分析研究,总结出科学可靠的市场调研报告,为企业决策者的新车型研发工程方案,提供科学合理的参考与建议。
汽车市场调研包括市场细分、目标市场选择、产品定位等几个方面。
工程可行性分析是在市场调研的根底上进展的,根据市场调研报告生成工程建议书,进一步明确汽车形式〔也就是车型确定是微型车还是中高级车〕以及市场目标。
可行性分析包括外部的政策法规分析、以及部的自身资源和研发能力的分析,包括设计、工艺、生产以及本钱等方面的容。
在完成可行性分析后,就可以对新车型的设计目标进展初步的设定,设定的容包括车辆形式、动力参数、底盘各个总成要求、车身形式及强度要求等。
将初步设定的要求发放给相应的设计部门,各部门确认各个总成部件要求的可行性以后,确认工程设计目标,编制最初版本的产品技术描述说明书,将新车型的一些重要参数和使用性能确定下来。
在方案筹划阶段还有确定新车型是否开发相应的变形车,确定变形车的形式以及种类。
2mm工程在白车身尺寸控制中的应用

工程与技术2mm工程在白车身尺寸控制中的应用王刚毅(上汽通用汽车有限公司,上海201206)摘要:2mm质量工程控制方法目前被广泛应用于汽车制造行业,用以控制白车身的制造质量d2m m工程 已经成为衡量汽车制造企业在尺寸控制方面能否达到国际先进水平的衡量指标。
主要介绍白车身尺寸波动的来 源、白车身尺寸控制方法、2mm质量工程控制原理等。
关键词:白车身;尺寸控制;2m m工程中图分类号:TB文献标识码:A doi:10. 19311/j,cnki. 1672-3198. 2016. 30. 0991前言车身是整个汽车零部件的载体,它的制造质量直接影响到整车的风噪性、密封性、美观性等,所以标准 要求非常严格因此20世纪90年代初,由美国密歇 根大学吴贤铭先进制造技术中心倡导、美国政府支持、三大汽车公司(GM、Ford、Chrysler)共同推动了车身2mm工程,目的就是提高车身尺寸的稳定性,减小尺寸 偏差,提高白车身质量。
2车身制造过程的不稳定因素车身制造偏差的定义:制造的车身尺寸实际值与理论值的差值。
车身尺寸不稳定的因素:(1)工装本身使用状态的 变化导致不稳定I工装结构由基准平台、立柱、气缸臂、控制系统等构成,有些工装还包括冲孔机构、钻孔机 构。
经过长时间使用工装的结构状态会逐渐发生变化,变化累积到一定程度会影响定位的精度、零件匹配。
(2》工装上设备故障、机构磨损:工装上控制机构如感应器等失效,冲孔机构故障,钻孔机构磨损等都会 导致不稳定。
(3)供应商来料变化:整车厂许多零件、分总成件由多家供应商供货,有些来料的质量稳定性 较差,尺寸偏差将直接影响车身整体尺寸u(4)制造1艺缺陷:车身生产工艺包括焊接、冲孔、钻孔、安装、涂 胶、折边等,有些环节的工艺无法完全保证产品质董的 高稳定性。
(5)工艺变化:零件国产化、工程更改等使零件状态发生变化导致尺寸数据波动。
3车身制造尺寸质量控制方法3.1过程控制的方法对于任何一+工艺过程一般可以用两种典型的方法对过程进行有效地监控,即工程过程控制和统计过程控制s工程过程控制(EPC)是指对于一个系统检测 量,它有一个明确并且恒定的控制界限,当检测量超出 该控制界限时系统即可报警。
1.3 现代汽车车身开发流程与设计方法

(6) 生产准备
生产准备主要完成制造确认和批量生产确认工作。经过几轮产品试制和试验 后,设计最终冻结,产品的生产准备开始全面启动。
第1章 车身概论
1.3 现代汽车车身开发流程与设计方法
实际上,不同车身的开发流程并不是完全相同的,那么有什么差异呢?下面通过案例进 行分析比较。
案例分析
资料表明,目前国内汽车主机厂都建有统一数据库,并大量采用计算机和网络技术,但 由于开发条件的局限性,车身设计开发主要偏重于制造规划的同步工程,车身成本、质 量等关键控制点要等到车身设计数据完全冻结后再进行控制。
一旦车身成本和质量超过预定要求,很可能要把已冻结的设计推翻,返回概念设 计从头开始,造成开发周期延长。
第1章 车身概论
1.3 现代汽车车身开发流程与设计方法
业务流程再造(BPR)后的车身开发流程
市场调研
车身概念 设计
制造同步 工程目标
设计
车身成本 设计
车身质量 设计
车身结构 设计
制造同步 工程控制
优化设计在车身上的应用详见第7章。
第1章 车身概论
1.3 现代汽车车身开发流程与设计方法
任何新车型的开发或改型设计,其车身都要重新设计,而车身设计又是 决定车型开发成败的关键因素之一。因此,汽车制造公司都非常重视车身设 计,不断扩大设计队伍,增加资金投入,充分应用先进的设计技术和手段。
汽车设计流程
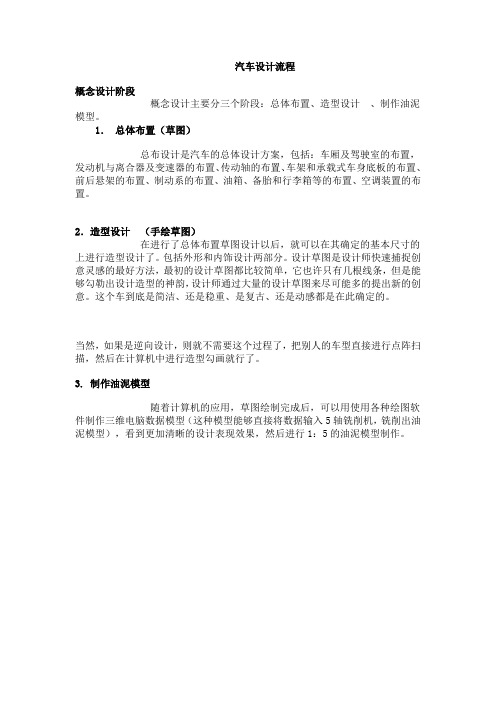
汽车设计流程概念设计阶段概念设计主要分三个阶段:总体布置、造型设计、制作油泥模型。
1.总体布置(草图)总布设计是汽车的总体设计方案,包括:车厢及驾驶室的布置,发动机与离合器及变速器的布置、传动轴的布置、车架和承载式车身底板的布置、前后悬架的布置、制动系的布置、油箱、备胎和行李箱等的布置、空调装置的布置。
2.造型设计(手绘草图)在进行了总体布置草图设计以后,就可以在其确定的基本尺寸的上进行造型设计了。
包括外形和内饰设计两部分。
设计草图是设计师快速捕捉创意灵感的最好方法,最初的设计草图都比较简单,它也许只有几根线条,但是能够勾勒出设计造型的神韵,设计师通过大量的设计草图来尽可能多的提出新的创意。
这个车到底是简洁、还是稳重、是复古、还是动感都是在此确定的。
当然,如果是逆向设计,则就不需要这个过程了,把别人的车型直接进行点阵扫描,然后在计算机中进行造型勾画就行了。
3.制作油泥模型随着计算机的应用,草图绘制完成后,可以用使用各种绘图软件制作三维电脑数据模型(这种模型能够直接将数据输入5轴铣削机,铣削出油泥模型),看到更加清晰的设计表现效果,然后进行1:5的油泥模型制作。
完成爱生活,爱悠悠濮阳例油泥模型制作后,进行评审,综合考虑各种因素:美学、工艺、结构等,OK后进行1:1的油泥模型制作。
传统的全尺寸油泥模型都是完全由人工雕刻出来的,这种方法费时费力而且模型质量不能得到很好的保证,制作一个整车模型大约要花上3个月左右的时间,现在随着技术的进步,各大汽车厂家的全尺寸整车模型基本上都是由5轴铣削机铣削出来的,这种方法制作一个模型只需要1个月甚至更少的时间。
三、工程设计阶段(数模构建)在完成造型设计后,开始进入工程设计阶段,工程设计是一个对整车进行细化设计的过程,各个总成分发到相关部门分别进行设计开发。
工程设计阶段主要包括以下几个方面:1.总布置设计在前面的总布置草图上,进行细化,精确各部件的尺寸和位置。
确定各部件的详细结构、特征参数及质量要求。
车身尺寸2mm工程讨论

车身尺寸2mm工程讨论内容(经典讨论)——转帖(特别声明!)力帆520的成功~尹明善得功于两个人~据说其一就是在国外搞两毫米工程的工程师~多少mm是质量/成本/能力决定的,各厂的评价方法也不一样,讨论具体的数字没有意义。
对于这种精益工程,其实还是需要搞得,比如说航天工程,但是对于目前的中国汽车工业,这种东西只能是骗人的东西,不会带来任何益处,我的建议是:国家加大技术投入,让中国的汽车行业少花冤枉钱,然后提高国际竞争力.最后我们就有本钱进行这项工程了.否则只能是面子工程,口号工程.2MM工程虽然提到得是具体的误差要求,但是要分配到整车不同的质量控制环节,决不是一件简单的事情。
误差的分配大致分为模具的制造误差,零件的制造误差,分总成焊接的误差,然后到总成的焊接误差,总装的误差。
再下去就是提供焊接的夹具制造误差等等。
研究的方向通常是从提高各个环节的精度以及减小各个环节误差相互影响两个方面入手。
RPS,MLP以及尺寸链研究等等都是整个系统工程的一部分内容。
2mm工程的概念是由美籍华人美国密歇根大学教授吴贤民先生提出,得到美国三大汽车公司认同,并得到美国联邦政府的科研基金资助。
目的是要改进汽车车身几何精度----主要是指车身的几何尺寸的一致性。
实现的手段是持续改进工程,衡量的指标是CII-- Continuouse improvement Index。
简而言之就是希望车身的几何尺寸的标准差(6sigma)要小于或等于2毫米。
工程由吴氏先进制造技术研究所和美国三大汽车公司在美国联邦政府的资助下合作完成,虽然不是所有的参与车型都达到了预期目标,确实使得美国三大汽车公司的车身几何制造精度有了一次飞跃。
过去美国汽车开闭件漏雨和风噪声大的蜜封问题从根本上得到改善。
它的意义已经超出了2mm工程本身,首先代表吴氏先进制造技术研究所去实施2mm工程的主体是从大陆到美国学习的中国人,使三大汽车公司的主管看到了中国人的能力。
汽车尺寸工程 -综合检具基础知识

GWM-PPT V2012.2
2016/1/12
4
综合检具简介
GWM-PPT V2012.2
2016/1/12
ห้องสมุดไป่ตู้
5
综合检具简介
GWM-PPT V2012.2
2016/1/12
6
二、综合检具结构
GWM-PPT V2012.2
2016/1/12
7
综合检具结构
综合检具主要结构包括基座、载体模型、标准件模块、连接件各 部分,如下图。
GWM-PPT V2012.2
综合检具基础知识
部 门:上车体平台管理部 讲 师:梁旭昌 课 时:1.5小时 日 期:
content
一、综合检具简介 二、综合检具结构 三、综合检具分类 四、综合检具功能 五、综合检具使用和误区 六、总结
GWM-PPT V2012.2
2016/1/12
2
一、综合检具简介
GWM-PPT V2012.2
2016/1/12
15
综合检具的功能
4.正式生产阶段:此阶段综合检具主要用于零部件质量的日常 控制和问题分析,遇到质量波动时,不能判定是零部件问题还是 白车身问题时,可利用综合检具快速找出问题的根本原因;也可 用于监控关键零部件的质量;通过对供应商零部件的定期抽检, 监控零部件质量的稳定性,预防质量问题的发生。
GWM-PPT V2012.2
2016/1/12
20
Thank you
GWM-PPT V2012.2
2016/1/12
21
1.产品设计阶段:对于全新车型的开发,参考资料比较少,只 能依靠标杆车型,此时综合检具能够帮助快速进行调试工作,特 别是前期零部件和设备状态都不稳定的时候,可以成为一个参考 的基准,既可用于评估零部件设计结构和匹配关系的合理性,及 时发现设计问题;也可通过零部件的装配,评估工艺上的合理性, 提前制定出合理的工艺。
整车尺寸工程理论和实战

功能尺寸
整车功能尺寸 车身功能尺寸 零部件功能尺寸
白车身总成 功能尺寸
外覆件功能 尺寸
白车身测点与功能尺寸关系
白车身测点
根据GD&T/Control Drawing的要求, 结合生产工艺,用 于监控、反应产品 和工艺尺寸特性的 测量点
白车身总成功能尺寸
在车身制造过程中 检验和控制车身匹 配质量,以计算测 点之间相对关系的 形式所规定的一系 列尺寸
由于尺寸链中所有零件都处在极限公差的概率非常 小,因此极值法是一种保守的分析方法。在尺寸链 较长的情况下为了保证最终尺寸,会对零件设计过 于严格的公差范围从而导致计算结果失效
均方根法(Root Sum Squares, RSS)
利用方差的可加性,采用方差叠加法对零件 公差进行设计
相比于极值法,均方根法更趋于合理
蒙特卡洛仿真法(Monte-Carlo)
从零件已知的尺寸偏差分布中进行随机采样, 通过已知的零件间的装配关系来求解装配偏差 的统计分布
a ±T1
Part1
3a ±Ttatal a±T2
Part2
a ±T3
Part3
TTatal T1 T2 T3
TTatal T12 T22 T32
VA-正态分布
拟次数
是 输出仿真结果
数模
工装精度 GD&T
Family Tree 测点
VA-三维尺寸模型
结构树
三维模型
模拟视频 单击观看
N-2-1法则
+Z
A1
+Y
A2
+X B1
A3
A1
C A2
B
B2
XY Z X Y Z
A1,A2,A3 Z X Y
公共汽车尺寸标准尺寸

公共汽车尺寸标准尺寸公共汽车是城市交通运输系统中重要的一部分,其尺寸标准对于保障乘客的安全和舒适具有重要意义。
根据国家相关规定,公共汽车的尺寸标准主要包括车身尺寸、座位布局和通道宽度等方面。
本文将就公共汽车尺寸标准尺寸进行详细介绍,以便相关从业人员和乘客了解和遵守相关规定。
首先,公共汽车的车身尺寸标准是指车辆的长度、宽度和高度等方面的规定。
一般来说,城市公共汽车的长度通常在10米至12米之间,而宽度则在2.5米至3米左右。
而在高度方面,一般在3.2米至3.8米之间。
这些尺寸的标准设计旨在保证公共汽车在城市道路上的安全行驶,并且能够适应城市道路的尺寸和限制。
其次,公共汽车的座位布局也是尺寸标准的重要部分。
根据规定,公共汽车的座位布局应合理,能够充分利用车厢空间,保证乘客的舒适性和安全性。
一般来说,座位的间距应该符合人体工程学的原则,座椅的高度和宽度也需要符合相关规定,以保证乘客乘坐时的舒适感。
此外,座位的数量也需要符合规定,以保证车辆的承载能力和乘客的安全乘坐。
最后,公共汽车的通道宽度也是尺寸标准的重要部分。
通道宽度的设计直接关系到乘客上下车的便利性和安全性。
根据规定,公共汽车的通道宽度应该能够容纳乘客的正常上下车活动,并且需要保证紧急情况下的疏散通道畅通。
因此,通道宽度的设计需要兼顾乘客的舒适性和安全性,确保乘客在车辆运行过程中能够安全有序地上下车。
综上所述,公共汽车的尺寸标准尺寸涉及车身尺寸、座位布局和通道宽度等多个方面,其设计和执行对于保障乘客的安全和舒适具有重要意义。
相关从业人员和乘客应该了解和遵守相关规定,确保公共汽车能够安全、舒适地运行,为城市交通运输系统的发展做出贡献。
- 1、下载文档前请自行甄别文档内容的完整性,平台不提供额外的编辑、内容补充、找答案等附加服务。
- 2、"仅部分预览"的文档,不可在线预览部分如存在完整性等问题,可反馈申请退款(可完整预览的文档不适用该条件!)。
- 3、如文档侵犯您的权益,请联系客服反馈,我们会尽快为您处理(人工客服工作时间:9:00-18:30)。
产品部门
尺寸工程 公差设计
工艺部门 生产部门
尺寸工程公差设计是多部门共同协作、参与完成的工作,规范公差设 计流程,有利于协调、梳理好各部门间的工作关系。
GWM-PPT V2012.2
4
范围
GWM-PPT V2012.2
5
范围
范围
该流程阐述了以全新车型开发为模板的新产品开发过程中尺寸工程设 计开展的流程,并为全新车型、局部改型、年度车型的开发提供参考。
CHK011机罩总成
GWM-PPT V2012.2
CHB031机罩总成
14
工作程序
三维偏差仿 真分析
Y
NC阶段GD&T图纸 设计
N
Y
NC阶段GD&T 图纸审核
关键点分析
各分总成、零件公差设计完成后,在NC阶段,进行三维偏差仿真计算, 对单件至总成的公差、RPS进行优化设计,确认最终目标后,由设计公司输 出GD&T图纸,由各专业院、工程院进行审核
尺寸工程公差设计流程
GWM-PPT V2012.2
部 门:上车体平台管理部 讲 师:梁旭昌 课 时:1.5小时 日 期:
GWM-PPT V2012.2
content
目的 范围 术语定义 工作程序
2
目的
GWM-PPT V2012.2
3
目的
目的
本文件依据《尺寸工程设计流程》编写,目的是细化并规范整车尺寸 工程公差设计流程,明确各部门与尺寸工程公差设计相关的职能职责, 明确对应的输入和输出,强化过程控制,统一管理模式,提高工作效率, 降低风险,以确保整车的顺利开发。
GWM-PPT V2012.2
工作程序
GWM-PPT V2012.2
9
工作程序
方案阶段 工艺阶段
工艺阶段 工艺阶段 NC阶段 NC阶段 NC阶段
GWM-PPT V2012.2
流程
基础公差库
《关键总成公差目标》 设计
N
《关键总成公差 目标》评审
Y
分总成、零件公差设计
N
三维偏差仿真 分析
Y
NC阶段GD&T图纸 设计
适用范围
全新车型
CHB071 CH051X CH061X CH171
. . .
GWM-PPT V2012.2
改款车型
CHB022 CHB032 CHB042 CHB025
. . .
6
术语定义
GWM-PPT V2012.2
7
术语定义
术语定义
尺寸工程 尺寸工程是一种结合计算机仿真技术(如3DCS),通过控制制造偏 差和推进稳健设计来提高产品尺寸质量、降低生产成本,缩短产品投 放市场时间的工程方法和手段。
《关键总 成公差目 标》评审
Y
分总成、零件公差设计
GWM-PPT V2012.2
零件公差关系表模板
例如分总成、零件公差设计,前期缺少总成公差尺寸链计算,只是依据经验确定其公差要求。 对于CHK011车型机罩总成匹配面面轮廓度1.6mm,而CHB031车型机罩总成匹配面面轮廓 度1.2mm,造成不同车型相似总成及零部件公差不同。
GD&T图纸 指形状与位置公差图纸,一般作为尺寸设计阶段的最终输出物,通过 GD&T图纸延伸到对模具、夹具、检具、螺钉车、Cubing的管控。
偏差分析 利用仿真分析软件(如3DCS),通过对装配过程及公差的模拟,验 证产品和工艺的设计方案能否满足目标要求;原理:模拟生产实际, 输出数据统计模型(SPC)及各装配环节对偏差的最终影响(贡献率)。
GWM-PPT V2012.2
例如对于定位孔的公差要求,由于缺少基础公差,导致不同车型对于定位孔的公差要求不 同,从而对总成公差的计算产生影响。
CHB021定位孔公差要求
CHB031定位孔公差要求
GWM-PPT V2012.2
12
工作程序
关键点分析
《关键总成公差目标》 设计
N
确定基础公差后,结合第一版DTS,初版工艺数模、对关键总成公差进行 分解,此公差进行评审通过,即为保证DTS目标必须实现的总称公差目标。 由此关键总成的公差目标分解至分总成、单件公差目标,此环节在以往车型 中为空白,直接导致生产阶段公差控制目标不明确,尺寸问题发生后无法追 溯与判断。
GWM-PPT V2012.2
Thank you
GWM-PPT V201T图纸审核
尺寸工程分析部 尺寸工程分析部 尺寸工程分析部 专业院、设计公司 尺寸工程分析部 专业院、设计公司 专业院、工程院、尺寸
10
工作程序
基础公差库
关键点分析
基础公差库是一个项目中公差设计的基础和关键,需车身、内外饰、底盘、 电器、工程院多部门参与讨论来确定,在以往的公差设计过程中没有确定基础公 差的环节,直接导致后续的公差设计缺少支持,在生产阶段的问题追溯则会由于 各部门对于基础公差确定的不统一,给问题的整改带来困难。