乘用车平台前端模块化设计
乘用车白车身平台结构设计

乘用车白车身平台结构设计作者:潘承鹏来源:《汽车与驾驶维修(维修版)》2020年第04期摘要:对汽车企业来讲,一个长期可持续开发的车身平台非常重要,企业会基于产品平台开发大量的车型数据、CAE分析模型及验证报告等,对后续二次开发车型具有指导意义,节约后续车型的开发时间及成本。
本文通过对白车身平台全新开发实列的研究和总结,介绍了几种在后续二次开发情况下的结构设计开发方案。
关键词:白车身平台;结构设计中图分类号:U462文献标识码:A当今的汽车企业,需要用最快的时间将新设计的多种变型车型推向市场。
同时,还要控制自身成本,向客户交付高质量、高性能和高安全性的汽车。
为了实现这一目标,车企需要有一个或者多个产品平台。
白车身平台的开发,在概念阶段将对后续车型的固有结构及动态特性產生影响。
因此在概念阶段,设计师及工程师都需要考虑即将投放市场的车型情况,还必须确保此平台在最大限度的满足成本、轻量化及性能等各种条件的情况下,平台能适用于后续开发的其他不同类型车型。
1白车身平台开发实例1.1平台开发需求及目标新平台的基础车定义为SUV车型,而且根据不同的底盘布置要求,需要开发出18款白车身下车体有以下要求。
(1)满足3种不同轴距的布置需求。
(2)满足2种车体空间(宽体/窄体)的布置需求。
(3)满足轿车布置需求。
(4)满足纯电动车布置需求。
(5)满足成本、轻量化及性能要求。
1.2不同轴距开发实例根据开发需求,下车体有3种轴距。
为了在轴距变换的同时满足成本需求,并尽可能提高通用化率,采取的设计方案如下。
(1)发动机舱总成和前地板总成沿用基础车型。
(2)后地板总成局部变更,其中前后地板连接板总成根据总布置所布置的第2排人机位置做相应的调整来满足座椅安装(基础车设计时候应尽可能考虑后续轴距变换时零件的通用性,或者通过更改切边模具等来实现通用性)。
后地板面板分总成根据轴距的变换平移相应距离,后地板骨架总成平移相应距离,同时后纵梁前端需要根据前后地板连接板总成重新匹配设计(图1)。
汽车前端模块总成模块化设计及应用
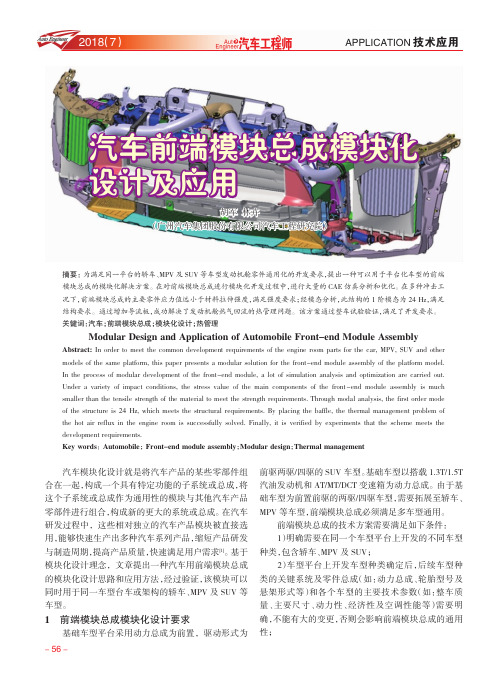
中冷器、散热器及风扇分总成、前端模块骨架总成等主
要零部件组成。其中,冷凝器通过螺栓固定至中冷器, 中冷器与散热器通过螺栓固定,散热器通过软垫固定
图 前端模块总成应力分布
在前端模块骨架总成上。前端模块总成主要部件及发 动机舱总布置简图,如图 1所示。
2018(7)
20技18术年应7用月
汽车前端模块总成模块化 设计及应用
胡军 林卉 (广州汽车集团股份有限公司汽车工程研究院)
摘要:为满足同一平台的轿车、"#$ 及 %&$ 等车型发动机舱零件通用化的开发要求,提出一种可以用于平台化车型的前端 模块总成的模块化解决方案。在对前端模块总成进行模块化开发过程中,进行大量的 '() 仿真分析和优化。在多种冲击工 况下,前端模块总成的主要零件应力值远小于材料拉伸强度,满足强度要求;经模态分析,此结构的 * 阶模态为 +, -.,满足
模块化设计理念,文章提出一种汽车用前端模块总成
2)车型平台上开发车型种类确定后,后续车型种
的模块化设计思路和应用方法,经过验证,该模块可以 类的关键系统及零件总成(如:动力总成、轮胎型号及
同时用于同一车型台车或架构的轿车、MPV及 SUV等 悬架形式等)和各个车型的主要技术参数(如:整车质
车型。
! 前端模块总成模块化设计要求
零部件进行组合,构成新的更大的系统或总成。在汽车 MPV等车型,前端模块总成必须满足多车型通用。
研发过程中,这些相对独立的汽车产品模块被直接选
前端模块总成的技术方案需要满足如下条件:
用,能够快速生产出多种汽车系列产品,缩短产品研发
1)明确需要在同一个车型平台上开发的不同车型
[1]
与制造周期,提高产品质量,快速满足用户需求 。基于 种类,包含轿车、MPV及 SUV;
汽车轻量化之前端模块
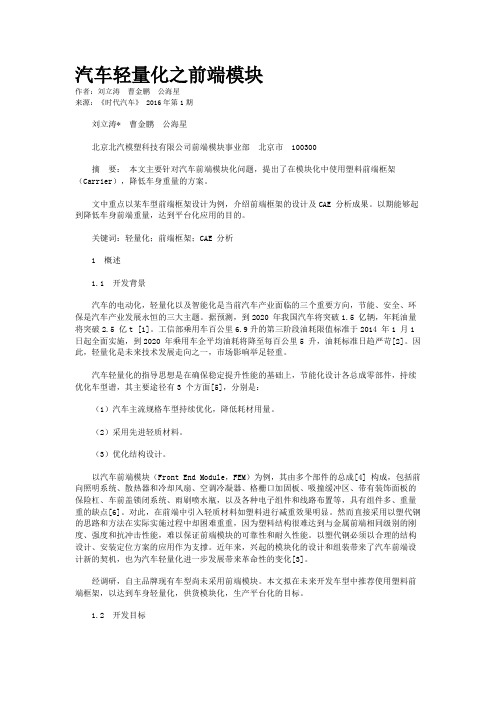
汽车轻量化之前端模块作者:刘立涛曹金鹏公海星来源:《时代汽车》 2016年第1期刘立涛* 曹金鹏公海星北京北汽模塑科技有限公司前端模块事业部北京市100300摘要:本文主要针对汽车前端模块化问题,提出了在模块化中使用塑料前端框架(Carrier),降低车身重量的方案。
文中重点以某车型前端框架设计为例,介绍前端框架的设计及CAE 分析成果。
以期能够起到降低车身前端重量,达到平台化应用的目的。
关键词:轻量化;前端框架;CAE 分析1 概述1.1 开发背景汽车的电动化,轻量化以及智能化是当前汽车产业面临的三个重要方向,节能、安全、环保是汽车产业发展永恒的三大主题。
据预测,到2020 年我国汽车将突破1.5 亿辆,年耗油量将突破2.5 亿t [1]。
工信部乘用车百公里6.9升的第三阶段油耗限值标准于2014 年1 月1日起全面实施,到2020 年乘用车企平均油耗将降至每百公里5 升,油耗标准日趋严苛[2]。
因此,轻量化是未来技术发展走向之一,市场影响举足轻重。
汽车轻量化的指导思想是在确保稳定提升性能的基础上,节能化设计各总成零部件,持续优化车型谱,其主要途径有3 个方面[5],分别是:(1)汽车主流规格车型持续优化,降低耗材用量。
(2)采用先进轻质材料。
(3)优化结构设计。
以汽车前端模块(Front End Module,FEM)为例,其由多个部件的总成[4] 构成,包括前向照明系统、散热器和冷却风扇、空调冷凝器、格栅口加固板、吸撞缓冲区、带有装饰面板的保险杠、车前盖锁闭系统、雨刷喷水瓶,以及各种电子组件和线路布置等,具有组件多、重量重的缺点[6]。
对此,在前端中引入轻质材料如塑料进行减重效果明显。
然而直接采用以塑代钢的思路和方法在实际实施过程中却困难重重,因为塑料结构很难达到与金属前端相同级别的刚度、强度和抗冲击性能,难以保证前端模块的可靠性和耐久性能。
以塑代钢必须以合理的结构设计、安装定位方案的应用作为支撑。
整车模块化平台关键尺寸L113设定

2021年第7期潘彦成赵国栋秦广义安鹏姜显丰(一汽奔腾轿车有限公司,长春130000)【摘要】基于整车平台化、模块化开发策略,论证分析了关键尺寸参数L113的设定过程。
通过对L113的尺寸链分解,提出了各部分对L113的限制因素,并且明确了设定方法。
平台开发过程中,L113的合理规划,既对汽车设计及零部件的成本降低起到重要作用,也对确定平台人机属性具有一定的指导意义。
主题词:L113平台化模块化人机工程中图分类号:U462.2+2文献标识码:ADOI:10.19822/ki.1671-6329.20210019The Key Dimension L113Setting of the Vehicle Modular PlatformPan Yancheng,Zhao Guodong,Qin Guangyi,An Peng,Jiang Xianfeng(FAW Car Co.,Ltd.,Changchun 130000)【Abstract 】Based on the vehicle platform and modular development strategies,the process of setting the key dimension parameter L113is demonstrated and analyzed.By decomposing the dimension chain of L113,the limiting factors of each part on L113are proposed,and the setting method is clarified.In the process of platform development,the reasonable planning of L113not only plays an important role in reducing the cost of automobile design and parts,but alsohas a certain guiding significance to determine the human-machine attributes of the platform.Key words:L113,Platform,Modular,Ergonomics整车模块化平台关键尺寸L113设定【欢迎引用】潘彦成,赵国栋,秦广义,等.整车模块化平台关键尺寸L113设定[J].汽车文摘,2021(7):22-26.【Cite this paper 】Pan Y,Zhao G ,Qin G,et al.The Key Dimension L113Setting of the Vehicle Modular Platform [J].Automotive Di⁃gest (Chinese),2021(7):22-26.1前言随着经济的发展,汽车产业成为了我国国民经济的支柱产业,汽车制造业产值约占经济总量的2%~3%[1]。
基于Android平台的智能行车导航系统设计与开发

基于Android平台的智能行车导航系统设计与开发随着科技的不断发展,智能导航系统已经成为现代汽车行业中不可或缺的一部分。
而基于Android平台的智能行车导航系统更是在用户体验和功能性上有着明显的优势。
本文将介绍基于Android平台的智能行车导航系统的设计与开发过程,包括系统架构设计、功能模块实现、地图数据集成等方面。
一、系统架构设计在设计智能行车导航系统时,系统架构是至关重要的一环。
基于Android平台的智能行车导航系统通常可以分为前端和后端两部分。
前端主要包括用户界面设计、地图显示、路线规划等功能,而后端则负责数据处理、算法计算等核心功能。
1.1 前端设计在前端设计中,用户界面的友好性和易用性是首要考虑的因素。
通过Android平台提供的各种UI组件和交互方式,可以实现地图显示、搜索功能、路线规划等操作。
同时,还可以结合语音识别、手势控制等技术,提升用户体验。
1.2 后端设计后端设计主要涉及到数据处理和算法计算。
地图数据的存储和管理、路线规划算法的选择和优化都是后端设计中需要考虑的问题。
同时,为了提高系统的实时性和准确性,还需要考虑数据更新机制和网络通信方面的设计。
二、功能模块实现基于Android平台的智能行车导航系统具有丰富的功能模块,包括但不限于地图显示、路径规划、实时交通信息、语音导航等功能。
2.1 地图显示地图显示是智能行车导航系统中最基本也是最核心的功能之一。
通过集成地图SDK,可以实现地图的加载、缩放、拖动等操作,并在地图上显示POI点、路况信息等。
2.2 路径规划路径规划是智能行车导航系统中的重要功能之一。
通过选择合适的路径规划算法,并结合实时交通信息和用户偏好,可以为用户提供最优的驾驶路线。
2.3 实时交通信息实时交通信息可以帮助用户避开拥堵路段,选择更加畅通的道路。
通过集成第三方交通数据服务,可以获取实时路况信息,并在地图上进行展示。
2.4 语音导航语音导航是提高驾驶安全性和便利性的重要功能之一。
自动驾驶模块化设计
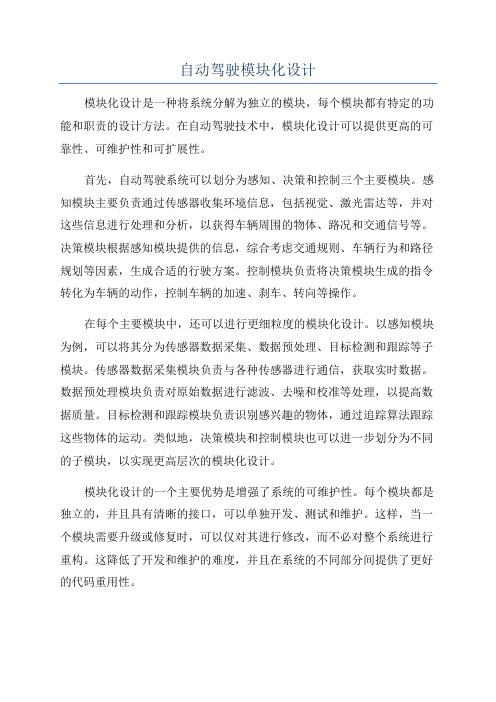
自动驾驶模块化设计模块化设计是一种将系统分解为独立的模块,每个模块都有特定的功能和职责的设计方法。
在自动驾驶技术中,模块化设计可以提供更高的可靠性、可维护性和可扩展性。
首先,自动驾驶系统可以划分为感知、决策和控制三个主要模块。
感知模块主要负责通过传感器收集环境信息,包括视觉、激光雷达等,并对这些信息进行处理和分析,以获得车辆周围的物体、路况和交通信号等。
决策模块根据感知模块提供的信息,综合考虑交通规则、车辆行为和路径规划等因素,生成合适的行驶方案。
控制模块负责将决策模块生成的指令转化为车辆的动作,控制车辆的加速、刹车、转向等操作。
在每个主要模块中,还可以进行更细粒度的模块化设计。
以感知模块为例,可以将其分为传感器数据采集、数据预处理、目标检测和跟踪等子模块。
传感器数据采集模块负责与各种传感器进行通信,获取实时数据。
数据预处理模块负责对原始数据进行滤波、去噪和校准等处理,以提高数据质量。
目标检测和跟踪模块负责识别感兴趣的物体,通过追踪算法跟踪这些物体的运动。
类似地,决策模块和控制模块也可以进一步划分为不同的子模块,以实现更高层次的模块化设计。
模块化设计的一个主要优势是增强了系统的可维护性。
每个模块都是独立的,并且具有清晰的接口,可以单独开发、测试和维护。
这样,当一个模块需要升级或修复时,可以仅对其进行修改,而不必对整个系统进行重构。
这降低了开发和维护的难度,并且在系统的不同部分间提供了更好的代码重用性。
此外,模块化设计还能够提高系统的可靠性。
由于每个模块是独立的,意味着一个模块的故障不会对其他模块产生严重影响。
例如,如果感知模块出现故障,决策和控制模块仍然可以继续工作,并采取相应的措施保证车辆的安全。
这种冗余设计减少了系统的单点故障,并提高了整个系统的可靠性和鲁棒性。
最后,模块化设计还可以提供更好的可扩展性。
当需要增加新的功能时,可以通过添加新的模块来实现扩展,而不影响现有的模块和系统架构。
这种灵活性使得自动驾驶系统能够适应未来的技术和需求的变化,例如增加对新传感器的支持或改进决策算法。
某车型前端模块设计和平台化构想
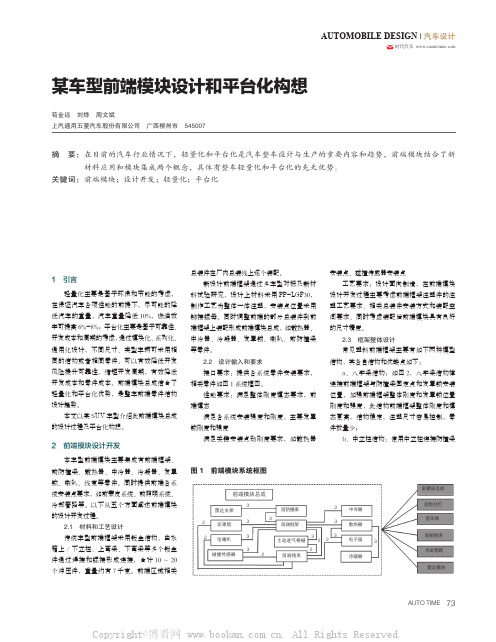
前端模块已实现了前端结构模块化集成, 具有先天平台化基础。初步构想从如下三方 向提供零件共用率,减少零件种类,实现前 端模块平台化。
1)结构和布置统一化:结构和布置的 统一是平台化的基础。在前期设计中需要 尽量考虑各种车型需要,选择合适的布置 位置和安装结构,将安装结构和布置位置 的统一。有效保证设计可靠性和延续性, 同时可以降低开发风险。例如散热器采用 统一的水箱结构,与车身安装点和方式也 统一;中冷器均布置在防撞梁下方,与前 端模块通过 4 颗螺栓前后方向连接,发罩 锁与散热器相对位置(限制造型发罩分缝 特征和位置)。
图 1 前端模块系统框图
前端模块总成
3 雷达支架
2
发罩锁
3
前防撞梁
3 前端框架
3
中冷器
3
散热器
2 电喇叭
3
主动进气格栅
3 2
2
3
电子扇
3
3
碰撞传感器
2
2 前端线束
冷凝器
前蒙皮总成 前组合灯 前车体 前舱线束 冷却管路
雷达模块
AUTO TIME 73
Copyright©博看网 . All Rights Reserved.
AUTOMOBILE DESIGN | 汽车设计
和发罩锁安装点。发罩锁刚度和强度更容易 满足要求,但由于框架整体为矩形,前端框 架相对刚度模态偏低,同时注塑后收缩不稳 定,需要前期多次分析和调整。 图 2 八字梁结构
图 3 中立柱结构
本车型前端框架设计选用中立柱结构。 前端框架整体为矩形,由上 / 下横梁和左右 立柱构成,发罩锁安装区域通过钣金中立柱 连接发罩锁和前防撞梁,有效满足发罩锁安 装各项刚度和强度要求。设计上对横梁与立 柱连接接头位置通过设计三角筋加强连接刚 度。布置上将对刚度和动刚度要求高的零件 布置在立柱上并靠近前端框架与放撞梁连接 部位。
汽车平台研发新趋势:生产模块化零部件通用化

汽车平台研发新趋势:生产模块化零部件通用化前言1.汽车平台概念其实“汽车平台”并没有一个切当的定义,概念较为笼统,主要体现在汽车的研发阶段。
简单而言就是开辟过程中用一个平台可以同时承载不同车型的开辟与生产创造,产生出外形、功能都不尽相同的产品。
在创造方面,同一平台的产品大量采用通用化的零部件和总成,大大降低了创造成本和采购成本;在研发方面,一个平台上实现了技术突破,等于这个平台上搭载的所有产品都实现了技术突破,对研发、对产品的供应链和服务链都产生了革命性的影响,同时为实现世界围的兼并重组。
汽车的大工业生产方式发生过三个转变:20 世纪初,福特公司在创造 T 型车时创造出影响整个世界工业的生产工艺——生产流水线,大幅度降低了生产周期和成本,同时也降低了售价。
流水线方式作为汽车生产的主流方式一致延续到 80 年代。
随着科技进步和市场的变化,一个型号的产品生命周期越来越短,大批量生产方式逐渐变得不能适应竞争。
在 80 年代,产生了一种称为"汽车平台"的概念,“汽车平台”是由汽车创造厂商设计的,几个车型共用的产品平台。
汽车平台与车辆的基本结构相关,出自于同一平台的不同车辆具有相同的结构要素,例如车门立柱、翼子板、车顶轮廓等。
同一平台的车型的轴距普通情况下是相同的,同时一些配件是通用的。
有时候不少种不同品牌的车在一个平台,而同一品牌的不同年度车型反而不在一个平台。
在"模块化"生产方式下,汽车技术创新的重心在零部件方面,零部件要超前发展,并参预汽车厂商的产品设计。
例如德尔福系统公司相继推出了座舱、接口盘制动、车门、前端、集成空气/燃油等模块。
而汽车厂商方面则以全球围作为空间,进行汽车模块的选择和匹配设计,优化汽车设计方案,将汽车装配生产线上的部份装配劳动转移到装配生产线以外的地方去进行。
采用"模块化"生产方式有利于提高汽车零部件的品种、质量和自动化水平,提高汽车的装配质量,并缩短汽车的生产周期。
汽车前端模块设计研究

汽车前端模块设计研究发布时间:2022-10-08T05:06:34.259Z 来源:《工程管理前沿》2022年6月11期作者:朱洪俊[导读] 汽车前端模块(automotivefront-endmodule,FEM)是集成汽车前端所有零部件的系统零件。
朱洪俊恒大新能源汽车(天津)有限公司,天津300301摘要:汽车前端模块(automotivefront-endmodule,FEM)是集成汽车前端所有零部件的系统零件。
伴随着汽车零部件的集成和模块化的模块化,汽车前端模块从单一框架演变为渐进的集成系统。
为了简化整辆车,汽车前端模块通常采用塑料替代策略而不是钢。
前端模块高度集成和塑料熔体不仅降低了整个车的质量,而且给零部件运输带来了困难和存储困难。
本文为前端模块设计了一个统一的运输箱,旨在实现无损安装、堆叠、回收、适应各种状态以解决这些问题。
关键词:汽车;前端模块;安装定位;前端框架;结构设计引言汽车轻量化是解决“节能”、“安全”、“环保”的最有效手段之一。
研究表明,汽车每降低100kg,可节省燃油0.3~0.5L/100km,可减少二氧化碳排放8~11kg/100km。
汽车零部件日益向轻量化、模块化方向发展。
其中,前端模块更是研究应用的重要课题之一。
结构优化主要是为了满足设计中使材料用量最少、成本达到最低、工艺步骤最简单的最优标准。
从工程设计角度,结构优化可分为尺寸优化、形状优化以及拓扑优化三个层次。
尺寸优化和形状优化已经得到充分的发展,在航空、航天、桥梁、汽车等一些领域得到了广泛的应用。
1前端模块的构成前端模块由前端框架和集成到前端框架中的组件组成,可集成到前端框架中的组件包括散热器、冷凝器、中间冷却器、风扇、盖板锁、扬声器、大灯、缓冲器、弹簧保护支架、防震梁、传感器这些组件位于发动机模块前面,包括全车辆冷却系统、信号照明系统、行人保护、碰撞安全、外观形状、传感器和辅助驾驶系统。
前端模块的集成程度取决于外形、布局、安全性能、制造技术和全车成本等因素。
汽车塑料前端模块设计策略与分析

汽车塑料前端模块设计策略与分析摘要:随着汽车需求者的要求提升,全球汽车设计者都开始了汽车设计新的征程,汽车技术研究人员也开始向模块化、集成化、轻量化方向发展。
近二十年来,有许多研究工作者已经开始关注汽车前端模的设计,汽车前端模的发展是实现整车轻量化、低耗油、低排放的关键部位。
本文简单介绍塑料前端模块的设计思路和构成单元,以某车型塑料前端框架为例浅析主要工作要点。
关键词:塑料;前端框架;CAE 分析;模块化;轻量化1 汽车塑料前端模块概述汽车前端模块位于汽车的最前端,其外形设计、功能结构和重量等,都对能耗有显著的影响。
其中,实现前端模块的轻量化、对进入发动机舱的气流进行动态调节进而降低气阻,都有利于减少燃油消耗和碳排放量。
而汽车前端模采用塑料材料就能够帮助整车更好的实现量轻化设计。
塑料模不同于传统的聚丙烯/钢混合板材料,其重量远小于钢板材料,同时,操作也可以更加简化,实现节省安装时间和成本的作用。
通过对汽车塑料前端模的大力推广,能够降低成本效率,满足供应链的灵活性要求。
汽车前端塑料模也有部分零件塑料化和全塑化的分别,将汽车前端的零件塑料化,可以使汽车的车身更加苗条,安装空间更为紧凑,车身比例也更加和谐美观,较轻的车体,更长的轴距和更大的车轮,才更符合当下汽车发展的需求。
2 前端模块构成分类汽车的前端是由多个零部件构成,主要包括了散热器组件、车灯、引擎盖锁、保险杠、横梁、小腿保护支架、格栅、喇叭和吸能泡沫,根据生产规划的要求,总体上我们可以将这些零部件分为三大类,①集成散热器总成、机盖锁(低度集成);②集成散热器总成、机盖锁、大灯、防撞梁(中度集成);③集成散热器总成、机盖锁、大灯、防撞梁、前保险杠(高度集成)。
3 安装点布置方式在设置安装点时,我们必须满足前端支架整体刚度,应用Hyper mesh软件对全塑前端模块支架进行承重模拟分析,考察其变形程度和应力的分布,得出最优方案应为在汽车前端框架的上、中、下均存在安装固定点。
前端模块自动合装技术设计与应用
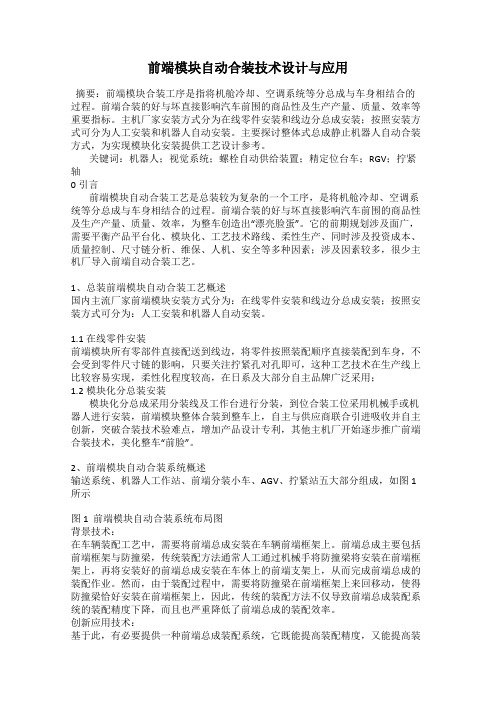
前端模块自动合装技术设计与应用摘要:前端模块合装工序是指将机舱冷却、空调系统等分总成与车身相结合的过程。
前端合装的好与坏直接影响汽车前围的商品性及生产产量、质量、效率等重要指标。
主机厂家安装方式分为在线零件安装和线边分总成安装;按照安装方式可分为人工安装和机器人自动安装。
主要探讨整体式总成静止机器人自动合装方式,为实现模块化安装提供工艺设计参考。
关键词:机器人;视觉系统;螺栓自动供给装置;精定位台车;RGV;拧紧轴0引言前端模块自动合装工艺是总装较为复杂的一个工序,是将机舱冷却、空调系统等分总成与车身相结合的过程。
前端合装的好与坏直接影响汽车前围的商品性及生产产量、质量、效率,为整车创造出“漂亮脸蛋”。
它的前期规划涉及面广,需要平衡产品平台化、模块化、工艺技术路线、柔性生产、同时涉及投资成本、质量控制、尺寸链分析、维保、人机、安全等多种因素;涉及因素较多,很少主机厂导入前端自动合装工艺。
1、总装前端模块自动合装工艺概述国内主流厂家前端模块安装方式分为:在线零件安装和线边分总成安装;按照安装方式可分为:人工安装和机器人自动安装。
1.1在线零件安装前端模块所有零部件直接配送到线边,将零件按照装配顺序直接装配到车身,不会受到零件尺寸链的影响,只要关注拧紧孔对孔即可,这种工艺技术在生产线上比较容易实现,柔性化程度较高,在日系及大部分自主品牌广泛采用;1.2模块化分总装安装模块化分总成采用分装线及工作台进行分装,到位合装工位采用机械手或机器人进行安装,前端模块整体合装到整车上,自主与供应商联合引进吸收并自主创新,突破合装技术验难点,增加产品设计专利,其他主机厂开始逐步推广前端合装技术,美化整车“前脸”。
2、前端模块自动合装系统概述输送系统、机器人工作站、前端分装小车、AGV、拧紧站五大部分组成,如图1所示图1 前端模块自动合装系统布局图背景技术:在车辆装配工艺中,需要将前端总成安装在车辆前端框架上。
前端总成主要包括前端框架与防撞梁,传统装配方法通常人工通过机械手将防撞梁将安装在前端框架上,再将安装好的前端总成安装在车体上的前端支架上,从而完成前端总成的装配作业。
汽车产品平台化模块化设计要则及案例分析_2010[1].1.13
![汽车产品平台化模块化设计要则及案例分析_2010[1].1.13](https://img.taocdn.com/s3/m/f9ffe839af45b307e87197b5.png)
1.5
•
实施平台战略应避免的问题
风险强度控制难度大:当汽车制造商们体验着在一个专用平台外以较低风 险制造出各种车型拓展产品的同时,如果他们已经发展和改进的基础平台 经证实是错误的,那么他们也许正在经受着更大的风险。 – 标准化工艺技术的一个缺点就是会在遍布众多的车型中使风险加倍, 使召回和重新设计潜在的费用非常昂贵。正如通用汽车公司近期因为 一个普通的刹车安全装置召回110万辆汽车,并为提供免费维修而使花 费超过了240万美元。 – 消费者的品位改变得很快(如从普通汽车到SUV),这便使得平台将做物 理上的修改或者其功能特性很有可能会同市场错位匹配。 – 工艺技术也会改变,尤其是汽车电子,因此平台不一定能够兼容这种 升级。 – 潜在地情况包括法律法规,公众焦点或者一次石油事件,这些都能够 使一个平台为了迎合不断增长的功能上的需求而在技术上错位。
1.4
•
实施平台化及模块化的好处
采取平台而生产的不同的车型在市场中更具有价值。 – 各具特色的汽车能更好地同目标消费者的需求相一致。 • 如有实用主义思想的美国消费者愿意花更高的价钱购买以运动性 能为主的变异汽车产品(如售价为五千美元的Subaru Outback和 本田CR-V远远胜过了其公司的主流产品Subaru Legacy和本田 Civic); – 脱离同一平台制造出的拓展产品通常通过品牌的强化能够给人以独特 感和优越感。 • 有1%的人“能从一辆卡车上得到更多”,GMC Sierras就同那些人 进行交易,并在事实上等同雪弗莱Silverado的装备上售出更高的 价钱。
零件
1.2
建立平台的四要素
尽管帕萨特和高尔夫的界面和零件不同,但发动机组装的程序是相似的:
敞开的发动机机厢
相同工艺流程:
CRH1A动车组的模块化设计和组装技术

CRH1A动车组的模块化设计和组装技术摘要文章介绍了CRH1A动车组采用车顶模块、司机室模块和车下设备安装模块,通过与传统组装方法比较,从操作的难易度、对整车生产线的影响等方面阐述模块化的优点。
关键词模块化;并行生产;环境组装1 概述车辆的生产制造是一项系统性工作,需要设计和工艺统筹考虑,在设计之初就须考虑后续生产中的各种问题,包括质量、成本、生产计划等,优秀的设计应该具有良好的可操作性并且对提高生产效率有所帮助。
传统车辆组装方法为串行方法,基本理念是在车辆上依次组装各种部件,突出问题是某一环节出现问题将会导致整个生产线的停滞,解决此问题的一种行之有效的方法是将车辆的组装工作分解成几个模块,模块的生产与车辆的生产并行,最后将模块整体与车辆组装。
CRH1A的设计和制造大量采用模块化理念,CRH1A是青岛四方庞巴迪铁路运输设备有限公司生产的时速250km不锈钢车体动车组,由8辆车编组(5动3拖,编组型式:Mc1a+Tp2+M2+Md2+T2+M2+Tp2+Mc1a)构成,列车内部功能齐全,具有良好的的舒适性。
本文以CRH1A动车组为参照,阐述其模块化组装的理念。
2.模块介绍2.1 车顶模块钢结构车顶固定在工装上,工装两侧与翻转设备固定,车顶板朝下、弯梁朝上放置,工人站在两侧的平台上进行操作,组装防寒材、风道、线槽、中顶板等部件,构成车顶模块,经过校线测试合格后,将整个车顶模块与无车顶车体焊接成一体。
这种组装工艺使车顶各部件的组装工作变得非常简便。
传统车体为整体焊接结构,车顶与侧墙、端墙、底架焊接成筒型结构,在组装车顶防寒材、线槽、风道等部件时,工人需要借助梯子、凳子等登高并且仰头施工,操作不便,劳动强度大。
车顶模块很好的解决此问题,。
另外,CRH1A车体在车顶组装前上部为开放式结构,为大部件的调入提供了便利。
在与车顶模块焊接前,整体调入地板、厕所、洗脸间、厨房设备等大部件。
传统方法为从车顶空调口调入部件,如果部件尺寸太大,就无法调入,需要将部件做成分体式结构或者加大空调开口。
汽车模块化设计技术的研究与应用

汽车模块化设计技术的研究与应用随着社会的发展以及人们生活水平的提高,汽车被越来越多的人所需要和关注。
然而,汽车的制造不仅涉及到机械、电子等技术,还需要考虑整车的设计、性能、舒适度等方面。
而引领汽车设计领域的新技术之一就是汽车模块化设计技术。
汽车模块化设计技术,指的是将汽车生产过程中的各个组成部分模块化,形成标准化的零部件,以方便生产、维护和更新。
这种技术可以有效地提高汽车生产效率和零部件的互换性,降低成本,提高质量。
从根本上优化汽车制造流程,降低制造成本,并提高产品创新能力和快速响应市场变化的能力。
因此,已经成为全球汽车制造领域的热门话题和趋势。
汽车模块化设计技术最早源于欧洲的汽车工业,随后逐渐在世界各地得到了推广和应用。
目前,已经有多家汽车公司采用了模块化设计技术生产汽车,包括德国的奥迪、宝马、大众,法国的标致、雪铁龙,日本的本田、丰田等。
它们在汽车零部件标准化、生产流程优化和协作型设计方面取得了显著的成果。
汽车模块化设计技术的应用不仅可以提高汽车生产效率,同时还可以提高整车的安全性、舒适度和智能化水平。
例如,在汽车的智能化方面,汽车模块化设计技术可以使汽车更易于更新和维护,降低系统升级的成本。
同时,还可以在汽车配置、驾驶体验等方面实现更多个性化的选择。
此外,汽车模块化设计技术不仅可以应用于传统汽车,也可以应用于新能源汽车领域。
它可以通过标准化的设计和制造流程,为新能源汽车提供更高效、更安全、更可靠的组装和维护手段。
大大减少了新能源汽车的制造成本,促进了其市场的竞争力和发展。
在汽车模块化设计技术的研究和应用方面,中国也在积极跟进。
近年来,中国的汽车产业也在不断探索和开发该技术,尤其是新能源汽车领域,已经初步取得了一定的成果。
目前,中国已成为全球最大的汽车市场,具有广阔的市场需求和生产潜力。
通过加强汽车模块化设计技术的研究和推广,不仅可以提高中国汽车行业的竞争力,同时也可以为中国企业进军国际市场提供更多的机会和优势。
整车平台工程化开发方案
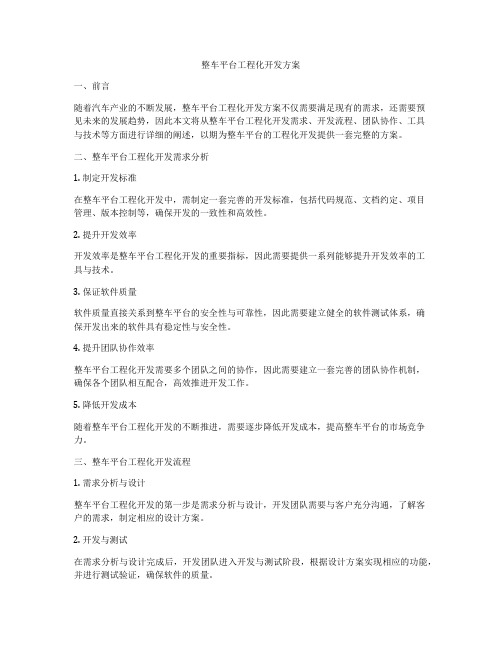
整车平台工程化开发方案一、前言随着汽车产业的不断发展,整车平台工程化开发方案不仅需要满足现有的需求,还需要预见未来的发展趋势,因此本文将从整车平台工程化开发需求、开发流程、团队协作、工具与技术等方面进行详细的阐述,以期为整车平台的工程化开发提供一套完整的方案。
二、整车平台工程化开发需求分析1. 制定开发标准在整车平台工程化开发中,需制定一套完善的开发标准,包括代码规范、文档约定、项目管理、版本控制等,确保开发的一致性和高效性。
2. 提升开发效率开发效率是整车平台工程化开发的重要指标,因此需要提供一系列能够提升开发效率的工具与技术。
3. 保证软件质量软件质量直接关系到整车平台的安全性与可靠性,因此需要建立健全的软件测试体系,确保开发出来的软件具有稳定性与安全性。
4. 提升团队协作效率整车平台工程化开发需要多个团队之间的协作,因此需要建立一套完善的团队协作机制,确保各个团队相互配合,高效推进开发工作。
5. 降低开发成本随着整车平台工程化开发的不断推进,需要逐步降低开发成本,提高整车平台的市场竞争力。
三、整车平台工程化开发流程1. 需求分析与设计整车平台工程化开发的第一步是需求分析与设计,开发团队需要与客户充分沟通,了解客户的需求,制定相应的设计方案。
2. 开发与测试在需求分析与设计完成后,开发团队进入开发与测试阶段,根据设计方案实现相应的功能,并进行测试验证,确保软件的质量。
3. 发布与部署经过开发与测试阶段的验证,软件达到客户的需求,即可发布与部署到整车平台中,提供给客户使用。
4. 运维与维护整车平台工程化开发不仅仅局限于开发、测试、发布与部署,还需要对整车平台进行运维与维护,确保整车平台的稳定运行。
四、整车平台工程化开发团队协作机制1. 制定开发规范与流程整车平台工程化开发需要制定相应的开发规范与流程,确保团队开发的一致性与高效性。
2. 实施项目管理整车平台工程化开发需要进行项目管理,包括需求管理、任务分配、进度跟踪等,确保项目的顺利进行。
汽车开发平台模块化特点及其发展趋势
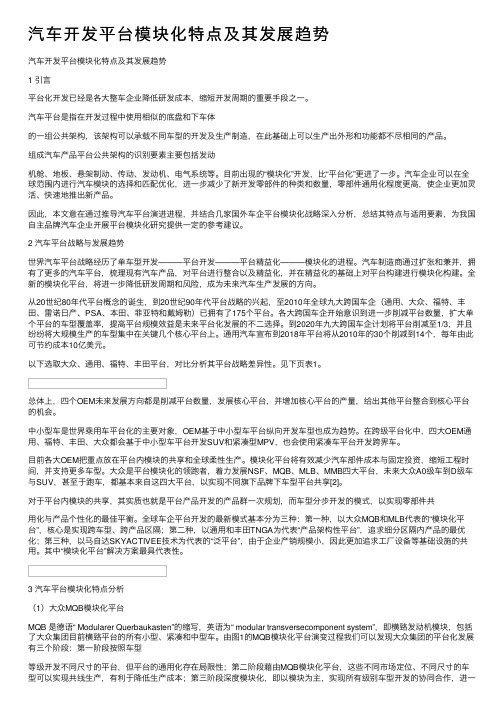
汽车开发平台模块化特点及其发展趋势汽车开发平台模块化特点及其发展趋势1 引⾔平台化开发已经是各⼤整车企业降低研发成本,缩短开发周期的重要⼿段之⼀。
汽车平台是指在开发过程中使⽤相似的底盘和下车体的⼀组公共架构,该架构可以承载不同车型的开发及⽣产制造,在此基础上可以⽣产出外形和功能都不尽相同的产品。
组成汽车产品平台公共架构的识别要素主要包括发动机舱、地板、悬架制动、传动、发动机、电⽓系统等。
⽬前出现的“模块化”开发,⽐“平台化”更进了⼀步。
汽车企业可以在全球范围内进⾏汽车模块的选择和匹配优化,进⼀步减少了新开发零部件的种类和数量,零部件通⽤化程度更⾼,使企业更加灵活、快速地推出新产品。
因此,本⽂意在通过推导汽车平台演进进程,并结合⼏家国外车企平台模块化战略深⼊分析,总结其特点与适⽤要素,为我国⾃主品牌汽车企业开展平台模块化研究提供⼀定的参考建议。
2 汽车平台战略与发展趋势世界汽车平台战略经历了单车型开发———平台开发———平台精益化———模块化的进程。
汽车制造商通过扩张和兼并,拥有了更多的汽车平台,梳理现有汽车产品,对平台进⾏整合以及精益化,并在精益化的基础上对平台构建进⾏模块化构建。
全新的模块化平台,将进⼀步降低研发周期和风险,成为未来汽车⽣产发展的⽅向。
从20世纪80年代平台概念的诞⽣,到20世纪90年代平台战略的兴起,⾄2010年全球九⼤跨国车企(通⽤、⼤众、福特、丰⽥、雷诺⽇产、PSA、本⽥、菲亚特和戴姆勒)已拥有了175个平台。
各⼤跨国车企开始意识到进⼀步削减平台数量,扩⼤单个平台的车型覆盖率,提⾼平台规模效益是未来平台化发展的不⼆选择。
到2020年九⼤跨国车企计划将平台削减⾄1/3,并且纷纷将⼤规模⽣产的车型集中在关键⼏个核⼼平台上。
通⽤汽车宣布到2018年平台将从2010年的30个削减到14个,每年由此可节约成本10亿美元。
以下选取⼤众、通⽤、福特、丰⽥平台,对⽐分析其平台战略差异性。
汽车平台架构设计方案
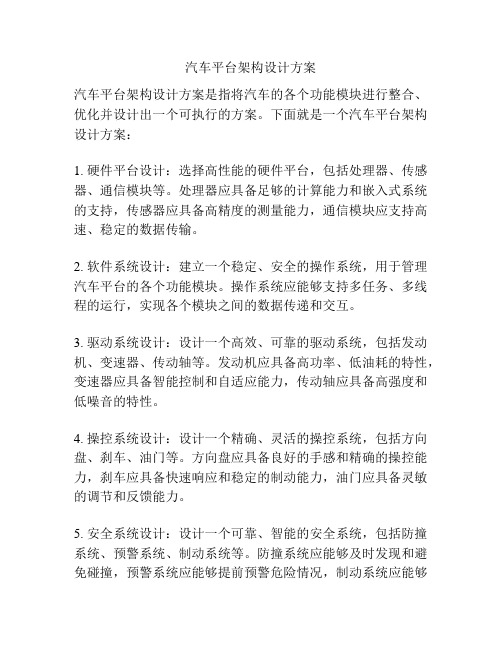
汽车平台架构设计方案汽车平台架构设计方案是指将汽车的各个功能模块进行整合、优化并设计出一个可执行的方案。
下面就是一个汽车平台架构设计方案:1. 硬件平台设计:选择高性能的硬件平台,包括处理器、传感器、通信模块等。
处理器应具备足够的计算能力和嵌入式系统的支持,传感器应具备高精度的测量能力,通信模块应支持高速、稳定的数据传输。
2. 软件系统设计:建立一个稳定、安全的操作系统,用于管理汽车平台的各个功能模块。
操作系统应能够支持多任务、多线程的运行,实现各个模块之间的数据传递和交互。
3. 驱动系统设计:设计一个高效、可靠的驱动系统,包括发动机、变速器、传动轴等。
发动机应具备高功率、低油耗的特性,变速器应具备智能控制和自适应能力,传动轴应具备高强度和低噪音的特性。
4. 操控系统设计:设计一个精确、灵活的操控系统,包括方向盘、刹车、油门等。
方向盘应具备良好的手感和精确的操控能力,刹车应具备快速响应和稳定的制动能力,油门应具备灵敏的调节和反馈能力。
5. 安全系统设计:设计一个可靠、智能的安全系统,包括防撞系统、预警系统、制动系统等。
防撞系统应能够及时发现和避免碰撞,预警系统应能够提前预警危险情况,制动系统应能够精确控制制动力度和距离。
6. 信息娱乐系统设计:设计一个多元化、便捷的信息娱乐系统,包括导航、音响、智能手机连接等。
导航应具备精准的定位和路线规划能力,音响应具备高保真的音质和多媒体播放能力,智能手机连接应能够实现手机与汽车平台的互联互通。
以上是一个关于汽车平台架构设计方案的简要描述,具体的实施方案需要根据实际情况进行细化和优化。
同时,还需要考虑安全性、可扩展性、成本等因素,以提高汽车的性能和用户体验。
“超级模块化平台”时代正在到来

“超级模块化平台”时代正在到来文 / 本刊记者 郑雪芹随着时间的推移和技术的进步,模块化平台的造车理念不仅进入了电动化、智能化时代,高度集成和通用的“超级模块化平台”也将出现。
车企模块化平台架构不断升级进化说到平台或架构,相信大家都不陌生了,例如大众的MQB平台、日产的CMF平台、奔驰的MFA平台,还有丰田的TNGA架构等等。
简单来说,平台化就是在一套共享的生产标准上,根据不同需要,调整零件、用料、尺寸等各项指标,从而设计出不同的车型。
模块化平台具有提高零部件通用率,减少研发及生产成本等优势。
目前,大部分车企都拥有属于自己的模块化平台,甚至多个平台。
相对于模块化平台,模块化架构更具优势,它是平台概念的延伸和拓展,具有更高的零部件通用化率、更高的可扩展性,可兼容更多级别、不同动力类型的车型,因此车企开始由模块化平台逐步向模块化架构过渡。
模块化架构带来了生产效率的提升、采购和制造成本的降低、研发周期的缩短。
目前广汽全球模块化平台架构GPMA零部件通用化率超过60%;吉利SEA平台通用率则超过了70%;丰田TNGA架构中,零部件通用率甚至达到了80%。
目前,国内车企在模块化架构方面布局相对更早,包括比亚迪、吉利、奇瑞、长安等在内的国内车企均已推出了自己的模块化架构。
(见表1)其中,吉利汽车算是目前自主品牌里平台架构应用最成熟的,其拥有四大汽车平台或架构,包括CMA超级母体、BMA基础模块、SEA浩瀚纯电以及SPA平台,其中既有自主研发的,也有和沃尔沃联合开发的,目前已广泛搭载在吉利、领克、极氪、沃尔沃、极星等品牌下的多款车型上。
再如长城汽车,此前已经有以ME、XEV为核心的5大新能源造车平台,30系列的第三代综合造车平台,以及覆盖纵置越野车及皮卡的P71平台,不过真正让大家熟知的,还是去年一口气发布的三大平台——柠檬、坦克和咖啡智能。
其中,柠檬平台定位为全球化高智能模块化技术平台,坦克平台定位为全球智能专业越野平台,咖啡智能是长城汽车整车智能化平台。
汽车模块化技术

车身模块是汽车的外壳模块,它决定了汽车的美观度和防护性能。
详细描述
车身模块包括车身结构、车门、车窗、前后保险杠等部分,这些部分在设计和生产过程中被整合为一 个整体。车身模块化可以提高汽车的美观度和防护性能,同时方便安装和维修。此外,车身模块化还 可以降低生产成本,有利于实现批量生产。
电气系统模块
为了提高汽车的燃油效率和性能,未来汽 车模块化技术将更加注重轻量化设计。
技术前景展望
市场规模不断扩大
随着汽车市场的不断发展和消费者 对汽车性能和环保性需求的提高, 汽车模块化技术的应用将越来越广 泛。
智能化和电动化的趋势
未来汽车的发展将更加注重智 能化和电动化,而模块化技术 将在这方面发挥重要作用。
03
汽车模块化生产
生产线的模块化设计
模块化生产线设计
将生产线划分为多个独立的生产模块,每个模块负责特定的生产 任务,以提高生产效率。
模块化生产线灵活性
通过模块化设计,生产线可以根据市场需求快速调整生产布局,适 应不同车型的生产需求。
模块化生产线标准化
标准化设计有助于降低生产成本,提高生产线的互换性和可维护性。
总结词
电气系统模块是汽车的大脑模块,它决 定了汽车的智能化水平和安全性。
VS
详细描述
电气系统模块包括电源系统、启动系统、 照明系统、仪表盘、导航系统等部分,这 些部分在设计和生产过程中被整合为一个 整体。电气系统模块化可以提高汽车的智 能化水平和安全性,同时方便安装和维修 。此外,电气系统模块化还可以降低生产 成本,有利于实现批量生产。
将电机、减速器和控制器 集成在一个模块中,简化 电动汽车的驱动系统,提 高能效和可靠性。
充电模块
设计独立的充电模块,支 持快速充电和无线充电, 方便用户随时为电动汽车 补充能量。
商用汽车产品模块化设计

汽车产品模块化设计摘要:提高产品的模块化水平,满足用户个性化的需求,降低企业的生产成本,提高企业的生产效率。
关键词:汽车、模块化、设计在我们实际工作中,存在大量的拿来主义,整车设计如同搭积木。
积木是一个个小块,通过这些小块块能拼出各式各样的模型,不由得联想到我们的产品设计。
汽车是一个复杂的系统,一般可以分为发动机、底盘、车身、电气设备等4大部分。
设计中我们是否也能将这些部分做成一个个模块,根据市场的需求做不同的搭配呢?中国市场由于地域辽阔以及行业众多,用户对于卡车有着千差万别的要求,作为企业,理应满足用户的需求,但是如果各种个性化需求都要满足的话,将降低企业的生产效率,增加企业的生产成本。
公司的发展经历了两个时期,最初的创业期和目前的成长期,由于历史的原因,在创业初期,由于技术力量的不足,产品设计没有完全导入模块化设计的理念。
公司在应对市场变化方面虽然有很快的反应能力,但是相应的是增加了设计人员的工作量,做了大量重复的工作,自制件、专用件特别多,造成很多零件不通用。
产品模块化设计是有效解决其问题的案之一。
用尽可能多的通用零部件,提高产品的模块化水平,是降低成本的有效途径,同时也要尽量满足用户的多样化需求。
要解决这一点,首先我们要将汽车产品进行模块化设计。
产品模块化设计就是将产品分成几个部分,也就是几个模块,每一部分都是具有独立功能,具有一致的几何连接接口和一致的输入、输出接口的单元,相同种类的模块在产品族中可以重用和互换,相关模块的排列组合就可以形成最终的产品。
通过模块的组合配置,就可以创建不同需求的产品,满足客户的定制需求;相似性的重用,可以使整个产品生命周期中的采购、物流、制造和服务资源简化。
当回归产品设计的本源,重新探讨产品开发方法论时,我们会发现,我们曾经忽视了一个重要阶段——产品开发阶段。
在产品开发阶段,产品设计师根据市场要求进行产品规划,比如:这个产品采用什么样的架构,企业供应链如何配套,如何进行模块化产品设计?这就是一个负责汽车总布置设计师要考虑的首要问题。
- 1、下载文档前请自行甄别文档内容的完整性,平台不提供额外的编辑、内容补充、找答案等附加服务。
- 2、"仅部分预览"的文档,不可在线预览部分如存在完整性等问题,可反馈申请退款(可完整预览的文档不适用该条件!)。
- 3、如文档侵犯您的权益,请联系客服反馈,我们会尽快为您处理(人工客服工作时间:9:00-18:30)。
于10倍圆孔直径;长孑L塞焊的开孔长度应不小于75衄,孔
的宽度应不小于板厚的2倍,孔端部呈半圆形;孔的间距应不 大于长孔长度的2倍等。
4厚薄板过渡焊接不满足规范要求 (觎勘要求强力甲板货舱舱口角隅的圆弧半径r应不小
于b/20(b为货舱舱口的宽度)。位于载货区域的货舱舱口角 隅应按规定的形式采用较货舱区域强力甲板增厚0.5倍的加厚 板予以补强。这样一来,与货舱角隅甲板相邻的首部甲板或尾 部甲板厚度差较大,常见的厚度差有时甚至达到10 mm。而检 验中发现,一些在建船舶施焊时没有将较厚板的边缘削斜,且 将不平面布置在甲板背面,造成背面的甲板骨架与甲板的焊接
图3中冷器布置在冷凝器与散热器之间
(2)中冷器位于冷凝器前面,前后布置顺序为中冷器(最
前端)一冷凝器一散热器一冷却风扇(最后端),该布置方式
多用于轿车。根据重力向下的原理,散热器进水管布置在散热 器芯体上部,出水管布置在芯体下部,散热器上部分水温比下 部分水温要高,需要散发的热量更多,需提供更好的散热环 境,且一般车辆前部造型都是上短下长。因此,布置中冷器时 应充分利用下部的空间,把中冷器布置在下部,也使得冷却系 统性能达到最佳。 中冷器采用2种布置形式:①中冷器与冷凝器前后布置, 高度方向上有重叠(如图4所示);②中冷器与冷凝器上下布 置,高度上不重叠,称为“吕”结构(如图5所示)。
厂质检员的角色。这不仅要求我们的验船师要具备专业的检验
技能,熟悉各项工艺要求,熟悉《观}酚要求,同时又要有耐 心,与船厂工人、质检员等保持良好的沟通,努力做到“一 检、二帮、三把关”。
注释 ①由于不同年份的《规范》要求可能存在少许差别,无法逐一罗列,此
处统称为《规范》,具体要求可详细查阅适用的《规范》要求。
向:整车架构开发;李柳林(1986一),男,广西上林人。硕士研究生,上汽通用五菱汽车股份有限公司助理工程师,研究方向:发动机舱物理集 成;李家烽(1983一),男,广西灵山人,上汽通用五菱汽车股份有限公司工程师,研究方向:发动机舱物理集成。
qiyekejiyufazhan
15
万方数据
析。在长度、宽度方向上不能再减小,因此只能降低中冷器高 度,减少l根散热扁管与l条散热带,测试结果见表3,结果 显示高度下降后的中冷器性能依然可以满足发动机性能要求。
【关键词】汽车平台;前端模块;模块化 【中圈分类号】U462 【文献标识码】A 【文章编号】1674—0688(2015)09—0015—02
器和冷却风扇、发动机进气中冷系统、空调冷凝器、散热器框 架集成(散热器左、右立柱总成、散热器上、下横梁总成)、 现今主要乘用车生产企业均采用平台战略构建自己的产品 系列,有行业分析报告指出,汽车平台开发已占据车企研发支 出费用的一半。如何进一步提高产品开发效率、缩短开发周 期,以满足市场需求的变化,将更多的资金用于新能源汽车等 新技术、新产品的开发,已经成为各企业必须面对的共同课 题。进一步削减平台数量、扩大主流单一平台车型覆盖率、提 高平台规模效益是不二选择。据有效统计数据显示,目前全球 主流几大汽车平台的产量占汽车总产销量的40%左右【11。
5其他焊接质量问题
(1)《规≯酚要求凡焊缝长度在300 mm以内者,一律采用 连续焊。骨材端面与板(如有时)、肘板与板或构件的焊接采 用双面连续焊;当船体结构采用间断焊缝时,对骨材的端部、 各种构件的切口、切角、开孑L等部位均应采用连续包角焊缝, 而现实中最常见的现象是肘板端部、骨材端部、构件切口、流 水孔、施焊孔等无包角焊。 (上接第16页) 由台架试验结果可知:经过中冷器的冷却空气会有一定的 温升,根据不同的芯体正面积大小、风速,冷却空气的温升也 不一样,一般为5。25℃,而且在相同条件下,芯子正面积越 小温升越大。中冷器位于各散热元器件的最前面容易使布置于 后面的冷凝器及散热器的冷却温度变高、散热性能变差。为了 实现Car、MPV车型前舱最大化共用且同时满足空调制冷性 能,最终选定方案二。
100
凝器(最前端)一中冷器一散热器一冷却风扇(最后端),如
图3所示。该布置方式多用于SUV、MPV等冷却系统上、下 安装支架空间较大的乘用车。
mm,选用现有中冷器成品,两者高度方向上有120 mm重
叠,中间间隔10mm(如图6所示)。 方案二:中冷器与冷凝器上下布置,冷凝器加高80 mm。新 开发高度降低的中冷器如图7所示。
图6方案一 图7方案二
台架试验约束条件如下。 (1)散热器控制介质:水,迎面风速为4.5 m/s,水流量 为80 Umin,气液温差为52℃(38~90℃)。 (2)中冷器控制迎面风速为45 m/s,热空气流量为0.08 k幽, 环境温度为38℃,进口热空气温度为150℃,进口压力为
220kPa。
(3)冷凝器控制进口压力为1
500
kPa,进口温度为80℃,
出口过冷度为8℃,进风温度为38℃,风速为4.5m/s。 前端模块热交换性台架试验结果见表4。
表4前端模块热交换性台架试验结果
模块总 能力 (kW) 冷凝器 中冷器 散热器 换热量 换热量 换热量 (kW)
(k冒) (kl『)
方案
模块
通风 阻抗 (Pa)
冷凝器 冷媒 流阻 (”a)
根据功能件布置差异分析可知,满足车身右边中冷器进气管布 置空间、大灯安装与散热器的安装工艺空间,散热器在上弯 梁、下弯梁右边固定点位置共用,根据不同的发动机性能要求 选用不同宽度尺寸的散热器,散热器车身框架中的上弯梁与下 弯梁预留安装固定位置,可满足平台散热器框架共用的策略 (如图2所示)。
3平台化前端模块布置
16
qiyekejiyufazhan
(下转第18页)
万方数据
甲板焊接。在现场检验中发现,一些船厂工人为徒省事,存在 弄虚作假的现象:如船舶甲板机械如系缆桩下方的要求为复 板,但看似有一个环形复板,而实际在缆桩下方并无复板,或 是有整块的复板,但塞焊的规格远远达不到规范要求。
(2)舷侧顶列板与甲板边板角接缝对船舶建造质量至关重 要,检验中偶尔会发现,强力甲板的边缘未开坡口,这就难以 保证能完全焊透。
31.410
1.455
6.7“
23.816
179.0
4.0
28.5
3.3
某型增压发动机对中冷器的进气性能的要求见表2。
表2某增压发动机中冷参数要求
l l
中冷器内压降 小于6.8
kPa
30.720
6.733
24.203
177.7
28.4
3.4
35.4ll
7
3ll
6
837
2l
668
173 9
144.0
29.1
企业科技与发展
乘用车平台前端模块化设计
宋建新L2,李柳林2,李家烽2
(1.上海交通大学机械与动力工程学院,上海200240;2.上汽通用五菱汽车股份有限公司,广西柳州545007)
【摘要】文章阐释了目前乘用车平台化的发展状况,然后对乘用车平台开发中前端模块的布置进行了详细的说明
和分析,包括边界条件、重要性能要求。最后分析前端模块的2种布置方案及进行台架试验,结果显示该前端模 块布置方案满足性能要求。
图1乘用车前端模块
1
引言
发盖锁闭系统、前蒙皮、前格栅及各种电子组件和线路布置等
(如图1所示)。
2乘用车平台化发展现状
汽车平台发展至今,已经形成以下3种开发模式。 (1)以“大众”为代表的模块化平台,主要特征是看重跨 车型和跨细分产品的分布,即每个平台可应对普通轿车、 SUV、MPV等多种车型,以及满足各细分车型区隔的要求, 如“大众”横置发动机MBQ模块平台包括了“大众”集团目 前横置平台的所有小型、紧凑型和中型车。 台可满足C级车和D级车的产品开发闭。 (2)以“通用”和“丰田TNGA”为代表的产品架构性平 台,不但总产销规模超800万台,而且单个细分产品区隔的产 销规模也非常巨大,通常超过150万台,因此更加看重每个细 分产品内的最优化。 (3)以“马自达SKYACTIVEE”技术为代表的“泛平 台”,由于企业产销规模小,总产销量在100万台左右,因此
3.1
在某乘用车平台开发项目中规划有2种车型,5座CAR、 7座MPV,动力总成配置有自然进气发动机、增压发动机。为 了降低成本、减少开发费用,平台开发策略定义为前舱功能件 实现布置最大共用。以CAR自然进气发动机车型配置的前端 模块功能件为基础,分析平台前端模块功能件的空间布置差 异,结果见表l。
有较大的间隙,严重影响焊接质量,而(觎≯酚的要求是不同
厚度的钢板进行对接时,若其厚度差大于或等于4 mm时,应 将较厚板的边缘削斜,使其均匀过渡,削斜宽度应不小于厚度 差的4倍。
参考文献
[1]中国船级社.钢质内河船舶建造规范[M].北京:人民交通出版 社,2015. [2]中国海事局.内河船舶法定检验技术规则[M].北京:人民交通 出版社。2015.
(觎
范》中关于塞焊有明确而具体的要求:圆孔塞焊的间距应不大
6结语Байду номын сангаас
以上问题是笔者多年在现场检验及图纸审查中发现的较为 典型的问题,但现实中存在的问题不止于此。由于生产力水平 及船厂质检人员的能力、责任心不够及管理制度存在缺陷,这 些看似简单的质量问题,却在这些小型的私营船厂里层出不 穷。因此,对于地方船检来说,需要做的不仅仅是检验,还需 要指导技术人员施工,指导质检员自检,甚至有时还要充当船
表3某增压发动机中冷器参数 图2散热器框架集成共用布置 l芯体尺寸(长X宽X高)(咖)l面积(m蛩l换热性能舶m/s(们l中冷器内压降(kPa)l
J
630X123X150 77 490 8088 ≤6.8
l
却,再进入发动机中。有数据表明,在相同的空燃比条件下, 增压空气的温度每下降10℃,发动机功率就能提高3%一5%。 增压发动机中冷器一般采用中冷器前置、中冷器侧置、中 冷器顶置3种布置方案。 中冷器前置时,中冷器放置于发动机舱前端、前保险杠后 面,中冷器与散热器、冷凝器及冷却风扇集成一个冷却模块, 方案普遍应用在乘用车上,中冷器前置可采用2种布置形式。 (1)中冷器位于冷凝器与散热器之间,前后布置顺序为冷