自动换刀故障处理
五轴加工中心的自动换刀故障
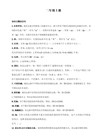
自动换刀装置控制原理及故障分析

第27 卷第1期2 0 0 9 年1 月西安航空技术高等专科学校学报Journal of Xi an Aerotechnical CollegeVol 2 7 No 1Jan . 2 0 0 9 自动换刀装置控制原理及故障分析罗庚合1, 黄万长2( 1. 西安航空技术高等专科学校机械工程系, 陕西西安710077; 2. 陕西法士特齿轮有限公司, 陕西西安710077)摘要: 加工中心自动换刀装置提高了数控机床的加工效率, 但由于加工中心换刀装置的动作控制比较复杂, 包含机械、电气与PM C、液压和检测等技术, 所以自动换刀装置的故障率比较高, 主要介绍自动换刀装置的类别和控制,自动换刀装置的故障诊断方法, 列举了自动换刀装置的一些常见故障及维修示例。
关键词: 加工中心; 选刀; 刀具交换; 乱刀与掉刀; PM C 诊断; I/ O 状态诊断中图分类号: T H161+ . 21 文献标识码: A 文章编号: 1008- 9233( 2009) 01- 0014- 051 引言4、6、8、12 工位, 有用电动机驱动的正传和反转, 也有用液压系统通过电磁换相阀和顺序阀进行控制加工中心可分为车削中心、镗铣中心和钻削中心等, 加工中心在加工过程中, 要使用多种刀具, 因此必须有自动换刀装置, 以便选择不同刀具, 完成不同工序的加工工艺。
常用的刀库形式有圆盘式刀库, 链式刀库, 格子盒式刀库。
按有无机械手又可分为不带机械手的自动换刀装置和带机械手的自动换刀装置。
按刀库的旋转和机械手的动作驱动方式可分为有液压、气动控制系统和电气与机械联合控制的驱动系统。
随着加工中心数控机床的普及和应用, 自动换刀装置控制过程中的故障率也比较高。
由于自动换刀装置结构比较复杂、控制为机、电、液联合控制, 复杂系数高等原因。
所以加工中心自动换刀装置的故障维修比较困难。
简要叙述换刀装置的分类和特点, 以立式镗铣中心普遍使用的圆盘式加工中心自动换刀装置为例, 分析自动换刀装置的控制原理及常见故障的维修方法。
自动换刀雕刻机的使用说明

大型数控加工中心使用说明正天恒业数控XX目录自动换刀雕刻机的使用说明2自动换刀雕刻机新代系统常用参数设定表14使用GHOST 制作系统卡〔DOS〕16自动换刀雕刻机的使用说明以下为工作步骤:1.把主控制箱的总开关扳到ON状态,此时控制箱红色电源指示灯亮。
2.按下控制箱面板的驱动器电源绿色按钮、变频器电源绿色按钮,使其处于上电状态。
检查气路压力要到达6bar,气缸吸合,除尘毛刷气缸处于行程的上部。
3.SYNTEC控制系统上电,进入界面后,提示:X、Y、Z轴尚未回机械原点。
如下操作完成回机械原点:先按〔键左上角灯亮〕,再按、、,此时雕刻机的XYZ方向往设定的机械坐标零点位置移动,直到面板界面里边机械坐标各轴都显示0,证明回机械原点动作完成,X回到最左边,Y回到最前面,Z上升到顶部。
如下列图:回机械原点时出现问题处理方法:故障现象:回机械原点方向反。
原因是限位感应器始终处于触发状态,检查感应器触发信号。
4.把要使用的刀具安装到刀具夹头内,并用手放到刀具库中:如下列图刀具排列的循序为左边是第一把刀〔系统默认为T1), 以此类推。
从左到右依次为T1, T2,T3, T4, T5, T6, T7, T8.如下列图:放上加工材料,按下开启真空吸附泵的绿色按钮吸附住材料,按下开启吸尘泵绿色按钮。
5. 加工开场之前需要设定机器的X Y Z 三轴的工作原点〔工件原点〕:先手动将刀具头装上主轴〔一般是程序中的第一把刀〕,按〔键左上角灯亮〕,再通过按X+, X-,Y+, Y-,Z+ Z- ,如图把机头移动到雕刻物件的左下角,既该图案路径的零点位置。
准确定位需要用手轮时,操作如下,先按下灯亮,手轮模式已启动。
通过手轮进展准确定位,主轴运行到加工物件的左下角的状态。
在系统控制器当前界面,如下操作→〔Position〕→〔Workpiece Coor〕→移动方向键,使光标移动到需要设置的G54-G59对应的X、Y坐标→〔tched〕,如下列图:再继续设T1的Z工件原点,回初始界面,选,再选,界面如下,把光标移动到序号01〔即对应T1〕Length列输入对应机械坐标,即完成T1Z轴的原点设定。
经济型数控车床自动换刀装置的故障分析及排除

和过 冲 ,如图 2所示 。
【 4 第3 卷 6】 4 第3 期 2 1—3下 ) 02 (
1 自动换 刀装 置与 自动刀架
经 济 型 换 刀 装 置 是 经济 型 数 控机 床 中 最 重 要
11 刀架 抬起 .
在 数 控 机 床 发 出更 换 刀 具 的 指 令 之 后 ,如 图
的 部 分 之 一 ,而 自动 刀 架 则 是 自动 换 刀 装
置 的 主 要 部 件 。统 计 资 料 显 示 , 目前使 用
中图分类号 :T 5 G69 文献标识码 :B 文章编号 :1 0—0 3 ( 0 2 3 下) 0 6 — 4 9 1 4 21 ) ( - 0 3 0 0
Do : . 9 9 J i n 1 0 -0 . 0 . ( ) 2 i1 3 6 / . s .0 9 1 4 21 3 下 . 0 0 s 3 2
会 出现 刀架的过 冲和 滞后现 象 。经过走 访调 查 ,并
且进 行反 复的 试验 ,结果依 旧如 此 。经 过 实践操 作 并 结合专 家意 见 ,我 们分析 得 出有 以下 四种 的机 械
13 刀架定 位 . 刀架体 转动 时会连 同电刷 座一 起转 动 ,当转到 指定 的 刀号时 ,粗定位 销便 会在弹 簧力 的作用 下进 入粗 定位 盘的槽 中再次 进行粗 定位 。 同时 ,另一 电 刷会 接触 导体使 电动机 反转 。 由于粗定 位槽 的某些 限制 ,刀架体 不能够转 动 ,并 使其 在该 位置上 垂直 落下 ,此 程序 中的刀 架体和 刀架 底座上 的端面 齿啮 合 实现精 确定位 ,从而 实现 刀架的定位 工作 。
数控机床自动换刀系统的故障排查与维修方法

数控机床自动换刀系统的故障排查与维修方法数控机床自动换刀系统在工业生产中扮演着重要角色,然而偶尔会遇到一些故障导致正常的生产工作受到干扰。
本文将介绍数控机床自动换刀系统常见故障的排查方法以及维修方法,帮助读者快速解决问题并恢复生产。
首先,我们来了解一下数控机床自动换刀系统的组成。
该系统由刀库、刀杆、刀座等主要组件构成。
故障通常出现在刀杆与刀座之间的连接部分。
常见的故障有刀杆卡滞、刀座松动、换刀定位错误等。
当遇到故障时,首先要做的是检查刀杆是否卡滞。
刀杆卡滞可能是由于过多的切屑或者油污导致的。
解决方法是清理刀杆和刀座之间的油污,以及及时清理刀座上的切屑。
此外,也应进行润滑保养,确保刀杆顺畅运行。
其次,如果刀座松动,我们可以采取以下步骤来解决问题。
首先,检查螺母是否松动,必要时紧固螺母。
其次,检查刀座与刀杆之间的连接是否紧密,避免松动。
如果刀座已经损坏或磨损,需要更换刀座。
最后,还应该检查刀座的弹簧是否失效,确认刀座的弹性是否符合要求。
换刀定位错误也是常见的故障之一。
如果发生换刀定位错误,首先要检查刀杆的长度和形状是否正常。
如果刀杆口径不匹配,需要更换合适的刀杆。
其次,刀座的定位销是否损坏,需要修复或者更换。
最后,还应检查换刀定位装置的传感器和控制系统是否正常,避免传感器故障导致定位不准确。
除了以上常见故障外,系统中的电气故障也可能导致自动换刀系统的故障。
在排查电气故障时,我们可以通过以下步骤来解决问题。
首先,检查电源线是否接触良好,确保电源正常供电。
其次,检查各个部件的电缆连接是否紧固,排除电线松动或者脱落的可能性。
如果电气故障仍然存在,建议寻求专业技术人员的帮助进行进一步的排查。
总结来说,数控机床自动换刀系统的故障排查与维修是一个复杂而又细致的过程。
在故障排查时,首先要根据故障现象进行针对性的检查,找出问题所在。
然后根据不同的故障类型采取相应的修复措施,如清洁、紧固或者更换部件。
若故障仍未解决,及时寻求专业技术人员的帮助。
数控机床技术中的自动换刀系统故障排解
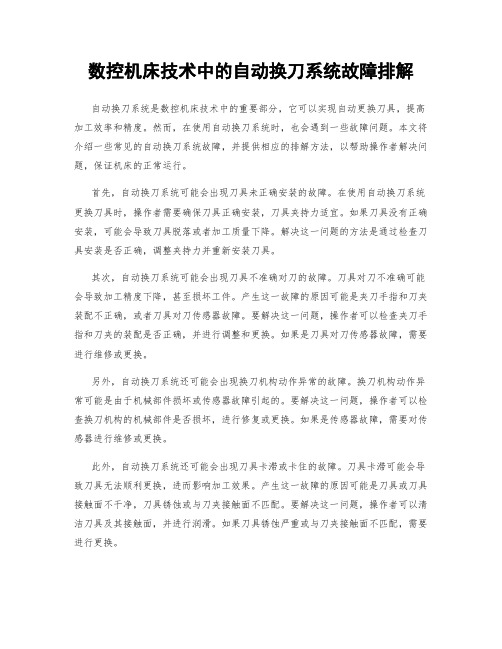
数控机床技术中的自动换刀系统故障排解自动换刀系统是数控机床技术中的重要部分,它可以实现自动更换刀具,提高加工效率和精度。
然而,在使用自动换刀系统时,也会遇到一些故障问题。
本文将介绍一些常见的自动换刀系统故障,并提供相应的排解方法,以帮助操作者解决问题,保证机床的正常运行。
首先,自动换刀系统可能会出现刀具未正确安装的故障。
在使用自动换刀系统更换刀具时,操作者需要确保刀具正确安装,刀具夹持力适宜。
如果刀具没有正确安装,可能会导致刀具脱落或者加工质量下降。
解决这一问题的方法是通过检查刀具安装是否正确,调整夹持力并重新安装刀具。
其次,自动换刀系统可能会出现刀具不准确对刀的故障。
刀具对刀不准确可能会导致加工精度下降,甚至损坏工件。
产生这一故障的原因可能是夹刀手指和刀夹装配不正确,或者刀具对刀传感器故障。
要解决这一问题,操作者可以检查夹刀手指和刀夹的装配是否正确,并进行调整和更换。
如果是刀具对刀传感器故障,需要进行维修或更换。
另外,自动换刀系统还可能会出现换刀机构动作异常的故障。
换刀机构动作异常可能是由于机械部件损坏或传感器故障引起的。
要解决这一问题,操作者可以检查换刀机构的机械部件是否损坏,进行修复或更换。
如果是传感器故障,需要对传感器进行维修或更换。
此外,自动换刀系统还可能会出现刀具卡滞或卡住的故障。
刀具卡滞可能会导致刀具无法顺利更换,进而影响加工效果。
产生这一故障的原因可能是刀具或刀具接触面不干净,刀具锈蚀或与刀夹接触面不匹配。
要解决这一问题,操作者可以清洁刀具及其接触面,并进行润滑。
如果刀具锈蚀严重或与刀夹接触面不匹配,需要进行更换。
最后,自动换刀系统还可能会出现控制系统故障。
控制系统故障可能导致自动换刀操作失效,无法正常更换刀具。
产生这一故障的原因可能是控制系统的电路板损坏或控制程序错误等。
要解决这一问题,操作者可以检查控制系统的电路板是否损坏,并进行修复或更换。
同时,对控制程序进行检查和修正。
在使用自动换刀系统时,操作者应注意安全操作规程,及时保养和维护系统,并进行定期的系统检查和保养。
自动换刀装置的结构原理与维修

自动换刀装置的结构原理与维修8.4.1 自动换刀装置的形式自动换刀装置是加工中心的重要执行机构,它的形式多种多样,目前常见的有以下几种。
1.回转刀架换刀数控机床使用的回转刀架是最简单的自动换刀装置,有四方刀架、六角刀架,即在其上装有四把、六把或更多的刀具。
回转刀架必须具有良好的强度和刚度,以承受粗加工的切削力:同时要保证回转刀架在每次转位的重复定位精度。
图8-17为数控车床六角回转刀架,它适用于盘类零件的加工。
在加工轴类零件时,可以用四方回转刀架。
由于两者底部安装尺寸相同,更换刀架十分方便。
图8-17 数控车床六角回转刀架1-活塞 2-刀架体 3、7-齿轮 4-齿圈 5-空套齿轮6-活塞 8-齿条 9-固定插销 10、11-推杆 12-触头回转刀架的全部动作由液压系统通过电磁换向阀和顺序阀进行控制,它的动作分为4个步骤:(1)刀架抬起当数控装置发出换刀指令后,压力油由a孔进入压紧液压缸的下腔,活塞1上升,刀架体2抬起,使定位用的活动插销10与固定插销9脱开。
同时,活塞杆下端的端齿离合器与空套齿轮5结合。
(2)刀架转位当刀架抬起后,压力油从c孔进入转位液压缸左腔,活塞6向右移动,通过联接板带动齿条8移动,使空套齿轮5作逆时针方向转动。
通过端齿离合器使刀架转过60º。
活塞的行程应等于齿轮5分度圆周长的1/6,并由限位开关控制。
(3)刀架压紧刀架转位之后,压力油从b孔进入压紧液压缸上腔,活塞1带动刀架体2下降。
齿轮3的底盘上精确地安装有6个带斜楔的圆柱固定插销9,利用活动插销10消除定位销与孔之间的间隙,实现反靠定位。
刀架体2下降时,定位活动插销10与另一个固定插销9卡紧,同时齿轮3与齿圈4的锥面接触,刀架在新的位置定位并夹紧。
这时,端齿离合器与空套齿轮5脱开。
(4)转位液压缸复位刀架压紧之后,压力油从d孔进入转位液压缸的右腔,活塞6带动齿条复位,由于此时端齿离合器已脱开,齿条带动齿轮3在轴上空转。
对自动换刀过程中常见故障的分析

导 致“送刀”无法满足。针对以上四点原因分别给 予解 决 就可排 除 主轴系统的问题。
图1 主轴结构示意图
1-刀具;2 - 拉钉;3 - 钢 球;4 - 锥套;5 - 蝶形弹簧;6 - 拉 杆; 7- 端盖;8 - 空心螺钉;9 - 液 压 缸;10 -顶杆
2 机械手不抓刀故障 2.1 故障现象
该机 床换刀时,在主轴定向后,ATC(自动换刀)无定向显示, 机 械手 没有 抓刀动 作,且 没有显 示 报警 信息。 2.2 文章编号:1674-098X(2013)03(a)-0079-01
自动 换刀装 置(ATC)作为加 工中心最 重要 结 构 部 件之一,其 换刀方 式 分为有机 械手 换刀和无 机 械手 换刀两 种,而机 械手 换刀 方 式 是大多数 加工中心采用的,在 这 种 换刀方 式下,机 械手成 为换 刀 过 程中 极 其 重要 的 机 械 装 置,它 的 作用 是 将上一 个工 序中用 过 的刀具送回刀库,并从刀库上取出新 的刀具安装 到主轴 上,以便 下 一 个工序的开展。由于换刀时动作 环 节 较多,广泛使用液 压元件、 行 程 开 关、感 应 开 关、电磁阀 等 机、电、液、气元 器件,只要 其中有 一 个 元 器 件出现 故 障,如 动 作 不 能 到 位 或 没有及 时 发出信号,机 械手就 无法完成 换刀动作,造成 加工中心不能 正常工作。下 面以配 FA NUC数 控系统的加工中心为例,对 该 加工中心机 械手无法 拔刀 和 取刀的 现 象 进行分 析 和 诊 断。
工业技术
科技创新导报 2013 NO.07
Science and Technology Innovation Herald
对自动换刀过程中常见故障的分析①
李玉琴 (安徽水利水电职业技术学院 安徽合肥 231603)
常见刀库故障排除步骤

1).将软操作开关MAG_JOG接通,PMC参数D499置为1;
2).JOG方式下,按操作面板上的刀库正转按钮或刀库反转按钮,使刀库停止在准确的位置上。
3).刀库停止准确后,将软操作开关MAG_JOG断开,PMC参数D499置为0.
手动转动刀臂:
1).软操作开关MAG_JOG接通,PMC参数D499置为1;
2).JOG模式下,按操作面板上的机械手旋转按钮,使机械手旋转至0度位置,此时操作面板上ATC READY指示灯亮起,表示机械手0度到位;
3).刀库停止在准确位置后,将软操作开关MAG_JOG断开,PMC参数D499置为0。
MAZAK型的机床卡刀和刀库方面的问题在机床的面板处都有详细说明,就按照做就好了;
Y1006.4
配天850机型:
配天的机是经常卡刀的,在遇到卡刀时,通常的做法就是把PLC开关10#和15#改成ON,再把程序编辑开关接通,按点动来手动转动刀库刀臂,此时应该注意的是手动转动过程中是不会自动松夹刀的,如果有刀在主轴上,要手动按松刀按钮;而在夹刀时也要按,这是很不好控制好的和很危险的过程,在实际操作中可以在主轴下方放一胶桶,让刀掉在里面。在调试换刀时就不要在刀臂上放刀转动。
LV-600 2号机
采用MAN模式操作时:
1. 主轴先定位。
2. 将PLC参数6403.0设为1.
3. 按FEED HOLD键来点动刀臂旋转。
4. 如果主轴没有定位,则同时按CYCLE START和FEED HOLD来点动刀臂旋转。
MDI模式下用M代码操作:
1. 将PLC参数6402.6设为1
手动方式驱动刀臂:
1. 将Operator’s panel “ATC MAN”开关切换至ON德位置。
机加工常见故障及检查、分析方法
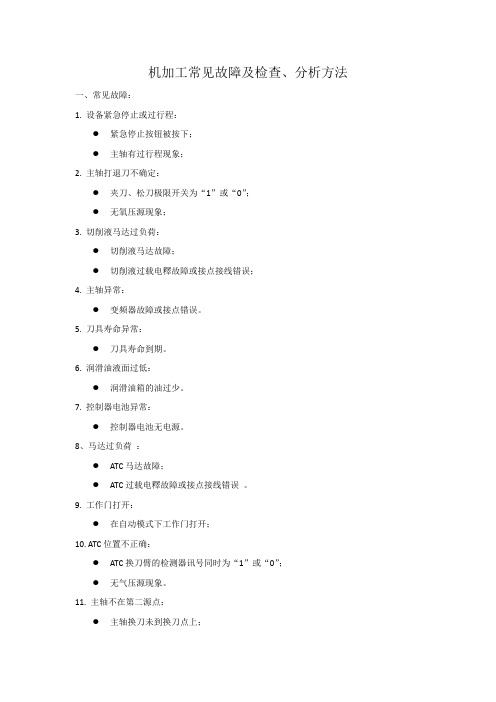
机加工常见故障及检查、分析方法一、常见故障:1. 设备紧急停止或过行程:●紧急停止按钮被按下;●主轴有过行程现象;2. 主轴打退刀不确定:●夹刀、松刀极限开关为“1”或“0”;●无氧压源现象;3. 切削液马达过负荷:●切削液马达故障;●切削液过载电釋故障或接点接线错误;4. 主轴异常:●变频器故障或接点错误。
5. 刀具寿命异常:●刀具寿命到期。
6. 润滑油液面过低:●润滑油箱的油过少。
7. 控制器电池异常:●控制器电池无电源。
8、马达过负荷:●ATC马达故障;●ATC过载电釋故障或接点接线错误。
9. 工作门打开:●在自动模式下工作门打开;10. ATC位置不正确:●ATC换刀臂的检测器讯号同时为“1”或“0”;●无气压源现象。
11. 主轴不在第二源点:●主轴换刀未到换刀点上;12. 主轴过热:●主轴冷却机异常。
13. 主轴没有定位:●主轴换刀时未在定位点上。
14. 主轴不在第一源点:●主轴取刀时未在第一源点上。
15. 须回源点:●开机后或曾执行紧急停止动作。
16、主轴不能旋转:●当主轴在松刀状况下,主轴不能转动。
二、主轴部件故障主轴是加工中心机床一大核心部件,加工表面精度绝大部分都和主轴有关,所以主轴的质量很关健。
由于使用调速电机,数控机床主轴箱结构比较简单,容易出现故障的部位是主轴内部的刀具自动夹紧机构、自动调速装置等。
为保证在工作中或停电时刀夹不会自行松脱,刀具自动夹紧机构采用弹簧夹紧。
若刀具夹紧后不能松开,则考虑调整松刀液压缸压力和行程开关装置或调整碟形弹簧上的螺母,减小弹簧压合量。
此外,主轴发热和主轴箱噪声问题,也不容忽视,此时主要考虑清洗主轴箱,调整润滑油量,保证主轴箱清洁度和更换主轴轴承,修理或更换主轴箱齿轮等。
三、进给传动链故障在加工中心进给传动系统中,普遍采用滚珠丝杠副、静压丝杠螺母副、滚动导轨、静压导轨和塑料导轨。
所以进给传动链有故障,主要反映是运动质量下降。
如:机械部件未运动到规定位置、运行中断、定位精度下降、反向间隙增大、爬行、轴承噪声变大(撞车后)等。
加工中心刀库分类、特点及典型故障分析
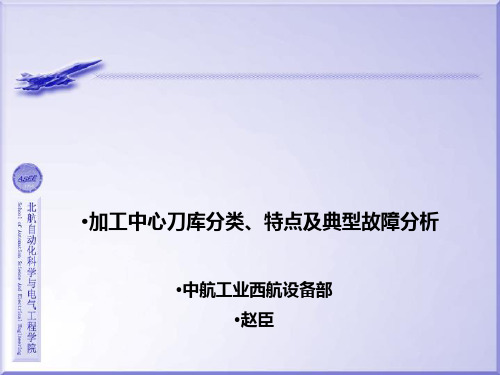
••AC..松装刀置机调构整回不退当故或障加。工误差过大而造成拨叉位置不正确。
••BD..限刀位具开超关重安。装不正确或调整不当而造成反馈信号错误。
5.刀具夹紧后松不开
•A.松锁的弹簧压合过紧或碟簧断裂,导致刀杆伸 缩量不够。
刀库故障
1.刀库不能转动的原因可能有:
•①联接电机轴与蜗杆轴的联轴器松动;
•②变频器故障,应检查变频器的输入、输出电压是 否正常; •2•.③ 刀库PL转C无不控到制位输的出原,因可可能能是有接:口板中的继电器失效; •3••.④ 刀电套动机不机械能转连夹动接紧故过刀障紧具,;原传因动可机能构是误差。 ••⑤A.电刀网套电上压的过调低整。螺钉松动。
⑷经常检查刀库的回零位置是否正确,检查机床主轴回换 刀点位置是否到位,发现问题要及时调整,否则不能完成换 刀动作。
⑸要注意保持刀具刀柄和刀套的清洁。 ⑹开机时,应先使刀库和机械手空运行,检查各部分工作 是否正常,特别是行程开关和电磁阀能否正常动作。检查机 械手液压系统的压力是否正常,刀具在机械手上锁紧是否可 靠,发现不正常时应及时处理。
(5)主轴系统有问题,刀具是靠碟簧通过拉杆和弹簧卡头而将刀具柄尾端 的拉钉拉紧的;松刀时,液压缸的活塞杆顶压顶杆,顶杆通过空心螺钉 推动拉杆,一方面使弹簧卡头松开刀具的拉钉,另一方面又顶动拉钉, 使刀具右移而在主轴锥孔中变“松”。
主轴系统不松刀的原因有以下5点: ①刀具尾部拉钉的长度不够,致使液压缸虽已运动到位,而仍未将刀具 顶“松”; ②拉杆尾部空心螺钉位置起了变化,使液压缸行程满足不了“松刀”的 要求; ③顶杆出了问题,已变形或磨损; ④弹簧卡头出故障,不能张开: ⑤主轴装配调整时,刀具移动量调得太小,致使在使用过程中一些综合 因素导致不能满足“松刀”条件。
自动换刀装置与离心泵中的故障分析和处理

2 0 1 3年第 1 期
自动换刀装置与离心泵 中的故 障分析和 处理
董 哲
北京 1 0 2 4 0 3 ) ( 北 京金 隅科技 学 校机 电系
摘 要
X H7 1 5型立式加工中心 自动换刀装置和单级离心泵的典型故障为例, 介绍 了故障诊断及排除故障的处理
方法 。讨论 了导致故障的原因 ,总结出排除 C NC 立式加工中心和单级单吸离心泵故障的经验,并提 出了相应 的
改 进 措 施 与 方 法 ,从 而 提 高 了工 作 效 率 。 关键词 立 式 加 工 中 心 自动 换 刀 装 置 A T C 单 级 单 吸 离 心 泵
1 C N C立 式 加工 中心 A T C故 障诊 断与处 理 方法
C NC 立 式 加 工 中 心 自 动 换 刀 装 置 A T C ( Au t o ma t i c t o o l c h a n g e r ) 是加工 中心 上必 不 可少 的
一
主轴
旦感 应 到低 于其所 设 定 的压 力值 时,立 即停止 运
图 1 双臂 回转机械手拔刀
行 的程 序指 令 ,A T C拔 刀 的动 作停 止 ,换 刀 失败 。
5 7
精密 制造 与 自动化
2 0 1 3年第 1 期
双 臂 回转机械 手 为 了防止 刀具 掉落 ,在刀 臂活 动 手 上安装 机械 自锁机 构 , 其 工作 原理 如 图 2所示 。
机的额 定压力,即可确保正常工作 。机械手刀臂 如何 复位 呢 ?在 设 备 顶 部 ,打 开 A T C 电动机 的防
护盖 ,用 扳手 人为地 完 成后续 动 作 ,使 刀臂 复位 ; 然 后 ,在 系 统 参 数 中完 成 以下 各 个 步 骤 : ( 1 ) 在
数控机床自动换刀系统的故障排除方法

数控机床自动换刀系统的故障排除方法数控机床自动换刀系统是现代机械加工中广泛使用的一种自动化装置,它能够提高生产效率和产品质量。
然而,在使用过程中难免会遇到故障问题,影响机床的正常运行。
本文将介绍数控机床自动换刀系统常见的故障排除方法。
一、故障现象:自动换刀系统无法自动完成换刀操作1. 检查刀具传感器:刀具传感器是检测刀具是否到位的关键装置。
首先检查传感器线路是否插好,有无松动;其次检查刀具传感器表面是否有污物或划痕,若有则需及时清洁或更换;最后检查传感器的供电电压是否正常。
2. 刀库定位故障:自动换刀系统需要将刀具准确地定位到刀库中的刀位,因此刀库定位的故障也是常见的问题。
首先检查刀库定位传感器是否工作正常,是否精度偏差过大。
若存在问题,应及时调整或更换传感器,确保定位的准确性。
此外,还要检查刀库定位系统的传动装置,如传动带、减速器等,是否运转正常。
3. 伺服系统故障:自动换刀系统的运动控制通常采用伺服电机,故障率相对较高。
若自动换刀无法完成操作,首先应检查伺服电机的供电线路是否正常,电压是否稳定。
其次,检查伺服驱动器的参数和通信连接是否正确,例如检查伺服电机的编码器信号是否清晰稳定。
如果有任何疑问,应及时联系专业人员进行维修和调试。
二、故障现象:自动换刀时出现刀具损坏或偏位问题1. 刀具锁紧故障:机床换刀时,刀具必须牢固地锁定在刀柄上,否则会导致刀具损坏或偏位。
检查刀具锁紧装置是否松动或磨损严重,必要时及时更换。
同时,应定期检查并调整刀具锁紧力度和锁紧角度,确保刀具的可靠固定。
2. 刀具夹持装置故障:刀具夹持装置是保证刀具位置和刚性的重要部件。
若出现换刀时刀具不稳定或偏位的情况,首先检查夹持装置是否松动或磨损,是否需要更换。
同时,在使用过程中要注意清洁夹持装置,避免灰尘或切削液的堆积对其性能造成影响。
三、故障现象:自动换刀速度慢或卡刀现象1. 刀盘液压系统故障:自动换刀时如果液压系统故障,可能会导致速度慢或卡刀现象。
加工中心自动换刀故障分析

—
—
圈
——_ Ac { T 目 i
1
电路 中 ,使 用 两只限 位开关 ¥ 3 1 1和 ¥ 3 1 2作 为 A C的位 置 开关 ,前 者 为 常开 触 点 ,后 者 用 常 闭 T 触点 ,两 者 串联 后接 到 X 06点 上 。进 一 步检查 发 2. 现 ¥3 、¥3 、Z轴原点减 速 开关 ¥ 3 、Z轴过 程 11 12 10
X 06的信号 为 1 2. ,这 时 可 正 常换 刀 。在 确 定换 刀
位 置 的两 开关及其 挡铁 撞块 良好 的前 提下 ,如果 参 随之 上移 ,主轴 刀位 上移 ,在换 刀机构 位置 不变 的 考 点上 移或 下移超 过 一定 范 围 ,¥ 3 和 S 3 11 1 2两 开
4 . 2 辊 槭I ^ ( 却 I ) 2 0 冷 0 2年 第 i 期
能 是 1状态 ,换 刀条件 不 时 ,都将 影 响 自动换 刀的 正常进行 。 满 足 ,此时 如果换 刀将 出现 1 1 0 9号报警 。 通 过 以上分 析 和现 场 检 查 ,换 刀 出现 1 1 0 9报 所 谓机床 参考 点 ,就 是机 床 的电气原 点 与机 械 警 的原 因是 机械传 动链 中 有相对偏 移 的现象 。故 障 原 点相重 台 的点 。 在本 机 床 中 ,其 z 轴 的机 械 原 处 理 步 骤 如 下 :
确定 。如 图 2中所示 A.一般小 于 0 5 .mm。显 然 ,
机床 的换 刀 点 与 机 床 某 一 轴 的参 考 点关 系非 常 密 硬件急停 开关及 使 用 一只 四组 的机 床 限位 开关 ,其 切 。
加工中心常见换刀故障的分类总结及排除方法

加工中心常见换刀故障的分类总结及排除方法加工中心已广泛应用于机加生产线中。
在当今时代,任何自动化生产设备都与数控技术密切关联,从数控设备的特征看,在其开发、生产、销售到使用与维护的过程中,都不可避免地涉及到许多相关领域和交叉学科。
因此,学习、理解和掌握数控技术,是从事加工行业人士的必经之路。
为了尽是减少加工中心的故障停机时间,根据个人多年的维修经验,针对加工中心故障频率较高的自动换刀装置部分,总结了一些快速诊断和查找故障的方法。
首先,加工中心常见的换刀方式分为带机械手和不带机械手:带机械手的加工中心换刀动作顺序为①主轴定位;②Z轴运行至换刀点;③刀套向下;④刀臂旋转60°;⑤主轴松刀吹气;⑥刀臂向下拉刀,然后旋转180°;⑦刀臂向上,主轴夹刀;⑧刀臂旋转至原点;⑨刀套向上回位,换刀完毕。
不带机械手的圆盘式刀库,换刀动作顺序为:①主轴定位;②Z轴运行至换刀点;③刀盘旋转至目标刀号;④Z轴向下至原点;⑤换刀完毕。
根据以往维修经验总结,自动换刀装置在换刀时,常见故障有以下几种:1、刀套动作位置错误,气缸故障2、刀臂夹不紧刀,发生掉刀3、主轴拉芯打不开,刀取不下来4、刀臂位置错误,不能刹车定位5、刀库乱刀6、刀库原点丢失7、刀库电机过载,刀臂电机过载8、刀库位置传感器损坏9、不执行换刀动作10、刀具没有夹紧11、主轴刀具不能夹紧到位下面就一些具体的故障排除方法进行总结:1、主轴刀具不能夹紧到位。
故障现象(1):刀具送入主轴时不能安全进入夹爪。
原因:①打杆与夹爪拉杆之间距离大于5mm。
②主轴换刀压力不够。
排除方法:①调整打杆处的调整螺母,使其与拉杆之间距离1~5mm以内。
②检查换刀液压油是否足够;气液缸及其管路是否存在泄漏;压缩空气压力是否达到0.392Mpa以上。
若有上述现象,则检修,使主轴换刀压力达到3.92~6.868Pma。
故障现象(2):工件加工质量变坏,如钻孔出现圆柱度变坏等。
数控机床常见故障
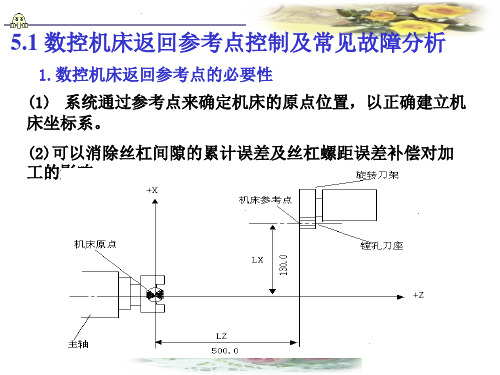
5.4 数控机床操作中常见故障及诊断方法
3) 熔断器F14熔断故障诊断
熔断器F14用来实现系统内部(各印刷电路板单元)、电源单元内部 +24E 电路及机床侧信号控制输入电路短路保护的 。当 F14 熔断 时 ,CRT 上将显示系统“ 950” 报警号 , 电源单元状态指示灯 PIL 亮 (故障状态指示灯 ALM 不亮) , 系统主板故障指示灯 L2 亮。产生故 障原因可能是: ① 系统内部+24E电路短路(包括电源单元内部电路)。 ② 机床侧+24E接线对地短路。 可以通过拔开系统 I/O 板的所有电缆接头后 , 测量系统 +24E 对地电 阻,当测量的电阻为 0 时,则故障在系统内部 +24E短路(需要更换相 应的印刷电路板)。如果测量的电阻为100Ω 左右时,则故障在机床 侧接线短路(详细检查机床侧所有的+24E接线)。 F14的规格为A60L-0001-0046(5A)。
熔断器F11 、F12用来实现电源单元输入侧电路短路保护的。 当F11、F12熔断时,CRT不亮,电源单元状态指示灯 PIL和故障 状态指示灯ALM不亮。产生故障原因可能是: ① 浪涌吸收器VS11故障。 ② 整流块DS11击穿短路或电容C12、C13严重漏电。 ③ 开关管Q14、Q15击穿短路或保护二极管D33、D34开路。
5.1 数控机床返回参考点控制及常见故障分析
1.数控机床返回参考点的必要性 (1) 系统通过参考点来确定机床的原点位置,以正确建立机 床坐标系。 (2)可以消除丝杠间隙的累计误差及丝杠螺距误差补偿对加 工的影响。
- 1、下载文档前请自行甄别文档内容的完整性,平台不提供额外的编辑、内容补充、找答案等附加服务。
- 2、"仅部分预览"的文档,不可在线预览部分如存在完整性等问题,可反馈申请退款(可完整预览的文档不适用该条件!)。
- 3、如文档侵犯您的权益,请联系客服反馈,我们会尽快为您处理(人工客服工作时间:9:00-18:30)。
例4.刀库报警的故障维修
故障现象:一台配套OKUMA OSP700系统,型号为XHAD765的数控机床,出现“2722、刀库刀套号0”报警。
例2.刀具设置错误报警的故障维修
故障现象:一台配套OKUMA OSP700系统,型号为XHAD765的数控机床,换班后,操作工设置刀具表时,显示“2714刀具数据设定出错”报警。
分析及处理过程:查看刀具刀位表,所要设3号刀位表中确实没有,设入即报警,估计该号刀可能在主轴上,而主轴却是其他刀具。再查看刀具表其他页面,发现3号刀数据前有一红星号,证实3号刀确实应在主轴上。手动将3号刀换上主轴,MDI方式下执行M61、M63指令将主轴上刀具还回刀库后,再打开刀具刀位表, 3号刀已显示在当前刀位,证实判断。经询问,交班前,前一班的操作工在手动换刀方式下用其他刀临时将3号刀换下,交班后又未交待,故造成人为故障。
分析及处理过程:该报警的含义为“刀库刀套号的数据不定”。切换到手动运行方式,打开刀库门,按上行或下行键,让刀库过一次零点,故障未能排除;打开PLC 数据查各开关状态,发现IMGRCT信号有闪烁,怀疑接触不良,关机将刀库内各传感器插头拔出,发现进油。清除油污再插好,开机后故障排除。
例5~例6.刀库门报警的故障维修
例1.换刀故障的故障维修
故障现象:一台配套OKUMA OSP700系统,型号为XHAD765的数控机床,换刀过程中,机械手未将主轴刀具拔出,随后显示2873“交换臂拔出检测器异常”报警,同时主轴负载逐渐增加,到80%时被迫关机。
分析及处理过程:按下急停钮,给CNC上电,在自动运行方式下输入“CHGCOND”,随后显示方式画面,将光标移到测试方式,按F1方式设定,断电后再上电,按软键PLC测试→扩展→找到调试画面,找到610参数将其改为0,按参数设定键,将任选参数16Bit7改为1,翻页将任选参数56BIT7改为 1。切换到手动方式,同时按下ATC、互锁解除两键点亮ATC灯,按扩展→PLC运行。这时机床应能起动,翻到M06调整画面,查看换刀调整画面将 EACH OPERATION POSSIBLE改为1,再先后将SPINDLE TOOL UNCLAMP (主轴松刀)、ARMFRONTMOVE (手臂向前)菜单COM位设为1,按单步退执行,如果刀具非机械卡死,则用小橡皮榔头轻轻敲击刀柄,刀柄应从主轴拔出,然后如上所述设置执行 RIGHT FINGER UNCLAMP(右手指松)、LEFT FINGER UNCLAMP(左手指松),将手臂上刀柄取下,然后将手臂各动作调整到准备状态,再将EACH OPERATION POSSIBLE改为0退出,按参数设定将任选参数16Bit7改为1,任选参数56Bit7改为0,同时按ATC、互锁解除两键将ATC灯熄灭。这时就可按常规检查刀具未拔出是油压低还是刀柄拉钉、或是刀柄、松刀液压缸引起。本例中经查发现油压偏低,将液压泵压力略调高0.2MPa后故障排除。调试正常后再将610号参数恢复到原来状态,找到方式转换画面,将方式设定为通常状况,断电开机后系统正常起动。
例5.故障现象:一台配套OKUMA OSP700系统,型号为XHAD765的数控机床,换刀过程中出现2834“刀库关门检测器异常”报警,刀库门未关上,随后出现1728“刀库防护门电动机断路器”报警。
分析及处理过程:出现“2834,刀库关门检测器异常”报警,原因有:刀库门未关上,超时报警,传感器SQ8不良或线路不良。根据故障现象,估计本例中刀库门未关上应该是刀库门关上动作超时报警。据操作工介绍,刀库门近期动作迟缓、停顿,似乎很费力,而1728报警说明刀库电动机过载,刀库门卡滞。关机后将刀库门驱动电动机传动带拆下,用手推拉刀库,确是有卡屑:用油冲洗,直到用手推拉灵活自由后,将刀库门关上,装上传动带。打开电柜,将热继电器FRM6复位,开机,将参数P16bit7设定为1,将P56bit7设定为1;再切换到手动运行方式,按“ATC+互锁解除”,ATC灯亮,按扩展→PLC测试进入M06调整方面,设EACH OPERATION POSSIBLE为1,设 MAGAZINE DOOROPEN为1,按单步退,打开刀库门,再设MAGAZINEDOOR CLOSE为1,按单步退,如此多次,刀库门开关正常;再将M06调整画面恢复到准备状态,按“ATC+互锁解除”,关闭ATC灯,设定参数P16 Bit7为1,P56 Bit7为0,切换到MDI方式,用 T#、M06指令换刀正常。
例6.故障现象:一台配套OKUMA OSP700系统,型号为XHAD765的数控机床,故障现象同上例。
分析及处理过程:关机后,拆下刀库门电动机传动带,用手推拉刀库门很轻松,无卡滞现象,负载很小,也不应是传动带松动的问题(传动带松动不会引起刀库门电动机过载保护)。查电动机供电正常,于是怀疑电动机本身的问题;送电开机按上例进入M06调整方面,打开、关闭刀库门,由于传动带未安装,这时需人为用手模拟将刀库门打开或关闭,同时观察刀库门电动机轴的转动情况,发现电动机轴转动有卡滞,证实电动机部分确有问题。断电关机,将电动机拆下检查,该电动机为普通微型三相异步电动机,在轴端加了一级电磁抱刹,结构原理类似交流伺服电动机上的电磁刹车。在电动机要运转时,电磁线圈级通电吸合铁心,松开刹车,电动机带动刀库门运转;动作结束,电磁线圈断电,弹簧将刹车抱紧。如果该电磁刹车不良,则也会导致电动机过载。将电磁刹车拆下检查,机械正常,用手拧电动机轴正常,用表测电动机绕组,无不平衡及碰壳短路现象:将电磁抱刹接上96V直流电源,观察衔铁未吸合到位,正常情况,通电后铁心应清脆地吸合;铁心未吸合到位,刹车不能完全解除,导致电动机过载;因为电压正常,而电磁力不足,说明电磁线圈有点问题。由于配件一时不易购到,临时将刹车弹簧加载螺钉调松,到铁心能清脆吸合即可;再安装回电动机,接通96V直流电,用手拧输出轴,手感轻松灵活。将该电动机装回机床,装上传动带,按上例,再调整刀库门,正常,恢复状态,退出后到MDI方式下,换刀正常.
例3.换刀错误的故障维修
故障现象:一台配套OKUMA OSP700系统,型号为XHAD765的数控机床,换刀中1号大刀未插回大刀刀位,大刀刀位插着其他刀,实际刀号刀位与机床控制系统中刀号刀位不符,即换刀错误,机床无报警,幸亏操作工细心,及时发现停机。
分析及处理过程:换刀错误是一种危险的故障,由于无报警,机床将继续工作,直到发生设备事故报警。由于换刀与众多位置开关和PLC控制程序及CNC处理过程有关,应重点检查这几部分。手工将实际刀具刀位调整到与控制系统中的一致,再执行换刀,发现除换1号刀外,其他换刀过程均正常。手动方式下,打开刀库侧门,按刀库上行或下行键,旋转刀库刀链,观察刀位表中当前刀位变化,发现在1号与30号刀位过渡时,刀位显示与实际刀位相差一个刀位,原来是刀库在过零点时出现刀位错误。关机后检查零点开关插头、刀库旋转计数开关插头与FUB-P4M4相关插头,发现进油。将插头清理后再重新插好,过20min再开机,换到手动方式,打开刀库门。手动上行、下行移动刀库,观察刀库在过零点时刀位显示正常,再切换到MDI方式,输入T1M6执行换刀,再输入T30 M6执行换刀。经查实际刀位刀号与刀位刀具表中一致,进行正常加工,未出现错误。