聚氨酯实用配方详细含硅油小料配比
聚氨酯胶水配方
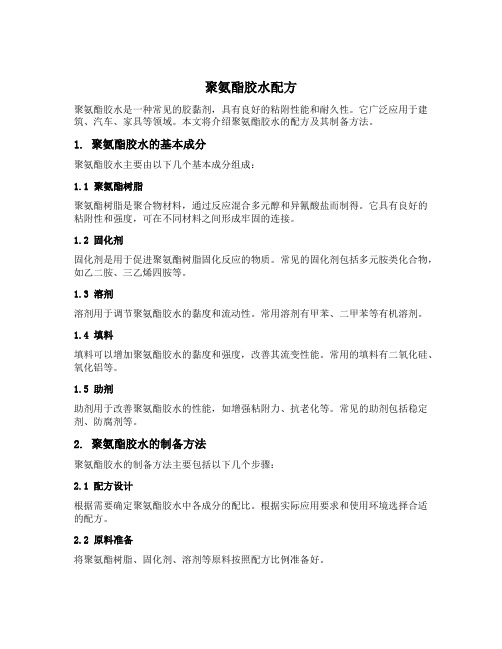
聚氨酯胶水配方聚氨酯胶水是一种常见的胶黏剂,具有良好的粘附性能和耐久性。
它广泛应用于建筑、汽车、家具等领域。
本文将介绍聚氨酯胶水的配方及其制备方法。
1. 聚氨酯胶水的基本成分聚氨酯胶水主要由以下几个基本成分组成:1.1 聚氨酯树脂聚氨酯树脂是聚合物材料,通过反应混合多元醇和异氰酸盐而制得。
它具有良好的粘附性和强度,可在不同材料之间形成牢固的连接。
1.2 固化剂固化剂是用于促进聚氨酯树脂固化反应的物质。
常见的固化剂包括多元胺类化合物,如乙二胺、三乙烯四胺等。
1.3 溶剂溶剂用于调节聚氨酯胶水的黏度和流动性。
常用溶剂有甲苯、二甲苯等有机溶剂。
1.4 填料填料可以增加聚氨酯胶水的黏度和强度,改善其流变性能。
常用的填料有二氧化硅、氧化铝等。
1.5 助剂助剂用于改善聚氨酯胶水的性能,如增强粘附力、抗老化等。
常见的助剂包括稳定剂、防腐剂等。
2. 聚氨酯胶水的制备方法聚氨酯胶水的制备方法主要包括以下几个步骤:2.1 配方设计根据需要确定聚氨酯胶水中各成分的配比。
根据实际应用要求和使用环境选择合适的配方。
2.2 原料准备将聚氨酯树脂、固化剂、溶剂等原料按照配方比例准备好。
2.3 混合反应将聚氨酯树脂和固化剂按照一定比例混合,并加入适量的溶剂进行搅拌反应。
反应时间和温度会影响胶水的性能,需要根据具体情况进行控制。
2.4 填料添加在混合反应过程中,适量的填料可以根据需要进行添加,提高胶水的黏度和强度。
2.5 助剂添加在混合反应过程中,根据需要可以添加适量的助剂,改善胶水的性能。
2.6 检测和调整制备好的聚氨酯胶水需要进行一系列的检测,如黏度、粘附力、耐久性等。
根据检测结果对配方进行调整,以获得符合要求的胶水产品。
3. 聚氨酯胶水的应用领域聚氨酯胶水广泛应用于以下领域:3.1 建筑领域聚氨酯胶水可用于建筑材料的粘接和密封,如玻璃、金属、石材等材料之间的连接。
3.2 汽车制造聚氨酯胶水可用于汽车零部件的粘接,如车身板材、挡风玻璃等。
聚氨酯软泡配方

聚氨酯软泡的配方因所需硬度、密度和弹性等特性而异,以下提供了三种不同配方的聚氨酯软泡:
1、密度为8kg/立方米的软泡配方:
聚醚:100份
水:7份
硅油:2.8份
辛酸亚锡:0.7份
胺催化剂:0.17份
二氯甲烷:30份
TDI指数:117(即79.7+8.7=76.61.17=89.6)
2、密度为12kg/立方米的软泡配方:
聚醚:100份
水:6份
硅油:1.5份
辛酸亚锡:0.3份
胺催化剂:0.14份
二氯甲烷:15份
TDI指数:120
3、密度为16kg/立方米的软泡配方:
聚醚:100份
水:4.9份
硅油(l-580):1.3份
辛酸亚锡:0.3份
a33催化剂:0.12份
二氯甲烷:9.3份
填料:8份
TDI指数:62
这些配方仅供参考,实际生产中可能因材料品牌、环境温度和湿度等因素有所调整。
建议在专业人士指导下进行操作。
聚氨酯(PU)白料配方比例详解,双组分聚氨酯特点组成
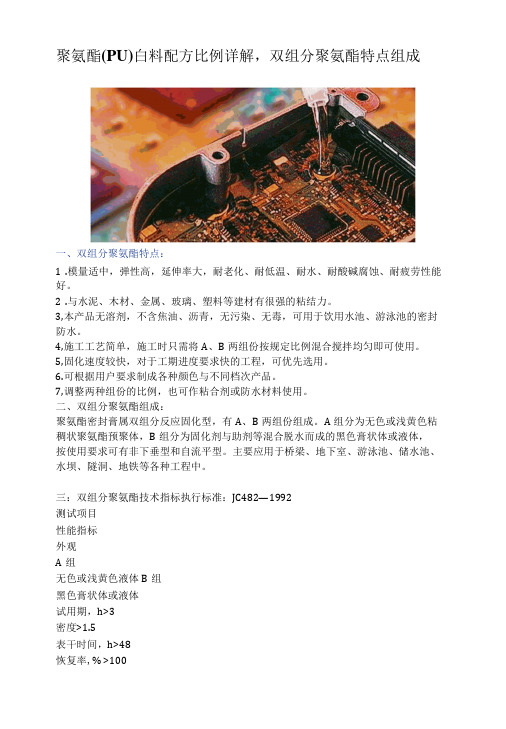
聚氨酯(PU)白料配方比例详解,双组分聚氨酯特点组成一、双组分聚氨酯特点:1.模量适中,弹性高,延伸率大,耐老化、耐低温、耐水、耐酸碱腐蚀、耐疲劳性能好。
2.与水泥、木材、金属、玻璃、塑料等建材有很强的粘结力。
3,本产品无溶剂,不含焦油、沥青,无污染、无毒,可用于饮用水池、游泳池的密封防水。
4,施工工艺简单,施工时只需将A、B两组份按规定比例混合搅拌均匀即可使用。
5,固化速度较快,对于工期进度要求快的工程,可优先选用。
6.可根据用户要求制成各种颜色与不同档次产品。
7,调整两种组份的比例,也可作粘合剂或防水材料使用。
二、双组分聚氨酯组成:聚氨酯密封膏属双组分反应固化型,有A、B两组份组成。
A组分为无色或浅黄色粘稠状聚氨酯预聚体,B组分为固化剂与助剂等混合脱水而成的黑色膏状体或液体,按使用要求可有非下垂型和自流平型。
主要应用于桥梁、地下室、游泳池、储水池、水坝、隧洞、地铁等各种工程中。
三:双组分聚氨酯技术指标执行标准:JC482—1992测试项目性能指标外观A组无色或浅黄色液体B组黑色膏状体或液体试用期,h>3密度>1.5表干时间,h>48恢复率,% >100低温柔性(℃) -30流变性下垂度(N)型<2mm拉伸粘接性最大拉伸强度,MPa >0.200最大拉伸率,% >200四、双组分聚氨酯施工方法:1)基层处理:用钢丝刷、棉纱等工具清理基层的浮浆皮、尘土等,若有油污需用有机溶剂擦洗干净,嵌填前保持基层表面干燥、洁净。
2)填塞衬垫材料:缝腔内要求填充作为衬垫材料的泡漠塑料,以保证嵌填尺寸满足设计要求3)嵌填双组份聚氨酯:按产品A:B=l:1.5的比例,充分混合均匀后,加入嵌缝枪或用腻子刀自下而上,或由前到后进行嵌填;嵌填要求饱满,尽量防止气泡及孔洞的形成;嵌填完成后,要在密封膏表干前,用腻子刀刮出平面或弧面并将多余的密封材料刮去。
4)为了得到更好的界面粘接效果,可以使用适当的底涂剂。
pu稀释剂标准配方

pu稀释剂标准配方PU稀释剂标准配方。
PU稀释剂是一种用于稀释聚氨酯涂料的溶剂,能够调整涂料的粘度和流动性,使其更易于施工和涂布。
在工业生产中,PU稀释剂的配方和使用对涂料的质量和性能有着重要的影响。
因此,了解PU稀释剂的标准配方是非常重要的。
一、配方原料。
1. 丙酮。
2. 甲苯。
3. 乙醇。
4. 丁醇。
5. 二甲苯。
6. 丙酮酸酯。
二、配方比例。
1. 丙酮,甲苯,乙醇=2,1,1。
2. 丙酮,丁醇=1,1。
3. 丙酮,二甲苯=1,1。
4. 丙酮,丙酮酸酯=2,1。
三、配方步骤。
1. 将丙酮、甲苯和乙醇按照2,1,1的比例混合搅拌均匀,得到第一组溶剂。
2. 将丙酮和丁醇按照1,1的比例混合搅拌均匀,得到第二组溶剂。
3. 将丙酮和二甲苯按照1,1的比例混合搅拌均匀,得到第三组溶剂。
4. 将丙酮和丙酮酸酯按照2,1的比例混合搅拌均匀,得到第四组溶剂。
5. 将以上四组溶剂按照一定比例混合搅拌均匀,即可得到PU稀释剂标准配方。
四、注意事项。
1. 在配方过程中,应注意安全防护措施,避免溶剂对人体和环境造成危害。
2. 配方时应严格按照比例进行,避免溶剂配方不当导致涂料性能下降或施工困难。
3. 配方后的PU稀释剂应密封保存,避免挥发和污染。
五、使用建议。
1. 在实际生产中,可以根据具体涂料的要求和施工环境的条件,适当调整PU稀释剂的配方比例,以获得最佳的稀释效果。
2. 在使用PU稀释剂时,应根据实际情况进行稀释,避免过量使用导致涂料流动性过强或干燥时间过长。
六、结语。
PU稀释剂的标准配方对于涂料的质量和性能有着重要的影响,正确的配方和使用方法能够提高涂料的施工性能和涂装效果。
因此,在生产和使用过程中,需要严格按照标准配方进行配制,并注意安全使用和储存,以确保涂料的质量和环境的安全。
聚氨酯胶粘剂配方
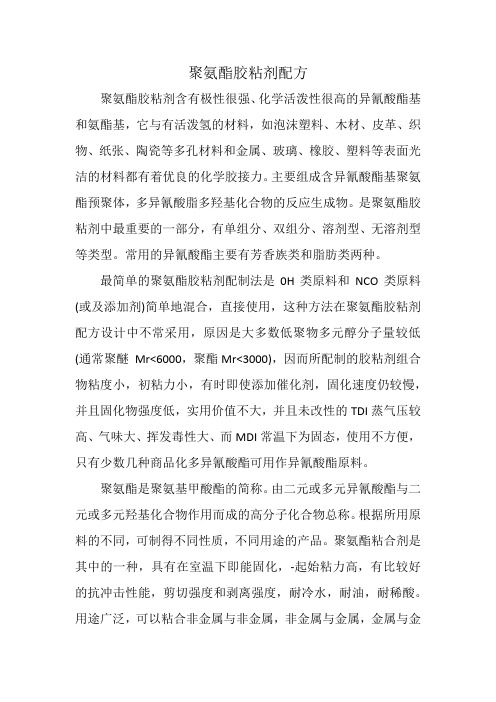
聚氨酯胶粘剂配方聚氨酯胶粘剂含有极性很强、化学活泼性很高的异氰酸酯基和氨酯基,它与有活泼氢的材料,如泡沫塑料、木材、皮革、织物、纸张、陶瓷等多孔材料和金属、玻璃、橡胶、塑料等表面光洁的材料都有着优良的化学胶接力。
主要组成含异氰酸酯基聚氨酯预聚体,多异氰酸脂多羟基化合物的反应生成物。
是聚氨酯胶粘剂中最重要的一部分,有单组分、双组分、溶剂型、无溶剂型等类型。
常用的异氰酸酯主要有芳香族类和脂肪类两种。
最简单的聚氨酯胶粘剂配制法是0H类原料和NCO类原料(或及添加剂)简单地混合,直接使用,这种方法在聚氨酯胶粘剂配方设计中不常采用,原因是大多数低聚物多元醇分子量较低(通常聚醚Mr<6000,聚酯Mr<3000),因而所配制的胶粘剂组合物粘度小,初粘力小,有时即使添加催化剂,固化速度仍较慢,并且固化物强度低,实用价值不大,并且未改性的TDI蒸气压较高、气味大、挥发毒性大、而MDI常温下为固态,使用不方便,只有少数几种商品化多异氰酸酯可用作异氰酸酯原料。
聚氨酯是聚氨基甲酸酯的简称。
由二元或多元异氰酸酯与二元或多元羟基化合物作用而成的高分子化合物总称。
根据所用原料的不同,可制得不同性质,不同用途的产品。
聚氨酯粘合剂是其中的一种,具有在室温下即能固化,-起始粘力高,有比较好的抗冲击性能,剪切强度和剥离强度,耐冷水,耐油,耐稀酸。
用途广泛,可以粘合非金属与非金属,非金属与金属,金属与金属,粘结力十分牢固。
其配方还体现在:一. 双组份的聚氨酯胶粘剂配方一:A组份甲苯二异氰酸酯(简称TDI)改性树酯(溶于醋酸乙酯成为溶液)100份B组份固化剂TDI的羟基化合物的改性物10~50份本法适用于金属与金属之间的粘合。
配方二:A组份100份B组份10份本法适用于一般材料之间的粘合。
配方三:A组份100份B组份5—10份本法适用于纸张、皮革、木材之间的粘合。
二、单组份的聚氨脂胶粘剂配方:蓖麻油38份甲苯二异氰酸酯11.75份苯乙烯49.75份过氧化二苯甲酰0.5份以上于20—80℃时溶化混合均匀。
聚氨酯配方
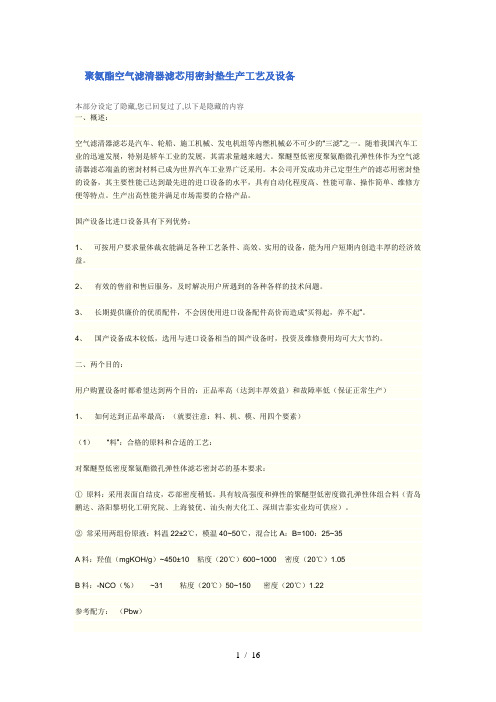
聚氨酯空气滤清器滤芯用密封垫生产工艺及设备本部分设定了隐藏,您已回复过了,以下是隐藏的内容一、概述:空气滤清器滤芯是汽车、轮船、施工机械、发电机组等内燃机械必不可少的“三滤”之一。
随着我国汽车工业的迅速发展,特别是轿车工业的发展,其需求量越来越大。
聚醚型低密度聚氨酯微孔弹性体作为空气滤清器滤芯端盖的密封材料已成为世界汽车工业界广泛采用。
本公司开发成功并已定型生产的滤芯用密封垫的设备,其主要性能已达到最先进的进口设备的水平,具有自动化程度高、性能可靠、操作简单、维修方便等特点。
生产出高性能并满足市场需要的合格产品。
国产设备比进口设备具有下列优势:1、可按用户要求量体裁衣能满足各种工艺条件、高效、实用的设备,能为用户短期内创造丰厚的经济效益。
2、有效的售前和售后服务,及时解决用户所遇到的各种各样的技术问题。
3、长期提供廉价的优质配件,不会因使用进口设备配件高价而造成“买得起,养不起”。
4、国产设备成本较低,选用与进口设备相当的国产设备时,投资及维修费用均可大大节约。
二、两个目的:用户购置设备时都希望达到两个目的:正品率高(达到丰厚效益)和故障率低(保证正常生产)1、如何达到正品率最高:(就要注意:料、机、模、用四个要素)(1)“料”:合格的原料和合适的工艺:对聚醚型低密度聚氨酯微孔弹性体滤芯密封芯的基本要求:①原料:采用表面自结皮,芯部密度稍低。
具有较高强度和弹性的聚醚型低密度微孔弹性体组合料(青岛鹏达、洛阳黎明化工研究院、上海彼优、汕头南大化工、深圳吉泰实业均可供应)。
②常采用两组份原液:料温22±2℃,模温40~50℃,混合比A:B=100:25~35A料:羟值(mgKOH/g)~450±10 粘度(20℃)600~1000 密度(20℃)1.05B料:-NCO(%) ~31 粘度(20℃)50~150 密度(20℃)1.22参考配方:(Pbw)聚醚多元醇 100 低粘度耐水解、高活性、高分子量聚醚及接枝聚醚扩链剂 2~5 降低粘度、提高互溶能力、改善物性,常用低分子二醇等表面活性剂 1~2 硅泡沫稳定剂催化剂0.2~1.0 胺及有机锡、催化发泡及凝胶反应水<0.1液化MDI指数 ~1.05③反应性:乳白期(CT):15~20S 起发期(RT):150~180S胶化期(GT):90~120S 脱模期(DMT):4~8min④物性:整体密度(kg/m3):400±150 硬度(邵A):40~50抗拉强度(MPa):≥0.7抗压强度(MPa):0.02~0.2断裂伸长率(%):≥10040%压缩变定(%):<10⑤为什么空气滤清器滤芯用密封垫采用聚醚型而不用聚酯型,采用微孔弹性体而不用一般软泡:ⅰ、聚醚型比聚酯型优点:常温下为粘度较低的液体,操作方便、工艺简单;价格较低;原液及混合液流动性均较佳,容易生成出表面光洁的制品;虽强度稍低但耐水解性大为提高,电化学性及手感较好,耐低温性及对氧、酸和碱的稳定性亦较佳。
聚氨酯的配方及工艺

线形热塑性聚氨酯原料用量(质量份)聚己内酯二醇(Mn:2000):20001,6-己二醇:112.0三羟甲基丙烷: 6.700TDI(80/20): 348.0有机锡催化剂: 1.2‰丁酮:1058聚氨酯油合成①配方:原料规格用量(质量份)醇酸树脂上步合成产品1000二甲苯聚氨酯级620.0甲苯二异氰酸酯工业级165.5二月桂酸二丁基锡分析醇 1.2‰丁醇5%②合成工艺:a. 将上步合成的醇酸树脂、50%二甲苯加入反应釜,升温至600C,在N2的继续保护下,将甲苯二异氰酸酯滴入聚合体系,约2h滴完;用剩余二甲苯洗涤甲苯二异氰酸酯滴加罐,并加入反应釜。
b. 保温1h,加入催化剂;将温度升至800C,保温反应;5h后取样测NCO含量,当NCO含量小于0.5%时,加入正丁醇封端0.5h。
降温,调固含、过滤、包装。
实例2聚酯基潮气固化聚氨酯的合成(1)配方:原料规格用量(质量份)聚己内酯二醇工业级,Mn:1500 3200聚己内酯三醇工业级,Mn:500 550.0二月桂酸二丁基锡化学纯0.5‰(以固体分计)二甲苯聚氨酯级2682甲苯二异氰酸酯工业级1230NCO理论含量:5.5%;NCO平均官能度:2.40。
(2)合成工艺:①依配方将聚己内酯多元醇加入聚合釜,加入50%的二甲苯共沸带水,至无水带出,通入N2保护,将温度降至600C。
②在N2的继续保护下,将甲苯二异氰酸酯滴入聚合体系,约2.5h滴完;用剩余二甲苯洗涤甲苯二异氰酸酯滴加罐,并加入反应釜。
③保温2h,加入催化剂;将温度升至800C,保温反应;2h后取样测NCO含量,当NCO含量稳定后(一般比理论值小0.5%),降温、过滤、包装。
1.羟基树脂合成实例实例1 羟基丙烯酸树脂的合成(1)配方:原料规格用量(质量份)丙二醇甲醚醋酸酯聚氨酯级111.0二甲苯(1)聚氨酯级140.0丙烯酸-β-羟丙酯工业级150.0苯乙烯工业级300.0甲基丙烯酸甲酯工业级100.0丙烯酸正丁酯工业级72.00丙烯酸工业级8.000叔丁基过氧化苯甲酰(1)工业级18.00叔丁基过氧化苯甲酰(2)工业级 2.000二甲苯(2)聚氨酯级100.0(2)合成工艺:①先将丙二醇甲醚醋酸酯、二甲苯(1)加入聚合釜中,通氮气置换反应釜中的空气,加热升温到1300C。
聚氨酯密封胶六个配方成分举例

聚氨酯密封胶六个配方成分举例聚氨酯密封胶六个配方成分举例2011-01-23 22:391.聚氨酯预聚体单组分湿固化聚氨酯密封胶是由端NCO基预聚体及填料、添加剂组成,其组成比例大致如下:预聚体35-65触变剂0-5填料及颜料20-40催化剂0-0.5增塑剂5-25稳定剂0-0.5溶剂0-10其他0-5双组分聚氨酯密封胶由主剂和固化剂两个组分组成。
其中主剂一般为端NCO基预聚体,固化剂一般由聚醚多元醇等活性氢化合物、填料、触变剂等添加剂组成,其组成比例大致为:聚醚多元醇15-20增塑剂0-15填料55-65催化剂0.05-1.5触变剂0-3其他0-5单组分胶料中的预聚体及双组分胶中的主剂和固化剂中的聚醚,是密封胶的基础聚合物(base-polymer)。
基础聚合物约占密封胶的35%-65%,它们固化后的性能对整个密封胶的性能有较大的影响。
与其他两大类弹性密封胶有机硅及聚硫相比,聚氨酯胶的一个特殊优点是聚氨酯树脂的原料组成和结构可变化范围大,因为聚氨酯分子设计的自由度大。
本节将介绍聚氨酯密封胶的主体成分--聚氨酯预聚体其组成结构与密封胶性能的关系。
2.端NCO基聚氨酯预聚体预聚体是PU密封胶配方的重要组成成分,大多数PU密封胶所用的基础聚合物为纯粹的端NCO聚醚型PU预聚体。
在其制备时通常通过选择其原料聚醚多元醇(一般为二元醇或三元醇)的分子量、二元醇及三元醇混合使用的比例、二异氰酸酯(TDI及MDI)的种类,以制备合适的预聚体。
在设计预聚体的制备配方时,一般要考虑使原料的NCO/OH摩尔比控制在1.5-2.5范围内,且所制备的预聚体的游离NCO质量百分含量在1%-4%之间。
据日本太阳星(Sunsta)技研株式会社伊藤等人报道,采用分子量在4000-8000之间的聚氧化丙烯-氧化乙烯三醇(含EO链节的量为20%以下)及过量的MDI制成预聚体A,用分子量2000-6000的PPG与过量TDI反应制成预聚体B。
聚氨酯白料配方

聚氨酯白料配方
聚氨酯是一种广泛应用的高分子材料,可用于制备各种产品,包括弹性体、涂料、胶粘剂等。
聚氨酯的白料配方取决于具体的应用和要求。
以下是一种常见的聚氨酯白料配方示例:
主要原料:
1. 聚醚多元醇或聚酯多元醇(聚氧化环丙烷、聚酯多元醇等)- 45%
2. 异佛尔酮二异氰酸酯或甲基苯异氰酸酯 - 40%
3. 反应助剂(催化剂、成链剂等) - 15%
配方过程:
1. 将聚醚多元醇或聚酯多元醇加入反应釜中,并在适当的温度下加热搅拌。
2. 逐渐加入异佛尔酮二异氰酸酯或甲基苯异氰酸酯,并在适当的温度下反应搅拌。
3. 加入反应助剂,如催化剂和成链剂,并继续搅拌反应。
4. 控制反应的时间和温度,使反应达到适当的程度。
5. 结束反应后,将白料熔融倾倒入模具或其他制品形成器具中。
6. 对制品进行固化或固化后的后处理,如修整、打磨等。
这只是一种常见的聚氨酯白料配方示例,实际配方可能会因具体应用、产品要求和原料的不同而有所不同。
在实际应用中,应根据具体需求进行合理的调整和优化。
聚氨酯实用配方(详细含硅油小料配比)

聚氨酯硬泡配方计算方法(实用)一:硬泡组合料里最需要计算的东西是黑白料比例(重量比)是不是合理,另一个正规的说法好像叫“异氰酸指数”是否合理,翻译成土话就是“按重量比例混合的白料和黑料要完全反应完”。
因此,白料里所有参和跟-NCO反应的东西都应该考虑在内。
理论各组分消耗的-NCO摩尔量计算如下㈠主料:聚醚、聚酯、硅油(普通硬泡硅油都有羟值,因为加了二甘醇之类的稀释,部分泡沫稳定剂型硅油还含有氨基)配方数乘以各自的羟值,然后相加得数Q,S1 = Q÷56100㈡水:水的配方量W S2 = W÷9㈢参和消耗-NCO的小分子物:配方量为K,其分子量为M,官能度为N S3 =K× N/M(用了两种以上小分子的需要各自计算再相加) S = S1+S2+S3 基础配方所需粗MDI份量[(S×42)÷0.30 ] ×1.05 (所谓异氰酸指数1.05)其实以上计算只是一个最基本的消耗量,由于黑白料反应过程复杂,实际-NCO消耗量肯定不止这个数,比如有三聚催化剂的情况,到底额外消耗了多少-NCO,这个没人说得清楚。
另外,聚醚里有水分,偏高0.1%就很严重;聚醚羟值也是看人家宣传单的,我见过有聚醚羟值范围跨度90mgKOH/g,那个计算数出来后只能参考,不能认真![试验设计]之“冰箱、冷柜”类本组合料体系重要要求及说明1、流动性要好,密度分布“尽量”均匀。
首先要考虑粘度,只有体系粘度小了,初期流动性才会好(主份平均粘度6000mPa.S以下,组合料350mPa.S以下),其次体系中的钾、钠杂离子要控制在一个低限(20ppm以内),从而可控制避免三聚反应提前,即:体系粘度过早变大。
如果流动性欠佳,发泡料行进至注料口远端就会出现拉丝痕致使泡孔结构橄榄球化,这个位置一定抗不住低温收缩。
2、泡孔细密,导热系数要低。
不难理解泡孔细密是导热系数低的第一前提,此时首先考虑加有403或某些芳香胺醚进入体系(它们所起的作用是首先和-NCO反应,其生成物和其它组份互溶、乳化稳定性提升,并保证发泡体系初期成核稳定,也就是避免迸泡,从而使泡孔细密)其次聚醚本身单独发泡其泡孔结构要好(例如以山梨醇为起始的635SA比蔗糖为起始的1050泡孔要细密均匀得多,还有含有甘油为起始剂的835比1050细密,即便是所谓的4110牌号的聚醚,含丙二醇起始的比二甘醇的好。
聚氨酯配方

聚氨酯床垫配方及性能①为非芳香族的胺类催化剂。
②为改性的甲苯二异氰酸酯。
③60%的MDI与40% 的TDI (65/35)的混合物。
半硬泡自结皮PU泡沫配方配方组成(质量份)1# 2# 3# 4#聚醚多元醇100 100 100 100乙二醇7 -- 7 --1,4丁二醇-- 8 -- 8三亚乙基二胺 1.5 1.5 1.5 1.5F11 17 17 17 17液化MDI(1040指数)30-40(105) 30-40(105)液化MDI(1050指数)30-40(105) 30-40(105) 低密度低硬度高回弹PU泡沫塑料配方组成(质量份)1# 2# 聚醚100 100 水 2.4 2.4 二乙醇胺 1 2二(2-二甲胺基乙基)醚0.06 0.06 硅泡沫稳定剂0.06 0.06 T9 0.10 0.15 F11 5 5 TDI8020 30-50(103) 30-50(103)高回弹海绵配方供参考高活性聚醚多元醇....................100份TDl........................................43.4份DEOA....................................1.5份水.........................................3.5份L5333...................................1.0份A230.....................................0.23份D22.......................................0.04份慢回弹枕头配方1030=40330=503628=10水=3A33=0.8DMEA=0.52乙=1.5A1=0.153002=0.8141B=25TDI/MDI=2:1聚氨酯高回弹MDI组合料配方A33--0.3DMEA--0.62乙--0.53乙--0.3141B--1.5H20--0.155596-5005=3比1中硬度高回弹PU配方配方组成(质量份)1# 2#聚醚100 100水 2.4 2.8二乙醇胺 1.2 1二(2-二甲胺基乙基)醚0.08 0.08硅泡沫稳定剂0.4 0.4T9 0.15 0.15TDI8020 30-40(110)30-40(110)密度为8kg/m3 的软泡配方配方原料重量份数聚醚三元醇,羟值56 100水 6.6三乙烯二胺(33 %溶液) 0.18TEGOSTAB B8110硅油 3.8(非水介性的聚硅烷一聚氧烷共聚物高活性泡沫稳定剂,高施米特公司产品)幸酸亚锡0.4二氯甲烷34TDI 80/20 103密度,kg/m3 8低密度自结皮配方(座椅用)330N:55POP:45EG: 6A33:0.3DMEA: 0.45TEOA: 0.85A-1: 0.2B8681:0.5H20: 0.3141B: 12NE-113:48~50聚氨酯床垫的配方聚氨酯床垫配方及性能生产方式聚醚型“冷熟化”模塑软泡聚醚型“冷熟化”模塑软泡用途作各种坐垫作全泡沫家具配方/份聚醚(分子量为3000)100 聚醚(分子量为4800) 100 水3 水2.5三亚乙基二胺0.3 稳定剂1三乙胺0.4 三乙醉胺1交联剂①0.6 三乙胺0.4稳定剂1 三亚乙基二胺0.2异氰酸酯②46.4 异氰酸酯③39性能密度/(kg/cm3) 43 密度/(kg/cm3) 40拉伸强度/MPa 0.06 拉伸强度/MPa 0.06伸长率/% 135 伸长率/% 90压缩负荷(40%)/Pa 2352 压缩负荷(40%)/Pa 2156压缩变形(90%)/% 4.1 压缩变形(90%)/% 3回弹率/% 62 回弹率/% 70①为非芳香族的胺类催化剂。
软泡聚氨酯配方和原材料价格成本分析及节约方法
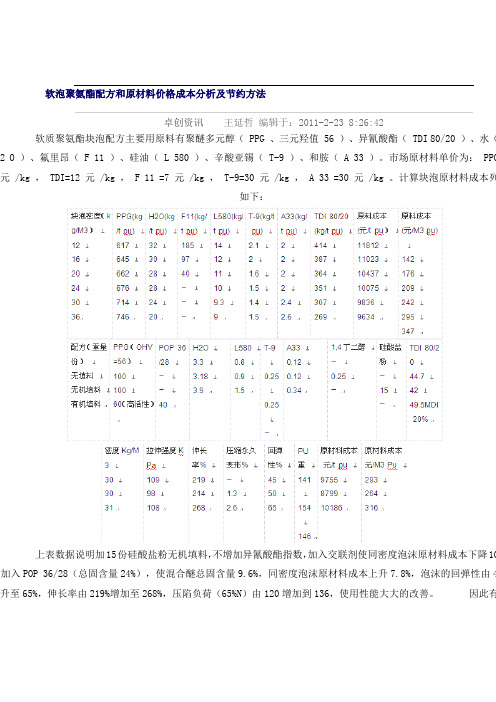
软泡聚氨酯配方和原材料价格成本分析及节约方法卓创资讯王延哲编辑于:2011-2-23 8:26:42软质聚氨酯块泡配方主要用原料有聚醚多元醇( PPG 、三元羟值 56 )、异氰酸酯( TDI 80/20 )、水(2 O )、氟里昂( F 11 )、硅油( L 580 )、辛酸亚锡( T-9 )、和胺( A 33 )。
市场原材料单价为: PPG 元 /kg , TDI=12 元 /kg , F 11 =7 元 /kg , T-9=30 元 /kg , A 33 =30 元 /kg 。
计算块泡原材料成本列如下:上表数据说明加15份硅酸盐粉无机填料,不增加异氰酸酯指数,加入交联剂使同密度泡沫原材料成本下降10加入POP 36/28(总固含量24%),使混合醚总固含量9.6%,同密度泡沫原材料成本上升7.8%,泡沫的回弹性由4升至65%,伸长率由219%增加至268%,压陷负荷(65%N)由120增加到136,使用性能大大的改善。
因此有定限量的填料加入配方,调整配方的合理性可以达到改进性能降低成本的目的。
接枝聚醚多元醇(POP)同聚醚混用混醚中总固含量5-10%时,软泡聚氨酯原料成本变化不大,可产品的回弹性、承载性高,有较高的使用价值和经济益。
鉴于前述三条降低软质块泡原料成本的途径,聚醚多元醇生产厂家将推出总固体含量5-12%,环氧乙烷7.8%羟值56mg KOH/g,平均分子量3000的三官能度的低接枝量聚合物多元醇。
软质块泡生产厂家将不断研制其他填料比适用性强的聚氨酯产品,以优质低价占领市场。
上述四组试验数据,用市场原材料价计算出块泡成本列表如下:通过表中成本比较,不难看出原料成本变化的趋势。
各生产厂家不断谋求低成本适用性强的软质聚氨酯配方一般通过三种途径:1 、选用抗氧化温度高的聚醚多元醇。
因聚醚多元醇配用的抗氧剂种类和浓度不同,其抗氧化温度一般在 1度至 190度之间变化,泡沫密度取决于发泡指数,在相同发泡指数时,发泡剂水和物理发泡剂不同的比例可以调节泡温度。
聚氨酯实用配方(详细含硅油小料配比)

聚氨酯实用配方(详细含硅油小料配比)聚氨酯硬泡配方计算方法(实用)一:硬泡组合料里最需要计算的东西是黑白料比例(重量比)是不是合理,另一个正规的说法好像叫“异氰酸指数”是否合理,翻译成土话就是“按重量比例混合的白料和黑料要完全反应完”。
因此,白料里所有参与跟-NCO反应的东西都应该考虑在内。
理论各组分消耗的-NCO摩尔量计算如下㈠主料:聚醚、聚酯、硅油(普通硬泡硅油都有羟值,因为加了二甘醇之类的稀释,部分泡沫稳定剂型硅油还含有氨基)配方数乘以各自的羟值,然后相加得数Q,S1 = Q÷56100㈡水:水的配方量W S2 = W÷9㈢参与消耗-NCO的小分子物:配方量为K,其分子量为M,官能度为N S3 =K× N/M(用了两种以上小分子的需要各自计算再相加) S = S1+S2+S3 基础配方所需粗MDI份量[(S×42)÷0.30 ] ×1.05 (所谓异氰酸指数1.05)其实以上计算只是一个最基本的消耗量,由于黑白料反应过程复杂,实际-NCO消耗量肯定不止这个数,比如有三聚催化剂的情况,到底额外消耗了多少-NCO,这个没人说得清楚。
另外,聚醚里有水分,偏高0.1%就很严重;聚醚羟值也是看人家宣传单的,我见过有聚醚羟值范围跨度90mgKOH/g,那个计算数出来后只能参考,不能认真![试验设计]之“冰箱、冷柜”类本组合料体系重要要求及说明1、流动性要好,密度分布“尽量”均匀。
首先要考虑粘度,只有4、相溶性。
指“聚醚、聚酯/硅油/水/催化剂/物理发泡剂”所组成的体系要互溶性好,均相稳定-----至少存放一段时间不能分层。
1)官能度构成及骨架类型。
原则上说官能度越高,所发泡体的物理性能数值(尺寸稳定、抗压强度等)就越“理想”,但往往官能度高的聚醚粘度偏大(多挂PO也能降低粘度,价格又下不来),所以,平均一下,4个官能度马马虎虎可以对付了;另外,如果聚醚体系中有芳香结构(苯环)引入,无疑也会提升泡体的物理性能。
聚氨酯弹性体参考配方

聚氨酯弹性体参考配方配方如下:1.聚酯多元醇:60-70份2.异佛尔酮二异氰酸酯(TDI):30-40份3.链延长剂:2-3份4.稳定剂:0.2-0.5份5.催化剂:0.5-1份6.塑料化剂:根据需要添加聚酯多元醇是聚氨酯制备的主要原料,可以选择聚酯多元醇根据需要的性能来确定。
常用的聚酯多元醇有聚酯多元醇A、聚酯多元醇B等。
聚酯多元醇具有良好的柔软性、耐磨性和低温性能。
异佛尔酮二异氰酸酯(TDI)是聚氨酯制备的硬段原料,可以通过调整其用量来控制聚氨酯材料的硬度和弹性。
在配方中,可以根据需要将TDI分为两个部分添加,一部分作为预聚体与聚酯多元醇反应,另一部分作为链延长剂与预聚体反应,从而得到所需的硬度和弹性。
链延长剂用于调节聚氨酯材料的分子量和柔软性,一般选择具有双官能团的分子作为链延长剂。
常用的链延长剂有乙二醇、丁二醇等。
稳定剂用于提高聚氨酯材料的稳定性,防止氧化和黄变等现象的发生。
可以选择有机锡化合物等作为稳定剂。
催化剂用于促进聚氨酯材料的硬化反应,常用的催化剂有二甲苯胺(DMA)、四乙基二氮唑(DABCO)等。
塑料化剂可以根据需要添加,用于调节聚氨酯材料的流动性和柔软性。
常用的塑化剂有聚醚、聚乙烯醇等。
配方制备过程如下:1.将聚酯多元醇、TDI和链延长剂按照配方比例混合搅拌,使其均匀混合。
2.添加稳定剂和催化剂,继续搅拌混合。
3.如有需要,可以添加塑化剂进行调节,继续搅拌混合。
4.将混合物倒入模具中,进行加热硬化过程,通常需要在150-200°C下进行。
5.根据需要,可以通过改变硬化温度和时间来调节聚氨酯弹性体的硬度和弹性。
以上是一种聚氨酯弹性体的参考配方和制备过程,需要根据具体需求进行调整。
在实际制备过程中,还需要进行反应的控制和工艺的优化,以获得所需的产品性能。
聚胺脂发泡小料配比
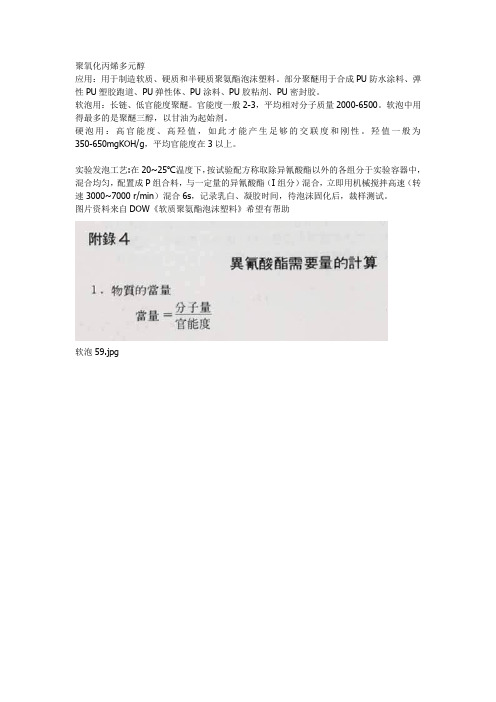
聚氧化丙烯多元醇
应用:用于制造软质、硬质和半硬质聚氨酯泡沫塑料。
部分聚醚用于合成PU防水涂料、弹性PU塑胶跑道、PU弹性体、PU涂料、PU胶粘剂、PU密封胶。
软泡用:长链、低官能度聚醚。
官能度一般2-3,平均相对分子质量2000-6500。
软泡中用得最多的是聚醚三醇,以甘油为起始剂。
硬泡用:高官能度、高羟值,如此才能产生足够的交联度和刚性。
羟值一般为350-650mgKOH/g,平均官能度在3以上。
实验发泡工艺:在20~25℃温度下,按试验配方称取除异氰酸酯以外的各组分于实验容器中,混合均匀,配置成P组合料,与一定量的异氰酸酯(I组分)混合,立即用机械搅拌高速(转速3000~7000 r/min)混合6s,记录乳白、凝胶时间,待泡沫固化后,裁样测试。
图片资料来自DOW《软质聚氨酯泡沫塑料》希望有帮助
软泡59.jpg
软泡60.jpg
软泡61.jpg
软泡62.jpg
软泡63.jpg
软泡64.jpg。
聚氨酯实用配方(详细含硅油小料配比)
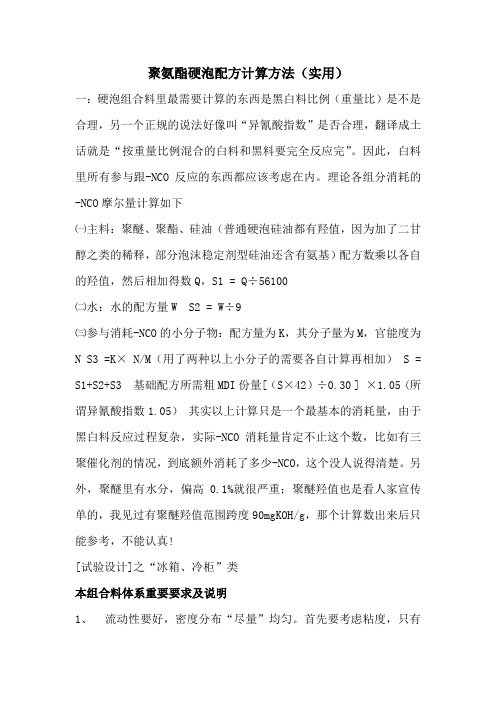
聚氨酯硬泡配方计算方法(实用)一:硬泡组合料里最需要计算的东西是黑白料比例(重量比)是不是合理,另一个正规的说法好像叫“异氰酸指数”是否合理,翻译成土话就是“按重量比例混合的白料和黑料要完全反应完”。
因此,白料里所有参与跟-NCO反应的东西都应该考虑在内。
理论各组分消耗的-NCO摩尔量计算如下㈠主料:聚醚、聚酯、硅油(普通硬泡硅油都有羟值,因为加了二甘醇之类的稀释,部分泡沫稳定剂型硅油还含有氨基)配方数乘以各自的羟值,然后相加得数Q,S1 = Q÷56100㈡水:水的配方量W S2 = W÷9㈢参与消耗-NCO的小分子物:配方量为K,其分子量为M,官能度为N S3 =K× N/M(用了两种以上小分子的需要各自计算再相加) S = S1+S2+S3 基础配方所需粗MDI份量[(S×42)÷0.30 ] ×1.05 (所谓异氰酸指数1.05)其实以上计算只是一个最基本的消耗量,由于黑白料反应过程复杂,实际-NCO消耗量肯定不止这个数,比如有三聚催化剂的情况,到底额外消耗了多少-NCO,这个没人说得清楚。
另外,聚醚里有水分,偏高0.1%就很严重;聚醚羟值也是看人家宣传单的,我见过有聚醚羟值范围跨度90mgKOH/g,那个计算数出来后只能参考,不能认真![试验设计]之“冰箱、冷柜”类本组合料体系重要要求及说明1、流动性要好,密度分布“尽量”均匀。
首先要考虑粘度,只有体系粘度小了,初期流动性才会好(主份平均粘度6000mPa.S以下,组合料350mPa.S以下),其次体系中的钾、钠杂离子要控制在一个低限(20ppm以内),从而可控制避免三聚反应提前,即:体系粘度过早变大。
如果流动性欠佳,发泡料行进至注料口远端就会出现拉丝痕致使泡孔结构橄榄球化,这个位置一定抗不住低温收缩。
2、泡孔细密,导热系数要低。
不难理解泡孔细密是导热系数低的第一前提,此时首先考虑加有403或某些芳香胺醚进入体系(它们所起的作用是首先与-NCO反应,其生成物与其它组份互溶、乳化稳定性提升,并保证发泡体系初期成核稳定,也就是避免迸泡,从而使泡孔细密)其次聚醚本身单独发泡其泡孔结构要好(例如以山梨醇为起始的635SA比蔗糖为起始的1050泡孔要细密均匀得多,还有含有甘油为起始剂的835比1050细密,即便是所谓的4110牌号的聚醚,含丙二醇起始的比二甘醇的好。
聚氨酯的配方
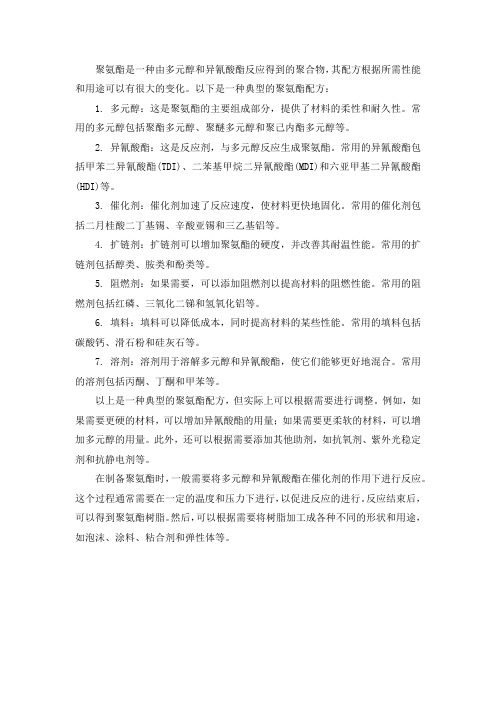
聚氨酯是一种由多元醇和异氰酸酯反应得到的聚合物,其配方根据所需性能和用途可以有很大的变化。
以下是一种典型的聚氨酯配方:1. 多元醇:这是聚氨酯的主要组成部分,提供了材料的柔性和耐久性。
常用的多元醇包括聚酯多元醇、聚醚多元醇和聚己内酯多元醇等。
2. 异氰酸酯:这是反应剂,与多元醇反应生成聚氨酯。
常用的异氰酸酯包括甲苯二异氰酸酯(TDI)、二苯基甲烷二异氰酸酯(MDI)和六亚甲基二异氰酸酯(HDI)等。
3. 催化剂:催化剂加速了反应速度,使材料更快地固化。
常用的催化剂包括二月桂酸二丁基锡、辛酸亚锡和三乙基铝等。
4. 扩链剂:扩链剂可以增加聚氨酯的硬度,并改善其耐温性能。
常用的扩链剂包括醇类、胺类和酚类等。
5. 阻燃剂:如果需要,可以添加阻燃剂以提高材料的阻燃性能。
常用的阻燃剂包括红磷、三氧化二锑和氢氧化铝等。
6. 填料:填料可以降低成本,同时提高材料的某些性能。
常用的填料包括碳酸钙、滑石粉和硅灰石等。
7. 溶剂:溶剂用于溶解多元醇和异氰酸酯,使它们能够更好地混合。
常用的溶剂包括丙酮、丁酮和甲苯等。
以上是一种典型的聚氨酯配方,但实际上可以根据需要进行调整。
例如,如果需要更硬的材料,可以增加异氰酸酯的用量;如果需要更柔软的材料,可以增加多元醇的用量。
此外,还可以根据需要添加其他助剂,如抗氧剂、紫外光稳定剂和抗静电剂等。
在制备聚氨酯时,一般需要将多元醇和异氰酸酯在催化剂的作用下进行反应。
这个过程通常需要在一定的温度和压力下进行,以促进反应的进行。
反应结束后,可以得到聚氨酯树脂。
然后,可以根据需要将树脂加工成各种不同的形状和用途,如泡沫、涂料、粘合剂和弹性体等。
- 1、下载文档前请自行甄别文档内容的完整性,平台不提供额外的编辑、内容补充、找答案等附加服务。
- 2、"仅部分预览"的文档,不可在线预览部分如存在完整性等问题,可反馈申请退款(可完整预览的文档不适用该条件!)。
- 3、如文档侵犯您的权益,请联系客服反馈,我们会尽快为您处理(人工客服工作时间:9:00-18:30)。
聚氨酯实用配方(详细含硅油小料配比)————————————————————————————————作者:————————————————————————————————日期:ﻩ聚氨酯硬泡配方计算方法(实用)一:硬泡组合料里最需要计算的东西是黑白料比例(重量比)是不是合理,另一个正规的说法好像叫“异氰酸指数”是否合理,翻译成土话就是“按重量比例混合的白料和黑料要完全反应完”。
因此,白料里所有参与跟-NCO反应的东西都应该考虑在内。
理论各组分消耗的-NCO摩尔量计算如下㈠主料:聚醚、聚酯、硅油(普通硬泡硅油都有羟值,因为加了二甘醇之类的稀释,部分泡沫稳定剂型硅油还含有氨基)配方数乘以各自的羟值,然后相加得数Q,S1 = Q÷56100㈡水:水的配方量W S2=W÷9㈢参与消耗-NCO的小分子物:配方量为K,其分子量为M,官能度为N S3=K× N/M(用了两种以上小分子的需要各自计算再相加) S = S1+S2+S3 基础配方所需粗MDI份量[(S×42)÷0.30 ] ×1.05 (所谓异氰酸指数1.05)其实以上计算只是一个最基本的消耗量,由于黑白料反应过程复杂,实际-NCO消耗量肯定不止这个数,比如有三聚催化剂的情况,到底额外消耗了多少-NCO,这个没人说得清楚。
另外,聚醚里有水分,偏高0.1%就很严重;聚醚羟值也是看人家宣传单的,我见过有聚醚羟值范围跨度90mgKOH/g,那个计算数出来后只能参考,不能认真![试验设计]之“冰箱、冷柜”类本组合料体系重要要求及说明1、流动性要好,密度分布“尽量”均匀。
首先要考虑粘度,只有体系粘度小了,初期流动性才会好(主份平均粘度6000mPa.S以下,组合料350mPa.S以下),其次体系中的钾、钠杂离子要控制在一个低限(20ppm以内),从而可控制避免三聚反应提前,即:体系粘度过早变大。
如果流动性欠佳,发泡料行进至注料口远端就会出现拉丝痕致使泡孔结构橄榄球化,这个位置一定抗不住低温收缩。
2、泡孔细密,导热系数要低。
不难理解泡孔细密是导热系数低的第一前提,此时首先考虑加有403或某些芳香胺醚进入体系(它们所起的作用是首先与-NCO反应,其生成物与其它组份互溶、乳化稳定性提升,并保证发泡体系初期成核稳定,也就是避免迸泡,从而使泡孔细密)其次聚醚本身单独发泡其泡孔结构要好(例如以山梨醇为起始的635SA比蔗糖为起始的1050泡孔要细密均匀得多,还有含有甘油为起始剂的835比1050细密,即便是所谓的4110牌号的聚醚,含丙二醇起始的比二甘醇的好。
聚醚生产的聚合催化剂不同,所生产出的聚醚性状也有差异:氢氧化钾催化的聚醚分子量分布比二甲胺催化的要窄。
另外:聚醚生产时的工艺控制-----温控、抽真空、PO--也就是环氧丙烷流量控制、PO原料质量、后处理等等-----也都会直接影响聚醚发泡的泡孔结构)第三,可以考虑加入一些可以改善泡孔细密度的聚酯成份。
第四,适当加入低粘度物调整总体粘度(如210聚醚)3、耐低温抗收缩性要好。
这个无须赘言。
一是官能度,总体平均要4以上。
其次是发泡体成型后空间交联点分布均匀(直观解释是:主聚醚反应活性尽量相差不大,连续的近似的空间结构要稳定得多。
)4、粘结性好。
所谓粘结性表面上是指泡沫体与冰箱、冷柜外壳和内胆之间的粘合,其实是指泡体柔韧性,以及抗收缩性,(水份用量、降低总体羟值,添加柔性结构成分,如210、330N之类都可以改进泡沫对壳体的粘附性)5、成本较低。
目前冰箱、冷柜行业竞争白热化,性能极佳价格昂贵的组合料没人用的起,所以我们必须为成本考虑(比如芳香聚酯价位要比聚醚的低,可以加一些。
)6、安全性。
这是对环戊烷体系的特别要求(至少环戊烷不象F11那样想加多少就加多少,不难理解加多环戊烷的更具有安全隐患)7、保证发泡生产工艺的连续稳定性冰箱、冷柜连续生产线一般控制很稳定,但不排除偶尔的工艺参数波动,比如料温、环境温度高个一两度,黑白料比例在小范围内波动等等,所以要求组合料有一定的“宽容性”.8、黑料配伍。
各款黑料自身性状、活性不同,那么,白料体系调整一下有时就显得异常必要。
(配合5005的没事,绝不代表与44v20可以任意切换)主聚醚聚酯的选取方向1)相溶性。
指“聚醚、聚酯/硅油/水/催化剂/物理发泡剂”所组成的体系要互溶性好,均相稳定-----至少存放一段时间不能分层。
2)官能度构成及骨架类型。
原则上说官能度越高,所发泡体的物理性能数值(尺寸稳定、抗压强度等)就越“理想”,但往往官能度高的聚醚粘度偏大(多挂PO也能降低粘度,价格又下不来),所以,平均一下,4个官能度马马虎虎可以对付了;另外,如果聚醚体系中有芳香结构(苯环)引入,无疑也会提升泡体的物理性能。
3)反应活。
含有伯羟基结构的聚醚(和诸如三乙醇胺之类的小分子交联剂)活性高,却多多少少会影响发泡反应的中后期流动性。
所以,其加入量一定要控制在某环围内。
4)羟值搭配。
根据水用量、黑白料比例预设,可以大体反算出主份平均羟值范围,一般为380-410mgKOH/g5)经济性。
不仅是指聚醚、聚酯采购价格低,还应综合其他方面考虑黑白料比例,毕竟现在黑料价格高企。
6)市售采购之方便性。
好不容易调整出一个配方,结果原料市面上只是你有用别人不会问津,除非财大气粗每月用量惊人,否则配料供货能不能保障就只得看“交情”浅薄。
匀泡剂(硅油)的选择1)与组合料其它成份的配伍性。
这个不难理解,否则,生产硅油的厂家就不会编出那么多型号了------什么F11型、141B型、环戊烷型、全水型、聚酯型、蔗糖聚醚型等等。
硅油型号选配得当,可以明显控制导热系数低限化。
2)与黑料的配伍性、核化能力。
这个关注的人不多。
其实多数情况下“泡孔不好”就是硅油对“黑白料整个体系的乳化能力不够”所致。
3)流动性。
能使发泡体系泡孔细密的硅油可以明显提升发泡流动性,同时另外一个佐证是:发泡速度略有加快。
4)稳定性及用量。
有些硅油遇见水、碱性催化剂、含氯发泡剂或含氯阻燃剂时会逐渐变质;有些则必须加大用量(用量2.5%以上)才会显示它是硅油。
5)价位。
能用22元/kg搞定的就不必去用进口的45元/kg,要知道每吨组合料中硅油14kg那差价就是过200元了。
水份额的确定1、粘结性。
水用量多,泡体表面偏脆,与壳面的粘结性就差,一般冰箱、冷柜料水用量1.7-2.3%(专指141B体系和环戊烷体系)2、物理发泡剂体系的选取。
现在到处喊着环保,141B早就说要限量使用了,可市面下居然还有F11型(或勾兑型F11)组合料交易。
水用量只好随行论价,F11型的---0.6/1.6,141B型的---1.7/2.2, 环戊烷型的---2.0/2.43、经济性.水确实很便宜的,不过它用多了,黑料量就得加上去,于是还是不合算的机会(自然,是使用组合料的客户买单。
催化体系确定1、前期要求。
以前很多朋友认为乳白起发慢一些,等料子稀哩哗啦地流到各自“岗位”底下后再直发起来。
其实不然,其一:液态料子极易从箱体缝隙中漏出去造成污物粘模;其二:影响泡孔细密度和整体结构,从而拔高泡体导热系数;其三:起发速度加快反而会加快发泡料行进速度。
一般说来,出枪乳白时间6-8秒最好。
2、中期流动。
在发泡定型期间,中期流动时间段(拉丝减去乳白时间)越长越好,可以保证泡体填充箱体各个角落,又不至于泡孔变形严重。
最理想的状态是拉丝开始前3-5秒钟,泡料已经充填到位,最远端排气孔有明显逸料出现。
3、后期固化。
这个要求不必太严,反正连续生产中模具不是冰冷的,如果生产线有保温炕道,不怕到期收不了庄稼。
4、建议搭配。
Am-1 + 环己胺。
工艺确认1、发泡体系确定:141B的还是环戊烷的。
水量/物理发泡剂量的范围预定2、首先闹清楚目标生产线的工艺细节:发泡机类型、灌注流量、灌注前的温控数值、炕道保温温控值及保温时间、箱体灌注口在哪及发泡料流经路线行程、灌注后合模封洞操作过程。
3、目前(工作)环境温度、湿度变化情况。
4、向现场作业员、质检员求询目前现行工艺、原料有什么缺陷和请他们提出什么其他具体要求。
具体试验1、相溶性:①100ml小烧杯加一短玻璃棒,归零,依次倒入主聚醚(聚酯)搅匀看是否透明。
②加入硅油、催化剂、水,搅匀,看是否透明。
③加入物理发泡剂搅匀看是否透明(注意搅拌后挥发的物理发泡剂要补回)。
④预配的组合料样品要存放至少3天透明不分层才好。
⑤组合料样分别放在35、15℃下贮存24hr看是否透明⑥有条件时,需要测设计中的组合料粘度(25℃及正常生产状态下的温度)看是不是粘度随温度变化有大幅度的波动。
2、抗收缩:自由发泡样1hr后切成规则方形体,量取定边尺寸后放在-20℃冰柜中24hr看尺寸变化情况,2%以内的线性收缩可以接受3、自由发泡:按设计的黑白料比例、温控执行自由发泡,关注料速、芯密度和拉丝痕迹。
4、流动性:自由泡密度、速度确定后,一定要进行流动性试验。
简易方法是:定量发泡料(一般为200g)搅匀后立即在发泡杯口套上稍大一点的长筒塑料袋,拉直垂直向上任由泡料向上生长直至定型(要两个人操作)。
杯口至顶高度L与料重G的比值将作为一个重要参数来评估组合料的流动性,L/G越大,流动性越好,此后还要分段测取芯密度作为辅助参考(自低向高密度差不能太大,否则流动性也不能视作良好,特别是最高点那一段)其实,如果试验做多了,在正常自由泡发泡时,可以看杯中残留泡的形状来大致判断流动性的优劣:泡提出杯后越象蘑菇越好,越象直棍则越差。
5、工艺条件宽容性:①执行预设温控+3、-3℃的发泡,看是否还保持良好的流动性及泡孔结构(“快料”与“慢料”的泡孔不能落差太大)②进行白料恒定量,黑料量+10%、-10%的自由发泡试验,常温下30min时泡体没有明显收缩的就算过得去。
[试产] 之“冰箱、冷柜”类这个简单了,整桶料子上机试产,按预定(或现实执行)的工艺条件生产,成品装机打冷,看箱体收缩情况和保温情况。
一般程序:试产箱中成品泡体要取样测试导热系数等综合数据。
现场需要微调的一般是:泡料温控、黑白料比例、添加催化剂、熟化温度调整。
仿木产品之组合料/工艺控制(内部讨论版) [白料体系要求及制品要求]1、白料粘度:涉及到出枪后的初始流动性(机发泡型)、搅拌混合效果(包括手工发泡型)以及出枪流量大小和黑白料比例,原则上不应高于2000mPa.S(25℃,以下同),高密度的(自由泡密度130kg/m3以上者)例外。
2、相容性:除非现配现用或是白料整桶上机边搅边打,白料应该均相透明不分层(如果选用浊点较低的硅油白料低温状态下也可能不透明,但不可以分层),手工料更是如此。
3、流动性:一般仿木料流动性要求不太高,这取决于其自身生产工艺的合理安排。