压力容器制造通用工艺规范
压力容器原材料检验通用工艺守则样本

压力容器原材料检验通用工艺守则样本压力容器是一种经过特殊设计和制造的装置,用于储存和运输高压气体、液体或固体。
由于容器内部承受着高压力,因此其原材料的质量和性能至关重要。
以下是压力容器原材料检验的一般工艺守则样本。
1.原材料选择:选择适用的原材料,如碳钢、合金钢、不锈钢等,根据容器的使用环境和工作条件来确定原材料的类型和规格。
2.原材料验收:接收原材料时,应对其进行质量检验。
检查原材料的化学成分、机械性能、外观等指标是否符合技术要求。
可以使用化学成分分析仪、拉伸试验机等设备进行检测。
3.材料切割:根据设计要求和材料规格,将原材料进行切割。
切割时应确保切割面光滑平整,无裂纹、间隙等缺陷。
4.材料加工:对切割好的材料进行加工,如冷冲压、热冲压、焊接等工艺。
加工过程中应注意避免产生过大的热变形和残余应力。
5.焊接:焊接是压力容器制造中最重要的工艺之一、焊接工艺应符合相关的规范和标准。
在焊接前,应对焊接材料进行质量检验,并选用适当的焊接材料和焊接工艺。
6.焊缝检验:焊接完成后,应对焊缝进行检验。
常用的焊缝检验方法有X射线检测、超声波检测、磁粉检测等。
通过检验,判断焊缝的质量是否符合要求。
7.热处理:对焊接完成的容器进行热处理,以消除焊接产生的残余应力,并提高材料的强度和韧性。
8.表面处理:对容器的表面进行处理,以提高其耐腐蚀性和美观度。
常用的表面处理方法有喷砂、热浸镀锌、电镀等。
9.容器测试:对已制造完成的容器进行压力测试、泄漏测试等。
通过测试,验证容器的密封性和安全性。
10.质量检验:对制造好的容器进行质量检验,包括外观检查、储罐容量测试、材料性能测试等。
以上是压力容器原材料检验的一般工艺守则样本。
严格按照这些守则进行原材料的选择、切割、加工、焊接、热处理和测试,可以确保压力容器的质量和安全性。
压力容器设计规范及制造要求
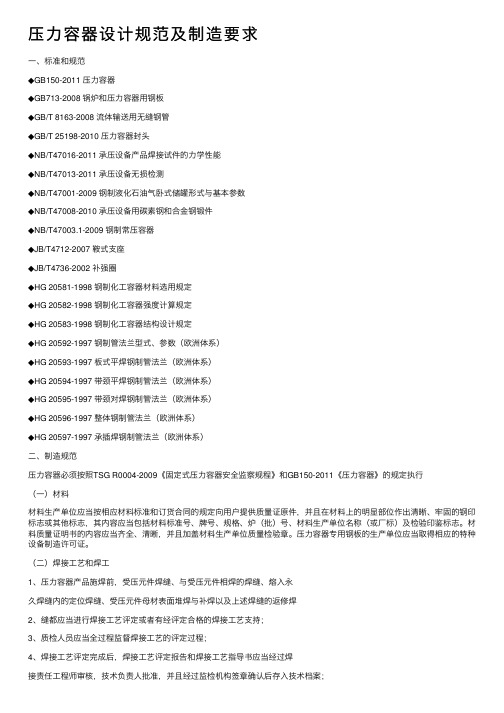
压⼒容器设计规范及制造要求⼀、标准和规范◆GB150-2011 压⼒容器◆GB713-2008 锅炉和压⼒容器⽤钢板◆GB/T 8163-2008 流体输送⽤⽆缝钢管◆GB/T 25198-2010 压⼒容器封头◆NB/T47016-2011 承压设备产品焊接试件的⼒学性能◆NB/T47013-2011 承压设备⽆损检测◆NB/T47001-2009 钢制液化⽯油⽓卧式储罐形式与基本参数◆NB/T47008-2010 承压设备⽤碳素钢和合⾦钢锻件◆NB/T47003.1-2009 钢制常压容器◆JB/T4712-2007 鞍式⽀座◆JB/T4736-2002 补强圈◆HG 20581-1998 钢制化⼯容器材料选⽤规定◆HG 20582-1998 钢制化⼯容器强度计算规定◆HG 20583-1998 钢制化⼯容器结构设计规定◆HG 20592-1997 钢制管法兰型式、参数(欧洲体系)◆HG 20593-1997 板式平焊钢制管法兰(欧洲体系)◆HG 20594-1997 带颈平焊钢制管法兰(欧洲体系)◆HG 20595-1997 带颈对焊钢制管法兰(欧洲体系)◆HG 20596-1997 整体钢制管法兰(欧洲体系)◆HG 20597-1997 承插焊钢制管法兰(欧洲体系)⼆、制造规范压⼒容器必须按照TSG R0004-2009《固定式压⼒容器安全监察规程》和GB150-2011《压⼒容器》的规定执⾏(⼀)材料材料⽣产单位应当按相应材料标准和订货合同的规定向⽤户提供质量证原件,并且在材料上的明显部位作出清晰、牢固的钢印标志或其他标志,其内容应当包括材料标准号、牌号、规格、炉(批)号、材料⽣产单位名称(或⼚标)及检验印鉴标志。
材料质量证明书的内容应当齐全、清晰,并且加盖材料⽣产单位质量检验章。
压⼒容器专⽤钢板的⽣产单位应当取得相应的特种设备制造许可证。
(⼆)焊接⼯艺和焊⼯1、压⼒容器产品施焊前,受压元件焊缝、与受压元件相焊的焊缝、熔⼊永久焊缝内的定位焊缝、受压元件母材表⾯堆焊与补焊以及上述焊缝的返修焊2、缝都应当进⾏焊接⼯艺评定或者有经评定合格的焊接⼯艺⽀持;3、质检⼈员应当全过程监督焊接⼯艺的评定过程;4、焊接⼯艺评定完成后,焊接⼯艺评定报告和焊接⼯艺指导书应当经过焊接责任⼯程师审核,技术负责⼈批准,并且经过监检机构签章确认后存⼊技术档案;5、焊接⼯艺评定技术档案应当保存⾄该⼯艺评定失效为⽌,焊接⼯艺评定试样应当保存5年;6、焊接压⼒容器的焊⼯,应当按照相应安全技术规范的规定考核合格。
压力容器技术规范最新标准

压力容器技术规范最新标准压力容器技术规范是确保压力容器安全运行的重要指导性文件,随着技术的发展和实践经验的积累,这些规范会不断更新以适应新的应用需求和安全标准。
以下是最新的压力容器技术规范的主要内容:1. 适用范围:本规范适用于所有工业用途的压力容器,包括但不限于储存、反应、换热等设备。
2. 设计原则:压力容器的设计应遵循安全、可靠、经济和环保的原则,确保在规定的使用条件下能够安全运行。
3. 材料选择:选用的材料应满足设计要求,包括力学性能、耐腐蚀性、焊接性等,并应符合相关材料标准。
4. 设计标准:压力容器的设计应符合国家或国际上认可的设计标准,如ASME(美国机械工程师协会)标准、EN(欧洲标准)等。
5. 制造和检验:压力容器的制造应严格按照设计图纸和技术规范进行,制造过程中应进行严格的质量控制和检验。
6. 焊接和无损检测:焊接是压力容器制造中的关键环节,应采用合格的焊接工艺和焊接材料。
无损检测包括射线检测、超声波检测等,以确保焊接质量。
7. 热处理:对于某些材料和结构形式的压力容器,可能需要进行热处理以改善材料性能或消除焊接应力。
8. 安全附件:压力容器应配备必要的安全附件,如安全阀、压力表、液位计等,并确保这些附件的可靠性和准确性。
9. 操作和维护:压力容器的操作应遵循操作规程,定期进行维护和检查,以确保其长期安全运行。
10. 事故预防和应急处理:应制定压力容器事故预防措施和应急处理预案,以应对可能发生的事故。
11. 法规和标准更新:压力容器的设计、制造和使用应随时关注相关法规和标准的更新,确保符合最新的安全和技术要求。
12. 环保要求:在设计和制造过程中,应考虑环保因素,减少对环境的影响。
13. 用户培训:压力容器的用户应接受专业培训,了解设备的操作规程和安全知识。
14. 记录和文档管理:应建立完整的压力容器记录和文档管理系统,记录设备的设计、制造、检验、使用和维护等信息。
15. 结束语:压力容器的安全运行对于保障人员安全和环境安全至关重要。
GB150.4压力容器-制造、检验和验收

GB150.4 《压力容器-制造、检验和验收》
主要修订依据: 4.1、 TSG R0004-2009《固定式压力容器安
全技术监察规程》
4.2、 GB 150-1998《钢制压力容器》
4.3、 HG 3129-1998《整体多层夹紧式高压 容器》 4.4、 钢带错绕压力容器相关资料
GB150.4 《压力容器-制造、检验和验收》
本标准条文
1 范围 1.1 本部分规定了GB 150适用范围内的钢制压力容器的 制造、检验与验收要求;其他材料制压力容器的制造、检 验与验收要求按相关标准。 1.2 本部分适用的压力容器结构形式为单层焊接压力容 器、锻焊压力容器和套合容器)。
●1、增加了对容器元件、焊材的要求; ●增加材 ●2、增加了容器制造过程中风险预防 料复验的 规定。 与控制的规定; ★3、增加了对新技术、新工艺和新方 法的使用规定; ★4、增加了容器制造过程中设计修改、 材料代用的规定; ★5、增加信息化管理规定; ▲6、将容器焊接接头分类的规定至 GB150.1,并增加E类接头; ▲7、删去了对质保体系,人员资格的 要求。
GB150.4 《压力容器-制造、检验和验收》
(3) 解决行业关注的突出问题的需要 如给予失效模式的制造、检验,成型受压 元件的性能恢复,无损检测的时间与方法等……
(4) 技术发展的需要
GB 150-1998《钢制压力容器》实施以来, 我国压力容器材料、设计、制造。检验水平大幅 度提高。 ——新材料开发:增加新材料制造、检验、与验 收要求。 ——材料新能提升:减少材料的复验。
GB150.4 《压力容器-制造、检验和验收》
——“基于风险(失效模式)的压力容器设计、制造与检 验”技术的应用:制造过程中的失效预防与控制。 ——封头成形技术提升:限制褶皱,采用全尺寸样板检 查形状。 ——焊接技术与装备提高:提高焊接工艺评定要求,减 少产品焊接试件数量。 ——检验技术开发:壳体直线度检查、TOFD检测技术、 气液组合压力试验…… ——相关标准修订与进步:NB/T 47014《承压设备焊接 工艺评定》等
钢制压力容器热处理通用工艺规程范文(二篇)
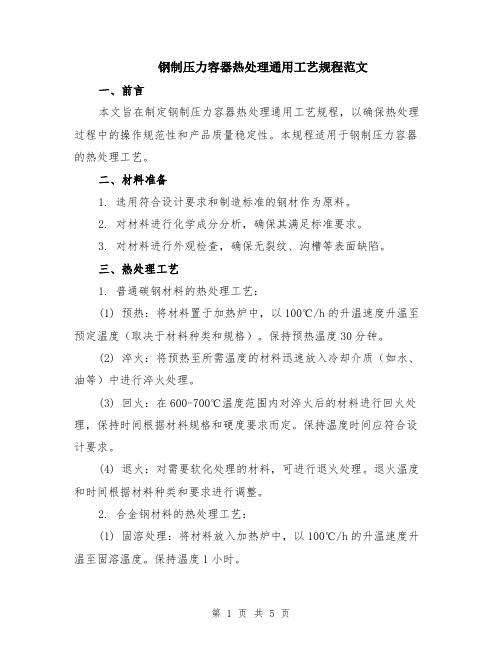
钢制压力容器热处理通用工艺规程范文一、前言本文旨在制定钢制压力容器热处理通用工艺规程,以确保热处理过程中的操作规范性和产品质量稳定性。
本规程适用于钢制压力容器的热处理工艺。
二、材料准备1. 选用符合设计要求和制造标准的钢材作为原料。
2. 对材料进行化学成分分析,确保其满足标准要求。
3. 对材料进行外观检查,确保无裂纹、沟槽等表面缺陷。
三、热处理工艺1. 普通碳钢材料的热处理工艺:(1) 预热:将材料置于加热炉中,以100℃/h的升温速度升温至预定温度(取决于材料种类和规格)。
保持预热温度30分钟。
(2) 淬火:将预热至所需温度的材料迅速放入冷却介质(如水、油等)中进行淬火处理。
(3) 回火:在600-700℃温度范围内对淬火后的材料进行回火处理,保持时间根据材料规格和硬度要求而定。
保持温度时间应符合设计要求。
(4) 退火:对需要软化处理的材料,可进行退火处理。
退火温度和时间根据材料种类和要求进行调整。
2. 合金钢材料的热处理工艺:(1) 固溶处理:将材料放入加热炉中,以100℃/h的升温速度升温至固溶温度。
保持温度1小时。
(2) 淬火:将固溶处理后的材料迅速放入冷却介质(如水、油等)中进行淬火处理。
(3) 回火:在450-600℃温度范围内对淬火后的材料进行回火处理,保持时间根据材料规格和硬度要求而定。
保持温度时间应符合设计要求。
四、操作注意事项1. 操作人员应经过相关培训,熟悉工艺要求和操作规程,严格按照规程进行操作。
2. 加热炉和冷却介质的温度应定期校准,确保温度准确性。
3. 热处理过程中,应定期检查冷却介质的质量,如有杂质应及时更换。
4. 淬火工艺中,应控制冷却介质的冷却速率,以避免材料出现裂纹等缺陷。
5. 温度控制器和计时器的准确性需要定期检查和校准。
五、质量控制1. 热处理后的材料应进行硬度测试和金相组织检查,确保满足标准要求。
2. 对热处理过程进行记录,包括材料种类、规格、加热炉温度、保温时间等重要参数。
钢制压力容器热处理通用工艺规程

钢制压力容器热处理通用工艺规范1、范围本规程规定了碳钢、低合金钢焊接件的焊后热处理工艺。
本规程适用于锅炉、压力容器的碳钢、低合金钢产品,以改善接头性能,以降低焊接残余应力为主要目的的焊后热处理。
其他产品的焊后热处理亦可参照执行。
2、参考标准下列标准所包含的条文,通过在本标准中引用而构成为本标准的条文。
在标准出版时,所示版本均为有效。
所有标准都会被修改,使用本标准的缔约方应探讨使用以下标准最新版本的可能性。
GB9452-1988 热处理炉有效区的确定。
3、要求3.1 人员和职责3.1.1 热处理操作员应接受培训、考核合格,取得上岗证,方可进行焊后热处理操作。
3.1.2 焊后热处理工艺由热处理技术人员制定,热处理责任工程师审核。
3.1.3 热处理方应严格按照焊后热处理工艺操作,并认真填写原始操作记录。
3.1.4 负责热处理的工程师负责审查焊后热处理原始操作记录(含时间—温度自动记录曲线),核实是否符合焊后热处理工艺要求,确认后签字盖章。
3.2 设备3.2.1 各种焊后热处理和装置应满足以下要求:a)满足焊后热处理工艺要求;b)在焊后热处理过程中,对加热部件没有有害影响;c)它可以确保加热部件的均匀热渗透;d)它可以精确地测量和控制温度;e)被加热件经焊后热处理之后,其变形能满足设计和使用要求。
3.2.2 焊后热处理设备可以是以下设备之一:a)电加热炉;b)钟罩式煤气炉;c)红外高温陶瓷电加热器;d)满足焊后热处理工艺要求的其他加热装置3.3 焊后热处理方法3.3.1 炉膛热处理a) 焊后热处理应优先采用在炉内加热的方法,其热处理炉应满足GB9452的有关规定。
当炉温和加热部件之间的对应关系值累积时,炉膛热处理时,一般允许利用炉温推算被加热件的温度,但对特殊或重要的焊接产品,温度测量应以安置在被加热件上的热电偶为准。
b) 被加热件应整齐地安置于炉内的有效加热区内,并保证炉内热量均匀、流通。
在火焰炉膛热处理时应避免火焰直接喷射到工件上。
压力容器及管道制造、安装焊接规范
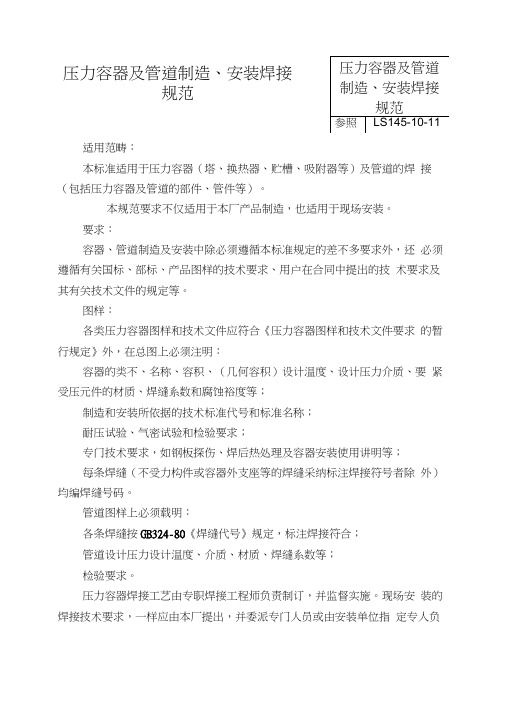
适用范畴:本标准适用于压力容器(塔、换热器、贮槽、吸附器等)及管道的焊 接(包括压力容器及管道的部件、管件等)。
本规范要求不仅适用于本厂产品制造,也适用于现场安装。
要求:容器、管道制造及安装中除必须遵循本标准规定的差不多要求外,还 必须遵循有关国标、部标、产品图样的技术要求、用户在合同中提出的技 术要求及其有关技术文件的规定等。
图样:各类压力容器图样和技术文件应符合《压力容器图样和技术文件要求 的暂行规定》外,在总图上必须注明:容器的类不、名称、容积、(几何容积)设计温度、设计压力介质、要 紧受压元件的材质、焊缝系数和腐蚀裕度等;制造和安装所依据的技术标准代号和标准名称;耐压试验、气密试验和检验要求;专门技术要求,如钢板探伤、焊后热处理及容器安装使用讲明等;每条焊缝(不受力构件或容器外支座等的焊缝采纳标注焊接符号者除 外)均编焊缝号码。
管道图样上必须载明:各条焊缝按GB324-80《焊缝代号》规定,标注焊接符合;管道设计压力设计温度、介质、材质、焊缝系数等;检验要求。
压力容器焊接工艺由专职焊接工程师负责制订,并监督实施。
现场安 装的焊接技术要求,一样应由本厂提出,并委派专门人员或由安装单位指 定专人负压力容器及管道制造、安装焊接 规范责指导、监督、执行、检查。
如遇重大技术咨询题,由用户、安装单位及本厂共同协商解决。
对容器、管道结构上的要求:容器管道的结构设计除必须符合一机部、石油部、化工部颁发的《钢制石油化工压力容器设计规定》及有关标准的规定外,焊缝设计应考虑制造时便于焊接,且应考虑便于无损探伤,并使气密性试验时便于观看、检漏。
固定的全位置焊缝打底层以及仅能进行单面焊的铝容器、管道的环焊缝应采纳嵌入环式的不锈垫板焊。
不等厚度焊件的对接焊,较厚一侧的板材应作14°削薄。
铝焊件厚壁的过滤应带有一段(至少为25mm)的园颈,在其余应符合JB741-80《钢制焊接压力容器技术条件》和JB1580-75《铝制焊接容器技术条件》的有关规定。
压力容器制造工艺规程

压力容器制造工艺规程1. 引言压力容器是一种广泛应用于工业和军事领域的设备,用于存储和运输气体或液体。
由于其特殊用途和工作条件,压力容器的制造工艺必须符合严格的规范和标准,以确保其安全使用。
本规程旨在介绍压力容器的制造工艺,并提供制造商遵循的指导原则。
2. 材料选择压力容器的材料选择非常重要,必须根据容器的设计压力和温度、介质的性质和容器的尺寸等因素来确定。
常见的材料包括碳钢、不锈钢、合金钢和钛合金等。
制造商应根据设计要求选择合适的材料,并确保其符合相关标准和规范。
3. 设计和制图在制造压力容器之前,制造商必须进行详细的设计和制图。
设计阶段包括确定容器的尺寸、形状、壁厚和支撑结构等。
制造商应使用计算软件和模型进行力学分析,以确保容器在工作条件下具有足够的强度和刚度。
制图阶段包括制作详细的图纸和说明,包括容器的各个部分、连接方式和焊接工艺等。
4. 板材切割和成形制造压力容器的第一步是根据图纸的要求切割和成形板材。
常用的切割方法包括火焰切割、等离子切割和激光切割等。
成形板材的方法包括冷弯、热弯和卷边等。
制造商必须确保切割和成形过程的精度和质量,以避免材料剪裁不准确和形状变形等问题。
5. 焊接焊接是制造压力容器的关键步骤,要求焊缝具有足够的强度和密封性。
焊接方法包括手工电弧焊、氩弧焊、埋弧焊和激光焊等。
制造商应根据设计要求选择合适的焊接方法,并确保焊工具有相关的资质和经验。
焊接后,焊缝必须进行无损检测,以确保其质量和完整性。
6. 表面处理制造压力容器后,表面处理是必要的步骤,以提高其耐腐蚀性和耐磨性。
常用的表面处理包括喷砂、酸洗和热浸镀等。
制造商在选择和执行表面处理方法时,必须遵循相关标准和规范,并确保处理后的表面平整、清洁和耐用。
7. 压力测试制造完成后,压力容器必须进行压力测试,以确保其能够承受设计压力而不泄漏。
压力测试应根据容器的尺寸和设计压力来确定,常用的方法包括水压试验和气压试验等。
制造商必须记录并报告测试结果,并在通过测试后提供合格证书。
最新压力容器国家标准规范

最新压力容器国家标准规范压力容器作为工业生产中不可或缺的设备,其安全性和可靠性直接关系到人员安全和生产效率。
随着技术的发展和标准的更新,压力容器的国家标准规范也在不断完善。
以下是最新压力容器国家标准规范的概述:1. 适用范围本规范适用于设计、制造、检验和使用的压力容器,包括但不限于锅炉、换热器、反应器等。
2. 设计要求- 应符合国家相关安全标准和行业规范。
- 必须考虑到材料的力学性能、腐蚀性、温度和压力等因素。
- 设计应确保结构合理,便于制造、安装和维护。
3. 材料选择- 应选择符合国家标准的金属材料,确保材料的质量和性能。
- 对于特殊环境下使用的压力容器,应选用具有相应耐腐蚀性能的材料。
4. 制造工艺- 制造过程中应严格控制焊接、成型、热处理等关键工艺。
- 所有制造工艺必须符合国家相关工艺标准。
5. 检验与试验- 压力容器在制造完成后,必须进行严格的无损检测和压力试验。
- 无损检测应包括射线检测、超声波检测等,确保无内部缺陷。
- 压力试验应模拟实际工作条件,确保容器在规定压力下无泄漏。
6. 安全附件- 压力容器应配备必要的安全附件,如安全阀、压力表、紧急切断装置等。
- 安全附件的选择和安装应符合国家相关标准。
7. 使用与维护- 使用单位应制定详细的操作规程和维护计划。
- 定期对压力容器进行检查和维护,确保其良好运行状态。
8. 事故处理与应急预案- 使用单位应制定压力容器事故处理程序和应急预案。
- 在发生事故时,应立即启动应急预案,确保人员安全和最小化损失。
9. 法规与标准更新- 压力容器的设计、制造和使用应随时关注国家法规和标准的更新,确保符合最新要求。
10. 结语压力容器的安全运行对于保障工业生产的顺利进行至关重要。
本规范的制定旨在提高压力容器的安全性和可靠性,减少事故发生的风险,保障人民生命财产安全。
请注意,以上内容仅为概述,具体实施时应详细参照最新的国家标准和行业规范。
压力容器及管道制造、安装焊接规范
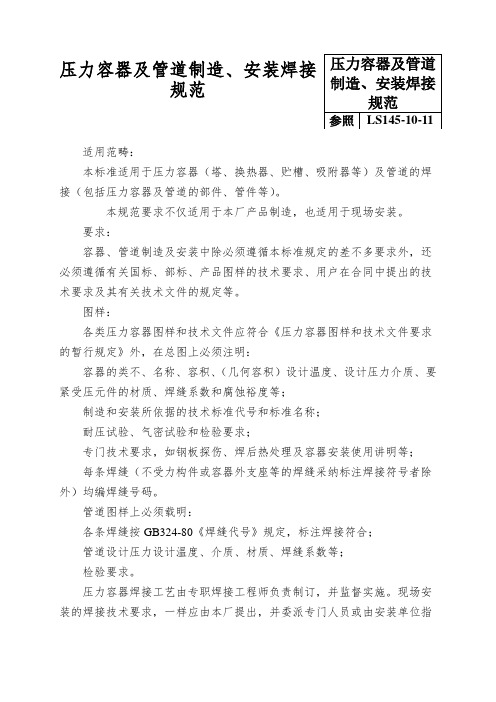
规范适用范畴:本标准适用于压力容器(塔、换热器、贮槽、吸附器等)及管道的焊接(包括压力容器及管道的部件、管件等)。
本规范要求不仅适用于本厂产品制造,也适用于现场安装。
要求:容器、管道制造及安装中除必须遵循本标准规定的差不多要求外,还必须遵循有关国标、部标、产品图样的技术要求、用户在合同中提出的技术要求及其有关技术文件的规定等。
图样:各类压力容器图样和技术文件应符合《压力容器图样和技术文件要求的暂行规定》外,在总图上必须注明:容器的类不、名称、容积、(几何容积)设计温度、设计压力介质、要紧受压元件的材质、焊缝系数和腐蚀裕度等;制造和安装所依据的技术标准代号和标准名称;耐压试验、气密试验和检验要求;专门技术要求,如钢板探伤、焊后热处理及容器安装使用讲明等;每条焊缝(不受力构件或容器外支座等的焊缝采纳标注焊接符号者除外)均编焊缝号码。
管道图样上必须载明:各条焊缝按GB324-80《焊缝代号》规定,标注焊接符合;管道设计压力设计温度、介质、材质、焊缝系数等;检验要求。
压力容器焊接工艺由专职焊接工程师负责制订,并监督实施。
现场安装的焊接技术要求,一样应由本厂提出,并委派专门人员或由安装单位指定专人负责指导、监督、执行、检查。
如遇重大技术咨询题,由用户、安装单位及本厂共同协商解决。
对容器、管道结构上的要求:容器管道的结构设计除必须符合一机部、石油部、化工部颁发的《钢制石油化工压力容器设计规定》及有关标准的规定外,焊缝设计应考虑制造时便于焊接,且应考虑便于无损探伤,并使气密性试验时便于观看、检漏。
固定的全位置焊缝打底层以及仅能进行单面焊的铝容器、管道的环焊缝应采纳嵌入环式的不锈垫板焊。
不等厚度焊件的对接焊,较厚一侧的板材应作14°削薄。
铝焊件厚壁的过滤应带有一段(至少为25mm)的园颈,在其余应符合JB741-80《钢制焊接压力容器技术条件》和JB1580-75《铝制焊接容器技术条件》的有关规定。
压力容器的单面焊缝不作封底焊时,应当设法对焊根部进行外观检查或按规定要求进行无损探伤。
压力容器常用标准.规范

压力容器常用标准.规范压力容器设计常用规范、规定和标准1.设计标准GB 150-1998 钢制压力容器*GB 151-1999 管壳式换热器*GB 12337-1998 钢制球型储罐HG/T 20569-1994 机械搅拌设备JB/T 4710-2019 钢制塔式容器JB/T 4731-2019 钢制卧式容器JB/T 4734-2002 铝制焊接容器JB/T 4735-1997 钢制焊接常压容器JB/T 4745-2019 钛制焊接容器2.基础标准HG 20580-1998 钢制化工容器设计基础规定*HG 20581-1998 钢制化工容器材料选用规定*HG 20582-1998 钢制化工容器强度计算规定HG 20583-1998 钢制化工容器结构设计规定*HG 20584-1998 钢制化工容器制造技术要求HG 20585-1998 钢制低温压力容器技术规定*HG 20652-1998 塔器设计技术规定3.设备型式参数标准GB/T 17261-1998 钢制球型储罐型式与基本参数JB/T 4714-1992 浮头式换热器和冷凝器型式与基本参数 JB/T 4715-1992 固定管板式换热器型式与基本参数JB/T 4716-1992 立式热虹吸式重沸器型式与基本参数JB/T 4717-1992 U型管式换热器型式与基本参数4.制造检验标准GB/T 4334.1-2000 不锈钢 10%草酸浸蚀试验方法GB/T 4334.2-2000 不锈钢硫酸-硫酸铁腐蚀试验方法 GB/T 4334.3-2000 不锈钢 65%硝酸腐蚀试验方法GB/T 4334.4-2000 不锈钢硝酸-氢氟酸腐蚀试验方法 GB/T 4334.5-2000 不锈钢硝酸-硫酸铜腐蚀试验方法 GB/T 4334.6-2000 不锈钢 5%硫酸腐蚀试验方法JB 4708-2000 钢制压力容器焊接工艺评定JB/T 4709-2000 钢制压力容器焊接规程JB/T 4730-2019 承压设备无损检测5.筒体GB/T 9019-2001 压力容器公称直径GB/T 17395-1998 无缝钢管尺寸、外形、重量及允许偏差 6.封头HG 21607-1996 异型筒体和封头JB/T 4746-2002 钢制压力容器用封头GB/T 539-1995GB/T 3985-1995GB/T 4622.1-2019GB/T 4622.2-2019GB/T 4622.3-1993GB/T 9112-2000GB/T 9113.1-2000GB/T 9113.2-2000GB/T 9113.4-2000 GB/T 9114-2000 GB/T 9115.1-2000 GB/T 9115.2-2000 GB/T 9115.3-2000 GB/T 9115.4-2000 GB/T 9116.1-2000 GB/T 9116.2-2000 GB/T 9116.3-2000 GB/T 9116.4-2000 GB/T 9117.1-2000 GB/T 9117.2-2000 GB/T 9117.3-2000 GB/T 9118.1-2000 GB/T 9118.2-2000 GB/T 9119-2000 GB/T 9120.1-2000 GB/T 9120.2-2000 GB/T 9120.3-2000 GB/T 9121.1-2000 GB/T 9121.2-2000 GB/T 9121.3-2000 GB/T 9122-2000 GB/T 9123.1-2000GB/T 9123.3-2000耐油石棉橡胶板石棉橡胶板缠绕式垫片分类缠绕式垫片管法兰用垫片尺寸缠绕式垫片技术条件钢制管法兰类型与参数平面、突面整体钢制管法兰凹凸面整体钢制管法兰榫槽面整体钢制管法兰环连接面整体钢制管法兰突面带颈螺纹钢制管法兰平面、突面对焊钢制管法兰凹凸面对焊体钢制管法兰榫槽面对焊钢制管法兰环连接面对焊钢制管法兰平面、突面带颈平焊钢制管法兰凹凸面带颈平焊钢制管法兰榫槽面带颈平焊钢制管法兰环连接面带颈平焊钢制管法兰突面带颈承插焊钢制管法兰凹凸面带颈承插焊钢制管法兰榫槽面带颈承插焊钢制管法兰突面对焊环带颈松套钢制管法兰环连接面对焊环带颈松套钢制管法兰平面、突面板式平焊钢制管法兰突面对焊环板式松套钢制管法兰凹凸面对焊环板式松套钢制管法兰榫槽面对焊环板式松套钢制管法兰突面平焊环板式松套钢制管法兰凹凸面平焊环板式松套钢制管法兰榫槽面对焊环板式松套钢制管法兰翻边环板式松套钢制管法兰平面、突面钢制管法兰凹凸面钢制管法兰榫槽面钢制管法兰GB/T 9123.4-2000 环连接面钢制管法兰GB/T 9124-2000 钢制管法兰技术条件GB/T 9125-2019 管法兰连接用紧固件GB/T 9126-2019 管法兰用非金属平垫片尺寸GB/T 9128-2019 钢制管法兰用金属环垫尺寸GB/T 9129-2019 管法兰用非金属平垫片技术条件GB 9130-1988 钢制管法兰连接用金属环垫技术条件HG 20592-2019 钢制管法兰型式、参数(欧洲体系)*HG 20615-1997 钢制管法兰型式、参数(美洲体系)*8.压力容器法兰、垫片、紧固件JB/T 4700-2000 压力容器法兰分类与技术条件JB/T 4701-2000 甲型平焊法兰JB/T 4702-2000 乙型平焊法兰JB/T 4703-2000 长颈对焊法兰JB/T 4704-2000 非金属软垫片JB/T 4705-2000 缠绕垫片JB/T 4706-2000 金属包垫片JB/T 4707-2000 等长双头螺柱9.试镜、液面(位)计HG 21505-1992 组合式视镜HG/T 21550-1993 防霜液面计HG/T 21575-1994 带灯视镜HG/T 21584-1995 磁性液位计HG 21588-1995 玻璃液面计标准系列及技术要求HG 21589.1-1995 透光式玻璃板液面计(PN2.5)HG 21589.2-1995 透光式玻璃板液面计(PN6.3)HG 21590-1995 反射式玻璃板液面计(PN4.0)HG 21591.1-1995 视镜式玻璃板液面计(常压)HG 21591.2-1995 视镜式玻璃板液面计(PN0.6)HG/T 21619-1986 视镜(Pg10,16,25)HG/T 21620-1986 带颈视镜(Pg10,16,25)HG/T 21622-1990 衬里视镜标准图HG/T 21622.3-1990 带颈衬里视镜JB/T 9243-1999 玻璃管液位计JB/T 9244-1999 玻璃板液位计10.安全附件GB 567-1999 爆破片与爆破片装置GB/T 12241-1989 安全阀一般要求GB/T 12243-1989 弹簧直接载荷式安全阀GB/T 12253-1999 拱形金属爆破片装置分类与安装尺寸GB/T 12266-1993 正拱形金属爆破片型式与参数GB/T 12267-1999 反形金属爆破片型式与参数GB/T 12268-1999 开缝形金属爆破片型式与参数GB/T 16181-1996 爆破片装置夹持型式和外形尺寸 11.人孔、手孔钢制人孔和手孔(HG/T 21514~21535-2019 )HG/T 21514-2019 钢制人孔和手孔的类型与技术条件 HG/T 21515-2019 常压人孔HG/T 21516-2019 回转盖板式平焊法兰人孔HG/T 21517-2019 回转盖带颈平焊法兰人孔HG/T 21518-2019 回转盖带颈对焊法兰人孔HG/T 21519-2019 垂直吊盖板式平焊法兰人孔HG/T 21520-2019 垂直吊盖带颈平焊法兰人孔HG/T 21521-2019 垂直吊盖带颈对焊法兰人孔HG/T 21522-2019 水平吊盖板式平焊法兰人孔HG/T 21523-2019 水平吊盖带颈平焊法兰人孔HG/T 21524-2019 水平吊盖带颈对焊法兰人孔HG/T 21525-2019 常压旋柄快开人孔HG/T 21526-2019 椭圆形回转盖快开人孔HG/T 21527-2019 回转拱盖快开人孔HG/T 21528-2019 常压手孔HG/T 21529-2019 板式平焊法兰手孔HG/T 21530-2019 带颈平焊法兰手孔HG/T 21531-2019 带颈对焊法兰手孔HG/T 21532-2019 回转盖带颈对焊法兰手孔HG/T 21533-2019 常压快开手孔HG/T 21534-2019 旋柄快开手孔HG/T 21535-2019 回转盖快开手孔不锈钢人孔、手孔(HG 21594~21604-1999) HG 21594-1999 不锈钢人、手孔分类与技术条件 HG 21595-1999 常压不锈钢人孔HG 21596-1999 回转盖不锈钢人孔HG 21597-1999 回转拱盖快开不锈钢人孔HG 21598-1999 水平吊盖不锈钢人孔HG 21599-1999 垂直吊盖不锈钢人孔HG 21600-1999 椭圆快开不锈钢人孔HG 21601-1999 常压快开不锈钢手孔HG 21602-1999 平盖不锈钢手孔HG 21603-1999 回转盖快开不锈钢手孔HG 21604-1999 旋柄快开不锈钢手孔JB/T 577-1979 常压人孔JB/T 579-1979 长圆形回转盖快开人孔JB/T 580-1979 回转盖人孔JB/T 581-1979 回转吊盖快开人孔JB/T 582-1979 垂直吊盖人孔JB/T 583-1979 水平吊盖人孔JB/T 584-1979 回转盖对焊法兰人孔JB/T 585-1979 水平吊盖对焊法兰人孔JB/T 586-1979 常压快开手孔JB/T 587-1979 回转盖快开手孔JB/T 588-1979 常压手孔JB/T 589-1979 平盖手孔JB/T 590-1979 旋柄快开手孔JB/T 591-1979 平盖对焊法兰手孔JB/T 592-1979 回转盖对焊法兰人孔JB/T 2555-1979 碳素钢、低合金钢人、手孔分类与技术条件 JB/T 2556-1979 垂直吊盖对焊法兰人孔JB/T 2557-1979 常压旋柄快开人孔12.搅拌传动装置、搅拌器HG/T 2043-1991 三叶后弯式搅拌器技术条件HG/T 2123-1991 搅拌器型式及主要参数HG/T 2124-1991 桨式搅拌器技术条件HG/T 2125-1991 涡轮式搅拌器技术条件HG/T 2126-1991 推进式搅拌器技术条件HG/T 2127-1991 框式搅拌器技术条件搅拌传动装置(HG 21563~21572-95 HG 21537.7~8-92)HG 21563-1995 搅拌传动装置系统组合、选用及技术要求 HG 21564-1995 搅拌传动装置--凸缘法兰HG 21565-1995 搅拌传动装置--安装底盖HG 21566-1995 搅拌传动装置--单支点机架HG 21567-1995 搅拌传动装置--双支点机架HG 21568-1995 搅拌传动装置--传动轴HG 21569.1-1995 搅拌传动装置--带短节联轴器HG 21569.2-1995 搅拌传动装置--块式弹性联轴器HG 21570-1995 搅拌传动装置--联轴器HG 21571-1995 搅拌传动装置-机械密封HG 21572-1995 搅拌传动装置-机械密封循环保护系统13.轴密封HG/T 2098-2001 釜用机械密封系列及主要参数HG/T 2269-2019 釜用机械密封技术条件HG 21537.1-1992 碳钢填料箱(施工图)(PN0.6DN30.160)HG 21537.2-1992 不锈钢填料箱(施工图)(PN0.6DN30.160) HG 21537.3-1992 常压碳钢填料箱(施工图)(PNHG 21537.8-1992 搅拌传动装置-不锈钢填料箱HG/T 21571-1995 搅拌传动装置--机械密封HG/T 21572-1995 搅拌传动装置--机械14.塔器部件HG 20652-1998 塔器设计技术规定HG/T 21512-1995 梁型气体喷射式填料支承板HG/T 21554.1-1995 碳钢矩鞍环填料HG/T 21554.2-1995 不锈钢矩鞍环填料HG/T21556-1995 鲍尔环填料HG/T 21556.1-1995 碳钢鲍尔环填料HG/T 21556.2-1995 不锈钢鲍尔环填料HG/T 21556.3-1995 聚丙烯鲍尔环填料HG/T 21556.4-1995 玻纤增强聚丙烯鲍尔环填料HG/T 21557-1995 阶梯环填料HG/T 21557.1-1995 碳钢阶梯环填料HG/T 21557.2-1995 不锈钢阶梯环填料HG/T 21559.1-1995 不锈钢网孔板波纹填料HG/T 21559.2-2019 不锈钢孔板波纹填料HG/T 21618-1998 丝网除沫器标准HG/T 21639-2019 塔顶吊柱JB/T 1118-2001 F1型浮阀JB/T 1119-1999 卡子JB/T 1120-1999 双面可拆连接件JB/T 1205-2001 塔盘技术条件JB/T 1212-1999 圆泡帽JB/T 2878.1-1999 X1型楔卡JB/T 2878.2-1999 X2型楔卡JB/T 3166-1999 S型双面可卸卡子15.支座、吊耳HG/T 21574-1994 设备吊耳JB/T 4712-1992 鞍式支座JB/T 4713-1992 腿式支座JB/T 4724-1992 支承式支座JB/T 4725-1992 耳式支座密封循环保护系统16.换热器零部件GB/T 12522-1996 不锈钢波形膨胀节GB 16749-1997 压力容器波形膨胀节JB/T 4718-1992 管壳式换热器用金属包垫片 JB/T 4719-1992 管壳式换热器用缠绕垫片 JB/T 4720-1992 管壳式换热器用非金属垫片 JB/T 4721-1992 外头盖侧法兰JB/T 6171-1992 多层金属波纹膨胀节17.其他零部件HG/T 21630-1990 补强管JB/T 4736-2002 补强圈18.材料GB/T 699-1999 优质碳素结构钢GB/T 700-2019 碳素结构钢GB/T 3077-1999 合金结构钢19.板材GB/T 912-1989 碳素结构钢和低合金结构钢热轧薄钢板及钢带 GB/T 2040-2002 铜及铜合金板材GB/T 2054-1980 镍及镍合金板GB/T 2531-1981 热交换器固定板用黄铜板GB/T 3274-1988 碳素结构钢和低合金结构钢热轧厚钢板和钢带 GB/T 3280-1992 不锈钢冷轧钢板GB 3531-1996 低温压力容器用低合金钢钢板GB/T 3621-1994 钛及钛合金板材GB/T 3880-1997 铝及铝合金轧制板材GB/T 4237-1992 不锈钢热轧钢板GB/T 4238-1992 耐热钢板GB 6654-1996 压力容器用钢板GB/T 8165-1997 不锈钢复合钢板和钢带GB/T 8546-1987 钛-不锈钢复合板GB/T 8547-1987 钛-钢复合板GB/T 13238-1991 铜钢复合钢板JB 4733-1996 压力容器用爆炸不锈钢复合钢板JB/T 4748-2002 压力容器用镍及镍基合金爆炸复合钢板20.钢管GB/T 1527-1997 铜及铜合金拉制管GB/T 1528-1997 铜及铜合金挤制管GB/T 2882-1981 镍及镍铜合金管GB/T 3624-1995 钛及钛合金管GB/T 4437.1-2000铝及铝合金热挤压管GB 5310-1995 高压锅炉用无缝钢管GB 6479-2000 高压化肥设备用无缝钢管GB/T 6893-2000 铝及铝合金拉GB/T 8163-1999 输送流体用无缝钢管GB/T 8890-1998 热交换器用铜合金无缝管GB 9948-1988 石油裂化用无缝钢管GB/T 12771-2000 流体输送用不锈钢焊接钢管GB 13296-1991 锅炉、热交换器用不锈钢无缝钢管 GB/T 14976-2002 流体输送用不锈钢无缝管21.锻件JB 4726-2000 压力容器用碳素钢和低合金钢锻件 JB 4727-2000 低温压力容器用低合金钢锻件 JB 4728-2000 压力容器用不锈钢锻件22.棒材GB/T 1220-1992 不锈钢棒GB/T 1221-1992 耐热钢棒GB/T 4423-1992 铜及铜合金拉制棒GB/T 4435-1984 镍及镍铜合金棒GB/T 13808-1992 铜及铜合金挤制棒23.铸件GB/T 1348-1988 球墨铸铁件GB/T 2100-2002 一般用途耐蚀钢铸件GB/T 7659-1987 焊接结构用碳素钢铸件GB/T 8492-2002 一般用途耐热钢和合金铸件GB/T 9437-1988 耐热铸铁件GB/T 9439-1988 灰铸铁件GB/T 9440-1988 可锻铸铁件GB/T 11352-1989 一般工程用铸造碳钢件GB/T 14408-1993 一般工程与结构用低合金铸钢件 JBT 6402-1992 大型低合金钢铸件JBT 6403-1992 大型耐热钢铸件JBT 6405-1992 大型不锈钢铸件。
压力容器常用标准、规范

压力容器设计常用规范、规定和标准1.设计标准GB 150-1998 钢制压力容器*GB 151-1999 管壳式换热器*GB 12337-1998 钢制球型储罐HG/T 20569-1994 机械搅拌设备JB/T 4710-2005 钢制塔式容器JB/T 4731-2005 钢制卧式容器JB/T 4734-2002 铝制焊接容器JB/T 4735-1997 钢制焊接常压容器JB/T 4745-2005 钛制焊接容器2.基础标准HG 20580-1998 钢制化工容器设计基础规定*HG 20581-1998 钢制化工容器材料选用规定*HG 20582-1998 钢制化工容器强度计算规定HG 20583-1998 钢制化工容器结构设计规定*HG 20584-1998 钢制化工容器制造技术要求HG 20585-1998 钢制低温压力容器技术规定*HG 20652-1998 塔器设计技术规定3.设备型式参数标准GB/T 17261-1998 钢制球型储罐型式与基本参数JB/T 4714-1992 浮头式换热器和冷凝器型式与基本参数JB/T 4715-1992 固定管板式换热器型式与基本参数JB/T 4716-1992 立式热虹吸式重沸器型式与基本参数JB/T 4717-1992 U型管式换热器型式与基本参数4.制造检验标准GB/T 4334.1-2000 不锈钢 10%草酸浸蚀试验方法GB/T 4334.2-2000 不锈钢硫酸-硫酸铁腐蚀试验方法GB/T 4334.3-2000 不锈钢 65%硝酸腐蚀试验方法GB/T 4334.4-2000 不锈钢硝酸-氢氟酸腐蚀试验方法GB/T 4334.5-2000 不锈钢硝酸-硫酸铜腐蚀试验方法GB/T 4334.6-2000 不锈钢 5%硫酸腐蚀试验方法JB 4708-2000 钢制压力容器焊接工艺评定JB/T 4709-2000 钢制压力容器焊接规程JB/T 4730-2005 承压设备无损检测5.筒体GB/T 9019-2001 压力容器公称直径GB/T 17395-1998 无缝钢管尺寸、外形、重量及允许偏差6.封头HG 21607-1996 异型筒体和封头JB/T 4746-2002 钢制压力容器用封头GB/T 539-1995 耐油石棉橡胶板GB/T 3985-1995 石棉橡胶板GB/T 4622.1-2003 缠绕式垫片分类GB/T 4622.2-2003 缠绕式垫片管法兰用垫片尺寸GB/T 4622.3-1993 缠绕式垫片技术条件GB/T 9112-2000 钢制管法兰类型与参数GB/T 9113.1-2000 平面、突面整体钢制管法兰GB/T 9113.2-2000 凹凸面整体钢制管法兰GB/T 9113.3-2000 榫槽面整体钢制管法兰GB/T 9113.4-2000 环连接面整体钢制管法兰GB/T 9114-2000 突面带颈螺纹钢制管法兰GB/T 9115.1-2000 平面、突面对焊钢制管法兰GB/T 9115.2-2000 凹凸面对焊体钢制管法兰GB/T 9115.3-2000 榫槽面对焊钢制管法兰GB/T 9115.4-2000 环连接面对焊钢制管法兰GB/T 9116.1-2000 平面、突面带颈平焊钢制管法兰GB/T 9116.2-2000 凹凸面带颈平焊钢制管法兰GB/T 9116.3-2000 榫槽面带颈平焊钢制管法兰GB/T 9116.4-2000 环连接面带颈平焊钢制管法兰GB/T 9117.1-2000 突面带颈承插焊钢制管法兰GB/T 9117.2-2000 凹凸面带颈承插焊钢制管法兰GB/T 9117.3-2000 榫槽面带颈承插焊钢制管法兰GB/T 9118.1-2000 突面对焊环带颈松套钢制管法兰GB/T 9118.2-2000 环连接面对焊环带颈松套钢制管法兰GB/T 9119-2000 平面、突面板式平焊钢制管法兰GB/T 9120.1-2000 突面对焊环板式松套钢制管法兰GB/T 9120.2-2000 凹凸面对焊环板式松套钢制管法兰GB/T 9120.3-2000 榫槽面对焊环板式松套钢制管法兰GB/T 9121.1-2000 突面平焊环板式松套钢制管法兰GB/T 9121.2-2000 凹凸面平焊环板式松套钢制管法兰GB/T 9121.3-2000 榫槽面对焊环板式松套钢制管法兰GB/T 9122-2000 翻边环板式松套钢制管法兰GB/T 9123.1-2000 平面、突面钢制管法兰GB/T 9123.2-2000 凹凸面钢制管法兰GB/T 9123.3-2000 榫槽面钢制管法兰GB/T 9123.4-2000 环连接面钢制管法兰GB/T 9124-2000 钢制管法兰技术条件GB/T 9125-2003 管法兰连接用紧固件GB/T 9126-2003 管法兰用非金属平垫片尺寸GB/T 9128-2003 钢制管法兰用金属环垫尺寸GB/T 9129-2003 管法兰用非金属平垫片技术条件GB 9130-1988 钢制管法兰连接用金属环垫技术条件HG 20592-2009 钢制管法兰型式、参数(欧洲体系)*HG 20615-1997 钢制管法兰型式、参数(美洲体系)*8.压力容器法兰、垫片、紧固件JB/T 4700-2000 压力容器法兰分类与技术条件JB/T 4701-2000 甲型平焊法兰JB/T 4702-2000 乙型平焊法兰JB/T 4703-2000 长颈对焊法兰JB/T 4704-2000 非金属软垫片JB/T 4705-2000 缠绕垫片JB/T 4706-2000 金属包垫片JB/T 4707-2000 等长双头螺柱9.试镜、液面(位)计HG 21505-1992 组合式视镜HG/T 21550-1993 防霜液面计HG/T 21575-1994 带灯视镜HG/T 21584-1995 磁性液位计HG 21588-1995 玻璃液面计标准系列及技术要求HG 21589.1-1995 透光式玻璃板液面计(PN2.5)HG 21589.2-1995 透光式玻璃板液面计(PN6.3)HG 21590-1995 反射式玻璃板液面计(PN4.0)HG 21591.1-1995 视镜式玻璃板液面计(常压)HG 21591.2-1995 视镜式玻璃板液面计(PN0.6)HG/T 21619-1986 视镜(Pg10,16,25)HG/T 21620-1986 带颈视镜(Pg10,16,25)HG/T 21622-1990 衬里视镜标准图HG/T 21622.3-1990 带颈衬里视镜JB/T 9243-1999 玻璃管液位计JB/T 9244-1999 玻璃板液位计10.安全附件GB 567-1999 爆破片与爆破片装置GB/T 12241-1989 安全阀一般要求GB/T 12243-1989 弹簧直接载荷式安全阀GB/T 12253-1999 拱形金属爆破片装置分类与安装尺寸GB/T 12266-1993 正拱形金属爆破片型式与参数GB/T 12267-1999 反形金属爆破片型式与参数GB/T 12268-1999 开缝形金属爆破片型式与参数GB/T 16181-1996 爆破片装置夹持型式和外形尺寸11.人孔、手孔钢制人孔和手孔(HG/T 21514~21535-2005 ) HG/T 21514-2005 钢制人孔和手孔的类型与技术条件HG/T 21515-2005 常压人孔HG/T 21516-2005 回转盖板式平焊法兰人孔HG/T 21517-2005 回转盖带颈平焊法兰人孔HG/T 21518-2005 回转盖带颈对焊法兰人孔HG/T 21519-2005 垂直吊盖板式平焊法兰人孔HG/T 21520-2005 垂直吊盖带颈平焊法兰人孔HG/T 21521-2005 垂直吊盖带颈对焊法兰人孔HG/T 21522-2005 水平吊盖板式平焊法兰人孔HG/T 21523-2005 水平吊盖带颈平焊法兰人孔HG/T 21524-2005 水平吊盖带颈对焊法兰人孔HG/T 21525-2005 常压旋柄快开人孔HG/T 21526-2005 椭圆形回转盖快开人孔HG/T 21527-2005 回转拱盖快开人孔HG/T 21528-2005 常压手孔HG/T 21529-2005 板式平焊法兰手孔HG/T 21530-2005 带颈平焊法兰手孔HG/T 21531-2005 带颈对焊法兰手孔HG/T 21532-2005 回转盖带颈对焊法兰手孔HG/T 21533-2005 常压快开手孔HG/T 21534-2005 旋柄快开手孔HG/T 21535-2005 回转盖快开手孔不锈钢人孔、手孔(HG 21594~21604-1999)HG 21594-1999 不锈钢人、手孔分类与技术条件HG 21595-1999 常压不锈钢人孔HG 21596-1999 回转盖不锈钢人孔HG 21597-1999 回转拱盖快开不锈钢人孔HG 21598-1999 水平吊盖不锈钢人孔HG 21599-1999 垂直吊盖不锈钢人孔HG 21600-1999 椭圆快开不锈钢人孔HG 21601-1999 常压快开不锈钢手孔HG 21602-1999 平盖不锈钢手孔HG 21603-1999 回转盖快开不锈钢手孔HG 21604-1999 旋柄快开不锈钢手孔JB/T 577-1979 常压人孔JB/T 579-1979 长圆形回转盖快开人孔JB/T 580-1979 回转盖人孔JB/T 581-1979 回转吊盖快开人孔JB/T 582-1979 垂直吊盖人孔JB/T 583-1979 水平吊盖人孔JB/T 584-1979 回转盖对焊法兰人孔JB/T 585-1979 水平吊盖对焊法兰人孔JB/T 586-1979 常压快开手孔JB/T 587-1979 回转盖快开手孔JB/T 588-1979 常压手孔JB/T 589-1979 平盖手孔JB/T 590-1979 旋柄快开手孔JB/T 591-1979 平盖对焊法兰手孔JB/T 592-1979 回转盖对焊法兰人孔JB/T 2555-1979 碳素钢、低合金钢人、手孔分类与技术条件JB/T 2556-1979 垂直吊盖对焊法兰人孔JB/T 2557-1979 常压旋柄快开人孔12.搅拌传动装置、搅拌器HG/T 2043-1991 三叶后弯式搅拌器技术条件HG/T 2123-1991 搅拌器型式及主要参数HG/T 2124-1991 桨式搅拌器技术条件HG/T 2125-1991 涡轮式搅拌器技术条件HG/T 2126-1991 推进式搅拌器技术条件HG/T 2127-1991 框式搅拌器技术条件搅拌传动装置(HG 21563~21572-95 HG 21537.7~8-92)HG 21563-1995 搅拌传动装置系统组合、选用及技术要求HG 21564-1995 搅拌传动装置--凸缘法兰HG 21565-1995 搅拌传动装置--安装底盖HG 21566-1995 搅拌传动装置--单支点机架HG 21567-1995 搅拌传动装置--双支点机架HG 21568-1995 搅拌传动装置--传动轴HG 21569.1-1995 搅拌传动装置--带短节联轴器HG 21569.2-1995 搅拌传动装置--块式弹性联轴器HG 21570-1995 搅拌传动装置--联轴器HG 21571-1995 搅拌传动装置-机械密封HG 21572-1995 搅拌传动装置-机械密封循环保护系统13.轴密封HG/T 2098-2001 釜用机械密封系列及主要参数HG/T 2269-2003 釜用机械密封技术条件HG 21537.1-1992 碳钢填料箱(施工图)(PN0.6DN30.160)HG 21537.2-1992 不锈钢填料箱(施工图)(PN0.6DN30.160)HG 21537.3-1992 常压碳钢填料箱(施工图)(PN<0.1DN30.160)HG 21537.4-1992 常压不锈钢填料箱(施工图)(PN<0.1DN30.160)HG 21537.5-1992 管用碳钢填料箱(施工图)(PN0.6DN25200)HG 21537.6-1992 管用不锈钢填料箱(施工图)(PN0.6DN25200)HG 21537.7-1992 搅拌传动装置-碳钢填料箱HG 21537.8-1992 搅拌传动装置-不锈钢填料箱HG/T 21571-1995 搅拌传动装置--机械密封HG/T 21572-1995 搅拌传动装置--机械14.塔器部件HG 20652-1998 塔器设计技术规定HG/T 21512-1995 梁型气体喷射式填料支承板HG/T 21554.1-1995 碳钢矩鞍环填料HG/T 21554.2-1995 不锈钢矩鞍环填料HG/T21556-1995 鲍尔环填料HG/T 21556.1-1995 碳钢鲍尔环填料HG/T 21556.2-1995 不锈钢鲍尔环填料HG/T 21556.3-1995 聚丙烯鲍尔环填料HG/T 21556.4-1995 玻纤增强聚丙烯鲍尔环填料HG/T 21557-1995 阶梯环填料HG/T 21557.1-1995 碳钢阶梯环填料HG/T 21557.2-1995 不锈钢阶梯环填料HG/T 21559.1-1995 不锈钢网孔板波纹填料HG/T 21559.2-2005 不锈钢孔板波纹填料HG/T 21618-1998 丝网除沫器标准HG/T 21639-2005 塔顶吊柱JB/T 1118-2001 F1型浮阀JB/T 1119-1999 卡子JB/T 1120-1999 双面可拆连接件JB/T 1205-2001 塔盘技术条件JB/T 1212-1999 圆泡帽JB/T 2878.1-1999 X1型楔卡JB/T 2878.2-1999 X2型楔卡JB/T 3166-1999 S型双面可卸卡子15.支座、吊耳HG/T 21574-1994 设备吊耳JB/T 4712-1992 鞍式支座JB/T 4713-1992 腿式支座JB/T 4724-1992 支承式支座JB/T 4725-1992 耳式支座密封循环保护系统16.换热器零部件GB/T 12522-1996 不锈钢波形膨胀节GB 16749-1997 压力容器波形膨胀节JB/T 4718-1992 管壳式换热器用金属包垫片JB/T 4719-1992 管壳式换热器用缠绕垫片JB/T 4720-1992 管壳式换热器用非金属垫片JB/T 4721-1992 外头盖侧法兰JB/T 6171-1992 多层金属波纹膨胀节17.其他零部件HG/T 21630-1990 补强管JB/T 4736-2002 补强圈18.材料GB/T 699-1999 优质碳素结构钢GB/T 700-2006 碳素结构钢GB/T 3077-1999 合金结构钢19.板材GB/T 912-1989 碳素结构钢和低合金结构钢热轧薄钢板及钢带GB/T 2040-2002 铜及铜合金板材GB/T 2054-1980 镍及镍合金板GB/T 2531-1981 热交换器固定板用黄铜板GB/T 3274-1988 碳素结构钢和低合金结构钢热轧厚钢板和钢带GB/T 3280-1992 不锈钢冷轧钢板GB 3531-1996 低温压力容器用低合金钢钢板GB/T 3621-1994 钛及钛合金板材GB/T 3880-1997 铝及铝合金轧制板材GB/T 4237-1992 不锈钢热轧钢板GB/T 4238-1992 耐热钢板GB 6654-1996 压力容器用钢板GB/T 8165-1997 不锈钢复合钢板和钢带GB/T 8546-1987 钛-不锈钢复合板GB/T 8547-1987 钛-钢复合板GB/T 13238-1991铜钢复合钢板JB 4733-1996 压力容器用爆炸不锈钢复合钢板JB/T 4748-2002 压力容器用镍及镍基合金爆炸复合钢板20.钢管GB/T 1527-1997 铜及铜合金拉制管GB/T 1528-1997 铜及铜合金挤制管GB/T 2882-1981 镍及镍铜合金管GB/T 3624-1995 钛及钛合金管GB/T 4437.1-2000铝及铝合金热挤压管GB 5310-1995 高压锅炉用无缝钢管GB 6479-2000 高压化肥设备用无缝钢管GB/T 6893-2000 铝及铝合金拉GB/T 8163-1999 输送流体用无缝钢管GB/T 8890-1998 热交换器用铜合金无缝管GB 9948-1988 石油裂化用无缝钢管GB/T 12771-2000 流体输送用不锈钢焊接钢管GB 13296-1991 锅炉、热交换器用不锈钢无缝钢管GB/T 14976-2002 流体输送用不锈钢无缝管21.锻件JB 4726-2000 压力容器用碳素钢和低合金钢锻件JB 4727-2000 低温压力容器用低合金钢锻件JB 4728-2000 压力容器用不锈钢锻件22.棒材GB/T 1220-1992 不锈钢棒GB/T 1221-1992 耐热钢棒GB/T 4423-1992 铜及铜合金拉制棒GB/T 4435-1984 镍及镍铜合金棒GB/T 13808-1992 铜及铜合金挤制棒23.铸件GB/T 1348-1988 球墨铸铁件GB/T 2100-2002 一般用途耐蚀钢铸件GB/T 7659-1987 焊接结构用碳素钢铸件GB/T 8492-2002 一般用途耐热钢和合金铸件GB/T 9437-1988 耐热铸铁件GB/T 9439-1988 灰铸铁件GB/T 9440-1988 可锻铸铁件GB/T 11352-1989 一般工程用铸造碳钢件GB/T 14408-1993 一般工程与结构用低合金铸钢件。
压力容器焊接通用工艺规程

1目的本标准为公司对钢制压力容器的焊接通用技术规定。
2适用范围本标准适用于公司压力容器的制造,若设计图纸和专用工艺文件有特殊要求时按设计图纸和专用工艺文件执行。
压力管道元件焊接参照执行。
3焊接材料3.1凡用于压力容器的焊接材料,必须NB/T47015《承压设备用焊接材料订货技术条件》进行采购并有焊接材料的质量证明书(原件)。
在使用过程中对焊接材料产生疑义或焊接材料用于重要设备时,由焊接试验室对焊接材料的工艺性能、熔敷金属的化学成分、力学性能、弯曲性能等进行复验。
具体复验按相应的标准执行。
3.2焊接材料的代用,必须按材料代用手续经焊接责任人员批准。
母材代料可能导致焊接材料的变更,其代料单必须经由焊接责任人员会签并依照材料代用规定另行补充下达焊接材料变更手续及相应焊接工艺变更手续。
3.3焊接材料的选择3.3.1相同钢号母材的相焊1)碳素钢、低合金钢的焊缝金属应保证力学性能,且其抗拉强度不应超过母材标准规定的上限值加30Mpa。
耐热型低合金钢的焊缝金属还应保证化学成分。
2)高合金钢的焊缝金属应保证力学性能和耐腐蚀性能。
3)不锈钢复合板基层的焊缝金属应保证力学性能,且其抗拉强度不应超过母材标准规定的上限值加30Mpa;复层的焊缝金属应保证耐腐蚀性能,当有力学性能要求时还应保证力学性能;复层焊缝与基层焊缝以及复层焊缝与基层钢板的交界处宜采用过渡焊缝。
3.3.2不相同钢号母材的相焊不同强度钢号的碳素钢、低合金钢之间的焊缝金属应保证力学性能,且其抗拉强度不应超过强度较高母材标准规定的上限值。
奥氏体高合金钢与碳素钢或低合金钢之间的焊缝金属应保证力学性能和抗裂性能。
宜采用铬镍含量较奥氏体高合金钢母材高的焊接材料。
3.3.3用于焊接压力容器受压元件及与受压元件相焊的焊条、焊剂应尽量选用碱性或低氢型的4焊前准备4.1焊缝坡口型式应符合图纸或焊接工艺规程的要求。
碳素钢和标准抗拉强度下限值不大于540Mpa的强度型低合金钢可采用冷加工方法,也可采用热加工方法制备坡口。
压力容器焊接通用工艺规程
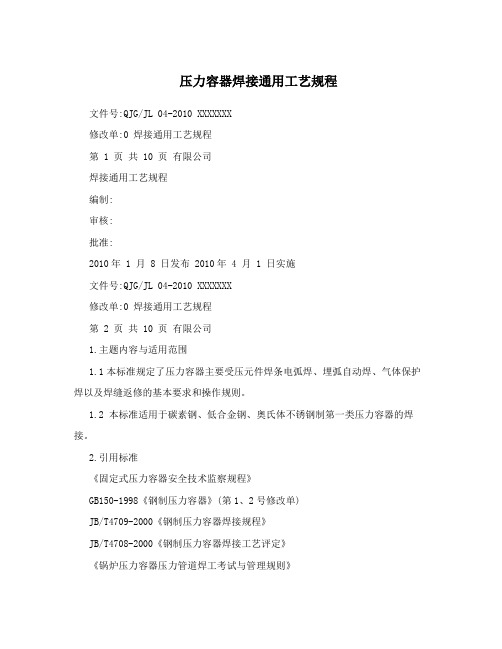
压力容器焊接通用工艺规程文件号:QJG/JL 04-2010 XXXXXXX修改单:0 焊接通用工艺规程第 1 页共 10 页有限公司焊接通用工艺规程编制:审核:批准:2010年 1 月 8 日发布 2010年 4 月 1 日实施文件号:QJG/JL 04-2010 XXXXXXX修改单:0 焊接通用工艺规程第 2 页共 10 页有限公司1.主题内容与适用范围1.1本标准规定了压力容器主要受压元件焊条电弧焊、埋弧自动焊、气体保护焊以及焊缝返修的基本要求和操作规则。
1.2 本标准适用于碳素钢、低合金钢、奥氏体不锈钢制第一类压力容器的焊接。
2.引用标准《固定式压力容器安全技术监察规程》GB150-1998《钢制压力容器》(第1、2号修改单)JB/T4709-2000《钢制压力容器焊接规程》JB/T4708-2000《钢制压力容器焊接工艺评定》《锅炉压力容器压力管道焊工考试与管理规则》JB/T4730-2005《承压设备无损检测》GB985-07《气焊、手工电弧焊及气体保护焊缝坡口的基本形式及尺寸》GB986-88《埋弧焊焊缝坡口的基本形式和尺寸》HG20583-1998《钢制化工容器结构设计规定》3. 材料3.1 焊接材料包括焊条、焊丝、焊剂、保护焊用气体等。
3.2 每批焊条应具有出厂证明和质量合格证。
3.3 焊条药皮应均匀、表面无气孔、没有明显的裂纹、脱皮现象,并存放在干燥的仓库内,要求温度?5?、相对湿度?60%,使用前对焊条按规定温度应进行烘干和保温,烘干后的焊条应放在保温筒内,随用随取,低氢型焊条一般在常温下4h 后应重新烘干,烘干次数不宜超过三次。
焊接时不允许使用受潮或药皮脱落的焊条。
3.4焊条、焊丝、焊剂及气体的选用应根据工艺、图样规定进行选择,对于非受压元件或图样中未注明的焊材可按下列原则选用。
3.4.1低碳钢、低合金钢焊接应按母材抗拉强度等级选用相应强度等级的焊材,不锈钢焊接一般应选用与母材金属成份相近的焊接材料,可按表1选用。
压力容器产品工艺文件

压力容器产品工艺文件一、产品概述:本压力容器为一款用于储存和输送压缩气体或液体的设备,由设计、制造、安装、调试和使用五个环节组成。
本文将对这五个环节进行详细描述。
二、设计:1. 根据用户需求和相关标准,确定压力容器的工作压力、温度、材料、几何尺寸等设计参数。
2. 利用计算机辅助设计软件进行压力容器的结构设计,采用有限元分析法进行强度校核。
3. 制定设计文件,包括压力容器的技术规范、设计图纸、材料清单等。
三、制造:1. 购买合格的原材料,包括金属板材、焊接材料、密封材料等。
2. 利用数控剪板机对金属板材进行裁剪,确保尺寸准确。
3. 使用焊接工艺对金属板材进行组装,包括对接焊、角焊、立焊等。
4. 对焊接接头进行无损检测,确保焊缝质量符合要求。
5. 完成焊接后,对压力容器进行喷砂处理,消除焊接残渣和氧化皮。
6. 进行压力试验,验证压力容器的耐压性能。
7. 进行泄漏试验,确保压力容器的密封性。
8. 完成涂装、标识等表面处理工作。
四、安装:1. 根据设计文件要求,选择合适的安装场地。
2. 使用合适的起重设备,将压力容器安装到指定位置。
3. 进行管道连接,确保与其他设备的接口密封可靠。
4. 安装仪表、阀门等附件,确保设备的正常运行。
五、调试及使用:1. 进行系统调试,确保压力容器和相关设备的配合运行。
2. 对压力容器进行定期检查和维护,确保设备的安全可靠。
3. 按照使用说明书规范使用压力容器,防止超负荷使用和操作失误。
六、结束语:本工艺文件详细介绍了压力容器的设计、制造、安装、调试和使用过程。
只有严格按照文件要求执行每个环节,才能保证压力容器的安全运行和长久使用。
七、质量控制:在压力容器的制造过程中,质量控制是非常重要的环节。
以下是一些质量控制措施:1. 原材料检验:在购买原材料时,要求供应商提供相关的质量检验证书,并对关键材料进行验收检查。
检查内容包括材料标识、尺寸、化学成分、力学性能等。
2. 焊接质量控制:焊接是制造过程中最关键的步骤之一,焊接质量的好坏直接影响到压力容器的安全性。
压力容器筒体制造通用工艺守则102

压力容器制造、检验通用工艺规程文件编号Q/PV-Q-3-102-2003第 1 版筒体制造通用工艺规程第0 次修改修改日期:第 1 页共8 页1总则1.1 本守则依据GB150—1998《钢制压力容器》和GB151—1999《管壳式换热器》标准,以及《压力容器安全技术监察规程》99版,结合我厂设备及技术力量,编制的压力容器筒体制造通用工艺守则。
1.2 由于压力容器种类较多,各种类型之间要求各不相同,因此,本守则若同产品设计或工艺文件有矛盾时,应以产品设计图样设计要求或工艺文件规定为准。
1.3 操作工人必须熟悉图样和工艺文件,对本岗位所使用的设备结构性能和操作规程必须了解。
1.4 筒体焊缝必须由持证合格焊工施焊。
2 材料2.1 制造筒体用的材料质量及规格应符合《容规》第10条国标、部标及相应的国家标准、行业标准有关的规定,并具有质量证明书,材料上明显部位有清晰、牢固的钢印标志或其他标志。
2.2 属下列之一的主要受压元件材料应复验2.2.1 设计图样要求复验的;2.2.2 用户要求复验的;2.2.3 制造单位不能确定材料真实性或材料的性能和化学成分有怀疑的;2.2.4 钢材质量证明书注明复印件无效或不等效的。
2.3 需要代用的材料,原则上应事先取得原设计单位出具的设计更改批准文件。
2.4 制造筒体的钢板表面不得有严重锈蚀或裂纹、斑疤、夹层等影响强度的缺陷。
2.5 严禁使用未经检验或检验不合格的材料。
3 筒体加工3.1 领料3.1.1 领料人员应根据领料单、图样、工艺过程卡,核对材料规格,材质标记,并在工艺过批准: 审核:编制: 2003.08.15实施压力容器制造、检验通用工艺规程文件编号Q/PV-Q-3-102-2003第 1 版筒体制造通用工艺规程第 0 次修改 修改日期: 第 2 页 共8 页程卡上作记录。
3.1.2 所领钢板平直度必须在允差范围内,其弧曲度与波浪度可根据具体产品图样要求确 定。
压力容器设计、制造和检测必备标准、规范
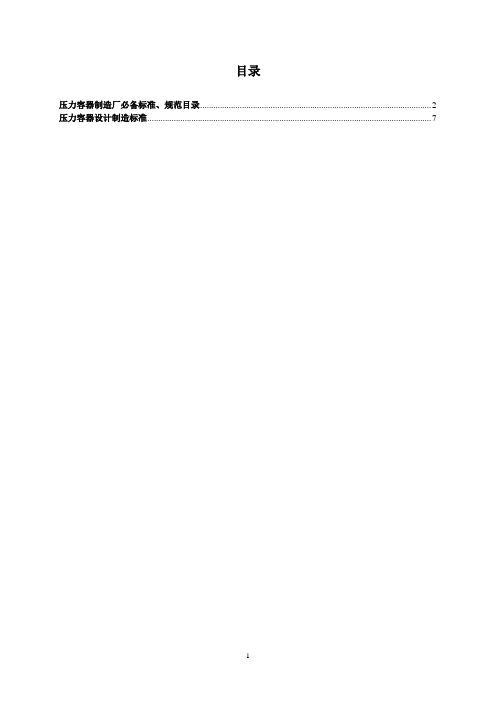
目录压力容器制造厂必备标准、规范目录 (2)压力容器设计制造标准 (7)压力容器制造厂必备标准、规范目录序号图书名称标准号数量(本)单价(元)总价(元)持有单位一、设计标准1 《钢制压力容器》GB150 8 80 640 设计4、工艺3、质检12 《钢制压力容器》标准释义 2 20 40 设计3 《管壳式换热器》GB151-19994 58 232 设计2、工艺1、质检14 《管壳式换热器》标准释义 2 48 96 设计5 《钢制压力容器—分析设计标准》及释义JB 4732-95 6 65 390 设计6 《压力容器安全技术监察规程》8 10 80 设计4、工艺3、质检17 《钢制卧式容器》JB/T4731-2005 2 60 120 设计8 《钢制塔式容器》JB/T4710-2005 1 80 80 设计9 《钢制球形储罐》GB12337-1998 1 25 25 设计10 《钢制焊接常压容器》及释义JB/T4735-1997 1 60 60 设计11 《钢制管法兰、垫片、紧固件》HG20592~20635-971 135 135 设计12 《补强圈钢制压力容器用封头》JB/T4736~4738,JB596-64,4746-20023 56 168设计、工艺、质检椭圆形封头JB/T4737-9590度折边锥形封头JB/T4738-95碟形封头JB596-64补强圈JB/T4736-200213 《压力容器法兰》JB/T4700~4707-20004 42 168设计2、工艺1、质检114 《容器支座》JB/T4712.1~4712.4-20072 100 200设计、工艺15 《钢制化工容器设计基础规定、材料选用规定、强度计算规定、结构设计规定、制造技术要求、低温压力容器技术规定》HG20580-1998~HG20585-19981 145 145 设计16 《压力容器波形膨胀节》GB16749-1997 1 38 38 设计17 《不锈钢人、手孔》HG21594~21604-19991 32 32 设计18 《焊缝符号表示法》GB/T324-2008 1 16 16 工艺、19 《标准紧固件实用手册-(第四版)》1 96 96 设计《普通螺纹基本尺寸》GB/T 196-2003《普通螺纹公差》GB/T 197-2003《普通螺纹收尾肩距退刀槽和倒角|》GB/T 3-1997《六角螺母》GB/T41-2000《I型六角螺母》GB/T6170-2000《紧固件表面缺陷螺母》GB/T5779.2-2000《六角头螺栓》GB/T5782-2000《六角头螺栓C级》GB/T5780-2000《普通螺纹公差》GB/T197-2003《紧固件机械性能螺栓、螺钉和螺柱》GB 3098.1-2000《紧固件机械性能螺母细牙螺纹》GB 3098.4-200020 《钢制人手孔》HG21514~21535-20051 148 148 设计21 《腐蚀数据与选材手册》 1 80 80 设计22 《设备吊耳》HG/T21574-94 1 18 18 设计23 《压力容器中化学介质毒性危害和爆炸危险程度分类》HG 20660-2000| 1 50 50 设计24 《JB/T 4718-1992管壳式换热器用金属包垫片》JB/T 4714~4720-1992;JB4721-1992;JB/T4722~4723-19921 150 150 设计25 《管路法兰及垫片》JB/T 74~90-94 1 85 85 设计二、工艺标准1《钢制压力容器焊接工艺评定、钢制压力容器焊接规程、承压设备产品焊接试件的力学性能检验》JB4708-2000、JB 4709-2000JB4744-20003 39 117工艺2、质检12 《钢制压力容器焊接评定、规程、性能检验》标准释义1 36 36 工艺3 《气焊、手工电弧焊及气体保护焊焊缝坡口的基本形式与尺寸》GB985-88 1 13 13 工艺4 《埋弧焊焊缝坡口的基本形式和尺寸》GB986-88 1 13 13 工艺5 《热处理工程师手册(第2版)》 1 89 89 工艺6 《热处理技术数据手册》 1 85 85 工艺三、材料标准1 《锅炉和压力容器用钢板》GB713-2008 3 14 42设计、工艺、质检2 《压力容器用钢板》GB6654-19963 10 30 设计、工艺、质检3 《压力容器用钢锻件压力JB4726~4728-2000 3 38 114 设计、工容器用镍铜合金》JB4741~4743-2000 艺、质检4 《压力容器用爆炸不锈钢复合钢板》JB 4733 -1996 1 12 12 设计5 《不锈钢复合钢板和钢带》GB/T 8165-2008 1 40 40 设计6《碳素结构钢和低合金结构钢热轧薄钢板和钢带》GB 912-2008 1 10 10 设计7 《不锈钢冷轧钢板和钢带》GB/T 3280-2007 1 26 26 设计8 《不锈钢热轧钢板和钢带》GB/T 4237-2007 1 26 26 设计9 《低温压力容器用低合金钢板》GB 3531-2008 1 14 14 设计10 《耐热钢钢板和钢带》GB/T4238-2007 1 18 18 设计11 《碳素结构钢和低合金结构钢热轧厚钢板和钢带》GB3274-2007 1 10 10 设计12 《合金结构钢》GB 3077-1999 1 13 13 设计13 《不锈钢焊条》GB/T983-1995 1 15 15 工艺14 《结构用无缝钢管》GB/T 8162-2008 1 16 16 设计15 《结构用不锈钢无缝钢管》GB/T 14975-2002 1 12 12 设计16 《输送流体用无缝钢管》GBT 8163-2008 1 12 12 设计17 《流体输送用不锈钢无缝钢管》GB/T14976-2002 1 12 12 设计18 《不锈钢棒》GB/T1220-2007 1 24 24 设计19 《耐热钢棒》GB/T1221-2007 1 22 22 设计20 《高压锅炉用无缝钢管》GB 5310-2008 1 22 22 设计21 《高压化肥设备用无缝钢管》GB6479-2000 1 20 20 设计22 《石油裂化用无缝钢管》GB9948-2006 1 20 20 设计23 《锅炉、热交换器用不锈钢无缝钢管》GB 13296-2007 1 16 16 设计24 《优质碳素结构钢》GB/T 699-1999 1 20 20 设计25 《碳素结构钢》GB700-2006 1 15 15 设计四、制造检测类标准1 《承压设备无损检测》JBT 4730-2005 4 170 680 设计2、工艺1、质检12 《金属夏比缺口冲击试验方法》GB/T229-2007 1 18 18 质检3 《金属低温夏比冲击试验方法》GB 4159-1984 1 8 8 质检4 《金属洛氏硬度试验方法》GB/T230-2004 1 20 20 质检5 《金属材料室温拉伸试验方法》GB 228-2002 1 40 40 质检6 《金属材料弯曲试验方法》GB232-1999 1 10 10 质检7 《厚钢板超声波检验方法》GB/T2970—2004 1 20 20 质检8 《金属材料金相热处理检验方法标准汇编》GB/T18876-2006 1 208 208 质检9 《金属和合金的腐蚀不锈钢晶间腐蚀试验方法》GB/T 4334-2008 1 18 18 质检10 《承压设备用钢焊条技术条件》JB/T4747-2002 1 38 38 质检11 《一般公差-未注公差的线性和角度尺寸的公差》GB-T 1804-2000 3 170 510设计、工艺、质检12 《热轧钢板和钢带的尺寸外形重量及允许偏差》GB/T709-2006 3 14 42设计、工艺、质检13 《压力容器涂敷与运输包装》JB/T4711-2003 3 30 90设计、工艺、质检合计117 5928压力容器设计制造标准2.1 GB150-1998 钢制压力容器2.2 GB151-1999 管壳式换热器2.3 GB12337-1990 钢制球形贮罐2.4 GB5044-1985 职业性接触毒物危险程度分级2.5 JB4710-2000 钢制塔式容器2.6 JB4732-1994 钢制压力容器-另一标准2.7 JB/T 4711-2003 压力容器涂敷与运输包装2.8 JB/T4717-1992 浮头式换热器和冷凝器型式与基本参数2.9 JB/T4715-1992 固定管板式换热器型式与基本参数2.10 JB/T4716-1992 立式热虹吸式重沸器型式与基本参数2.11 JB/4717-1992 U型管式换热器型式与基本参数2.12 JB/T4735-1997 钢制焊接常压容器2.13 HG20580-1998 钢制化工容器设计基础规定2.14 HG20581-1998 钢制化工容器材料选用规定2.15 HG20582-1998 钢制化工容器强度计算规定2.16 HG20583-1998 钢制化工容器结构设计规定2.17 HG20584-1998 钢制化工容器制造技术规定2.18 HG20585-1998 钢制低温压力容器技术规定2.19 HG20652-1998 塔器设计技术规定2.20 HG21503-1992 钢制固定式薄管板列管换热器2.21 HG20660-1991 压力容器用化学介质毒性危害和爆炸危险程度分类2.22 HG20536-1993 聚四氟乙烯衬里设备2.23 HG/T20678-1991 衬里钢壳设计技术规定2.24 HG/T20677-1990 橡胶衬里化工设备2.25 HG/T20679-1990 化工设备、管道外防腐设计规定2.26 HG/T20569-1994 机械搅拌设备2.27 CD130A3-1984 不锈钢复合钢板焊接压力容器技术条件2.28 HG/T 21563-21572-95 搅拌传动装置2.29 HG/T20668-2000 化工设备设计文件编制规定2.30 TCED41002-2000 化工设备图样技术要求2.31 TEMA 美国管式换热器制造商协会标准2.32 JB/T4718-1992 管壳式换热器用金属包垫片2.33 JB/T4718-1992 管壳式换热器用缠绕垫片2.34 JB/T4719-1992 管壳式换热器用非金属包垫片2.35 JB/T4720-1992 外头盖恻法兰2.36 JB/T17261-1998 钢制球形储罐形式与基本参数3.1 GB567-1999 爆破片与爆破片装置3.2 GB9112-9123-1988 钢制管法兰3.3 GB1220-12240-1989 通用阀门3.4 GB12241-12243-1989 安全阀3.5 GB12244-12246-1989 减压阀3.6 GB12247-12251-1989 蒸汽疏水阀3.7 GB6749-1997 压力容器波形膨胀节3.8 GB/T3098.1-2000 紧固件机械性能螺栓、螺钉和螺柱3.9 GB/T3098.2-2000 紧固件机械性能螺母粗牙螺纹3.10 GB/T12252-1989 通用阀门供货要求3.11 GB/T13306-1991 标牌3.12 GB/T9019-2001 压力容器公称直径3.13 JB8-1982 产品标牌3.14 JB576-1964 碟形封头3.15 JB4700-4707-2000 压力容器法兰3.16 JB4729-1994 旋压封头3.17 JB/T84-1994 凹凸面对焊环板式松套钢制管法兰3.18 JB/T85-1994 翻边板式松套钢制管法兰3.19 JB/T86.1-1994 凸面钢制管法兰盖3.20 JB/T86.2-1992 凹凸面钢制管法兰盖3.21 JB/T4712-1992 鞍式支座3.22 JB/T4713-1992 腿式支座3.23 JB/T4724-1992 支承式支座3.24 JB/T4725-1992 耳式支座3.25 JB/T4736-2002 补强圈3.26 JB/T4737-1995 椭圆形封头(作废)3.27 JB/54738-1995 90°折边锥形封头3.28 JB/T4739-1995 60°折边锥形封头3.29 JB/T4746-2002 钢制压力容器用封头3.30 HG5-220-1965 浆式搅拌器3.31 HG5-221-1965 涡轮式搅拌器3.32 HG5-222-1965 推进式搅拌器3.33 HG5-227-1980 玻璃管液面计3.34 HG5-748-1978 釜用机械密封基本型式及参数3.35 HG5-751-756-1978 机械密封装置3.36 HG5-757-1978 钢制框式搅拌器3.37 HG5-1364-1370-1980 玻璃板液面计3.38 HG20527-1992 不锈钢凸面对焊钢制管法兰3.39 HG20528-1992 衬里钢管用承插环松套钢制管法兰3.40 HG20529-1992 不锈钢衬里法兰盖3.41 HG20530-1992 钢制管法兰用焊唇密封环3.42 HG20592-20635-1997 钢制管法兰、垫片、紧固件3.43 HG21505-1992 组合式视镜3.44 HG21506-1992 补强圈3.45 HG21514-21535-1995 碳素钢、低合金钢制人孔和手孔3.46 HG21537.1-21537.6-1992 填料箱3.47 HG21594-21604-1999 不锈钢人孔3.48 HG/T21550-1993 防霜液面计3.49 HG/T21575-1993 设备吊耳3.50 HG/T21583-1995 快开不锈钢活动盖3.51 HG/T21584-1995 磁性液位计3.52 HG/T21619-21620-1986 压力容器视镜3.53 HG/T21622-1990 衬里视镜3.54 HG/T21630-1990 补强管3.55 TH3009-1959 无折边球形封头3.56 JB4731-2000 钢制卧式容器(含标准释义)3.57 JB/T4722-1992 管壳式换热器用螺纹换热器基本参数与技术条件3.58 JB/T4723-1992 不可拆卸螺纹换热器形式与基本参数4.1 GB/T699-1999 优质碳素结构钢4.2 GB/T700-1988 碳素结构钢4.3 GB/T710-1991 优质碳素结构钢热轧薄钢板和钢带4.4 GB/T711-1988 优质碳素结构钢热轧厚钢板和宽钢带4.5 GB/T712-2000 船体用结构钢4.6 GB/T713-1997 锅炉用钢板4.7 GB/T716-1991 碳素结构钢冷轧钢带4.8 GB/T 912-1989 碳素结构钢和低合金结构钢热轧薄钢板及钢带4.9 GB/T1220-1992 不锈钢棒4.10 GB/T1221-1992 耐热钢棒4.11 GB/T1591-1994 低合金高强度结构钢4.12 GB/T2101-1989 型钢验收、包装、标志及质量证明书的一般规定4.13 GB/T3077-1999 合金结构钢4.14 GB/T3087-1999 低中压锅炉用无缝钢管4.15 GB/T3274-1988 碳素结构钢和低合金结构钢热轧厚钢板和钢带4.16 GB/T3280-1992 不锈钢冷轧钢板4.17 GB/T3522-1983 优质碳素结构钢冷轧钢带4.18 GB/T3524-1992 碳素结构钢和低合金结构钢热轧钢带4.19 GB/T4237-1992 不锈钢热轧钢板4.20 GB/T4238-1992 耐热钢板4.21 GB/T5310-1995 高压锅炉用无缝钢管4.22 GB6479-2000 高压化肥设备用无缝钢管4.23 GB6654-1996 压力容器用钢板4.24 GB/T8162-1999 结构用无缝钢板4.25 GB/T8163-1999 输送流体用无缝钢管4.26 GB/T8165-1997 不锈钢复合钢板和钢带4.27 GB/T9948-1988 石油裂化用无缝钢管4.28 GB/T11251-1989 合金结构钢热轧厚钢板4.29 GB/T11253-1898 碳素结构钢和低合金结构钢冷轧薄钢板及钢带4.30 GB/T12770-1991 机械结构用不锈钢焊接钢管4.31 GB/T12771-2000 流体输送用不锈钢焊接钢管4.32 GB/T13237-1991 优质碳素结构风冷轧薄钢板和钢带4.33 GB/T13296-1991 锅炉、热交换器用不锈钢无缝钢管4.34 GB/T14292-1993 碳素结构钢和低合金结构钢热轧条钢技术条件4.35 GB/T14976-1994 流体输送用不锈钢无缝钢管4.36 YB/T5059-1993 低碳钢冷轧钢带4.37 YB/T5139-1993 压力容器用热轧钢带4.38 YB(T)32-1986 高压锅炉用冷拔无缝钢管4.39 YB(T)33-1986 低中压锅炉用冷拔无缝钢管4.40 YB(T)40-1986 压力容器用碳素钢和低合金钢厚钢板4.41 YB(T)41-1987 锅炉用碳素钢及低合金钢厚钢板4.42 YB(T)44-1986 流体输送用电焊钢管4.43 JB4726-4728-2000 压力容器用钢铸件4.44 JB4741-4743-2000 压力容器用镍铜合金11。
- 1、下载文档前请自行甄别文档内容的完整性,平台不提供额外的编辑、内容补充、找答案等附加服务。
- 2、"仅部分预览"的文档,不可在线预览部分如存在完整性等问题,可反馈申请退款(可完整预览的文档不适用该条件!)。
- 3、如文档侵犯您的权益,请联系客服反馈,我们会尽快为您处理(人工客服工作时间:9:00-18:30)。
1.适用范围及照相质量等级1.1。
本工艺规程规定了承压设备金属材料受压元件的熔化焊对接接头的X射线检测方法、底片质量和质量分级的要求。
1.2本工艺规程适用于承压设备受压元件的对接焊接接头的检测。
用于制作焊接接头的金属材料包括碳素钢、低合金钢、不锈钢。
1.2射线照相质量等级不应低于AB级。
对重要设备、结构专门材料和专门焊接工艺制作的对接焊接接头,可采纳B级技术进行检测。
1,3非承压设备元件对接焊接接头的X射线检测可参照使用。
2.制定依据及参考标准《固定式压力容器安全技术监察规程》GB150.1-4—2011 《压力容器》JB/T4730.2—2005 《承压设备无损检测》射线检测JB/T4730.1—2005 《承压设备无损检测》通用部分GBZ117-2002 《工业X射线探伤放射卫生防护标准》JB/T7902-2006 无损检测射线照相检测用线型像质计JB/T7902-1999 线型象质计JB/T7903-1999 工业射线照相底片观灯片HB7684-2000 射线照相用线型象质计3.人员资格及职责3.1从事射线检测的人员应按照《特种设备无损检测人员考核与监督治理规则》的要求持有国家质量技术监督部门颁发的与其工作相适应的技术等级资格证书。
评片人员必须持有中级及以上资格证书。
3.2从事射线检测人员上岗前应进行辐射安全知识的培训,并取得放射工作人员证。
3.3射线检测人员必须躯体健康,经体检合格,评片人员视力应每年检查一次。
未经矫正或经矫正的近(距)视力和远(距)视力应不低于5.0(小数记录值为1.0)。
3.4射线检测人员应能熟练操作射线机,正确选用透照工艺,合理使用暗室处理方法,并应熟悉焊接工艺、金属材料等知识,应了解压力容器制造工艺,熟悉有关压力容器的法规、标准和技术条件。
3. 5对接接头的表面质量要求应符合通用部分4.2条要求。
4.射线检测和验收标准4.1范围:必须符合《容规》,GB150和设计文件的要求。
4.2凡要求进行百分百射线检测的容器,对其A类,B类焊接接头应不低于JB4730.2-2005标准中质量等级Ⅱ级的要求。
凡局部射线检测的容器,对其A类和B类焊接接头应不低于JB4730.2-2005标准中质量等级Ⅲ级的要求,检测长度许多于各条焊接接头总长的20%,且许多于250mm。
4.3 局部射线检测的容器对其所有的T型连接部位,以及拼接封头(管板)的对接接头,必须进行射线检测。
4.4局部射线检测的容器,如在焊接接头上开孔,则以开孔中心为圆心,1.5倍开孔直径为半径的圆中所包容的焊接接头,被补强圈、支座、垫片、内件等所覆盖的焊接接头必须进行射线检测。
4.5如封头采纳拼接焊缝,则在压制之后进行100%射线检测。
公称直径大于250mm的接管对接接头应进行射线检测。
4.6对局部射线检测的焊接接头,若在检测部位发觉超标缺陷时,则应返修, 并在该缺陷两端的延伸部位,增加许多于该焊缝长度的10%的补充检查,且不小于250mm,若仍有不同意的缺陷时,则对该条焊接接头做100%的射线检测。
5.检验程序5.1焊缝外观经焊接检验人员检验合格,由检验员填写好承压设备被检工件编号后开出无损检测通知单及设备制作流转过程卡,送交检测室。
无损检测室接到托付单后,方可安排射线检测5.2焊缝及热阻碍区若不符3.5的要求时,无损检测室应将托付单反馈焊接检验员。
5.3除非另有规定,射线检测应在焊后进行,对有延迟裂纹倾向的材料,至少应在焊接完成24h后进行射线检测。
5.5探伤室RT-II级或III级人员依照有关标准、按本工艺做好一切预备工作,并编制射线探伤专用工艺卡,操作人员按本工艺程序进行操作、暗室处理和底片评定。
6.布片(划线)规定6.1焊缝射线检测编号的规定。
6.1.1产品试板的编号,按该试板所代表的产品编号为检测编号。
同时应有试板的编号1AS1、1AS2……(连1A纵缝).工艺评定试板的工艺评定号为检测编号,片号以S1、S2…表示之。
6.1.2 整台产品以产品编号作为检测编号.6.1.3 整台产品的焊缝编号以焊接工艺卡节点图上的编号为依据,纵缝以“A”表示,第一条纵缝为1A、第二条纵缝为2A。
纵缝第1张为A1、纵缝第2张为A2。
如第1条纵缝第二张片即以1A2表示之。
环缝以“B”表示,第一条环缝为1B、第二条环缝为2B。
环缝第1张B1、环缝第2张为B2。
如第1条环缝第二张片即以1B2表示之6.1.4 封头焊缝检测以“FA”表示,第一条1FA表示,第一张片为1FA1表示,封头焊缝以所配的产品编号及焊卡上的编号为准6.1.5焊缝返修标记,一次返修在片号后加“R1”,二次返修在片号后加“R2”表示,增拍片在片号前加”Z”表示。
如:1B1R1表示第一条焊缝第一张片第一次返修。
1B1R2表示第一条焊缝第一张片第二次返修。
Z1B3表示第一条环缝第三张片,该片为增拍片。
6.1.6不论检测比例如何,检测人员对容器均应按100%检测划线。
对直径较大或壁厚较厚的容器环焊缝划线时,应注意限制累积误差和筒体内外中心位置的重叠准确性,在容器内中心曝光只要在容器外壁划线布片。
6.2焊缝检测一次透照长度L3和透照等分数N的确定。
6.2.1 纵缝(包括试板纵缝)的L3规定一般为300mm。
专门情况下L3可增大和缩小,但应满足AB级K≯1.03, B级K≯1.01要求。
封头、旋边R处(折边)部分应单独按K值要求进行划线布片6.2.2 环缝;周向机;中心周向-次曝光则依照JB4730.2-2005标准,L3规定一般为300mm。
定向机;对外径大于100mm环对接接头透照次数确定方法按取JB4730.2-2005附录D执行, 但应满足AB级K≯1.1, B级K≯1.06要求。
所需最少透照次数与透照方式和透照厚度比有关,这一数值可从图D.1-D.6中直接查出, 首先计算和查图表,确定整圈环缝透照等分数N,再以下式计算L3。
L3′=πD/N并依照L3′取整数确定L3,注:1)为保证相邻边界标记能重叠,防止漏检,标记带上的搭接标记可适当扩展。
2)透照长度应操纵在300mm以内;公称厚度较厚时,透照长度应操纵在280mm以内。
6.3 布片(划线)方法6.3.1全部(100%)和局部≥20%射线透照检测的产品均采纳100%布片,对局部检测的产品除本工艺规定必须检测的部位外,由检测人员或焊接检验员自行任意抽查.布片(划线)方法检测人员在摄片定位图中注明。
6.3.2纵缝(包括封头拼缝)的具体布片顺序,从该焊缝的一端(左)到另一端(右)进行划分片号,序号由小到大。
环缝首先从容器的1B之T字接头处开始按顺时针划分片号,以同样的方法划分其余各环缝片号,片号由小到大用阿拉伯数字表示(1B1在1A1丁字口处,2B1在2A1的丁字口处,以此类推)。
6.4 射线透照检测部位打钢印规定:6.4.1纵缝的起始号1号片, 2号片及最后一张片位置应打焊缝编号,环缝包括1号片, 2号片、所有丁字口及最后一张片位置应打焊缝编号。
包括片号、中心标记、所有位置应打中心标记、中心标记钢印与标记带上的中心位置必须重合。
6.4.2其余透照部位应在摄片定位图中注明,所摄片号,并与实物、X光底片相符,保证追溯的准确性和重复性。
6.4.3凡打钢印的部位,钢印应离焊缝边缘10-20mm,深度不宜超过0.5mm。
6.4.4对某种专门的材料不准打钢印的产品,由检测人员负责绘制详细焊缝检测部位示意图,标注尺寸,并用由色笔在检测部位写上焊缝编号、片号及中心标记。
7射线透照器材选择要求7.1射线透照7.1.1选用的射线源至工件表面的距离f应满足如下要求:…AB级射线检测技术:f≥10d.b22/3…B级射线检测技术:f≥15d.b22/3射线源至工件表面的距离最小距离满足JB/T4730.2—2005第4.3条. 图2要求.7.1.2曝光量; 当焦距为700mm时曝光量推举值为;AB级为不小于15毫安分,B级为不小于20毫安分, 当焦距改变时按平方反比定律对曝光量进行换算。
7.1.3. 射线能量;x射线照相应尽量选用较低管电压. 本公司现有四台射线能量不同的x光机. 可在曝光曲线范围内择优选择. X光机能量应留有20%余量,以保证仪器使用寿命。
7.1.3对每台X射线机均应作出经常检测材料的曝光曲线,依据曝光曲线确定曝光参数。
对使用中的曝光曲线每年应校验一次。
(祥见曝光曲线制作)7.2射线胶片;AB 级采纳T3类或更高级胶片如:Agfa C7,B 级采纳T2类胶片或更高级胶片胶片的本底灰雾度不大于0.3.7.3增感屏:采纳铅箔增感,前屏厚度0.02-0.05mm ,后屏厚度大于前屏,一般采纳0.03/0.03。
增感屏和胶片在透照中应保证紧贴。
7.4暗盒:一般使用80X360mm ,暗盒不得漏光,对初次制定的检测工艺,或使用中工艺条件及环境发生改变时,应进行背散射防护检查,暗盒背面要贴附“B ”铅字标记。
(其高度为13mm ,厚度为16mm )。
7.5像质计:7.5.1线型像质计的型号&规格应符合JB/T7902的规定,其线号、丝径应符合HB7684的有关规定。
7.5.2像质计的选用应符合下列表格的要求。
表1 单壁透照、像质计置于源侧(AB 级)注; 其它透照方法,像质计的选用应符合满足JB/T4730.2—2005表6, 表7要求.不同焊接型式的透照厚度W 见 表2注:1)T ――表示受检工件名义厚度。
2)W ――表示射线照耀方向上的公称厚度。
多层透照时,透照厚度为通过的各层材料公称厚度之和。
(不考虑垫板厚度及余高)3)焊缝两侧母材厚度不同时,以薄板厚度计算。
7.5.3像质计应放在射源一侧的工件表面上被检区的一端(被检区长度1/4部位)钢丝应横跨焊缝垂直细钢丝置于外侧。
7.5.4单壁透照时像质计应放置在源侧,双壁单影透照时像质计应放置于胶片侧。
双壁双影透照时可放置于源侧,也可放置于胶片侧。
7.5.5单壁透照中,假如像质计无法放置于源侧,也可放置于胶片侧。
但应进行对比试验,以保证实际透照的底片灵敏度符合要求。
7.5.6小径管(D0≤100MM)可选用线型像质计或JB/T4730.2-2005附录F规定的专用(等径金属丝)像质计,金属丝应横跨焊缝放置。
7.5.7底片黑度均匀部位(一般是邻近焊缝的母材金属区)能够清晰地看到长度不小于10mm的连续金属丝影像时,则认为该丝是识不的。
专用像质计至少应识不两根金属丝。
7.6标记:7.6.1被检测的每段焊缝附近(底)应有下列铅质的识不标记,产品编号、像质返修标记“R”,需增拍时还应增拍标记“Z”,及必要时的“F”标记。
其排列示意如下图。
搭接标记工作令号焊缝编号及号片增拍编号标记搭接标记像质计像质计放胶片侧标记注:透照日期的放置按惯例排列6位数进行。