基于PLC的锅炉燃烧控制系统
基于PLC单片机控制中小型蒸汽锅炉智能燃烧系统

产。
4
3、锅炉引风控制
炉膛负压控制系统一般采用的控制流程图 如下图所示,调节原理比较简单属于单闭 环调节系统,它的输入量是炉膛负压输出 量是引风变频器,同时引入鼓风量作为前 馈信号。
给定蒸汽压力
+ -
引风调节单元
引风机变频器
锅炉系统
抗干扰滤波
炉膛负压信号
5
4、锅炉鼓风控制
鼓风控制系统一般采用的控制流程图如下图所示,
先通过蒸汽压力变送器经滤波后取得信号,与设 定蒸汽压力进行比较,判断出鼓风PID调节器调节 的方向和大小,通过鼓风PID调节单元计算出鼓风 变频器的输出大小
给定蒸汽压力
+ -
炉排调节单元
风煤比
炉排变频器
鼓风调节单元 抗干扰滤波
鼓风变频器 蒸汽压力信号
炉排系统
6
二、控制系统硬件设计
PLC不仅具有逻辑控制功能,而且还具有了 运算、数据处理和数据传送等功能 ,采用可编 程控制器设计的控制系统可以实现对锅炉精确地 实时自动控制,并且实现了整个系统的优化控制。 变频调速的基本原理是通过改变电动机工作电源 频率达到改变电机转速的目的,采用变频调速技 术来控制锅炉的泵与风机,可以使电动机不必总 在工频下运行,可以大大的节省电能。
2、程序设计结果,见论文P35~P37
13
四、上位机系统制作
MCGS (Monitor and Control Generated System, 通用监控系统)是一套用于快速构造和生成计算机 监控系统的组态软件,它能够在基于Microsoft (各种 32 位 Windows 平台上)运行,通过对现 场数据的采集处理,以动画显示、报警处理、流 程控制、实时曲线、历史曲线和报表输出等多种 方式向用户提供解决实际工程问题的方案,它充 分利用了 Windows图形功能完备、界面一致性好、 易学易用的特点,在自动化领域有着广泛的应用。
基于PLC的锅炉燃烧控制系统设计_毕业设计论文正文

基于PLC的锅炉燃烧控制系统设计1 绪论1.1锅炉燃烧控制项目的背景改革开放以来,我国经济社会快速发展,生产力水平不断提高,在生产中,锅炉起着十分重要的作用,尤其是在火力发电中发挥重要作用的工业锅炉,是提供能源动力的主要设备之一。
锅炉产生的蒸汽可以作为蒸馏,干燥,反应,加热等各过程的热源,另外也可以作为动力源驱动动力设备。
工业过程中对于锅炉燃烧控制系统的要求是非常高的,要求锅炉燃烧控制系统必须满足控制精度高,响应速度快[1]。
作为一个非常复杂的设备,锅炉同时具有了数十个包括了扰动、测量、控制在内的参数,参数之间有着复杂的关系,并且相互关联[2]。
而锅炉燃烧过程中的效率问题、安全问题一直是大众关注的重要方面。
1.2锅炉燃烧控制的发展历史对于锅炉燃烧的控制,已经经历了四个阶段[3~5](1)手动控制阶段因为20世纪60年代以前,电力电子技术和自动化技术还没有得到完全发展,技术尚不成熟,因此,这个时期工业人员的自动化意识不强,锅炉燃烧的控制方式一般多采用纯手动的方法。
这种控制方法,要求进行控制的操作工人依靠他们的经验决定送风量,引风量,给煤量的多少,然后利用手动的操作工具等操控锅炉,该方法控制的程度完全取决于操作工人的经验。
因此,要求操作工人必须具有非常丰富的经验,这样无疑大大提高了操作工人的劳动强度,由十人的主观意识,所以事故率非常大,同时,也不能保证锅炉高效稳定的运行。
(2)仪器继电器控制阶段随着科技的不断进步,自动化技术以及电力电子技术快速提高,国内外以继电器为基础的自动化仪表工业锅炉控制系统也得到发展,并且广泛应用于实际生产过程。
在上个世纪60年代前期,我国锅炉的控制系统开始得到迅速发展;到了60年代的中后期,我国引进了国外全自动的燃油锅炉的控制系统;到了上个世纪的70年代末,我国逐渐自主研发了一些工业锅炉的自动化仪器,同时,在工业锅炉的控制系统方面也在逐步推广应用自动化技术。
在仪表继电器控制阶段,锅炉的热效率得到了提高,并且大幅度的降低了锅炉的事故率。
基于PLC的锅炉燃烧控制系统设计
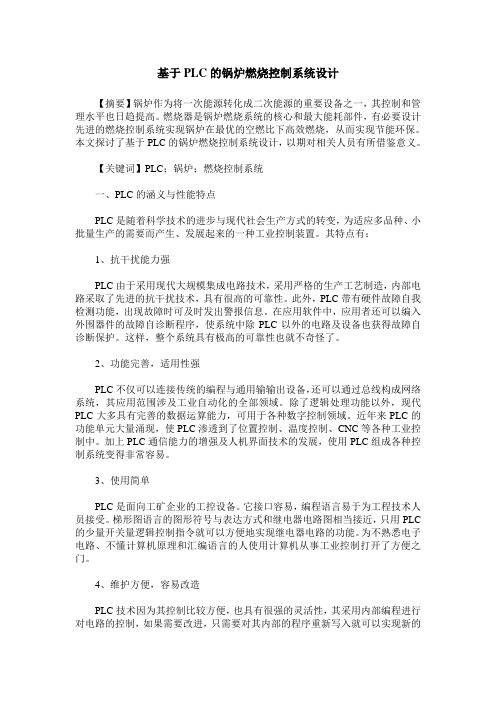
基于PLC的锅炉燃烧控制系统设计【摘要】锅炉作为将一次能源转化成二次能源的重要设备之一,其控制和管理水平也日趋提高。
燃烧器是锅炉燃烧系统的核心和最大能耗部件,有必要设计先进的燃烧控制系统实现锅炉在最优的空燃比下高效燃烧,从而实现节能环保。
本文探讨了基于PLC的锅炉燃烧控制系统设计,以期对相关人员有所借鉴意义。
【关键词】PLC;锅炉;燃烧控制系统一、PLC的涵义与性能特点PLC是随着科学技术的进步与现代社会生产方式的转变,为适应多品种、小批量生产的需要而产生、发展起来的一种工业控制装置。
其特点有:1、抗干扰能力强PLC由于采用现代大规模集成电路技术,采用严格的生产工艺制造,内部电路采取了先进的抗干扰技术,具有很高的可靠性。
此外,PLC带有硬件故障自我检测功能,出现故障时可及时发出警报信息。
在应用软件中,应用者还可以编入外围器件的故障自诊断程序,使系统中除PLC以外的电路及设备也获得故障自诊断保护。
这样,整个系统具有极高的可靠性也就不奇怪了。
2、功能完善,适用性强PLC不仅可以连接传统的编程与通用输输出设备,还可以通过总线构成网络系统,其应用范围涉及工业自动化的全部领域。
除了逻辑处理功能以外,现代PLC大多具有完善的数据运算能力,可用于各种数字控制领域。
近年来PLC的功能单元大量涌现,使PLC渗透到了位置控制、温度控制、CNC等各种工业控制中。
加上PLC通信能力的增强及人机界面技术的发展,使用PLC组成各种控制系统变得非常容易。
3、使用简单PLC是面向工矿企业的工控设备。
它接口容易,编程语言易于为工程技术人员接受。
梯形图语言的图形符号与表达方式和继电器电路图相当接近,只用PLC 的少量开关量逻辑控制指令就可以方便地实现继电器电路的功能。
为不熟悉电子电路、不懂计算机原理和汇编语言的人使用计算机从事工业控制打开了方便之门。
4、维护方便,容易改造PLC技术因为其控制比较方便,也具有很强的灵活性,其采用内部编程进行对电路的控制,如果需要改进,只需要对其内部的程序重新写入就可以实现新的控制要求。
基于PLC的锅炉供热控制系统的设计

基于PLC的锅炉供热控制系统的设计一、本文概述随着科技的不断发展,可编程逻辑控制器(PLC)在工业自动化领域的应用日益广泛。
作为一种高效、可靠的工业控制设备,PLC以其强大的编程能力和灵活的扩展性,成为现代工业控制系统的重要组成部分。
本文旨在探讨基于PLC的锅炉供热控制系统的设计,通过对锅炉供热系统的分析,结合PLC控制技术,实现对供热系统的智能化、自动化控制,提高供热效率,降低能耗,为工业生产和居民生活提供稳定、可靠的热源。
文章首先介绍了锅炉供热系统的基本构成和工作原理,分析了传统供热系统存在的问题和不足。
然后,详细阐述了PLC控制系统的基本原理和核心功能,包括输入/输出模块、中央处理单元、编程软件等。
在此基础上,文章提出了基于PLC的锅炉供热控制系统的总体设计方案,包括系统硬件选型、软件编程、系统调试等方面。
通过本文的研究,期望能够实现对锅炉供热控制系统的优化设计,提高供热系统的控制精度和稳定性,降低运行成本,促进节能减排,为工业生产和居民生活提供更加安全、高效的供热服务。
也为相关领域的研究人员和技术人员提供有价值的参考和借鉴。
二、锅炉供热系统基础知识锅炉供热系统是一种广泛应用的热能供应系统,其主要任务是将水或其他介质加热到一定的温度,然后通过管道系统输送到各个用户端,满足各种热需求,如工业生产、居民供暖等。
该系统主要由锅炉本体、燃烧器、热交换器、控制系统和辅助设备等几部分构成。
锅炉本体是供热系统的核心设备,负责将水或其他介质加热到预定温度。
其根据燃料类型可分为燃煤锅炉、燃油锅炉、燃气锅炉、电锅炉等。
锅炉的性能参数主要包括蒸发量、蒸汽压力、蒸汽温度等。
燃烧器是锅炉的重要组成部分,负责燃料的燃烧过程。
燃烧器的性能直接影响到锅炉的热效率和污染物排放。
燃烧器需要稳定、高效、低污染,同时要适应不同的燃料类型和负荷变化。
热交换器是锅炉供热系统中的关键设备,负责将锅炉产生的热能传递给水或其他介质。
热交换器的设计应保证高效、稳定、安全,同时要考虑到热能的充分利用和防止结垢、腐蚀等问题。
基于PLC的蒸汽锅炉控制系统的设计

基于PLC的蒸汽锅炉控制系统的设计摘要:目前,随着工业的发展,锅炉作为能源转化的重要动力设备之一,其主要作用体现在城市供热和现代化工业生产中。
由于我国目前多数主流锅炉自动化控制水平不高,许多问题接踵而至,比如能源转化率低,导致资源浪费和环境污染;工人的操作水平参差不齐,导致各种安全隐患等。
通过现代化控制手段改造锅炉的燃烧系统,可以提高能源转化率,有效减少资源的浪费。
利用上位机实时监控生产全过程,降低风险,减少一线人员的工作量。
这样在节约能源的同时,也保证了生产运行的安全。
关键词:PLC;蒸汽锅炉;控制系统引言在工业生产阶段,应用与之相匹配的设备不仅能够有效提高生产效率,更能实现对成本的合理缩减。
尤其是在锅炉生产中,安全指标的提升逐渐成为长远发展的关键点,蒸汽锅炉的正确使用也就显得尤为重要。
以技术发展为依托,蒸汽锅炉的PLC系统抓紧被应用到实践生产中,这就大大提高了自动化发展能效。
但是蒸汽锅炉的自动化水平与预期目标之间存在显著差距,相对的能源消耗量大、参数缺少精准调控等问题也频繁发生,这就需要针对PLC的自动控制技术进行全面分析及探究,找寻更为有效的发展路径,促使其能效作用充分发挥。
1基于PLC的新型蒸汽锅炉自动控制系统总体方案基于PLC的新型蒸汽锅炉自动控制系统设计目标为将原来由继电器等基础器件控制或者人工操作的锅炉控制系统通过对水位、蒸汽流量、压力、排烟温度等参数的联合调控实现自动控制。
整个自动控制系统分为三级操控模式。
蒸汽锅炉控制系统的主要功能是实现锅炉的水位控制、蒸汽流量控制、蒸汽压力控制、排烟温度控制和监测。
具体功能如下:(1)自动控制:自动控制锅炉的运行参数,使蒸汽锅炉满足工作要求,并且可以安全、经济地运行。
(2)程序控制:通过对锅炉设定一个具体的操作顺序以及各参数的定义来编制程序实现对锅炉的自动控制,完成锅炉的正常运行。
如首先进行启动设置,然后将煤斗中的煤炭运送至炉膛进行燃烧,并按照顺序控制启动引风机、鼓风机以及炉排。
基于PLC的生物质锅炉燃烧控制系统设计

c o n t r o l s y s t e m u s i n g S i e me n s S 7 — 3 0 0 p r o g r a m ma b l e 1 o g i c c o n t r o l l e r( P LC) wa s p r e s e n t e d . Th e p r a c t i c a 1
第4 4卷
第4 期
热
力 发 电 Байду номын сангаас
Vo I . 4 4 NO . 4
Ap r . 2 01 5
2 0 1 5年 4月
TH ERM A L POW ER GEN ERAT 1 0N
基于P L C 的 生 物 质 锅 炉 燃 烧 控 制 系 统 设 计
胡 南 江 , 陈 罡 , 连坤 宙 , 汤 伟。
质锅 炉控 制 系统应 用 中存 在 的鲁棒 性差 、 精 度低 等 问题 , 通过 分析 生物 质燃烧 过程 , 基于 P L C 设计 了生物质锅 炉燃烧控 制 系统 。应 用表 明 , 该 控 制 系统 的稳 定性 和 调 节速 度 均较 好 , 蒸汽
压 力最 大超调 量为 0 . 5 %, 响应 时 间为 6 5 S 。
a p pl i c a t i o n s h ows t hi s c o nt r o l s ys t e m ha s g oo d pe r f o r ma n c e i n s t a b i l i t y a nd r e s po ns e s pe e d, o f whi c h t he max i mum ov e r s ho o t o f t h e s t e a m p r e s s ur e i S 0 . 5 , a nd t he r e s p o ns e t i me i S 6 5 S .
基于PLC的锅炉控制系统
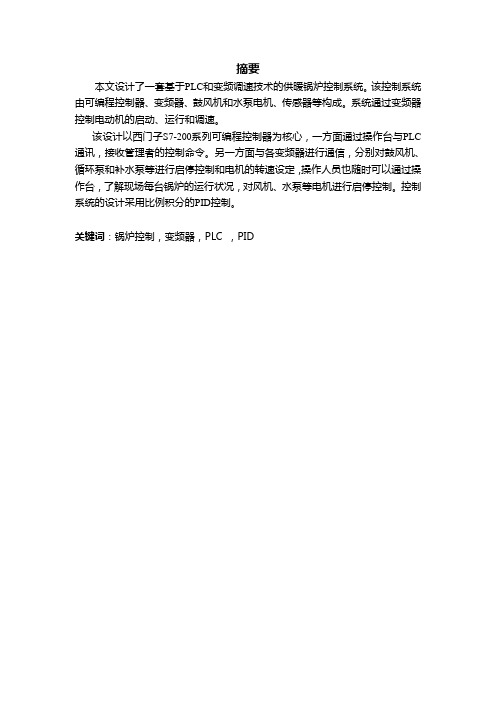
摘要本文设计了一套基于PLC和变频调速技术的供暖锅炉控制系统。
该控制系统由可编程控制器、变频器、鼓风机和水泵电机、传感器等构成。
系统通过变频器控制电动机的启动、运行和调速。
该设计以西门子S7-200系列可编程控制器为核心,一方面通过操作台与PLC 通讯,接收管理者的控制命令。
另一方面与各变频器进行通信,分别对鼓风机、循环泵和补水泵等进行启停控制和电机的转速设定,操作人员也随时可以通过操作台,了解现场每台锅炉的运行状况,对风机、水泵等电机进行启停控制。
控制系统的设计采用比例积分的PID控制。
关键词:锅炉控制,变频器,PLC ,PIDThe design of heating boiler auto control reformation system basedon PLC technologyAbstractIn this Paper,a heating boiler control system based on PLC and variable frequency Speed-regulating technology is designed. The control system is made up of PLC,transducers,electromotor units of Pumps and fans, sensors, etc. It can control electromotor starting,running and timing by means of transducers.The design is based on Siemens S7-200 series programmable controller as the core; on the one hand through the console it can communicate with the PLC, to receive control commands from managers. On the other hand it communicate with the variable frequency Speed-regulating, to fulfilled such as starting and stopping pump motor control and speed settings, the operator at console can find out at the scene of the operation of each boiler to fans, pumps and other motor control to start and stop. at any time.Key words:boiler control, variable frequency Speed-regulating, PLC technology目录1 绪论 (2)2 供暖锅炉改造设计思路 (2)2.1 供暖锅炉改造设计要求 (2)2.2 锅炉系统的结构 (3)2.3 整体方案选择 (3)3 变频调速在供暖锅炉控制中的应用 (4)3.1 变频调速基本原理 (4)3.2 变频调速在供暖锅炉系统中的应用 (5)4 锅炉控制系统总体设计 (5)4.1系统功能分析 (5)4.2 总体设计思路 (6)4.3 系统结构 (6)5 系统硬件设计 (7)5.1 可编程控制器PLC的选型 (7)5.2 PLC配置 (8)5.3 I/O接线 (9)5.4 变频器配置 (9)5.5 传感器与变送器 (11)5.5.1 压力变送器工作原理 (11)5.5.2 压力变送器选型 (11)5.5.3 温度传感器选型 (11)6 系统构成 (13)6.1 补水泵控制系统 (13)6.2 循环泵控制系统 (15)6.3 燃烧控制系统 (16)7 PID控制原理 (17)8 程序设计 (20)8.1 主程序设计 (16)8.2 子程序设计 (16)9 结束语 (26)致谢 (28)参考文献 (28)1 绪论锅炉是供热设备中最普遍的动力设备之一,它的功能是把燃料中的贮能,通过燃烧转化成热能,以蒸汽或热水的形式输向各种设备。
基于PLC的锅炉控制系统设计说明
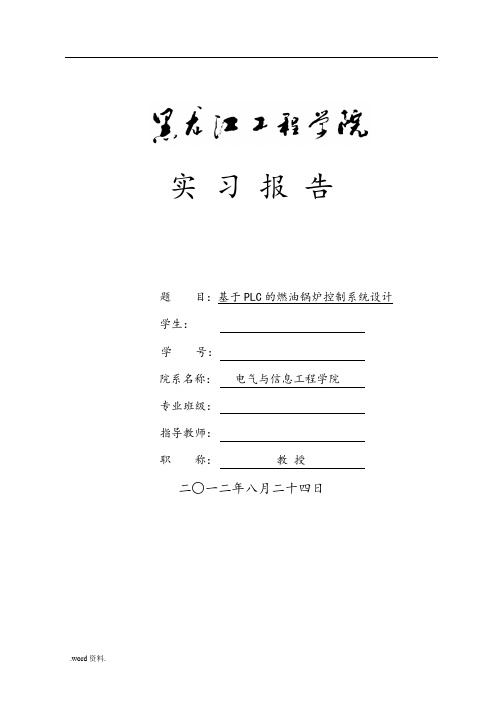
实习报告题目:基于PLC的燃油锅炉控制系统设计学生:学号:院系名称:电气与信息工程学院专业班级:指导教师:职称:教授二○一二年八月二十四日实习任务书组学生王鹏、历丽、冰冰、佳欣、会鸿人数5人系部名称电气与信息工程学院专业电气工程及其自动化班级、学号电气09-120091501指导教师徐鹿眉、王希凤职称教授从事专业电气工程及其自动化题目名称基于PLC的燃油锅炉控制系统设计一、工程实践的目的、意义通过对燃油锅炉PLC控制的程序设计,使我懂得了锅炉一直在发展,随着对控制精度和对环境的要求越来越高,传统的继电器控制不能满足要求,燃煤锅炉也渐渐不再适应现代发展的需要。
燃油锅炉替代燃煤锅炉是发展的结果。
本次工程实践,收获很多,既完成了设计任务,又学的了很多新知识。
当然,个人的设计或多或少总存在一些不足和缺陷,只有在不断学习使用和在别人的帮助指点下,才能不断改进缺陷和不足。
整个设计过程比较复杂,在设计中反映出个人知识的不足,需要学习更多的知识以弥补不足。
二、工程实践的主要容、技术要求(包括原始数据、技术参数、设计要求、工作量要求等)用PLC控制燃油锅炉的自动控制,保证其安全、可靠、稳定地按着预期的设计方案工作。
基于PLC的燃油锅炉控制系统技术要求如下:(1) 按下起动按钮,燃油首先通过燃油预热器预热,1min后,接通点火变压器,打开瓦斯阀门,同时由鼓风机送风,持续3S后,喷油泵喷油,持续3S后,点火变压器和瓦斯阀门同时关闭。
(2) 按下停止按钮,燃油预热器关闭,喷油泵关闭,鼓风机继续送风持续15S后送风停止。
(3) 锅炉燃烧过程中,当出现异常情况时(即蒸汽压力超过允许值或水位通过上限或低于下限L能自动关K;异常情况消失后,又能自动接起燃烧程序重新点火燃烧。
(4) 锅炉水位控制,锅炉工作起动后,当水位低于下限时,进水阀打开,排水阀关闭,当水位高于上限时,排水阀打开,进水阀关闭。
(5) 当水温低于90度时,喷油电机以较大转速运行;当水温高于90度时,Q0.7输出,喷油电机减速运行;当油温高于设定值25度时,喷油机才能喷油。
基于PLC的锅炉燃烧控制系统毕业设计正文

基于PLC的锅炉燃烧控制系统设计1 绪论1.1锅炉燃烧控制项目的背景改革开放以来,我国经济社会快速发展,生产力水平不断提高,在生产中,锅炉起着十分重要的作用,尤其是在火力发电中发挥重要作用的工业锅炉,是提供能源动力的主要设备之一。
锅炉产生的蒸汽可以作为蒸馏,干燥,反应,加热等各过程的热源,另外也可以作为动力源驱动动力设备。
工业过程中对于锅炉燃烧控制系统的要非常高的,要求锅炉燃烧控制系统必须满足控制精度高,响应速度快[1]。
作为一个非常复杂的设备,锅炉同时具有了数十个包括了扰动、测量、控制在的参数,参数之间有着复杂的关系,并且相互关联[2]。
而锅炉燃烧过程中的效率问题、安全问题一直是大众关注的重要方面。
1.2锅炉燃烧控制的发展历史对于锅炉燃烧的控制,已经经历了四个阶段[3~5](1)手动控制阶段因为20世纪60年代以前,电力电子技术和自动化技术还没有得到完全发展,技术尚不成熟,因此,这个时期工业人员的自动化意识不强,锅炉燃烧的控制方式一般多采用纯手动的方法。
这种控制方法,要求进行控制的操作工人依靠他们的经验决定送风量,引风量,给煤量的多少,然后利用手动的操作工具等操控锅炉,该方法控制的程度完全取决于操作工人的经验。
因此,要求操作工人必须具有非常丰富的经验,这样无疑大大提高了操作工人的劳动强度,由十人的主观意识,所以事故率非常大,同时,也不能保证锅炉高效稳定的运行。
(2)仪器继电器控制阶段随着科技的不断进步,自动化技术以及电力电子技术快速提高,国外以继电器为基础的自动化仪表工业锅炉控制系统也得到发展,并且广泛应用于实际生产过程。
在上个世纪60年代前期,我国锅炉的控制系统开始得到迅速发展;到了60年代的中后期,我国引进了国外全自动的燃油锅炉的控制系统;到了上个世纪的70年代末,我国逐渐自主研发了一些工业锅炉的自动化仪器,同时,在工业锅炉的控制系统方面也在逐步推广应用自动化技术。
在仪表继电器控制阶段,锅炉的热效率得到了提高,并且大幅度的降低了锅炉的事故率。
基于plc的锅炉供热控制系统的设计
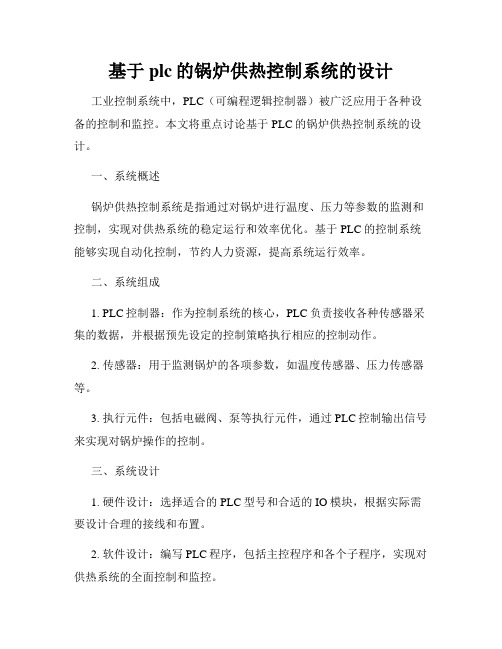
基于plc的锅炉供热控制系统的设计工业控制系统中,PLC(可编程逻辑控制器)被广泛应用于各种设备的控制和监控。
本文将重点讨论基于PLC的锅炉供热控制系统的设计。
一、系统概述锅炉供热控制系统是指通过对锅炉进行温度、压力等参数的监测和控制,实现对供热系统的稳定运行和效率优化。
基于PLC的控制系统能够实现自动化控制,节约人力资源,提高系统运行效率。
二、系统组成1. PLC控制器:作为控制系统的核心,PLC负责接收各种传感器采集的数据,并根据预先设定的控制策略执行相应的控制动作。
2. 传感器:用于监测锅炉的各项参数,如温度传感器、压力传感器等。
3. 执行元件:包括电磁阀、泵等执行元件,通过PLC控制输出信号来实现对锅炉操作的控制。
三、系统设计1. 硬件设计:选择适合的PLC型号和合适的IO模块,根据实际需要设计合理的接线和布置。
2. 软件设计:编写PLC程序,包括主控程序和各个子程序,实现对供热系统的全面控制和监控。
四、系统功能1. 温度控制:根据设定的温度范围,实现对锅炉加热的自动控制,确保供热系统温度稳定。
2. 压力保护:设定压力上下限,一旦超过范围即刻停止加热,确保系统安全运行。
3. 水位控制:通过水位传感器监测水位,保持恰当的水位以确保供热效果。
4. 故障诊断:PLC系统能够实时监测各个元件的运行状态,一旦有异常即可及时报警并进行故障诊断。
五、系统优势1. 自动化程度高:基于PLC的供热控制系统可以实现全自动化控制,减少人为干预,节约人力成本。
2. 稳定可靠:系统通过对各项参数的实时监测和控制,确保供热系统的稳定性和可靠性。
3. 灵活性强:PLC程序可以根据实际需要进行定制化设计,满足不同应用场景的需求。
六、总结基于PLC的锅炉供热控制系统的设计,能够实现对供热系统的智能化控制和监测,提高系统的稳定性和效率,减少运行成本,是目前工业控制领域的主流趋势。
希望本文的介绍能够对您有所帮助。
感谢阅读!。
基于PLC的锅炉控制系统的设计
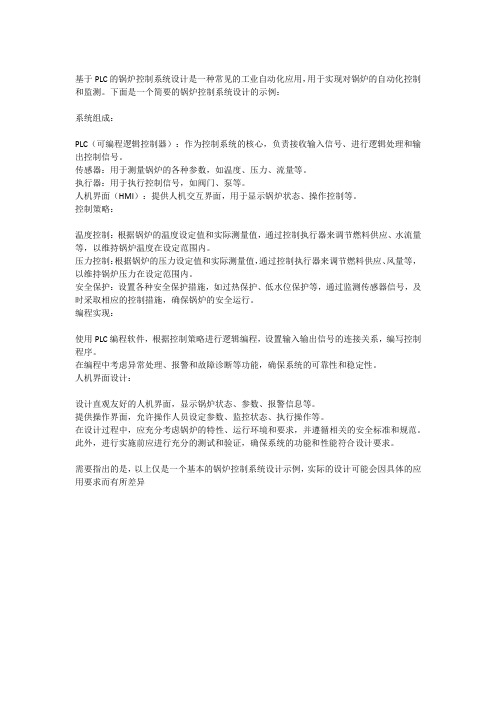
基于PLC的锅炉控制系统设计是一种常见的工业自动化应用,用于实现对锅炉的自动化控制和监测。
下面是一个简要的锅炉控制系统设计的示例:
系统组成:
PLC(可编程逻辑控制器):作为控制系统的核心,负责接收输入信号、进行逻辑处理和输出控制信号。
传感器:用于测量锅炉的各种参数,如温度、压力、流量等。
执行器:用于执行控制信号,如阀门、泵等。
人机界面(HMI):提供人机交互界面,用于显示锅炉状态、操作控制等。
控制策略:
温度控制:根据锅炉的温度设定值和实际测量值,通过控制执行器来调节燃料供应、水流量等,以维持锅炉温度在设定范围内。
压力控制:根据锅炉的压力设定值和实际测量值,通过控制执行器来调节燃料供应、风量等,以维持锅炉压力在设定范围内。
安全保护:设置各种安全保护措施,如过热保护、低水位保护等,通过监测传感器信号,及时采取相应的控制措施,确保锅炉的安全运行。
编程实现:
使用PLC编程软件,根据控制策略进行逻辑编程,设置输入输出信号的连接关系,编写控制程序。
在编程中考虑异常处理、报警和故障诊断等功能,确保系统的可靠性和稳定性。
人机界面设计:
设计直观友好的人机界面,显示锅炉状态、参数、报警信息等。
提供操作界面,允许操作人员设定参数、监控状态、执行操作等。
在设计过程中,应充分考虑锅炉的特性、运行环境和要求,并遵循相关的安全标准和规范。
此外,进行实施前应进行充分的测试和验证,确保系统的功能和性能符合设计要求。
需要指出的是,以上仅是一个基本的锅炉控制系统设计示例,实际的设计可能会因具体的应用要求而有所差异。
基于PLC的船用辅锅炉燃烧控制系统设计

专科毕业设计(论文)设计题目:基于PLC的船用辅锅炉燃烧控制系统摘要可编程序控制器(PLC)作为现代工业控制的四大支柱之一,而且具有体积小,编程简单,组装灵活,可靠性高及抗干扰能力强等优点,非常适合于在恶劣的工作环境下使用,被认为是工业上的无故障产品,将替代传统继电接触器控制系统设备成为自动化控制系统的主要控制设备。
本文将主要介绍PLC在船用辅锅炉燃烧控制系统中的应用。
关键词可编程序控制器船用辅锅炉燃烧控制Abstract目录1 引言 (1)2 可编程序控制器概述 (1)2.1 PLC的产生、定义、分类 (1)2.1.1 PLC的产生 (1)2.1.2 PLC的定义 (1)2.1.3 PLC的分类 (2)2.2 PLC的基本结构 (2)2.2.1 PLC的硬件组成 (2)2.2.2 PLC的软件组成 (3)2.3 PLC的特点及主要功能 (3)2.4 PLC的应用领域及发展趋势 (3)3 锅炉概述 (4)3.1 锅炉的定义 (4)3.2 锅炉的重要性 (4)3.3 锅炉的分类 (4)3.4 锅炉的基本构造及工作过程 (4)3.4.1 锅炉的基本构造 (4)3.4.2 锅炉的工作过程 (5)4 船用辅锅炉的燃烧控制系统 (5)4.1 PLC系统在锅炉燃烧控制系统中的控制要求 (5)4.2 PLC选型及输入/输出端口的设计 (6)4.2.1 PLC的选型 (6)4.2.2 输入/输出点的设计 (6)4.3 PLC控制燃烧系统梯形图 (7)4.4 PLC 控制锅炉燃烧系统过程分析 (7)结论 (11)致谢 (12)参考文献 (13)1 引言可编程控制器(PLC)作为传统继电接触控制系统的替代产品,已广泛应用于工业控制的各个领域,由于它可通过软件来改变过程,而且具有体积小,编程简单,组装灵活,可靠性高及抗干扰能力强等优点,非常适合于在恶劣的工作环境下使用,被公认为是工业上的无故障产品。
因此,为了提高船用辅锅炉控制安全及减少船员的工作量和提高工作效率,从而提高经济效益,所以在船用辅锅炉燃烧自动控制系统中,PLC控制替代传统辅锅炉燃烧自动控制系统是一种必然。
基于PLC的锅炉燃烧控制系统的设计-毕业论文

摘要随着社会经济的飞速发展,城市建设规模的不断扩大,以及人们生活水平的不断提高,对城市生活供暖的用户数量和供暖质量提出了原来越高的要求。
结合现状,本论文供暖锅炉监控系统,设计了一套基于PLC和变频调速技术的供暖锅炉控制系统。
该控制系统以一台工业控制机作为上位机,以西门子S7-300可编程控制机为下位机,系统通过变频器控制电机的启动,运行和调速。
上位机监控采用WinCC设计,主要完成系统操作界面设计,实现系统启停控制,参数设定,报警联动,历史数据查询等功能。
下位机控制程序采用西门子公司的STEP7编程软件设计,主要完成模拟量信号的处理,温度和压力信号的PID控制等功能,并接受上位机的控制指令以完成风机启停控制,参数设定,循环泵的控制和其余电动机的控制。
本文设计的变频控制系统实现了锅炉燃烧过程的自动控制,系统运行稳定可靠。
采用锅炉的计算机控制和变频控制不仅可大大节约能源,促进环保,而且可以提高生产自动化水平,具有显著的经济效益和社会效益。
关键字:锅炉控制;变频调速;组态软件;PLCAbstractAlong with social economy’s swift development, the urban construction scale’s unceasing expansion , as well as the peple living standard’s unceasing enhancement , set more and more high request to the city life heating’s user quantity and the heating quality. The union present situation, the present paper heating boiler supervisory sysem, has designed a set based on PLC and the frequency conversion velocity modulation technology heating boiler control system.This control system takes the superior machine by one Industry cybertrons , west of family household S7-300 programmable controller for lower position machine ,system through frequency changer control motor’s start , movement and vclocity modulation .the superior machine monitoring software uses the three dimensional strength to control the WinCC design , mainly completes the system operation contract surface design ,realizes the system to open/stops functions and so on control ,parameter hypothesis ,warning linkage,historical data inquiry. The lower position machine control procedure uses Siemen’s STEP7 programming software design , mainly completes the simulation quantity signal processing , temperature and pressure signal functions and so on PID control , and receives the superior machine control command to complete the air blower to open/stops the control , the parameter hypothesis, the circulating pump control and other electric motor’s control.This article designs the frequency conversion processs automatic control, the systems operation is stable, is reliable. Uses boiler’s computer control and the frequency converseon control noe only may save the energy greatly, the promotion environmental protection moreover may raise the production automation level, has the remarkable economic efficiency and the social efficiency.Key Words:Boiler control;Frequency conversion velocity modulation ;Configuration Software;PLC目录摘要 0Abstract (1)第1章概述 (4)1.1 项目背景及课题的研究意义 (4)1.2 供暖锅炉控制的国内外研究现状 (5)1.3锅炉控制系统的发展趋势 (6)1.4本文所做工作 (7)第2章系统方案设计 (9)2.1锅炉控制研究简介 (9)2.2 总体设计思路 (9)2.3方案比较 (10)2.3.1方案1 (10)2.3.2 方案2 (10)2.4方案论证与方案确定 (11)第3章硬件设计 (12)3.1 用户系统框图 (12)3.2 锅炉系统的理论分析 (13)3.2.1变频调速基本原理 (13)3.2.2变频调速在供暖锅炉中的应用 (13)3.2.3变频调速节能分析 (14)3.3燃烧过程控制 (19)3.4锅炉控制系统设计 (20)3.5控制系统构成介绍 (21)第4章软件设计 (25)4.1 S7-300系列PLC简介 (26)4.2 PLC编程语言简介 (28)4.2.1 PLC编程语言的国际标准 (28)4.2.2复合数据类型与参数类型 (29)4.2.3系统存储器 (29)4.2.4 S7-300 CPU中的寄存器 (30)4.3 STEP7 的原理 (31)4.3.1 STEP7概述 (31)4.3.2 硬件组态与参数设置 (32)4.3.3 符号表 (36)4.3.4 逻辑块 (37)4.3程序设计 (38)4.4通信系统 (41)4.5人机界面 (43)4.5.1监控软件WinCC介绍 (43)4.5.2监控系统设计 (45)4.5.3锅炉监控界面设计 (49)第5章结论 (53)5.1 成果的创造性和先进性 (53)5.2作用意义(经济效益和社会意义) (53)5.3 推广应用范围和前景 (53)5.4 需要进一步改进之处 (54)参考文献 (55)外文资料翻译 (56)外文翻译原文 (56)外文翻译译文 (68)致谢 (75)附录 (76)附录1 程序清单 (76)附录2 I/O点数分配表 (96)附录3 物理参数比较表 (97)第1章概述1.1 项目背景及课题的研究意义工业锅炉是工业生产和集中供热过程中重要的动力设备。
基于PLC的锅炉燃烧控制系统

专业英语项目作业指导教师班级姓名学号齐齐哈尔工程学院电气工程及其自动化专业2016年12月29日基于PLC的锅炉燃烧控制系统1 引言燃烧控制系统是电厂锅炉的主控系统,主要包括燃料控制系统、风量控制系统、炉膛压力控制系统。
目前大部分电厂的锅炉燃烧控制系统仍然采用PID控制。
燃烧控制系统由主蒸汽压力控制和燃烧率控制组成串级控制系统,其中燃烧率控制由燃料量控制、送风量控制、引风量控制构成,各个子控制系统分别通过不同的测量、控制手段来保证经济燃烧和安全燃烧。
2 控制方案锅炉燃烧自动控制系统的基本任务是使燃料燃烧所提供的热量适应外界对锅炉输出的蒸汽负荷的要求,同时还要保证锅炉安全经济运行。
一台锅炉的燃料量、送风量和引风量三者的控制任务是不可分开的,可以用三个控制器控制这三个控制变量,但彼此之间应互相协调,才能可靠工作。
对给定出水温度的情况,则需要调节鼓风量与给煤量的比例,使锅炉运行在最佳燃烧状态。
同时应使炉膛内存在一定的负压,以维持锅炉热效率、避免炉膛过热向外喷火,保证了人员的安全和环境卫生。
2.1 控制系统总体框架设计燃烧过程自动控制系统的方案,与锅炉设备的类型、运行方式及控制要求有关,对不同的情况与要求,控制系统的设计方案不一样。
将单元机组燃烧过程被控对象看作是一个多变量系统,设计控制系统时,充分考虑工程实际问题,既保证符合运行人员的操作习惯,又要最大限度的实施燃烧优化控制。
控制系统的总体框架如图1所示。
图1单元机组燃烧过程控制原理图11徐亚飞,温箱温度PID与预测控测控制.2004,28(4):554-5572P为机组负荷热量信号。
控制系统包括:滑压运行主汽压力设定值计算模块(由热力系统实验获得数据,再拟合成可用DCS折线功能块实现的曲线)、负荷—送风量模糊计算模块、主蒸汽压力控制系统和送、引风控制系统等。
主蒸汽压力控制系统采用常规串级PID控制结构。
2.2 燃料量控制系统当外界对锅炉蒸汽负荷的要求变化时,必须相应的改变锅炉燃烧的燃料量。
PLC控制在锅炉燃烧系统中的应用
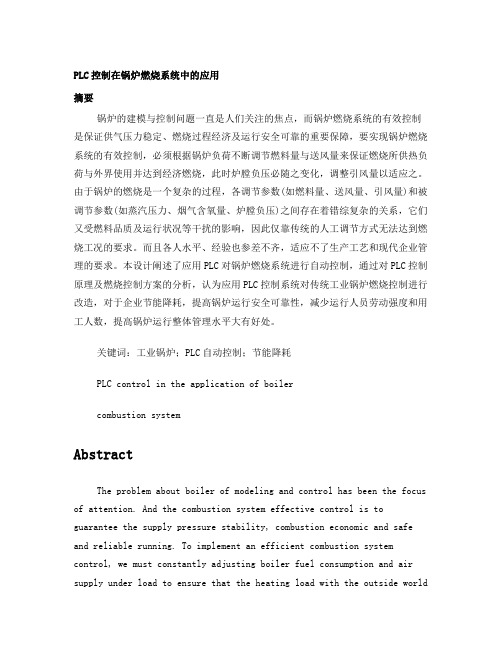
PLC控制在锅炉燃烧系统中的应用摘要锅炉的建模与控制问题一直是人们关注的焦点,而锅炉燃烧系统的有效控制是保证供气压力稳定、燃烧过程经济及运行安全可靠的重要保障,要实现锅炉燃烧系统的有效控制,必须根据锅炉负荷不断调节燃料量与送风量来保证燃烧所供热负荷与外界使用并达到经济燃烧,此时炉膛负压必随之变化,调整引风量以适应之。
由于锅炉的燃烧是一个复杂的过程,各调节参数(如燃料量、送风量、引风量)和被调节参数(如蒸汽压力、烟气含氧量、炉膛负压)之间存在着错综复杂的关系,它们又受燃料品质及运行状况等干扰的影响,因此仅靠传统的人工调节方式无法达到燃烧工况的要求。
而且各人水平、经验也参差不齐,适应不了生产工艺和现代企业管理的要求。
本设计阐述了应用PLC对锅炉燃烧系统进行自动控制,通过对PLC控制原理及燃烧控制方案的分析,认为应用PLC控制系统对传统工业锅炉燃烧控制进行改造,对于企业节能降耗,提高锅炉运行安全可靠性,减少运行人员劳动强度和用工人数,提高锅炉运行整体管理水平大有好处。
关键词:工业锅炉;PLC自动控制;节能降耗PLC control in the application of boilercombustion systemAbstractThe problem about boiler of modeling and control has been the focus of attention. And the combustion system effective control is to guarantee the supply pressure stability, combustion economic and safe and reliable running. To implement an efficient combustion system control, we must constantly adjusting boiler fuel consumption and air supply under load to ensure that the heating load with the outside worldto use and economical combustion. Furnace pressure will change with time, adjusting the air volume to meet the guidelines. As the combustion of boiler is a complex process. And there are a complex relationship between the adjustment parameters (such as fuel consumption, air supply, air flow lead) and the adjustable parameters (such as steam pressure, oxygen content in the flue gas, furnace pressure). They are alsoaffected by fuel quality and the health effects of such interference, so only on the traditional manual adjustment mode does not meet the requirements of the combustion co nditions. And people’s level, experience recognizing, adapt the production process and the requirements of modern business management. The article gives the PLC on system for automatic control. Through the PLC control principles and combustion control methods, we argue that the transform of PLC control system on the traditional industrial combustion is good at heatingenergy enterprises, improving the boiler operation safety andreliability, reducing our labor and employment for the operating personnel, increasing the number of overall management of the boiler operation.Key words: industrial boiler, PLC automatic control, energy conservation目录摘要 IAbstract II目录 III1 绪论 11.1 课题研究背景及意义 11.2 锅炉燃烧控制系统的国内外发展现 1 1.2.1 锅炉燃烧控制系统发展简介 11.2.2 锅炉燃烧控制策略研究现状 21.3 PLC控制在国内外的发展近况 21.4 本课题研究内容 32 锅炉燃烧系统设计 42.1 锅炉的工作过程简介 42.2 锅炉燃烧系统简介 52.2.1 锅炉燃烧系统工艺 52.2.2 锅炉燃烧控制系统要求 62.3 锅炉燃烧控制系统设计 62.3.1 锅炉燃烧控制系统结构 62.3.2 锅炉燃烧控制总体框架 72.3.3 燃料子系统设计 72.3.4 送风子系统设计 82.3.5 引风子系统设计 83 锅炉燃烧控制系统硬件部分设计 10 3.1 可编程控制器(PLC)简介 103.1.1 可编程控制器(PLC)工作原理 10 3.1.2 可编程控制器的主要特点 113.2 可编程控制器(PLC)选型 113.2.1 可编程控制器CPU选择 113.2.2 模拟量输入/输出扩展模块 123.3 PLC及其扩展模块接线 123.3.1 PLC I/O地址分配表 123.3.2 PLC及其模块接线 123.4 变频器 133.4.1 变频器基本结构 143.4.2 变频器驱动风机原理 153.4.3 变频器选择 164 锅炉燃烧控制系统软件部分设计 17 4.1 Step7软件简介 174.2 PLC系统的软件设计 184.2.1 控制算法流程 184.2.2 梯形图 19结论 24致谢 25参考文献 26附录梯形图 271 绪论1.1 课题研究背景及意义锅炉是工业生产中普遍使用的动力设备,是能源转换的重要工具。
燃煤锅炉PLC控制系统设计

燃煤锅炉PLC控制系统设计摘要:本文设计了一种基于PLC的燃煤锅炉控制系统。
该系统采用了微型PLC来进行燃煤锅炉控制,能够实现数字化、自动化、智能化的控制方式,提高了燃煤锅炉的运行效率和安全性。
该系统还具有故障自动检测和报警处理功能,可以及时发现并排除系统中的故障,确保了系统的可靠性。
关键词:PLC,燃煤锅炉,控制系统,数字化,自动化,智能化正文:燃煤锅炉是工业生产中常见的一种设备,对于实现工业生产的高效、低成本运行具有重要作用。
传统的燃煤锅炉控制方式主要是采用模拟控制方式,但由于模拟控制存在误差大、灵敏度不高、抗干扰能力差等问题,近年来越来越多的燃煤锅炉采用数字化控制方式进行控制。
数字化控制方式采用先进的PLC控制器来控制燃煤锅炉,能够实现数字化、自动化、智能化的控制方式。
本文设计的基于PLC的燃煤锅炉控制系统主要由微型PLC、人机界面、执行器、传感器等组成。
系统的控制算法采用PID 控制方法,能够实现对燃煤锅炉的加热温度、空燃比等参数进行精确控制,提高了燃煤锅炉的运行效率和安全性。
同时,该系统还具有故障自动检测和报警处理功能,当系统出现异常情况时能够及时发现并排除故障,确保了系统的可靠性。
系统的人机界面采用触摸屏和键盘进行交互,能够实时显示燃煤锅炉的运行状态,并支持远程监控和控制功能。
为了验证该系统的性能,本文进行了模拟实验和现场应用测试。
模拟实验结果表明,系统的控制精度高、稳定性好;现场应用测试结果表明,系统可靠性高、使用方便,运行效率明显提高。
总之,本文设计的基于PLC的燃煤锅炉控制系统具有数字化、自动化、智能化的控制方式,能够确保燃煤锅炉的高效、安全运行。
同时,该系统具有故障自动检测和报警处理功能,能够及时发现并排除故障。
本文的设计思路和实验结果可以为相关领域的工程技术人员和研究人员提供借鉴和参考。
本文设计的燃煤锅炉PLC控制系统具有以下几个特点:1.数字化控制:传统的燃煤锅炉控制方式主要是采用模拟控制方式,但由于模拟控制存在误差大、灵敏度不高、抗干扰能力差等问题,近年来越来越多的燃煤锅炉采用数字化控制方式进行控制。
- 1、下载文档前请自行甄别文档内容的完整性,平台不提供额外的编辑、内容补充、找答案等附加服务。
- 2、"仅部分预览"的文档,不可在线预览部分如存在完整性等问题,可反馈申请退款(可完整预览的文档不适用该条件!)。
- 3、如文档侵犯您的权益,请联系客服反馈,我们会尽快为您处理(人工客服工作时间:9:00-18:30)。
专业英语项目作业指导教师班级姓名学号齐齐哈尔工程学院电气工程及其自动化专业2016年12月29日基于PLC的锅炉燃烧控制系统1 引言燃烧控制系统是电厂锅炉的主控系统,主要包括燃料控制系统、风量控制系统、炉膛压力控制系统。
目前大部分电厂的锅炉燃烧控制系统仍然采用PID控制。
燃烧控制系统由主蒸汽压力控制和燃烧率控制组成串级控制系统,其中燃烧率控制由燃料量控制、送风量控制、引风量控制构成,各个子控制系统分别通过不同的测量、控制手段来保证经济燃烧和安全燃烧。
2 控制方案锅炉燃烧自动控制系统的基本任务是使燃料燃烧所提供的热量适应外界对锅炉输出的蒸汽负荷的要求,同时还要保证锅炉安全经济运行。
一台锅炉的燃料量、送风量和引风量三者的控制任务是不可分开的,可以用三个控制器控制这三个控制变量,但彼此之间应互相协调,才能可靠工作。
对给定出水温度的情况,则需要调节鼓风量与给煤量的比例,使锅炉运行在最佳燃烧状态。
同时应使炉膛内存在一定的负压,以维持锅炉热效率、避免炉膛过热向外喷火,保证了人员的安全和环境卫生。
2.1 控制系统总体框架设计燃烧过程自动控制系统的方案,与锅炉设备的类型、运行方式及控制要求有关,对不同的情况与要求,控制系统的设计方案不一样。
将单元机组燃烧过程被控对象看作是一个多变量系统,设计控制系统时,充分考虑工程实际问题,既保证符合运行人员的操作习惯,又要最大限度的实施燃烧优化控制。
控制系统的总体框架如图1所示。
图1单元机组燃烧过程控制原理图11徐亚飞,温箱温度PID与预测控测控制.2004,28(4):554-5572P为机组负荷热量信号。
控制系统包括:滑压运行主汽压力设定值计算模块(由热力系统实验获得数据,再拟合成可用DCS折线功能块实现的曲线)、负荷—送风量模糊计算模块、主蒸汽压力控制系统和送、引风控制系统等。
主蒸汽压力控制系统采用常规串级PID控制结构。
2.2 燃料量控制系统当外界对锅炉蒸汽负荷的要求变化时,必须相应的改变锅炉燃烧的燃料量。
燃料量控制是锅炉控制中最基本也是最主要的一个系统。
因为给煤量的多少既影响主汽压力,也影响送、引风量的控制,还影响到汽包中蒸汽蒸发量及汽温等参数,所以燃料量控制对锅炉运行有重大影响。
燃料控制可用图2简单表示。
图2 燃料量控制策略其中:NB为锅炉负荷要求;B为燃料量;F(x)为执行机构。
设置燃料量控制子系统的目的之一就是利用它来消除燃料侧内部的自发扰动,改善系统的调节品质。
另外,由于大型机组容量大,各部分之间联系密切,相互影响不可忽略。
特别是燃料品种的变化、投入的燃料供给装置的台数不同等因素都会给控制系统带来影响。
燃料量控制子系统的设置也为解决这些问题提供了手段。
2.3 送风量控制系统为了实现经济燃烧,当燃料量改变时,必须相应的改变送风量,使送风量与燃料量相适应。
燃料量与送风量的关系见图3。
2刘官敏,温箱温度PID与预测控测控制.2004,28(4):554-5572图3 燃料量与送风量关系燃烧过程的经济与否可以通过剩余空气系数是否合适来衡量,过剩空气系数通常用烟气的含氧量来间接表示。
实现经济燃烧最基本的方法是使风量与燃料量成一定的比例。
送风量控制子系统的任务就是使锅炉的送风量与燃料量相协调,可以达到锅炉的最高热效率,保证机组的经济性,但由于锅炉的热效率不能直接测量,故通常通过一些间接的方法来达到目的。
如图4所示,以实测的燃料量B作为送风量调节器的给定值,使送风量V和燃料量B成一定的比例。
图4 燃料量空气调节系统在稳态时,系统可保证燃料量和送风量间满足选择vα使送风量略大于B完全燃烧所需要的理论空气量。
这个系统的优点是实现简单,可以消除来自负荷侧和燃料侧的各种扰动。
2.4 引风量控制系统为了保持炉膛压力在要求的范围内,引风量必须与送风量相适应。
炉膛压力的高低也关系着锅炉的安全和经济运行。
炉膛压力过低会使大量的冷风漏入炉膛,将会增大引风机的负荷和排烟损失,炉膛压力太低甚至会引起内爆;反之炉膛压力高且高出大气压力的时候,会使火焰和烟气冒出,不仅影响环境卫生,甚至可能影响设备和人生安全。
引风量控制子系统的任务是保证一定的炉膛负压力,且炉膛负压必须控制在允许范围内,一般在-20Pa左右。
33高国章,温箱温度PID与预测控测控制.2004,28(4):554-5572vB Vα=控制炉膛负压的手段是调节引风机的引风量,其主要的外部扰动是送风量。
作为调节对象,炉膛烟道的惯性很小,无论在内扰和外扰下,都近似一个比例环节。
一般采用单回路调节系统并加以前馈的方法进行控制,如图5所示。
图5 引风量控制子系统图中Ts为炉膛负压给定值,S为实测的炉膛负压,Q为引风量,V为送风量。
由于炉膛负压实际上决定于送风量和引风量的平衡,故利用送风量作为前馈信号,以改善系统的调节性能。
另外,由于调节对象相当于一个比例环节,被调量反应过于灵敏,为了防止小幅度偏差引起引风机挡板的频繁动作,可设置调节器的比例带自动修正环节,使得在小偏差时增大调节器的比例带。
对于负压S的测量信号,也需进行低通滤波,以抑制测量值的剧烈波动。
3系统硬件配置在锅炉燃烧过程中,用常规仪表进行控制,存在滞后、间歇调节、烟气中氧含量超过给定值、低负荷和烟气温度过低等问题。
采用PLC对锅炉进行控制时,由于它的运算速度快、精度高、准确可靠,可适应复杂的、难于处理的控制系统。
因而,可以解决以上由常规仪表控制难以解决的问题。
所选择的PLC系统要求具有较强的兼容性,可用最小的投资使系统建成及运转;其次,当设计的自动化系统要有所改变时,不需要重新编程,对输入、输出系统不需要再重新接线,不须重新培训人员,就可使PLC系统升级;最后,系统性能较高。
硬件结构图如图6所示。
图6 硬件结构图44曾贵娥,邱丽,石油化工自动化,2005,7(4):89-91根据系统的要求,选取西门子PLCS7-200 CPU226 作为控制核心,同时还扩展了2个EM231模拟量输入模块和1个CP243-1以太网模块。
CPU226的I/O点数是2416,这样完全可以满足系统的要求。
同时,选用了EM231模块,它是AD转换模块,具有4个模拟量输入,12位A/D,其s ,温度传感器、压力传感器、流量传感器以及含氧检测传感器的输出信号经过调采样速度25理和放大处理后,成为0~5V的标准信号,EM231模块自动完成A/D转换。
S7-200的PPI接口的物理特性为RS-485,可在PPI、MPI和自由通讯口方式下工作。
为实现PLC与上位机的通讯提供了多种选择。
为实现人机对话功能,如系统状态以及变量图形显示、参数修改等,还扩展了一块Eview500系列的触摸显示屏,操作控制简单、方便,可用于设置系统参数,显示锅炉温度等。
还有一个以太网模块CP243-1,其作用是可以让S7-200直接连入以太网,通过以太网进行远距离交换数据,与其他的S7-200进行数据传输,通信基于TCP,安装方便、简单。
4 系统软件设计控制程序采用STEP7-Micro Win软件以梯形图方式编写,其软件框图如图7所示。
图7 软件主框图S7-200PLC给出了一条PID指令,这样省去了复杂的PID算法编程过程,大大方便了用户的使用。
使用PID指令有以下要点和经验:(1)比例系数和积分时间常数的确定。
应根据经验值和反复调试确定。
(2)调节量、给定量、输出量等参数的标准归一化转换。
(3)按正确顺序填写PID回路参数表(LOOP TABLE),分配好各参数地址。
5朱学峰.PID控制器参数整定方法的仿真与实验研究5 结束语单元机组燃烧过程控制系统在某火电厂发电机组锅炉协调控制系统中投入使用。
实际运行情况表明:由于引入负荷模糊前馈,使得锅炉燃烧控制系统作为协调控制的子系统,跟随机组负荷变化的能力显著提高,风煤比能够在静态和动态过程中保持一致;送、引风控制系统在逻辑控制系统的配合下运行的平稳性和安全性提高,炉膛负压波动减小,满足了运行的要求;在机组负荷不变时,锅炉燃烧稳定,各被调参数动态偏差显著减少,实现了锅炉的优化燃烧;采用非线性PID 调节方式,解决了引风挡板的晃动问题。
采用西门子的PLC控制,不仅简化了系统,提高了设备的可靠性和稳定性,同时也大幅地提高了燃烧能的热效率。
通过操作面板修改系统参数可以满足不同的工况要求,机组的各种信息,如工作状态、故障情况等可以声光报警及文字形式表示出来,主要控制参数(温度值)的实时变化情况以趋势图的形式记录显示,方便了设备的操作和维护,该系统通用性好、扩展性强,直观易操作。
6朱学峰.PID控制器参数整定方法的仿真与实验研究THE PLC-BASED BOILER COMBUSTION CONTROL SYSTEM1 IntroductionCombustion control system is the master of the power plant boiler system, which including a fuel control system, air flow control system, and furnace pressure control system. Most of the power plant boiler combustion control system is still using PID control. Combustion control system by the main steam pressure control and the burn rate control to form a cascade control system, in which the combustion rate control is controlled by the amount of fuel, air volume control, cited air volume control constitute. Each sub-control system is respectively, and through the different measurement can control methods to ensure economic burning combustion and safety.2 The control programBoiler burning the basic task of the automatic control system is to make fuel combustion, so that can provide heat to adapt to the requirements of the boiler output steam load. But it must to ensure the safe and economic operation of the boiler. A boiler fuel, air supply and bleed air volume control of the three tasks are not separate. These three control variables can be controlled with three controllers, but each other should be co-coordinated in order to work reliably. To set the water temperature, you need to adjust the blast volume and the proportion in the amount of coal to the boiler running at optimum combustion state. When the furnace memory at a certain negative pressure, it can maintain the boiler thermal efficiency and avoid the outward flame of the furnace overheated in order to ensure the safety of personnel and environmental hygiene.2.1 The control system in the overall framework of designCombustion process automatic control system the program and the type of boiler equipment, operation and control requirements, it related to the different circumstances and requirements. Unit power plant combustion process controlled object seen as a multivariable systems, design control system and fully consider the practical engineering problems. Both of them can ensure that operating personnel not only accustomed to the operation, but also to maximize the implementation of the combustion optimization. The overall framework of the control system is shown in Figure 1.Figure 1 unit power plant combustion process control schematic P is the unit load heat signal. The control system includes: sliding pressure operation of the main team pressure setting value calculation module (obtained by the thermal system experimental data, fitted curve of the available DCS poly line function block), the load-air supply fuzzy calculation module, and the main steam pressure control system and sent as quoted in the air control system. The main steam pressure control system uses conventional cascade PID control structure.2.2 The amount of fuel control systemWhen outside the requirements of the boiler steam load changes, it must be appropriate to change the amount of fuel burned by the boiler. The fuel control is a system boiler control the basic and important part. It also affects not only the main steam pressure to the amount of coal sent to lead the air flow control, also affects the steam evaporation and steam temperature and other parameters in the drum So the amount of fuel control have a major impact on boiler operation. Fuel control can be used in Figure 2.Figure 2 the amount of fuel control strategyOf which: NB the requirements for the boiler load; B is the amount of fuel; F (x) as the executing agency.One of the purposes set the amount of fuel control subsystem is to use it to eliminate the fuel side of the internal spontaneous disturbance and improve the quality of regulation. In addition, due to the large capacity of the units, between the various parts closely linked and influence each other can not be ignored. In particular, changes in fuel type, and put into the fuel supply device and the number of different factors to the control system. The fuel control subsystem setting also provides the means to address these issues.2.3 Air volume control systemIn order to achieve economic combustion, when the amount of fuel changes, it must be appropriate to change the air flow, so that change the air supply and the amount of fuel. The relationship between the amount of fuel and air supply are shown in Figure 3.Figure 3 the amount of fuel and air supply relationshipCombustion process in the economy whether or not is measured by the surplus air coefficient, excess air coefficient is usually indirect effects the oxygen content of the flue gas. The most basic economic combustion air volume and the amount of fuel must be in a certain proportion.Air supply control subsystem task is to make the boiler air supply and fuel the amount of phase coordination, the boiler the highest thermal efficiency can be achieved, to ensure the unit economics, but the boiler thermal efficiency can not direct measurements, and therefore usually through some indirect methods to achieve purpose. Shown in Figure 4, measured the amount of fuel B as the air flow regulator for a given value, the air volume V and the amount of fuel B into a certain proportion.Figure 4 the amount of fuel air-conditioning systemsIn the steady state, the system can guarantee the amount of fuel and air supply to meetv B V α=Select v α air volume is slightly larger than the theoretical air B complete combustion needs. The advantage of this system is simple; it can be eliminated from the load side and fuel side of the various disturbances.2.4 Citation of air volume control systemThe extent required in order maintaining the furnace pressure of the wind and the air supply to adapt Furnace pressure will also influence the level of security and economic operation of the boiler. Furnace pressure is too low to make a lot of cold air to leak into the furnace will increase the load and smoke damage induced draft fan, the furnace pressure is too low and may even cause the implosion; furnace pressure higher than atmospheric pressure, will The flames and smoke to emerge, not only a health hazard, and may even affect the equipment and life safety. Lead the task of the air volume control subsystem is to ensure that the furnace negative pressure, and vacuum furnace must be controlled within the allowable range, generally-20Pa .Means to control the furnace pressure and adjust the amount of induced draft fan, induced draft fan, its main external disturbance is the air supply. As a regulator of the inertia of the furnace flue, no matter, including interferenceand outside interference are similar to a proportional component. Generally use a single loop controller system, plus the method of the feed forward control is shown in Figure 5Figure 5 cited the air volume control subsystemFurnace pressure and the figure for a given value, S is the measured furnace pressure and Q is the lead air volume, V is the air supply. Furnace pressure and actually determine the balance of air volume and the amount of the wind, the air flow as a feed forward signal to improve the regulation performance of the system. In addition, because the adjustment object is equivalent to a proportional component, was the amount of reaction is too sensitive, in order to prevent minor deviations caused by the frequent action of the induced draft fan baffle, you can set the ratio of the regulator with auto-correction link, making a small deviation increase regulator proportional band. S is measure signal for the negative pressure, and the need for low-pass filter to suppress the volatility of the measured value, the system hardware configuration.Conventional instruments in the boiler combustion process control, lag, intermittent adjustment, the oxygen content in the flue gas exceeds a given value, low load and low flue gas temperature. Adopts PLC to control the boiler, due to its fast computing speed, high precision, accurate and reliable, can be adapted to the complex and difficult to deal with the control system. Thus, you can solve a difficult problem to solve the above control by conventional instruments. The selected PLC system requires a strong compatibility with minimum investment in the system to the completion and operation. Secondly, when the design automation system to change does not require re-programming, input and output system does not require. The wiring does not need to re-train of personnel, would enable the PLC system upgrade. Finally, higher system is performance. The hardware structure is shown in Figure 6..Figure 6 hardware structureAccording to the requirements of the system, select Siemens PLCS7-200 CPU226 as control core, and it also extends the two EM231 Analog Input Modules and a CP243-1 Ethernet module. The CPU226 I/O point is 2416, so that fully meet the requirements of the system. At the same time, the choice of the EM231 module, which is the A/D converter module has four analog inputs 12 A/D, its sampling rate of 25μs, temperature sensors, pressure sensors, flow sensors and oxygen detection sensor output signal conditioning and amplification processing become the standard signal of 0~5V, the EM231 module automatically complete the A/D converter.The physical characteristics of the S7-200 PPI interface RS-485 can work in the PPI, MPI, and free communication port mode. It provides a variety of options for communication between PC and PLC.For the realization of the man-machine dialogue function, such as system status and variable graphics, parameter changes, etc., but also extends a Eview500 series of touch screen, simple, convenient operation control, can be used to set system parameters, display the boiler temperature. There is an Ethernet module CP243-1, whose role is to allow the S7-200 directly connected to Ethernet via Ethernet long-distance exchange data with other S7-200 for data transmission, communication based on TCPIP easy to install, simple.3 system software designControl procedures using the STEP 7-Micro Win Software, ladder way to write its software block diagram shown in Figure 7.Figure 7 the main block diagram softwareS7-200PLC given to a PID instruction, thus eliminating the need for complex PID algorithm programming process, which is the greatly facilitates the use of the user. Using the PID instruction has the following main points and experience:①The scale factor and the integration time constant. Should be determined based on experience and repeated debugging.②Adjust the volume, normalized to the quantitative output parameters of the standard conversion.③Fill in the correct order of the PID loop parameter table (LOOP TABLE), allocated to each parameter address.4 ConclusionsUnit power plant combustion process control system is put into use in a thermal power plant generating units boiler coordinated control system. The actual operation: fuzzy feed-forward due to the introduction of the load, the boiler combustion control system as a coordination and control subsystem, the ability to follow the unit load changes significantly improve the oxy-acetylene ratio consistent with the static and dynamic process; to send the wind improve the control system logic control system with the smooth running and safety, the furnace pressure and reduce the fluctuations, to meet the demands of the run; constant of the unit load, boiler combustion stability, each tune the parameters of dynamic deviation significantly reduce the achieve the optimization of combustion ofthe boiler; nonlinear PID regulation to solve the shaking of the wind baffle.Siemens PLC control, not only simplifies the system, improve equipment reliability and stability, but also significantly improve the thermal efficiency of the combustion energy. Real-time changes in different conditions require the operator panel to modify the system parameters to meet a variety of information of the unit, such as work status, fault conditions can be audible and visual alarm and text form, the main control parameters (temperature) to the trend graph in the form of records to facilitate the operation and maintenance of equipment, the system versatility, scalability, intuitive and easy to operate.。