影响PDC钻头技术性能指标的因素
浅谈聚晶金刚石复合片(PDC)钻头失效的原因及解决对策2
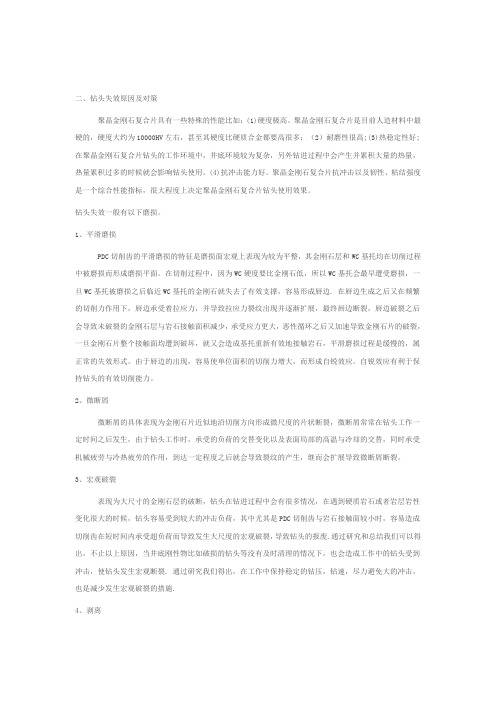
二、钻头失效原因及对策聚晶金刚石复合片具有一些特殊的性能比如:(1)硬度极高。
聚晶金刚石复合片是目前人造材料中最硬的,硬度大约为10000HV左右,甚至其硬度比硬质合金都要高很多;(2)耐磨性很高;(3)热稳定性好;在聚晶金刚石复合片钻头的工作环境中,井底环境较为复杂,另外钻进过程中会产生并累积大量的热量,热量累积过多的时候就会影响钻头使用。
(4)抗冲击能力好。
聚晶金刚石复合片抗冲击以及韧性、粘结强度是一个综合性能指标,很大程度上决定聚晶金刚石复合片钻头使用效果。
钻头失效一般有以下磨损。
1、平滑磨损PDC切削齿的平滑磨损的特征是磨损面宏观上表现为较为平整,其金刚石层和WC基托均在切削过程中被磨损而形成磨损平面。
在切削过程中,因为WC硬度要比金刚石低,所以WC基托会最早遭受磨损,一旦WC基托被磨损之后临近WC基托的金刚石就失去了有效支撑,容易形成唇边. 在唇边生成之后又在频繁的切削力作用下,唇边承受着拉应力,并导致拉应力裂纹出现并逐渐扩展,最终唇边断裂,唇边破裂之后会导致未破裂的金刚石层与岩石接触面积减少,承受应力更大,恶性循环之后又加速导致金刚石片的破裂,一旦金刚石片整个接触面均遭到破坏,就又会造成基托重新有效地接触岩石,平滑磨损过程是缓慢的,属正常的失效形式。
由于唇边的出现,容易使单位面积的切削力增大,而形成自锐效应。
自锐效应有利于保持钻头的有效切削能力。
2、微断屑微断屑的具体表现为金刚石片近似地沿切削方向形成微尺度的片状断裂,微断屑常常在钻头工作一定时间之后发生,由于钻头工作时,承受的负荷的交替变化以及表面局部的高温与冷却的交替,同时承受机械疲劳与冷热疲劳的作用,到达一定程度之后就会导致裂纹的产生,继而会扩展导致微断屑断裂。
3、宏观破裂表现为大尺寸的金刚石层的破断,钻头在钻进过程中会有很多情况,在遇到硬质岩石或者岩层岩性变化很大的时候,钻头容易受到较大的冲击负荷,其中尤其是PDC切削齿与岩石接触面较小时,容易造成切削齿在短时间内承受超负荷而导致发生大尺度的宏观破裂,导致钻头的报废.通过研究和总结我们可以得出,不止以上原因,当井底刚性物比如破损的钻头等没有及时清理的情况下,也会造成工作中的钻头受到冲击,使钻头发生宏观断裂. 通过研究我们得出,在工作中保持稳定的钻压,钻速,尽力避免大的冲击,也是减少发生宏观破裂的措施.4、剥离由于钻头是由不同的材料构成,一旦金刚石层与碳化钨基托的粘接破坏就容易造成剥离. 剥离现象出现之后就会使刃口不复存在之后失去切削能力。
PDC钻头工作原理及相关特点

第二章 PDC 钻头工作原理及相关特点PDC 钻头是依靠安装在钻头体上的切削齿切削地层的,这些切削齿有复合片切削齿和齿柱式两种结构,它们的结构以及在钻头上的安装方式如图1-2所示。
复合片式切削齿是将复合片直接焊接在钻头体上预留的凹槽内而形成的。
它一般用于胎体钻头;齿柱式切削齿是将复合片焊接在碳化钨齿柱上而形成的,安装时将其齿柱镶嵌或焊接在钻头体上的齿空内,它一般用于钢体钻头,也有用于胎体钻头的。
复合片(即聚晶金刚石复合片)是切削齿的核心。
复合片一般为圆片状,其结构如图1-3所示,它是由人造聚晶金刚石薄层及碳化钨底层组成,具有高强度、高硬度及高耐磨性,可耐温度750℃。
人们早就从实验中发现,岩石的诸力学强度中,抗拉强度最低,剪切强度次之,而抗压强度最高,抗压强度往往比剪切强度高数倍至十多倍。
显然采用剪切方式破碎岩石比用压碎方式要容易而有效的多。
PDC 钻头的复合片切削结构正是利用了岩石这一力学特性,采用高效的剪切方式来破碎岩石,从而达到了快速钻井的(a) 复合片式切削齿 (b)齿柱式切削齿图1-2 切削齿在钻头上的安装方式图1-3 复合片的结构图1-4 PDC 钻头的切削方式目的。
当PDC钻头在软到中等级硬度地层进时,复合片切削齿在钻压和扭矩作用下克服地层应力吃入地层并向前滑动,岩石在切削齿作用下沿其剪切方向破碎并产生塑性流动,切削所产生的岩削呈大块片状,这一切削过程与刀具切削金属材料非常相似(见图1-4)。
被剪切下来的岩屑,再由喷嘴射出泥浆带走至钻头与井壁间的环空运至井外。
PDC钻头因使用了聚晶金刚石复合片作切削元件而使得切削齿有很高的硬度和耐磨性。
PDC齿的缺点是热稳定性差,当温度超过700℃时,金刚石层内的粘结金属将失效而导致切削齿破坏,因此PDC齿不能直接烧结在胎体上而只能采用低温钎焊方式将其固定在钻头体上。
在工作中,切削齿底部磨损面在压力作用下一直与岩石表面滑动摩擦要产生大量的摩擦热,当切削齿清洗冷却条件不好,局部温度较高时,就有可能导致切削齿的热摩损(350-700℃时,切削齿的磨损速度很快,这一现象称为切削齿的热磨损)而影响钻头正常工作,所以钻头要避免热磨损出现就必须有很好的水力清洗冷却,润滑作用配合工作,这就是要求泥浆从喷嘴流出后水力分布要合理,能有效地保护切削齿,这即是对钻头水力计的基本要求之一。
自-PDC钻头的检测与误差原因解析
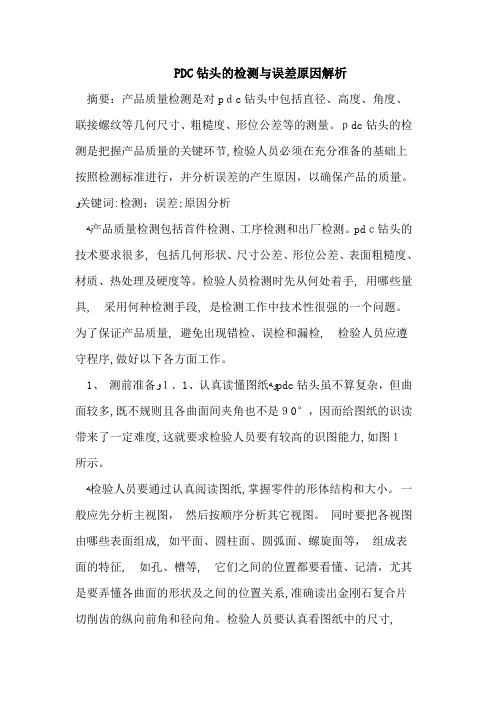
PDC钻头的检测与误差原因解析摘要:产品质量检测是对pdc钻头中包括直径、高度、角度、联接螺纹等几何尺寸、粗糙度、形位公差等的测量。
pdc钻头的检测是把握产品质量的关键环节,检验人员必须在充分准备的基础上按照检测标准进行,并分析误差的产生原因,以确保产品的质量。
ﻭ关键词:检测;误差;原因分析ﻪ产品质量检测包括首件检测、工序检测和出厂检测。
pdc钻头的技术要求很多, 包括几何形状、尺寸公差、形位公差、表面粗糙度、材质、热处理及硬度等。
检验人员检测时先从何处着手, 用哪些量具, 采用何种检测手段, 是检测工作中技术性很强的一个问题。
为了保证产品质量, 避免出现错检、误检和漏检, 检验人员应遵守程序,做好以下各方面工作。
1、测前准备ﻭ1.1、认真读懂图纸ﻪﻭpdc钻头虽不算复杂,但曲面较多,既不规则且各曲面间夹角也不是90°,因而给图纸的识读带来了一定难度,这就要求检验人员要有较高的识图能力,如图1所示。
ﻪ检验人员要通过认真阅读图纸,掌握零件的形体结构和大小。
一般应先分析主视图,然后按顺序分析其它视图。
同时要把各视图由哪些表面组成, 如平面、圆柱面、圆弧面、螺旋面等,组成表面的特征, 如孔、槽等, 它们之间的位置都要看懂、记清,尤其是要弄懂各曲面的形状及之间的位置关系,准确读出金刚石复合片切削齿的纵向前角和径向角。
检验人员要认真看图纸中的尺寸,通过看尺寸, 可以了解零件的大小, 看尺寸要从长、宽、高三个方向的设计基准进行分析, 要分清定形尺寸、定位尺寸、关键尺寸,要分清精加工面、粗加工面和非加工面。
在关键尺寸中,根据公差精度、表面粗糙度等级分析零件各尺寸的作用。
有表面需热处理的工序零件, 应注意处理前后尺寸公差变化的情况。
检验人员还应分析图纸中的标题栏,标题栏内标有所用零件名称, 通过看标题栏, 掌握零件所用材料规格、牌号和标准,从中分析材料的工艺性能, 以及对加工质量的影响。
工作中, 我曾遇到这样一个问题, 有一批pdc钻头表面粗糙度不好,并且加工效率较低, 严重影响了产品精度与产品质量。
PDC钻头保径特征对定向性能的影响
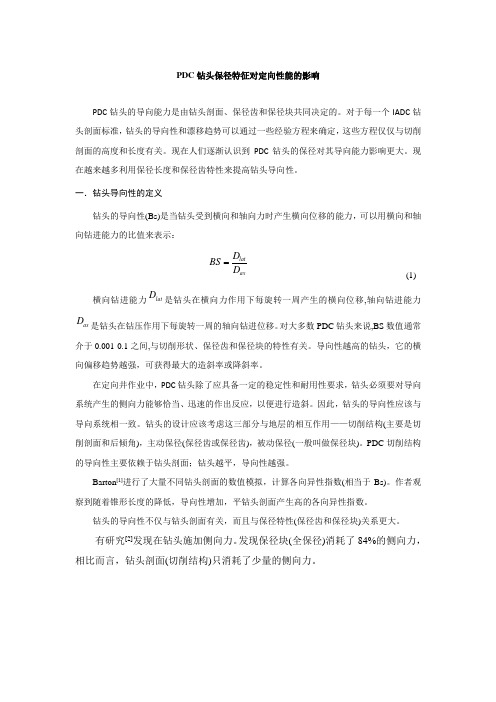
PDC 钻头保径特征对定向性能的影响PDC 钻头的导向能力是由钻头剖面、保径齿和保径块共同决定的。
对于每一个IADC 钻头剖面标准,钻头的导向性和漂移趋势可以通过一些经验方程来确定,这些方程仅仅与切削剖面的高度和长度有关。
现在人们逐渐认识到PDC 钻头的保径对其导向能力影响更大。
现在越来越多利用保径长度和保径齿特性来提高钻头导向性。
一.钻头导向性的定义钻头的导向性(Bs)是当钻头受到横向和轴向力时产生横向位移的能力,可以用横向和轴向钻进能力的比值来表示:latax D BS D (1)横向钻进能力lat D 是钻头在横向力作用下每旋转一周产生的横向位移,轴向钻进能力ax D 是钻头在钻压作用下每旋转一周的轴向钻进位移。
对大多数PDC 钻头来说,BS 数值通常介于0.001-0.1之间,与切削形状、保径齿和保径块的特性有关。
导向性越高的钻头,它的横向偏移趋势越强,可获得最大的造斜率或降斜率。
在定向井作业中,PDC 钻头除了应具备一定的稳定性和耐用性要求,钻头必须要对导向系统产生的侧向力能够恰当、迅速的作出反应,以便进行造斜。
因此,钻头的导向性应该与导向系统相一致。
钻头的设计应该考虑这三部分与地层的相互作用——切削结构(主要是切削剖面和后倾角),主动保径(保径齿或保径齿),被动保径(一般叫做保径块)。
PDC 切削结构的导向性主要依赖于钻头剖面;钻头越平,导向性越强。
Barton [1]进行了大量不同钻头剖面的数值模拟,计算各向异性指数(相当于Bs)。
作者观察到随着锥形长度的降低,导向性增加,平钻头剖面产生高的各向异性指数。
钻头的导向性不仅与钻头剖面有关,而且与保径特性(保径齿和保径块)关系更大。
有研究[2]发现在钻头施加侧向力。
发现保径块(全保径)消耗了84%的侧向力,相比而言,钻头剖面(切削结构)只消耗了少量的侧向力。
图1 定向井PDC钻头各部位消耗的侧向力Fig1 The lateral force consumed by each part of the PDC bit in directional drilling二.保径特性对其导向性的影响主动保径由PDC 钻头的直径位置上的削平部分构成,形成了切削结构和被动保径之间的过渡区。
关于PDC钻头破岩效率的研究
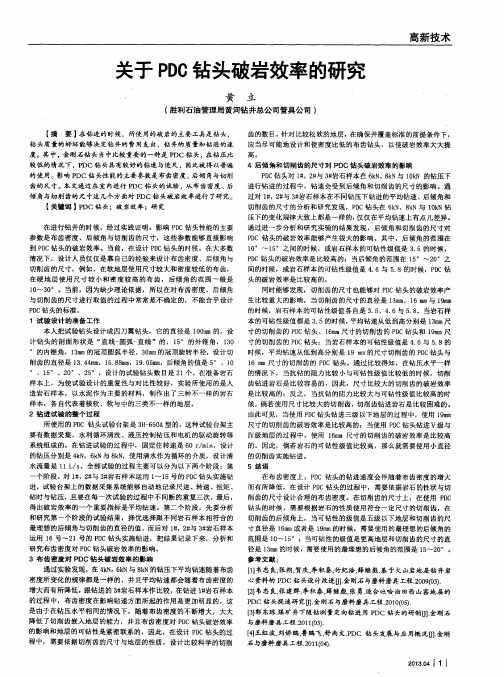
【 关键词 】 P DC钻 头 ; 破 岩效率 ; 研 究
在进行钻井的时候 ,经过实践证明,影响 P D C钻头性能 的主要
压下的变化规律大致上都是一样的, 仅 仅在 平均钻速上有 点儿差异 。 参数是布齿密度 、后倾角 与切 削齿 的尺 寸,这些参数能够直接影响
到P D C钻头 的破岩效 率。当前,在 设计 P D C钻头的时候 ,在大多数 情况下 ,设计人员仅仅是靠 自己的经验 来设计布齿密度、后倾角与 切削齿的尺寸 。例如 ,在软地层使 用尺 寸较 大和 密度较低的布齿 ,
高。
钻 头质量的好 坏能够决定钻井的 费用支 出、钻 井的质量和钻进 的速
度。其 中, 金刚石钻头 当中比较重要的一种是 P D C钻 头, 在钻压 比 较低的情况下 , P D C钻 头具有较好的钻速与进尺 ,因此被得 以普遍 的使用 。 影响 P D C钻头性能的主要参数是布齿密度、 后倾 角与切 削
高新技 术
关于 P D 0 钻头破岩效率 的研究
黄 立
( 胜利石油管理局黄河钻井总公司管具公司 )
【 摘 要】 在 钻进 的时候 ,所使用的破岩 的主要 工具是钻 头,
齿的数 目。 针对 比较松软 的地层 ,在确保井覆盖标准 的前提条件下 , 应当尽可能地设计和使密度 比低的布齿钻头 ,以使破岩效率大大提
由此可见 ,当使用 P D C钻头钻进三级 以下地层 的过程 中,使用 1 9 m m 尺寸 的切削齿的破岩效率是比较高的;当使用 P D C钻头钻进 V级与 Ⅳ级地层 的过程 中,使用 1 6 m m尺寸 的切 削齿 的破岩效率是 比较高 的 因此 ,倘若岩石 的可钻性级值 比较 高,那么就 需要使用小直径 的切削齿实施钻进。
PDC_钻头钻井提速关键影响因素研究
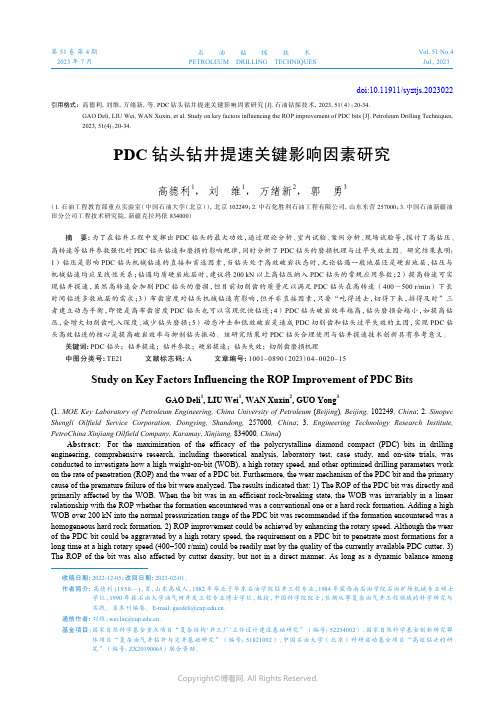
第 51 卷 第 4 期石 油 钻 探 技 术Vol. 51 No.4 2023 年 7 月PETROLEUM DRILLING TECHNIQUES Jul., 2023doi:10.11911/syztjs.2023022引用格式:高德利,刘维,万绪新,等. PDC钻头钻井提速关键影响因素研究[J]. 石油钻探技术,2023, 51(4):20-34.GAO Deli, LIU Wei, WAN Xuxin, et al. Study on key factors influencing the ROP improvement of PDC bits [J]. Petroleum Drilling Techniques,2023, 51(4):20-34.PDC钻头钻井提速关键影响因素研究高德利1, 刘 维1, 万绪新2, 郭 勇3(1. 石油工程教育部重点实验室(中国石油大学(北京)),北京 102249;2. 中石化胜利石油工程有限公司,山东东营 257000;3. 中国石油新疆油田分公司工程技术研究院,新疆克拉玛依 834000)摘 要: 为了在钻井工程中发挥出PDC钻头的最大功效,通过理论分析、室内试验、案例分析、现场试验等,探讨了高钻压、高转速等钻井参数强化对PDC钻头钻速和磨损的影响规律,同时分析了PDC钻头的磨损机理与过早失效主因。
研究结果表明:1)钻压是影响PDC钻头机械钻速的直接和首选因素,当钻头处于高效破岩状态时,无论钻遇一般地层还是硬岩地层,钻压与机械钻速均应呈线性关系;钻遇均质硬岩地层时,建议将200 kN以上高钻压纳入PDC钻头的常规应用参数;2)提高转速可实现钻井提速,虽然高转速会加剧PDC钻头的磨损,但目前切削齿的质量足以满足PDC钻头在高转速(400~500 r/min)下长时间钻进多数地层的需求;3)布齿密度对钻头机械钻速有影响,但并非直接因素,只要“吃得进去,切得下来,排得及时”三者建立动态平衡,即便是高布齿密度PDC钻头也可以实现优快钻进;4)PDC钻头破岩效率越高,钻头磨损会越小,如提高钻压,会增大切削齿吃入深度、减少钻头磨损;5)动态冲击和低效破岩是造成PDC切削齿和钻头过早失效的主因,实现PDC钻头高效钻进的核心是提高破岩效率与抑制钻头振动。
PDC钻头执行标准

PDC钻头执行标准PDC钻头是一种广泛应用于石油钻井、煤矿开采和地质勘探等领域的钻井工具,其执行标准的制定对于保障钻头质量、提高钻井效率具有重要意义。
本文将从PDC钻头的材料要求、制造工艺、性能测试等方面,对PDC钻头执行标准进行详细阐述。
一、材料要求。
PDC钻头的刀片通常采用聚晶金刚石复合片作为切削元件,刀体则采用优质的合金钢材料。
PDC钻头的执行标准应明确规定刀片和刀体材料的选用标准、化学成分要求、热处理工艺等,以保证PDC钻头具有良好的耐磨性、抗冲击性和热稳定性。
二、制造工艺。
PDC钻头的制造工艺对其质量和性能具有重要影响。
执行标准应规定PDC钻头的整体设计要求、刀片与刀体的结合工艺、焊接工艺、表面涂层工艺等,确保PDC钻头具有良好的耐磨性和抗冲击性,同时提高钻头的使用寿命和钻井效率。
三、性能测试。
PDC钻头的性能测试是保证其质量的重要手段。
执行标准应明确规定PDC钻头的性能测试项目和测试方法,包括静态性能测试、动态性能测试、耐磨性测试、抗冲击性测试等,以确保PDC钻头符合设计要求,并能在实际工程中发挥良好的钻井效果。
四、质量控制。
PDC钻头的质量控制是执行标准的核心内容。
标准应规定PDC钻头的质量控制要求,包括原材料的采购检验、生产过程中的质量控制、成品的检测验收等,以确保PDC钻头的质量稳定可靠。
五、使用与维护。
执行标准还应包括PDC钻头的使用与维护要求,包括钻头的安装与拆卸、使用过程中的注意事项、钻头的修复与保养等,以延长PDC钻头的使用寿命,降低钻井成本。
六、结语。
PDC钻头执行标准的制定对于规范PDC钻头的生产与使用具有重要意义。
本文从材料要求、制造工艺、性能测试、质量控制、使用与维护等方面对PDC钻头执行标准进行了全面的阐述,希望能为相关行业的从业人员提供参考,推动PDC 钻头行业的健康发展。
PDC_钻头齿的破岩机理和性能测试方法研究现状

PDC钻头齿的破岩机理和性能测试方法研究现状李彦操(中石化胜利油田分公司, 工程技术管理中心, 山东东营 257000)摘要 聚晶金刚石复合片(polycrystalline diamond compact,PDC)钻头,是钻井工程中主要破岩工具之一。
PDC钻头切削齿的破岩效率、耐磨性、热稳定性和抗冲击性等性能指标对PDC钻头的使用效果影响很大,相关研究在国内外备受关注。
本文总结了国内外有关PDC钻头齿破岩机理和性能测试的实验装置、测试方法等代表性成果,按照PDC钻头齿与岩石相互作用的方式,相关实验主要包括5大类:PDC钻头齿直线切削实验、旋转切削实验、落锤冲击实验、PDC钻头单齿静压实验以及全尺寸PDC钻头实验;按照测试目的,又可分为PDC钻头齿的破岩机理和性能测试2大类。
通过调研分析这些实验研究的优缺点,以期为PDC钻头齿的研究与优化、PDC钻头的整体个性化设计等提供参考。
关键词 PDC钻头齿;直线切削实验;旋转切削实验;落锤冲击实验;PDC单齿静压实验;全尺寸PDC 钻头实验中图分类号 TQ164; TG74; TG58 文献标志码 A 文章编号 1006-852X(2023)05-0553-15DOI码 10.13394/ki.jgszz.2023.0155收稿日期 2023-08-01 修回日期 2023-08-16自2000年起,随着科研人员对PDC钻头齿破岩机理的深化理解和超硬材料科学与生产工艺的不断进步,PDC钻头在石油和天然气钻井工程中的应用逐渐普及。
如今,PDC钻头在油气钻井领域占据了超过80%的市场份额,贡献了90%以上的全球钻井进尺,几乎成为全球高端钻头市场的主导力量[1]。
PDC钻头齿的技术进步极大地推动了油气钻井工程的效益增长,然而,其有限的耐磨性、热稳定性和抗冲击性仍是制约PDC钻头齿更广泛应用的因素。
因此,研究PDC钻头齿本身的材料特性及其破岩机理,存在着广阔的创新空间和潜力巨大的工业应用前景。
PDC钻头使用方法
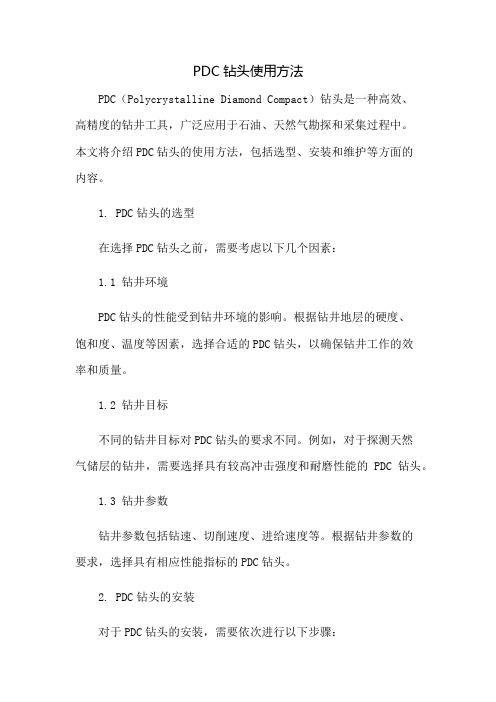
PDC钻头使用方法PDC(Polycrystalline Diamond Compact)钻头是一种高效、高精度的钻井工具,广泛应用于石油、天然气勘探和采集过程中。
本文将介绍PDC钻头的使用方法,包括选型、安装和维护等方面的内容。
1. PDC钻头的选型在选择PDC钻头之前,需要考虑以下几个因素:1.1 钻井环境PDC钻头的性能受到钻井环境的影响。
根据钻井地层的硬度、饱和度、温度等因素,选择合适的PDC钻头,以确保钻井工作的效率和质量。
1.2 钻井目标不同的钻井目标对PDC钻头的要求不同。
例如,对于探测天然气储层的钻井,需要选择具有较高冲击强度和耐磨性能的PDC钻头。
1.3 钻井参数钻井参数包括钻速、切削速度、进给速度等。
根据钻井参数的要求,选择具有相应性能指标的PDC钻头。
2. PDC钻头的安装对于PDC钻头的安装,需要依次进行以下步骤:2.1 准备PDC钻头在安装PDC钻头之前,需要检查钻头的质量和完整性。
确保PDC钻头没有损坏或磨损。
2.2 加固钻头连接部分将PDC钻头安装在钻杆的连接部分。
使用正确的扳手和力量,将钻头牢固地固定在钻杆上。
2.3 进行预检安装好PDC钻头后,进行预检。
确保钻头连接部分牢固可靠,并进行必要的检查和调整。
3. PDC钻头的使用注意事项在使用PDC钻头时,需要注意以下几点:3.1 控制钻速在钻井过程中,要根据地层的硬度和井眼的尺寸,适当控制钻头的转速。
过高的钻速可能导致钻头过度磨损或损坏。
3.2 保持稳定保持钻井过程的稳定性是使用PDC钻头的关键。
通过控制进给速度和注浆质量,保持钻头的稳定工作。
3.3 注意钻头冷却PDC钻头因为切削过程中会产生高温,所以需要进行有效的冷却。
采用合适的冷却液体,保持钻头的正常工作温度。
4. PDC钻头的维护定期进行PDC钻头的维护,可以延长其使用寿命。
以下是几个常见的维护方法:4.1 清洗和磨削定期清洗和磨削PDC钻头,去除切削面上的积土和残留物。
影响PDC钻头在定向井中性能的原因
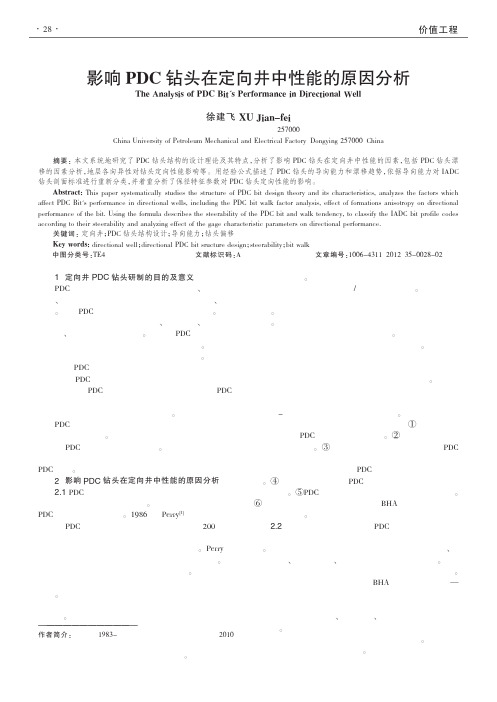
价值工程1定向井PDC 钻头研制的目的及意义PDC 钻头在砂岩和泥岩地层机械钻速高、钻头工作寿命长、耐高温能力强于牙轮钻头,同样适合定向井、水平井施工。
现在PDC 钻头已成为油气钻井的主力钻头。
但在定向井作业中,常出现初始造斜困难、方位不稳、钻头偏移趋势增加、钻头进尺缓慢等现象。
在影响PDC 钻头定向钻进能力的因素中,其整体结构设计特点尤为关键。
决定着定向造斜是否成功,稳斜阶段能否保持平稳钻进。
研究PDC 钻头不同的结构参数对定向钻进的影响,找出影响PDC 钻头定向钻进中不稳定的关键结构性因素,为定向井PDC 钻头的设计提供一种依据,让PDC 钻头在定向钻进中发挥出更大的优势,提高定向钻井速度,降低钻井成本是一项有待解决的问题。
PDC 钻头的结构变化多,设计灵活性大,对地层和使用条件敏感性很强。
因而,针对特定地层和使用条件进行设计是PDC 钻头的一项关键技术。
本文针对长庆油田鄂尔多斯盆地的地层特点,研究设计适合该地层的定向井PDC 钻头。
2影响PDC 钻头在定向井中性能的原因分析2.1PDC 钻头漂移的因素分析在数十年的石油钻井中,已经发现钻头的偏转现象。
牙轮钻头一般向右偏转,PDC 钻头一般向左偏转。
1986年,Perry [1]在泰国湾用五种类型的PDC 钻头做了一个关于钻头漂移超过200组实验的系统分析,发现钻头的钻进趋势不但受到钻头切削剖面影响,还受到操作参数影响,例如钻压和转速。
Perry 得出结论,钻头钻进趋势不会受到钻头保径长度的影响。
钻头的偏移可能受到许多因素的影响。
在给定的特定钻进条件下确定钻头的向左偏移还是向右便宜是非常困难的。
在定向钻进中,仅仅了解钻头的偏移趋势是不够的,钻头偏移率尤其重要,它是钻头偏移力和钻头转向率作用的结果。
正偏移速率代表钻头向右偏移,负移位速率代表钻头向左偏移。
模拟上述不同情况下钻头偏移的机理需要完全理解在定向钻进中钻头/地层的相互作用。
钻头的定向行为主要受钻头的导向能力和漂移角度影响。
PDC钻头应用性能的影响因素分析
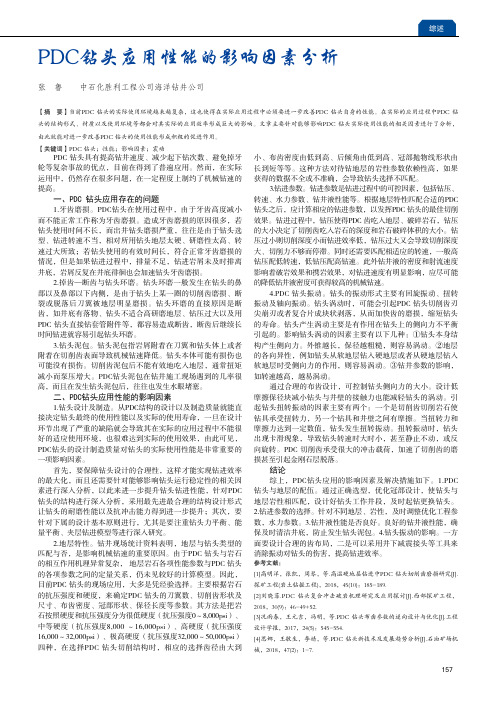
PDC 钻头具有提高钻井速度、减少起下钻次数、避免掉牙轮等复杂事故的优点,目前在得到了普遍应用。
然而,在实际运用中,仍然存在很多问题,在一定程度上制约了机械钻速的提高。
一、PDC 钻头应用存在的问题1.牙齿磨损。
PDC钻头在使用过程中,由于牙齿高度减小而不能正常工作称为牙齿磨损。
造成牙齿磨损的原因很多,若钻头使用时间不长,而出井钻头磨损严重,往往是由于钻头选型、钻进转速不当,相对所用钻头地层太硬、研磨性太高、转速过大所致;若钻头使用的有效时间长,符合正常牙齿磨损的情况,但是如果钻进过程中,排量不足,钻进岩屑未及时排离井底,岩屑反复在井底徘徊也会加速钻头牙齿磨损。
2.掉齿—断齿与钻头环磨。
钻头环磨一般发生在钻头的鼻部以及鼻部以下内侧,是由于钻头上某一圈的切削齿磨损、断裂或脱落后刀翼被地层明显磨损。
钻头环磨的直接原因是断齿,如井底有落物、钻头不适合高研磨地层、钻压过大以及用PDC 钻头直接钻套管附件等,都容易造成断齿,断齿后继续长时间钻进就容易引起钻头环磨。
3.钻头泥包。
钻头泥包指岩屑附着在刀翼和钻头体上或者附着在切削齿表面导致机械钻速降低。
钻头本体可能有损伤也可能没有损伤。
切削齿泥包后不能有效地吃入地层,通常扭矩减小而泵压增大。
PDC钻头泥包在钻井施工现场遇到的几率很高,而且在发生钻头泥包后,往往也发生水眼堵塞。
二、PDC钻头应用性能的影响因素1.钻头设计及制造。
从PDC结构的设计以及制造质量就能直接决定钻头最终的使用性能以及实际的使用寿命,一旦在设计环节出现了严重的缺陷就会导致其在实际的应用过程中不能很好的适应使用环境,也很难达到实际的使用效果,由此可见,PDC钻头的设计制造质量对钻头的实际使用性能是非常重要的一项影响因素。
首先,要保障钻头设计的合理性,这样才能实现钻进效率的最大化,而且还需要针对能够影响钻头运行稳定性的相关因素进行深入分析,以此来进一步提升钻头钻进性能,针对PDC 钻头的结构进行深入分析,采用最先进最合理的结构设计形式让钻头的耐磨性能以及抗冲击能力得到进一步提升;其次,要针对下属的设计基本原则进行,尤其是要注重钻头力平衡、能量平衡、夹层钻进模型等进行深入研究。
pdc钻头生产标准

pdc钻头生产标准PDC钻头的生产标准是确保其质量和性能的重要环节。
下面将详细介绍PDC钻头的生产标准。
1.材料选用PDC钻头的刀片材料应采用高质量的聚结金刚石,其粒度分布均匀,颗粒度适中,以确保钻头的切削效率和使用寿命。
2.刀片设计PDC钻头的刀片应具有合适的尺寸和形状,以适应井筒壁面的形态和孔径。
刀片的数量、密度和布局应根据具体需求进行科学设计。
3.刀片焊接刀片与刀头的焊接是确保PDC钻头性能稳定和寿命长久的关键环节。
焊接工艺应具备以下特点:-高温高压:采用高温高压条件下的热压焊接工艺,确保刀片和刀头的结合牢固稳定。
-清洁环境:焊接过程应在洁净无尘环境下进行,以避免杂质进入焊缝,影响焊接质量。
-焊接参数:焊接过程中的温度、压力和时间等参数应根据刀片和刀头材料的特性进行准确控制。
4.刀片涂覆刀片涂覆是提高PDC钻头耐磨性能的重要步骤。
涂覆通常采用热化学气相沉积(CVD)或物理气相沉积(PVD)技术,以在刀片表面形成坚硬耐磨的涂层。
5.钻头平衡在生产过程中,应该检测钻头的静态和动态平衡。
静态平衡是指钻头静止时的平衡状态,而动态平衡是指钻头在高速旋转时的平衡状态。
平衡不良会导致钻头振动和摇摆,影响钻井效果和安全。
6.性能测试生产完成的PDC钻头应进行性能测试,以确保其满足设计要求和规范。
常见的测试项目包括切削效率、耐磨性、抗压强度和抗破裂强度等。
7.质量控制在整个生产过程中,应建立严格的质量控制体系,包括原材料的采购、生产工艺的控制、检测设备的使用和维护等环节。
每个环节都应有相应的记录和监测,以确保产品质量的稳定和可靠。
综上所述,PDC钻头的生产标准涉及材料选用、刀片设计、焊接工艺、涂覆技术、平衡调整、性能测试和质量控制等方面。
只有严格按照相关标准进行生产,才能生产出具备高质量和可靠性能的PDC钻头。
影响PDC钻头进尺因素
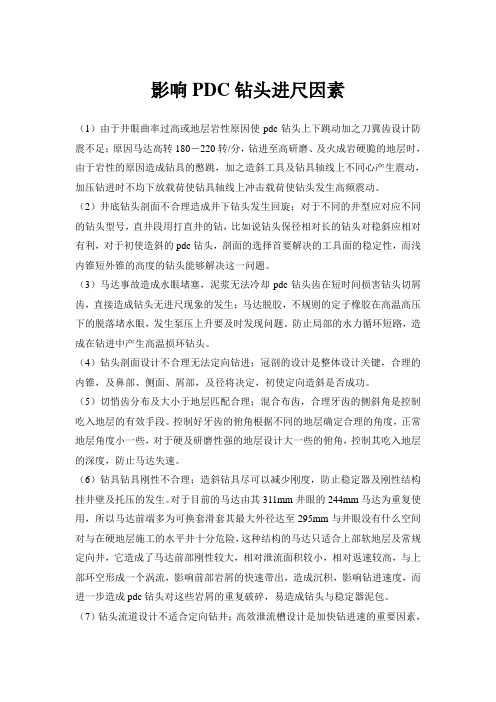
影响PDC钻头进尺因素(1)由于井眼曲率过高或地层岩性原因使pdc钻头上下跳动加之刀冀齿设计防震不足;原因马达高转180-220转/分,钻进至高研磨、及火成岩硬脆的地层时,由于岩性的原因造成钻具的憋跳,加之造斜工具及钻具轴线上不同心产生震动,加压钻进时不均下放载荷使钻具轴线上冲击载荷使钻头发生高频震动。
(2)井底钻头剖面不合理造成井下钻头发生回旋;对于不同的井型应对应不同的钻头型号,直井段用打直井的钻,比如说钻头保径相对长的钻头对稳斜应相对有利,对于初使造斜的pdc钻头,剖面的选择首要解决的工具面的稳定性,而浅内锥短外锥的高度的钻头能够解决这一问题。
(3)马达事故造成水眼堵塞,泥浆无法冷却pdc钻头齿在短时间损害钻头切屑齿,直接造成钻头无进尺现象的发生;马达脱胶,不规则的定子橡胶在高温高压下的脱落堵水眼,发生泵压上升要及时发现问题。
防止局部的水力循环短路,造成在钻进中产生高温损环钻头。
(4)钻头剖面设计不合理无法定向钻进;冠剖的设计是整体设计关键,合理的内锥,及鼻部、侧面、屑部,及径将决定,初使定向造斜是否成功。
(5)切悄齿分布及大小于地层匹配合理;混合布齿,合理牙齿的侧斜角是控制吃入地层的有效手段。
控制好牙齿的俯角根据不同的地层确定合理的角度,正常地层角度小一些,对于硬及研磨性强的地层设计大一些的俯角,控制其吃入地层的深度,防止马达失速。
(6)钻具钻具刚性不合理;造斜钻具尽可以减少刚度,防止稳定器及刚性结构挂井壁及托压的发生。
对于目前的马达由其311mm井眼的244mm马达为重复使用,所以马达前端多为可换套滑套其最大外径达至295mm与井眼没有什么空间对与在硬地层施工的水平井十分危险,这种结构的马达只适合上部软地层及常规定向井,它造成了马达前部刚性较大,相对泄流面积较小,相对返速较高,与上部环空形成一个涡流,影响前部岩屑的快速带出,造成沉积,影响钻进速度,而进一步造成pdc钻头对这些岩屑的重复破碎,易造成钻头与稳定器泥包。
pdc钻头参数

pdc钻头参数
PDC钻头是一种高效的钻井工具,由多个单独的聚结体交替着排列。
每个聚结体包含多个聚合碳化物薄片,其中碳化硅和钨是最常使用的材料。
PDC钻头是一种先进的钻井工具,既具有高强度和高硬度,又能提供良好的耐磨性和高速度的抓取力。
PDC钻头的参数包括钻头的直径,刀齿的数量和排列方式,以及转速和功率等。
钻头直径的选择取决于在钻探过程中需要达到的深度和目标层的特性。
较小的钻头更适合钻探较浅的目标,而较大的钻头更适合钻探深部。
刀齿的数量和排列方式也会影响钻头的效率和性能。
较多的刀齿可以提供更好的切削能力,而刀齿的排列方式可以更好地适应不同的地质条件。
除此之外,PDC钻头所需的转速和功率也是非常重要的参数。
转速和功率的设置应根据目标层的硬度、厚度和地质条件等因素进行调整。
较硬的地层需要更高的转速和功率,而较软的地层则需要较低的转速和功率。
总的来说,PDC钻头的参数设置应该根据具体的钻井条件和目标层的特性来确定。
通过合理的参数配置,可以提高钻头的效率和性能,同时减少钻头损耗和维护成本,从而提高钻井作业的效率和经济效益。
PDC钻头的主要几何参数对其力学性能影响的研究的开题报告

PDC钻头的主要几何参数对其力学性能影响的研究的开题报告1. 研究背景随着石油钻探技术的不断发展,钻头作为石油钻井中不可或缺的元件,在其设计制造中有着重要的地位。
其中,PDC钻头的优点在于其硬度高、磨损耐用,能够提高钻头在钻探中的效率和稳定性。
然而,PDC钻头的设计仍然存在一些难点,其中主要就是如何通过主要几何参数的调整来影响PDC钻头的力学性能,以便更好地适应不同的钻探工况。
2. 研究目的本研究旨在通过分析PDC钻头的主要几何参数,探究这些参数对其力学性能的影响规律,从而为PDC钻头的优化设计提供更为准确的理论依据。
3. 研究内容(1) PDC钻头的主要几何参数:PDC钻头的主要几何参数包括刀翼角度、刀翼间距、齿长宽比等。
本研究将分析这些几何参数的影响规律并探究它们之间的相互关系。
(2) PDC钻头的力学性能:PDC钻头的力学性能主要包括切削力、转矩、抗磨性等。
本研究将通过实验测试、数值模拟等方法,分析不同几何参数对其力学性能的影响规律。
(3)参数优化设计:基于以上研究结果,本研究将提出一种适用于PDC钻头的参数优化设计方案,以提高钻头在钻探过程中的效率和稳定性。
4. 研究方法(1)实验测试法:通过设计一套合理的实验装置,对不同几何参数的PDC钻头进行力学性能测试。
(2)数值模拟法:通过建立PDC钻头的数值模型,对其力学性能进行仿真分析,以探究不同几何参数对其力学性能的影响。
(3)统计分析法:通过对实验数据和数值模拟结果进行统计分析,探究不同几何参数之间的相互关系,并确定最优几何参数。
5. 预期成果(1)对PDC钻头主要几何参数与力学性能之间的关系进行全面深入的探究,揭示其内在规律。
(2)提出一套适用于PDC钻头的参数优化设计方案,以提高钻头在钻探过程中的效率和稳定性。
(3)为PDC钻头的制造企业提供更为科学的理论指导和技术支持,促进其技术创新和产业发展。
影响PDC钻头胎体强度韧性的因素及提高措施
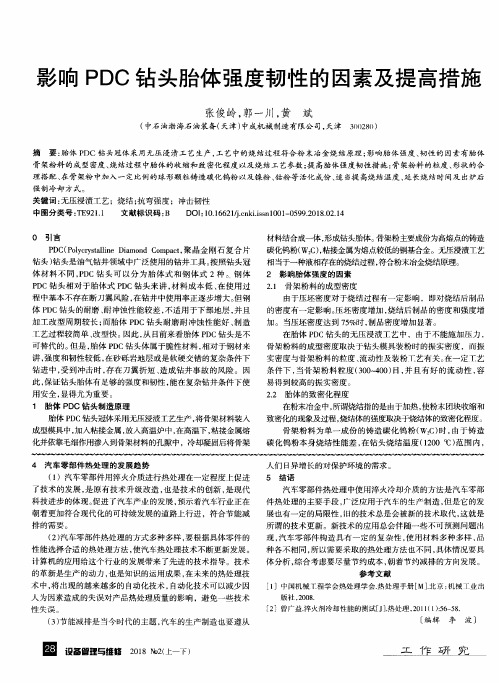
人们 日异增长的对保护环境的需求 。 5 结 语
汽车零部件热处理中使用 淬火 冷却介质 的方法是汽车零部 件热处理的主要手段 ,广泛应用于汽车 的生产制造 ,但是它 的发 展也有一定 的局限性 ,旧的技术总是会被新的技术取代 ,这就是 所谓 的技术更新 。新技术的应 用总会伴 随一些不可预测问题 出 现 ,汽车零部件构造具有 一定的复杂性 ,使用材 料多种多样 ,品 种各不相 同,所 以需要采取 的热处理方法也不同 ,具体情况要具 体分析 ,综合考虑要尽量节约成本 ,朝着节约减排 的方 向发展 。
影响 PDC钻 头胎体 强度韧性 的因素及提 高措 施
张俊 岭,郭一川 ,黄 斌
(中石油渤海石 油装备 (天津 )中成机械制造有限公司 ,天 津 30028())
摘 要 :胎 体 PDC钻 头冠 体 采 用无 压 浸 渍 工 艺 生 产 ,工 艺 中 的烧 结过 程 符合 粉 末 冶金 烧 结 原 理 ;影 响 胎体 强 度 、韧 性 的 因 素有 胎体 骨架粉料 的成型 密度 、烧 结过程 中胎体的收缩和致密化程度 以及烧 结工艺参数 ;提 高胎体 强度韧性措施 :骨架粉料 的粒度 、形状 的合 理搭 配、在骨架粉 中加入 一定比例 的球形颗粒铸造碳 化钨粉 以及镍粉 、钴粉 等活化成份 、适 当提 高烧结温度 、延长烧结时间及 出炉后 强制 冷 却 方 式 。 关键词 :无 压浸 渍工艺 ;烧结 ;抗 弯强度 ;冲击韧性 中 图分 类 号 :TE921.1 文 献标 识码 :B DOI:10.166210.cnki.issn1001—0599.2018.02.14
在粉末冶金中,所谓烧结指的是 由于加热 ,使粉末团块收缩和 致密化 的现象及过程 ,烧结体的强度取决于烧结体的致密化程度 。
PDC钻头使用技术

PDC钻头使用技术
1.钻头选型:
2.钻头设计:
3.钻头组装:
4.钻头润滑:
钻井过程中,润滑油的选用和使用对PDC钻头的寿命有着重要影响。
润滑油要具备良好的润滑性能和冷却性能,以确保钻头能够正常工作。
同时,还需定期检查和更换润滑油,以确保其正常工作。
5.钻具管理:
钻具管理是提高钻头使用寿命和降低钻井成本的重要环节。
在钻具管
理中,需要对钻头进行定期检查,及时处理钻头磨损和切削元件脱落等问题。
另外,需要进行钻头修复和磨损分析,并记录钻头的使用情况和寿命。
6.钻具维护:
维护是保持钻头使用寿命的关键。
在钻井过程中,钻头会不可避免地
与钻井液、岩屑和井壁等物质接触,导致钻头表面磨损和切削元件磨损。
因此,需要定期对钻头进行清洁和维护,尽量减少磨损和损坏。
7.钻具修复:
钻头的损坏和磨损是不可避免的。
当钻头表面磨损或切削元件失效时,需要进行修复或更换。
修复通常包括补焊、镶嵌切削元件等方式,以恢复
钻头的工作能力。
及时修复能够延长钻头的使用寿命并降低钻井成本。
8.钻进参数:
钻进参数是指在钻井过程中控制切削速度和切削力的参数。
合理选择
钻进参数可以提高钻头的使用寿命。
其中包括推进速度、转速、进给速度、压力等,需要根据具体情况进行调整和控制。
总之,PDC钻头的使用技术涉及到选型、设计、组装、润滑、管理、
维护、修复和钻进参数等多个方面,需要综合考虑各种因素来提高钻头的
使用寿命和钻井的效率。
PDC钻头钻速方程影响因素综述
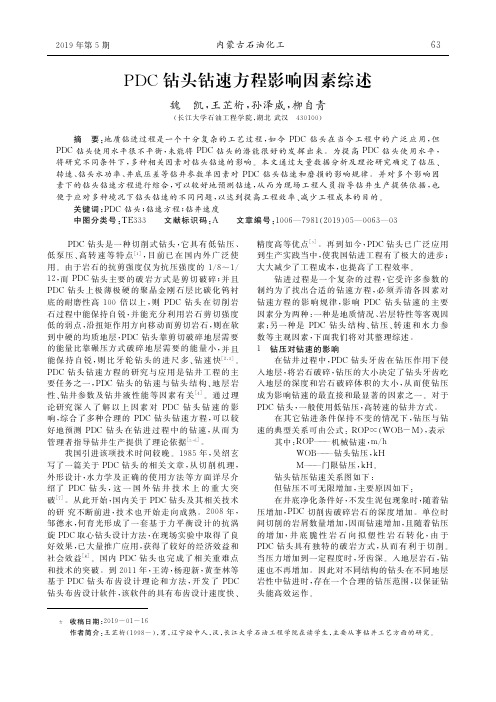
精度高等优点 。 [9] 再 到 如 今,PDC 钻 头 已 广 泛 应 用 到 生 产 实 践 当 中 ,使 我 国 钻 进 工 程 有 了 极 大 的 进 步 ; 大 大 减 少 了 工 程 成 本 ,也 提 高 了 工 程 效 率 。
钻进 过 程 是 一 个 复 杂 的 过 程,它 受 许 多 参 数 的 制约为了找出合适 的 钻 速 方 程,必 须 弄 清 各 因 素 对 钻速方程 的 影 响 规 律,影 响 PDC 钻 头 钻 速 的 主 要 因 素 分 为 两 种 :一 种 是 地 质 情 况 、岩 层 特 性 等 客 观 因 素;另一种 是 PDC 钻 头 结 构、钻 压、转 速 和 水 力 参 数 等 主 观 因 素 ,下 面 我 们 将 对 其 整 理 综 述 。 1 钻 压 对 钻 速 的 影 响
关键词:PDC 钻头;钻速方程;钻井速度 中 图 分 类 号 :TE333 文 献 标 识 码 :A 文 章 编 号 :1006—7981(2019)05—0063—03
PDC 钻头是一 种 切 削 式 钻 头,它 具 有 低 钻 压、 低 泵 压、高 转 速 等 特 点[1],目 前 已 在 国 内 外 广 泛 使 用。由于岩石的抗剪强度仅为抗压强度的 1/8~1/ 12,而 PDC 钻头主要 的 破 岩 方 式 是 剪 切 破 碎;并 且 PDC 钻 头 上 极 薄 极 硬 的 聚 晶 金 刚 石 层 比 碳 化 钨 衬 底的耐磨性 高 100 倍 以 上,则 PDC 钻 头 在 切 削 岩 石过程中能保持自 锐,并 能 充 分 利 用 岩 石 剪 切 强 度 低 的 弱 点 ,沿 扭 矩 作 用 方 向 移 动 而 剪 切 岩 石 ,则 在 软 到中硬的均质地层,PDC 钻头靠剪切破碎 地 层 需 要 的能量比靠碾压方 式 破 碎 地 层 需 要 的 能 量 小,并 且 能 保 持 自 锐,则 比 牙 轮 钻 头 的 进 尺 多、钻 速 快 。 [2,3]
影响PDC钻头应用性能的因素分析
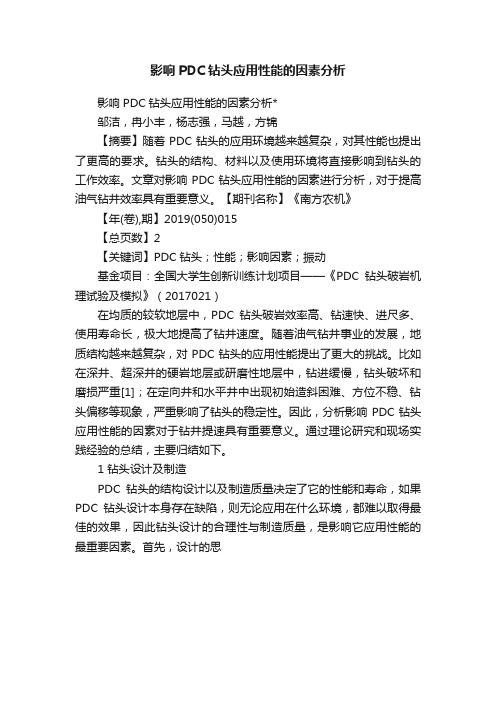
影响PDC钻头应用性能的因素分析
影响PDC钻头应用性能的因素分析*
邹洁,冉小丰,杨志强,马越,方锦
【摘要】随着PDC钻头的应用环境越来越复杂,对其性能也提出了更高的要求。
钻头的结构、材料以及使用环境将直接影响到钻头的工作效率。
文章对影响PDC钻头应用性能的因素进行分析,对于提高油气钻井效率具有重要意义。
【期刊名称】《南方农机》
【年(卷),期】2019(050)015
【总页数】2
【关键词】PDC钻头;性能;影响因素;振动
基金项目:全国大学生创新训练计划项目——《PDC钻头破岩机理试验及模拟》(2017021)
在均质的较软地层中,PDC钻头破岩效率高、钻速快、进尺多、使用寿命长,极大地提高了钻井速度。
随着油气钻井事业的发展,地质结构越来越复杂,对PDC钻头的应用性能提出了更大的挑战。
比如在深井、超深井的硬岩地层或研磨性地层中,钻进缓慢,钻头破坏和磨损严重[1];在定向井和水平井中出现初始造斜困难、方位不稳、钻头偏移等现象,严重影响了钻头的稳定性。
因此,分析影响PDC钻头应用性能的因素对于钻井提速具有重要意义。
通过理论研究和现场实践经验的总结,主要归结如下。
1 钻头设计及制造
PDC钻头的结构设计以及制造质量决定了它的性能和寿命,如果PDC钻头设计本身存在缺陷,则无论应用在什么环境,都难以取得最佳的效果,因此钻头设计的合理性与制造质量,是影响它应用性能的最重要因素。
首先,设计的思。
- 1、下载文档前请自行甄别文档内容的完整性,平台不提供额外的编辑、内容补充、找答案等附加服务。
- 2、"仅部分预览"的文档,不可在线预览部分如存在完整性等问题,可反馈申请退款(可完整预览的文档不适用该条件!)。
- 3、如文档侵犯您的权益,请联系客服反馈,我们会尽快为您处理(人工客服工作时间:9:00-18:30)。
影响PDC钻头技术性能指标的因素第一、地层的因素,地层含有灰质、石英质、玄武岩等火成岩及其他质硬的砾石等,极易造成复合片先期磨损、崩齿、断齿,甚至在刀翼上磨出凹槽、断刀翼等严重井下复杂情况的发生;含有吸水性较强的泥质地层,在泥浆性能相同的情况下极易造成钻头泥包,甚至卡钻等复杂情况。
第二、操作的因素,猛提猛刹、顿钻、溜钻、钻井参数匹配不当(钻压、转盘转速、泵压、排量、螺杆转速、螺杆扭矩)、井下落物等,也是造成复合片先期磨损、崩齿、断齿,甚至在刀翼上磨出凹槽、断刀翼等严重复杂情况的重要因素。
第三、钻井液的因素,比重、固相含量、失水量、流变性、粘度、切力也对钻头的性能指标有着密切的关系,比重大、固相含量高机械钻速就变低(权威试验证明,固相含量每升高1%,机械钻速就下降8%),对钻头的冲蚀作用就厉害;粘度高、切力大机械钻速变慢;切力小,携带井底沉砂的能力弱,也降低钻头的机械钻速;失水大,在泥岩段极易造成地层吸水膨胀井眼缩径,在砂岩段容易由于失水大造成虚泥饼增厚而井眼缩径,严重影响机械钻速,加速对钻头的磨损报废。
第四、随意变更钻头的水力配置,新出厂的钻头一般都按甲方的要求,进行了科学的水力参数设计,当盲目变更钻头水眼的配置后,就人为地改变了钻头的冷却流场环境,为钻头的先期损坏提供了条件。
【摘要】本文在简要介绍了PDC钻头的物质成份,两大类别(胎体钻头和刚体钻头)及其不同物质在钻井作业过程中所起的作用的基础上,归纳、总结了PDC钻头特点,包括其设计特点和结构特点;同时较详细地分析了在打定向井时,PDC钻头的结构特征因素对造斜率的影响;另外也在分析、归纳、总结国内外专家、学者的独特见解的基础上,对PDC钻头的破岩机理,也在一定程度上给予阐述。
并在此基础上,最后也提出了一些PDC钻头的选型依据。
【关键词】PDC钻头; 特点; 机理分析Abstract:This themsis briefly introduces which materials PDC bit is made from,how it is manufactured,and the different types of PDC bits,also shows you the principal functionsof the different materials of PDC bit in drilling----on the basis of these,summaries the characteristics of PDC bit,including its designing characteristics and structural characteristics,and specificly analyses the effect of its structural characteristics on the leaning ration in the controlled directional drilling。
At the same time ,after studying the specific ideas of the different experts at home and abroad,to some extent,analyses and summaries the rock breaking mechanism of PDC bit。
In the end ,on this basis,gives you some facters that can help you how to choose PDC bit effiently。
Key words: PDC bit; characteristics; Mechanism analysis近年内,随着PDC钻头的广泛应用,PDC钻头在型号和质量上都进行了较大的改进,已经在软到硬的地层中逐步使用,并且取得了较好的经济效益,为更好地使用PDC钻头,使其最大限度地发挥优势,以便更好地服务于钻井作业,特从其特点和破岩机理方面撰写此文。
PDC钻头,就是聚晶金刚石复合片钻头,即Polycrystalline Diamond CompactBit。
它以金刚石为原料加入粘结剂在高温下烧结而成。
复合片为圆片状,金刚石层厚度一般小于1mm,切削岩石时作为工作层,碳化钨基体对聚晶金刚石薄层起支撑作用。
两者地有机结合,使PDC既具有金刚石地硬度和耐磨性,又具有碳化钨地结构强度和抗冲击能力。
由于聚晶金刚石内晶体间地取向不规则,不存在单晶金刚石固有地解理面,所以PDC的抗磨性及强度高于天然金刚石的,且不易破碎。
PDC由于多种材料的存在,热稳定性较差,同时脆性较强,不能经受冲击载荷。
PDC钻头的特点1973年美国开发了聚晶金刚石复合片钻头,国外广泛应用于软-中硬地层。
在中东和北海的深井及海洋钻井中首先获得了高井尺、高钻速,大大缩短了建井周期,降低了钻井成本,受到了钻境界的广泛重视,成为钻井工具的一项重大成就。
国内对PDC钻头也引起了极大的关注和兴趣,随着钻井技术人员对PDC钻头的认识和实践,它正在逐步取得较好的使用效果。
按钻头材料及切削齿结构划分,PDC钻头有钢体和胎体两大类别(间上图1-2)胎体钻头用碳化钨粉末烧结而成,用人造聚晶金刚石复合片钎焊在碳化钨胎体上,用天然金刚石保径。
碳化钨胎体耐冲蚀、耐磨、强度高、保径效果好。
钻头水眼水道面积可以根据钻井工艺需要的水力参数来设计,有较大的灵活性。
胎体外形可以根据地层特点设计,变化胎体形状只要改变模具而不需要增加设备。
钢体PDC钻头,是用镍、铬、钼合金机械加工成形。
经过热处理后在钻头体上钻孔,强人造聚晶金刚石复合片压入(紧配合)钻头体内,用柱状碳化钨保径。
它比胎体钻头成本低20%左右,但不耐磨且易被冲蚀。
PDC钻头的设计特点1.PDC钻头采用爪型设计PDC钻头的性能在很大程度上取决于切削齿的质量,PDC钻头都采用了高质量爪型齿和环形齿,经过与其它类型复合片对比试验分析,证明它具有抗剪强度高、耐冲击、寿命长、热稳定性能好的特点,与同尺寸普通PDC齿相比,爪型齿的金刚石含量提高了2。
7倍,抗冲击破坏能力提高2倍。
2.大刀翼设计全部PDC钻头系列的刀翼进行加高加大,采用超大排屑流道设计,可以更加有效的运移钻屑,清洗钻头,防止钻头泥包,提高机械钻速。
3.抗回旋设计采用力学平衡设计,对PDC钻头进行螺旋保径设计、轨道布齿设计、缓冲块设计以保证钻头抗回旋性能。
4.防泥包涂层设计和制造技术QP系列钻头可根据地层情况进行防泥包涂层设计,它采用了独特的对钻头表面负离子处理技术,使钻头表面带有负电荷,在钻头周围形成一个阳板,形成电流,钻头与钻井液之间形成一个水的集区,其作用就如同润滑剂或象隔板,在钻进中,泥页岩钻屑中的负离子与钢体表面的负电荷相斥,从而起到防泥包的效果。
5.可修复性钢体PDC钻头的本体磨损和切削齿破碎后可进行修复和更换,使得钻头的使用成本大大降低。
PDC钻头结构特征及此因素对造斜率的影响钻头的费用在一口井中的总费用中所占的比例不是很大,但选好和用好一只钻头对提高机械钻速、提高造斜率和降低全井费用却是关系重大。
为了高速、优质、低成本地钻好定向井,应从定向钻井的独特性出发优选钻头。
定向造斜段钻井的特点使使用井下马达,钻头转速高,钻头切削齿和钻头外径磨损快钻头寿命缩短。
在定向段钻进过程中,需要钻头能保持住所要求的工具面角度,如果所选的钻头布能提供合适的导向能力,就会获取布到所设计的造斜率或偏离所定的方位。
这样,就会增多纠斜和扭方位的次数或增多更换下部钻具组合的次数。
由于PDC钻头具有无活动件、适应高转速低钻压钻进工况之特点和钻头使用寿命长的优点,因此更适合与动力钻具配合使用,多次现场施工结果表明,动力钻具+PDC钻头钻进方式有利于提高钻井速度,减少起下钻次数、保证钻具安全,取得了动力钻具+牙轮钻头钻进方式无法比拟的技术经济效益。
常规定向井施工主要时通过选择合适的造斜工具(弯接头+动力钻具、单弯动力钻具、双弯动力钻具等)调整侧向力的大小,从而控制造斜率的高低,而同样的侧向力与不同结构的PDC钻头配合对造斜率时有极大的影响的。
在此,我本人认为影响PDC钻头造斜率的钻头结构特征因素主要有以下几点:钻头体长度、钻头冠状形状、钻头保径类型、保径切削齿侧倾角等等。
结构特征因素影响PDC钻头造斜率的机理分析众所周知,定向钻具组合的造斜率时通过下部钻具组合的弯曲形状产生钻头侧向力,使钻头在沿轴线方向钻进的同时侧向切削井壁而产生轨迹偏移的。
钻头轴向钻进和侧向切削的偶合产生一定的造斜率。
在侧向力和钻头轴向钻速一定的情况下,很显然钻头的侧向切削能力越强,钻具组合的造斜率就越高。
钻头体长度对造斜率的影响在如图1-3所示的带弯接头的造斜钻具组合中,依据文献(《短弯外壳导向钻具的造斜率计算》(帅健))中的导向动力钻具造斜率计算公式:式中:k------导向钻具造斜率;a-------弯接头弯角;L1------弯接头肘点至钻头的距离;L2-------弯接头肘点至下部钻具组合上切点的距离;F C-------作用在钻头上的侧向力从公式(1)可知:在其它结构参数一定的情况下,L1、k增大,即选用轴径短的PDC钻头能增加造斜率。
1.2 钻头的冠部形状对造斜率的影响在侧向力FC一定的情况下,钻头和地层地侧向接触面积越小,作用在单位井壁上地侧向力越大、侧切力越强、钻头地造斜率越高。
因此要想获得较高地造斜率,因选用冠部平坦,与地层侧向接触面小地PDC 钻头。
1.3 钻头保径类型对造斜率地影响定向段钻井地特点之一是侧向载荷大,下部钻具组合地弯曲角度越大或弯曲部分离钻头越远所引起地侧向载荷越严重,井下马达高速运转、井底沉积岩屑床、受侧向载荷等因素底综合影响,会使钻头外径很快磨损。
为了克服定向钻头外径的磨损,发展了PDC钻头保径技术,常见的保径方式有在钻头的台肩上镶焊PDC 齿或在钻头的外径上镶焊硬质合金块。
钻头保径长度取决于耐磨性和可导性。
钻头保径长度越长,耐磨性越强,但可导向性差;而保径长度较段则耐磨性较差,而导向性好,要根据地层的可钻性、可研磨性和导向能力来拳衡钻头的保径长度。
保径长的钻头一般比保径段的钻头更稳定,但这种钻头所能获得的最大造斜率小,定向施工人员一般都避免使用。
保径上径向排列PDC切削齿,这种设计制造的钻头具有导向和保径双重功能,比硬质合金块保径的钻头造斜率效果好。
1.4钻头保径切削齿侧倾角对造斜率的影响图1-4为PDC钻头保径切削齿侧倾角示意图,显然径切削齿侧倾角B越小,切削齿吃入岩石的深度越大,钻头的侧向切削能力越强。