复杂曲面叶片的数控加工技术探讨
复杂曲面数控加工技术的研究

一
曲面造 型技 术是 复杂 形状 零件建 模 的基础 和 工具 。 目前 对 曲线 曲面 已经形 成 了一套 较为完 整
般铣 削加 工 凹槽 的走刀 路线 有两 种 :行 切
收 稿 日期 :20 — 8 9 0 8 0—1;修 回 日期 :2 0 — 9 1 080— 1
12 刀具轨 迹的生成 技术 .
好地完成 ,达到较高的稳定性 ,但 曲面加工的质 量 和效率 在很 大程 度上 依赖 于高效 的 刀具路 径生 成 算 法 、加 工 方 案 和 加 工 参 数 的 优 化 选 取 ,所 以 ,对 三轴加 工 的研 究 热点集 中在 加工 特征 识别 和刀具路 径规 划 。多轴 加工在 加工 复杂 形状 零件
20 0 8年 第 6期 ( 16期 ) 总 2
法和环 切法 。在 大多数 情 况下 ,行 切法 的走 刀 路
线 长度 要大 于环切 法 。 由于采 用行 切法 时 刀具 轨
21 数 控编 程与 CN . C的集成
复杂零 件 数控 编程 包 括建 立 几何模 型 到控制
迹 计算 比较 简单 ,在Байду номын сангаас 多 C DC M 系统 中仍 采 A /A
《 一重技术》
复杂 曲面数控加工技术 的研究
李 嵬
富拉尔基 114 ) 6 0 2
(. 1东北特钢集团北满特殊钢有限责任公 司工程师 ,黑龙江
摘要:综述了面向复杂曲面数控加工的关键技术 ,分析 了传统 C M系统针对高速切削的不足,最后 A
探讨 了复 杂 曲 面数 控 加工 技 术 的发 展 趋 势 。
的能力 、质量 和效 率等 诸多方 面有 显著 优势 ,但
复杂曲面零件的加工与测量技术
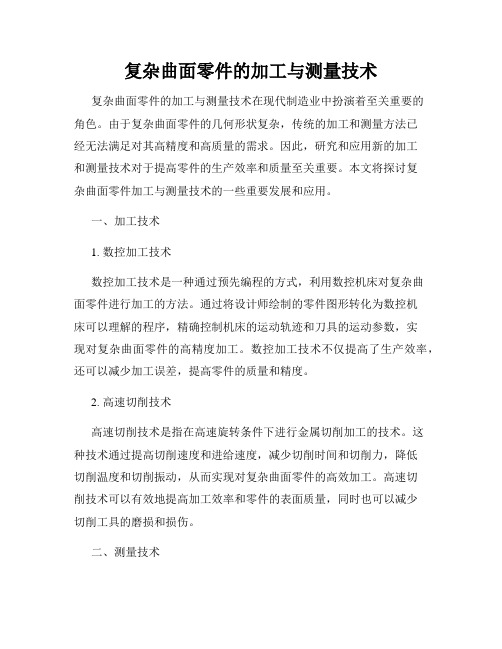
复杂曲面零件的加工与测量技术复杂曲面零件的加工与测量技术在现代制造业中扮演着至关重要的角色。
由于复杂曲面零件的几何形状复杂,传统的加工和测量方法已经无法满足对其高精度和高质量的需求。
因此,研究和应用新的加工和测量技术对于提高零件的生产效率和质量至关重要。
本文将探讨复杂曲面零件加工与测量技术的一些重要发展和应用。
一、加工技术1. 数控加工技术数控加工技术是一种通过预先编程的方式,利用数控机床对复杂曲面零件进行加工的方法。
通过将设计师绘制的零件图形转化为数控机床可以理解的程序,精确控制机床的运动轨迹和刀具的运动参数,实现对复杂曲面零件的高精度加工。
数控加工技术不仅提高了生产效率,还可以减少加工误差,提高零件的质量和精度。
2. 高速切削技术高速切削技术是指在高速旋转条件下进行金属切削加工的技术。
这种技术通过提高切削速度和进给速度,减少切削时间和切削力,降低切削温度和切削振动,从而实现对复杂曲面零件的高效加工。
高速切削技术可以有效地提高加工效率和零件的表面质量,同时也可以减少切削工具的磨损和损伤。
二、测量技术1. 光学测量技术光学测量技术是利用光学原理对复杂曲面零件进行测量的方法。
常用的光学测量技术包括激光测量、视觉测量和相机测量等。
这些技术可以非接触地获取零件的三维形貌和尺寸信息,并通过计算机处理和分析,得到零件的测量结果。
光学测量技术具有高精度、高效率和非接触等优点,广泛应用于复杂曲面零件的测量领域。
2. 接触式测量技术接触式测量技术是指通过接触传感器对复杂曲面零件进行测量的方法。
常用的接触式测量技术包括坐标测量、形状测量和表面测量等。
这些技术通过在零件表面接触传感器进行测量,获取零件的形状、尺寸和表面粗糙度等信息。
接触式测量技术具有高精度和可靠性的特点,适用于对复杂曲面零件的几何形状和尺寸进行测量。
三、加工与测量技术的应用1. 航空航天工业在航空航天工业中,复杂曲面零件的加工和测量技术对飞机和宇宙飞船的制造具有重要意义。
复杂曲面数控加工论文

复杂曲面数控加工论文近年来,随着工业自动化的推进,数控加工技术在工业制造领域中得到了广泛的应用。
对于复杂曲面件的加工,数控加工技术可以更加精确和高效地实现。
因此,复杂曲面数控加工技术的研究一直受到人们的关注。
本篇文档将阐述复杂曲面数控加工的现状和发展趋势,并介绍一篇有关复杂曲面数控加工的论文。
一、复杂曲面数控加工的现状和发展趋势复杂曲面数控加工,又称为高精度数控加工,是一种可以在三维空间中精确和高效地加工曲面件的技术。
随着科技的不断发展和人们对产品精度的要求不断提高,复杂曲面数控加工已经逐渐成为了现代工业生产中不可或缺的一部分。
在数控加工技术的发展历程中,复杂曲面数控加工无疑是重要的一环。
目前,复杂曲面数控加工已经应用于飞机制造、汽车制造、医疗器械和电子设备等领域。
与传统的手工制造和机械加工相比,复杂曲面数控加工具有精度高、重复性好、生产效率高等优点。
未来,复杂曲面数控加工技术还将继续在工业制造领域中发挥重要作用。
在未来的数控加工技术发展中,人工智能和机器学习等技术的应用将有助于进一步提高复杂曲面数控加工的精度和生产效率。
二、复杂曲面数控加工论文的介绍在对复杂曲面数控加工技术的研究中,有一篇值得关注的论文,它是中国科学院合肥物质科学研究院的苏宗安、陶亚民、张学军等人于2017年发表的《一种基于耗散耦合的五轴数控机床轮廓误差分析和补偿方法》。
该论文利用了一种基于耗散耦合的五轴数控机床,并通过在五轴加工过程中加入动态误差来模拟加工过程的实际情况。
利用误差传递与补偿技术对五轴数控加工中的轮廓误差进行了分析和优化处理,通过建立轮廓误差传递模型和优化主轴转速、进给速度和刀具半径等因素,成功实现了高精度的复杂曲面加工。
这篇论文具有一定的实用价值和理论意义,对于复杂曲面数控加工的研究和应用具有一定的指导作用。
同时,该论文也对五轴数控加工机床的研究和发展提出了新的思路和方法。
三、总结复杂曲面数控加工技术的研究在近年来有了长足的发展,未来也将继续得到推进和应用,研究人员需要不断地探索并创新加工技术,将其应用于更广泛的领域。
数控加工中心五轴复杂曲面零件加工技术研究及加工精度控制

数控加工中心五轴复杂曲面零件加工技术研究及加工精度控制摘要:随着社会经济的不断发展,各行各业对产品制造精度的要求越来越高。
而数控加工中心是一种高效率、高精度、多功能的加工设备,已成为现代制造业必不可少的工具。
为了满足现代制造业对于高精度、高效率及多样化的加工需求,数控加工中心五轴复杂曲面零件加工技术得到广泛关注。
本文研究该领域中的加工过程和加工精度控制,并提出一种基于机器学习的方法用于优化加工参数,显著地提高了加工效率和精度。
关键词:数控加工中心;五轴复杂曲面;加工技术;精度控制;机器学习一、数控加工中心和五轴复杂曲面零件的特点和加工难点数控加工中心和五轴复杂曲面零件是现代制造业中的重要设备和关键部件。
数控加工中心以其高效、高精度和多功能等特点,成为现代制造业不可或缺的加工工具,而五轴复杂曲面零件则由于其异常复杂的形状和表面几何变化,难以通过常规方式进行加工,因此充满挑战性,也因此引起了广泛的关注。
在加工过程中,数控加工中心一般采用立式刀库,能够根据需要调整角度和位置,实现多种加工操作。
五轴复杂曲面零件的特点则在于它们所具有的极端复杂的几何形状和表面设计,包括向外突出的棱和边、开口孔和内部各种壁面,而这些都需要经过精密的加工才能达到标准。
然而,在面对加工复杂曲面零件时,存在着以下几大加工难点:几何参数测量:针对五轴复杂曲面零件,必须完全了解这样一个元件形状中的复杂性质并产生命令来摆放该物体进行加工;工具路径规划:为了处理复杂曲面上的不同加工区域,需要寻找合适的、高效率的轨迹以用来掌控工件在加工期间机器终端上的运动;剪力和热源问题:五轴复杂曲面零件的特殊形态给剪力和热源性能带来了挑战。
较大的压力会导致断屑、撕裂,并影响表面质量;同时温度过高也会导致损坏。
加工精度控制:由于其表面几何变化比较大,需要高精度的控制方案才能够确保正常完成任务。
二、数控加工中心和五轴复杂曲面零件在现代制造业中的重要性数控加工中心和五轴复杂曲面零件在现代制造业中具有极为重要的地位。
复杂曲面零件数控加工方法研究
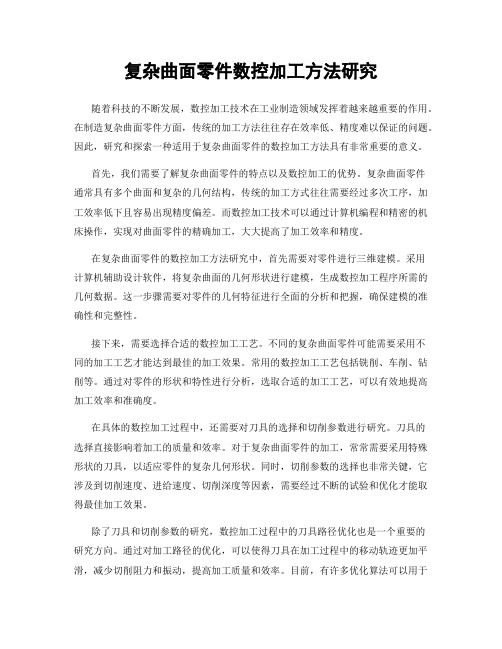
复杂曲面零件数控加工方法研究随着科技的不断发展,数控加工技术在工业制造领域发挥着越来越重要的作用。
在制造复杂曲面零件方面,传统的加工方法往往存在效率低、精度难以保证的问题。
因此,研究和探索一种适用于复杂曲面零件的数控加工方法具有非常重要的意义。
首先,我们需要了解复杂曲面零件的特点以及数控加工的优势。
复杂曲面零件通常具有多个曲面和复杂的几何结构,传统的加工方式往往需要经过多次工序,加工效率低下且容易出现精度偏差。
而数控加工技术可以通过计算机编程和精密的机床操作,实现对曲面零件的精确加工,大大提高了加工效率和精度。
在复杂曲面零件的数控加工方法研究中,首先需要对零件进行三维建模。
采用计算机辅助设计软件,将复杂曲面的几何形状进行建模,生成数控加工程序所需的几何数据。
这一步骤需要对零件的几何特征进行全面的分析和把握,确保建模的准确性和完整性。
接下来,需要选择合适的数控加工工艺。
不同的复杂曲面零件可能需要采用不同的加工工艺才能达到最佳的加工效果。
常用的数控加工工艺包括铣削、车削、钻削等。
通过对零件的形状和特性进行分析,选取合适的加工工艺,可以有效地提高加工效率和准确度。
在具体的数控加工过程中,还需要对刀具的选择和切削参数进行研究。
刀具的选择直接影响着加工的质量和效率。
对于复杂曲面零件的加工,常常需要采用特殊形状的刀具,以适应零件的复杂几何形状。
同时,切削参数的选择也非常关键,它涉及到切削速度、进给速度、切削深度等因素,需要经过不断的试验和优化才能取得最佳加工效果。
除了刀具和切削参数的研究,数控加工过程中的刀具路径优化也是一个重要的研究方向。
通过对加工路径的优化,可以使得刀具在加工过程中的移动轨迹更加平滑,减少切削阻力和振动,提高加工质量和效率。
目前,有许多优化算法可以用于刀具路径的自动生成,如遗传算法、模拟退火算法等。
通过这些算法的应用,可以实现自动化的刀具路径规划,提高数控加工的效率和精度。
总结起来,复杂曲面零件数控加工方法的研究包括三维建模、数控加工工艺的选择、刀具和切削参数的研究,以及刀具路径优化等多个方面。
复杂曲面零件的数控加工

复杂曲面零件的数控加工近年来,随着科技的发展和制造业的现代化需求,数控加工在零件制造领域扮演着越来越重要的角色。
对于复杂曲面零件的加工来说,传统的加工方法已经无法满足精度和效率的要求。
而数控加工凭借其高精度、高效率以及灵活性的特点,成为了复杂曲面零件加工的一种重要选择。
在数控加工中,复杂曲面零件的加工是一项技术要求相对较高的工作,需要通过先进的数控机床和相应的刀具设备来完成。
传统的机械加工方法对于复杂曲面零件的制造过程中会出现很多问题,如加工难度大、制造周期长、精度难以保证等。
而数控加工的出现,使得这些问题得以解决。
首先,数控加工具有高精度的特点。
在复杂曲面零件的加工过程中,精度往往是一个非常重要的指标。
与传统的机械加工不同,数控加工通过数控机床控制工具刀具的运动轨迹,能够精确地进行加工,保证了零件的几何形状和尺寸的精度。
这对于一些对精度要求较高的零件来说,尤为重要。
其次,数控加工具有高效率的特点。
复杂曲面零件的加工往往需要进行多个加工步骤,传统的机械加工方式需要不断地更换刀具、调整机床等,非常繁琐耗时。
而数控加工可以通过事先编写好的数控程序来进行自动化加工,减少了操作工人的工作量,大大提高了加工效率。
同时,数控加工还可以进行多任务加工,即同时进行多个刀具进行加工,使得整个加工过程更加快速高效。
此外,数控加工还具有灵活性的特点。
在复杂曲面零件的加工过程中,往往需要根据零件的形状和要求进行不同的加工工艺。
传统的机械加工方法可能需要重新设计和制造加工装备,而数控加工则能够通过改变数控程序和参数的方式来适应不同的加工要求,具有更高的灵活性。
然而,复杂曲面零件的数控加工也存在一些挑战和难点。
首先,对于复杂曲面的加工轨迹和刀具路径的规划是一项复杂的技术问题。
在数控加工中,需要通过数学建模和算法来确定零件的加工轨迹,保证加工的完整性和精度。
其次,数控加工需要对加工过程进行全程监控和调试,以及对刀具磨损、机床误差等进行实时检测和修正。
复杂曲面数控加工技术及其应用研究_1
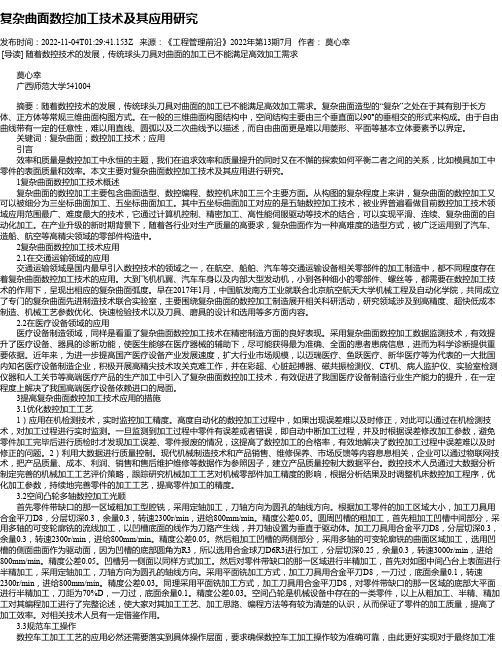
复杂曲面数控加工技术及其应用研究发布时间:2022-11-04T01:29:41.153Z 来源:《工程管理前沿》2022年第13期7月作者:莫心幸[导读] 随着数控技术的发展,传统球头刀具对曲面的加工已不能满足高效加工需求莫心幸广西师范大学541004摘要:随着数控技术的发展,传统球头刀具对曲面的加工已不能满足高效加工需求。
复杂曲面造型的“复杂”之处在于其有别于长方体、正方体等常规三维曲面构图方式。
在一般的三维曲面构图结构中,空间结构主要由三个垂直面以90°的垂相交的形式来构成。
由于自由曲线带有一定的任意性,难以用直线、圆弧以及二次曲线予以描述,而自由曲面更是难以用菱形、平面等基本立体要素予以界定。
关键词:复杂曲面;数控加工技术;应用引言效率和质量是数控加工中永恒的主题,我们在追求效率和质量提升的同时又在不懈的探索如何平衡二者之间的关系,比如模具加工中零件的表面质量和效率。
本文主要对复杂曲面数控加工技术及其应用进行研究。
1复杂曲面数控加工技术概述复杂曲面的数控加工主要包含曲面造型、数控编程、数控机床加工三个主要方面。
从构图的复杂程度上来讲,复杂曲面的数控加工又可以被细分为三坐标曲面加工、五坐标曲面加工。
其中五坐标曲面加工对应的是五轴数控加工技术,被业界普遍看做目前数控加工技术领域应用范围最广、难度最大的技术,它通过计算机控制、精密加工、高性能伺服驱动等技术的结合,可以实现平滑、连续、复杂曲面的自动化加工。
在产业升级的新时期背景下,随着各行业对生产质量的高要求,复杂曲面作为一种高难度的造型方式,被广泛运用到了汽车、造船、航空等高精尖领域的零部件构造中。
2复杂曲面数控加工技术应用2.1在交通运输领域的应用交通运输领域是国内最早引入数控技术的领域之一,在航空、船舶、汽车等交通运输设备相关零部件的加工制造中,都不同程度存在着复杂曲面数控加工技术的应用。
大到飞机机翼、汽车车身以及内部大型发动机,小到各种细小的零部件、螺丝等,都需要在数控加工技术的作用下,呈现出相应的复杂曲面弧度。
复杂曲面机械零件的数控加工优化研究

复杂曲面机械零件的数控加工优化研究1. 引言复杂曲面机械零件的数控加工是现代制造技术领域的关键问题之一。
在机械零件的加工过程中,通过合理的数控加工优化研究,可以提高加工效率、降低成本、提高零件质量。
本文将探讨复杂曲面机械零件的数控加工优化问题,并提出相应的解决策略。
2. 数控加工的挑战与需求复杂曲面机械零件具有形状复杂、加工难度大、加工工艺复杂等特点,使得数控加工面临一系列挑战。
首先,复杂曲面的数学描述与数控机床的坐标系描述存在差异,需要进行坐标系变换和数学模型转换。
其次,复杂曲面的加工路径不规则,需要合理设计加工路径,减少加工时间和误差。
此外,由于复杂的曲面结构,加工过程中容易出现切削震动、刀具磨损等问题,也需要进行相应的优化处理。
3. 数控加工优化的策略为了解决复杂曲面机械零件加工过程中的问题,需要采取针对性的数控加工优化策略。
以下是几个常用的策略:3.1 五轴加工技术五轴加工技术是一种常用的复杂曲面机械零件数控加工优化策略。
通过增加刀具在不同方向上的旋转能力,可以减少加工路径,提高加工效率,减少误差。
这种技术能够处理复杂曲面的多个曲率变化,提高加工精度和表面质量。
3.2 加工路径优化加工路径优化是为了减少加工时间和误差,提高加工效率的一项重要技术。
通过合理规划加工路径,减少刀具在曲面上的移动距离,可以大大提高加工效率。
同时,还可以通过优化刀具进给速度、切削深度等参数,减少切削震动等问题。
3.3 刀具轨迹优化复杂曲面加工过程中,刀具的接触点会发生变化,而曲面的局部特性也会影响刀具的入射角度。
因此,刀具轨迹的优化是提高加工精度和表面质量的关键。
通过合理设计刀具轨迹,保证刀具与曲面的最佳接触,可以实现高质量的加工效果。
3.4 切削参数优化切削参数的优化对于复杂曲面机械零件数控加工至关重要。
通过合理选择切削速度、进给速度、切削深度等参数,可以最大程度地减少切削震动、刀具磨损等问题,提高加工质量。
4. 数控加工优化实例分析以某复杂曲面机械零件的数控加工为例进行分析。
浅谈基于UG的复杂曲面叶轮三维造型及五轴数控加工技术

叶轮数控加工仿真研究【 J 】 . 陕 西 国防 工
业 职 业技 术学 院 学 报 , 2 0 1 l , 2 1 ( 2 ) : 4 5 -
47.
工程序都应经过分 度和旋转 , 且 在 轮 毂 和
可 能存在 一些不需 要的拐点 , 即 出 现 不 光 叶 片 没 有 全 部 加 工 完 时 , 不应 进 入 下 一 个 【 4 】阎长 罡 , 贾 国高 . 基于 UG N X 4 . O 的整体
行 于 气 流 通 道 的 方 向进 行 走 刀 。 具 体 加 工
比较 完 美 地 完 成 对 整 体 叶 轮 的 三 维 造 型 。 应 用 uG软 件 对 整 体 叶 轮 进 行 五 轴 加 工 的
/C AM 软 件 , 在 的 中间位置设 置开槽加 工槽 , 铣 刀应 沿 平 但 它 作 为 一 款 通 用 的 CAD
迹 生 成研 究 【 D 】 . 哈 尔 滨 工程 大 学 硕士 学 位论文 , 2 0 l 2 .
【 3 】李俊 涛 , 吴 让利 . 基于 UG N X 6 . 0 的 整体
.
维造 型工作( 如 图2 所示) 。 2 . 5 光顺 曲线 实 际工作 中 , 生 成 叶 片 的 曲线 和 曲 面
工 业 技 术
建议采用 第二种方式 。 2 . 4 建立 整体 叶轮 在 完成 单个叶 片和 轮毂的 造型后 , 我
们 要 建 立 整 个 叶轮 的 CAD 模型 , 建 立 步 骤 如下: ( 1 ) 因 为 叶片 是 沿 圆周 均布 的 , 所以 需 要 根 据 叶 片 的 数 量 确 定 叶 片 沿 圆 周分 布 的
3 叶轮 的五 轴数控加工流程
( 1 ) 锻压毛坯 : 毛 坯 采 用 高 强度 的锻 压
复杂曲面数控加工技术研究
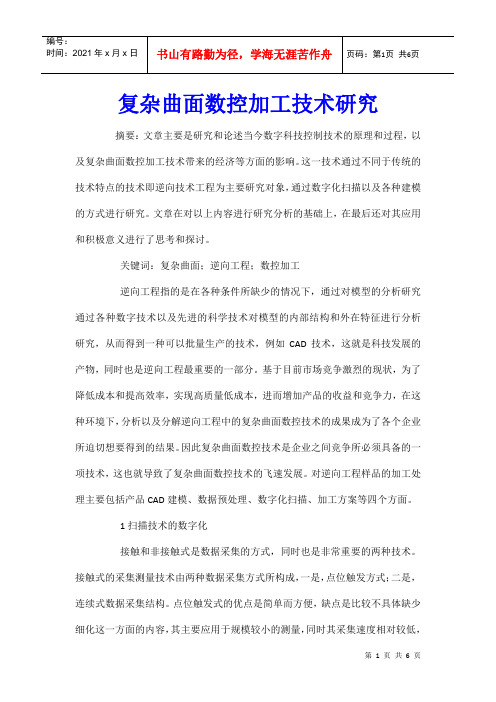
复杂曲面数控加工技术研究摘要:文章主要是研究和论述当今数字科技控制技术的原理和过程,以及复杂曲面数控加工技术带来的经济等方面的影响。
这一技术通过不同于传统的技术特点的技术即逆向技术工程为主要研究对象,通过数字化扫描以及各种建模的方式进行研究。
文章在对以上内容进行研究分析的基础上,在最后还对其应用和积极意义进行了思考和探讨。
关键词:复杂曲面;逆向工程;数控加工逆向工程指的是在各种条件所缺少的情况下,通过对模型的分析研究通过各种数字技术以及先进的科学技术对模型的内部结构和外在特征进行分析研究,从而得到一种可以批量生产的技术,例如CAD技术,这就是科技发展的产物,同时也是逆向工程最重要的一部分。
基于目前市场竞争激烈的现状,为了降低成本和提高效率,实现高质量低成本,进而增加产品的收益和竞争力,在这种环境下,分析以及分解逆向工程中的复杂曲面数控技术的成果成为了各个企业所迫切想要得到的结果。
因此复杂曲面数控技术是企业之间竞争所必须具备的一项技术,这也就导致了复杂曲面数控技术的飞速发展。
对逆向工程样品的加工处理主要包括产品CAD建模、数据预处理、数字化扫描、加工方案等四个方面。
1扫描技术的数字化接触和非接触式是数据采集的方式,同时也是非常重要的两种技术。
接触式的采集测量技术由两种数据采集方式所构成,一是,点位触发方式;二是,连续式数据采集结构。
点位触发式的优点是简单而方便,缺点是比较不具体缺少细化这一方面的内容,其主要应用于规模较小的测量,同时其采集速度相对较低,一般只用于零件表面形状及规格的测量,数字化成都相对较低。
与触发式数据采集相比较,精细而准确是连续式数据采集的最大的优点,如扫描测量仪和监控测量仪,由于其具有较快和较精准的采集速度,所以满足绝大部分大规模数据采集的要求。
接触式测量方法虽然成本较低,操作简单,精度较高,抗干扰能力较强,但是由于测量时接触压力的存在,这就导致了一些质地柔软体积较小的的零件测量存在较大的误差。
复杂曲面数控加工探讨
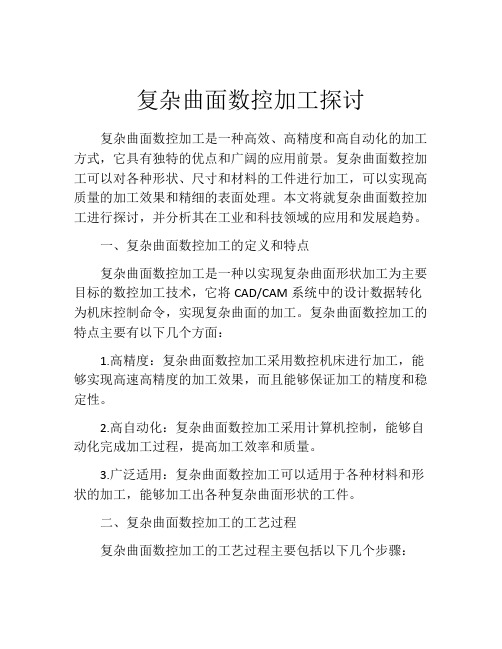
复杂曲面数控加工探讨复杂曲面数控加工是一种高效、高精度和高自动化的加工方式,它具有独特的优点和广阔的应用前景。
复杂曲面数控加工可以对各种形状、尺寸和材料的工件进行加工,可以实现高质量的加工效果和精细的表面处理。
本文将就复杂曲面数控加工进行探讨,并分析其在工业和科技领域的应用和发展趋势。
一、复杂曲面数控加工的定义和特点复杂曲面数控加工是一种以实现复杂曲面形状加工为主要目标的数控加工技术,它将CAD/CAM系统中的设计数据转化为机床控制命令,实现复杂曲面的加工。
复杂曲面数控加工的特点主要有以下几个方面:1.高精度:复杂曲面数控加工采用数控机床进行加工,能够实现高速高精度的加工效果,而且能够保证加工的精度和稳定性。
2.高自动化:复杂曲面数控加工采用计算机控制,能够自动化完成加工过程,提高加工效率和质量。
3.广泛适用:复杂曲面数控加工可以适用于各种材料和形状的加工,能够加工出各种复杂曲面形状的工件。
二、复杂曲面数控加工的工艺过程复杂曲面数控加工的工艺过程主要包括以下几个步骤:1.设计模型:采用CAD软件设计出要加工的模型,并进行验证,确保设计的准确性和可行性。
2.程序编写:根据设计模型,通过CAM软件编写加工程序,设置加工参数和路径,生成机床控制程序。
3.机床安全:机床运行前必须进行检查,确保各部件的安装和调整,保障机床运转的安全性和稳定性。
4.开机调试:开机前,进行刀具和工件的装夹,安装和调整刀具和工件等,根据加工程序进行机床调试和检测。
5.自动加工:机床运行后,进行自动加工,根据加工程序进行工件加工,控制刀具的运动、加工深度和切削速度等参数。
6.加工监测:在加工过程中,对工件尺寸、表面粗糙度等进行监测和检测,根据检测结果进行刀具调整和工艺优化。
7.加工完成:完成加工后,对工件进行检验和验证,确认加工质量和精度是否符合要求。
三、复杂曲面数控加工的应用领域复杂曲面数控加工在工业和科技领域具有广泛的应用,主要包括以下几个领域:1.航空航天:航天器和大型飞机等航空器件通常需要采用复杂曲面结构,而复杂曲面数控加工能够满足该领域的加工需求。
精密复杂曲面零件多轴数控加工技术研究

精密复杂曲面零件多轴数控加工技术研究摘要:随着时代发展的推动,各行各业的发展与改革也在不断向前推进,在现代工业领域,多轴数控加工技术已经成为了该领域的标志性加工技术,在我国的运载工具、国防、能源、航空航天、动力等领域的关键零部件加工中,多轴数控加工技术均发挥着重要的作用。
而伴随着各个领域对于装备性能的要求在不断提升,精密复杂曲面零件随之产生,该零件本身具备性能指标要求苛刻、加工难度大等特点,关于精密复杂曲面零件的加工,已经从原有的形位精度要求,转变成为性能指标与形位并重的高性能加工要求,这种转变的产生,给传统精密复杂曲面零件技术的革新带来了契机。
本文将针对精密复杂曲面零件的多轴数控加工技术进行分析与研究。
关键词:精密复杂曲面零件;多轴数控加工;技术研究随着我国综合国力的增强以及科学技术水平的不断提升,我国的制造业领域也在不断发展和拓展,在这其中,一批精密复杂曲面零件不断涌现出来,例如,航空发动机的叶片和机匣、大型航空运载工具的天线罩以及精密壳体等都属于精密复杂曲面零件。
因为此类零件的超常规使役环境,在进行制造的过程中,主要制造要求就要以气动特性、透波、导流以及抗疲劳性等的性能指标为主。
而为了进一步满足相关性能指标的要求,该类软件的结构以及形状发展的愈发复杂,一般具有极端大尺度比以及薄壁悬挂等显著特点。
1多轴数控加工的相关概述数控加工的过程是经过模型曲面上的加工路径直接进行驱动的,所以,高效的加工路径设计方法是保证零件表面形成精度以及加工效率提升的关键所在。
但是,传统的路径规划方法具有拘泥于几何层面进行离散调整以及逐点进行路径设计的特点,这种特点的具备从切割特性层面以及运动学角度考虑,能够将加工路径拓扑成几何形状的方法较少,无法将曲面几何的物理特性进行兼顾,也难以实现关于路径的整体性调控,十分不利于加工生产工作的进行。
在进行复杂曲面的数控加工过程中,运动规划也是非常重要的,特别是在复杂曲面零件的高精度高速加工过程中,关于适应性进给率定制加工技术的使用,是保证加工效率、保证加工精度的有效措施[1]。
复杂曲面高效加工的关键技术方法分析.docx
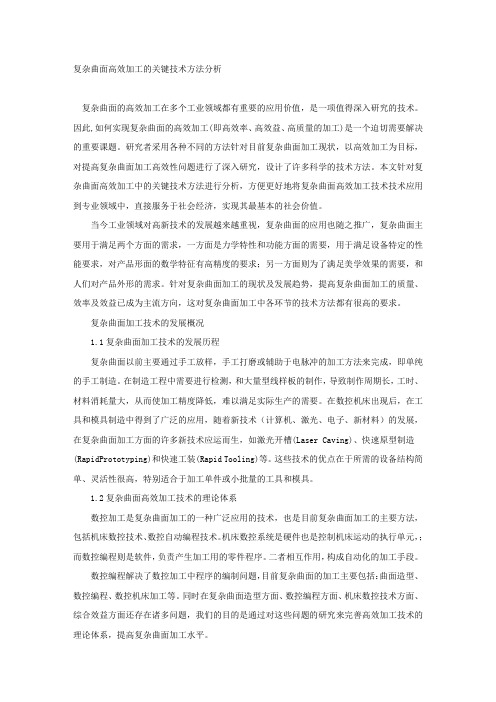
复杂曲面高效加工的关键技术方法分析复杂曲面的高效加工在多个工业领域都有重要的应用价值,是一项值得深入研究的技术。
因此,如何实现复杂曲面的高效加工(即高效率、高效益、高质量的加工)是一个迫切需要解决的重要课题。
研究者采用各种不同的方法针对目前复杂曲面加工现状,以高效加工为目标,对提高复杂曲面加工高效性问题进行了深入研究,设计了许多科学的技术方法。
本文针对复杂曲面高效加工中的关键技术方法进行分析,方便更好地将复杂曲面高效加工技术技术应用到专业领域中,直接服务于社会经济,实现其最基本的社会价值。
当今工业领域对高新技术的发展越来越重视,复杂曲面的应用也随之推广,复杂曲面主要用于满足两个方面的需求,一方面是力学特性和功能方面的需要,用于满足设备特定的性能要求,对产品形面的数学特征有高精度的要求;另一方面则为了满足美学效果的需要,和人们对产品外形的需求。
针对复杂曲面加工的现状及发展趋势,提高复杂曲面加工的质量、效率及效益已成为主流方向,这对复杂曲面加工中各环节的技术方法都有很高的要求。
复杂曲面加工技术的发展概况1.1复杂曲面加工技术的发展历程复杂曲面以前主要通过手工放样,手工打磨或辅助于电脉冲的加工方法来完成,即单纯的手工制造。
在制造工程中需要进行检测,和大量型线样板的制作,导致制作周期长,工时、材料消耗量大,从而使加工精度降低,难以满足实际生产的需要。
在数控机床出现后,在工具和模具制造中得到了广泛的应用,随着新技术(计算机、激光、电子、新材料)的发展,在复杂曲面加工方面的许多新技术应运而生,如激光开槽(Laser Caving)、快速原型制造(RapidPrototyping)和快速工装(Rapid Tooling)等。
这些技术的优点在于所需的设备结构简单、灵活性很高,特别适合于加工单件或小批量的工具和模具。
1.2复杂曲面高效加工技术的理论体系数控加工是复杂曲面加工的一种广泛应用的技术,也是目前复杂曲面加工的主要方法,包括机床数控技术、数控自动编程技术。
最新复杂曲面的加工方法
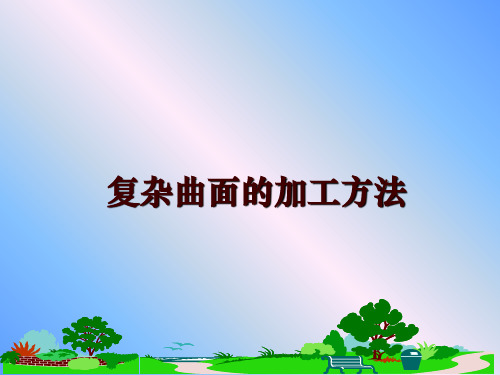
路径截面线法
在走刀过程中,将刀具与被加工曲面的CC点(接触点)约 束在另一组曲面内,即用一组约束曲面与被加工曲面的截交线 作为刀具接触点路径来生成刀具轨迹。
常用的约束面有平面法
直接用一组约束曲面与被加工曲面的刀具偏置面的截交线 作为刀具轨迹。
自由曲线是指不能用直线、圆弧和二次曲线描述的任意形 状的曲线。
自由曲面是指不能用基本立体要素(如棱柱、棱锥、球、 有界平面等)描述的呈自然形状的曲面。
2.1.2曲面造型方法
复杂曲面造型常用的方法主要有Coons曲面、Bezier曲面 和B样条曲面三类。
由于NURBS曲面方便灵活,具有强大的形状描述能力, 被国际标准化IS0组织在STEP(工业产口数据交换)标准中定义 为描述产品形状的主要数学方法。
常见的刀轴控制方式:
1.垂直于表面方式 即刀轴始终平行于个切削点处的表面法矢,适用于大型平
坦无干涉凸曲面端铣加工。 2.平行于表面方式
即刀具轴线或母线始终处于各切削点的切平面内,对应方 式一般为侧铣。这种方式的重要应用时直纹面的加工。 3.倾斜于表面方式
由刀轴矢量在局部坐标系中与坐标平面所成的两个角度 α 和γ定义。其中,n为切削点处的单位法矢,a切削点处沿进给 方向的切矢,v=n x a,( a, v, n )为切削点处的局部坐标系。 α为前倾角;γ为倾斜角
曲面加工的刀具轨迹理论上是由刀具与曲面的啮合关系所 确定的复杂曲线,由于CNC插补能力的限制,该轨迹只能用一 系列小直线段进行插补。
走刀步长(逼近线段)
曲面加工刀具轨迹步长算法
1.等步长法: 包括等参数步长和等距离步长,为满足加工精度,通常参
数步长取值偏于保守,所以计算点位信息多。 2.步长筛选法
数控机床的仿形加工与复杂曲面加工技术

数控机床的仿形加工与复杂曲面加工技术数控机床是当今制造业中不可或缺的设备之一。
它以其高精度、高效率的加工能力,广泛应用于各个领域。
在数控机床的应用中,仿形加工和复杂曲面加工技术是两个重要的方面。
一、仿形加工技术仿形加工技术是一种通过模板或样品来制造相同形状的工件的方法。
在数控机床中,仿形加工技术通过将样品或模板放置在机床上,通过传感器感知样品或模板的形状,然后将这些信息输入到数控系统中,控制机床进行相应的加工操作。
仿形加工技术在一些特殊的工件加工中非常有用。
例如,在一些复杂形状的零件加工中,传统的加工方法可能无法满足要求,而仿形加工技术可以通过样品或模板来实现精确的加工。
此外,仿形加工技术还可以用于一些特殊材料的加工,如陶瓷、玻璃等。
二、复杂曲面加工技术复杂曲面加工技术是数控机床中另一个重要的技术。
它主要用于加工具有复杂曲面形状的工件,如汽车零部件、飞机零部件等。
复杂曲面加工技术通过数控系统控制机床进行多轴联动加工,以实现复杂曲面的加工。
复杂曲面加工技术的实现需要数控系统具备强大的计算和控制能力。
它需要根据工件的曲面形状,计算出每个刀具的加工路径和切削参数,然后通过数控系统控制机床进行加工。
这种技术的应用可以大大提高工件的加工精度和效率。
三、仿形加工与复杂曲面加工的结合在实际应用中,仿形加工技术和复杂曲面加工技术经常会结合在一起使用。
例如,在一些汽车零部件的加工中,可能需要同时考虑工件的复杂曲面形状和与其他零部件的配合要求。
在这种情况下,可以使用仿形加工技术来制造配合零件的样品或模板,并通过复杂曲面加工技术来实现工件的加工。
仿形加工与复杂曲面加工的结合可以提高加工的精度和效率。
通过仿形加工技术,可以准确地制造出与样品或模板相同形状的工件;而通过复杂曲面加工技术,可以实现工件的复杂曲面加工。
这种结合不仅可以满足工件的形状要求,还可以提高加工的效率,减少人工操作的难度。
总结:数控机床的仿形加工与复杂曲面加工技术在现代制造业中起着重要的作用。
浅谈基于UG的复杂曲面叶轮三维造型及五轴数控加工技术

浅谈基于UG的复杂曲面叶轮三维造型及五轴数控加工技术摘要:整体叶轮是能源动力、航空航天、石油化工等行业广泛使用的关键零件,也是一类典型的难加工零件。
本文以UG软件为背景,提出了一套从叶轮造型到应用五轴数控加工技术对其进行加工的数控加工方案,希望对叶轮的设计制造工作能够有所借鉴。
关键词:叶轮复杂曲面三维造型五轴数控加工叶轮是由复杂空间曲面构成的非常有代表性的典型零件,具有结构复杂、种类繁多、设计周期长、加工工作量大的特点,它可以被认作是很多机械的“心脏”,其造型质量和加工方案的选取将会对机械的使用性能和效率造成直接影响。
UG软件是西门子公司旗下的一个集CAD/CAM为一体的三维机械设计平台,它对曲面曲线的造型有着一套成熟完整的方法和理论体系,并且因为其还具有功能强大的加工制造模块,能够对已建立的叶轮CAD模型作加工工艺分析,并通过后处理程序直接生成加工代码,是同类软件中的佼佼者。
因此,本文采用UG 平台对叶轮的造型及加工技术进行分析。
1 叶轮的CAD/CAM系统方案为了保证整体叶轮的强度,使加工得到的叶面曲面误差较小,宜采用整体铣削加工的方法。
整体铣削加工的步骤为:(1)将锻压好的毛坯件车削成叶轮回转体的基本形状。
(2)用五轴数控加工中心在毛坯上一次性完成对轮毂和叶片的加工。
近年来,伴随着CAD/CAE/CAM一体化技术的发展以及五轴数控加工设备的普及,传统的依靠手工对叶轮进行加工的方法已经遭到淘汰,而采用CAD/CAM系统的叶轮整体加工方案已经得到了广泛地应用。
2 叶轮的三维造型2.1 叶片数据的获取现阶段获取叶片数据的方法主包括测量现成叶片和理论计算两种类型。
前者主要应用于逆向工程领域,一般是利用CMM(三坐标测量机)或激光扫描仪对现成叶轮进行测量,生成iges等通用格式的数据文件,然后将这些文件导入UG中进行模型建立;后者主要通过有限元分析和流体力学的原理来完成对叶片数据的计算。
本文的叶片数据是采用理论计算得到的。
复杂曲面零件数控加工的关键问题——解读《复杂曲面零件五轴数控加工理论与技术》

1五轴数控加工简介复杂曲面零件作为数字化制造的主要研究对象之一,在航空、航天、能源和国防等领域中有着广泛的应用,其制造水平代表着一个国家制造业的核心竞争力。
复杂曲面零件往往具有形状和结构复杂、质量要求高等难点,是五轴数控加工的典型研究对象。
当前,复杂曲面零件主要包括轮盘类零件、航空结构件以及火箭贮箱壁板等,如图1所示。
轮盘类零件是发动机完成对气体的压缩和膨胀的关键部件,主要包括整体叶盘类零件和叶片类零件。
整体叶盘类零件的叶展长、叶片薄且扭曲度大,叶片间的通道深且窄,开敞性差,零件材料多为钛合金、高温合金等难加工材料,因此零件加工制造困难。
叶片是一种特殊的零件,数量多、形状复杂、要求高、加工难度大且故障多发,一图1复杂曲面零件直以来都是各发动机厂生产的关键。
航空整体结构件由整块大型毛坯直接加工而成,在刚度、抗疲劳强度以及各种失稳临界值等方面均比铆接结构胜出一筹,但由于其具有尺寸大、材料去除率大、结构复杂、刚性差等缺点,因此加工后会产生弯扭组合等加工变形。
随着新一代大型运载火箭设计要求的提高,为保证火箭的可靠性,并减轻结构质量,提高有效载荷,对火箭贮箱壁板网格壁厚精度和根部圆弧过渡尺寸都提出了更严格的要求。
五轴数控铣削加工具有高可达性、高效率和高精度等优势,是加工大型与异型复杂零件的重要手段。
五轴数控机床在3个平动轴的基础上增加了2个转动轴,不但可以使刀具相对于工件的位置任意可控,而且刀具轴线相对于工件的方向也在一定的范围内任意可控。
五轴数控加工的主要优势包括:①提高刀具可达性。
通过改变刀具方向可以提高刀具可达性,实现叶轮、叶片和螺旋桨等复杂曲面零件的数控加工。
②缩短刀具悬伸长度。
通过选择合理刀具方向可以在避开干涉的同时使用更短的刀具,提高铣削系统的刚度,改善数控加工中的动态特性,提高加工效率和加工质量。
③可用高效加工刀具。
通过调整刀轴方向能够更好地匹配刀具与工件曲面,增加有效切宽,实现零件的高效加工。
基于UG NX的复杂曲面叶轮五轴数控加工技术

基于UG NX的复杂曲面叶轮五轴数控加工技术前言作为动力机械的关键部件,整体式叶轮广泛应用于航天航空等领域,其加工技术一直是制造业中的一个重要课题。
从整体式叶轮的几何结构和工艺过程可以看出[1],加工整体式叶轮时加工轨迹规划的约束条件比较多,相邻的叶片之间空间较小,加工时极易产生碰撞干涉,自动生成无干涉加工轨迹比较困难。
因此在加工叶轮的过程中不仅要保证叶片表面的加工轨迹能够满足几何准确性的要求,而且由于叶片的厚度有所限制,所以还要在实际加工中注意轨迹规划以保持加工的质量[1]。
目前,我国大多数生产也轮的厂家多数采用国外大型CAD/CAM软件,如UG NX、CATIA、MasterCAM等。
本文选用目前流行且功能强大的UG NX3.0对复杂曲面整体叶轮进行加工轨迹规划。
1 整体叶轮数控加工工艺流程规划根据叶轮的几何结构特征和使用要求(如图1),其基本加工工艺流程为:1)在锻压铝材上车削加工回转体的基本形状;2)开粗加工流道部分;3)半精加工流道部分;4)叶片精加工;5)对倒圆部分进行清根。
图1. 叶轮的基本几何特征1.1 刀具的选择为提高加工效率,在进行流道开粗和流道半精加工过程中尽可能选用大直径球头铣刀,但是也要注意使刀具直径2R1min小于两叶片间最小距离L1min,L1min的大小可以根据UG NX 3.0软件的分析(Analysis)功能测得。
R1min<L1min/2在叶片精加工过程中,应在保证不过切的前提下尽可能选择大直径球头刀,即保证刀具半径R2min大于流道和叶片相接部分的最大倒圆半径rmax。
R2min>rmax在对流道和相邻叶片的交接部分进行清根时,选择的刀具半径R3min小于流道和叶片相接部分的最小倒圆半径rmin。
R3min<rmin1.2 驱动方法选择本文将基于UG NX 3.0重点介绍流道开粗、流道半精加工、叶片精加工和倒圆部分清根的加工轨迹规划方法。
- 1、下载文档前请自行甄别文档内容的完整性,平台不提供额外的编辑、内容补充、找答案等附加服务。
- 2、"仅部分预览"的文档,不可在线预览部分如存在完整性等问题,可反馈申请退款(可完整预览的文档不适用该条件!)。
- 3、如文档侵犯您的权益,请联系客服反馈,我们会尽快为您处理(人工客服工作时间:9:00-18:30)。
1 叶片的数控加工方法 . 2 叶 片 加 工 的复 杂 性 在 于 其 叶 身 部 分 由复 杂 曲 面组 成 。多 年 来 ,工 业 发达 国家 曾经 先 后 研 究 出
叶 片 的 多种 加 工 方 法 , 如 铸造 成 形 后 修 光 法 、石 蜡精 密 铸 造 法 、电 火 花 加 工法 、三 坐 标 仿 形 加 工 等 ,这 些 制 造 方 法 不 仅 效 率 低 ,而 且 质 量 也 差 。
务l 匐 似 违
叶 片就 能 随机 床 的工 作 台作 旋 转 运 动 ,其 旋 转 轴
通 常 为机 床 的a 。 只需一 次 装夹 , 可 以 完成 叶根 轴 就 的全 部 加 工 任 务 ,足 以保 证 叶 片 的 各 个 部 分 的 精 度达 到 设计 要 求 。
在 加 工 中 ,刀 具沿 机 床 的3 个平 移 坐 标方 向作 进 给 运 动 ,形 成 刀 具 相 对 叶 身 的 连 续 环 绕 运 动 轨
模 、 叶 片 的加 工 方 式 选 择 、叶 片 的过 切 、清 根 处
理等。
示 。在 建 模 时 要 考 虑 到 后 面 的加 工 , 因此 在 建模 的时 候 将 叶 片 的 第 一 个 截 面沿 顺 时 针 方 向旋 转 了 2 。 。 在 后面 加 工 的 时 候 可 以大 大 节 约 时 间 ,省 0
台 ,进 行 自 由分 度 。将 零 件 装 在 旋 转 工 作 台上 , 用 夹 具 将 叶 片 樟头 固定 在 机 床 的 旋 转 工 作 台上 , 另一 端 使 用 顶 尖 顶住 叶 尖 尾 部 的 工 艺 卡头 ,这 样
收稿日期:2 1 - 8 2 0 1 0— 6 作者简介 :刘 国群 ( 9 0一),女 ,四川威远 人 ,高级工程师 ,本科 ,主要从事汽 车底盘系统系列零部件的加工 、装 配 17 过程控制和质量管理工作。 【8 第3 卷 3】 3 第1 期 2 21— 2上 ) 01 1 (
精加 工 ,选 球 形 铣 刀 ( 8e速 钢 ) 0 号刀 :精 加 ii :3
工 ,选 球 形 铣 刀 ( 6 速 钢) N 。全 部 采 用 冷却 液 降
低铣 削 温度 ,粗加 工 余量 留05mm , 精车 余量 留 .
0.m m 。 2
图3 叶 片 平 滑 效 果 图
分 ,在 自 由 曲面 的 多 坐 标数 控 / T 中 ,刀具 轨 迹 J _ n
的优 劣 直接影 响其 加工 精度 和加 工效率 。 1 )刀具 切触 点 的确定
刀 具 切 触 点 ,是 指 刀 具 在 加 工过 程 中与 被 加
工 零 件 的 理 论 接 触 点 。从 几 何 关 系上考 虑 , 刀具
与加 工面 的接 触关 系为 点接 触 。如 图4 所示 。
刀轴 矢量
图2叶片截面线
() 铣 刀 a立
第3 卷 3
第1 期 2
2 1 — 2 上 ) [9 01 1 ( 3 1
1 匐 化 注
刀轴 矢量
曲
曲
() 面加 工 b平
图6走刀步长 与残 留高度的关系
置 而 改变 ,不论 刀具 路径如 何规 划 ,只要 刀具 半
创 建 、 曲面 等 操作 ,可 以得 到 叶 片 的 叶身 型 面 ,
用UG里 面 的 曲面组 的方 式将 截 面连 接起 来 ,就 可
得到 平 滑 后 的效 果 图 ,如 图3 示 。从这 个 图可 以 所
看 出 。 叶 片 的 背部 形 状 较 规 则 , 呈现 出类 似 于 圆
柱面 ,较容 易 加工 。 1 . 叶片刀具轨迹的计算 .2 2 刀具 轨 迹 生 成 是 自由 曲面 数 控 加 工 的核 心部
1 )叶片 的数控 加工 工艺分 析
零 件 图 件 1 成 车 削 加 工 后 ,应 进 行 叶 片 加 完 工 。选 四 轴联 动 加 工 中心 ( 中数 控 系统 )铣 叶 华
片 , 四轴 联 动 的 数 控 加 工 中 心 , 可 以 加 工 出高 质 量 的 复 杂 曲面 。装 有 一 个 分 度 精 密 的旋 转 工 作
( )零 件 整 体 a
1 叶片 的数控加工及关键技术
11 零 件 图的分析 _
认 真 分 析 零 件 图 。 了解 零件 的 几何 尺寸 、尺
( )叶 片 实 物 b
图 1 零 件 图件 1
寸 精 度 、 形 位 公 差 、表 面 粗 糙 度 等 技 术 要 求 , 了
解 零件 的材料 、毛坯种 类 、加工性 能 等 。
及清根等 关键性的技 术问题 。叶片的数控加 工开始 引入高职教学 ,可供高职 学生 、初学 者及 教师教学参考。 关键词 :数控加工 ;程序 编制 ;叶片建 模 ;叶片的过 切及清根处理 中图分类号 :T 6 9 G 5 文献标 识码 :B 文章编号 :1 0—0 3 ( 0 1 1 ( 一 0 8 0 9 1 4 2 1 ) 上) 0 3 — 6 0 2
R:刀具半 径 ;
n :加 工表 面在P 点处 的单 位法 矢量 ; 可将 上式 写成 分量 的形 式 ;
Xo r+Rn c= p x yo r+Rn c= p y Zo p c=r+Rn z
4 )走刀 行距 的计 算 走 刀 行 距 是 指 相 邻 两 行 刀 具 轨 迹之 间 的 最 短
功 能 方 便 直 观 , 可 以 直 接 在 点 、 线 、 曲面 、实 体
上 产 生 刀轨 ,生成 叶 片的三 维 几何模 型 。 1 )构 建 截面 线 按 设 计 给 定 数 据 绘 制 出 各 个 平 面 上 的 截 面 线 , 叶 片 是 由五个 截 面相 同 的 曲线 组 成 ,在 建 模 时 , 先作 出一 个 截 面 ,叶 盆 和 叶 背上 的型 线 均 为 自由曲线 ,进 排气 边缘 为一 段 圆弧 。
Do : . 9 9 i s n 1 0 -0 3 .0 1 1 (I . 3 i1 3 6 / . s .0 9 1 4 2 1 .2 - 1 0 i )
0 引言
2 1年 4 3 5 0 0 月2 至2 日, 由四川 省教 育 厅主 办 , 四 川 航 天 职 业 技 术 学 院 承 办 的 2 1 年 四 川 省 职 00 业 院 校 学 生 《 杂 部件 造 型 、 多轴 联 动 编 程 与 加 复 工 》 全 国 数 控 大 赛 预 选 赛 。这 次 大 赛 由4 零 件 个
出,残 留高度h 与切 削 行宽 度d 间 的关 系为: 之
h /( 一k ) = 1 b _ 1(
若 允 许 的最 大 残 留 高度 为 eh ,经 推导 可 得 切
削 行 宽度:
d 2 2 ( R ≤ x R£ 1 k) / /一
式 中R为 刀具 半 径 ;k 为加 工 表面 沿 切 削行 进 给 方 向的法 曲率 ,p l b =/ k
径 小于 被加 工 曲面的 凹主 曲率半 径 ,则不 会发 生
局 部 曲率干 涉 ,均能 铣削 出所 要求 的 曲面形状 。
() 形 刀 c环
3 )球 形 刀刀位 计算 如下
r。 r+Rn c= p
图4 不 同 刀具 的切 触 点
2 )球 形 刀加工 原理
式 中 :r :刀心 的矢 径 ; c 。
:
采 用 球 形 刀 端 铣 加 工 自 由曲 面 ,球 形 刀 球 面 具有 法 矢 自适 应性 ,如 图5 所示 ,球 形 刀 刀心 约 束 在加 工 曲 面 的 等距 面 上 ,刀 轴 矢 量 则 可 以根 据 曲 面形 状和 约束 面( 包括 导动 面和 检查 面) 的形状 和位
乍/ T_ 面上切 触 点P 矢径 ; J 表 U 的
去 了不 少不 必要 的刀路 。
121 叶片建 模 __
叶 片 建 模 是 数 控 加 工 的 前 提 条 件 ,根 据 叶 片 的设 计数 据 或 实物 测量 数 据 ,应用 C D/ AM软件 A C
2 )构建 曲面 在 叶 片 截 面 完 成 后 ,将 所 得 到 的截 面 线 通 过
() a曲面 / r Ja u
1 . 叶片的刀轴矢量计算与干涉 分析 .3 2
[0 第3 卷 41 3
第上
参I
1 )四坐 标数 控加 工 刀轴 矢量 的计 算 四 坐 标 加 工 的 特 点 是 刀 具 可 以 同 时 具 有 X, Y,Z 个 方 向和绕 工 件的 转动 进给 。转 动 围绕 a , 三 / J 工 轴 ,在采 用球 形 刀加 工时 ,球形 刀端 点与 加工 表 面 切 触时切 削 速度 为零 ,切 削性能 较差 ,为 了保 持 切 削 速度 的相 对稳 定和 加工 质量 ,通 常将 刀轴置 于
务l 訇 化
复杂 曲面叶片的数控加工技术探讨
The di cu i s ss on ofnum ercalcont olm achi echnol i r ne t ogy of com pl x e cur ed s f v ur ace
刘国群’ ,刘祖其 ,卢丽琴 ‘
2 )叶片数 控加 工 的关键 技 术 叶 片 加 工 一 直 是 数 控 加 工 领 域 具 有 挑 战 性 的 课 题 , 其 需 要 解 决 的 问 题 复 杂 繁 多 , 如 叶 片 建
将 各 曲 线 光 滑 过 渡 ,并 保 证 各 段 曲 线 的 连 续 。然 后 根 据给 定 的扭 转 角 将 各 个平 面 上 的 曲线 通 过 命 令进 行旋 转 ,得 到 一组 空 间 曲线 ,如 图2 所
迹 。每 换 一 把 刀 具 都 要 对 刀 ,每 把 刀 具 的 长 度 必
须 很 精 确 。加 工 路 线 分 粗 铣 、半 精 铣 、精 铣 三 次
切 削 。根 据 叶 片的加 工 要求选 用 3 铣刀 。0 号 刀: 把 l