第一讲 表面微机械加工技术
第1章 机械加工方法概述ppt课件
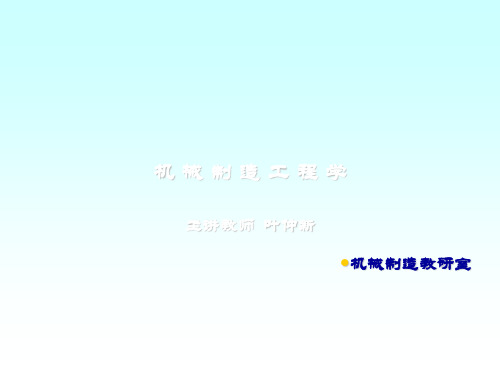
圆锥面、平面、螺旋面、齿面等各种成形表面的加工。
• 磨削加工的主运动是砂轮的旋转运动。磨削加工所用的
刀具以砂轮和砂带为主。与前述的刀具切削有着不同的加工 机理。
状和尺寸制件的工具。按填充方法和填充材料的不同,模 具可分为:锻压具模、冲裁具模、拉伸具模、压铸模具、
冷冲模具、注射模具、吹塑模具、粉末冶金模具等。
2、△m<0的制造过程
• △m<0 制造过程是指从表面去除材料来获得零件形状
的方法。包括切削加工和特种加工。
• 切削加工是指零件在切削机床上,通过机床的传动系
2) 插削加工
• 插削主要用于加
工工件的内表面,如
键槽、内孔等,相当
于立式刨削。
2) 拉削加工
• 拉削可使加工表面一次切削成形。机床运动简单,切
削速度低,效率高,刀具成本高,适用于大批量生产。拉床 可分为卧式和立式,内拉和外拉等。
4)钻削与镗削加工
• 在钻床上,用旋转的钻头钻削孔是孔加工最常用的方法,
可以一次完成粗精加工。
8) 特种加工
• 随着科学技术的不断发展,许多具有高硬度、高强度、
高脆性或高熔点的难加工新型材料(如硬质合金、钛合金、 淬火工具钢、陶瓷、玻璃等),以及具有较低刚度或复杂曲 面形状的特殊零件(如薄壁件、弹性元件、具有复杂曲面形 状的模具、叶轮机械的叶片、喷埋头等)的出现,采用传统 切削加工方法以无法完成其加工任务。特种加工方法正是在
• 用成形法加工齿轮齿形时,刀刃的形状应与被加工齿
轮的齿槽的横截面形状相同。这类刀具有盘状和指状铣刀、 刨刀、拉刀。
第十二章 表面微细加工技术

• 3、超细线条曝光技术 • 1)远紫外光曝光技术:远紫外光的波长为 200~300nm,与常规光刻曝光工艺中采用的 400nm左右的紫外光相比,光的波长缩短一 半左右,因此,可以获得更高分辨率的光刻 线条。 • 2)电子束曝光技术:电子束曝光是利用电 子束在涂有光刻胶的晶片上直接描画或投影 复印图形的技术。电子束曝光系统的加速电 压通常在10~50kV之间,其相应的电子束波 长范围为0.005~0.01nm。如此短的波长就克 服了衍射效应的限制,从而使电子束曝光具 有极高的分辨率,其极限分辨率可达3~8nm。
• 4、显影 • 将曝光后的Si片在显影液中浸泡数十秒,则 负性光刻胶的未感光部分将被溶解,从而 使掩模上的图形被完整地复制到光刻胶上。 显影后一般应检测图形是否套准,是否符 合质量要求。
• 5、坚膜 • 显影完并经清洗后,对有光刻胶膜图像的Si 片再次烘烤,称为坚膜。此过程是为了排 除光刻胶膜中残留的显影液和水分,使胶 膜硬化并使其与SiO2膜有更好的黏附性, 并提高胶膜的耐刻蚀能力。坚膜一般是在 180~200摄氏度的温度下烘烤大约30mi量比电子大, 在光刻胶和基片中的散射小,所以离子束 曝光的分辨率比电子束曝光高。 • 4)X射线曝光:X射线曝光光源的波长为 0.1~1.4nm,比紫外光短2~3个数量级,用 作曝光源时可提高光刻图形的分辨率,可 以刻出0.02微米的细微线条。
12.1.2 LIGA微细加工技术
• LIGA能在微米级制造平面尺寸,高宽比大 于200的三维微形立体结构件;而且加工的 材料比较广泛,可以是金属、陶瓷和塑料 等材料,尤其适合进行高重复精度的大批 量生产。
• 1、LIGA的工艺过程 • LIGA是德文的光刻照相(Lithographie)、电 铸(Galvanoformng)、模铸(Abformung) 三个词语的缩写,依次表示了该工艺的三个加 工过程:深度同步辐射X射线光刻、电铸成形 和注塑成形。
各种表面机械加工方法

各种表面机械加工方法(P93自己总结)
1.外圆表面:是轴类、盘套类零件的主要组成表面。
加工方法:轨迹法、成形法。
多采用车削加工和磨削加工。
技术要求包括:尺寸精度、形状精度、位置精度、表面粗糙度等。
2.车外圆锥面:车刀相对于工件轴线斜向进给实现的。
3.成形回转面:母线为曲线的回转表面。
一般由车刀的纵向与横向进给互相配合实现的。
4.磨削:用砂轮或其他磨具以较高的线速度对工件表面进行加工的方法。
属于精加工。
5.内圆表面(内孔):基本方法:钻削、镗削。
机械加工表面质量加工培训教材PPT85页课件

1. 磨削用量对表面粗糙度值的影响
*
2. 非几何因素
(1)工件材料的影响
韧性材料:工件材料韧性愈好,金属塑性变形愈大,加工表面愈粗糙。故对中碳钢和低碳钢材料的工件,为改善切削性能,减小表面粗糙度,常在粗加工或精加工前安排正火或调质处理。 脆性材料:加工脆性材料时,其切削呈碎粒状,由于切屑的崩碎而在加工表面留下许多麻点,使表面粗糙。
砂轮硬度。太硬,磨粒脱落↓,表面粗糙度增大;太软,磨粒脱落↑,使表面粗糙度值增大。硬度合适、自励性好↑→Ra↓ 砂轮组织。紧密组织在精密磨获得高精度和较小的表面粗糙度值;疏松组织不易堵塞。
砂轮材料。氧化物(刚玉)砂轮磨钢类零件;碳化物(碳化硅、碳化硼)砂轮磨铸铁、硬质合金等;高硬材料(人造金刚石、立方氮化硼)砂轮可获极小表面粗糙度值,成本高。 磨削液。
(4)其它因素的影响
此外,合理使用冷却润滑液,适当增大刀具的前角,提高刀具的刃磨质量等,均能有效地减小表面粗糙度值。振动
(3)进给量的影响
减小进给量f固然可以减小表面粗糙度值,但进给量过小,表面粗糙度会有增大的趋势。
*
影响切削加工表面粗糙度的因素
刀具几何形状
*
(2)切削速度的影响
加工塑性材料时,切削速度对表面粗糙度的影响(对积屑瘤和鳞刺的影响)。加工脆性材料,切削速度影响不大。 此外,切削速度越高,塑性变形越不充分,表面粗糙度值越小 选择低速宽刀精切和高速精切,可以得到较小的表面粗糙度。
表面技术(第1讲 表面技术概论(新))

Surface Technology
联系方式:
总成绩= 作业成绩+ 考勤成绩+ 考试成绩????
严肃活泼:课堂活跃而不失严肃!
电镀与电刷镀、化学镀、涂装、粘接等19种喷丸强化、表面热处理、化学热处理等如:热喷涂与喷丸复合等
如:电铸、抛光、蚀刻等
物理气相沉积、化学气相沉积
热喷涂
激光表面处理、电子束表面处理、离子注入
1.提高耐腐蚀能力
2.提高耐磨与减磨能力
3.赋予表面特种功能
4.赋予表面特殊物理、化学性能
5.提高表面完整性
6.表面装饰性
公元前585年
长二F 火箭
(服役16架)
“先进高频材料”(AHFM)的隐身涂料,它是一种基于环氧树脂的、可有效吸收雷达信号的材料,将用于替换目前B-2使用的近3000英尺的吸波带。
幽
灵
全长16.5米,高3.2米,重量13.5吨,机翼长13米,正常飞行速度为461公里/小时,飞行高度为9140米。
隐形技术
面电阻:150~500(Ω/□)应
用:触摸屏特性:高透光率、低电阻值、高洁净度
应用:液晶显示器
一个P-N结在标准光照条件下额定输出电压为0.48
V。
MEMS工艺表面微机械加工技术

综上,可以看出,刻蚀选择性应当尽可能地大。
•构造层和牺牲层材料的制备方法
实际中广泛应用到的构造层和牺牲层材料的淀积方法是化学气相沉积〔CVD〕, 根据提供能量不同有如下分类:
LPCVD沉积腔(多 个温度区用于提高材 料生长的均匀性)
在MEMS中应用的LPCVD材料主要有三种:多晶硅、氮化硅和二氧化硅:
2.它制造的机械结构基本上都是二 维,因为机械 结构的厚度完全受限 于沉积薄膜的厚度。
2.由于体微机械加工 工艺无法做到零部件 的平面化布局,因此 它不能够和微电子线 路直接兼容。
二、根本工艺流程
•举例:方案一 —— 微型马达根本制造工艺流程
a) 在硅片上淀积一层牺牲层。 b) 淀积多晶硅作为构造层材料,制造转子。 c) 光刻胶作掩膜,反响离子刻蚀使图形转移到多晶硅构造层上。 d) 硅片外表沉积另一层氧化物牺牲层〔材料可能与前一层不同,常选择
表面微机械加工
体微机械加工
充分利用了现有的IC生产工艺,对 可以相对容易地 制造
优点 机械零部件尺度的控制与IC一样好, 出大质量的零部 件。 因此这种技术和IC完全兼容。
1.机械加工层越 多微 型元件的布局 1.很难制造精细灵敏 问题、平面化问题 和减小残余应力 的悬挂系统。 问题也更难解决。
缺点
LPCVD 二氧化硅〕 e) 加工出与衬底相连的锚区窗口〔为了制造定子,限制转子的侧向平移〕 f) 沉积第二层构造层,该构造层通过锚区窗口与衬底相连〔制造定子〕 g) 再次涂敷光刻胶用于光刻第二层构造形状。 h) 浸入氢氟酸刻蚀液以除去两层牺牲层。
•方案一带来的问题:
定子 转子 衬底
1. 转子在重力作用下很容易落在衬底上,产生大面积接触。 2. 转子在高速转动过程中会与定子产生接触,产生额外的摩
第12章 表面微细加工技术-用

50 μm 图4-3 X射线刻蚀的三维实体
LIGA技术采用深度X射线光刻、微电铸成型和塑料铸模等技 术相结合的一种综合性加工技术,它是进行三维立体微细加 工最有前途的方法之一,同时也是制作非硅材料微机电系统 的首选工艺。 利用LIGA技术制作微金属图形主要由两步关键工艺组成, 即首先利用同步辐射X射线光刻技术光刻出所要求的图形, 然后利用电铸方法制作出与光刻胶图形相反的金属模具,再 利用微塑铸制备微结构,具体的工艺步骤如图所示。
尺寸在微米级范围内的加工方式,曾广泛应用于大规模集成 电路的加工制作并由此涉及更广泛的领域。
在微机械研究领域中,微细加工技术已经成为其前沿关键技
术之一,它是微米级、亚微米级微细加工的通称。
微细加工具备精密和超精密加工的特征。广义上的微细加工 ,其方式十分丰富,几乎涉及了各种现代特种加工、高能束 加工方式。 从基本加工类型看,微细加工可大致分为四类:
显影就是用显影液溶解掉 不需要的光刻胶,将光刻 掩模板上的图形转移到光 刻胶上。显影液的选择原 则是:对需要去除的那部 分光刻胶膜溶解的快,溶 解度大;对需要保留的那 部分光刻胶膜溶解度极小。
坚膜也是一个热处理步骤。 坚膜的目的就是使残留的 光刻胶溶剂全部挥发,提 高光刻胶与衬底之间的粘 附性以及光刻胶的抗腐蚀 能力。
12.1.1光刻
根据曝光时所用辐照源波长的不同,光刻可以分为
− − − − 光学光刻法 电子束光刻法(主要用于掩模的制造) 离子束光刻法 X射线光刻法
40
基本原理
(a)涂胶(b)曝光(c)显影、烘片(d)蚀刻(e)剥膜
第一阶段为原版制作,生成工作原版或工作掩膜,为光刻时 的模板;第二阶段为光刻。 光刻加工的主要过程: (1) 涂胶
来,称为显影;显影后进行200~250℃的高温处理,以提高光 致抗蚀剂的强度,称为烘片。
中职课程《机械加工技术》精品课件之典型表面的机械加工

内圆磨头上装有内圆磨具5,用来磨削内圆。它由电动机经平 带带动主轴高速回转(10 000 r/min以上),实现内圆磨削的主运 动。不用时,将内圆磨头翻转到砂轮架上方,磨内圆时翻下。
任务1 内、外圆表面的机械加工
活动1 万能外圆磨床的切削运动 1.主运动
任务3 螺纹表面的机械加工
【任务描述】
1.了解螺纹的分类、种类、代号及各部分的名称。 2.熟悉螺纹车刀的刃磨与装刀要求。 3.掌握车削普通螺纹的进刀方法和切削用量选择。 4.了解车螺纹时乱扣原因,掌握克服乱扣的方法。 5.了解套螺纹与攻螺纹的方法。
任务3 螺纹表面的机械加工
【任务分析】
在各种机械产品中,带有螺纹的零件应用广泛。车削 螺纹是螺纹加工的常用方法,本任务主要介绍车削普通螺 纹的方法、原理等,并简要介绍螺纹加工的其他方法,即 套螺纹与攻螺纹。
(1)螺纹牙型。 (2)牙型角α。 (3)螺距P。 (4)导程Ph。 (5)大径D(d)。 (6)中径D2(d2)。 (7)小径D1(d1)。 (8)原始三角形高度h。 (9)螺旋升Байду номын сангаасλ。
图4-18普通螺纹基本牙型
任务3 螺纹表面的机械加工
活动2 螺纹车刀的刃磨与装刀要求 1.螺纹车刀的刃磨要求 (1)车刀的左右切削刃必须是直线,且无崩刃。 (2)根据粗、精车的要求,刃磨时要磨出合理的背前角和两侧后 角。粗车刀背前角大,后角小;精车刀则相反。 (3)刀头不应歪斜,车出螺纹的牙型半角α2必须相等。 (4)高速车削时,牙型角会扩大,此时,要将车刀刀尖角适当减 少约30′。 (5)内螺纹车刀刀尖平分线必须与刀柄垂直,其后角应适当大些。
万能外圆磨床磨削工件时砂轮的回转运动为主运动。
【优质】表面微细加工解析PPT资料

硅基底的氧化
半导体的制作过程
半导体芯片中的双层金属布线连接
半导体芯片中的金属布线连接
半导体芯片中的金属布线连接
半导体芯片中的NPN结双极晶体管
表面超微图形加工技术
光刻 技术
光致抗蚀剂 光刻SiO2膜
衬底硅
涂光致抗蚀剂
紫外光(193nm) 掩模版
衬底硅
曝光
衬底硅
显影
SiO2 衬底硅
去胶
衬底硅
②生长型加工方法,即以一种材料作为基材,在 其上添加另一种材料,形成所需的形状或者图形 的加工方法。按此定义,在前面章节所介绍的物 理气相沉积、化学气相沉积、离子注入、电镀、 化学镀都属于微细加工技术;
③变形加工,指材料形状发生变化的加工,如塑 性变形、流体变形等。
集成电路的制作步骤
MOS晶体管的制作步骤
常用微细加工技术
1.光刻工艺 2.掩模板制作工艺 3.电子束与离子束微细加工 4.激光微细加工
光刻的基本原理: 利用光致抗蚀剂(或称光刻胶)感光后因光化学反 应而形成耐蚀性的特点,将掩模版上的图形刻制 到被加工表面上。
掩膜(mask)的概念: 它是一块印有所需要加工图形的透光玻璃片。当 光线照在掩模版上时,图形区与非图形区对光线 的吸收与透过能力不同。
表面微细加工技术指那些能够制造微小尺寸元器 件或薄膜图形的方法。
微细加工的
加工尺寸一般在亚毫米(常指低于100μm)至纳 米级范围内,
加工的单元则从微米级、纳米级到原子级(Å 级)。
纳米量级结构的制作是纳 米技术的关键技术之一。 我国SPM系统在Au-Pd合金膜 表面上机械刻画出的最小线宽 为25nm。
用AFM机械刻蚀原理刻 写的亚微米尺寸的唐诗
第一讲 表面微机械加工技术

硅表面微机械加工技术及其应用1.概述表面微机械加工技术典型工艺示意图硅表面微机械加工的典型结构示意图薄膜层材料常用多晶硅、氧化硅、氮化硅、玻璃和金属等,为微结构器件提供敏感元件、电接触线、结构层、掩模和牺牲层。
牺牲层(常用SiO2)做在淀积和光刻形成图形的结构层的下面,可以选择性刻蚀除去,使结构层与基底隔开。
该技术在硅片上用连续生长功能层、结构层、牺牲层工艺来制作微机械结构,借助多次光刻-套刻实现图形复制和层间对准,依靠牺牲层技术控制结构的分离与衔接,硅片本身并不被刻蚀,因而是一种平面加工或准三维加工工艺,适用于制作厚度几至几十微米和深宽比为几至十几的微机械结构。
该技术有别于传统半导体工艺的本质在于可以制作可活动构件,如悬臂梁、转子、齿轮、振子等,这些都是MEMS器件的基本结构单元。
所以:构成硅表面微机械加工技术的要素:电子材料积累半导体微加工技术基础自支持结构单元设计牺牲层技术总结:利用半导体技术的材料体系和微加工技术,将基于薄膜材料制备的机械结构或者传感部件,与填充介质层组合,叠层定位制造在单晶硅衬底上,借助选择性刻蚀技术控制部分结构(或局部)脱离支撑而释放,从而实现机械结构的批量制造,也可以与控制部分的电路集成,这便是典型的硅表面微机械加工技术。
迄今为止研究开发的多数微机电系统(器件)都包含硅表面微机械加工技术工艺的单元,或者说:几乎所有的MEMS器件都有借助硅表面微机械工艺实现的设计形式。
2.主要单元技术常用材料简介:硅表面微机械加工技术主要采用半导体工业常用的部分硅基材料,如单晶硅:仅作为衬底使用,通常不会对其进行结构加工,但是经常需要进行表面氧化以形成牺牲层或绝缘层,掺杂或注入以形成导电层或者阻挡层。
单晶硅在微尺度下具有非常优越的机械性能,那是在体硅加工中才能够得到充分利用的性质。
研究者将SOI(silicon on insulator)硅片用作衬底可以得到一层以单晶硅为结构材料的微结构,所以,也有把SOI作为MEMS材料的说法。
典型表面的机械加工

f)刨曲面
38
2.铣削
铣刀旋转作主运动,工件作进给运动的切削加工方法称为铣削。 通常平面的铣削可以分为粗铣、半精铣和精铣三个加工阶段。
39
(1)粗铣 粗铣加工精度为IT12~IT11,表面粗糙度Ra值为25~ 12.5μm,为半精铣、精铣加工作准备。
17
二、内圆表面的加工方法
1.钻孔、扩孔和铰孔
(1)钻孔 一般加工精度可达IT13~IT11,表面粗糙度Ra值可达50~12.5μm, 主要用于孔的粗加工。
18
(2)扩孔 加工精度可达IT10,表面粗 糙度Ra值可达 6.3~3.2μm,可作 为孔的半精加工;也可作为精度 要求较低孔的最终加工。扩孔可 以修正孔轴线的歪斜。
43
5.研磨
(1) 研具 研具是保证被研磨工件几何形状精度的重要因素,因此,对研 具材料、精度和表面粗糙度都有较高的要求。 (2)研磨余量
研磨是微量切削,因此研磨余量不能太大,也不宜太小,一 般在0.005~0.030mm之间。
(3) 研磨特点及作用 (4)研磨方法及注意事项 研磨分手工研磨和机械研磨两种。
1—底座 2—工作台 3—主轴 4—进给箱 5— 主轴箱 6—电机 7—立柱 30
(3)摇臂钻床 摇臂钻床适合于大型箱体零件
或形状复杂零件的钻削。
1—立柱座 2—立柱 3—摇臂 4—主轴吧 5— 工作台 6—底座
31
2.镗床
镗床又分为普通镗床和坐标 镗床,普通镗床的加工精度可达 IT8~IT6,表面粗糙度Ra值可达 1.6~0.8μm;坐标镗床的加工精 度可达IT7~IT5,表面粗糙度Ra 值可达0.8~0.2μm。
模具基本表面的机械加工方法_PPT文档59页

16、自己选择的路、跪着也要把它走 完。 17、一般情况下)不想三年以后的事, 只想现 在的事 。现在 有成就 ,以后 才能更 辉煌。
18、敢于向黑暗宣战的人,心里必须 充满光 明。 19、学习的关键--重复。
20、懦弱的人只会裹足不前,莽撞的 人只能 引为烧 身,只 有真正 勇敢的 人才能 所向披 靡。
31、只有永远躺在泥坑里的人,才不会再掉进坑里。——黑格尔 32、希望的灯一旦熄灭,生活刹那间变成了一片黑暗。——普列姆昌德 33、希望是人生的乳母。——科策布 34、形成天才的决定因素应该是勤奋。——郭沫若 35、学到很多东西的诀窍,就是一下子不要学很多。——洛克
- 1、下载文档前请自行甄别文档内容的完整性,平台不提供额外的编辑、内容补充、找答案等附加服务。
- 2、"仅部分预览"的文档,不可在线预览部分如存在完整性等问题,可反馈申请退款(可完整预览的文档不适用该条件!)。
- 3、如文档侵犯您的权益,请联系客服反馈,我们会尽快为您处理(人工客服工作时间:9:00-18:30)。
硅表面微机械加工技术及其应用1.概述表面微机械加工技术典型工艺示意图硅表面微机械加工的典型结构示意图薄膜层材料常用多晶硅、氧化硅、氮化硅、玻璃和金属等,为微结构器件提供敏感元件、电接触线、结构层、掩模和牺牲层。
牺牲层(常用SiO2)做在淀积和光刻形成图形的结构层的下面,可以选择性刻蚀除去,使结构层与基底隔开。
该技术在硅片上用连续生长功能层、结构层、牺牲层工艺来制作微机械结构,借助多次光刻-套刻实现图形复制和层间对准,依靠牺牲层技术控制结构的分离与衔接,硅片本身并不被刻蚀,因而是一种平面加工或准三维加工工艺,适用于制作厚度几至几十微米和深宽比为几至十几的微机械结构。
该技术有别于传统半导体工艺的本质在于可以制作可活动构件,如悬臂梁、转子、齿轮、振子等,这些都是MEMS器件的基本结构单元。
所以:构成硅表面微机械加工技术的要素:电子材料积累半导体微加工技术基础自支持结构单元设计牺牲层技术总结:利用半导体技术的材料体系和微加工技术,将基于薄膜材料制备的机械结构或者传感部件,与填充介质层组合,叠层定位制造在单晶硅衬底上,借助选择性刻蚀技术控制部分结构(或局部)脱离支撑而释放,从而实现机械结构的批量制造,也可以与控制部分的电路集成,这便是典型的硅表面微机械加工技术。
迄今为止研究开发的多数微机电系统(器件)都包含硅表面微机械加工技术工艺的单元,或者说:几乎所有的MEMS器件都有借助硅表面微机械工艺实现的设计形式。
2.主要单元技术常用材料简介:硅表面微机械加工技术主要采用半导体工业常用的部分硅基材料,如单晶硅:仅作为衬底使用,通常不会对其进行结构加工,但是经常需要进行表面氧化以形成牺牲层或绝缘层,掺杂或注入以形成导电层或者阻挡层。
单晶硅在微尺度下具有非常优越的机械性能,那是在体硅加工中才能够得到充分利用的性质。
研究者将SOI(silicon on insulator)硅片用作衬底可以得到一层以单晶硅为结构材料的微结构,所以,也有把SOI作为MEMS材料的说法。
多晶硅:该工艺体系中最常用的结构材料之一,可以掺杂成为半导体,作为结构材料通常厚度在2微米左右,借助ACVD、LPCVD、PECVD 都可以制备,但是以LPCVD工艺最常用,成膜条件通常取10-100Pa压力,基片温度600度,借助硅烷的分解沉积硅。
多晶硅膜可以借助RIE方法精确图形化。
多晶硅的优越特性:∙Stronger than steel (polysilicon has a strength of 2-3 GPa, while steel has a strength of 200MPa -1GPa)∙Extremely flexible (the maximum strain before fracture is ~0.5%)∙Resists fatigue∙ultra-low-stress mechanical polysilicon maintains device integrity.∙polysilicon is directly compatible with modern IC fabrication processes. In fact, polysilicon iscurrently used in virtually all IC fabs,Its depositionand etch properties are very well known.氮化硅:同样是常用的结构材料之一,CVD 制备,常借助RIE技术图形化,有时也可以湿法加工。
作为绝缘材料使用,厚度一般在1微米以下。
不同条件下制备的CVD氮化硅薄膜性质有很大差异,高温工艺倾向于得到致密、高稳定性的薄膜。
低温工艺通常借助PECVD实现。
氧化硅:主要是作为牺牲层材料使用,与多晶硅和氮化硅拥有湿法刻蚀的选择性;经常作为绝缘材料使用,隔绝衬底与结构材料之间的电接触。
有时也可以作为结构材料使用,刚度大于多晶硅和氮化硅,透明度高,刻蚀选择比高,是既可以用湿法加工,也可以用干法图形化的薄膜。
氧化硅在表面微机械加工技术体系中主要借助CVD方法制备,但是其它用途多采用基体氧化法在单晶硅表面生成,热氧化膜性质稳定,内应力低,与基体结合牢固,但是厚度难以大幅度提高,所以,作为牺牲层的氧化硅对本体特性要求不多,多采用CVD制备。
铝薄膜:常用的金属膜结构材料和导电材料,特别适合RF MEMS器件中兼顾上述两种功能的结构采用,比金有更好的机械特性,质轻而易于加工,通常采用蒸镀或溅射方法制备,可以采用离子铣加工,但更多采用湿法刻蚀,刻蚀剂大多采用磷酸。
金膜:导电或结构材料,有时也会用作牺牲性材料或者键合过渡层。
稳定性好,可以采用蒸镀、溅射或者电镀方法制备,能够采用离子铣和湿法刻蚀加工,更多采用后者,也可以采用掩膜电镀直接图形化成型。
除了作为硅-硅键合过渡层使用,其它硅基体系中应尽量避免后续高温工序,以免造成扩散污染等负作用。
氧化锆、氧化钽介电绝缘材料,通常只在需要高介电常数绝缘膜的体系中采用,作为功能材料,厚度较薄,一般采用溅射方法制备,干法刻蚀图形化。
多孔硅膜:特殊的牺牲层介质,借助硅的电极氧化形成,拥有高对比度选择性刻蚀的特性,能够提供比氧化硅更大的牺牲层空间(厚度),可以作为功能性衬底,同时也是体硅加工的一种手段。
综合上述几种常用材料,可以看到以下几个特点:材料均为薄膜形态,作为结构材料的厚度通常较厚,一般要进行微细加工,部分薄膜结构最终会形成自支撑结构。
其中最后一点与半导体技术的差异最为明显,也是MEMS材料最为重要的关注因素。
影响自支撑形态的主要因素是薄膜的内应力,因此,应力控制是表面微机械加工的重要课题。
单层膜体内的应力与一般体系没有太多差别,但是,以多层膜结构见长的表面微加工还要特别关注邻近材料热膨胀系数不同造成的内应力,特别是当一种材料必须在高温制备时。
材料选择尽量同种或同类,只在有意利用内应力的情况下才会选择差异显著的材料搭配,如Au/Si结合的蜷曲梁。
过大的内应力会造成薄膜结构破裂或变形。
因此,需要对材料体系的设计给予充分重视,特别是材料制备技术。
薄膜制备技术湿法干法湿法制备的薄膜在硅表面微机械加工技术体系中很少用到,主要是电镀、湿氧化,用于制备金属膜和多孔硅膜等,有时也采用湿法电化学氧化生长氧化硅。
电镀主要是制备金膜,将在LIGA/准LIGA 技术章节重点介绍。
多孔硅膜的湿法氧化:在高浓度的氢氟酸溶液中,以硅为正极通小电流氧化,就可以在硅基体表层得到多孔硅,适当改变制备条件就能够使多孔层转化成氧化硅,是更为理想的牺牲层。
干法制备薄膜是主要技术手段,包括CVD、蒸镀、溅射、扩散、离子注入和热氧化等,其中后三者实际上是对基体的表层进行改性。
CVD(化学气相沉积):在有控制的气相氛围中,使包含目标物质的气体原料在基板表面发生反应,产生所需要的物质,沉积在基板表面,形成薄膜。
有常压CVD(ACVD),低压CVD(LPCVD),等离子体增强CVD(PECVD)之分。
常压CVD在常压下工作,工作温度多在1000度左右,工作区内仅对基板加热,沉积速度较快,镀层调控能力较差。
LPCVD:工作时对整个炉体加热,并施加一高频激励电源,工作温度一般略低,可以调控腔室压力,拥有更多的调节手段,但是,沉积速度也低得多。
国内外对在此体系中进行多晶硅薄膜沉积展开了深入的研究工作,LPCVD成为低应力多晶硅主要制备手段。
PECVD同样在低气压下工作,但是,借助高频放电所形成的等离子体,能够在较低温下成膜,通常可以降低到300度左右。
尽管有等离子体相助,不同温度下沉积的薄膜还是有一定区别的,应根据需要合理选择薄膜制备方法。
总体看来,CVD方法提供了更多选择和更高的生产效率,在微电子工艺中已经得到充分考验和验证,所以它的技术开发一直未有间断,各种辅助措施的CVD方法和相应的设备名目繁多,有兴趣者可以参考相关专门资料进一步学习。
蒸镀通常用于制备金属膜,在真空系统中加热金属材料,使之蒸发,蒸汽原子运动到基片表面堆积成为薄膜。
本地真空一般小于1mTorr,蒸汽压力一般大于10mTorr,蒸镀的主要缺点是台阶覆盖能力差,由于金属化工艺通常是最后的一步,待加工表面有高低落差是难免的,所以常采用旋转和基片加热方法加以改进。
溅射方法与蒸镀相比最突出的有时也在其台阶覆盖能力上,溅射的金属材料种类很多,其限制因素较少,所以,现在的金属化大多数采用溅射方法。
溅射不但能够沉积金属,采用射频溅射还可以制备化合物薄膜,但以反应溅射更为可取,因为化合物靶材不同成份的溅射产额差异会导致成份显著偏差。
溅射膜一般处于张应力状态,可以通过台阶仪测量沉积后的形变加以研究,调节溅射参数可以改进该方面的性质。
离子注入和扩散等更多是在体硅加工时有用,后面再讲述。
图形复制技术:光刻-套刻借助光刻技术实现图形批量复制和转移是微电子技术最重要的特征之一,MEMS技术完全继承了这一点,但是追求的不只是纳米化线宽,而是高深宽比结构,它所要克服的困难更多来自于曝光深度和高低落差所造成的空间一致性难题。
更多内容会在准LIGA技术章节阐述,本节仅简单介绍简单工艺过要素。
光刻必须具备的先决条件是光源、光刻胶和掩膜版。
表面微机械加工继承半导体加工的传统,以紫外光作光源。
光源要尽量均匀平行。
掩膜版是设计成部分透光的玻璃板,一系列这样的模版所产生的图案是实现目标结构的基础。
掩膜版要拥有尽量高的通透/隔断对比度光刻胶要能够准确复制掩膜版的图案,这就要求有高的感光灵敏度和对比度。
目前的商品光刻胶完全能够满足表面微机械加工的技术要求。
光刻图形复制的基本步骤包括:涂胶-前烘-曝光-显影-后烘-图形转移-去胶,除却必须严格遵守的技术参数取值范围之外,经验是非常重要的影响因素。
本实验室所用双面光刻机的光源波长是248nm,光刻胶是AZ系列的正胶,最小线宽可达1微米,套准精度也在1微米左右。
图形转移技术――刻蚀把光刻胶图形转移到目标材料中形成微结构层,主要借助刻蚀将暴露在光刻胶之外的部分全部清除掉,留下部分便是构造目标结构的单元结构(可以看成是一层积木图案)。
刻蚀分干法和湿法。
干法主要离子束刻蚀、反应离子刻蚀等湿法主要是化学刻蚀。
干法刻蚀拥有更高的图形尺寸控制能力,因此受到更多重视。
鉴于硅表面微机械加工技术体系内需要刻蚀的材料主要是硅基的多晶硅、氮化硅和氧化硅,所以,反应离子刻蚀成为最有价值的刻蚀工具。
反应离子刻蚀优点:加工精度高,图形复制能力强,各向异性可调控,物理损伤小。
主要是硅的刻蚀刻蚀剂:SF6,CHF3,Ar等掩膜材料:光刻胶,多种金属膜。