几种疲劳裂纹扩展模型的比较分析
09--裂纹扩展与疲劳裂纹扩展

m2
a0
2m 2
ae
2m 2
M不等于2
• 大作业与课堂讨论
• 在位移控制加载条件下,K a曲线的斜率总是负值, 因此,按照裂纹扩展的稳定性条件,裂纹的扩展 总是稳定的。
裂纹扩展稳定性分析
P, T
b
a
b
设在载荷的作用下, 试件的位移为 ,
•
总的位移(即试验
机加载点位移 为) ,则T :
T M
•
假设在裂纹发生扩展时, 保持试验机加载点的总位 移 T为常数:
展到尺寸a0 a ,如图中D点所示,
比较K a和 KR a两条曲线的二次导数。
且此时K a KR a ,则可以用相同
的方法判断裂纹接下来扩展的稳定性。
确定在给定加载条件下裂纹失稳扩 展的临界应力强度因子的方法
• K-R曲线实质上表示的是裂纹尖端塑性, K 损伤等机制的能量耗散的变化,随着裂
纹的扩展,裂尖的断裂过程区逐渐增大,
KR a
Kc
度上的塑性,微孔洞或微裂纹的形核与 演化。
➢要使裂纹扩展,不仅要提供新形成的 断裂面的表面能,而且要支付这些细观
a
o
a 耗散机制所需的能量。
b
➢随着裂纹的起裂,裂纹尖端的断裂过 程区也发展,它们所耗散的能量随着裂
纹的扩展中逐渐增大,并最终达到某一
➢临界应力强度因子 KR a 随 稳定值。
a
o
b
➢对于这样的材料,裂纹 K 一 旦达到K IC就很容易发生失稳
扩展,除非K a随着裂纹的长
大,逐渐减小。对于很脆的材 料(如玻璃)以及在平面应变 条件下的高强低韧金属,作为 一次近似,通常可以采用上图 所示的这种关系。
K
疲劳裂纹扩展速率 模型

疲劳裂纹扩展速率模型简介疲劳裂纹扩展速率是材料力学领域一个重要的研究课题。
疲劳裂纹扩展是指在材料受到疲劳载荷作用下,裂纹会以一定速率扩展,最终导致材料的疲劳失效。
了解疲劳裂纹扩展速率模型,对材料的疲劳寿命预测和结构设计具有重要意义。
本文将深入探讨疲劳裂纹扩展速率模型及其应用。
疲劳裂纹扩展速率模型的基本原理疲劳裂纹扩展速率模型是基于疲劳裂纹扩展的基本机理和实验数据建立的。
疲劳裂纹扩展通常表现为裂纹的逐渐扩展和材料的逐渐疲劳破坏。
疲劳裂纹扩展速率模型的基本原理可以归纳如下:1.裂纹尖端应力分布:裂纹尖端是裂纹扩展的起点,其应力集中在该处。
裂纹尖端的应力分布对裂纹扩展速率有重要影响。
2.应力强度因子:应力强度因子是表征裂纹尖端应力分布的一个重要参数。
它可以通过应力分析或实验测量得到。
3.断裂力学:根据线弹性断裂力学理论,裂纹尖端的应力强度因子与裂纹扩展速率之间存在一定的关系。
4.实验数据拟合:通过对大量实验数据进行分析和处理,建立裂纹扩展速率模型。
常用的实验数据包括裂纹扩展速率与应力强度因子、载荷频率、温度等因素的关系。
疲劳裂纹扩展速率模型的应用疲劳裂纹扩展速率模型在工程实践中具有广泛应用,主要包括以下几个方面:1. 疲劳寿命预测疲劳寿命是指材料在特定工况下能够承受多少次疲劳载荷循环而不发生裂纹扩展和失效。
基于疲劳裂纹扩展速率模型,可以通过计算裂纹扩展速率和已有裂纹长度,预测材料的疲劳寿命。
2. 结构设计在工程结构设计中,了解材料的疲劳裂纹扩展速率模型对于提高结构的耐久性和安全性非常重要。
根据疲劳裂纹扩展速率模型,可以针对不同材料和结构形式,选择合适的材料和结构设计方案,以延长结构的使用寿命。
3. 材料评估和筛选通过疲劳裂纹扩展速率模型,可以评估和筛选材料的疲劳性能。
根据不同材料的裂纹扩展速率特性,可以选择适用于不同工况和要求的材料。
4. 裂纹控制和修复了解疲劳裂纹扩展速率模型,可以对已发生裂纹的结构进行控制和修复。
08_疲劳裂纹扩展

飞机结构损伤容限设计第8讲疲劳裂纹扩展内容概要1.裂纹扩展规律2.裂纹扩展速率3.裂纹扩展描述模型4.常幅载荷下裂纹扩展寿命估算5.变幅载荷下裂纹扩展寿命估算结构在交变载荷(机械力或热、电磁等)作用下裂纹的扩展称为疲劳裂纹扩展,由此产生的破坏称为疲劳破坏。
统计结果表明在各类工程结构断裂事故中,约80%是由疲劳裂纹扩展引起的。
1960年前后,波音公司最先发现应力强度因子在疲劳裂纹扩展中起关键作用,并在1963年由Paris 和Erdogan整理发表,他们将裂纹扩展数据和应力强度因子幅值联系起来的做法被学术界和工程界所普遍接受,从而开创并奠定了疲劳断裂理论。
在时间次序上,疲劳裂纹扩展的阶段不同。
疲劳破坏按照其发展大致可分为四个阶段:1∘裂纹成核阶段。
起始于应力集中下微结构的滑移、位错等;2∘微观裂纹扩展阶段。
成长于滑移面,裂纹与载荷方向成45º;3∘宏观裂纹扩展阶段。
裂纹与载荷方向垂直;4∘断裂阶段。
裂纹扩展至临界长度时失稳扩展断裂。
实际工程应用中,需要对裂纹的扩展进行量化描述,常用的量是:Δa /ΔN 或d a /d N 。
ΔN 是交变载荷的循环次数增量,Δa 是相应裂纹长度的增量。
d d aN 疲劳裂纹扩展速率疲劳裂纹扩展速率:表示交变载荷下每循环一次裂纹长度的平均增量,它是长度a 和载荷幅值的函数。
由疲劳裂纹扩展速率定义可得:01d d d ca P a N a aN=∫通过对疲劳裂纹扩展速率的研究,可获得裂纹的扩展理论、建立裂纹扩展与外载荷的联系,由此预测带裂纹结构的剩余寿命,为设计人员提供参考意见。
对疲劳裂纹扩展速率的研究通常有两种途径:1) 试验观察,根据试验结果总结扩展规律;2) 结合试验进行机理分析,构建疲劳裂纹扩展的理论模型。
¾试验结果:在裂纹扩展寿命期内,试验表明裂纹长度的扩展速率呈先慢后快的规律,在临界断裂时裂纹失稳迅速扩展而导致结构见断裂。
应力强度因子能合适描述裂纹尖端附近应力场强度,影响裂纹扩展速率的因素也很多,而大量试验证明应力强度因子是扩展裂纹扩展速率的主要参量。
材料疲劳裂纹的扩展

第六章 疲劳裂纹扩展的阻滞和瞬态过程 6.1 疲劳裂纹的闭合效应
6.1.1 塑性诱发裂纹闭合
第六章 疲劳裂纹扩展的阻滞和瞬态过程 6.1 疲劳裂纹的闭合效应
6.1.1 塑性诱发裂纹闭合
右示 意图表示 的典型柔 度曲线对 多种合金 都是适用 的。
第五节 疲劳裂纹的扩展
5.8 I—II复合型疲劳裂纹的扩展 之前所讨论的是延性固体的I型疲劳裂纹扩展 问题,现在开始研究复合型裂纹扩展。
第五节 疲劳裂纹的扩展 5.8 I—II复合型疲劳裂纹的扩展
5.8.1 复合型疲劳断裂图
高桦等人(1985)研究了 几种铁合金和有色金属疲 劳裂纹的扩展,他们用两 种不同几何形状的试样进 行双轴加载,一种是单边 缺口试样受非对称的四点 弯曲循环加载,另一种是 含倾斜中心裂纹板试样承 受双轴拉伸。
第六章 疲劳裂纹扩展的阻滞和瞬态过程
6.1 疲劳裂纹的闭合效应 还有其它的解释导致疲劳裂纹闭合的理论: (ⅰ)在疲劳裂纹内部形成的腐蚀层(氧化物诱 发的裂纹闭合);
(ⅱ)疲劳断裂面的显微粗糙(裂纹面粗糙诱发 的裂纹闭合);
(ⅲ)渗入裂纹内的粘性流体(粘性流体诱发的 裂纹闭合); (ⅳ)应力或应变诱发的裂纹顶端相变(相变诱 发的裂纹闭合)。
5.7.3 钝化扩展机制(第Ⅰ阶段)
第5节 疲劳裂纹的扩展
5.7 疲劳裂纹扩展的物理模型
5.7.5 钝化扩展机制(第Ⅱ阶段)
第5节 疲劳裂纹的扩展
5.7 疲劳裂纹扩展的物理模型
5.7.6 钝化扩展机制
( a ) 裂纹钝化扩展模型;( b ) 铜单晶疲劳裂纹扩展实例
第五节 疲劳裂纹的扩展
5.8 I—II复合型疲劳裂纹的扩展
通过III型疲劳裂纹扩展的研究, 发现了延性固体材料裂纹扩展具有 下列基本特征: 在高幅循环扭转作用下, 发生纯扭转裂纹扩展(径向), 它导致平面断口形貌,如 图(b)所示;
材料断口分析第6章-疲劳断裂
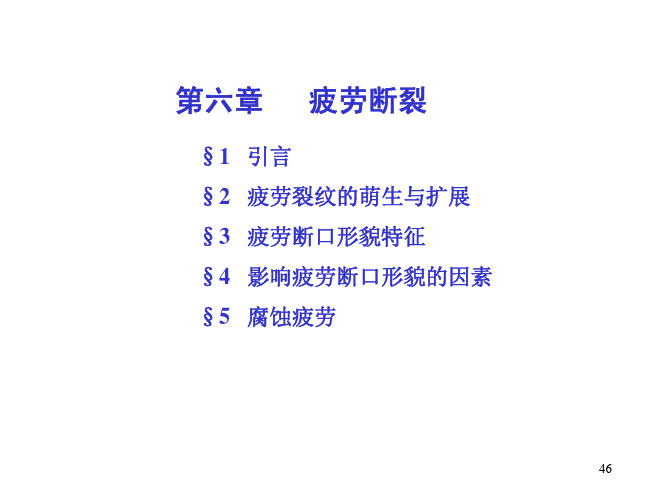
§1 引言 §2 疲劳裂纹的萌生与扩展 §3 疲劳断口形貌特征 §4 影响疲劳断口形貌的因素 §5 腐蚀疲劳
46
§1 引言
1、定义: 由于交变应力或循环载荷所引起的低应力脆断。 在所有的损坏中,疲劳断裂的比例最高,约占70%
2、类型:依负载和环境条件的不同,分为五类: 高周疲劳:材料在低应力(σ<σ0.2)的作用下而寿命较高
66
锯齿形断口
棘轮花样
67
3、瞬断区
形貌:具有断口三要素(放射区、剪切唇)的特征 对于塑性材料,断口为纤维状、暗灰色 对于脆性材料,断口为结晶状
位置:自由表面 断面中心 非对称(次表面)
68
瞬断区面积越大,越靠近中心部位,工件过载程度越大 瞬断区面积越小,越靠近 边缘,工件过载程度越小
69
二、疲劳断口显微形貌特征
疲劳辉纹 1、定义:在光学显微镜、SEM或TEM下观察疲劳断口时,断口上细
小的、相互平行的具有规则间距的,与裂纹扩展方向垂直 的显微特征条纹
疲劳辉纹与疲劳条纹(贝纹线)的区别:
贝纹线是宏观特征线,因交变应力幅度变化或载荷停歇等造成的 辉纹是显微特征线,是一次交变应力循环裂纹尖端塑性钝化形成的
铝合金疲劳辉纹
(Nf > 105)的疲劳 低周疲劳:材料在反复变化的大应力或大应变作用下,使材
料的局部应力往往超过σ0.2 ,在断裂过程中产 生较大塑性变形,是一种短寿命(Nf < 102 — 105)的疲劳
47
接触疲劳:材料在较高接触压应力的作用下,经过多次应力 循环后,其接触面的局部区域产生小片或小块金 属剥落,形成麻点或凹坑,导致材料失效的现象
▲工程构件对疲劳抗力比对静载荷要敏感得多。其疲劳抗力不仅取 决于材料本身特性,而且与其形状、尺寸、表面质量、服役条件 环境等密切相关
疲劳裂纹扩展速率 模型
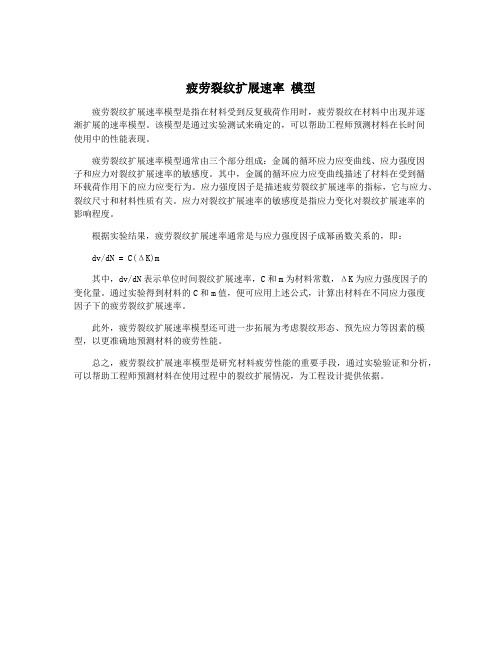
疲劳裂纹扩展速率模型
疲劳裂纹扩展速率模型是指在材料受到反复载荷作用时,疲劳裂纹在材料中出现并逐
渐扩展的速率模型。
该模型是通过实验测试来确定的,可以帮助工程师预测材料在长时间
使用中的性能表现。
疲劳裂纹扩展速率模型通常由三个部分组成:金属的循环应力应变曲线、应力强度因
子和应力对裂纹扩展速率的敏感度。
其中,金属的循环应力应变曲线描述了材料在受到循
环载荷作用下的应力应变行为。
应力强度因子是描述疲劳裂纹扩展速率的指标,它与应力、裂纹尺寸和材料性质有关。
应力对裂纹扩展速率的敏感度是指应力变化对裂纹扩展速率的
影响程度。
根据实验结果,疲劳裂纹扩展速率通常是与应力强度因子成幂函数关系的,即:
dv/dN = C(ΔK)m
其中,dv/dN表示单位时间裂纹扩展速率,C和m为材料常数,ΔK为应力强度因子的变化量。
通过实验得到材料的C和m值,便可应用上述公式,计算出材料在不同应力强度
因子下的疲劳裂纹扩展速率。
此外,疲劳裂纹扩展速率模型还可进一步拓展为考虑裂纹形态、预先应力等因素的模型,以更准确地预测材料的疲劳性能。
总之,疲劳裂纹扩展速率模型是研究材料疲劳性能的重要手段,通过实验验证和分析,可以帮助工程师预测材料在使用过程中的裂纹扩展情况,为工程设计提供依据。
裂纹顶端钝化锐化模型分析

1.疲劳裂纹扩展的方式
从第Ⅰ阶段向第Ⅱ阶段的转变,一般认为 是内部晶粒难于滑移造成的。当裂纹端部由约 束少的表面晶粒进入金属内部时,因内部晶粒 各向都受约束,滑移受到强烈抑制,从而使裂 纹由开始的剪切扩展方式转变为拉伸扩展方式。 由第Ⅰ阶段向第Ⅱ阶段转变的裂纹长度,决定 于材料和应力幅,一般不超过十分之几个毫米。
e-压应力达到最大值时,裂纹完全闭 合,应力回到0时又达到一个新的a状 态。
2.裂纹顶端钝化锐化模型
每循环加载一次,裂纹向前扩展一段距 离,这就是裂纹的扩展速率da/dN,同时在 断口上留下疲劳带,在拉压循环下钝化锐化, 这就是顶端钝化锐化模型的机理。
3.参考文献
[1]小林英男,有关疲劳裂纹扩展的最近研究.
[2]石凯凯,蔡力勋,包 陈,预测疲劳裂纹扩展的多种理论模型研究,2014. [3]中国知网 /kns/brief/default_result.aspx. /refbook/R200910074.html.
The End,Thank You!
裂纹顶端钝化锐化模型分析
1.疲劳裂纹扩展的方式
疲劳裂纹扩展可分为第Ⅰ阶段裂纹扩展和 第Ⅱ阶段裂纹扩展两个阶段。
第Ⅰ阶段:裂纹在滑移带上萌生以后,首 先沿着切应力最大的活性面扩展,具有一定的 结晶学特性。在单轴应力下,即沿着与外加应 力成接近45°角的滑移面扩展,这种切变型式 的裂纹扩展称为第Ⅰ阶段裂纹扩展。
a-循环开始时,交变应力为0,裂纹处 于闭合状态。
b-拉应力开始增加,裂纹张开,并且 裂纹顶端沿最大, 裂纹顶端变为圆形,停止扩展。并且 裂纹顶端由于塑性变形产生塑性钝化, 应力集中减少。
机械工程中的裂纹扩展与疲劳分析研究

机械工程中的裂纹扩展与疲劳分析研究在现代机械工程中,疲劳是一种十分常见的现象,它是金属材料在连续受到交变载荷作用后所出现的渐进性损伤过程。
疲劳问题一旦发生,往往会对机械系统的安全性和可靠性产生严重影响,因此,对疲劳问题的研究与分析成为机械工程领域中的一个重要课题。
裂纹扩展作为疲劳破坏的一种主要形式,是引起机械元件失效的关键因素之一。
因此,对裂纹扩展行为的研究具有重要意义。
一般而言,裂纹扩展行为可通过数学模型来预测和分析。
在研究机械工程中的裂纹扩展时,最常用的方法之一就是有限元法。
有限元法是一种通过将复杂结构分割为无限小的有限元素,以近似求解连续介质力学问题的数值方法。
通过有限元法对裂纹扩展行为进行建模和仿真,可以揭示裂纹扩展的机制和规律,为裂纹扩展的控制和预测提供依据。
此外,还可以通过实验手段对模型进行验证,从而提高数值模拟的准确性。
在裂纹扩展的机理研究中,马尔文等人提出了著名的“裂纹扩展力学”理论,即线弹性力学中的弹性应力场理论与线弹塑性力学中的应变能释放率理论相结合。
根据这一理论,裂纹扩展的驱动力主要来自应变能释放率,即裂纹前端的弹性应力能转化为其扩展所需的变形能。
根据裂纹形态的不同,裂纹扩展的方式也有所不同,常见的扩展方式包括沿单一平面、沿不同平面和远离应力场。
在疲劳分析研究中,我们也需要考虑到应力幅和寿命之间的关系。
疲劳寿命是指材料在一定应力幅范围内经历的循环次数,其与应力幅呈相反的指数关系。
通过疲劳试验,我们可以获得不同应力幅下的疲劳寿命数据,并通过拟合得到应力寿命曲线。
通过应力寿命曲线,我们可以预测在特定应力幅下的疲劳寿命,从而为机械元件的设计和优化提供指导。
除了裂纹扩展与疲劳分析的基础研究外,工程实践中还需要考虑到实际工况下的各种复杂因素。
例如,在航空航天领域,飞机机身结构处于动态载荷的作用下,高空环境下氧化腐蚀等因素也可能引起裂纹扩展和疲劳失效。
因此,我们需要进行更加全面和深入的研究,以便更好地应对复杂工况下的疲劳问题。
第5讲 疲劳裂纹扩展速率、影响因素、疲劳机理、工程塑料的疲劳、影响疲劳强度的主要因素
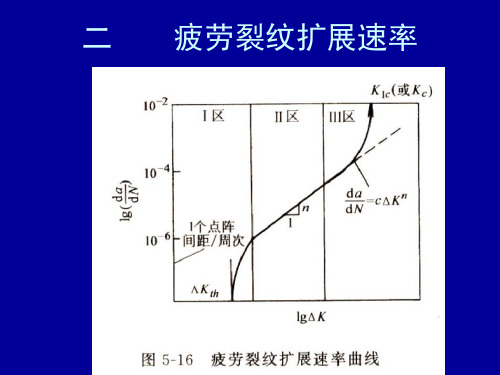
K th
lg(K)
C、m和Kth, 是描述疲劳裂
纹扩展性能的 基本参数。
常用材料的Paris关系可以查阅有关资料(如下表所示)
三 影响疲劳裂纹扩展速率的因素
1.应力比或平均应力的影响
S
Sm
O r=-1
r=-1/3
r=0 N
Sa
r增大
Sm>0
Sm<0 Sm=0
N
另外,考虑材料和环境的共同作用,有些资料 中的修正公式为
• 长期受交变应力或脉动应力作用,在应力集中区产 生。
• 从零件上划伤、刻槽、内凹拐角处及表面缺陷处。 • 红色光滑线条。
焊接缺陷
5. 温度的影响
Effect of Temperature on Fatigue
• Low-Temperature Fatigue • High-Temperature Fatigue
第七节、影响疲劳强度的主要因素
第五节 疲劳过程及机理
一.疲劳裂纹萌生过程及机理(裂纹形成 阶段,Ⅰ阶段)
对于宏观均匀的材料,零件上的疲劳裂纹 发展都是由表面裂纹的形核、微(短)裂纹的 扩展和长裂纹的扩展三个阶段所组成的
(一)滑移带开裂产生裂纹
(二) 相界面开裂产生裂纹
举 例
(三) 晶界开裂产生裂纹
在循环应力的作用下,位错在多晶 体晶界处塞积,当塞积位错和应力集中 得不到释放、应力峰值超过晶界强度时 就会在晶界处形成裂纹,造成晶界开裂 产生裂纹
回火温度越低、门 槛值越小,材料变 脆越容易产生裂纹
试验观察表明,疲劳裂纹扩展的三个区域对 应着三个不同的断裂机制。Ⅰ区的疲劳断口类似 解理断裂,由许多小断裂平面组成;Ⅱ区的疲劳 断口则对应着出现疲劳条纹;在高△K的Ⅲ区, 断口形貌则转向微孔的形成与聚合。
材料的疲劳性能

滑ห้องสมุดไป่ตู้带开裂
(1)驻留滑移带 在交变载荷作用下,永留或能再现的循环滑移
带,称为驻留滑移带。 通过位错的交滑移,使驻留滑移带加
(2)挤出脊和侵入沟 滑移带在表面加宽过程中,还会向前或向后移
动,形成挤出峰和挤入槽。 (3)循环过程中,峰、槽不断增加,增高(或变
深)。(柯垂耳-赫尔模型)。 孪晶处也易出现挤出峰和挤入槽。
陶瓷材料的疲劳破坏机理 静态疲劳、循环疲劳和动态疲劳 循环疲劳与金属疲劳具有相同含义,同属长期 变动应力作用下,材料的破坏行为 静态疲劳则相当于金属中的延迟断裂,即在一 定载荷作用下,材料耐用应力随时间下降的 现象 动态疲劳是在恒定速率加载条件下研究材料断 裂失效对加载速率的敏感性。
1、疲劳源 裂纹的萌生地;裂纹处在亚稳扩展过程中。 由于应力交变,断面摩擦而光亮。且表面加工硬化。 随应力状态及其大小的不同,可有一个或几个疲劳源。
2、疲劳区(贝纹区) 断面比较光滑,并分布有贝纹线。 循环应力低,材料韧性好,疲劳区大,贝纹线细、明显。 有时在疲劳区的后部,还可看到沿扩展方向的疲劳台阶
应力低(<σs ),所以也叫低应力疲劳。 低周疲劳( Nf {102-105}周次),由于断裂 应力水平高, ≥σs ,往往伴有塑性变形, 故称为高应力疲劳(或应变疲劳) 破坏原因 机械疲劳、腐蚀疲劳、热疲劳。
疲劳宏观断口的特征
断口拥有三个形貌不同的 区域:疲劳源、疲劳区、瞬断 区。
随材质、应力状态的不同, 三个区的大小和位置不同。 (表5-1)
疲劳造成的事故
1998年6月3日,德国一列高速列车在行驶中突然 出轨,造成100多人遇难身亡的严重后果。事后经过 调查,人们发现,造成事故的原因竟然是因为一节车 厢的车轮内部疲劳断裂而引起。从而导致了这场近 50年来德国最惨重铁路事故的发生。 2001年11月7日,四川宜宾南门大桥一断为三,造 成两死两伤。专家分析,断桥是多种因素共同作用的 结果:落后的工艺无法杜绝吊索生锈,而过度的金属 疲劳加速了大桥夭折。
疲劳裂纹扩展的微观阶段

第Ⅱ阶段裂纹扩展
当Δ K 值较大时, 裂纹顶端塑性区跨越 多个晶粒 ,此时裂纹 扩展沿两个滑移系统 同时或交替进行, Forsyth 将 这 种 双 滑 移 机制定义为裂纹的第 Ⅱ阶段扩展,左图为 第Ⅱ阶段裂纹扩展的 理想模型。
图2为铜单晶的第Ⅱ 阶段裂纹扩展实例, 可以看到两组滑移面。 单晶从第阶段扩展转 变为第阶段扩展时, 形成位错胞结构,同 时裂纹顶端的 PSB 消 失。许多工程合金在 该阶段产生疲劳辉纹。
机械系统Hale Waihona Puke 故障诊断疲劳裂纹扩展的微观阶段
疲劳裂纹扩展的微观阶段
材料的滑移特性和显微组织特征尺度、应力 水平及近顶端塑性区尺寸对疲劳裂纹扩展的微观 模式有强烈影响。根据其微观模式的不同,将疲 劳裂纹扩展分为两个阶段(第Ⅰ阶段裂纹扩展和 第Ⅱ阶段裂纹扩展)。
第Ⅰ阶段裂纹扩展
循环载荷对延性固体引起的裂纹扩展可以看作在裂纹顶 端近旁的滑移带内发生的急剧局部变形过程,该过程可通过 剪切脱粘而形成新裂纹面。当裂纹和裂纹顶端塑性变形区局 限在几个晶粒直径的范围时,裂纹主要沿主滑移系方向以纯 剪切方式扩展,下图为第Ⅰ阶段裂纹扩展的示意图。
参考文献
S.Suresh著.王中光等译.《材料的疲劳》/国防工
业出版社 陈建桥著.《材料强度学》/华中科技大学出版 社
谢谢
疲劳辉纹的形成与 第Ⅱ阶段裂纹扩展 可用Laird(1967)的裂 纹顶端钝化锐化模 型解释。
在拉伸应力作用下,裂纹顶端由于双滑移而发生塑性钝 化,该钝化过程可使裂纹向前扩展一段距离;如果远场应力 变为压应力,则裂纹顶端会重新锐化。由于压缩时的裂纹闭 合不能完全消除拉伸应力造成的钝化,裂纹会在随后的拉应 力下继续向前扩展一段距离,疲劳辉纹正是因为一个疲劳循 环中的裂纹净扩展导致的。
第十四讲--疲劳裂纹扩展

第十四讲疲劳裂纹扩展上节回顾Dugdale模型(带状屈服模型)裂纹尖端张开位移(COD)无限大板的COD,有限宽板的CODCOD准则J积分,J积分的守恒性,J积分准则平面应力断裂的R阻力曲线1.疲劳裂纹扩展速率疲劳裂纹扩展的定量表示用da/dN,称为裂纹扩展速率,表示每个循环裂纹长度的平均增量。
da/dN-ΔK曲线与S-N、ε-N曲线类似,描述疲劳裂纹扩展规律的曲线为da/dN-ΔK曲线只有在拉伸应力作用下裂纹才能扩展,则疲劳裂纹应力强度因子幅度定义为ΔK = K max-K min R > 0ΔK = K max R < 0基本da/dN-ΔK曲线:R = 0的da/dN-ΔK曲线双对数坐标下da/dN-ΔK曲线的形状疲劳裂纹扩展的三个区域Array一般情况下,da/dN-ΔK曲线在双对数坐标上可分为三个区域1区:低速率区,该区内ΔK的微小降低,da/dN急剧下降。
存在ΔK的一个下限值ΔK th,该值处裂纹扩展速率近似为零,ΔK th称为门槛值。
ΔK th受R的影响较大。
2区:中速裂纹扩展区,裂纹扩展速率一般在10-9~10-5m/C范围内。
中速裂纹扩展区的da/dN-ΔK在双对数坐标上近似为线性关系。
3区:高速扩展区,即K max K C时,裂纹快速扩展,其寿命通常不考虑。
其上限值以铅垂渐近线表示2.裂纹扩展速率公式1)低速率区一般是进行裂纹不扩展设计ΔK < ΔK th2)中速裂纹扩展区,Paris公式Paris 对具有中心穿透裂纹平板拉伸实验数据归纳, 对中速裂纹扩展区(2区)提出的经验关系式m K C dNda)(∆= C ,m :材料常数m 不随构件的形状和荷载性质(拉伸或弯曲)改变,C 与材料性能相关。
由于存在门槛值ΔKth ,Donahue 等(Donahue ,1972)建议如下修正公式m th K K C dNda)(∆-∆= 3)高速扩展区可由下式估计裂纹扩展速率从2区向3区转变的应力强度因子 ys T E K σ00637.0max =K maxT :R = 0时的最大循环应力作用下的应力强度因子3.da /dN 的理论公式 塑性钝化模型C. Laird (1967)的观测结果裂纹尖端载循环荷载下出现反复钝化和 重新尖锐化的交替过程。
海上风力发电风轮叶片材料疲劳裂纹扩展行为分析
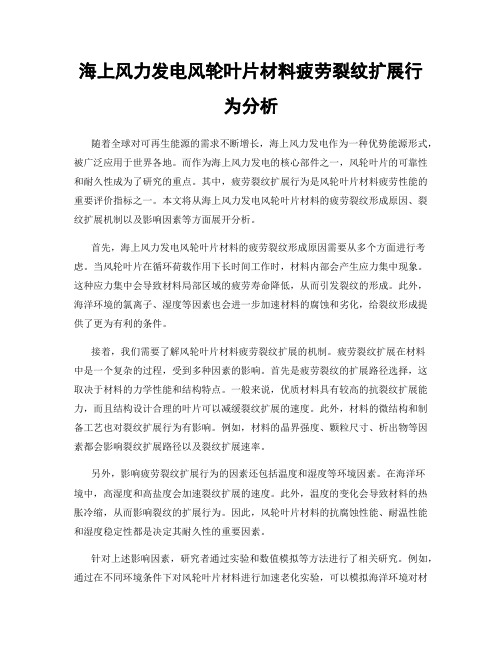
海上风力发电风轮叶片材料疲劳裂纹扩展行为分析随着全球对可再生能源的需求不断增长,海上风力发电作为一种优势能源形式,被广泛应用于世界各地。
而作为海上风力发电的核心部件之一,风轮叶片的可靠性和耐久性成为了研究的重点。
其中,疲劳裂纹扩展行为是风轮叶片材料疲劳性能的重要评价指标之一。
本文将从海上风力发电风轮叶片材料的疲劳裂纹形成原因、裂纹扩展机制以及影响因素等方面展开分析。
首先,海上风力发电风轮叶片材料的疲劳裂纹形成原因需要从多个方面进行考虑。
当风轮叶片在循环荷载作用下长时间工作时,材料内部会产生应力集中现象。
这种应力集中会导致材料局部区域的疲劳寿命降低,从而引发裂纹的形成。
此外,海洋环境的氯离子、湿度等因素也会进一步加速材料的腐蚀和劣化,给裂纹形成提供了更为有利的条件。
接着,我们需要了解风轮叶片材料疲劳裂纹扩展的机制。
疲劳裂纹扩展在材料中是一个复杂的过程,受到多种因素的影响。
首先是疲劳裂纹的扩展路径选择,这取决于材料的力学性能和结构特点。
一般来说,优质材料具有较高的抗裂纹扩展能力,而且结构设计合理的叶片可以减缓裂纹扩展的速度。
此外,材料的微结构和制备工艺也对裂纹扩展行为有影响。
例如,材料的晶界强度、颗粒尺寸、析出物等因素都会影响裂纹扩展路径以及裂纹扩展速率。
另外,影响疲劳裂纹扩展行为的因素还包括温度和湿度等环境因素。
在海洋环境中,高湿度和高盐度会加速裂纹扩展的速度。
此外,温度的变化会导致材料的热胀冷缩,从而影响裂纹的扩展行为。
因此,风轮叶片材料的抗腐蚀性能、耐温性能和湿度稳定性都是决定其耐久性的重要因素。
针对上述影响因素,研究者通过实验和数值模拟等方法进行了相关研究。
例如,通过在不同环境条件下对风轮叶片材料进行加速老化实验,可以模拟海洋环境对材料的影响,从而评估材料的性能和寿命。
另一方面,通过数学模型和有限元分析等方法,可以模拟材料中裂纹的扩展过程,并预测材料在特定工作条件下的寿命和可靠性。
此外,对于材料的选择和优化也是提高风轮叶片材料耐久性的重要途径。
第5章 疲劳断裂 第3节 疲劳裂纹扩展
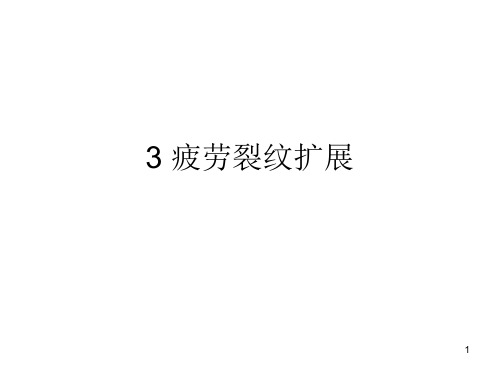
16
疲劳寿命的估算
采用稳定扩展阶段 寿命估算总寿命
17
环境对第2扩展阶段的影响
1968年发现的现象:在潮湿空气中铝合金 能够形成清晰的疲劳条纹,但在真空中却 不能形成疲劳条纹。 1983年发现在真空中铝合金疲劳裂纹扩展 速率低于潮湿空气条件 在2024Al,7075Al,TC4中也有类似现象。 上述材料共同的特点是在潮湿空气中能够 形成氧化膜。
23
新形成的裂纹面附近金属发生弹性恢复
可以解释应力比、瞬时过载对疲劳裂纹扩展的 24 影响
3.2.2 氧化物诱发的裂纹闭合
潮湿气氛在新形成的表面形成氧化物,氧化物诱发裂纹闭合
25
3.2.3 裂纹面粗糙诱发裂纹闭合
应力场强度因子低,裂纹张开角度小; 粗晶粒引起裂纹面呈现锯齿形状; 晶界,第二相,载荷突然变化引起裂纹偏折。
18
19
3.1.3 疲劳裂纹第3阶段扩展
断裂时裂纹长度取决于材料的断裂韧性 此时裂纹长度已经较大,因此δK较大,此时裂纹 扩展速率很快,试验环境对扩展速率影响不大。 断口上有疲劳条纹,还可能有韧窝或结理断裂刻 面,而韧窝或解理断裂对组织敏感,因此这一阶 段扩展速率对材料组织十分敏感。 从机制上有交变应力作用下的塑性锐化机制,也 有单调加载条件下的微孔聚集机制
9
材料的组织
欠时效态: 位错能够剪切GP区, 位错容易运动,滑 移容易进行;容易 形成单滑移;在遇 到晶界后滑移改变 方向;使得裂纹运 动方向改变。 过时效态: 位错只能绕过析出 相,形变时往往形 成双滑移,裂纹扩 展平直。
10
11
欠时效时材料强度较低,但门槛值大。 但材料的强度低,其疲劳强度(σ-1)小。 门槛值适用于疲劳裂纹扩展,尤其是低应力强度因子范围的疲 劳裂纹扩展。 疲劳强度主要适用于疲劳裂纹萌生。
化学技术中材料疲劳寿命的预测模型
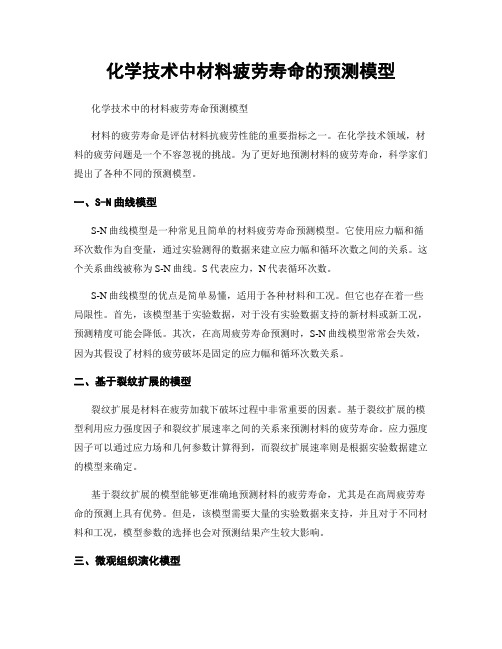
化学技术中材料疲劳寿命的预测模型化学技术中的材料疲劳寿命预测模型材料的疲劳寿命是评估材料抗疲劳性能的重要指标之一。
在化学技术领域,材料的疲劳问题是一个不容忽视的挑战。
为了更好地预测材料的疲劳寿命,科学家们提出了各种不同的预测模型。
一、S-N曲线模型S-N曲线模型是一种常见且简单的材料疲劳寿命预测模型。
它使用应力幅和循环次数作为自变量,通过实验测得的数据来建立应力幅和循环次数之间的关系。
这个关系曲线被称为S-N曲线。
S代表应力,N代表循环次数。
S-N曲线模型的优点是简单易懂,适用于各种材料和工况。
但它也存在着一些局限性。
首先,该模型基于实验数据,对于没有实验数据支持的新材料或新工况,预测精度可能会降低。
其次,在高周疲劳寿命预测时,S-N曲线模型常常会失效,因为其假设了材料的疲劳破坏是固定的应力幅和循环次数关系。
二、基于裂纹扩展的模型裂纹扩展是材料在疲劳加载下破坏过程中非常重要的因素。
基于裂纹扩展的模型利用应力强度因子和裂纹扩展速率之间的关系来预测材料的疲劳寿命。
应力强度因子可以通过应力场和几何参数计算得到,而裂纹扩展速率则是根据实验数据建立的模型来确定。
基于裂纹扩展的模型能够更准确地预测材料的疲劳寿命,尤其是在高周疲劳寿命的预测上具有优势。
但是,该模型需要大量的实验数据来支持,并且对于不同材料和工况,模型参数的选择也会对预测结果产生较大影响。
三、微观组织演化模型材料的微观组织演化与其疲劳寿命密切相关。
微观组织演化模型通过考虑材料中的晶体形变、位错与晶界的相互作用等因素,来预测材料的疲劳寿命。
这种模型通常基于晶体塑性理论和位错动力学,通过数值模拟来模拟材料在疲劳加载下的行为。
微观组织演化模型能够更深入地了解材料的疲劳机制,并对疲劳寿命进行准确预测。
然而,该模型的建立和计算较为复杂,且需要大量的计算资源和时间。
综上所述,化学技术中的材料疲劳寿命预测模型有多种选择。
选择适合的预测模型需要考虑材料的特性、工况以及可用的实验数据,并结合实际需求进行合理选择。
疲劳裂纹扩展规律的正切模型

疲 劳 裂 纹 扩 展 规 律 的正 切 模 型
杨 鹏 ,顾 学康
( 中国船舶科学研究 中心 ,无锡 24 8 10 2)
摘
要
为 了用解 析 方法合理地描 述疲 劳裂纹扩展 的三个 阶段 ,提 出 了一种新 的疲劳 裂纹扩展 模型—— 正切模
型。该模型驱动 力使 用应 力强度 因子幅值 A ,能够描 述裂纹扩展 的三 个阶段 ,且只有 四个参数需要确定 。 K
收稿 日期:21 0.2 01 8 ;修改稿收稿目期:21.1 1 . 2 01 . 10
中
国
造
船
学术 论 文
纹 扩展 速 率方 面 的差 别 , 以及 在根 据裂 纹 扩展 速率 计算 得 到 的 _ 曲线方 面 的差别 。 Ⅳ
1疲 劳裂 纹 扩 展 正 切 模 型
在 疲 劳裂 纹扩 展过 程 ,当扩 展速 率 / N 趋 向于零 时,裂 纹尖 端 的应力 强度 因子幅 值 A 趋 于 一 d K 个 极 小值 。这 个对 应 于零裂 纹 扩展速 度 的应 力 强度 因子 是一 个 与加 载应 力 比 有 关 的材料 参 数 ,称 为
通过非线性拟合确定疲劳裂 纹扩展正切模型 中的四个参数。 研究 了门槛值 和 失稳值 A f K 与应力 比 R的 关
系,以及四个参数对裂纹扩展速率 的影 响。最后 比较 了试验值 、九参数模 型和正切模型在疲劳裂纹扩展速率
曲线和裂纹扩展长度 变化 曲线等 方面的差 别,发现 正切模 型结果与试验数据较为吻合 。该模型描述的裂纹扩
展长度变化曲线能够较好地用于疲劳寿命评估。
关 键 词 :疲劳裂纹扩展;门槛值;正切模型;非线性拟合;敏感性分析 中图分 类号 :0 4. 36 2 文献标 识码 :A
预测疲劳裂纹扩展的多种理论模型研究_石凯凯_蔡力勋_包陈

1
I 型裂纹尖端循环应力应变场
基于材料低周疲劳行为预测 I 型疲劳裂纹扩展 的预测模型是由裂纹尖端循环载荷下的应力应变 场,继而结合裂纹尖端失效准则分析疲劳裂纹扩展 规律。现有的预测模型采用的循环应力应变场是基 于小范围屈服条件下的静应力应变场结合 RICE 的 塑性叠加法衍生得到的。 1.1 静态拉伸下的裂纹尖端应力应变场 目前可用于描述平面应力条件下裂尖区的应 力应变场主要有两类。 [18] [19] 一类是 KUJAWSKI 等 将 RICE 对 III 型裂 纹尖端的应力应变场,扩展应用至 I 型裂纹尖端小 范围屈服应力应变场
n /(1 n ) 2 K y 2 (1 n) π y r n /(1 n ) 1/(1 n ) 2 K K2 y y 2 2 (1 ) π n r y (1 n) π y r
在往复载荷作用下,构件均会发生疲劳破坏 。线 弹性断裂力学认为,疲劳失效分析中裂纹尖端附近 的应力场是由应力强度因子 K 控制的,所以裂纹在 疲劳载荷下的扩展行为可利用应力强度因子进行定 性和定量的描述。 基于材料低周疲劳行为预测 I 型疲劳裂纹扩展 行为,国外已经提出了多种模型,其模型从研究对 象的角度分为材料微观参量描述的裂纹扩展模 [4-5] 型 和材料宏观参量表征的裂纹扩展模型,如 [6-7] GLINKA 等 基于裂尖扩展区内常应变假定, [8-12] SKELTON KUJAWSKI 等 在裂尖引入钝化假定,
(1) 式中 σ, ε ——裂纹尖端应力和应变; σy, εy ——屈服强度和屈服应变; n——材料应变硬化指数; r ——离裂纹尖端的距离。
52
机
械 50 卷第 18 期期
机械结构的疲劳裂纹扩展特性分析与优化

机械结构的疲劳裂纹扩展特性分析与优化概述:机械结构的疲劳裂纹扩展特性是工程设计和使用过程中必须要考虑的重要问题之一。
疲劳裂纹扩展会导致结构强度下降,甚至引起严重事故。
因此,对机械结构的疲劳裂纹扩展特性进行深入分析和优化是至关重要的。
疲劳裂纹扩展的基本理论:疲劳裂纹扩展是指材料内部或表面的裂纹在受到交变载荷作用时逐渐扩展,在终止于结构破裂之前的过程。
裂纹扩展主要受到应力水平、载荷频率、环境条件以及材料的力学性能等因素的影响。
根据线弹性断裂力学理论,裂纹扩展速率可以用裂纹尖端位移增量和应力强度因子之间的关系来描述。
疲劳裂纹扩展的影响因素:1. 应力水平:应力水平是疲劳裂纹扩展的重要因素之一。
较高的应力水平会加速裂纹扩展过程,而较低的应力水平则会减缓裂纹扩展。
2. 载荷频率:载荷频率是指材料在受到交变载荷作用时的频率。
高频率下的载荷会加速裂纹扩展速度,而低频率下的载荷则会减缓裂纹扩展。
3. 环境条件:环境条件包括温度、湿度、腐蚀介质等因素。
某些环境条件下,如高温、高湿等,会导致材料的腐蚀和渗透,从而加速裂纹扩展。
4. 材料的力学性能:材料的强度、韧性和断裂韧性等力学性能会影响疲劳裂纹扩展的速率和路径。
疲劳裂纹扩展分析方法:1. 线性弹性断裂力学法:该方法假设材料具有线弹性行为,在结构的局部区域进行裂纹尖端位移和应力强度因子的计算。
2. 塑性力学法:该方法考虑材料的塑性行为,将材料的强度和塑性变形考虑在内,从而可以更准确地计算裂纹尖端位移和应力强度因子。
3. 数值模拟方法:数值模拟方法通过建立有限元分析模型,利用计算机进行裂纹扩展过程的模拟,得到裂纹尖端位移和应力强度因子。
疲劳裂纹扩展优化方法:1. 结构优化:通过改变结构的几何形状和尺寸,减少应力集中和应力激励,从而减缓裂纹扩展速率。
2. 材料优化:选择具有较高强度、韧性和断裂韧性的材料,可以增加结构的抵抗裂纹扩展的能力。
3. 加工和热处理优化:通过合理的加工和热处理工艺,降低材料中的缺陷和应力,减少裂纹扩展的可能性。
裂纹顶端钝化锐化模型分析

The End,Thank You!
e-压应力达到最大值时,裂纹完全闭 合,应力回到0时又达到一个新的a状 态。
2.裂纹顶端钝化锐化模型
每循环加载一次,裂纹向前扩展一段距 离,这就是裂纹的扩展速率da/dN,同时在 断口上留下疲劳带,在拉压循环下钝化锐化, 这男,有关疲劳裂纹扩展的最近研究.
第Ⅱ阶段:当微裂纹扩展到一个或两三个 晶粒的深度以后,裂纹的扩展方向开始由与外 加应力成接近45°角的方向逐渐转向与拉伸应 力相垂直的方向。这种拉伸型式的裂纹扩展称 为第Ⅱ阶段裂纹扩展,它不再有结晶学特性。
1.疲劳裂纹扩展的方式
从第Ⅰ阶段向第Ⅱ阶段的转变,一般认为 是内部晶粒难于滑移造成的。当裂纹端部由约 束少的表面晶粒进入金属内部时,因内部晶粒 各向都受约束,滑移受到强烈抑制,从而使裂 纹由开始的剪切扩展方式转变为拉伸扩展方式。 由第Ⅰ阶段向第Ⅱ阶段转变的裂纹长度,决定 于材料和应力幅,一般不超过十分之几个毫米。
裂纹顶端钝化锐化模型分析
1.疲劳裂纹扩展的方式
疲劳裂纹扩展可分为第Ⅰ阶段裂纹扩展和 第Ⅱ阶段裂纹扩展两个阶段。
第Ⅰ阶段:裂纹在滑移带上萌生以后,首 先沿着切应力最大的活性面扩展,具有一定的 结晶学特性。在单轴应力下,即沿着与外加应 力成接近45°角的滑移面扩展,这种切变型式 的裂纹扩展称为第Ⅰ阶段裂纹扩展。
2.裂纹顶端钝化锐化模型
由于第Ⅱ阶段裂纹扩展的速率和辉纹间距都比第Ⅰ阶段大 得多,因此对第Ⅱ阶段的扩展机制进行了较多的研究,有较多 的了解。Laird C.(莱尔德)通过对延性金属裂纹尖几何形状变 化的直接观察,提出了描述第Ⅱ阶段裂纹扩展过程的“裂纹顶 端钝化锐化模型”。
弹簧疲劳裂纹扩展第二阶段的机理
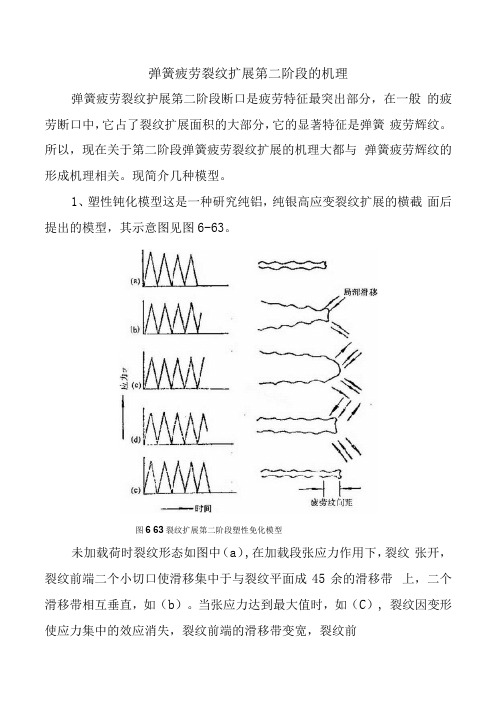
弹簧疲劳裂纹扩展第二阶段的机理弹簧疲劳裂纹护展第二阶段断口是疲劳特征最突出部分,在一般的疲劳断口中,它占了裂纹扩展面积的大部分,它的显著特征是弹簧疲劳辉纹。
所以,现在关于第二阶段弹簧疲劳裂纹扩展的机理大都与弹簧疲劳辉纹的形成机理相关。
现简介几种模型。
1、塑性钝化模型这是一种研究纯铝,纯银高应变裂纹扩展的横截面后提出的模型,其示意图见图6-63。
图6 63裂纹扩展第二阶段塑性免化模型未加载荷时裂纹形态如图中(a),在加载段张应力作用下,裂纹张开,裂纹前端二个小切口使滑移集中于与裂纹平面成45余的滑移带上,二个滑移带相互垂直,如(b)。
当张应力达到最大值时,如(C), 裂纹因变形使应力集中的效应消失,裂纹前端的滑移带变宽,裂纹前端钙化,呈半园状,在此过程中产生新的表面并使裂纹向前扩展。
此后,转入去载后辛周期,沿滑移带向相反方向滑移,图(d),裂纹前端相互挤压,在加载半周期中形成的新表面被压向裂纹平面,其中一部分发生折叠而形成新的切口(图e),结果造成一个新的弹簧疲劳辉纹,其间距为c。
如此循环往复,裂纹不断向前扩展,不断形成弹簧疲劳辉纹。
按照这个模型,裂纹是连续地向前扩展的,而且从本质上看,它是非晶体学的,另一方面,在多晶体中由于它并不要求按一定的晶体学平面扩展。
存在晶界与夹杂物,上述裂纹前端滑移带的对称性可能难以满足,同时,由一结晶学位向的关系,那些有可能滑移的滑移系处于与裂纹前端不相对称的角度上,这时,便按稍不同于上述理想的机构扩展,其过程如图6-64所示。
图&64非晶体学的延性疲劳坡形成机构首先,裂纹在压缩载荷作用下,常常会形成如图(a)那样不对称的二次裂纹。
当张应力作用时,裂纹前端的变形,大部分集中于最前面的那个裂纹处。
在最大张应力下,形成了如图(b)所示的形状。
最后在压缩载荷下,弹簧疲劳裂纹前端的形状如图(c),这与图631, (3)、(4)所实际观察到的弹簧疲劳辉纹(山、谷互不对应)相一致。