新型氯化石蜡介绍
氯化石蜡分子式

氯化石蜡分子式
(原创实用版)
目录
1.氯化石蜡的概述
2.氯化石蜡的分子式
3.氯化石蜡的用途
4.氯化石蜡的环保问题
正文
氯化石蜡是一种常见的化学物质,它是石蜡经过氯化反应而得到的产物。
氯化石蜡在工业领域有着广泛的应用,比如作为润滑剂、防水剂、阻燃剂等。
氯化石蜡的分子式为 C18H26Cl4,它是一种无色或淡黄色的粘稠液体,不溶于水,但可溶于许多有机溶剂。
它的制备过程通常是将石蜡和氯气在催化剂的作用下进行反应,生成氯化石蜡。
氯化石蜡的主要用途是在工业领域,如在润滑剂、防水剂、阻燃剂等方面的应用。
此外,它还可以用于制备农药、染料、树脂等。
然而,氯化石蜡的使用也带来了一些环保问题。
因为它是一种难降解的物质,所以在环境中的存在时间较长,可能会对环境造成污染。
第1页共1页。
短链氯化石蜡的用途

短链氯化石蜡的用途
短链氯化石蜡是一种广泛应用于化工、塑料、橡胶、油墨和涂料等领域的化学品。
它具有优异的物理化学性质和卓越的加工性能,因此被广泛用于以下领域:
1.塑料工业:短链氯化石蜡作为一种优秀的阻隔剂,可以提高塑料的防潮、防氧化、阻隔和耐热性能,延长塑料的使用寿命。
2.橡胶工业:短链氯化石蜡可以作为橡胶加工助剂,增强橡胶的流动性和加工性能,减少粘度和流动阻力,提高橡胶的耐磨性、耐候性和耐腐蚀性。
3.油墨工业:短链氯化石蜡可以作为油墨中的流平剂、降粘剂和增稠剂,提高油墨的附着力、耐水性和耐光性。
4.涂料工业:短链氯化石蜡可以作为涂料中的增塑剂、增稠剂和流平剂,提高涂料的耐磨性、耐候性和耐腐蚀性。
总之,短链氯化石蜡在化工、塑料、橡胶、油墨和涂料等领域具有广泛的用途和应用前景,是一种不可缺少的重要化学品。
- 1 -。
氯化石蜡介绍

氯化石蜡产品介绍1、产品介绍中文名称:氯化石蜡—52英文名称:Chloro Paraffin—52分子式:C15H26Cl6分子量:419性状:本品为浅黄色至黄色透明液体,不溶于水,不燃、不爆、无毒,不挥发,阻燃,能溶于许多溶剂,不溶于水及乙醇。
与聚氯乙烯、天然橡胶、聚氨酯等高聚物有较好的相溶性,绝缘性好,加热见光发生分解颜色加深。
受热超过一定温度时(通常为120℃)会缓缓分解,放出氯化氢气体。
用途:主要作为聚氯乙烯、天然橡胶、聚氨酯等高聚物的增塑剂,纤维防水浸渍剂,润滑油抗凝剂、抗极压剂。
2、市场概况(1)生产现状氯化石蜡是石蜡烃的氯化衍生物,与PVC树脂、天然橡胶等具有良好的相容性;尤其是氯化石蜡具有不燃性、介电性好等优点,使其成为一种独特的阻燃型增塑剂;还可以用作油类添加剂、纺织润滑剂、耐火防火纺织品涂覆剂、1、2丁腈橡胶与氯丁橡胶的黏接剂等。
氯化石蜡-52是一种浅黄色至黄色的油状黏稠液体,凝固点低于-20℃,溶于苯、醚,微溶于醇,不溶于水。
氯化石蜡-52主要用作阻燃剂和聚氯乙烯的助增塑剂,其挥发性低、电性能好,广泛应用于电缆料、地板、压延板材、塑胶质鞋类制品,也可用于橡胶制品;与聚氯乙烯等黏合剂制成磁漆,可用作防火涂料。
在我国增塑剂系列中,氯化石蜡是仅次于DOP、DBP 产量占第三位的品种。
氯化石蜡主要品种有氯蜡-52、氯蜡-42和氯蜡-70等,其中前两种产量占氯化石蜡的90%以上。
氯化石蜡作为辅助增塑剂和阻燃剂,广泛应用于塑料制品、涂料、输送带、塑胶等领域,消费结构为:增塑剂63%、润滑油15%、阻燃剂8%、橡胶2%、其他7%。
我国塑料增塑剂DOP、DBP价格高,许多塑料生产厂家转向价格相对较低的氯化石蜡。
氯化石蜡是企业平衡氯气的主要产品,所需的生产原料相对宽松易得,近年来氯化石蜡需求发展过快,国内市场竞争也较为激烈。
我国是氯化石蜡生产大国,2007年总产能为70万吨/年,产量48万吨/年。
氯化石蜡用途
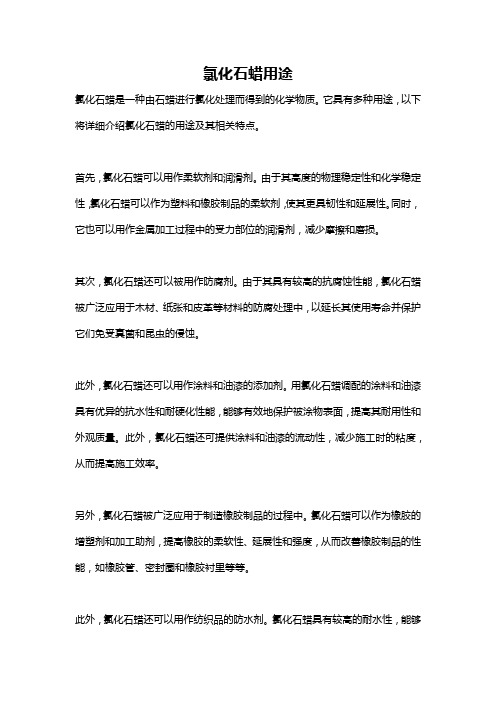
氯化石蜡用途氯化石蜡是一种由石蜡进行氯化处理而得到的化学物质。
它具有多种用途,以下将详细介绍氯化石蜡的用途及其相关特点。
首先,氯化石蜡可以用作柔软剂和润滑剂。
由于其高度的物理稳定性和化学稳定性,氯化石蜡可以作为塑料和橡胶制品的柔软剂,使其更具韧性和延展性。
同时,它也可以用作金属加工过程中的受力部位的润滑剂,减少摩擦和磨损。
其次,氯化石蜡还可以被用作防腐剂。
由于其具有较高的抗腐蚀性能,氯化石蜡被广泛应用于木材、纸张和皮革等材料的防腐处理中,以延长其使用寿命并保护它们免受真菌和昆虫的侵蚀。
此外,氯化石蜡还可以用作涂料和油漆的添加剂。
用氯化石蜡调配的涂料和油漆具有优异的抗水性和耐硬化性能,能够有效地保护被涂物表面,提高其耐用性和外观质量。
此外,氯化石蜡还可提供涂料和油漆的流动性,减少施工时的粘度,从而提高施工效率。
另外,氯化石蜡被广泛应用于制造橡胶制品的过程中。
氯化石蜡可以作为橡胶的增塑剂和加工助剂,提高橡胶的柔软性、延展性和强度,从而改善橡胶制品的性能,如橡胶管、密封圈和橡胶衬里等等。
此外,氯化石蜡还可以用作纺织品的防水剂。
氯化石蜡具有较高的耐水性,能够使纺织品表面形成一层防水薄膜,防止水分渗透,保持纺织品的干燥性和舒适性。
此外,氯化石蜡还可以用于制造蜡烛。
由于其具有不易燃烧的特点,氯化石蜡在制造蜡烛时可以起到调节燃烧速度和防止滴蜡的作用,使蜡烛更加安全和稳定。
最后,氯化石蜡还可以用于制造涂料和印刷油墨的添加剂,用于制造脱脂剂,用于制造医药产品以及化妆品的添加剂等等。
综上所述,氯化石蜡具有广泛的用途,包括柔软剂和润滑剂、防腐剂、涂料和油漆添加剂、橡胶制品、纺织品防水剂、蜡烛制造、涂料和印刷油墨添加剂等等。
随着科学技术的不断发展,氯化石蜡的应用领域将继续扩展,并在各个领域中发挥重要作用。
氯化石蜡的用途配方

氯化石蜡的用途配方
氯化石蜡是一种天然有机物质,其中含有氯、碳和氢等元素。
古代人们已经知道它的煮沸时能形成极坚硬的蜡,也可以用来做各种物品的保护和装饰。
现在,氯化石蜡的用途众多,经常被用来做汽车、家具和其他物品的保护层。
在做氯化石蜡的配方时,有一些这些原料很重要,可以有效增强蜡的硬度和抗污性:甲醛、月桂醇、二甲苯、邻羟基苯甲酸甲酯和胺类。
首先我们需要将甲醛与月桂醇、二甲苯和邻羟基苯甲酸甲酯混合,然后将其加入到胺类中,搅拌均匀,放入适当容器中,加入适量氯乙烷,然后放入加热器中加热至70℃,搅拌均匀即可。
氯化石蜡可以通过多种方式使用,它可以涂在物体表面,可以做饰面处理,也可以用于塑胶和金属表面处理,可以使表面光滑而又抗污。
此外,氯化石蜡还可以用于汽车玻璃保护罩,汽车底盘保护、建筑物装饰保护、家具保护以及铝锭制造等。
此外,氯化石蜡还可以用于各种家用用品的保护和装饰,比如皮鞋,家具,窗帘,垃圾桶,垃圾袋等。
它可以有效保护这些物体的外观,使其保持光亮,也可以减少零件损坏的概率。
氯化石蜡的另一大优点是它具有良好的抗蚀性和抗污性,能有效防护物体表面的腐蚀,提高表面硬度,降低物体被水和污渍侵蚀的概率,延长物体的使用寿命。
总之,氯化石蜡是一种非常好的保护和装饰材料,可以被用来做各种表面的保护和装饰,它的特点是它具有良好的硬度、抗蚀性和抗
污性,可以对物体表面进行有效的保护和延长其使用寿命。
只要按照正确的配方进行制作,氯化石蜡可以有效增强其硬度和抗污能力,使其具有更长久而有效的保护功能。
氯化石蜡-中国氯碱网

氯化石蜡产品生产、市场状况分析氯化石蜡是石蜡烃的氯化衍生物,具有低挥发性、阻燃、电绝缘性良好、价廉等优点,可用作阻燃剂和聚氯乙烯助增塑剂。
广泛用于生产电缆料、地板料、软管、人造革、橡胶等制品。
以及应用于涂料、润滑油等的添加剂。
在我国增塑剂系列中,氯化石蜡是仅次于DOP,DBP产量占第三位的品种。
一、国内生产情况目前国内有氯化石蜡生产厂100多家,其中千吨级以上规模约六十家,万吨级规模有十家,总生产能力30万吨/年,实际产量15万吨/年。
国内生产氯化石蜡品种主要有氯烃-42、52、70。
另外还有氯烃-13、30、40、45、55、60等。
其中氯烃-42、52占氯化石蜡总量80%以上。
国内氯烃-52、42普遍采用间歇热氯化工艺,近年来也有少数厂家采用光催化氯化工艺。
氯烃-70生产方法有四氯化碳溶剂法、水相悬浮法和本体法三种。
其中四氯化碳溶剂法又分为热氯化法和光氯化法。
水相悬浮氯化法多数厂家处于中试开发阶段。
我国是世界上的主要氯化石蜡生产国和出口国之一,出口的品种主要为氯烃-42、氯烃-52和氯烃-70,主要出口地区为东南亚和西欧。
出口量约1万吨/年。
近年受环保限制,出口量逐渐萎缩。
国内氯化石蜡主要生产企业产能一览表近年来,国内氯化石蜡市场竞争激烈。
一些规模大的生产企业,为提高市场占有率,不断扩大产销量,靠规模取胜。
同时,还有很多新建氯化石蜡生产厂纷纷建成投产。
在激烈市场竞争中,一些中小氯蜡生产厂由于规模小或质量差被市场淘汰。
近几年有20余家中小氯蜡厂或停产或倒闭。
还有部分企业开工率不足50%。
二、2003年市场状况今年以来全国氯化石蜡市场走势良好,价格运行平稳。
部分厂家产销量的所增加,库存量也大幅下降。
1-8月,全国氯化石蜡专业委员会氯蜡-42、52、70三个牌号产品,分别完成7039吨、69374吨和3300吨。
附:1-8月份氯蜡专业委员会会员单位52%氯蜡产销存一览表三、后市展望氯化石蜡作为辅助增塑剂及阻燃剂,在电缆料、胶带、塑胶跑道等领域广泛应用。
2024年环保氯化石蜡市场规模分析

2024年环保氯化石蜡市场规模分析引言环保氯化石蜡是一种环保型的化学材料,可广泛应用于塑料、润滑剂、橡胶和化妆品等行业。
本文旨在分析环保氯化石蜡市场的规模,并探讨其未来发展趋势。
环保氯化石蜡市场概述定义和分类环保氯化石蜡是一种以石蜡为主要原料,通过氯化反应获得的化合物。
根据不同的制备方法和产品特性,环保氯化石蜡可分为普通型和改性型两类。
市场趋势目前,环保氯化石蜡市场呈现出以下几个趋势:1.由于环保压力的增加和法规的加强,对传统石蜡产品的需求下降,环保氯化石蜡逐渐成为替代品;2.化妆品和食品包装行业对环保氯化石蜡的需求增加,推动了市场的发展;3.制造业的持续发展和市场竞争的加剧,促进了环保氯化石蜡市场的扩大。
2024年环保氯化石蜡市场规模分析市场规模根据市场研究机构的数据显示,2019年环保氯化石蜡市场规模达到XX亿元,预计到2025年将增长至XX亿元。
影响因素分析环保氯化石蜡市场规模的增长受到以下几个因素的影响:1.政策法规:环保氯化石蜡作为环保替代品,在政策法规的支持下,受到市场和企业的青睐;2.应用需求:食品包装、化妆品等行业对环保氯化石蜡的需求增加,拉动了市场规模的增长;3.技术进步:随着技术的发展,环保氯化石蜡的性能和质量不断提高,增强了市场竞争力。
市场份额据市场研究数据显示,目前环保氯化石蜡市场主要由几家大型企业垄断,其中厂商A占据市场份额约XX%,厂商B和C分别占据XX%和XX%的份额。
市场竞争格局目前,环保氯化石蜡市场竞争激烈,主要竞争因素包括产品质量、价格、服务和创新能力等。
大型企业通过技术优势、规模效应和品牌影响力等方面取得竞争优势,小型企业则通过差异化和专业化经营来提升竞争力。
环保氯化石蜡市场发展趋势展望市场机遇随着全球环保意识的提升和环保政策的加强,环保氯化石蜡市场将迎来更多机遇:1.市场需求增长:受到政策驱动和消费升级的影响,环保氯化石蜡的需求将进一步增加;2.创新产品开发:开发更高性能、更环保的环保氯化石蜡,满足市场需求,也为企业带来机遇。
氯化石蜡安全技术说明书
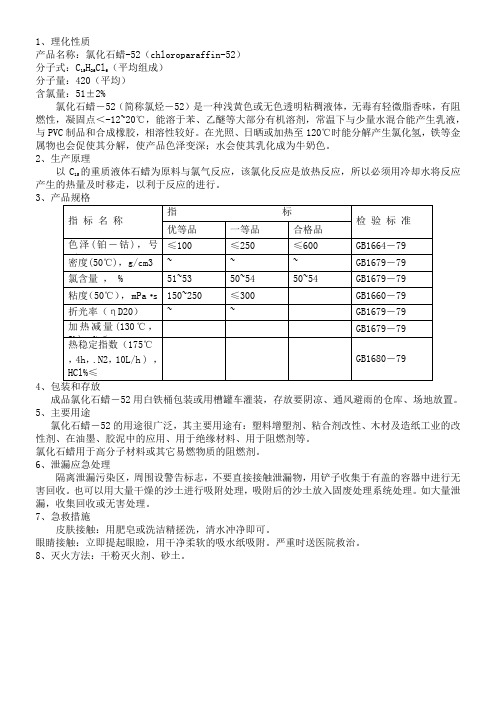
1、理化性质
产品名称:氯化石蜡-52(chloroparaffin-52)
分子式:C 15H 26Cl 6(平均组成)
分子量:420(平均)
含氯量:51±2%
氯化石蜡-52(简称氯烃-52)是一种浅黄色或无色透明粘稠液体,无毒有轻微脂香味,有阻燃性,凝固点<-12~20℃,能溶于苯、乙醚等大部分有机溶剂,常温下与少量水混合能产生乳液,与PVC 制品和合成橡胶,相溶性较好。
在光照、日晒或加热至120℃时能分解产生氯化氢,铁等金属物也会促使其分解,使产品色泽变深;水会使其乳化成为牛奶色。
2、生产原理
以C 15的重质液体石蜡为原料与氯气反应,该氯化反应是放热反应,所以必须用冷却水将反应
产生的热量及时移走,以利于反应的进行。
3
4 成品氯化石蜡-52用白铁桶包装或用槽罐车灌装,存放要阴凉、通风避雨的仓库、场地放置。
5、主要用途
氯化石蜡-52的用途很广泛,其主要用途有:塑料增塑剂、粘合剂改性、木材及造纸工业的改性剂、在油墨、胶泥中的应用、用于绝缘材料、用于阻燃剂等。
氯化石蜡用于高分子材料或其它易燃物质的阻燃剂。
6、泄漏应急处理
隔离泄漏污染区,周围设警告标志,不要直接接触泄漏物,用铲子收集于有盖的容器中进行无害回收。
也可以用大量干燥的沙土进行吸附处理,吸附后的沙土放入固废处理系统处理。
如大量泄漏,收集回收或无害处理。
7、急救措施
皮肤接触:用肥皂或洗洁精搓洗,清水冲净即可。
眼睛接触:立即提起眼睑,用干净柔软的吸水纸吸附。
严重时送医院救治。
8、灭火方法:干粉灭火剂、砂土。
简述氯化石蜡的增塑机理

简述氯化石蜡的增塑机理
氯化石蜡是一种特殊的增塑剂,其增塑机理如下:
1. 氯化石蜡可以作为辅助增塑剂使用,因为它单独使用时并无增塑作用。
但当它与主增塑剂一起使用时,能够显示出一种类似于增塑剂使塑料产生柔软性能的效果。
这主要是因为氯化石蜡能与主增塑剂共同作用,削弱聚合物分子链间的引力,增加了聚合物分子链的移动性,降低了聚合物分子链间的缠结,从而使树脂在较低的温度下就可发生玻璃化转变,增加了塑料的塑性。
2. 氯化石蜡对橡胶制品的增塑效果主要体现在提高了橡胶的可塑性。
这是因为氯化石蜡可以在橡胶分子链之间形成一层润滑薄膜,减少了分子链之间的相互吸引力,从而使橡胶分子链更容易滑动和移动。
这种润滑效果使得橡胶更加柔软,更易于加工成型,并且可以提高橡胶制品的延展性和伸长率。
此外,聚合物的分子结构也会影响聚合物分子链间的引力。
特别是聚合物分子链上各基团的性质,具有强性基团的聚合物易于成型,这时可以加入耐寒增塑剂。
耐寒增塑基团会与聚合物性基团相互作用,从而削弱了聚合物间的引力,达到了增塑的目的。
以上信息仅供参考,如需更准确的信息,建议查阅化学领域相关的书籍或咨询该领域的专家。
氯化石蜡52标准
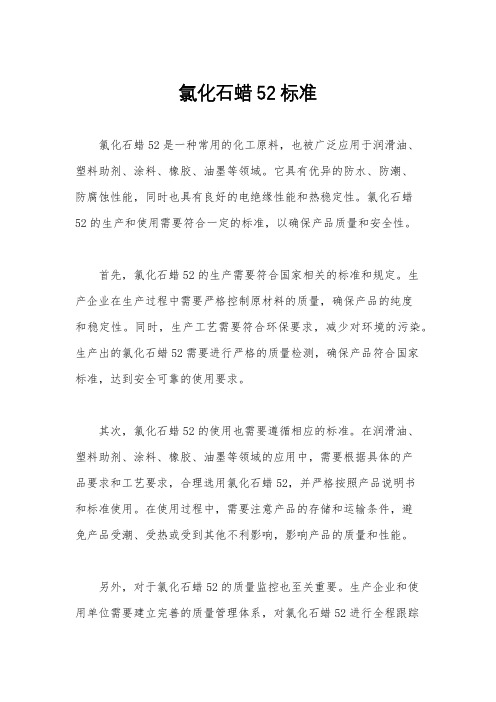
氯化石蜡52标准
氯化石蜡52是一种常用的化工原料,也被广泛应用于润滑油、
塑料助剂、涂料、橡胶、油墨等领域。
它具有优异的防水、防潮、
防腐蚀性能,同时也具有良好的电绝缘性能和热稳定性。
氯化石蜡
52的生产和使用需要符合一定的标准,以确保产品质量和安全性。
首先,氯化石蜡52的生产需要符合国家相关的标准和规定。
生
产企业在生产过程中需要严格控制原材料的质量,确保产品的纯度
和稳定性。
同时,生产工艺需要符合环保要求,减少对环境的污染。
生产出的氯化石蜡52需要进行严格的质量检测,确保产品符合国家
标准,达到安全可靠的使用要求。
其次,氯化石蜡52的使用也需要遵循相应的标准。
在润滑油、
塑料助剂、涂料、橡胶、油墨等领域的应用中,需要根据具体的产
品要求和工艺要求,合理选用氯化石蜡52,并严格按照产品说明书
和标准使用。
在使用过程中,需要注意产品的存储和运输条件,避
免产品受潮、受热或受到其他不利影响,影响产品的质量和性能。
另外,对于氯化石蜡52的质量监控也至关重要。
生产企业和使
用单位需要建立完善的质量管理体系,对氯化石蜡52进行全程跟踪
和监控,确保产品的质量稳定和可靠。
定期对产品进行抽样检测,及时发现和解决质量问题,保障产品的安全性和可靠性。
总之,氯化石蜡52作为一种重要的化工原料,在生产和使用过程中需要严格遵循相关的标准和规定,确保产品质量和安全性。
只有这样,才能更好地发挥氯化石蜡52的优异性能,为各个领域的应用提供可靠的保障。
氯化石蜡
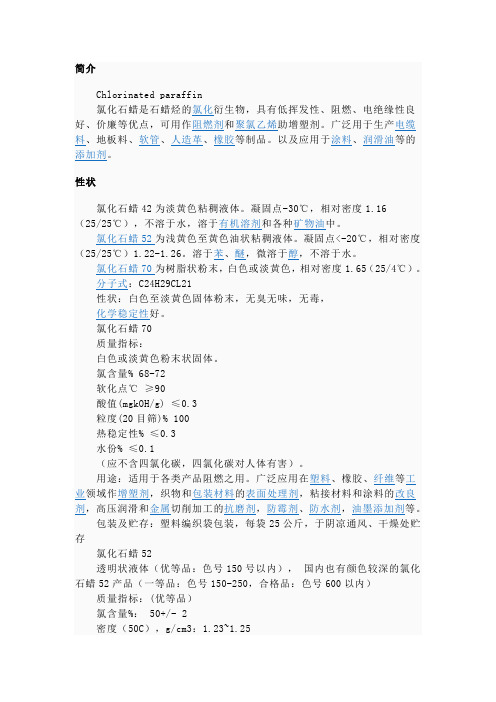
Chlorinated paraffin
氯化石蜡是石蜡烃的氯化衍生物,具有低挥发性、阻燃、电绝缘性良好、价廉等优点,可用作阻燃剂和聚氯乙烯助增塑剂。广泛用于生产电缆料、地板料、软管、人造革、橡胶等制品。以及应用于涂料、润滑油等的添加剂。
性状
氯化石蜡42为淡黄色粘稠液体。凝固点-30℃,相对密度1.16(25/25℃),不溶于水,溶于有机溶剂和各种矿物油中。
粘度(50C),mpa.s:150-250
热稳定指数(175C,4h氯氮(10L /h),HCL%≤: 0.1
用途:主要用于聚氯乙烯制品辅助增塑剂和润滑油的添加剂等。
包装:镀锌桶包装,净重250KG(也有塑料桶包装的)
储存:于阴凉通风、干燥处贮存。
生成方法
将计量的液体石蜡加入反应釜中,在搅拌下滴加氯化亚砜,回流5~7h后,常压回收过量的氯化亚砜。用水、NaOH水溶液依次洗涤减压脱水至含水量小于2%,出料为成品。[1]
质量指标:
白色或淡黄色粉末状固体。
氯含量% 68-72
软化点℃≥90
酸值(mgkOH/g)≤0.3
粒度(20目筛)% 100
热稳定性%≤0.3
水份%≤0.1Βιβλιοθήκη (应不含四氯化碳,四氯化碳对人体有害)。
用途:适用于各类产品阻燃之用。广泛应用在塑料、橡胶、纤维等工业领域作增塑剂,织物和包装材料的表面处理剂,粘接材料和涂料的改良剂,高压润滑和金属切削加工的抗磨剂,防霉剂、防水剂,油墨添加剂等。
包装及贮存:塑料编织袋包装,每袋25公斤,于阴凉通风、干燥处贮存
氯化石蜡52
透明状液体(优等品:色号150号以内),国内也有颜色较深的氯化石蜡52产品(一等品:色号150-250,合格品:色号600以内)
短链氯化石蜡的用途

短链氯化石蜡的用途
短链氯化石蜡是一种石蜡衍生产品,可以通过将石蜡以一定的工艺方法进行氯化处理后得到。
它的分子结构中含有大量的氯原子,使得其物理化学性质发生了明显的变化。
在实际的应用中,短链氯化石蜡被广泛用于以下方面:
1.塑料加工中的添加剂
短链氯化石蜡具有较好的增塑效果,能够提高塑料的柔软性、延展性和可加工性,使得塑料制品更容易加工成型。
因此,短链氯化石蜡常常被用作塑料加工中的添加剂,例如聚乙烯、聚丙烯、聚氯乙烯、聚苯乙烯等。
2.涂料和油漆中的溶剂
短链氯化石蜡具有较好的溶解性质,可以在涂料和油漆中作为低粘度的溶剂使用。
通过添加短链氯化石蜡,不仅可以降低涂料的粘度,提高其流动性和涂覆性,还可以增加其附着力和耐候性,使得涂料具有更好的性能和持久性。
4.蜡烛和照明用品中的添加剂
短链氯化石蜡在蜡烛和照明用品中也有应用。
它可以用作蜡烛的增稠剂,使得蜡烛的凝固特性得到改善,提高其加工性能和燃烧时间。
此外,短链氯化石蜡还可以作为照明灯泡的填充材料,可以防止灯泡受到外部冲击或挤压而破裂。
氯化石蜡 标准

氯化石蜡标准氯化石蜡啊,这可是个挺有趣的东西呢。
一、氯化石蜡是啥。
氯化石蜡就是一种化学物质啦。
它是石蜡烃的氯化衍生物,简单来说,就是在石蜡的基础上进行了一些化学变化,加进去了氯原子。
它的样子呢,一般是白色或者浅黄色的固体,当然也有一些是比较粘稠的液体状态。
这种物质有很多不同的型号,就像不同的兄弟姐妹一样,各有各的特点。
比如说,有的氯化石蜡含氯量高一些,有的就低一点,这就导致了它们在各种性能上有差别。
二、氯化石蜡的用途。
氯化石蜡的用途可广泛了。
在塑料行业里,它就像一个小助手一样。
它可以作为增塑剂使用,能让塑料变得更加柔软,可塑性更强。
想象一下,如果塑料是一个很僵硬的东西,加了氯化石蜡之后,就像给它做了一场按摩,让它变得柔软起来,这样就可以更好地被加工成各种形状啦,像我们日常用的塑料薄膜、塑料管材之类的东西,很多都有氯化石蜡的功劳呢。
在橡胶行业,氯化石蜡也没闲着。
它可以提高橡胶的阻燃性和耐油性。
比如说汽车的一些橡胶部件,要是没有氯化石蜡帮忙,可能就很容易着火或者被油腐蚀,那可就危险啦。
有了氯化石蜡,就像是给橡胶部件穿上了一层保护衣,让它们可以更安全、更持久地工作。
在涂料行业,氯化石蜡也扮演着重要的角色。
它能够增强涂料的附着力和耐磨性。
就好比是给墙面上的涂料打了一针强心剂,让涂料紧紧地附着在墙面上,不容易脱落,而且还能经受住一些摩擦和磨损,让墙面长时间保持美观。
三、氯化石蜡的标准。
氯化石蜡的标准可是很重要的哦。
这就像是给氯化石蜡制定的一套规则,告诉大家什么样的氯化石蜡才是合格的。
从纯度方面来说,不同用途的氯化石蜡对纯度有不同的要求。
如果纯度不够,那在使用的时候就可能会出现各种各样的问题。
比如说在塑料增塑的时候,纯度不够的氯化石蜡可能就没办法让塑料达到理想的柔软度。
含氯量也有标准。
含氯量过高或者过低都不行。
含氯量过高可能会导致一些安全隐患,比如在燃烧的时候可能会释放出更多有害物质;含氯量过低呢,又可能影响到它的性能发挥,像在阻燃方面就可能效果不好。
新型氯化石蜡介绍

高粘度氯化石蜡介绍4万吨/年氯化石蜡项目2017-3—264万吨/年高粘度氯化石蜡项目介绍1o传统氯化石蜡性能、用途与生产技术介绍:1.1、慨况:由链长C|2〜C|6的正构烷烧,与氯气多级反应后,形成含氯量在50〜54%的氯化石蜡,简称氯妙一52,世界上最早是在1910年由贝尔公司试制成功,于1930年才形成具有一定应用范围的化工产品,流通于国际市场•此后,几近一个世纪的应用开发和使用实践后,这一以其广泛用途和良好的使用性能为基础的产品,现在还正在不断地扩大自己的市场地位。
特别是作为增塑剂在PVC塑料制品配方上有较大比例的应用,使得其增长速度几乎等同于PVC的增长。
所以,氯妙-52是一个具有较长经济寿命、较大市场基础,并具有较好经济效益的精细化工产品。
我国大陆直到六十年代才陆续开发而建成氯烧一52的生产装置。
最早是沈阳永新化工厂,稍迟是上海氯碱总厂和武汉葛店化工厂。
他们都是氯碱厂。
进入上世纪就是年代,随着中国经济的飞速发展,氯化石蜡产能和技术跟随着主要的石油化工产品的发展而高速发展。
生产厂家也由氯碱行业延伸到专业化的个体户、私营民营企业。
产品从单一的标准产品演变成多牌号多用途。
1. 2、氯化石蜡一52的主要用途:1.2.1、增塑剂:最早我国只用固体皂蜡为原料生产的氯化石蜡一42,用于辅助增塑剂,由于它粘度大,分散性和捏合性都差,与塑料制品的相溶性亦差,产出的塑料制品不理想。
所以大部份用户都改用C15 精重液蜡生产的氯化石蜡-52。
由于它具有低挥发性、难燃、粘度低、色泽好等优点,近年来逐渐发展为作为主要增塑剂应用于塑料加工,从而降低了塑料制品的生产成本,使得颇具竞争力。
1. 2. 2、防滑剂:氯化石蜡渗混入无规聚丙稀树脂当中,可以制造防滑包装材料。
1. 2-3,阻燃剂:电线包皮,耐热塑料制品,煤碳输送带,防水帆布, 防火涂料均需用氯化石蜡一52做阻燃剂参与配方。
1. 2. 4、静电消除剂:纺织品用氯化石蜡处理后,不仅能防火,防水,抗辐射,还可作静电消除剂.1. 2. 5、切削油添加剂:高速高硬切削机床,在其冷却油中配以氯化石蜡一52,就可以大幅度提高切削速度,从而提高了车床的工作效率和切削性能,并因此提高了加工工件的光洁度,同时还可大大延长了切削刃具的使用寿命。
氯化石蜡MSDS化学品安全说明书
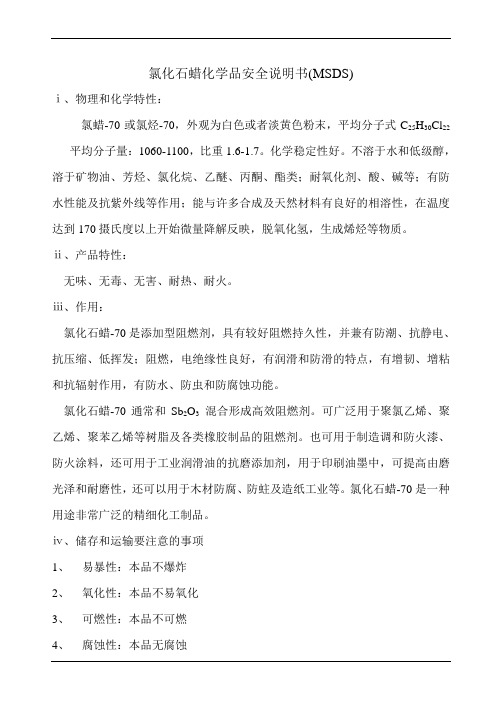
氯化石蜡化学品安全说明书(MSDS)ⅰ、物理和化学特性:氯蜡-70或氯烃-70,外观为白色或者淡黄色粉末,平均分子式C25H30Cl22平均分子量:1060-1100,比重1.6-1.7。
化学稳定性好。
不溶于水和低级醇,溶于矿物油、芳烃、氯化烷、乙醚、丙酮、酯类;耐氧化剂、酸、碱等;有防水性能及抗紫外线等作用;能与许多合成及天然材料有良好的相溶性,在温度达到170摄氏度以上开始微量降解反映,脱氧化氢,生成烯烃等物质。
ⅱ、产品特性:无味、无毒、无害、耐热、耐火。
ⅲ、作用:氯化石蜡-70是添加型阻燃剂,具有较好阻燃持久性,并兼有防潮、抗静电、抗压缩、低挥发;阻燃,电绝缘性良好,有润滑和防滑的特点,有增韧、增粘和抗辐射作用,有防水、防虫和防腐蚀功能。
氯化石蜡-70通常和Sb2O3混合形成高效阻燃剂。
可广泛用于聚氯乙烯、聚乙烯、聚苯乙烯等树脂及各类橡胶制品的阻燃剂。
也可用于制造调和防火漆、防火涂料,还可用于工业润滑油的抗磨添加剂,用于印刷油墨中,可提高由磨光泽和耐磨性,还可以用于木材防腐、防蛀及造纸工业等。
氯化石蜡-70是一种用途非常广泛的精细化工制品。
ⅳ、储存和运输要注意的事项1、易暴性:本品不爆炸2、氧化性:本品不易氧化3、可燃性:本品不可燃4、腐蚀性:本品无腐蚀5、毒性:本品不属于有毒产品6、辐射性:本品无辐射7、结论:本品无危害ⅴ、运输的建议1、主要注意:氯化石蜡-70 不属于危险品。
2、运输等级:普通货物运输。
3、兼容性:禁止与重氧物质一起运输。
4、特殊要求:远离有火和高温的地方5、溢出后的防范:把货物搬离火, 清理泄露的物品,防止粉尘碰到皮肤和眼睛。
戴手套把废弃物放到封闭的罐中等待处理。
6、消防:每个人必须带呼吸器,穿防护服。
站在背风的方向。
消防设备:泡沫、干粉、二氧化碳、雾水。
7、急救措施:进到眼睛里,用清水立即冲洗,如果长时间感觉不适,立即就医。
接触皮肤:脱去弄脏的衣服,用清水清洗接触处。
氯化石蜡沸点

氯化石蜡沸点
(最新版)
目录
1.氯化石蜡的概述
2.氯化石蜡的沸点特性
3.氯化石蜡沸点的应用领域
4.氯化石蜡的安全性和环保性
正文
氯化石蜡是一种常见的化学物质,它是通过将石蜡与氯气进行反应而得到的。
氯化石蜡具有许多优良的特性,如高熔点、低挥发性和良好的电绝缘性,因此在多个领域都有广泛的应用。
氯化石蜡的沸点是一个重要的物理特性。
它的沸点通常在 120 摄氏度到 180 摄氏度之间,这使得氯化石蜡在常温下是固态,但在高温下又可以变为液态。
这种特性使得氯化石蜡在工业生产中具有很大的灵活性。
氯化石蜡沸点的特性使其在许多领域都有应用。
比如,在涂料工业中,氯化石蜡可以作为增稠剂和防水剂,提高涂料的性能。
在建筑行业,氯化石蜡可以用于制造防水材料和保温材料。
此外,氯化石蜡还广泛应用于塑料、橡胶和印刷油墨等行业。
尽管氯化石蜡在许多领域都有应用,但它的安全性和环保性也引起了人们的关注。
长期接触氯化石蜡可能会对人体健康产生影响,因此在使用氯化石蜡时需要注意防护。
此外,氯化石蜡的生产和处理过程可能会对环境造成污染,因此需要采取相应的环保措施。
总的来说,氯化石蜡是一种重要的化学物质,它的沸点特性使其在多个领域都有广泛的应用。
第1页共1页。
2023年环保氯化石蜡行业市场分析现状
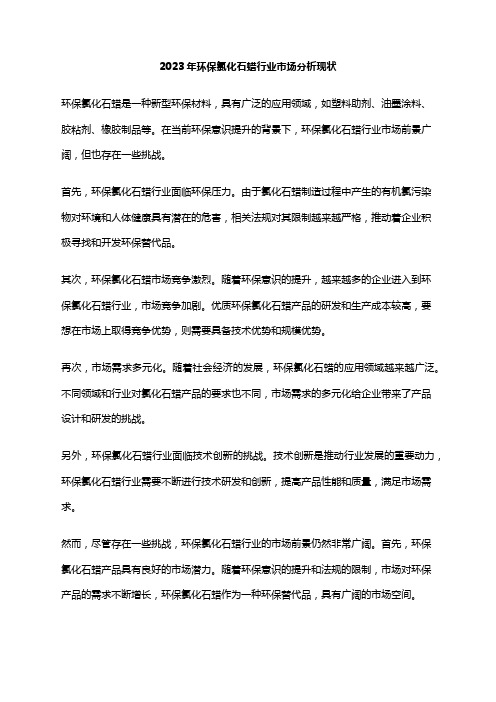
2023年环保氯化石蜡行业市场分析现状环保氯化石蜡是一种新型环保材料,具有广泛的应用领域,如塑料助剂、油墨涂料、胶粘剂、橡胶制品等。
在当前环保意识提升的背景下,环保氯化石蜡行业市场前景广阔,但也存在一些挑战。
首先,环保氯化石蜡行业面临环保压力。
由于氯化石蜡制造过程中产生的有机氯污染物对环境和人体健康具有潜在的危害,相关法规对其限制越来越严格,推动着企业积极寻找和开发环保替代品。
其次,环保氯化石蜡市场竞争激烈。
随着环保意识的提升,越来越多的企业进入到环保氯化石蜡行业,市场竞争加剧。
优质环保氯化石蜡产品的研发和生产成本较高,要想在市场上取得竞争优势,则需要具备技术优势和规模优势。
再次,市场需求多元化。
随着社会经济的发展,环保氯化石蜡的应用领域越来越广泛。
不同领域和行业对氯化石蜡产品的要求也不同,市场需求的多元化给企业带来了产品设计和研发的挑战。
另外,环保氯化石蜡行业面临技术创新的挑战。
技术创新是推动行业发展的重要动力,环保氯化石蜡行业需要不断进行技术研发和创新,提高产品性能和质量,满足市场需求。
然而,尽管存在一些挑战,环保氯化石蜡行业的市场前景仍然非常广阔。
首先,环保氯化石蜡产品具有良好的市场潜力。
随着环保意识的提升和法规的限制,市场对环保产品的需求不断增长,环保氯化石蜡作为一种环保替代品,具有广阔的市场空间。
其次,环保氯化石蜡产品的应用领域广泛。
氯化石蜡产品在传统领域中的应用已经非常广泛,如塑料助剂、油墨涂料、胶粘剂等。
同时,随着新兴产业的发展,氯化石蜡产品在新领域的应用也在不断扩大,如新能源领域、材料领域等,这为环保氯化石蜡行业提供了更多的市场机会。
再次,环保氯化石蜡行业发展潜力巨大。
目前,国内外环保氯化石蜡行业市场规模庞大,但仍然存在较大的发展空间。
当前国内环保氯化石蜡行业规模相对较小,企业数量较少,市场竞争相对较低,这为企业提供了更好的发展机会。
综上所述,环保氯化石蜡行业市场存在一些挑战,但其市场前景仍然非常广阔。
液蜡与氯化石蜡简介

液蜡及氯化石蜡简介1、前言石油蜡类产品是一类附加值很高的石油产品,由于其具有许多特殊的理化性质,被广泛应用于社会生活各个领域。
随着科学技术的不断发展,对石油蜡类产品的要求愈来愈高,一方面对产品质量要求不断提高,另一方面由于应用领域不断拓宽,石油蜡类产品的功能用途也在不断扩大。
液蜡又称石蜡油,无色、无臭、无味,无萤光的油状液体,由重油经减压蒸馏而获得。
熔点在40℃以下的从C10到C18的各种正构烷烃组成的混合物。
主要用途是可以做为生产氯化石蜡的原料,还有洗涤剂原料、化妆品、日用品稀释剂、溶剂等。
2、液蜡产品及生产工艺液蜡产品有三种,即C10-C13正构烷烃(轻蜡I);C11-C14正构烷烃(轻蜡II)和C14-C17重液蜡;C9以下为轻蜡;C17以上为重蜡。
液蜡下游产品氯化石蜡是石蜡经氯化后所得产品,是石蜡烃的氯化衍生物。
适用于各类产品阻燃之用,应用在塑料、橡胶、纤维等工业领域作增塑剂,织物和包装材料的表面处理剂,粘接材料和涂料的改良剂,高压润滑和金属切削加工的抗磨剂,防霉剂、防水剂,油墨添加剂等。
广泛用于生产电缆料、地板料、软管、人造革、橡胶等制品。
我国重液蜡的生产有分子筛脱蜡(典型的分子筛脱蜡工艺有Molex法和ISO 一SIV法)和异丙醇-尿素脱蜡(IUDW)两种生产工艺。
此外也有用溶剂脱蜡和压榨脱蜡法生产一部分质量较低的液蜡。
3、液蜡主要生产工艺对比分析、分子筛法和尿素脱蜡法实验对比分析(1)1975年大岛洋三经过试验室认真研究证明,异丙醇-尿素脱蜡的液蜡比分子筛脱蜡纯度高。
(2)分子筛脱蜡能耗较大,因现在分子筛催化剂价格昂贵,消耗量大,每生产1t液蜡产品能耗万MJ左右,而异丙醇-尿素脱蜡能耗为万MJ左右。
(3)异丙醇-尿素脱蜡不需要预处理,即可生产重液蜡,也可生产轻液蜡,对市场的适应性更强。
(4)异丙醇-尿素脱蜡工艺流程较复杂,但投资费用低,建设周期短,在工艺上较成熟。
、分子筛法和尿素脱蜡法技术经济对比分析目前国内分子筛脱蜡和尿素脱蜡生产液蜡主要技术经济指标比较见表1和表2。
氯化石蜡化学品安全说明书
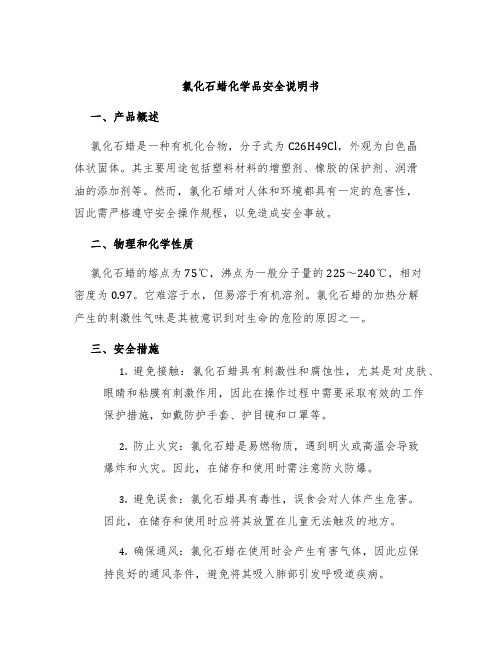
氯化石蜡化学品安全说明书一、产品概述氯化石蜡是一种有机化合物,分子式为C26H49Cl,外观为白色晶体状固体。
其主要用途包括塑料材料的增塑剂、橡胶的保护剂、润滑油的添加剂等。
然而,氯化石蜡对人体和环境都具有一定的危害性,因此需严格遵守安全操作规程,以免造成安全事故。
二、物理和化学性质氯化石蜡的熔点为75℃,沸点为一般分子量的225~240℃,相对密度为0.97。
它难溶于水,但易溶于有机溶剂。
氯化石蜡的加热分解产生的刺激性气味是其被意识到对生命的危险的原因之一。
三、安全措施1.避免接触:氯化石蜡具有刺激性和腐蚀性,尤其是对皮肤、眼睛和粘膜有刺激作用,因此在操作过程中需要采取有效的工作保护措施,如戴防护手套、护目镜和口罩等。
2.防止火灾:氯化石蜡是易燃物质,遇到明火或高温会导致爆炸和火灾。
因此,在储存和使用时需注意防火防爆。
3.避免误食:氯化石蜡具有毒性,误食会对人体产生危害。
因此,在储存和使用时应将其放置在儿童无法触及的地方。
4.确保通风:氯化石蜡在使用时会产生有害气体,因此应保持良好的通风条件,避免将其吸入肺部引发呼吸道疾病。
5.安全处理废弃物:在处理废弃物时,需遵守环保相关规定,采取安全的处理方式。
四、急救措施1.吸入氯化石蜡的气味时,应立即移动到通风良好的地方,保持呼吸顺畅,如有呼吸困难,应立即送往医院抢救。
2.皮肤接触氯化石蜡时,应立即用大量清水冲洗至少15分钟,并去掉被污染的衣物和鞋袜,立即送往医院治疗。
3.如果不慎将氯化石蜡误入口中,应立即用大量清水漱口,并送往医院治疗。
五、包装和储存氯化石蜡的包装应符合国家规定的危险化学品包装标准。
在储存时,应避免阳光直射、高温、潮湿和火源。
储存过程中需要定期检查包装是否完好,是否存在泄漏等危险。
六、环境保护在使用氯化石蜡时,应遵守国家法律法规、规范、标准和行业标准,避免对环境造成污染。
废弃氯化石蜡应安全处理,避免直接倾倒到地面、水源、下水道等处,以免对环境造成影响。
- 1、下载文档前请自行甄别文档内容的完整性,平台不提供额外的编辑、内容补充、找答案等附加服务。
- 2、"仅部分预览"的文档,不可在线预览部分如存在完整性等问题,可反馈申请退款(可完整预览的文档不适用该条件!)。
- 3、如文档侵犯您的权益,请联系客服反馈,我们会尽快为您处理(人工客服工作时间:9:00-18:30)。
高粘度氯化石蜡介绍/年氯化石蜡项目4万吨2017-3-26年高粘度氯化石蜡项目介绍/万吨4.1.传统氯化石蜡性能、用途与生产技术介绍:1.1、慨况:由链长C~C的正构烷烃,与氯气多级反应后,形成含1612氯量在50~54%的氯化石蜡,简称氯烃-52,世界上最早是在191O年由贝尔公司试制成功,于1930年才形成具有一定应用范围的化工产品,流通于国际市场。
此后,几近一个世纪的应用开发和使用实践后,这一以其广泛用途和良好的使用性能为基础的产品,现在还正在不断地扩大自己的市场地位。
特别是作为增塑剂在PVC塑料制品配方上有较大比例的应用,使得其增长速度几乎等同于PVC的增长。
所以,氯烃-52是一个具有较长经济寿命、较大市场基础,并具有较好经济效益的精细化工产品。
我国大陆直到六十年代才陆续开发而建成氯烃-52的生产装置。
最早是沈阳永新化工厂,稍迟是上海氯碱总厂和武汉葛店化工厂。
他们都是氯碱厂。
进入上世纪就是年代,随着中国经济的飞速发展,氯化石蜡产能和技术跟随着主要的石油化工产品的发展而高速发展。
生产厂家也由氯碱行业延伸到专业化的个体户、私营民营企业。
产品从单一的标准产品演变成多牌号多用途。
1.2、氯化石蜡-52的主要用途:1.2.1、增塑剂:最早我国只用固体皂蜡为原料生产的氯化石蜡-42,用于辅助增塑剂,由于它粘度大,分散性和捏合性都差,与塑料制品的1相溶性亦差,产出的塑料制品不理想。
所以大部份用户都改用C精重液15蜡生产的氯化石蜡-52。
由于它具有低挥发性、难燃、粘度低、色泽好等优点,近年来逐渐发展为作为主要增塑剂应用于塑料加工,从而降低了塑料制品的生产成本,使得颇具竞争力。
1.2.2、防滑剂:氯化石蜡渗混入无规聚丙稀树脂当中,可以制造防滑包装材料。
1.2-3、阻燃剂:电线包皮,耐热塑料制品,煤碳输送带,防水帆布,防火涂料均需用氯化石蜡-52做阻燃剂参与配方。
1.2.4、静电消除剂:纺织品用氯化石蜡处理后,不仅能防火,防水,抗辐射,还可作静电消除剂。
1.2.5、切削油添加剂:高速高硬切削机床,在其冷却油中配以氯化石蜡-52,就可以大幅度提高切削速度,从而提高了车床的工作效率和切削性能,并因此提高了加工工件的光洁度,同时还可大大延长了切削刃具的使用寿命。
1.2.6、另外,氯化石蜡-52还在阻电材料,防腐材料,耐磨材料中都有广泛的应用。
1.3、目前生产该产品所采用的工艺方法和国内外生产技术现状:1.3.1、氯化石蜡-52。
其化学反应的表达式为:CH+6CL→CCLH+6HCL+Q26152153262从反应式可见:液体原料石蜡油与气体原料氯经充分反应后,生成液态的成品氯化石蜡和气态的副产品氯化氢,生产中用氯化氢经工业水吸收成产盐酸作副产品出售。
反应过程是氯气对正构石蜡烷烃进行多级氧化,因而产生大量的热能。
为了维持反应,必须不断将其系统中反应热强制除去,才能延续生产。
要达到成品氯化石蜡-52合格的含氯量,就要在十多个碳原子的石蜡分子链上,先后有氢原子依此被六个开键的氯原子所取代。
这是一个深度氯化的过程。
(反应机理略)反应温度控制在70~100℃之间。
要达到匀称的氯化度、物料在反应区域中差不多要动态地留滞40个小时。
这期间依靠非扩散进行活化能的传递及元素置换的传质传热,周而复始地进行六个轮回的反应才能完成。
而且随着氯化度的加深,物料粘度在加大,而化学反应的动力在下降,所以反应时间很长,而且要给予扩散传递的反应容积和充分混合接触的动态空间。
1.3.2、氯烃-52目前国内外的生产方法和技术现状:1.3.2.1、日本碳化物工业有限公司,采用多只6000升搪瓷釜,每釜投以平均分子量为216的石蜡油3吨,予热到75℃,在强烈搅拌下通入氯化氢进猛氧氢化予处理,继而通入氯气缓慢诱导反应,逐渐升温到85℃时开启冷却水,调节控制在90℃左右维持反应约3小时后达到合格然后出料进行后处理。
3国外许多大的氯气公司生产大吨位的氯烃-52产品,台湾的合迪公司也大多采用类似的工艺方法进行该产品的生产。
1.3.2.2、西德的赫斯特公司采用了三个直径400、高度5000的硼硅玻璃泡罩塔,石蜡油从第一塔中进入循环喷淋,依次用泵过料到第二塔和第三塔去也形循环喷淋吸收。
氯气从第三塔底导入,依此经第二塔和第一塔的氯化反应后控制一定的氯化氢转化率,然后引出送去制盐酸,而液相喷淋液则控制适当回流比,使之第三塔釜液始终保持含氯合格。
这是九十年代初报导国外成功的连续化生产法。
据说此法设备制作难度极大,且难以维修,损耗很大,综合技术经济指标并不好,最后竞难以维持运行而终止生产。
此后欧、美、日本、南韩等氯烃-52的技术专利都没有连续化生产方法。
1.3.2.3、我国沈阳、上海、葛店三家大厂,从七十年代初联合开发出5000升搪瓷釜上再接搪瓷塔节,再配石墨列管进行外冷却由两个搪瓷塔釜组成一套,每套是年产2500吨,万吨规模则要四套,这种配有外冷却的塔釜间断生产法是我国自创的比较成熟的间断而有较好效率的生产法,一直沿用到现在几乎没有作大的变动。
1.3.2.4、中国原化工部曾多次鼓励全国的化研单位、设计单位、大专院校从事氯化石蜡-52进行连续生产的试验,也确实有研究、设计单位和院校对这方面做了大量的中扩试工作,但终因生产的物料腐蚀性4大、粘度大、反应缓慢、反应物中各阶段反应参差不齐,致使成品生熟不匀,所以最终未能成功。
九十年代初,中国化工部责成中国氯碱协会,组成专职调查组,对国内外氯化石蜡生产的设备和工艺进行了一次较全面的查询,对各种生产装制进行了比较,最后得出结论发表在氯碱产品调查综合资料编上:目前国际国内氯化石蜡生产的工艺过程,分为间歇法和连续法(指赫斯特公司)两大类。
生产方法有热氯化法、光氯化法、催化氯化法等。
但是,无论制备低含氯量或高含氯量的氯化石蜡,相对较成熟的工艺路线还是间歇的热氯化工艺生产法。
进入二十一世纪,间歇法逐渐被连续法取代。
我国创新的多釜连续法工艺开始出现,各个厂家也都在最早的原型工艺上进行改进提高,出现了多种风格的连续法工艺。
有代表性的有:浙江巨化原型工艺,采用六个主釜、三级副釜加三级降膜吸收器交叉串联尾气吸收的工艺。
这个工艺生产连续性好,尾气清洁排放,缺点是对员工操作素质要求比较高,尾气处理过程中酸蜡分离容易出现不彻底情况。
单线产能5000t/a。
上海氯碱原型工艺,采用5个高塔式主釜,两级副釜加两级降膜吸收器串联尾气吸收工艺。
这个工艺产能大,需要加强自动化仪表的配置。
缺点是尾气吸收不彻底,最后排放的尾气含氯气量较高,需要用大量烧碱来进行处理。
5河南荥阳一带的巨化原型简化式工艺,这种工艺对六釜连续法工艺进行了简化,自然溢流、自然循环冷却。
并对设备进行了改造,对尾气吸收工艺进行了针对性的改造,具有操作简便投资最省的优点。
但是其最大的缺点是安全保障降低,产品质量不稳定,单线产能不及原型的50%。
2.新型高粘度氯化石蜡生产与市场需求介绍2.1新型氯化石蜡定义与市场指向:新型高粘度氯化石蜡指的的粘度在400~3000范围内氯化石蜡,其产品用途也由传统氯化石蜡的增塑/阻燃剂转移到胶粘剂行业,目前胶粘剂行业特别是聚氨酯泡沫填缝剂行业上正大量推广使用,极大的降低了填缝剂的制造成本,目前尚处于供不应求状态。
以此为突破口,国内聚氨酯发泡保温行业也开始添加高粘度氯化石蜡作为阻燃剂,取代原有的阻燃剂和部分聚氨酯材料,极大的降低了生产成本。
高粘度氯化石蜡作为添加型的阻燃剂,还为发泡体增强了韧性,成型美观。
预测未来五年,本产品在聚氨酯泡沫应用领域年需求量将达到50~80万吨以上,早生产早获利。
2.2原料与生产技术难点:生产高粘度氯化石蜡所用的原料相对传统氯化石蜡所用的300#标准石油蜡要廉价很多,是高粘度氯化石蜡低成本生产的主要动力。
这种原料主要来自煤制油行业产生的石蜡,馏程较宽,粘度较高,组分分散,6批次质量差异度较大。
这样的原料生产的产品粘度也是五花八门,质量不稳定,无法直接满足客户需要。
因此大多数的氯化石蜡生产厂家生产时需要进行工艺改进的核心技术,核心技术方面这是当前各个厂家为聚氨酯填缝剂厂家供货的最大障碍。
如何取得核心技术成为是本生产技术改进的重要一环。
2.3生产工艺技术简介:新型氯化石蜡由于其粘度很高,生产过程中反应速度降低,氯化深度不够强,所以需要对传统的生产工艺进行大幅度的改进。
与传统连续法氯化工艺一样,主流程也是采用六级串联氯化工艺,但是与传统的日光灯光照催化不同的是,本工艺采用新型蓝光灯加日光灯组合的方式,增强催化效果,加快反应速度。
同时采用非标的细高型反应釜外挂冷却器,强制循环冷却,提高产能。
进一步优化改进设备管口,使之适应高粘度生产的要求。
新设计的尾气吸收系统,采用三级尾气吸收釜串联吸收主釜尾气中的氯气,加强了石蜡冷凝分离,防止短链组分在尾气系统大量集结影响安全生产;优化了盐酸吸收流程,采用两级降膜塔吸收加两级填料塔吸收工艺,其中末级填料塔起到把关的作用,正常生产情况下,尾气可以直接排空。
在末级填料塔出口接出一支路,接入碱喷射器,用于处理反应过程中过量的氯气,也是作为事故时系统真空处理的装置。
7整个系统引入大量自动化仪表,包括氯气流量监测与控制、氯气连锁切断、液蜡流量监测与控制、反应温度监测报警与连锁、出料流量监测与调节、吹风流量与调节、冷却水流量自动调节、系统压力监测报警与连锁、盐酸浓度监测与进酸流量调节等、循环水压力温度监测、贮罐液位温度监测、仪表风氮气压力温度监测、氯气压力温度监测、机泵运系统控制,设立中心DCS行状态监测和远程控制等。
以上仪表全部采用控制室。
现场员工以巡检、出料精制操作为主。
产品可根据用户需要,生产出满足用户需求不同规格的合格产品。
稳定和提高产品粘度是该产品的核心技术。
新型氯化石蜡成本简单分析3.、原料的配比和产品的联产比例,按下列平衡式进行:3.1+6.28HCL+ CLH+6.28CLCH→C (1)反应式:25.72156.2832215428+230 212+446→ (2)分子量:)(3)物料量:(kg496+1042)1050-1000+538(氯化氢 1700 多加钢瓶余氯8另加工业水1162kg伐(盐酸)(4)理论的消耗和产量:496+1050-1000+1700盐酸浓度≥31%8含氯量52%(5)控制指标的消耗和产量:500+1070-1000+1680根据上面平衡式设定:(一)500公斤石蜡油与1070公斤液氯经氯化制造538公斤氯化氢和1000公斤氯化石蜡-52。
(二)538公斤氯化氢再加1162公斤工业水经吸收制造成1700公斤付产盐酸。
3.2、产品规模与主要原料消耗:设计4套生产装置,年产40000吨氯化石蜡,联产约67200吨工业付酸。
理论上年消耗20000吨石蜡,42800吨液氯,属于物料消耗的近48000吨吸收水纳入冷却蒸发水的能耗统计。