橡胶与金属的粘合是橡胶制品制造过程中的重要环节
橡胶与金属粘接后剥离 残余面积百分比

橡胶与金属粘接后剥离残余面积百分比在工程学和材料科学领域,橡胶与金属的粘接问题一直备受关注。
橡胶与金属之间的粘合强度对于许多应用来说至关重要,例如汽车轮胎、密封件和电缆等。
然而,橡胶与金属粘接后的剥离现象,特别是剥离时残余面积百分比的变化,一直是研究的热点之一。
要了解橡胶与金属粘接后的剥离过程,我们需要先了解橡胶与金属之间的界面现象。
橡胶与金属粘接的关键在于界面的化学键和物理键。
橡胶表面上的官能团与金属表面形成的化学键,以及物理键如机械锁和吸附力等,都会增强橡胶与金属的粘合强度。
这样的粘合强度对于橡胶制品的性能和寿命至关重要。
然而,橡胶与金属粘接后的剥离现象可能导致粘合强度的降低,这对于工程应用来说是一个主要的问题。
为了研究橡胶与金属粘接剥离时的残余面积百分比变化,研究人员通常采用剥离试验来评估粘合强度。
在剥离试验中,橡胶样品被黏附在金属表面上,然后通过施加剪切力将其剥离。
此过程中,可以测量橡胶与金属分离的力和剥离面积,由此得到粘合强度和残余面积百分比的数据。
研究表明,橡胶与金属粘接后的剥离现象受到多种因素的影响。
界面的表面粗糙度会影响粘接强度和剥离行为。
金属表面的粗糙度可以增加机械锁效应,从而提高粘合强度。
橡胶与金属之间的化学反应也对粘合强度起着重要作用。
一些化学键的形成可以增强粘接强度,而其他化学反应可能导致剥离时的残余面积百分比降低。
温度和湿度等环境条件也会对粘接剥离性能产生影响。
在实际应用中,人们通常希望橡胶与金属粘接后的剥离残余面积百分比尽可能小。
一个较小的残余面积百分比意味着粘接强度较高,耐久性较好。
研究人员一直在努力开发新的粘接技术和材料来改善橡胶与金属的粘接性能。
改变橡胶表面的化学组成、使用新型粘接剂和表面处理剂等都是改善橡胶与金属粘接性能的常用方法。
橡胶与金属粘接后的剥离残余面积百分比是评估粘接性能的重要参数之一。
研究橡胶与金属的粘接问题,深入了解界面的化学键和物理键,对改善橡胶制品的性能和寿命具有重要意义。
橡胶的工艺流程

橡胶的工艺流程(精品)2014—10—22橡胶技术网橡胶工艺流程开始1 综述橡胶制品的主要原料是生胶、各种配合剂、以及作为骨架材料的纤维和金属材料,橡胶制品的基本生产工艺过程包括塑炼、混炼、压延、压出、成型、硫化6个基本工序.橡胶的加工工艺过程主要是解决塑性和弹性矛盾的过程,通过各种加工手段,使得弹性的橡胶变成具有塑性的塑炼胶,在加入各种配合剂制成半成品,然后通过硫化是具有塑性的半成品又变成弹性高、物理机械性能好的橡胶制品。
2 橡胶加工工艺2.1塑炼工艺生胶塑炼是通过机械应力、热、氧或加入某些化学试剂等方法,使生胶由强韧的弹性状态转变为柔软、便于加工的塑性状态的过程.生胶塑炼的目的是降低它的弹性,增加可塑性,并获得适当的流动性,以满足混炼、亚衍、压出、成型、硫化以及胶浆制造、海绵胶制造等各种加工工艺过程的要求.掌握好适当的塑炼可塑度,对橡胶制品的加工和成品质量是至关重要的。
在满足加工工艺要求的前提下应尽可能降低可塑度。
随着恒粘度橡胶、低粘度橡胶的出现,有的橡胶已经不需要塑炼而直接进行混炼。
在橡胶工业中,最常用的塑炼方法有机械塑炼法和化学塑炼法。
机械塑炼法所用的主要设备是开放式炼胶机、密闭式炼胶机和螺杆塑炼机。
化学塑炼法是在机械塑炼过程中加入化学药品来提高塑炼效果的方法.开炼机塑炼时温度一般在80℃以下,属于低温机械混炼方法.密炼机和螺杆混炼机的排胶温度在120℃以上,甚至高达160-180℃,属于高温机械混炼。
生胶在混炼之前需要预先经过烘胶、切胶、选胶和破胶等处理才能塑炼.几种胶的塑炼特性:天然橡胶用开炼机塑炼时,辊筒温度为30—40℃,时间约为15—20min;采用密炼机塑炼当温度达到120℃以上时,时间约为3-5min。
丁苯橡胶的门尼粘度多在35—60之间,因此,丁苯橡胶也可不用塑炼,但是经过塑炼后可以提高配合机的分散性顺丁橡胶具有冷流性,缺乏塑炼效果。
顺丁胶的门尼粘度较低,可不用塑炼.氯丁橡胶得塑性大,塑炼前可薄通3-5次,薄通温度在30-40℃。
橡胶制品生产工艺流程

橡胶制品生产工艺流程一、橡胶制品基本工艺流程伴随现代工业尤其是化学工业的迅猛发展,橡胶制品种类繁多,但其生产工艺过程,却基本相同。
以一般固体橡胶 ( 生胶 ) 为原料的制品,它的生产工艺过程主要包括:原材料准备→塑炼→混炼→成型→硫化→休整→检验二、橡胶制品原材料准备橡胶制品的主要材料有生胶、配合剂、纤维材料和金属材料。
其中生胶为基本材料 ; 配合剂是为了改善橡胶制品的某些性能而加入的辅助材料 ; 纤维材料 ( 棉、麻、毛及各种人造纤维、合成纤维 ) 和金属材料 ( 钢丝、铜丝 ) 是作为橡胶制品的骨架材料,以增强机械强度、限制制品变型。
在原材料准备过程中,配料必须按照配方称量准确。
为了使生胶和配合剂能相互均匀混合,需要对某些材料进行加工:生胶要切胶、破胶成小块 ;块状配合剂如石蜡、硬脂酸、松香等要粉碎 ;粉状配合剂若含有机械杂质或粗粒时需要筛选除去 ;液态配合剂 ( 松焦油、古马隆 ) 需要加热、熔化、蒸发水分、过滤杂质;配合剂要进行干燥,不然容易结块、混炼时旧不能分散均匀,硫化时产生气泡,从而影响产品质量;三、橡胶制品的塑炼生胶富有弹性,缺乏加工时的必需性能 ( 可塑性 ) ,因此不便于加工。
为了提高其可塑性,所以要对生胶进行塑炼 ; 这样,在混炼时配合剂就容易均匀分散在生胶中 ; 同时,在压延、成型过程中也有助于提高胶料的渗透性 ( 渗入纤维织品内 ) 和成型流动性。
将生胶的长链分子降解,形成可塑性的过程叫做塑炼。
生胶塑炼的方法有机械塑炼和热塑炼两种。
机械塑炼是在不太高的温度下,通过塑炼机的机械挤压和摩擦力的作用,使长链橡胶分子降解变短,由高弹性状态转变为可塑状态。
热塑炼是向生胶中通入灼热的压缩空气,在热和氧的作用下,使长链分子降解变短,从而获得可塑性。
四、橡胶制品的混炼为了适应各种不同的使用条件、获得各种不同的性能,也为了提高橡胶制品的性能和降低成本,必须在生胶中加入不同的配合剂。
混炼就是将塑炼后的生胶与配合剂混合、放在炼胶机中,通过机械拌合作用,使配合剂完全、均匀地分散在生胶中的一种过程。
增粘剂Ricobond1756HS在氢化丁腈橡胶骨架油封中的应用
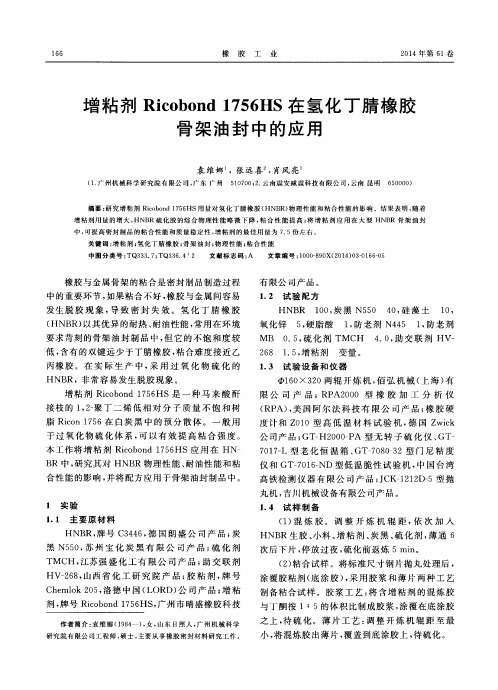
摘 要 :研 究 增 粘剂 Ricobond 1756HS用 量 对氢 化 丁腈 橡 胶 (HNBR)物 理 性 能 和 粘 合 性 能 的影 响 。结 果 表 明 :随 着 增 粘 剂 用 量 的 增 大 ,HNBR 硫 化 胶 的综 合 物 理 性 能 略 微 下 降 ,粘 合 性 能 提 高 ;将 增 粘 剂 应 用 在 大 型 HNBR 骨 架 油 封 中 ,可 提 高 密 封 制 品 的 粘合 性 能 和质 量 稳 定 性 ,增 粘 剂 的 最 佳用 量 为 7.5份 左 右 。
1 实 验 1.1 主 要 原 材 料
HNBR,牌 号 C3446,德 国 朗盛 公 司 产 品 ;炭 黑 N550,苏 州 宝 化 炭 黑 有 限 公 司 产 品 ;硫 化 剂 TMCH,江 苏强 盛 化 工 有 限 公 司产 品 ;助 交 联 剂 HV一268,山西 省 化 工 研 究 院产 品 ;胶 粘 剂 ,牌 号 Chemlok 205,洛 德 中 国 (LORD)公 司 产 品 ;增 粘 剂 ,牌号 Ricobond 1756HS,广 州市 晴盛 橡胶 科技
作 者 简 介 :袁 维 娜 (1984一 ),女 ,山 东 日照 人 ,广 州 机 械 科 学 研 究 院 有 限 公 司 工程 师 ,硕 士 ,主要 从 事 橡 胶 密 封 材 料 研 究 工作 。
有 限 公 司 产 品 。 1.2 试 验 配 方
HNBR 1OO,炭黑 N550 40,硅 藻 土 10, 氧化锌 5,硬脂 酸 1,防老 剂 N445 1,防 老 剂 MB 0.5,硫 化 剂 TMCH 4.0,助 交 联 剂 HV一 268 1.5,增 粘剂 变 量 。 1.3 试 验 设 备 和 仪 器
增粘 剂 Ricobond 1756HS是 一 种 马来 酸 酐 接枝 的 1,2一聚 丁 二 烯 低 相 对 分 子 质 量 不 饱 和 树 脂 Ricon 1756在 白炭 黑 中 的预 分 散 体 。一 般 用 于 过 氧 化 物 硫 化 体 系 ,可 以 有 效 提 高 粘 合 强 度 。 本 工作将 增 粘 剂 Ricobond 1756HS应 用 在 HN BR 中 ,研究 其对 HNBR物理 性能 、耐油 性能 和粘 合性 能 的影 响 ,并将 配方 应用 于骨 架油封 制 品 中。
橡胶的工艺流程
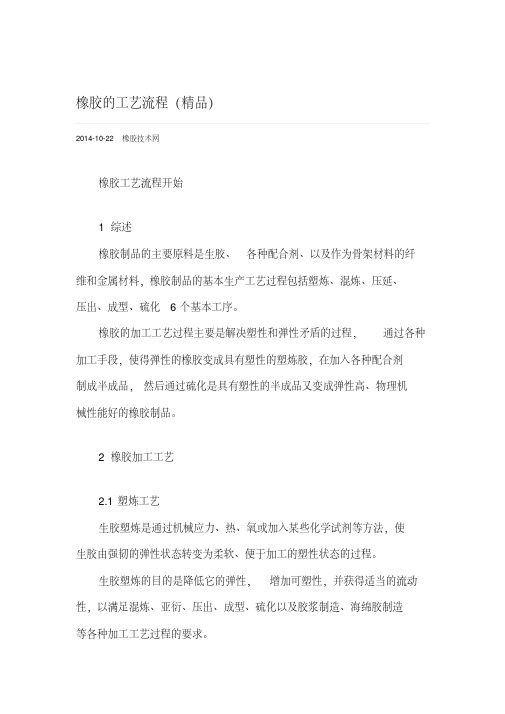
橡胶的工艺流程(精品)2014-10-22橡胶技术网橡胶工艺流程开始1 综述橡胶制品的主要原料是生胶、各种配合剂、以及作为骨架材料的纤维和金属材料,橡胶制品的基本生产工艺过程包括塑炼、混炼、压延、压出、成型、硫化6个基本工序。
橡胶的加工工艺过程主要是解决塑性和弹性矛盾的过程,通过各种加工手段,使得弹性的橡胶变成具有塑性的塑炼胶,在加入各种配合剂制成半成品,然后通过硫化是具有塑性的半成品又变成弹性高、物理机械性能好的橡胶制品。
2 橡胶加工工艺2.1塑炼工艺生胶塑炼是通过机械应力、热、氧或加入某些化学试剂等方法,使生胶由强韧的弹性状态转变为柔软、便于加工的塑性状态的过程。
生胶塑炼的目的是降低它的弹性,增加可塑性,并获得适当的流动性,以满足混炼、亚衍、压出、成型、硫化以及胶浆制造、海绵胶制造等各种加工工艺过程的要求。
掌握好适当的塑炼可塑度,对橡胶制品的加工和成品质量是至关重要的。
在满足加工工艺要求的前提下应尽可能降低可塑度。
随着恒粘度橡胶、低粘度橡胶的出现,有的橡胶已经不需要塑炼而直接进行混炼。
在橡胶工业中,最常用的塑炼方法有机械塑炼法和化学塑炼法。
机械塑炼法所用的主要设备是开放式炼胶机、密闭式炼胶机和螺杆塑炼机。
化学塑炼法是在机械塑炼过程中加入化学药品来提高塑炼效果的方法。
开炼机塑炼时温度一般在80℃以下,属于低温机械混炼方法。
密炼机和螺杆混炼机的排胶温度在120℃以上,甚至高达160-180℃,属于高温机械混炼。
生胶在混炼之前需要预先经过烘胶、切胶、选胶和破胶等处理才能塑炼。
几种胶的塑炼特性:天然橡胶用开炼机塑炼时,辊筒温度为30-40℃,时间约为15-20min;采用密炼机塑炼当温度达到120℃以上时,时间约为3-5min。
丁苯橡胶的门尼粘度多在35-60之间,因此,丁苯橡胶也可不用塑炼,但是经过塑炼后可以提高配合机的分散性顺丁橡胶具有冷流性,缺乏塑炼效果。
顺丁胶的门尼粘度较低,可不用塑炼。
氯丁橡胶得塑性大,塑炼前可薄通3-5次,薄通温度在30-40℃。
橡胶制品常见问题及解决方法
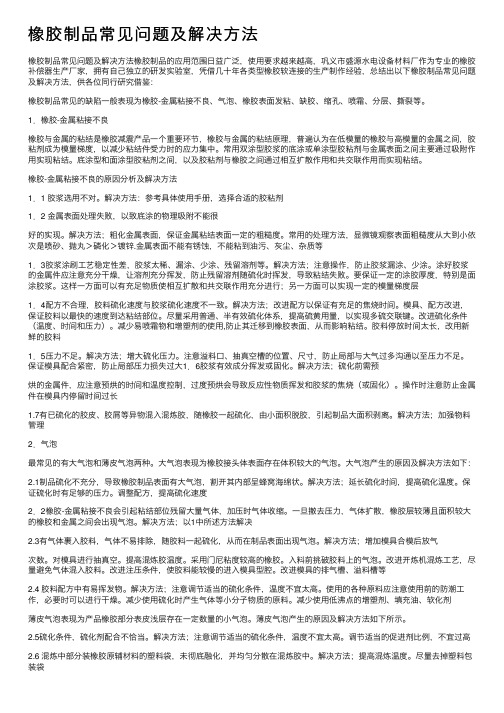
橡胶制品常见问题及解决⽅法橡胶制品常见问题及解决⽅法橡胶制品的应⽤范围⽇益⼴泛,使⽤要求越来越⾼,巩义市盛源⽔电设备材料⼚作为专业的橡胶补偿器⽣产⼚家,拥有⾃⼰独⽴的研发实验室,凭借⼏⼗年各类型橡胶软连接的⽣产制作经验,总结出以下橡胶制品常见问题及解决⽅法,供各位同⾏研究借鉴:橡胶制品常见的缺陷⼀般表现为橡胶-⾦属粘接不良、⽓泡、橡胶表⾯发粘、缺胶、缩孔、喷霜、分层、撕裂等。
1.橡胶-⾦属粘接不良橡胶与⾦属的粘结是橡胶减震产品⼀个重要环节,橡胶与⾦属的粘结原理,普遍认为在低模量的橡胶与⾼模量的⾦属之间,胶粘剂成为模量梯度,以减少粘结件受⼒时的应⼒集中。
常⽤双涂型胶浆的底涂或单涂型胶粘剂与⾦属表⾯之间主要通过吸附作⽤实现粘结。
底涂型和⾯涂型胶粘剂之间,以及胶粘剂与橡胶之间通过相互扩散作⽤和共交联作⽤⽽实现粘结。
橡胶-⾦属粘接不良的原因分析及解决⽅法1.1 胶浆选⽤不对。
解决⽅法:参考具体使⽤⼿册,选择合适的胶粘剂1.2 ⾦属表⾯处理失败,以致底涂的物理吸附不能很好的实现。
解决⽅法;粗化⾦属表⾯,保证⾦属粘结表⾯⼀定的粗糙度。
常⽤的处理⽅法,显微镜观察表⾯粗糙度从⼤到⼩依次是喷砂、抛丸>磷化>镀锌.⾦属表⾯不能有锈蚀,不能粘到油污、灰尘、杂质等1.3胶浆涂刷⼯艺稳定性差,胶浆太稀、漏涂、少涂、残留溶剂等。
解决⽅法;注意操作,防⽌胶浆漏涂、少涂。
涂好胶浆的⾦属件应注意充分⼲燥,让溶剂充分挥发,防⽌残留溶剂随硫化时挥发,导致粘结失败。
要保证⼀定的涂胶厚度,特别是⾯涂胶浆。
这样⼀⽅⾯可以有充⾜物质使相互扩散和共交联作⽤充分进⾏;另⼀⽅⾯可以实现⼀定的模量梯度层1.4配⽅不合理,胶料硫化速度与胶浆硫化速度不⼀致。
解决⽅法;改进配⽅以保证有充⾜的焦烧时间。
模具、配⽅改进,保证胶料以最快的速度到达粘结部位。
尽量采⽤普通、半有效硫化体系,提⾼硫黄⽤量,以实现多硫交联键。
改进硫化条件(温度、时间和压⼒)。
减少易喷霜物和增塑剂的使⽤,防⽌其迁移到橡胶表⾯,从⽽影响粘结。
橡胶表面粘合力
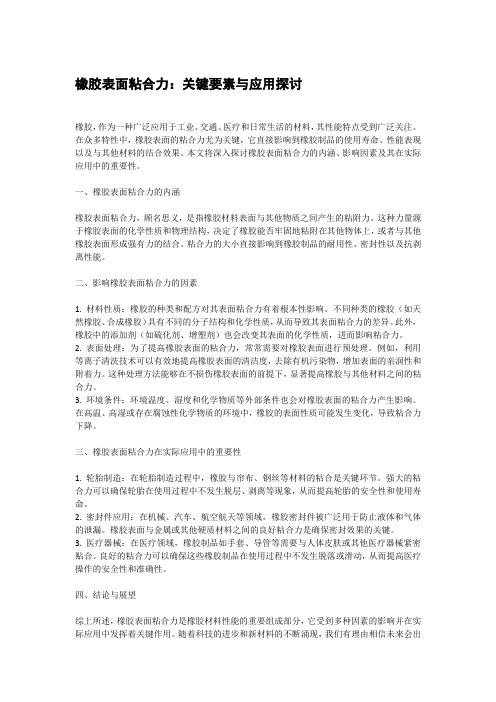
橡胶表面粘合力:关键要素与应用探讨橡胶,作为一种广泛应用于工业、交通、医疗和日常生活的材料,其性能特点受到广泛关注。
在众多特性中,橡胶表面的粘合力尤为关键,它直接影响到橡胶制品的使用寿命、性能表现以及与其他材料的结合效果。
本文将深入探讨橡胶表面粘合力的内涵、影响因素及其在实际应用中的重要性。
一、橡胶表面粘合力的内涵橡胶表面粘合力,顾名思义,是指橡胶材料表面与其他物质之间产生的粘附力。
这种力量源于橡胶表面的化学性质和物理结构,决定了橡胶能否牢固地粘附在其他物体上,或者与其他橡胶表面形成强有力的结合。
粘合力的大小直接影响到橡胶制品的耐用性、密封性以及抗剥离性能。
二、影响橡胶表面粘合力的因素1. 材料性质:橡胶的种类和配方对其表面粘合力有着根本性影响。
不同种类的橡胶(如天然橡胶、合成橡胶)具有不同的分子结构和化学性质,从而导致其表面粘合力的差异。
此外,橡胶中的添加剂(如硫化剂、增塑剂)也会改变其表面的化学性质,进而影响粘合力。
2. 表面处理:为了提高橡胶表面的粘合力,常常需要对橡胶表面进行预处理。
例如,利用等离子清洗技术可以有效地提高橡胶表面的清洁度,去除有机污染物,增加表面的亲润性和附着力。
这种处理方法能够在不损伤橡胶表面的前提下,显著提高橡胶与其他材料之间的粘合力。
3. 环境条件:环境温度、湿度和化学物质等外部条件也会对橡胶表面的粘合力产生影响。
在高温、高湿或存在腐蚀性化学物质的环境中,橡胶的表面性质可能发生变化,导致粘合力下降。
三、橡胶表面粘合力在实际应用中的重要性1. 轮胎制造:在轮胎制造过程中,橡胶与帘布、钢丝等材料的粘合是关键环节。
强大的粘合力可以确保轮胎在使用过程中不发生脱层、剥离等现象,从而提高轮胎的安全性和使用寿命。
2. 密封件应用:在机械、汽车、航空航天等领域,橡胶密封件被广泛用于防止液体和气体的泄漏。
橡胶表面与金属或其他硬质材料之间的良好粘合力是确保密封效果的关键。
3. 医疗器械:在医疗领域,橡胶制品如手套、导管等需要与人体皮肤或其他医疗器械紧密贴合。
橡胶和金属的粘结技术

橡胶和金属的粘结技术橡胶和金属是两种不同性质的材料,将两者很好地粘接可以制得具有不同构型和特性的复合件,这种复合体系在工业中有着广泛的用途,如汽车工业、机械制造工业、固体火箭发动机的柔性接头、桥梁的支撑缓冲垫等。
橡胶与金属之间化学结构和力学性能巨大的差异,使获得具有高强度的粘接有着很大的困难。
研制出高性能粘接和适用范围更广的新型胶粘剂始终是研究的热点。
借助于胶粘剂在硫化过程中将橡胶与金属粘接起来是目前采用的基本方法之一。
本文将就其进展进行综述。
1金属-橡胶粘接体系发展现状橡胶与金属之间的粘接已有很久的历史,可以追溯到1850年,目前采用的粘接方法可分为直接粘接法、硬质橡胶法、镀黄铜法和胶粘剂粘接法。
直接粘接法工艺简单,操作方便,将粘接材料表面进行适当处理后直接在加热加压过程中实现粘接。
可通过在橡胶中加入一些组分、在胶料表面涂偶联剂或对对橡胶进行环化处理等来提高橡胶与金属的粘接性能。
尹寿琳、陈日生等在天然橡胶中加入多硫化合物粘合剂B和酸性化合物助剂C,用此粘合A3钢板作挖泥泵耐磨衬里,挖泥1000h以上未发现橡胶与金属脱开。
此法不足的是,处理的金属件要尽快与胶料粘接,以免金属表面深层氧化;在胶料中添加一些多价金属的有机盐和无机盐,虽可提高粘接效果,但会改变橡胶材料原先的物理机械性能,且造成出模困难。
硬质橡胶法是最古老的粘接体系,在金属表面贴一层硫磺含量较高的硬质胶料或一层硬质胶浆,通过硫化使橡胶与金属粘接起来,硬质橡胶法粘接力较强,工艺简便,适于粘接大型制件,但是不耐冲击和震动,60℃以上粘接强度发生显著下降。
镀黄铜法较硬质橡胶法有较好的耐高温性,黄铜或表面镀黄铜金属件不同胶粘剂,借助于被粘橡胶中的硫磺扩散到金属表面与CuO、ZnO结合形成界面粘接层与橡胶产生牢固粘合,至今在轮胎工业中钢丝圈的粘接、钢丝帘线与帘布层胶的粘接、内胎气门嘴的制造中仍采用此法。
胶粘剂法是目前应用最广和最有效的方法,已经历了酚醛树脂、多异氰酸酯、卤化橡胶、特种硫化剂的卤化橡胶、硅橡胶和水基胶粘剂等不同的发展阶段。
橡胶制品的生产流程

橡胶制品的生产流程橡胶制品是指通过橡胶材料加工而成的各种物品,比如轮胎、橡胶管、橡胶制品等。
橡胶制品的生产流程经过多个环节,下面我们就来详细介绍一下。
首先,橡胶制品的生产需要准备原材料。
橡胶制品的原材料主要是橡胶乳和橡胶粉。
橡胶乳是橡胶树割皮后流出的白色胶液,它是橡胶制品生产中最重要的原料之一。
橡胶粉则是指将橡胶乳加热干燥后得到的粉末状物质。
接下来,将橡胶乳和橡胶粉混合制备成制品所需的橡胶胶料。
在混合的过程中,通常会加入一些辅助原料,如硫化剂、促进剂、防老剂等,以提高胶料的性能。
混合的设备通常是橡胶开炼机,通过机械切割和滚压的方式将橡胶乳和橡胶粉充分混合在一起,形成均匀的橡胶胶料。
然后,将橡胶胶料放入模具中进行成型。
模具的种类有很多,根据制品的不同而有所差异。
例如,制造轮胎的模具是由一对对称的金属模具组成,用来成型胎面、胎侧等部位。
模具的尺寸和形状决定了最终制品的外形和尺寸。
橡胶胶料通过加热软化后,被挤压到模具中,经过一定的时间形成所需的形状。
成型过程中需要控制好温度、时间和压力等因素,以保证制品的质量。
成型完成后,橡胶制品需要经过硫化处理。
硫化是指橡胶胶料中的硫化剂与橡胶中的双键发生化学反应,使胶料变得硬化、耐磨、耐高温等。
硫化的方法有很多种,常用的包括热硫化、冷硫化、热风硫化等。
热硫化是指将成型好的橡胶制品放入硫化罐中,通过加热使硫化剂与橡胶发生反应。
硫化时间通常在几分钟到几个小时之间,具体时间根据橡胶制品的种类和厚度而定。
最后,经过硫化处理的橡胶制品需要进行清洗和修整。
清洗是将橡胶制品表面的杂质和残留物清除,以保证表面的光洁度。
修整是对制品进行切割、打磨等处理,以使制品达到所需的尺寸和外观效果。
修整过程中需要注意操作技巧,以防止制品表面被刮伤或损坏。
综上所述,橡胶制品的生产流程包括准备原材料、混合制备橡胶胶料、模具成型、硫化处理、清洗和修整等环节。
每个环节都需要严格控制各种因素,以保证制品的质量和性能。
橡胶与金属的粘合是橡胶制品制造过程中的重要环节

橡胶与金属的粘合是橡胶制品制造过程中的重要环节,如果粘合不良或无法粘合,一些橡胶制品如轮胎、钢丝输送带、橡胶软管,橡胶骨架油封、汽门油封,橡胶金属组合垫圈、组合胶套等橡胶金属复合制品就无法制作。
就橡胶密封制品而言,上世纪80年代初,青岛密封件厂协同青岛化工厂研制成功了RM-1粘合剂,替代日本TD870成功生产出与国外同等水平的骨架油封,使引进的国外技术得以消化吸收,开辟了骨架油封制作的新工艺。
上世纪90年代,由于汽车工业的发展,不少厂家要求用氟橡胶制作骨架油封、汽车油封,但是粘合问题不好解决,严重的制约了该产品的开发,当时青岛双星集团密封件厂成功的研制了FG-1氟橡胶与黑色金属的热硫化粘合剂,使氟橡胶与金属骨架牢牢的粘合成一体,顺理成章的研发成功斯太尔发动机曲轴前后油封和气门油封替代了进口,满足了配套需要,该粘合剂一直使用至今。
因此橡胶与金属粘合是极其重要的应用技术,应引起生产企业的高度重视。
1 金属骨架的表面处理) 骨架表面无油污、无锈蚀,有一定粗糙度的新鲜表面才能有效的与金属粘合,因此骨架必须进行表面处理,处理大体有两种方法:一是机械法处理。
如采用履带式的抛丸清理机326或滚筒式的抛丸清理机Q3110,将粒径0.5mm的钢砂喷射到骨架表面,将表面的锈蚀等有害物料喷掉,使表面新鲜并增大表面积,加大骨架与胶粘剂间的接触面;二是化学法。
即酸洗处理,磷化钝化处理,其工艺过程是碱液去油,酸液去锈,磷化上磷化膜,然后进行钝化烘干,碱液是有多种材料如苛性钠、硅酸钠(表面湿润剂)、焦磷酸钠(阴离子表面活性剂)、烷基磺酸钠组成的水溶液,清洗温度80-90℃,时间视表面的油污多少而有差异,一般是5min左右。
去油污的骨架经流动的自来水冲洗后,进行酸洗处理,而不同的金属去锈时对酸的品种是有选择性的。
例如,铁件要用盐酸清洗处理。
铜件和不锈钢骨架采用硫酸、硝酸混合液协同去锈。
铝件用硫酸、铬酸混合液进行处理。
要求对周围环境不产生或少产生腐蚀时,而金属骨架锈蚀较轻的骨架,可采用以草酸为主,掺用少量硫酸和加入缓钝剂的水溶液进行处理。
橡胶金属硫化粘结
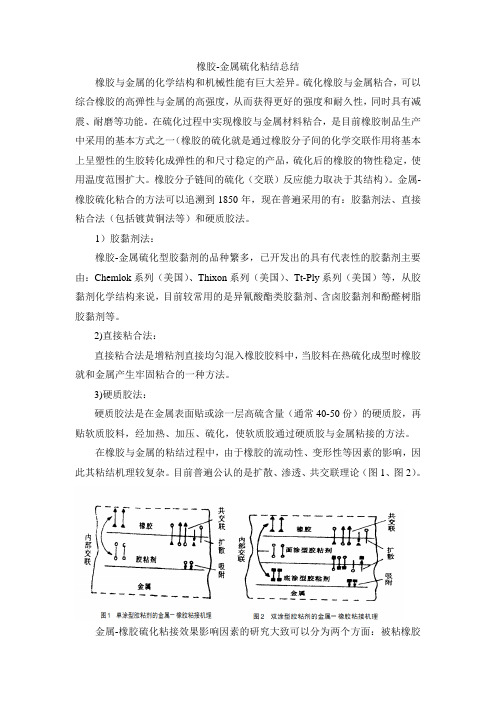
橡胶-金属硫化粘结总结橡胶与金属的化学结构和机械性能有巨大差异。
硫化橡胶与金属粘合,可以综合橡胶的高弹性与金属的高强度,从而获得更好的强度和耐久性,同时具有减震、耐磨等功能。
在硫化过程中实现橡胶与金属材料粘合,是目前橡胶制品生产中采用的基本方式之一(橡胶的硫化就是通过橡胶分子间的化学交联作用将基本上呈塑性的生胶转化成弹性的和尺寸稳定的产品,硫化后的橡胶的物性稳定,使用温度范围扩大。
橡胶分子链间的硫化(交联)反应能力取决于其结构)。
金属-橡胶硫化粘合的方法可以追溯到1850年,现在普遍采用的有:胶黏剂法、直接粘合法(包括镀黄铜法等)和硬质胶法。
1)胶黏剂法:橡胶-金属硫化型胶黏剂的品种繁多,已开发出的具有代表性的胶黏剂主要由:Chemlok系列(美国)、Thixon系列(美国)、Tt-Ply系列(美国)等,从胶黏剂化学结构来说,目前较常用的是异氰酸酯类胶黏剂、含卤胶黏剂和酚醛树脂胶黏剂等。
2)直接粘合法:直接粘合法是增粘剂直接均匀混入橡胶胶料中,当胶料在热硫化成型时橡胶就和金属产生牢固粘合的一种方法。
3)硬质胶法:硬质胶法是在金属表面贴或涂一层高硫含量(通常40-50份)的硬质胶,再贴软质胶料,经加热、加压、硫化,使软质胶通过硬质胶与金属粘接的方法。
在橡胶与金属的粘结过程中,由于橡胶的流动性、变形性等因素的影响,因此其粘结机理较复杂。
目前普遍公认的是扩散、渗透、共交联理论(图1、图2)。
金属-橡胶硫化粘接效果影响因素的研究大致可以分为两个方面:被粘橡胶配方和粘接工艺,在橡胶和金属的粘合过程中,工艺直接影响粘合强度。
工艺包括金属表面处理、硫化条件、镀层等。
橡胶与金属粘合时,不论采用什么方法,均要求对金属表面进行预处理,其目的在于清除金属表面的油污及氧化膜,使金属呈露新鲜表面,并进而适当改变金属表面的结构和极性,以便于它和胶黏剂或橡胶结合。
常用的处理方法有脱脂法、机械打磨法和化学处理法三种。
硫化条件是粘合工艺的核心部分,硫化温度是一个重要因素。
丁腈橡胶与金属粘接的研究进展
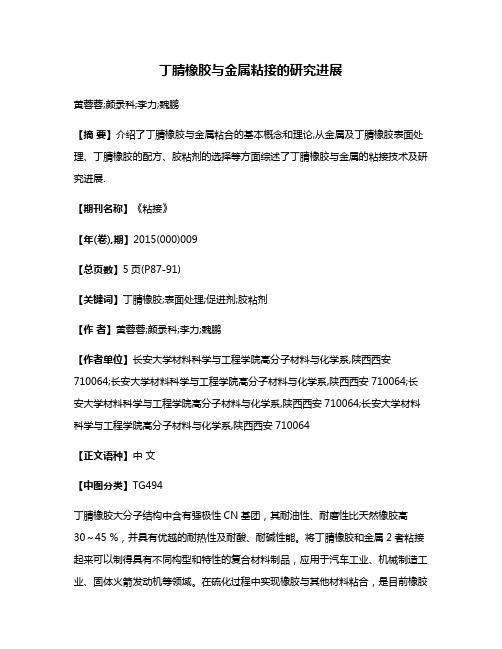
丁腈橡胶与金属粘接的研究进展黄蓉蓉;颜录科;李力;魏鹏【摘要】介绍了丁腈橡胶与金属粘合的基本概念和理论,从金属及丁腈橡胶表面处理、丁腈橡胶的配方、胶粘剂的选择等方面综述了丁腈橡胶与金属的粘接技术及研究进展.【期刊名称】《粘接》【年(卷),期】2015(000)009【总页数】5页(P87-91)【关键词】丁腈橡胶;表面处理;促进剂;胶粘剂【作者】黄蓉蓉;颜录科;李力;魏鹏【作者单位】长安大学材料科学与工程学院高分子材料与化学系,陕西西安710064;长安大学材料科学与工程学院高分子材料与化学系,陕西西安710064;长安大学材料科学与工程学院高分子材料与化学系,陕西西安710064;长安大学材料科学与工程学院高分子材料与化学系,陕西西安710064【正文语种】中文【中图分类】TG494丁腈橡胶大分子结构中含有强极性CN基团,其耐油性、耐磨性比天然橡胶高30~45 %,并具有优越的耐热性及耐酸、耐碱性能。
将丁腈橡胶和金属2者粘接起来可以制得具有不同构型和特性的复合材料制品,应用于汽车工业、机械制造工业、固体火箭发动机等领域。
在硫化过程中实现橡胶与其他材料粘合,是目前橡胶制品生产中采用的基本方式。
由于丁腈橡胶和金属是2种性能完全不同的材料,为了实现丁腈橡胶与金属的牢固结合,要求从金属及丁腈橡胶表面处理、丁腈橡胶配方、胶粘剂的选择等方面进行考虑[1,2]。
金属表面被氧化后生成氧化层,并具有较高的自由能。
任何一种高聚物都会润湿金属表面,而使分界面的自由能降低。
这种物理吸附所形成的粘合强度要大于高聚物本身的粘合强度。
丁腈橡胶的极性较强,粘合指数高,易于与金属骨架粘合。
为了提高丁腈橡胶与金属的粘合强度,胶料与金属粘合后要进行硫化。
硫化后橡胶与金属的粘合界面模型如图1所示,界面层由金属一侧的金属氧化物层和硫化橡胶一侧的复合补强层组成,这2者对硫化橡胶与金属的粘合缺一不可,例如要生成适当的补强层就必需要有金属氧化物层。
橡胶硫化工高级理论知识题库
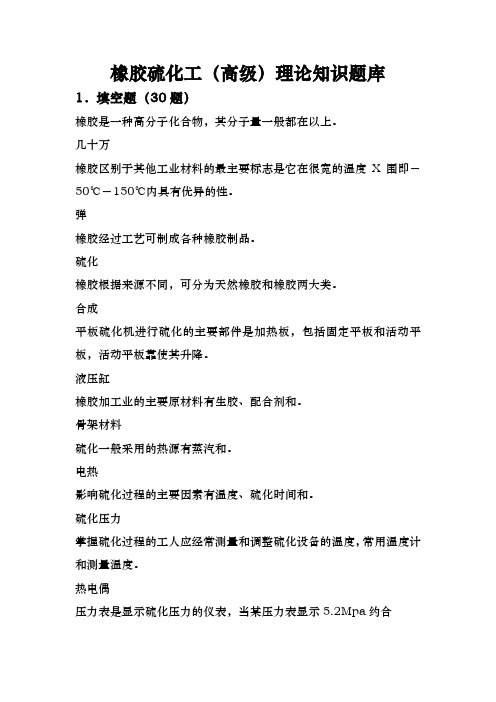
橡胶硫化工(高级)理论知识题库1.填空题(30题)橡胶是一种高分子化合物,其分子量一般都在以上。
几十万橡胶区别于其他工业材料的最主要标志是它在很宽的温度X围即-50℃-150℃内具有优异的性。
弹橡胶经过工艺可制成各种橡胶制品。
硫化橡胶根据来源不同,可分为天然橡胶和橡胶两大类。
合成平板硫化机进行硫化的主要部件是加热板,包括固定平板和活动平板,活动平板靠使其升降。
液压缸橡胶加工业的主要原材料有生胶、配合剂和。
骨架材料硫化一般采用的热源有蒸汽和。
电热影响硫化过程的主要因素有温度、硫化时间和。
硫化压力掌握硫化过程的工人应经常测量和调整硫化设备的温度,常用温度计和测量温度。
热电偶压力表是显示硫化压力的仪表,当某压力表显示5.2Mpa约合大气压。
52橡胶制品的主要硫化设备有平板硫化机和等。
硫化罐平板硫化机按结构形式分为柱式硫化机、框式硫化机等,按工作面分单层、层。
多橡胶加工中的配合剂,按性质可分为硫化剂、硫化促进剂、填充剂、等。
补强剂天然橡胶常温下具有较高的弹性,稍带塑性,温度降低则逐渐变,低于-70℃则变成象玻璃一样的物质。
硬或脆使用切胶机,胶料必须预热,否则不经的胶料本身是硬的,在切胶时,当胶放入刀下容易弹出碰伤或打伤操作人。
预热按照国际标准和我国国家标准,合成橡胶按其主链结构的不同分为6类,即饱和碳—碳链橡胶M类,不饱和碳—碳橡胶R类,聚合物链含硅的橡胶Q类,聚合物链含氧的橡胶O类,聚合物类含硫的橡胶T类,以及聚合物链含碳、氧、氮的橡胶类。
R胶片硬度是表示橡胶混炼均匀和硫化程度的主要标识,硬度是橡胶抵抗外来力的性能。
压常用测胶片硬度。
硬度计橡胶模具是生产橡胶制品硫化的主要设备之一,模具设计的依据是制品的形状、特性和,根据同一件橡胶制品可以设计出几种不同结构的模具。
使用要求为使模具保持较好的光洁度,应对模具进行定期。
保养橡胶制品的工作面分为静态和动态两类。
静态工作面用于固定密封部位,工作面用于活动密封部位。
橡胶与金属骨架粘合失效原因分析及解决方法探讨
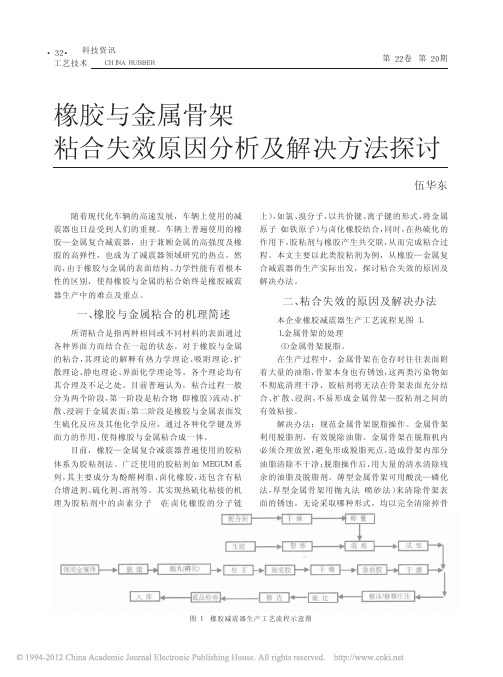
CHINARUBBER橡胶与金属骨架粘合失效原因分析及解决方法探讨伍华东随着现代化车辆的高速发展,车辆上使用的减震器也日益受到人们的重视。
车辆上普遍使用的橡胶—金属复合减震器,由于兼顾金属的高强度及橡胶的高弹性,也成为了减震器领域研究的热点。
然而,由于橡胶与金属的表面结构、力学性能有着根本性的区别,使得橡胶与金属的粘合始终是橡胶减震器生产中的难点及重点。
一、橡胶与金属粘合的机理简述所谓粘合是指两种相同或不同材料的表面通过各种界面力而结合在一起的状态。
对于橡胶与金属的粘合,其理论的解释有热力学理论、吸附理论、扩散理论、静电理论、界面化学理论等。
各个理论均有其合理及不足之处。
目前普遍认为,粘合过程一般分为两个阶段,第一阶段是粘合物(即橡胶)流动、扩散、浸润于金属表面;第二阶段是橡胶与金属表面发生硫化反应及其他化学反应,通过各种化学键及界面力的作用,使得橡胶与金属粘合成一体。
目前,橡胶—金属复合减震器普遍使用的胶粘体系为胶粘剂法。
广泛使用的胶粘剂如MEGUM系列,其主要成分为酚醛树脂、卤化橡胶,还包含有粘合增进剂、硫化剂、溶剂等。
其实现热硫化粘接的机理为胶粘剂中的卤素分子(在卤化橡胶的分子链上),如氯、溴分子,以共价键、离子键的形式,将金属原子(如铁原子)与卤化橡胶结合,同时,在热硫化的作用下,胶粘剂与橡胶产生共交联,从而完成粘合过程。
本文主要以此类胶粘剂为例,从橡胶—金属复合减震器的生产实际出发,探讨粘合失效的原因及解决办法。
二、粘合失效的原因及解决办法本企业橡胶减震器生产工艺流程见图1。
1.金属骨架的处理(1)金属骨架脱脂。
在生产过程中,金属骨架在仓存时往往表面附着大量的油脂,骨架本身也有锈蚀,这两类污染物如不彻底清理干净,胶粘剂将无法在骨架表面充分结合、扩散、浸润,不易形成金属骨架—胶粘剂之间的有效粘接。
解决办法:规范金属骨架脱脂操作。
金属骨架利用脱脂剂,有效脱除油脂。
金属骨架在脱脂机内必须合理放置,避免形成脱脂死点,造成骨架内部分油脂清除不干净;脱脂操作后,用大量的清水清除残余的油脂及脱脂剂。
橡胶配方设计及橡胶与金属的粘接工艺
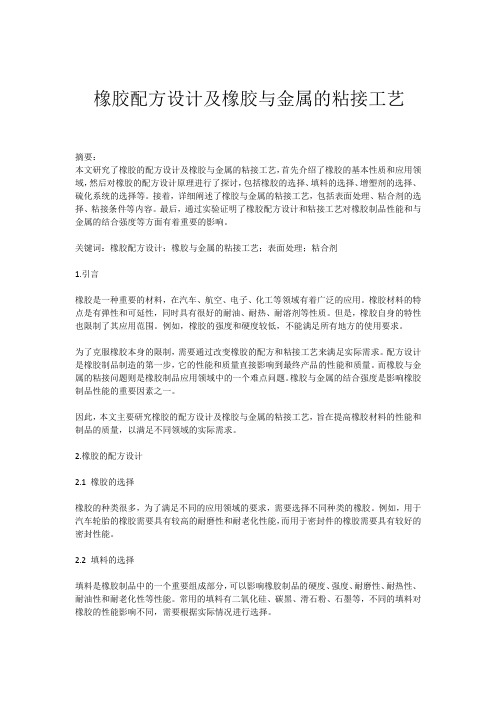
橡胶配方设计及橡胶与金属的粘接工艺摘要:本文研究了橡胶的配方设计及橡胶与金属的粘接工艺,首先介绍了橡胶的基本性质和应用领域,然后对橡胶的配方设计原理进行了探讨,包括橡胶的选择、填料的选择、增塑剂的选择、硫化系统的选择等。
接着,详细阐述了橡胶与金属的粘接工艺,包括表面处理、粘合剂的选择、粘接条件等内容。
最后,通过实验证明了橡胶配方设计和粘接工艺对橡胶制品性能和与金属的结合强度等方面有着重要的影响。
关键词:橡胶配方设计;橡胶与金属的粘接工艺;表面处理;粘合剂1.引言橡胶是一种重要的材料,在汽车、航空、电子、化工等领域有着广泛的应用。
橡胶材料的特点是有弹性和可延性,同时具有很好的耐油、耐热、耐溶剂等性质。
但是,橡胶自身的特性也限制了其应用范围。
例如,橡胶的强度和硬度较低,不能满足所有地方的使用要求。
为了克服橡胶本身的限制,需要通过改变橡胶的配方和粘接工艺来满足实际需求。
配方设计是橡胶制品制造的第一步,它的性能和质量直接影响到最终产品的性能和质量。
而橡胶与金属的粘接问题则是橡胶制品应用领域中的一个难点问题。
橡胶与金属的结合强度是影响橡胶制品性能的重要因素之一。
因此,本文主要研究橡胶的配方设计及橡胶与金属的粘接工艺,旨在提高橡胶材料的性能和制品的质量,以满足不同领域的实际需求。
2.橡胶的配方设计2.1 橡胶的选择橡胶的种类很多,为了满足不同的应用领域的要求,需要选择不同种类的橡胶。
例如,用于汽车轮胎的橡胶需要具有较高的耐磨性和耐老化性能,而用于密封件的橡胶需要具有较好的密封性能。
2.2 填料的选择填料是橡胶制品中的一个重要组成部分,可以影响橡胶制品的硬度、强度、耐磨性、耐热性、耐油性和耐老化性等性能。
常用的填料有二氧化硅、碳黑、滑石粉、石墨等,不同的填料对橡胶的性能影响不同,需要根据实际情况进行选择。
2.3 增塑剂的选择增塑剂是用来提高橡胶的可加工性和弹性的。
常用的增塑剂有道地油、减压蒸馏油、芳烃溶剂等。
配方及工艺对橡胶与金属粘合性能的影响

题目:配方及工艺对橡胶与金属粘合性能的影响摘要文章综述了近十年来配方及工艺对橡胶与金属粘合性能的影响,橡胶与金属的发展现状、粘合基本原理及理论解释和粘合方法,从配方和工艺探讨橡胶与金属的粘合性能,针对橡胶与金属粘合过程出现的问题,分析粘合失效的类型和原因,并提出相应的解决对策。
AbstractThis article reviewed the formula and process over the past decade on the rubber and metal adhesion property, the development of rubber and metal status of the basic principles and theories to explain agglutinate and adhesive methods, from the formula and technology of adhesion property of rubber and metal for rubber to metal agglutinate process problem, analyze the types and causes of adhesion failure, and corresponded countermeasures.关键词:配方工艺胶黏剂橡胶与金属粘合Key word: Formula Technology Adhesive Rubber and metal Agglutinate目录引言 (1)1 橡胶与金属粘合发展现状 (2)2 粘合的基本原理和理论解释 (3)2.1 粘合的基本原理 (3)2.2 理论解释[3] (4)2.2.1 热力学理论 (4)2.2.2 吸附理论 (4)2.2.3 扩散理论 (5)2.2.4 静电理论 (5)3 橡胶与金属的粘合 (5)3.1 橡胶与金属的粘合方法 (5)4 配方对橡胶与金属粘合性能的影响[5] (6)4.1 橡胶材料对粘合性能的影响 (6)4.1.1 胶种 (7)4.1.2 硫化体系 (7)4.1.3 硫化剂 (8)4.1.4 增塑剂 (8)5 工艺对橡胶与金属粘合性能的影响[6] (9)5.1表面处理工艺 (9)5.1.1 抛丸工艺 (9)5.1.1.1抛丸时间 (10)5.1.1.2钢丸粒径 (10)5.2 磷化工艺 (11)5.2.1 磷化液的酸点对粘合性能的影响 (11)5.2.2 磷化时间对粘合性能的影响 (12)5.2.3 磷化温度对粘合性能的影响 (13)5.3 胶粘剂工艺对粘合性能的影响[7] (14)6 橡胶与金属粘合失效类型、失效分析以及解决对策[8] (14)6.1 橡胶与金属粘合失效类型 (14)6.2 橡胶与金属粘合失效的原因分析以及解决对策 (14)6.2.1底涂型胶粘剂与金属间破坏 (14)6.2.1.1金属表面处理不当 (14)6.2.1.2 胶粘剂选择不当 (15)6.2.1.3 涂胶工艺不当 (16)6.2.2 胶粘剂内部破坏、面涂型胶粘剂与底涂型胶粘剂之间破坏 (16)6.2.3 橡胶与面涂型胶粘剂之间破坏 (17)6.2.3.1 橡胶胶料不合适 (17)6.2.3.2 胶粘剂因素 (17)6.2.3.3 硫化工艺不合适 (18)6.2.4 橡胶内部破坏 (18)结语 (19)参考文献 (20)引言19世纪发明了用硫黄硫化橡胶,这种方法可以在许多领域使用。
橡胶的工艺流程
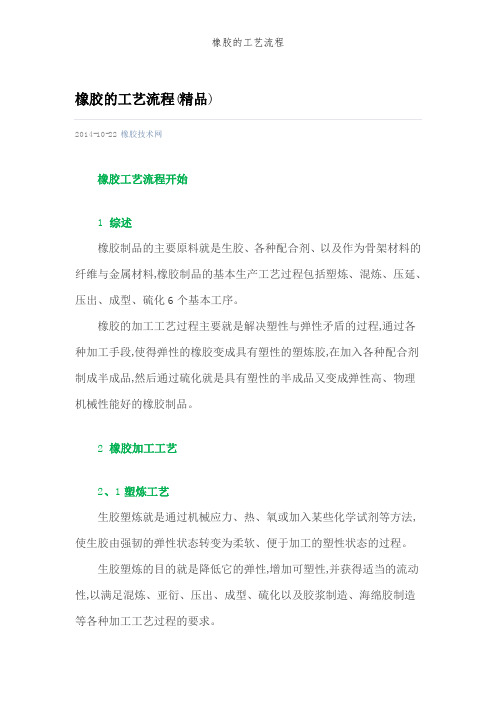
橡胶的工艺流程(精品)2014-10-22橡胶技术网橡胶工艺流程开始1 综述橡胶制品的主要原料就是生胶、各种配合剂、以及作为骨架材料的纤维与金属材料,橡胶制品的基本生产工艺过程包括塑炼、混炼、压延、压出、成型、硫化6个基本工序。
橡胶的加工工艺过程主要就是解决塑性与弹性矛盾的过程,通过各种加工手段,使得弹性的橡胶变成具有塑性的塑炼胶,在加入各种配合剂制成半成品,然后通过硫化就是具有塑性的半成品又变成弹性高、物理机械性能好的橡胶制品。
2 橡胶加工工艺2、1塑炼工艺生胶塑炼就是通过机械应力、热、氧或加入某些化学试剂等方法,使生胶由强韧的弹性状态转变为柔软、便于加工的塑性状态的过程。
生胶塑炼的目的就是降低它的弹性,增加可塑性,并获得适当的流动性,以满足混炼、亚衍、压出、成型、硫化以及胶浆制造、海绵胶制造等各种加工工艺过程的要求。
掌握好适当的塑炼可塑度,对橡胶制品的加工与成品质量就是至关重要的。
在满足加工工艺要求的前提下应尽可能降低可塑度。
随着恒粘度橡胶、低粘度橡胶的出现,有的橡胶已经不需要塑炼而直接进行混炼。
在橡胶工业中,最常用的塑炼方法有机械塑炼法与化学塑炼法。
机械塑炼法所用的主要设备就是开放式炼胶机、密闭式炼胶机与螺杆塑炼机。
化学塑炼法就是在机械塑炼过程中加入化学药品来提高塑炼效果的方法。
开炼机塑炼时温度一般在80℃以下,属于低温机械混炼方法。
密炼机与螺杆混炼机的排胶温度在120℃以上,甚至高达160-180℃,属于高温机械混炼。
生胶在混炼之前需要预先经过烘胶、切胶、选胶与破胶等处理才能塑炼。
几种胶的塑炼特性:天然橡胶用开炼机塑炼时,辊筒温度为30-40℃,时间约为15-20min;采用密炼机塑炼当温度达到120℃以上时,时间约为3-5min。
丁苯橡胶的门尼粘度多在35-60之间,因此,丁苯橡胶也可不用塑炼,但就是经过塑炼后可以提高配合机的分散性顺丁橡胶具有冷流性,缺乏塑炼效果。
顺丁胶的门尼粘度较低,可不用塑炼。
橡胶制品生产过程质量控制考核试卷
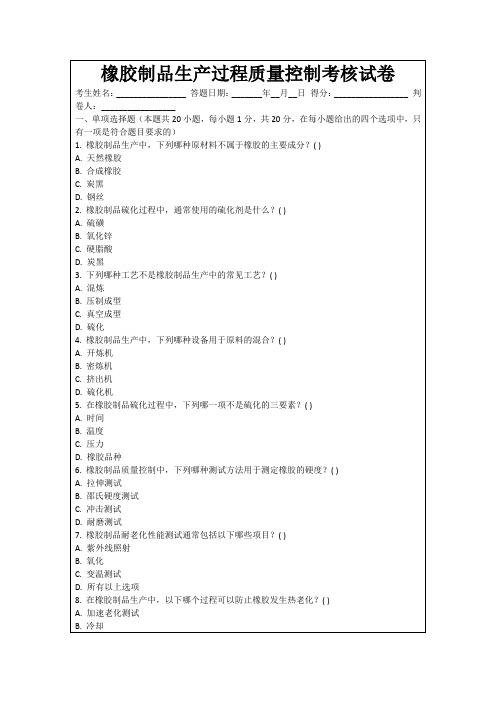
B.氧化
C.变温测试
D.所有以上选项
8.在橡胶制品生产中,以下哪个过程可以防止橡胶发生热老化?( )
A.加速老化测试
B.冷却
C.硫化
D.混炼
9.橡胶制品生产过程中,哪个环节对产品的尺寸精度影响最大?( )
A.混炼
B.成型
C.硫化
D.后处理
10.下列哪种材料不适合用于橡胶制品的填充剂?( )
A.温度
B.橡胶类型
C.硫化剂的用量
D.环境湿度
17.下列哪种工艺可以减少橡胶制品生产中的废料?( )
A.精密成型
B.大批量生产
C.简化工艺流程
D.以上所有选项
18.橡胶制品质量控制中,下列哪种测试主要用于评估产品的耐化学性?( )
A.耐酸碱测试
B.拉伸测试
C.硬度测试
D.耐磨测试
19.下列哪种设备常用于橡胶制品的切割和冲孔?( )
10.橡胶制品的耐臭氧性能测试通常在_______条件下进行。()
四、判断题(本题共10小题,每题1分,共10分,正确的请在答题括号中画√,错误的画×)
1.橡胶制品的硬度越高,其弹性越好。()
2.硫化过程中,温度越高,硫化速度越快。()
3.橡胶制品生产中,所有添加剂都是必要的。()
4.橡胶制品的耐磨性仅与橡胶的硬度有关。()
A.成型模具磨损
B.橡胶流动性差
C.成型压力不足
D.后处理不当
19.以下哪些情况可能导致橡胶制品在储存或运输过程中损坏?( )
A.温度变化
B.湿度变化
C.压缩堆放
D.橡胶之间的摩擦
20.橡胶制品生产中,以下哪些措施可以提高生产效率和产品质量?( )
- 1、下载文档前请自行甄别文档内容的完整性,平台不提供额外的编辑、内容补充、找答案等附加服务。
- 2、"仅部分预览"的文档,不可在线预览部分如存在完整性等问题,可反馈申请退款(可完整预览的文档不适用该条件!)。
- 3、如文档侵犯您的权益,请联系客服反馈,我们会尽快为您处理(人工客服工作时间:9:00-18:30)。
橡胶与金属的粘合是橡胶制品制造过程中的重要环节,如果粘合不良或无法粘合,一些橡胶制品如轮胎、钢丝输送带、橡胶软管,橡胶计架油封、汽门油封,橡胶金属组合垫圈、组合胶套等橡胶金属复合制品就无法制作。
就橡胶密封制品而言,上世纪80年代初,青岛密封件厂协同青岛化工厂研制成功了 RM-1粘合剂,替代日本TD870成功生产岀与国外同等水平的許架油封,使引进的国外技术得以消化吸收,开辟了卄架汕封制作的新工艺。
上世纪 90年代,由于汽车工业的发展,不少厂家要求用氟橡胶制作骨架汕封、汽车汕封,但是粘合问题不好解决,严重的制约了该产品的开发,当时青岛双星集团密封件厂成功的研制了 FG-1氟橡胶与黑色金属的热硫化粘合剂,使氟橡胶与金属计架牢牢的粘合成一体,顺理成章的研发成功斯太尔发动机曲轴前后油封和气门油封替代了进口,满足了配套需要,该粘合剂一直使用至今。
因此橡胶与金属粘合是极其重要的应用技术,应引起生产企业的高度重视。
1金属竹架的表面处理)计架表而无油污、无锈蚀,有一左粗糙度的新鲜表而才能有效的与金属粘合,因此竹架必须进行表面处理,处理大体有两种方法:一是机械法处理。
如采用履带式的抛丸淸理机326或滚筒式的抛丸淸理机Q3110,将粒径0.5mm的钢砂喷射到计架表面,将表面的锈蚀等有害物料喷掉,使表面新鲜并增大表而积,加大计架与胶粘剂间的接触面:二是化学法。
即酸洗处理,磷化钝化处理,其工艺过程是碱液去油,酸液去锈,磷化上磷化膜,然后进行钝化烘干,碱液是有多种材料如苛性钠、硅酸钠(表而湿润剂)、焦磷酸钠(阴离子表而活性剂)、烷基磺酸钠组成的水溶液,淸洗温度80-9CTC,时间视表而的汕污多少而有差异,一般是5min左右。
去油污的计架经流动的自来水冲洗后,进行酸洗处理,而不同的金属去锈时对酸的品种是有选择性的。
例如,铁件要用盐酸淸洗处理。
铜件和不锈钢忖架采用硫酸、硝酸混合液协同去锈。
铝件用硫酸、馅酸混合液进行处理。
要求对周IM环境不产生或少产生腐蚀时,而金属件架锈蚀较轻的竹架,可采用以草酸为主,掺用少戢硫酸和加入缓钝剂的水溶液进行处理。
磷化是黑色金属表而处理的重要方法。
磷化液的品种很多, 如常温磷化液,采用的是铁系磷化液,骨架经酸洗后进行表调,放入常温磷化液中(温度30°C 左右)处理5-6min:中温磷化是采用锌系或锌钙系的磷化液,件架在65-75°C下处理6min左右:髙温磷化液是锚系磷化液,骨架在80-90°C下处理3-4min,目前采用中温磷化液较好,因常温磷化表面磷化膜磷化后停放时容易造成再生锈,髙温磷化的竹架表而磷化膜粗糙而且较厚,易造成脱落,中温磷化,磷化膜细致而牢固有利于粘合。
磷化后的丹架要进行钝化处理,主要是通过钝化液的表而处理,封闭骨架表而的易氧化离子,防止件架再生锈。
钝化液的品种很多,如以辂酸盐类、硝酸盐类,三乙酸胺为代表的有机胺类,其中珞酸盐类钝,化效果好,表而的珞离子有利于与橡胶的粘合,但珞酸盐类环保控制较严格,需进行废液的处理,对于难粘合如不锈钢件架除混合酸淸冼后进行表而钝化后还需进行偶化处理,这有利于提高粘合强度。
如无锡威力达公司生产的全电脑控制双勾磷化处理线,温度、浸洗时间、烘干时间、停放滴水时间等全部自动控制,可有效的保证处理质量。
其工艺过程是碱液去锈(5°C X3n】in),吊起滴水(常温X lmin)-*自来水冲洗(常温X lminL酸液去锈(常温X3minL吊起滴液(常温XlminL流动自来水冲洗(常温X0.5min)-磷化处理(65-70a C X5-6min)-*吊起滴液(常温X lmin)-*流动自来水冲洗(常温X lmin)-*吊起滴液(常温><11血)-*钝化(90°。
X 0.5minL烘干备用。
2粘合胶、胶料配方的设计要使橡胶与金属件架产生良好的粘合强度,必须要在粘合剂与金属界而上和粘合剂与橡胶界面上,具有良好的扩散、湿润、吸附、渗透能力,大的分子间的引力(即范徳华引力)和密集的化学键及良好的共硫化效应,要达到上述要求,除选择高活性的粘合剂、严格的金属骨架表而处理工艺和正确的配制浸涂、预固化粘合剂之外,橡胶配方是极其重要的因素,若胶料配方不当,苴粘着强度低而且适应性也差。
丁腊橡胶勺铁骨架浸涂酚类粘合剂,以进行热硫化为例,通过试验发现丁腊橡胶随着丙烯猜含量的增加,粘合强度随之提髙(见表1)。
不同丙烯腊含量丁腊橡胶的粘合强度生胶品种国产丁尉橡胶40日本丁睛橡胶203S国产丁腊橡胶26、27-30日本丁尉橡胶N-41日本丁睛橡胶240S国产丁腊橡胶18丙烯睛含 S:/%36-3832-3426-3027-2822-2418-20粘着强度/MPa5.04.84.73.5光面光而试验配方:丁睛橡胶变量,氧化锌5:硬脂酸防老剂RD 2;MB二辛酯15:炭黑95:硫黄0.5:TMTD 1: TETD 1份:DM 2.5。
从表1可看岀不同品种的丁睛橡胶,粘着强度的差异很大,丁腊橡胶40最好,230尚可,中低丙烯腊含量的胶料粘着强度最差。
+ e k:S!A3@7_1 e本文来自:橡胶技术网2.5o从表1可看出不同品种的丁腊橡胶,粘着强度的差异很大,丁腊橡胶40最好,230尚可,中低丙烯膳含量的胶料粘着强度最差。
试验中还发现丁席橡胶的硫化体系对粘合强度有较大影响8不同硫化体系的丁腊胶与铁件架的粘合强度硫化体系 DCP+TMTD+DM+S2 , 1.5, 1.5 , O.3DCP+S+DM2 , 0.3 , 1.5S+DM1.5 ,1.5S+TMTD+DM0.5, 2, 3 粘着强度 /MPa>5.04.54.03.7试验配方组成:丁腊橡胶26 100:氧化锌5:硬脂酸1:炭黑90:二辛酪15:凡士林3;防老剂3。
件架喷砂后,浸涂RM-1粘合剂经145°C预固化15min进行热硫化粘着。
从表2中看岀过氧化物硫化体系的粘着强度〉硫黄体系的粘着强度>低硫髙促硫化体系的粘着强度。
在试验和生产实践中还发现,中低丙烯腊含量的生胶采用过氧化物硫化体系的胶料配方,其补强剂对粘着强度的影响也很大。
白炭黑胶料的粘着强度〉白炭黑+喷雾炭黑(1:2)>喷雾炭黑+ 半补强,炭黑(1: 1)。
在丁腊橡胶26中在硫黄1.5份,DM 1.5份的配方中加入间甲白体系(即 RS2, RH2.5,白炭黑15)的粘合强度较高,拉力机无法拉断,在白炭黑的胶料中加入凡丄林有助于粘合,若加入适量的硅烷偶联剂可进一步提髙粘合强度。
其他通用性非极性橡胶与金属的粘合与丁睛橡胶相类似。
如天然橡胶与铜嘴的直接粘合配方(不涂粘合剂)采用高氧化锌 40份、硫黄3.5-份,添加适量的增粘剂松焦油、黄油、氧化铁红可使酸液淸洗后的铜嘴恃架直接进行热硫化粘着,英他通用型橡胶如丁苯橡胶、氯丁橡胶、三元乙丙橡胶、顺丁橡胶添加上述材料也可提髙橡胶与金属的粘合强度。
粘合剂主要分五大类:⑴异鼠酸酯类,如列克钠;(2)树脂类如RM-K TD870, GN-1等: (3)卤化橡胶或环化橡胶类如开姆洛克220,开姆希尔211等:(4)硅烷类如3290.5150和GF-1 等:(5)硅烷和树脂混介类如512、PC-22等。
目前市场销售较多的是美国开姆洛克系列粘合剂,徳国汉髙的开姆希尔系列粘合剂。
该系列粘合剂为开姆洛克新品,另外还有麦加母系列粘合剂,国内青岛化工厂的BM-1和青岛鲁中泰化工公司的GF-1和GN-1粘合剂等。
氟橡胶与金属的粘合可选择徳国汉高公司开姆希尔512、保乐固PC-22、美加母3290和青岛鲁中泰的GF-K 丁腊橡胶、ACM胶、聚氨酯橡胶可选择韩国产的TD870,青岛化工厂的 RM-1,青岛鲁中泰公司的GN-1,无色制品可选择透明粘合剂PC-35。
英他通用类型的橡胶, 如天然橡胶、丁苯,橡胶、顺丁橡胶、氯丁橡胶、三元乙丙橡胶等,可选择树脂类的粘合剂做底胶如开姆希尔211,麦加母的3270/3276,开姆洛克205然后再涂如开姆希尔225,美加母100、115,开姆洛克250、252o硅橡胶与金属的粘合,可选择3290,过氧化硅烷VTPS 和GF-1进行热硫化粘合。
粘合剂的应用工艺也很重要,用于TD870粘合剂的溶剂和稀释剂必须用甲醇或乙醇做溶剂。
粘合剂与溶剂的配比,因金属竹架板材的料厚有所差别,料厚0.3-0.&nm的配比(粘合剂:溶剂)是 1: 8-1: 12;料厚 0.8-1.2mm 配比是 1: 8-1: 6): 1.2 以上的是 1: 6-1: 4, 512 和PC-22必须用甲乙酮做溶剂配比是1: 4-1: 8。
3290必须,用无水乙醇做溶剂,配比是1:3-1:4。
橡胶类的粘合剂如开姆希尔411,开姆洛克250,麦加母14450,可用甲苯、二甲苯做稀释剂,用量20%左右,金属骨架浸涂粘合剂和浸涂后的预固化停放时间也很重要,一般树脂类、硅烷类、硅烷和树脂混介类的粘合剂,可将骨架全部浸到粘合剂溶剂溶液中进行离心浸涂,橡胶类粘合剂因粘度髙,必须进行刷涂或喷涂,涂后的金属计架必须进行常温停放,挥发掉溶剂后进行预固化。
如TD870、RM-k GN-1粘合剂需径145±3*C X lOmin的预固化。
3290和GF-1粘合剂常温停放5min后,须经150°CX10min的预固化。
橡胶类的粘合剂可常温停放待溶剂挥发后,即可进行热硫化,预固化后的计架要放巻在于燥淸洁场地, TD87O的计架可放置于3周左右,3290和GF-1世架不宜超过5天。
1.金属计架表而必须进行喷砂处理或化学处理,才能与金属进行热硫化粘着。
2.—般通用型橡胶如丁腊橡胶、丁苯橡胶等采用过氧化物硫化体系或硫黄硫化体系,有利于粘合,配方中加入适量的白炭黑、硅烷偶联剂、增粘树脂、氧化铁红等可提高粘合强度。
3•开姆希尔新品种粘合剂可应用于橡胶与金属的热硫化粘着。
粘合剂与溶剂的配比及其浸涂工艺、预固化工艺是热硫化粘着的重要工艺过程,必须严格控制。