8D报告培训资料
8D报告培训资料(精典实用)
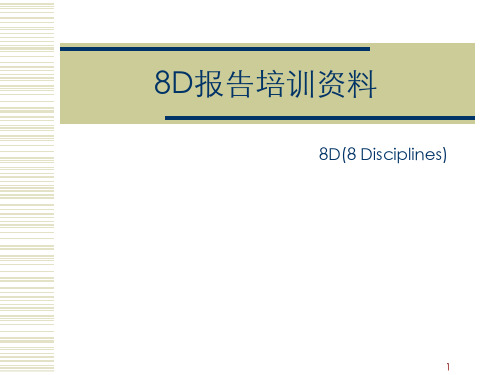
8
6
4
83.33%
2
0 A
10
8 8
6
53.33%
4
2
0 A
ZT-188色差制程不良原因统计
不良数
累积不良
100.00%
91.67%
1
1
B
C
ZT-188色差流出原因统计
不良数
累积不良
86.67% 5
93.33%
1
B
C
100.00%
0 D 100.00%
1 D
105.00% 100.00% 95.00% 90.00% 85.00% 80.00% 75.00%
22
恭贺小组成员
对所有积极参与的小组成员 进行适当的承认
对小组的效益进行沟通
23
8D报告常用到的分析工具
旧QC七大手法:
新QC七大手法:
层别法(Stratification)
亲和图(也称KJ法)
管制图(Control Chart控制图)
关连图
直方图(Histogram)
过程决策程序图PDPC法
特性要因图(鱼骨图Cause and effect diagram) 网络图(统筹法)
9
何谓 5W2H
Who: Identify customers complaining What: Identify the problem adequately and accurately When: Timing when did the problem start Where: Location where is it occurring Why: Identify known explanations How: In what mode or situation did the
8D报告培训教材

根本原因确定
深入分析
对已经确认的问题原因进行进一 步分析,找出根本原因。
跨部门合作
邀请相关部门和专家共同参与分 析,确保根本原因确定的准确性
和全面性。
制定措施
根据根本原因,制定相应的纠正 和预防措施,避免问题再次发生
。
04
纠正措施与预防措施
纠正措施制定
问题分析
对发生的问题进行深入分析,找出根本原因。
8D报告培训教材
目录
• 8D报告概述 • 问题识别与定义 • 原因分析与验证 • 纠正措施与预防措施 • 效果评估与持续改进 • 8D报告编写技巧与注意事项 • 案例分析与实战演练
01
8D报告概述
定义与背景
定义
8D报告是一种结构化的问题解决 工具,用于识别、分析和解决产 品或过程中的问题。
背景
05
效果评估与持续改进
效果评估
01
评估标准
制定明确的评估标准,包括问题解决率、客户满意度、生产效率等关键
指标,以便客观地衡量8D报告的效果。
02
数据收集
收集相关的数据和信息,如问题发生频率、处理时长、资源消耗等,以
便对8D报告的执行情况进行全面分析。
03
结果分析
对收集到的数据进行分析,识别改进的机会和潜在问题,为持续改进提
避免方法包括制定具体的实施 计划、明确责任人和完成时间 、提供必要的资源支持等。
04
验证效果不佳
避免方法包括制定科学的验证 方案、收集客观的数据进行验 证、及时调整纠正措施等。
07
案例分析与实战演练
案例介绍与背景
案例来源
选取具有代表性的实际案例,涉及产品缺陷、客户投诉等问题。
8D报告培训资料课件

• Eliminate the problems the first time.
做到第一次就消除问题所在
• Prevention of future problems.
实现潜在问题的预防
2012.10.17GS/wey
8D Training
5
CAR/8D Report Problems 完成CAR/8D报告存在的问题
是否对产品的所有流程采取了围堵措施(如生产线、仓库及 发
货)?
• Has detailed instructions on containment been issued to people responsible for containment?
2012是.10否.17G给S/w负ey 责实施围堵措施8D的Tr人ain员ing发放了详细的清拉单?
• Poor Problem Description 差劲的问题描述
–“Customer received wrong part.”
–客户接收到错误零件
• Good Problem Description 完美的问题描述
–“Customer received incorrect value CRCW-0603 resistors on 4/1/12. Customer P.O. 441960 (GS P.O. X765644-30) specified CRCW-0603, 8.2K ohm and received CRCW-0603, 82K ohm parts.”
建立跨功能小组
• Identify a Champion. 确定小组长
• Members should be from all affected areas, not just quality! i.e. Sales, Logistics, Marketing, Engineering, Line Operators, Production Mgmt., etc…
8D报告培训材料(PPT 44页)

D2 问题确认
练习:
XX月XX日,你正在办公室忙碌着,手机响了,你没看就接 听,结果电话里出来你妈妈焦急的声音:“满屋子都是水, 怎么办哪?” 你会怎么做D0、D2?
D3 临时措施
临时措施是什么? ➢在实施前被验证为有效的 ➢使用过程中是被监控的 ➢是被文件化了的 ➢将要被永久措施(PCA)所取代 ➢这个过程/操作要增加成本
1、要解决的问题: ➢任命领导者。 ➢小组中有供方。 ➢小组中有顾客。 ➢小组中有其他相关人员。 ➢小组头脑风暴活动有书面文件。
2、易犯的错误 ➢所选择的完成8D过程的小组成员没有技术知识。 ➢只有一两个人实施该过程。
D2 问题确认
确定问题发生时: 时间:X月XX日XX(时):XX(分) 地点(工况):路况是山路、水泥路、高速路等?时速?Km/h, 人物(谁):司机是谁,开车时的状态(是否按时吃饭、休息、喝酒、身体
8D培训
案例:找错
D2:确认问题: 贵公司反馈:B301后雨刮臂安装孔超差,抽查38件发现6件,故障比例为15.8%。技术要求:6(0.1— 0.3)mm,实测值:7.20mm,7.04mm,6.60mm,6.60mm,7.06mm,6.58mm.我公司在内部进行了排 查确认。 D3:临时措施: 在制品的处置:将注塑后的成品件使用专用止规进行全检,确保接头内衬直径不超过6.3mm,1月17日新 生产的700套已全检(检出不良品65Pcs) 库存品的处置:我公司现场服务人员将安排人员对贵方现场所有库存品进行全检上线。 以上措施立即执行 D4:根本原因分析: 压铸零件是我公司采购的零部件,经过供应商排查发现:接头锥孔衬套压铸件一出四,压铸模其中一根芯 支外径偏大造成模具压出的对应衬套产品内径变大。进一步追溯属于供应商在生产过程中压铸模具芯支断 裂,更换芯支后生产时检验员发现内衬孔有超差,然后重新更换芯支。供应商不合格产品没有清理干净混 入合格品中发往我公司。进料检验抽检时没有抽到不合格品而判定此批合格 D5:纠正措施: 1.要求供应商完善对模具维修后的质量检测控制; 2.该零件的检验方式由正常检验调整为加严检验; 3.注塑成形的半成品接头组件使用专用止规全检,确保不合格的产品不流出。 以上措施完成时间:2011-2-1 D6:措施验证: 出货检验对成品库1000套产品进行抽检,未发现不良品。 D7:预防再发生: 1.要求供应商完善对模具维修后的质量检测控制; 2.该零件的检验方式由正常检验调整为加严检验; 3.注塑成形的半成品接头组件使用专用止规全检,确保不合格的产品不流出。
8D报告培训

8D报告培训一、概述8D报告是一种用于问题解决和持续改进的工具,广泛应用于企业、组织和个人。
8D报告培训旨在帮助学员掌握8D报告的基本原理和应用技巧,提高问题解决和持续改进的能力。
本文档将详细介绍8D报告培训的目标、内容、方法、效果评估等方面,以便于培训者和学员更好地开展和参与培训。
二、培训目标1.了解8D报告的起源、发展和应用背景;2.掌握8D报告的基本原理和步骤;3.学会运用8D报告进行问题分析和解决;4.培养持续改进的思维和方法;5.提高团队协作和沟通能力;6.提升个人和组织的问题解决能力。
三、培训内容1.8D报告的起源和发展介绍8D报告的起源、发展历程及其在现代企业和组织中的应用背景。
2.8D报告的基本原理和步骤详细讲解8D报告的八个步骤,包括问题陈述、团队组建、根本原因分析、行动计划制定、行动计划实施、效果验证、预防措施制定和总结与关闭。
3.问题分析和解决方法介绍常见的问题分析工具和方法,如鱼骨图、5个为什么、头脑风暴等,并指导学员如何运用这些工具和方法进行问题分析和解决。
4.持续改进的思维和方法培养学员持续改进的思维,介绍持续改进的方法和工具,如PDCA循环、六西格玛、Kzen等。
5.团队协作和沟通技巧讲解团队协作的重要性,教授团队协作和沟通的技巧,如有效沟通、冲突解决、团队建设等。
6.案例分析和实战演练通过案例分析,让学员了解8D报告在实际工作中的应用,并进行实战演练,提高学员的问题解决能力。
四、培训方法1.讲授法通过讲解、演示、案例分析等方式,传授8D报告的基本原理和应用技巧。
2.互动讨论组织学员进行小组讨论,分享经验和心得,促进学员之间的交流和互动。
3.案例分析分析实际案例,让学员了解8D报告在实际工作中的应用,提高学员的问题解决能力。
4.实战演练设置实际工作场景,让学员运用所学知识进行问题分析和解决,提高学员的实际操作能力。
5.角色扮演通过角色扮演,让学员体验不同角色在问题解决过程中的责任和作用,提高学员的沟通和协作能力。
8D报告培训全

8D报告培训全8D报告培训全解析一、概述8D报告是一种广泛应用于品质管理和问题解决的工具,起源于美国汽车行业,后被众多企业借鉴和应用。
8D报告培训旨在帮助企业和员工掌握8D报告的方法和技巧,提高问题解决和品质管理能力。
本文将从8D报告的定义、培训内容、培训方法和培训效果等方面进行全面解析。
二、8D报告的定义和作用8D报告是一种结构化的问题解决方法,它包括8个D,即8个步骤,分别是:D0-问题识别、D1-团队组建、D2-问题描述、D3-临时措施、D4-根本原因分析、D5-永久措施、D6-实施和验证、D7-预防措施、D8-团队表彰和总结。
8D报告的作用在于帮助企业和员工系统地解决问题,避免问题重复发生,提高产品和服务的品质。
三、8D报告培训内容1. 8D报告的基本原理和步骤:培训学员了解8D报告的起源、发展、基本原理和8个步骤,掌握8D报告的结构和逻辑。
2. 问题识别和描述:培训学员学会如何识别和描述问题,包括问题的现象、影响、范围等。
3. 团队组建和沟通:培训学员学会如何组建高效的问题解决团队,以及如何进行有效的沟通和协作。
4. 临时措施和根本原因分析:培训学员掌握制定临时措施的方法,以及进行根本原因分析的技巧。
5. 永久措施和预防措施:培训学员学会制定和实施永久措施,以防止问题再次发生,以及制定预防措施,以避免类似问题的发生。
6. 实施和验证:培训学员学会如何实施和验证解决方案,确保问题得到有效解决。
7. 团队表彰和总结:培训学员学会如何进行团队表彰和总结,以激励团队成员,提高团队士气。
四、8D报告培训方法8D报告培训可以采用多种方法,如课堂讲授、案例分析、角色扮演、模拟演练等。
其中,模拟演练是一种非常有效的培训方法,它可以让学员在实际操作中学习和掌握8D报告的方法和技巧。
五、8D报告培训效果1. 提高问题解决效率:通过8D报告培训,企业和员工可以更加系统和高效地解决问题,提高问题解决效率。
2. 提升产品和服务的品质:通过8D报告培训,企业和员工可以更好地识别和解决产品和服务的质量问题,提升产品和服务的品质。
8D报告培训教材

抱怨是来自哪里的投诉,如来自市 场投诉,客户工厂等 Where the complaint arises from, such as: market, customer factory, etc.
产品分类,如:电池、电芯、机构件、 塑胶件等 Product Classification, such as battery, cell, housing, plastic, etc.
• D8:祝贺你的小组
• • • • • 目的:认识小组的集体努力 步骤: 1.向QOS委员会汇报; 1).编写案例分析报告 2).录象带,新闻发布,成果发表,向专门小组汇 报等方式来认可问题解决的意义和价值。 3).更新8D报告 2. 总评提问 是否对前7D中作出的贡献的每一个人表达赞赏? 是否可以写成报告在全公司分发? 是否获得了主办公司的评估?
• D2:描述问题
• • • • • • • • • • • 目的:准确的描述问题有助于找到问题的根本原因 步骤: 1.完成操作确定工作表 用5W2H叙述问题 1). WHO 谁在抱怨? 2). WHAT 什么发生了? 3). WHERE 在何处发生? 4). WHEN 何时发生? 5). HOW 如何发生? 6). WHY 为什么说它是个问题? 7). HOW MUCH 问题有多大?
Huizhou Hong Da Metals Produce Co.,LTD
编号Report NO.: 客户投诉信息描述 D e s c r i p t i o n o f C u s t o m e r c o m p l a i n t 客户名称 问题类型 失效模式 Customer Name Problem Type Failure Mode
四. 具体步骤阐述
8D报告培训资料(PPT 50张)

5.异常记录
四. 8D步骤—D4原因分析
5-Why 分析
当一个原因被发现时,不停地问为什么、为什么、为什么、 为什么、为什么,一直到无法拆解下去 。
TOYOTA
5-Why?
1W
2W
3W
4W
5W
WHY 问题
WHY 中间原因
WHY 中间原因
WHY 中间原因
WHY 根本原因
四. 8D步骤—D4原因分析
经确认后,没有不良品再流出的可能,不会再扩大损 失。
五.8D改善案例 D4. 原因分析
识别可能原因(因果图) 选择最有可能的原因(柏拉图) 确定是否是根本原因 识别可能方案
五.8D改善案例 4.1 因果分析
环
库房湿度大
法
速度设定多快 包装方式不合理
产品堆放高度过高
端 面 受 伤 PE强度不稳定
五.8D改善案例
D0.了解问题
2012年11月4日客户“星光宝光电设备有限公司”投诉, 在其半导体封装车间对“ALT-5检测器”进行包装时,使用 公司的CT3100机用膜时一拉就断裂 , 并发现使用的机用 膜端口破裂。造成ALT-5检测器包装工作进度延误,顾客 要求派人处理。
五.8D改善案例 D1.成立小组
识别可能的解决方案。
修改搬运、贮存作业方法,将原来搬运 和堆放高度3层改为 2层,减少重力。 改变包装方法,每卷产品用托盘运装。 包装箱内部增加泡沫,以减少碰撞冲力。 ……。
临时措施
消除问题及后果
只能治标 (可能再发)
长期措施
消除问题原因
可以治本 (不会再发)
四. 8D步骤—D4原因分析
2024年8D报告培训教材教程

8D报告培训教材教程1.引言8D报告是一种广泛应用于质量管理和问题解决的方法,其名称来源于8个解决问题的步骤(Disciplines)。
本教材旨在为您提供关于8D报告的全面培训,帮助您掌握8D报告的编写和应用技巧。
2.8D报告的背景和目的8D报告起源于汽车行业,并逐渐被其他行业所采用。
其主要目的是系统地解决问题,防止问题再次发生,并提高产品和服务的质量。
8D报告通常用于处理客户投诉和内部问题,以及推动持续改进。
3.8D报告的8个步骤3.1步骤1:建立团队在开始编写8D报告之前,需要建立一个跨部门的团队,团队成员应具备相关领域的专业知识和经验。
团队应由一名负责人领导,负责协调和推动整个解决问题的过程。
3.2步骤2:问题描述问题描述是8D报告的核心部分,需要清晰地描述问题的现象、影响和发生的时间。
问题描述应尽量具体、准确,并使用数据和事实来支持。
3.3步骤3:临时措施在找到根本原因之前,需要采取一些临时措施来减轻问题的影响。
这些措施应尽快实施,并在报告中详细说明。
3.4步骤4:根本原因分析根本原因分析是解决问题的关键步骤,需要运用各种工具和技术来找到问题的根本原因。
常用的工具包括鱼骨图、5个为什么等。
3.5步骤5:制定行动计划根据根本原因分析的结果,制定详细的行动计划来解决问题。
行动计划应包括具体的行动步骤、责任人和完成时间。
3.6步骤6:实施行动计划按照行动计划,组织资源并实施解决方案。
在实施过程中,需要监控进度,并及时调整计划以确保问题得到有效解决。
3.7步骤7:效果验证在实施解决方案后,需要对效果进行验证,以确保问题得到根本解决。
验证可以通过数据分析、客户反馈等方式进行。
3.8步骤8:预防措施和持续改进为了防止问题再次发生,需要制定预防措施,并对整个问题解决过程进行总结和反思,提出改进建议。
4.8D报告的编写技巧4.1结构清晰8D报告应遵循一定的结构,包括引言、问题描述、临时措施、根本原因分析、行动计划、实施结果、效果验证、预防措施和持续改进等部分。
8D报告培训(经典)
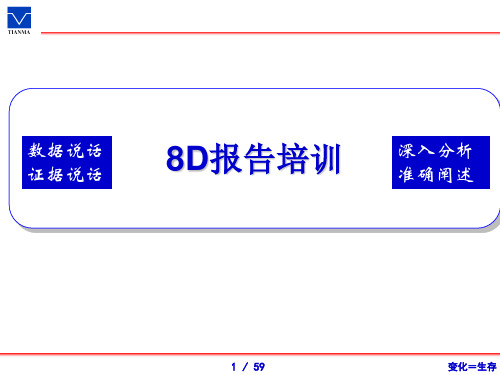
10 / 59
变化=生存
2D 问题描述
顾客 时间 地点 事件 影响
尽量落到客户满意度和
财务上的影响
11 / 59
图片需要加 上缺陷说明
图片
变化=生存
2D 问题描述
工具箱
走势图 描述一直以来存在的问题,比如某 种缺陷的不良率 适用: 一段时间内不断发生的问题
GAT CD loss range
1.00 0.75 0.50 0.25 0.00
19 / 59
变化=生存
4D 原因分析及验证-疑点排查确认(简明测试)
对前面列出所有疑点进行排查, 排除疑点或确认疑点。
对5M1E 进行排查
➢人--人员相关信息是否有变更 ➢机--设备维修保养记录, ➢料--物料更改记录(主料、辅料) ➢环--温湿度记录 ➢法--工艺更改记录,生产原始记录, ➢测--检测条件方法人员
Count Percent
彩色产品电测废品排列图
350000
100
博拉图 描述某项不良的严重程度,也可 300000
80
以用于描述课题研究的不良的分类各占多 250000
少。
200000
重点解
60
150000
决项目
40
适用: 找关键问题 或 问题的关键
100000
20
50000
Y
0
0
Defect
此页可删除 白 斑
5D-制定改善对策 及初步验证
2D-定义问题
6D-执行改善措施 及效果验证
3D-制定临时措施
7D-预防再发生 (标准化)
4D- 原因分析 及验证
4 / 59
8D-团队祝贺 (财务结余)
8D报告编写培训资料

的DZ47-32外壳均合格。
9
D1
D2
不合格描述 成立解决小组
目的 成立解决问题所需的小组并进行小组分工
➢ 选定小组成员:
1.人数限制在4-10人 2.选取合适人员 3.根据需要变更小组成员
a.与该问题有关的人员 b.具备工艺/产品知识的人员 c.能解决问题和实施措施能力的人员 d.有相应时间参与工作的人员
生产批次管理
批次管理作用: 是有效制订紧急处置措施的前提
批次管理原则: 遵循5M1E原则,重点关注人、机、料; 重点监控工序流转、批次信息衔接
批次管理要求: 批次信息贯穿生产全过程,批次管理 需要全员参与
批次管理验证: 追溯管理,采用逆向思维
12
D1
D2
D3
不合格描述 成立解决小组 紧急处置措施
D4 根本原因分析
19
本课程的内容
一 8D基础知识 二 8D报告编写 三 8D报告现存问题
20
8D报告现存问题
➢未按时间要求提交报告 ➢小组成员资格未满足解决问题的需求 ➢根本原因没有彻底分析清楚 ➢措施没有针对根本原因制定 ➢措施制订不具体、不可量化、难执行 ➢措施不执行或部分执行 ➢未能提供合适的证据
21
8D报告评价
3 按标准化管理要求,相关措施在日常生产中给予落实执行
和推广
18
D1
D2
D3
不合格描述 成立解决小组 紧急处置措施
D4 根本原因分析
D5 长期改善措施
D6 效果验证
D7 措施标准化
D8 复发的原因
目的 8D报告最后一个阶段,确认不合格是否复发
不合格复发原因分析:
1. D3紧急处置措施,措施制订不完整或措施执行未彻底 2. D4根本原因分析不彻底或是错误 3. 改善措施在日常生产中未按要求执行
8D报告培训教材PPT精选全文

8D步骤—D3暂时计策
纠正措施(计策)
为排除已发觉的不合格或其它不期望情形的原因所采取的 措施。
预防措施(预防再发计 策)
为排除埋伏不合格或其它埋伏不期望情形的原因所采取 的措施。
什么是问题???
问题
期望 目标
现实
8D步骤—D2问题描写
问题描写方法:5W/2H
WHO
5W2H 谁
WHAT
什么
WHEN WHERE WHY HOW
何时 何地 为何 怎么样
HOW MUCH 什么程度
说明 辨认那一个客户(内/外部)在抱怨 问题的症状,没法用文字描写清楚的,借助于数 字或图片将问题表达清楚 记入问题产生的日期 记入问题产生的场所 辨认已知的说明 在什么的模式或状态这问题会产生
火花塞湿润沾水(WHY4)
状态5-原因4
引擎盖密封差漏水(WHY5)
状态6-原因5
密封圈老化
8D步骤—D4原因分析
5-WHY分析案例2
状态1 状态2-原因1
生产线现场油污操作员行走滑倒 机器漏油
WHY1 WHY2
状态3-原因2
机器橡胶密封不好
WHY3
状态4-原因3
密封橡胶圈质量差 WHY4
状态5-原因4 状态6-原因5
8D改进案例
D0.了解问题
20XX年12月16日客户“浙江**机械厂”投诉,在其包装车间对“ALT-5 检测器”进行包装时,使用公司的MHT机用膜时一拉就断裂, 并发觉使用 的机用膜端口破裂。造成ALT-5检测器包装工作进度延误,顾客要求派人 处理。
8D报告培训资料

二.8D的步骤
2.8 D7-预防再发生 需要用8D解决的问题,往往是由于系统或者过程失误造成的 水平展开,以防同一问题及类似问题再发生
Quality Inspection WI Control plan SOP
Engineer Drawing Flow chart PFMEA WI Form
Others DFMEA Lessons learn BOM standards
8D报告
概述 8D的步骤
一.概述
1.1 起源 8D最先是由福特汽车汽车提出 后续在汽车行业全供应链以及各种
制造业进行推广使用
CAPA
一.概述
1.2 为什么使用8D?
有效地解决问题 8D能够给人以信心
一.概述
1.3 几个概念 PDCA: Plan,Do,Check,Action 遏制措施:防止不合格继续发生采取的措施 纠正:为消除已发生的不合格采取的措施 纠正措施:为消除已发生的不合格或其他不期望情况的原因采
状态进行,并且不会导致新的失效模式
二.8D的步骤
2.2 D1-成立8D团队
二.8D的步骤
2.2 D1-成立8D团队
二.8D的步骤
2.3 D2-问题描述 把问题陈述清楚 帮助团队关注问题本身,避免主观的假设判断问题,或者
对问题作出毫无现实根据的判断 解决问题之前,知道可能多的关于该问题的信息
的产生 根本原因——发生问题的根源,一个经验证的原因
二.8D的步骤
2.5 D4-根本原因 回顾问题描述,推测所有可能的原因 变化点,5M1E 常用的工具:流程图、鱼骨图,检查表,3L5Why, 头脑风暴、DOE,散点图等等
二.8D的步骤
2.6 D5-定义永久措施
8D培训资料

总结
无论是产发段发现的问题,或是量产、客诉问题 ,若组织每年有近百项的工程问题依照8D的方式 来解决,对工程人员实力的培养着实可观,成为 公司重要的资产,这也是很多公司/组织将8D制 式化的原因。
四、8D提交的时间
一般要求:
1.发现问题的24H内,提交包含所 采取的临时对策的8D报告;
2.发现问题的72H内提交包含问题发生原 因初步分析的报告。
特殊要求:
根据顾客要求确定。
五、8D方法的常用工具
工具
应用时机
应用场合
头脑风暴
D4,D5
推移图
D0,D2,D8
1.成本削减,财务贡献;2.品质目标达 成情况;3.不良率达到控制
二、8D的好处
使用8D有以下好处: 1.能确定问题的根本原因和纠正问题; 2.通过建立小组训练内部合作技巧; 3.推进有效的问题解决和预防技术; 4.改进整个质量和生产效率; 5.防止相同或者类似问题的再发生; 6.提高顾客的满意度; 7.增强对供应商的产品和过程的信心。
三、8D方法的应用时机
1.顾客投诉问题时; 2.重大不合格的产品问题时; 3.严重和反复重发的问题; 4.对那些需要长期纠正措施解决的缺陷; 5.采取行动时; 6.需要团队共同作业的问题。
D1-第一步骤: 建立解决问题团队
成员包括: • 最高指导员(Champion)
一般为主管阶层,对小组的进度有监督,支持 及决策决定权力 • 指导员(Leader) 负责协调,活动进行的引导,汇整小组的意见 及决策并呈报,指导员需以其专业素养引导成 员循8D格式找寻问题及解决方案 • 一般成员(Members) 各部门相关人员,对被指定的工作有义务提出 相关的结果及提供意见, (例:PE,PTE,WS, AE,QA……等相关人员) 小组人员以4~10人为佳 常见错误:1.完成8D过程的小组成员没有专业知 识;2.只有一两个人实施该过程。
8D报告培训

8D报告培训一、引言8D报告是一种用于问题解决和持续改进的工具,广泛应用于企业、组织和个人。
8D报告培训旨在帮助学员掌握8D报告的基本原理和应用技巧,提高问题解决和持续改进的能力。
本文将介绍8D报告培训的内容、方法和步骤,帮助学员更好地了解和运用8D报告。
二、8D报告概述1. 8D报告的定义8D报告是一种结构化的、系统的问题解决和持续改进方法,它包含8个步骤,用于识别、分析和解决根本问题,防止问题再次发生,并持续改进过程。
2. 8D报告的起源8D报告起源于美国汽车行业,最初用于解决质量问题。
随着企业对持续改进的需求不断增加,8D报告逐渐被广泛应用于各个领域,成为一种通用的问题解决和持续改进工具。
3. 8D报告的优点(1)结构化:8D报告提供了一种清晰的问题解决框架,使问题解决过程更加系统化和规范化。
(2)团队合作:8D报告强调团队合作,通过多学科、多部门合作,提高问题解决的效率和质量。
(3)持续改进:8D报告不仅关注问题的解决,还关注问题根本原因的分析和预防,从而实现持续改进。
(4)可操作性:8D报告具有明确的步骤和工具,易于操作和实施。
三、8D报告培训内容1. 8D报告的基本原理(1)问题解决:8D报告以问题解决为核心,通过分析问题的现象、原因和解决方案,实现问题的根本解决。
(2)持续改进:8D报告强调持续改进,通过不断分析问题、改进过程,提高组织绩效。
(3)团队合作:8D报告鼓励团队成员积极参与,共同解决问题,提高团队效能。
2. 8D报告的步骤和工具(1)D0:准备和团队建设(2)D1:问题描述(3)D2:临时措施(4)D3:根本原因分析(5)D4:制定和实施行动计划(6)D5:行动计划的效果验证(7)D6:预防措施(8)D7:总结和认可3. 8D报告的应用技巧(1)如何进行有效的问题描述(2)如何进行根本原因分析(3)如何制定和实施有效的行动计划(4)如何进行行动计划的效果验证(5)如何制定和实施预防措施四、8D报告培训方法1. 理论讲解:通过讲解8D报告的基本原理、步骤和工具,帮助学员建立对8D报告的全面认识。
8D报告培训教材(ppt 41页)
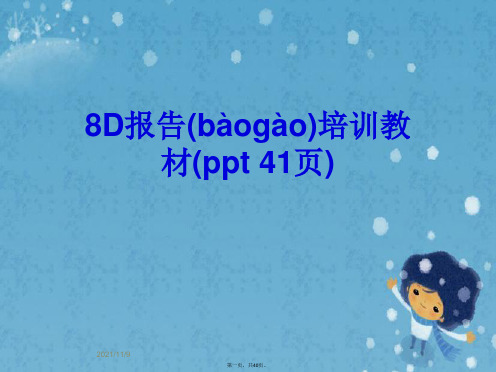
第十八页,共401页8。
D4:基本缘由(yuányóu)剖 析-魚骨圖
要因:召扫尾脑风暴研讨会,在最后的草案阶段,
基本缘由
D4:基本(jīběn)缘由剖析■5WHY不是(bù 5WHY
五s个hi)5为次什么 问五次为什么 原那么:找到基本(jīběn)缘由
5
24
第二十四页,共40页。
D4:基本(jīběn)缘由剖析5WHY
■〝5WHY〞案例(àn lì)1
效果:〝明天(míngtiān)下班迟到了10分钟 〞
比拟(bǐnǐ)严重的制程质量效果
影響水平嚴重和需改善的項目 客户(kèhù)要求回复的质量赞扬
何时采
用8D
5
第五页,共40页。
1
什么是8D?为什么要推行(tuīxíng)8D?何时采用8D?
2 8D步骤(bùzhòu)
3
8D改善案例分享(fēn xiǎnɡ)及8D報告填寫要求
6
第六页,共40页。
●此小组应指定一位团队指导人员(组长),组长应做到日常分配,全体协调,资源 应用等…
●各团员的职责(zhízé) 权限 角色 分工 目的 人际关系
树立(shùlì)小组需求思索的要素:
小组的指导: 谁来推进
小组的资源: 谁提供支持?
小组的成员: 协作及分工? 人员的数量: 多少为宜?(4-10人)
10
●目的: 以量化的方式來評估問題點及對 客戶端所形成的影響,並藉此計算出一個短期 (duǎn qī)對策來降低影響的水平。
•注意要項:
- 1、下载文档前请自行甄别文档内容的完整性,平台不提供额外的编辑、内容补充、找答案等附加服务。
- 2、"仅部分预览"的文档,不可在线预览部分如存在完整性等问题,可反馈申请退款(可完整预览的文档不适用该条件!)。
- 3、如文档侵犯您的权益,请联系客服反馈,我们会尽快为您处理(人工客服工作时间:9:00-18:30)。
5/30/2002 Rev. Orig 8D Training 12
D3 Containment Example D3 围堵措施案例
• Poor Containment 差劲的围堵措施 – “Operator was alerted of the failure.” –让操作工提防/注意此不良 • Good Containment 完美的围堵措施 – “Production and warehouse material was inspected on 4/1/02 by J. Smith (quality assurance personnel) and there were 0 lots out of 320 containing mixed devices.” – J. Smith(质量保证人员)于4/1/02检查了生产线及仓库 材料
5/30/2002 Rev. Orig 8D Training
5
8 Disciplines to Problem Solving 解决问题的8 解决问题的8个准则
• • • • • • • • D1 Establish a Team 组建问题解决小组 D2 Describe the Problem 描述问题 D3 Contain the problem 采取围堵措施(即短期对策) D4 Identify the root causes 识别/确认根本原因(真因) D5 Corrective Actions 确认纠正措施 D6 Implement Corrective Actions 实施纠正措施(即长期对策) D7 Prevent Recurrence 防止再发 D8 Congratulate the Team 小组庆祝
5/30/2002 Rev. Orig
8D Training
8
D2 Describe the Problem Elements D2 描述问题要素
• What is the Problem? Describe the failure mode. 问题是什么? 描述失效模式 • Where was it detected? 问题是在哪里被发现? • When was it detected? 问题是什么时候被发现? • What lots/date codes are affected? 被影响的批次/日期码是那些? • How many pieces are affected? 被影响的数量是多少? • Is the Customer information included? 是否包含客户信息?
5/30/2002 Rev. Orig 8D Training 7
D2 Describe the Problem D2 描述问题
• Clearly Identify and Define the Problem. 明确识别和定义问题 • In many cases Problems are ambiguous or imprecise. 在许多案例中,问题是模棱两可或不明确的 • Clarity ensures that everyone is trying to solve the same Problem. 明确问题可确保任何人将尽力去解决问题
5/30/2002 Rev. Orig 8D Training
2
CUSTOMER 8D EXPECTATION 客户应用8D的期望
• • • • • • • • Immediate Containment. 采取迅速的围堵措施(短期对策) Clear identification of Root Cause. 真正识别问题产生的根本原因(真因) Robust Corrective Actions. 充分的纠正措施 Verified Corrective Actions. 验证纠正措施 System fixes. 系统化(即纠正措施标准化或文件化) 100% On-time response. 100%准时反应(即及时解决问题,准时回复客户) Eliminate the problems the first time. 做到第一次就消除问题所在 Prevention of future problems. 实现潜在问题的预防
8D Training 3
5/30/2002 Rev. Orig
CAR/8D Report Problems 完成CAR/8D报告存在的问题 完成CAR/8D报告存在的问题
• Not identifying the true processes, escape, and system root causes. 没有识别出过程、流出(逃脱)及系统的根本原因(真因) • Not implementing system corrective actions. 没有实施系统性纠正措施 • Not properly containing entire pipeline of product. 没有针对产品的所有流程采取正确的围堵措施 • Unclear or ambiguous wording. 对问题采取的不明确或模棱两可的描述 • Not meeting customer expectations regarding content and cycle time.
5/30/2002 Rev. Orig
8D Training
6
D1 Establish Team D1 组建问题解决小组
• Establish Cross Functional Team. 建立跨功能小组 • Identify a Champion. 确定小组长 • Members should be from all affected areas, not just quality! i.e. Sales, Logistics, Marketing, Engineering, Line Operators, Production Mgmt., etc… 小组成员应来自于所有被涉及区域,并非只是质量部 !如销售、物流、市场、工程、生产线操作工、生产 管理等等······ • The Team should ask themselves do they have the correct skill mix to solve the problem? 小组应询问自己是否具有解决问题所必需的能力?
Vishay Customer Corrective Action Request (CAR) Guidelines Vishay《客户纠正措施要求CAR》 Vishay《客户纠正措施要求CAR》应用指南
5/30/2002 Rev. Orig
8D Training
1
What is a CAR/ 8D? 何谓CAR/8D 何谓CAR/8D ?
不符合客户关于内容及回复时间的要求
5/30/2002 Rev. Orig
8D Training
4
CAR/8D Requirements CAR/8D的要求 CAR/8D的要求
• All corrective action requests must be completed using an 8D report (unless a different method is required by Customer). 所有的《纠正措施要求》必须采用8D报告形式(除非 客户要求采用不同的方法 • Must use Corporate format. 必须采用Vishay公司的格式 • Must use 8D checklist as a guideline in completing the 8D’s. 在完成报告的过程中必须采用8D检查表进行检查
5/30/2002 Rev. Orig 8D 11
D3 Containment Elements D3 围堵措施要素
• Has an effective containment method been identified and documented? 是否有有效的围堵方法已经被确定和文件化? • Have dates (or date codes) for temporary containment actions been identified? 是否已经确定了临时围堵措施实施的日期(日期码)? • Have actions been verified with before and after data? 是否已经验证了围堵措施实施前后的效果? • Has the entire pipeline been contained (production, warehouse, distributors)? 是否对产品的所有流程采取了围堵措施(如生产线、仓库及发 货员)? • Has detailed instructions on containment been issued to people responsible for containment? 是否给负责实施围堵措施的人员发放了详细的围堵作业指导书?
5/30/2002 Rev. Orig 8D Training 9
D2 Describe the Problem Examples D2 描述问题案例
• Poor Problem Description 差劲的问题描述 – “Customer received wrong part.” – 客户接收到错误零件 • Good Problem Description 完美的问题描述 – “Customer received incorrect value CRCW-0603 resistors on 4/1/02. Customer P.O. 441960 (Vishay P.O. X765644-30) specified CRCW-0603, 8.2K ohm and received CRCW-0603, 82K ohm parts.” – 客户在4/1/02接收到阻值错误的CRCW-63电阻。客户 订单号码441960( Vishay订单号码X765644-30)指 定的CRCW-63电阻的阻值为8.2欧姆,而收到的 CRCW-63电阻的阻值为82欧姆。