压接工艺设计
VPX连接器压接工艺技术探讨
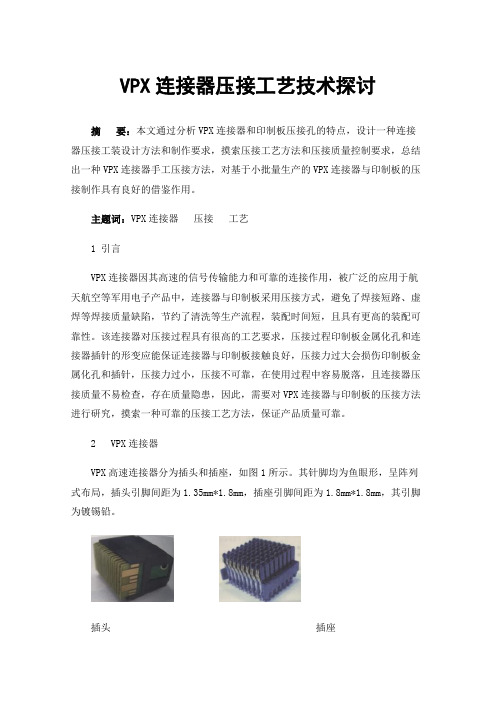
VPX连接器压接工艺技术探讨摘要:本文通过分析VPX连接器和印制板压接孔的特点,设计一种连接器压接工装设计方法和制作要求,摸索压接工艺方法和压接质量控制要求,总结出一种VPX连接器手工压接方法,对基于小批量生产的VPX连接器与印制板的压接制作具有良好的借鉴作用。
主题词:VPX连接器压接工艺1 引言VPX连接器因其高速的信号传输能力和可靠的连接作用,被广泛的应用于航天航空等军用电子产品中,连接器与印制板采用压接方式,避免了焊接短路、虚焊等焊接质量缺陷,节约了清洗等生产流程,装配时间短,且具有更高的装配可靠性。
该连接器对压接过程具有很高的工艺要求,压接过程印制板金属化孔和连接器插针的形变应能保证连接器与印制板接触良好,压接力过大会损伤印制板金属化孔和插针,压接力过小,压接不可靠,在使用过程中容易脱落,且连接器压接质量不易检查,存在质量隐患,因此,需要对VPX连接器与印制板的压接方法进行研究,摸索一种可靠的压接工艺方法,保证产品质量可靠。
2 VPX连接器VPX高速连接器分为插头和插座,如图1所示。
其针脚均为鱼眼形,呈阵列式布局,插头引脚间距为1.35mm*1.8mm,插座引脚间距为1.8mm*1.8mm,其引脚为镀锡铅。
插头插座图1 VPX连接器3 印制板焊盘的设计要求用于VPX连接器压接的印制板焊盘设计应满足以下要求:a)印制板焊盘应采用与连接器相同的电镀通孔设计要求,镀层为铜底镀层上覆盖锡层或锡铅层,PCB板材选用FR4;b)印制板厚度至少为1.6mm,印制板的拱形在0.03mm以内;c)用于插头压接的印制板金属化孔镀后孔径为0.56mm,焊盘直径为1.02mm;d)用于插座的印制板金属化孔镀后孔径为0.46mm,焊盘直径为0.92mm。
4 工装的设计与制作根据两种连接器(插头和插座)及印制板布局的特点,制作了一套专用压接工装,如图2所示。
选择手工压接机。
压接工装分为两个部分,底座和上模,工装底座如图2左图所示,压接工装上模如图2右所示。
压接工艺规范

****有限公司工作指令文件修改记录表保存期限:新版发行后1个月第 1 页, 共 10 页 第 A 版第 0 次修改一、 范围本规范规定了连接器压接的基本工艺要求。
本规范适用于所有压接型连接器的压接。
二、 规范性引用文件下列文件中的条款通过本规范的引用而成为本规范的条款。
凡是注日期的引用文件,其随后所有的修改单(不包括勘误的内容)或修订版均不适用于本规范,然而,鼓励根据本规范达成协议的各方研究是否可使用这些文件的最新版本。
凡是不注日期的引用文件,其最新版本适用于本规范。
三、 术语和定义压接:压接是由弹性可变形插针或刚性插针与PCB 金属化孔配合而形成的一种连接。
在插针与金属化孔之间形成紧密的接触点,靠机械连接实现电气互连。
为了形成紧密的配合,针脚的横截面尺寸必须大于PCB 金属化孔孔径,在压接过程中,针脚横截面或金属化孔要产生变形。
刚性插针:在压接过程中不产生变形,而孔会变形。
因对孔径的公差要求严格,已经淘汰。
柔性插针:在压接过程中会受挤压而变形,而孔不变形。
压接垫板:fixture ,压接时用于支撑PCB ,防止连接器插针和PCB 损伤的工艺装置。
压接模具:tooling ,压接时适应不同连接器的需要而设计的,置于连接器的上面将连接器压接到PCB 的金制 作:洪 登 月 审 核: 生效日期 :2006.05.20 批 准: 批准日期:未 经 同 意 不 得 复 印***** 有 限 公 司 工 作 指 令 文 件 题 目:压接工艺规范***** 有限公司工作指令文件第 4 页,共10 页5.2 垫板和PCB厚度的处理能力IMPRESS 500E 垫板的厚度+PCB的厚度≤35mmTOX 垫板的厚度+PCB的厚度≤40mmHT604 垫板的厚度+PCB的厚度≤40mmHKP16 垫板的厚度+PCB的厚度≤50mm5.3 相关工艺参数压接模式:定行程(fixed stroke)、定压力(fixed force)、压力增量(delta force)压接行程:35~160mm压接力:根据不同的连接器进行设定压接速度:和压接模式对应,设备无此显示和调节功能六、品质水平压接后连接器和PCB的间隙在0~0.2mm,连接器无移位、扭曲、弯针、塑壳损坏、不出针等不良现象,PCB 无任何损坏,具体参见《PCBA验收标准》中第三部分“压接件”七、初始参数7.1 压接行程采用任何设备压接连接器,必须首先根据连接器、PCB、压接垫板、压接模具的尺寸调节好或设定好设备的行程,以保证压接时连接器不会过压。
完整版)薄壁不锈钢管卡压式连接施工工艺

完整版)薄壁不锈钢管卡压式连接施工工艺直径32~50mm时应为50mm,工程直径65mm及以上时应为60mm。
4.管道连接1)薄壁不锈钢管卡压式连接的连接方式有三种:单卡压式、双卡压式、三卡压式。
2)连接前应确保管子插入管件的深度符合要求,卡压工具的选择应根据管子直径和卡压式连接的类型选择相应的卡压工具。
3)连接完成后,应进行水压试验,试验压力应符合设计要求,无渗漏现象。
5.管道保温1)管道保温应按设计要求进行,保温材料应符合国家现行标准。
2)保温材料的厚度应根据设计要求确定,保温层应均匀、紧密、无空鼓、无裂缝。
3)保温层表面应光滑、平整、无砂眼、无毛刺、无划痕。
4)保温层应与管道连接紧密,不得有松动现象。
6.管道试压1)管道敷设、连接完成后,应进行水压试验,试验压力应符合设计要求。
2)试验时应按设计要求逐级增加试验压力,试验时间应不少于30分钟。
3)试验中应注意观察管道和连接处是否有渗漏现象,如发现渗漏应及时处理。
7.管道冲洗消毒1)管道试压合格后,应进行冲洗消毒,确保管道卫生达标。
2)冲洗消毒应按XXX颁布的《建筑给水排水及采暖工程施工及验收规范》GB )的要求进行。
3)冲洗消毒完成后,应进行水质检测,水质应符合国家有关标准。
薄壁不锈钢管卡压式连接施工工艺可以降低管道施工成本,因为这种工艺不需要复杂的套丝机和电焊机等机具,也不需要切削液和焊剂等添加物。
相比传统的焊接和丝扣连接,薄壁不锈钢管卡压式连接施工工艺更加简单易行,无需高超的操作技巧和大量的人工,因此可以大幅度减少工艺成本。
在进行薄壁不锈钢管卡压式连接施工工艺之前,需要进行施工准备。
这包括施工设计图纸和技术文件的齐全和会审,施工方案或组织设计的技术交底,以及材料、施工人员和施工机具等的准备。
此外,还需要了解建筑物的结构,以制定与土建工程和其他工程的配合措施。
管道敷设、连接和保温都是薄壁不锈钢管卡压式连接施工工艺的重要环节。
在敷设管道时,需要注意管道明敷的时机和固定支架的间距。
压接工艺设计范文
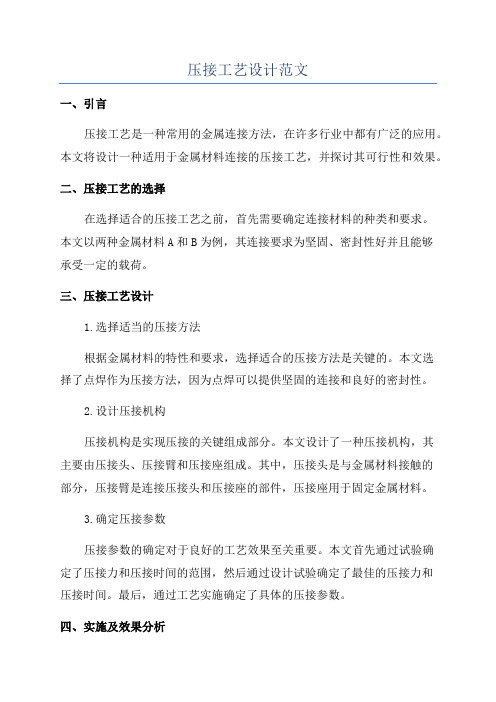
压接工艺设计范文一、引言压接工艺是一种常用的金属连接方法,在许多行业中都有广泛的应用。
本文将设计一种适用于金属材料连接的压接工艺,并探讨其可行性和效果。
二、压接工艺的选择在选择适合的压接工艺之前,首先需要确定连接材料的种类和要求。
本文以两种金属材料A和B为例,其连接要求为坚固、密封性好并且能够承受一定的载荷。
三、压接工艺设计1.选择适当的压接方法根据金属材料的特性和要求,选择适合的压接方法是关键的。
本文选择了点焊作为压接方法,因为点焊可以提供坚固的连接和良好的密封性。
2.设计压接机构压接机构是实现压接的关键组成部分。
本文设计了一种压接机构,其主要由压接头、压接臂和压接座组成。
其中,压接头是与金属材料接触的部分,压接臂是连接压接头和压接座的部件,压接座用于固定金属材料。
3.确定压接参数压接参数的确定对于良好的工艺效果至关重要。
本文首先通过试验确定了压接力和压接时间的范围,然后通过设计试验确定了最佳的压接力和压接时间。
最后,通过工艺实施确定了具体的压接参数。
四、实施及效果分析1.实施过程本文按照设计的压接工艺进行了实施。
首先,将金属材料A和B放置在压接座上;然后,调整压接机构,使得压接头与金属材料接触;最后,施加压接力并保持一定的时间。
完成压接后,进行了检测和评估。
2.效果分析通过对压接接头进行断裂强度测试,验证了压接工艺的可行性和连接强度。
测试结果表明,压接接头的断裂强度远高于要求的工作载荷,证明了压接工艺的有效性。
此外,通过观察压接接头的断面形貌,验证了压接工艺的密封性。
五、总结本文设计了一种适用于金属材料连接的压接工艺,并对其进行了实施和效果分析。
结果表明,所设计的压接工艺具有良好的可行性和效果。
尽管本文以金属材料A和B为例进行了设计,但该压接工艺可以应用于其他金属材料的连接,具有一定的普适性。
8.1导线接续管钢管穿管及压接工艺

8.1导线接续管钢管穿管及压接工艺导线接续是电力工程中常见的操作工艺之一。
而在导线接续中,钢管穿管与压接也是其中重要的步骤。
本文将详细介绍8月1日的导线接续管钢管穿管及压接工艺。
导线接续是电力工程中不可或缺的步骤,它主要包括导线与导线之间的接头连接、导线与设备之间的连接等。
而在导线接续过程中,钢管穿管及压接是关键的工艺,它们不仅能保证电流的传输质量,还能提高系统的稳定性和安全性。
一、钢管穿管1. 确定穿管位置:根据工程设计图纸,确定钢管穿管的位置。
一般情况下,钢管穿入设备顶部或侧面的孔洞中,且穿入的位置应尽量靠近接线盒或设备连接点。
2. 检查钢管尺寸:根据设计要求,选择合适尺寸的钢管。
钢管应具备足够的强度和耐腐蚀性能,并且长度要与工程要求相符。
3. 清理孔洞:在确定的穿管位置,清理孔洞,确保孔口光滑。
如果孔洞较大,可使用填缝材料填充,以增加孔洞的封闭性。
4. 定位钢管:将选定的钢管对准孔洞,确保钢管与孔洞垂直。
5. 固定钢管:使用合适的固定夹具将钢管固定在孔洞附近,以确保钢管的稳定性和安全性。
固定夹具应具备足够的强度和可靠性,避免因负载过大而松动或脱落。
二、压接工艺1. 准备工作:在进行压接之前,需要准备好所需的工具和材料,包括导线、压接工具、导线端子等。
2. 导线剥皮:根据不同的导线规格,使用合适的工具剥去导线两端的绝缘层,露出足够长度的导线。
3. 导线端子选择:根据导线规格和接头类型,选择合适的导线端子。
导线端子应与导线规格相匹配,并且具备可靠的电气连接和耐腐蚀性能。
4. 导线端子压接:将导线端子按照压接工具的要求,正确安装在导线末端。
在压接之前,应先清理导线末端的表面,确保导线与导线端子之间没有杂质和氧化层。
5. 压接操作:将导线端子与压接工具正确对位,并施加适当的压力,进行压接。
压接应均匀、稳定,确保导线端子与导线之间的电气连接良好。
6. 压接质量检查:压接完成后,应进行质量检查。
检查导线端子与导线之间的接触是否牢固,表面是否平整,无明显裂缝和变形。
压接工艺设计

目录1、概况 (1)2、导线、避雷线机械物理性能 (1)3、液压管参数 (1)4、液压压接前的准备工作 (3)5、画印、切割、穿管、施压顺序 (3)6、压模 (5)7、压接机具 (6)8、液压操作 (6)9、质量要求 (6)10、施工安全措施 (7)1. 概况xxx10kV输电线路,简称xx线。
全线导线使用型号为LGJ—300/40钢芯铝绞线;避雷线使用型号为GJ—50镀锌钢绞线。
线路设计导线耐张及直线连接、地线直线连接均采用液压连接,地线耐张选用NX—2线夹弯头绑扎.为了保证工程施工质量,特编写此工艺.本工艺编写依据为SDJ226—87《架空送电线路导线及避雷线液压施工工艺规程》.耐张管及直线接续管压前外形形状为圆形,压后外形形状呈六角形。
2。
导线、避雷线机械物理性能(见表一)表一导线、避雷线机械物理性能导线、避雷线型号导线避雷线LGJ—300/40 GJ-50股数/直径(mm)铝股48/2.85 / 钢芯7/2。
22 7/3.0截面积(mm2)铝部306.21 /钢芯27.10 49。
46 综合333。
31 49。
46计算直径(mm )23。
76 9.0 单位重量(kg/km) 1058 423.7 瞬时拉断力(N) 83410 58165 弹性系数(N/mm2)65000 181420 线膨胀系数(1/ 0C)20.5×10-611.5×10-6直流电阻(20℃)(Ω/km)0.09433 /3。
液压管参数3.1液压管外形(如图一、图二,图中尺寸均为实测值)3。
2 液压管尺寸(见表二)表二液压管尺寸表(单位:mm)3。
3液压管内外径测量和计算方法外径在管上均选三点检测,每点互成90°测量二个数据,以三个检测点共六个数据的平均值作为压前的外径;内径在管两端检测,每端互成90°测两个数据,以两端共四个数据的平均值作为压前内径(耐张管外径只检测二点,内径只检测管口一点)。
薄壁不锈钢管卡压式连接施工工艺

薄壁不锈钢管卡压式连接施工工艺直径32~50mm时应为50mm,工程直径大于50mm时应为60mm。
4.管道连接1)管道连接前应先将管道内外表面清洁干净,管道插入管件时应注意方向和深度。
2)薄壁不锈钢管卡压连接时,应先将管子插入管件内,再用专用的卡压工具卡压。
瞬间即可完成连接。
连接前应检查卡压工具是否正常、管子是否插入到位。
3)管道连接后,应进行试压,试压时间不少于30分钟,试压压力应达到设计压力的1.5倍,无渗漏为合格。
5.管道保温1)管道保温应在管道敷设、连接、试压后进行,保温材料应符合国家现行有关标准。
保温层厚度应符合设计要求。
2)保温材料应密实、平整,保温层表面应涂刷防腐漆。
3)管道保温后,应进行保温层厚度、密度、压缩率等检查,合格后方可进行下一步工作。
薄壁不锈钢管卡压式连接施工工艺一、工艺原理传统的不锈钢管连接工艺,无论是焊接还是丝扣连接,对管材壁厚有严格的要求,需要使用套丝机、电焊机等机具,添加切削液、焊剂等副材料,而且需要熟练的操作工才能完成。
这些复杂的操作需要消耗大量人工,工艺成本较高。
相比之下,采用薄壁钢管卡压连接施工工艺,只需要用专用的卡压工具卡压管子插入管件,即可瞬间完成连接作业。
不需要螺纹连接时复杂的套丝作业,也不需要焊接时前处理、后处理作业,管道施工综合成本大幅度减少。
二、工艺流程与操作要点1.工艺流程2.施工准备1)管道安装工程施工前,必须具备以下条件:施工设计图纸和其它技术文件齐全并经过审查、施工方案或施工组织设计已进行技术交底、材料、施工人员、施工机具等能保证正常施工、施工现场的用水、用电和材料贮放场地条件能满足需要、提供的管材和管件符合国家现行有关产品标准,其实物与资料一致,并附有产品说明书和质量合格证。
2)在了解建筑物的结构后,根据设计图纸和施工方案制定与土建工程及其它工程的配合措施。
安装人员应经过专业培训,熟悉薄壁不锈钢管和管件的性能,掌握操作要点。
3)管件和管材的外观和接头应及时清洗,清除污物和杂质。
不锈钢管卡压式连接施工工艺

不锈钢管卡压式连接施工工艺在完成干管安装和试压后,进行立管的安装和试压。
具体步骤如下:1)根据设计图纸规定的坐标和标高线,在干管上开出立管接口,并进行卡压连接。
2)立管长度应符合设计要求,且应保证立管垂直度不超过1/500,立管的支撑应符合规范要求。
3)进行立管试压,试压压力应为工作压力的1.5倍且不小于0.6MPa,试压时间应不少于30min,试压结束后应进行外观检查,以确保立管连接牢固、密封无漏。
5、支管安装1)根据设计要求,在干管上开出支管口,并进行卡压连接。
2)支管的长度应符合设计要求,支管的支撑应符合规范要求。
3)进行支管试压,试压压力应为工作压力的1.5倍且不小于0.6MPa,试压时间应不少于30min,试压结束后应进行外观检查,以确保支管连接牢固、密封无漏。
通过以上安装施工工艺,可以保证不锈钢管卡压连接的安装质量,确保管道系统的安全运行。
将预制好的立管段运至安装现场,并进行卡压连接。
明装立管时,公称管径≤25mm时距装饰墙面的距离为40mm,公称直径32~40mm时为50mm。
管道井的暗装立管应按施工图尺寸进行安装,穿越楼板处应加设塑料套管,穿过屋面时采用金属防水套管,套管高出地面和屋面50mm。
管道安装必须在墙壁粉饰完成后进行,以免污染管道。
立管安装完成后进行水压试验,试验压力及试验方法同干管试压。
将预制好的支管运至施工现场组装。
明装支管一般沿墙敷设,并设有2‰~3‰的坡度,坡向立管或配水点。
支管与墙壁之间可用塑料管卡固定,在给水栓或配水点处则应采用金属管卡或吊架固定。
管卡或吊架宜设置在距配件40~80mm处。
暗装的支管敷设在墙槽内,不锈钢管件应加设防护套管或外缠防腐胶带。
支管安装完成后进行水压试验,试验压力及试验方法同干管试压。
不锈钢管卡压式连接应注意以下几点。
管材下料截管后,必须清除管子内外的毛刺。
管子插入管件前,应确认管件O型密封圈已安装管件端部的U形槽内,严禁使用润滑油。
QGDW 571-2010 大截面导线压接工艺导则

II
Q / GDW 571 — 2010
大截面导线压接工艺导则
1
范围
1.1 本标准规定了架空送电线路用大截面导线的压接工艺。 1.2 本标准适用于架空送电线路所采用的四层铝股结构的圆线同心绞钢芯铝绞线。大跨越导线和其它 导线的压接可参照执行。 2 引用标准
下列文件对于本标准的应用是必不可少的。 凡是注日期的引用文件, 仅注日期的版本适用于本标准。 凡是不注日期的引用文件,其最新版本(包括所有的修改单)适用于本标准。 GB 50233 110~500kV 架空送电线路施工及验收规范 GB/T 2317.1 电力金具 机械试验方法 SDJ 226 架空送电线路导线及避雷线液压施工工艺规程(试行) 3 定义 下列定义适用于本标准: 3.1 大截面导线 由多根硬铝线和镀锌钢线组成,以多根镀锌钢线为芯,外部同心螺旋绞四层硬铝线,铝导体标称截 面不小于 800mm2。 顺压 第一段从直线接续管铝管的管口开始连续施压至压接定位印记;第二段从压接定位印记开始连续施 压至另一侧管口。 3.2 3.3 3.4 3.5 3.6 倒压 从耐张线夹铝管的拔梢端开始压接。 导线设计计算拉断力 导线的设计计算拉断力等同于设计使用拉断力,为导线额定拉断力(RTS)的 95%。 铝钢比 铝部分总截面积与镀锌钢绞线截面积之比乘以 100。
2
kP HB D
(2)
Q / GDW 571 — 2010 5.5 穿管 5.5.1 导线接续管的穿管过程如图 1、图 2、图 3 所示。 5.5.1.1 剥铝线如图 1 所示: a) 用钢尺测量接续管钢管的实长 L1 及接续管铝管的实长 L2; b) 用钢尺自导线端头 O 向线内量 L1+Δ L1+L2+60 并标定为 P 点,在 P 点用绑线扎牢(Δ L1 约为 L1 的 11%) ; c) 将接续管铝管套入,铝管穿入时顺铝线绞制方向,向内旋转推入直至露出铝线端头; d) 自导线端头 O 向线内量 L1+Δ L1+25mm 处标记为 N; e) 在 N 处向线内量 20mm 标记为 P1,在 P1 处用绑线扎牢; f) 在 N 处切断铝线,注意不要伤及钢芯。
铝合金型材压接开裂原因
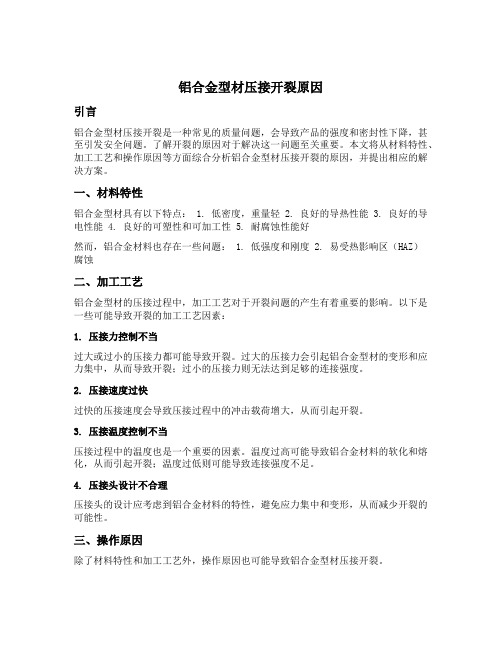
铝合金型材压接开裂原因引言铝合金型材压接开裂是一种常见的质量问题,会导致产品的强度和密封性下降,甚至引发安全问题。
了解开裂的原因对于解决这一问题至关重要。
本文将从材料特性、加工工艺和操作原因等方面综合分析铝合金型材压接开裂的原因,并提出相应的解决方案。
一、材料特性铝合金型材具有以下特点: 1. 低密度,重量轻 2. 良好的导热性能 3. 良好的导电性能 4. 良好的可塑性和可加工性 5. 耐腐蚀性能好然而,铝合金材料也存在一些问题: 1. 低强度和刚度 2. 易受热影响区(HAZ)腐蚀二、加工工艺铝合金型材的压接过程中,加工工艺对于开裂问题的产生有着重要的影响。
以下是一些可能导致开裂的加工工艺因素:1. 压接力控制不当过大或过小的压接力都可能导致开裂。
过大的压接力会引起铝合金型材的变形和应力集中,从而导致开裂;过小的压接力则无法达到足够的连接强度。
2. 压接速度过快过快的压接速度会导致压接过程中的冲击载荷增大,从而引起开裂。
3. 压接温度控制不当压接过程中的温度也是一个重要的因素。
温度过高可能导致铝合金材料的软化和熔化,从而引起开裂;温度过低则可能导致连接强度不足。
4. 压接头设计不合理压接头的设计应考虑到铝合金材料的特性,避免应力集中和变形,从而减少开裂的可能性。
三、操作原因除了材料特性和加工工艺外,操作原因也可能导致铝合金型材压接开裂。
1. 操作不规范操作人员在压接过程中的不规范操作,如过度施力、不均匀施力等,都可能导致开裂。
2. 设备故障设备的故障,如压力不稳定、温度控制失效等,也可能导致开裂。
3. 材料质量问题铝合金型材的质量问题,如含杂质、不均匀组织等,也会增加开裂的风险。
四、解决方案针对铝合金型材压接开裂问题,可以采取以下解决方案:1. 优化加工工艺合理控制压接力、速度和温度,避免过大或过小的冲击载荷和温度对铝合金材料的影响。
2. 设计合理的压接头优化压接头的设计,避免应力集中和变形,提高连接强度。
压装工艺知识点总结
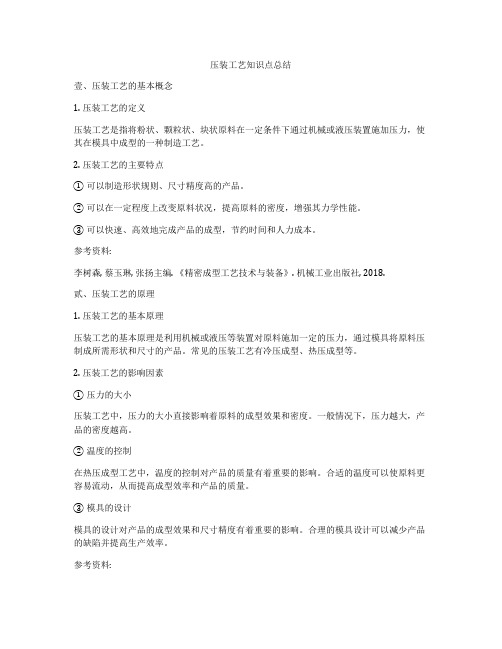
压装工艺知识点总结壹、压装工艺的基本概念1. 压装工艺的定义压装工艺是指将粉状、颗粒状、块状原料在一定条件下通过机械或液压装置施加压力,使其在模具中成型的一种制造工艺。
2. 压装工艺的主要特点① 可以制造形状规则、尺寸精度高的产品。
② 可以在一定程度上改变原料状况,提高原料的密度,增强其力学性能。
③ 可以快速、高效地完成产品的成型,节约时间和人力成本。
参考资料:李树森, 蔡玉琳, 张扬主编. 《精密成型工艺技术与装备》. 机械工业出版社, 2018.贰、压装工艺的原理1. 压装工艺的基本原理压装工艺的基本原理是利用机械或液压等装置对原料施加一定的压力,通过模具将原料压制成所需形状和尺寸的产品。
常见的压装工艺有冷压成型、热压成型等。
2. 压装工艺的影响因素① 压力的大小压装工艺中,压力的大小直接影响着原料的成型效果和密度。
一般情况下,压力越大,产品的密度越高。
② 温度的控制在热压成型工艺中,温度的控制对产品的质量有着重要的影响。
合适的温度可以使原料更容易流动,从而提高成型效率和产品的质量。
③ 模具的设计模具的设计对产品的成型效果和尺寸精度有着重要的影响。
合理的模具设计可以减少产品的缺陷并提高生产效率。
参考资料:秦刚, 程闵, 陈旭彬编著. 《金属塑性加工原理》. 机械工业出版社, 2016.叁、压装工艺的应用1. 压装工艺在粉末冶金中的应用粉末冶金是一种利用金属和非金属粉末作为原料,经过混合、压制、烧结等工艺生产制造金属零部件的工艺。
压装工艺在粉末冶金中起着至关重要的作用,可以生产出形状复杂、性能优异的零部件。
2. 压装工艺在制药行业的应用在制药行业中,药片、胶囊等产品的生产往往需要通过压装工艺完成。
通过对药品原料进行压制成型,可以提高药品的稳定性和服用方便性。
3. 压装工艺在食品行业的应用食品行业中,很多颗粒状的食品制品(如巧克力豆、糖果等)需要经过压装工艺进行成型。
通过压装工艺,可以将食品原料压制成各种形状的产品,并且保持其外观和口感。
press fit 设计-压接设计知识讲解

针对以上两点要求, (1)CompliantPin于插入PTH后必需与PTH有紧密之结合,两者间的接触阻抗必需够低
2
3
4
5. 端子拔出時,保持力迅速到达峰值,随即迅速减小. 6. 端子继续拔除,过渡区和插入区此时已完全形變,与PCB间的干涉力几乎为零.
Page:8
(三)鱼眼孔功能区的划分
依据插拔力曲線,将鱼眼结构划分为5个功能區,各功能区的位置,名稱,及功能如下 表所示.
Press-fit结构 功能区 区域功能说明入力曲线
插入力第二波峰
Force: kgf
0
预插
位移(mm)
开始干涉
插入力减小 压入到位
鱼眼孔端子插拔力曲线图
保持力曲线 拔出力最大值
Page:7
(二)鱼眼孔插拔过程分析
1. 端子预放入PCB. 端子尖端进入PCB孔,尚未产生变形. 2. 端子开始压入,鱼眼开始变形,压入过程出现第一波峰 3. 端子继续压入,鱼眼形變压合, 变形量减小,插入力略有减小. 4. 端子继续下压,鱼眼形變压合变形,压入力曲线出现第二波峰.
D>0.70mm D<0.70mm
(D-0.11) ±0.025 0.81-0.86
(D-0.075) ±0.025 0.735~0.785
0.025Min 0.025Min 0.025Min 0.025Min
0.015max 0.015max 0.015max 0.015max
打端子基本工艺设计要求

打端子基本工艺设计要求打端子是一种常见的电线电缆连接工艺,它能够确保电线电缆的电气连接可靠,并具有良好的机械强度和耐候性。
为了保证打端子的质量,以下是一些基本的工艺设计要求。
1.材料选择在进行打端子工艺设计时,材料的选择至关重要。
首先,选择适用于电线电缆的绝缘材料,并确保其具有良好的电绝缘性能,耐热性能和耐腐蚀性能。
其次,选择合适的导体材料,如铜或铝,以确保电流传递的效率和稳定性。
此外,还需要选择合适的端子材料和压接工具,以确保打端子的可靠性和一致性。
2.绝缘剥除在打端子之前,需要对电线电缆进行绝缘剥除。
正确的绝缘剥除是确保打端子质量的关键步骤。
剥除长度应符合规定要求,既要保证绝缘层与端子之间的绝缘距离符合安全要求,又要确保导体露出的长度能够满足端子的压接要求。
剥除绝缘层时,要注意不要损伤导体,以免影响电流传输和机械强度。
3.端子选择根据电线电缆的规格和要求,选择合适的端子进行压接。
端子的选择应考虑到导体的材料、形状和尺寸,并确保端子与电线电缆之间的良好适配性。
在选择端子时,还要注意其耐腐蚀性能和耐候性能,以满足使用环境的要求。
4.压接工艺压接是打端子的关键步骤,其质量直接影响到打端子连接的可靠性。
在进行压接之前,需根据端子和电线电缆的尺寸选择合适的压接工具,并确保其完好无损。
压接时,需控制好压接力度和时间,确保端子和导体的良好接触,并且不会损伤电线电缆。
压接之后,需进行拉力测试,以确保打端子的机械强度满足要求。
5.绝缘保护打端子之后,需要对打端子部位进行绝缘保护。
使用合适的绝缘套管或绝缘帽覆盖端子,以防止绝缘层受到损伤或湿气侵入,保证打端子的绝缘性能和耐候性能。
6.检测和质量控制在打端子过程中,需进行相应的检测和质量控制。
使用合适的仪器和设备对打端子的电气性能、机械强度和外观质量进行检测,确保打端子的符合设计要求。
同时,还需建立相应的质量控制体系,对打端子的每个环节进行监控和管理,确保打端子质量的一致性和稳定性。
- 1、下载文档前请自行甄别文档内容的完整性,平台不提供额外的编辑、内容补充、找答案等附加服务。
- 2、"仅部分预览"的文档,不可在线预览部分如存在完整性等问题,可反馈申请退款(可完整预览的文档不适用该条件!)。
- 3、如文档侵犯您的权益,请联系客服反馈,我们会尽快为您处理(人工客服工作时间:9:00-18:30)。
目录
1、概况 (1)
2、导线、避雷线机械物理性能 (1)
3、液压管参数 (1)
4、液压压接前的准备工作 (3)
5、画印、切割、穿管、施压顺序 (3)
6、压模 (5)
7、压接机具 (6)
8、液压操作 (6)
9、质量要求 (6)
10、施工安全措施 (7)
1. 概况
10输电线路,简称线。
全线导线使用型号为—300/40钢芯铝绞线;避雷线使用型号为—50镀锌钢绞线。
线路设计导线耐张及直线连接、地线直线连接均采用液压连接,地线耐张选用—2线夹弯头绑扎。
为了保证工程施工质量,特编写此工艺。
本工艺编写依据为226—87《架空送电线路导线及避雷线液压施工工艺规程》。
耐张管及直线接续管压前外形形状为圆形,压后外形形状呈六角形。
2. 导线、避雷线机械物理性能(见表一)
表一
导线、避雷线机械物理性能
导线、避雷线型号
导线避雷线
—300/40 —50
股数/直径()铝股48/2.85 / 钢芯7/2.22 7/3.0
截面积(2)铝部306.21 / 钢芯27.10 49.46 综合333.31 49.46
计算直径()23.76 9.0 单位重量()1058 423.7 瞬时拉断力(N)83410 58165 弹性系数(2)65000 181420 线膨胀系数(1/ 0C)20.5×10-611.5×10-6直流电阻(20℃)(Ω)0.09433 /
3. 液压管参数
3.1液压管外形(如图一、图二,图中尺寸均为实测值)
3.2 液压管尺寸(见表二)
表二液压管尺寸表(单位:)
3.3液压管内外径测量和计算方法
外径在管上均选三点检测,每点互成90°测量二个数据,以三个检测点共六个数据的平均值作为压前的外径;内径在管两端检测,每端互成90°测两个数据,以两端共四个数据的平均值作
为压前内径(耐张管外径只检测二点,内径只检测管口一点)。
所得的内外径必须符合压前管内外径允许的公差范围。
4.液压压接前的准备工作
4.1对使用的导线、避雷线,其结构及规格应认真进行检查,其规格应与工程设计相符,并符合同家标准的各项规定。
4.2所使用的各种接续管及耐张管,应用精度为0.02 mm的游标卡尺测量受压部分的内外直径;外观检查应符合规定;用钢尺测量各部长度,其尺寸、公差应符合标准要求。
4.3在使用液压设备之前,应检查其完好程度,以保证正常操作。
油压表必须定期校核,做到准确可靠。
4.4断线
4.4.1导线及避雷线的受压部分应平整完好,同时与管口距离15 m以内应不存在必须处理的缺陷。
4.4.2液压的导线及避雷线的端部在割线前应先将线掰直,并用小铁线绑扎好防止导地线松股,切割时剪刀应与被割导地线轴线垂直。
4.4.3在钢芯铝绞线割断铝股时,严禁伤及钢芯。
4.5管、线清洗
4.5.1对使用各种规格的接续管及耐张管,应用汽油清洗管内壁的油垢,并清除影响穿管的锌疤与焊渣。
4.5.2导线及避雷线液压部分穿管前应以棉纱擦去泥土。
如有油垢应以汽油清洗。
清洗长度应不短于穿管长的1.5倍。
4.5.3钢芯铝绞线的液压部分在穿管前,应以汽油清除其表面油垢,清除的长度对先套入铝管端应不短于铝管套入部位,对另一端应不短于半管长的1.5倍。
4.5.4对外层铝股应以棉纱蘸少量汽油(以用手攥不出油滴为适度),擦净表面油垢。
4.6涂801电力脂及清除铝股表面氧化膜的操作程序如下:
4.6.1涂801电力脂及清除铝股表面氧化膜的范围为铝股进入铝管部分。
4.6.2按第4.
5.3条将外层铝股及汽油清洗并干燥后,再将801电力脂薄薄地均匀涂上一层,以将外层铝股覆盖住。
4.6.3用钢丝刷沿钢芯铝绞线轴线方向对已涂801电力脂部分进行擦刷,将液压后能与铝管接触的铝股表面全部刷到。
5.画印、切割、穿管、施压顺序
5.1—50镀锌钢绞线(避雷线)的直线接续管(对接)—50G画印、切割、穿管、施压顺序见图三。
5.2—300/25钢芯铝绞线的直线接续管—300/25画印、切割、穿管、施压顺序见图四。
1
2
35
4
钢绞线
钢管
导线
铝管
2
1
铝管不压区
1
2346
5
3
铝管
LGJ-300/25导线
5mm
80mm 85mm
10mm
160mm 10mm 300mm
300mm 导线划印、割线
铝管穿管、施压
铝管划印、穿管、施压图四 JY-300/25管操作
5.3—300/25钢芯铝绞线的耐张管液压管—300/25穿管、施压顺序见图五。
耐张塔的耐张管引流板朝向规定:边导线耐张管线引流板垂直朝下;中导线耐张管线引流板往内角侧朝上30度。
铝管导线
钢锚
21
3
4
3
4
21
铝管不压区
60~62mm
钢芯
引流板
166mm
铝管
管口拔稍部分长度
图五 NY-300/25管操作
(注:以上导、地线直线、耐张管画印、线材切割、穿管数据及施压模数视厂家供应管子实际尺寸而定,并严格按226—87“架空送电线路导线及避雷线液压施工工艺规程”执行。
)
5.4导线耐张引流管的施压顺序见图六。
6.压模(见表三)
表三压模表(单位:)
名称适用管型适用线型
压模
对角距
压模
对边距
压模
长
备注
钢管模
-50G 50 18 15.4(-0.1)地线直线管的钢管钢模
300/25 300/25 16 13.7(-0.1)导线耐张管的钢管钢模
300/25 300/25 14
17.1(-0.1)
直线管的钢管钢模
铝管模
300/25
300/25
300
300/25 40 30.9(-0.1)
导线耐张、直线、修补管的
铝管钢模
7.压接机具
7.1超高压泵见表四
表四
7.2液压钳见表五
表五
8.液压操作
8.1使用的钢模应与被压管相配套,液压机的缸体应垂直地面,并放置平稳。
8.2被压管放入下钢模时,位置应正确。
检查印记是否处于指定位置,双手托住管、线后合上模。
这时使两侧导线或地线与管保持水平状态,并与液压机轴心相一致,以减少管子受压后可能产生弯曲。
8.3各种液压管在第一模压好后应检查压后对边距尺寸,符合标准后再继续操作。
8.4各种液压管的施压部位及操作顺序见图一至图六。
8.5每模的施压压力不应小于70 ,并保证模具合缝及压后尺寸不超标。
相邻两模之间至少应重叠5mm 。
靠近管口侧的一模与管口应保持有5mm 距离为不压区,耐张铝管自钢锚凹处反向施压时所压长度不小于60mm 。
8.6当管子压完后有飞边时,应将飞边锉掉,并用砂纸将锉过处磨光。
8.7钢管压后,凡锌皮脱落者,不论是否裸露于外,皆涂以富锌漆以防锈。
9. 质量要求
9.1架线前应对实际使用的导线、避雷线及相应的液压管,同配套的钢模,按“226—87”《架空送电线路导线及避雷线液压施工工艺规程》规定的操作工艺,制作检验性试件。
每种型式的试件不少于3根。
试件的据着力均不应小于导线及避雷线保证计算拉断力的95%。
9.2各种液压管压后对边距尺寸S的最大允许值为:
0.866×(0.993D)+0.2
D——管外径
而且三个对边距只允许有一个达到最大值,超过此规定时应更换钢模重压。
9.3液压后管子不应有肉眼可以看出的扭曲及弯曲现象,有明显弯曲时应校直,校直后不应出现裂
缝。
9.4各压接管施压后,应认真填写记录。
液压操作人员自检合格后,在管子指定部位打上自已的钢印,质检人员检查合格后,在记录表上签名。
10.施工安全措施
10.1割线材时线头应扎牢,并防止线头回弹伤人。
10.2压接操作时液压机应放置平稳;压件两侧扶线人应对准位置,手指不得伸入压模内。
10.3压接前检查液压钳体与顶盖的接触口,液压钳体有裂纹者严禁使用。
10.4液压机启动后先空载运行检查各部位运行情况,正常后方可使用,压接活塞起落时,人体不得位于压接上方。
10.5放入顶盖时,必须使顶盖与钳体完全吻合;严禁在末旋转到位的状态下压接。
10.6液压泵操作人员应与压接操作人员密切配合,并注意压力指示,不得过荷载。
10.7液压泵的安全溢流阀不得随意调整,并不得用溢流阀卸荷。