空分工艺流程说明
空分流程简介
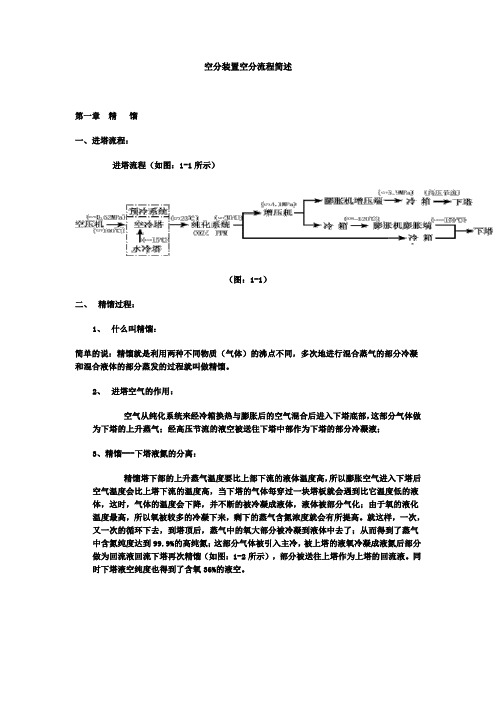
空分装置空分流程简述第一章精馏一、进塔流程:进塔流程(如图:1-1所示)(图:1-1)二、精馏过程:1、什么叫精馏:简单的说:精馏就是利用两种不同物质(气体)的沸点不同,多次地进行混合蒸气的部分冷凝和混合液体的部分蒸发的过程就叫做精馏。
2、进塔空气的作用:空气从纯化系统来经冷箱换热与膨胀后的空气混合后进入下塔底部,这部分气体做为下塔的上升蒸气;经高压节流的液空被送往下塔中部作为下塔的部分冷凝液;3、精馏---下塔液氮的分离:精馏塔下部的上升蒸气温度要比上部下流的液体温度高,所以膨胀空气进入下塔后空气温度会比上塔下流的温度高,当下塔的气体每穿过一块塔板就会遇到比它温度低的液体,这时,气体的温度会下降,并不断的被冷凝成液体,液体被部分气化;由于氧的液化温度最高,所以氧被较多的冷凝下来,剩下的蒸气含氮浓度就会有所提高。
就这样,一次,又一次的循环下去,到塔顶后,蒸气中的氧大部分被冷凝到液体中去了;从而得到了蒸气中含氮纯度达到99.9%的高纯氮;这部分气体被引入主冷,被上塔的液氧冷凝成液氮后部分做为回流液回流下塔再次精馏(如图:1-2所示),部分被送往上塔作为上塔的回流液。
同时下塔液空纯度也得到了含氧36%的液空。
(图:1-2)4、上塔精馏:将下塔液空经节流降压后送到上塔中部,作为上塔精馏原料;而从主冷部分抽出的液氮则成为上塔的回流液;与下塔精馏原理相同,液体下流时,经多次部分蒸发和冷凝,氮气较多的蒸发出来,于是下流液体中含氧浓度不断提高,到达上塔底部时,可以获得含氧99.9%的液氧;部分液氧作为产品抽出;由于下塔上升蒸气(纯氮气),被引入主冷冷凝,所以它将热量较多的传给了液氧,致使液氧复热蒸发作为上塔的上升气;在上升过程中,一部分蒸气冷凝成液体流下,另一部分蒸气随着不断上升,氮含量不断增加;到塔顶时,可得到99%以上的氮气。
第二章开车步骤一、启动步骤:1、空气压缩机;2、空气预冷系统;3、空气纯化系统;4、空气增压机;5、空气膨胀机;6、分馏塔系统操作。
空分工艺流程
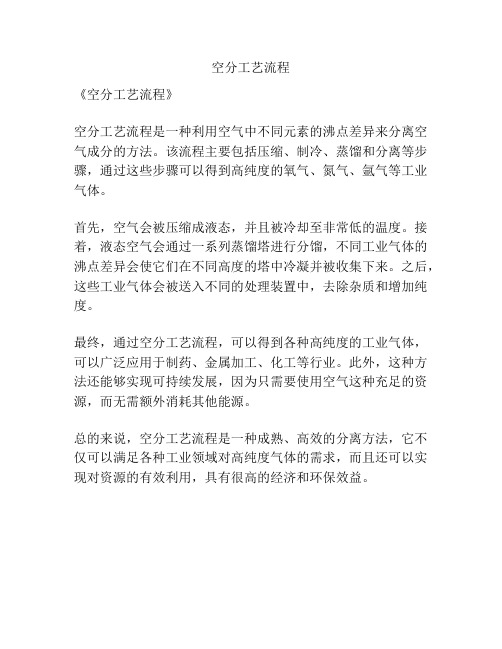
空分工艺流程
《空分工艺流程》
空分工艺流程是一种利用空气中不同元素的沸点差异来分离空气成分的方法。
该流程主要包括压缩、制冷、蒸馏和分离等步骤,通过这些步骤可以得到高纯度的氧气、氮气、氩气等工业气体。
首先,空气会被压缩成液态,并且被冷却至非常低的温度。
接着,液态空气会通过一系列蒸馏塔进行分馏,不同工业气体的沸点差异会使它们在不同高度的塔中冷凝并被收集下来。
之后,这些工业气体会被送入不同的处理装置中,去除杂质和增加纯度。
最终,通过空分工艺流程,可以得到各种高纯度的工业气体,可以广泛应用于制药、金属加工、化工等行业。
此外,这种方法还能够实现可持续发展,因为只需要使用空气这种充足的资源,而无需额外消耗其他能源。
总的来说,空分工艺流程是一种成熟、高效的分离方法,它不仅可以满足各种工业领域对高纯度气体的需求,而且还可以实现对资源的有效利用,具有很高的经济和环保效益。
空分的工艺流程

空分的工艺流程
《空分工艺流程》
空分是一种将空气中的氧气、氮气、稀有气体和其他成分通过物理分离的工艺。
空分工艺通常包括空气压缩、冷却凝华、蒸汽冷凝和分离等步骤。
首先,空气通常会被压缩到高压状态,以便进行后续的处理。
然后,被压缩的空气会在减压阀的作用下迅速减压并且冷却,在这个过程中会发生冷凝和液化。
接着,液化后的空气还会在蒸馏塔中进行进一步的分离工艺。
在蒸馏塔中,液化的空气会被升温并且进入一个叫做精馏塔的设备,通过塔内填料层的多级分馏逐步分离成不同的成分。
这些成分包括氧气、氮气、稀有气体等。
通过这种分馏过程,不同的气体可以被选择性地收集和提纯。
最终,通过这种工艺流程,空气中的各种成分可以被有效地分离和提纯,得到高纯度的氧气、氮气和其他气体产品。
这些高纯度的气体产品被广泛应用于医疗、工业、科学研究等领域。
总的来说,《空分工艺流程》是一种高效的气体分离技术,其具体步骤和设备设计可以根据需要进行调整和优化,以满足不同领域的需求。
空分工艺技术操作规程
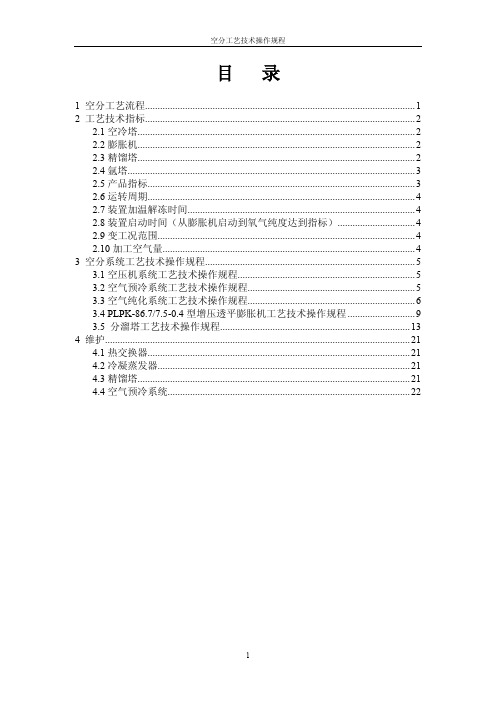
目录1 空分工艺流程 (1)2 工艺技术指标 (2)2.1空冷塔 (2)2.2膨胀机 (2)2.3精馏塔 (2)2.4氩塔 (3)2.5产品指标 (3)2.6运转周期 (4)2.7装置加温解冻时间 (4)2.8装置启动时间(从膨胀机启动到氧气纯度达到指标) (4)2.9变工况范围 (4)2.10加工空气量 (4)3 空分系统工艺技术操作规程 (5)3.1空压机系统工艺技术操作规程 (5)3.2空气预冷系统工艺技术操作规程 (5)3.3空气纯化系统工艺技术操作规程 (6)3.4 PLPK-86.7/7.5-0.4型增压透平膨胀机工艺技术操作规程 (9)3.5 分溜塔工艺技术操作规程 (13)4 维护 (21)4.1热交换器 (21)4.2冷凝蒸发器 (21)4.3精馏塔 (21)4.4空气预冷系统 (22)1 空分工艺流程由空压机来的高温空气经空冷塔降至~15.5℃,脱去其中的游离水后送入分子筛纯化系统。
在纯化系统采用变温吸附法连续分离空气中的水分和二氧化碳后,干燥空气分三路:一路入增压机,经增压后的空气入增压机后冷却器冷却到所需温度,进入主换热器换热后入透平膨胀机膨胀,然后进上塔参与精馏;一路仪表空气;绝大部分气体经主换热器换热后去下塔精馏,在顶部获得氮气,除一小部分作为冷热源到纯氩塔外,其余经冷凝蒸发器冷凝,冷凝的液体一部分作为下塔的回流液,一部分经过过冷器过冷后,再节流后作为上塔回流液送至上塔顶部,在下塔底部得到富氧液空,过冷器过冷后,节流送至上塔中部参与精馏。
经上塔精馏,在顶部得到产品氮气,在上塔中上部得到洿氮气,氮气及污氮气经过冷器,主换热器组复热。
复热后氮气除一部分送往用户管往外,其余均入水冷塔制冷;而污氮气除一部分用作再生气外,其余均入水冷塔制冷。
在上塔底部得到氧气,经主换热器复热后入氧平衡筒,经氧压机吸入压缩到2.5MPa后进入输气管网。
液氧经主冷凝蒸发器底部抽出入储槽。
从上塔中部抽出一部分氩馏份气,进入粗氩Ⅰ塔进行精馏,使氧的含量降低。
空分工艺流程简介
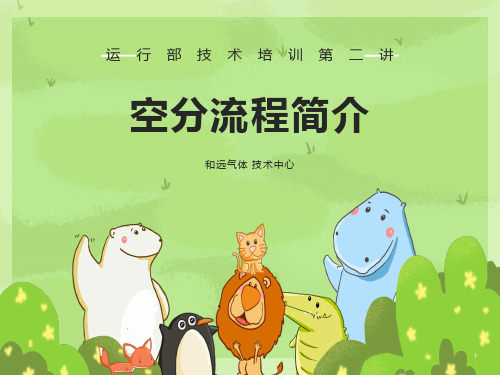
和远气体 技术中心
三、压缩系统
电机
压缩机头
润滑系统
冷却系统
电控、仪表系统
压缩系统
压缩系统将空气压缩到一定压力,为节流或膨胀产生冷量,为气体液化做准备。压缩系统耗电是空分系统耗能主要来源,无论从安全还是能耗角度来看,压缩系统地位都尤为突出突出,是制冷液化系统的心脏!
带动压缩机
压缩空气
润滑压缩机和电机轴承
污氮预冷水冷塔
换热效果
换热温差
换热系数
换热器材料结构
换热器是否结垢、阻塞
流体流动速度、流向
换热介质
水冷塔
空冷塔
和远气体 技术中心
四、冷却系统
冷箱内换热系统
主换热器
冷凝蒸发器
过冷器
是上塔底部液氧汽化、下塔顶部氮气液化,冷量自上塔传至下塔
回收返流气体的冷量
将空气冷却到所需状态
过冷去上塔夜空、液氮,减小节流气化率,增加回流液。
二、净化系统
和远气体 技术中心
净化系统主要由自洁式空气过滤器、纯化器组成。前者原理为过滤除尘,后者原理为吸附法除水蒸气、二氧化碳、碳氢化合物。具体的原理及操作,我们以后再讲,这里强调一下日常我们所要关注的内容。
1、流量(处理能力):选加工空气量的两倍; 2、压力损失; 3、除尘效率; 4、寿命
1、温度 2、压力 3、出纯化器后空气露点 4、出纯化器二氧化碳含量
三、压缩系统
1、活塞式压缩机从低压到超高压,适用范围广;效率高,排量范围广; 2、排气不稳定,脉动大;结构复杂,易损件多;活塞油润滑,导致空气带油。
压缩机应用实况
1、转速高,处理气量大,体积质量相对较小;结构简单;排气平稳,不受润滑油污染; 2、气量小的时侯效率低
空分工艺流程介绍07
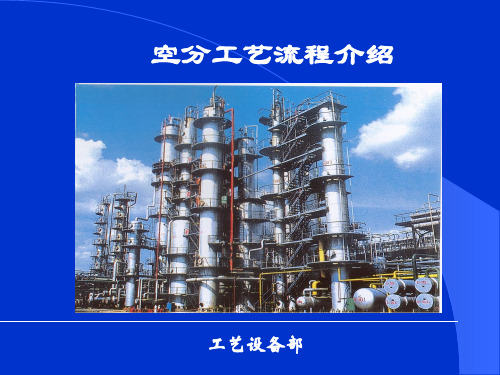
5.分子筛纯化系统
分子筛纯化系统由两台分子筛吸附器和 三台电加热器组成。
分子筛吸附器吸附空气中的水份、二氧 化碳和一些碳氢化合物,两台分子筛吸附 器一台工作,另一台再生,交替运行。再 生气的加热由电热器提供热量在其中完成。
6.分馏塔精馏系统 出分子筛吸附器的空气首先分为两部分:
第一部分直接进入主换热器冷却后进入 下塔;
第二部分通过空气增压机进一步压缩, 经增压机末级后冷却器冷却后再次分成两 部分。
一部分经膨胀机增压端增压并冷却后进 入主换热器,在主换热器合适的位置抽出, 进入膨胀机膨胀端膨胀后进入下塔参加精馏;
另一部分经过主换热器,然后经节流阀 节流成液体后进入下塔参加精馏。
下塔中的上升气体通过与回流液体接触 含氮量增加。所需的回流液氮来自下塔顶部 的冷凝蒸发器,在这里液氧得到蒸发,而气 氮得到冷凝。
利用双泵内压缩的流程使其投资低、安全 性能高、操作方便,还能控制优化。
二、工艺技术总述
本套制氧站工艺流程采用常温分子筛 预净化,空气增压透平膨胀机提供装置 所需冷量,双塔精馏,单泵内压缩流程, 同时设有液体贮存及汽化装置系统,整套 空分装置采用DCS系统控制。
三、总工艺流程图
四、工艺流程说明
空气经下塔初步精馏后,在下塔底部获 得液空,在顶部获得纯液氮。
6.1下塔从上到下产生以下产品或中间 产物:
·压力氮气 ·污液氮 ·富氧液空(36~40%) 下塔各产品去向如下:
①压力氮气:从下塔顶部抽出后经主换 复热后进入氮气压缩系统。
②污液氮:污液氮在过冷器中过冷后送 入上塔顶部作回流液。
1.流路简述 整套空分设备包括: 空气过滤系统、空气压缩系统、空气预 冷系统、分子筛纯化系统、分馏塔系统、 液体贮存系统、仪控系统、电控系统等八 大系统。
空分工艺流程描述(共8页)

2 工艺流程2工艺流程总体概述空气过滤及压缩来自大气中的空气经自洁式过滤器S01101,将空气中大于1μm的尘埃和机械杂质去除后,送离心式空气压缩机K01101,自洁式空气过滤器采用PLC控制,带自动反吹系统,反吹系统有时间、压差、时间和压差三种控制程序。
流量约168000Nm3〔A〕。
温度<105℃后进入空气预冷系统。
空气流量由空压机入口导叶B011101的开度来调节,空压机K01101采用3组内置段间冷却器冷却压缩空气;并在末级出口还设有一放空阀BV011121,在开车、停车期间,局部空气将由BV011121放空,以防止压缩机喘振。
润滑油系统:空压机和增压机共用一个润滑油站T011101,油系统包括润滑油系统、事故油系统〔2个高位油箱和4个蓄能器,空压机组和增压机组各1个高位油箱,2个蓄能器〕。
润滑油主要对机组各轴承起润滑、冷却及清洗杂质等作用。
油箱内的润滑油经润滑油泵加压后后送入润滑油冷却器E-011101A/B中冷却,经温度调节阀控制好油温后进入润滑油过滤器S-011101A/B,过滤掉油中杂质后进入润滑油总管,然后送到各润滑点经机组润滑后返回油箱;润滑油泵出口有一总管压力调节阀,用于调节润滑油过滤器S-011101A/B出口总管油压。
该油路同时为增压机提供润滑油,在空压机供油总管和增压机供油总管上分别设置有蓄能器和高位油箱。
以保证在主、辅油泵出现故障情况下向空压机、增压机供油,保证压缩机组的平安。
2.2空气预冷系统〔A〕、温度<105℃的空气由底部进入空冷塔C01201内;空冷塔的水分循环冷却水和循环冷冻水两路,进入空冷塔的空气首先经循环冷却水泵P01201A/B送至下塔顶部,流量为452t/h 、32℃的冷却水洗涤冷却,再经过循环冷冻水泵P01202A/B送至上塔上部流量为100t/h 、8℃的冷冻水进行洗涤冷却后由塔顶出来,温度被降至10℃送进入分子筛纯化系统。
循环冷却水流量由V012004〔FIC012002〕控制,空冷塔C01201下塔的液位由V012038〔LIC012001〕控制,循环冷却水流量设有高、低流量连锁,当循环冷却水到达联锁值时将自动启停泵用循环冷却水泵。
空分流程详细讲解

空分流程详细讲解
在化工生产中,空分技术是一项非常重要的工艺,它能够将空气中的氧气、氮
气等气体进行分离,以满足工业生产和生活需求。
下面我们将详细介绍空分的工艺流程。
首先,空分的工艺流程可以分为压缩、预冷、精馏、蒸汽回收等步骤。
1. 压缩空气从大气中获取,首先需要将其进行压缩,以增加气体分子的密度,提高分离效率。
压缩后的空气会进入压缩机,经过一系列压缩工艺,压缩比达到要求后,进入下一个环节。
2. 预冷压缩后的空气含有大量水分和杂质,需要通过冷却器进行预冷处理。
在预冷过程中,空气中的水分和杂质会凝结成液体,然后通过分离装置将其分离出去,以保证后续工艺的顺利进行。
3. 精馏精馏是空气分离的核心步骤,通过精馏塔将空气中的氧气、氮气等气体按照其沸点的不同进行分离。
在精馏塔内,气体混合物被加热至沸点,然后在不同高度上凝结成液体,从而实现气体的分离。
4. 蒸汽回收在精馏过程中,会产生大量的废热,为了提高能源利用效率,通常会将废热通过蒸汽回收装置进行回收利用。
蒸汽回收装置可以将废热转化为蒸汽,用于加热其他部分的工艺设备,实现能量的循环利用。
通过以上流程,空分技术能够高效地将空气中的氧气、氮气等气体进行有效分离,为工业生产和生活提供了重要的物质基础。
在实际应用过程中,还需要根据不同的需求和工艺要求进行调整和优化,以实现最佳的分离效果和能源利用效率。
空分技术作为一种成熟的工艺,在化工领域中扮演着至关重要的角色,不仅广
泛应用于气体生产、化工生产等领域,还在医疗、食品加工等领域有着重要的应用价值。
随着工业化进程的不断推进,空分技术将继续发挥重要作用,为人类的生产生活提供更广阔的发展空间。
空分设备工艺流程图的讲解
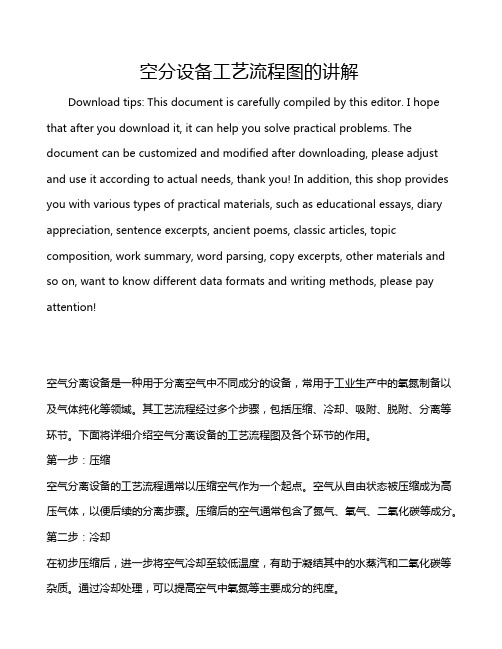
空分设备工艺流程图的讲解Download tips: This document is carefully compiled by this editor. I hope that after you download it, it can help you solve practical problems. The document can be customized and modified after downloading, please adjust and use it according to actual needs, thank you! In addition, this shop provides you with various types of practical materials, such as educational essays, diary appreciation, sentence excerpts, ancient poems, classic articles, topic composition, work summary, word parsing, copy excerpts, other materials and so on, want to know different data formats and writing methods, please pay attention!空气分离设备是一种用于分离空气中不同成分的设备,常用于工业生产中的氧氮制备以及气体纯化等领域。
其工艺流程经过多个步骤,包括压缩、冷却、吸附、脱附、分离等环节。
下面将详细介绍空气分离设备的工艺流程图及各个环节的作用。
第一步:压缩空气分离设备的工艺流程通常以压缩空气作为一个起点。
空气从自由状态被压缩成为高压气体,以便后续的分离步骤。
压缩后的空气通常包含了氮气、氧气、二氧化碳等成分。
空分工艺流程简介

设备紧凑,能耗低,操作简便。但膜材料性能要求较高,分离效率受膜材料影响较大。
03
空分设备组成及功能
空气压缩机
01
将大气中的空气吸入并进行压缩,提高空气的压力 和温度。
02
为后续的冷却、纯化和分离过程提供必要的动力。
03
通常采用多级压缩和级间冷却的方式,以提高压缩 效率和降低能耗。
冷却器与纯化器
原理
空分工艺主要基于空气中氧气、氮气等组分的沸点不同,通过精馏方法将其分 离。在低温条件下,空气被液化后送入精馏塔,经过多次部分汽化和部分冷凝, 实现各组分的分离。
空分工艺应用领域
冶金工业
用于高炉富氧炼铁、炼 钢吹氧等,提高产量和
降低能耗。
化学工业
石油工业
医疗保健
作为合成氨、合成甲醇 等化工过程的原料气。
分离过程
精馏塔分离
利用精馏塔中的温度梯度和浓度梯度,使空气组分在塔内多次部分汽化和部分冷凝,实现氧气、氮气等组 分的分离。
冷凝蒸发法
通过冷凝器将空气液化后,利用不同组分的沸点差异进行分离。液氧在冷凝蒸发器中蒸发,同时吸收热量, 使液氮冷凝成液体,从而实现氧氮分离。
产品输出与储存
产品输出
将分离得到的氧气ቤተ መጻሕፍቲ ባይዱ氮气等产品通过管道 输送至用户端或储存设备。
再生技术
采用加热、减压等方法对 吸附剂进行再生,恢复其 吸附性能。
膜分离法关键技术与参数
膜材料选择
选用具有高渗透性、选择 性和稳定性的膜材料,如 有机膜、无机膜等。
膜组件设计
通过合理的膜组件结构设 计和优化,提高膜分离效 率。
操作条件
控制适当的操作温度、压 力和膜两侧浓度差,以实 现目标组分的有效分离。
空分制氮机工艺流程

空分制氮机工艺流程
一、压缩环节
空分制氮机的工艺流程首先是对大气空气进行压缩。
大气中的氧气、氮气等成分在通过压缩机进行压缩后,可以增加其浓度和密度,为后续的分离打下基础。
压缩机将空气压缩至一定压力后,送入预处理环节。
二、预处理环节
在预处理环节,主要是对压缩后的空气进行清洁和除尘处理,以确保后续的分离过程能够顺利进行。
通常采用滤网、脱水器等设备对空气进行过滤和干燥处理,以去除其中的杂质和水分。
三、分离环节
在分离环节中,采用分子筛等吸附材料对压缩后的空气进行分离,将其中的氧气、水蒸气等成分吸附下来,从而提高氮气的纯度。
通过调节分离器的工作参数,可以实现对不同成分的高效分离和提纯。
四、制氮环节
分离出的氮气在制氮环节中通过膜分离、压力摩擦或冷却凝结等方式进一步提纯和提纯,最终得到所需的纯氮气产品。
制氮过程中需要根据实际生产需求和要求,调节工艺参数和设备运行状态,确保生产出优质的氮气产品。
五、回收环节
在制氮过程中产生的废气和气体残余物质,可以通过回收环节进行处理和再利用,减少资源浪费和环境污染。
通过回收设备将废气中的氮气等可再利用成分进行回收,并进行再处理和利用,提高生产效率和资源利用率。
综上所述,空分制氮机的工艺流程是一个复杂而精密的过程,需要依靠各种设备和技术手段协同作用,确保生产出高质量的氮气产品。
通过不断优化工艺流程和设备配置,可以提高生产效率和产品质量,推动空分制氮技术的进一步发展和应用。
空分车间工艺流程

空分车间工艺流程空分车间工艺流程简介空分车间是空气分离设备的生产车间,主要用于将空气中的不同成分进行分离,以获取纯净的气体产品。
以下是空分车间工艺流程的详细说明。
工艺流程1.原料空气进料–空气通过进气管道进入空分车间。
–空气中的杂质通过过滤器进行初步过滤,以确保进入空分设备的空气质量。
2.原料空气压缩–空气通过压缩机进行压缩,以提高其浓度。
–压缩机会消耗一定能量,因此需要进行能量平衡计算,以确保生产的经济性和能源效率。
3.空分设备分离–经压缩的空气进入空分设备,如空分列塔。
–在空分设备中,空气中的氮气、氧气等成分会因其沸点差异而分离出来。
–不同的空分设备可能采用不同的分离方式,如吸附、膜分离等。
4.产品收集–分离后的纯净气体产品根据需要进行收集。
–收集方式可以是直接存储在储罐中,也可以通过管道输送至其他生产线。
5.尾气处理–分离过程中产生的尾气需要进行处理,以减少对环境的污染。
–尾气处理方式可以是燃烧、吸附等,以将有害物质转化为无害物质或减少其污染程度。
6.能源回收–在空分车间的工艺流程中,可以采用能量回收系统,将一部分能量进行回收利用。
–回收的能量可以用于提供压缩机、空分设备等的动力需求,从而降低能源消耗。
结论空分车间工艺流程的设计和优化对于提高空分设备的生产效率、节约能源和降低环境污染具有重要意义。
通过合理规划每个流程的参数和操作方式,可以实现高效、可持续的空气分离生产。
工艺流程的顺序、参数和设备的选择对空气分离的效果和经济效益有着重要影响。
以下是一些在设计和运营空分车间时需要考虑的因素:1.原料空气质量:为确保分离效果和产品质量,需要对原料空气的质量进行监控和控制。
通过定期清洁和更换过滤器,可以避免杂质对设备的损坏和产品的污染。
2.压缩机效率:压缩机在空气分离工艺中起到关键作用。
选择高效率的压缩机,优化压缩比和排气温度,可以提高工艺的能源利用率和经济性。
3.分离设备选择:根据产品需求和生产规模,选择适合的空分设备。
全液体空分工艺流程说明
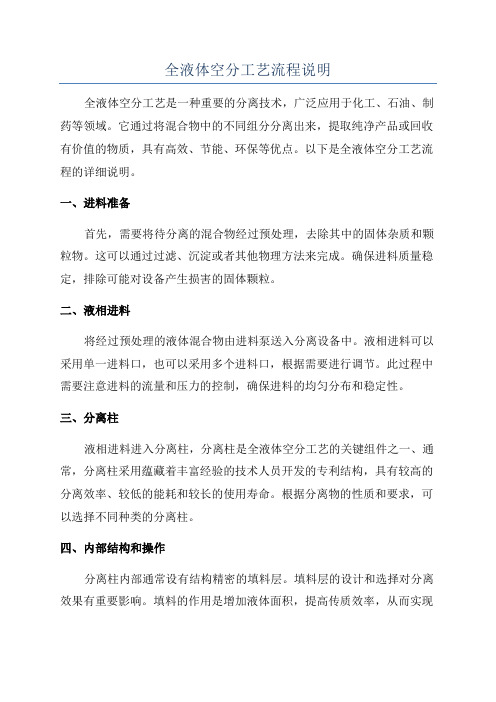
全液体空分工艺流程说明全液体空分工艺是一种重要的分离技术,广泛应用于化工、石油、制药等领域。
它通过将混合物中的不同组分分离出来,提取纯净产品或回收有价值的物质,具有高效、节能、环保等优点。
以下是全液体空分工艺流程的详细说明。
一、进料准备首先,需要将待分离的混合物经过预处理,去除其中的固体杂质和颗粒物。
这可以通过过滤、沉淀或者其他物理方法来完成。
确保进料质量稳定,排除可能对设备产生损害的固体颗粒。
二、液相进料将经过预处理的液体混合物由进料泵送入分离设备中。
液相进料可以采用单一进料口,也可以采用多个进料口,根据需要进行调节。
此过程中需要注意进料的流量和压力的控制,确保进料的均匀分布和稳定性。
三、分离柱液相进料进入分离柱,分离柱是全液体空分工艺的关键组件之一、通常,分离柱采用蕴藏着丰富经验的技术人员开发的专利结构,具有较高的分离效率、较低的能耗和较长的使用寿命。
根据分离物的性质和要求,可以选择不同种类的分离柱。
四、内部结构和操作分离柱内部通常设有结构精密的填料层。
填料层的设计和选择对分离效果有重要影响。
填料的作用是增加液体面积,提高传质效率,从而实现更好的分离效果。
同时,填料还可以提供支撑和保护作用,防止液流运动造成的堆积和破坏。
五、分离原理六、分离过程的控制在分离过程中,需要根据需要对分离柱的操作参数进行调节和控制。
这些参数包括流量、温度、压力等。
通过合理的调整,可以提高分离效果,同时降低能耗和操作成本。
七、产品回收经过分离后,不同组分的纯净产品可以分别收集和回收利用。
同时,废液可以进行处理和排放。
确保产品的质量和回收率是全液体空分工艺的重要目标之一八、设备维护和保养九、安全措施和环保要求在全液体空分工艺的运行过程中,需要严格遵守安全操作规程和环境保护要求。
必须采取必要的措施,确保工作人员的安全和设备的可靠性。
综上所述,全液体空分工艺流程可以根据具体需求和分离物的特性进行调整和优化。
它是一种高效、节能、环保的分离方法,对于提高产品质量、降低能耗和减少污染物排放具有重要意义。
18000Nm3h空分工艺流程介绍

18000Nm3h 空分工艺流程介绍法液空18000Nm3/h 空分工艺流程介绍一、空分工艺流程概况:空气主要是由O2、N2组成的混合物,其中N2占78.084%,O2占20.948%,Ar占0.934%。
在一个标准大气压的下,各组分的沸点不同,N2:-195.8OC,Ar:-185.9 OC,O2:-183.0 OC。
我们装置就是利用了空气混合物中各组分的沸点这一物理性质的不同,采用深度冷冻法的原理,通过精馏来达到分离空气中各组分的目的。
空气分离装置主要由空气压缩、预冷、净化、热交换、制冷、精馏和产品气的压缩七个系统组成,另外,空分还有一个精氩生产系统。
空气压缩系统主要是由空气吸入过滤器、压缩机组和冷却器组成,用来压缩空气至所需的分离压力,压力太高,能耗增大;压力太低,空气分离困难。
空气预冷系统主要由空冷塔、水冷塔、水泵、冷冻机组成,采用经过冷却的水来冷却空气,减少空气中的含水量,减轻分子筛吸附器的工作负荷,延长分子筛的使用寿命。
同时,也起到洗涤空气的作用,如一些灰尘,细小的机械杂质和空气中的一些有害气体(硫化物等)。
空气净化系统主要由分子筛吸附器、蒸汽(或电)加热器组成,主要用来清除空气中的H2O、C2O和部分碳氢化合物,防止它们进入管道和设备,造成管道和设备堵塞,阻力增加,甚至造成安全等事故,影响设备的正常运行。
气体的热交换系统主要是各流体在热交换器中发生热量交换,使热流体空气冷却至液化温度,而冷流体O2、N2、WN2被复热至常温出冷箱。
制冷系统主要由膨胀机和冷却器组成,用于制冷量,来补充热交换不完全损失(热端温差)、跑冷损失(箱板等结霜)和排液损失(液体产品的生产)等损失冷量。
精馏系统主要由精馏塔(下塔、主塔、上塔、辅塔)和过冷器组成,通过冷热流体的接触换热和多次部分蒸发和部分冷凝,低沸点组分被蒸发,高沸点组分被冷凝,从而在塔的下部得到纯度较高的高沸点组分,而在塔的上部得到纯度较高的低沸点组分。
空气化工空分工艺流程

1.0设备选择和流程说明Equipment selection and Process description1.1工艺流程概述Process description本装置以空气为原料,冷却水为辅助原料,经空气压缩、空气净化与冷却以及精馏分离等过程,将空气分离得到氧气、氮气、液氧、液氮和液氩。
大致流程叙述如下(详细说明参见文件工艺流程描述DOC0000382869):The primary raw material in the air separation process is atmospheric air, with auxiliary utilities of cooling water and lubrication oil for machinery. Nitrogen, Oxygen and Argon are separated from the air by a process of compression, liquefactioin and cryogenic distillation. The products may be recovered in both gaseous and liquid phase. Brief process is summarized below and details refer to document”Process Description” DOC0000382869:1.1.1 空气压缩Air compression空气从入口空气过滤器吸入,过滤除去悬浮固体颗粒(污物,灰尘等)后,经主空压机入口消音器,削弱从压缩机第一级叶轮产生的噪音,然后进入K111主空压机(MAC)进行压缩。
Air is drawn through the Inlet Air Filter to remove suspended solid particles (dirt, dust, etc.) and then passes through the MAC Suction Silencer which attenuates the noise radiating from the first stage impeller. The air is then compressed in the K111 Main Air Compressor (MAC).空气被压缩后温度会升高。
空分工艺流程
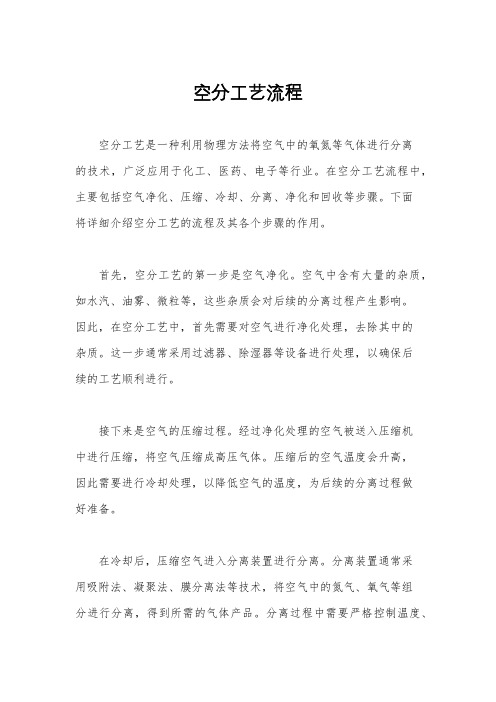
空分工艺流程空分工艺是一种利用物理方法将空气中的氧氮等气体进行分离的技术,广泛应用于化工、医药、电子等行业。
在空分工艺流程中,主要包括空气净化、压缩、冷却、分离、净化和回收等步骤。
下面将详细介绍空分工艺的流程及其各个步骤的作用。
首先,空分工艺的第一步是空气净化。
空气中含有大量的杂质,如水汽、油雾、微粒等,这些杂质会对后续的分离过程产生影响。
因此,在空分工艺中,首先需要对空气进行净化处理,去除其中的杂质。
这一步通常采用过滤器、除湿器等设备进行处理,以确保后续的工艺顺利进行。
接下来是空气的压缩过程。
经过净化处理的空气被送入压缩机中进行压缩,将空气压缩成高压气体。
压缩后的空气温度会升高,因此需要进行冷却处理,以降低空气的温度,为后续的分离过程做好准备。
在冷却后,压缩空气进入分离装置进行分离。
分离装置通常采用吸附法、凝聚法、膜分离法等技术,将空气中的氮气、氧气等组分进行分离,得到所需的气体产品。
分离过程中需要严格控制温度、压力等参数,以确保产品气体的纯度和产量。
分离后的气体产品还需要进行进一步的净化处理。
这一步主要是去除残余的杂质、水汽等,提高气体产品的纯度和品质。
净化过程通常采用吸附剂、膜分离器等设备进行处理,将气体产品中的杂质去除,得到高纯度的气体产品。
最后,经过净化处理的气体产品被送入储气罐进行储存,或者直接输送到用户现场使用。
储气罐通常采用高压气瓶或液氮罐等设备进行储存,以确保气体产品的安全和稳定供应。
综上所述,空分工艺流程包括空气净化、压缩、冷却、分离、净化和储存等步骤。
通过这些步骤,可以将空气中的氧氮等气体进行有效分离,得到高纯度的气体产品,满足不同行业的需求。
空分工艺在化工、医药、电子等领域具有重要的应用价值,对于促进工业发展和提高产品质量具有重要意义。
- 1、下载文档前请自行甄别文档内容的完整性,平台不提供额外的编辑、内容补充、找答案等附加服务。
- 2、"仅部分预览"的文档,不可在线预览部分如存在完整性等问题,可反馈申请退款(可完整预览的文档不适用该条件!)。
- 3、如文档侵犯您的权益,请联系客服反馈,我们会尽快为您处理(人工客服工作时间:9:00-18:30)。
2.2.2 工艺流程简述
2.2.2.1压缩、预冷
原料空气通过空气过滤系统,去除灰尘和机械杂质。
过滤后的空气由多级压缩机压缩到工艺所需压力,然后进入空冷塔进行冷却。
压缩过程中产生的冷凝疏水在厂房内凝液罐中汇集后,由凝液泵加压送入循环回水管线。
空气自下而上穿过空冷塔,以对流形式被循环冷却水和低温冷冻水分段冷却,同时也得到了清洗。
在空冷塔底部,空气被由冷却水泵送入的循环冷却水预冷。
在顶部,空气由冷冻水泵送入的冷冻水进一步冷却。
低温冷冻水是在水冷塔中产生,其产生的原理是利用从冷箱来的干燥的污氮气汽化小部分循环冷却水,水在汽化过程中吸收热量,同时使冷却水的温度降低。
空气离开空冷塔的温度越低,对于下游空气纯化单元的负荷就越小。
空气中的少量化学杂质也被冷却水吸收。
空冷塔和水冷塔为填料塔,在空冷塔顶部设置有除沫器以去除空气中的水雾。
2.2.2.2 吸附净化
、氮氧化合物和绝大多数碳氢化合物都被吸附。
空气纯化单元包括两台交替运行的分子筛吸附器,压缩空气通过吸附器时,水、CO
2
吸附器交替循环,即一只吸附器吸附杂质而另一只吸附器被再生。
吸附和再生过程顺序自动控制以保证装置连续运行。
采用来自冷箱的污氮对吸附器进行再生。
再生时吸附器与吸附流程隔离,再生气放空。
与吸附流程隔离的吸附器先卸压,然后先用经蒸汽加热器加热的低压污氮进行再生,然后用从蒸汽加热器旁路来的冷低温氮气对吸附器进行冷却,之后再用吸附后的空气对吸附器升压并返
回吸附流程。
再生循环主要有下面几个组成部分:
泄压-加热-冷却-增压
单台吸附器的设计切换周期不少于4小时。
法液空流程的纯化单元设置特殊再生加热器,必要时可用特殊再生加热器进行特殊再生。
针对厂区空气中CO
2含量波动大的特点,在分子筛吸附器空气出口设有CO
2
在线分析仪,可以随时监测吸附器的运行工况,从而保
证出口的CO
2
组分满足工艺要求。
净化后的空气分为两股:其中一股进入低压换热器;另一股去空气增压机增压。
2.2.2.3 空气精馏
净化后的空气分为两部分:
一部分净化空气主气流直接进入冷箱,并在低压主换热器中与返流产品进行热交换而冷却至接近于露点。
这股气流然后进入中压塔底部作首次分离。
上升气体和下降液体接触后氮的含量升高。
中压塔顶部的氮气在主冷凝蒸发器中被沸腾液氧冷凝成液氮作为中压塔的回流液。
另一部分净化空气经增压机压缩后部分送入透平膨胀机的增压端中增压后送入冷箱,在冷箱的高压主换热器中与高压氧换热被液化,然后经过高压节流阀节流后作为回流液进入中压塔和低压塔。
剩余部分增压空气在高压主换热器中冷却至适当温度抽出,然后经透平膨胀机膨胀端膨胀后送入中压塔。
从上到下,中压塔产出如下产品:液氮产品、低压氮气产品(下游MTO装置启动时的氮气)、中压氮气产品、污氮回流液、富氧液空。
液氮产品经过过冷器后作为液体产品输出,部分送入贮槽。
中压氮气在低压主换热器中被汽化并复热作为氮气产品输出。
在进低压主换热器前,中压塔抽出来的液氮已经过液氮泵压缩至中压氮气产品压力。
低压氮气从中压塔顶部抽取,经过低压主换热器中被复热后送出。
低压氮气也包括下游MTO装置启动时所需的低压氮气,该股氮气在送出冷箱后经节流减压至常压进入氮压机增压至规格压力。
污氮回流液和富氧液空在过冷器中过冷后,经节流送入低压塔。
低压塔产生如下产品:在底部的液氧、在顶部的污氮。
从低压塔的底部抽出液氧,送入高压液氧泵增压至产品压力后,进入冷箱内高压主换热器在其中被汽化并复热作为高压氧气产品输出。
高压液氧泵采用3×50%配置,两台满负荷运转,另一台冷备,当运行的这两台泵其中有一台发生故障时,备用泵立即投用工作。
在低压塔的顶部抽出污氮,复热后出冷箱,一部分送到分子筛吸附器做为再生气体,剩下的被送到水冷塔。
2.2.2.4 液氧、液氮储存及气化
(1)液氧贮槽和后备系统
来自低压塔的液氧产品经过过冷器后可送入3,000m3的液氧贮槽。
后备系统自动启动时,贮槽中的液氧产品经过高压液氧后备泵升压至所需压力后,在水浴式汽化器中汽化作为紧急情况时的后备高压氧气产品输出。
配置两台低压液氧后备泵(2×100%,排压0.9 MPag,连接到汽化器,)用于生产低压氧气。
另外,低压液氧后备泵后预留液氧充车接口。
(2)液氮贮槽和后备系统
来自中压塔的液氮产品经过过冷器后送入3,000m3的液氮贮槽。
当需要启动低压液氮后备系统时,贮槽中的液氮产品可经过低压液氮后备泵升压至所需压力后,在水浴式汽化器中汽化作为低压氮气产品输出。
当需要启动高压液氮后备系统时,贮槽中的液氮产品可经过高压液氮后备泵升压至所需压力后,在水浴式汽化器中汽化作为高压氮气产品输出。
从低压液氮后备泵出口接出一根液氮装车线。
液氮装车设施包括快速切断阀、手阀、安全阀。
后备系统设置返液氮至精馏塔的管线。
增加外购液氮至后备液氮罐充装装置,进口为低温阀门。
事故氮气的生产,来自液氮贮槽的液氮,进入事故液氮后备泵增压至1.0MPag。
之后液氮送入空浴式蒸发器和与之串联的电热式蒸发器。
后备系统液氮贮槽2130-V50中液氮经过高压液氮后备泵2130-P53A/B增压至8.5MPaG后,经过高压液氮汽化器2130-E53复热至常温后送入高压氮气缓冲罐2130-V04,再送入高压氮气管网。
高压氮气缓冲罐2130-V04后设置压力控制阀,保持高压氮气管网稳定在6~8.0MPaG。
当高压氮气管网压力低于6 MPaG,启动高压液氮后备泵给高压氮罐充压,当高压氮气罐压力达到8.5 MPaG,停高压液氮后备泵。
2.2.2.5冷量的制取
装置所需的大部分冷量由增压透平膨胀机组膨胀制冷和高压液空节流时产生制冷所提供。
2.2.2.6 稀有气体粗提装置
(1)贫氪氙的提取
氪和氙比空气中主要成份的沸点均高,因此它们在空分装置中积聚在温度较高的塔底。
抽取低压塔主冷凝蒸发器底部的含Kr/Xe 的液氧,经过液氧过滤器除去N
O,送入贫氪氙塔中精馏,在贫氪氙塔的底部得到纯度约0.2%的氪氙液体;而大部分液氧在塔中被气
2
化,之后返送至低压塔内。
积聚塔底部设有冷凝蒸发器, 来自中压塔的中压氮气作为热源,冷凝后的液氮送至低压塔。
(2)粗氖氦的提取
抽取中压塔顶部含Ne/He的气氮,送入粗氖氦混合液塔精馏,在塔顶部通过粗氖氦冷凝器得到氖氦气体产品;塔底部的液氮返送回中压塔内。
(3)产品输送
贫氪氙、粗氖氦由液体产品泵通过真空管道送到界区外稀有气体精制装置。
2.2.2.7仪表空气和工厂空气的供应
正常生产时仪表空气和工厂空气由空分装置供气,开车和空分故障时由空压站供气;
仪表空气由空分装置空气增压机一级出口抽取。
每套空分抽取气量为11000Nm3/h,0.97MPa(G)的压缩空气,其中6000Nm3/h 用于仪表空气,5000Nm3/h用于工厂空气。
来自三套空分共18000Nm3/h的仪表空气进入仪表空气缓冲罐(2160-V02),经仪表空气压力调节阀减压后送全厂使用。
为保障全厂仪表空气用气安全,仪表空气压力调节阀采用两台调节阀,其中一台作为备用。
从三套空分装置空气增压机末级出口共抽取3000Nm3/h,4.8MPa(G)的压缩空气送入仪表空气储罐(2160-V01A/B),作为全厂事故时仪表空气储罐的补充气源。
事故仪表空气储罐选用两台,储罐工作压力 4.8MPa(G),为单台全容积~134m3,两台总容积~264m3。
事故工况下可连续向全厂供应0.7MPa(G)(出仪表空气界区)的仪表空气≥30分钟。
事故工况时,经仪表空气压力调节阀减压后送全厂使用。
为保障全厂仪表空气事故时用气安全,仪表空气压力调节阀也采用两台调节阀,其中一台作为备用。
2.2.2.8 空压站
空压站用于空分装置开车前为全厂提供仪表空气和工厂空气
空气经过空气过滤器进入离心式空气压缩机入口,经压缩机压缩到1.0MPag后,高温、饱和的湿空气由压缩机排出后直接进入干燥机,其中先进入干燥机的一塔对其进行加热,后进入后冷却器,再进入气水分离器,液态水份被分离后再进入另一塔进行干燥,达到压力下的露点温度≤-45℃后干燥空气,送到仪表空气缓冲罐或工厂空气缓冲罐,再经过管道送到各用户。
150分钟后,被加热的塔由旁通阀旁通,高温、饱和的湿空气直接进入后冷却器冷却,再经过气水分离、干燥进入使用管网,而由干燥机的出口引一部分气流经过节流孔,完成对被加热的塔冷吹,这一部分气流最后由再生排气口排出。
85分钟后,冷吹结束,开始升压;5分钟后双塔压力均衡,4小时整,双塔切换,干燥机进行另外一塔的再生过程。
如干燥机处于露点监控状态,在升压结束后,干燥机根据出口露点情况切换。
合格的仪表空气和压缩空气被送入相应的管网,仪表空气和工厂空气的气量可以根据实际生产需要灵活分配。
2.2.2.9 氮气增压
0.4MPaG氮气管网引出30000Nm3/h 0.4MPaG氮气,通过减压阀减压至常压,送入氮气压缩机增压至0.9MPaG后,供MTO装置开车使用。
氮气压缩机采用多轴离心式压缩机。
另全厂装置开车前,可通过该氮气压缩机压缩空气,供全厂管道吹扫使用。