塑料螺纹等结构设计演示文稿
塑胶件的结构设计:螺纹连接结构篇(上)

塑胶件的结构设计:螺纹连接结构篇(上)塑胶件的连接结构,有两种应用较广泛,一种是卡扣连接(之前文章已有介绍),另一种是螺纹连接。
其中螺纹连接我认为是应用最广泛、最常见的连接结构。
基于成本考虑,尽管大家都在尽量减少螺纹连接的使用,但是,对于绝大部分产品结构设计的需要,螺纹连接结构还是很难完全被取代,因为,其相对于卡扣连接有以下优点:•连接强度比卡扣大得多,即使受到额外负载也不容易松脱,可靠性高;•可拆卸次数多,特别是使用机牙螺丝的情况下,连接强度并不会受影响很大;•螺丝柱在模具上成型方便,模具结构简单,且容易调整;•操作简单,易学,谁不会打个螺丝呢。
当然,相对于卡扣,其缺点如下:•成本相对高些,螺丝、螺母、电批、螺丝刀等紧固件与工具的成本;•对于外观零件,会在外壳上存在放置螺丝以及操作的孔洞,破坏外观的完整性;•装配时间长,预埋螺母、放置螺丝、使用电批或螺丝工具的时间成本,间接增加装配成本;•螺纹连接的结构类型少,设计自由度比较受限,常常在主出模方向设计居多。
结合卡扣和螺纹连接的优缺点,在实际产品结构设计上,常常兼容这两种连接方式,使产品能够实现性能与成本的平衡。
塑胶件的螺纹连接结构一般有以下两种:•一种是采用机械牙螺丝(简称机牙螺丝)的结构;•一种是采用自攻牙螺丝(简称自攻螺丝)的结构;这两种结构比较常见的结构形式如下图,共同点是两个塑胶零件上分别有用于与螺丝配合的螺丝柱(BOSS柱)和用于支承螺丝头的套司;区别在于采用机牙螺丝的螺丝柱内孔需预埋螺母。
机牙螺丝与自攻螺丝的区别:从外形上看:常用机牙螺丝的尾部一般为平尾,头部形状如下图:常用自攻螺丝的尾部一般分尖尾和平尾,头部形状如下图:最主要的区别在于牙型:机牙螺丝(Machine Screw),牙峰与牙底的大小相差无几,牙距比较小,牙型的标准角度为60°,螺纹的标记为M*/*。
使用机牙螺丝需要要搭配合适的螺母或在预制孔内预先攻牙。
自攻螺丝(Self tapping screw),牙峰很尖,牙底平面较宽,而牙型的标准角度则小于60°,螺纹的标记为ST*/*。
塑料模基本结构及零部件的设计
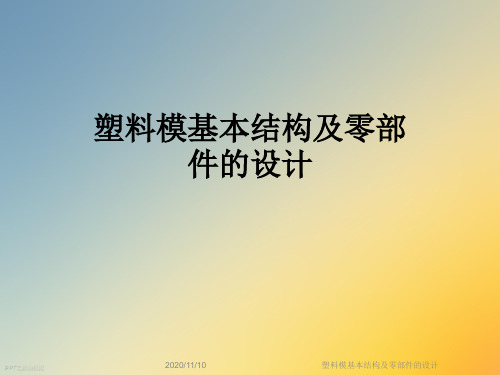
PPT文档演模板
塑料模基本结构及零部件的设计
•4.1.1 塑料模的分类
1.按模塑方法分类
(1)注射模:系在注射机上使用的模 具。目前它主要用与成型热塑性塑料,少 数品种的热固性塑料适用于该模具成型。
(2)压缩模:系在液压机上采用压缩工 艺来成型塑件的模具。它主要用于成型热 固性塑料。
(3)压注模:系在液压机上采用压注工 艺来成型塑件的模具。它适用于成型热固 性塑料。
•第4章 塑料模基本结构及零部件设计
4.1 塑料模的分类和基本结构 4.2 塑料模分型面的选则 4.3 模具型腔数目的确定 4.4 成型零部件设计 4.5 结构零件的设计 4.6 排气结构设计 4.7 塑料模材料及其选用 4.8 思考题
PPT文档演模板
塑料模基本结构及零部件的设计
•4.1 塑料模的分类和基本结构
➢ 分型面的表达方法:如图4—8所示用 短,粗实线标出分型面位置,箭头表 示分离动作方向。
➢ 分型面的形状有平面、斜面、阶梯面 和曲面。
PPT文档演模板
塑料模基本结构及零部件的设计
•4.2.2 塑料模分型面选择的一般原则
分型面选择的一般原则
• 基本原则:必须选择塑件断面轮廓最大 的地方作为分型面,这是确保塑件能够脱出 模具的基本原则。 • • 影响:塑件质量、模具加工、的生产难 易度
3.设置滞留结构
在模具零件的侧面加工浅凹槽、设 锥形拉料穴或拉料杆等,都可以起到 滞留塑件作用,如图4-25所示。
PPT文档演模板
塑料模基本结构及零部件的设计
•4.3 模具型腔数目的确定
确定模具型腔数目时,应考虑:
1.塑件大小与设备的关系 2.充分利用现有设备 3.使塑件精度比较容易得到满足 4.不使模具结构复杂化 5.视塑件生产批量要求 6.降低模具制造费用
ProeCreo塑胶零件结构设计【自攻螺丝及相关螺柱设计】
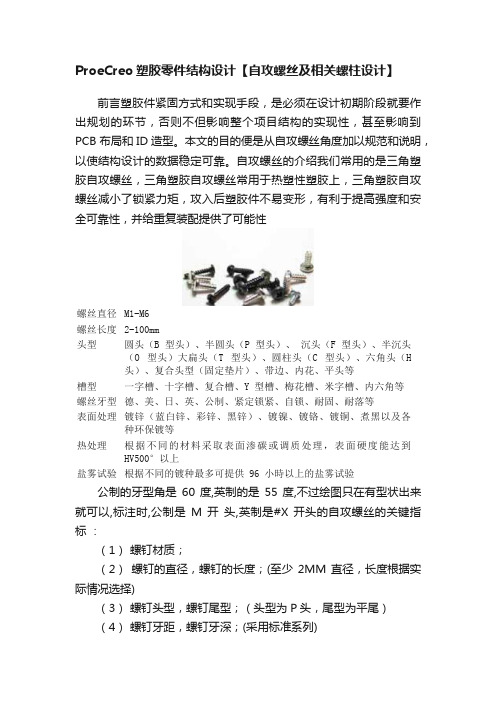
ProeCreo塑胶零件结构设计【自攻螺丝及相关螺柱设计】前言塑胶件紧固方式和实现手段,是必须在设计初期阶段就要作出规划的环节,否则不但影响整个项目结构的实现性,甚至影响到PCB 布局和 ID 造型。
本文的目的便是从自攻螺丝角度加以规范和说明,以使结构设计的数据稳定可靠。
自攻螺丝的介绍我们常用的是三角塑胶自攻螺丝,三角塑胶自攻螺丝常用于热塑性塑胶上,三角塑胶自攻螺丝减小了锁紧力矩,攻入后塑胶件不易变形,有利于提高强度和安全可靠性,并给重复装配提供了可能性螺丝直径M1-M6螺丝长度2-100mm头型圆头(B 型头)、半圆头(P 型头)、沉头(F 型头)、半沉头(O 型头)大扁头(T 型头)、圆柱头(C 型头)、六角头(H头)、复合头型(固定垫片)、带边、内花、平头等槽型一字槽、十字槽、复合槽、Y 型槽、梅花槽、米字槽、内六角等螺丝牙型德、美、日、英、公制、紧定锁紧、自锁、耐固、耐落等表面处理镀锌(蓝白锌、彩锌、黑锌)、镀镍、镀铬、镀铜、煮黑以及各种环保镀等热处理根据不同的材料采取表面渗碳或调质处理,表面硬度能达到HV500°以上盐雾试验根据不同的镀种最多可提供 96 小時以上的盐雾试验公制的牙型角是60 度,英制的是55 度,不过绘图只在有型状出来就可以,标注时,公制是M 开头,英制是#X 开头的自攻螺丝的关键指标:(1)螺钉材质;(2)螺钉的直径,螺钉的长度;(至少2MM直径,长度根据实际情况选择)(3)螺钉头型,螺钉尾型;(头型为P头,尾型为平尾)(4)螺钉牙距,螺钉牙深;(采用标准系列)(5)螺钉的头径,螺钉头的厚度,螺钉的槽型及槽深; (采用标准系列)(6)螺钉的热处理及表面处理;前期设计说明:(一)设计师应在 ID 设计输入阶段便大致选择螺钉、配用螺柱的类型与规格,以及设计摆放位置。
设计初始阶段的规避,作为设计输入评审项目之一,设计评审时将对该项内容严格把关。
(二)注意与螺钉配合的塑料件材料选用。
各种螺纹介绍演示文稿
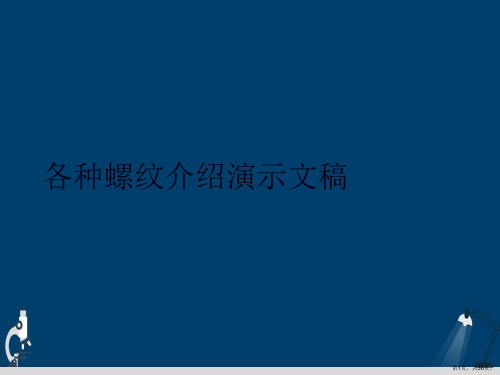
强度、硬度正常情况下相当于碳钢(6.8级)故对不锈钢 产品应不可撞击、敲打、注意维护其表面光洁度、精度, 且不能和使用碳钢产品一样随便施加力量,亦不可施力 过大,同时因不锈钢延展性好,在使用时产生钢屑易粘 于螺帽牙级处,增加摩檫力,易导致锁死,而使用碳钢 即使产生铁屑也会掉落,相对于不锈钢不易锁死。
注意:美制与英制的普通螺纹区别主要是:角度上的差异,英制螺纹为55°, 美制螺纹为60°,一般情况采用美制的螺纹;高低牙一般高牙的角度为 60°,低牙为30°
第6页,共36页。
三、螺纹配合及等级:
螺纹配合定义:螺纹配合是旋合螺纹之 间松或紧的大小,配合的等级是作用在 内外螺纹上偏差和公差的规定组合。
(一)、大径/牙外径(D、d)
定义::为外螺纹牙顶或内螺纹牙底重 合的假想圆柱直径。螺纹大径基本代表 螺纹尺寸的公称直径。
第13页,共36页。
(二)、中径(D2、d2):
定义:D2=d2=D(d)-2x3H/8 ,式中H为 原始三角形高:
H=(√3 /2)P=0.866025P(60O牙山角); H=0.960491P(55 O牙山角)
第9页,共36页。
(二)、公制螺纹,外螺纹有 三种螺纹等级:
4h、6h和6g,内螺纹有三种螺纹等级:5H、6 H、 7H。(日标螺纹精度等级分为I、II、III三级,通常 状况下为II级)在公制螺纹中,H和h的基本偏差为 零。G的基本偏差为正值,e、f和g的基本偏差为
负值。
H是内螺纹常用的公差带位置,一般不用作表面镀 层,或用极薄的磷化层。G位置基本偏差用于特殊 场合,如较厚的6h的螺栓,其镀前螺纹采用6g的 公差带。 一般电镀为3-5um可以使用6g的;6g和6h
塑料管道配件螺纹结构的设计分析
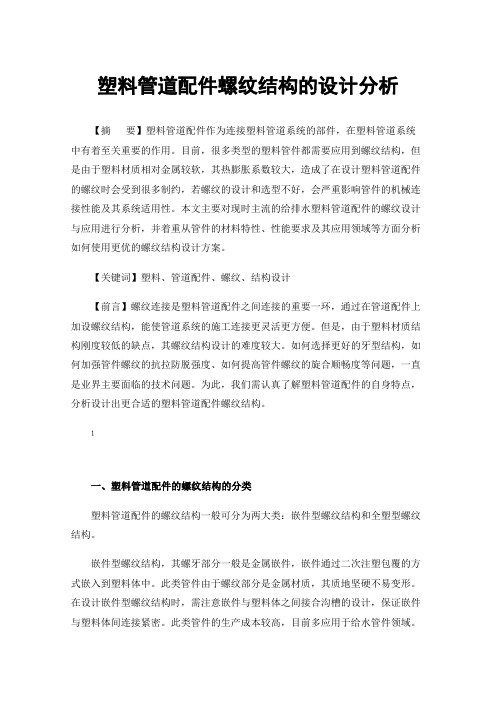
塑料管道配件螺纹结构的设计分析【摘要】塑料管道配件作为连接塑料管道系统的部件,在塑料管道系统中有着至关重要的作用。
目前,很多类型的塑料管件都需要应用到螺纹结构,但是由于塑料材质相对金属较软,其热膨胀系数较大,造成了在设计塑料管道配件的螺纹时会受到很多制约,若螺纹的设计和选型不好,会严重影响管件的机械连接性能及其系统适用性。
本文主要对现时主流的给排水塑料管道配件的螺纹设计与应用进行分析,并着重从管件的材料特性、性能要求及其应用领域等方面分析如何使用更优的螺纹结构设计方案。
【关键词】塑料、管道配件、螺纹、结构设计【前言】螺纹连接是塑料管道配件之间连接的重要一环,通过在管道配件上加设螺纹结构,能使管道系统的施工连接更灵活更方便。
但是,由于塑料材质结构刚度较低的缺点,其螺纹结构设计的难度较大。
如何选择更好的牙型结构,如何加强管件螺纹的抗拉防脱强度、如何提高管件螺纹的旋合顺畅度等问题,一直是业界主要面临的技术问题。
为此,我们需认真了解塑料管道配件的自身特点,分析设计出更合适的塑料管道配件螺纹结构。
一、塑料管道配件的螺纹结构的分类塑料管道配件的螺纹结构一般可分为两大类:嵌件型螺纹结构和全塑型螺纹结构。
嵌件型螺纹结构,其螺牙部分一般是金属嵌件,嵌件通过二次注塑包覆的方式嵌入到塑料体中。
此类管件由于螺纹部分是金属材质,其质地坚硬不易变形。
在设计嵌件型螺纹结构时,需注意嵌件与塑料体之间接合沟槽的设计,保证嵌件与塑料体间连接紧密。
此类管件的生产成本较高,目前多应用于给水管件领域。
全塑型螺纹结构,其螺牙部分与管件主体是一个或整体,螺牙部分是塑料材质。
由于塑料材质质地较软,在设计管件螺纹结构时需考虑螺牙强度、螺纹使用要求、螺纹旋合顺畅度等要点,此类管件的生产成本较低,被广泛应用于给排水塑料管件中。
二、塑料管件螺纹的设计选型塑料管件的螺纹部位按使用功能分,可分为外接型和自接型。
外接型螺纹是指其管件螺牙处需与外部管件相连接,多应用于外丝直接、内丝直接等管件;自接型螺纹是指其管件螺纹主要负责管件中各零部件间的连接,不需与外部管件相连接,多应用于活接头、清扫口接头等管件。
8塑料制品螺纹结构的设计(精)
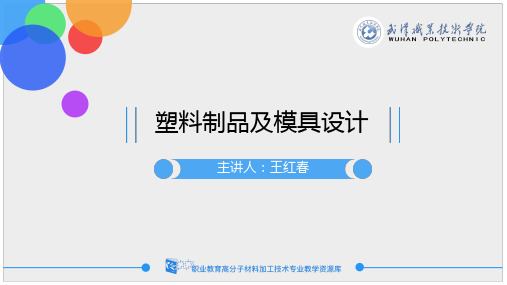
否则模具结构复杂,须采用两次脱模装置,如图2-8-2所示。
THANKS!!!
8
塑料制品螺纹结构的设计
塑料制品螺纹结构的设计要点
(1)塑料螺纹与金属螺纹的配合长度,不应大于螺纹直径的1.5倍。 (2)外螺纹与内螺纹塑件应分别设计成图2-8-1所示的结构,以便于装配并提高螺
牙强度。螺纹始末长度L由表2-8-2选取。
(3)同一塑件上前后两段螺纹,应尽可能使其螺距相等、旋向相同,以便脱模。
X
标 记 与 图 案 的 设 计
Ⅺ
支 承 面 结 构 设 计
目
塑 件 的 尺 寸 及 精 度
tttl
的 设 计
孔 结 构
录
8
塑料制品螺纹结构的设计
塑料制品螺纹结构的加工方法
(1)直接成型 采用螺纹型芯(成型内螺纹)和螺纹型环(成型外螺纹)成型, 成型后使制件与型芯(环)间相对旋转脱出制品。对外螺纹也可采用哈夫模成型。
塑料制品及模具设计 tt
主讲人:王红春
塑料制品设计原则
材料选择、成型方法、模具总体结构
结构合理、造型美观、便于制造
1
2
壁 厚 的 设 计
3
脱 模 斜 度
的 设 计
4
加 强 筋 的 设 计
5 构
的 设 计
8
螺 纹 结 构
的 设 计
9
嵌 件 结 构 的 设 计
对要求不高的软塑料成型的内螺纹,可强制脱螺纹。
(2)机械加工 对生产批量不大的塑件,采用后加工的方法加工螺纹。
(3)采用金属螺纹嵌件 该结构用于经常拆装、精度要求较高和受力较大的场合。
(4)自攻螺纹。
8
塑料制品螺纹结构的设计
塑料旋钮结构毕业设计正文

* * * * * * * * * * 装* * * * * * * * * * * * 订* * * * * * * * * * * * 线* * * * * * * * * * * *1塑件的工艺性分析1.1 制件的产品图插座产品三维结构如图1-1所示,其二维图如图1-2所示。
图1-1 插座三维示意图图1-2 插座二维图塑料旋钮结构如图1-3所示。
图1-3 旋钮三维图* * * * * * * * * * 装* * * * * * * * * * * * 订* * * * * * * * * * * * 线* * * * * * * * * * * * 1.2 尺寸及精度塑料制件的尺寸精度是指所获得的塑件与产品图中尺寸的符合程度。
影响塑件尺寸的精度很多,首先是模具的的制造精度,和模具的磨损程度,其次是塑料收缩率的波动以及成型时工艺条件的变化,塑件成型后的时效变化和模具的形状结构等。
因此,塑件的尺寸精度往往不高,应该在保证使用的前提下尽可能选用低精度等级。
根据定义图纸的要求公差为自由公差,结合塑料制件公差数值标准SJ137278,确定公差等级为4级,即一般精度标准。
1.3表面粗糙度塑件的外观要求越高,表面粗糙度应越低。
这除了在成型时从工艺上尽可能避免冷疤,云纹等疵点来保证外,主要是取决于模具型腔表面粗糙度。
一般模具表面粗糙度要比塑件的要求低1~2级。
由于此产品的外观要求不高,塑件的表面粗糙度定为Ra0.4μm。
1.4脱模斜度塑件冷却时的收缩会使它包紧住模具型芯或型腔中凸起的部分,因此为方便制件从型芯后从型腔中取出,必须设计一定的脱模斜度。
根据常用的塑件脱模斜度表查询得,型腔的脱模斜度为1°,型芯的脱模斜度为30'。
1.5塑件壁厚塑料制品应该有一定的厚度,这不仅是为了塑料制品本身在使用中有足够的强度和刚度,而且也是为了塑料在成型时有良好的流动状态。
塑件壁厚受使用要求、塑料材料性能、塑件几何尺寸以及成型工艺等众多因素的制约。
塑料螺纹等结构设计_图文_图文

塑件壁厚不均匀时,成型中各部分
所需冷却时间不同,收缩率也不同,容易造
成塑件的内应力和翘曲变形,因此设计塑件
时应尽可能减小各部分的壁厚差别,一般情
况下应使壁厚差别保持在30%以内。
对于由于塑件结构所造成的壁厚差
别过大情况,可采取如下两种方法减小壁厚
差:
(1)可将塑件过厚部分挖空,如图2-8
所示。
塑件内表面的脱模斜度应大于其外表面的 脱模斜度。
开模脱出塑件时,希望塑件留在有脱模装置 的模具一侧。要求塑件留在型芯上,则该塑件 内表面脱模斜度应比其外表面小。反之,若要 求塑件留在型腔内,则其外表面的脱模斜度应
小于其内表面的脱模斜度。 塑件上脱模斜度可以用线性尺寸、角度、比例 等三种方式来标注,如图2-7所示。 脱模斜度的推荐值可供设计塑件时参考。
图2—11 盒盖、容器等塑件采用拱形设计 返回
图2—12 大表面容器、罩壳增加刚度的设计
返回
图2—13 容器边缘采用弯边增加刚度
返回
2.4.5 塑件的支承面
当采用塑件的整个底平面作为支承面时,
应将塑件底面设计成凹形或设置加强筋,这样不
仅可提高塑件的基面效果,而且还可以延长塑件
的使用寿命,如图2-14(b)、(c)所示,支承
短。
如果不能满足要求,则需增大壁
厚或增设浇口及改变浇口位置,以满足
模塑要求。
制件最小壁厚与流程之间关系 :
返回
2.4.3 设置加强筋
塑件上增设加强筋是为了在不增加塑件
壁厚的情况下增加塑件的刚性,防止塑件变形
。
对加强筋设计的基本要求是
1)筋条方向应不妨碍脱模,筋本身应带有大 于塑件主体部分的脱模斜度,筋的设置不应使 塑件壁厚不均匀性明显增加。图2-9
塑料螺纹等结构设计
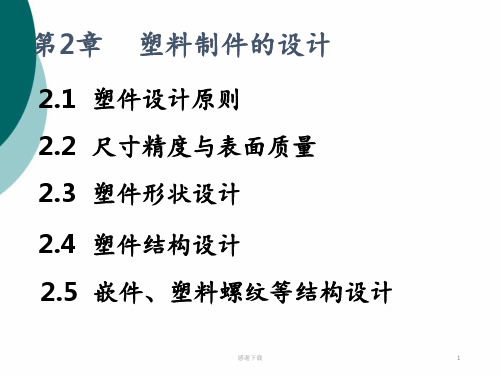
图a 2-1具有b
a图2-2塑件内b 侧
侧孔的塑件 感谢下载 表面形状改进11
2.3 形状和结构设计
图2-3、2-4的图a形式需要侧抽芯,图b形式不需侧型 芯。
ab 图2-3取消 塑件上不 必要的侧
a
b
图2-4无需
采用侧向抽芯结构成型感谢来自载的孔结构12
感谢下载
2
塑件设计原则:
⑴满足使用要求和外观要求 ⑵针对不同物理性能扬长避短 ⑶便于成型加工 ⑷尽量简化模具结构
感谢下载
3
2.2 尺寸精度与表面质量 2.2.1 尺寸精度 2.2.2 尺寸精度的确定 2.2.3 表面质量
感谢下载
4
2.2 尺寸精度与表面质量
2.2.1 尺寸精度
1、塑件尺寸概念 塑件尺寸——塑件的总体尺寸。
感谢下载
16
2.4.1 脱模斜度
• 为便于塑件从模腔中脱出,在平行于脱模方向的塑件表面上, 必须设有一定的斜度,此斜度称为脱模斜度。
• 斜度留取方向,对于塑件内表面是以小端为基准(即保证径向基 本尺寸),斜度向扩大方向取,塑件外表面则应以大端为基准(保证 径向基本尺寸),斜度向缩小方向取,如图2-6所示。
感谢下载
20
图2—7 脱模斜 度的标注
感谢下载
返回
21
2.4.2 壁厚及壁厚均匀性
在满足工作要求和工艺要求的前提下,塑件壁 厚设计应遵循如下两项基本原则:
• 尽量减小壁厚;减小壁厚不仅可以节约材料,节约 能源,也可以缩短成型周期,也有利于获得质 量较优的塑件。塑件允许的最小壁厚与塑料品 种和塑件尺寸有关。
2、塑料制品总体尺寸受限制的主要因素: *塑料的流动性 *成型设备的能力
塑料螺丝柱设计与制造

注塑中,温度升高使得塑 料外层受压应力,压力升 高使得塑料外层受到拉应 力,而外层的拉应力更容 易使塑料表层失效,故注 塑时候保压压力太大,容 易应力开裂,保压压力只 要能保证防止缩水的最小 值。
流动残余应力是熔融塑胶 料填充流动过程中的剪切 应力。如果这种剪切应力 过大或分布不均匀,会造 成尺寸变化、分子链断裂、 局部残余应力过大、制品 强度下降。
右图依次为结晶塑料、非 结晶塑料、液晶塑料的性 能对比。包括力学性能、 热性能、光学性能、耐化 学溶剂性能等对比。
聚合物分子量越大,大分 子链间作用力和缠结程度 增加,其制品抗应力开裂 能力较强;聚合物分子量 分布越宽,其中低分子量 成分越大,容易首先形成 微观撕裂,造成应力集中, 便制品开裂。选取分子量 大、分子量分布窄的树脂
塑料螺丝柱尽可能不要出 现径向的熔接痕,如右图, 否则螺柱的强度等级会有 较大降低,容易开裂。可 以通过调整注塑来改善, 但不能完全解决。
熔接痕可以通过调整注塑 来改善。
四、残余应力的影响
残余应力是指注塑件出模 后残余在制品中未松弛的 各种应力之和,通常认为 残余应力包括流动残余应 力和热残余应力。
螺钉旋入螺柱时,螺柱开 口端产生的应力是最大的, 加入一个导入凹槽,可以 减小开口端的应力,一定 程度防止开裂,同时方便 装配时候螺丝导向。
没有导入凹槽时,螺钉旋 入时候螺柱开口端产生的 应力,容易引起开裂。
螺杆结构PPT幻灯片

L
L
M
K
t
L E
eE
h E
螺杆直径 60 mm 螺杆长 1200mm 长径比 L : D 20 : 1 各段长度
齿深
压缩比
齿间距
= 60 m
Symbol
L g
e
s
= 符120号0
mm
加料段长度Einzug 压K缩om 段p长re度ssion Meterin计g量段长度
L鋘geder Zone L LE 10D E
5. 还要注意螺杆与料筒的同心度! 6. 添加剂的影响: 阻燃剂在加工过程中会分解腐蚀性气体,由于在喂料段
温度较低,易积聚气体,故易腐蚀. 螺杆磨损的表现 加料段磨损主要表现在:进料慢加料困难,预塑时间过长。 压缩段磨损主要表现在:预塑时间过长。 均化段磨损主要表现在:料往回流, 螺杆正转, 背压不稳,预塑时间过长。
8
3. 螺杆的材料及加工
1. 料筒:
2.
(1)普通料筒: 氮化钢(硬度:HV850 –950);氮化层深度0.5 – 0.7 mm
3.
(2)双金属料筒: ( a ) 镍基合金表面硬化,
4. HRC55- 62。
( b ) 表面离心铸造 40%碳化钨衬里, 深度大于2mm, 硬度
5.
使用寿命是普通料筒的4 - 5倍。
螺杆介绍 Screw Introduction
1
注射螺杆和料筒的结构:
喷嘴 法兰盘
料筒
下料口
螺杆头
止回阀环 止回阀座 螺杆
2
DH
MH 3
MH 2
MH 1
MZ
EZ = 加料区 KZ = 压缩区 MZ= 计量区
KZ
LL/D/D20:1
塑件螺纹的设计
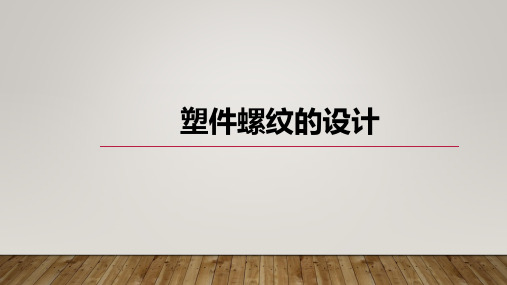
塑件螺纹的设计
塑件螺纹的设计
(1)为了使用方便和提高塑件使用寿命,则在螺纹端部有大于0.5mm
的无螺纹区。
无螺纹区
无螺ห้องสมุดไป่ตู้区
塑件螺纹的设计
(2)在同一塑件的同一部位的同轴线上有前后两段螺纹时,其螺纹的螺距 和旋转方向应一致。螺纹不等或旋转方向相反,则螺纹型芯应分别做出组 合装配,成型后分别旋出。
塑件螺纹的设计
- 1、下载文档前请自行甄别文档内容的完整性,平台不提供额外的编辑、内容补充、找答案等附加服务。
- 2、"仅部分预览"的文档,不可在线预览部分如存在完整性等问题,可反馈申请退款(可完整预览的文档不适用该条件!)。
- 3、如文档侵犯您的权益,请联系客服反馈,我们会尽快为您处理(人工客服工作时间:9:00-18:30)。
2.3 塑件形状设计
2.3.1 侧凹与侧凸
设计塑件的内外表面形状要尽量避免侧 凹结构,以避免模具采用侧向分型和侧向抽 芯机构,否则因设置这些机构而使模具结构 复杂.不但模具的制造成本提高,而且还会在 塑件上留下分型面线痕,增加了去除飞边的 后加工的困难。
塑件内表面的脱模斜度应大于其外表面的脱模斜 度。
开模脱出塑件时,希望塑件留在有脱模装置
的模具一侧。要求塑件留在型芯上,则该塑件 内表面脱模斜度应比其外表面小。反之,若要 求塑件留在型腔内,则其外表面的脱模斜度应小于其 内表面的脱模斜度。 塑件上脱模斜度可以用线性尺寸、角度、比例等三 种方式来标注,如图2-7所示。 脱模斜度的推荐值可供设计塑件时参考。
图2—7 脱模斜度的标注
返回
2.4.2 壁厚及壁厚均匀性
在满足工作要求和工艺要求的前提下,塑件壁 厚设计应遵循如下两项基本原则:
尽量减小壁厚;减小壁厚不仅可以节约材料,
节约能源,也可以缩短成型周期,也有利于获 得质量较优的塑件。塑件允许的最小壁厚与塑 料品种和塑件尺寸有关。
尽可能保持壁厚均匀。
2.2 尺寸精度与表面质量
2.2.3 表面质量
1、塑件制品的表面质量要求: ①表面粗糙度要求。
②表面光泽性、色彩均匀性要求。 ③云纹、冷疤、表面缩陷程度要求。 ④熔结痕、毛刺、拼接缝及推杆痕迹等缺陷 的要求。
2.2 尺寸精度与表面质量
2.2.3 表面质量
2、模具表面粗糙度要求
①一般,型腔表面粗糙度要求达0.20.4mm,模具表面粗糙度要比塑件的要求低 1~2级。
图2-2b避免了组合式型芯, 模具结构简单。
a
b
图2-1具有侧孔的塑件
a
b
图2-2塑件内侧表面形状改进
2.3 形状和结构设计
图2-3、2-4的图a形式需要侧抽芯,图b形式不需侧型 芯。
a
b
图2-3取消塑件上不必 要的侧凹结构
a
b
图2-4无需采用侧向抽 芯结构成型的孔结构
2.3 形状和结构设计
2.3.2 强制脱模
设计塑件时如果未注明斜度,模具设计时 必须考虑脱模斜度。模具上脱模斜度留取方向是:
型芯是以小端为基准,向扩大方向取。 型腔是以大端为基准,向缩小方向取。
这样规定斜度方向有利于型芯和型腔径向尺寸修整。斜度 大小应在塑件径向尺寸公差范围内选取。当塑件尺寸精度与 脱模斜度无关时,应尽量地选取较大的脱模斜度。当塑件尺 寸精度要求严格时,可以在其尺寸公差范围内确定较为适当 的脱模斜度。
塑料螺纹等结构设计演示文稿
第2章 塑料制件的设计
内容简介: 本章主要讲述塑件形状设计要求和设计
实例;脱模斜度的确定;塑件壁厚的设计 及壁厚均匀性;塑件的支承面、塑件上的 孔、嵌件、文字、凸凹纹的设计;塑件结 构设计示例;塑件的尺寸精度和表面粗糙 度的确定。
塑件设计原则:
⑴满足使用要求和外观要求 ⑵针对不同物理性能扬长避短 ⑶便于成型加工 ⑷尽量简化模具结构
2.2 尺寸精度与表面质量
2.2.2 尺寸精度的确定
表3—2是模塑件尺寸公差国家标准(GB/T 14486-1993),表3—3是常用塑料材料的 公差等级选用。
将表3—2和表3—3结合起来使用,先查表 3—3,根据模塑件的材料品种及用要求选定塑 件的尺寸精度等级,再从表3—2中查取塑件尺 寸公差。然后根据需要进行上、下偏差分配。 如基孔制的孔可取表中数值冠以(+)号,如基 轴制的轴可取表中数值冠以(-)号,其余情况则 根据材料特性和配合性质进行分配。
以成型侧孔和凸凹结构为例。比较两种 方案,从而选择优良的设计方案。
2.3 塑件形状设计
图2-1a所示塑件在取出模 具前,必须先由抽芯机构 抽出侧型芯,然后才能, 取出模具结构复杂。
图2-1b侧孔形式,无需侧 向型芯,模具结构简单。
图2-2a所示塑件的内侧有 凸起,需采用由侧向抽芯 机构驱动的组合式型芯, 模具制造困难。
当塑件的内外侧凹陷较浅,同时成型塑件 的塑料为聚乙烯、聚丙烯、聚甲醛这类仍带 有足够弹性的塑料时,模具可采取强制脱模。
为使强制脱模时的脱模阻力不要过大引起 塑件损坏和变形,塑件侧凹深度必须在要求 的合理范围内,见图2—5下面的说明(公式), 同时还要重视将凹凸起伏处设计为圆角或斜 面过渡结构。
2.3 塑件形状设计
2.2 尺寸精度与表面质量 2.2.1 尺寸精度 2.2.2 尺寸精度的确定 2.2.3 表面质量
2.2 尺寸精度与表面质量
2.2.1 尺寸精度
1、塑件尺寸概念 塑件尺寸——塑件的总体尺寸。
2、塑料制品总体尺寸受限制的主要因素: *塑料的流动性 *成型设备的能力
2.2 尺寸精度与表面质量
影响塑件尺寸精度的因素: 1、模具制造的精度,约为1/3。 2、成型时工艺条件的变化,约为1/3。 3、模具磨损及收缩率的波动。 具体来说,对于小尺寸制品,模具制造 误差对尺寸精度影响最大;而大尺寸制品 则收缩波动为主要。
2.4.1 脱模斜度
为便于塑件从模腔中脱出,在平行于 脱模方向的塑件表面上,必须设有一定的 斜度,此斜度称为脱模斜度。
斜度留取方向,对于塑件内表面是以小 端为基准(即保证径向基本尺寸),斜度向 扩大方向取,塑件外表面则应以大端为基 准(保证径向基本尺寸),斜度向缩小方向 取,如图2-6所示。
图2—6 塑件上斜度留取方向
图2—5 可强制脱模的浅侧凹结构
a)(A-B)×100%/B≤5% b) (A-B)×100%/C≤5%
2.4 塑件结构设计
2.4.1 脱模斜度设计 2.4.2 塑件壁厚设计 2.4.3 设置加强筋 2.4.4 增加刚性减少变形的其他措施 2.4.5 塑件支承面的设计 2.4.6 塑件圆角的设计 2.4.7 塑件孔的设计 2.4.8 采用型芯拼合复杂型孔
塑件壁厚不均匀时,成型中各部分所需
冷却时间不同,收缩率也不同,容易造成塑件
的内应力和翘曲变形,因此设计塑件时应尽可
能减小各部分的壁厚差别,一般情况下应使壁
厚差别保持在30%以内。
对于由于塑件结构所造成的壁厚差别过大 情况,可采取如下两种方法减 Nhomakorabea壁厚差: