球墨铸铁件表面缺陷
球墨铸铁件产生缺陷的原因有哪些?

球墨铸铁件产生缺陷的原因有哪些?球墨铸铁件产生缺陷的原因不单是球化处理问题,那么还有什么问题?在球墨铸铁件生产中,常见的铸件缺陷除有灰铸铁件的一般缺陷外,还有球化不良、球化衰退、夹渣、缩松、石墨漂浮、皮下气孔等。
通常,产生这些缺陷的原因不单是球化处理问题,有时还有造型制芯、熔炼浇注、配砂质量、落砂清理等许多生产工序的问题,因此必须具体分析。
以便采取相应的合理措施加以解决。
(1)球化不良特征:在铸件或试棒断面上分布有明显可见的小黑点,愈往中心愈密。
金相组织中.有聚集分布的厚片状石墨原因分析:1.原铁液硫含量过高2.铁液氧化3.残余球化剂量不足4反球化元素的干扰防止方法:1.尽量选用低硫的焦炭和新生铁。
若原铁液含硫量过高,应采用炉内、炉外脱硫或相应提高球化剂的加入量。
交界铁液一定要分离干净,灰铸铁的铁掖不应混入球墨铸铁中。
球化处理时,防止炉渣出到浇包中2.操作中严防铁液氧化3.熔制配比适当、成分稳定的中间合金,并采用合适的处理温度,注意球化处理操作。
防止铁液与合金作用过分激烈或“结死”在包底4镁球墨铸铁中。
加人少量的稀土,可中和反球化元素的干扰(2)球化衰退特征:球墨铸铁铁液,停留一定时间后,球化效果会消失原因分析: 铁液的残余镁量和残余稀土量随着时间的延长会逐渐减少,过了一定时间后。
球化剂残余量已减少到不足以保证铸件球化时,就造成球化衰退镁量和稀土量逐渐减少的原因是:1. 在铁液表面的MgS、CeS与空气中氧作用,发生下列反应:2MgS+O2=2MgO气↑+2S2CeS+ O2=2CeO气+2S烟状的MgO和CeO在空气中逸损,S返回铁液与Mg、Ce作用又生成MgS、CeS,这样循环,Mg、Ce不断损失2.镁在铁液中溶解度极小,大部分镁以微小的气泡悬浮在铁液中。
当有搅拌、回包、浇注、机械振动等情况时,镁气泡会集聚上浮,并穿出铁液表面。
遇空气燃浇而损失3.镁、稀土与氧有极大的亲和力。
铁液表面的镁和稀土要逐渐氧化、镁还有蒸发损失等防止方法:1.经球化处理的铁液应有足够的球化剂残余量2.降低原铁液硫含量,并防止铁液氧化3.球化处理后应扒净渣子4.缩短铁液经球化处理后的停留时间5.在铁液表面加覆盖熔剂,如石墨粉、木炭粉、冰晶石粉等(3)夹渣(黑渣)特征: 在铸件断面上呈现暗黑色,没有光泽,主要由琉化镁、硫化锰、氧化镁、二氧化硅、氧化铁、氢化镁等所组成,是一种非金属夹杂物,可用硫印、氧印等方法显示出来。
球墨铸铁件热节部位表面缩凹缺陷的形成机理及消除对策

球墨铸铁件热节部位表面缩凹缺陷的形成机理及消除对策一、引言球墨铸铁件是一种常用的材料,在工业生产中扮演着重要的角色。
然而,球墨铸铁件在生产过程中常常出现一些缺陷,其中表面缩凹缺陷是常见且影响较大的一种缺陷。
本文将深入探讨球墨铸铁件热节部位表面缩凹缺陷的形成机理,并提出相应的消除对策。
二、热节部位表面缩凹缺陷的形成机理2.1 温度梯度引起的收缩不均匀球墨铸铁件的热节部位由于形状复杂,存在较大的厚度差异,因此在冷却过程中,会产生温度梯度。
高温区域冷却速度较慢,低温区域冷却速度较快,导致收缩不均匀。
这种不均匀的收缩会引起表面缩凹缺陷的形成。
2.2 冷却过程中的应力集中由于球墨铸铁件热节部位的几何形状特殊,冷却时会产生内部应力,应力会集中在几何形状的弯曲处、凸缘处等地方。
这些应力会导致局部区域的收缩产生变形,从而形成表面缩凹缺陷。
三、消除热节部位表面缩凹缺陷的对策3.1 优化设计通过对球墨铸铁件热节部位的优化设计,可以减少温度梯度对冷却速度和收缩的影响。
合理调整热节部位的几何形状,避免明显的厚度差异,从而减少收缩不均匀引起的缺陷。
3.2 合理选择材料选择合适的材料也是消除缩凹缺陷的重要对策之一。
通过选择具有良好热传导性能的材料,可以减少温度梯度的产生,降低收缩不均匀的程度,从而减少表面缩凹缺陷的形成。
3.3 加强冷却控制在生产过程中,加强冷却控制可以有效减少缩凹缺陷的产生。
通过合理控制冷却速度和冷却介质的流量,可以使球墨铸铁件的热节部位均匀冷却,降低温度梯度,从而减少缺陷的形成。
3.4 应力释放处理对于已经形成缩凹缺陷的球墨铸铁件,可以通过应力释放处理来消除缺陷。
应力释放处理是指在一定温度范围内进行加热保温处理,使应力得到释放并达到平衡,从而消除缩凹缺陷。
四、结论球墨铸铁件热节部位表面缩凹缺陷的形成主要由温度梯度引起的收缩不均匀和冷却过程中的应力集中导致。
为了消除这一缺陷,可以通过优化设计、合理选择材料、加强冷却控制和应力释放处理等对策来降低温度梯度、减少应力集中,从而消除缩凹缺陷,提高球墨铸铁件的质量。
铸件常见缺陷和处理

铸件常见缺陷和处理 The pony was revised in January 2021铸件常见缺陷、修补及检验一、常见缺陷1.缺陷的分类铸件常见缺陷分为孔眼、裂纹、表面缺陷、形状及尺寸和重量不合格、成份及组织和性能不合格五大类。
(注:主要介绍铸钢件容易造成裂纹的缺陷)孔眼类缺陷孔眼类缺陷包括气孔、缩孔、缩松、渣眼、砂眼、铁豆。
1.1.1气孔:别名气眼,气泡、由气体原因造成的孔洞。
铸件气孔的特征是:一般是园形或不规则的孔眼,孔眼内表面光滑,颜色为白色或带一层旧暗色。
(如照片)气孔照片1产生的原因是:来源于气体,炉料潮湿或绣蚀、表面不干净、炉气中水蒸气等气体、炉体及浇包等修后未烘干、型腔内的气体、浇注系统不当,浇铸时卷入气体、铸型或泥芯透气性差等。
1.1.2缩孔缩孔别名缩眼,由收缩造成的孔洞。
缩孔的特征是:形状不规则,孔内粗糙不平、晶粒粗大。
产生的原因是:金属在液体及凝固期间产生收缩引起的,主要有以下几点:铸件结构设计不合理,浇铸系统不适当,冷铁的大小、数量、位置不符实际、铁水化学成份不符合要求,如含磷过高等。
浇注温度过高浇注速度过快等。
1.1.3缩松缩松别名疏松、针孔蜂窝、由收缩耐造成的小而多的孔洞。
缩松的特征是:微小而不连贯的孔,晶粒粗大、各晶粒间存在明显的网状孔眼,水压试验时渗水。
(如照片2)缩松照片2产生的原因同以上缩孔。
1.1.4渣眼渣眼别名夹渣、包渣、脏眼、铁水温度不高、浇注挡渣不当造成。
渣眼的特征是:孔眼形状不规则,不光滑、里面全部或局部充塞着渣。
(如照片3)渣眼照片3产生的原因是:铁水纯净度差、除渣不净、浇注时挡渣不好,浇注系统挡渣作用差、浇注时浇口未充满或断流。
1.1.5砂眼砂眼是夹着砂子的砂眼。
砂眼的特征是:孔眼不规则,孔眼内充塞着型砂或芯砂。
产生的原因是:合箱时型砂损坏脱落,型腔内的散砂或砂块未清除干净、型砂紧实度差、浇注时冲坏型芯、浇注系统设计不当、型芯表面涂料不好等。
球墨铸铁常见缺陷的分析与对策
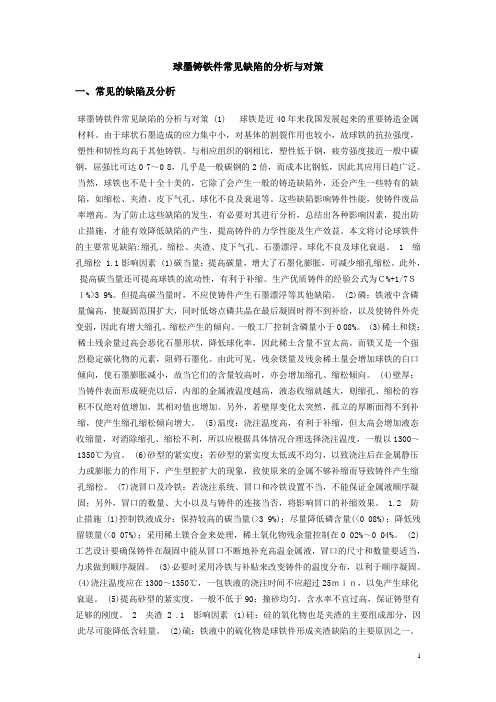
球墨铸铁件常见缺陷的分析与对策一、常见的缺陷及分析球墨铸铁件常见缺陷的分析与对策 (1) 球铁是近40年来我国发展起来的重要铸造金属材料。
由于球状石墨造成的应力集中小,对基体的割裂作用也较小,故球铁的抗拉强度,塑性和韧性均高于其他铸铁。
与相应组织的钢相比,塑性低于钢,疲劳强度接近一般中碳钢,屈强比可达0 7~0 8,几乎是一般碳钢的2倍,而成本比钢低,因此其应用日趋广泛。
当然,球铁也不是十全十美的,它除了会产生一般的铸造缺陷外,还会产生一些特有的缺陷,如缩松、夹渣、皮下气孔、球化不良及衰退等。
这些缺陷影响铸件性能,使铸件废品率增高。
为了防止这些缺陷的发生,有必要对其进行分析,总结出各种影响因素,提出防止措施,才能有效降低缺陷的产生,提高铸件的力学性能及生产效益。
本文将讨论球铁件的主要常见缺陷:缩孔、缩松、夹渣、皮下气孔、石墨漂浮、球化不良及球化衰退。
1 缩孔缩松 1.1影响因素 (1)碳当量:提高碳量,增大了石墨化膨胀,可减少缩孔缩松。
此外,提高碳当量还可提高球铁的流动性,有利于补缩。
生产优质铸件的经验公式为C%+1/7Si%>3 9%。
但提高碳当量时,不应使铸件产生石墨漂浮等其他缺陷。
(2)磷:铁液中含磷量偏高,使凝固范围扩大,同时低熔点磷共晶在最后凝固时得不到补给,以及使铸件外壳变弱,因此有增大缩孔、缩松产生的倾向。
一般工厂控制含磷量小于0 08%。
(3)稀土和镁:稀土残余量过高会恶化石墨形状,降低球化率,因此稀土含量不宜太高。
而镁又是一个强烈稳定碳化物的元素,阻碍石墨化。
由此可见,残余镁量及残余稀土量会增加球铁的白口倾向,使石墨膨胀减小,故当它们的含量较高时,亦会增加缩孔、缩松倾向。
(4)壁厚:当铸件表面形成硬壳以后,内部的金属液温度越高,液态收缩就越大,则缩孔、缩松的容积不仅绝对值增加,其相对值也增加。
另外,若壁厚变化太突然,孤立的厚断面得不到补缩,使产生缩孔缩松倾向增大。
浅析球墨铸铁件缺陷产生原因及防止措施

浅析球墨铸铁件缺陷产生原因及防止措施
1、坯料的缺陷:由于坯料的杂质含量过高,砂砾过大,沿铸缸边缘空隙较大等,都有可能导致炉内坯料缺陷大,从而产生球墨铸铁件缺陷。
2、成型工艺有问题:如砂芯型腔孔形不规则,型腔深度低,入型质量差,表面光洁度及粘结质量差等,都有可能产生球墨铸铁件缺陷。
3、浇注不合理:球墨铸铁件的浇注工艺过程中需要满足一定的条件,当不合理时,会导致溶质的不均匀分布,产生球墨铸铁件缺陷。
4、冷却不合理:冷却工艺是球墨铸铁件质量重要影响因素,冷却不合理,有可能使坯体结晶不良,从而产生球墨铸铁件缺陷。
二、防止球墨铸铁件缺陷的措施
1、提高坯料质量:在生产过程中,应加强原料检查,确保原料质量良好,并严格控制杂质含量,以减少成型过程中缺陷的发生。
2、改进成型工艺:应采用有利于消除和避免缺陷的成型工艺,如采用自动模具成型等技术,减少缺陷产生的可能性。
3、改善浇注工艺:采用有利于消除缺陷的浇注工艺,如采用连续浇铸或提高浇注压力,改善浇注品质,以减少球墨铸铁件缺陷。
4、优化冷却工艺:采用合理的冷却系统可以有效地控制坯体扩大速度,减少坯体内部残余应力,提高结晶度,以减少球墨铸铁件缺陷的产生。
三、结论
球墨铸铁件的缺陷的产生主要由坯料质量、成型工艺、浇注工艺以及冷却工艺不合理等原因引起。
因此,为防止球墨铸铁件缺陷的产生,应采取提高坯料质量、改进成型工艺、改善浇注工艺以及优化冷却工艺等措施。
只有这样,才能在生产过程中控制住缺陷,获得优良质量的球墨铸铁件。
球墨铸铁件表面缺陷

球墨铸铁件表面缺陷清华大学于震宗引言球墨铸铁件的缺陷分为表面缺陷和内在缺陷两大类,后者即有关金属材质方面的缺陷,不属于本文范围内。
本文内容重点是砂型铸件的表面缺陷,包括用湿型砂、水玻璃砂、树脂砂等砂型和砂芯生产的铸件。
砂型球墨铸件的表面缺陷有多种,本文仅选择①粘砂,②砂孔和渣孔,③夹砂,④气孔,⑤胀砂、缩孔和缩松等缺陷进行讨论。
有的缺陷如灰班虽然发生在铸件表面上,而产生原因完全属于材质方面,则不包括在本文内:一. 球墨铸件气孔缺陷气孔是最难分析其形成原因和最难找出防治方法的铸件缺陷。
这是因为气孔的形成原因很多,从外观上又不易分清气孔是属于那种类型的。
虽然采用扫描电镜和能谱等微观分析方法有助于估计气孔的产生原因,但是这些先进的技术都还处于研究阶段,大多数铸造工厂尚难在生产中利用。
根据气孔发生机理,可分为裹入、侵入、析出和反应四类气孔。
其中裹入气孔是浇注时金属液中裹带着空气泡,随着液流进入型腔中而产生的气孔缺陷。
侵入气孔是铸件表面凝固成壳以前,砂型、砂芯等造型材料受热产生的气体侵入金属液中,形成气泡而产生的气孔球铁铸件最常遇到的气孔缺陷是反应气孔和析出气孔。
以下将分别讨论:1. 析出气孔金属液中溶解的原子态氢、氮气体元素,随金属温度下降而溶解度逐渐减小。
下降至结晶温度或凝固温度时,溶解度突然变小,氢、氮以分子态气相析出形成气泡,使铸件产生气孔,称为析出气孔。
生产铸铁的工厂中,最常见的析出气孔是使用树脂砂型和砂芯造成氨氮气孔,也有来自炉料和增碳剂的氮气孔。
①氨氮酚醛树脂覆膜砂的硬化剂为乌洛托平(六亚甲基四胺(CH2)6N4)。
铸铁件用热芯盒呋喃树脂含有尿素(CO(NH2)2)。
硬化剂用含有尿素和NH4Cl的水溶液。
冷芯盒和自硬砂用酚醛脲烷树脂的聚异氰酸酯组分中含有-RNCO基团。
上述树脂砂都含有多少不等的氨或胺,都是引起析出气孔的根源。
所含氮不同于空气中的氮,大气中78%是由氮组成,并不引起析出气孔缺陷。
消失模球墨铸铁件表面皱皮(积碳)缺陷的防止

消失模球墨铸铁件表面皱皮(积碳)缺陷的防止针对我司采用消失模生产的汽车模具类球磨铸铁表面皱皮缺陷严重进行原因分析原因,并通过试验验证泡沫密度及浇注温度等因素变动对缺陷改善情况。
标签:消失模;皱皮;试验由于汽车模具具有单一、不重复的特性,因此多数采用消失模进行铸造,我公司现生产的汽车模具中第一序的拉延模等多采用QT600-3或更高牌号的材质,生产过程中铸件侧面及顶面常常会出现不同程度的皱皮,未抛丸前明显存在炭黑。
皱皮的出现严重影响铸件质量,对顶面进行加工发现炭黑深度在3~5mm,严重的甚至更深达到10mm。
特别是在铸件四个吊耳周边特别严重,部分要求严格的客户甚至要求报废模具,给公司造成极大困扰,也严重影响公司在客户心目中的形象,因此解决该问题公司迫在眉睫。
1 产生原因(1)塑料模型材料的影响:浇注过程中铁水进入砂型内,高温使EPS塑料剧烈分解,在EPS与铁液之间存在液态、气态两相,由于EPS塑料模型碳含量高达92%[1],碳含量越高,产生的液相就越多,就越容易形成炭黑包裹在铁液中。
(2)浇注温度的影响:由于EPS模型分解需要吸收热量,提高浇注温度有利于加快EPS模型分解,使PES模型和铁水间的液相变少,从而减少炭黑的产生。
(3)浇注速度的影响:提高浇注速度,减少热量损失,有利于减少炭黑的产生。
但由于提高浇注温度会增加铁液的液相收缩,同时提高浇注温度还会使型砂烧结、铸件粘砂等问题,浇注温度不能无限制的增加。
(4)冒口集、排渣系统的影响:在铸件顶部安放冒口,集、排渣系统进行收集EPS分解产生的炭黑。
(5)其他因素影响:涂料透气性[2]、真空度等由于未进行试验,这里不做赘述。
2 试验方案(1)方案一、验证浇注速度对炭黑、皱皮缺陷的影响。
通过改变直浇道、横浇道、内浇道大小,改变浇注速度[3],其他条件不变,验证浇注速度对炭黑、皱皮缺陷的影响。
设定浇注速度分别为50kg/s和100kg/s。
试验结果都次重復试验发现,浇注速度为100kg/s铸件外观质量优于浇注速度为50kg/s,但表面外观质量仅仅是好转,并不能消除表面炭黑、皱皮缺陷。
检测铸件缺陷的三大技巧

如果铸件表面存在缺陷,则涡流的电特征会发生畸变,从而检测出缺陷的存在,涡流检测的主要缺点是不能直观显示探测出的缺陷大小和形状,一般只能确定出缺陷所在表面位置和深度,另外它对工件表面上小的开口缺陷的检出灵敏度不如渗透检测。
3. 磁粉检测
磁粉检测适合于检测表面缺陷及表面以下数毫米深的缺陷,它需要直流(或交流)磁化设备和磁粉(或磁悬浮液)才能进行检测操作。磁化设备用来在铸件内外表面产生磁场,磁粉或磁悬浮液用来显示缺陷。当在铸件一定范围内产生磁场时,磁化区域内的缺陷就会产生漏磁场,当撒上磁粉或悬浮液时,磁粉被吸住,这样就可以显示出缺陷来。
1. 液体渗透检测
液体渗透检测用来检查铸件表面上的各种开口缺陷,如表面裂纹、表面针孔等肉眼难以发现的缺陷。常用的渗透检测是着色检测,它是将具有高渗透能力的有色(一般为红色)液体(渗透剂)浸湿或喷洒在铸件表面上,渗透剂渗入到开口缺陷里面,快速擦去表面渗透液层,再将易干的显示剂(也叫显像剂)喷洒到铸件表面上,待将残留在开口缺陷中的渗透剂吸出来后,显示剂就被染色,从而可以反映出缺陷的形状、大小和分布情况。
这样显示出的缺陷基本上都是横切磁力线的缺陷,对于平行于磁力线的长条型缺陷则显示不出来,为此,操作时需要不断改变磁化方向,以保证能够检查出未知方向的各个缺陷。
以上转载请注明: 谢谢!
ห้องสมุดไป่ตู้
需要指出的是,渗透检测的精确度随被检材料表面粗糙度增加而降低,即表面越光检测效果越好,磨床磨光的表面检测精确度最高,甚至可以检测出晶间裂纹。除着色检测外,荧光渗透检测也是常用的液体渗透检测方法,它需要配置紫外光灯进行照射观察,检测灵敏度比着色检测高。
2. 涡流检测
涡流检测适用于检查表面以下一般不大于6~7MM深的缺陷。涡流检测分放置式线圈法和穿过式线圈法2种。当试件被放在通有交变电流的线圈附近时,进入试件的交变磁场可在试件中感生出方向与激励磁场相垂直的、呈涡流状流动的电流(涡流),涡流会产生一与激励磁场方向相反的磁场,使线圈中的原磁场有部分减少,从而引起线圈阻抗的变化。
球墨铸铁缺陷
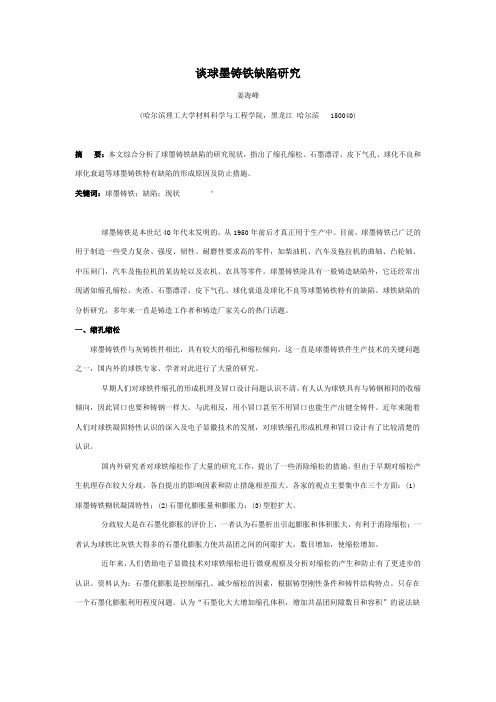
谈球墨铸铁缺陷研究姜海峰(哈尔滨理工大学材料科学与工程学院,黑龙江哈尔滨 150040)摘要:本文综合分析了球墨铸铁缺陷的研究现状,指出了缩孔缩松、石墨漂浮、皮下气孔、球化不良和球化衰退等球墨铸铁特有缺陷的形成原因及防止措施。
关键词:球墨铸铁;缺陷;现状‘球墨铸铁是本世纪4O年代末发明的,从1950年前后才真正用于生产中。
目前,球墨铸铁已广泛的用于制造一些受力复杂、强度、韧性、耐磨性要求高的零件,如柴油机、汽车及拖拉机的曲轴、凸轮轴、中压闸门,汽车及拖拉机的某齿轮以及农机、农具等零件。
球墨铸铁除具有一般铸造缺陷外,它还经常出现诸如缩孔缩松、夹渣、石墨漂浮、皮下气孔、球化衰退及球化不良等球墨铸铁特有的缺陷。
球铁缺陷的分析研究,多年来一直是铸造工作者和铸造厂家关心的热门话题。
一、缩孔缩松球墨铸铁件与灰铸铁件相比,具有较大的缩孔和缩松倾向,这一直是球墨铸铁件生产技术的关键问题之一,国内外的球铁专家、学者对此进行了大量的研究。
早期人们对球铁件缩孔的形成机理及冒口设计问题认识不清。
有人认为球铁具有与铸钢相同的收缩倾向,因此冒口也要和铸钢一样大。
与此相反,用小冒口甚至不用冒口也能生产出健全铸件。
近年来随着人们对球铁凝固特性认识的深入及电子显徽技术的发展,对球铁缩孔形成机理和冒口设计有了比较清楚的认识。
国内外研究者对球铁缩松作了大量的研究工作,提出了一些消除缩松的措施,但由于早期对缩松产生机理存在较大分歧,各自提出的影响因素和防止措施相差很大。
各家的观点主要集中在三个方面:(1)球墨铸铁糊状凝固特性;(2)石墨化膨胀量和膨胀力;(3)型腔扩大。
分歧较大是在石墨化膨胀的评价上,一者认为石墨析出引起膨胀和体积胀大,有利于消除缩松;一者认为球铁比灰铁大得多的石墨化膨胀力使共晶团之间的间隙扩大,数目增加,使缩松增加。
近年来,人们借助电子显微技术对球铁缩松进行微观观察及分析对缩松的产生和防止有了更进步的认识。
资料认为:石墨化膨胀是控制缩孔、减少缩松的因素,根据铸型刚性条件和铸件结构特点。
球墨铸铁金相组织缺陷原因及防止方法概述
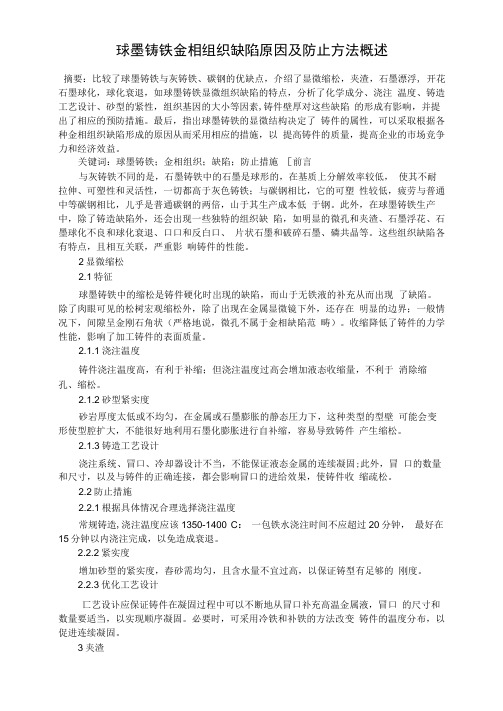
球墨铸铁金相组织缺陷原因及防止方法概述摘要:比较了球墨铸铁与灰铸铁、碳钢的优缺点,介绍了显微缩松,夹渣,石墨漂浮, 开花石墨球化,球化衰退,如球墨铸铁显微组织缺陷的特点,分析了化学成分、浇注温度、铸造工艺设计、砂型的紧性,组织基因的大小等因素,铸件壁厚对这些缺陷的形成有影响,并提出了相应的预防措施。
最后,指岀球墨铸铁的显微结构决定了铸件的属性,可以采取根据各种金相组织缺陷形成的原因从而采用相应的措施,以提高铸件的质量,提高企业的市场竞争力和经济效益。
关键词:球墨铸铁;金相组织;缺陷;防止措施[前言与灰铸铁不同的是,石墨铸铁中的石墨是球形的,在基质上分解效率较低,使其不耐拉伸、可塑性和灵活性,一切都高于灰色铸铁;与碳钢相比,它的可塑性较低,疲劳与普通中等碳钢相比,儿乎是普通碳钢的两倍,山于其生产成本低于钢。
此外,在球墨铸铁生产中,除了铸造缺陷外,还会出现一些独特的组织缺陷,如明显的微孔和夹渣、石墨浮花、石墨球化不良和球化衰退、口口和反白口、片状石墨和破碎石墨、磷共晶等。
这些组织缺陷各有特点,且相互关联,严重影响铸件的性能。
2显微缩松2.1特征球墨铸铁中的缩松是铸件硬化时岀现的缺陷,而山于无铁液的补充从而出现了缺陷。
除了肉眼可见的松树宏观缩松外,除了出现在金属显微镜下外,还存在明显的边界;一般情况下,间隙呈金刚石角状(严格地说,微孔不属于金相缺陷范畴)。
收缩降低了铸件的力学性能,影响了加工铸件的表面质量。
2.1.1浇注温度铸件浇注温度高,有利于补缩;但浇注温度过高会增加液态收缩量,不利于消除缩孔、缩松。
2.1.2砂型紧实度砂岩厚度太低或不均匀,在金属或石墨膨胀的静态圧力下,这种类型的型壁可能会变形使型腔扩大,不能很好地利用石墨化膨胀进行自补缩,容易导致铸件产生缩松。
2.1.3铸造工艺设计浇注系统、冒口、冷却器设计不当,不能保证液态金属的连续凝固;此外,冒口的数量和尺寸,以及与铸件的正确连接,都会影响冒口的进给效果,使铸件收缩疏松。
浅析球墨铸铁件缺陷产生原因及防止措施
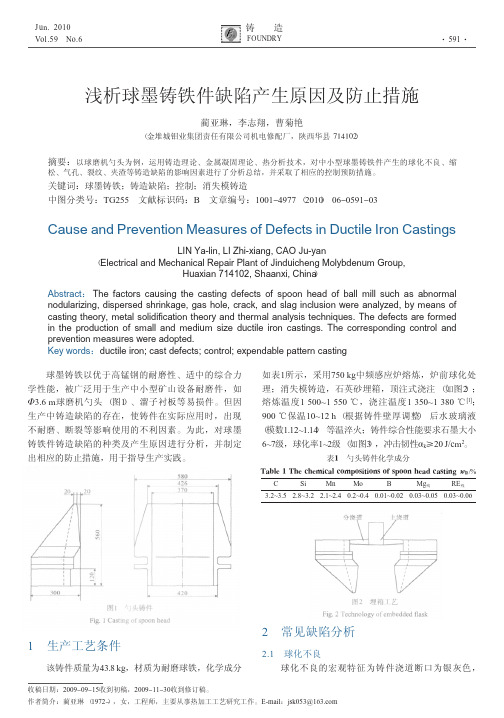
如表1所示,采用750 kg中频感应炉熔炼,炉前球化处
理;消失模铸造,石英砂埋箱,顶注式浇注 (如图2);
熔炼温度1 500~1 550 ℃,浇注温度1 350~1 380 ℃[1];
900 ℃保温10~12 h (根据铸件壁厚调整) 后水玻璃液
(模数1.12~1.14) 等温淬火;铸件综合性能要求石墨大小
金属凝固过程中的铸造应力超出铸件断面金属抗 断裂强度形成裂纹。在高温下 (1 150~1 000 ℃) 形成 热裂,呈暗褐色不平整断口;在600 ℃以下弹性范围 内出现冷裂,呈浅褐色光滑平直断口。
原因分析:球化孕育不足,白口倾向增大,促进 冷裂纹产生[3];冷却速度过快,组织应力增大都可促进 铸件沿铸孔边缘或死角处产生冷裂纹;P>0.25%时可 引起热裂纹,尤其对壁厚差别大、形状复杂的铸件。 此外,铸件在热处理过程中,加热、冷却速度过快, 可促进内缩松产生裂纹并扩张或形成断裂。 2.5 夹渣
球墨铸铁以优于高锰钢的耐磨性、适中的综合力 学性能,被广泛用于生产中小型矿山设备耐磨件,如 Φ3.6 m球磨机勺头 (图1)、溜子衬板等易损件。但因 生产中铸造缺陷的存在,使铸件在实际应用时,出现 不耐磨、断裂等影响使用的不利因素。为此,对球墨 铸铁件铸造缺陷的种类及产生原因进行分析,并制定 出相应的防止措施,用于指导生产实践。
关键词:球墨铸铁;铸造缺陷;控制;消失模铸造 中图分类号:TG255 文献标识码:B 文章编号:1001-4977 (2010) 06-0591-03
Cause and Prevention Measures of Defects in Ductile Iron Castings
LIN Ya-lin, LI Zhi-xiang, CAO Ju-yan (Electrical and Mechanical Repair Plant of Jinduicheng Molybdenum Group,
球墨铸铁件热节部位表面缩凹缺陷的形成机理及消除对策

球墨铸铁件热节部位表面缩凹缺陷的形成机理及消除
对策
球墨铸铁件经过冷却后,会形成热节部位。
在这个部位,由于冷却速度较慢,铁水凝固过程中形成的石墨距离比较远,从而造成了热节部位的结构和性能与普通部位不同。
而这种不同会导致热节部位表面缩凹缺陷的形成,具体的机理如下:
1. 热节部位在冷却时缩短,使得铸件的表面受到收缩的约束。
因此,热节表面在铸造过程中可能会出现缩凹现象。
2. 热节部位的组织结构不均匀,与普通部位相比,热节部位的强度和硬度差异较大。
因此,热节表面极易受到挤压和变形,出现缩凹现象。
针对球墨铸铁件热节部位表面缩凹缺陷问题,我们可以采取以下消除对策:
1. 通过优化铸造工艺,控制冷却速度,使得热节部位结构和性能与普通部位尽量趋于一致。
从而降低表面缩凹缺陷的发生概率。
2. 采用增加壁厚、减小热节缩孔、增加辅助冷却等措施,以减少热节部位的收缩,防止热节表面受到约束而形成缩凹现象。
3. 对球墨铸铁铸件的热节部位进行特殊处理,例如加厚和加强结构设计,以增加热节部位的强度和硬度,减少表面的挤压和变形,从而降低表面缩凹缺陷的发
生。
- 1、下载文档前请自行甄别文档内容的完整性,平台不提供额外的编辑、内容补充、找答案等附加服务。
- 2、"仅部分预览"的文档,不可在线预览部分如存在完整性等问题,可反馈申请退款(可完整预览的文档不适用该条件!)。
- 3、如文档侵犯您的权益,请联系客服反馈,我们会尽快为您处理(人工客服工作时间:9:00-18:30)。
球墨铸铁件表面缺陷清华大学于震宗引言球墨铸铁件的缺陷分为表面缺陷和内在缺陷两大类,后者即有关金属材质方面的缺陷,不属于本文范围内。
本文内容重点是砂型铸件的表面缺陷,包括用湿型砂、水玻璃砂、树脂砂等砂型和砂芯生产的铸件。
砂型球墨铸件的表面缺陷有多种,本文仅选择①粘砂,②砂孔和渣孔,③夹砂,④气孔,⑤胀砂、缩孔和缩松等缺陷进行讨论。
有的缺陷如灰班虽然发生在铸件表面上,而产生原因完全属于材质方面,则不包括在本文内:一. 球墨铸件气孔缺陷气孔是最难分析其形成原因和最难找出防治方法的铸件缺陷。
这是因为气孔的形成原因很多,从外观上又不易分清气孔是属于那种类型的。
虽然采用扫描电镜和能谱等微观分析方法有助于估计气孔的产生原因,但是这些先进的技术都还处于研究阶段,大多数铸造工厂尚难在生产中利用。
根据气孔发生机理,可分为裹入、侵入、析出和反应四类气孔。
其中裹入气孔是浇注时金属液中裹带着空气泡,随着液流进入型腔中而产生的气孔缺陷。
侵入气孔是铸件表面凝固成壳以前,砂型、砂芯等造型材料受热产生的气体侵入金属液中,形成气泡而产生的气孔球铁铸件最常遇到的气孔缺陷是反应气孔和析出气孔。
以下将分别讨论:1. 析出气孔金属液中溶解的原子态氢、氮气体元素,随金属温度下降而溶解度逐渐减小。
下降至结晶温度或凝固温度时,溶解度突然变小,氢、氮以分子态气相析出形成气泡,使铸件产生气孔,称为析出气孔。
生产铸铁的工厂中,最常见的析出气孔是使用树脂砂型和砂芯造成氨氮气孔,也有来自炉料和增碳剂的氮气孔。
①氨氮酚醛树脂覆膜砂的硬化剂为乌洛托平(六亚甲基四胺(CH2)6N4)。
铸铁件用热芯盒呋喃树脂含有尿素(CO(NH2)2)。
硬化剂用含有尿素和NH4Cl的水溶液。
冷芯盒和自硬砂用酚醛脲烷树脂的聚异氰酸酯组分中含有-RNCO基团。
上述树脂砂都含有多少不等的氨或胺,都是引起析出气孔的根源。
所含氮不同于空气中的氮,大气中78%是由氮组成,并不引起析出气孔缺陷。
区别在于上述树脂的氮是“氨氮”。
浇注时,树脂砂中粘结剂分解出NH3,在高温下NH3进一步分解出原子态的[N]和[H]。
溶解在金属液中并向内扩散。
随着金属液温度下降,溶解度也下降。
凝固时溶解度突然变小,氢和氮以分子态析出成小气泡。
两种气泡合称“氮气孔”。
由于[N]在铁水中扩散较缓慢,气孔在远处少。
除了一小部分露在铸件表面以外,大部分形成的气孔就位于表皮下面,经抛丸或初加工后显露出来,因此又称为“皮下气孔”。
大多为表面光洁的细小圆球形孔洞,孔内有石墨膜。
孔径大约只有~1mm左右,因而又常称为“针孔”。
分布较弥散,主要靠近树脂砂型和砂芯处和热节处较多。
有时也会成为枝晶间裂隙状。
大多数向铸件内延深不超过6mm。
用电炉或冲天炉熔化废钢生产铸铁件和使用增碳剂沥青焦炭或SiC,都有可能将原材料所含氮带入而形成裂隙状氮气孔。
③防止措施a)严格控制铁水中、粘结剂中和树脂砂中氮含量和降低树脂加入量。
根据工厂经验,含氮量控制数值见下表,表中上下限对应于薄壁及厚壁铸件:b) 铸铁件树脂砂中加氧化铁粉(Fe2O3)约~%。
有人认为其原理是铁水遇到Fe2O3快速放出氧,立即与从粘结剂的N分解产物反应形成稳定的NOx化合物。
也有人认为氧化铁与铁水接触后发生分解,并与碳作用生成一氧化碳。
通过一氧化碳气泡的逸出,同时带走了铁水中的氮和氢。
但会降低芯砂强度或增加树脂耗量,非万不得已,最好不用。
应从原砂质量和树脂改性上着手。
c) 在铁水中加入%的氮稳定剂Ti,或Fe-Ti合金(含钛24~28%)。
钛与氮可形成不溶于铁水的氮化物TiCN或TiN。
但会恶化切削加工性能,此法慎用。
d) 砂型和砂芯上涂刷不含氮的高温烧结型涂料,在高温下涂料能够烧结成为密实的防护壳,阻止粘结剂分解出的气体溶解入金属液。
也有时采用含氧化铁粉的专用涂料。
e) 烘烤冷芯盒和自硬砂用酚醛脲烷树脂砂芯使颜色变成巧克力棕色,粘结剂的挥发达55%。
对消除气孔有明显作用。
组分II树脂中氮成分可以继续进行反应形成稳定的化合物。
2. 反应气孔铁水与砂型、砂芯、夹杂物等之间发生化学反应生成气体,以及铁水与溶解的化合物发生化学反应生成气体,所产生的气孔称为反应气孔。
一般为直径1~3mm的小孔,分布在铸件表皮下,所以又称为皮下气孔。
球墨铸铁件的皮下气孔特征是在铸件表面以下1~3mm 处,有成串、成簇的直径1~3mm的小气孔。
孔呈球形或泪滴形,孔壁光滑发亮,覆盖着一层石墨膜。
孔洞边缘常是无石墨组织的金属层。
有的孔洞存在很小的开口,孔壁呈氧化色。
小部分孔洞表面粗糙,含有Mg、Al、Mn、Si等夹杂物。
皮下气孔的形成机理为:①冲天炉中反应冲天炉中熔炼所用铁料有锈与焦炭反应生成CO。
浇注后从铁水中分离出而成气泡。
FeO + C → CO因此冲天炉用废钢等铁料应当预先除锈。
冲天炉鼓风的空气相对湿度高时,所含水分与焦炭反应生成氢、一氧化碳和二氧化碳等气体。
随铁水带入砂型成为气孔。
H2O + C → [H], CO, CO2在潮湿地区和潮湿季节,冲天炉鼓风最好经除湿处理。
②出铁槽、处理包、浇包中反应如型砂中的水分同样,出铁槽、处理包和浇注包用搪泥修理后未烤干,含有大量水份,与铁水反应产生氢气。
Fe + H2O → FeO + 2[H]③氧化物与碳反应铁水中有大量FeO、MnO和SiO2等氧化物熔渣。
与铁水中碳反应产生CO皮下气孔。
例如SiO2+ 2C → Si + 2CO④湿砂型水份反应a)湿型砂所含水分与铁水反应和出铁槽等处水份同样与铁水反应生成[H]和FeO。
其中FeO又会与砂型所含煤粉中C 和铁水中C反应生成CO,使铸件产生[H]气孔和CO气孔。
气孔成排排列在与砂型接触表面的铸件表皮下面。
Fe + H2O → FeO + 2[H]FeO + C → Fe + COb)湿型砂的水份与铁水中铝、钛反应铝的来源为炉料和孕育剂。
与水反应放出[H]。
生成的Al2O3是气泡形核的外来核心。
2Al + 3H2O → Al2O3 + 6[H]结果使铁水层吸氢,成为富集氢的液层。
凝固时被包封在液相中的氢析出成为氢气泡核,继而氢扩散入气核使长大成为氢气泡。
灰铸铁件残留铝量应小于%。
球墨铸铁件残留铝量小于%时一般不会产生皮下气孔。
在铁水中加入过多的、含铝又高的硅铁孕育剂是铸件产生严重皮下气孔的重要原因之一。
硅铁孕育剂的含铝量最好不超过%。
钛与铝情况类似,使用含钛多的生铁时,铁水中含钛>%时气孔严重。
反应式为:Ti + 2H2O → TiO2 + 4[H]c) 湿型砂水份与球墨铸铁铁水中残留镁反应球墨铸铁的铁水浇入湿型后,残留镁同水分子中氧强烈反应而产生原子态[H],形成大量氧化物,都是[H]气泡的外来核心。
如下式所示:Mg + H2O → MgO + 2[H]在保证球化质量的前提下,铁水中残留镁量以低为好,一般应小于~%。
d) 湿型砂水份与铁水中硫化镁反应原铁水含有硫分,球化处理后成为硫化镁夹杂。
如果扒渣不干净,流入砂型中。
上浮至砂型界面的硫化镁渣与砂型水分反应生成硫化氢气体,混入铸件中而成皮下气孔缺陷。
反应式如下:MgS + H2O → MgO + H2S铁水含硫高,皮下气孔严重。
气孔周边金属组织中常有片状石墨出现。
原铁水含硫量小于%只能勉强生产球铁件。
但如生产高质量球铁件,应当对对冲天炉铁水预先进行脱硫处理,将含硫量降到%以下。
含硫超过%的电炉铁水也都最好先行脱硫处理。
为了防止湿型砂铸铁件产生气孔缺陷,还应当注意采取以下措施:a) 严格控制型砂干湿程度,造型处的型砂紧实率必须低,最好不可超过40%。
含水量也应尽可能低。
否则不但反应气孔难以避免,就连侵入气孔也会出现。
b) 湿型砂中所含煤粉不仅能防止铸件粘砂缺陷和改善铸件表面光洁程度,对防止铸铁件气孔缺陷,尤其是防止球墨铸铁件皮下气孔缺陷极为关键。
浇注时煤粉产生大量还原性气体,可以大大冲淡水汽的浓度,削弱水汽对铁水的反应。
最好使浇注出铸铁件表面呈现明显深蓝色,可代表型腔内气氛为强烈还原性,有利于防止球墨铸铁件产生皮下气孔。
c) 在球墨铸铁的湿型腔表面抖冰晶石粉(氟铝酸钠Na3AlF6)。
在高于1011℃高温下冰晶石分解产生AlF3气体能保护界面铁水层不致与水汽发生化学反应,从而防止界面铁水层吸氢。
还能夺走砂型水份,减少水与镁的反应。
可以有效地防止球墨铸铁件产生皮下气孔。
反应式如下:Na3AlF6→ 3NaF + AlF3↑2Na3AlF6 + 3H2O → Al2O3+ 6NaF + 6HF↑有的工厂不采取撒冰晶石粉,而是在砂型表面喷柴油、煤油。
喷煤油后再撒石墨粉也对防止气孔也有一定效果。
d) 浇注温度低,铁水中夹杂物多。
夹杂物也吸附大量气体,并且增多气泡外来核心。
提高浇注温度可延缓铁水表面氧化膜的生成和延长铁水凝固时间,有利于铁水中气体逸出。
研究工作表明高于1450℃时铁水表面洁净,1352~1450℃铁水表面有液态氧化物渣,低于1350℃表面出现固态熔渣。
对于一般厚壁简单铸铁件浇注温度在1360℃以上不易出现气孔。
对于复杂薄壁铸铁件(如内燃机机体、缸盖),则不能低于1380℃。
二. 铸件粘砂缺陷砂型铸件表面牢固粘连的粘砂缺陷可以分为机械粘砂和化学粘砂两种。
机械粘砂是金属液钻入砂型砂粒间孔隙造成的。
化学粘砂是砂型的SiO2与金属氧化物如FeO等产生化学反应生成硅酸亚铁(铁橄榄石)与铸件粘连在一起的。
球铁铸件的化学成分含碳高,不产生硅酸亚铁,所产生的粘砂只是机械粘砂。
1.球墨铸铁大件粘砂生产大件采用粘土干型、树脂砂型、水玻璃砂型。
浇注较大铸件通常采用锆英粉、铬铁矿粉、棕刚玉粉、镁砂粉、石墨粉等耐火骨料的优质涂料。
但涂料厂商可能为了节约生产成本,粉料中过多掺入某些价廉材料如石英粉、铝矾土粉、焦炭粉等,就会降低其防粘砂效果。
2. 湿型中、小球铁件粘砂铸铁件型砂中大多含有煤粉,浇铸时产生大量还原性气体,不会引起化学粘砂。
以下分别讨论各种因素对机械粘砂的影响。
(1)砂型紧实程度手工造型和震压造型的紧实程度一般较低,砂型表面的砂粒比较疏松,金属液钻入砂粒之间孔隙之间的可能性较大,砂型型腔的坑凹处和拐角处局部也都有可能出现疏松。
工人可以采取手指塞紧、用冲锤的尖头局部冲紧。
高生产率的高密度造型是否有局部疏松,则取决于型砂流动性如何,因而很多工厂尽量降低型砂紧实率来提高型砂的流动性。
在加砂和压实过程中采用微震是十分有效的。
此外也取决于对造型机紧实压力高低的设定。
(2)浇注温度金属液温度高,流动性好,就容易渗入砂粒间孔隙而产生机械粘砂和表面粗糙。
但从避免铸件产生气孔、冷隔等缺陷考虑,浇注温度不可任意降低。
生产复杂薄壁铸件时尤其需要较高浇注温度。
(3)型砂的粒度和透气性湿型的砂粒粗细一方面要保证浇注后排气通畅,另一方面湿型砂的透气能力又不可太高,以免金属液容易渗透入砂粒孔隙中。