超声加工技术的现状及发展趋势
超声辅助加工的研究与实践

超声辅助加工的研究与实践近年来,随着科技的不断进步和发展,超声辅助加工技术逐渐成为了新型高效加工生产技术的热点研究方向。
不仅如此,越来越多的实践证明,采用超声辅助加工技术可以大幅度提升加工效率,并且可实现对加工材料加强热和冷加工过程的控制,从而使材料的性能得以进一步优化。
超声辅助加工技术是一种创新性的加工技术。
其主要特点在于通过超声波的能量作用下,能够改变材料的物化性质,从而实现对材料进行更加精准的加工。
因此,超声辅助加工技术不仅适用于单纯的热加工,还适用于冷加工、疲劳、塑性和腐蚀等方面。
超声辅助加工技术的优势在于其加工效率高、效果好、材料损伤小,具有生产节约、资源节约等诸多优点。
这些特点意味着它在工业生产以及研究领域中都具有广泛的应用前景。
但是,超声辅助加工技术也存在一定的挑战和问题。
要想实现超声辅助加工技术的应用,关键是要深入研究超声波作用下材料的变化规律及机理。
另外,还需要针对不同的加工方案,进行适当的技术和应用上的优化,以来提高超声辅助加工技术的效率和可操作性。
目前,相关研究和开发工作正在逐步推进中。
超声辅助加工技术的具体应用包括了很多领域。
在航空领域,超声辅助加工技术被用于翼板、螺旋桨的制造中。
利用这种技术,不仅保证了加工精度和质量,而且还有效地提高了生产效率。
另外,在电子行业中,超声辅助加工技术可以被用于半导体、电子元件包装等的生产中,也被广泛应用到了制备二维材料、金属材料表面的精细处理等方面。
尽管目前超声辅助加工技术应用的范围还不是很广泛,但是在未来的发展中,它必将在工业制造领域中发挥更为突出和重要的作用。
同时,相关的学者和研究人员也应该积极地进行技术和应用的创新,来为这项技术的发展和推广提供更为有力的支持。
超声波加工技术
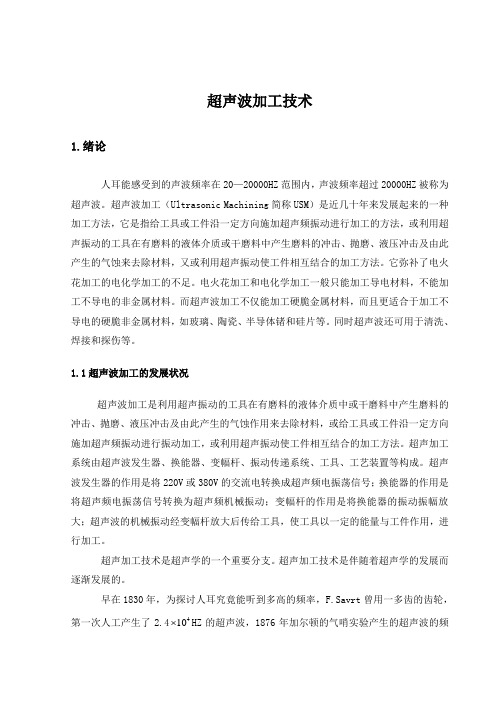
超声波加工技术1.绪论人耳能感受到的声波频率在20—20000HZ范围内,声波频率超过20000HZ被称为超声波。
超声波加工(Ultrasonic Machining简称USM)是近几十年来发展起来的一种加工方法,它是指给工具或工件沿一定方向施加超声频振动进行加工的方法,或利用超声振动的工具在有磨料的液体介质或干磨料中产生磨料的冲击、抛磨、液压冲击及由此产生的气蚀来去除材料,又或利用超声振动使工件相互结合的加工方法。
它弥补了电火花加工的电化学加工的不足。
电火花加工和电化学加工一般只能加工导电材料,不能加工不导电的非金属材料。
而超声波加工不仅能加工硬脆金属材料,而且更适合于加工不导电的硬脆非金属材料,如玻璃、陶瓷、半导体锗和硅片等。
同时超声波还可用于清洗、焊接和探伤等。
1.1超声波加工的发展状况超声波加工是利用超声振动的工具在有磨料的液体介质中或干磨料中产生磨料的冲击、抛磨、液压冲击及由此产生的气蚀作用来去除材料,或给工具或工件沿一定方向施加超声频振动进行振动加工,或利用超声振动使工件相互结合的加工方法。
超声加工系统由超声波发生器、换能器、变幅杆、振动传递系统、工具、工艺装置等构成。
超声波发生器的作用是将220V或380V的交流电转换成超声频电振荡信号;换能器的作用是将超声频电振荡信号转换为超声频机械振动;变幅杆的作用是将换能器的振动振幅放大;超声波的机械振动经变幅杆放大后传给工具,使工具以一定的能量与工件作用,进行加工。
超声加工技术是超声学的一个重要分支。
超声加工技术是伴随着超声学的发展而逐渐发展的。
早在1830年,为探讨人耳究竟能听到多高的频率,F.Savrt曾用一多齿的齿轮,第一次人工产生了2.44HZ的超声波,1876年加尔顿的气哨实验产生的超声波的频10率达到了34⨯HZ.这些实验使人们开始对超10⨯HZ,后改用氢气时,其频率达到了8410声波的性质有了一定的认识。
对超声波的诞生起重大推进作用的是1912年豪华客轮泰坦尼克号在首航中碰撞冰山后沉没,这个当时震惊世界的悲剧促使科学家提出用声学方法来探测冰山。
超声加工技术的应用及发展趋势
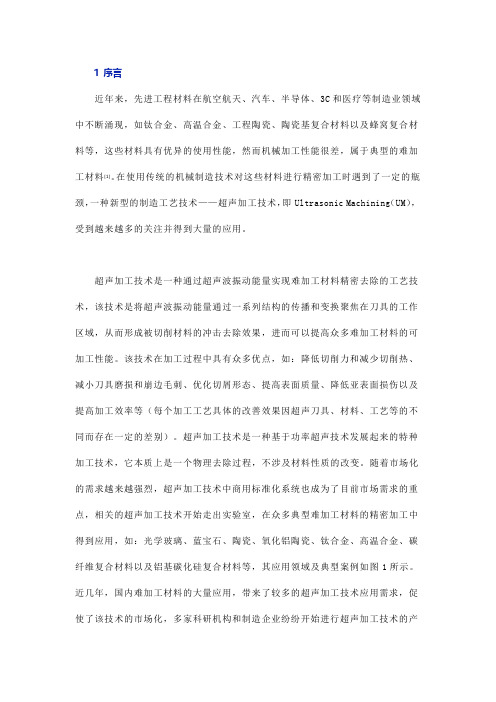
1 序言近年来,先进工程材料在航空航天、汽车、半导体、3C和医疗等制造业领域中不断涌现,如钛合金、高温合金、工程陶瓷、陶瓷基复合材料以及蜂窝复合材料等,这些材料具有优异的使用性能,然而机械加工性能很差,属于典型的难加工材料[1]。
在使用传统的机械制造技术对这些材料进行精密加工时遇到了一定的瓶颈,一种新型的制造工艺技术——超声加工技术,即Ultrasonic Machining(UM),受到越来越多的关注并得到大量的应用。
超声加工技术是一种通过超声波振动能量实现难加工材料精密去除的工艺技术,该技术是将超声波振动能量通过一系列结构的传播和变换聚焦在刀具的工作区域,从而形成被切削材料的冲击去除效果,进而可以提高众多难加工材料的可加工性能。
该技术在加工过程中具有众多优点,如:降低切削力和减少切削热、减小刀具磨损和崩边毛刺、优化切屑形态、提高表面质量、降低亚表面损伤以及提高加工效率等(每个加工工艺具体的改善效果因超声刀具、材料、工艺等的不同而存在一定的差别)。
超声加工技术是一种基于功率超声技术发展起来的特种加工技术,它本质上是一个物理去除过程,不涉及材料性质的改变。
随着市场化的需求越来越强烈,超声加工技术中商用标准化系统也成为了目前市场需求的重点,相关的超声加工技术开始走出实验室,在众多典型难加工材料的精密加工中得到应用,如:光学玻璃、蓝宝石、陶瓷、氧化铝陶瓷、钛合金、高温合金、碳纤维复合材料以及铝基碳化硅复合材料等,其应用领域及典型案例如图1所示。
近几年,国内难加工材料的大量应用,带来了较多的超声加工技术应用需求,促使了该技术的市场化,多家科研机构和制造企业纷纷开始进行超声加工技术的产业化应用。
图1超声加工应用领域及典型案例2 超声加工技术发展现状“工欲善其事,必先利其器”,超声加工技术是针对难加工材料精密加工的利器。
在大多数切削加工领域,超声加工更确切的名称应该为“超声辅助精密加工”,即在传统切削加工技术上辅助超声振动,从而实现特殊的材料去除效果。
超声波加工技术
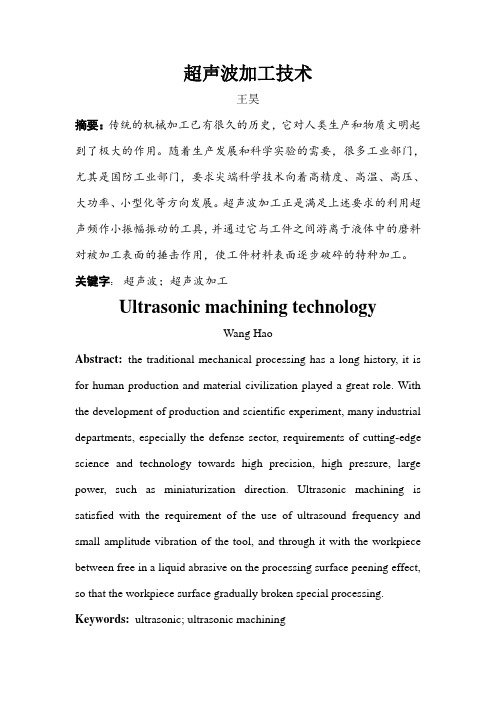
超声波加工技术王昊摘要:传统的机械加工已有很久的历史,它对人类生产和物质文明起到了极大的作用。
随着生产发展和科学实验的需要,很多工业部门,尤其是国防工业部门,要求尖端科学技术向着高精度、高温、高压、大功率、小型化等方向发展。
超声波加工正是满足上述要求的利用超声频作小振幅振动的工具,并通过它与工件之间游离于液体中的磨料对被加工表面的捶击作用,使工件材料表面逐步破碎的特种加工。
关键字:超声波;超声波加工Ultrasonic machining technologyWang HaoAbstract:the traditional mechanical processing has a long history, it is for human production and material civilization played a great role. With the development of production and scientific experiment, many industrial departments, especially the defense sector, requirements of cutting-edge science and technology towards high precision, high pressure, large power, such as miniaturization direction. Ultrasonic machining is satisfied with the requirement of the use of ultrasound frequency and small amplitude vibration of the tool, and through it with the workpiece between free in a liquid abrasive on the processing surface peening effect, so that the workpiece surface gradually broken special processing. Keywords:ultrasonic; ultrasonic machining前言超声波加工(Ultrasonic Machining, USM)有时候也称超声波加工,是特种加工的一种。
超声波加工技术在制造业中的应用及发展
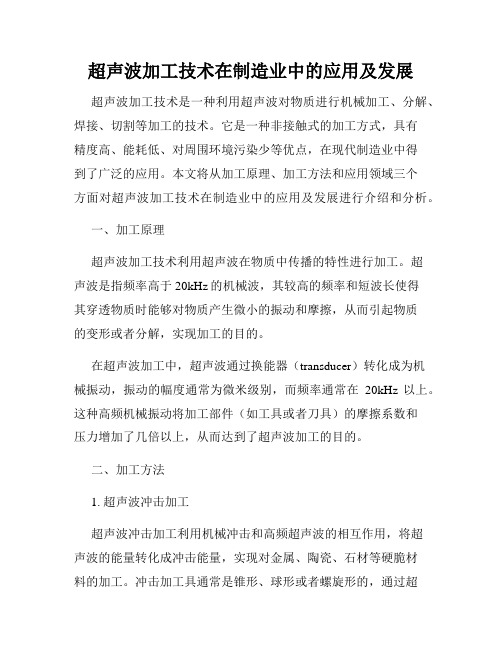
超声波加工技术在制造业中的应用及发展超声波加工技术是一种利用超声波对物质进行机械加工、分解、焊接、切割等加工的技术。
它是一种非接触式的加工方式,具有精度高、能耗低、对周围环境污染少等优点,在现代制造业中得到了广泛的应用。
本文将从加工原理、加工方法和应用领域三个方面对超声波加工技术在制造业中的应用及发展进行介绍和分析。
一、加工原理超声波加工技术利用超声波在物质中传播的特性进行加工。
超声波是指频率高于20kHz的机械波,其较高的频率和短波长使得其穿透物质时能够对物质产生微小的振动和摩擦,从而引起物质的变形或者分解,实现加工的目的。
在超声波加工中,超声波通过换能器(transducer)转化成为机械振动,振动的幅度通常为微米级别,而频率通常在20kHz以上。
这种高频机械振动将加工部件(如工具或者刀具)的摩擦系数和压力增加了几倍以上,从而达到了超声波加工的目的。
二、加工方法1. 超声波冲击加工超声波冲击加工利用机械冲击和高频超声波的相互作用,将超声波的能量转化成冲击能量,实现对金属、陶瓷、石材等硬脆材料的加工。
冲击加工具通常是锥形、球形或者螺旋形的,通过超声波的震动驱动,加工部分会发生爆炸性的形变和裂纹,从而实现加工的目的。
超声波冲击加工的优点是能够进行精细加工,但加工速度较慢,只适用于小加工量的生产。
2. 超声波切割加工超声波切割加工是利用超声波在物质中产生的高频振动,通过对切割工具施加高频振动,实现对材料的切割。
切割工具通常是金属薄板、金属丝、钻头和锯片等。
切割时,超声波的能量通过切割工具传递到材料中,使其发生振动和变形,从而实现切割的目的。
超声波切割加工的优点是能够进行高速切割,不会产生粉尘和机床磨损,但是对材料有一定的厚度限制。
3. 超声波焊接超声波焊接是利用超声波在物质中产生的高频振动,通过对金属表面施加振动,从而实现金属的焊接。
焊接时,将金属部分挤压在一起,在部件接触面上施加高频振动,使金属表面微观颗粒之间不断摩擦和碰撞,达到焊接的目的。
超声振动加工技术发展趋势
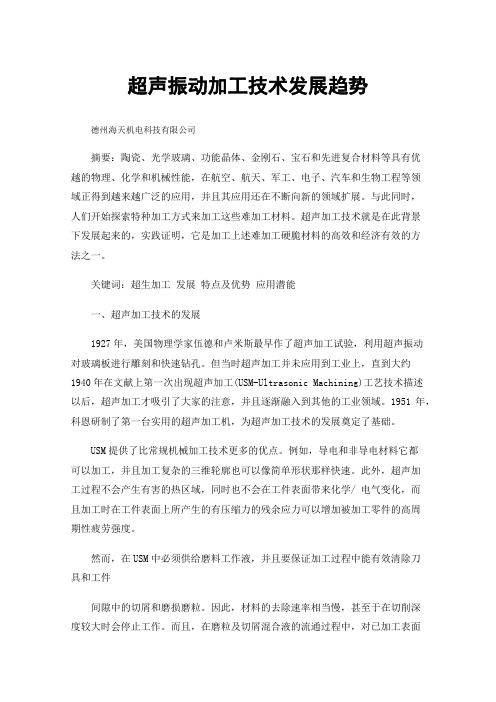
超声振动加工技术发展趋势德州海天机电科技有限公司摘要:陶瓷、光学玻璃、功能晶体、金刚石、宝石和先进复合材料等具有优越的物理、化学和机械性能,在航空、航天、军工、电子、汽车和生物工程等领域正得到越来越广泛的应用,并且其应用还在不断向新的领域扩展。
与此同时,人们开始探索特种加工方式来加工这些难加工材料。
超声加工技术就是在此背景下发展起来的,实践证明,它是加工上述难加工硬脆材料的高效和经济有效的方法之一。
关键词:超生加工发展特点及优势应用潜能一、超声加工技术的发展1927年,美国物理学家伍德和卢米斯最早作了超声加工试验,利用超声振动对玻璃板进行雕刻和快速钻孔。
但当时超声加工并未应用到工业上,直到大约1940年在文献上第一次出现超声加工(USM-Ultrasonic Machining)工艺技术描述以后,超声加工才吸引了大家的注意,并且逐渐融入到其他的工业领域。
1951年,科恩研制了第一台实用的超声加工机,为超声加工技术的发展奠定了基础。
USM提供了比常规机械加工技术更多的优点。
例如,导电和非导电材料它都可以加工,并且加工复杂的三维轮廓也可以像简单形状那样快速。
此外,超声加工过程不会产生有害的热区域,同时也不会在工件表面带来化学/ 电气变化,而且加工时在工件表面上所产生的有压缩力的残余应力可以增加被加工零件的高周期性疲劳强度。
然而,在USM中必须供给磨料工作液,并且要保证加工过程中能有效清除刀具和工件间隙中的切屑和磨损磨粒。
因此,材料的去除速率相当慢,甚至于在切削深度较大时会停止工作。
而且,在磨粒及切屑混合液的流通过程中,对已加工表面或者孔壁会造成二次磨蚀,导致工件加工精度的降低,尤其是小孔加工。
此外,磨料工作液还会磨蚀刀具本身,它将引起刀具端面及径向的大量磨损,从而很难保证加工精度。
为了克服这些问题,P. Legge提出采用固结金刚石刀具,结合工件的旋转进行孔加工的方法,形成了最初的旋转超声加工。
这种加工方法克服了普通超声加工中游离超硬磨料液在刀具和工件之间流通不畅,以及磨料对加工刀具和加工孔壁的磨蚀等问题,同时使加工精度和材料的去除率得到了显著提高。
超声加工技术的应用现状及其发展趋势
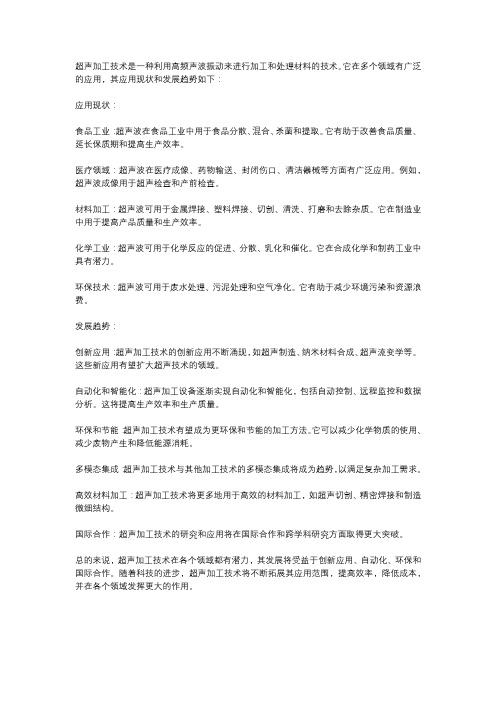
超声加工技术是一种利用高频声波振动来进行加工和处理材料的技术。
它在多个领域有广泛的应用,其应用现状和发展趋势如下:应用现状:食品工业:超声波在食品工业中用于食品分散、混合、杀菌和提取。
它有助于改善食品质量、延长保质期和提高生产效率。
医疗领域:超声波在医疗成像、药物输送、封闭伤口、清洁器械等方面有广泛应用。
例如,超声波成像用于超声检查和产前检查。
材料加工:超声波可用于金属焊接、塑料焊接、切割、清洗、打磨和去除杂质。
它在制造业中用于提高产品质量和生产效率。
化学工业:超声波可用于化学反应的促进、分散、乳化和催化。
它在合成化学和制药工业中具有潜力。
环保技术:超声波可用于废水处理、污泥处理和空气净化。
它有助于减少环境污染和资源浪费。
发展趋势:创新应用:超声加工技术的创新应用不断涌现,如超声制造、纳米材料合成、超声流变学等。
这些新应用有望扩大超声技术的领域。
自动化和智能化:超声加工设备逐渐实现自动化和智能化,包括自动控制、远程监控和数据分析。
这将提高生产效率和生产质量。
环保和节能:超声加工技术有望成为更环保和节能的加工方法。
它可以减少化学物质的使用、减少废物产生和降低能源消耗。
多模态集成:超声加工技术与其他加工技术的多模态集成将成为趋势,以满足复杂加工需求。
高效材料加工:超声加工技术将更多地用于高效的材料加工,如超声切割、精密焊接和制造微细结构。
国际合作:超声加工技术的研究和应用将在国际合作和跨学科研究方面取得更大突破。
总的来说,超声加工技术在各个领域都有潜力,其发展将受益于创新应用、自动化、环保和国际合作。
随着科技的进步,超声加工技术将不断拓展其应用范围,提高效率,降低成本,并在各个领域发挥更大的作用。
超声加工技术的现状及其发展趋势
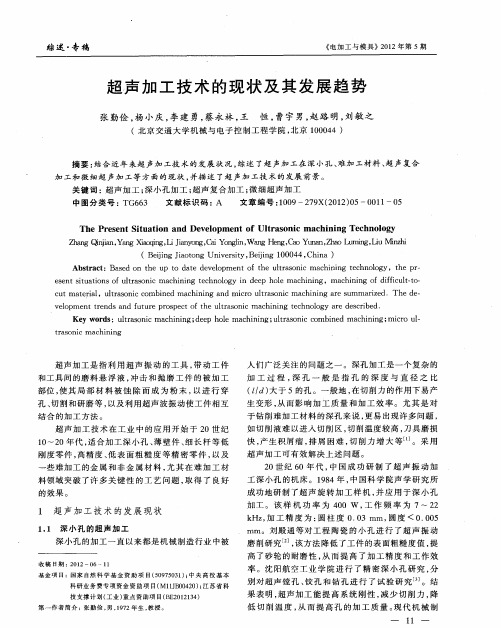
成 功地研 制 了超 声 旋转 加 工 样 机 , 应 用 于深 小 孔 并 加 工 。该 样 机 功 率 为 4 0 W , 作 频 率 为 7~ 2 0 工 2
k , 工精度 为: Hz 加 圆柱 度 0 0 .3 mm, 度 <0 0 5 圆 . 0
1 超 声加 工技 术 的发 展 现 状
合加 工研 究 , 验结 果认 为 , 实 该方 法能 有效 改善 微
粒 聚积现 象 , 于 电蚀产物 的排 出 , 而提 高加 工稳 利 从
定性 和加 工速 度 。 1 2 难 加 工 材 料 的 超 声 加 工 .
Hale Waihona Puke 随着 科学技 术 的发展 , 耐热 钢 、 合金 、 钛 不锈 钢 、
上加 工 出平 均 直径 为 1 0 b 的 通孑 , 径 比高 达 2 t m L深
2 。 朱 钰 铧 等 对 钛 合 金 深 小 孔 进 行 了 超 声 电 火 花 复 9
椭 圆) 超声 波辅 助磨 削技 术 , 工硬 而脆 的单 晶硅材 加 料¨ 。实验 证 明 , 与传 统磨 削 相 比, 最 大 的优 点 其
综述 ・ 稿 专
《 加工与 电 模具》 02 21 年第5 期
超声 加 工技 术 的现 状及 其发 展 趋 势
张 勤俭 , 小 庆 , 建 勇 , 永 林 , 杨 李 蔡 王 恒 , 曹宇 男 , 路 明 , 赵 刘敏 之
(北京交 通 大学机 械 与电子 控制工 程 学院 , 京 1 0 4 北 0 0 4)
Z a gOi i , n aq g L i y n C i ogl , n n ,a n n Z a u n UuMi h h n a YagXi i ,i a og,a Y n i Wag Heg C oYu a ,h oL mi n jn on Jn n g, n i z
超声波加工机床的发展历程与趋势分析
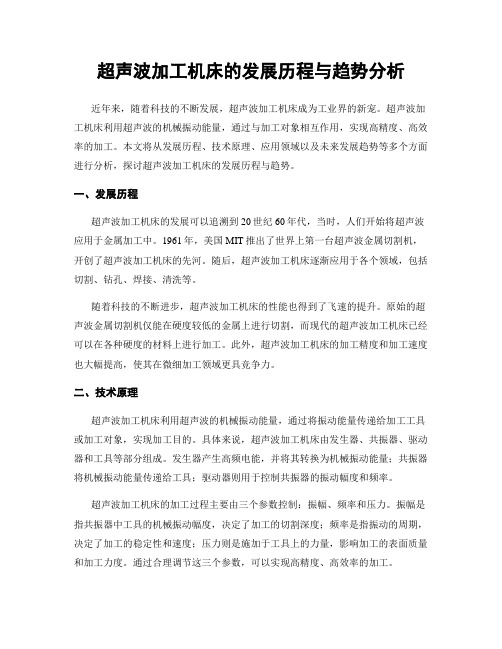
超声波加工机床的发展历程与趋势分析近年来,随着科技的不断发展,超声波加工机床成为工业界的新宠。
超声波加工机床利用超声波的机械振动能量,通过与加工对象相互作用,实现高精度、高效率的加工。
本文将从发展历程、技术原理、应用领域以及未来发展趋势等多个方面进行分析,探讨超声波加工机床的发展历程与趋势。
一、发展历程超声波加工机床的发展可以追溯到20世纪60年代,当时,人们开始将超声波应用于金属加工中。
1961年,美国MIT推出了世界上第一台超声波金属切割机,开创了超声波加工机床的先河。
随后,超声波加工机床逐渐应用于各个领域,包括切割、钻孔、焊接、清洗等。
随着科技的不断进步,超声波加工机床的性能也得到了飞速的提升。
原始的超声波金属切割机仅能在硬度较低的金属上进行切割,而现代的超声波加工机床已经可以在各种硬度的材料上进行加工。
此外,超声波加工机床的加工精度和加工速度也大幅提高,使其在微细加工领域更具竞争力。
二、技术原理超声波加工机床利用超声波的机械振动能量,通过将振动能量传递给加工工具或加工对象,实现加工目的。
具体来说,超声波加工机床由发生器、共振器、驱动器和工具等部分组成。
发生器产生高频电能,并将其转换为机械振动能量;共振器将机械振动能量传递给工具;驱动器则用于控制共振器的振动幅度和频率。
超声波加工机床的加工过程主要由三个参数控制:振幅、频率和压力。
振幅是指共振器中工具的机械振动幅度,决定了加工的切割深度;频率是指振动的周期,决定了加工的稳定性和速度;压力则是施加于工具上的力量,影响加工的表面质量和加工力度。
通过合理调节这三个参数,可以实现高精度、高效率的加工。
三、应用领域超声波加工机床广泛应用于多个领域,包括航空航天、汽车制造、电子器件、医疗器械等。
具体应用如下:1. 切割与钻孔:超声波加工机床在金属切割和钻孔领域有着广泛的应用。
由于振动频率高、能量集中,超声波切割和钻孔可以在短时间内完成工作,并且不会产生较大的机械变形。
超声辅助加工发展现状及未来趋势分析
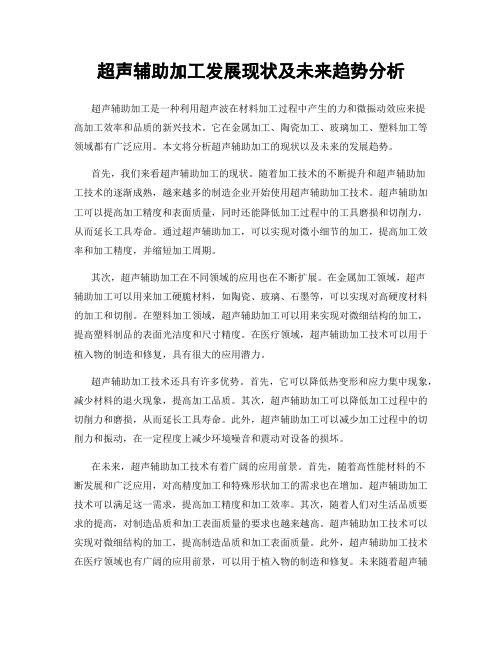
超声辅助加工发展现状及未来趋势分析超声辅助加工是一种利用超声波在材料加工过程中产生的力和微振动效应来提高加工效率和品质的新兴技术。
它在金属加工、陶瓷加工、玻璃加工、塑料加工等领域都有广泛应用。
本文将分析超声辅助加工的现状以及未来的发展趋势。
首先,我们来看超声辅助加工的现状。
随着加工技术的不断提升和超声辅助加工技术的逐渐成熟,越来越多的制造企业开始使用超声辅助加工技术。
超声辅助加工可以提高加工精度和表面质量,同时还能降低加工过程中的工具磨损和切削力,从而延长工具寿命。
通过超声辅助加工,可以实现对微小细节的加工,提高加工效率和加工精度,并缩短加工周期。
其次,超声辅助加工在不同领域的应用也在不断扩展。
在金属加工领域,超声辅助加工可以用来加工硬脆材料,如陶瓷、玻璃、石墨等,可以实现对高硬度材料的加工和切削。
在塑料加工领域,超声辅助加工可以用来实现对微细结构的加工,提高塑料制品的表面光洁度和尺寸精度。
在医疗领域,超声辅助加工技术可以用于植入物的制造和修复,具有很大的应用潜力。
超声辅助加工技术还具有许多优势。
首先,它可以降低热变形和应力集中现象,减少材料的退火现象,提高加工品质。
其次,超声辅助加工可以降低加工过程中的切削力和磨损,从而延长工具寿命。
此外,超声辅助加工可以减少加工过程中的切削力和振动,在一定程度上减少环境噪音和震动对设备的损坏。
在未来,超声辅助加工技术有着广阔的应用前景。
首先,随着高性能材料的不断发展和广泛应用,对高精度加工和特殊形状加工的需求也在增加。
超声辅助加工技术可以满足这一需求,提高加工精度和加工效率。
其次,随着人们对生活品质要求的提高,对制造品质和加工表面质量的要求也越来越高。
超声辅助加工技术可以实现对微细结构的加工,提高制造品质和加工表面质量。
此外,超声辅助加工技术在医疗领域也有广阔的应用前景,可以用于植入物的制造和修复。
未来随着超声辅助加工技术的不断发展和创新,它将能够适应各种复杂、高精度和高材料性能要求的加工需求。
超声加工的技术发展与行业应用
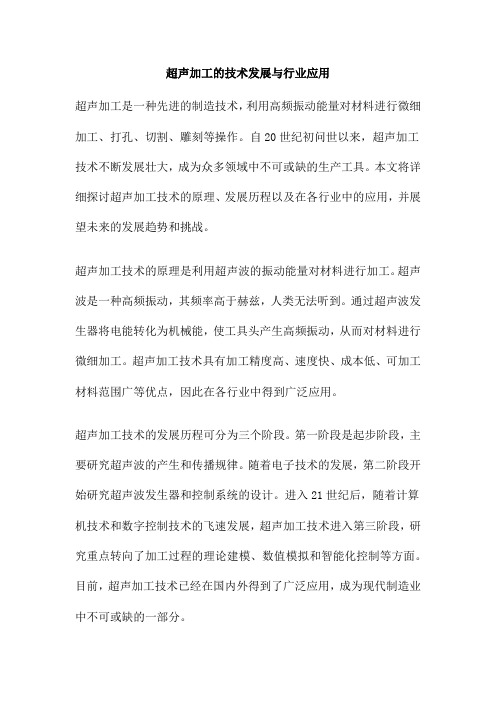
超声加工的技术发展与行业应用超声加工是一种先进的制造技术,利用高频振动能量对材料进行微细加工、打孔、切割、雕刻等操作。
自20世纪初问世以来,超声加工技术不断发展壮大,成为众多领域中不可或缺的生产工具。
本文将详细探讨超声加工技术的原理、发展历程以及在各行业中的应用,并展望未来的发展趋势和挑战。
超声加工技术的原理是利用超声波的振动能量对材料进行加工。
超声波是一种高频振动,其频率高于赫兹,人类无法听到。
通过超声波发生器将电能转化为机械能,使工具头产生高频振动,从而对材料进行微细加工。
超声加工技术具有加工精度高、速度快、成本低、可加工材料范围广等优点,因此在各行业中得到广泛应用。
超声加工技术的发展历程可分为三个阶段。
第一阶段是起步阶段,主要研究超声波的产生和传播规律。
随着电子技术的发展,第二阶段开始研究超声波发生器和控制系统的设计。
进入21世纪后,随着计算机技术和数字控制技术的飞速发展,超声加工技术进入第三阶段,研究重点转向了加工过程的理论建模、数值模拟和智能化控制等方面。
目前,超声加工技术已经在国内外得到了广泛应用,成为现代制造业中不可或缺的一部分。
超声加工技术在各行业中有广泛的应用。
在机械制造领域,超声加工技术主要用于精密零件的加工、微细孔的钻削、难加工材料的切割等。
在医疗领域,超声加工技术可用于制备药物微粒、粉碎结石、治疗肿瘤等方面。
在珠宝行业,超声加工技术可用于宝石打孔、切割、雕刻等操作。
在航空航天、电子、汽车等领域,超声加工技术也有着广泛的应用前景。
展望未来,超声加工技术将面临更多的挑战和机遇。
随着科技的不断进步,新材料的不断涌现,对超声加工技术的加工效率、精度和可靠性提出了更高的要求。
同时,智能化、自动化和数字化是超声加工技术未来的重要发展方向。
通过计算机技术和数字控制技术,实现超声加工过程的智能控制和自动化操作,提高加工效率和精度,降低成本,是未来超声加工技术的发展趋势。
随着绿色制造和环保要求的不断提高,如何实现超声加工技术的绿色、环保和可持续发展也成为未来研究的重要方向。
超声波检测技术在材料工程中的应用

超声波检测技术在材料工程中的应用近年来,随着科技的发展和工业生产技术的不断进步,超声波检测技术在材料工程中得到了广泛的应用。
超声波检测技术是一种非破坏性检测技术,简单、高效、精度高。
本文将从超声波检测技术的原理、材料工程中的应用等方面进行探讨。
一、超声波检测技术的原理超声波检测技术是指利用超声波在材料中传播的规律来检测材料中的缺陷或者其他有关特性的技术。
其原理基于超声波在材料中传播的规律,根据材料中的缺陷和不同性质的介质对超声波的吸收和散射作用,通过超声波检测设备将传播回来的波形以及波形的幅度、相位等信息进行分析和处理,得出材料中的缺陷情况或其他有关信息。
二、超声波检测技术在材料工程中的应用1. 缺陷检测超声波检测技术在材料工程中的最主要应用就是检测缺陷。
由于材料工程中的缺陷通常是微小的,难以直接观察或者使用其他检测方法进行检测。
而超声波检测技术具有非破坏性、高精度、简单易用等优点,能够精确地检测材料中的缺陷,从而有效提高材料的品质和使用性能。
2. 质量评估在材料工程中,超声波检测技术还可以用来进行质量评估。
主要是通过测量材料中的声速、声阻抗、反射等参数来评估材料的品质,例如测量声速可以反映材料的密度和弹性模量等物理特性,反映材料的质量以及加工过程中是否存在问题。
3. 无损检测超声波检测技术具有非破坏性,因此可以用于材料的无损检测。
通过利用超声波技术来检测材料表面下隐藏的缺陷或其他有关信息,而不会对材料造成任何损伤,从而实现对材料进行无损检测。
4. 材料加工过程检测对于某些复杂组件的制造,在加工过程中往往需要对其进行检测和修整。
而超声波检测技术可以在加工过程中进行实时检测,通过测定加工后材料中出现的缺陷和问题,及时对其进行修复和调整,从而大大减少了材料成本和加工时间。
三、超声波检测技术的发展趋势超声波检测技术在材料工程中的应用逐渐扩展和深入,未来的发展趋势主要包括以下方面:1. 智能化随着人工智能技术的不断发展,超声波检测技术也将逐渐实现智能化。
超声加工技术的现状及其应用
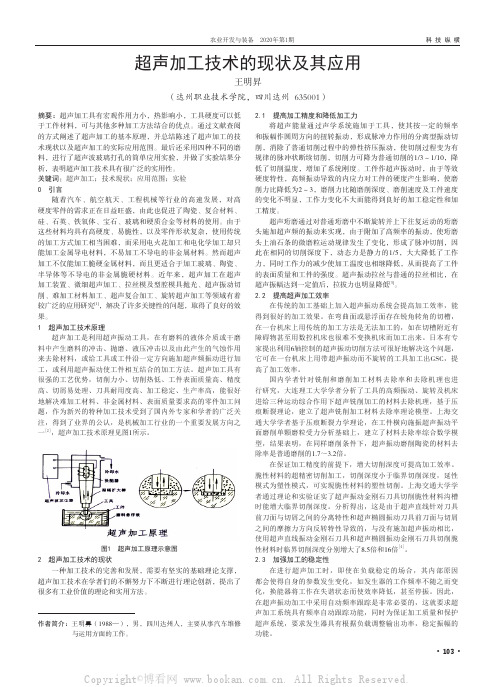
随着汽车、航空航天、工程机械等行业的高速发展,对高 硬度零件的需求正在日益旺盛,由此也促进了陶瓷、复合材料、 硅、石英、铁氧体、宝石、玻璃和硬质合金等材料的使用。由于 这些材料均具有高硬度、易脆性,以及零件形状复杂,使用传统 的加工方式加工相当困难,而采用电火花加工和电化学加工却只 能加工金属导电材料,不易加工不导电的非金属材料。然而超声 加工不仅能加工脆硬金属材料,而且更适合于加工玻璃、陶瓷、 半导体等不导电的非金属脆硬材料。近年来,超声加工在超声 加工装置、微细超声加工、拉丝模及型腔模具抛光、超声振动切 削、难加工材料加工、超声复合加工、旋转超声加工等领域有着 较广泛的应用研究[1],解决了许多关键性的问题,取得了良好的效 果。 1 超声加工技术原理
和振幅作圆周方向的扭转振动,形成脉冲力作用的分离型振动切 削,消除了普通切削过程中的弹性挤压振动,使切削过程变为有 规律的脉冲状断续切削,切削力可降为普通切削的1/3~1/10,降 低了切削温度,增加了系统刚度。工件作超声振动时,由于等效 硬度特性,高频振动导致的内应力对工件的硬度产生影响,使磨 削力比降低为2~3,磨削力比随磨削深度、磨削速度及工件速度 的变化不明显,工作力变化不大而能得到良好的加工稳定性和加 工精度。
超声加工技术的现状与发展趋势

超声加工技术的现状及发展趋势前言:超声波加工是利用超声振动工具在有磨料的液体介质中或干磨料中产生磨料的冲击、抛磨、液压冲击及由此产生的气蚀作用来去除材料,或给工具或工件沿一定方向施加超声频振动进行振动加工,或利用超声振动使工件相互结合的加工方法。
超声波加工技术是一种涉及面广且更新快的机械加工技术。
结合近年来超声加工技术的发展状况,综述了超声振动系统的研究进展和超声加工技术在深小孔加工、拉丝模及型腔模具研磨抛光、难加工材料的加工、超声振动切削、超声复合加工等方面的最新应用,并阐述了超声加工技术的发展趋势。
关键词:超声波加工、超声振动、声复合加工、应用、发展、正文:1、超声振动系统的研究进展及其应用超声振动系统由换能器、变幅杆和工具头等部分组成,是超声设备的核心部分。
在传统应用中,超声振动系统大都采用一维纵向振动方式,并按“全调谐”方式工作。
但近年来,随着超声技术基础研究的进展和在不同领域实际应用的特殊需要,对振动系统的工作方式和设计计算、振动方式及其应用研究都取得了新的进展。
日本研究成功一种半波长弯曲振动系统,其切削刀具安装在半波长换能振动系统细端,该振动系统换能器的压电陶瓷片采用半圆形,上下各两片,组成上下两个半圆形压电换能器(压电振子),其特点是小型化,结构简单,刚性增强。
日本还研制成一种新型“纵-弯”型振动系统,并已在手持式超声复合振动研磨机上成功应用。
该系统压电换能器也采用半圆形压电陶瓷片产生“纵-弯”型复合振动。
日本金泽工业学院的研究人员研制了加工硬脆材料的超声低频振动组合钻孔系统。
将金刚石中心钻的超声振动与工件的低频振动相结合,制造了一台组合振动钻孔设备,该设备能检测钻孔力的变化以及钻孔精度和孔的表面质量,并用该组合设备在不同的振动条件下进行了一系列实验。
实验结果表明,将金刚石中心钻的超声振动与工件的低频振动相结合是加工硬脆材料的一种有效方法。
另一种超声扭转振动系统已在“加工中心”用超声扭转振动装置上应用。
超声技术在材料加工中的新进展
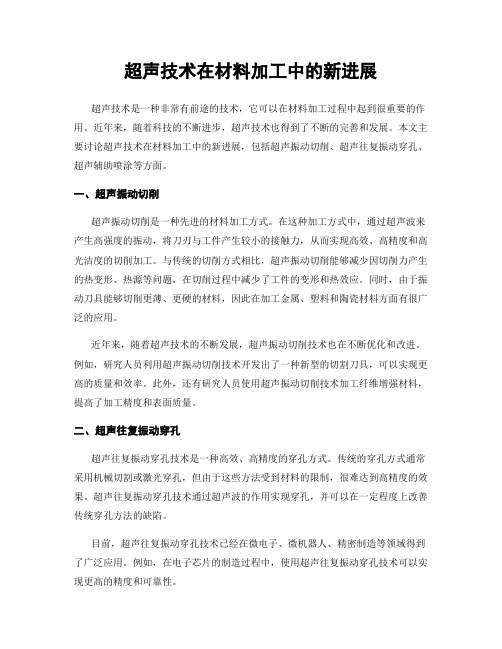
超声技术在材料加工中的新进展超声技术是一种非常有前途的技术,它可以在材料加工过程中起到很重要的作用。
近年来,随着科技的不断进步,超声技术也得到了不断的完善和发展。
本文主要讨论超声技术在材料加工中的新进展,包括超声振动切削、超声往复振动穿孔、超声辅助喷涂等方面。
一、超声振动切削超声振动切削是一种先进的材料加工方式。
在这种加工方式中,通过超声波来产生高强度的振动,将刀刃与工件产生较小的接触力,从而实现高效、高精度和高光洁度的切削加工。
与传统的切削方式相比,超声振动切削能够减少因切削力产生的热变形、热源等问题,在切削过程中减少了工件的变形和热效应。
同时,由于振动刀具能够切削更薄、更硬的材料,因此在加工金属、塑料和陶瓷材料方面有很广泛的应用。
近年来,随着超声技术的不断发展,超声振动切削技术也在不断优化和改进。
例如,研究人员利用超声振动切削技术开发出了一种新型的切割刀具,可以实现更高的质量和效率。
此外,还有研究人员使用超声振动切削技术加工纤维增强材料,提高了加工精度和表面质量。
二、超声往复振动穿孔超声往复振动穿孔技术是一种高效、高精度的穿孔方式。
传统的穿孔方式通常采用机械切割或激光穿孔,但由于这些方法受到材料的限制,很难达到高精度的效果。
超声往复振动穿孔技术通过超声波的作用实现穿孔,并可以在一定程度上改善传统穿孔方法的缺陷。
目前,超声往复振动穿孔技术已经在微电子、微机器人、精密制造等领域得到了广泛应用。
例如,在电子芯片的制造过程中,使用超声往复振动穿孔技术可以实现更高的精度和可靠性。
三、超声辅助喷涂超声辅助喷涂技术是一种新兴的涂层技术。
该技术通过超声波的高频振动使涂料微粒受到激励,形成颗粒的聚合体,从而形成更加均匀和致密的涂膜。
与传统的涂层方式相比,超声辅助喷涂技术可以提高涂层的质量和成形率,并且节省材料成本。
近年来,该技术已经在汽车制造、建筑物防水材料、涂料喷涂等领域得到了广泛的应用。
总体来看,超声技术在材料加工中的新进展主要集中在超声振动切削、超声往复振动穿孔和超声辅助喷涂等方面。
超声波加工技术的发展和应用
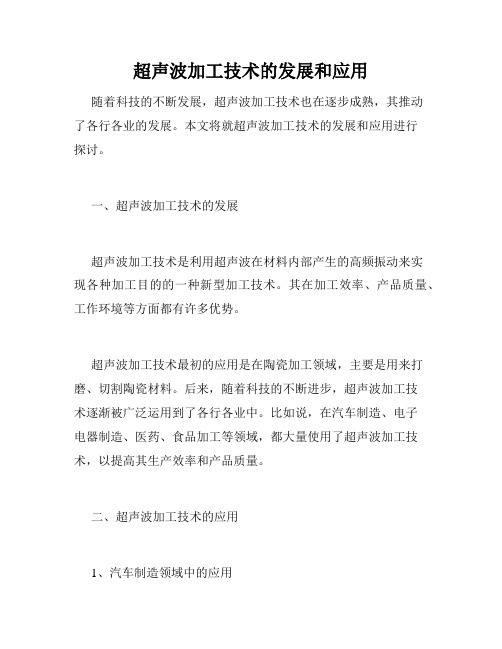
超声波加工技术的发展和应用随着科技的不断发展,超声波加工技术也在逐步成熟,其推动了各行各业的发展。
本文将就超声波加工技术的发展和应用进行探讨。
一、超声波加工技术的发展超声波加工技术是利用超声波在材料内部产生的高频振动来实现各种加工目的的一种新型加工技术。
其在加工效率、产品质量、工作环境等方面都有许多优势。
超声波加工技术最初的应用是在陶瓷加工领域,主要是用来打磨、切割陶瓷材料。
后来,随着科技的不断进步,超声波加工技术逐渐被广泛运用到了各行各业中。
比如说,在汽车制造、电子电器制造、医药、食品加工等领域,都大量使用了超声波加工技术,以提高其生产效率和产品质量。
二、超声波加工技术的应用1、汽车制造领域中的应用超声波在汽车制造领域中的应用非常广泛。
比如,在汽车零件的制造中,超声波清洗机被广泛应用。
超声波清洗机不仅可以彻底清洗零件上的污渍和油垢,还可以达到很高的清洗效率。
同时超声波加工技术还被应用于汽车轮毂的表面清理,有效地避免了零件表面出现毛刺和堆积,提高了产品质量。
2、电子电器制造领域中的应用在电子电器制造领域中,超声波加工技术同样发挥了重要作用。
比如,在印刷电路板的制造中,超声波点焊机可以达到比传统点焊更高的焊接质量。
此外,超声波剪切机还可以用于电子元件的切割、拼接等工作。
这些设备的使用大幅提高了电子电器产品的质量和生产效率。
3、医药领域中的应用超声波加工技术在医药领域中也被广泛运用。
比如,在药物的制备中,超声波技术可以被用来加速药物分散、合成和浸提等过程。
此外,超声波在医疗器械的清洗过程中也发挥了重要作用。
超声波清洗机可以对手术器械等医疗器械进行高效清洗,保障患者的生命安全和健康。
4、食品加工领域中的应用在食品加工领域中,超声波加工技术不仅可以提高加工效率,还可以提高产品的质量。
比如,在食品中添加少量的超声波可以加速食品的固化过程,改善食品的口感。
同时,超声波清洗机也可以保证食品加工的卫生安全。
三、结语综上所述,超声波加工技术的应用极为广泛,其在加工效率、产品质量和工作环境等方面都有很大的优势。
2024年超声波市场发展现状

2024年超声波市场发展现状简介超声波技术是一种利用高频声波在物体中传播和反射的原理来进行测量、检测和成像的技术。
这种技术在医疗、工业、安防等领域有着广泛的应用。
本文将介绍超声波市场的发展现状。
市场规模超声波市场规模庞大,且呈现稳定增长态势。
根据市场研究机构的数据显示,2019年全球超声波市场规模达到100亿美元,并预计在2025年时将达到150亿美元。
市场规模的增长主要得益于其在医疗和工业领域的广泛应用,并且随着技术不断进步和创新,超声波市场的发展潜力巨大。
医疗领域超声波技术在医疗领域是最为广泛应用的领域之一。
其在危急诊断、手术导航、病理学研究等方面都有着重要作用。
尤其是在超声影像学领域,超声波成像技术在医学诊断中起到了重要的辅助作用。
随着医疗技术的不断发展,超声波成像技术的分辨率和灵敏度也在不断提高,进一步推动了超声波市场的发展。
工业领域在工业领域,超声波技术主要应用于无损检测和清洗工艺。
无损检测是指利用超声波在材料中传播和反射的特性来检测材料的缺陷和损伤。
这种技术被广泛应用于航空航天、汽车制造、电力设备等领域。
另外,超声波清洗技术是一种高效、环保的清洗方法,可以去除工件表面的污垢和油脂,提高工件的质量和效率。
安防领域超声波技术在安防领域也有着重要的应用。
超声波传感器可以用来检测和测量物体的距离、速度和方向,被广泛用于入侵报警、智能门禁、智能家居等领域。
超声波无线通信技术是一种安防领域的新兴技术,可以实现无线数据传输和位置跟踪,大大提高了安防设备的性能和可靠性。
发展趋势超声波技术在各个领域的应用前景广阔,并且随着技术的不断进步和创新,其市场潜力将进一步释放。
未来,超声波市场的发展可能会出现以下几个趋势:1.精细化:超声波技术将不断提高图像的分辨率和清晰度,实现更加精准的检测和成像。
2.多功能化:超声波设备将集成更多的功能和应用,满足多样化需求。
3.联网化:超声波设备将与互联网和物联网技术结合,实现远程监测和控制。
超声加工技术的应用及其发展趋势
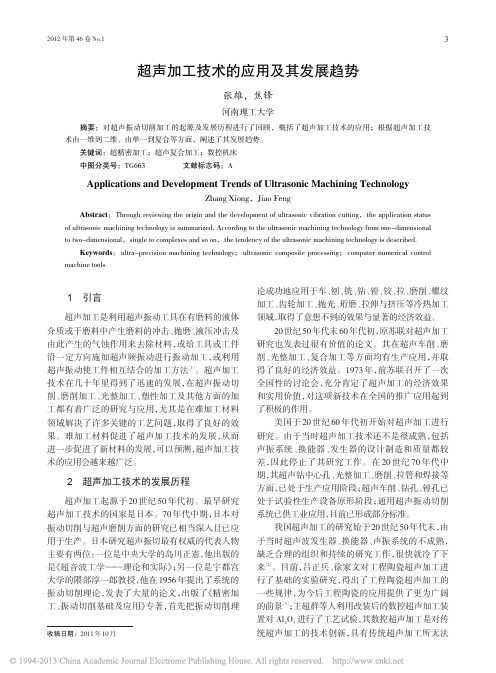
1引言超声加工是利用超声振动工具在有磨料的液体介质或干磨料中产生磨料的冲击、抛磨、液压冲击及由此产生的气蚀作用来去除材料,或给工具或工件沿一定方向施加超声频振动进行振动加工,或利用超声振动使工件相互结合的加工方法[1]。
超声加工技术在几十年里得到了迅速的发展,在超声振动切削、磨削加工、光整加工、塑性加工及其他方面的加工都有着广泛的研究与应用,尤其是在难加工材料领域解决了许多关键的工艺问题,取得了良好的效果。
难加工材料促进了超声加工技术的发展,从而进一步促进了新材料的发展,可以预测,超声加工技术的应用会越来越广泛。
2超声加工技术的发展历程超声加工起源于20世纪50年代初。
最早研究超声加工技术的国家是日本。
70年代中期,日本对振动切削与超声磨削方面的研究已相当深入且已应用于生产。
日本研究超声振切最有权威的代表人物主要有两位:一位是中央大学的岛川正憲,他出版的是《超音波工学——理论和实际》;另一位是宇都宫大学的隈部淳一郎教授,他在1956年提出了系统的振动切削理论,发表了大量的论文,出版了《精密加工、振动切削基础及应用》专著,首先把振动切削理论成功地应用于车、刨、铣、钻、镗、铰、拉、磨削、螺纹加工、齿轮加工、抛光、珩磨、拉伸与挤压等冷热加工领域,取得了意想不到的效果与显著的经济效益。
20世纪50年代末60年代初,原苏联对超声加工研究也发表过很有价值的论文。
其在超声车削、磨削、光整加工、复合加工等方面均有生产应用,并取得了良好的经济效益。
1973年,前苏联召开了一次全国性的讨论会,充分肯定了超声加工的经济效果和实用价值,对这项新技术在全国的推广应用起到了积极的作用。
美国于20世纪60年代初开始对超声加工进行研究。
由于当时超声加工技术还不是很成熟,包括声振系统、换能器、发生器的设计制造和质量都较差,因此停止了其研究工作。
在20世纪70年代中期,其超声钻中心孔、光整加工、磨削、拉管和焊接等方面,已处于生产应用阶段;超声车削、钻孔、镗孔已处于试验性生产设备原形阶段;通用超声振动切削系统已供工业应用,目前已形成部分标准。
- 1、下载文档前请自行甄别文档内容的完整性,平台不提供额外的编辑、内容补充、找答案等附加服务。
- 2、"仅部分预览"的文档,不可在线预览部分如存在完整性等问题,可反馈申请退款(可完整预览的文档不适用该条件!)。
- 3、如文档侵犯您的权益,请联系客服反馈,我们会尽快为您处理(人工客服工作时间:9:00-18:30)。
超声加工技术的现状及发展趋势
前言:超声波加工是利用超声振动工具在有磨料的液体介质中或干磨料中产生磨料的冲击、抛磨、液压冲击及由此产生的气蚀作用来去除材料,或给工具或工件沿一定方向施加超声频振动进行振动加工,或利用超声振动使工件相互结合的加工方法。
超声波加工技术是一种涉及面广且更新快的机械加工技术。
结合近年来超声加工技术的发展状况,综述了超声振动系统的研究进展和超声加工技术在深小孔加工、拉丝模及型腔模具研磨抛光、难加工材料的加工、超声振动切削、超声复合加工等方面的最新应用,并阐述了超声加工技术的发展趋势。
关键词:超声波加工、超声振动、声复合加工、应用、发展、正文:
1、超声振动系统的研究进展及其应用
超声振动系统由换能器、变幅杆和工具头等部分组成,是超声设备的核心部分。
在传统应用中,超声振动系统大都采用一维纵向振动方式,并按“全调谐”方式工作。
但近年来,随着超声技术基础研究的进展和在不同领域实际应用的特殊需要,对振动系统的工作方式和设计计算、振动方式及其应用研究都取得了新的进展。
日本研究成功一种半波长弯曲振动系统,其切削刀具安装在半波长换能振动系统细端,该振动系统换能器的压电陶瓷片采用半圆形,上下各两片,组成上下两个半圆形压电换能器(压电振子),其特点是小型化,结构简单,刚性增强。
日本还研制成一种新型“纵-弯”型
振动系统,并已在手持式超声复合振动研磨机上成功应用。
该系统压电换能器也采用半圆形压电陶瓷片产生“纵-弯”型复合振动。
日本金泽工业学院的研究人员研制了加工硬脆材料的超声低频振动组合钻孔系统。
将金刚石中心钻的超声振动与工件的低频振动相结合,制造了一台组合振动钻孔设备,该设备能检测钻孔力的变化以及钻孔精度和孔的表面质量,并用该组合设备在不同的振动条件下进行了一系列实验。
实验结果表明,将金刚石中心钻的超声振动与工件的低频振动相结合是加工硬脆材料的一种有效方法。
东南大学研制了一种新型超声振动切削系统。
该系统采用压电换能器,由超声波发生器、匹配电路、级联压电晶体、谐振刀杆、支承调节机构及刀具等部分组成。
当发生器输出超声电压时,它将使级联晶体产生超声机械伸缩,直接驱动谐振刀杆实现超声振动。
该装置的特点是:能量传递环节少,能量泄漏减小,机电转换效率高达90%左右,而且结构简单、体积小,便于操作。
沈阳航空工业学院建立了镗孔用超声扭转振动系统,采用磁致伸缩换能器,将超声波发生器在扭转变幅杆的切向作纵向振动时在扭振变幅杆的小端就输出沿圆周方向的扭转振动,镗刀与扭振变幅杆之间采用莫氏锥及螺纹连接,输出功率小于500W,频率为16~23 KH z,具有频率自动跟踪性能。
西北工业大学设计了一种可在内圆磨床上加工硬脆材料的超声振动磨削装置。
该装置由超声振动系统、冷却循环系统、磨床连接系统和超声波发生器等组成,其超声换能器采用纵向复合式换能器结构,冷却循环系统中使用磨削液作为冷却液;磨床连接系统由辅助支承、制动机
构和内圆磨床连接杆等组成。
该磨削装置工具头旋转精度由内圆磨床主轴精度保证,结构比专用超声波磨床的主轴系统要简单得多,因此成本低廉,适合于在生产中应用。
另一种超声扭转振动系统已在“加工中心”用超声扭转振动装置上应用。
主要用作电火花加工后的模具异形(如三角形、多边形)孔和槽底部尖角研磨抛光,以及非导电材料异形孔加工。
该振动系统的换能器采用按圆周方向极化的8块扇形压电陶瓷片构成,产生扭转振动。
2、超声加工技术应用研究
2.1 深小孔加工
众所周知,在相同的要求及加工条件下,加工孔比加工轴要复杂得多。
一般来说,孔加工工具的长度总是大于孔的直径,在切削力的作用下易产生变形,从而影响加工质量和加工效率。
特别是对难加工材料的深孔钻削来说,会出现很多问题。
例如,切削液很难进入切削区,造成切削温度高;刀刃磨损快,产生积屑瘤,使排屑困难,切削力增大等。
其结果是加工效率、精度降低,表面粗糙度值增加,工具寿命短。
采用超声加工则可有效解决上述问题。
前苏联在20世纪60年代就生产出带磨料的超声波钻孔机床。
英国申请了电火花超声复合穿孔的专利,该装置主要用于加工在导电基上有非导电层的零件,如在金属基上涂有压电陶瓷层的零件。
整个加工过程分两个阶段进行:首先用超声振动将非导电层去除掉,当传感器感知金属层出现时,即改用电加工或电火花与超声复合的方法进行加。