QC工作流程-产品首件确认作业流程
IPQC工作流程
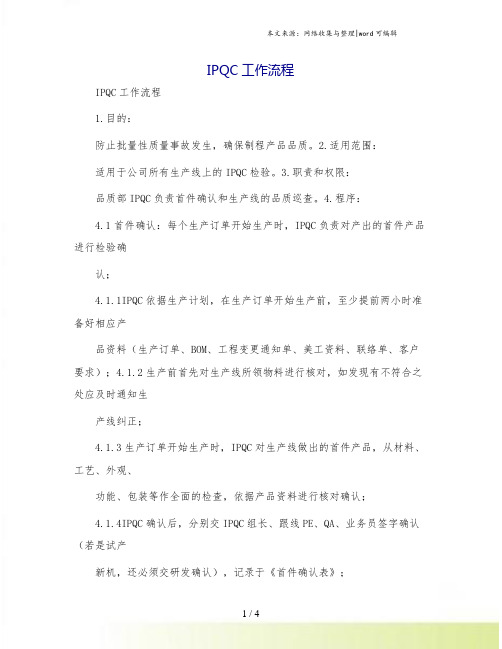
IPQC工作流程IPQC工作流程1.目的:防止批量性质量事故发生,确保制程产品品质。
2.适用范围:适用于公司所有生产线上的IPQC检验。
3.职责和权限:品质部IPQC负责首件确认和生产线的品质巡查。
4.程序:4.1首件确认:每个生产订单开始生产时,IPQC负责对产出的首件产品进行检验确认;4.1.1IPQC依据生产计划,在生产订单开始生产前,至少提前两小时准备好相应产品资料(生产订单、BOM、工程变更通知单、美工资料、联络单、客户要求);4.1.2生产前首先对生产线所领物料进行核对,如发现有不符合之处应及时通知生产线纠正;4.1.3生产订单开始生产时,IPQC对生产线做出的首件产品,从材料、工艺、外观、功能、包装等作全面的检查,依据产品资料进行核对确认;4.1.4IPQC确认后,分别交IPQC组长、跟线PE、QA、业务员签字确认(若是试产新机,还必须交研发确认),记录于《首件确认表》;4.1.5首件确认必须在生产线做出首件产品后半小时之内完成;4.1.6首件确认合格方可进行批量生产;首件确认不合格由IPQC立即通知相关责任部门整改,由IPQC负责跟进,改善后再由IPQC负责确认。
4.2生产线的巡查:4.2.1量产后时IPQC依据产品资料和检查表对生产线进行巡查(内容包括生产工艺、物料、员工操作、品质状况、仪器工具状况等),如有不符合之处应立即通知线长或跟线PE纠正,结果记录于《IPQC巡检日报表》;4.2.2IPQC对生产线物料的更换要及时跟进检查,各工位人员的变动时要及时跟其作业品质;4.2.3IPQC随时了解各QC位和修理位品质状况,并对一些有代表性的问题进行追踪或向生产线线长、跟线PE反映,分析原因并记录于《IPQC巡检日报表》;4.2.4品质有异常时,IPQC应及时报告上级主管和车间主任或厂长处理,并填写《品异常联络书》发至责任部门整改,由IPQC负责跟进和改善后的验证。
4.3IPQC每天下班前对当天发生的主要品质问题进行总结,对未解决的问题继续保持跟进。
IPQC的工作流程及检验流程

IPQC工作流程IPQC(In Process Quality Control)中文意思为制程控制,是指产品从物料投入生产到产品最终包装过程的品质控制。
(属品质保证部)1.负责首检和部分过程检查、制程中不良品的确认,标识及统计;2.负责巡检,对整个生产过程物料使用、装配操作、机器运行、环境符合性等全方位的定时检查确认。
IPQC工作流程简单的说:工作内容包括:首件检查、各类变更文件的跟踪。
4M1E的巡查。
发现异常的提出、跟踪与验证。
详细的说:过程检验(IPQC,in process quality contrl):目的是为了防止出现大批不合格品,避免不合格品流入下道工序去继续进行加工。
因此,过程检验不仅要检验产品,还要检定影响产品质量的主要工序要素(如 4MIE)。
实际上,在正常生产成熟产品的过程中,任何质量问题都可以归结为4M1E中的一个或多个要素出现变异导致,因此,过程检验可起到两种作用:1. 根据检测结果对产品做出判走,即产品质量是否符合规格和标准的要求;2. 根据检测结果对工序做出判定,即过程各个要素是否处于正常的稳定状态,从而决定工序是否应该继续进行生产。
为了达到这一目的,过程检验中常常与使用控制图相结合。
过程检验通常有三种形式:(1)首件检验:首件检验也称为“首检制”,长期实践经验证明,首检制是一项尽早发现问题、防止产品成批报废的有效措施。
通过首件检验,可以发现诸如工夹具严重磨损或安装定位错误、测量仪器精度变差、看错图纸、投料或配方错误等系统性原因存在,从而采取纠正或改进措施,以防止批次性不合格品发生。
通常在下列情况下应该进行首件检验:一,一批产品开始投产时;二,设备重新调整或工艺有重大变化时;三,轮班或操作工人变化时;四,毛坯种类或材料发生变化时。
首件检验一般采用“三检制”的办法,即操作工人实行自检,班组长或质量员进行复检,检验员进行专检。
首件检验后是否合格,最后应得到专职检验人员的认可,检验员对检验合格的首件产品,应打上规定的标记,并保持到本班或一批产品加工完了为止。
OQC作业流程图
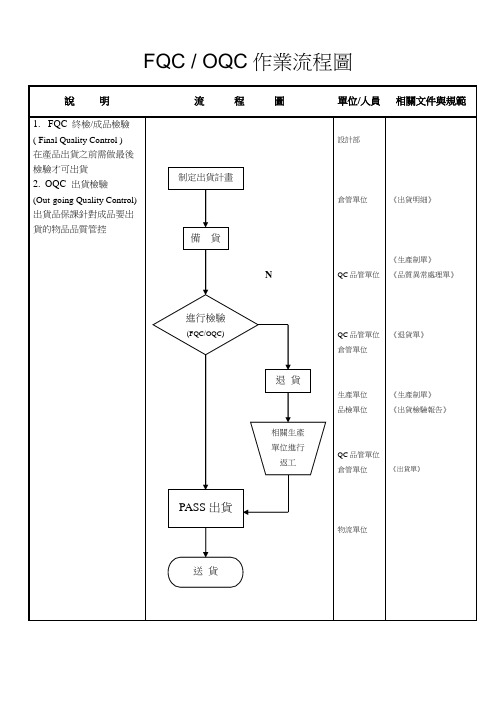
FQC / OQC作業流程圖製程巡檢作業辦法目的:落實品質意識在現場作業人員于制程過程中,實施檢驗或試驗以查證制程之合格性。
三〃範圍:凡本公司產品之各制程。
四、職責:生產部門:負責自製品自檢、送檢、重工、維修及入庫。
品保部門:負責自製品檢驗及記錄、標示。
五、內容:1、首件(產前樣/批版)、自主、巡迴檢驗:(1)品保部門IPQC人員在以下時段需做首件檢驗。
(1)每台機開始生產前開機需做首件檢驗。
(2)設計規格變更時需做首件檢驗。
(3)人員或材料更換時需做首件檢驗。
(2)生產部門作業人員應隨時注意生產產品品質狀況,並按照規定做好自主檢驗。
(3)品保部門IPQC人員應到現場做巡迴檢驗並做好記錄。
(4)品保部門檢驗管制程式,應按照規範和作業指導書之要求訂制(QC工程圖)。
(5)生產部門相關人員在制程中,發現不合格又無法矯正時,應及時停機報告主管,並通知品保部門,而品保部門應按照相關程式處理。
(6)品保部門IPQC人員按照實際檢驗情況記錄不合格品,並對制程式不良品作統計分析把結果回饋於相關部門,作糾正預防對策之依據。
(7)不合格品處理與標示(紅豆標&件投標):(1)、經判定為不合格品時,應在該批半成品貼上紅色圓點貼紙(故障貼紙)又稱紅豆,並加以區分,隨後將不合格批移至返工區或報廢區進行處理。
(2)、發生不合格品時,品保部門IPQC人員應填寫《IPQC服裝(巡廠)驗貨報告》加以記錄,並按照相關程序處理,並通知相關部門處理。
六〃使用表單:1、首件(制前樣/批版)吊卡2、特采申請單3、IPQC服裝(巡廠)驗貨報告4、返工\返修單5、報廢單6、制程異常備忘錄不合格品處理作業辦法一、目的:按照品質計畫及管制措施找出不合格品,採取各項管理及處理措施,並對不合格品進行分析,以防誤用。
二、範圍:供方之原材料、主輔料;廠內制程中之半成品、成品和庫存品;顧客之退貨品。
三、職責:生產、資材部門:負責不合格品標示、隔離及處理,必要時參與評審。
QC工作流程(含各工序5个)

生产部门挑选/加工/翻修后的产品要 再次摆放在待检区内通知QC复查,直 至产品检验合格为止。
入库/转下工序
通过QC检验合格,产品标签上盖有QC 合格印章,或特采印章后产品才可入
库或转入下一部门生产。
编号
QC工作流程
生效日期 2020年11月10日
版本
1.0
制程品质异常处理流程
保密级别:C 级
第5页 共6页
生产上线
生产部根据PMC排产计划,领取合格物 料安排生产。
生产技术 部
调机或试组装 OK
技工/组长自检 NG
OK
NG
首件确认表 (不合格)
品管确认 OK
记录并签发 临时生产样板
员工操作前经生产技工/组长按图纸或 工艺要求调试机器、模具、夹具、试 装配,制作首件确认产品(有模号的 产品不同模号要各制作1件或多件)。
批量生产
生产部在接到QC的首件确认表和合格 的临时生产样板后,安排批量生产。
NG 生产组长
IPQC
员工自检 OK
QC巡检
NG
做巡检记录 不合格标识
OK
做巡检记录
生产组长 QC组长 不
合格处理
报 废
特 用采
使
挑 修选
翻
OK
入待检区
异常改善 效果确认
操作员在生产中每隔半小时或生产出 50--100PCS产品后要对照样板自检, 看产品的外观、形状是否出现变异后 有漏工序的现象。发现异常要及时通 知生产管理人员或QC确认处理。
现场做出改善措施后,QC要在1小时内 确认改善措施是否实施或改善的效 果,向上级(组长)汇报。
编号
QC工作流程
生效日期 2020年11月10日
QC-06、QC工作流程培训演义
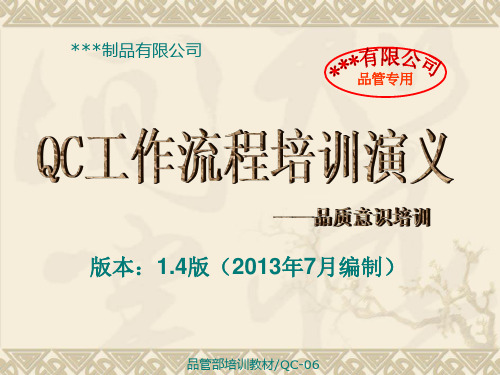
生产上线
生产部根据PMC排产计划,领取合格物 料安排生产。
生产技术部
调机或试组装 OK
技工/组长自检 NG
OK
NG 首件确认表 (不合格)
品管确认
调模产品 送首检QC 全检确认 品质状况 。判定合 格方可放 行。不合 格的退回
OK
记录并签发 临时生产样板
首件确认表 OK
临时生产样板 OK
员工操作前经生产技工/组长按图纸或 工艺要求调试机器、模具、夹具、试装 配,制作首件确认产品(有模号的产品 不同模号要各制作1件或多件)。
五金加工 □手动抛光 □自动抛光 □装配 □首饰 □工模 □生产技术 □样品 □设备维护 □仓储 □采购 □PM
待检验 出货产品
所有生产好的产品在转下一部门或入 库前,产品都要摆放到待检区内。
产品标识
待检区的产品要按要求贴好《产品/物 料状态标签》然后通知QC检验。
合格
记录 盖合格印章
QC抽查
不合格
QC确认首件合格,要做首件确认记录, 并给生产部签发临时生产样板。(首件 确认记表生产部一份,品管部一份)
QC将首件确认表和合格的临时生产样板 一起交给生产部。(旧产品从生产交首 件样板开始在30分钟内确认完成,新产 品在1--4小时内完成)
生产部在接到QC的首件确认表和合格的
批量生产
临时生产样板后,安排批量生产。(临 时生产样板要挂在操作员易看到、方便
首件产品生产技工/组长要先自检,确定 产品符合图纸工艺要求后再交品管确认。 (不可不自检就交品管确认,如品管确认 不合格一次,生产调模一次,这样来回确 认可能会耽误很多时间)
QC根据产品图纸、样板、产品检查核对表 全面检验产品是否符合品质要求。如确认 不合格将首件确认表和产品一起退回生产 部,要求改善。生产部不能改善合格可要 求生产技术部协助处理,改善后产品要继 续交给品管做首件确认。
IPQC的工作流程及检验流程

IPQC工作流程IPQC(In Proces s Qualit y Contro l)中文意思为制程控制,是指产品从物料投入生产到产品最终包装过程的品质控制。
(属品质保证部)1.负责首检和部分过程检查、制程中不良品的确认,标识及统计;2.负责巡检,对整个生产过程物料使用、装配操作、机器运行、环境符合性等全方位的定时检查确认。
IPQC工作流程简单的说:工作内容包括:首件检查、各类变更文件的跟踪。
4M1E的巡查。
发现异常的提出、跟踪与验证。
详细的说:过程检验(IPQC,in proces s qualit y contrl):目的是为了防止出现大批不合格品,避免不合格品流入下道工序去继续进行加工。
因此,过程检验不仅要检验产品,还要检定影响产品质量的主要工序要素(如 4MIE)。
实际上,在正常生产成熟产品的过程中,任何质量问题都可以归结为4M1E中的一个或多个要素出现变异导致,因此,过程检验可起到两种作用:1. 根据检测结果对产品做出判走,即产品质量是否符合规格和标准的要求;2. 根据检测结果对工序做出判定,即过程各个要素是否处于正常的稳定状态,从而决定工序是否应该继续进行生产。
为了达到这一目的,过程检验中常常与使用控制图相结合。
过程检验通常有三种形式:(1)首件检验:首件检验也称为“首检制”,长期实践经验证明,首检制是一项尽早发现问题、防止产品成批报废的有效措施。
通过首件检验,可以发现诸如工夹具严重磨损或安装定位错误、测量仪器精度变差、看错图纸、投料或配方错误等系统性原因存在,从而采取纠正或改进措施,以防止批次性不合格品发生。
通常在下列情况下应该进行首件检验:一,一批产品开始投产时;二,设备重新调整或工艺有重大变化时;三,轮班或操作工人变化时;四,毛坯种类或材料发生变化时。
IPQC工作流程图

品质部:IPQC 工作流程
工作流程 检验概述 流程概述 责任部门 或人员 生产部 QA 及班组长 现场 QC 及班 组品质主管
原料投产 ●首检:首件产品生产组长要先自检,确 定产品符合生产单要求和客户要求后再交 QA 确认。 (不可不自检就交巡检确认,如 巡检确认不合格一次,生产需返工一次, 这样来回确认可能会耽误很多时间)
NG 首检 OK OK 批量生产 OK 员工自检 OK 巡检 NG OK 终检 OK 转下工序 NG NG
反馈质检、班组 长改进
检验员
品质主管/车 间主管/生产 经理/班组长
标识、 隔离 下工序
通知车间主管或 班组长改进
检验员 全 检 返 工 报 废 ●终检:当一批产品生产结束后转序前巡 检员对其外观进行全检,功能进行抽检, 功能性有 1 件不合格需加抽,有再有 1 件 不合格判定该批不合格。 终检:对转序产品全检或抽样检验 各指标; 入仓:检验合格产品在放行单上签 检 验 员 / 仓 管 字,入仓保存; 员 存档:把各项检验记录,检查记录, 整改意见书等保存起来。
IPQC作业指导书及流程
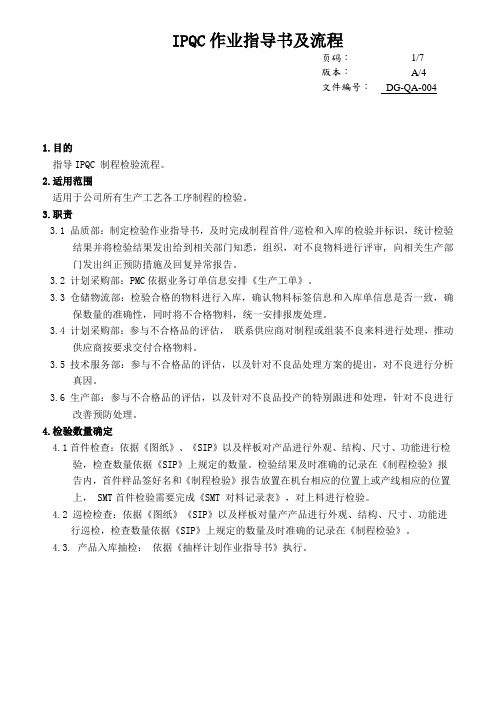
文件編号:DG-QA-0041.目的指导IPQC 制程检验流程。
2.适用范围适用于公司所有生产工艺各工序制程的检验。
3.职责3.1 品质部:制定检验作业指导书,及时完成制程首件/巡检和入库的检验并标识,统计检验结果并将检验结果发出给到相关部门知悉,组织,对不良物料进行评审, 向相关生产部门发出纠正预防措施及回复异常报告。
3.2 计划采购部:PMC依据业务订单信息安排《生产工单》。
3.3 仓储物流部:检验合格的物料进行入库,确认物料标签信息和入库单信息是否一致,确保数量的准确性,同时将不合格物料,统一安排报废处理。
3.4 计划采购部:参与不合格品的评估,联系供应商对制程或组装不良来料进行处理,推动供应商按要求交付合格物料。
3.5 技术服务部:参与不合格品的评估,以及针对不良品处理方案的提出,对不良进行分析真因。
3.6 生产部:参与不合格品的评估,以及针对不良品投产的特别跟进和处理,针对不良进行改善预防处理。
4.检验数量确定4.1首件检查:依据《图纸》、《SIP》以及样板对产品进行外观、结构、尺寸、功能进行检验,检查数量依据《SIP》上规定的数量。
检验结果及时准确的记录在《制程检验》报告内,首件样品签好名和《制程检验》报告放置在机台相应的位置上或产线相应的位置上, SMT首件检验需要完成《SMT 对料记录表》,对上料进行检验。
4.2 巡检检查:依据《图纸》《SIP》以及样板对量产产品进行外观、结构、尺寸、功能进行巡检,检查数量依据《SIP》上规定的数量及时准确的记录在《制程检验》。
4.3. 产品入库抽检:依据《抽样计划作业指导书》执行。
文件編号:DG-QA-0045.检验作业流程5.1 IPQC检验作业流程:文件編号:DG-QA-004 5.2 抛光QC检验作业流程:文件編号:DG-QA-004 5.3 IPQC首件完成时间规定文件編号:DG-QA-004 6.判定结果6.1若检查结果在允收范围内,则判整批合格。
QC工作流程图、生产流程图
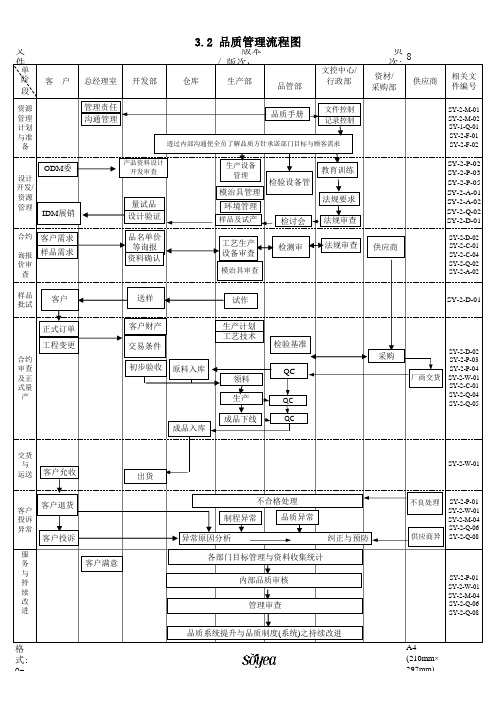
文件编号: SY-1-Q-01
单 阶 位 段
资源 管理 计划 与准 备
版本/ 版次:A/0
开发部 仓库 生产部 品管部 品质手册 文控中心/ 行政部
文件控制 记录控制
页
次:
资材/ 采购部
8
供应商 相关文 件编号
SY-2-M-01 SY-2-M-02 SY-1-Q-01 SY-2-F-01 SY-2-F-02
试作 生产计划 工艺技术
SY-2-D-01
正式订单
工程变更
合约 审查 及正 式量 产
检验基准 采购 QC QC
SY-2-D-02 SY-2-P-03 SY-2-P-04 SY-2-W-01 SY-2-C-01 SY-2-Q-04 SY-2-Q-05
成品下线 成品入库
交货 与 运送
SY-2-W-01
客户允收
出货
不合格处理
不良处理
SY-2-P-01 SY-2-W-01 SY-2-M-04 SY-2-Q-06 SY-2-Q-08
客户 投诉 异常 服 务 与 持 续 改 进
客户退货
制程异常 客户投诉
客户满意
品质异常 纠正与预防
供应商异
异常原因分析 各部门目标管理与资料收集统计 内部品质审核 管理审查
q00101法规要求教育训练品质手册客户承认正式订单客户允收客户退货试作不合格处理品质异常异常原因分析纠正与预防措施客户投诉客户需求检测审查法规审查检验基准qc工艺技术领料供应商管理管理审查品质系统提升与品质制度系统之持续改进记录控制文件控制检验设备管理工艺生产设备审查厂商交货内部品质审核标达成管理责任沟通管理样品需求品名单价承认工程变更客户满意客户财产交易条件审初步验收原料入库成品入库生产设备管理模治具审查环境管理生产计划生产成品下线qcqc采购不良处理供应商异常透过内部沟通使全员了解品质方针承诺部门目标与顾客需求模治具管理制程异常各部门目标管理与资料收集统计标达成出货odm委托资料确认产品资料设计开发审查idm展销与odm设计验证样品及试产检讨会法规审查ngngok车手把大扶手等前轮座后轮座等扶手轮子等车手把车手管大扶手前脚管前轮座后轮座轮轴扶手组装贴贴纸贴纸后脚管轮子组装轮轴等车手管前脚管后脚管等靠背太阳罩等车手贴纸说明书等领料平车车缝平车车缝搭dy平车缝制半成品上拉链各部位压明线成品包边锁眼打四合扣塑胶原材料外加五金件外加铝管外加缝制品外加印刷品外加包装纸箱外加检查仓库投入生产车手部分组装大扶手部分组装前轮座后轮座部分组装车手部分组装共它部分组装检查领料在线组装仓库检查包装仓库检查出货物料抽检首件确认各单位按单取料包装组合车架qc检查车架组合软件部分擦拭车台成品qc包装搬运车台不良品处理报废退回仓库合格不合格合格附表qc检验流程图生产二科检验标准的建立供应商交货仓库点收通知检验免检iqc检验标识入库完成品检验判定包装入库出货检验判定出货出货标识不合格原材料不良退货选用投入生产制成qc检验判定合格巡查日记不合格成品不合格在制品报废返工选用报废返工选用完成检验日记半成品
IPQC工作流程

制
检,并填写《注塑制程巡回检验报表》。
程
b 当出现异常应知会到生产部进行调试,并 将不良品进行隔离、标识等后续处理,出
检
现批量不良时应开具《品质异常联络单》
验
对于生产包装OK的产品应对产品进行抽
流
检,防止不良的流出(所有抽检的产品应 c 对其进行还原处理)
程
应核对物料标签是否填写正确(包括物料
编号、工单号、品名、规格、生产日期
文件名称
作业流程
检验 序 流程 号
流程详细说明
塑胶部生产组长按照《塑胶部生产排期》 通知技术人员进行生产安排,技术人员在 a 接到生产通知时,需按照要求对所需生产 的产品严格按照《成型条件记录卡》对产 品进行调试。
技术人员在按照《成型条件记录卡》调试 好产品后,需自检产品无外观性不良的情 b 况下,然后填写《塑胶制品首件确认单》 并取两啤样品送至IPQC办公室。
首件送检 NG
OK 首件单的确认
生产部 IPQC
《塑胶制品首件确认单》属于
《成型条件记录卡》 生产部填写的内容(工单号、
《塑胶制品首件确认单 物料名称、物料编号、模具编
》
号、材质、颜色、外观检验结
果)必需填写清晰、完整及正
确检验《塑胶制品首件确认单》
《塑胶制品首件确认单 上上述所填写的内容是否有错
》
验
生产部根据IPQC抽检判定OK的产品进行入
流
库 b
程
制 作:
xxx电器(深圳)有限公司
塑胶部 首件调试
塑胶部IPQC检验流程
流程图 品质部
项目部
责任人
生产部
文件编号: WI-PCD-045
版本:
A0 页次: 1/1相关文件及表单Fra bibliotek相关要求
IPQC作业规范

IPQC作业规范一、目的:通过IPQC首检和巡检预防生产线批量性品质事故发生,提高生产线品质水平。
二、适用范围:三、作业流程1.首件检查作业:1.1 首件检查作业时机:当新产品首次批量试产、老产品空拉下机、老产品机型转换、新材料试用、工程更改时,生产线应及时填写《转拉通知单》知会IPQC作首检,如有新材料、工程更改等需注明。
1.2IPQC首件检查项目:IPQC首件检查的项目包括工艺、材料、人员、仪器设备(夹具),IP QC接到《转拉通知单》后开始做首件检查工作。
针对要首件检查的机型,从下拉开始,检查每个工位的工艺、物料、特殊工位的人员、仪器设备是否符合要求。
产品流到哪里,IPQC就跟到哪里。
1.2.1 工艺核对:有无挂作业指导书,工序排位,操作是否符合作业指导书要求及有效《工程指导书》,对于关键工位需严格确认相关品质要求是否执行到位。
1.2. 2 物料核对:检验核对物料应尽可能提前,保证BOM清单,IQC PASS贴,实际物料三者一致。
对于部件需确认关的品质点,例如:原材料的生产厂家、塑胶组件是否放置2个小时以上,连板的版本号等,针对关键物料、特采物料需重点跟踪。
检查核对物料要在投产以前完成,如遇到急转拉,不能提前核对时就把BOM单(样板)等拿到线上一件一件核对,在核对物料时,严格以BOM清单为参照标准,如果BOM清单不是最新版本,需查相应的ECO和EIN更改。
部件加工组IPQC需要对辅料每周检查,确认辅料的有效期、规格、使用点。
同种物料外箱上标注的进料日期是否一致(或接近),如不一致要看是新进物料还是库存物料,如是仓库库存物料,则要特别注意过程中有无品质异常。
IPQC需对有机溶剂进行确认。
1.2.3 人员核对:特殊工位的员工是否具有《上岗实习证》或《上岗合格证》,关键工位的员工是否了解该工位的品质控制点。
1.2.4 样板仪器夹具核对:确认有合格的首件样板,当发生物料及工艺变更时,IPQC需对样板及时更新,IPQC在转拉时用首件样板核对工艺、物料,用首件样板核对插件方式,内部加工工艺,结构等与样板一致(此项适用于插件波峰项目)。
IPQC的工作流程及检验流程

IPQC工作流程IPQC(In Process Quality Control)中文意思为制程控制,是指产品从物料投入生产到产品最后包装过程的质量控制。
(属质量保证部)1.负责首检和部分过程检查、制程中不良品确实认,表记及统计;2.负责巡检,对整个生产过程物料使用、装置操作、机器运转、环境切合性等全方向的准时检查确认。
IPQC工作流程简单的说:工作内容包含:首件检查、各种更改文件的追踪。
4M1E 的巡逻。
发现异样的提出、追踪与考证。
详细的说:过程查验(IPQC,in process quality contrl):目的是为了防备出现大量不合格品,防止不合格品流入下道工序去持续进行加工。
所以,过程查验不单要查验产品,还要检定影响产质量量的主要工序因素(如 4MIE)。
实质上,在正常生产成熟产品的过程中,任何质量问题都能够归纳为 4M1E 中的一个或多个因素出现变异致使,所以,过程查验可起到两种作用:1.依据检测结果对产品做出判走,即产质量量能否切合规格和标准的要求;2.依据检测结果对工序做出判断,即过程各个因素能否处于正常的平定状态,进而决定工序能否应当持续进行生产。
为了达到这一目的,过程查验中经常与使用控制图相联合。
过程查验往常有三种形式:( 1)首件查验:首件查验也称为“首检制”,长久实践经考证明,首检制是一项尽早发现问题、防备产品成批报废的实用举措。
经过首件查验,能够发现诸如工夹具危机磨损或安装定位错误、丈量仪器精度变差、看错图纸、投料或配方错误等系统性原由存在,进而采纳纠正或改良举措,以防备批次性不合格品发生。
往常在以下状况下应当进行首件查验:一,一批产品开始投产时;二,设施重新调整或工艺有巨大变化时;三,轮班或操作工人变化时;四,毛坯种类或资料发生变化时。
首件查验大凡采纳“三检制”的方法,即操作工人推行自检,班组长或质量员进行复检,查验员进行专检。
首件查验后能否合格,最后应获得专职查验人员的认同,查验员对查验合格的首件产品,应打上规定的标志,并保持到本班或一批产品加工完了为止。
QC工作流程-产品首件确认作业流程

OKNGOKNGOKOK OK生产部根据PMC排产计划,领取合格物料安排生产。
QC确认首件合格,要做首件确认记录,并给生产部签发临时生产样板。
QC将首件确认表和合格的临时生产样板一起交给生产部。
(旧产品从生产交首件样板开始在30分钟内确认完成,新产品在1--4小时内完成)1、每一款产品上线生产2、新产品上线生产(新产品第一次生产时品管部通知生产技术课,由生产技术课签样)。
7、首件产品提供不能少于5PCS数量。
生产上线首件产品生产技工/组长要先自检,确定产品符合图纸工艺要求后再交品管确认。
(不可不自检就交品管确认,如品管确认不合格一次,生产调模一次,这样来回确认可能会耽误很多时间)编号版本WI-PG-0111.1生效日期2020年4月17日第1页 共6页QC工作流程产品首件确认作业流程员工操作前经生产技工/组长按图纸或工艺要求调试机器、模具、夹具、试装配,制作首件确认产品(有模号的产品不同模号要各制作1件或多件)。
调机或试组装6、首件产品以一个部门为单位完成所有加工工序,有模号区别的要提供每个模号产品。
生产部在接到QC的首件确认表和合格的临时生产样板后,安排批量生产。
(临时生产样板要挂在操作员易看到、方便拿取的地方。
)记录并签发临时生产样板临时生产样板QC根据产品图纸、样板、产品检查核对表全面检验产品是否符合品质要求。
如确认不合格将首件确认表和产品一起退回生产部,要求改善。
生产部不能改善合格可要求生产技术部协助处理,改善后产品要继续交给品管做首件确认。
批量生产首件确认条件:3、同一款产品中途停产3天后再生产。
4、产品换机、换材料、换工艺、图纸更改、模具/夹具维修5、不良品加工/翻修。
首件确认表(不合格)首件确认表生产技术部技工/组长自检品管确认。
WIISO 9000 14001 作业指导书 033首件确认工作指引(1)
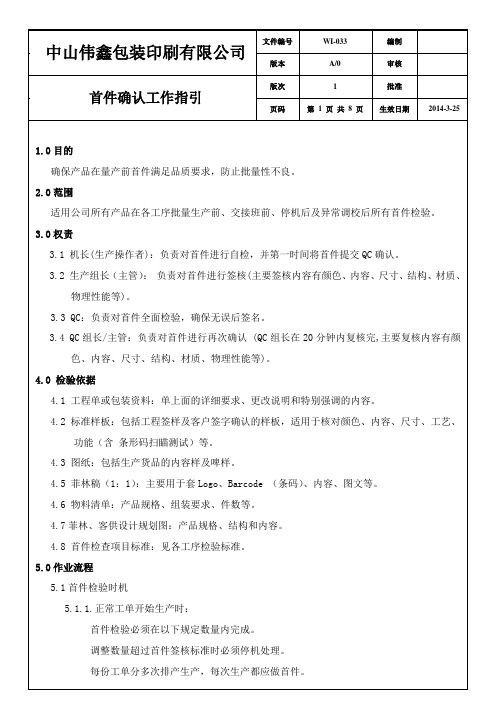
版次 1 批准首件确认工作指引页码第 1 页共8 页生效日期2014-3-251.0目的确保产品在量产前首件满足品质要求,防止批量性不良。
2.0范围适用公司所有产品在各工序批量生产前、交接班前、停机后及异常调校后所有首件检验。
3.0权责3.1 机长(生产操作者):负责对首件进行自检,并第一时间将首件提交QC确认。
3.2 生产组长(主管):负责对首件进行签核(主要签核内容有颜色、内容、尺寸、结构、材质、物理性能等)。
3.3 QC:负责对首件全面检验,确保无误后签名。
3.4 QC组长/主管:负责对首件进行再次确认 (QC组长在20分钟内复核完,主要复核内容有颜色、内容、尺寸、结构、材质、物理性能等)。
4.0 检验依据4.1 工程单或包装资料:单上面的详细要求、更改说明和特别强调的内容。
4.2 标准样板:包括工程签样及客户签字确认的样板,适用于核对颜色、内容、尺寸、工艺、功能(含条形码扫瞄测试)等。
4.3 图纸:包括生产货品的内容样及啤样。
4.5 菲林稿(1:1):主要用于套Logo、Barcode (条码)、内容、图文等。
4.6物料清单:产品规格、组装要求、件数等。
4.7菲林、客供设计规划图:产品规格、结构和内容。
4.8 首件检查项目标准:见各工序检验标准。
5.0作业流程5.1首件检验时机5.1.1.正常工单开始生产时:首件检验必须在以下规定数量内完成。
调整数量超过首件签核标准时必须停机处理。
每份工单分多次排产生产,每次生产都应做首件。
首件确认工作指引版次 1批准 页码第 2 页 共 8 页生效日期2014-3-255.1.2.换班开始时:如生产牵涉两班生产,两班均需做首件,如果不停机生产,在30分钟内必须签完首件;如果停机生产,按正常首件制度执行。
5.1.3.换版开始时:如印刷重新晒版、啤板拆板重新校板时,需同步完成首件确认。
5.1.4.换材料开始时:需重新确认首件。
5.1.5.机器故障后再开始生产时:由生产、品管组级以上人员确认是否需要重新确认首件。
IPQC岗位操作准则

5.8.3当出现严重质量异常或重复出现(2次或以上)异常时,由IPQC技术员通过《内部质量改善需求》将异常情况描述出来,经QA经理(或经理授权人)核实后由责任单位改善,IPQC技术员跟进改善结果。
5.4.1.2材料(包括上道工序转序之产品):是否为料表规定之规格,有无合格标示,有无超期(不合格的产品是否有上一道工序IPQC技术员处理意见)。
文件类别
深圳市鑫昆鹏电源科技有限公司
文件编号
KPA-QAD-004
标准文件
版 别
文件名称:IPQC岗位操作准则
页 码
2of3
5.4.1.3 设备、工具:有无校验标识,有无按期校正,设备、量规、检测仪器的运行参数与操作规程是否一致。
5.5半成品转序检验
5.5.1转序抽样由生产车间负责进行,IPQC技术员不定时抽查待转序之产品, 抽查过程若有不良由生产线进行处理,并发出《内部改善行动要求》要求相关部门作出改善行动及预防行动,IPQC技术员跟进其改善效果.
5.6资料的收集
5.6.1由生产部根据TQC的全检报告及相关的抽查报告每日进行一次汇总,生产部将汇总的报告提交一份给QE,IPQC高级技术员根据每日的汇总报告汇总成周报、月报,并作分析,将相关的重点问题点列入下周或下月的重点管理项目。
文件类别
xx科技有限公司
文件编号
KPA-QAD-004
标准文件
版 别
文件名称:IPQC岗位操作准则
页 码
1of3
1.目的
在制程中,通过巡检,依靠统计技术等对品质进行监控,达到预防不良产生的目的。
- 1、下载文档前请自行甄别文档内容的完整性,平台不提供额外的编辑、内容补充、找答案等附加服务。
- 2、"仅部分预览"的文档,不可在线预览部分如存在完整性等问题,可反馈申请退款(可完整预览的文档不适用该条件!)。
- 3、如文档侵犯您的权益,请联系客服反馈,我们会尽快为您处理(人工客服工作时间:9:00-18:30)。
OK
NG
OK
NG
OK
OK OK
生产部根据PMC排产计划,领取合格物料安排生产。
QC确认首件合格,要做首件确认记录,并给生产部签发临时生产样板。
QC将首件确认表和合格的临时生产样板一起交给生产部。
(旧产品从生产交首件样板开始在30分钟内确认完成,新产品在1--4小时内完成)
1、每一款产品上线生产
2、新产品上线生产(新产品第一次生产时品管部通知生产技术课,由生产技术课签样)。
7、首件产品提供不能少于5PCS数量。
生产上线
首件产品生产技工/组长要先自检,确定产品符合图纸工艺要求后再交品管确认。
(不可不自检就交品管确认,如品管确认不合格一次,生产调模一次,这样来回确认可能会耽误很多时间)
编号版本
WI-PG-0111.1
生效日期2020年4月17日第1页 共6页
QC工作流程
产品首件确认作业流程
员工操作前经生产技工/组长按图纸或工艺要求调试机器、模具、夹具、试装配,制作首件确认产品(有模号的产品不同模号要各制作1件或多件)。
调机或试组装
6、首件产品以一个部门为单位完成所有加工工序,有模号区别的要提供每个模号产品。
生产部在接到QC的首件确认表和合格的临时生产样板后,安排批量生产。
(临时生产样板要挂在操作员易看到、方便拿取的地方。
)
记录并签发临时生产样板临时生产样板
QC根据产品图纸、样板、产品检查核对表全面检验产品是否符合品质要求。
如确认不合格将首件确认表和产品一起退回生产部,要求改善。
生产部不能改善合格可要求生产技术部协助处理,改善后产品要继续交给品管做首件确认。
批量生产
首件确认条件:
3、同一款产品中途停产3天后再生产。
4、产品换机、换材料、换工艺、图纸更改、模具/夹具维修
5、不良品加工/翻修。
首件确认表(不合格)
首件确认表生产技术部技工/组长自检
品管确认。