线材的生产工艺和用途
线材的工艺流程
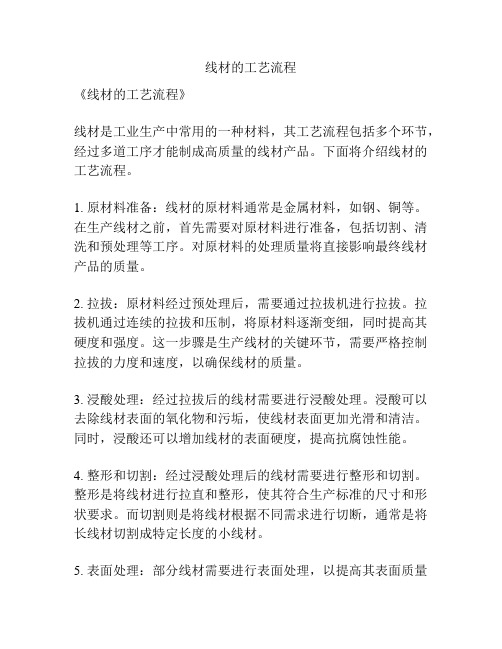
线材的工艺流程《线材的工艺流程》线材是工业生产中常用的一种材料,其工艺流程包括多个环节,经过多道工序才能制成高质量的线材产品。
下面将介绍线材的工艺流程。
1. 原材料准备:线材的原材料通常是金属材料,如钢、铜等。
在生产线材之前,首先需要对原材料进行准备,包括切割、清洗和预处理等工序。
对原材料的处理质量将直接影响最终线材产品的质量。
2. 拉拔:原材料经过预处理后,需要通过拉拔机进行拉拔。
拉拔机通过连续的拉拔和压制,将原材料逐渐变细,同时提高其硬度和强度。
这一步骤是生产线材的关键环节,需要严格控制拉拔的力度和速度,以确保线材的质量。
3. 浸酸处理:经过拉拔后的线材需要进行浸酸处理。
浸酸可以去除线材表面的氧化物和污垢,使线材表面更加光滑和清洁。
同时,浸酸还可以增加线材的表面硬度,提高抗腐蚀性能。
4. 整形和切割:经过浸酸处理后的线材需要进行整形和切割。
整形是将线材进行拉直和整形,使其符合生产标准的尺寸和形状要求。
而切割则是将线材根据不同需求进行切断,通常是将长线材切割成特定长度的小线材。
5. 表面处理:部分线材需要进行表面处理,以提高其表面质量和外观。
常见的表面处理包括镀锌、镀镍、喷涂等工序,这些处理可以增加线材的耐腐蚀性和美观度,进一步提高其使用寿命。
6. 包装和存储:最后,经过各种工艺流程处理的线材需要进行包装和存储。
线材通常会根据规格和尺寸进行分类包装,以便于运输和使用。
同时,需要注意线材的存储环境和条件,确保其不受潮湿和腐蚀。
以上就是线材的工艺流程,经过以上各个环节,才能生产出高质量的线材产品。
每个环节都需要严格控制,以确保最终产品符合要求。
高速线材生产工艺技术

高速线材生产工艺技术
一、前言
高速线材是一种重要的金属产品,在现代工业生产中扮演着重要的角色。
本文将介绍高速线材的生产工艺技术,包括材料选取、生产工艺流程、设备及技术要点等方面的内容。
二、材料选取
高速线材的生产需要选用优质的原材料,通常是优质碳素钢、合金钢等。
这些原材料需要具备良好的硬度、强度、韧性和耐磨性等特性,以确保生产出高质量的线材产品。
三、生产工艺流程
1.原材料准备:将选用的原材料进行清洗、除铁等预处理工序。
2.热处理:通过加热、保温、冷却等工艺,调整原材料的组织结构,
提高其机械性能。
3.坯料加工:将经过热处理的原材料进行拉拔、锻造等加工,使其形
成符合要求的线材坯料。
4.精整加工:通过轧制、精整等工艺,将坯料进行细致加工,使其直
径、表面质量等达到要求。
5.检验与包装:对成品进行检验,保证质量合格后进行包装。
四、设备及技术要点
1.轧机:高速线材的生产需要使用高效的轧机设备,以保证生产效率
和产品质量。
2.管控系统:通过先进的管控系统,实现对生产过程的精确把控,保
证产品质量的稳定性和可靠性。
3.冷却技术:采用合适的冷却技术,可以有效控制产品的温度和晶粒
结构,提高线材的硬度和强度。
五、结语
高速线材的生产工艺技术是一个复杂而精密的过程,需要依靠先进的设备和技术手段,才能生产出高质量的线材产品。
同时,生产过程中的质量管控和技术创新也是至关重要的。
希望本文所介绍的内容能够为相关行业提供一定的参考和帮助。
缝纫线生产工艺

缝纫线生产工艺一、原料选择缝纫线是一种由纤维和塑料制成的线材,其质量直接影响到服装、家居和工业用品的品质。
为了生产出高品质的缝纫线,首先需要选择优质的原料。
1. 纤维选择:缝纫线的主要原料是纤维,如棉、麻、涤纶、尼龙等。
选择纤维时,需要考虑其强度、耐磨性、耐热性、抗皱性等因素。
根据不同的需求,可以选择单一纤维或多种纤维的混纺。
2. 塑料选择:缝纫线通常需要具有一定的弹性和韧性,因此需要添加适量的塑料。
常用的塑料有聚酯、聚酰胺等。
选择塑料时,需要考虑其与纤维的相容性、耐热性、耐磨性等因素。
二、纺纱纺纱是缝纫线生产的关键环节之一,它通过将纤维和塑料混合并加工成线材。
纺纱的过程包括以下步骤:1. 混合:将纤维和塑料按照一定的比例混合,确保它们在纺纱过程中能够均匀分布。
2. 梳理:通过梳理机将混合后的原料梳理成单纤维状态,并除去其中的杂质和残次品。
3. 纺纱:将梳理后的单纤维通过锭子和钢丝圈旋转,并逐渐加捻成线材。
4. 加捻:在纺纱过程中,需要对线材进行加捻处理,以增加其强度和韧性。
加捻的程度需要根据不同的原料和用途进行调整。
5. 卷绕:将纺好的线材卷绕在筒子上,以便后续的加工和使用。
三、后处理纺纱完成后,需要对缝纫线进行后处理,以确保其质量和稳定性。
后处理包括以下步骤:1. 热定型:通过热定型工艺使缝纫线变得更加稳定,减少其在使用过程中的形变。
2. 染色:根据客户的需求,对缝纫线进行染色处理,以增加其色彩多样性。
3. 加工处理:根据不同的需求,可以对缝纫线进行抗静电处理、抗菌处理等特殊处理。
4. 包装:将处理好的缝纫线按照规格和颜色进行包装,以便客户使用。
总之,缝纫线生产工艺需要经过多个环节的精细操作才能得到高品质的产品。
从原料选择到纺纱再到后处理都需要严格的质量控制和技术管理以确保产品的质量和稳定性。
铝合金线材生产工艺及车间设计
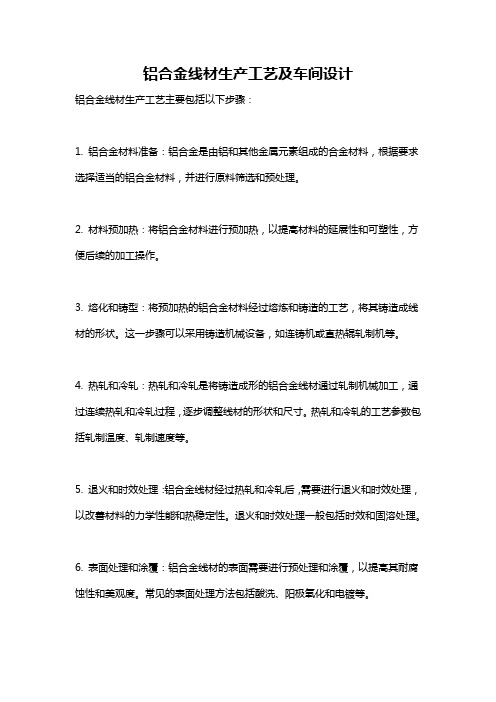
铝合金线材生产工艺及车间设计铝合金线材生产工艺主要包括以下步骤:1. 铝合金材料准备:铝合金是由铝和其他金属元素组成的合金材料,根据要求选择适当的铝合金材料,并进行原料筛选和预处理。
2. 材料预加热:将铝合金材料进行预加热,以提高材料的延展性和可塑性,方便后续的加工操作。
3. 熔化和铸型:将预加热的铝合金材料经过熔炼和铸造的工艺,将其铸造成线材的形状。
这一步骤可以采用铸造机械设备,如连铸机或直热辊轧制机等。
4. 热轧和冷轧:热轧和冷轧是将铸造成形的铝合金线材通过轧制机械加工,通过连续热轧和冷轧过程,逐步调整线材的形状和尺寸。
热轧和冷轧的工艺参数包括轧制温度、轧制速度等。
5. 退火和时效处理:铝合金线材经过热轧和冷轧后,需要进行退火和时效处理,以改善材料的力学性能和热稳定性。
退火和时效处理一般包括时效和固溶处理。
6. 表面处理和涂覆:铝合金线材的表面需要进行预处理和涂覆,以提高其耐腐蚀性和美观度。
常见的表面处理方法包括酸洗、阳极氧化和电镀等。
铝合金线材的车间设计需要考虑以下几个方面:1. 生产线布局:根据生产工艺流程,合理规划生产线的布局。
生产线之间应有足够的空间,以便设备的安装和维护。
同时,要确保生产线之间的物料和人员的流动线路畅通无阻。
2. 设备选择和摆放:根据生产工艺的要求,选择适当的设备。
设备摆放应合理,以便操作人员能够方便地进行操作和维护,同时要考虑安全和环保要求。
3. 设备安全:在生产车间中,应设置必要的安全设施,如防护网、防护栏等,以保障操作人员的安全。
此外,还需要设置紧急停机装置和灭火设备等应急设施。
4. 工艺参数控制:根据生产工艺的要求,合理设置工艺参数控制系统,以确保生产过程的稳定性和产品质量的一致性。
5. 环境管理:在车间设计中,还需要考虑环境管理,包括噪音控制、粉尘控制、废水处理等方面的工作。
总结起来,铝合金线材的生产工艺包括材料准备、熔化和铸型、热轧和冷轧、退火和时效处理、表面处理和涂覆等步骤。
铜包钢线材及其生产工艺
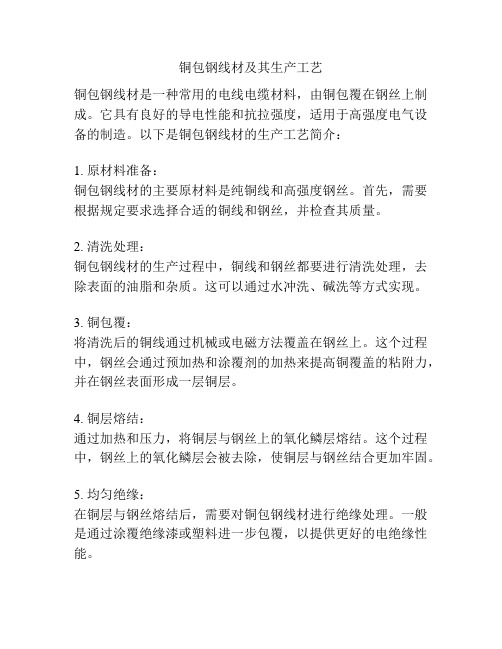
铜包钢线材及其生产工艺铜包钢线材是一种常用的电线电缆材料,由铜包覆在钢丝上制成。
它具有良好的导电性能和抗拉强度,适用于高强度电气设备的制造。
以下是铜包钢线材的生产工艺简介:1. 原材料准备:铜包钢线材的主要原材料是纯铜线和高强度钢丝。
首先,需要根据规定要求选择合适的铜线和钢丝,并检查其质量。
2. 清洗处理:铜包钢线材的生产过程中,铜线和钢丝都要进行清洗处理,去除表面的油脂和杂质。
这可以通过水冲洗、碱洗等方式实现。
3. 铜包覆:将清洗后的铜线通过机械或电磁方法覆盖在钢丝上。
这个过程中,钢丝会通过预加热和涂覆剂的加热来提高铜覆盖的粘附力,并在钢丝表面形成一层铜层。
4. 铜层熔结:通过加热和压力,将铜层与钢丝上的氧化鳞层熔结。
这个过程中,钢丝上的氧化鳞层会被去除,使铜层与钢丝结合更加牢固。
5. 均匀绝缘:在铜层与钢丝熔结后,需要对铜包钢线材进行绝缘处理。
一般是通过涂覆绝缘漆或塑料进一步包覆,以提供更好的电绝缘性能。
6. 冷却和整形:完成绝缘处理后,需要对铜包钢线材进行冷却和整形。
通过冷却,可以固定铜包钢线材的形状和尺寸,使其达到要求的标准。
7. 检验和包装:最后,对铜包钢线材进行各项检验,确保其质量符合要求。
检验项目包括导电性、机械性能和绝缘性能等。
合格的铜包钢线材经过包装后,可以进行存储和运输。
以上是铜包钢线材的主要生产工艺。
随着科技的发展,生产工艺也在不断改进和创新,以提高铜包钢线材的质量和生产效率。
铜包钢线材在电力、通信和交通等领域有广泛的应用,对于现代社会的发展具有重要作用。
线材工艺流程
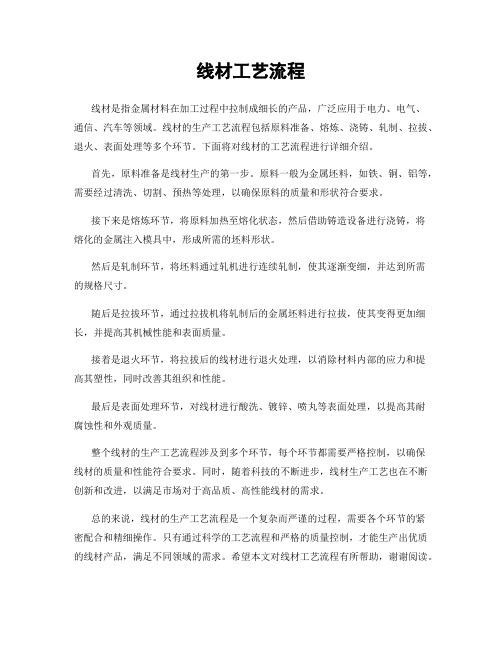
线材工艺流程
线材是指金属材料在加工过程中拉制成细长的产品,广泛应用于电力、电气、
通信、汽车等领域。
线材的生产工艺流程包括原料准备、熔炼、浇铸、轧制、拉拔、退火、表面处理等多个环节。
下面将对线材的工艺流程进行详细介绍。
首先,原料准备是线材生产的第一步。
原料一般为金属坯料,如铁、铜、铝等,需要经过清洗、切割、预热等处理,以确保原料的质量和形状符合要求。
接下来是熔炼环节,将原料加热至熔化状态,然后借助铸造设备进行浇铸,将
熔化的金属注入模具中,形成所需的坯料形状。
然后是轧制环节,将坯料通过轧机进行连续轧制,使其逐渐变细,并达到所需
的规格尺寸。
随后是拉拔环节,通过拉拔机将轧制后的金属坯料进行拉拔,使其变得更加细长,并提高其机械性能和表面质量。
接着是退火环节,将拉拔后的线材进行退火处理,以消除材料内部的应力和提
高其塑性,同时改善其组织和性能。
最后是表面处理环节,对线材进行酸洗、镀锌、喷丸等表面处理,以提高其耐
腐蚀性和外观质量。
整个线材的生产工艺流程涉及到多个环节,每个环节都需要严格控制,以确保
线材的质量和性能符合要求。
同时,随着科技的不断进步,线材生产工艺也在不断创新和改进,以满足市场对于高品质、高性能线材的需求。
总的来说,线材的生产工艺流程是一个复杂而严谨的过程,需要各个环节的紧
密配合和精细操作。
只有通过科学的工艺流程和严格的质量控制,才能生产出优质的线材产品,满足不同领域的需求。
希望本文对线材工艺流程有所帮助,谢谢阅读。
线材加工工艺流程
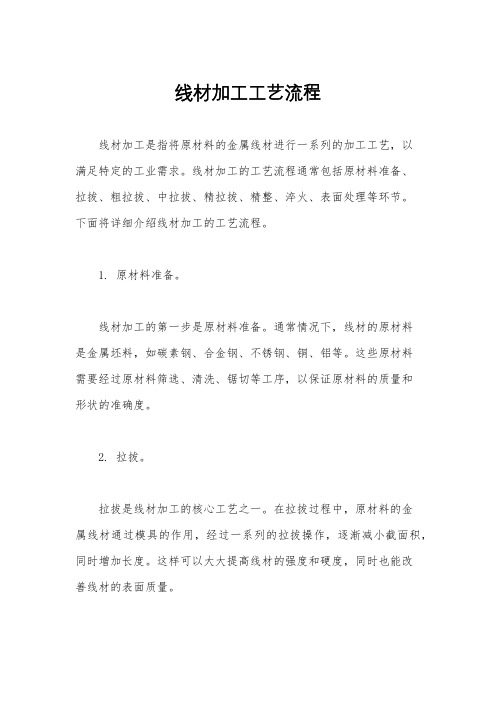
线材加工工艺流程线材加工是指将原材料的金属线材进行一系列的加工工艺,以满足特定的工业需求。
线材加工的工艺流程通常包括原材料准备、拉拔、粗拉拔、中拉拔、精拉拔、精整、淬火、表面处理等环节。
下面将详细介绍线材加工的工艺流程。
1. 原材料准备。
线材加工的第一步是原材料准备。
通常情况下,线材的原材料是金属坯料,如碳素钢、合金钢、不锈钢、铜、铝等。
这些原材料需要经过原材料筛选、清洗、锯切等工序,以保证原材料的质量和形状的准确度。
2. 拉拔。
拉拔是线材加工的核心工艺之一。
在拉拔过程中,原材料的金属线材通过模具的作用,经过一系列的拉拔操作,逐渐减小截面积,同时增加长度。
这样可以大大提高线材的强度和硬度,同时也能改善线材的表面质量。
3. 粗拉拔、中拉拔、精拉拔。
在拉拔过程中,通常会分为粗拉拔、中拉拔和精拉拔三个阶段。
粗拉拔是指通过较大的模具将原材料进行初步的拉拔,中拉拔是指通过适中的模具将线材进行进一步的拉拔,精拉拔则是指通过较小的模具将线材进行最终的拉拔。
这三个阶段的拉拔工艺可以有效地提高线材的强度和硬度,同时也能够改善线材的表面质量。
4. 精整。
精整是指通过切割、修整等工艺,对线材的尺寸、形状进行精确控制,以满足客户的特定要求。
精整工艺可以有效地提高线材的精度和表面质量,同时也能够改善线材的机械性能。
5. 淬火。
淬火是指将线材加热至一定温度,然后迅速冷却,以改善线材的组织结构和硬度。
淬火工艺可以有效地提高线材的强度和硬度,同时也能够改善线材的耐磨性和耐腐蚀性。
6. 表面处理。
表面处理是指对线材的表面进行镀锌、镀铬、喷涂等工艺,以提高线材的耐腐蚀性和美观度。
表面处理工艺可以有效地延长线材的使用寿命,同时也能够提高线材的市场竞争力。
综上所述,线材加工的工艺流程包括原材料准备、拉拔、粗拉拔、中拉拔、精拉拔、精整、淬火、表面处理等环节。
这些工艺环节相互配合,共同完成线材加工的全过程,最终生产出满足客户需求的高质量线材产品。
线材生产工艺及特点

汽车行业
在汽车行业中,线材主要用于 制造汽车零部件,如弹簧、紧 固件、车架等。
线材的强度和耐腐蚀性是汽车 零部件制造的关键因素,因此 对线材的质量要求较高。
汽车行业对线材的需求量较大, 且对线材的品质和性能要求严 格,因此对线材生产工艺的要 求也较高。
非金属线材
如塑料、橡胶等材料制成的线材,具有绝缘性好、耐腐蚀等特点 ,主要用于电线电缆、汽车配件等领域。
按生产方式分类
拉丝工艺
将金属锭通过多道拉丝模具拉成细丝,具有生产效 率高、成本低等特点。
挤出工艺
将塑料或橡胶等材料通过挤出机加热熔融后挤出成 线材,具有连续生产、产品长度无限等特点。
编织工艺
将多股线相互交织形成编织线,具有结构稳定、强 度高等特点,主要用于纺织、电缆等领域。
生产工艺的重要性
02
01
03
线材生产工艺是线材产品质量的关键,通过优化工艺 可以提高产品质量和性能。
先进的生产工艺可以提高生产效率,降低能耗和减少 环境污染。
生产工艺的持续改进和创新是企业发展的重要驱动力 ,能够提高企业的市场竞争力。
02
线材生产工艺分类
按材料分类
金属线材
包括不锈钢、铜、铝等金属材料制成的线材,具有高强度、导电 性好等特点,主要用于电子、电器、通讯等领域。
性能多样化
根据不同的材料和工艺, 线材可以具备各种不同的 性能,如导电性、耐腐蚀 性、强度等。
应用广泛
线材作为基础材料,广泛 应用于各个领域,如电子、 通讯、建筑、机械等。
04
线材生产工艺的应用
建筑行业
建筑行业是线材的主要应用领 域之一,线材主要用于钢筋混 凝土结构中的钢筋连接和固定 。
- 1、下载文档前请自行甄别文档内容的完整性,平台不提供额外的编辑、内容补充、找答案等附加服务。
- 2、"仅部分预览"的文档,不可在线预览部分如存在完整性等问题,可反馈申请退款(可完整预览的文档不适用该条件!)。
- 3、如文档侵犯您的权益,请联系客服反馈,我们会尽快为您处理(人工客服工作时间:9:00-18:30)。
线材的生产工艺和用途
一、线材的生产工艺
线材是指直径为5-22mm的热轧圆钢或相当此断面的异形钢,因以盘卷形式交货,故又通称为盘条。
常见的线材产品规格直径为5-13mm。
根据轧机的不同可分为高速线材(高线)和普通线材(普线)两种。
高线采用高速线材轧机上轧制,生产节奏快、盘较大(包中盘元通常是整根、最大盘重可达2500kg)、包装通常比较紧匝、漂亮。
高线是指用“高速无扭轧机”轧制的盘条。
轧制速度在80-160米/秒,每根重量(盘)在1.8-2.5吨,尺寸公差精度高(可达到0.02mm),在轧制过程中可通过调整工艺参数(特别是在冷却线上)来保证产品的不同要求。
普线是指用“普通轧机(一般是横列式复二重轧机)”轧制的盘条。
轧制速度20-60米/秒,每根重量(盘)在0.4-0.6吨(市场上见到的一般是三根六头为一大盘),在轧制过程中仅可通过冷却线上风冷或空冷来保证产品性能。
普线是用普通轧机轧制、一般盘重较小,一包通常由几段盘元包装而成、包装较松、较凌乱。
普通线材扎机已被列为落后产能,将被逐步淘汰。
线材的特点是断面小、长度大,对尺寸精度和表面质量要求较高。
主要的轧制工序有:
1)坯料线材的坯料以连铸小方坯为主,其边长一般为120~150mm,长度一般在6~12米左右。
在实际生产中,采用目测、电磁感应探伤和超声波探伤等方式检验连铸小方坯的质量;
2)加热一般采用步进式加热炉加热。
加热的要求是氧化脱碳少、钢坯不发生扭曲、不产生过热过烧等。
现代化的高速线材轧机坯料大且长,这就要求加热温度均匀、温度波动范围小。
3)轧制线材的断面比较单一,因此轧机专业化程度较高。
由于坯料到成品,总延伸较大,因此轧机架数较多,一般为21~28架,分为粗、中、精轧机组。
目前高速线材轧机成品出口速度已达100m/s以上。
4)精整由于现代线材轧制速度较高,轧制中温降较小甚至是升温轧制,因此线材精轧后的温度很高,为保证产品质量,要进行散卷控制冷却。
根据产品用途有珠光体控制冷却和马氏体控制冷却。
线材轧制工艺及设备示意图
其生产工艺流程如下:
钢坯运入→成批称重→入库存放→炉前上料→钢坯质量检查→单根称重→加热→粗轧→切头尾→中轧→预精轧(轧间水冷)→切头尾→精轧(轧间水冷)→穿水冷却→吐丝成圈→散卷冷却→集卷→切头尾→压紧打捆→称重挂牌→卸卷→入库
二、线材的特性与质量。